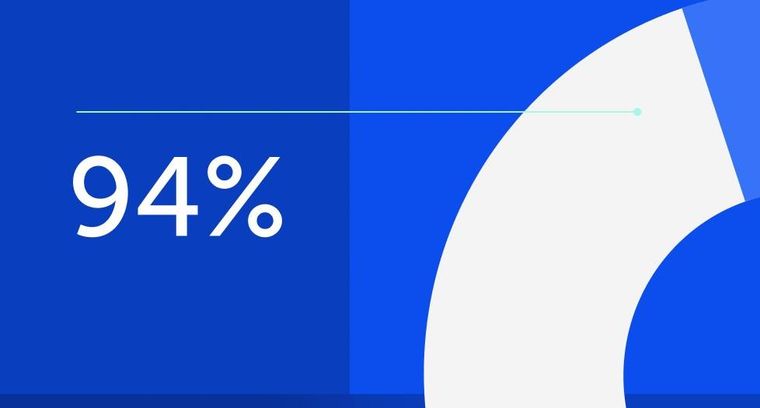
94% of researchers rate our articles as excellent or good
Learn more about the work of our research integrity team to safeguard the quality of each article we publish.
Find out more
FIELD GRAND CHALLENGE article
Front. Coat. Dyes Interface Eng., 03 April 2023
Volume 1 - 2023 | https://doi.org/10.3389/frcdi.2023.1110162
The subject areas of Coatings, Dyes and Interface Engineering are rarely seen together although there is potentially a huge synergy from embracing coatings-dyes-interface interactions. This allows an enabling science that aligns with global grand challenges such as net zero (batteries, renewal energy systems, low drag, antifouling and low friction interfaces, self-healing coatings, functionally graded, composite and multi-layered coatings sustainability of coatings, etc.), biomedical/health technologies, space and security. Coatings, dyes and interfaces engineering are used to optimize the functionality and to improve the entire function of materials and surfaces. Coatings have a wide range of forms, such as paints, adhesives, semiconductor thin films, hard facings and have a varied application route such as mechanical systems, solar cells, domestic appliances, photonics, smart coatings, micro-electronics, offshore renewables, biomedical and photographic films. Several application and synthesis methods, such as sol–gel, spin, dip, physical and chemical vapour deposition, thermal spray, weld overlays, plasma electrolytic oxidation, atomic layer deposition, electroplating and so on, have been used for thin or thick hard and soft coatings and films.
This article looks at recent state-of-the-art and related special issues and review papers to identify trends and future challenges for research in these areas. In scope for embracing coatings-dyes-interface interactions are thin and thick, composite, hard and soft coatings, coating structure and properties, processes for coating deposition, modification and characterization techniques, functional, smart, self-healing and sensing coatings, dyes, pigments and their intermediates. These in turn rely on fundamental mechanical and chemical as well as functional properties of surfaces and interfaces, theoretical and computational modelling of surfaces and interfaces as well as colloids, nanoparticles and large interfaces. The key to improved performance of coatings-dyes-interface engineering is understanding the manufacturer-composition-properties-performance interactions aligned to the service environment and operating conditions. Such research will be essential for energy research, photovoltaics, battery and electrochemical surfaces, biomedical applications, electronic applications of dyes and pigments, low friction, efficient machines and low drag, hydrophobic and nature inspired coatings. However, new understanding is needed for dynamic interfaces covering wear, corrosion, erosion for example. Modern measurement and imaging systems now allow in-situ and non-destructive monitoring of these interfaces. Miniaturisation of sensors and embedding sensors alongside or within interfaces is now possible which should provide a digital data stream for machine learning algorithms to allow smart interface management. Therefore, the challenges now lie around the synthesis and characterization of thin films and multifunctional coatings and the use of novel interface characterization techniques (Special Issue, 2022) and Butt, M.A (Butt, 2022).
Currently, industry and their designers are seeking improved efficiency of surface-surface interactions and extended service life times of engineering components, particularly those that operate in harsh environments (e.g., corrosive, high-temperature, and varied mechanical loading conditions), for multi-industrial sector applications (Mondal et al., 2021). Recent drivers to create biomimetic surfaces (nature inspired surfaces) have also challenged the engineering and generation of such surfaces.
There are still challenges around filling gaps in knowledge of how materials and coatings respond to service conditions that inhibit their replacement. Recent work looks at real-time evaluation of the mechanical response of materials which is essential to enable improved performance of coated systems (Amer et al., 2022). Details of the microstructural-compositional changes and their evolution are critical to improved interface engineering designs to extend life and functionality of these surfaces. Instrumented mechanical testing can provide in-situ measurement of the degradation and crack propagation mechanisms within coatings during service relevant loading conditions. Different real-time monitoring techniques have been used such as scanning and tunnelling electron microscopy to monitor the deformation and fracture mechanisms at multiple scale lengths. Digital image correlation systems and acoustic emissions sensors have been used for measuring surface strain fields and stress waves released within and on surfaces, respectively.
The increasing demand for more sustainable products in response to societal challenges has been driving research efforts to develop novel sustainable coatings solutions by deploying green materials or processes while offering desired performance in a variety of applications (Pourhashem, 2020). Another key driver that challenges conventional coating selection is legislation around the registration, evaluation, authorisation and restriction of chemicals (REACH) which is still driving development of replacement coatings for Hard Chromium and Cadmium for example. The difficulty is that there is incomplete understanding of how coatings deliver extremely good tribological and corrosion resistance.
There is a very large family of coating deposition types, compositions, thicknesses and hardness that can be selected. This article will touch on a few to give examples of challenges researchers need to solve. Starting with phosphate conversion coatings, where recent research highlights the importance of the acid-pickling conditions used to clean substrates needs to be understood. Inorganic acids need to be compared to less harmful organic acids as recent studies show significant differences in the coating morphology and chemical composition whereas no changes in coating weight or porosity were found when using organic acids. The study also showed the importance of understanding process such as bath temperature-substrate interactions that control appearance, porosity and composition of such conversion coatings (Díaz et al., 2021).
Another family of coatings are generated by electrodeposition that use acidic and alkaline aqueous baths but these suffer from hydrogen gas evolution, low Coulombic efficiencies, and environmental toxicity. Switching to ionic liquids to overcome such drawbacks has gained significant attention (Maniam and Paul, 2020). The electrodeposition of composite coatings containing particles in a metal matrix is reviewed by (Walsh and Larson, 2020). Key challenges they conclude are i) understanding the interactions among bath composition, operational conditions and deposit properties and ii) limitations in models describing composite electrodeposition.
Cold gas dynamic spray or simply cold spray (CS) is a kinetic based coating process that can deposit metallic, ceramic, polymer and metal matrix composite (MMC) coatings and can use nanostructured materials without changing their microstructure. The challenges for cold spray are i) the microstructural bonding mechanisms for material systems, ii) the quantification of the process parameters and the behaviour of the material systems during deposition (Moridi et al., 2014).
The deposition of a family of functional coatings using volatile compounds are offered by the chemical vapor deposition processes but these still require better understanding of and modelling of the multi-scale phenomena induced (Igumenov and Lukashov, 2022). These include quantum effects, molecular dynamics, kinetic Monte Carlo methods, as well as computational fluid dynamics in the framework of macroscopic continuum models (Cheimarios et al., 2021); (Cave et al., 2008). Another challenge here is that macroscopic CFD modelling of heat, substance, and momentum transfer processes are currently based on databases and as (Bernard et al., 2007) points out, without high-quality and system specific data, even the most advanced model maybe compromised.
Physical vapour deposition (PVD) is widely used to deposit thin films but there is a need to optimise by increasing plasma ionization, decreasing dark areas (zones where there is no deposition), improving target use, enhancing atomic bombardment efficiency, or even increasing the deposition rate and optimizing the selection of gases to improve thin film quality and increase adhesion to the substrate (Baptista et al., 2018). Due to the increasing maintenance costs of hydraulic machines caused by cavitation erosion and/or erosion by solid particles, PVD coatings offer a solution. The designs use the hardness/elastic modulus (H/E) ratio (inverse plasticity model) to predict resistance. In the case of cavitation erosion and solid particle erosion, a weak correlation is seen based on H/E but in tribological tests, there is evidence of some correlation exists (Krella, 2020). Therefore, better understanding of the damage mechanisms and thus the properties needed to be modelled is needed.
Hybrid deposition processes are being explored as protective coatings such as high-velocity oxygen–fuel coupled physical vapor deposition (HVOF-PVD) duplex coatings. These duplex coatings superimpose the synergistic advantages of coatings deposited by HVOF and PVD, where the traditional weaknesses of each technique are modified to a great certain extent (Zhang et al., 2022).
Hip and knee joint replacements in patients can produce metallic ions and particles from both the bearing surfaces and non-articulating interfaces (taper joints). These can cause hypersensitivity and local tissue necrosis while particles originating from polymer cups have been associated with aseptic loosening and osteolysis. A possible solution is offered by ceramic coatings that inhibit ion release from the underlying material caused by corrosion. However, there are challenges around adhesion of implant coatings (Skjöldebrand et al., 2022).
Thermal Barrier Coatings (TBCs) used to protect structural parts in both industrial and aviation gas turbines are deposited using electron beam physical vapor deposition (EB-PVD) and atmospheric plasma spraying (APS). These coatings have been challenged recently to resist CMAS (Calcium-Magnesium-Alumino-Silicate) attack and thus research to develop new systems is needed. Another area that needs attention is understanding the ideal modification needed to the bond coat surface, such as laser-assisted processes, before depositing the topcoat to extend lifetime of TBCs. Within the context of increased use of renewables, gas turbines will play an increasing role to fill the gap between energy demand and generation. This operational requirement shows TBC research needs to be focused on the effects of varying operation times and different heating and cooling phases (Vaßen et al., 2022). Environmental barrier coatings (EBC) to protect Ceramic Matrix Composites (CMC) used in gas-turbine engines are another family of coatings that need to be developed to improve performance. Current challenges are the optimisation of sintering temperatures and understanding how to control grain growth rates (Paksoy and Xiao, 2022).
System performance in Li-ion batteries (LiBs) and supercapacitors is hugely reliant on cathode materials used. Research challenges focus on the surface modification of the electrode materials by coatings for ease of synthesis and cost effectiveness. Coating techniques used include wet chemical (e.g., sol-gel), dry deposition (spray, CDV and atomic layer) and electroless plating. The challenges for the wet deposition techniques are to better understand the surface properties of the cathode to boost performance and to capture the liquid, dispersant and pH effects on coating uniformity (Chaudhary et al., 2021).
Smart icephobic coatings based on polymeric systems are of growing interest to inhibit icing on blades to enable wind turbines and aircraft to operate efficiently. However, more research is needed (Shamshiri et al., 2021) to improve performance. This is also true of other functionalised polymer coatings for biocompatibility, osteoinduction, hydrophobicity, self-healing, antibacterial performance and drug sustained release for a wide range of biomedical applications (Li et al., 2018). New research is also needed to improve the adhesion performance of polymeric coatings for ship hulls designed with tunable viscoelasticity (Smith and Lamprou, 2014; Verma et al., 2019).
The hydrophobic properties of modified graphene oxide can reduce the migration and adsorption of corrosive species and thus be used to improve the corrosion resistance of composite materials. Thus different processes to produce graphene oxide and their incorporation into a coating are being actively explored (Kumari Ola et al., 2021).
Traditionally organic dyes have been used for colouring textiles, food and hair but recently have become increasingly important in advanced materials. These functional dyes can, for example, be used to convert sunlight in solar cells, in optical data storage, and in sensors as well as for the labelling of biomolecules. Current research is focused on supporting their application in organic electronics, for example, in organic field-effect transistors (OFETs) (Special Issue, 2010). Supramolecular systems such as monolayer and multilayer, polymer films of various crown-containing dyes, surface-active monomers and polymers are active areas of research as is the design, production and investigation of the membrane nanostructures based on crown ethers. These nanostructures can serve as convenient models for studying the self-organization and molecular recognition processes at interfaces. This could lead to the development of surfaces that possess specific properties such as chemosensor, photochromic and photorefractive functions (Zaitsev et al., 2010). The role of dyes in the photoinitiation processes of polymerization reactions along with the introduction of the silyl radical chemistry that enhances the polymerization efficiency are reviewed by Fouassier (Fouassier et al., 2010).
Interface monitoring that goes beyond classic approaches of vibration and friction measurement is needed. The emerging techniques that monitor acoustic emissions, optical line scans of surface topography, in-situ and ex-situ electrochemical techniques for detailing the electrochemical reactions occurring during corrosion and tribocorrosion are good examples. Such electrochemical techniques include the scanning vibrating electrode, scanning microcell, scanning Kelvin probe, Kelvin probe force microscopy, and scanning electrochemical microscopy that can characterize the surfaces at the micro and nano scale (Thierry et al., 2021).
Another issue for interfaces is that material processing and fabrication can induce random surface roughness and surface distortions. Tailoring the surface conditions is especially challenging for thermo-mechanically stable materials, including refractory metals, such as tungsten (W), and polar dielectrics, such as silicon carbide (SiC). Hence, recent numerical modelling of the surface roughness has focused on the effects on the spectral reflectivity and emissivity of such materials and shows a strong dependency on the correlation length of the Gaussian surface, (Cao and Sendur, 2019). Interface engineering optimisation occurs largely through trial and error (Röttger et al., 2022), Röttger et al. define three central challenges that account for this disconnect: i) the fusion of many different types of measurement for the same surface to capture the multi-scale nature of roughness; ii) the technical complexity of implementing spectral analysis methods, and of applying mechanical or numerical models to describe surface performance; iii) a lack of consistency and compliance with ISO standards in how surfaces are measured, quantified, and communicated.
However, there are some specific interface engineering examples worth mentioning such as the use of carbon nanotubes (CNTs) in the next-generation electronics. Such CNT-metal systems have application specific challenges, for instance, the controlled synthesis and placement of CNTs in transistor applications. For bulk composites, a uniform dispersion of CNTs is the main concern, however, poor interfacial interaction between metals and CNTs is a more universal problem (Daneshvar et al., 2021). Switching to metal joint interfaces, the creation of an accurate equivalent method is of importance to optimize the dynamic performance of whole machines (Han et al., 2019).
Another area of intense research activity is surface texturing to help in the pursuit of low emissions and environmental sustainability of mechanical systems to lower friction and control wear (Lu and Wood, 2020). The key challenges identified in the review are i) determining the relationships between the scale of features and the contact area and ii) the application of texturing in non-conformal contacts, iii) the long-term performance of textures, iv) cost-benefit analysis of texturing should be considered, v) more focus is needed on the suitable use of texturing to reduce consumption of hydrocarbon-based lubricants in mechanical applications, vi) modelling validations should use experimental tests and vii) modelling needs to consider the actual manufactured textures rather than the design surface and include lubricant decay and contamination effects such as water contamination, soot contamination, thermal degradation and additive depletion (Lu and Wood, 2020).
The author confirms being the sole contributor of this work and has approved it for publication.
The author declares that the research was conducted in the absence of any commercial or financial relationships that could be construed as a potential conflict of interest.
All claims expressed in this article are solely those of the authors and do not necessarily represent those of their affiliated organizations, or those of the publisher, the editors and the reviewers. Any product that may be evaluated in this article, or claim that may be made by its manufacturer, is not guaranteed or endorsed by the publisher.
Amer, M., Hayat, Q., Janik, V., Jennett, N., Nottingham, J., and Bai, M. (2022) A review on in situ mechanical testing of coatings. Coatings, 12 (3): 299. doi:10.3390/coatings12030299
Baptista, A., Silva, F., Porteiro, J., Miguez, J., and Pinto, G. (2018) Sputtering physical vapour deposition (PVD) coatings: A critical review on process improvement and market trend demands. Coatings, 8 (11): 402. doi:10.3390/coatings8110402
Bernard, C., Blanquet, E., and Pons, M. (2007) Chemical vapor deposition of thin films and coatings: Evaluation and process modeling. Surf. Coatings Technol., 202 (4–7): 790–797. doi:10.1016/j.surfcoat.2007.04.131
Butt, M. A. (2022) Thin-film coating methods: A successful marriage of high-quality and cost-effectiveness—a brief exploration. Coatings, 12 (8): 1115. doi:10.3390/coatings12081115
Cao, L., and Sendur, K. (2019) Surface roughness effects on the broadband reflection for refractory metals and polar dielectrics. Materials, 12 (19): 3090. doi:10.3390/ma12193090
Cave, H. M., Krumdieck, S. P., and Jermy, M. C. (2008) Development of a model for high precursor conversion efficiency pulsed-pressure chemical vapor deposition (PP-CVD) processing. Chem. Eng. J., 135 (1–2): 120–128. doi:10.1016/j.cej.2007.03.027
Chaudhary, M., Tyagi, S., Gupta, R. K., Singh, B. P., and Singhal, R. (2021) Surface modification of cathode materials for energy storage devices: A review. Surf. Coatings Technol., 412: 127009. doi:10.1016/j.surfcoat.2021.127009
Cheimarios, N., Kokkoris, G., and Boudouvis, A. G. (2021) Multiscale modeling in chemical vapor deposition processes: Models and methodologies. Archives Comput. Methods Eng., 28 (2): 637–672. doi:10.1007/s11831-019-09398-w
Daneshvar, F., Chen, H., Noh, K., and Sue, H. J. (2021) Critical challenges and advances in the carbon nanotube–metal interface for next-generation electronics. Nanoscale Adv., 3 (4): 942–962. doi:10.1039/D0NA00822B
Díaz, B., Nóvoa, X. R., Pérez, C., and Silva-Fernandez, S. (2021) Characterization of phosphate coatings: Influence of the acid pickling conditions. Materials, 14 (4): 1048. doi:10.3390/ma14041048
Fouassier, J.-P., Morlet-Savary, F., Lalevée, J., Allonas, X., and Ley, C. (2010) Dyes as photoinitiators or photosensitizers of polymerization reactions. Materials, 3 (12): 5130–5142. doi:10.3390/ma3125130
Han, R., Li, G., Gong, J., Zhang, M., and Zhang, K. (2019) Equivalent method of joint interface based on persson contact theory: Virtual material method. Materials, 12 (19): 3150. doi:10.3390/ma12193150
Igumenov, I. K., and Lukashov, V. V. (2022) Modern solutions for functional coatings in CVD processes. Coatings, 12 (9): 1265. doi:10.3390/coatings12091265
Krella, A. (2020) Resistance of PVD coatings to erosive and wear processes: A review. Coatings, 10 (10): 921. doi:10.3390/coatings10100921
Kumari Ola, S., Priyanka Soni, S., Soni, S., Dhayal, V., and Singh Shekhawat, D. (2021) A review: Graphene modified polymer coatings for corrosion protection. IOP Conf. Ser. Earth Environ. Sci., 796 (1): 012027. doi:10.1088/1755-1315/796/1/012027
Li, L.-Y., Cui, L.-Y., Zeng, R.-C., Li, S. Q., Chen, X. B., Zheng, Y., et al. (2018) Advances in functionalized polymer coatings on biodegradable magnesium alloys – a review. Acta Biomater., 79: 23–36. doi:10.1016/j.actbio.2018.08.030
Lu, P., and Wood, R. J. K. (2020) Tribological performance of surface texturing in mechanical applications—A review. Surf. Topogr. Metrology Prop., 8 (4): 043001. doi:10.1088/2051-672X/abb6d0
Maniam, K. K., and Paul, S. (2020) Progress in electrodeposition of zinc and zinc nickel alloys using ionic liquids. Appl. Sci., 10 (15): 5321. doi:10.3390/app10155321
Mondal, K., Nuñez, L., Downey, C. M., and van Rooyen, I. J. (2021) Thermal barrier coatings overview: Design, manufacturing, and applications in high-temperature industries. Industrial Eng. Chem. Res., 60 (17): 6061–6077. doi:10.1021/acs.iecr.1c00788
Moridi, A., Hassani-Gangaraj, S. M., Guagliano, M., and Dao, M. (2014) Cold spray coating: Review of material systems and future perspectives. Surf. Eng., 30 (6): 369–395. doi:10.1179/1743294414Y.0000000270
Paksoy, A. H., and Xiao, P. (2022) Study on sintering behaviour of ytterbium disilicate and ytterbium monosilicate for environmental barrier coating applications. Ceram. Int., 48 (8): 11238–11250. doi:10.1016/j.ceramint.2021.12.344
Pourhashem, G. (2020) Coating a sustainable future. Coatings, 10 (8): 713. doi:10.3390/coatings10080713
Röttger, M. C., Sanner, A., Thimons, L. A., Junge, T., Gujrati, A., Monti, J. M., et al. (2022) Contact.engineering—create, analyze and publish digital surface twins from topography measurements across many scales. Surf. Topogr. Metrology Prop., 10 (3): 035032. doi:10.1088/2051-672X/ac860a
Shamshiri, M., Jafari, R., and Momen, G. (2021) Potential use of smart coatings for icephobic applications: A review. Surf. Coatings Technol., 424: 127656. doi:10.1016/j.surfcoat.2021.127656
Skjöldebrand, C., Tipper, J. L., Hatto, P., Bryant, M., Hall, R. M., and Persson, C. (2022) Current status and future potential of wear-resistant coatings and articulating surfaces for hip and knee implants. Mater. Today Bio, 15: 100270. doi:10.1016/j.mtbio.2022.100270
Smith, J. R., and Lamprou, D. A. (2014) Polymer coatings for biomedical applications: A review. Trans. IMF, 92 (1): 9–19. doi:10.1179/0020296713Z.000000000157
Special Issue “Advances in dyes and pigments (2010). Materials https://www.mdpi.com/journal/materials/special_issues/dyes_pigments.
Special Issue “Coatings and interfaces II (bWRwaS5jb20=)” (2022). Coatings. https://www.mdpi.com/journal/coatings/special_issues/interface_II.
Thierry, D., Nazarov, A., and Persson, D. (2021) “Mechanical and chemical coupling in tribocorrosion: In situ and ex situ characterization techniques.” In European Federation of Corrosion (EFC) Series, Mechanical and Electro-Chemical Interactions Under Tribocorrosion. Editors P. Ponthiaux, and J.-P. Celis (Woodhead Publishing), 29–66. Available at: https://www.sciencedirect.com/science/article/pii/B9780128237656000031. doi:10.1016/B978-0-12-823765-6.00003-1
Vaßen, R., Bakan, E., Mack, D. E., and Guillon, O. (2022) A perspective on thermally sprayed thermal barrier coatings: Current status and trends. J. Therm. Spray Technol., 31 (4): 685–698. doi:10.1007/s11666-022-01330-2
Verma, S., Mohanty, S., and Nayak, S. K. (2019) A review on protective polymeric coatings for marine applications. J. Coatings Technol. Res., 16 (2): 307–338. doi:10.1007/s11998-018-00174-2
Walsh, F. C., and Larson, C. (2020) Towards improved electroplating of metal-particle composite coatings. Trans. IMF, 98 (6): 288–299. doi:10.1080/00202967.2020.1819022
Zaitsev, S. Yu., Solovieva, D. O., and Zaitsev, I. S. (2010) Membrane and films based on novel crown-containing dyes as promising chemosensoring materials. Materials, 3 (12): 5293–5310. doi:10.3390/ma3125293
Keywords: coatings, dyes, pigments, thin films, hard coatings, soft coatings, interface engineering
Citation: Wood RJK (2023) Grand challenges in coatings, dyes and interface engineering. Front. Coat. Dyes Interface Eng. 1:1110162. doi: 10.3389/frcdi.2023.1110162
Received: 28 November 2022; Accepted: 06 January 2023;
Published: 03 April 2023.
Edited and Reviewed by:
Mark Alan Baker, University of Surrey, United KingdomCopyright © 2023 Wood. This is an open-access article distributed under the terms of the Creative Commons Attribution License (CC BY). The use, distribution or reproduction in other forums is permitted, provided the original author(s) and the copyright owner(s) are credited and that the original publication in this journal is cited, in accordance with accepted academic practice. No use, distribution or reproduction is permitted which does not comply with these terms.
*Correspondence: Robert J. K. Wood, ci53b29kQHNvdG9uLmFjLnVr
Disclaimer: All claims expressed in this article are solely those of the authors and do not necessarily represent those of their affiliated organizations, or those of the publisher, the editors and the reviewers. Any product that may be evaluated in this article or claim that may be made by its manufacturer is not guaranteed or endorsed by the publisher.
Research integrity at Frontiers
Learn more about the work of our research integrity team to safeguard the quality of each article we publish.