- 1Department of Electrical Engineering, Universidad de Concepción, Concepción, Chile
- 2Computer Science Department, Universidad Católica de La Santísima Concepción, Concepción, Chile
In this work, we introduce signal-to-noise ratio (SNR) based fault detection and identification mechanisms for a networked control system feedback loop, where the network component is represented by an additive white noise (AWN) channel. The SNR approach is known to be a steady-state analysis and design tool, thus we first introduce a finite time approximation for the estimated AWN channel SNR. We then consider the case of a general linear time-invariant plant model with one unstable pole. The potential faults that we discuss here cover simultaneously the plant model gain and/or the unstable pole. The fault detection is performed relative to the estimated AWN channel SNR. The fault identification is performed using recursive least squares ideas and then further validated with the observed SNR value, when a fault has been previously detected. We show that the proposed SNR-based fault mechanism (fault detection plus fault identification) is capable of processing the proposed faults. We conclude discussing future research based on the contributions exposed in the present work.
1 Introduction
Control theory, from the 20th century up to the 21st century, moved from what is known as classic control into new research areas such as networked control systems (NCSs). Theory and practice experts have been very busy (Chen et al., 2011), since results in NCSs are intrinsically multidisciplinary by definition, for example, by considering simultaneously established results in control and also information theory (Nair and Evans, 2004; Martins and Dahleh, 2008). Other examples joined linear optimal control results together with communication theory results (Elia, 2004; Braslavsky et al., 2007; Rojas, 2012) for additive white noise (AWN) channels. Similarly, an optimal approach for output tracking control over erasure channels has been proposed for stability and subject to model uncertainties in Jiang et al. (2021). In more recent years, we have also seen an increase in results that involve event-triggered NCS controllers (Heemels et al., 2012; da Silva et al., 2014; Campos-Delgado et al., 2015) which attempt to use limited available communication and energy resources with paucity, and nevertheless achieve a set of given goals, be those goals stability, performance, or robustness. These and other NCS results can constitute the foundation for a better control practice in the near future.
An NCS result, contributed early on in Braslavsky et al. (2007), imposes a channel input power constraint
A large body of contributions also exist on the topic of fault detection and identification, with many books already written on these topics (Gertler, 1998; Chen and Patton, 1999; Blanke et al., 2003; Isermann, 2006; Saberi et al., 2007; Varga, 2017), together with informative review articles such as Ding et al. (2000) and Saberi et al. (2000). A fault is usually defined as an abnormal behavior occurring in a process, which in turn is of interest to first detect, identify, and then (ideally) properly recover from. There are different formulations for the problem of fault detection for LTI systems, which can be roughly categorized as approximate (such as the synthesis of fault detection filters subject to noise) and exact formulations (such as the nullspace method).
The variability inherent in NCSs might also be caused by anomalous variations in the plant model. An NCS example of the proposed setup is presented in Figure 1, where in this article we have considered a memoryless AWN communication channel in place of the communication network, specifically over the feedback path. These anomalous variations can be given the interpretation of faults, thus the need to develop a fault mechanism to detect and identify them (Figure 1) to later on inform a possible controller adaptation in order to achieve what is known as a fault-tolerant control feedback loop. Ding (2012) contributed a survey on NCS fault detection and fault-tolerant control. Another review on fault diagnosis for NCS can be found in Aubrun et al. (2008) with the objective of reducing performance degradation due to the different NCS communication features. A dynamic observer is designed for sensor fault detection under finite frequency disturbance and noise in a linear NCS (Dai et al., 2021). In Ren et al. (2018), an event-triggered H-infinity fault detection filter has been contributed in order to reduce unnecessary communication in the NCS dominated by time-varying latency and fading phenomena. A Bayesian approach, on the other hand, is the basis in Lami et al. (2020) for a fault detection proposal, in the context of an NCS irrigation canal application, while Li et al. (2009) use a Markov jumping linear system (MJLS) approach to define their residual generator. An NCS robust fault-tolerant control feedback loop is designed in Bahreini and Zarei (2019) with faults also modeled as MJLS, but with incomplete transition probabilities knowledge, for which Linear Matrix Inequalities based sufficient conditions are then presented as to ensure stochastic stability. In a multi-agent context, task allocation is proposed in Schenk and Lunze (2020) to achieve fault tolerance through the cooperation between a set of healthy and faulty agents, instead of focusing on recovering nominal performance; see also Wang et al. (2021). A nonlinear model predictive control, subject to random network latencies and random packet dropout phenomena, is used to design a fault-tolerant control feedback loop in Wang et al. (2016) based on a predictive observer with guaranteed input-to-state stability. On the other hand, a class of nonlinear NCSs, where the nonlinear terms is modeled using neural networks, has been studied by Ye et al. (2021), and LMIs are used to obtain the fault detection filter gains. Fault detection for nonlinear NCSs subject to random delays has also been considered when using the LMIs by Li et al. (2020), Huang and Pan (2020), and Gu and Yao (2021). Finally, a robust neural network-based controller was designed to detect and mitigate false data injection attacks (which can be interpreted as malicious faults) in Sargolzaei et al. (2020).
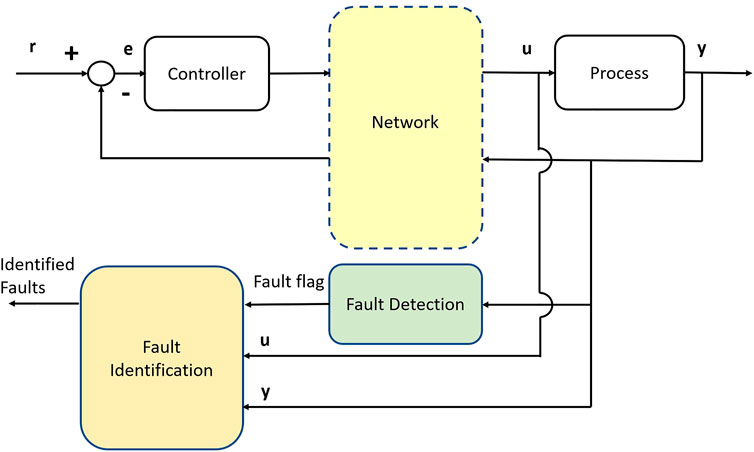
FIGURE 1. Networked control system (NCS) single-input single-output (SISO) feedback loop with fault detection and fault identification stages.
The current state of the art on fault mechanism designs for NCS still lacks the option of an SNR approach-based fault detection and identification mechanism. We also observe that most of the reported NCS contributions include a communication network simultaneously over the controller-to-plant (C2P) and the plant to controller (P2C) paths (Figure 1). However, when designing the NCS feedback loop, there is always the potential to collocate either the controller with the sensor devices, thus considering only the C2P path, or the controller with the plant model, and only then dealing with the P2C path for explicit AWN channel location. In this work, we focus on the P2C path, since for fault detection, the C2P path option, or the simultaneous presence of AWN communication channels in both locations, can be addressed in a similar manner.
Our first contribution in this article is to establish a fault detection algorithm to determine the occurrence of faults based on an finite time estimated AWN channel SNR. This for a SISO LTI plant model with one unstable pole. Our second contribution is to add to the previous detection algorithm, a fault identification stage using the recursive least square (RLS) algorithm which, upon a fault being flagged, can discriminate faults consistent with the estimated AWN channel SNR. We use examples, when appropriate, to further illustrate the proposed contributions.
This article is organized as follows: Section 2 presents the general assumptions, introducing the plant and AWN channel models. We also present here the AWN channel SNR deduction for a control feedback loop. Section 3 addresses the contributions of this work; that is, we define in full the proposed finite time AWN channel SNR estimation, the SNR-based fault detection stage and the fault identification stage for the proposed plant model. In Section 4, we discuss the possible avenues for generalization in future research of the presented results and summarize the present work.
2 Methods
In the following subsection, we proceed to list the assumptions for the present work.
2.1 Assumptions
–LTI plant model: The LTI plant model G(z) is assumed to be an LTI model given by
with
–AWN channel model: The AWN channel model is characterized by its channel input power constraint
–Channel additive noise process n(k): The channel additive noise process n(k) is assumed, to be in this work, as a zero mean, independent and identically distributed, white noise process. The noise variance σ2 is assumed to be known.
– Reference signal: The reference signal is assumed to be constant and of value
The plant LTI model, AWN channel model, and channel additive noise process assumptions are in line with the SNR approach and can be traced to the seminal work of Braslavsky et al. (2007). The reference signal is adapted from the work of Rojas (2021).
2.2 Signal-to-Noise Ratio Constrained Control Approach
We now proceed to illustrate the SNR constrained control approach. For this, we take the case of r = 0.
From Figure 2, we have that the channel input power
Here T(z) is the complementary sensitivity function feedback loop transfer function with output y(k) and input r(k). We can then restate the channel input power inequality as an SNR inequality by means of the H2 norm of T(z)
where
2.3 Finite Time Approximation
For designing a fault detection scheme, we cannot in practice guarantee k → ∞ to compute the channel input power definition from the available measurement of y(k). To achieve this, we introduce the following definition:
Definition 1. L is the sample length on which the stationarity assumption for the control feedback loop signals (in particular, the channel input signal) holds for a given tolerance value ϵ defined by the user.Based on Definition 1, we then propose an L sample length moving average of the channel input signal y(k) as its finite time approximation version
We are then left with appropriately selecting the value of L. For this, we propose to use the averaged signal variance such that
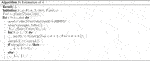
Algorithm 1. Estimation of L.Starting with the initialization stage, Algorithm 1 runs an outer for loop of a simulation based on Figure 2, evaluating the infimal SNR over an AWN channel over the P2C path (using, for example, MATLAB). Then, the inner for loop retrieves the simulated output vector y(k) data to repeat the yL calculation a total of N times over a rolling time-window of selected length L, from Tss + k + 1 to Tss + k + L. Tss is a time value set so as to avoid any initial conditions in transient. The selections for the inner for loop will test the candidate value of L through a specific channel noise realization, when the closed-loop dynamics have settled (by means of Tss). The outer for loop completes the algorithm by averaging the selection of L through a number of noise realizations determined by the parameter iter and by testing the ϵ stopping condition with the sample variance of yL(k) obtained from the inner loop. If the sample variance fails the test, then we add one to the working value of L and repeat each of the steps. If the sample variance satisfies the ϵ stopping condition, we then output the last working value L as the selected time window length in Eq. 4.
3 Results
By considering the value of L settled using Algorithm 1, we now move on into providing a lemma for SNR-based fault detection.
Lemma 1. SNR Fault Detection. The Fault Flag (FF) variable is raised to 1 when a fault is detected in an NCS feedback loop as shown in Figure 2; that is,
where SNRL(k) is the finite time SNR approximation defined as
and Γo is the nominal theoretical SNR (with no faults), with L chosen using Algorithm 1. In turn, the confidence level
equal to α times the ratio between σy, the theoretical stationary standard deviation of the channel input y(k), and σ, the channel noise n(k) standard deviation.The fault detection mechanism proposed in Lemma 1 constitutes the first contribution of the present work.
Remark 1. We observe that the proposed SNR fault detection mechanism is transparent to the simultaneous presence of the AWN channels over the C2P and P2C paths. The presence of both AWN channels will result in a different value of Γo, which is predicted to be (for example, see Rojas, 2013):
where To(z) is the nominal complementary sensitivity (without faults),
Remark 2. Since
Remark 3. The value of α, on the other hand, is a design parameter for the fault detection mechanism, highlighting a trade-off between the rate of false positive fault detection (detecting a fault when there is none) and false negative detection (not detecting a fault when there is one). Therefore, the α parameter needs to be selected with care depending on the specific problem. If α is too small, then the noise level will trigger more false positive detections. This could still be traded-off against a larger value of L, but would imply an increased delay in detecting a fault when it occurs, due to the need of averaging a larger number of samples to obtain SNRL. On the other hand, if the value of α is too large, there will be an opposite effect; that is, it would increase the occurrence of false negatives (the claim that there is no fault when there is really one). We would expect that if the expected fault SNR level is big with respect to the nominal SNR level Γo, then larger values of α could be used because there would be a less likelihood of false negatives. On the other hand, if there exists previous information of a smaller fault SNR level with respect to the nominal SNR level Γo, then a smaller α should be used, with a lower limit imposed by the presence of the channel noise.
Remark 4. We observe that the SNR approach behind Lemma 1 is a stationary approach. As a consequence, assuming stability of the control feedback loop, the same proposed detection mechanism could potentially be applied to nonlinear plant models, since it is well known that a nonlinear state trajectory can be approximated by a linear state trajectory in the vicinity of a stable equilibrium point.We now address, in the next lemma, our second contribution which consists of adding to the previous SNR-based detection algorithm a fault identification stage based on the process identification RLS algorithm.
Lemma 2. Fault Identification. Consider that a fault takes place in the plant model Eq. 1 due to a simultaneous change ΔK in the value of K and Δρ in the value of ρ when in feedback loop (Figure 2) with the controller defined as
where Ki is known as the integral action gain. The above controller is assumed to stabilize the nominal feedback loop and the faulty feedback loop. The fault identification mechanism (Figure 1) has access to the values of u(k) and y(k) and can identify the fault values ΔK and Δρ, when the FF(k) in (Eq. 5) is 1, by means of a finite memory recursive least square (FM-RLS) algorithm as
where us(k) is the output of the stable part of the plant model, that is, us(k) = gs(k) ∗ u(k), with
Proof. When the AWN channel is over the P2C path, the complementary sensitivity function describes the feedback loop relationship between y(k) and n(k) (bar a negative sign), as well as the feedback loop relationship between y(k) and r(k). Given the proposed controller structure, the theoretical channel SNR will be defined as
Due to the channel noise being white, we satisfy the condition of persistent excitation for closed loop identification. In the presence of a fault due to a simultaneous change ΔK and Δρ, if signals y(k) and u(k) are available, then it is a matter of observing the correct regressor matrix to identify the changing values of the parameters K(k) and ρ(k) (time-varying values due to the faults) together with a FM-RLS. The use of process identification methods, such as RLS, for a correct fault identification is suggested, for example, in Isermann (2006, Ch. 9). Observing that Gs(z), the stable part of the plant model, is not subject to change, we can then filter u(k) and obtain us(k) = gs(k) ∗ u(k). The resulting regressor matrix for a vector parameter
The estimated parameters vector is then
Example 1. We proceed with the present example by stating the values for the proposed parameters of this example in Table 1.The parameters values in Table 1 are a representative selection. The greater the values of r, ρ, and K, the greater value of the nominal SNR Γo. The values of the parameters iter, Tsim, and ϵ related to Algorithm 1 are such that we achieve convergence of L to the value of 92. The plant model parameters Gs(z) and controller C(z) are such that we have control feedback loop stability at nominal and faulty conditions. The controller C(z) contains integral action to achieve reference signal tracking.In Figure 3, we have the numerical evaluation for the proposed plant model:
The plant model has one unstable pole as to have nominal SNR Γo greater than one (see Braslavsky et al., 2007 for more details). The other pole and transmission zero are stable.The plant model in Eq. 14 is then put in a feedback loop together with the proposed controller:
The proposed controller above is such that it grants tracking of the proposed constant reference signal r = 1 due to the pole at z = 1, as well as invert cancel out the stable part Gs(z) of the plant model.As the iterations in Algorithm 1 increase (Figure 3), the L value for the finite time approximation is tested and, failing the comparison with the stop value of ϵ, is then increased to the final selected value of L = 92 after the set of 500 iterations. It is reasonable to assume convergence is achieved, since for the last 300 iterations, the value of L grew less than 10%. Notice from Figure 3 that the value of L is also effectively updated when the variance of yL(k) exceeds the threshold limit defined by ϵ in Table 1(shown by the horizontal orange dashed line).We consider the effect of two faults for the proposed time model, described by the values in Table 2.Observe that the proposed faults focus on ΔK, which can be interpreted as an input fault, and on Δρ, which is a fault that more directly affects the SNR level under faulty conditions. We do not consider here, and leave as future research, the case of fault changes on the stable part Gs(z) of the plant model since this would affect the controller stable cancellation of it and might result in an unstable control feedback loop under faulty conditions.The feedback loop starts in the nominal condition until time sample k = 5,000 when the first fault, described by the pair (ΔK1, Δρ1), takes place. The first fault ends at time sample k = 10,000, recovering nominal conditions. At time sample k = 15,000, the second fault described by the pair (ΔK2, Δρ2) now takes place up to time sample k = 20,000. We then recover again nominal conditions up to time sample 25,000 when the simulation concludes. The theoretical SNR at nominal conditions is 9.9474, whereas the theoretical SNR under the first fault condition is 60.7302, while the theoretical SNR for the second fault is 60.9940.We now consider the application of Lemma 1 to detect the proposed faults. Notice that with G(z) in Eq. 14 and the controller C(z) in Eq. 15, the nominal feedback loop complementary sensitivity To will have an H2 norm of 2.9912. Thus, the confidence level is obtained as
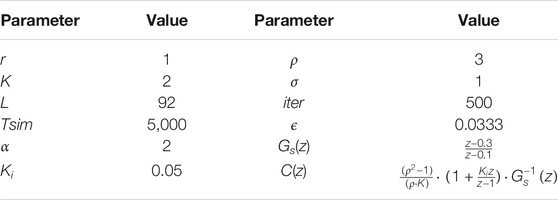
TABLE 1. Parameters values for Example 1.
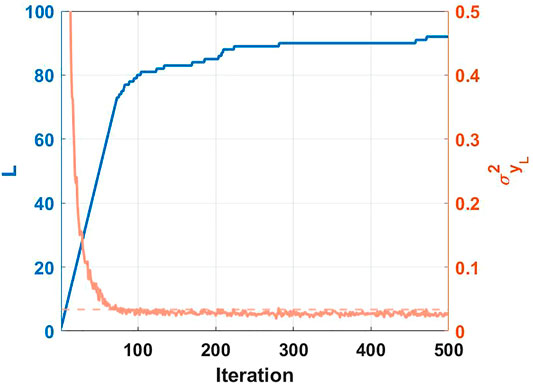
FIGURE 3. Evolution of the estimated value of L as per Algorithm 1.
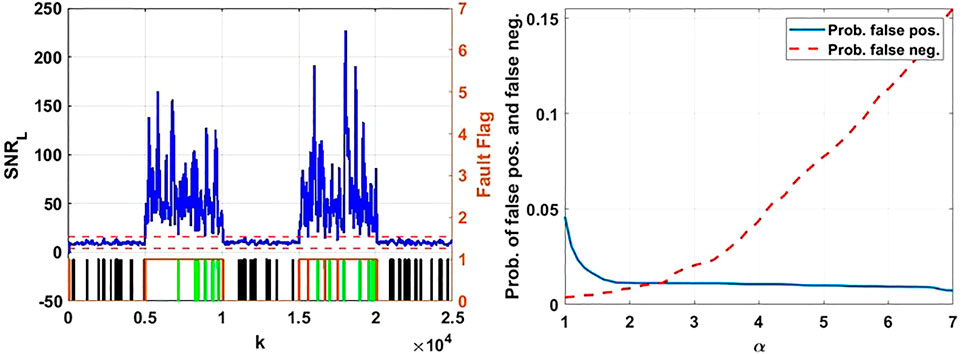
FIGURE 4. (A) Estimated finite time SNRL, blue solid line. Fault flag variable FF for α = 1, solid black line; for α = 2, solid orange line; and for α = 4, solid green line. (B) Evaluation of false positive probability, blue solid line, and false negative probability, red dashed line, as functions of α.
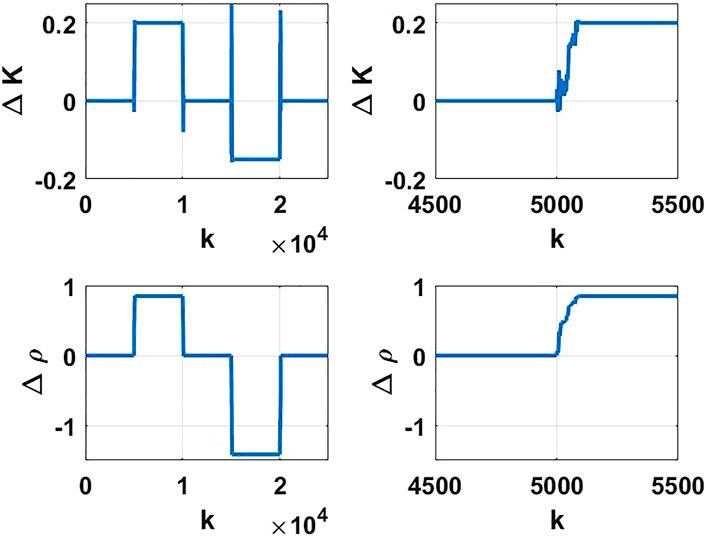
FIGURE 5. ΔK(k) and Δρ(k) estimates, left panels. Zoom on the estimates at the start of the first fault, right panels.
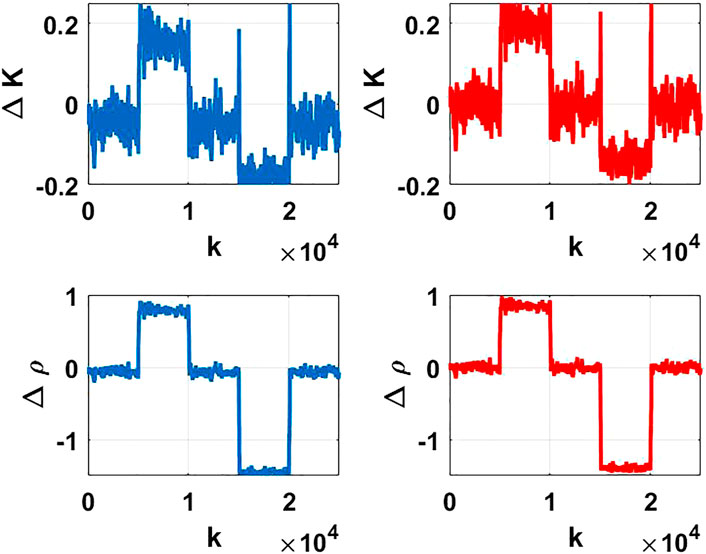
FIGURE 6. ΔK(k) and Δρ(k) estimates with noisy u(k), left panels in blue. Detrended ΔK(k) and Δρ(k) estimates with noisy u(k), left panels in red.
4 Discussion
In this work, we present an SNR-based fault detection and fault identification mechanisms for an NCS feedback loop, when the network is represented by an AWN channel over the P2C path. To the best of the authors' knowledge, the stated contribution is novel in as much that in the current state of the art no fault mechanism designs for NCS uses the SNR approach nor deals with the AWN channel model. The steady-state SNR approach required the introduction of a finite time approximation to estimate the relevant feedback loop signals, which we developed here. We also considered a fairly general LTI plant model containing one unstable pole. The faults that we studied were represented by sudden changes in both the plant model gain and/or the unstable pole values. The fault detection was achieved comparing with Γo, the AWN channel nominal SNR over the P2C path. The effect of the inclusion of an optimal tracking objective or the potential inclusion of simultaneous channels in the C2P and P2C paths can also readily be included in the proposed SNR of the AWN channel nominal SNR over the P2C value Γo.
On the other hand, the fault identification was performed here using an FM-RLS approach, when a fault has been previously detected. We showed with an example that the proposed SNR-based fault mechanism (fault detection plus fault identification) was capable of processing the proposed faults, with the caveat of almost perfect access to the signal u(k) at the process input. The SNR-based fault detection mechanism was not compared with other NCS-based fault mechanisms because, as far as the authors have surmised from the current state of the art, no other comparable results exist for AWN channel models subject to a power constraint (the core of the SNR approach). There are indeed other fault detection and identification solutions for NCS, as presented in the Introduction, but they focus on different communication features (channel latencies, erasure, fading, etc.). More so, even if a comparison with other NCS fault detection results was feasible, considering the result of Example 1, the fault detection response of our contribution successfully detects the proposed faults, and other methods could only perform equally as good. This is in the on-off nature of the fault detection question, either there is a fault or not, and at best, the answer from any other method would be the same. With respect to the SNR-based fault identification mechanism, the comparison with other methods could indeed be more nuanced, but again considering the results in Figure 6, we obtained an excellent fault identification result when using the FM-RLS approach here, a performance which could only be tied at best by other current NCS fault identification methods if they were actually comparable (which they are not, because they consider different communication network features, than additive channel noise and channel input power constraint).
Future research should consider relaxing the requirement on u(k) for fault identification, propose a different fault identification mechanism using perhaps a priori knowledge on the types of faults to be expected, the case of fault changes on the stable part Gs(z) of the plant model, and consider the case of other types of communication channel models. For example, if we want to consider optimal output tracking over erasure channels, we can adapt the results in Jiang et al. (2021) to obtain a new analytical expression for a power constraint expression akin to Γo.
Data Availability Statement
The raw data supporting the conclusion of this article will be made available by the authors, without undue reservation.
Author Contributions
All authors listed have made a substantial, direct, and intellectual contribution to the work and approved it for publication.
Funding
The authors are thankful to the Chilean Research Agency ANID for its support through Project Grant FONDECYT Regular No. 1190196 and Basal Project FB0008.
Conflict of Interest
The authors declare that the research was conducted in the absence of any commercial or financial relationships that could be construed as a potential conflict of interest.
Publisher’s Note
All claims expressed in this article are solely those of the authors and do not necessarily represent those of their affiliated organizations, or those of the publisher, the editors, and the reviewers. Any product that may be evaluated in this article, or claim that may be made by its manufacturer, is not guaranteed or endorsed by the publisher.
References
Aubrun, C., Sauter, D., and Yamé, J. (2008). Fault Diagnosis of Networked Control Systems. Int. J. Appl. Maths. Comput. Sci. 18, 525–538. doi:10.2478/v10006-008-0046-3
Bahreini, M., and Zarei, J. (2019). Robust Fault-Tolerant Control for Networked Control Systems Subject to Random Delays via Static-Output Feedback. ISA Trans. 86, 153–162. doi:10.1016/j.isatra.2018.10.034
Blanke, M., Kinnaert, M., Lunze, J., and Staroswiecki, M. (2003). Diagnosis and Fault-Tolerant Control. Berlin: Springer-Verlag.
Braslavsky, J. H., Middleton, R. H., and Freudenberg, J. S. (2007). Feedback Stabilization over Signal-To-Noise Ratio Constrained Channels. IEEE Trans. Automat. Contr. 52, 1391–1403. doi:10.1109/tac.2007.902739
Campos-Delgado, D. U., Rojas, A. J., Luna-Rivera, J. M., and Gutiérrez, C. A. (2015). Event-triggered Feedback for Power Allocation in Wireless Networks. IET Control. Theor. Appl. 9, 2066–2074.
Chen, J., de Silva, C., Olariu, S., Paschalidis, I. C., and Stojmenovic, I. (2011). “IEEE Transactions on Automatic Control,” in Special Issue on Wireless Sensor and Actuator Networks, Vol. 56.
Chen, J., and Patton, R. J. (1999). Robust Model-Based Fault Diagnosis for Dynamic Systems. London: Kluwer Academic Publishers.
da Silva, J. M. G., Lages, W. F., and Sbarbaro, D. (2014). “Event-triggered PI Control Design,” in Proceedings of the 19th IFAC World Congress, Cape Town, South Africa, 6947–6952. doi:10.3182/20140824-6-za-1003.01824IFAC Proc. Volumes47
Dai, X.-W., Zheng, Z.-D., Gao, Y., Cui, D.-L., and Zhao, H.-T. (2021). Pole-zero Optimization Design of Dynamic Observer for Fault Detection of Networked Control Systems. Kongzhi Yu Juece/Control Decis. 36, 1351–1360.
Ding, S. X. (2012). A Survey of Fault-Tolerant Networked Control System Design. IFAC Proc. Volumes 45, 874–885. doi:10.3182/20120829-3-mx-2028.00259
Ding, S. X., Jeinsch, T., Frank, P. M., and Ding, E. L. (2000). A Unified Approach to the Optimization of Fault Detection Systems. Int. J. Adapt. Control. Signal. Process. 14, 725–745. doi:10.1002/1099-1115(200011)14:7<725::aid-acs618>3.0.co;2-q
Elia, N. (2004). When Bode Meets Shannon: Control-Oriented Feedback Communication Schemes. IEEE Trans. Automat. Contr. 49, 1477–1488. doi:10.1109/tac.2004.834119
Gu, Z., and Yao, L. (2021). Fault Diagnosis and Fault‐tolerant Control of Uncertain Network Control Systems. Int. J. Adapt Control. Signal. Process. 35, 1941–1956. doi:10.1002/acs.3300
Heemels, W., Johansson, K., and Tabuada, P. (2012). “An Introduction to Event-Triggered and Self-Triggered Control,” in Proceedings of the 51th Conference on Decision and Control, 3270–3285. doi:10.1109/cdc.2012.6425820
Huang, K., and Pan, F. (2020). Fault Detection for Nonlinear Networked Control Systems with Sensor Saturation and Random Faults. IEEE Access 8, 92541–92551. doi:10.1109/access.2020.2992540
Jiang, X., Chi, M., Chen, X., Yan, H., and Huang, T. (2021). Output Tracking Control Performance of Discrete Networked Systems over Erasure Channel with Model Uncertainty. IEEE Trans. Cybern., 1–9. In Press. doi:10.1109/tcyb.2021.3053010
Lami, Y., Lefevre, L., Lagreze, A., and Genon-Catalot, D. (2020). “A Bayesian Approach for Fault Diagnosis in an Irrigation Canal,” in 24th International Conference on System Theory, Control and Computing, Sinaia, Romania, 328–335. doi:10.1109/icstcc50638.2020.9259694
Li, L., Yao, L., Jin, H., and Zhou, J. (2020). Fault Diagnosis and Fault‐tolerant Control Based on Laplace Transform for Nonlinear Networked Control Systems with Random Delay. Int. J. Robust Nonlinear Control. 30, 1223–1239. doi:10.1002/rnc.4823
Li, W., Ding, S. X., and Ding, X. (2009). On Fault Detection Design for Networked Control Systems. IFAC Proc. Volumes 42, 792–797. doi:10.3182/20090630-4-es-2003.00130
Martins, N. C., and Dahleh, M. A. (2008). Feedback Control in the Presence of Noisy Channels: "Bode-Like" Fundamental Limitations of Performance. IEEE Trans. Automat. Contr. 53, 1604–1615. doi:10.1109/tac.2008.929361
Nair, G. N., and Evans, R. J. (2004). Stabilizability of Stochastic Linear Systems with Finite Feedback Data Rates. SIAM J. Control. Optim. 43, 413–436. doi:10.1137/s0363012902402116
Ren, W., Sun, S., Hou, N., and Kang, C. (2018). Event-triggered Non-fragile H∞ Fault Detection for Discrete Time-Delayed Nonlinear Systems with Channel Fadings. J. Franklin Inst. 355, 436–457. doi:10.1016/j.jfranklin.2017.11.015
Rojas, A. J. (2013). “Control over Direct and Feedback Path Signal-To-Noise Ratio Constrained Channels,” in 2013 American Control Conference, Washington, DC, USA, 3183–3188. doi:10.1109/acc.2013.6580320
Rojas, A. J. (2021). “Signal-to-Noise Ratio Feedback Constraint for Non-zero Mean Noise Processes,” in IEEE ICA/ACCA 2021, Santiago, Chile, 1–6. doi:10.1109/icaacca51523.2021.9465244
Rojas, A. J. (2012). Signal-to-noise Ratio Fundamental Limitations in the Discrete-Time Domain. Syst. Control. Lett. 61, 55–61. doi:10.1016/j.sysconle.2011.09.010
Saberi, A., Stoorvogel, A. A., and Sannuti, P. (2007). Filtering Theory: With Applications to Fault Detection, Isolation, and Estimation. Basel: Birkhauser.
Saberi, A., Stoorvogel, A. A., Sannuti, P., and Niemann, H. (2000). Fundamental Problems in Fault Detection and Identification. Int. J. Robust Nonlinear Control. 10, 1209–1236. doi:10.1002/1099-1239(20001215)10:14<1209::aid-rnc524>3.0.co;2-c
Sargolzaei, A., Yazdani, K., Abbaspour, A., Crane, C. D., and Dixon, W. E. (2020). Detection and Mitigation of False Data Injection Attacks in Networked Control Systems. IEEE Trans. Ind. Inf. 16, 4281–4292. doi:10.1109/tii.2019.2952067
Schenk, K., and Lunze, J. (2020). “Fault-Tolerant Task Allocation in Networked Control Systems,” in 28th Mediterranean Conference on Control and Automation, Saint-Raphael, France, 313–318. doi:10.1109/med48518.2020.9182977
Varga, A. (2017). Solving Fault Diagnosis Problems: Linear Synthesis Techniques. Studies in Systems, Decision and Control. Berlin, Germany: Springer.
Wang, B., Zhang, B., and Su, R. (2021). Optimal Tracking Cooperative Control for Cyber-Physical Systems: Dynamic Fault-Tolerant Control and Resilient Management. IEEE Trans. Ind. Inf. 17, 158–167. doi:10.1109/tii.2020.2965538
Wang, T., Gao, H., and Qiu, J. (2016). A Combined Fault-Tolerant and Predictive Control for Network-Based Industrial Processes. IEEE Trans. Ind. Electron. 63, 2529–2536. doi:10.1109/tie.2016.2515073
Ye, Z.-H., Ni, H.-J., Zhang, D., and Xue, H.-x. (2021). Neural Network-Based Fault Detection for Nonlinear Networked Systems with Uncertain Medium Access Constraint: Application to Motor Systems. ISA Trans. 111, 211–222. doi:10.1016/j.isatra.2020.11.003
Keywords: networked control systems, AWN channel, SNR limitation, fault detection, fault identification
Citation: Rojas AJ and Garcés HO (2022) Signal-to-Noise Ratio Based Fault Detection and Identification. Front. Control. Eng. 3:806558. doi: 10.3389/fcteg.2022.806558
Received: 01 November 2021; Accepted: 02 February 2022;
Published: 18 March 2022.
Edited by:
Yong Xu, Guangdong University of Technology, ChinaReviewed by:
Alejandro Maass, The University of Melbourne, AustraliaXiaowei Jiang, China University of Geosciences Wuhan, China
Afzal Sikander, Dr. B. R. Ambedkar National Institute of Technology Jalandhar, India
Copyright © 2022 Rojas and Garcés. This is an open-access article distributed under the terms of the Creative Commons Attribution License (CC BY). The use, distribution or reproduction in other forums is permitted, provided the original author(s) and the copyright owner(s) are credited and that the original publication in this journal is cited, in accordance with accepted academic practice. No use, distribution or reproduction is permitted which does not comply with these terms.
*Correspondence: Alejandro J. Rojas, YXJvamFzbkB1ZGVjLmNs