- Centre for Sol-Gel Coatings, International Advanced Research Centre for Powder Metallurgy and New Materials (ARCI), Balapur, Hyderabad, India
The sol–gel process is a simple wet chemical method used to generate nano-crystalline or nano-scaled amorphous ceramic and ceramic–polymer hybrid coatings. Pure ceramic and pure polymer coatings have certain limitations for use over a wide range of applications due to the high-temperature heat treatment requirement for the former and poor mechanical properties of the latter. Hence, ceramic–polymer hybrid coatings are the need of the hour for use in diverse applications on different substrates. Furthermore, bioinspired multifunctional coatings that mimic complex geometrics of the lotus leaf, pitcher plant, etc., are being investigated for their use in corrosion protection, biofilm inhibition, antifouling, etc. Such complex geometries can be generated by a combination of physical and chemical modifications of a surface. In the case of the chemical modification of a surface, instead of a pure ceramic or pure polymer coating, a ceramic–polymer hybrid coating would be the choice, as, a rigid backbone is provided by the ceramic (metal oxide network) moiety and a flexible structure by the polymeric moiety. This review discusses the sol–gel-derived pure ceramic and ceramic–polymer hybrid coatings, their applications, challenges, research gaps as they have been evolving over the years, and two nature-inspired phenomena, namely, superhydrophobicity and self-healing, that have been widely researched for use in various applications.
1 Introduction
Fundamentally, wet chemical process-derived protective coatings can be classified into a) inorganic or ceramic coatings, (b) organic or polymer coatings, and (c) inorganic–organic or ceramic–polymer hybrid coatings. Among the wet chemical coating techniques, the sol–gel process is a versatile and innovative method used to produce thin ceramic and ceramic–polymer hybrid coatings. When the sol–gel process was discovered in late 18th century by Ebelman, it was used to generate only pure inorganic (ceramic) coatings. Ceramic coatings are very hard, and coating thicknesses are limited to a nano-metre scale. Moreover, sol–gel-derived ceramic coatings needed high temperatures (>400°C) for densification. As there was a restriction in the use of the pure ceramic coatings on polymer substrates, these coatings could be used only on glass, ceramic, or metal substrates, which are able to withstand high temperatures.
The development on sol–gel-derived ceramic–polymer hybrid coatings took place in the mid-1980s (Wilkes et al., 1989; Schmidt and Wolter, 1990) and is still ongoing for different applications. The introduction of ceramic–polymer hybrid coatings can yield transparent coatings with excellent mechanical properties such as hardness and adhesion strength and has resulted in widening the application segment due to a drastic reduction in heat treatment conditions.
Different functionalities such as hydrophilicity, hydrophobicity, corrosion protection, antireflection, and anti-bacterial and photocatalytic properties could be imparted to the coating based on the selection of precursors or feed stock material during sol synthesis. Each sol formulation is unique, and the coating properties depend on the choice of precursors, precursor concentration, sol pH, viscosity, and moisture content. All of the factors influence the properties of the resulting coating material for both ceramic and ceramic–polymer hybrid coatings. This review discusses the evolution of the sol–gel process over time, with a focus on the application development for ceramic–polymer hybrid coatings.
A brief description of the sol–gel process is given below. Sol is a nano-particulate dispersion synthesized by dispersing metal/silicon alkoxide precursors in a solvent medium, which is mostly an alcohol containing water and an acid/base catalyst. The sol undergoes a controlled polymeric transition to form a three-dimensional ceramic (metal oxide) network called the gel, which can be applied as a film and dried. The gel is further consolidated by heat treatment at higher temperatures for achieving the required mechanical properties. The sol–gel process allows the synthesis of coating materials with unique properties such as transparency, high surface area, and tailored porosity, with precise control over composition and structure. Different types of coatings, their salient features, current research gaps for various recipes, and potential development and applications, as shown in Figure 1, is discussed in detail.
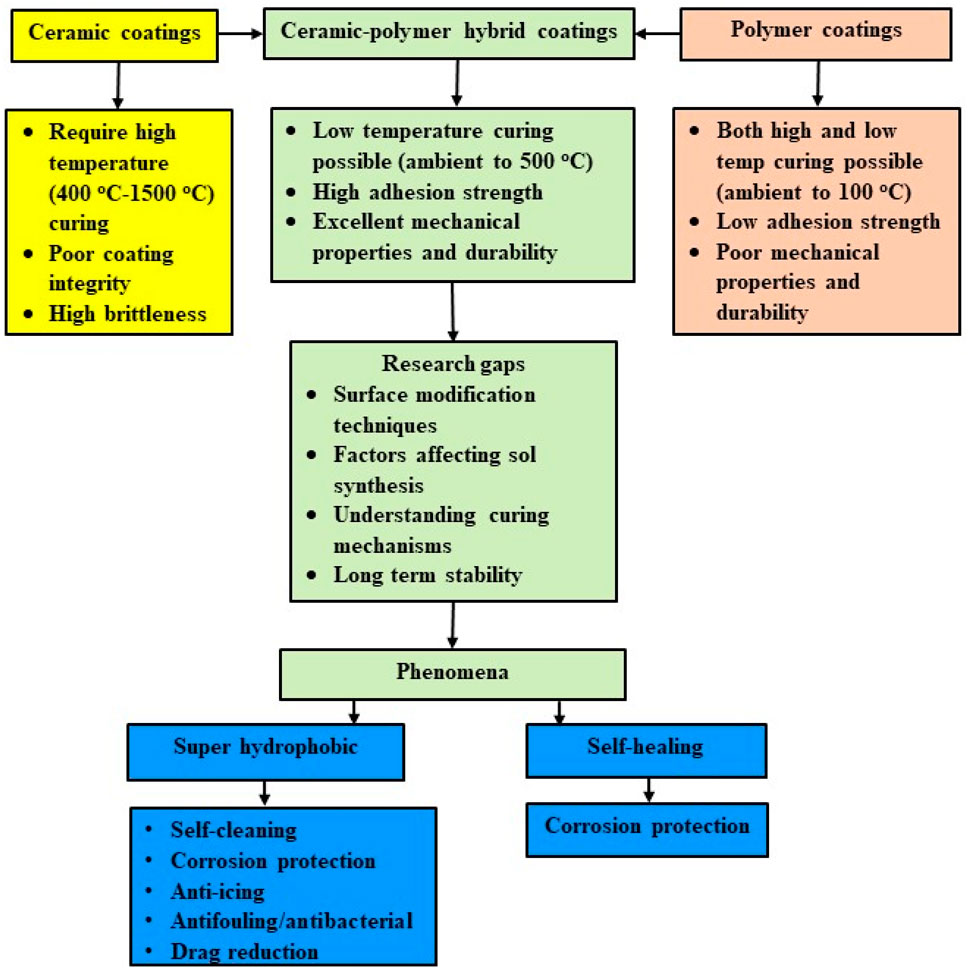
Figure 1. Schematic representation of wet chemical coatings, their salient features, current research gaps for various recipes, potential development, and applications.
Organic coatings such as paints are polymeric coatings that are well-known for their poor abrasion resistance, but excellent corrosion protection properties. Polymer coatings were also used as platforms for incorporating additional functionalities such as self-healing capabilities. The combination of the sol–gel and polymeric material yields a ceramic–polymer hybrid coating material with synergistic properties combining the advantages of the sol–gel and polymer systems. The advantage of the hybrid system is that the sol composition and coating structure can be tailor-made to achieve specific functionalities and enhanced durability. However, each of the coating systems has its own merits and demerits in the implementation for commercial applications. The authors’ laboratory has worked extensively on using ceramic coatings and ceramic–polymer hybrid coatings for various applications, and hence, this review mainly focuses only on ceramic and ceramic–polymer hybrid coatings for diverse applications.
2 Types of coatings
2.1 Inorganic sol–gel coatings
Inorganic sol–gel synthesis consists of hydrolysis and condensation reactions of at least one silicon/metal alkoxide as per the reactions shown in Figure 2. Although fully hydrolysable metal alkoxides such as titanium alkoxide, aluminium isopropoxide, zirconium n-propoxide, and silicon alkoxide were used as precursors for organic solvent-based inorganic sol synthesis, aqueous inorganic sols can also be prepared from metal salts such as TiCl4 and AlCl3.6H2O (Kobayashi et al., 2005). Both of them result in the production of their respective metal oxide ceramic layers such as TiO2, Al2O3, ZrO2, and SiO2 after the heat treatment of the deposited coating at high temperatures. More often, the sol–gel synthesis of inorganic precursors was used for the preparation of gels and, thereafter, preparation of monolithic glasses and or nano-structured oxide ceramic powders (Li et al., 2002). Various applications developed through the sol–gel process are shown in Figure 3. Inorganic sol synthesis is a low-temperature (<100°C) process, but its coatings essentially require high temperatures for the consolidation of the wet films and are often referred to as sintering temperatures, which range anywhere between 400°C and 1,500°C (Kajihara, 2013). The microstructure, phases, and mechanical properties of the coatings depend on ageing of the sol, pH, viscosity, and heat treatment temperature of the gel or coating (Li et al., 2002; Catauro et al., 2018). Therefore, such coatings could only be applied on high temperature-resistant substrates such as glass (600°C), superalloys, and ceramics, thereby narrowing down the application segments.
The solid content of only inorganic sols is usually low, in the order of 5%–10%, leading to excessive shrinkage and build-up of residual stresses in the coating during the consolidation process in the sintering step. Residual stresses are always tensile and influenced by factors such as the alkoxide-to-water ratio and chelating agent used in the sol. The residual stress also increases with the increase in coating thickness, heat treatment temperatures, rate of heating, and coefficient of thermal expansion of the substrate material (Kozuka, 2003). Two metal organic precursors, tetraethoxysilane (TEOS) and perhydropolysilazane (PHPS), are routinely used for the synthesis of sols that result in silica films after heat treatment. Sintering temperature of the TEOS-based sol was approximately 500°C and that of the PHPS-based sol was slightly higher, approximately 600°C, resulting in a non-crystalline silica coating. The densification in the case of the silica film obtained from PHPS involved the hydrolysis and condensation of Si-H, Si-N, and N-H bonds, and the TEOS-based sol densification involved hydrolysis and condensation involving –OH groups. In both cases, the shrinkage, refractive index, residual stresses, coating density, and critical coating thickness as a function of heat treatment temperature (Zhang et al., 2023) were different.
The thickness of the coatings derived from inorganic sols was often limited to 1 or 2 μm only or lower since, if deposited to higher thickness, coatings tended to crack due to excessive stresses. Since the coatings were ceramic in nature, they are very hard and brittle. A lower solid content implied a higher-volatile organic compound (VOC) such as isopropyl alcohol, ethanol, and methanol, which are not environmentally friendly. The optimization of process conditions was required for the synthesis of a robust sol. Precursor concentration, pH, and moisture content in the sol influence the properties of the resulting coating material to a large extent.
Since pure inorganic coatings are very thin, this process is suitable for the generation of transparent optical coatings such as antireflective coatings, fully dielectric solar control coatings, and solar selective coatings on glass/metal substrates. Antireflection coatings on a transparent substrate like glass or plastic increases the transmission of the substrate and can be used in various applications such as ophthalmic lenses, display panels, camera lenses, and photovoltaic cells. An antireflection property can be achieved by tuning the refractive index and thickness of the coating, and several methods can be used such as using single-layer or multilayer or graded index antireflection coatings. Such optical coatings need to be very thin, of the order of few hundreds of nm, and transparent. Pure ceramic coatings were appropriate for such applications. SiO2 layers were normally used as low-refractive index layers, and TiO2/Al2O3/ZrO2 was used as high-refractive index layers (Manasa and Subasri, 2016; Barua et al., 2017; Subasri et al., 2019).
Multilayer coatings with alternating layers of ceramic and cermet can yield solar-selective property, which can be used in a heat collection element of a solar-to-thermal power conversion device for converting solar radiation to heat, which, in turn, can be converted to electricity. Subasri et al. used an Ag–TiO2 and SiO2 multilayer stack, which exhibited an average absorbance of 94% ± 1% over 300–1,500 nm and emissivity of 0.13, as measured using an emissometer. The thickness of the single layers ranged from 59 to 78 nm for the TiO2 and Ag–TiO2 layers, whereas it was 35–40 nm for the silica layer. Such thin optical coatings obtained by the sol–gel technique could be achieved only if pure inorganic coatings were deposited and durable under the testing conditions (Subasri et al., 2016).
Coatings that can considerably transmit visible wavelength radiation by cutting off near-infrared (NIR) radiation are called solar control coatings. These find applications in automobile windows and architectural glasses. Metal dielectric coatings (Ag–TiO2) or transparent conducting oxide (indium–tin oxide) coatings on glass can enable the glass to display solar control properties. Recently, a fully dielectric coating stack with alternating high-refractive index (BaTiO3/SrTiO3) and low-refractive index layers (MgF2 or zeolite), with the thickness of each layer being 188 nm (high-refractive index layer) and 71 nm (low-refractive index layer), was also shown to exhibit solar control properties (Subasri et al., 2019). High heat treatment temperatures resulted in excellent adhesion strength. However, the coating integrity depended on the optimization of process parameters. Commercialization efforts of inorganic sol–gel coatings showed that the process was expensive, and there were several process-related challenges during the scale-up of the process for large-scale industrial applications.
The above discussion shows that thin ceramic coatings derived from the sol–gel process can have several optical applications.
2.2 Polymer coatings
Polymers, which are long-chain molecules and repetitive monomers of short-chain molecules, were used as binding materials in coatings to protect structural materials from atmospheric degradation and enhance durability. Polymer synthesis using epoxy resin is shown in Figure 4. Bisphenol A diglycidyl ether (DGEBA) epoxy (diane resin ED-20) added with 1 wt% curing catalyst 2,4,6-bis(dimethylamine methyl)phenol (alkophen, DMP-30) (4a and 4b) yields cross-linked polymers as per the polymerization reaction shown in Figure 4C (Voytik et al., 2020). Natural polymers include proteins and polysaccharides, as well as biopolymers like silk and rubber, whereas synthetic polymers include nylon, polystyrene, polyurethane (PU), polyethylene, and Teflon. Various kinds of polymer coatings include polyurethane, epoxy, polyacrylic, polyesters, polyvinyl alcohol, and phenolics and are primarily used to protect metals from corrosion (He S. et al., 2023). Polymeric coating solution includes binders, fillers, plasticizers, surfactants, and pigments. Usually, polymer matrices are used in coatings to reduce the curing temperature. As mentioned earlier, if the coating matrix was ceramic, it requires higher temperatures for consolidation. Hence, if the coating requires to be cured at low temperatures, then, polymer matrices are used.
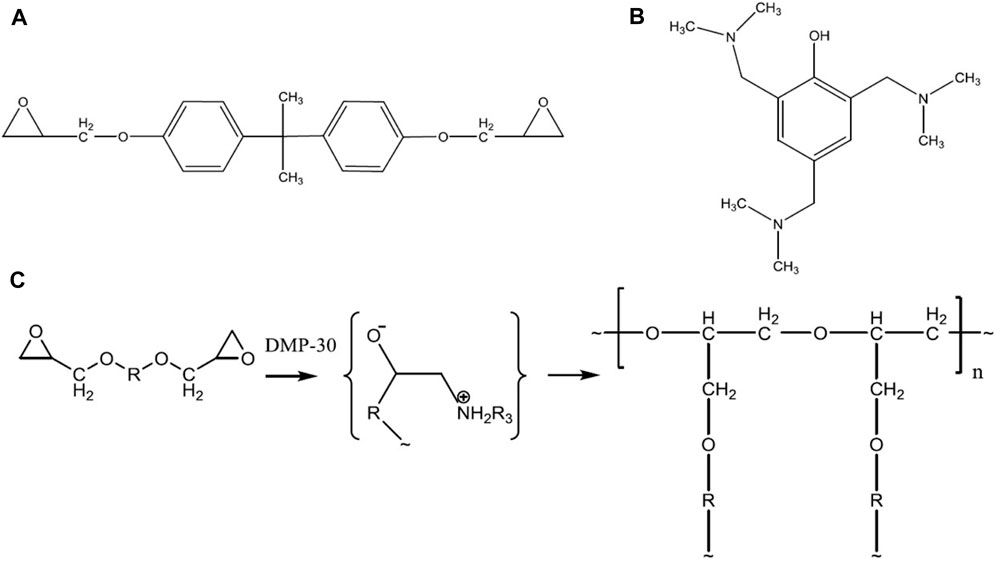
Figure 4. Structural formulae of initial compounds: (A) ED-20 epoxy and (B) DMP-30 catalyst and (C) schematic representation of the epoxy resin polymerization process (reprinted under the terms of the creative commons attribution from IOP Publishing Ltd—Voytik et al., 2020).
Among the above polymers, the bond strength of polyester materials was considered to be low, along with poor physical properties. Phenolic coatings are brittle and exhibit low toughness with a high solvent content. Epoxy polymers fall under the thermosetting polymer category, which are stable and possess enhanced adhesion strength. Polymeric coatings exhibit excellent adhesion to the substrate and can be made resistant to heat, chemicals, moisture, and saline environment. PU coatings based on polyisocyanate and polyester polyol were developed by Zhang et al. (2001), but they degrade in the presence of ultraviolet (UV) light (Zhang et al., 2001). UVA-induced embrittlement causes the chemical degradation of coatings and decomposition under salt spray test conditions due to the hydrolysis and dissolution of pigments, leading to physical degradation (Cai et al., 2018). Zinc phosphate, iron zinc phosphate, zinc aluminium polyphosphate, aluminium zinc phosphate, potassium zinc phosphate, and strontium aluminium polyphosphate pigments were used as corrosion inhibitors in the polymeric coating matrix.
Hybrid pigments, such as benzotriazole/zinc acetate, benzotriazole/potassium zinc phosphates, and urtica dioica/zinc acetate, and chelation products of caffeic and chicoric acids and zinc cations in an EE-430CS epoxy ester coating were found to exhibit enhanced corrosion protection (Salehi et al., 2017). Acrylic polymers such as 2,2,33,4,4,5,5-octafluoropentyl methacrylate, 2-3-(2H-benzotriazol-2-yl)-4-hydroxyphenylethyl methacrylate, 2,2,3,4,4,4-hexafluorobutyl acrylate, and butyl acrylate were used in various fields. Fluorinated acrylic polymer coatings with benzotriazole exhibited low surface free energy and high thermal stability while maintaining high visible light transmittance and UV blocking performance (Han et al., 2023). Pentaerythritol and ethylene glycol were used to prepare bio-derived polymeric nano-composites using multiwalled carbon nanotubes (MWCNTs) and TiO2 nanotubes as fillers to impart corrosion protection and self-healing properties while maintaining thermal stability, hardness, and adhesion strength (Parihar and Gaur, 2023). Polyvinyl chloride (PVC) and polyvinyl alcohol (PVA)-modified polyfunctional epoxy are used as binders in primers and base coats, while alkyd silicone is used in the top coat. PVC induces high flexibility and thermal stability, while PVA enhances adhesion, oil resistance, and biocompatibility to the coatings (Perrin et al., 2009; Bashta et al., 2016; Zhang et al., 2022). The use of polymer coatings depends on the substrate and the service conditions, such as temperature and other weathering conditions.
Epoxy resins such as DGEBA, bisphenol F diglycidyl ether (DGEBF), cycloaliphatic epoxy resins, novolac epoxy resins, and epoxy acrylate resins, epoxy monomers such as glycidyl methacrylate (GMA), glycidyl acrylate (GA), vinyl cyclohexane oxide (VCHO), and 1,4-butanediol diglycidyl ether (BDGE), and cycloaliphatic epoxy monomers such as 3,4-epoxycyclohexylmethyl-3,4-epoxycyclohexane carboxylate (Cyracure UVR-6110), tetraglycidyl methylenedianiline (TGMDA), and phenylmethylsiloxane epoxy were used extensively to synthesize polymeric and hybrid coatings. Different polymers as discussed above were selected as binders based on the functional property requirement in the coating. Typical polymeric coating thicknesses range from 30 to 200 µm. Moreover, various additives are usually added in small quantities to impart different functionalities to the polymeric coatings. Organic corrosion inhibitors such as benzotriazole, poly(o-anisidine) nanoparticles, polydimethylsiloxane filled in urea formaldehyde, dimethyldineodecanoate tin filled with polyurethane microcapsules, dodecylamine in aluminosilicate clay (halloysite) nanotubes, benzotriazole-loaded mesoporous silica nanoparticles, and 8,2-mercaptobenzimidazole were extensively investigated as corrosion inhibitors, while ZnO, CeO2, and graphene nanoparticles were used as inorganic corrosion inhibitors (Ulaeto et al., 2023) in polymer coating matrices. Majority of polymeric compositions can be cured at ambient temperatures, but temperatures below the respective glass transition temperatures or higher temperatures like 100°C allow complete cross-linking to achieve the envisioned properties and, hence, are attractive from the large-scale application perspective (Michel and Ferrier, 2020).
Polymeric coatings are extensively used in household, marine, magnetic media, and storage devices, food packaging, and the aviation sector, such as paints on an aircraft body. Coating functionalities include aesthetic appeal for kitchen utensils, cosmetic packaging, drug packaging, and easy-to-clean coatings such as Teflon, and are also used in the transportation sector and industry for corrosion protection and aesthetic appeal. The energy sector uses coatings for protection against heat and light, as easy-to-clean coatings on solar panels, breathable clothing, antibacterial coatings in medical facilities, antifouling coatings on boat and ship hulls, and encapsulation of electronic circuits, as well as different structural parts for improving productivity and efficiency of the systems (Rawat et al., 2020).
Polymeric coatings exhibited low adhesion strength, and their mechanical properties depend on the composition. Although polymeric coatings have high solid content, the VOC such as the thinner used in the synthesis was not environmentally friendly. Alternative polymeric coatings are aqueous and nonhazardous.
2.3 Ceramic–polymer hybrid coatings
Different methods can be used to prepare hybrid coatings. A simple dispersion of ceramic nanoparticles in a polymeric system yields a hybrid composite coating. It is a mere physical mixture and, hence, lacks the mechanical properties required for practical applications due to poor linkage between inorganic particles and polymer groups. Hybrid nano-composite coatings could also be prepared by a sol–gel process using a metal alkoxide precursor in combination with one or more organically modified silanes, water, catalyst, and a solvent. Such an in situ prepared organic–inorganic hybrid network sol yielded transparent coatings with excellent mechanical properties such as hardness and adhesion strength and suitable for large-scale coating applications in an industrial environment (Jeevajothi et al., 2012). The formation of the hybrid network due to the interaction of methacryloxypropyltrimethoxysilane with zirconium-n-propoxide is shown in Figure 5. Mechanical properties of the coating could be enhanced by introducing SiO2 nanoparticles duly functionalized with the same organic group that was already available as the polymerisable group in the hybrid sol. Compatibility between the organic groups of the nanoparticles and hybrid sol could thus be established (Sowntharya et al., 2012; Sowntharya and Subasri, 2013). Polydimethylsiloxane (PDMS) is an organic–inorganic hybrid polymer that is characterized by a polysiloxane backbone. PDMS coatings are generally used to generate hydrophobic coatings. Similarly, polyphosphazene and polyborazylene are also inorganic–organic hybrid materials, and hybrid coatings can be generated using these materials. Major applications of polyphosphazene reported were for drug delivery and tissue regeneration.
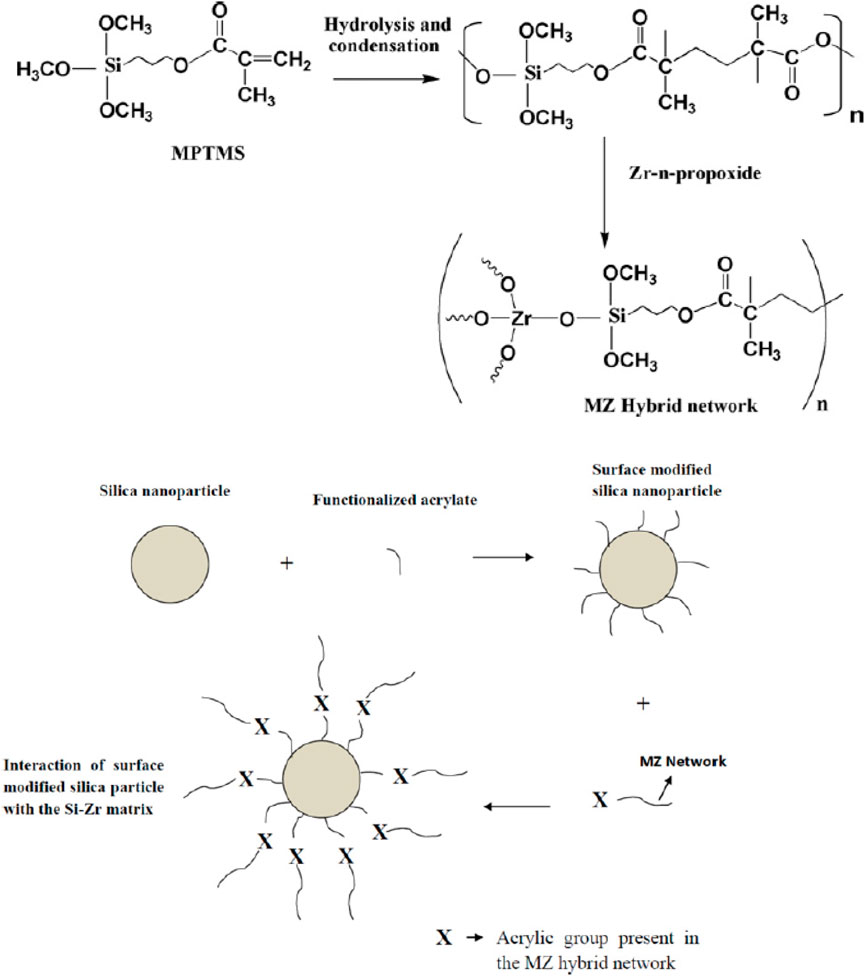
Figure 5. Hybrid network formation between organically modified and inorganic precursors in sol synthesis (reprinted with permission from Elsevier—Sowntharya et al., 2013).
The solid content of inorganic–organic hybrid sols is in the order of 25%–40%, leading to reduced shrinkage during curing, and therefore, a substantial reduction occurs in residual stresses in the coating compared to a pure ceramic (inorganic) coating. Hybrid coatings can be cured at lower temperatures, such as ambient to approximately 500°C. Residual stresses are lowered further due to the presence of organic ligands from the organically modified precursors and chelating agents used, since they link different precursors and lower the stress concentration. However, similar to inorganic sol–gel coatings, residual stress in hybrid coatings is also greatly influenced by the amount of water used to hydrolyse the precursors and the kind of chelating agent used in the sol and increases with the increase in coating thickness, heat treatment temperatures, and rate of heating due to densification.
In situ observations indicated that the coating fractured during the ramp-up stage of the curing cycle, indicating that the cracking was initiated while the tensile stress increased beyond a certain amount when the coating was still in the densification stage. Excessive stresses tend to crack the coatings when deposited to a higher coating thickness, and investigators could successfully enhance a hybrid coating thickness to 10–25 μm depending on the hybrid coating composition. A hybrid sol prepared with phenyltriethoxysilane (PhTES), toluene, and isopropanol using HCl as the catalyst in the presence of polycyclic aromatic hydrocarbon functional molecules such as fullerene, pentacene, and anthracene could successfully yield 100-µm-thick films under cast conditions for biomedical applications (Falcaro et al., 2011).
The coatings were ceramic in nature, but with organic ligands, hence they exhibited excellent mechanical properties such as hardness, abrasion resistance, and formable. A higher solid content means a lower VOC such as isopropyl alcohol, ethanol, and methanol, making the hybrid coating process more environmentally friendly. Sol synthesis optimization ensured consistency in coating quality with reproducible coating characteristics. Precursor concentration, sol pH, viscosity, and moisture content influenced the properties of the resulting coating material.
The in situ preparation of ceramic nanoparticles in hybrid systems through the sol–gel process allowed the fine dispersion of the inorganic phase in epoxy matrices. Organoalkoxysilane as a coupling agent builds covalent linkages between organic and inorganic phases, thereby enhancing the mechanical properties of the composite material, while maintaining transparency of the coating. Epoxy-based hybrid coatings find many applications such as flame retardant coatings, antimicrobial and corrosion protection coatings (Serra et al., 2016). DGEBA epoxy material could be modified using coupling agents such as 3-isocyanatopropyltriethoxysilane to make them compatible to synthesize hybrid coatings that can be used for flame retardant applications (Chiang and Ma, 2002).
The use of ionic liquids in the synthesis of ceramic–polymer hybrid coatings has been a new topic of research. Ionic liquids are organic salts that stay in liquid state below 100°C. Synthesis steps include homogenization of resin, its curing agent, coupling agent, metal alkoxide precursor, catalyst, water, solvent, and an ionic liquid. The appropriate selection and use of ionic liquid as a solvent or cosolvent inhibited the crack generation in coatings due to the high thermal stability and negligible vapour pressure of ionic liquids at room temperature (Vioux et al., 2010). Some of the ionic liquids investigated recently include 1-triethylene glycol monomethyl ether-3-methylimidazolium tetrafluoroborate (C7O3MImBF4), 1-decyl-3-methylimidazolium tetrafluoroborate (C10MImBF4), and 1-triethylene glycol monomethyl ether-3-methylimidazolium methanesulfonate (C7O3MImMeS) (Branda et al., 2023).
3 Current research gaps in hybrid coatings
Extensive research has been carried out in the last three decades to reduce the defect formation in the ceramic–polymer hybrid coatings for improving consistency and developing new application areas for the coatings. A careful review of the literature showed abundant scope of work in the following areas to make the technology amenable for scale-up:
1. Modification of the substrate surface to improve the adhesion strength of coatings;
2. Factors affecting sol synthesis;
3. Understanding curing mechanisms;
4. Long-term stability (shelf life) of the sol.
The literature revealed that researchers have always used only one particular sol recipe on one identified substrate material. However, no same research groups have worked on one sol recipe for distinctly different substrate materials such as glass, transparent plastics such as polycarbonate (PC) or polymethyl methacrylate, metals, mild steel, stainless steel, and aluminium. Different surface activation/modification techniques are required for such wide ranging substrate materials. A sol composition that resulted in excellent adhesion strength and scratch hardness on the metal need not exhibit the same properties on plastics and glass even though the same surface activation and curing conditions are employed. Similarly, the shelf life of the sol was observed to be different for different ambient and storage conditions. Hence, it necessitates systematic investigations and data generation in the above areas for each sol composition and substrate combination, which is highly essential for reproducibility of the films in a defect-free regime and for generating a technology document.
3.1 Modification of the substrate surface to improve the adhesion strength of coatings
Surface activation is essential to improve the adhesion strength of coatings irrespective of whether the substrate is plastic, metal, or ceramic in nature. Various surface activation techniques including the simple wet cleaning method such as mechanical polishing on silicon carbide paper, swiping or ultrasonic cleaning with solvents and distilled water, chemical etching, dry cleaning like shot blasting, and activation like flame treatment and corona or plasma treatment are in practice. Plasma treatment is essential for the polyolefin material substrates that are hydrophobic in nature, such as polypropylene (PP), polyethylene (PE), and blow-moulded automobile parts.
Alkaline, acidic, and H2O2 pretreatments have been reported for metallic substrates such as Ti, Mg and its alloys, mild steel, and stainless steel. Soaking of the Ti substrate in NaOH helped in the generation of hydroxide groups on the titanium substrate prior to the deposition of hydroxyapatite (HAp) coating. Similarly, acidic pretreatment with sulphuric acid (H2SO4) helped in increasing the surface area due to the etching process and the subsequent increase in the oxide layer thickness. Hydrofluoric acid (HF) was also used to improve the surface free energy and for faster coating formation with high crystallinity compared to the titanium substrate pretreated with H2O2. H2O2 treatment increased the bioactive properties of calcium phosphate coatings and resulted in low-crystalline TiO2 coatings (Huynh et al., 2019).
Shot blasting uses abrasives such as sand, alumina (Al2O3), or silicon carbide (SiC) grit to propel and impinge on to the substrate surface with certain kinetic energy acquired from the compressed air, which was used as a carrier gas. This technique was used as a tool to clean and induce roughness on the substrate surface. Kinetic energy transfer from the grit creates large area defects upon impact on the substrate and create roughness. This process increases the effective surface area by many folds and enhances the adhesion strength of the coating applied over the shot-blasted surface.
A superhydrophobic (SH) surface can be created by mimicking the hierarchical double structure of a lotus leaf. Shot blasting was used to create macro-level surface roughness, over which a nano-scale surface structure was created with methyltriethoxysilane (MTEOS), glycidoxypropyltrimethoxysilane (GPTMS), and fluoro-functionalized colloidal silica (1H,1H,2H,2H-perfluoro octyl triethoxysilane)-based sol–gel coating to successfully generate SH coating with an average water contact angle (WCA) of 160o and an average sliding angle (SA) of 2o (Rao et al., 2021a).
Plasma surface activation involves the generation of ionized gas species in the low-temperature plasma and the bombardment of the same on to the substrate surface. Surface activation has a two-fold benefit. First, hydrogen and carbon atoms from the organic contaminants on the substrate decompose due to oxygen from plasma, form H2O and CO2, and leave the surface. Second, the pristine substrate surface is grafted with hydroxyl, carboxyl, and carbonyl functional (-(C-O)-, -(C=O)-, -(C=O)-O-, etc.) groups. The surface of an as-received substrate will be hydrophobic due to various organic contaminants and low surface free energy. The surface energy after activation increases substantially, making the surface hydrophilic, and hence, improves the wettability of the treated surface. Plasma surface activation can be used for all substrates such as paper, plastic, metal, and ceramic and other composite materials. Investigations also revealed that the functionalized surface is very active for 10 min. The high-surface free energy condition was retained for nearly 1 h and decreased slowly with time thereafter. Scratch hardness, abrasion resistance, and adhesion strength of both the UV- and thermal-cured coatings based on zirconium n-propoxide, along with 3-methacryloxypropyltrimethoxysilane and 3-glycidoxypropyl trimethoxy silane, along with titanium tetraisopropoxide on PC and polymethyl methacrylate (PMMA) substrates, were found to be substantially enhanced due to plasma surface activation (Gururaj et al., 2011; Raju et al., 2012). Similarly, improved mechanical properties were reported when TEOS, GPTMS, and aluminium-tri-sec-butoxide-based sol was applied on dielectric barrier discharge (DBD)-treated PC substrates and, subsequently, thermally cured (Kiomarsipour, 2023).
3.2 Factors affecting the sol synthesis
Sol synthesis has many variables such as the selection of proper precursor(s), water content, and judicious selection of the catalyst along with chelating agent. All of them need to be scientifically studied and optimized to find out the proper operational window for each variable to obtain consistent results to utilize the technology on a commercial scale. All of the above variables contribute significantly to identifying critical coating thickness for each composition with respect to the substrate on which the coatings were applied (Malzbender and De With, 2000). The critical thickness above which the coating cracks was investigated with a SiO2–TiO2 sol on a silica glass substrate, and it was found that the critical thickness decreased with increased water content in the sol. Such a behaviour was attributed to the surface tension of the volume of the liquid present in the pores of the gel and increased with the increase in the water content of the sol. Investigations also showed that the shrinkage along the surface of the substrate was much higher than the shrinkage in thickness, thereby inducing stress-related fractures in the coating (Garino, 1990). The use of an organically modified precursor such as methyltriethoxysilane (MTES) greatly enhanced coating thickness when added to an inorganic precursor tetraethoxysilane (TEOS) in sol synthesis. It helped in reducing the shrinkage of the hybrid layer compared to the inorganic coating, thereby reducing stress generation (Innocenzi et al., 1994).
Another important conclusion was that fractures occur at lower temperature if SiO2 and TiO2 films were thicker. It was observed that the fracturing also occurs if the coatings were subjected to lower heating rates at lower heat treatment temperatures. It was also reported that lower heating rates resulted in lower porosity in the coatings. This observation was quite similar to that of thicker coatings cracking and spalling off while they dry at ambient temperature. The coefficient of thermal expansion of the substrate material in relation to coating was also an important parameter to be considered in order to avoid thermal stress-induced cracking. The structural relaxation of the coating can be promoted by the proper selection of a chelating agent and by introducing proper organic groups such as polyvinylpyrrolidone (PVP) to suppress stress evolution during heating. This was due to PVP hybridizing with inorganic precursors through hydrogen bonds between the C=O groups of PVP and OH groups of the precursor. The investigators successfully enhanced inorganic barium titanate (BaTiO3) and lead zirconate titanate (PZT) coating thickness by 10-fold from 0.2 µm to 2 μm, when the metal oxide precursor to PVP addition was kept at a molar ratio of 1:0.5–1 (Kozuka et al., 2003).
In another study, the molar ratio of H2O/metal oxide precursor ratio was varied between 2 and 8, and the residual stress of the coating was measured. Lower stress levels were recorded for a molar ratio of 2, indicating a low degree of hydrolysis for the metal oxide precursor that resulted in crack-free coatings. In another study, investigators found that the proper selection of a chelating agent is also significant. TiO2 coating on glass with three different chelating agents, namely, acetic acid, acetylacetone, and diethanolamine, followed by heat treatment at the same temperature resulted in different residual stresses, i.e., 490 ± 60, 720± 70, and 1,090± 70, respectively (Kozuka, 2003). Such investigations are extremely necessary for each combination of a sol recipe and a substrate to obtain quality coatings, which can be adopted for large-scale production. A list of various inorganic, organic, and hybrid compositions successfully used for different functionalities is presented in Table 1. It reflects how different functionalities could be imparted to the coating based on the judicious choice of precursors or feed stock material during sol synthesis.
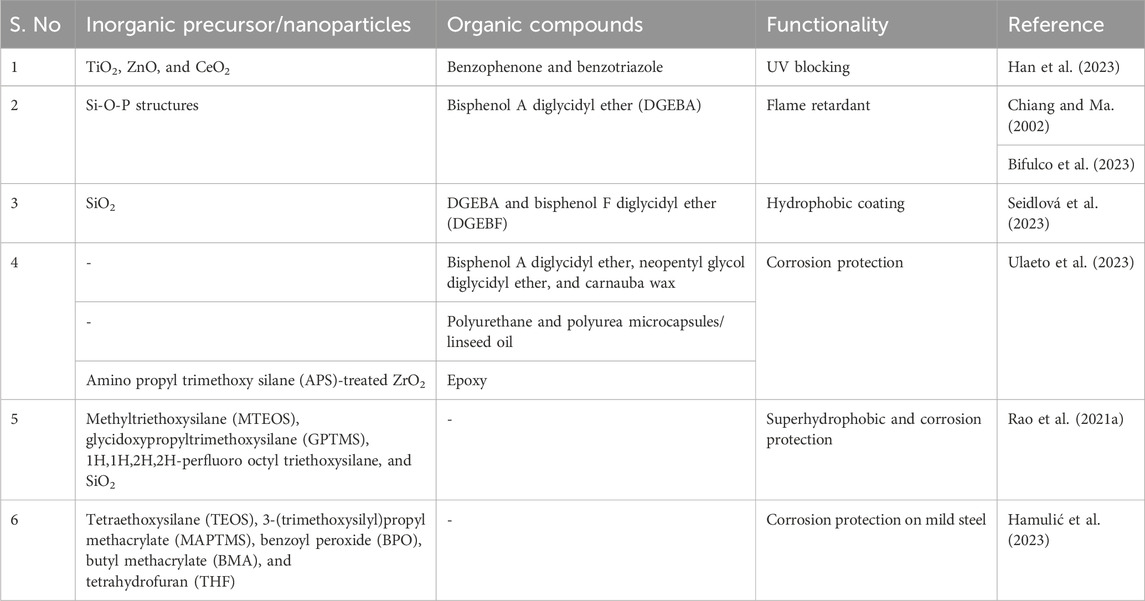
Table 1. List of various inorganic, organic, and hybrid compositions successfully used for different functionalities.
3.3 Understanding curing mechanisms
Different curing techniques have generally been employed for the densification of hybrid sol–gel coatings. Thermal curing is a high-temperature, high-energy process requiring cycle times in multiples of hours. The cycle time consists of the ramp-up time for attaining the curing temperature, soaking the coated sample at the curing temperature for a specified time, and oven cooling to bring it to ambient temperature. A long cycle time indicates low productivity and high product cost. Direct loading of the coated substrate at the soaking temperature and sudden quenching to shift the cured object to ambient temperature have also been evaluated to reduce the curing cycle time. However, heat curing requires a definite soaking time. In this regard, improvement in mechanical properties has been observed with the increase in the curing temperature and soaking time for hybrid sol–gel coatings due to increased cross-linking between organic and inorganic groups and reduced porosity. A sol derived from a combination of TEOS, 3-(trimethoxysilyl)propyl methacrylate (MAPTMS), benzoyl peroxide (BPO), butyl methacrylate (BMA), and tetrahydrofuran (THF) applied on mild steel, followed by curing at different temperatures starting from ambient temperature to 180°C, revealed that complete copolymerization/polycondensation occurred at temperatures beyond 150°C. Therefore, coatings cured at temperatures ranging from 150°C to 180°C resulted in coatings with higher hardness, lowest porosity, and improved corrosion protection compared to coatings cured at lower curing temperatures (Hamulić et al., 2023).
The main advantage of ceramic–polymer hybrid coatings derived by the sol–gel technique is that radiation curing has been possible for the polymerization of the monomer that is present in the organically modified silane precursor. UV-assisted radiation curing is generally employed for hybrid sol–gel coatings to produce tack-free coatings. In one of the reports, where radiation curing was carried out on coatings deposited on temperature-sensitive substrates like transparent plastics (Gururaj et al., 2011; Sowntharya et al., 2012), and the exposure time was in seconds, the process cost worked out to be minimum. However, it was required that a photoinitiator such as 2-hydroxy-2-methylpropiophenone (Darocur 1173) or 1-hydroxycyclohexyl phenyl ketone (Irgacure® 184) to be present in the sol composition. Any functional additive can be added to the sol composition while curing with any of the above-mentioned techniques, and no degradation of the properties was reported. UV-cured functional coatings such as hydrophobic layers were successfully developed on stainless steel objects by both dip- and spray-coating processes (Rico et al., 2023). Hard and scratch- and abrasion-resistant coatings with UV-curable hybrid sol compositions were also developed on plastic objects such as PC and PMMA. Mechanical properties of UV-cured coatings, when subjected to secondary thermal curing below the glass transition temperature of plastic substrates, showed substantial improvement (Gururaj et al., 2011).
A recent advancement in the field of radiation-assisted curing is the use of LED systems for irradiation instead of harmful UV lamps (Karasu et al., 2014). UV-LED lamps provide much cooler curing than traditional UV lamps, which is useful when curing the coatings deposited on heat-sensitive substrates. UV-LED technology can greatly reduce the environmental impact and carbon footprint without compromising the coating performance. UV-LED curing was observed to be fast, energy efficient, and safe for the operators since it does not expose them to mercury, and no ozone generation was observed. Another reason why UV-LED curing is preferred in recent times is that in the case of UV-curing formulations, in addition to the photoinitiators, UV stabilizers are added for providing durability to coatings when used under outdoor conditions. Such UV stabilizers can hinder the curing process by absorbing the UV radiation required for the photopolymerization process. This can be circumvented by using longer-wavelength radiation instead of UV illumination for the curing. A photoinitiator absorbing in the visible wavelength range when used with a LED irradiation of 385/395/405 nm could be appropriate to overcome the filtering effect of the UV absorbers/UV stabilizers that are added to photocurable formulations.
An alternative heat-curing technique that has gained significant interest is NIR curing, where NIR lamps generate heat rapidly with a very high ramp-up time, and coatings normally require low soaking and ramp-down times. The NIR curing cycle time is found to be in multiples of minutes. Similar to oven curing, coated objects can be directly loaded using a conveyorized system into the soaking temperature zone and unloaded into the ambient temperature zone if further reduction in the cycle time is warranted. However, this requires the addition of an IR absorber component during sol synthesis. Experimental investigations revealed that the properties of NIR-cured coatings with a 45-min cycle time were nearly the same as those of conventional thermal-cured hydrophobic hybrid coating compositions with a 3-h cycle time. An insignificant difference in corrosion protection properties between coatings cured by NIR and thermal techniques was noticed. A slight improvement in the mechanical properties such as abrasion resistance and functional properties such as hydrophobicity measured in terms of the WCA was observed in the conventional thermal-cured sol–gel composition, when applied on a stainless steel substrate (Rao K. S. et al., 2021).
Curing conditions were also found to be very important to obtain defect-free functional coatings. For example, in order to generate a superhydrophobic surface, different curing conditions were found to create different surface asperities, which are very important for rendering a surface superhydrophobic. The curing rate was found to dictate the surface morphology, surface roughness, and porosity of the coatings. One of the recent investigations concluded that the WCA and durability of coatings cured using an air-drying oven were higher than those of NIR-cured coatings. Coatings cured with both techniques resulted in a hierarchical micro-nano-structure essential for superhydrophobicity. However, higher durability was attributed to tall and broader asperities in air-drying oven-cured coatings (Patra et al., 2022b). The differences in the evolution of the surface topography obtained with different curing techniques are shown in Figure 6, and the results obtained were explained based on the difference in the heating rates achievable in conventional thermal and near-infrared curing methods.
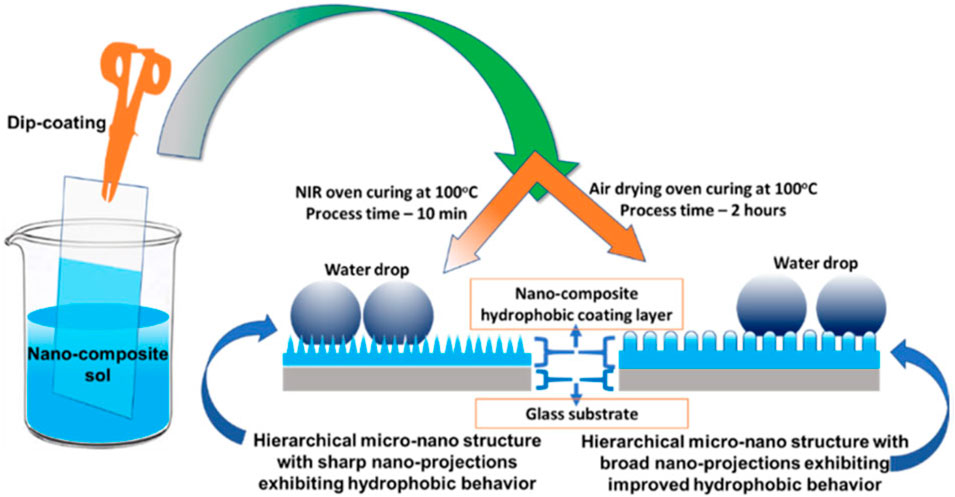
Figure 6. Difference in the evolution of surface topography obtained with different curing methods (reprinted with permission from Springer Nature—Patra et al., 2022b).
It should be mentioned here that in the case of thermal curing of coatings, heat transfer from the source of heat to the coating occurs by conduction, thereby requiring higher temperatures and longer soaking times for complete densification/crosslinking to occur. In the case of radiation-assisted curing (UV, NIR, or microwave [MW]), absorption of radiation occurs by the coating itself, which leads to volumetric heating, resulting in fast and uniform curing. In this context, MW curing is, to a certain extent, less explored than UV or NIR curing. Microwaves have been extensively used to sinter bulk ceramics, where, usually, microwave susceptors are used for preheating up to a certain temperature, after which the material itself starts to absorb and is heated rapidly. In the case of MW curing of ceramic–polymer hybrid coatings as well, a similar strategy was reported. Despite the advantages of using MW radiation for the fast curing of materials, hardly few reports have been published. A possible reason could be due to the restriction of using metal substrates in an MW field. Since metals reflect microwaves, it was not possible to cure coatings on metal substrates using microwaves. Nevertheless, promising results have been reported for investigations using microwaves for the rapid curing of coatings on plastic substrates.
MW susceptors such as SiC nanopowders were reportedly used, along with silicone, to cure silicone resin coatings on polycarbonate and polymethylmethacrylate substrates. Silicone resins were generally cured using a hardener or cured at elevated temperatures without using a hardener. In this case, no considerable curing of the coatings using microwaves was reported (Debowski, 2017). Interestingly, an improvement in the surface properties of organic–inorganic hybrid coatings on PC substrates was reported when they were cured using microwaves (Fabbri et al., 2008). In another study, poly(ethylene oxide) (PEO) or polycaprolactone (PCL) was used as an organic component, and an inorganic network derived from TEOS was used to obtain the hybrid coating, which was deposited on PC substrates and subjected to both microwave and conventional oven curing. Microwave irradiation led to cross-linked coatings with a process time of few seconds (5–10 s), whereas the same level of conversion degree was reached in approximately 40 min in the case of oven heating. The scratch hardness of the microwave-cured coatings was comparable to that of the oven-cured coating. The authors concluded that the possibility of performing fast curing processes through microwave irradiation represented an attractive possibility for scaling up this application (Fabbri et al., 2008). In a comparative study of different curing techniques on SiO2–TiO2 hybrid coatings on polycarbonate, hybrid nanocomposite coatings derived from titanium tetraisopropoxide and an acrylic modified silane (methacryloxypropyltrimethoxysilane) by the sol–gel method were deposited on PC. The coatings were cured by thermal, MW, and ultraviolet (UV) radiations independently and in a combined mode, and the mechanical properties of the coatings, along with their optical properties, were compared. The pencil scratch hardness of the conventionally cured coating was found to be maximum, i.e., 3H for coatings generated using a withdrawal speed of 6 mm/s, and it was found to be maximum when compared to only UV- or MW-cured coatings. Microwave curing, followed by UV curing, showed a marked improvement in pencil scratch hardness (2H) compared to that of only MW or UV curing, whereas MW+UV curing took only 6 min for the completion of the curing process compared to the 4-h cycle time for conventional thermal curing. They concluded that fine-tuning in the dual curing process (MW+UV) to obtain uniform thickness on both sides with further enhancement in mechanical properties provided substantial time saving for curing of the coatings and, from a technological point of view, will prove to be a very good alternative to thermal curing.
Recently, curing using an atmospheric-pressure plasma jet (JET) has also gained interest. It was found that using plasma as a curing source helps manufacturing processes become more efficient, in addition to producing products of higher quality and improving versatility. It was also claimed that the combination of sol–gel coating and plasma treatment provides new opportunities for developing surfaces with improved mechanical, chemical, and biochemical properties. The use of an atmospheric pressure plasma source for curing thicker sol–gel layers ensured complete, uniform, and faster curing, in addition to functionalizing the coating in a single step. In order to cure thick coatings, usually, a combination of UV and thermal curing is adopted. In a recent study, copper micropowders were introduced into the plasma jet, which was then used to cure a hybrid sol–gel coating. The plasma jet helped in ex situ introducing the copper into the sol–gel matrix and curing the sol–gel coating (Chwatal et al., 2022). Investigators also compared the feasibility of using advanced plasma technologies, such as diffuse coplanar surface barrier discharge (DCSBD), gliding arc (GA), and JET, for the modification of sol–gel coatings on a microscopic level under controlled conditions. Coating hardness and adhesion to the substrate were found to improve significantly after the plasma jet curing (Chwatal et al., 2024).
There is also interest in depositing sol–gel films using a cold atmospheric pressure plasma (CAPP) jet, followed by conventional oven curing to yield hard and corrosion-resistant barrier coatings on metal substrates. In a recent study, investigators used the CAPP jet for plasma-assisted polymerization of SiOxCy organosilicon thin films, followed by conventional post curing in air within a short duration of 96 s to substantially improve the scratch and corrosion resistance of Al alloy (AA) 1050 (Lin et al., 2024).
3.4 Long-term stability (shelf life) of the sol
Any coating that is aimed for scaling up for large-scale industrial applications requires stability of the sol for a certain time period, during which the coating characteristics such as coating thickness, adhesion strength, scratch hardness, and corrosion protection property should not vary with time. The sol–gel synthesis process is a continuous chain process, where hydrolysis and condensation reactions take place one after the other. The size of nanoparticles in the sol grows with time. As a result, a transparent coating from a fresh sol, where the particle is nano-sized, can became a translucent and opaque coating thereafter, even if the coating deposition parameters were not changed (Adelkhani et al., 2007). The degree of polymerization of organic groups increases, leading to an increase in viscosity over time. The corrosion protection property of the coatings was reported to decrease with the ageing of the sol. There is a definite time window during which the viscosity of the sol is nearly stable for each composition and suitable to obtain defect-free coatings. The reaction kinetics of the sol can be decreased, and its shelf life increased by storing the sol at sub-zero temperatures. Excessive condensation in the sol during longer ageing deteriorated coating properties (Yasakau et al., 2014; Agustín-Sáenz et al., 2019).
Apart from sol stability, coating stability under the envisaged service condition should also be investigated for developing industrial applications. Long-term stability of methyltrimethoxysilane (MTMS) and colloidal SiO2-based matrix sol, along with a 1H-benzotriazole (BTA)-encapsulated zeolitic imidazolate framework-8 (ZIF-8) core, i.e., BTA-ZIF-8, and silica-coated BTA-ZIF-8 nano-containers as corrosion inhibitor-coated aluminum alloy AA 1060 substrates were assessed for 28 days of immersion in 3.5% NaCl solution. It was observed that silica shell encapsulation of the inhibitor improved compatibility with the matrix sol coating and exhibited excellent corrosion protection and self-healing properties (Huang et al., 2023).
An anti-reflective coating with simple TEOS and ethanol-based sol using NH3 (aq) as a catalyst was applied on glass after ageing for 14 days. The mechanical stability of the silica coatings was enhanced by exposing them to an ammonia atmosphere prior to curing at 130°C for 1 h, where the coating hardness was increased to 2H and 100% peak transmittance was obtained as against 92% transmittance on uncoated glass (Chi et al., 2020). In another work, it was reported that an appropriate selection of precursors and catalyst exhibited a stable superhydrophobic coating under extreme working conditions such as low or high temperature, sand impact, and water flow (Zhang et al., 2017).
Hydrophobic sol-coated, aluminium samples were subjected to five different tests to evaluate their stability: the coated sample was heated to 100°C in an oven, with the coated substrate side facing down kept at a distance of 3 cm and exposed to boiling water vapour and air stream; coated samples submerged in deionized water maintained at 20°C and 90°C separately, while the exposure time was fixed at 7 h for each test to evaluate factors influencing coating degradation; coatings were robust and intact, except in the test where the coated sample was submerged in 90°C boiling water (Basso et al., 2023).
4 Discussion on the most researched applications of ceramic–polymer hybrid coatings
Since it is not possible to discuss all the possible applications, few exciting applications of ceramic–polymer hybrid coatings are described below. The two most researched nature-inspired phenomena are 1) superhydrophobicity and (2) self-healing.
4.1 Superhydrophobicity
Superhydrophobicity is a phenomenon, and its applications for anticorrosion, antibacterial, antireflective, antifouling, and anti-icing properties arise as a consequence. Hydrophobicity, as the name suggests, is the characteristic of any surface to repel water. The degree to which water can be repelled is quantified in terms of the WCA (Ɵ). When Ɵ is greater than 90o and less than 150o, it is termed as a hydrophobic surface, and when Ɵ is greater than 150°, it is called a superhydrophobic surface. However, it is not only the water contact angle that qualifies a superhydrophobic surface.
There are two additional parameters, namely, the sliding angle (SA) and contact angle hysteresis (CAH), that a surface needs to fulfil with respect to the required conditions in order to be labelled as a superhydrophobic surface. For a superhydrophobic surface, WCA >150°, the sliding angle <5°, and CAH <10°, or, in other words, water drops tend to roll off from the surface. Superhydrophobicity is observed to be exhibited by many species of flora and fauna such as lotus leaves, tropical leaves such as moringa leaves (Sridar et al., 2014), fenugreek leaves, cicadas, butterfly wings, and gecko feet. The most common example of a superhydrophobic surface is the lotus leaf, and the reason attributed to this property is the hierarchical micro-nano-structure, along with the low-surface free energy wax present on its surface. Essentially, a combination of a physical and chemical modification of the surface is required to render a surface superhydrophobic, as shown in Figure 7 (Subasri et al., 2012).
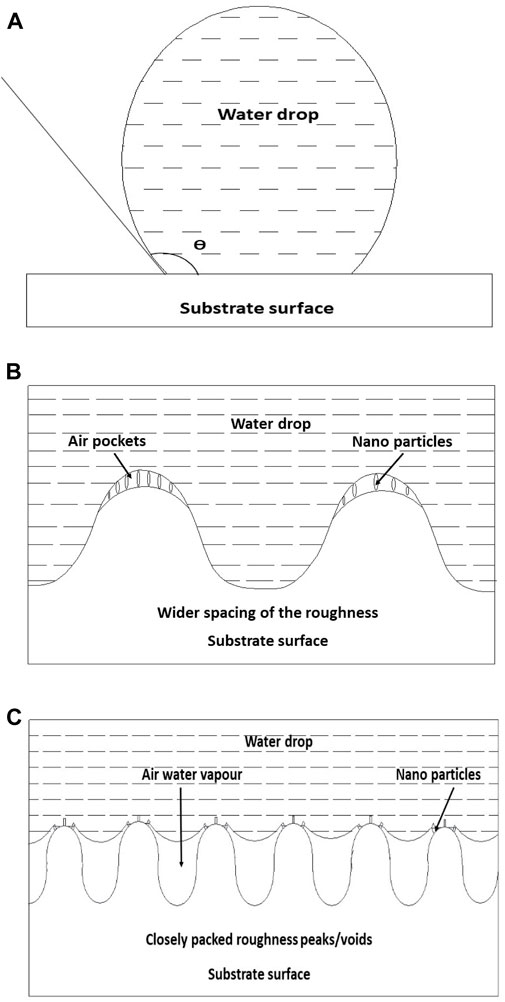
Figure 7. Schematic diagram showing the wetting behaviour of the pigmented hydrophobic surface. (A) Spherical water droplet sitting on the substrate surface; (B, C) magnified view of the contact area in the case of coating according to Wenzel and Cassie–Baxter models, respectively (reprinted with permission from Elsevier—Subasri et al., 2012).
A lot of factors affect the degree of superhydrophobicity, such as the nature of the low-surface energy material, the height and shape of the protrusions creating the micro/nano-roughness, and the distance between the protrusions. Several review papers discuss the fundamentals of the phenomenon of superhydrophobicity (Ganesh et al., 2011; Jeevahan et al., 2018; Liravi et al., 2020). Cassie–Baxter and Wenzel have proposed different models to explain the process of wetting in superhydrophobic surfaces. Satdive et al. (2023) provided a comprehensive review of superhydrophobic (SHP) surfaces, mapping the current research trends and recent advances. Figure 8 shows the country-wise publication of review papers on SHP coatings for the period 2019–2024, as obtained by search using the Scopus database. It was interesting to note that China is leading in the publication of reviews on SHP coatings, followed by India, which is followed by the United States. This also indicates the importance of the development of superhydrophobic surfaces for diverse applications.
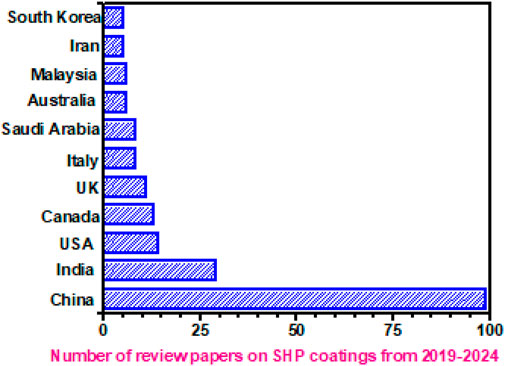
Figure 8. Country-wise publication of review papers on SHP coatings (www.scopus.com) for the period 2019–2024. Accessed as on April 2024.
Superhydrophobic surfaces can be generated by various methods (Manoharan and Bhattacharya, 2019), which can be broadly classified as top-down and bottom-up approaches, or sometimes, a combination of both. Basically, a micro-nano-dual roughness structure, along with low-surface free energy material, will render a surface superhydrophobic. Hence, in order to generate such a surface, either a material removal strategy to create the dual-scale roughness can be adopted (top-down) or a wet chemical route where ceramic nanoparticles modified with low-surface energy materials can be introduced into the coating matrix to create the dual-scale roughness (bottom-up). The material removal strategies can be any of the following: chemical/electrochemical etching, shot peening/shot blasting, lithography, laser micromachining (Pradheebha et al., 2018; Deng and Ki 2020), templating, and electric discharge machining. The bottom-up approaches include the sol–gel technique, layer-by-layer method, and electrochemical methods like anodization, electrodeposition, and electrospinning. Figure 9 summarizes the different methods for preparing SHP surfaces.
One of the wet chemical methods for producing superhydrophobic surfaces involve the use of aerogel beads made of amorphous SiO2 with 99.8% porosity, along with a polymer for coating deposition on metallic substrates (Samaha et al., 2012). Superhydrophobic surfaces can be used for different applications, such as anti-icing (Chauhan et al., 2022), self-cleaning, biofilm inhibition (Song and Mano, 2013), antifouling (Vanithakumari et al., 2015; Kumar et al., 2023), reducing drag reduction (Liravi et al., 2020), antireflection (Satya and Ponraj, 2023), and corrosion protection (Satdive et al., 2023). The entrapped air in the pores of the rough superhydrophobic surface was reported to be responsible for the drag reduction.
4.1.1 Challenges
It is not difficult to generate a superhydrophobic surface by any of the above-mentioned techniques. However, the inherent challenge in the case of superhydrophobic surfaces, which researchers have been investigating for quite some time, was their durability. Retention of the superhydrophobic property after mechanical stresses were introduced that tend to destroy the hierarchical microstructure, and prolonged submergence of the coated surface in water result in the escape of air from the pockets, as shown in Figure 10, and cause the failure of the hierarchical structure of the surface just like a falling pack of cards. The rough structures of superhydrophobic surfaces can also be destroyed under high pressure and humidity, causing the loss of water-repelling characteristics. In order to circumvent this, either passive regeneration or active repairing has been investigated. Creating durable superhydrophobic surfaces for practical applications is still a recent advancement, which leaves sufficient room for further investigations.
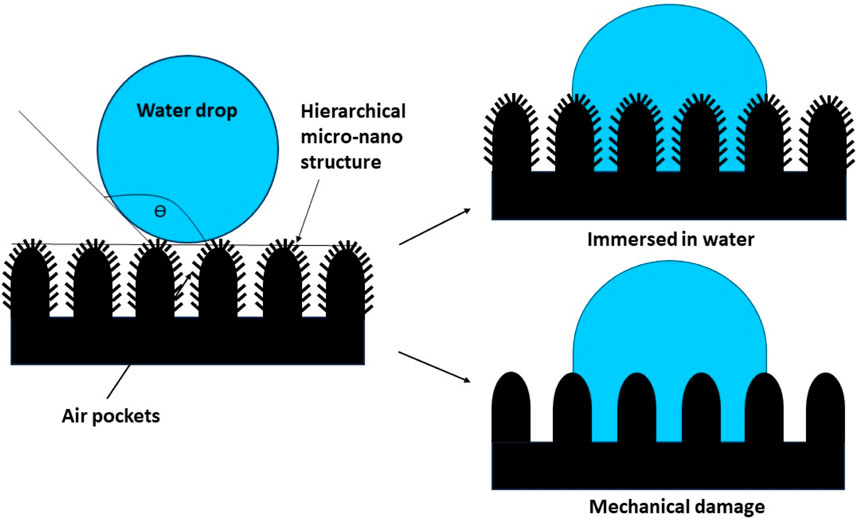
Figure 10. Superhydrophobic surface and its failure under different circumstances, such as prolonged immersion in water and mechanical damage to the surface features.
4.1.2 Recent advances
A recent development in this direction has been the slippery liquid-infused porous surfaces (SLIPSs) that could be more stable than a superhydrophobic surface and which was inspired by Nepenthes or the tropical pitcher plant. SLIPSs consist of a lubricant liquid that is entrapped in the porous structure of superhydrophobic coatings (Samaha and Gad-el-Hak, 2021; He et al., 2023; Tripathi et al., 2023). The SLIPS surface is shown in Figure 11. The lubricating liquid film can serve as a self-healing coating that rapidly restores the slippery properties when the SLIPS is damaged via abrasion or impact, as shown in the schematic diagram.
SLIPSs can exhibit very effective icephobic properties. The icephobic performance of a one-step silicone oil-infused slippery coating was investigated (Cui and Pakkanen, 2019). The coating matrix was made up of polyvinylidene fluoride (PVDF), along with hydrophobic silica nanoparticles. This slightly hydrophobic coating was infused with 20 wt% silicone oil to provide the icephobic properties. The silica nanoparticles were used to anchor the oil over the layer. The addition of nanoparticles not only secured the lubricant binding in the textures but also endowed surface dryness for contaminant rejection (Cui and Pakkanen, 2019).
Recently, a solvent-free method for generating slippery coating from edible raw materials was reported for reducing yoghurt adhesion (Hao et al., 2022). Most of the slippery coatings that have been reported were solvent-based. There have also been reports on aqueous coating compositions for generating robust, slippery, transparent coatings on various substrates (Baidya et al., 2018).
Other interesting approaches have been employed to generate slippery surfaces such as UV illumination of PDMS-coated silicon substrates, where PDMS dissociated and played two roles: (i) to reduce the surface free energy and (ii) as a lubricating oil. This approach was environmentally friendly since it did not involve the use of perfluoroalkyl silanes that are generally employed for reducing the surface free energy (Tesler et al., 2021).
However, the apparent limitation of SLIPSs was that the liquid lubricant layer can be easily removed after large-area abrasion, which degrades their slippery performance. The recent development in this area is the self-repairing property of SLIPSs (Rao Q. et al., 2021). Another interesting consequential application of superhydrophobic surfaces or SLIPSs was for reducing bacterial cell adhesion or biofilm inhibition or antifouling (Wei et al., 2016). There have been several reports where the role of the surface micro/nanostructure in bacterial cell adhesion behaviour has been studied (Hejazi et al., 2015; Patra et al., 2022a).
Silica nanoparticles have been introduced either in a polymer matrix or an organic–inorganic hybrid sol–gel matrix, where the low-surface energy-modified silica nanoparticles provide the roughness to render the superhydrophobic properties, as shown in Figure 12.
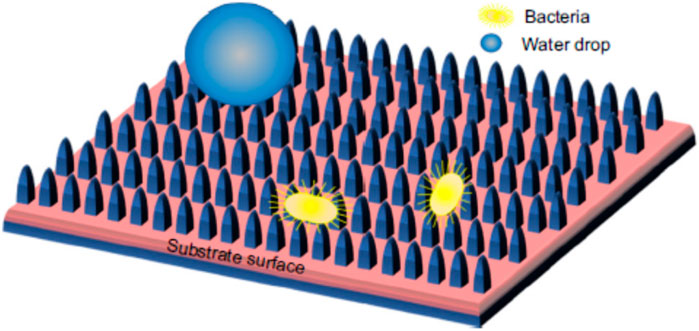
Figure 12. Schematic diagram showing the anti-adhesion property of a superhydrophobic surface to bacteria and water (reprinted with permission from Elsevier—Patra et al., 2022a).
Although the strategy of using SHP for biofilm inhibition is an environmentally friendly method, the challenge in using SHP or SLIPS for antifouling or antibacterial applications was that there could be a threshold in the antibacterial action of such surfaces, as reported by Ellinas et al. (2017). Hence, a heavy metal-free environmentally friendly bactericide added along with the superhydrophobic surface could be a durable solution to provide longstanding antibacterial activity. SLIPSs are also widely investigated as a solution to prevent marine fouling (Deng et al., 2020). Water quality monitoring equipment and sensors made of glass used in ocean research instrumentation require proper maintenance due to marine biofouling. Transparent ceramic coatings have also been employed for antifouling applications for marine optical windows (Dineshram et al., 2009).
4.1.3 Corrosion protection
Another interesting consequential application of superhydrophobic surfaces on metal substrates is for corrosion protection (Deng et al., 2020). Recently, self-healing coatings for corrosion protection have gained increasing interest. This phenomenon was also nature-inspired and stems from autonomous healing exhibited by the human body. In the case of coatings on metal substrates, whenever there was damage that extends deep down to the substrate, it initiated the corrosion process; the presence of self-healing materials, mostly a corrosion inhibitor encapsulated in a nanocontainer, in the coating matrix healed the damage, thereby improving the corrosion protection properties of the coating. Inorganic nanocontainers like halloysite nanotubes and layered clays like montmorillonite have been explored to encapsulate organic/inorganic corrosion inhibitors.
Researchers have studied the self-healing ability of corrosion inhibitor benzotriazole loaded into a tubular nanocontainer such as halloysite nanoclay, as shown in Figure 13, added to a sol–gel matrix and deposited on mild steel substrates. The effect of capping the ends of the inhibitor-loaded clay nanotubes was studied, and it was found that capping using urea–formaldehyde nanocapsules enabled a slow release of the corrosion inhibitor benzotriazole in the event of damage in the coating, thereby improving the durability of the protective coating (Gautam et al., 2022).
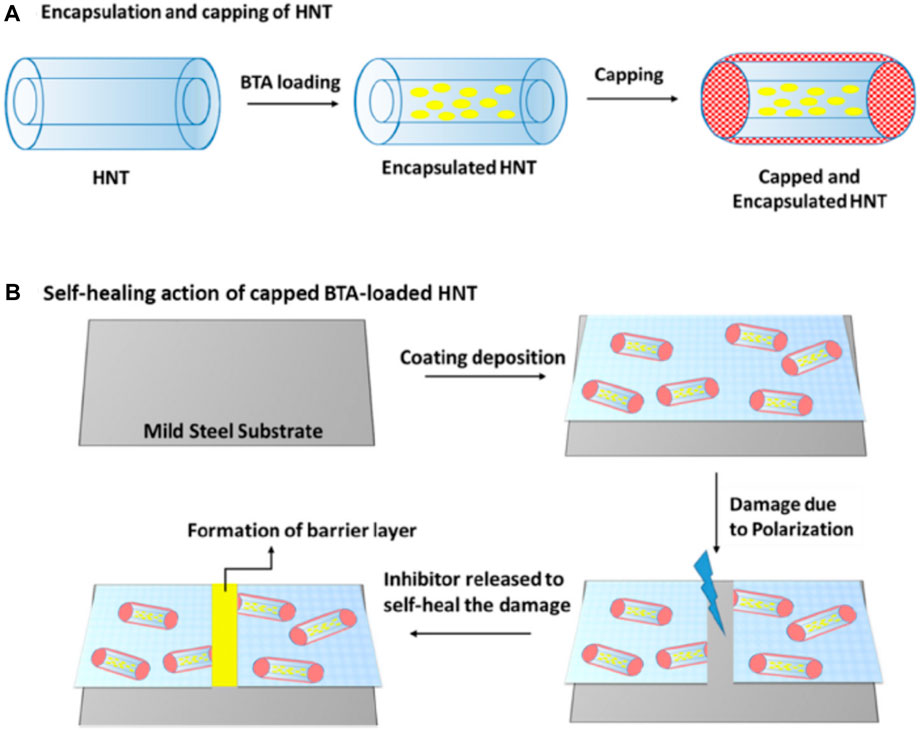
Figure 13. Proposed mechanism of (A) encapsulation and capping of Halloysite nanotubes (HNTs) and (B) automatic healing of the surface defects after the release of the corrosion inhibitor (reprinted with permission from Elsevier–Gautam et al., 2022).
Such self-healing materials can either be introduced into a sol–gel matrix or a polymer matrix to generate the self-healing coatings and can be used on metallic substrates. Adsul et al. (2017) introduced inorganic corrosion inhibitors such as Ce3+/Zr4+ into halloysite nanoclay tubes and dispersed the inhibitor-loaded nanocontainers into a sol–gel matrix and studied the self-healing effect by a scanning vibrating electrode technique, where localized anodic currents were mapped as a function of time after introducing artificial damage by scribing, followed by exposure to a corrosive medium such as 3.5 wt% NaCl. Figure 14 shows that the anodic currents were suppressed after some time in the case of self-healing coatings, which was possible due to the self-healing effect (Adsul et al., 2017; Gautam et al., 2022).
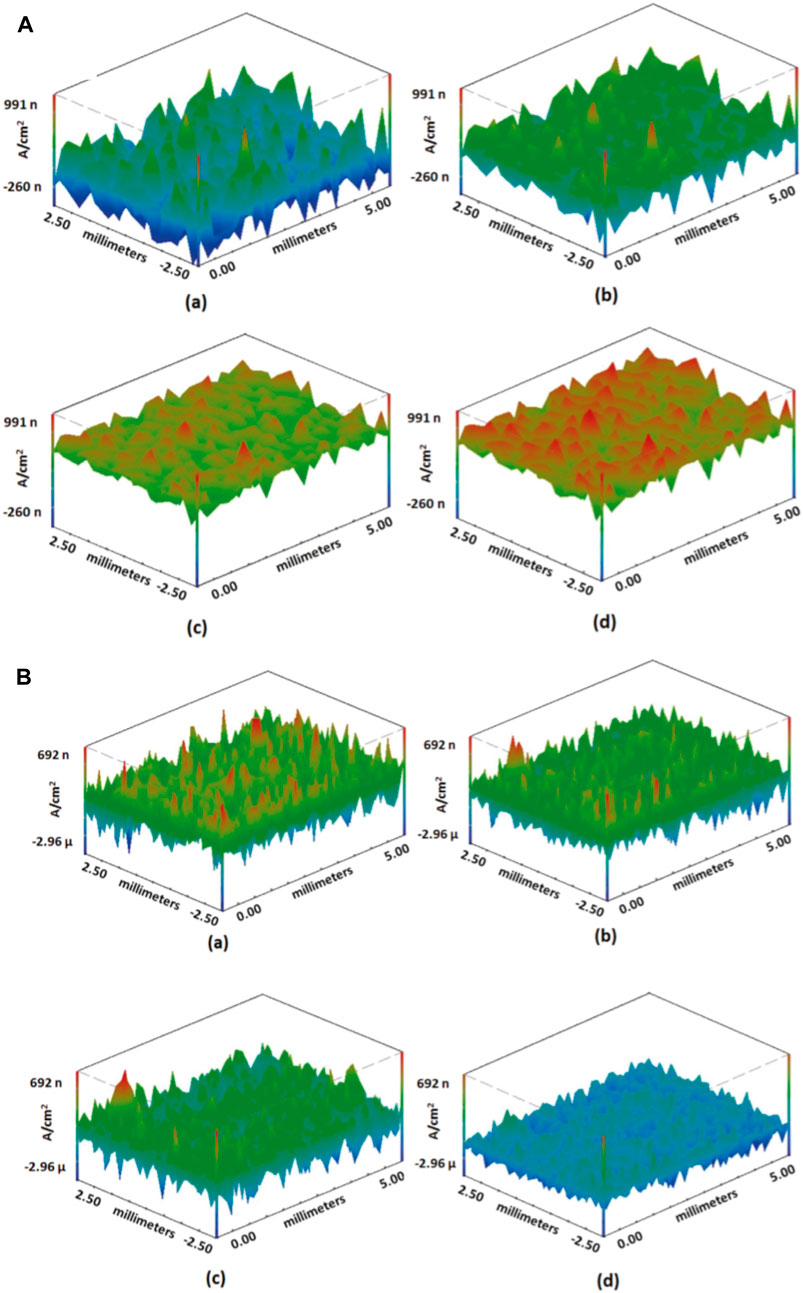
Figure 14. Current density maps for (A) bare and (B) matrix sol-coated AZ91 after exposure to 3.5 wt% NaCl: (A) initial, (B) after 1 h, (C) after 12 h, and (D) after 24 h (reprinted with permission from Elsevier—Adsul et al., 2017).
It can be discerned from the above discussions that there is a huge scope for the applications of ceramic–polymer hybrid nanocomposite coatings on various substrates for diverse and niche applications, where a pure ceramic coating or a pure polymer coating may not be appropriate. Other than the above applications, ceramic–polymer hybrid coatings are popularly used as scratch/abrasion-resistant coatings on transparent polymer substrates like PMMA or PC. Since these substrates are temperature-sensitive, it is not possible to deposit pure ceramic coatings, which may require high temperatures for curing. In such cases, a ceramic–polymer coating is appropriate, where ceramic nanoparticles such as silica, alumina, titania, or zirconia were dispersed in a hybrid sol–gel matrix. The organic component of the matrix helps in curing at low temperatures. The ceramic fillers help in imparting the improved scratch/abrasion resistance to the polymer substrate (Gururaj et al., 2011; Sowntharya et al., 2013).
5 Conclusion
Various aspects of ceramic and ceramic–polymer hybrid sol–gel coatings have been discussed. Pure ceramic and pure polymer coatings have limitations in using for a wide variety of applications due to the high-temperature heat treatment requirement for the former and poor mechanical properties of the latter. Hence, ceramic–polymer hybrid coatings are the need of the hour for use in diverse applications on different substrates. The technological aspect of the sol–gel science needs further research in understanding the factors affecting the sol synthesis and shelf life, improving adhesion strength, and curing the coatings under ambient conditions. Furthermore, bioinspired multifunctional coatings that mimic complex geometrics of the lotus leaf and pitcher plant first act as simple barriers for corrosion species and protect the coated surface from corrosion and, second, by the nature acquired from the nano-scale geometry and the hierarchical surface roughness and surface modification, exhibit hydrophobic property and protect the surface by repelling the water body coming into contact with the surface, thereby keeping the surface clean. The review has discussed most of the applications derived from the hybrid coatings, keeping in view the possibility of the commercialization of such coatings. Although there are still several challenges to be worked on for practical use, the research on such coatings is evolving with time, solving the challenges step by step, thereby increasing the possibility of commercialization.
Author contributions
SKRC: writing–original draft and writing–review and editing. SR: conceptualization, writing–original draft, and writing–review and editing. RK: writing–original draft and writing–review and editing.
Funding
The author(s) declare that no financial support was received for the research, authorship, and/or publication of this article.
Acknowledgments
The authors thank the Director, ARCI, Hyderabad, for the constant encouragement provided throughout the course of writing this chapter. The authors would like to thank Prof Shrikant V Joshi for the encouragement and support provided.
Conflict of interest
The authors declare that the research was conducted in the absence of any commercial or financial relationships that could be construed as a potential conflict of interest.
Publisher’s note
All claims expressed in this article are solely those of the authors and do not necessarily represent those of their affiliated organizations, or those of the publisher, the editors, and the reviewers. Any product that may be evaluated in this article, or claim that may be made by its manufacturer, is not guaranteed or endorsed by the publisher.
References
Adelkhani, H., Mellatnavaz, B., Roohi, H., and Noorbakhsh, M. (2007). New sol-gel solution with 45 days stability for preparation silica thin films. Iran. J. Chem. Chem. Eng. 26, 25–29. doi:10.30492/IJCCE.2007.7627
Adsul, S. H., Siva, T., Sathiyanarayanan, S., Sonawane, S. H., and Subasri, R. (2017). Self-healing ability of nanoclay-based hybrid sol-gel coatings on magnesium alloy AZ91D. Surf. Coatings Technol. 309, 609–620. doi:10.1016/j.surfcoat.2016.12.018
Agustín-Sáenz, C., Martín-Ugarte, E., Jorcin, J. B., Imbuluzqueta, G., Santa Coloma, P., and Izagirre-Etxeberria, U. (2019). Effect of organic precursor in hybrid sol–gel coatings for corrosion protection and the application on hot dip galvanised steel. J. Sol-Gel Sci. Technol. 89, 264–283. doi:10.1007/s10971-018-4840-6
Baidya, A., Das, S. K., and Pradeep, T. (2018). An aqueous composition for lubricant-free, robust, slippery, transparent coatings on diverse substrates. Glob. Challenges 2, 1700097. doi:10.1002/gch2.201700097
Barua, N. K., Ragini, T., and Subasri, R. (2017). Sol-gel derived single-layer zeolite-based coatings on glass for broadband antireflection properties. J. Non Cryst. Solids 469, 51–55. doi:10.1016/j.jnoncrysol.2017.04.016
Bashta, B., Brostow, W., Granowski, G., and Hnatchuk, N. (2016). Modification of poly(vinyl chloride) + epoxy systems for improved thermal and aging stability. Macromol. Symp. 365, 239–245. doi:10.1002/masy.201650023
Basso, M., Colusso, E., Tancon, M., Bortolin, S., Mirafiori, M., Guglielmi, M., et al. (2023). Hydrophobic hybrid silica sol-gel coating on aluminium: stability evaluation during saturated vapour condensation. J. Non-Crystalline Solids X 17, 100143. doi:10.1016/j.nocx.2022.100143
Bifulco, A., Avolio, R., Lehner, S., Errico, M. E., Clayden, N. J., Pauer, R., et al. (2023). In situ P-modified hybrid silica-epoxy nanocomposites via a green hydrolytic sol-gel route for flame-retardant applications. ACS Appl. Nano Mater 6, 7422–7435. doi:10.1021/acsanm.3c00590
Branda, F., Grappa, R., Costantini, A., and Luciani, G. (2023). Sol–gel approach for fabricating silica/epoxy nanocomposites. Polym. (Basel) 15, 2987. doi:10.3390/polym15142987
Cai, G., Wang, H., Jiang, D., and Dong, Z. (2018). Degradation of fluorinated polyurethane coating under UVA and salt spray. Part I: corrosion resistance and morphology. Prog. Org. Coatings 123, 337–349. doi:10.1016/j.porgcoat.2018.07.025
Catauro, M., Tranquillo, E., Dal Poggetto, G., Pasquali, M., Dell’Era, A., and Ciprioti, S. V. (2018). Influence of the heat treatment on the particles size and on the crystalline phase of TiO2 synthesized by the sol-gel method. Mater. (Basel) 11, 2364. doi:10.3390/ma11122364
Chauhan, K. V., Desai, M. K., and Patel, A. C. (2022). Recent progress in the development and anti-icing applications of superhydrophobic coatings. Mater Today Proc. 62, 3922–3928. doi:10.1016/j.matpr.2022.04.556
Chi, F., Zeng, Y., Liu, C., Liang, D., Li, Y., Xie, R., et al. (2020). Enhancing mechanical stability of sol-gel silica antireflection coatings via ammonia treatment at low temperature. Results Phys. 18, 103315. doi:10.1016/j.rinp.2020.103315
Chiang, C. L., and Ma, C. C. M. (2002). Synthesis, characterization and thermal properties of novel epoxy containing silicon and phosphorus nanocomposites by sol-gel method. Eur. Polym. J. 38, 2219–2224. doi:10.1016/S0014-3057(02)00123-4
Chwatal, S., Stummer, M., Steiner, H., Brandner, A., P¨olzl, S., Kittinger, C., et al. (2022). Cross-linking processes in antimicrobial UV-sol-gel systems initiated by atmospheric pressure plasma. Thin Solid Films 763, 139598. doi:10.1016/j.tsf.2022.139598
Chwatal, S., Zazˇı´mal, F., Bursˇı´kova´, V., Kaindl, R., and Homola, T. (2024). Modification of silicon-polyurethane-based sol–gel coatings through diverse plasma technologies: investigation of impact on surface properties. New J. Chem. 48, 5232–5246. doi:10.1039/d3nj05986c
Cui, W., and Pakkanen, T. A. (2019). Icephobic performance of one-step silicone-oil-infused slippery coatings: effects of surface energy, oil and nanoparticle contents. J. Colloid Interface Sci. 558, 251–258. doi:10.1016/j.jcis.2019.09.119
Debowski, M. A. (2017). Low temperature microwave processing of silicone resin coatings containing microwave susceptors. Surf. Coat. Technol. 320, 13–17. doi:10.1016/j.surfcoat.2017.02.030
Deng, C., and Ki, H. (2020). Tunable wetting surfaces with interacting cavities via femtosecond laser patterning and wet etching. J. Appl. Phys. 128. doi:10.1063/5.0011885
Deng, R., Shen, T., Chen, H., Lu, J., Yang, H. C., and Li, W. (2020). Slippery liquid-infused porous surfaces (SLIPSs): a perfect solution to both marine fouling and corrosion? J. Mater Chem. A 8, 7536–7547. doi:10.1039/d0ta02000a
Dineshram, R., Subasri, R., Somaraju, K. R. C., Jayaraj, K., Vedaprakash, L., Ratnam, K., et al. (2009). Biofouling studies on nanoparticle-based metal oxide coatings on glass coupons exposed to marine environment. Colloids Surfaces B Biointerfaces 74, 75–83. doi:10.1016/j.colsurfb.2009.06.028
Ellinas, K., Kefallinou, D., Stamatakis, K., Gogolides, E., and Tserepi, A. (2017). Is there a threshold in the antibacterial action of superhydrophobic surfaces? ACS Appl. Mater Interfaces 9, 39781–39789. doi:10.1021/acsami.7b11402
Fabbri, P., Leonelli, C., Messori, M., Pilati, F., Toselli, M., Veronesi, P., et al. (2008a). Improvement of the surface properties of polycarbonate by organic–inorganic hybrid coatings. J. Appl. Polym. Sci. 108, 1426–1436. doi:10.1002/app.27765
Fabbri, P., Messori, M., Toselli, M., Veronesi, P., Rocha, J., and Pilati, F. (2008b). Enhancing the scratch resistance of polycarbonate with poly(ethylene oxide)–silica hybrid coatings. Adv. Polym. Technol. 27 (2), 117–126. doi:10.1002/adv.20122
Falcaro, P., Costacurta, S., Malfatti, L., Buso, D., Patelli, A., Schiavuta, P., et al. (2011). Chemical tailoring of hybrid sol-gel thick coatings as hosting matrix for functional patterned microstructures. ACS Appl. Mater Interfaces 3, 245–251. doi:10.1021/am100901m
Ganesh, V. A., Raut, H. K., Nair, A. S., and Ramakrishna, S. (2011). A review on self-cleaning coatings. J. Mater Chem. 21, 16304–16322. doi:10.1039/c1jm12523k
Garino, T. J. (1990). The cracking of sol-gel films during drying. MRS Proc. 180, 497–506. doi:10.1557/proc-180-497
Gautam, A., Siva, T., Sathiyanarayanan, S., Gobi, K. V., and Subasri, R. (2022). Capped inhibitor-loaded halloysite nanoclay-based self-healing silica coatings for corrosion protection of mild steel. Ceram. Int. 48, 30151–30163. doi:10.1016/j.ceramint.2022.06.288
Gururaj, T., Subasri, R., Raju, K. R. C. S., and Padmanabham, G. (2011). Effect of plasma pretreatment on adhesion and mechanical properties of UV-curable coatings on plastics. Appl. Surf. Sci. 257, 4360–4364. doi:10.1016/j.apsusc.2010.12.060
Hamulić, D., Medoš, G., Korte, D., Rodič, P., and Milošev, I. (2023). The effect of curing temperature and thickness of polybutyl methacrylate siloxane coatings on the corrosion protection of structural steel S355. Coatings 13, 675. doi:10.3390/coatings13040675
Han, D. C., Kim, H., and Kwak, G. (2023). Benzotriazole-containing fluorinated acrylic polymer coatings with high thermal stability, low surface energy, high visible-light transparency, and UV-blocking performance. Polym. Bull. 80, 5641–5654. doi:10.1007/s00289-022-04340-w
Hao, P., Lou, X., Tang, L., Wang, F., Chong, Z., and Guo, L. (2022). Solvent-free fabrication of slippery coatings from edible raw materials for reducing yogurt adhesion. Prog. Org. Coatings 162, 106590. doi:10.1016/j.porgcoat.2021.106590
He, S., Gao, Y., Wu, C., Chen, Z., and Cen, H. (2023a). A self-healing and anticorrosion epoxy coating based on the novel polymer filler containing a side-linked grafting 2-mercaptobenzothiazole. J. Mater Res. Technol. 26, 1107–1121. doi:10.1016/j.jmrt.2023.07.264
He, Z., Mu, L., Wang, N., Su, J., Wang, Z., Luo, M., et al. (2023b). Design, fabrication, and applications of bioinspired slippery surfaces. Adv. Colloid Interface Sci. 318, 102948. doi:10.1016/j.cis.2023.102948
Hejazi, I., Seyfi, J., Hejazi, E., Sadeghi, G. M. M., Jafari, S. H., and Khonakdar, H. A. (2015). Investigating the role of surface micro/nano structure in cell adhesion behavior of superhydrophobic polypropylene/nanosilica surfaces. Colloids Surfaces B Biointerfaces 127, 233–240. doi:10.1016/j.colsurfb.2015.01.054
Huang, Y., Zhao, C., Li, Y., Wang, C., Shen, T., Cheng, D., et al. (2023). Development of self-healing sol-gel anticorrosion coating with pH-responsive 1H-benzotriazole-inbuilt zeolitic imidazolate framework decorated with silica shell. Surf. Coatings Technol. 466, 129622. doi:10.1016/j.surfcoat.2023.129622
Huynh, V., Ngo, N. K., and Golden, T. D. (2019). Surface activation and pretreatments for biocompatible metals and alloys used in biomedical applications. Int. J. Biomater. 2019, 1–21. doi:10.1155/2019/3806504
Innocenzi, P., Abdirashid, M. O., and Guglielmi, M. (1994). Structure and properties of sol-gel coatings from methyltriethoxysilane and tetraethoxysilane. J. Sol-Gel Sci. Technol. 3, 47–55. doi:10.1007/BF00490148
Jeevahan, J., Chandrasekaran, M., Britto Joseph, G., Durairaj, R. B., and Mageshwaran, G. (2018). Superhydrophobic surfaces: a review on fundamentals, applications, and challenges. J. Coatings Technol. Res. 15, 231–250. doi:10.1007/s11998-017-0011-x
Jeevajothi, K., Crossiya, D., and Subasri, R. (2012). Non-fluorinated, room temperature curable hydrophobic coatings by sol-gel process. Ceram. Int. 38, 2971–2976. doi:10.1016/j.ceramint.2011.11.075
Kajihara, K. (2013). Recent advances in sol-gel synthesis of monolithic silica and silica-based glasses. J. Asian Ceram. Soc. 1, 121–133. doi:10.1016/j.jascer.2013.04.002
Karasu, F., Barghorn, C., Allonas, X., and Van Der Ven, L. G. J. (2014). J. Polym. Sci. A 52, 3597–3607. doi:10.1002/pola.27427
Kiomarsipour, N., Eshaghi, A., Ramazani, M., Zabolian, H., and Abbasi-Firouzjah, M. (2023). Investigation of upward speed and thickness effects on optical and mechanical properties of hard transparent thin films deposited on polycarbonate substrate. Prog. Org. Coatings 177, 107405–107419. doi:10.1016/j.porgcoat.2023.107405
Kobayashi, Y., Ishizaka, T., and Kurokawa, Y. (2005). Preparation of alumina films by the sol-gel method. J. Mater Sci. 40, 263–283. doi:10.1007/s10853-005-6080-8
Kozuka, H. (2003). On ceramic thin film formation from gels: evolution of stress, cracks and radiative striations. J. Ceram. Soc. Jpn. 111 (9), 624–632. doi:10.2109/jcersj.111.624
Kozuka, H., Takenaka, S., Tokita, H., Hirano, T., Higashi, Y., and Hamatani, T. (2003). Stress and cracks in gel-derived ceramic coatings and thick film formation. J. Sol-Gel Sci. Technol. 26, 681–686. doi:10.1023/A:1020773415962
Kumar, A., Mishra, V., Negi, S., and Kar, S. (2023). A systematic review on polymer-based superhydrophobic coating for preventing biofouling menace. J. Coatings Technol. Res. 20, 1499–1512. doi:10.1007/s11998-023-00773-8
Li, B., Wang, X., Yan, M., and Li, L. (2002). Preparation and characterization of nano-TiO2 powder. Key Eng. Mater 224–226, 184–188. doi:10.1016/S0254-0584(02)00226-2
Lin, Y. S., Wu, C. Y., Wu, B. R., and Zhang, G. M. (2024). Rapid synthesis of organosilicon oxide thin films and post-curing for enhanced scratch and corrosion resistance of aluminum alloy. Vacuum 221, 112879. doi:10.1016/j.vacuum.2023.112879
Liravi, M., Pakzad, H., Moosavi, A., and Nouri-Borujerdi, A. (2020). A comprehensive review on recent advances in superhydrophobic surfaces and their applications for drag reduction. Prog. Org. Coatings 140, 105537. doi:10.1016/j.porgcoat.2019.105537
Malzbender, J., and De With, G. (2000). The effects of drying, aging and curing on an organic - inorganic coating. J. Mater Sci. 35, 4809–4814. doi:10.1023/A:1004824812867
Manasa, S., and Subasri, R. (2016). Effect of heat treatment on the optical properties of sol–gel-derived, fully dielectric solar control coatings on glass. J. Coatings Technol. Res. 13, 623–628. doi:10.1007/s11998-015-9755-3
Manoharan, K., and Bhattacharya, S. (2019). Superhydrophobic surfaces review: functional application, fabrication techniques and limitations. J. Micromanufacturing 2, 59–78. doi:10.1177/2516598419836345
Michel, M., and Ferrier, E. (2020). Effect of curing temperature conditions on glass transition temperature values of epoxy polymer used for wet lay-up applications. Constr. Build. Mater 231, 117206. doi:10.1016/j.conbuildmat.2019.117206
Parihar, S., and Gaur, B. (2023). High performance self-healing polymeric nanocomposite coatings. Prog. Org. Coat. 182, 107626–107642. doi:10.1016/j.porgcoat.2023.107626
Patra, R., Raju, K. R. C. S., Bhaskar, B., Sarkar, D., Chaudhuri, S., Garg, P., et al. (2022a). Biofilm inhibiting nanocomposite coatings—a promising alternative to combat surgical site infections. J. Coatings Technol. Res. 19, 1697–1711. doi:10.1007/s11998-022-00642-w
Patra, R., Raju, K. R. C. S., Murugan, K., and Subasri, R. (2022b). Effect of heating rate on asperities pattern formed in sol-gel derived nanocomposite hydrophobic coatings. J. Sol-Gel Sci. Technol. 103, 50–61. doi:10.1007/s10971-022-05762-8
Perrin, F. X., Merlatti, C., Aragon, E., and Margaillan, A. (2009). Degradation study of polymer coating: improvement in coating weatherability testing and coating failure prediction. Prog. Org. Coatings 64, 466–473. doi:10.1016/j.porgcoat.2008.08.015
Pradheebha, S., Unnikannan, R., Bathe, R. N., Padmanabham, G., and Subasri, R. (2018). Effect of plasma pretreatment on durability of sol-gel superhydrophobic coatings on laser modified stainless steel substrates. J. Adhes. Sci. Technol. 32, 2394–2404. doi:10.1080/01694243.2018.1482735
Raju, K. R. C. S., Sowntharya, L., Lavanya, S., and Subasri, R. (2012). Effect of plasma pretreatment on adhesion and mechanical properties of sol-gel nanocomposite coatings on polycarbonate. Compos Interfaces 19, 259–270. doi:10.1080/15685543.2012.702580
Rao, K. S., Yogapriya, R., Raju, K. R. C. S., and Subasri, R. (2021a). Effect of curing technique on the properties of superhydrophobic coatings. Trans. Indian Inst. Met. 74, 1923–1932. doi:10.1007/s12666-021-02287-6
Rao, Q., Lu, Y., Song, L., Hou, Y., Zhan, X., and Zhang, Q. (2021b). Highly efficient self-repairing slippery liquid-infused surface with promising anti-icing and anti-fouling performance. ACS Appl. Mater Interfaces 13, 40032–40041. doi:10.1021/acsami.1c09491
Rawat, M., Sharma, D., Sharma, J., Ahuja, S. K., Chandra, A., and Barman, S. (2020). “Introduction to polymer coatings,” in Polymer coatings: technologies and applications. Editors S. M. Rangappa, J. Parameswaranpillai, and S. Siengchin (Boca Raton, FL: CRC Press), 1–18. doi:10.1201/9780429199226
Rico, L. F., Conejero Iglesias, O., de la Rua García, R. B., Moriones Domeño, J., Fernández de Ara, J., and Fuentes, G. G. (2023). Modular UV curing sol-gel coating for invisible, levelling and easy to clean multi-layer systems. Mater. (Basel) 16, 5442. doi:10.3390/ma16155442
Salehi, E., Naderi, R., and Ramezanzadeh, B. (2017). Synthesis and characterization of an effective organic/inorganic hybrid green corrosion inhibitive complex based on zinc acetate/Urtica Dioica. Appl. Surf. Sci. 396, 1499–1514. doi:10.1016/j.apsusc.2016.11.198
Samaha, M. A., and Gad-el-Hak, M. (2021). Slippery surfaces: a decade of progress. Phys. Fluids 33. doi:10.1063/5.0056967
Samaha, M. A., Vahedi Tafreshi, H., and Gad-el-Hak, M. (2012). Effects of hydrostatic pressure on the drag reduction of submerged aerogel-particle coatings. Colloids Surfaces A Physicochem Eng. Asp. 399, 62–70. doi:10.1016/j.colsurfa.2012.02.025
Satdive, A., Tayde, S., Toksha, B., Kundu, D., Naik, J., Hazra, C., et al. (2023). Superhydrophobic hybrid nanocomposites: mapping the current research trends and recent advances. Chem. Eng. Sci. 278, 118941. doi:10.1016/j.ces.2023.118941
Sathya, R. A., and Ponraj, C. (2023). Superhydrophobic route of fabricating antireflective, self-cleaning, and durable coatings for solar cell applications. J. Coatings Technol. Res. 21, 1–30. doi:10.1007/s11998-023-00843-x
Schmidt, H., and Wolter, H. (1990). Organically modified ceramics and their applications. J. Non-Cryst Solids 121, 428–435. doi:10.1016/0022-3093(90)90171-H
Seidlová, M., Hodul, J., Žižková, N., and Borg, R. P. (2023). Possibilities of influencing the crystallization process of bisphenol A- and bisphenol F-based epoxy resins used for hydrophobic coatings on concrete. Polym. (Basel) 15, 3871. doi:10.3390/polym15193871
Serra, A., Ramis, X., and Fernández-Francos, X. (2016). Epoxy sol-gel hybrid thermosets. Coatings 6, 8–19. doi:10.3390/coatings6010008
Song, W., and Mano, J. F. (2013). Interactions between cells or proteins and surfaces exhibiting extreme wettabilities. Soft Matter 9, 2985–2999. doi:10.1039/c3sm27739a
Sowntharya, L., Gundakaram, R. C., Raju, K. R. C. S., and Subasri, R. (2013). Effect of addition of surface modified nanosilica into silica – zirconia hybrid sol – gel matrix. Ceram. Int. 39 (2013), 4245–4252. doi:10.1016/j.ceramint.2012.10.276
Sowntharya, L., Lavanya, S., Chandra, G. R., Hebalkar, N. Y., and Subasri, R. (2012). Investigations on the mechanical properties of hybrid nanocomposite hard coatings on polycarbonate. Ceram. Int. 38, 4221–4228. doi:10.1016/j.ceramint.2012.01.081
Sowntharya, L., and Subasri, R. (2013). A comparative study of different curing techniques for SiO2–TiO2 hybrid coatings on polycarbonate. Ceram. Int. 39, 4689–4693. doi:10.1016/j.ceramint.2012.11.045
Sridar, S., Kumar, R., and Raman, S. (2014). Nature’s design for superhydrophobicity in tropical leaves. Surf. Innov. 3. doi:10.1680/si.14.00010
Subasri, R., Madhav, C. S., Somaraju, K. R. C., and Padmanabham, G. (2012). Decorative, hydrophobic sol-gel coatings densified using near-infrared radiation. Surf. Coatings Technol. 206, 2417–2421. doi:10.1016/j.surfcoat.2011.10.043
Subasri, R., Reddy, D. S., Soma Raju, K. R. C., Rao, K. S., Kholov, P., and Gaponenko, N. (2019). Sol–gel derived Ba/SrTiO3–MgF2 solar control coating stack on glass for architectural and automobile applications. Res. Chem. Intermed. 45, 4179–4191. doi:10.1007/s11164-019-03899-w
Subasri, R., Soma Raju, K. R. C., Reddy, D. S., Hebalkar, N. Y., and Padmanabham, G. (2016). Sol-gel derived solar selective coatings on SS 321 substrates for solar thermal applications. Thin Solid Films 598, 46–53. doi:10.1016/j.tsf.2015.12.002
Tesler, A. B., Prado, L. H., Khusniyarov, M. M., Thievessen, I., Mazare, A., Fischer, L., et al. (2021). A one-pot universal approach to fabricate lubricant-infused slippery surfaces on solid substrates. Adv. Funct. Mater 31. doi:10.1002/adfm.202101090
Tripathi, D., Ray, P., Singh, A. V., Kishore, V., and Singh, S. L. (2023). Durability of slippery liquid-infused surfaces: challenges and advances. Coatings 13, 1095–1134. doi:10.3390/coatings13061095
Ulaeto, S. B., Ravi, R. P., Udoh, I. I., Mathew, G. M., and Rajan, T. P. D. (2023). Polymer-based coating for steel protection, highlighting metal–organic framework as functional actives: a review. Corros. Mater Degrad. 4, 284–316. doi:10.3390/cmd4020015
Vanithakumari, S. C., Yadavalli, P., George, R. P., and Mudali, U. M. (2015). Lotus effect-based coatings on marine steels to inhibit biofouling. Surf. Innov. 3, 115–126. doi:10.1680/si.14.00009
Vioux, A., Viau, L., Volland, S., and Le Bideau, J. (2010). Use of ionic liquids in sol-gel; ionogels and applications. Comptes Rendus Chim. 13, 242–255. doi:10.1016/j.crci.2009.07.002
Voytik, A. E., Malkov, G. V., Kapasharov, A. T., Knerelman, E. I., and Kostin, A. Y. (2020). Preparation and researching the properties of organic aerogels based on epoxy resins. IOP Conf. Ser. Mater Sci. Eng. 848, 012097. doi:10.1088/1757-899X/848/1/012097
Wei, C., Zhang, G., Zhang, Q., Zhan, X., and Chen, F. (2016). Silicone oil-infused slippery surfaces based on Sol−Gel process-induced nanocomposite coatings: a facile approach to HighlyStable bioinspired surface for biofouling resistance. ACS Appl. Mat. Interfaces 8, 34810–34819. doi:10.1021/acsami.6b09879
Wilkes, G. L., Brennan, A. B., Huang, H. H., Rodrigues, D., and Wang, B. (1989). The synthesis, structure and property behavior of inorganic-organic hybrid network materials prepared by the sol gel process. MRS Online Proc. Libr. 171, 14–29. doi:10.1557/PROC-171-14
Yasakau, K. A., Carneiro, J., Zheludkevich, M. L., and Ferreira, M. G. S. (2014). Influence of sol-gel process parameters on the protection properties of sol-gel coatings applied on AA2024. Surf. Coatings Technol. 246, 6–16. doi:10.1016/j.surfcoat.2014.02.038
Zhang, R., Chen, H., Cao, H., Huang, C. M., Mallon, P. E., Li, Y., et al. (2001). Degradation of polymer coating systems studied by positron annihilation spectroscopy. IV. Oxygen effect of UV irradiation. J. Polym. Sci. Part B Polym. Phys. 39, 2035–2047. doi:10.1002/polb.1179
Zhang, Y., Dong, B., Wang, S., Zhao, L., Wan, L., and Wang, E. (2017). Mechanically robust, thermally stable, highly transparent superhydrophobic coating with low-temperature sol-gel process. RSC Adv. 7, 47357–47365. doi:10.1039/c7ra08578h
Zhang, Y., Fang, K., Wang, W., and Niu, H. (2022). A water-soluble epoxy-based green crosslinking system for stabilizing PVA nanofibers. Molecules 27, 4177. doi:10.3390/molecules27134177
Keywords: hybrid, sol–gel, bioinspired, superhydrophobicity, self-healing, antifouling, corrosion
Citation: K R C SR, R S and K SR (2024) Ceramic–polymer hybrid coatings for diverse applications. Front. Coat. Dye In. 2:1386920. doi: 10.3389/frcdi.2024.1386920
Received: 16 February 2024; Accepted: 26 April 2024;
Published: 21 August 2024.
Edited by:
Shrikant Joshi, University West, SwedenReviewed by:
Vilko Mandić, Faculty of chemical engineering and technology University of Zagreb, CroatiaKamalan Kirubaharan Amirtharaj Mosas, Alexander Dubcek University in Trencin, Slovakia
Aruna S. T., National Aerospace Laboratories (CSIR), India
Copyright © 2024 K R C, R and K. This is an open-access article distributed under the terms of the Creative Commons Attribution License (CC BY). The use, distribution or reproduction in other forums is permitted, provided the original author(s) and the copyright owner(s) are credited and that the original publication in this journal is cited, in accordance with accepted academic practice. No use, distribution or reproduction is permitted which does not comply with these terms.
*Correspondence: Subasri R, c3ViYXNyaUBhcmNpLnJlcy5pbg==