- 1State Key Laboratory of Geomechanics and Geotechnical Engineering, Institute of Rock and Soil Mechanics, Chinese Academy of Sciences, Wuhan, China
- 2University of Chinese Academy of Sciences, Beijing, China
The rock properties are related to the stress environment and dynamic disturbance during construction, and the testing-while-drilling-technique was used for evaluation of rock properties. However, the related research ignored the influences of stress environment and drilling parameters. In this study, triaxial compression tests and laboratory drilling tests under different confining stresses and drilling parameters were conducted for intact granite, and the numerical changes of drilling parameters were recorded. Then the static elastic energy and drilling specific energy (dynamic energy) of rock were calculated by using linear energy storage theory and rock breaking energy theory, respectively. According to the characteristics of energy variation, an energy analysis method based on drilling process was proposed, and the sum of static elastic energy and dynamic elastic energy was defined as the total energy. The results showed that: 1) the static elastic energy increased with the increase of confining stress, while the drilling specific energy was opposite. 2) For the same rock, the total energy was constant under the same drilling parameters. 3) The influence of drilling parameters on total energy was quantified by dynamic load influence factor. Finally, the potential application of energy analysis method in stress estimation was discussed through drilling tests.
1 Introduction
An engineering rock mass is generally in a state of combined action of static stress and dynamic load. Self-weight and tectonic stress constitute the static environment of the rock. Explosive blasting, mechanical drilling, and other construction-related factors can cause dynamic disturbances to the rock mass. Drilling plays a vital role in engineering construction and monitoring, energy exploration and development. In recent years, test-while-drilling (TWD) technology has fully exploited the advantages of in-situ testing.
TWD is a typical field test method (Xia et al., 2022) to evaluate rock properties by collecting and analyzing drilling parameters (drilling rate, drilling force, bit rotation speed, and bit torque). Many studies have proved that differences in rock properties can lead to changes in drilling parameters, and the hardness, rock integrity and spatial distribution of faults and holes can be determined by drilling rate (Yang et al., 2012; Chen and Yue, 2015), bit torque (Gui et al., 2002; Van Wyk et al., 2014; Wang et al., 2018a), and specific energy (Yasar et al., 2011). Determination of rock grade by drilling energy analysis is a commonly used method (Tan et al., 2007; Oparin et al., 2018; Sakiz et al., 2021), and current TWD theory assumes the energy required to break the same rock is a constant value, and this energy is only related to the grade and type of rock (Kahraman, 1999; Karasawa et al., 2002; Mostofi et al., 2011; Wang et al., 2018b; Wang et al., 2019). However, in engineering practice, drilling parameters vary greatly in the same stress environment. The strength and stiffness of rock vary with confining stresses and loading rates (Yang et al., 2006; Liu S. H. et al., 2014). Compared with other types of rocks, the confining stress and loading rate have more significant effects on intact, hard and brittle rocks, implying that the confining stress and drilling parameters have a greater impact on the drilling specific energy of intact rock. The drilling specific energy is the energy required to excavate unit volume of rock by the bit. In the process of rock failure, it is not only necessary to absorb energy from the outside, but also to dissipate energy in the form of plastic properties or kinetic energy (Bai et al., 2019; Bai et al., 2021; Bai et al., 2022). However, current TWD energy analysis methods ignore the stress environment, drilling parameters (Zhang and Gao, 2015; Su et al., 2022; Zhao et al., 2022), and energy dissipation which leads to limited applicability of energy analysis results.
In the drilling tests, the authors have found that for the same rock, the drilling specific energy varies under different confining stresses and drilling parameters. The tests results cannot be reasonably explained by the current TWD energy theory, which indicates that the TWD energy theory needs to be improved.
In the analysis of rockburst energy in hard rock, considering the influence of confining stress and construction disturbance, a coupled static-dynamic loading theory was proposed (Li and Gu, 2002). This theory assumes that rock failure is the result of the combined action of confining static stress and construction disturbance, the initial stress condition determines the intensity and quantity of energy released during failure, and the dynamic disturbance is only the induced condition (Gong et al., 2010; Gong et al., 2010, 2014; Gong et al., 2020), this theory is currently applied to rockburst prediction in tunnel excavation and underground mining (Liu Q. S. et al., 2014; Luo et al., 2015; Wang et al., 2015; He et al., 2018; Li et al., 2019). Studies have shown that when the confining stress is constant, different dynamic load conditions will affect the absorption and release of energy by rocks, resulting in changes in its mechanical properties (Li et al., 2011a). The stronger the dynamic disturbance, the less energy released during rock failure (Gong et al., 2011). These findings are consistent with the drilling tests results performed by the authors.
Therefore, in order to reasonably explain the impact of confining stress and drilling parameters on rock drilling energy and better evaluate rock properties through TWD, triaxial compression tests under different confining stresses and drilling tests under different confining stresses and drilling parameters were conducted on intact granite. The influence of stress conditions and drilling parameters on drilling specific energy was analyzed. Referring to the coupled static-dynamic loading theory for rockburst, a new energy analysis method based on drilling process was proposed to evaluate rock properties.
2 Energy of intact granite under static load
2.1 Linear energy storage theory
The confining stress can be regarded as static load, and the energy generated is referred to as static load energy
where
where
2.2 Rock compression tests
Granite is a common engineering rock mass. Many hydropower stations and pumped storage dam foundations are based on intact granite, and some underground power plants are built in intact granite rock mass. The natural intact granite from Changtai County, Quanzhou, Fujian, China, was sampled. The average compressive strength obtained by the uniaxial compression test is 251 MPa, the tensile strength is 13.57 MPa, the cohesion is 39.49 MPa, and the internal friction angle is 56.95°. The granite was processed into a standard triaxial sample with a diameter of 50 mm and a height of 100 mm. Since the depth of most underground power plants is usually less than 1 km, and the confining stress at this depth is about 25 MPa. The confining stresses in the compression test were set to 0, 5, 10, 15, 20 and 25 MPa. According to “DZ/T 0276.19-2015 Rock Physical and Mechanical Property Test Specification Part 19: Rock Uniaxial Compression Deformation Test”, China, “DZ/T 0276.20-2015 Rock Physical and Mechanical Property Test Specification Part 20: Rock Triaxial Compression Strength Test,” China, confining and axial stresses were applied at a rate of .05 MPa/s. When the confining stress was increased to a predetermined value, the variation therein should not exceed 2%. The axial load was controlled by displacement, and the cross-head displacement rate was .001 mm/s until the sample breaks. The compression test under each confining stress is repeated five times (error less than 1 MPa). The average value of five tests is taken as the compressive strength of rock under this confining stress. Figures 2, 3 show the rock failure mode and stress-strain curve of only one of the five tests. Axial and confining stress were recorded during the compression process, and the stress-strain curve of rock was plotted. Test design and stress-strain data are displayed in Table 1.
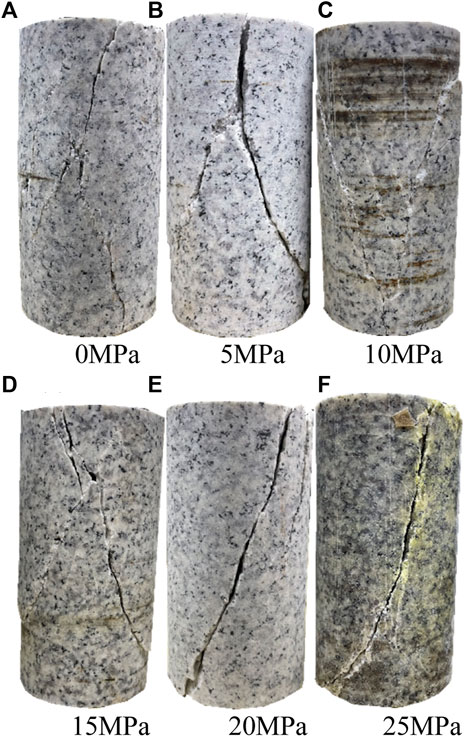
FIGURE 2. Typical failure modes of samples. (A) 0 MPa (B) 5 MPa (C) 10 MPa (D) 15 MPa (E) 20 MPa (F) 25 MPa.
According to Table 1, the peak stress and peak strain increase with the increase of confining stress. The failure mode of intact granite is a typical brittle failure; especially in unconfined compression tests, rock failure is accompanied by a tremendous release of energy, a loud sound, and ejection of debris. This finding indicates that granite is an elastic brittle rock that stores a significant amount of energy before failure. Typical failure modes are shown in Figure 2. The stress-strain curves are depicted in Figure 3, and each curve only truncates before the peak stress.
The stress-strain curves of each group accord with the typical characteristics of elastic materials. Upon initiation of loading, the pores and micro-cracks in the granite are gradually closed, and the stress-strain curve is slightly concave. Then it enters the elastic stage, and the stress-strain relationship is linear. When failure is imminent, the curve is concave, and the micro-cracks in the granite are in the state of branching and expansion. At peak stress, the fissures are connected to form a failure surface, and the granite breaks. The linear part accounts for a large proportion of the whole stress-strain curve, which indicates that the mechanical properties of granite are elastic when the confining stress is within 25 MPa.
2.3 Static elastic energy
The values of
In the elastic stage,
3 Energy of intact granite under dynamic load
3.1 Laboratory drilling test design
According to the working characteristics of a drilling rig in engineering practice, a laboratory drilling test platform that can simulate the stress environment of surrounding rock was developed. The test platform comprises a servo-motor control system, drilling acquisition system, propulsion acquisition system, and confining stress system. The four systems control and collect drilling parameters, including drilling rate, drilling force, bit rotation speed, bit torque, and confining stress. The platform allows controllable drilling under different confining stresses. The internal structure of the confining stress system is shown in Figure 5. The main technical parameters of the test platform are listed in Table 3.
Three-edge, three-water way flat-tooth diamond-impregnated core bits were used in drilling tests. The outer diameter of the bit is 32 mm, the inner diameter is 24 mm, and the water way spacing is 6 mm (Figure 6). The granite sample used in the drilling test is the same as that used in the compression test. The sample size is 100 mm × 100 mm ×100 mm.
The granite sample is put into the confining stress system, and the hydraulic servo-motor controlled jack exerts and maintains the confining stress in two directions. The bit rotates from the free face, as shown in Figure 7. The test adopts the working mode of adjusting drilling rate and bit rotation speed, monitoring drilling depth, drilling force, and bit torque. According to “DZ/T 0227-2010 geological core drilling regulations,” China, in the rotary core drilling mode, the recommended drilling rate of 32 mm diameter-impregnated bit in granite is 13.33–35.00 mm/min, and the recommended bit rotation speed is about 800 rpm. Drilling test parameters are designed as follows: the drilling rate is 15 mm/min, the bit speed is 600 rpm, and the confining stresses are 0, 5, 10, 15, 20, and 25 MPa, respectively, corresponding depth 0–1,000 m from the ground. To study the influences of different drilling parameter combinations and confining stress conditions on the test results, the drilling test design is as follows: the bit rotation speed is 800 rpm, drilling velocities are 15 mm/min and 25 mm/min, and the confining stresses are 0, 5, 15, 25, and 35 MPa, corresponding depth 0–1,400 m from the ground. To ensure the reliability of the test data, the drilling test was repeated three times under the same conditions. The results show that the corresponding characteristics of the three tests are consistent. For illustrative purposes, only one test result is shown for each test condition.
Results are summarized in Table 4. Drilling tests are numbered from A to P. There are three combinations of drilling parameters: 15 mm/min-600 rpm (drilling parameter combination 1); 15 mm/min-800 rpm (drilling parameter combination 2); 25 mm/min-800 rpm (drilling parameter combination 3), as listed in Table 4. The sample after drilling test is shown in Figure 8.
3.2 Drilling specific energy analysis
Rapid loading rate is deemed to be dynamic, and the energy generated is called dynamic load energy
Where
The curves of drilling force and bit torque for 16 groups of tests are as shown in Figures 9, 10. To better display the data, the drilling force and bit torque results for each drilling parameter combination are divided into two parts. The results of A, C, and E are shown in Figures 9A, 10A and results of B, D, and F are shown in Figures 9B, 10B. The drilling force and bit torque results for drilling parameter combination 2 (tests G–K) are shown in Figures 9C, 10C, respectively. The drilling force and bit torque for drilling parameter combination 3 (tests L–P) are shown in Figures 9D, 10D, respectively. As shown in Figures 9, 10, the drilling force and bit torque fluctuate throughout the drilling process, but the fluctuation range is small. Although there are some overlaps between the data among different test groups, there are significant differences in the distribution domains. The higher the confining stress, the lower the drilling force and bit torque.
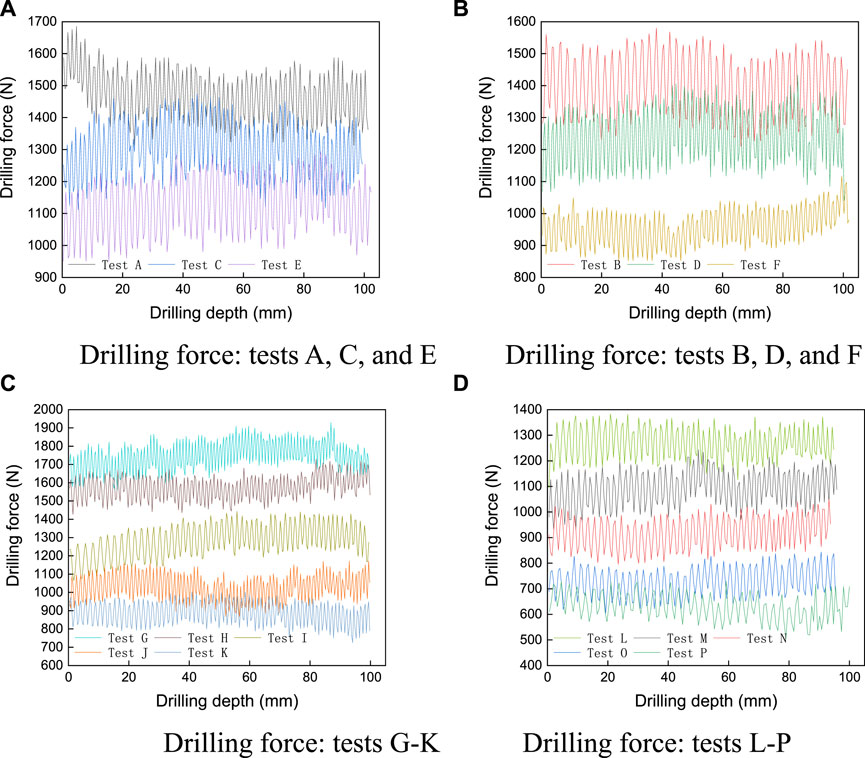
FIGURE 9. Drilling force v. drilling depth. (A) Drilling force: tests A, C, and E (B) Drilling force: tests B, D, and F. (C) Drilling force: tests G–K (D) Drilling force: tests L–P.
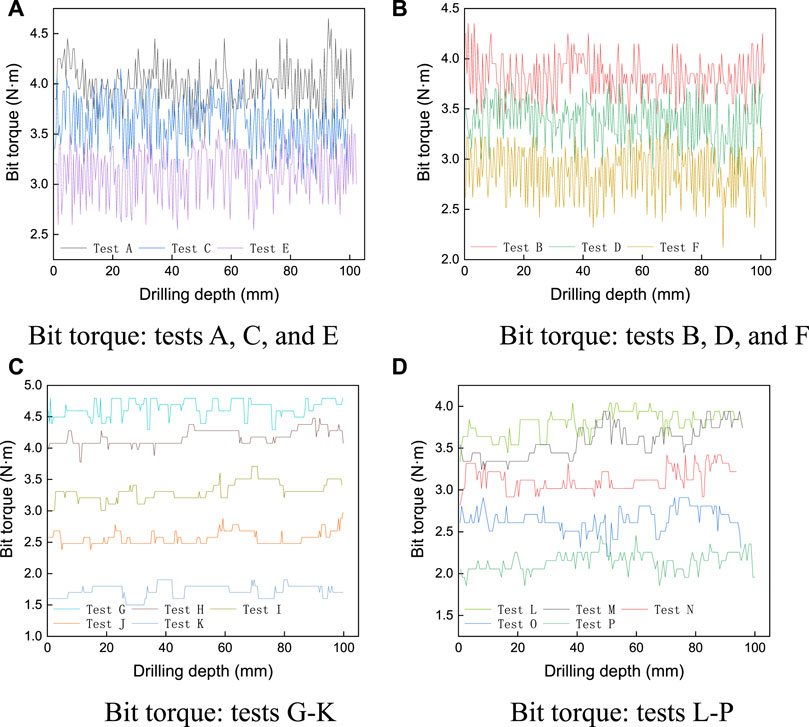
FIGURE 10. Torque v. drilling depth. (A) Bit torque: tests A, C, and E (B) Bit torque: tests B, D, and F (C) Bit torque: tests G–K (D) Bit torque: tests L–P.
The average (AVG) and standard deviation (STD) of drilling force and bit torque in each test were calculated as shown in Table 5. With the increase of confining stress, the AVG of drilling force and bit torque decrease, and the STDs of each group are similar, suggesting that the drilling force and bit torque fluctuate regularly around the average. The fluctuation range of each test is consistent.
The results of the drilling test are shown in Figure 11. The theory of specific energy in rock drilling assumes that the drilling specific energy of the same rock is similar, and the rock properties can be inferred based thereon. He (2017) found that the drilling specific energy of the same kind of rock remains near a constant value under different drilling parameters. Based on the research results and the classification of rock hardness in “GB/T 50,218-2014 Engineering Rock Mass Classification Standard,” China, they established a rock hardness evaluation criterion as shown in Table 6; however, their drilling tests did not take into account confining stress. The drilling test results undertaken in the present work show that the confining stress condition and the drilling parameter combinations greatly influences the drilling specific energy. E.g., in drilling parameter combination 1, the drilling specific energy is 2,783.78
According to “GB/T 50,218-2014 Engineering Rock Mass Classification Standard,” China, the intact granite used in these tests is a hard rock. In this paper, the drilling specific energy range of intact granite under different confining stresses is 1,508.41–5,410.00
Except for tests G and H, the other prediction results are inconsistent with the actual situation, and the misjudgement rate is as high as 87.5%. This shows that although the evaluation criteria has certain applicability under low confining stress, it is easy to misjudge the rock properties by the drilling specific energy without considering the confining stress conditions. In drilling parameter combination 1, when the confining stress is 0 MPa, hard rock can be predicted only when the drilling specific energy reaches 2,783.78
For a particular site, the confining stress conditions are similar, and it is feasible to use the drilling specific energy to predict the rock properties, however, such conclusions have significant limitations when applied to different confining stress and drilling conditions. The results of the test in this paper confirm this.
4 Energy analysis of intact granite under different confining stresses and drilling parameters
The test results of intact granite under different confining stresses and drilling parameters cannot be explained by the existing drilling specific energy theory. Based on the characteristics of the drilling process and the coupled static-dynamic loading theory, a rock energy analysis method based on drilling process is proposed.
Both the original rock mass and the engineering rock mass exchange energy with the external environment (Li et al., 2011b). The energy in the rock mainly comes from the self-weight stress and tectonic stress. According to the coupled static-dynamic loading theory, the engineering rock mass is generally in the combined stress state of “static and dynamic load” (Li et al., 2019). The totale energy required for rock failure remains unchanged and is mainly controlled by the initial static stress.
In the drilling tests, the static load energy
The energy in a unit volume of rock consists of two parts: that generated by the stress environment
where
The influences of dynamic load conditions such as drilling rate must be considered when quantizing
According to Eq. 3, when the confining stress is 35 MPa,
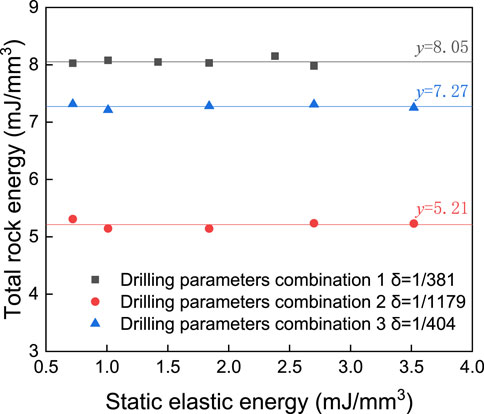
FIGURE 14. Relationship between confining stress and total energy under different drilling parameter combinations.
The drilling parameters controlled herein are drilling rate and bit rotation speed. Therefore, the relationship between
where
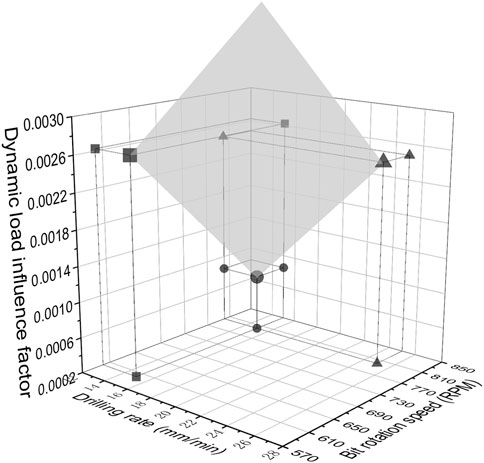
FIGURE 15. Relationship between dynamic load influence factors and drilling rate and bit rotation speed.
The results show that
The larger value of
When the drilling parameters are the same, the total energy of intact granite equals a certain value. When the drilling parameters change, the total energy changes accordingly. The total energy is an energy index considering confining stress and drilling parameters, which provides a basis for evaluating rock properties. Through further drilling tests, the relationship between drilling parameters, dynamic load influence factor and total energy can be established, and the total energy can be calculated using drilling parameters and dynamic load influence factor to evaluate rock properties.
The total energy can also be used to estimate the in-situ stress of rocks. Taking drilling parameter combination 3 as an example, the dynamic elastic energy is calculated by using the drilling parameters of test L, test M, and test N, and the static elastic energy is calculated by using the compression tests results, and the total energy is obtained to be about 7.23
5 Discussion
According to the tests results herein, when the drilling parameters are the same, the total energy of intact granite is constant and independent of the confining stress, when the drilling parameters change, the total energy varies significantly. The dynamic load influence factor was proposed to characterize the influence of drilling parameters on the energy of intact granite. The tests results show that the total energy of intact granite increases exponentially with the increase of the dynamic load influence factor. The dynamic load influence factor depends on the drilling parameters. Since only 3 drilling parameter combinations were considered in the tests, more drilling tests are needed to ascertain a more accurate relationship between the total energy and the dynamic load influence factor for intact granite.
With the increase of confining stress, the plastic characteristics of rock become more apparent, and rock gradually transforms from brittle to ductile behavior (Yang, 2012). The value of confining stress that causes brittle rocks to become ductile is generally .33–1.0 times the uniaxial compressive strength (Yang et al., 2008). For the intact granite tested in this paper, this stress is not less than 82 MPa. The maximum confining stress in the drilling test of intact granite in this paper is 35 MPa, and the granite is in a brittle state. Therefore, the conclusions drawn herein are based on the premise that the granite is in a brittle state. Since the energy is closely related to the type and state of rock, it is helpful to improve the energy analysis method based on the drilling process through experimental research on more types of rocks. In addition, for simplicity, the confining stress conditions of the drilling tests in this paper are biaxial, and the stresses are equal. The energy analysis method of rock under unequal biaxial and triaxial stress is also worthy of further study.
6 Conclusion
Triaxial compression tests and laboratory drilling tests under different confining stresses and drilling parameters are conducted on intact granite specimens. According to the test results, it is found that the drilling specific energy for same rock is not a constant value but varies with confining stress and drilling parameters. Subsequently, an energy analysis method based on drilling process was proposed, and the main conclusions are drawn as follows:
(1) Based on linear energy storage theory, the static elastic energy in the rock is calculated according to the triaxial compression test results. The static elastic energy increases with the increase of confining stress.
(2) Drilling test results show that when the confining stress is within the range of 0–35 MPa, the drilling specific energy decreases with the increase of confining stress, showing a linear relationship and it varies significantly with drilling parameters, differing from the current understanding. When the rotation speed is within the range of 600–800 and the drilling speed is within the range of 15–25 mm/min as recommended by “DZ/T 0227-2010 geological core drilling regulations, China,” the drilling specific energy increases with the increase of bit rotation speed and decreases with the increase of drilling rate. The limitation of using drilling specific energy to evaluate rock properties without considering confining stress conditions and drilling parameter combinations was highlighted. In terms of the test results herein, the rate of misjudgement of rock properties using drilling specific energy reaches 87.5%.
(3) An energy analysis method based on drilling process was proposed. A total energy index was defined as the sum of static elastic energy and dynamic elastic energy, which varies with drilling parameters and is constant under the same drilling parameters. The total energy considers the confining stresses and drilling parameters and provides a new energy index for evaluating rock properties. A dynamic load influence factor was proposed to characterize the influence of drilling parameters on the total energy of intact granite.
(4) The potential application of the energy analysis method in rock stress estimation was explored, and the error in rock stress estimation is less than 3% in drilling test.
Data availability statement
The original contributions presented in the study are included in the article/supplementary material, further inquiries can be directed to the corresponding author.
Author contributions
HT: Write papers and analyze experiments D-CL: Conduct and analyze experiments Z-JW: Theory analysis XC: Experimental design.
Funding
The study is financially supported by Traffic Science and Technology Project of Yunnan Province, China [Grant No. (2020)-74].
Conflict of interest
The authors declare that the research was conducted in the absence of any commercial or financial relationships that could be construed as a potential conflict of interest.
The reviewer (KX) declared a shared affiliation with the authors to the handling editor at time of review.
Publisher’s note
All claims expressed in this article are solely those of the authors and do not necessarily represent those of their affiliated organizations, or those of the publisher, the editors and the reviewers. Any product that may be evaluated in this article, or claim that may be made by its manufacturer, is not guaranteed or endorsed by the publisher.
References
Bai, B., Wang, Y., Rao, D. Y., and Bai, F. (2022). The effective thermal conductivity of unsaturated porous media deduced by pore-scale SPH simulation. Front. Earth Sci. (Lausanne). 10 (10), 943853. doi:10.3389/feart.2022.943853
Bai, B., Yang, G. C., Li, T., and Yang, G. S. (2019). A thermodynamic constitutive model with temperature effect based on particle rearrangement for geomaterials. Mech. Mater. 139, 103180. doi:10.1016/j.mechmat.2019.103180
Bai, B., Zhou, R., Cai, G. Q., Hu, W., and Yang, G. C. (2021). Coupled thermo-hydro-mechanical mechanism in view of the soil particle rearrangement of granular thermodynamics. Comput. Geotechnics 137, 104272. doi:10.1016/j.compgeo.2021.104272
Chen, J., and Yue, Z. Q. (2015). Ground characterization using breaking-action-based zoning analysis of rotary-percussive instrumented drilling. Int. J. Rock Mech. Min. Sci. 75, 33–43. doi:10.1016/j.ijrmms.2014.11.008
Gong, F. Q., Li, X. B., and Liu, X. L. (2011). Preliminary experimental study of characteristics of rock subjected to 3d coupled static and dynamic loads. Chin. J. Rock Mech. Eng. 30 (06), 1179–1190.
Gong, F. Q., Li, X. B., Liu, X. L., and Zhao, J. (2010). Experimental study of dynamic characteristics of sandstone under one-dimensional coupled static and dynamic loads. Chin. J. Rock Mech. Eng. 29 (10), 2076–2085.
Gong, F. Q., Lu, D. H., Li, X. B., Rao, Q. H., and Fu, Z. T. (2014). Toughness increasing or decreasing effect of hard rock failure with pre-static loading under dynamic disturbance. Chin. J. Rock Mech. Eng. 33 (9), 1905–1915. doi:10.13722/j.cnki.jrme.2014.09.022
Gong, F. Q., Wu, W. X., and Zhang, L. (2020). Brazilian disc test study on tensile strength-weakening effect of high pre-loaded red sandstone under dynamic disturbance. J. Cent. South Univ. 27 (10), 2899–2913. doi:10.1007/s11771-020-4517-5
Gong, F. Q., Yan, J. Y., and Li, X. B. (2018). A new criterion of rock burst proneness based on the linear energy storage law and the residual elastic energy index. Chin. J. Rock Mech. Eng. 37 (09), 1993–2014. doi:10.13722/j.cnki.jrme.2018.0232
Gui, M. W., Soga, K., Bolton, M. D., and Hamelin, J. P. (2002). Instrumented borehole drilling for subsurface investigation. J. Geotech. Geoenviron. Eng. 128 (4), 283–291. doi:10.1061/(asce)1090-0241(2002)128:4(283)
He, M. C., Wang, Y., Su, J. S., and Liu, D. Q. (2018). Analysis of fractal characteristics of fragment of sandstone impact rock burst under static and dynamic coupled loads. J. China Univ. Min. Technol. 47 (04), 699–705. doi:10.13247/j.cnki.jcumt.000876
He, M. M. (2017). “Research on the prediction of rock mass mechanics characteristics based on the rotary penetration technology,”. PhD Thesis (Xi'an, Shaanxi, China: Xi'an University of Technology).
Kahraman, S. (1999). Rotary and percussive drilling prediction using regression analysis. Int. J. Rock Mech. Min. Sci. 36 (7), 981–989. doi:10.1016/S0148-9062(99)00050-9
Karasawa, H., Ohno, T., Kosugi, M., and Rowley, J. C. (2002). Methods to estimate the rock strength and tooth wear while drilling with roller-bits—Part 1: Milled-tooth bits. J. Energy Resour. Technol. 124 (3), 125–132. doi:10.1115/1.1482405
Li, X. B., Gong, F. Q., Wang, S. F., Li, D. Y., Tao, M., Zhou, J., et al. (2019). Coupled static-dynamic loading mechanical mechanism and dynamic criterion of rockburst in deep hard rock mines. Chin. J. Rock Mech. Eng. 38 (04), 708–723. doi:10.13722/j.cnki.jrme.2018.1496
Li, X. B., and Gu, D. S. (2002). “The hazard control and cataclastic muta-genesis induced by high stress in hard rock mining at depth,” in Proceedings of the 175th Xiangshan Science Congress, Beijing, China, April 28.
Li, X. B., Tao, M., Gong, F. Q., Yin, Z. Q., and Du, K. (2011a). Theoretical and experimental study of hard rock spalling fracture under impact dynamic loading. Chin. J. Rock Mech. Eng. 30 (06), 1081–1088.
Li, X. B., Yao, J. R., and Gong, F. Q. (2011b). Dynamic problems in deep exploitation of hard rock metal mines. Chin. J. Nonferrous Metals 10, 2551–2563. doi:10.19476/j.ysxb.1004.0609.2011.10.022
Liu, Q. S., Liu, K. D., Lu, X. L., and Zhu, J. B. (2014a). Study of mechanical properties of raw coal under high stress with triaxial compression. Chin. J. Rock Mech. Eng. 36 (01), 24–34. doi:10.13722/j.cnki.jrme.2014.s2.006
Liu, S. H., Mao, D. B., Qi, Q. X., and Li, F. M. (2014b). Under static loading stress wave propagation mechanism and energy dissipation in compound coal-rock. J. China Coal Soc. 16 (S1), 15–22. doi:10.13225/j.cnki.jccs.2013.0411
Lu, X. S., Wang, Y. Z., and Lei, M. (2007). Using mathematical statistics to optimize bits and comment on the effects of use. Fault-Block Oil Gas Field 30 (06), 63–65+93.
Luo, Y., Li, X. P., Dong, Q., Huang, J. H., and Guo, Y. H. (2015). Damage cause study for static and dynamic combination of excavation and unloading in deep underground tunnels. Chin. J. Rock Mech. Eng. 34 (S1), 3365–3371. doi:10.13722/j.cnki.jrme.2014.0839
Mostofi, M., Rasouli, V., and Mawuli, E. (2011). An estimation of rock strength using a drilling performance model: A case study in blacktip field, Australia. Rock Mech. Rock Eng. 44 (3), 305–316. doi:10.1007/s00603-011-0142-9
Niu, T., Liang, H. W., and Xu, Y. J. (2009). Study on the pressure loss laws in micro hole circulatory system. Drill. Prod. Technol. 32 (04), 31–33.
Oparin, V. N., Timonin, V. V., Karpov, V. N., and Smolyanitsky, B. N. (2018). Energy-based volumetric rock destruction criterion in the rotary-percussion drilling technology improvement. J. Min. Sci. 53 (6), 1043–1064. doi:10.1134/S1062739117063114
Sakiz, U., Aydin, H., and Yarali, O. (2021). Investigation of the rock drilling performance of rotary core drilling. Bull. Eng. Geol. Environ. 81, 24. doi:10.1007/s10064-021-02534-6
Su, Y. Q., Gong, F. Q., Luo, S., and Liu, Z. X. (2022). Experimental study on energy storage and dissipation characteristics of granite under two-dimensional compression with constant confining pressure. J. Cent. South Univ. 28 (03), 848–865. doi:10.1007/s11771-021-4649-2
Tan, Z. Y., Yue, Z. Q., and Cai, M. F. (2007). Analysis of energy for rotary drilling in weathered granite formation. Chin. J. Rock Mech. Eng. 26 (3), 478–483.
Teale, R. (1965). The concept of specific energy in rock drilling. Int. J. Rock Mech. Min. Sci. Geomechanics Abstr. 2 (1), 245–273. doi:10.1016/0148-9062(65)90016-1
Van Wyk, G., Els, D. N. J., Akdogan, G., Bradshaw, S. M., and Sacks, N. (2014). Discrete element simulation of tribological interactions in rock cutting. Int. J. Rock Mech. Min. Sci. 65, 8–19. doi:10.1016/j.ijrmms.2013.10.003
Wang, Q., Gao, H. K., Yu, H. C., Jiang, B., and Liu, B. H. (2019). Method for measuring rock mass characteristics and evaluating the grouting-reinforced effect based on digital drilling. Rock Mech. Rock Eng. 52 (3), 841–851. doi:10.1007/s00603-018-1624-9
Wang, Q., Gao, S., Jiang, B., Li, S. C., He, M. C., Gao, H. K., et al. (2018a). Rock-cutting mechanics model and its application based on slip-line theory. Int. J. Geomech. 18 (5), 1–10. doi:10.1061/(ASCE)GM.1943-5622.0001136
Wang, Q., Gao, S., Li, S. C., He, M. C., GaoHK, , Jiang, B., et al. (2018b). Upper bound analytic mechanics model for rock cutting and its application in field testing. Tunn. Undergr. Space Technol. 73, 287–294. doi:10.1016/j.tust.2017.12.023
Wang, W., Li, H. M., Gu, H. L., and Wang, C. (2015). Feature analysis of energy dissipation of water-saturated coal samples under coupled static-dynamic loads. Chin. J. Rock Mech. Eng. 34 (S2), 3965–3971. doi:10.13722/j.cnki.jrme.2015.0546
Xia, K. Z., Chen, C. X., Wang, T. L., Zheng, Y., and Wang, Y. (2022). Estimating the geological strength index and disturbance factor in the Hoek–Brown criterion using the acoustic wave velocity in the rock mass. Eng. Geol. 306 (306), 106745. doi:10.1016/j.enggeo.2022.106745
Yang, D. H. (2012). “Preliminary research of rock breaking methods and impregnated diamond core bit in scientific ultra-deep drilling process,”. PhD Thesis (Wuhan, China: China University of Geosciences).
Yang, G. L., Huang, R. Q., Cai, G. J., Fu, X. M., Lin, F., and Xu, D. M. (2008). Conventional triaxial compression test I of altered rock:study of classification of strain-stress curve before and after destruction and brittle-ductile diversion confining pressure. Rock Soil Mech. 30 (10), 2759–2763. doi:10.16285/j.rsm.2008.10.044
Yang, W. W., Yue, Z. Q., and Tham, L. G. (2012). Automatic monitoring of inserting or retrieving SPT sampler in drillhole. Geotech. Test. J. 35 (3), 420–436. doi:10.1520/gtj103450
Yang, Y. J., Song, Y., and Chen, S. J. (2006). Test study of coal's strength and deformation characteristics under triaxial compression. Min. Eng. 31 (02), 150–153.
Yasar, E., Ranjith, P. G., and Viete, D. R. (2011). An experimental investigation into the drilling and physico-mechanical properties of a rock-like brittle material. J. Petroleum Sci. Eng. 76 (3), 185–193. doi:10.1016/j.petrol.2011.01.011
Zhang, Z. Z., and Gao, F. (2015). Confining pressure effect on rock energy. Chin. J. Rock Mech. Eng. 34 (01), 1–11. doi:10.13722/j.cnki.jrme.2015.01.001
Zhao, G. M., Liu, Z. X., Meng, X. R., Zhang, R. F., Kao, S. M., and Qi, M. J. (2022). Energy accumulation and dissipation test and analysis method of height-diameter ratio sandstone. J. China Coal Soc. 47 (03), 1110–1121. doi:10.13225/j.cnki.jccs.xr21.1606
Glossary
The following abbreviations are used in this document:
L Drilling depth
Keywords: granite, confining stress, drilling parameters, drilling specific energy, energy analysis
Citation: Tang H, Liang D-C, Wu Z-J and Cheng X (2023) Energy analysis of intact granite based on test while drilling under different confining stresses and drilling parameters. Front. Earth Sci. 10:1057187. doi: 10.3389/feart.2022.1057187
Received: 29 September 2022; Accepted: 02 December 2022;
Published: 19 January 2023.
Edited by:
Dongdong Yao, China University of Geosciences Wuhan, ChinaReviewed by:
Kaizong Xia, Institute of Rock and Soil Mechanics (CAS), ChinaBing Bai, Beijing Jiaotong University, China
Zhongjian Zhang, China University of Geosciences, China
Copyright © 2023 Tang, Liang, Wu and Cheng. This is an open-access article distributed under the terms of the Creative Commons Attribution License (CC BY). The use, distribution or reproduction in other forums is permitted, provided the original author(s) and the copyright owner(s) are credited and that the original publication in this journal is cited, in accordance with accepted academic practice. No use, distribution or reproduction is permitted which does not comply with these terms.
*Correspondence: Dong-Cai Liang, bGlhbmdkb25nY2FpMThAbWFpbHMudWNhcy5hYy5jbg==