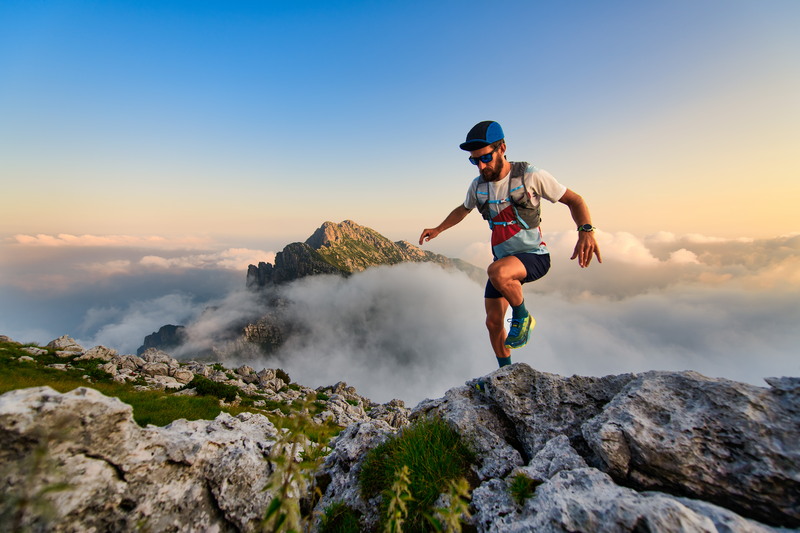
95% of researchers rate our articles as excellent or good
Learn more about the work of our research integrity team to safeguard the quality of each article we publish.
Find out more
ORIGINAL RESEARCH article
Front. Earth Sci. , 09 January 2023
Sec. Economic Geology
Volume 10 - 2022 | https://doi.org/10.3389/feart.2022.1089248
This article is part of the Research Topic Gas-Water-Rock Interaction and Multi Physical Field Coupling Mechanism View all 16 articles
This study is focused on coal mass fracture grouting sealing and seepage reduction with coal-based grouting sealing materials. First, a new type of coal-based grouting sealing materials was developed and applied to the fractured coal sample in the grouting test. Then, the coal sample before and after grouting was scanned and reconstructed with the aid of industrial computed tomography (CT). Based on CT images and reconstructed data, a theoretical model of grouting sealing for fractured coal mass was constructed by taking the migration and sedimentation of grouting slurry particles into consideration. Furthermore, on the ground of the theoretical model, a numerical calculation model of grouting sealing for the fractured coal sample was established, and the mechanism of grouting sealing and seepage reduction with coal-based sealing materials was simulated. Finally, a field test of gas extraction drilling and sealing was performed using the coal-based grouting sealing technology. The results show that: 1) The new type of coal-based grouting materials is effective in sealing the coal mass fracture, as the fracture is tightly filled with slurry particles after grouting. 2) The numerical simulation reproduces the whole process of grouting slurry flow and fracture sealing. After the permeability of the grouting coal sample decreases rapidly, it gradually tends to stabilize. The permeability of the whole coal sample goes down by 96% on average, and that of the fracture drops by more than 99.9% on average. The law of slurry diffusion and permeability variation calculated by numerical simulation is in line with the test results, which verifies the reasonableness of the model. 3) The application of the coal-based grouting sealing technology achieves an excellent sealing effect, promoting the gas extraction concentration by 1.43 times. The research results provide guidance for revealing mechanism of coal mass fracture grouting sealing with coal-based materials and bolstering the effect of extraction borehole sealing.
As coal mining in China extends into the deep, disasters such as coal and gas outburst are becoming increasingly severe. Since the increase in coal mining depth amplifies the in situ stress, the coal mass in deep coal seams is broken and soft with a weak bearing capacity (Chen et al., 2016). Under the influence of mining, a large number of fractures appear in the coal mass, causing changes in its stress state and inducing its instability and failure. Ultimately, disasters such as coal and gas outburst are likely to occur (Huang et al., 2019; Hao et al., 2021; Bao et al., 2022). Gas extraction is an important technical method to develop and utilize gas resources and prevent gas disasters in coal mines (Yu et al., 2015; Zhang et al., 2022a; Bi et al., 2022; Zhang et al., 2022b; Gao and Ren, 2022). However, under the influence of the excavation and mining of the roadway and borehole, the coal layer could be damaged by different degrees of deformation, so there are a large number of fractures and leakage channels around the extraction borehole (Liu et al., 2020; Wang et al., 2021; Li et al., 2022a). And seriously impacts the gas extraction effect (Zhou et al., 2016; Zhang et al., 2022c; Yao et al., 2022), the average concentration of coal mine gas extraction is merely 30% (Wang and Cheng, 2012; Wang et al., 2020).
In order to improve the efficiency of gas extraction scholars proposed cement mortar sealing technology (Zhang et al., 2022d), the polyurethane sealing technology, the sealing technology of “two plugs and one injection” and the bag sealing technology (Sun et al., 2022). Among them, “two plugs and one injection” is a common method to sealing boreholes in Chinese coal mines. The principle is to create a grouting space in the boreholes through the “two plugs” materials and then inject the sealing slurry under pressure (Yang et al., 2019). This method can promote the combination of slurry and fractures on the borehole wall in the coal seam, pertinently strengthen the sealing, and effectively enhance the gas extraction effect.
Under practical working conditions, sealing materials and sealing parameters are often selected according to experience, which lacks a scientific theoretical basis. This restricts the optimization of sealing effect for gas extraction boreholes (Li et al., 2016). Other scholars also have important reference significance for the test of sealing materials in this paper (Liu et al., 2020a). Therefore, in-depth study on the property of grouting materials and the mechanism of coal seam fracture sealing is of great engineering significance for enhancing the sealing effect of extraction boreholes and improving the efficiency of gas extraction.
Currently, scholars at home and abroad have carried out a series of research on grouting materials, characteristics of slurry flow inside coal rock fractures and mechanism of grouting sealing and seepage reduction with slurry (Li et al., 2022b). At present, the major object of research on grouting sealing materials is cement-based sealing materials. In terms of relevant research on slurry materials, primary consideration is given to the influence of slurry properties on bearing capacity and durability (Ge et al., 2014; Di et al., 2021; Guo et al., 2021). In order to utilize coal resources efficiently, scholars use coal debris as slurry material, on the ground of cement-based sealing materials, the addition of a certain concentration of coal fly ash. Research shows that compared to cement-based sealing materials, they not only enhance the mechanical strength and behavior of slurry, but also enhance the durability of sealing materials (Chindaprasirt et al., 2003; Liu et al., 2010; Nath and Sarker, 2011). Coal debris has the benefit of obtaining materials locally and low cost, utilizing waste resources rationally. Meanwhile, developed a new type of green sealing materials with borehole coal debris as the base material (Li et al., 2015). The property of slurry flow inside coal rock fractures plays an important role in investigating fracture evolution during the grouting process, and taking into account the time-varying concentration in the midst of slurry flow can more faithfully reflect the influence of sedimentation during solid particle migration (Yang et al., 2011; Zhang et al., 2015).
Some scholars have explored the sealing performance of grouting slurry for fractured rock mass. For instance, through engineering tests, Kang (Kang, 2021) proved the variation process of organic polymer materials in the field of grouting sealing and seepage reduction, and found that under the same grouting pressure, such materials boast a larger diffusion range and a better bonding effect in roadway surrounding rock. Based on the engineering practice of high-pressure grouting in mine roadways. Zhang et al. (2020) revealed the mechanism of grouting sealing and seepage reduction of coal mass, i.e., the slurry, as a semi-fluid, entered into the coal fractures under pressure, which restricts the entrance of gas and liquid. Yang et al. (2016) analyzed the fracture changes in mudstone samples before and after grouting under laboratory conditions with the aid of the computerized tomography CT scanning technology, and evaluated the fracture sealing performance using the fractal dimension method. Wei et al. (2020) investigated the grouting sealing and seepage reduction characteristics of fractured coal mass by means of industrial CT and numerical simulation. Liu et al. (2020b) studied the permeability evolution characteristics of rock mass before and after grouting through tests. Xu et al. (2019) explored the effect of grouting sealing and seepage reduction for deep fractured rock on a self-developed grouting physical simulation platform.
In the above research, scholars have conducted many useful explorations in grouting sealing materials, slurry flow models as well as grouting sealing and seepage reduction for fractured coal mass. However, the existing theoretical models rarely consider the coupling between slurry flow and coal deformation, and fail to investigate the fracture evolution under the combined effect of stress and slurry particle sedimentation. In this study, the fracture distribution of coal mass was reconstructed by adopting advanced experimental methods such as CT scanning, and the model of grouting sealing and seepage reduction for fractured coal mass was constructed. Besides, the fracture sealing mechanism of a new type of grouting slurry was quantitatively analyzed. Finally, the model of grouting sealing for gas extraction boreholes was established. The research results can lay a foundation for optimizing the grouting and sealing process of gas extraction boreholes and is of great theoretical and practical significance.
Bituminous coal from the 360803 working face of a mine in Huainan City, China, was selected and processed into a standard coal sample of 50 mm × 100 mm. Then, the sample was split with the Brazilian splitting method by the NY-60 pressure tester. Afterwards, a penetrating fracture would emerge in the coal sample. Next, the residual broken coal blocks were crushed and a 100-mesh sieve was used to screen pulverized coal (Figure 1). Finally, a new type of coal-based sealing materials was prepared with pulverized coal. The slurry was comprised of water, curing agent, expansion agent and pulverized coal whose particle size was less than 100 meshes at the water-solid ratio of 1.5. Configured a new coal-based sealing material using coal debris with a slurry water-solid ratio of 1.5, consisting of 500 g coal debris with particle size less than 100 mesh, 2 g curing agent, 400 g expansive agent, and 1,353 g water.
The grouting test on fractured coal mass adopted the “rock strata grouting test system-pour into system” independently developed and designed by Henan Polytechnic University. The test system mainly comprises six parts: a grouting pressure controller, a confining pressure controller, a digital collector, a slurry tank, a grouting pressure head and a coal sample holder. The photo and schematic diagram of the rock strata grouting test system are presented in Figures 2, 3, respectively. The test method are as follows: 1) The fractured coal sample was wrapped with sealing ring and then loaded into the grouting chamber. Grouting chamber left side connected to the grouting pressure head, right side connected to the slurry outlet and valve, and closed all the valves in the system, keeping the coal sample in an airtight environment. 2) Adjust confining pressure to 0.8 MPa through confining pressure controller. 3) Prepared slurry according to the slurry water-solid ratio of 1.5, and put into the slurry tank. 4) The coal-based grouting materials were poured into the fractured coal sample by the booster pump under the grouting pressure of 0.2 MPa for 30–40 min. The upper and lower valves of the grouting chamber were opened to keep the grouting circuit unblocked. 5) The grouting valves were closed and the coal sample was taken out for tests, after which the grouting pipeline and the booster pump were cleaned.
The permeability test was performed using the self-designed nitrogen seepage test system (Figure 4). The test system mainly consists of a gas path, a coal sample holder, a pressure gauge, a confining pressure controller and a measuring cylinder. Among them, the coal sample holder includes a confining pressure chamber, a permeability test pressure head and other components. Meanwhile, the confining pressure chamber is connected with the confining pressure controller to control the confining pressure that the coal sample is subject to. The permeability test pressure head is linked to the gas pipeline so as to test the permeability of the coal sample in the holder. The main parameters of the nitrogen seepage test system are as follows:
1) Coal sample size: Ф50 mm × 100 mm, precision ± 2 mm;
2) Confining pressure: 0–50 MPa, precision ± 0.1 MPa;
3) Gas pressure: 0–15 MPa, precision ± 0.05 MPa.
Before carrying out the permeability test, the following assumptions were made: 1) Nitrogen flows in the coal sample fracture as laminar flow, and gas seepage conforms to Darcy’s law; 2) Gas permeability is irrelevant to seepage pressure. The volume of gas seepage per unit time is measured by means of the water drainage method and substituted into the permeability calculation formula (Li et al., 2021):
where k is the permeability of the coal sample, mD; Q is the volume flow rate of nitrogen at the outlet under standard atmospheric pressure, m3/s; P0 is the standard atmospheric pressure, 101.325 kPa; μ is the dynamic viscosity of nitrogen, 1.66×10−5 Pa•s; B is the length of the coal sample, cm; P is the pressure of nitrogen at the inlet, MPa; A is the cross-sectional area of the coal sample, m2.
Under a confining pressure of 0.8 MPa, and measured the coal sample permeability before fracturing k1, the permeability after splitting k2 and the permeability after grouting k3 respectively, and listed in Table 1.
The permeability after grouting k3 is greatly reduced compared with the permeability after splitting k2. Indicating that the grouting of fractured coal mass would produce a better grouting effect and achieve the leakage sealing performance. However, the permeability after grouting k3 is little higher than the permeability before fracturing k1, the reason is that the slurry failed to completely sealing the detailed fractures in the coal sample, resulting in higher permeability.
The industrial CT equipment was used to scan the coal samples before and after grouting to obtain the CT images in Figure 5. Figure 5A displays the CT images before grouting, from which it can be seen that the fracture penetrates the coal sample and is of simple distribution overall. As the fracture extends from the top to the middle of the coal sample, it gradually narrows and tilts to the right, and the main fracture is found in the upper 2/3 of the coal sample. When stretching to 2/3 of the coal sample, the fracture begins to extend horizontally to the lower left, during which the fracture width changes insignificantly. Subsequently, it further extends downward, during which it becomes comparatively twisted, serrated and narrow. Finally, it turns into a crack at the bottom of the coal sample.
FIGURE 5. CT scan of coal sample before and after grouting. (A) Before grouting. (B) After grouting.
Figure 5B gives the CT images of fracture distribution of the reconstructed coal sample after grouting. As can be observed from the top view, the slurry has filled the fracture. As can be seen from the front view, the main fracture is filled with the slurry, except for the upper part. According to the side view, the filling effect is remarkable on the whole, but the slurry fails to fill the upper part of the coal sample sufficiently, probably because the fracture has such a large twist angle that the slurry cannot stay at the corner. Besides, the fracture at the bottom of the coal sample is not completely filled. The is attributed to the fact that this part of fracture is too narrow and too far from the top of the coal sample; consequently, the slurry whose pressure decreases gradually in the filling process fails to open up and fill the fracture at the bottom.
The coal mass is a pore-fracture dual-porosity medium. The grouting slurry mainly seeps into the coal mass alongside the fracture structure. The particles in the grouting slurry experience sedimentation while flowing under the influence of gravity. As a result, the pores and fractures of the coal mass become narrow or even blocked, thus affecting the porosity and permeability of the coal mass (Si et al., 2021a; Si et al., 2021b). For the convenience of modeling research, the following assumptions were made:
1) In the pore-fracture dual-porosity structure of fractured coal mass, the fracture variation plays a major role in seepage, and the influence of pores in the coal matrix is ignored;
2) The solid particles in the grouting slurry are incompressible, and the grouting concentration is stable and invariant;
3) The grouting slurry can be regarded as a Newtonian fluid;
4) The sedimentation of suspended particles in the grouting slurry is an irreversible process.
The fracture structure model of fractured coal mass is established (Figure 6). In the model, the coal matrix blocks are cubes with a side length of a; the width of the fracture is b; the volumes of the micro-unit of the coal matrix are V=(a+b) (Huang et al., 2019) and V1=a (Huang et al., 2019), respectively. The fracture rate φ of the micro-unit can be expressed as:
Figure 7 presents the micro-unit. By adopting the Euler description method, the equation of mass conservation for fractured coal mass during grouting is established as (Zhu et al., 2020):
where D is the volume fraction of particles in the fracture; φ is the fracture rate of fractured coal mass; Kdep is the sedimentation coefficient of particles; L is the length of the whole fracture, m; v is the absolute velocity when the particles migrate in the fractured coal mass, m/s.
The process of slurry flow in the micro-unit fractures is shown in Figure 8. The micro-unit method is adopted to divide the rough fracture into several smooth sections along the slurry flow direction, and each section is of relatively small lengths and different widths. In this way, the rough fracture can be replaced by a series of smooth sections.
Eq. 4 is the equation of permeability coefficient when the slurry flows in the coal mass that bears a single fracture (Li et al., 2017):
where Kf is the permeability coefficient of the coal fracture; ρ is the density of the slurry; g is the gravity of the slurry; n is the number of micro-unit fracture sections; and ek is the width of each section.
The grouting slurry seeps into the coal mass alongside the fracture and gradually migrates to the deep part of the fracture. In this process, it experiences sedimentation as a result of seepage velocity reduction and gravity. Under the impact of sedimentation, the particles gradually seal the coal fracture, which will inevitably lead to the decline of coal mass permeability. Eq. 5 is the equation of permeability variation (Wei et al., 2020):
where φ0 is the initial fracture rate of fractured coal mass; ρs is the density of suspended particles, g/cm3; S is the concentration of sedimented particles, g/cm3; C is the concentration of suspended particles in the fracture, g/cm3.
The above equations of mass conservation (3), slurry flow (4) and permeability evolution (5) together constitute the slurry flow coupling theoretical model.
In the above tests, industrial CT was used to scan the coal sample after splitting to obtain its internal fracture distribution. In this section, the multi-physics coupling software COMSOL Multiphysic was adopted to establish a numerical calculation model that shared the same size (50 mm in diameter and 100 mm in height) as the tested coal sample (Figure 9). CT images contain pore and frame information in each pixel, and the smaller the gray value of the image pixel, the higher porosity of the sample at that location. By selecting a reasonable threshold value, the porosity of the sample can be effectively described. Using a self-written Matlab program to extract and arrange the pixels of the CT scanned coal samples, and then import the reconstructed 3D pixel values of the coal samples into COMSOL by difference method, and refined mesh division was conducted.
The boundary conditions and initial conditions of the numerical calculation model were set up based on the test conditions. Since the coal-based sealing materials were injected from one end of the coal sample, the upper boundary of the model served as the slurry injection end, with the grouting pressure being 0.2 MPa and the model confining pressure being 0.8 MPa. The remaining boundaries were all impermeable ones, that is, the slurry would not overflow from these boundaries. The initial slurry concentration of the numerical calculation model was 0. Major parameters of numerical simulation are shown in Table 2.
As can be known in Figure 10, the grouting pressure on the fractured coal sample varies as time goes by. Specifically, the diffusion range of grouting pressure increases from the top to the bottom alongside the fracture. When the grouting time is 1,000 s, the grouting pressure basically runs through the whole coal sample, after which it remains basically stable. Moreover, the grouting pressure diffuses faster in the upper part of the coal sample and relatively slowly in the local area at the bottom. At 2,000 s, the grouting pressure in part of the fracture at the bottom is still rising. From the CT images, it can be known that the slurry diffuses fast in the upper part because the fracture is well developed and the permeability is high there, while it diffuses slowly in the lower part because the fracture is poorly developed there.
FIGURE 10. Cloud map of grouting pressure variation with time. (A–F) refers to the grouting pressure clouds at different times, in accordance with the numerical simulation specification.
The time-varying cloud map of coal permeability during grouting is exhibited in Figure 11 where the parts with a wide fracture and a high permeability are red and orange while those with a narrower fracture and a low permeability are light blue and dark blue. A penetrating fracture can be observed at 2/3 of the model. Before grouting, the permeability of the fracture is much higher than that of the unfractured area.
FIGURE 11. Cloud map of permeability variation with time. (A–F) refers to the permeability clouds at different times, in accordance with the numerical simulation specification.
As the grouting time passes by, the grouting slurry seeps into the coal mass along the fracture and gradually migrates and settles to the deep part of the fracture, resulting in the continuous narrowing and even sealing of the fracture. Ultimately, the permeability of the model decreases. When the grouting time is 100 s, the permeability in the upper part of the coal sample changes from reddish orange to light blue, which indicates that the permeability begins to drop as the slurry begins to enter the coal mass from the top. The permeability falls significantly in the early stage of grouting (before 400 s). With the passage of grouting time, the sealing effect gradually weakens. When the grouting time is 1,000 s, the permeability of the upper 2/3 of the coal sample gradually turns into dark blue, and slurry only fails to reach the left boundary. When the grouting time is 2,000 s, the coal sample changes into dark blue as a whole, which means that the slurry has basically filled the entire fracture. From the permeability variation in the grouting process, it can be found that the upper part of the fracture is sealed by the slurry first. As the grouting proceeds, the slurry continues to diffuse and seal the fracture downward until it finally seals the fracture. The reason is that the upper part of the fracture, which is developed, is conducive to slurry flow and sealing, while the lower part of the fracture, which is poorly developed, is unfavorable for slurry flow and sealing.
The curve of permeability of the grouting coal sample with time obtained by numerical simulation is shown in Figure 12. The numbers therein correspond to the permeabilities of the model at 0 s, 10 s, 100 s, 400 s, 1,000 s and 2,000 s, respectively. Overall, the permeability gradually goes down with time, by 93.5% on average. The permeability after splitting of the coal sample is 47.4 mD, stabilizes after around 1,000 s, and eventually reaches about 1.86 mD at 2,000 s, a decrease of 96.0%. In the test, the measured values of the permeability before and after grouting are 53.8 mD and 2.6 mD, respectively. The numerical simulation results are consistent with the test results, yet some errors still exist, because the permeability test was carried out after the grouting slurry inside the coal sample was dried. As can be seen from the permeability curve, after the grouting time exceeds 1,500 s, the permeability curve starts to decline slowly, barely affecting the overall permeability value of the model. Figure 13 presents the curve of permeability of the fracture with time in the grouting process obtained by numerical simulation. Clearly, the permeability of the fracture varies in the same trend as the overall permeability of the coal sample. The difference lies in that the fracture is of a higher initial permeability and a greater decrease range (more than 99.9%). The above numerical simulation results of fractured coal sample during grouting are basically the same as the measured results, which confirms the reasonableness of the theoretical model.
The above research shows that the coal-based grouting materials can tightly seal the coal mass fracture. On this basis, the borehole sealing device of “two plugs and one injection” was employed to seal the gas extraction borehole on site. The schematic diagram of the technology and relevant device coal-based grouting sealing for a gas extraction borehole is depicted in Figure 14. The borehole device is mainly composed of two 1-m-long capsular bags, two grouting pipes and a blast valve. One capsular bag is about 1 m away from the borehole outlet, and the other is about 1 m from the suction hole section. A slurry outlet containing a blast valve is set between the two capsular bags. During grouting, as the grouting pressure inside the capsular bags and the grouting pipelines rise, the blast valve will blast and open up to realize the sealing and filling the surrounding rock fracture between the capsular bags. In this way, the gas extraction borehole is sealed.
The coal-based grouting sealing technology was adopted to seal the gas extraction borehole in the coal seam of a track roadway in Zhaogu No. 2 Coal Mine. After the completion of gas extraction borehole construction, the sealing device of “two plugs and one injection” was fixed on the gas extraction pipe line and then transferred to the borehole. According to the water-solid ratio of 1.5, an appropriate number of additives was added into the slurry to configure the coal-based slurry which was then injected into the sealing device of “two plugs and one injection” by using the grouting pump. As the grouting process continued, the two capsular bags were gradually filled with the coal-based slurry, and the grouting pressure also rose accordingly. Subsequently, the grouting pressure opened up the bast valve. At this time, the grouting pressure would plunge. As the slurry filled the fracture in the surrounding rock, the grouting pressure went up again, and finally reached 1 MPa or so, which marks the completion of gas extraction borehole sealing. After the sealing, the gas extraction data were recorded with the average concentration of a single borehole within 3 months as the evaluation index (Figure 15). According to the recorded data, the gas extraction concentration after ordinary cement mortar borehole sealing ranges from 7.8% to 13.5% with an average of 10.7%, while the average gas extraction concentration after coal-based grouting sealing ranges from 11.6% to 18.9% with an average of 15.3%. The gas extraction concentration is promoted by 1.43 times, which suggests that the coal-based grouting sealing technology can achieve a better sealing effect.
In this paper, a new type of coal-based grouting sealing materials was developed and applied to the fractured coal sample in the grouting test. Furthermore, the coal sample before and after grouting was scanned and reconstructed by means of industrial CT. On this basis, the numerical calculation model of grouting sealing for the fractured coal sample was established, and the mechanism of grouting sealing and seepage reduction with coal-based sealing materials was simulated. Finally, the field test on gas extraction borehole sealing was performed using the coal-based grouting sealing technology. The main conclusions are listed as follows.
1) Through the permeability test on the fractured coal sample before and after grouting, it is found that the coal-based grouting materials can fill the fracture tightly, and the permeability plunges after grouting, which means that the coal-based grouting materials exert an excellent sealing effect on the coal sample. The numerical simulation results are basically the same as the measured results, which confirms the correctness of the theoretical model.
2) By constructing the fracture structure model, established a slurry flow coupling theoretical model of mass conservation, slurry flow and permeability evolution equation. On the ground of the real-time fracture industrial CT scanning reconstruction model, the whole process of coal sample fracture sealing by coal-based slurry was simulated by importing the reconstructed CT images into COMSOL numerical simulation software with the self-compiled Matlab program. By doing so, the variation of coal sample permeability with time was concluded. The research results provide guidance for exploring the mechanism of grouting sealing and seepage reduction and strengthening the sealing effect for gas extraction boreholes.
3) The gas extraction concentration after ordinary cement mortar borehole sealing ranges from 7.8% to 13.5% with an average of 10.7%, while the average gas extraction concentration after coal-based grouting sealing ranges from 11.6% to 18.9% with an average of 15.3%. The gas extraction concentration is promoted by 1.43 times, which indicates that the coal-based grouting sealing technology can achieve a better sealing effect.
The original contributions presented in the study are included in the article/Supplementary Material, further inquiries can be directed to the corresponding author.
YGwas responsible for writing and framing articles; BY offered a great deal of guidance and advice on writing articles; HZ assisted in completing the simulation part; BZ assisted in completing the experimental part; JS, QW, JN, and JL assisted in completing the field test part. All authors have read and agreed to the published version of the manuscript.
This study was supported by the National Natural Science Foundation of China (Grant Nos 52274193 and 52274192), promotion projects in Henan Province (Grant No. NSFRF220205) and the Innovative Scientific Research Team of Henan Polytechnic University in China (T2022-1). Natural Science Foundation of Henan (Grant No. 202300410182).
We thank the State Key Laboratory Cultivation Base for Gas Geology and Gas Control. We would like to express our gratitude to engineers of Zhaogu No. 2 Mine of Jiaozuo Coal Industry (Group) Co., Ltd. for their help in the field tests.
JS, QW, JN, and JL were empolyed by the Sima Coal Industry Co., Ltd., Shanxi Lu’an Group.
The remaining authors declare that the research was conducted in the absence of any commercial or financial relationships that could be construed as a potential conflict of interest.
All claims expressed in this article are solely those of the authors and do not necessarily represent those of their affiliated organizations, or those of the publisher, the editors and the reviewers. Any product that may be evaluated in this article, or claim that may be made by its manufacturer, is not guaranteed or endorsed by the publisher.
Bao, R. Y., Shi, B., and Zhang, C. (2022). Research and application of concentric ring reinforcement and sealing technology for gas drainage boreholes in soft-coal seams. ACS omega 7, 34763–34769. doi:10.1021/ACSOMEGA.2C01388
Bi, R. Q., Chen, X. X., Zhang, L., Wang, S. Y., Liu, X. H., and Hua, S. (2022). Refinement study on pressure relief zone of gas extraction borehole considering roughness. Sustainability 14, 9541. doi:10.3390/SU14159541
Chen, J. T., Guo, W. J., Yin, L. M., Lu, C., Chang, X. K., Zhang, S. C., et al. (2016). Experimental study of floor cracking under deep mining. Chin. J. Rock Mech. Eng. 35, 2298–2306. doi:10.13722/j.cnki.jrme.2015.1557
Chindaprasirt, P., Homwuttiwong, S., and Sirivivatnanon, V. (2003). Influence of fly ash fineness on strength, drying shrinkage and sulfate resistance of blended cement mortar. Cem. Concr. Res. 34, 1087–1092. doi:10.1016/j.cemconres.2003.11.021
Di, H. F., Zhang, H. B., Hou, C. Y., Zheng, D. D., Chai, H. C., Liu, L., et al. (2021). Effect of pre-curing stress on strength and micro structure of sulphoaluminate grouting materials. J. Henan Polytech. Univ. Nat. Sci. 40 (03), 163–168. doi:10.16186/j.cnki.1673-9787.2019120053
Gao, Y. B., and Ren, J. (2022). Study on the effect of borehole size on gas extraction borehole strength and failure mode. ACS omega 7, 25635–25643. doi:10.1021/ACSOMEGA.2C02834
Ge, Z. L., Mei, X. D., Lu, Y. Y., Xia, B. W., and Chen, J. F. (2014). Mechanical model and test study of sealed drilling for hydraulic fracturing in underground coal mines. Rock Soil Mech. 35 (07), 1907–1913. doi:10.16285/j.rsm.2014.07.019
Guo, X., Xue, S., Zheng, C. S., and Li, Y. B. (2021). Experimental research on performance of new gas drainage borehole sealing material with high fluidity. Adv. Mater. Sci. Eng. 2021, 1–12. doi:10.1155/2021/6645425
Hao, J., Li, X., Song, Y., Zhang, P., and Liu, H. (2021). Analysis of mining roadway with large deformation of broken soft coal and research on supporting technology: A case study in xin’an coal mine, China. Eng. Fail. Anal. 130, 105761. doi:10.1016/J.ENGFAILANAL.2021.105761
Huang, M. Q., Zhang, L., Zhang, C., and Chen, S. (2019). Characteristics of permeability changes in bituminous coal under conditions of stress variation due to repeated mining activities. Nat. Resour. Res. 29, 1687–1704. doi:10.1007/s11053-019-09542-0
Kang, H. P. (2021). Seventy years development and prospects of strata control technologies for coal mine roadways in China. Chin. J. Rock Mech. Eng. 40, 1–30. doi:10.13722/j.cnki.jrme.2020.0072
Li, B., Zhang, J. X., Liu, Y. W., Qu, L. N., Liu, Q., Sun, Y. X., et al. (2022). Interfacial porosity model and modification mechanism of broken coal grouting: A theoretical and experimental study. Surf. Interfaces 33, 102286. doi:10.1016/J.SURFIN.2022.102286
Li, H., Guo, S. S., and Li, C. (2015). Research and application of drilling cuttings backfill hole sealing technology. Saf. Coal Mines 46 (11), 14–20. doi:10.13347/j.cnki.mkaq.2015.11.004
Li, S. C., Liu, R. T., Zhang, Q. S., and Zhang, X. (2016). Protection against water or mud inrush in tunnels by grouting: A review. J. Rock Mech. Geotechnical Eng. 8, 753–766. doi:10.1016/j.jrmge.2016.05.002
Li, S. C., Zheng, Z., Liu, R. T., Wang, X. C., Zhang, L. Z., and Wang, H. B. (2017). Analysis on fracture grouting mechanism considering grout-rock coupling effect. Chin. J. Rock Mech. Eng. 36, 812–820. doi:10.13722/j.cnki.jrme.2016.0765
Li, T., Yao, B. H., Liu, Y., and Wang, D. K. (2021). Grouting fractured coal permeability evolution based on industrial CT scanning. Geofluids 2021, 1–12. doi:10.1155/2021/5564786
Li, X., Si, G. Y., Oh, J., Canbulat, I., Xiang, Z. Z., and Li, T. B. (2022). A pre-peak elastoplastic damage model of gosford sandstone based on acoustic emission and ultrasonic wave measurement. Rock Mech. Rock Eng. 55 (8), 4819–4838. doi:10.1007/s00603-022-02908-6
Liu, J. W., Wu, N., Si, G. Y., and Zhao, M. X. (2020). Experimental study on mechanical properties and failure behaviour of the pre-cracked coal-rock combination. Bull. Eng. Geol. Environ. 80, 2307–2321. doi:10.1007/s10064-020-02049-6
Liu, J. Z., Sun, W., Miao, C. W., and Liu, J. P. (2010). Research on the hydration heat of paste in ultra high strength concrete at low water-binder ratio. J. Build. Mat. (Shanghai, China. 13, 139–142. doi:10.3969/j.issn.1007-9629.2010.02.002
Liu, Q., Chen, W. Z., Yuan, J. Q., Wang, Y. X., and Wan, H. (2020). Evaluation of grouting reinforcement effect for karst filling medium based on seepage-erosion theory. Chin. J. Rock Mech. Eng. 39 (3), 1–9. doi:10.13722/j.cnki.jrme.2019.1112
Liu, Y., Zhang, J., Wei, J. P., and Liu, X. T. (2020). Optimum structure of a Laval nozzle for an abrasive air jet based on nozzle pressure ratio. Powder Technol. 364, 343–362. doi:10.1016/j.powtec.2020.01.086
Nath, P., and Sarker, P. (2011). Effect of fly ash on the durability properties of high strength concrete. Procedia Eng. 14, 1149–1156. doi:10.1016/j.proeng.2011.07.144
Si, L. L., Wei, J. P., Xi, Y. J., Wang, H. Y., Wen, Z. H., Li, B., et al. (2021). The influence of long-time water intrusion on the mineral and pore structure of coal. Fuel 290, 119848. doi:10.1016/J.FUEL.2020.119848
Si, L. L., Zhang, H. T., Wei, J. P., Li, Bo., and Han, H. K. (2021). Modeling and experiment for effective diffusion coefficient of gas in water-saturated coal. Fuel 284, 118887. doi:10.1016/j.fuel.2020.118887
Sun, X. Y., Li, K., and Wang, X. (2022). Capsule-bag-type sealing technology for gas drainage boreholes and its application. Geofluids 2022, 1–14. doi:10.1155/2022/1671859
Wang, C. B., Si, G. Y., Zhang, C. G., Cao, A. Y., and Canbulat, I. (2021). Location error based seismic cluster analysis and its application to burst damage assessment in underground coal mines. Int. J. Rock Mech. Min. Sci. (1997). 143, 104784. doi:10.1016/j.ijrmms.2021.104784
Wang, L., and Cheng, Y. P. (2012). Drainage and utilization of Chinese coal mine methane with a coal-methane co-exploitation model: Analysis and projections. Resour. Policy 37, 315–321. doi:10.1016/j.resourpol.2012.06.013
Wang, W., Li, H., Liu, Y., Liu, M., Wang, H., and Li, W. (2020). Addressing the gas emission problem of the world’s largest coal producer and consumer: Lessons from the sihe coalfield, China. Energy Rep. 6, 3264–3277. doi:10.1016/J.EGYR.2020.11.199
Wei, J. P., Yao, B. H., Liu, Y., Wang, D. K., Cui, P. F., and Yao, S. (2020). Grouting fluid diffusion law and variable mass seepage model for fractured coal. J. China Coal Soc. 45 (01), 204–212. doi:10.13225/j.cnki.jccs.YG19.1526
Xu, Z. P., Liu, C. W., Zhou, X. W., Gao, G. R., and Feng, X. H. (2019). Full-scale physical modelling of fissure grouting in deep underground rocks. Tunn. Undergr. Space Technol. 89, 249–261. doi:10.1016/j.tust.2019.04.008
Yang, H. M., Ren, F. K., Wang, Z. F., Chen, S. W., and Pei, G. Z. (2019). Quality inspection and quantitative evaluation method for borehole sealing in gas drainage. J. China Coal Soc. 44 (S1), 164–170. doi:10.13225/j.cnki.jccs.2018.1176
Yang, R. S., Xue, H. J., Guo, D. M., He, T. Y., Li, T. T., Zhao, P. F., et al. (2016). Laboratory grouting experiment based CT analysis of grouted soft rocks in deep mines. J. China Coal Soc. 41 (2), 345–351. doi:10.13225/j.cnki.jccs.2015.0328
Yang, Z. Q., Hou, K. P., and Guo, T. T., and , M. Q. (2011). Study of column-hemispherical penetration grouting mechanism based on Bingham fluid of time-dependent behavior of viscosity. Rock Soil Mech. 32, 2697–2703. doi:10.16285/j.rsm.2011.09.037
Yao, B. H., Yao, S., Wei, J. P., Wen, Z. H., Liu, Y., and Si, L. L. (2022). A new method for determining the sealing depth of extraction borehole based on the constant-pressure gas injection and its applications. Rock Mech. Rock Eng. 55, 3703–3717. doi:10.1007/S00603-022-02844-5
Yu, B. H., Su, C., and Wang, D. (2015). Study of the features of outburst caused by rock cross-cut coal uncovering and the law of gas dilatation energy release. Int. J. Min. Sci. Technol. 25, 453–458. doi:10.1016/j.ijmst.2015.03.020
Zhang, H. D., Liu, Y., Tang, J. R., Liu, W. C., and Chen, C. J. (2022). Investigation on the fluctuation characteristics and its influence on impact force of supercritical carbon dioxide jet. Energy 253, 124125. doi:10.1016/J.ENERGY.2022.124125
Zhang, J. F., Lin, H. F., Li, S. G., Yang, E. H., Yang, D., Yang, B., et al. (2022). Accurate gas extraction(age) under the dual-carbon background: Green low-carbon development pathway and prospect. J. Clean. Prod. 377, 134372. doi:10.1016/J.JCLEPRO.2022.134372
Zhang, J. X., Li, B., Liu, Y., Li, P., Fu, J. W., Chen, L., et al. (2022). Dynamic multifield coupling model of gas drainage and a new remedy method for borehole leakage. Acta Geotech. 17, 4699–4715. doi:10.1007/S11440-021-01444-X
Zhang, Q. S., Zhang, L. Z., Zhang, X., Liu, R. T., Zhu, M. T., and Zheng, D. Z. (2015). Grouting diffusion in a horizontal crack considering temporal and spatial variation of viscosity. Chin. J. Rock Mech. Eng. 34 (6), 1198–1210. doi:10.13722/j.cnki.jrme.2014.0958
Zhang, X. B., Gao, J. L., Jia, G. N., and Zhang, J. W. (2022). Study on the influence mechanism of air leakage on gas extraction in extraction boreholes. Energy Explor. Exploitation 40, 1344–1359. doi:10.1177/01445987211070664
Zhang, Z. F., Kang, H. P., Jiang, Z. Y., Li, W. Z., Jiang, P. F., Cai, R. C., et al. (2020). Study and application of high-pressure splitting grouting modification technology in coalmine with depth more than 1 000 m. J. China Coal Soc. 45, 972–981. doi:10.13225/j.cnki.jccs.SJ19.1545
Zhou, F. b., Sun, Y. N., Li, H. J., and Yu, G. F. (2016). Research on theoretical model and engineering technology of the coal seam gas drainage hole sealing. J. China Univ. Min. Technol. Engl. Ed. . 45 (03), 433–439. doi:10.13247/j.cnki.jcumt.000498
Keywords: gas extraction, coal-based materials, grouting sealing, fractured coal mass, seepage reduction mechanism, sealing test
Citation: Gao Y, Yao B, Zhang H, Zhang B, Song J, Wang Q, Niu J and Li J (2023) Study on the test of coal mass fracture grouting sealing with coal-based materials and its application. Front. Earth Sci. 10:1089248. doi: 10.3389/feart.2022.1089248
Received: 04 November 2022; Accepted: 22 November 2022;
Published: 09 January 2023.
Edited by:
Guangyao Si, University of New South Wales, AustraliaReviewed by:
Yinlong Lu, China University of Mining and Technology, ChinaCopyright © 2023 Gao, Yao, Zhang, Zhang, Song, Wang, Niu and Li. This is an open-access article distributed under the terms of the Creative Commons Attribution License (CC BY). The use, distribution or reproduction in other forums is permitted, provided the original author(s) and the copyright owner(s) are credited and that the original publication in this journal is cited, in accordance with accepted academic practice. No use, distribution or reproduction is permitted which does not comply with these terms.
*Correspondence: Banghua Yao, eWFvYmFuZ2h1YUAxMjYuY29t
Disclaimer: All claims expressed in this article are solely those of the authors and do not necessarily represent those of their affiliated organizations, or those of the publisher, the editors and the reviewers. Any product that may be evaluated in this article or claim that may be made by its manufacturer is not guaranteed or endorsed by the publisher.
Research integrity at Frontiers
Learn more about the work of our research integrity team to safeguard the quality of each article we publish.