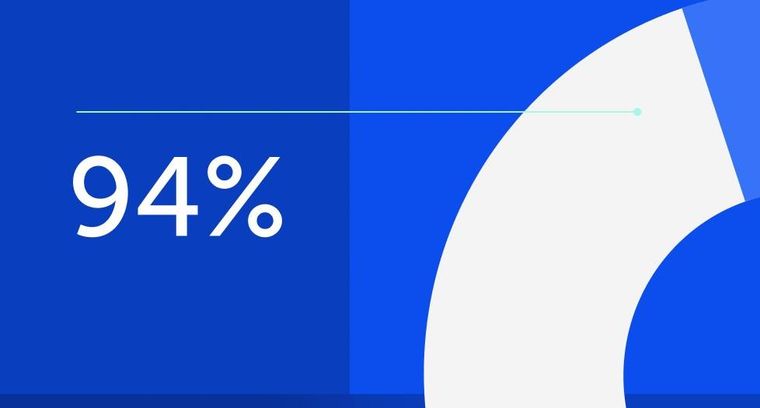
94% of researchers rate our articles as excellent or good
Learn more about the work of our research integrity team to safeguard the quality of each article we publish.
Find out more
REVIEW article
Front. Coat. Dyes Interface Eng., 11 July 2024
Sec. Hard Films and Coatings
Volume 2 - 2024 | https://doi.org/10.3389/frcdi.2024.1426164
This article is part of the Research TopicFrontiers in Coatings, Dyes and Interface Engineering: Inaugural CollectionView all 10 articles
Electric vehicles (EVs) represent a new paradigm for a sustainable transportation future with the potential to offer unparalleled energy security, environmental cleanliness, and economic prosperity for all humanity. However, rapid development and adaptation of this new transportation approach depend on addressing multiple challenges, including the development of new materials and coatings that can meet the more stringent thermal, electrical, and tribological requirements of EV drivetrains. Specifically, the operating conditions of moving mechanical assemblies (i.e., bearings, gears, among others) in EVs differ radically from those found in conventional internal combustion (IC) engines—thus giving rise to notable reliability issues. In particular, as the function of bearings and gear systems shift from mostly load-carrying (in IC engines) to the torque-transferring mode in EVs, durability concerns of these assemblies due to severe deformation, wear, micro-pitting, fatigue, and scuffing may worsen—as electric motors can generate maximum torque at near zero speeds but maximum efficiency at around 90% speed (this is opposite of conventional IC engines, which generate high torques at high speeds). These conflicting requirements require a different set of lubricant-material combinations to circumvent such problems under high loads and low-speed conditions of EVs. Therefore, new materials, coatings, and lubrication strategies need to be developed and implemented for future EVs to become tribologically viable and reliable. Accordingly, EV drivetrains can potentially benefit from advanced functional coatings that have already significantly improved the functionality of moving components of IC engines. The main objective of this article is to draw attention to some of the tribological issues in EVs and how advanced functional coatings can help resolve these issues due to their unique thermal, electrical, mechanical, and tribological properties, ultimately making EVs more durable and reliable.
The protection of moving mechanical surfaces against wear and other types of degradations goes back to the period of early civilization (Rosenkranz et al., 2021). Some of the examples include the uses of naturally abundant products (such as gypsum, clay, tallow, animal fats, olive oil, etc.) on the wheels of carriages, chariots or in the bottom of sleds to move people or heavy stones and statues from one place to another (Ludema, 2001). Since then, the search for and practice of producing hard and self-lubricating materials intensified (especially during the 19th and 20th centuries) and reached a point where they can be produced as thin or thick coatings using physical and chemical vapor deposition (PVD and CVD), plasma spraying, electron beam- and/or laser-based cladding/deposition methods (Figure 1) (Holmberg and Matthews, 2009). In particular, PVD and CVD are well-established for applying highly functional nanostructured and composite thin solid coatings on all kinds of tools and other mechanical components at industrial scales. Thicker coatings produced by electro-plating, sol-gel, and thermal diffusion processes like carburizing, nitriding, and boriding are also extensively used to enhance anti-friction, -wear, and -seize properties of tribological components in manufacturing, aerospace, power generation, and automotive fields (Campbell et al., 1966; Sliney, 1982; Booser, 1983; Erdemir, 2001; Erdemir and Voevodin, 2010; Scharf and Prasad, 2013; Ang and Berndt, 2014; Vazirisereshk et al., 2019). Among others, hard chrome electro- and/or electroless-plating together with thermal and/or plasma-sprayed coatings were widely used to enhance the wear resistance (abrasive, adhesive, erosive, and corrosive wear) of critical machine tools and automotive components for a very long time (Oswald, 1970; Chagnon and Fauchais, 1984; Gérard, 2006; Ang and Berndt, 2014; Berger, 2015; Jacques et al., 2021). The hard chrome plating has now been severely restricted mainly because of the hexavalent chromium (which is highly carcinogenic) used during the plating process.
Figure 1. Summary of the different classes of protective coatings and their corresponding deposition approaches. Modified with permission from (Marian et al., 2021).
Appreciating the importance of surface engineering and coatings in combating friction and wear, researchers and practitioners alike intensified their work on tribological coatings after the 1980s. They developed far more advanced coatings that have markedly enhanced the performance, efficiency, and reliability of all kinds of manufacturing tools and moving mechanical components (Sliney, 1982; Scharf and Prasad, 2013). These more advanced coatings were also suitable to withstand more extreme tribological conditions involving sub-zero or very high temperatures (several hundred Celsius), high vacuum (space), radiation, high-pressure environments (e.g., natural gas or refrigerator compressors), severe contact pressures (several GPa), etc., where conventional coatings could not function (Roberts, 1990; Dugger and Totten, 2017; Zhu et al., 2019; Aouadi et al., 2020). In particular, these coatings afforded impressive property enhancements in machining and manufacturing, while some also sparked the interest of automotive companies. They were already using all kinds of relatively thick plasma-sprayed coatings as barriers to thermal degradation, but since the 2000s, with the cost-effective large-scale manufacturing of low-friction and high wear-resistant coatings (i.e., diamond-like carbon (DLC), chromium nitride, titanium nitride, and a host of other superhard and self-lubricating nanocomposite coatings), the usage of these coatings in engine and drivetrain components increased tremendously and played a major role in further enhancing their performance, efficiency, and durability (Cha and Erdemir, 2015; Vetter, 2015; Tung and Wong, 2021).
The coating field has continued to evolve rapidly during the last three decades, especially with the latest advances in PVD incorporating pulse DC, high-power impulse magnetron sputtering, cathodic arc, and femtosecond pulse laser ablation (Erdemir, 2005; Holmberg and Matthews, 2009; Anders, 2014; Jacques et al., 2021; Al-Asadi and Al-Tameemi, 2022). Coatings produced by these methods have become far more effective and functional in tribological applications, providing superior physical, chemical, and mechanical properties. As a result of these advances, machine tools and other industrial components now last much longer, consume less energy, and thus ensure a cleaner environment. Undoubtedly, the coatings field will continue to expand in the coming years and potentially play a crucial role in advancing many engineering fields. Coatings have already been essential to extend and improve the efficiency and reliability of conventional vehicles based on IC engines (Vetter et al., 2005; Cha and Erdemir, 2015; Tung and Wong, 2021). They can equally play pivotal roles in the advancement of electric vehicles (EVs), enabling unparalleled reliability (lasting nearly for the lifetime of such vehicles) and improved efficiency (through ultra-low friction), thus enabling an environmentally friendly, and efficient form of transportation in coming decades.
This review article will mainly concentrate on the potential uses of coatings in rapidly expanding manufacturing and the use of EVs in general and their moving mechanical components in particular. These vehicles have lately become popular and are expected to reach more than 60 million sold by 2040 (Muratori et al., 2021). We will particularly emphasize the potential benefits of functional coatings in terms of tribology, electrical and thermal management issues, reliability, and environmental benefits. In the following section, we will describe how state-of-the-art coatings can potentially increase the functionality of various EV components (like bearings, gears, seals, etc.) and give some examples where coatings already show great improvements in wear resistance, especially under electrified contact conditions.
As with conventional IC engine vehicles, combating wear, corrosion, fatigue, scuffing, and fretting-related failures is very important in EVs. Increasingly harsher or more extreme operational conditions in EVs (especially for their drivetrains involving high torque, high speed, and elevated temperatures) make using functional coatings ideal for achieving a smooth, safe, and long-lasting operation. In addition to these tribological challenges, a new set of thermal, electrical, and material-oriented challenges exist that require the use of functional coatings. Current advances related to the development of multi-component and hence functional coatings can be useful for these more challenging applications. Specifically, they can simultaneously meet most tribological, thermal, and electrical challenges, making such vehicles more durable and reliable. For instance, to help with the electrified conditions creating charge breakouts and accelerating degradation of materials, coatings could be tailor-made of highly conductive or insulating materials to eliminate drivetrain failures associated with stray electricity and electrical discharges at rolling/sliding interfaces of bearings and gears (Farfan-Cabrera, 2019). Furthermore, through the design and incorporation of multi-component and functional nanocomposite coatings, other key features, including lubricity, thermal conductivity, catalytic reactivity, and self-healing properties, can be improved in a combinatorial manner.
In EVs, electric motors (such as brushless DC motors, synchronous brushed motors, induction motors, synchronous permanent-magnet motors, reluctance motors, etc.), power electronics (AC/DC and DC/DC converters, etc.), drivetrains (single-speed or two-speed gear transmissions), and batteries can generate huge amounts of heat (Kim et al., 2019). Switching from a 400-V to 800V architecture may also bring additional challenges both thermally and electrically. The proper selection and use of highly thermally and electrically conducting coatings could be very useful in alleviating such challenges. For example, in a multi-target sputtering or arc-PVD system, these coatings can even be prepared by incorporating highly thermally conductive metals (such as Ag, Cu) into nanocomposite coatings or dopants to enhance the resulting thermal conductivity of the coatings and hence prevent thermally induced degradations. The inclusion of catalytic metals, such as Cu, Ni, Co, among others, in the composite coating, besides improvements in thermal and electrical properties, further promotes their anti-friction and -wear properties through the formation of carbon-based tribofilms from lubricating oils (Berman and Erdemir, 2021). Alternatively, nano-powders of such highly heat-conducting metals and metal oxides can be used to produce colloidal nanofluids, thus helping to alleviate the deleterious effects of high heat (Goharshadi et al., 2013; Lee et al., 2019).
Concerning EVs, a variety of self-lubricating coatings exist that can also help with friction and wear control (Berman et al., 2024). Some of these may consist of layered transition-metal dichalcogenide (like MoS2, WS2, and NbS2) as self-lubricating materials (Scharf and Prasad, 2013; Miyoshi, 2019; Vazirisereshk et al., 2019), while others may be prepared using graphite, hexagonal boron nitride (h-BN), as well as other 2D materials like graphene, black phosphorous, MXenes, etc. (Berman et al., 2015; Berman et al., 2018a; Berman et al., 2019; Zhai and Zhou, 2019; Gao et al., 2021; Ayyagari et al., 2022; Gao et al., 2023). One of the major challenges with these low-friction materials relates to substrate adhesion, the uniformity of distribution, and their thickness across large areas on coated surfaces. Since they tend to be soft (exceptions may relate to the family of MXenes due to their inherent wear resistance), their thickness should be limited and they may wear out over time, thus losing their effectiveness and even inducing catastrophic wear. The same argument applies to coatings made of pure metallic solid lubricants (i.e., In, Ag, Pb, Sn, Bi, Sb, etc.). Specifically, these metals wear out quickly due to their soft and highly deformable natures (although their high electrical conductivity could be a desirable property as this property alone has been exploited very successfully in rotating anode tube bearings of CT scans) (Danyluk and Dhingra, 2012; Reeves et al., 2013).
In the past, 0D nano-onions, nano-diamonds, and amorphous carbon nano-spheres; 1D nano-tubes, -fibers, -rods, and -whiskers; and 2D graphene, h-BN, metal dichalcogenides, and MXenes, as well as larger nano-scale particles with various 3D architectures were all shown to induce superior friction and wear properties. Some of these were also used as nano-colloidal lubrication additives or self-lubricating materials and coatings (Berman et al., 2013a; Berman et al., 2013b; Berman et al., 2014a; Berman et al., 2018b; Ayyagari et al., 2022). Prime examples are the uses of nano-fullerenes or -flakes of transition metal dichalcogenides (such as MoS2 and WS2) and carbon nano-onions, nano-tubes, graphene, nano-diamond particles to combat friction and wear as well as anti-scuffing agents under severe boundary conditions (Tenne, 2006; Matsumoto et al., 2012). Even though still expensive, coatings based on graphene and other 2D materials (e.g., MoS2, h-BN, MXenes, black phosphorous, etc.) can also be considered to properly control the thermal, electrical, and tribological properties of EV drivetrains. Nano-colloids in a carrier oil or fluid can certainly enhance the resistance to heat-related degradations while reducing friction and wear. The relatively high cost of these nanomaterials prevented their large-scale use in conventional IC vehicles.
With the current advancements related to the design of robust and multi-target deposition systems (both PVD and CVD), it became possible to easily create multi-functional coatings and/or architectures. By strategically selecting the coating ingredients, one may also trigger high-entropy alloying effects, thus enabling additional functionalities. Specifically, each discreet phase in composite structure alone and in combination with other phases provides a range of beneficial functionalities besides low friction and wear (Murthy et al., 2023; Kumar, 2023; Macknojia et al., 2024). Luckily, these coating systems with many targets are now more cost-effectively available from multiple coating companies and have become affordable and upscalable lately. In the past, CrN and DLC coatings were used the most in IC engines (Vetter et al., 2005), but it is possible that they can also be tailored to deliver coated drivetrain components to be used in EVs.
Many other coating types or compositions have been developed and tested for combatting friction and wear under severe operating conditions. Chief among them are CrN, TiN, ZrN, and various self-lubricating and nanocomposite coatings. Compared to DLC, these coatings suffered from a few shortcomings. For instance, most of them could not form protective boundary films through tribochemical reactions with anti-friction and -wear oil additives and hence could not help reduce friction as DLC coatings were able to (Mehran et al., 2018). In the case of composite solid lubricant coatings (i.e., MoS2), they were found to be vulnerable to environmental degradation and aging. If the ambient temperature is high, they would also degrade or oxidize, hence losing their effectiveness. For example, at high relative humidities, the friction coefficients of MoS2 substantially increase, and their wear lives become considerably short (Winer, 1967; Macknojia et al., 2023; Cairns et al., 2023). Once the first signs of wear occur, low-friction materials are difficult to re-apply or replenish.
During the last century, several kinds of other solid lubricants (i.e., waxes, manganese phosphate, polytetrafluoroethylene (PTFE), low and high-density polyethylenes, PEEK, etc.) were developed and used to control friction and wear (Kurdi and Chang, 2018). In EVs, their highly dielectric nature and low friction could make them appealing. However, due to their soft nature, they may wear out very quickly, which limits their overall applicability and durability. Among other solid lubricant coatings, if it were possible to deposit, polycrystalline diamond coatings could be desirable since they can resist wear, dissipate heat, and provide high dielectric properties to tribological surfaces. Since most EV drivetrain components are made of bearing or gear quality steels, the deposition of polycrystalline diamond coatings on these substrates is rather difficult, if not impossible. The only other solid lubricant coating that looks promising relates to diamond-like carbon (DLC), which resembles the amorphous form of carbon, as it can provide low friction and wear, and ensure excellent insulation against electrical discharges at the contact interfaces.
Combatting friction and wear has come a long way during the last century. Lately, low-friction materials and coatings have significantly influenced such advances. With the emergence of EVs in recent years, a new opportunity exists for coatings to play a major role in the safe, smooth, and long-lasting operation of these vehicles’ drivetrains. In the following sections, some solid lubricant coatings will be discussed in more detail, along with their performance characteristics under electrified conditions. In addition to the relatively thin PVD and CVD coatings, a variety of nanomaterials with 0 to 3D dimensions have been applied as novel self-lubricating materials on moving surfaces (Zhmud and Pasalskiy, 2013; Berman et al., 2014b; Chen et al., 2019; Manu et al., 2021; Marian et al., 2021; Martin and Ohmae, 2022; Marian et al., 2022; Wang et al., 2022; Shirani et al., 2023a). In short, we will highlight some potential applications of these coatings in EVs. Among others, DLC coatings have now been widely used in IC engines to achieve higher efficiency and reliability in numerous components. Hence, a particular emphasis will be placed on DLC and other promising coatings that can afford superior performance under severe application conditions of EV drivetrains. Farfan-Cabrera et al. (Farfan-Cabrera et al., 2023) demonstrated the effectiveness of hydrogenated-DLC (H-DLC) in withstanding severe electrical environments in lubricated contacts in contrast to AISI 52100 bearing steel, see Figure 2. H-DLC generated lower CoF and negligible wear for both unelectrified and electrified conditions compared to the bearing steel pair.
Figure 2. A comparison of CoF and wear obatined for bearing steel, H-DLC and H-free DLC pairs under unelectrified and electrified lubricated conditions: (A) coefficient of friction; (B) wear volume of ball samples. Modified with permission from (Farfan-Cabrera et al., 2023).
Most tribological coatings are designed to control friction and wear of interacting surfaces in relative motion. For friction control, various self-lubricating coatings (i.e., transition-metal dichalcogenides, DLCs, soft metals, etc.) have been developed and used extensively in the past (Scharf and Prasad, 2013). Hard coatings made of transition metal nitrides, carbides, and borides are preferred for wear control, especially in metal-cutting and -forming operations. Some of these can also enable low friction, as in the case of DLC coatings. All in all, superior friction and wear properties of tribological coatings can benefit the performance, efficiency, and reliability of drivetrain components of EVs. In addition, they can also provide superior thermal, electrical, and oxidational properties, which will be useful in addressing thermal management, electrical discharge, corrosion, and oxidational challenges.
In EV drivetrains, the great majority of relative motion is in the form of pure rolling (in the case of ball and roller bearings) and/or mostly rolling and sliding (in the case of gears) (Farfan-Cabrera, 2019; Hemanth et al., 2021). Solid lubricant coatings like MoS2 can benefit these applications by providing easy shear to such contact interfaces to minimize energy losses due to high-torque and high-speed operational conditions of bearings and gears. Likewise, DLC coatings can reduce friction and wear, thus increasing the efficiency and reliability of drivetrain components of EVs. They have already been used in ICE vehicles to control friction and wear under severe contact conditions of valve lifters and fuel injector systems (Gangopadhyay, 2015; Kano, 2015). These coatings may also work equally well in EVs by providing low friction and wear combined with a high dielectric constant or insulating properties to minimize the deleterious effects of electrical discharges or arcing at interacting surfaces. It is important to remember that if DLC or other hard coatings fail or fracture due to severe cyclic loading, they may trigger much-accelerated wear due to a third-body wear mechanism.
On the other hand, metal-based solid lubricant coatings (In, Ag, Pb, Sn, Au, etc.) can potentially enhance the electrical conductivity of the contact interface to provide an easy path for electrical discharge, thus avoiding or reducing surface damage. Their easy shear character can help to tailor friction and wear as needed. Some of these coatings, like Ag, are routinely used in rotating anode X-ray tube bearings of CT scanners to provide excellent lubricity, dissipate heat and discharge electricity across the rolling surfaces at high speeds (Danyluk and Dhingra, 2015). As already reported, these metallic solid lubricants have multiple slip systems, which tend to work even under severe shear conditions, thus inducing excellent wear resistance (Donnet and Erdemir, 2004).
As with most other tribomaterials, most existing tribological coatings may also interact with the chemical species in their surrounding. For instance, self-lubricating coatings made from transition metals and DLCs interact with oxygen and humidity in the environment (Kim et al., 2006; Eryilmaz and Erdemir, 2008; Domínguez-Meister et al., 2019; Vazirisereshk et al., 2019; Babuska et al., 2022). Such an interaction gives rise to rapid degradation of these coatings and diminishes their effectiveness in combatting friction and wear. Coatings made of transition metal dichalcogenides work best in dry, vacuum, or non-reactive environments. Depending on the type, DLC coatings may or may not work in humid or dry test environments. In reality, it has been demonstrated that highly hydrogenated DLC coatings work best in dry and inert test environments, while hydrogen-free DLCs are better applicable in humid environments (Erdemir and Donnet, 2006).
Concerning their use in EV drivetrains, one has to consider creating environments where the mentioned coatings will work best. Since most gears and bearings in the drivetrains of EVs operate in an enclosed or sealed box, it might be relatively easy to create the type of environment in advance and occasionally replenish the type of gas most desirable for these components’ functionality. To reduce the environmental vulnerability of these coatings, one can also create composite coating architectures that can provide a chameleon effect (Muratore and Voevodin, 2009; Aouadi et al., 2020; Shirani et al., 2020); this implies that the functionality of the composite coating does not degrade or change much with changing environmental conditions. Researchers have already demonstrated this for some composite coatings intended for space applications. Through such hybridization, it became possible to control or tune the electrical and thermal properties of coatings. The thermal and electrical properties of transition metal and DLC-based coatings can be fine-tuned by incorporating highly electrically and thermally conducting metals like Ag and Cu.
Some of the tribological coatings have already been tested under different tribological conditions (lubrication regiomes) using various types of oil-based lubricants in past years. In general, it was found that the friction and wear performance of DLC coatings is sensitive to the chemistry of the lubricating oils and additives. For instance, the presence of polar additives (glycerol and other organic friction modifiers) was shown to reduce friction and wear markedly under severe boundary lubrication for hydrogen-free DLC coatings. However, hydrogenated DLC coatings showed much higher friction and relatively poor wear performance under similar sliding conditions (Kano, 2006). Initial studies on graphene and other 2D materials demonstrated that they have a strong sensitivity to the chemical nature of test environments or media (Ayyagari et al., 2022). As with most solid lubricant coatings, the thermal and electrical properties of these 2D materials also strongly influence the resulting functionalities when employed on contact interfaces of driveline components of EVs. For example, due to its very high thermal and electrical conductivity combined with its superlubric behavior under certain conditions (Berman et al., 2014c; Hu et al., 2018; Lee et al., 2018), graphene and MXenes can benefit the tribological performance of gears and bearings in EV drivetrains.
Overall, the presence or absence of certain chemical species in operating environments or additives in lubricants can notably impact the functionality and durability of tribological coatings for EV applications. Furthermore, the extent of contact pressure, speed, and temperature of interfaces of driveline components in EVs can become high, which also may negatively affect their durability. In particular, if the temperature rises notably, the longer-term functionality of DLC and transition-metal dichalcogenide-based solid lubricant coatings may be compromised as they lose effectiveness at elevated temperatures. In this regard, the durability or functionality of hydrogenated DLCs dramatically deteriorates at elevated temperatures as their disordered or amorphous structures tend to crumble with the loss of excess hydrogen in their structures, making them wear out quickly due to reduced structural integrity (Erdemir and Fenske, 1996; Zeng et al., 2015). In contrast, hydrogen-free DLC coatings can withstand higher temperatures, which implies enhanced wear resistance at elevated temperatures. To moderate these problems and/or further improve the thermal stability of DLCs, nano-scale alloying or doping with certain elements, such as Si, B, and N (Rajak et al., 2021), appears to be a promising research avenue. Certain metal-doped DLCs like W, Cr, and Ti can also provide additional benefits besides lubrication in terms of superior thermal and electrical properties that are also desired in electrified driveline systems (Figure 3).
Most coatings are employed on interacting tribo-surfaces to combat friction and wear. Mechanistically, when applied on a sliding surface, soft solid lubricant coatings often deform or shear easily to form a transfer layer on both rubbing surfaces. During relative motion, the transfer layer shears easily to accommodate velocity and involves energy-dissipating processes (Singer et al., 2003; Singer and Pollock, 2012). A soft solid lubricant coating like MoS2 shears through an interlayer shear mechanism, while the most dominant shear mechanism of soft metallic coatings can be attributed to the flow of the soft film followed by a quick recovery or recrystallization, thus avoiding work hardening. In contrast, the underlying shear mechanism of hard DLC coatings connects to slip events right at the contact interface.
Under electrified conditions, the governing tribological mechanisms may change depending on the type of coatings and lubricant being used. If the coating is made out of a transition metal dichalcogenide, like MoS2, the vulnerability to enhanced oxidation and rapid degradation may occur. Electric currents passing through may accelerate oxidation or corrosion processes thus inducing and/or accelerating failure. Hence, if the lubricant possesses high conductivity and reduced breakdown voltage, the electrical discharges occurring at the tribological interfaces will be less severe (Berman et al., 2024). Moreover, Using an inert environment is expected to slow down coating degradation due to oxidation. The passage of current through these coatings is another potential problem. Specifically, current discharge at the contact interface may cause ohmic or resistive heating (because of the semi-conductive nature of such coatings), which, in turn, induces chemical and structural alteration, thus impairing the overall performance or durability of the coating and lubricant system. Doping such coatings with Ag, Cu, and Au can help resolve these problems, which has already been successfully demonstrated for MoS2 coatings applied in space applications.
In the case of highly electrically conducting coatings like Ag, In, Sb, etc., the passage of electricity through contact interfaces may not create notable problems. Some of these coatings are already used in electrical contacts to enable high electrical conductivity, while their easy shear properties can ensure good solid lubrication properties. However, due to their thin natures, their lifetimes and beneficial effects may be limited. In a best-case scenario, it will be most desirable to blend or introduce such metals into hard nitride and carbide coatings in a nanocomposite architecture, which provides good electrical conductivity and good shear properties to achieve low friction and wear simultaneously.
Regarding DLC coatings, their performance largely depends on the composition. Some of the best-performing DLC coatings, such as tetragonal amorphous carbon (ta-Cs), are produced by cathodic arc deposition (Kano, 2014; Vetter, 2015). Due to their extreme hardness (approaching well over 50 GPa), they provide excellent protection against wear. They are also thermally more durable and, hence, could be used in piston rings to reduce friction and wear. However, under electrified conditions, these coatings may experience major problems. Specifically, their predominantly amorphous microstructures may contain some pockets of graphitic micro-droplets or particles with high electrical conductivity. Most of these are scattered across the top surface but some may extend from the surface to the underlying substrates. When these DLC (H-free DLC) coatings are used under electrified conditions, these particles act as short circuits for electricity to pass through, and in the long run, such a discharge destroys the entire coating, as shown in Figure 4 (Farfan-Cabrera et al., 2023). Fragmented or chipped ta-C films tend to accelerate wear due to a third-body wear process (Farfan-Cabrera et al., 2023). Conversely, if the DLC (H-DLC) film is produced by plasma-enhanced CVD or sputtering, these failures are unlikely to occur due to the dense and uniform structure preventing current leakages or passage from the surface to the substrate material generating excessive wear and removal of the coating. A comparison of the CoF and wear generated by unelectrified and electrified pin-on-disc tests for H-DLC and H-free DLC is shown in Figure 2. Consequently, by designing and selecting the most appropriate solid lubricant coatings for the electrified contact interfaces in EV drivetrains, significant improvements in tribological performance are feasible.
Figure 4. Comparison of the wear tracks produced in hydrogen-free DLC under (A) unelectrified and (B) electrified conditions. Adapted with permission from (Farfan-Cabrera et al., 2023).
For all coatings discussed above, one must also consider the effects induced by the test environment, temperature, and other extrinsic factors. As briefly mentioned, the performance of many tribological coatings is also controlled by environmental species like water and oxygen. Again, under electrified conditions, they can accelerate oxidation and/or corrosion. In the case of DLCs, these species can also interfere with friction and wear. Concerning MoS2 coatings, humidity is detrimental to tribological performance as it accelerates the oxidation of the coating, thus limiting its lifetime. Adverse environmental effects may be further exacerbated if the ambient temperature is high, as most solid lubricants have a limited temperature range. Metallic coatings may provide better tribological properties due to reduced environmental and thermal sensitivities, while their shear properties may even increase at elevated temperatures, thus enabling better lubricity (Erdemir, 2001). Multiple slip systems available in their crystalline structures can ensure much better shear due to the lack of work-hardening and rapid recovery. When some of these metals are incorporated into transition metal nitrides and carbides or other metal-based matrices as nano-scale phases, they can trigger catalytic effects (Erdemir et al., 2016; Berman and Erdemir, 2021; Shirani et al., 2021; Shirani et al., 2022; Al Sulaimi et al., 2023; Shirani et al., 2023b; Jacques et al., 2023). Specifically, they crack long-chain hydrocarbon molecules of lubricating oils during rubbing to produce a self-replenishing carbon-rich tribolayer at the contact interface, ensuring stable friction and low wear (Figure 5).
Figure 5. Summary of tribocatalytic nanocarbon film generation concept for ultralow friction and wear. Solid, liquid, or gaseous carbon sources or precursors on the left are introduced to the catalytically active interface (in the middle), subsequently, these precursors are converted to self-lubricating solid carbon forms on the right. Reproduced with permission from (Berman and Erdemir, 2021).
Strong adhesion, uniformity of coating thickness, and structural density are some of the key requirements of all tribological coatings. Due to the much severe operating conditions of EVs, such requirements will be far more important. Fortunately, there have been major advances in PVD and CVD coating processes in recent years and hence, they can reliably meet these requirements by providing strong bonding/adhesion, uniform thickness, and coating composition across the coated surfaces (even on curved or odd-shaped surfaces of bearings and gears). Most of the highly functional tribological coatings for severe conditions (such as metal-cutting and -forming) are now produced by these methods (Deng et al., 2020; Alhafian et al., 2021; Al-Asadi and Al-Tameemi, 2022). They can ensure excellent coating-substrate adhesion and provide structurally dense and chemically stoichiometric coatings on most substrate materials. They can also induce a uniform film thickness, dense structural morphologies, desirable surface roughness, and chemical stoichiometry, which all play a crucial role in the tribological performance of the resulting coatings. All these coating attributes are essential for their functionality under electrified conditions.
Among the major PVD approaches, DC or RF magnetron sputtering, ion-plating, cathodic arc PVD, and pulse laser deposition (PLD) are used to deposit many types of solid lubricant coatings for tribological applications. Coatings produced by conventional PVD and CVD methods occasionally have some structural and chemical issues, including coatings with an open columnar morphology leading to an easy fracture along the column boundaries, especially under severe loading conditions (Spalvins, 1987). Furthermore, coatings with open columnar structures wore out faster and were vulnerable to environmental degradation.
To alleviate these problems, researchers have developed novel methods such as pulse DC magnetron sputtering, cathodic arc-PVD, PLD, and high-power impulse magnetron sputtering (HIPIMS) (Anders, 2008; Gudmundsson et al., 2012) to densify and/or nanostructure the film morphology (Berman et al., 2014a). The tribological coatings produced by these methods cannot be deformed or fractured along their grain boundaries or removed easily from the surface due to interfacial failure or delamination, even under severe tribological conditions. Due to these notable structural, mechanical, and adhesive properties, modern tribological coatings of today could benefit the performance, reliability, and efficiency of EV drivetrains. Advanced deposition approaches may also help to further improve the underlying adhesion, which can notably contribute towards enhanced durability. Due to the highly energetic nature of their plasmas, the film microstructure consists of densely packed nano-scale grains and induces a smooth surface finish, which is also desirable to establish and maintain superior tribological performance.
Among these methods, pulse DC, arc-PVD and HIPIMS magnetron sputtering are among the most widely used commercial methods at present. In particular, HIPIMS can provide a high-rate sputtering capability and a highly ionized and energetic plasma, allowing for the generation of very thin or thick coatings in monolithic or nanocomposite forms. Using multiple targets, one can produce composite coatings made of nano-to-micro scale layers of hard/hard, hard/soft, and soft/soft phases, providing unique multifunctionality (Hovsepian et al., 2004; Erdemir et al., 2005). Coatings may also be produced in a nanocomposite form, in which various nano-scale phases are combined or mixed uniformly across the coating thickness (Sánchez-López and Fernández, 2008). Consequently, the generation of catalytically active nanocomposite coatings is rather straightforward. These coatings can ensure a wide range of multifunctionality for the bearings or gears in EV drivetrains, in addition to their beneficial catalytic activity.
Cathodic-arc PVD is widely used to deposit tribological coatings, especially ta-C coatings. It uses high-current/low-voltage power sources to create arcing on the target surface under the influence of overlapping electrical and magnetic fields. Extreme heating ejects atoms and/or clusters from the surface in the form of highly ionized species, which subsequently deposit on the negatively biased substrates (Sanders and Anders, 2000; Anders, 2008; Martin, 2009). Some of the major drawbacks of cathodic-arc PVD relate to the generation and transfer of micro/macro-droplets from the surface of the target material to the surface of the substrate material; this often leads to a rough surface finish and both structurally and compositionally non-uniform coating microstructure (Panjan et al., 2020). These coatings may not be acceptable for EV applications, as initial tests under electrified conditions confirmed that micro-droplets in DLC films caused short circuits and eventually rendered them useless. To prevent the problems associated with micro-droplets, researchers developed a range of filtering techniques that were effective in preventing most of the larger droplets from reaching the substrate surface, while smaller ones were still able to escape and cause a non-uniform microstructure and chemistry. Besides the arc-PVD and HIPIMS, PLD is also available for the production of tribological coatings (Zabinski et al., 1994). However, this method suffers from problems connecting to scalability, uncontrollable surface roughness, and substrate selection. It is mostly used as a research tool at present. Due to line-of-sight issues, PLD may not be suitable for the curved surfaces of bearings and gears used in EVs.
As for CVD methods, the deposition of certain solid lubricant coatings is possible. Plasma-activated or -enhanced CVD has been around for a long time and is widely used to deposit DLC films (Erdemir and Donnet, 2006; Erdemir and Martin, 2018). There are also a host of other types of CVD methods, including hot-filament or microwave CVD (mostly used for the deposition of diamond coatings), metal-organic CVD, and atomic layer deposition for very thin layers or clusters (Bachmann and van Enckevort, 1992; Scharf et al., 2009; Doll et al., 2010). If it were possible to produce diamond coatings on drivetrain components of EVs, they would certainly be highly desirable. However, these coatings cannot be homogenously deposited on ferrous metals such as steel bearings and gears, hence, they will not be applicable to EVs. The production of these coatings also requires high temperatures, i.e., 1000C. Electron-beam deposition, plasma spraying, and high-velocity oxyfuel methods are also available for the deposition of thicker coatings, whose potential for EV applications is unknown but might be worth exploring.
In general, the aforementioned PVD and CVD methods hold great promise in producing highly functional tribological coatings for EV drivetrain applications. They can also allow nano-scale alloying or the creation of nanocomposite with a multi-functional character that can enhance the overall tribological performance. Both methods can produce DLC coatings, which have already been used in multiple industrial applications, including traditional IC engines (Sánchez-López and Fernández, 2008). In particular, nano-alloyed or composite coatings were shown to be durable in tribological applications (Polcar et al., 2012). Cathodic-arc and HIPIMS can create coatings with excellent interfacial properties (smooth interfaces and good adhesion) as well as highly desirable film morphology and chemistry. These more advanced methods are available for large-scale productions at reasonable costs. They have multiple targets, from which the same or different types of metals can be sputtered at the same time or in sequence to achieve multi-layered or nanocomposite coatings easily. These methods allow for very close control of the resulting structural morphology and density, surface topography, and chemical stoichiometry of the resulting coatings, leading to an increased wear life and reliability in EV applications.
In the foregoing, we attempted to provide a comprehensive overview of tribological coatings that may be useful in enhancing the tribological performance of EV drivetrains. We can summarize the key points raised as follows.
1. The coating field has emerged over the past several decades and there now exist many types or classes of thin, thick, soft, and hard coatings that can be considered for friction and wear control in EVs.
2. Softer solid lubricant coatings (e.g., MoS2, Ag, etc.) could be beneficial for enhancing lubrication, especially under high-torque conditions.
3. Hard coatings (e.g., DLCs, nanocomposite metal nitride, carbide coatings, etc.) may be used to achieve longer wear lives under high-stress rolling/sliding conditions.
4. Using coatings, the electrical and thermal conductivity of contact interfaces may also be optimized, and hence, the damage due to electrical discharges or arcing may be avoided.
Overall, compared to traditional internal combustion-engine-based vehicles, EVs present far more stringent operating conditions tribologically, thermally, and electrically. Therefore, the proper design and application of multi-functional tribological coatings in EV applications may lead to superior performance, reliability, and efficiency in future EVs.
Some of the future perspectives on the uses of coatings for EV applications are.
1. Due to the presence of stray electricity floating through the system, some coatings (e.g., highly electrically conducting metals like Ag, Cu, etc.) may suffer from accelerated oxidation and/or corrosion as well as thermal cycling. Accordingly, such coatings must be optimized in their thickness, structural nature, and composition (perhaps considering their alloy forms).
2. Oxygen and moisture in the air may degrade the performance of soft and hard tribological coatings. Hence, nano-scale doping or alloying may be needed to reduce their environmental sensitivity. Alternatively, the operating environment may be changed to an inert gas, such as N2 to decrease environmental degradations.
3. Alternatively, one can consider adaptive or chameleon-type coatings with strategically selected ingredients affording greater environmental compatibility besides multifunctionality and good lubricity.
4. Due to high torque and contact pressures in EV drivetrains, coatings without strong bonding can rapidly delaminate or wear out and thus become useless. Hence strong coating-to-substrate adhesion is imperative for long service lives.
5. Modern PVD and CVD methods with HIPIMS, pulsed DC, and cathodic arc can provide a very strong bonding between coatings and driveline components. Such more advanced methods should be used to produce the coatings on EV components.
In conclusion, there now exist a variety of tribological coatings used in all kinds of industrial applications, including engines. Under the very harsh operating conditions of EVs involving a wide range of electrical, thermal, and tribological issues, coatings can equally make a positive difference by providing superior performance, efficiency, and durability.
SL: Data curation, Investigation, Methodology, Writing–original draft. LF-C: Conceptualization, Data curation, Formal Analysis, Investigation, Methodology, Writing–original draft, Writing–review and editing. DB: Conceptualization, Data curation, Writing–original draft, Writing–review and editing. AR: Conceptualization, Data curation, Writing–original draft, Writing–review and editing. AE: Conceptualization, Data curation, Investigation, Project administration, Supervision, Writing–original draft, Writing–review and editing.
The author(s) declare that financial support was received for the research, authorship, and/or publication of this article. The National Science Foundation (NSF) (Award No. 2323452). The Texas A&M Engineering Experiment Station startup funds and the Governor’s University Research Initiative. Tecnologico de Monterrey within the Challenge-based research project IJST070-23EG68001 (call 2023). The financial support of ANID-Chile within the projects Fondecyt Regular 1220331 and Fondequip EQM190057.
The authors declare that the research was conducted in the absence of any commercial or financial relationships that could be construed as a potential conflict of interest.
All claims expressed in this article are solely those of the authors and do not necessarily represent those of their affiliated organizations, or those of the publisher, the editors and the reviewers. Any product that may be evaluated in this article, or claim that may be made by its manufacturer, is not guaranteed or endorsed by the publisher.
Al-Asadi, M. M., and Al-Tameemi, H. A. (2022). A review of tribological properties and deposition methods for selected hard protective coatings. Tribol. Int. 176, 107919. doi:10.1016/j.triboint.2022.107919
Alhafian, M., Chemin, J., Fleming, Y., Bourgeois, L., Penoy, M., Useldinger, R., et al. (2021). Comparison on the structural, mechanical and tribological properties of TiAlN coatings deposited by HiPIMS and Cathodic Arc Evaporation. Surf. Coatings Technol. 423, 127529. doi:10.1016/j.surfcoat.2021.127529
Al Sulaimi, R., Eskandari, M., Shirani, A., Macknojia, A. Z., Miller, W., and Berman, D. (2023). Effect of Cu and Ni inclusion on tribological performance of tribocatalytically active coatings in hydrocarbon environments. Coatings 14, 61. doi:10.3390/coatings14010061
Anders, A. (2014). A review comparing cathodic arcs and high power impulse magnetron sputtering (HiPIMS). Surf. Coatings Technol. 257, 308–325. doi:10.1016/j.surfcoat.2014.08.043
Ang, A. S. M., and Berndt, C. C. (2014). A review of testing methods for thermal spray coatings. Int. Mater. Rev. 59, 179–223. doi:10.1179/1743280414y.0000000029
Aouadi, S., Gu, J., and Berman, D. (2020). Self-healing ceramic coatings that operate in extreme environments: a review. J. Vac. Sci. Technol. A Vac. Surfaces, Films 38. doi:10.1116/6.0000350
Ayyagari, A., Alam, K. I., Berman, D., and Erdemir, A. (2022). Progress in superlubricity across different media and material systems - a review. Front. Mech. Eng. 8. doi:10.3389/fmech.2022.908497
Babuska, T. F., Curry, J. F., Dugger, M. T., Lu, P., Xin, Y., Klueter, S., et al. (2022). Role of environment on the shear-induced structural evolution of MoS2 and impact on oxidation and tribological properties for space applications. ACS Appl. Mater. Interfaces 14, 13914–13924. doi:10.1021/acsami.1c24931
Bachmann, P. K., and van Enckevort, W. (1992). Diamond deposition technologies. Diam. Relat. Mater. 1, 1021–1034. doi:10.1016/0925-9635(92)90073-w
Berger, L.-M. (2015). Application of hardmetals as thermal spray coatings. Int. J. Refract. Metals Hard Mater. 49, 350–364. doi:10.1016/j.ijrmhm.2014.09.029
Berman, D., Deshmukh, S. A., Sankaranarayanan, S. K., Erdemir, A., and Sumant, A. V. (2014a). Extraordinary macroscale wear resistance of one atom thick graphene layer. Adv. Funct. Mater. 24, 6640–6646. doi:10.1002/adfm.201401755
Berman, D., Deshmukh, S. A., Sankaranarayanan, S. K., Erdemir, A., and Sumant, A. V. (2015). Macroscale superlubricity enabled by graphene nanoscroll formation. Science 348, 1118–1122. doi:10.1126/science.1262024
Berman, D., and Erdemir, A. (2021). Achieving ultralow friction and wear by tribocatalysis: enabled by in-operando formation of nanocarbon films. ACS Nano 15, 18865–18879. doi:10.1021/acsnano.1c08170
Berman, D., Erdemir, A., and Sumant, A. V. (2013a). Few layer graphene to reduce wear and friction on sliding steel surfaces. Carbon 54, 454–459. doi:10.1016/j.carbon.2012.11.061
Berman, D., Erdemir, A., and Sumant, A. V. (2013b). Reduced wear and friction enabled by graphene layers on sliding steel surfaces in dry nitrogen. Carbon 59, 167–175. doi:10.1016/j.carbon.2013.03.006
Berman, D., Erdemir, A., and Sumant, A. V. (2014b). Graphene: a new emerging lubricant. Mater. today 17, 31–42. doi:10.1016/j.mattod.2013.12.003
Berman, D., Erdemir, A., and Sumant, A. V. (2014c). Graphene as a protective coating and superior lubricant for electrical contacts. Appl. Phys. Lett. 105. doi:10.1063/1.4903933
Berman, D., Erdemir, A., and Sumant, A. V. (2018b). Approaches for achieving superlubricity in two-dimensional materials. ACS Nano 12, 2122–2137. doi:10.1021/acsnano.7b09046
Berman, D., Farfan-Cabrera, L. I., Rosenkranz, A., and Erdemir, A. (2024). 2D materials for durable and sustainable electric vehicles. Nat. Rev. Mater. in print. doi:10.1038/s41578-024-00680-3
Berman, D., Mutyala, K., Srinivasan, S., Sankaranarayanan, S., Erdemir, A., Shevchenko, E., et al. (2019). Iron-nanoparticle driven tribochemistry leading to superlubric sliding interfaces. Adv. Mater. Interfaces 6. doi:10.1002/admi.201901416
Berman, D., Narayanan, B., Cherukara, M. J., Sankaranarayanan, S. K., Erdemir, A., Zinovev, A., et al. (2018a). Operando tribochemical formation of onion-like-carbon leads to macroscale superlubricity. Nat. Commun. 9, 1164. doi:10.1038/s41467-018-03549-6
Cairns, E., Ayyagari, A., McCoy, C., Berkebile, S., Berman, D., Aouadi, S., et al. (2023). Tribological behavior of molybdenum disulfide and tungsten disulfide sprayed coatings in low viscosity hydrocarbon environments. Tribol. Int. 179, 108206. doi:10.1016/j.triboint.2022.108206
Campbell, M., Loser, J. B., Sneegas, E., and Institute, M. R. (1966). Solid lubricants, national aeronautics and space administration.
Chagnon, P., and Fauchais, P. (1984). Thermal spraying of ceramics. Ceram. Int. 10, 119–131. doi:10.1016/0272-8842(84)90001-4
Chen, Y., Renner, P., and Liang, H. (2019). Dispersion of nanoparticles in lubricating oil: a critical review. Lubricants 7, 7. doi:10.3390/lubricants7010007
Danyluk, M., and Dhingra, A. (2012). Rolling contact fatigue using solid thin film lubrication. Wear 274-275, 368–376. doi:10.1016/j.wear.2011.10.005
Deng, Y., Chen, W., Li, B., Wang, C., Kuang, T., and Li, Y. (2020). Physical vapor deposition technology for coated cutting tools: a review. Ceram. Int. 46, 18373–18390. doi:10.1016/j.ceramint.2020.04.168
Doll, G., Mensah, B., Mohseni, H., and Scharf, T. (2010). Chemical vapor deposition and atomic layer deposition of coatings for mechanical applications. J. Therm. spray Technol. 19, 510–516. doi:10.1007/s11666-009-9364-8
Domínguez-Meister, S., Rojas, T. C., Frías, J., and Sánchez-López, J. C. (2019). Silver effect on the tribological and antibacterial properties of aC: Ag coatings. Tribol. Int. 140, 105837. doi:10.1016/j.triboint.2019.06.030
Donnet, C., and Erdemir, A. (2004). Solid lubricant coatings: recent developments and future trends. Tribol. Lett. 17, 389–397. doi:10.1023/b:tril.0000044487.32514.1d
Dugger, M. T. (2017). “Solid lubricants,” in Friction, lubrication, and wear Technology. Editor G. E. Totten (USA: ASM International), 191–203.
Erdemir, A. (2005). Review of engineered tribological interfaces for improved boundary lubrication. Tribol. Int. 38, 249–256. doi:10.1016/j.triboint.2004.08.008
Erdemir, A., and Donnet, C. (2006). Tribology of diamond-like carbon films: recent progress and future prospects. J. Phys. D Appl. Phys. 39, R311–R327. doi:10.1088/0022-3727/39/18/r01
Erdemir, A., Eryilmaz, O., Urgen, M., Kazmanli, K., Mehta, N., and Prorok, B. (2005). Tribology of nanostructured materials and coatings, Handbook of nanomaterials. Boca Ratton: CRC Publication, 685–711.
Erdemir, A., and Fenske, G. (1996). Tribological performance of diamond and diamondlike carbon films at elevated temperatures. Tribol. Trans. 39, 787–794. doi:10.1080/10402009608983596
Erdemir, A., and Martin, J. M. (2018). Superior wear resistance of diamond and DLC coatings. Curr. Opin. Solid State Mater. Sci. 22, 243–254. doi:10.1016/j.cossms.2018.11.003
Erdemir, A., Ramirez, G., Eryilmaz, O. L., Narayanan, B., Liao, Y., Kamath, G., et al. (2016). Carbon-based tribofilms from lubricating oils. Nature 536, 67–71. doi:10.1038/nature18948
Erdemir, A., and Voevodin, A. A. (2010). Nanocomposite coatings for severe applications, Handbook of deposition technologies for films and coatings. Germany: Elsevier, 679–715.
Eryilmaz, O., and Erdemir, A. (2008). TOF-SIMS and XPS characterization of diamond-like carbon films after tests in inert and oxidizing environments. Wear 265, 244–254. doi:10.1016/j.wear.2007.10.012
Farfan-Cabrera, L. I. (2019). Tribology of electric vehicles: a review of critical components, current state and future improvement trends. Tribol. Int. 138, 473–486. doi:10.1016/j.triboint.2019.06.029
Farfan-Cabrera, L. I., Cao-Romero-Gallegos, J. A., Lee, S., Komurlu, M. U., and Erdemir, A. (2023). Tribological behavior of H-DLC and H-free DLC coatings on bearing materials under the influence of DC electric current discharges. Wear 522, 204709. doi:10.1016/j.wear.2023.204709
Gangopadhyay, A. (2015). Coating technologies for automotive engine applications. Coat. Technol. Veh. Appl., 63–79. doi:10.1007/978-3-319-14771-0_4
Gao, K., Bin, W., Berman, D., Ren, Y., Luo, J., and Xie, G. (2023). Self-adaptive macroscale superlubricity based on the tribocatalytic properties of partially oxidized black phosphorus. Nano Lett. 23, 6823–6830. doi:10.1021/acs.nanolett.3c00611
Gao, K., Wang, B., Shirani, A., Chang, Q., and Berman, D. (2021). Macroscale superlubricity accomplished by Sb2O3-MSH/C under high temperature. Front. Chem. 9, 667878. doi:10.3389/fchem.2021.667878
Gérard, B. (2006). Application of thermal spraying in the automobile industry. Surf. Coatings Technol. 201, 2028–2031. doi:10.1016/j.surfcoat.2006.04.050
Goharshadi, E., Ahmadzadeh, H., Samiee, S., and Hadadian, M. (2013). Nanofluids for heat transfer enhancement-a review.
Gudmundsson, J. T., Brenning, N., Lundin, D., and Helmersson, U. (2012). High power impulse magnetron sputtering discharge. J. Vac. Sci. Technol. A Vac. Surfaces, Films 30. doi:10.1116/1.3691832
Hemanth, G., Suresha, B., and Ananthapadmanabha, H. (2021). Hybrid and electric vehicle tribology: a review. Surf. Topogr. Metrology Prop. 9, 043001. doi:10.1088/2051-672x/ac2bf6
Holmberg, K., and Matthews, A. (2009). Coatings tribology: properties, mechanisms, techniques, and applications in surface engineering. Germany: Elsevier.
Hovsepian, P. E., Kok, Y., Ehiasarian, A., Erdemir, A., Wen, J.-G., and Petrov, I. (2004). Structure and tribological behaviour of nanoscale multilayer C/Cr coatings deposited by the combined steered cathodic arc/unbalanced magnetron sputtering technique. Thin solid films 447-448, 7–13. doi:10.1016/j.tsf.2003.09.009
Hu, X., Lee, J., Berman, D., and Martini, A. (2018). Substrate effect on electrical conductance at a nanoasperity-graphene contact. Carbon 137, 118–124. doi:10.1016/j.carbon.2018.05.028
Jacques, K., Murthy, N., Dixit, S., Berman, D., and Berkebile, S. (2021). Method for tribological experiment to study scuffing initiation on AISI 52100 steel and hard ceramic coatings. Tribol. Int. 160, 107001. doi:10.1016/j.triboint.2021.107001
Jacques, K., Shirani, A., Smith, J., Scharf, T., Walck, S., Berkebile, S., et al. (2023). MoVN-Cu coatings for in situ tribocatalytic formation of carbon-rich tribofilms in low-viscosity fuels. ACS Appl. Mater. Interfaces 15, 30070–30082. doi:10.1021/acsami.3c01953
Kano, M. (2006). DLC coating technology applied to sliding parts of automotive engine, New Diamond and Frontier. Carbon Technol. 16, 201–210.
Kano, M. (2014). Diamond-like carbon coating applied to automotive engine components. Tribol. online 9, 135–142. doi:10.2474/trol.9.135
Kano, M. (2015). Overview of DLC-coated engine components. Coat. Technol. Veh. Appl., 37–62. doi:10.1007/978-3-319-14771-0_3
Kim, H., Lince, J., Eryilmaz, O., and Erdemir, A. (2006). Environmental effects on the friction of hydrogenated DLC films. Tribol. Lett. 21, 51–56. doi:10.1007/s11249-005-9008-1
Kim, J., Oh, J., and Lee, H. (2019). Review on battery thermal management system for electric vehicles. Appl. Therm. Eng. 149, 192–212. doi:10.1016/j.applthermaleng.2018.12.020
Kumar, D. (2023). Recent advances in tribology of high entropy alloys: a critical review. Prog. Mater. Sci. 136, 101106. doi:10.1016/j.pmatsci.2023.101106
Kurdi, A., and Chang, L. (2018). Recent advances in high performance polymers—tribological aspects. Lubricants 7, 2. doi:10.3390/lubricants7010002
Lee, J., Hu, X., Voevodin, A. A., Martini, A., and Berman, D. (2018). Effect of substrate support on dynamic graphene/metal electrical contacts. Micromachines 9, 169. doi:10.3390/mi9040169
Lee, J., Kuchibhotla, A., Banerjee, D., and Berman, D. (2019). Silica nanoparticles as copper corrosion inhibitors. Mater. Res. Express 6, 0850e3. doi:10.1088/2053-1591/ab2270
Ludema, K. (2001). History of tribology and its industrial significance, fundamentals of tribology and bridging the gap between the macro-and micro. Nanoscales 1–11. doi:10.1007/978-94-010-0736-8_1
Macknojia, A., Ayyagari, A., Zambrano, D., Rosenkranz, A., Shevchenko, E. V., and Berman, D. (2023). Macroscale superlubricity induced by MXene/MoS2 nanocomposites on rough steel surfaces under high contact stresses. ACS Nano 17, 2421–2430. doi:10.1021/acsnano.2c09640
Macknojia, A. Z., Montoya, V. L., Cairns, E., Eskandari, M., Liu, S., Chung, Y. -W., et al. (2024). Tribological analysis of steels in fuel environments: impact of alloy content and hardness. Appl. Sci. 14, 1898. doi:10.3390/app14051898
Manu, B. R., Gupta, A., and Jayatissa, A. H. (2021). Tribological properties of 2D materials and composites—a review of recent advances. Materials 14, 1630. doi:10.3390/ma14071630
Marian, M., Berman, D., Necas, D., Emami, N., Rosenkranz, A., and Rosenkranz, A. (2022). Roadmap for 2D materials in biotribological/biomedical applications – a review. Adv. Colloid Interface Sci. 307, 102747. doi:10.1016/j.cis.2022.102747
Marian, M., Berman, D., Rota, A., Jackson, R., and Rosenkranz, A. (2021). Layered 2D nanomaterials to tailor friction and wear in machine elements—a review. Adv. Mater. Interfaces 9, 2101622. doi:10.1002/admi.202101622
Martin, P. M. (2009). Handbook of deposition technologies for films and coatings: science, applications and technology. USA: William Andrew.
Matsumoto, N., Mistry, K., Kim, J., Eryilmaz, O., Erdemir, A., Kinoshita, H., et al. (2012). Friction reducing properties of onion-like carbon based lubricant under high contact pressure. Tribol. - Mater. Surfaces Interfaces 6, 116–120. doi:10.1179/1751584x12y.0000000014
Mehran, Q., Fazal, M., Bushroa, A., and Rubaiee, S. (2018). A critical review on physical vapor deposition coatings applied on different engine components. Crit. Rev. Solid State Mater. Sci. 43, 158–175. doi:10.1080/10408436.2017.1320648
Muratore, C., and Voevodin, A. A. (2009). Chameleon coatings: adaptive surfaces to reduce friction and wear in extreme environments. Annu. Rev. Mater. Res. 39, 297–324. doi:10.1146/annurev-matsci-082908-145259
Muratori, M., Alexander, M., Arent, D., Bazilian, M., Cazzola, P., Dede, E. M., et al. (2021). The rise of electric vehicles—2020 status and future expectations. Prog. Energy 3, 022002. doi:10.1088/2516-1083/abe0ad
Murthy, N., Berkebile, S., Macknojia, A., McCoy, C., Montoya, V., Cairns, E., et al. (2023). Tribological evaluation of additively manufactured steels for applications in fuel environments. doi:10.21236/ad1215150
Oswald, J. (1970). The properties and applications of hard chromium for engineering purposes. Trans. IMF 48, 169–171. doi:10.1080/00202967.1970.11870149
Panjan, P., Drnovšek, A., Gselman, P., Čekada, M., and Panjan, M. (2020). Review of growth defects in thin films prepared by PVD techniques. Coatings 10, 447. doi:10.3390/coatings10050447
Polcar, T., Gustavsson, F., Thersleff, T., Jacobson, S., and Cavaleiro, A. (2012). Complex frictional analysis of self-lubricant WSC/Cr coating. Faraday Discuss. 156, 383–401. doi:10.1039/c2fd00003b
Rajak, D. K., Kumar, A., Behera, A., and Menezes, P. L. (2021). Diamond-like carbon (DLC) coatings: classification, properties, and applications. Appl. Sci. 11, 4445. doi:10.3390/app11104445
Reeves, C. J., Menezes, P. L., Lovell, M. R., and Jen, T.-C. (2013). Tribology of solid lubricants, Tribology for scientists and engineers: from basics to advanced concepts, 447–494.
Roberts, E. (1990). Thin solid lubricant films in space. Tribol. Int. 23, 95–104. doi:10.1016/0301-679x(90)90042-n
Rosenkranz, A., Costa, H. L., Baykara, M. Z., and Martini, A. (2021). Synergetic effects of surface texturing and solid lubricants to tailor friction and wear–a review. Tribol. Int. 155, 106792. doi:10.1016/j.triboint.2020.106792
Sánchez-López, J., and Fernández, A. (2008). Doping and alloying effects on DLC coatings. Tribol. Diamond-Like Carbon Films, 311–338. doi:10.1007/978-0-387-49891-1_12
Sanders, D. M., and Anders, A. (2000). Review of cathodic arc deposition technology at the start of the new millennium. Surf. Coatings Technol. 133-134, 78–90. doi:10.1016/s0257-8972(00)00879-3
Scharf, T., Diercks, D., Gorman, B., Prasad, S., and Dugger, M. (2009). Atomic layer deposition of tungsten disulphide solid lubricant nanocomposite coatings on rolling element bearings. Tribol. Trans. 52, 284–292. doi:10.1080/10402000802369747
Scharf, T., and Prasad, S. (2013). Solid lubricants: a review. J. Mater. Sci. 48, 511–531. doi:10.1007/s10853-012-7038-2
Shirani, A., Al Sulaimi, R., Macknojia, A. Z., Eskandari, M., and Berman, D. (2023b). Tribocatalytically-active nickel/cobalt phosphorous films for universal protection in a hydrocarbon-rich environment. Sci. Rep. 13, 10914. doi:10.1038/s41598-023-37531-0
Shirani, A., Berkebile, S., and Berman, D. (2023a). Promoted high-temperature lubrication and surface activity of polyolester lubricant with added phosphonium ionic liquid. Tribol. Int. 180, 108287. doi:10.1016/j.triboint.2023.108287
Shirani, A., Joy, T., Rogov, A., Lin, M., Yerokhin, A., Mogonye, J.-E., et al. (2020). PEO-Chameleon as a potential protective coating on cast aluminum alloys for high-temperature applications. Surf. Coatings Technol. 397, 126016. doi:10.1016/j.surfcoat.2020.126016
Shirani, A., Li, Y., Eryilmaz, O. L., and Berman, D. (2021). Tribocatalytically-activated formation of protective friction and wear reducing carbon coatings from alkane environment. Sci. Rep. 11, 20643. doi:10.1038/s41598-021-00044-9
Shirani, A., Li, Y., Smith, J., Curry, J. F., Lu, P., Wilson, M., et al. (2022). Mechanochemically driven formation of protective carbon films from ethanol environment. Mater. Today Chem. 26, 101112. doi:10.1016/j.mtchem.2022.101112
Singer, I., Dvorak, S., Wahl, K., and Scharf, T. (2003). Role of third bodies in friction and wear of protective coatings. J. Vac. Sci. Technol. A Vac. Surfaces, Films 21, S232–S240. doi:10.1116/1.1599869
Singer, I. L., and Pollock, H. (2012). Fundamentals of friction: macroscopic and microscopic processes. Germany: Springer Science and Business Media.
Sliney, H. E. (1982). Solid lubricant materials for high temperatures—a review. Tribol. Int. 15, 303–315. doi:10.1016/0301-679x(82)90089-5
Spalvins, T. (1987). A review of recent advances in solid film lubrication. J. Vac. Sci. Technol. A Vac. Surfaces, Films 5, 212–219. doi:10.1116/1.574106
Tenne, R. (2006). Inorganic nanotubes and fullerene-like nanoparticles. Nat. Nanotechnol. 1, 103–111. doi:10.1038/nnano.2006.62
Tung, S. C., and Wong, V. (2021). Surface engineering development trends and impact of surface coatings and textures on automotive powertrain friction and wear control. Mater. Perform. Charact. 10, 620–650. doi:10.1520/mpc20200091
Vazirisereshk, M. R., Martini, A., Strubbe, D. A., and Baykara, M. Z. (2019). Solid lubrication with MoS2: a review. Lubricants 7, 57. doi:10.3390/lubricants7070057
Vetter, J. (2015). Surface treatments for automotive applications. Coat. Technol. Veh. Appl., 91–132. doi:10.1007/978-3-319-14771-0_6
Vetter, J., Barbezat, G., Crummenauer, J., and Avissar, J. (2005). Surface treatment selections for automotive applications. Surf. Coatings Technol. 200, 1962–1968. doi:10.1016/j.surfcoat.2005.08.011
Wang, B., Qiu, F., Barber, G. C., Zou, Q., Wang, J., Guo, S., et al. (2022). Role of nano-sized materials as lubricant additives in friction and wear reduction: a review. Wear 490-491, 204206. doi:10.1016/j.wear.2021.204206
Winer, W. O. (1967). Molybdenum disulfide as a lubricant: a review of the fundamental knowledge. Wear 10, 422–452. doi:10.1016/0043-1648(67)90187-1
Zabinski, J., Donley, M., Prasad, S., and McDevitt, N. (1994). Synthesis and characterization of tungsten disulphide films grown by pulsed-laser deposition. J. Mater. Sci. 29, 4834–4839. doi:10.1007/bf00356530
Zeng, Q., Eryilmaz, O., and Erdemir, A. (2015). Superlubricity of the DLC films-related friction system at elevated temperature. RSC Adv. 5, 93147–93154. doi:10.1039/c5ra16084g
Zhai, W., and Zhou, K. (2019). Nanomaterials in superlubricity. Adv. Funct. Mater. 29, 1806395. doi:10.1002/adfm.201806395
Zhmud, B., and Pasalskiy, B. (2013). Nanomaterials in lubricants: an industrial perspective on current research. Lubricants 1, 95–101. doi:10.3390/lubricants1040095
Keywords: electrified conditions, friction, wear, coatings, electrical properties, thermal management
Citation: Lee S, Farfan-Cabrera LI, Berman D, Rosenkranz A and Erdemir A (2024) Tribological coatings for electric vehicle applications. Front. Coat. Dye In. 2:1426164. doi: 10.3389/frcdi.2024.1426164
Received: 30 April 2024; Accepted: 21 June 2024;
Published: 11 July 2024.
Edited by:
Robert Wood, University of Southampton, United KingdomReviewed by:
Yanfei Liu, Beijing Institute of Technology, ChinaCopyright © 2024 Lee, Farfan-Cabrera, Berman, Rosenkranz and Erdemir. This is an open-access article distributed under the terms of the Creative Commons Attribution License (CC BY). The use, distribution or reproduction in other forums is permitted, provided the original author(s) and the copyright owner(s) are credited and that the original publication in this journal is cited, in accordance with accepted academic practice. No use, distribution or reproduction is permitted which does not comply with these terms.
*Correspondence: Ali Erdemir, YWVyZGVtaXJAdGFtdS5lZHU=
Disclaimer: All claims expressed in this article are solely those of the authors and do not necessarily represent those of their affiliated organizations, or those of the publisher, the editors and the reviewers. Any product that may be evaluated in this article or claim that may be made by its manufacturer is not guaranteed or endorsed by the publisher.
Research integrity at Frontiers
Learn more about the work of our research integrity team to safeguard the quality of each article we publish.