- Heirloom Carbon Technologies, Inc, Brisbane, CA, United States
Direct Air Capture (DAC) offers a promising pathway for combating climate change by removing carbon dioxide (CO2) directly from the atmosphere. Here, we discuss Heirloom’s approach to DAC, which uses naturally occurring minerals, namely, calcium carbonate (CaCO3), in a cyclic process that leverages warehouse automation systems previously developed for large warehouses. The integration of DAC with warehouse automation systems unlocks a degree of manufacturability, scalability, operational efficiency, and financial viability. For successful scaling, DAC technologies and project developers must think through key scalability constraints, including modularity, constructability, supply chains, and leveraging existing infrastructure.
1 Introduction
It has been well-established that to keep global temperature rise below 2°C we must develop and deploy technologies that not only decarbonize our current infrastructure, but that can remove carbon dioxide (CO2) directly from the atmosphere (IPCC Special Report, 2018). Here, carbon removal is critical as it aims to address both emissions from hard-to-abate industries, as well as historic (or legacy) emissions (NASEM, 2019; Bergman and Rinberg, 2020).
The UN Intergovernmental Panel on Climate Change (UN IPCC) estimates that up to 1,000 Gt of CO2\ will need to be removed from the atmosphere by 2,100 to meet climate goals (IPCC Special Report, 2018). There are many paths that can be taken to achieve carbon removal. These include direct air capture (DAC) coupled to CO2 storage; carbon mineralization; biomass carbon removal and storage (BiCRS), which includes bioenergy with carbon capture and storage (BECCS); soil carbon sequestration; and afforestation and reforestation (NASEM, 2019; Sandalow et al., 2021). Multiple Carbon Dioxide Removal (CDR) approaches will play a crucial role in the integrated portfolio of technologies necessary to achieve gigatonne-scale carbon removal by 2050. Among these approaches, DAC stands out due to several advantages it offers over existing carbon removal technologies – it is additional, permanent (when coupled with permanent storage methods like geological storage), and is capable of clear measurement, reporting and verification (MRV) (Pisciotta et al., 2022; Küng et al., 2023).
DAC describes a suite of engineered technologies that capture CO2 directly from the air and produce a concentrated stream of CO2. The concentrated stream of CO2 can either be utilized, such as to form fuels, construction materials, engineered materials, polymers, or chemicals, or stored geologically (NASEM, 2023). DAC technologies use chemicals to capture and release CO2, where these chemicals include solid sorbents, liquid solvents, naturally occurring minerals, and industrial byproducts, among others (McQueen et al., 2021).
In recent years, numerous advancements have been made in the development of various materials, approaches, and technologies for DAC. Several iterations of DAC employ engineered solid sorbents. Swiss company Climeworks uses engineered solid sorbents to bind with CO2 at near-atmospheric conditions, regenerating a concentrated stream of CO2 at an elevated temperature (80–120°C) and reduced pressure (Beuttler et al., 2019). By contrast, North American-based company, Carbon Engineering, uses liquid alkali metal hydroxides (such as potassium hydroxide, KOH, and sodium hydroxide, NaOH) to capture CO2 from air at near-atmospheric conditions and a high-temperature calcination process to release that CO2 in a concentrated form (Holmes and Keith, 2012; Keith et al., 2018).
As of today, there are over 100 companies developing improvements to existing DAC technologies or entirely new DAC technologies (Faber, 2024). A few of these companies are currently operating industrial facilities, including Climeworks, Carbon Engineering, Global Thermostat and Heirloom (International Energy Agency, 2022). However, the total scale of DAC globally is roughly 8,000 tons of CO2 per year. While these small-scale plants are important to de-risking new technologies and demonstrating the technological, social, and political benefits and challenges to deployment, reaching gigaton scale DAC by 2050 requires annual growth rates of nearly 50% – exponential scaling (McQueen et al., 2021). To achieve this, DAC technologies and project developers must think through key scalability constraints, including modularity, constructability, supply chains, and leveraging existing infrastructure.
This article discusses Heirloom’s approach to DAC and how the capture technology can leverage off-the-shelf, industrial automation technologies to accelerate scale. We present an overview of Heirloom’s DAC process, detail the integration of the CO2 capture stage with warehouse automation technologies, and offer a case study on Amazon’s warehouse expansion, illustrating the potential scalability of DAC when integrated with these automated warehouse technologies.
2 Process overview
Heirloom’s DAC process leverages the properties of natural occurring minerals (McQueen et al., 2022). While the process can theoretically accommodate any alkaline mineral feedstock, Heirloom uses calcium carbonate (CaCO3) which makes up more than 4% of the Earth’s crust (Carmeuse, 2024; Dietrich, 2024). The process is divided into two steps, regeneration, and carbonation, as outlined in Figure 1.
Regeneration comprises two stages: calcination and hydration. The CaCO3 feedstock is sent into a high temperature, electrically powered reactor. Inside this reactor the CaCO3 undergoes endothermic decomposition to calcium oxide (CaO) and CO2 at temperatures near 900°C at atmospheric conditions (Eq. 1). Since the kiln is powered entirely by renewable energy, a pure stream of CO2 is captured directly from the kiln and is stored permanently via geologic storage.
The resulting CaO is then hydrated to form calcium hydroxide [Ca(OH)2] (Eq. 2). The hydration reaction is exothermic, releasing roughly 30% of the energy required for the calcination process. This reaction thereby presents an ideal opportunity for heat recovery.
Once exposed to air, the Ca(OH)2 will react with the CO2 to reform CaCO3 via a reaction called carbonation (Eq. 3). When the material is sufficiently recarbonated, it is sent back to the regeneration process to begin the cycle again. The process then continues cyclically with the mineral sorbent being repeatedly carbonated and regenerated.
Heirloom built its first operational prototypes in 2021 and first integrated pilot facility in 2022. In collaboration with Canadian company CarbonCure, the integrated pilot facility also highlighted the first time that CO2 captured from the atmosphere was permanently sequestered in concrete (CarbonCure Technologies, 2023). In November of 2023, Heirloom officially launched the first commercial DAC facility in the United States in Tracy, CA with the capacity to capture up to 1,000 tons of CO2 from the air per year (Figure 2) (Plumer, 2023).
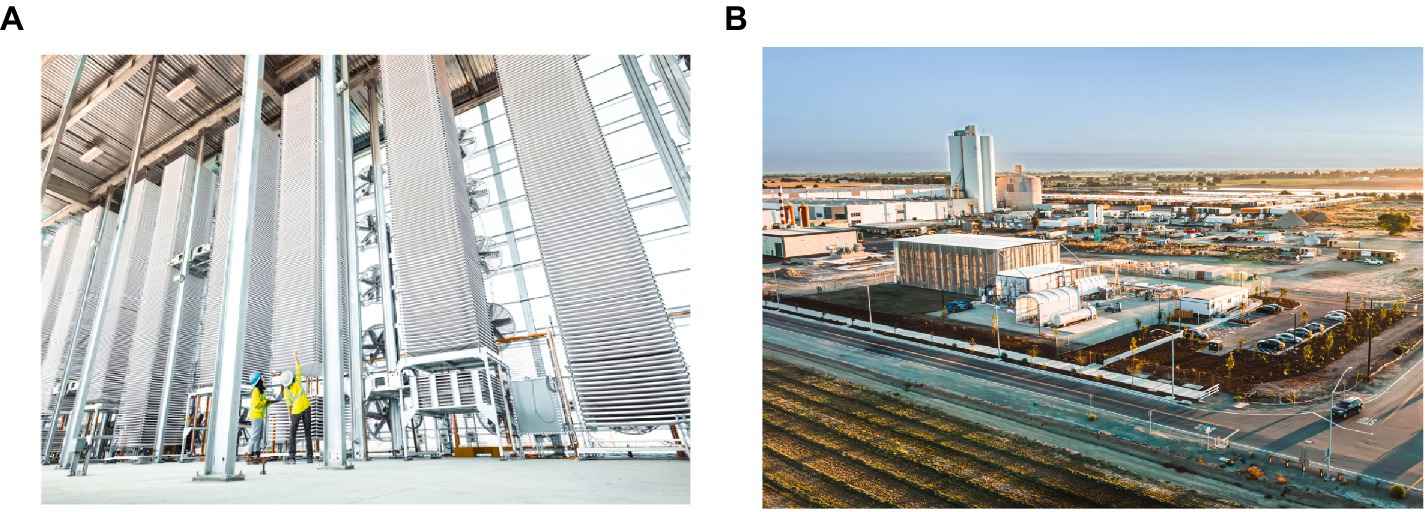
Figure 2. The first commercial direct air capture (DAC) facility in the United States in Tracy, California. (A) A close up of the contactor system in the first commercial system and (B) an aerial view of Heirloom’s first commercial deployment.
The rapid scaling of the technology from lab to a commercial facility in less than 3 years was broadly enabled using low-cost materials and technologies with existing supply chains. The three biggest inputs to the process are limestone, plastic, and steel. To achieve the necessary scale required to meet climate goals, DAC companies must persist in utilizing easily manufacturable and constructable systems that offer high scalability, while also drawing upon experiential knowledge from relevant industries.
3 A novel capture system that leverages industrial automation
The removal of vast quantities of CO2 via Heirloom’s cyclic process requires that large amounts of CO2-capturing materials be exposed to the atmosphere so that they can bind with CO2. The majority of the research around optimizing the physical infrastructure that holds the sorbent material (designated “contactors”) has focused on increasing CO2 capture while decreasing the pressure drop across the capture medium and the associated energy consumption (Holmes and Keith, 2012; Mazzotti et al., 2013; Gebald et al., 2017; Kasturi et al., 2023). To date, all DAC facilities have leveraged designs similar to traditional chemical processes, including cooling towers and monolith filters (APS, 2011; Holmes and Keith, 2012; Gebald et al., 2017; Beuttler et al., 2019; NASEM, 2019; Spiteri et al., 2021). Heirloom has taken a different approach by leveraging industrial automation for DAC, creating an automated warehouse to remove CO2 from the atmosphere.
3.1 Warehouse automation technology and DAC
Warehouse automation refers to the integration of various technologies and systems to streamline and optimize the operations within a warehouse. This approach aims to enhance efficiency, accuracy, and speed in tasks such as inventory management, order fulfillment, and material handling. Warehouse automation typically consists of several key components, including automated storage and retrieval systems (AS/RS), which use robotic mechanisms to store and retrieve goods from designated locations within the warehouse. Another component is conveyor systems, which facilitate the movement of materials between different areas of the warehouse. Additionally, robotic picking systems employ robots equipped with sensors and grippers to pick items. High bay racking systems are also essential components, maximizing vertical storage space by storing goods in tall, densely packed racks accessed by AS/RS. Warehouse management software orchestrates and coordinates these various automation components, optimizing workflows, and providing real-time visibility into inventory levels and order status. Other components may include sorting systems, automated guided vehicles for material transportation, and packaging automation systems. Overall, this type of warehouse automation aims to enhance operational efficiency, reduce labor costs, minimize errors, and create faster order processing and fulfillment.
Advancements in automated warehouse systems have steadily increased efficiency and reduced operational costs across a variety of industries, including logistics, distribution centers, and manufacturing facilities (Custodio and Machado, 2020; Funaki, 2023). These systems, exemplified by the AS/RS, offer a mechanized solution for storing and retrieving items within a facility, streamlining tracking and operations and reducing the need for manual labor.
At a high level, these automated warehouse technologies use a combination of vertical lifts, stacker cranes, and shuttles to store modular loads that are several layers deep, across multiple levels of vertical racking. In traditional warehouse storage, these modular loads are typically pallets. As applied to DAC, these modular loads are called caddies, and in Heirloom’s DAC facilities, these caddies are a pallet-sized modular carbon capture unit containing the calcium hydroxide sorbent material. This physical infrastructure is complemented by software and controls automation that schedules and tracks the placement and Research Topic of caddies (Figure 3).
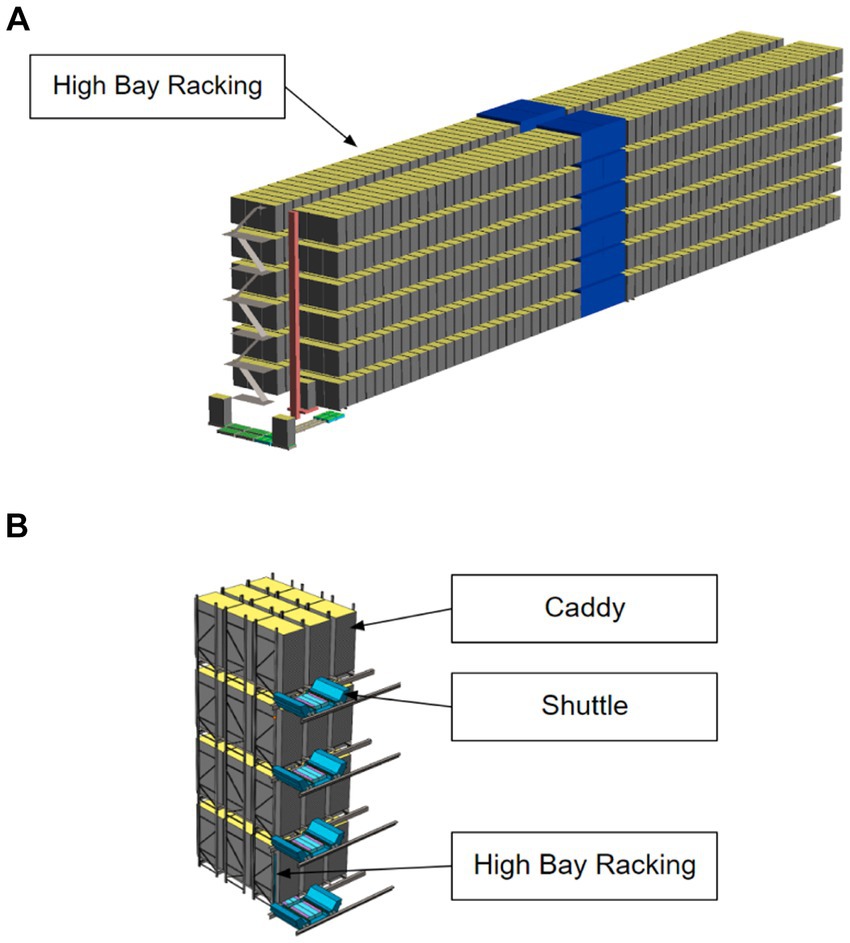
Figure 3. (A) A full-building view of warehouse automation infrastructure that can be leveraged for DAC. The yellow layered structure represents the high bay racking. (B) An example subsection of the contactor system where the shuttles are shown in light blue and the high bay racking with caddies by the gray and yellow stacked structure. Both images are representative subsections of the technology but may not be accurate to scale.
In traditional warehouse storage, the AS/RS automation and high bay racking system simplifies and standardizes placement and retrieval of modular units while providing dense and structurally efficient vertical storage, leading to cost savings across the system. The advantages that enable the success of warehouse automation for storage are directly transferable to DAC.
3.2 Advantages of automated warehouse technology for DAC
The benefits of integrating DAC with automated warehouse technologies include increased manufacturability, constructability (ease of onsite assembly), operational efficiency, and financial viability. In this section, each of these categories are explored in more detail and tied back to their potential impact on DAC deployment and the ability to achieve billion-ton scale carbon removal.
3.2.1 Manufacturability
The integration of warehouse automation systems within DAC leads to advantages in manufacturing efficiency and cost reduction – the primary benefit being the facilitation of low-cost, mass manufacturing. The modular design approach enables the repetition of component designs, such as trays, caddies and racking members, thereby reducing capital expenses. For example, the high bay racking design and manufacturing has been optimized and standardized over several decades (Custodio and Machado, 2020; Bedard, 2021). This enables the automated warehouse DAC system to utilize tools and equipment that are already available and widely used in the production of roll-formed steel members. Existing racking design solutions address freight efficiency (effectiveness and optimization of transporting goods or materials), installation time, and interfacing to AS/RS equipment. There already exists tooling to manufacture racking for varying system heights and load sizes, enabling an efficiently scaled system without significant design or infrastructure development.
The caddy, which captures the CO2, interacts with the AS/RS automation and racking with one standardized physical interface on the bottom, allowing for flexibility, rapid iteration, and parallel manufacturing of the caddies. The trays, which rest inside a caddy and hold Ca(OH)2 in contact with air, serve as the collection beds for CO2 inside the integrated system. The trays are standardized across the system which lends to the ability to mass manufacture and increases system flexibility.
The entirety of the integrated DAC capture system demonstrates a high degree of modularity. Modularity is the structural property of a system characterized by the degree of compartmentalization and functional independence among its constituent elements, facilitating flexibility, robustness, and efficiency in design, analysis, and adaptation (Ulrich, 1994; Gershenson et al., 2003). This modularity principle, central to reducing manufacturing costs, leverages the uniformity of parts to streamline production processes and diminish design complexity.
The technology learning rate quantifies the percentage decrease in production costs with each doubling of cumulative production experience, indicating efficiency improvements, learning by doing, and economies of scale over time. It serves as a metric for understanding how quickly and consistently the cost of producing a technology declines as experience with that technology accumulates. Differences in learning rates across technologies are influenced by factors such as design complexity and the need for customization (Malhotra and Schmidt, 2020). Technologies with higher degrees of modularity tend to also have higher technology learning rates (Flyvbjerg, 2021). For example, lithium-ion batteries have shown learning rates of 30% (Schmidt et al., 2017), while solar PV panels have demonstrated 23% (Rubin et al., 2015). In contrast, pulverized coal-fired boilers demonstrated learning rates of roughly 6% (Yeh and Rubin, 2007) and natural gas turbines 15% (Rubin et al., 2015). Manufacturing plays a large role in this cost reduction as more modular technologies rely on standardized components and assembly processes, which allow for ease of mass manufacturing as well as replication across different manufacturing facilities, leading to economies of scale and cost reduction (Jacobs et al., 2010). Additionally, modular designs streamline manufacturing by breaking down the system into smaller, more manageable components, leading to increased production efficiency, shorter lead times, and lower costs of manufacturing. This allows for a shorter feedback loop between production improvements and manufacturing, facilitating more rapid iteration and improvement cycles.
3.2.2 Constructability
Leveraging modular, off-the-shelf warehouse automation technologies also presents an opportunity for favorable material lead times, shorter construction timelines, and reduced construction complexity. The warehouse automation technologies leverage two key advantages: global scale and modularity in construction.
These warehouse automation technologies have been widely implemented on a global scale, leading to more efficient design and construction processes, ultimately resulting in shorter development timelines. The high bay racking structure minimizes steel use within the integrated DAC system, leveraging pre-engineered, roll-formed structures. This reduces the capital cost of the storage system as well as the construction complexity. Additionally, the pre-engineered, roll-formed structures enable ease of construction by facilitating straightforward assembly and installation processes (via pieces that ‘snap together’ in the field) (Meera, 2013). This reduces the installation time compared to conventional construction. Additional benefits include increasing project quality, reducing waste (material waste, defects, waiting times), decreasing greenhouse gas emissions, and improving overall safety (Cassino et al., 2011; Quale et al., 2012).
The modularity of the system, discussed above, also leads to fewer cost overruns during the construction and commissioning of large-scale projects by minimizing on-site work where delays are more likely to occur (Flyvbjerg and Gardner, 2023). A report by McKinsey suggests that modular construction has been shown to reduce construction timelines by 20–50% and those making the shift to modular construction may save 20% in construction costs (Bertram et al., 2019). Modularity in construction also has non-monetary impacts, including ergonomics and work satisfaction (Chauhan et al., 2022). Additionally, modularity can lead to greater benefits when coupled with pre-fabrication, further streamlining the construction process.
A final benefit of the warehouse automation system lies in the installation process. Once the warehouse is built, there is no additional installation required for the CO2-absorbing caddies. The caddies can be fed into the system and the automation system will install them throughout the facility, decreasing labor requirements and increasing the overall utilization of the installed equipment.
3.2.3 Operating costs
Operational costs are reduced by integrating automated systems into warehouse technologies. Automation technologies reduce labor requirements, enhance reliability, and simplify complex operational procedures, resulting in higher throughput and net productivity of a warehouse. The same operational advantages are expected for the integrated DAC technology.
The impact of automation technology on operating requirements in a warehouse environment is exemplified by the picking system, which refers to the method used to select and retrieve items from an inventory. In traditional warehousing, workers spend roughly 55% of their time traveling between picks, which make up over 50% of overall distribution center costs and drive the majority of labor-related operating costs (Tompkins et al., 2014; Custodio and Machado, 2020). Therefore, automating the picking system results in a roughly 30% decrease in the overall distribution center operational costs. In China, operators spend up to 70% of their time on picking (Xiao-Long et al., 2017). This would accordingly result in a nearly 40% reduction in overall distribution center operational costs. Automation of picking typically involves a system that uses various automation technologies such as robotics, conveyors, and AS/RS to pick items efficiently and accurately from storage locations. By automating routine tasks and facilitating greater vertical stacking of products, the automated picking system minimizes land area requirements, as well as reducing costs, labor hours, and the overall space needed within the warehouse (Custodio and Machado, 2020).
Finally, AS/RS has long-leveraged centralized software-based controls and management systems, which further contribute to maximizing efficiency, accuracy, and productivity while reducing disruptions and ensuring the safety and security of both equipment and personnel. Such software solutions are also highly scalable, flexible, and easily extendable to multiple warehouses. Additionally, as discussed, the components of warehouse automation are modular, enabling flexible maintenance and / or upgrades to each piece of equipment.
4 Scaling up: a scenario analysis
Amazon’s warehouse expansion serves as a compelling case study for scalable warehouse technology. Amazon, a global e-commerce leader, has significantly grown their warehouse capabilities over the past decade from a land area of roughly 6 km2 in 2012 to roughly 53 km2 in 2022 (Figure 4).
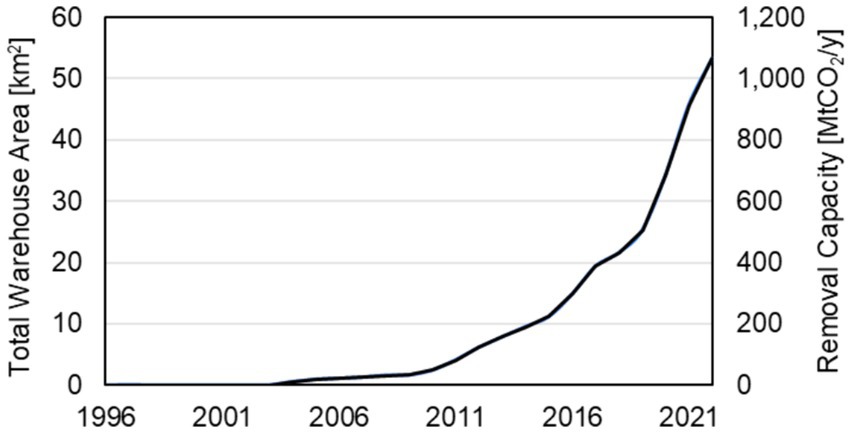
Figure 4. Growth in Amazon warehouse square footage from 1996 through 2022 used to estimate the rough equivalent amount of DAC that could be done on that same land area. The land area for warehouses are estimated from Amazon’s Annual Reports from 2004 through 2022 (Amazon.com, 2005, 2006, 2007, 2008, 2009, 2010, 2011, 2012, 2013, 2014, 2015, 2016, 2017; Amazon, 2018, 2019, 2020, 2021, 2022, 2023) less estimated land area usage for Data Centers using the available information on data center buildout (Amazon, 2024) and an average data center size of roughly 100,000 square feet (Zhang, 2023). Data is unavailable for the years 1998 through 2003.
The rack system is foundational to the warehouse infrastructure as well as to the integration of DAC with automated warehouse technology. While not all Amazon warehouses are automated, the foundational warehouse infrastructure buildout is represented in Figure 4. Additionally, in 2012 Amazon bought Kiva Systems, a company that specializes in automation technology for warehouses (Rao, 2012). Their systems utilize mobile robots to move goods around warehouses.
This case study speaks to a singular application of warehouse automation technology, and it is limited in breadth as it only considers application via Amazon technologies. The same supplier could engineer and design for several different applications and companies, which would be a truer representation of the technology buildout. In the absence of this detailed information, a singular company provides a suitable proxy.
Using the warehouse land area estimates, the rough equivalent DAC capacity can be calculated. A DAC facility requires roughly 0.4 km2 per million metric tons of removal capacity per year including both direct and indirect land use (Lebling et al., 2022). Direct land use refers to the physical space occupied by the DAC facility itself, including the land required for equipment, operations, and maintenance activities. Indirect land area encompasses spatial requirements beyond the immediate footprint of the DAC facility, such as the space needed between contactors for mixing CO2 or other ancillary processes associated with DAC technology. We anticipate that the direct land area usage for DAC contactors will be somewhere between solar and wind generation at ~70% and ~ 2% direct land area, respectively (Ong et al., 2013; Harrison-Atlas et al., 2022). The assumption here is that the direct land use of the contactors is roughly 25% of overall land area requirements, or 0.1 km2 per million metric tons of removal capacity per year. Using this estimate, the current capacity of Amazon warehouses could equivalently capture over 1 billion tons of CO2 from the atmosphere per year. This growth included an expansion in the warehouse area by roughly 12 km2 in one year, which could be equivalent to roughly 230 MtCO2 per year in DAC capacity. To reach 1 GtCO2 / year by 2035 would require scaling DAC at an average rate of ~91 MtCO2 / year. Achieving 5 Gt of removal by 2050 will require 192 MtCO2 / year on average.
5 Conclusion
DAC is a promising technology to remove CO2 from the atmosphere at scale in accordance with global climate goals. Rapid deployment of these technologies is imperative, necessitating close attention to supply chain scalability and the ability to manufacture DAC systems at a massive scale. The integration of DAC with warehouse automation presents clear advantages with respect to manufacturing, construction, operational efficiency, and financing, which offer cost-effectiveness and enhance scalability. However, it’s essential to recognize that a diverse portfolio of solutions will be required to effectively reach our global climate goals and attain net-zero emissions.
Data availability statement
The original contributions presented in the study are included in the article/supplementary material, further inquiries can be directed to the corresponding author.
Author contributions
NM: Writing – review & editing, Writing – original draft. DD: Writing – review & editing.
Funding
The author(s) declare that no financial support was received for the research, authorship, and/or publication of this article.
Acknowledgments
The authors would like to acknowledge our colleagues at Heirloom.
Conflict of interest
NM and DD were employed by the Heirloom Carbon Technologies, Inc.
Publisher’s note
All claims expressed in this article are solely those of the authors and do not necessarily represent those of their affiliated organizations, or those of the publisher, the editors and the reviewers. Any product that may be evaluated in this article, or claim that may be made by its manufacturer, is not guaranteed or endorsed by the publisher.
References
Amazon . (2018). “2017 Amazon Annual Report.” Available at: https://s2.q4cdn.com/299287126/files/doc_financials/annual/Amazon_AR.PDF
Amazon . (2019). “2018 Amazon Annual Report.” Available at: https://s2.q4cdn.com/299287126/files/doc_financials/annual/2018-Annual-Report.pdf.
Amazon . (2020). “2019 Amazon Annual Report.” Available at: https://s2.q4cdn.com/299287126/files/doc_financials/2020/ar/2019-Annual-Report.pdf.
Amazon . (2021). “2020 Amazon Annual Report.” Available at: https://s2.q4cdn.com/299287126/files/doc_financials/2021/ar/Amazon-2020-Annual-Report.pdf.
Amazon . (2022). “2021 Amazon Annual Report.” Available at: https://s2.q4cdn.com/299287126/files/doc_financials/2022/ar/Amazon-2021-Annual-Report.pdf.
Amazon . (2023). “2022 Amazon Annual Report.” Available at: https://s2.q4cdn.com/299287126/files/doc_financials/2023/ar/Amazon-2022-Annual-Report.pdf.
Amazon . (2024). “AWS Global Infrastructure.” Available at: https://aws.amazon.com/about-aws/global-infrastructure/
Amazon.com . (2005). “2004 Amazon.com annual report.” Available at: https://s2.q4cdn.com/299287126/files/doc_financials/annual/2004_Annual_report.pdf.
Amazon.com . (2006). “2005 Amazon.com annual report.” Available at: https://s2.q4cdn.com/299287126/files/doc_financials/annual/AMZN2005AnnualReport.pdf.
Amazon.com . (2007). “2006 Amazon.com annual report.” Available at: https://s2.q4cdn.com/299287126/files/doc_financials/annual/2006AnnualReport.pdf.
Amazon.com . (2008). “2007 Amazon.com annual report.” Available at: https://s2.q4cdn.com/299287126/files/doc_financials/annual/2007AR.pdf.
Amazon.com . (2009). “2008 Amazon.com annual report.” Available at: https://s2.q4cdn.com/299287126/files/doc_financials/annual/Amazon_Annual_Report_2008.pdf.
Amazon.com . (2010). “2009 Amazon.com annual report.” Available at: https://s2.q4cdn.com/299287126/files/doc_financials/annual/AMZN_Annual-Report-2009-(final).pdf.
Amazon.com . (2011). “2010 Amazon.com annual report.” Available at: https://s2.q4cdn.com/299287126/files/doc_financials/annual/117006_099_bmk_AR.pdf.
Amazon.com . (2012). “2011 Amazon.com annual report.” Available at: https://s2.q4cdn.com/299287126/files/doc_financials/annual/269317_023_bmk.pdf.
Amazon.com . (2013). “2012 Amazon.com annual report.” Available at: https://s2.q4cdn.com/299287126/files/doc_financials/annual/2012-Annual-Report.PDF.
Amazon.com . (2014). “2013 Amazon.com annual report.” Available at: https://s2.q4cdn.com/299287126/files/doc_financials/annual/2013-Annual-Report.pdf.
Amazon.com . (2015). “2014 Amazon.com annual report.” Available at: https://s2.q4cdn.com/299287126/files/doc_financials/annual/AMAZON-2014-Annual-Report.pdf.
Amazon.com . (2016). “2015 Amazon.Com annual report.” Available at: https://s2.q4cdn.com/299287126/files/doc_financials/annual/2015-Annual-Report.pdf.
Amazon.com . (2017). “2016 Amazon.Com annual report.” Available at: https://s2.q4cdn.com/299287126/files/doc_financials/annual/2016-Annual-Report.pdf.
APS . (2011). “Direct air capture of CO2 with chemicals.” Available at: http://www.aps.org/policy/reports/popa-reports/loader.cfm?csModule=security/getfile&PageID=244407.
Bedard, Mathieu . (2021). “The history of pallet racks.” Damotech. Available at: https://www.damotech.com/blog/the-history-of-pallet-racks (Accessed June 2, 2021).
Bergman, A, and Rinberg, A. (2020). The case for carbon dioxide removal: from science to justice. In CDR Primer. eds. Wilcox, J., Kolosz, B., Freeman, J. Available at: https://cdrprimer.org/read/chapter-1#sec-1-4.
Bertram, N, Fuchs, S, Mischke, J, Palter, R, Strube, G, and Woetzel, J. (2019). Modular construction: from projects to products, McKinsey & Company.
Beuttler, C., Charles, L., and Wurzbacher, J. (2019). The role of direct air capture in mitigation of anthropogenic greenhouse gas emissions. Front. Climate 1:10. doi: 10.3389/fclim.2019.00010
CarbonCure Technologies . (2023). “Heirloom, CarbonCure technologies and central concrete achieve first-ever storage of atmospheric CO2 captured by direct air capture in concrete.” GlobalNewswire. San Jose, California: 2023. Available at: https://www.globenewswire.com/news-release/2023/02/03/2601156/0/en/Heirloom-CarbonCure-Technologies-and-Central-Concrete-Achieve-First-Ever-Storage-of-Atmospheric-CO2-Captured-By-Direct-Air-Capture-In-Concrete.html.
Carmeuse . (2024). “What is calcium carbonate limestone?” Available at: https://www.carmeuse.com/na-en/references/case-studies-success-stories/what-calcium-carbonate-limestone.
Cassino, Kathryn E, Bernstein, Harvey M, Gudgel, John, Gudgel Michele Russo, John A, Laquidara-Carr, Donna, Director, Leed AP, et al. (2011). “Construction prefabrication and modularization: increasing productivity in the construction.” Available at: https://www.nist.gov/system/files/documents/el/economics/Prefabrication-Modularization-in-the-Construction-Industry-SMR-2011R.pdf.
Chauhan, K., Peltokorpi, A., Lavikka, R., and Seppänen, O. (2022). The monetary and non-monetary impacts of prefabrication on construction: The Effects of Product Modularity. doi: 10.3390/buildings12040459
Custodio, L., and Machado, R. (2020). Flexible automated warehouse: a literature review and an innovative framework. Int. J. Adv. Manuf. Technol. 106, 533–558. doi: 10.1007/s00170-019-04588-z
Dietrich, R. V. March 13, (2024). “Calcite.” In Britannica, The Editors of Encyclopedia Britannica. Available at: https://www.britannica.com/science/calcite.
Faber, Grant . (2024). “A list of every direct air capture (DAC) company in the world.” January 2024. Available at: https://carbonbasedcommentary.substack.com/p/a-list-of-every-direct-air-capture
Flyvbjerg, Bent . (2021). “Make megaprojects more modular.” Available at: https://ssrn.com/abstract=3937465.
Flyvbjerg, B, and Gardner, D. (2023). How big things get done: The surprising factors that determine the fate of every project, from home renovations to space exploration and everything in between. Signal.
Funaki, K. (2023). “Product automation and innovation” in Springer Handbooks, vol. F674 (Springer Science and Business Media Deutschland GmbH), 561–584. doi: 10.1007/978-3-030-96729-1_24
Gebald, C, Piatkowski, N, Rüesch, T, and André Wurzbacher, J. (2017). Low-Pressure Drop Structure of Particle Adsorbent Bed for Adsorption Gas Separation Process.
Gershenson, J. K., Prasad, G. J., and Zhang, Y. (2003). Product modularity: definitions and benefits. J. Eng. Des. 14, 295–313. doi: 10.1080/0954482031000091068
Harrison-Atlas, D., Lopez, A., and Lantz, E. (2022). Dynamic land use implications of rapidly expanding and evolving wind power deployment. Environ. Res. Lett. 17. doi: 10.1088/1748-9326/ac5f2c
Holmes, G., and Keith, D. W. (2012). An air-liquid contactor for large-scale capture of CO2 from air. Philos. Trans. R. Soc. A Math. Phys. Eng. Sci. 370, 4380–4403. doi: 10.1098/rsta.2012.0137
International Energy Agency . (2022). “Direct air capture: a key Technology for net Zero.” Available at: www.iea.org/t&c/.
Intergovernmental Panel on Climate Change (IPCC) . (2018). Global warming of 1.5 °C. Intergovernmental Panel on Climate Change. Available online at: https://www.ipcc.ch/sr15/
Jacobs, M., Droge, C., Vickery, S. K., and Calantone, R. (2010). Product and process Modularity’s effects on manufacturing agility and firm growth performance. J. Prod. Innov. Manag. 28, 123–137. doi: 10.1111/j.1540-5885.2010.00785.x
Kasturi, A., Jang, G. G., Akin, A. D.-T., Jackson, A., Jun, J., Stamberga, D., et al. (2023). An effective air–liquid contactor for CO2 direct air capture using aqueous solvents. Sep. Purif. Technol. 324:124398. doi: 10.1016/j.seppur.2023.124398
Keith, D. W., Holmes, G., Angelo, D. S., and Heidel, K. (2018). A process for capturing CO2 from the atmosphere. Joule 2, 1573–1594. doi: 10.1016/j.joule.2018.05.006
Küng, L., Aeschlimann, S., Charalambous, C., McIlwaine, F., Young, J., Shannon, N., et al. (2023). A roadmap for achieving scalable, safe, and low-cost direct air carbon capture and storage. Energy Environ. Sci. 16, 4280–4304. doi: 10.1039/d3ee01008b
Lebling, K., Leslie-Bole, H., Psarras, P., Bridgwater, E., Byrum, Z., and Pilorgé, H. (2022). Direct air capture: assessing impacts to enable responsible scaling. World Res. Inst. doi: 10.46830/wriwp.21.00058
Malhotra, A., and Schmidt, T. S. (2020). Accelerating low-carbon innovation. In Joule: Cell Press, 4:2259–2267. doi: 10.1016/j.joule.2020.09.004
Mazzotti, M., Baciocchi, R., Desmond, M. J., Socolow, R. H., Tavoni, M., Socolow, R., et al. (2013). Direct air capture of CO2 with chemicals: optimization of a two-loop hydroxide carbonate system using a countercurrent air-liquid contactor. Clim. Chang. 118, 119–135. doi: 10.1007/s10584-012-0679-y
McQueen, N., Ghoussoub, M., Mills, J., and Scholten, M. (2022). A scalable direct air capture process based on accelerated weathering of calcium hydroxide. Heirloom Carbon Technol., 1–9.
McQueen, N., Gomes, K. V., McCormick, C., Blumanthal, K., Pisciotta, M., and Wilcox, J. (2021). A review of direct air capture (DAC): scaling up commercial technologies and innovating for the future. Prog. Energy 3. doi: 10.1088/2516-1083/abf1ce
Meera, C. M. (2013). Pre-engineered building Design of an Industrial Warehouse. Int. J. Eng. Sci. Emerg. Technol. 5:75–82.
NASEM (2019). Negative emissions technologies and reliable sequestration: A research agenda. National Academies Press. Washington, DC: The National Academies Press.
NASEM (2023). Carbon dioxide utilization markets and infrastructure: Status and opportunities: A first report. Washington, DC: National Academies Press.
Ong, Sean, Campbell, Clinton, Denholm, Paul, Margolis, Robert, and Heath, Garvin. (2013). “Land-use requirements for solar power plants in the United States.” Available at: www.nrel.gov/publications.
Pisciotta, M., Davids, J., and Wilcox, J. (2022). “Greenhouse gas removal: overview and current status of deployment” in Greenhouse gas removal technologies eds. M. Bui and N. Mac Dowell, (The Royal Society of Chemistry), 6–26. doi: 10.1039/9781839165245-00006
Plumer, Brad . (2023). “In a U.S. first, a commercial plant starts pulling carbon from the air.” The New York Times, November 9, 2023. Available at: https://www.nytimes.com/2023/11/09/climate/direct-air-capture-carbon.html.
Quale, J., Eckelman, M. J., Williams, K. W., Sloditskie, G., and Zimmerman, J. B. (2012). Construction matters: comparing environmental impacts of building modular and conventional homes in the United States. J. Ind. Ecol. 16, 243–253. doi: 10.1111/j.1530-9290.2011.00424.x
Rao, Leena . (2012). “Amazon acquires robot-coordinated order fulfillment company kiva systems for $775 million in cash.” TechCrunch. Available at: https://techcrunch.com/2012/03/19/amazon-acquires-online-fulfillment-company-kiva-systems-for-775-million-in-cash/?guccounter=1&guce_referrer=aHR0cHM6Ly93d3cuZ29vZ2xlLmNvbS8&guce_referrer_sig=AQAAAGKY8-deg9KOXDyP-mvdD3D5lOV5U2kbrz25655h6MHLkuOhIT3Uw_xOmvYTzx8st0t7SDUZimeS0fR2V0TGsfq1u83f_Tb5IWCU_QT6QZuilwmjLalN6tXFzRcoJbYOF1g05R9djELoc9RGs-WnbaOPje9rJbKF0v12qtjfVn4b (Accessed March 19, 2012).
Rubin, E. S., Azevedo, I. M. L., Jaramillo, P., and Yeh, S. (2015). A review of learning rates for electricity supply technologies. Energy Policy 86, 198–218. doi: 10.1016/j.enpol.2015.06.011
Sandalow, D., Aines, R., Friedmann, J., McCormick, C., and Sanchez, D. (2021). Biomass carbon removal and storage (BiRCS) roadmap. Livermore. doi: 10.2172/1763937
Schmidt, O., Hawkes, A., Gambhir, A., and Staffell, I. (2017). The future cost of electrical energy storage based on experience rates. Nat. Energy 2:17110. doi: 10.1038/nenergy.2017.110
Spiteri, Alexander, Megerle, Benjamin, Calbry-Muzyka, Adelaide, Casas, Nathalie, and Wurzbacher, Jan. (2021). “Method for capture of carbon dioxide from ambient air and corresponding Adsorber structures with a plurality of parallel surfaces.”
Tompkins, J., White, J., Bozer, Y., and Tanchoco, J. M. (2014). Facilities planning. 4th. Hoboken, NJ: Edn: Wiley.
Ulrich, K. (1994). “Fundamentals of product modularity” in Management of Design (Dordrecht: Springer Netherlands), 219–231.
Xiao-Long, W., Wu, C.-F., Guo-Dong, L., and Qing-Xie, C. (2017). “A robot navigation method based on RFID and QR code in the warehouse” in 2017 Chinese automation congress (CAC). Jinan, China:(IEEE), 7837–7840.
Yeh, S., and Rubin, E. S. (2007). A centurial history of technological change and learning curves for pulverized coal-fired utility boilers. Energy 32, 1996–2005. doi: 10.1016/j.energy.2007.03.004
Zhang, Mary . (2023). “United States data centers: top 10 locations.” Dgtl Infra. Available at: https://dgtlinfra.com/united-states-data-centers/ (Accessed February 1, 2023).
Keywords: direct air capture, carbon dioxide removal, automation, industrial automation, warehouse automation, carbon capture
Citation: McQueen N and Drennan D (2024) The use of warehouse automation technology for scalable and low-cost direct air capture. Front. Clim. 6:1415642. doi: 10.3389/fclim.2024.1415642
Edited by:
Volker Sick, University of Michigan, United StatesReviewed by:
Mijndert Van Der Spek, Heriot-Watt University, United KingdomStephen McCord, University of Michigan, United States
Copyright © 2024 McQueen and Drennan. This is an open-access article distributed under the terms of the Creative Commons Attribution License (CC BY). The use, distribution or reproduction in other forums is permitted, provided the original author(s) and the copyright owner(s) are credited and that the original publication in this journal is cited, in accordance with accepted academic practice. No use, distribution or reproduction is permitted which does not comply with these terms.
*Correspondence: Noah McQueen, aGVsbG9AaGVpcmxvb21jYXJib24uY29t