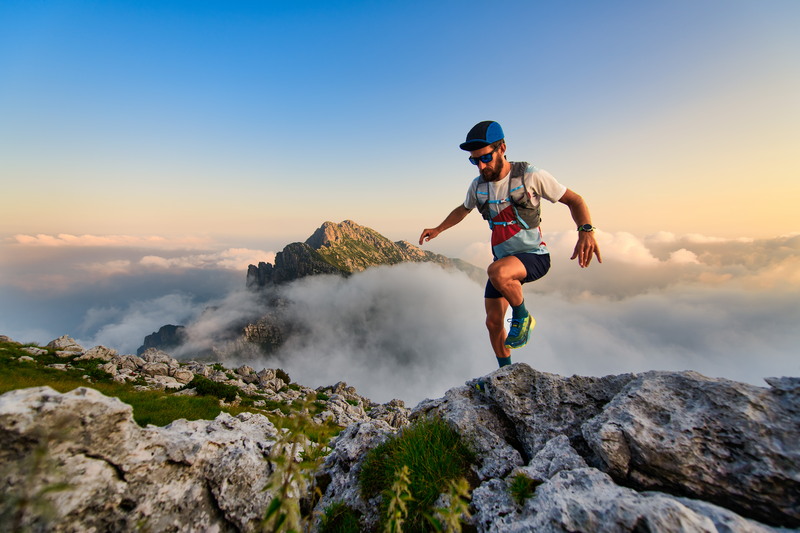
95% of researchers rate our articles as excellent or good
Learn more about the work of our research integrity team to safeguard the quality of each article we publish.
Find out more
ORIGINAL RESEARCH article
Front. Earth Sci. , 10 January 2023
Sec. Economic Geology
Volume 10 - 2022 | https://doi.org/10.3389/feart.2022.1054896
This article is part of the Research Topic Gas-Water-Rock Interaction and Multi Physical Field Coupling Mechanism View all 16 articles
Surface roughness has an important effect on the wettability and surface energy of coal. Although the predecessors had studied the effect of surface roughness on the wettability of coal, there were few researches on the effect of surface energy of coal, and the relationship between wettability and surface energy had not been thoroughly studied. This paper aimed to study the effect of surface roughness on the wettability and surface energy of coal, and revealed the relationship between the wettability and surface energy of coal. Based on the surface roughness of coal, this paper selected Hami lignite, Anyang coking coal and Zhaogu anthracite as the research objects, used the experimental methods to measure the surface roughness and experimental contact angle of coal under different conditions to study the effect of surface roughness on the wettability, and then applied the OWRK method to calculate the surface energy of coal to study the effect of surface roughness on the surface energy. The experimental results showed that the wettability of hydrophilic coal became better and the surface energy increased with the increase of surface roughness, while the results of hydrophobic coal were opposite. There was a positive correlation between the wettability and surface energy of coal, and the wettability of coal could be analyzed from the perspective of surface energy. Surfactant could change the wettability of coal, but unchanged the law of wettability with surface roughness.
As an important energy source in China, coal will still play a dominant role in the coming decades (Wei et al., 2019; Du et al., 2020; Yang and He, 2020; Du and Song, 2022). In recent years, coal mining technology is tending to be more automated and intelligent, and production rate of coal is therefore gradually increasing. However, with the increase operation of coal mining, mine dust production is also growing, and meanwhile the harm of mine dust is increasingly serious. As one of the seven major disasters in coal mines, the harm of mine dust is multifaceted, mainly including pneumoconiosis (Wu, 2019) and coal dust explosion (Chen et al., 2018). Effective treatment of mine dust is one of the important measures to improve the working environment, provide safe operating conditions and ensure the safety of coal mine workers. Wet dust removal is one of the effective measures to control mine dust. Studies have shown that increasing the water content of coal can greatly reduce the amount of dust generated during coal mining (Wang, 2011). Injecting aqueous solutions containing surfactants into coal seams can also achieve the effect of dust removal (Wang, 2020). Chen (Chen et al., 2019) analyzed the wettability of low rank coal based on the development of bedding samples and pore characteristics of coal, and found that the wettability of coal was related to the direction of bedding. The better the pore size sorting of coal, the better the wettblity of coal. In the study of micro-wettability characteristics of coal dust, Zhang (Zhang et al., 2021) analyzed the influence of surface characteristics of coal dust on the wettability of coal dust, and found that the wettability of coal dust was positively correlated with the specific surface area of coal dust. The better the wettability of coal dust, the faster the settling rate of coal dust. Xia (Xia et al., 2016; Xia, 2017) used the experimental method to determine the surface roughness and contact angle of ultra-low ash coal to study the effect of surface roughness on the wettability of coal, and found that the wettability of coal first increased, second decreased, and then slightly increased with the surface roughness increased. Li (Li et al., 2021) used the phase field interfacial tracking method to simulate the wetting of droplets on the surface of coal samples. The simulation results showed that the contact angle of hydrophilic coal samples decreased and the wettability increased with the increase of surface roughness, and the results of hydrophobic coal samples were opposite. Li (Li et al., 2015) measured the surface tension of surfactants at different concentrations by capillary rise method, and found that surfactants effectively reduced the surface tension of pure water and improved the wetting effect of pure water on coal. Huang (Huang et al., 2010) studied the wetting ability of different surfactants by sedimentation method, and found that the type and concentration of surfactants had different effects on the wettability of coal.
Based on the effect of coal surface morphology and surfactant on the wettability of coal, the above studies had made an important contribution to improving the efficiency of mine wet dust removal. However, they did not analyze the surface energy of coal and study the relationship between wettability and surface energy. Therefore, this paper studied the wettability and surface energy of coal based on surface roughness, analyzed the experimental contact angle under different surface roughness to reflect the effect on the wettability, then used OWRK method to calculate the surface energy of coal, studied the effect of surface roughness on the surface energy, and finally revealed the relationship between the wettability and surface energy.
Surface roughness is the unevenness of the machined surface with smaller spacing and tiny peaks and valleys (Wang X. G., 2011), which generally occurs on the cutting surface during solid machining or the structural surface damaged by external shear forces. The smaller the surface roughness, the smoother the surface. According to the calculation method and sampling method, the classification of roughness is divided into arithmetic roughness, mean square roughness and maximum profile roughness. Since the calculation of mean square roughness is faster and more accurate, it is used to characterize the surface roughness in this study.
Based on the surface roughness of coal samples, this study selected three coal samples with different ranks as the research objects, which were Hami lignite, Anyang coking coal and Zhaogu anthracite. Proximate analysis of the three coal samples are shown in Table 1.
Roughness measurement methods can be divided into contact and non-contact for solid matters. Contact measurement refers to the contact between the probing instrument and the solid part to be measured, which can directly obtain the surface roughness of the part to be measured. It can be divided into comparison method, impression method and probe contact method (Puttkamer and Jiang, 1984; Sherrington and Smith, 1992). Non-contact measurement refers to the feedback of roughness information of the measured surface by indirect means without contact with the measured surface. It can be divided into ultrasonic technology (Coker and Shin, 1996; Bui et al., 2015), laser triangulation method (Lu and Huang, 2004; Wang et al., 2004), machine vision technology (Tsai, 1987; Zhang et al., 2012), speckle method (Gao, 2009) and scattering method (Ni and Chen, 2001). The contact measurement method is slow, low accuracy, less applicable occasions, and the measured surface is easy to cause damage in the measurement process. Therefore, this study chooses the non-contact measurement method, which can quickly, accurately and stably detect the surface roughness of the objects online. The optical contact angle topography instrument was used to measure the surface roughness of coal samples, as is shown in Figure 1.
The surface of coal samples was directly polished by 120 mesh, 240 mesh, 320 mesh, 600 mesh and 1,000 mesh sand paper, respectively. Then the coal samples were cleaned with distilled water. Finally, the coal samples were dried for measurement. Three surfaces were selected for each coal sample, and each surface was measured five times. The measurement results were shown in Figure 2.
The concept of contact angle was proposed to quantitatively characterize the hydrophilicity and hydrophobicity of solid substance (Good, 2012). Solid surface with contact angle values less than 90° is considered to be hydrophilic, and it is deemed more hydrophilic against the contact angle. In contrast, the values greater than 90° have hydrophobic properties, and the larger the value, the worse the wettability. When the droplet is in a stable state on the solid surface, a tangent line of the vapor-liquid contact line was made at a point on the solid-liquid-vapor three-phase contact line. The angle formed between the tangent line and the solid-liquid contact line is the contact angle, as shown in Figure 3 γlv, γsl and γsv represent the surface tension or surface energy between liquid-vapor, solid-liquid and solid-vapor, respectively.
The optical contact angle topography instrument was used to measure the contact angle of coal samples in this study. The measurement principle was shown in Figure 4. The droplet was suspended in the dropper, and the LED light source was provided on the side to illuminate where the droplets come into contact with the solid surface. The contour of the droplet and the solid surface was recorded by the camera. Then the angle between the tangent line of the three-phase contact line and the phase interface was calculated by the Young–Laplace method (Rior and Neumann, 1997) to obtain the value of the contact angle.
The dropper was filled with deionized water and glycerol, respectively. The coal samples were placed on the loaded platform. The dropper was set to drop 10 μL of liquid, and automatically descend to make the droplet contact with the surface of the coal sample. The process and images of the contact angle measurement were recorded by the camera automatically. The contact angle value was obtained by software processing. The roughness of each coal sample was measured at 5 to 6 points, and the average value is taken. From the experimental point of view, the liquid itself has a certain surface tension, and in the case of small size, it mostly exists in a nearly spherical state. In order to reduce the measurement error of the experiment, this experiment was conducted on the surface of the coal sample without cracks.
The experimental contact angles of the coal samples surfaces after wetting by deionized water and glycerol under different roughness were measured respectively. The former contact angle can characterize the intuitive influence of the surface roughness on the wettability of coal. The latter contact angle was used to calculate the surface energy of coal under different surface roughness, which can further explain the influence of the change of surface energy on the wettability change of the former. The test results are shown in Figure 5, where 1 represents deionized water and 2 represents glycerol.
It can be seen from Figure 5 that the experimental contact angle values of the three coal samples are different, and their wettability is also different. After the surface of the three coal samples was wetted by deionized water, the experimental contact angle values of Hami lignite were all less than 60°, showing hydrophilicity. The experimental contact angle values of Anyang coking coal were all greater than 100°, showing hydrophobicity. The experimental contact angle values of Zhaogu anthracite were all greater than 76° and less than 90°, showing weak hydrophilicity. The result is the same as the conclusion obtained by Li (Li and Li, 2016) that lignite has the best hydrophilicity, coking coal has the worst hydrophilicity, and anthracite is in between. It is found from Figure 5 that with the increase of coal surface roughness, the experimental contact angle values of Hami lignite and Zhaogu anthracite gradually decrease, and their wettability becomes better, while the experimental contact angle value of Anyang coking coal gradually increase, and its wettability becomes worse. This is because of the different degrees of coal metamorphism, resulting in different components of coal. Lignite has the most oxygen-containing functional groups, followed by anthracite, and the least in coking coal. Coking coal has the most aromatic hydrocarbons and aliphatic hydrocarbons, followed by anthracite, and lignite has the least. The different ranges of variation in contact angle values for the three coal samples are also due to the differences in the surface structural properties of coal caused by the different degrees of coal metamorphism. At the same time, it was also found that after the surfaces of the three coal samples were wetted by glycerol, the contact angle values decreased, which showed that the hydrophilicity of lignite was increased, the hydrophobicity of coking coal was decreased, and the hydrophilicity of anthracite was improved. This is because glycerol reduces the surface tension of the liquid, which in turn improves the wettability of the coal samples.
The surface energy of coal is caused by the balanced intermolecular forces on the interior and the unbalanced forces on the surface. Coal is a complex polymer structure with carbon as the skeleton, and the forces among internal carbon elements and between carbon elements and other elements are balanced. When coal is destroyed by external forces, the force balance is broken and the coal will produce a new surface. The surface molecules of coal are attracted by the internal forces, and this force is the surface energy (force).
The surface force parameters of deionized water and glycerol include surface tension, dispersion force and polarity force. The results are shown in Table 2.
The calculation method of coal surface energy is divided into gas adsorption method (Nie et al., 2000) and contact angle calculation method. The gas adsorption method usually takes a long time, while the contact angle calculation method takes a short time and several mature calculation models can be used for contact angle calculation method. The contact angle calculation methods include the Fowkes method (Fowkes, 1963), the Wu average method (Wu, 1971) and the OWRK method. In this paper, the OWRK method is used to calculate the surface energy of coal.
The OWRK method is an improvement of the Fowkes method. Owens and Wendt (Owens and Wendt, 1969) considered the effect of polarity force on the surface energy and obtained a new Eq. 1. Equation 1 combines with the Young’s equation and the surface force parameters of the two liquids, and the Eqs 2, 3 of the dispersion force and the polarity force are obtained.
Where γsl γsv and γlv represent the surface tension of coal between solid-liquid, solid-vapor and liquid-vapor, γsv,d and γsv,p represent the dispersion force and polarity force between solid and vapor, γlv,d and γlv,p represent the dispersion force and polarity force between liquid and vapor. The unit is mJ/m2. Where the subscript 1 represents deionized water, the subscript 2 represents glycerol, and θ represents the experimental contact angle of the two liquids.
The contact angle values measured by the experiment were brought into the above equation. The surface energies of Hami lignite, Anyang coking coal and Zhaogu anthracite at different roughness were obtained. The calculation results are shown in Figure 6.
FIGURE 6. Surface energy of three coal samples (A) Hami lignite, (B) Anyang coking coal, (C) Zhaogu anthracite.
It is found from Figure 6 that the surface energy of lignite is provided by both dispersion force and polarity force, while that of coking coal and anthracite is mainly provided by dispersion force. This is related to the degree of metamorphism of the coal samples. Lignite has lower degree of metamorphism and more polar components, while coking coal and anthracite have higher degree of metamorphism and less polar components. The surface energy of coal samples with different hydrophilicity and hydrophobicity is different under the action of roughness, and the trend of change with roughness is also different. With the surface roughness of lignite increases, the dispersion force decreases, the polarity force increases, and the total surface energy tends to increase. With the surface roughness of coking coal increases, the dispersion force decreases, the polarity force does not change significantly, and the total surface energy tends to decrease. With the increase of anthracite surface roughness, the dispersion force and the polarity force increase, and the total surface energy tends to increase. Combined with the analysis in Figure 5 again, it was found that the surface energy of the three coal samples showed a negative correlation with the contact angle values of the coal samples. With the increase of coal surface energy, the contact angle values of the three coal samples gradually decreased, the wettability of lignite and anthracite increased, and the hydrophobicity of coking coal decreased. The surface energy and wettability of the three coal samples showd the same trend with the change of surface roughness. The influence of surface roughness on the wettability of coal samples can be analyzed from the perspective of coal surface energy.
Surfactants are usually added to liquids to change its properties. At present, surfactants are widely used in modern coal mining. Such as coal seam water injection, which is injected into the coal seam containing a certain concentration of surfactant water solution to improve the water content of the coal seam. It is conducive to the control of coal dust and gas in the underground.
There are thousands of surfactants, and they can be divided into anionic surfactants, cationic surfactants and non-ionic surfactants according to the type. When anionic/cationic surfactants are dissolved in deionized water, negative/positive charges are ionized, giving the solution a negative/positive nature. The non-ionic surfactants do not ionize when dissolved in deionized water, and the solution becomes electrically neutral. This paper selected two different types of surfactants, namely Sodium Dodecyl Sulfate (SDS) and Cetyl Trimethyl Ammonium Chloride (CTAC). Their introduction are shown in Table 3.
Because of its high efficiency, the surfactants can be added in small amounts to obtain good results and save the cost of raw materials. Combined with the previous experience of using surfactants, the surfactant solutions with mass concentrations (wt%) of 0.1%, 0.2% and 0.3% were prepared by using experimental instruments, such as balance, beaker, glass rod, distilled water and liquid storage bottles. The solutions were filled into the liquid storage bottles and labeled for convenient experimental use.
The prepared surfactant solutions were drawn into the dropper, and the contact angles of the coal samples were measured according to the above experimental procedure. The results are shown in Figure 7.
FIGURE 7. Experimental contact angle of three coal samples. (A) Hami lignite (B) Anyang coking coal (C) Zhaogu anthracite.
It can be seen from Figure 7 that the same surfactant has the same trend of change in the contact angle values of the three coal samples. With the increase of CTAC concentration, the contact angle values are decreasing gradually and the wettability becomes better. However, with the increase of SDS concentration, the contact angle values first decreases and then increases. When SDS concentration is 0.2%, the contact angle values is the smallest and the wettability is the best. The contact angle variation trend of the same coal sample under different surfactants is different. This is because the solid-liquid interfaces within different solutions have an optimal number of active molecules adsorbed. Before the optimum adsorption number is reached, with the surfactant concentration increases, the more number of active molecules adsorbed at the interface, the better stability of the interface and the better wettability of the coal sample. After the optimum adsorption number is exceeded, if the surfactant concentration continues to increase, the repulsive force between the surfactant molecules will increase, which will decrease the stability of the interface. When the repulsive force increases to a certain value, the surfactant molecules at the interface will be squeezed out of the adsorption layer, which increases the solid-liquid interfacial tension and thus reduces the wettability of the coal sample. It is also found that the presence of surfactant did not change the variation law of wettability with surface roughness of the three coal samples.
Through the above experiments, the effect of surface roughness on the wettability and surface energy of coal was studied, and the relationship between the wettability and surface energy was revealed. The following conclusions were obtained:
1) The degree of coal metamorphism affected both wettability and surface energy properties. The three coals had different degree of metamorphism, which resulted in different components. Lignite had a low degree of metamorphism, more oxygen-containing functional groups, better wettability, more polar components, and the surface energy was provided by both dispersion force and polarity force. However, coking coal and anthracite had a high degree of metamorphism, more aromatic hydrocarbons and aliphatic hydrocarbons, less wettability, less polar components, and the surface energy was mainly provided by dispersion force.
2) There was a positive correlation between the wettability and surface energy of coal, and the wettability of coal could be analyzed from the perspective of surface energy. For the coal with the same properties, the surface energy and wettability had a same variation trend as the surface roughness. With the surface roughness of coal increased, the surface energy of lignite and anthracite increased, the experimental contact angle decreased, and the wettability became better. While the surface energy of coking coal decreased, the experimental contact angle increased, and the wettability became worse.
3) Surfactant could change the wettability of coal, but unchanged the law of wettability with surface roughness. With the increase of CTAC surfactant concentration, the experimental contact angle of coal decreased and the wettability became better. With the increase of SDS surfactant concentration, the experimental contact angle of coal first decreased and then increased, the wettability first became better and then worse. They unchanged the law of wettability with surface roughness.
There are some shortcomings in the experiments and research process. 1) The experimental coal samples polished by hand will cause errors in the determination results. In order to reduce the errors, the subsequent research should try to use mechanical devices to polish coal samples. 2) There are two surfactants used in the experiments, and a variety of different surfactants can be used in the subsequent experiments for comparison and analysis to summarize the rules.
The original contributions presented in the study are included in the article/Supplementary Material, further inquiries can be directed to the corresponding author.
All authors contributed to the study conception and design. Data collection and analysis were performed by JZ, BX, PZ, MC, and BL. All authors read and approved the final manuscript.
The study is mainly supported by National Nature Science Foundation of China (Grant No. 52174171). The authors also acknowledge the support by Henan Province Key Scientific Research Projects of Institution of Higher Education (22A440012) and Outstanding Youth Fund of Henan Polytechnic University.
The authors would like to thank all editors and reviewers for their comments and suggestions.
The authors declare that the research was conducted in the absence of any commercial or financial relationships that could be construed as a potential conflict of interest.
All claims expressed in this article are solely those of the authors and do not necessarily represent those of their affiliated organizations, or those of the publisher, the editors and the reviewers. Any product that may be evaluated in this article, or claim that may be made by its manufacturer, is not guaranteed or endorsed by the publisher.
Bui, G. T., Chen, Y. Z., and Pang, D. C. (2015). Polymer-based capacity micromachined ultrasonic transducer for surface roughness measurement. Key Eng. Mater. 661 (4145), 22–28. doi:10.4028/www.scientific.net/kem.661.22
Chen, H. H., Shi, S. L., and Zheng, M. L. (2018). Analysis on coal dust explosion based on fuzzy fault tree. Coal Technol. 37 (08), 180–182. doi:10.13301/j.cnki.ct.2018.08.068
Chen, Y., Ma, D. M., Xia, Y. C., Guo, C., Yang, P., and Shao, K. (2019). Study on wettability and influencing factors of different macroscopic components in low rank coal. Coal Sci. Technol. 47 (09), 97–104. doi:10.13199/j.cnki.cst.2019.09.009
Coker, S. A., and Shin, Y. C. (1996). In-process control of surface roughness due to tool wear using a new ultrasonic system. Int. J. Mach. Tools Manuf. 36 (3), 411–422. doi:10.1016/0890-6955(95)00057-7
Du, H., Song, D. Q., Chen, Z., and Guo, Z. Z. (2020). Experimental study of the influence of structural planes on the mechanical properties of sandstone specimens under cyclic dynamic disturbance. Energy Sci. Eng. 8 (11), 4043–4063. doi:10.1002/ese3.794
Du, H., and Song, D. Q. (2022). Investigation of failure prediction of open-pit coal mine landslides containing complex geological structures using the inverse velocity method. Nat. Hazards 111, 2819–2854. doi:10.1007/s11069-021-05159-w
Fowkes, F. M. (1963). Additivity of intermolecular forces at interfaces. I. Determination of the contribution to surface and interfacial tensions of dispersion forces in various liquids. J. Phys. Chem. 67 (12), 2538–2541. doi:10.1021/j100806a008
Gao, Z. (2009). Study of spatial-average-based surface roughness measurement techniques using static and dynamic speckle patterns. Harbin, China: Harbin Institute of Technology.
Good, R. J. (2012). Contact angle, wetting, and adhesion: A critical review. J. Adhesion Sci. Technol. 6 (12), 1269–1302. doi:10.1163/156856192x00629
Huang, W. G., Hu, F., and Liu, N. Q. (2010). Study on surfactant wettability for coal dust. Min. Saf. Environ. Prot. 37 (3), 4–6. doi:10.3969/j.issn.1008-4495.2010.03.002
Li, J., Zhou, F., and Liu, H. (2015). The selection and application of a compound wetting agent to the coal seam water infusion for dust control. Int. J. Coal Prep. Util. 36 (4), 192–206. doi:10.1080/19392699.2015.1088529
Li, J. Y., and Li, K. Q. (2016). Influence factors of coal surface wettability. J. China Coal Soc. 41 (S2), 448–453. doi:10.13225/j.cnki.jccs.2015.1656
Li, C., Zhang, J., Han, J., and Yao, B. H. (2021). A numerical solution to the effects of surface roughness on water-coal contact angle. Sci. Rep. 11 (1), 459. doi:10.1038/s41598-020-80729-9
Lu, J. R., and Huang, Y. Q. (2004). Laser triangulation method for surface measurement. J. Xiamen Univ. Sci. 43 (01), 50–53. doi:10.3321/j.issn:0438-0479.2004.01.013
Ni, Q. L., and Chen, B. (2001). Measurement of surface roughness by scattering method. Opt. Precis. Eng. 9 (02), 151–154. doi:10.3321/j.issn:1004-924X.2001.02.012
Nie, B. S., He, X. Q., and Wang, E. Y. (2000). Surface free energy of coal and its calculation. J. Taiyuan Univ. Technol. 31 (04), 346–348. doi:10.16355/j.cnki.issn1007-9432tyut.2000.04.002
Owens, D. K., and Wendt, R. C. (1969). Estimation of the surface free energy of polymers. J. Appl. Polym. Sci. 13 (8), 1741–1747. doi:10.1002/app.1969.070130815
Puttkamer, H. V., and Jiang, Z. Q. (1984). The surface roughness was measured with electric stylus profile status-the current situation and problems of surface roughness measurement. China: China Inspection Body & Laboratory, 16–17. CNKI:SUN:XDJL.0.1984-06-005.06
Rior, D., and Neumann, A. W. (1997). Axisymmetric drop shape analysis: Computational methods for the measurement of interfacial properties from the shape and dimensions of pendant and sessile drops. J. Colloid Interface Sci. 196 (2), 136–147. doi:10.1006/jcis.1997.5214
Sherrington, I., and Smith, E. H. (1992). Performance assessment of stylus based areal roughness measurement systems. Int. J. Mach. Tools Manuf. 32 (1-2), 219–226. doi:10.1016/0890-6955(92)90081-Q
Tsai, R. Y. (1987). A versatile camera calibration technique for high-accuracy 3D machine vision metrology using off-the-shelf TV cameras and lenses. IEEE J. Robot. Autom. 3 (4), 323–344. doi:10.1109/JRA.1987.1087109
Wang, X. J., Gao, J., and Wang, L. (2004). Survey on the laser triangulation. Chin. J. Sci. Instrum. 25 (S2), 601–604+608. doi:10.19650/j.cnki.cjsi.2004.s2.185
Wang, W. H. (2011). Appliation present status and outlook of seam water injection dust control technology. Coal Sci. Technol. 39 (01), 57–60. doi:10.13199/j.cst.2011.01.63.wangwh.021
Wang, X. G. (2011). The measurement method of surface roughness and the correct application of parameters. Shanghai Meas. Test. 38 (05), 48–49+52. doi:10.3969/j.issn.1673-2235.2011.05.016
Wang, X. N. (2020). Study on synergistic effect of surfactant compounding on wettability of coal dust. Huainan, China: AnHui University of Science and Technology. doi:10.26918/d.cnki.ghngc.2020.000038
Wei, X. F., Wang, J. G., and Ding, Y. J. (2019). Progress and development trend of clean and efficient coal utilization technology. Bull. Chin. Acad. Sci. 34 (04), 409–416. doi:10.16418/j.issn.1000-3045.2019.04.005
Wu, S. (1971). Calculation of interfacial tension in polymer systems. J. Polym. Sci. C. Polym. Symp. 34 (1), 19–30. doi:10.1002/polc.5070340105
Wu, X. J. (2019). The mortality rate of pneumoconiosis is as high as 22.04% and the prevention and control work in coal field is urgent. Saf. Health 457 (01), 45–47. CNKI:SUN:LDAQ.0.2019-01-026.
Xia, W. C., Ni, C., and Xie, G. Y. (2016). The influence of surface roughness on wettability of natural/gold-coated ultra-low ash coal particles. Powder Technol. 288, 286–290. doi:10.1016/j.powtec.2015.11.029
Xia, W. C. (2017). Role of surface roughness in the attachment time between air bubble and flat ultra-low-ash coal surface. Int. J. Mineral Process. 168, 19–24. doi:10.1016/j.minpro.2017.09.006
Yang, Y., and He, Z. (2020). China's overseas oil and gas dependence: Situation, geographical risks, and countermeasures. Resour. Sci. 42 (08), 1614–1629. doi:10.18402/resci.2020.08.15
Zhang, J. G., Li, H. M., Liu, Y. T., Li, X. Y., Xie, J., Dai, Z. X., et al. (2021). Micro-wetting characteristics of coal dust and preliminary study on the development of dust suppressant in Pingdingshan mining area. J. China Coal Soc. 46 (03), 812–825. doi:10.13225/j.cnki.jccs.YT21.0140
Keywords: coal dust, surface roughness, wettability, surface energy, surfactant
Citation: Zhang J, Xu B, Zhang P, Cai M and Li B (2023) Effects of surface roughness on wettability and surface energy of coal. Front. Earth Sci. 10:1054896. doi: 10.3389/feart.2022.1054896
Received: 27 September 2022; Accepted: 30 November 2022;
Published: 10 January 2023.
Edited by:
Yihuai Zhang, Imperial College London, United KingdomReviewed by:
Muhammad Arif, Khalifa University, United Arab EmiratesCopyright © 2023 Zhang, Xu, Zhang, Cai and Li. This is an open-access article distributed under the terms of the Creative Commons Attribution License (CC BY). The use, distribution or reproduction in other forums is permitted, provided the original author(s) and the copyright owner(s) are credited and that the original publication in this journal is cited, in accordance with accepted academic practice. No use, distribution or reproduction is permitted which does not comply with these terms.
*Correspondence: Bo Li, YW5xdWFubGlib0BocHUuZWR1LmNu
Disclaimer: All claims expressed in this article are solely those of the authors and do not necessarily represent those of their affiliated organizations, or those of the publisher, the editors and the reviewers. Any product that may be evaluated in this article or claim that may be made by its manufacturer is not guaranteed or endorsed by the publisher.
Research integrity at Frontiers
Learn more about the work of our research integrity team to safeguard the quality of each article we publish.