- 1School of Control and Computer Engineering, North China Electric Power University, Beijing, China
- 2School of Power Engineering, Mongolian University of Science and Technology, Ulaanbaatar, Mongolia
In this study, a state-space pole placement approach is first proposed to design high-order PID controllers for high-order processes. The method makes use of a single parameter to determine the locations of closed-loop poles; thus, a high-order PID controller can be tuned with this parameter. To implement the high-order PID controller in practice, an observer-based PID structure is proposed. The structure utilizes a model-free observer to estimate the plant output and its derivatives, thus retaining the high-order PID structure but can filter the measurement noise and make the high-order derivatives of the plant output available for control. The proposed method is applied to design high-order PID controllers for second-order processes with time delay. Simulation results show that high-order PID can indeed improve the performance of conventional PID controllers for second-order processes with time delay in disturbance rejection and robustness.
1 Introduction
Proportional–integral-derivative (PID) control is the most common feedback control mechanism in the industrial process (Åström and Hägglund, 2001; Chen and Seborg, 2002; Åström and Hägglund, 2006). The reason is that the three parameters of the PID controller have a clear relationship with the performance of the system, so it is easy to tune online. However, with the increase in the complexity of industrial processes and the uncertainties of the controlled plant, the traditional PID control may not meet the requirements of control performance due to its structural characteristics. Some limitations of the PID controller are illustrated in Oliveira et al. (2009). Some techniques are proposed to improve the PID control, including adding integral feedback, feedforward, or delay compensation to the traditional PID loop, which makes the PID structure complicated and requires extra parameters (Duan et al., 2008). On the other hand, control scholars put forward many advanced control methods to replace PID control, such as LQG (Garrido-Moctezuma et al., 1997), H infinity (Tan et al., 2006), and adaptive control (Mocci et al., 2020). Although these advanced control methods improve the control performance, they are rarely used in practice due to implementation, tuning, and maintenance issues. Therefore, more than 90% of the loops in the industrial process still use the PID structure (Dash et al., 2015; Latif et al., 2020).
It is well-known that PI control is suitable for first-order processes and PID control is suitable for second-order processes. For second-order processes with time delays, will high-order PID with a second-order derivative
Vrančić and Huba, (2021) show that the high-order PID controllers can significantly improve the control performance of various process models. Lin et al. (2021) illustrate that high-order linear active disturbance rejection controllers (LADRCs) can be interpreted as high-order PID with low-pass filters for speed servo systems and position servo systems. Huba et al. (2021) find that high-order PID control enables faster transients by simultaneously reducing the negative effects of measurement noise and increasing the closed-loop robustness. Huba and Vrani (2018) extend the 2DOF PI and PID controller design for the first-order time-delayed plant by the multiple real dominant pole method to the 2DOF
In practice, PI controllers are used more often than PID controllers, since the latter significantly increases the controller output noise (Ediga and Ambati, 2021). One reason is that the derivative term is very sensitive to the measurement noise, so an appropriate filter can significantly improve the closed-loop performance (Segovia et al., 2014). Naturally, with higher degrees of controllers, the problem becomes aggravated. Therefore, the appropriate high-order filter is inevitable in practical applications. Furthermore, obtaining derivative and high-order derivative signals may amplify sensor noises. Therefore, the filter is usually considered an integral part of the PID design, and the filter constants need to be selected as a compromise between robustness and performance, so PID tuning is essentially a four-parameter design procedure. However, noise is not considered in high-order PID at present. In view of this, considering the form of the high-order PID controller and ensuring the selection of its adjustable poles should be an improvement way that can be considered. Therefore, a high-order PID design method and noise suppression method are proposed in this study.
In this study, an observer is used to estimate the output and derivative of the system, and a high-order PID control structure is proposed, which does not depend on the controlled plant model and retains the traditional PID control structure but increases the controller’s disturbance rejection ability. Usually, a time delay is an approximation of high-order dynamics of the controlled plant except the pure transport delay. So, a process with time delay is in fact a high-order system; thus, a high-order PID controller can be used to achieve better control performance. The goal of the study was to propose a practical control structure that can utilize high-order derivatives of the process to improve the control performance, as compared with the conventional three-term PID controller, and we tried to design the controller via the modern control method. The structure and the design method can build a link between the modern control theory and classical control theory. The main contributions of this study are as follows: 1) an observer-based PID structure is proposed to improve the performance of conventional PID by providing high-order derivatives. The proposed observer-based PID structure is an extension of the conventional PID + filter structure in which high-order derivatives can be incorporated into the structure and the measurement noise can be handled through the extended state observer. 2) A state-space pole placement method is proposed to directly design PID gains, thus linking the modern control theory with the classical control theory. It retains the essential terms of conventional PID. To obtain a PID controller gain, the trick is to transform the model into the canonical observable form. The method is applied to second-order processes with time delay, and the simulation results show that the structure can achieve better performance than other variations of PID, and the design is in the usual modern control theory framework.
The structural arrangement of this study is as follows: in Section 2, the high-order PID controller is proposed to design through the pole placement method; in Section 3, an observer-based PID is proposed to implement high-order PID in practice; the structure and tuning of high-order PID for a variety of second-order timed-delayed systems are tested in Section 4; finally, conclusions are given in Section 5.
2 Design of high-order PID controllers via pole placement
There are many methods to get the parameters of an ideal PID. It is possible to apply the state feedback design in the PID design which is a convenient and useful control design method in the modern control theory. It is shown that the available plant model information used in the high-order PID design can guarantee the stability of the actual plant. Suppose the controlled plant has a minimal state-space realization as follows:
In this study, we will propose a method to design a high-order PID controller. Our idea is to obtain a state feedback control law
where
where
Since
Define a new variable
Here,
Suppose a state-feedback control law
To obtain a static state feedback gain with only derivatives and integral of y, by ignoring the derivatives of u, then we have
Here, u is the combination of the derivatives and integrals of y. It is in the form of a high-order PID control, with gain.
For the second-order system (m = 2), (10) is the conventional PID control, with
For the third-order system (m = 3), (10) is
The state-feedback law (9) can be designed by the well-known pole-placement method. It is well-known that the dominant poles determine the rise time and damping of the closed-loop system, so they can be used to tune the parameters of high-order PID. To design different-order controllers, different numbers of poles are selected as suggested in (13). The two poles
From extensive simulations, in order to have good damping and fast settling time in the disturbance rejection response, the damping ratio
3 Practical implementation of high-order PID controllers
In the previous section, ideal PID and
In this study, we try to estimate the derivatives of the output via an observer instead of using filters. Consider the ideal
It can be treated as the state-feedback gain
where the state vector is defined as
and the controller gain is
and the state-space matrices are
The state vector
with the observer gain
For simplicity, the observer gain
when the observer gain is chosen properly,
Combining the state feedback control and the observer, a state-space realization (mth-order) of
Note that (23) is a standard state-feedback-observer form; however, the novelty is that the state-feedback gain can be interpreted as the (high-order) PID gain due to the special state-space coefficients, and thus it builds a link between modern control and classical control theories. Not every state-feedback-observer form can be interpreted as this. It is a practical implementation of the ideal
The structure of
It is noted that the output
instead of using the true model. Thus, the model-independent control structure of PID is retained.
when
4 Simulation
This section verifies the high-order PID design for a variety of second-order processes with time delay. To use the state-space pole placement method, the delay can be approximated using the first-order Pade approximation. As an application of the high-order PID control, we consider disturbance rejection and robustness analysis of different control methods. To measure the robustness of the designed system, the peak of the sensitivity function
where
Example 1. Considering the following second-order plus time delay (SOPTD) process
a high-order PID control can be tuned with
The observer bandwidth
where a setpoint weight
The performance indexes for the two controllers are listed in Table 1. It clearly shows that the observer-based PID (29) has better disturbance rejection performance and robustness than the practical PID (30). Figure 2A shows the responses of the closed-loop system, where at t = 0 s, a unit step reference is inserted and a step disturbance input of magnitude 1 is inserted at t = 40 s. The red dotted dashed red line and black solid line represent the responses of the practical PID form (30) and observer-based PID (29), respectively.It can be clearly seen from Figure 2A that the observer-based PID has better disturbance rejection, faster response speed, and smaller overshoot than the practical PID as shown in Wang et al. (2016). The Bode plots (Figure 2C) show that the observer-based PID (29) and the practical PID (30) roll off at high frequencies, thus attenuating measurement noise as expected. The observer-based PID has a larger roll-off rate; thus, the observer-based PID has better performance against high-frequency noise. In Figure 2D, the system with a white noise with the power of 0.0001 and a sampling period of 0.1 s is introduced into the process output. It shows that the proposed observer-based PID has better sensor noise rejection performance than the practical PID (30). In the actual situation, there always exists a model mismatch. In order to evaluate the robustness of the controller, a 20% increase in the process gain and time delay and a 20% decrease in the two-time constants are considered, i.e., the perturbed plant is
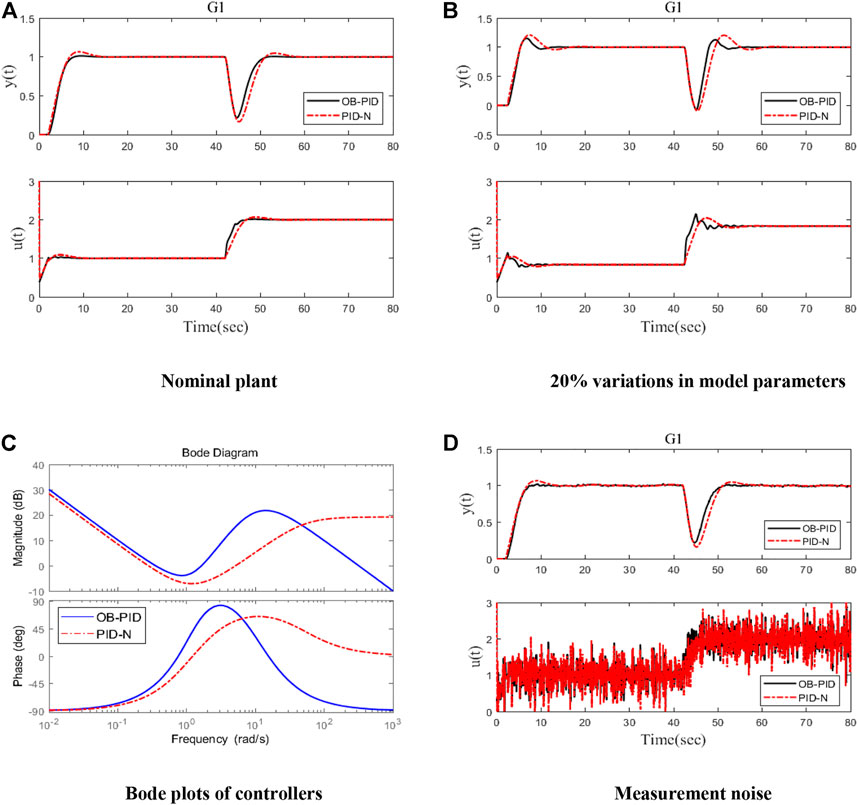
FIGURE 2. Responses for Example 1. (A) Nominal plant. (B) 20% variations in model parameters. (C) Bode plots of controllers. (D) Measurement noise.
Example 2. Considering the unstable process with a large time delay (USOPDT):
To tune a high-order PID for this plant,
The extended observer gain can be tuned with the observer bandwidth
Consider the controller designed by Shamsuzzoha and Lee (2009). A practical PID (n = 20) is implemented in practice for the controller:
The responses of the processes under the observer-based PID (33) proposed in this study and practical PID in Shamsuzzoha and Lee, (2009) are shown in Figure 3. Compared with the practical PID, the observer-based PID can achieve better tracking and disturbance rejection performance. The performance indexes for different controllers are listed in Table 2. It clearly shows that the observer-based PID (33) has better disturbance rejection performance and better control effort with smaller TV than the practical PID (34). Figure 3A shows the responses of closed-loop systems, where at t = 0 s, a unit step reference is inserted and a step disturbance input of magnitude 0.1 is inserted at t = 100 s. The red dotted dashed red line and black solid line represent the response of the practical PID form (34) and observer-based PID (33), respectively.It can be clearly seen from Figure 3A that the observer-based PID has better disturbance rejection and faster response speed than the practical PID in Shamsuzzoha and Lee, (2009). The Bode plots (Figure 3C) show that the observer-based PID (33) and the practical PID (34) roll off at high frequencies, thus attenuating measurement noise as expected. The observer-based PID has a larger roll-off rate; thus, the observer-based PID has better performance against high-frequency noise. In Figure 3D, the system with a white noise with a power of 0.00001, and a sampling period of 0.1 s is introduced into the process output. It shows that the proposed observer-based PID has better noise rejection performance than the practical PID (34). In the actual situation, there always exists a model mismatch. In order to evaluate the robustness of the controller, a 5% increase in the process gain and time delay and a 5% decrease in two-time constants are considered, i.e., the perturbed plant is
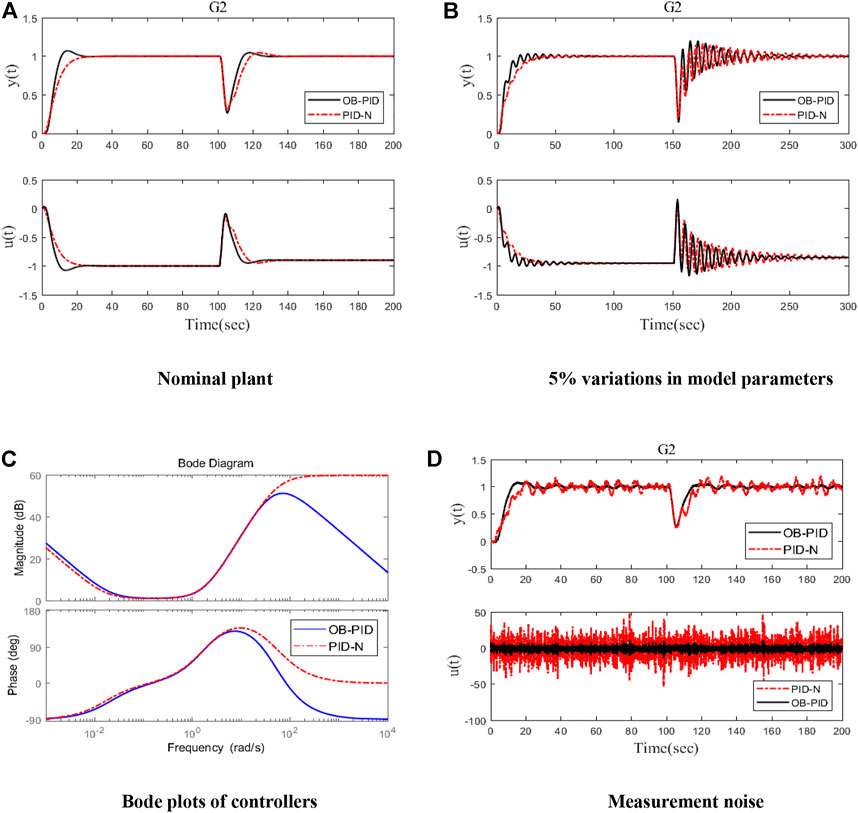
FIGURE 3. Responses for Example 2. (A) Nominal plant (b) 5% variations in model parameters. (C) Bode plots of controllers. (D) Measurement noise.
Example 3. The following second-order dead time process with two unstable poles process (SODPTUP) is considered:
A two-degree-of-freedom control structure with a disturbance estimator in the form of the practical PID (n = 20) was proposed by Shamsuzzoha and Lee (2009) for this process:
To tune a high-order PID for this plant, choose
The extended observer gain can be tuned with the observer bandwidth
The performance indexes for different controllers are listed in Table 3. It clearly shows that the observer-based PID (38) has better robustness and control effort than the practical PID (36). Figure 4A shows the responses of the closed-loop system, where at t = 0 s, a unit step reference is inserted and a step disturbance input of magnitude 1 is inserted at t = 20 s. The red dotted dashed red line and black solid line represent the response of the practical PID form (36) and observer-based PID (38), respectively. The Bode plots (Figure 4C) show that the observer-based PID (38) and the practical PID (36) roll off at high frequencies, thus attenuating measurement noise as expected. The observer-based PID has a larger roll-off rate; thus, the observer-based PID has better performance against high-frequency noise. In Figure 4D, the system with a white noise with a power of 0.00001 and a sampling period of 0.1 s is introduced into the process output. In order to evaluate the robustness of the controller, a 20% increase in the process gain and time delay and a 20% decrease in two-time constant are considered, i.e., the perturbed plant is
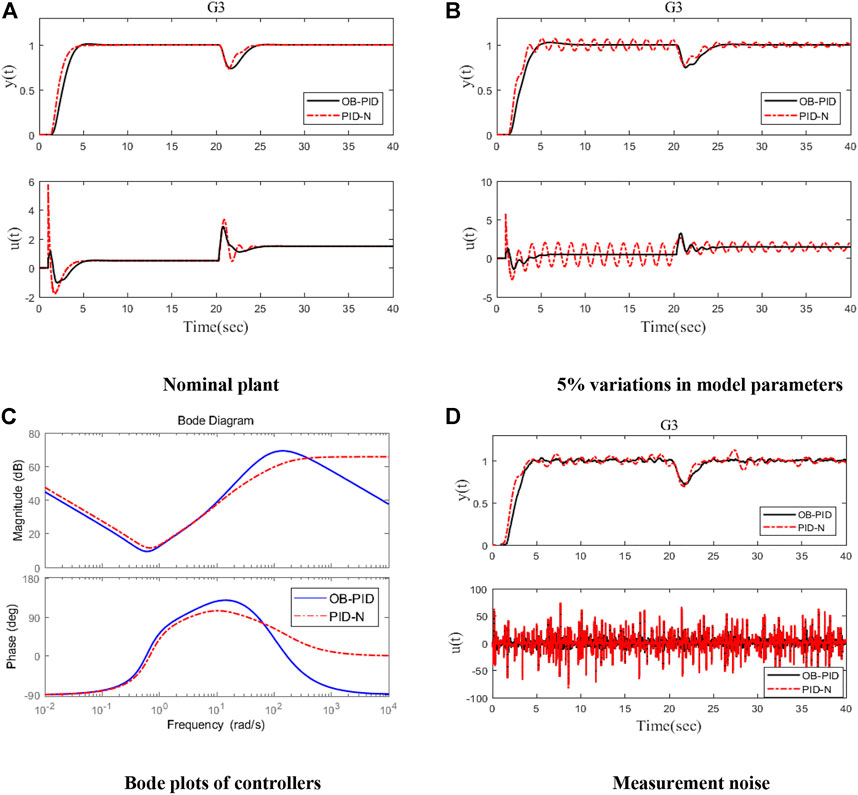
FIGURE 4. Responses for Example 3. (A) Nominal plant. (B) 5% variations in model parameters. (C) Bode plots of controllers. (D) Measurement noise.
Example 4. Considering the unstable process with an integrator:
To tune a high-order PID for this plant, choose
With
For comparison, consider the two-degree-of-freedom control structure with a disturbance estimator in the form of the practical PID (n = 20) proposed by Shamsuzzoha and Lee, (2009) for this process.
The performance indexes for different controllers are listed in Table 4. It clearly shows that the observer-based PID (41) has better control effort than the practical PID (42) but disturbance rejection performance and robustness similar to the practical PID. Figure 5A shows the responses of the closed-loop system, where at t = 0 s, a unit step reference is inserted and a step disturbance input of magnitude 1 is inserted at t = 15 s. The red dotted dashed red line and black solid line represent the response of the practical PID form (42) and observer-based PID (41), respectively.It can be clearly seen from Figure 5A that the observer-based PID has almost the same disturbance rejection performance as the practical PID as shown in Shamsuzzoha and Lee, (2009). The Bode plots (Figure 5C) show that the observer-based PID and the practical PID roll off at high frequencies, thus attenuating measurement noise as expected. The observer-based PID has a larger roll-off rate; thus, the observer-based PID has better performance against high-frequency noise. In Figure 5D, the system with a white noise with a power of 0.0001 and a sampling period of 0.1 s is introduced into the process output. It shows that the proposed observer-based PID has better noise rejection performance than the practical PID. In order to evaluate the robustness of the controller, a 10% increase in the process gain and time delay and a 10% decrease in the time constant are considered, i.e., the perturbed plant is
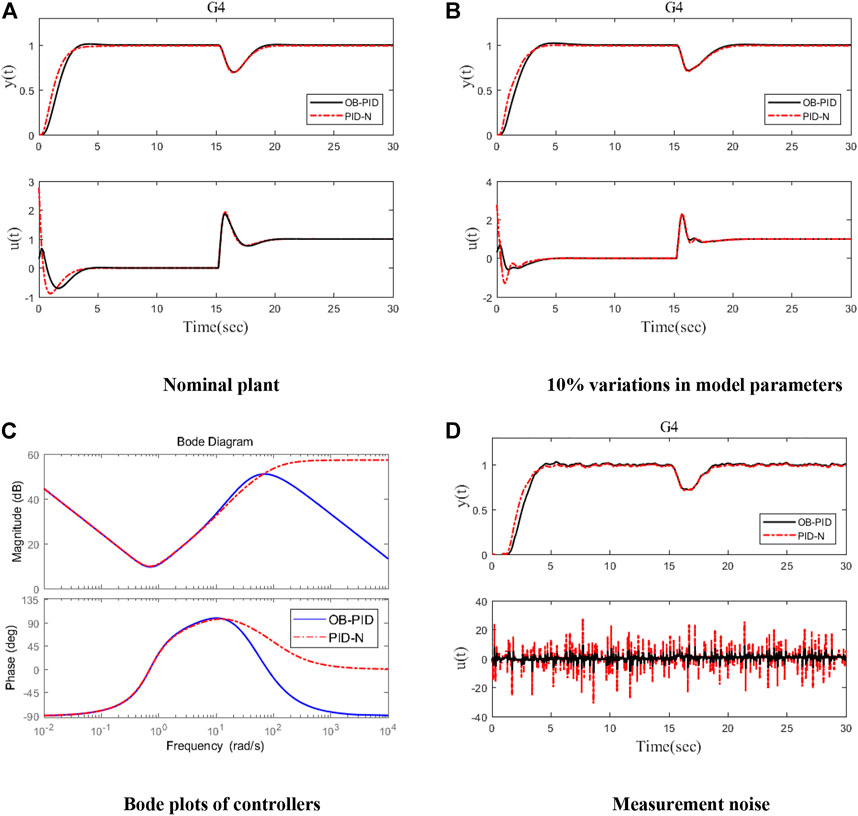
FIGURE 5. Responses for Example 4. (A) Nominal plant. (B) 10% variations in model parameters. (C) Bode plots of controllers. (D) Measurement noise.
5 Conclusion
A state feedback pole-placement method was proposed to design high-order PID controllers, and an observer-based PID structure was proposed to implement high-order PID controllers. The observer-based PID can effectively suppress noise by estimating the derivatives of the plant output through a model-independent observer. It was shown that the observer-based PID can be tuned with two parameters,
It is observed that if a cost function is used in the state-feedback design and observer design, then it can be directly related to an optimal controller; thus, an observer-based PID can also be designed via the well-known LQG method, which will be investigated in the future.
Data availability statement
The original contributions presented in the study are included in the article/Supplementary Material; further inquiries can be directed to the corresponding author.
Author contributions
WH substantially contributed to the conception and design of the work and the acquisition of data for the work. QH analyzed and interpreted data for the work. UD drew the picture and checked the work. WT revised the manuscript critically for important intellectual content.
Conflict of interest
The authors declare that the research was conducted in the absence of any commercial or financial relationships that could be construed as a potential conflict of interest.
Publisher’s note
All claims expressed in this article are solely those of the authors and do not necessarily represent those of their affiliated organizations, or those of the publisher, the editors, and the reviewers. Any product that may be evaluated in this article, or claim that may be made by its manufacturer, is not guaranteed or endorsed by the publisher.
References
Åström, K. J., and Hägglund, T. (2006). Advanced PID control. Research Triangle Park: ISA-The Instrumentation, Systems, and Automation Society 461.
Åström, K. J., and Hägglund, T. (2001). The future of PID control. Control Eng. Pract. 9, 1163–1175. doi:10.1016/S0967-0661(01)00062-4
Chen, D., and Seborg, D. E. (2002). PI/PID controller design based on direct synthesis and disturbance rejection. Ind. Eng. Chem. Res. 41, 4807–4822. doi:10.1021/ie010756m
Dash, P., Saikia, L. C., and Sinha, N. (2015). Automatic generation control of multi area thermal system using Bat algorithm optimized PD–PID cascade controller. Int. J. Electr. Power & Energy Syst. 68, 364–372. doi:10.1016/j.ijepes.2014.12.063
Du, Y., Cao, W., and She, J. (2022). Analysis and design of active disturbance rejection control with improved extended state observer for systems with measurement noise. IEEE Trans. Ind. Electron., 1. doi:10.1109/TIE.2022.3153821
Duan, X. G., Li, H. X., and Deng, H. (2008). Effective tuning method for fuzzy PID with internal model control. Ind. Eng. Chem. Res. 47, 8317–8323. doi:10.1021/ie800485j
Ediga, C. G., and Ambati, S. R. (2021). Measurement noise filter design for unstable time delay processes in closed loop control. Int. J. Dyn. Control 10, 138–161. doi:10.1007/s40435-021-00798-0
Gao, Z. (2003). “Scaling and bandwidth-parameterization based controller tuning,” in Proceedings of the 2003 American Control Conference, 2003. Presented at the 2003 American Control Conference, Denver, CO, USA, 04-06 June 2003 (IEEE), 4989–4996. doi:10.1109/ACC.2003.1242516
Garrido-Moctezuma, R., Suarez, D. A., and Lozano, R. (1997). “Adaptive LQG control of positive real systems,” in 1997 European Control Conference (ECC), Brussels, Belgium, 01-07 July 1997. doi:10.23919/ECC.1997.7082083
Huba, M., Vrancic, D., and Bistak, P. (2021). PID control with higher order derivative degrees for IPDT plant models. IEEE Access 9, 2478–2495. doi:10.1109/ACCESS.2020.3047351
Huba, M., and Vrani, D. (2018). “Comparing filtered PI, PID and PIDD 2 control for the FOTD plants,” in 3rd IFAC Conference on Advances in Proportional-Integral-Derivative Control, Ghent, Belgium, May 9–11, 2018 51 (4), 954–959.
Latif, A., Shankar, K., and Nguyen, P. T. (2020). Legged fire fighter robot movement using PID. JRC. 1, 15–19. doi:10.18196/jrc.1104
Lin, P., Wu, Z., Fei, Z., and Sun, X. M. (2021). A generalized PID interpretation for high-order LADRC and cascade LADRC for servo systems. IEEE Trans. Ind. Electron. 1, 5207–5214. doi:10.1109/tie.2021.3082058
Mocci, J., Quintavalla, M., Chiuso, A., Bonora, S., and Muradore, R. (2020). PI-shaped LQG control design for adaptive optics systems. Control Eng. Pract. 102, 104528. doi:10.1016/j.conengprac.2020.104528
Oliveira, V. A., Cossi, L. V., Teixeira, M., and Silva, A. (2009). Synthesis of PID controllers for a class of time delay systems. Automatica 45, 1778–1782. doi:10.1016/j.automatica.2009.03.018
Sahib, M. A. (2015). A novel optimal PID plus second order derivative controller for AVR system. Eng. Sci. Technol. Int. J. 13, 194–206. doi:10.1016/j.jestch.2014.11.006
Segovia, V. R., Hägglund, T., and Åström, K. J. (2014). Measurement noise filtering for PID controllers. J. Process Control 24, 299–313. doi:10.1016/j.jprocont.2014.01.017
Shamsuzzoha, M., and Lee, M. (2009). Enhanced disturbance rejection for open-loop unstable process with time delay. ISA Trans. 48, 237–244. doi:10.1016/j.isatra.2008.10.010
Simanenkov, A. L., Rozhkov, S. A., and Borisova, V. A. (2017). “An algorithm of optimal settings for PIDD 2 D 3-controllers in ship power plant,” in 2017 IEEE 37th International Conference on Electronics and Nanotechnology (ELNANO) (IEEE), 152–155.
Tan, W., Liu, J., Chen, T., and Marquez, H. J. (2006). Comparison of some well-known PID tuning formulas. Comput. Chem. Eng. 30, 1416–1423. doi:10.1016/j.compchemeng.2006.04.001
Vrančić, D., and Huba, M. (2021). High-order filtered PID controller tuning based on magnitude optimum. Mathematics 9, 1340. doi:10.3390/math9121340
Keywords: observer-based PID, high-order PID, second-order processes with time delay, parameter tuning, pole placement
Citation: Han W, Hu X, Damiran U and Tan W (2022) Design and implementation of high-order PID for second-order processes with time delay. Front. Control. Eng. 3:953477. doi: 10.3389/fcteg.2022.953477
Received: 26 May 2022; Accepted: 27 July 2022;
Published: 29 August 2022.
Edited by:
Tao Liu, Dalian University of Technology, ChinaReviewed by:
Ramon Vilanova, Universitat Autònoma de Barcelona, SpainShengquan Li, Yangzhou University, China
Copyright © 2022 Han, Hu, Damiran and Tan. This is an open-access article distributed under the terms of the Creative Commons Attribution License (CC BY). The use, distribution or reproduction in other forums is permitted, provided the original author(s) and the copyright owner(s) are credited and that the original publication in this journal is cited, in accordance with accepted academic practice. No use, distribution or reproduction is permitted which does not comply with these terms.
*Correspondence: Wenjie Han, MTMyNTMxNTE1MzJAMTYzLmNvbQ==