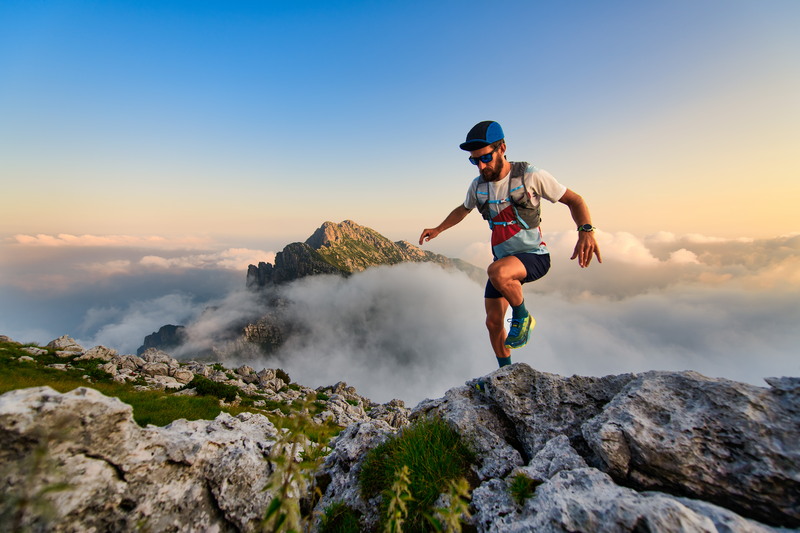
95% of researchers rate our articles as excellent or good
Learn more about the work of our research integrity team to safeguard the quality of each article we publish.
Find out more
ORIGINAL RESEARCH article
Front. Clim. , 13 October 2021
Sec. Carbon Dioxide Removal
Volume 3 - 2021 | https://doi.org/10.3389/fclim.2021.729259
This article is part of the Research Topic Pathways Towards Negative Emissions in Industry View all 6 articles
Switzerland, such as most of the other countries which are part of the Paris agreement, decided to reduce GHG emissions to zero by 2050. The ambition of net-zero GHG emission across all industrial sectors can only be achieved by rapid decarbonization and the deployment of negative emission technologies to compensate residual emissions from for example agriculture. In the scope of this work, the proof of technology of a negative emission value chain at industrial scale in the concrete sector is presented. The core of the system is a mineralization technology, which fixes biogenic CO2 permanently as calcium carbonate in concrete aggregate. In addition, the net-negativity in terms of GHG emissions and environmental burdens beyond these are quantified in a Life Cycle Assessment (LCA). It could be shown that an industrial-scale mineral carbonation process can be seamlessly integrated in today's concrete recycling processes and that it can process relevant amounts of concrete aggregate while storing on average 7.2 kg CO2 per ton of concrete aggregate. Moreover, material tests revealed that the carbonated concrete aggregate fulfills the same service as the regular one—thus no significant effects on the concrete properties could be observed. The LCA shows that every processing step requires materials and energy, and thus generates associated emissions. However, from a cradle to gate perspective, the carbon removal efficiency is 93.6%. Thus, 1,000 kg of CO2 stored generate 64 kg of CO2-eq. emissions. Furthermore, it could be shown that biogas upgrading can supply sufficient amounts of CO2 until 2030 in Switzerland. From 2030 on, more and more CO2 from other emission sources, such as waste incineration, need to be utilized to exploit the full potential of the value chain, which is going to be 560 kt of negative CO2 emissions in Switzerland in 2050, corresponding to 30% of the projected demand within the national borders.
Limiting global warming to 1.5–2 degrees requires substantial and fast reduction of greenhouse gas (GHG) emissions in basically all economic sectors (Tollefson, 2018; Allen et al., 2018). Several countries and economic regions have announced the goal of “carbon neutrality” by around mid of this century the European Union and Switzerland among them (Runge-Metzger, 2018; Geden and Schenuit, 2019; Geden et al., 2019; Kirchner, 2020). However, it is virtually impossible to eliminate GHG emissions entirely from some economic activities, such as agriculture, and it is also very likely that in the long term some industrial processes will cause “residual emissions”, which cannot be reduced to zero (Allen et al., 2018; Waisman et al., 2019). Therefore, so-called “negative emission technologies” (NET) or “carbon dioxide removal” (CDR) options become important. Such NET or CDR options permanently remove carbon dioxide from the atmosphere they act as carbon sinks and allow for compensation of residual GHG emissions, therefore enabling “net-zero” GHG emissions without actually reducing overall antrophogenic GHG emissions to zero (Van Vuuren et al., 2013; Rogelj et al., 2015; Geden and Schenuit, 2019; Geden et al., 2019; Kirchner, 2020). Model-based evaluations of energy scenarios have shown that reaching the 1.5 degree goal will be almost impossible without implementing NETs at scale (Gasser et al., 2015; Van Vuuren et al., 2017, 2018; Creutzig et al., 2019; Fuhrman et al., 2019). Without NET in place, drastic reductions of energy demand and consumption in general would be required (Grubler et al., 2018).
A broad set of CDR options could be employed the most frequently discussed ones are afforestation and reforestation, biochar, soil carbon sequestration, enhanced weathering, ocean fertilization, Bioenergy with Carbon Capture and Storage (BECCS) and Direct Air Carbon Capture and Storage (DACCS) (Fuss et al., 2018; Minx et al., 2018). All of them have their specific merits, but can also face certain obstacles and implementation barriers - be it due to high costs, land, water (Rosa et al., 2020a,b) or energy use, or unknown potentially harmful side-effects (Anderson and Peters, 2016; Fajardy and Mac Dowell, 2017; Fuss et al., 2018; Nemet et al., 2018; Bednar et al., 2019). To generate negative emission of the required scale, a portfolio of CDR options - each suitable for specific regional conditions—needs to be deployed and the corresponding obstacles in their value chains have to be addressed and overcome. A CDR option largely overlooked so far is related to the construction sector, which itself constitutes a large source of GHG emissions (CEMSUISSE, 2020; Miller and Moore, 2020): pilot and demonstration projects have shown that recycled concrete aggregate (RCA) can be carbonated, i.e., it can mineralize CO2, when it is exposed to a concentrated CO2 stream.1 This mineralized CO2 is permanently fixed and if the CO2 is of biogenic origin, carbonating RCA results in a negative emission technology. Biogenic CO2 is easily available when biogas, the output of anaerobic digestion of biogenic waste, is “upgraded” to methane by removing the CO2 fraction, which is commonly between 30 and 45% (Angelidaki et al., 2019; Kober et al., 2019; Teske et al., 2019; Zhang et al., 2020). Today, main sources for such biogenic waste are agriculture and wastewater treatment plants. It is commonly agreed that, because this CO2 was initially removed from the atmosphere as a result of biomass growth, its release within a short time span does not contribute to the long-term radiative forcing of the atmosphere (Levasseur et al., 2010; Wiloso et al., 2016; Lueddeckens et al., 2020). Globally, 30 Gigatonnes of concrete have been used in 2020 (van Oss, 2021), and due to growing economies after the Second World War, amounts of available demolition concrete are rising quickly. As a result, CO2 mineralization in RCA could—depending on its actual negative emission effect—represent an important CDR option. As for any CDR option, also the environmental performance of carbonating RCA must be evaluated from a life-cycle perspective before large-scale implementation (Goglio et al., 2020; Terlouw et al., 2021). The method at hand for this purpose is Life Cycle Assessment (LCA), which is used to quantify a comprehensive set of environmental indicators of products and services, considering their production, use, and end-of-life (Guinée and Lindeijer, 2002; Arvanitoyannis, 2008). Some of the environmental impacts of the concrete sector (Worrell et al., 2001; Miller and Moore, 2020) as well as its role on a national pathway toward carbon-neutrality (Obrist et al., 2021) have been analyzed. Also various potentially environmentally beneficial production and recycling pathways have been examined by means of LCA already (Knoeri et al., 2013; Gursel et al., 2014; Vieira et al., 2016; Hafez et al., 2019; Zhang et al., 2019; Colangelo et al., 2020; Farina et al., 2020). However, to the best of our knowledge we present the first LCA of carbonated RCA potentially acting as negative emission technology.
Mineralization of CO2 in concrete is a reaction which occurs in concrete structures that are exposed to a CO2 source, e.g., ambient air. More precisely, the carbonation reaction takes place in the pore water. This phenomenon, termed natural carbonation, reduces the pH of concrete, thus triggering corrosion of reinforced steel bars—and then determining the end of life of structural concrete. For this reason, carbonation of concrete structures was intensively studied in the past. The thickness of the carbonated layer increases with exposure time, CO2 partial pressure and diffusivity of CO2 within the pore network of the cement matrix (Lagerblad, 2005; Leemann and Moro, 2017). The diffusivity of CO2 depends on the water saturation of the concrete's pore network. A relative humidity range of 50 to 70% was identified to provide the ideal pore water saturation for a fast progression of carbonation. Based on these relationships, models have been developed which have been experimentally validated (Papadakis et al., 1989, 1991).
In the last decade, CO2 mineralization in concrete during the concrete batching phase (Monkman et al., 2016; Meyer et al., 2018), natural carbonation throughout the service life of a concrete structure and at the end of life (Leemann and Hunkeler, 2016) gained attention since they are viewed as options to mitigate part of the concrete's climate impact. A group of researchers made a model based attempt to determine the global annual CO2 fixed by natural carbonation. They estimate that 43% of the global annual amount of calcination emissions are mitigated by natural carbonation (Xi et al., 2016). However, other researchers experimentally studied the degree of carbonation at end-of-life concrete structures and determined that 3.6% (Birolini, 2019) to 10% (Leemann and Hunkeler, 2016) of the process based cement manufacturing emissions are reabsorbed, thus questioning the conclusions drawn by Xi et al. (2016).
After concrete structures are dismantled and broken into concrete aggregate, they can undergo accelerated carbonation that fixes even more CO2. The principles of accelerated carbonation and of natural carbonation are the same—with the difference that accelerated carbonation processes may profit of increased CO2 partial pressures. Furthermore, Seidemann et al. (2015) identified that a temperature increase from 25 to 50°C can increase the CO2 uptake within a processing time of 3–9 h by a factor of 3 to 10. As a concluding step, Seidemann et al. (2015); Xuan et al. (2016) assessed the performance of carbonated concrete aggregate incorporated in fresh concrete. They measured an increase of the 28-day compressive strength of concrete, in case the RCA had been carbonated prior to its incorporation.
So far, research and development in accelerated carbonation has mainly focused on lab-scale activities. Results are promising, and have motivated an academic and industrial consortium of partners, namely the clean tech company neustark AG, the concrete recycling facility Kästli Bau AG in collaboration with the concrete plant Frischbeton Rubigen AG, the waste water treatment and biogas upgrading plant Ara Region Bern AG in collaboration with ETH Zurich, to demonstrate a negative emission value chain at scale in the scope of the RECARB2 project. For this purpose, all components of the value chain, namely the CO2 supply chain as well as the mineralization technology were constructed and operated—and the use of the material in concrete was tested.
Our analysis primarily answers the questions whether carbonated RCA using biogenic CO2 can indeed deliver negative GHG emissions from a technological and life-cycle perspective, i.e., whether it can permanently remove CO2 from the atmosphere, and what the driving factors determining the amount of potential CO2 removal are. Furthermore, we quantify the effect of using carbonated RCA in concrete on the environmental performance of such concrete compared to virgin concrete and concrete made of standard RCA. We also discuss the main driving forces behind the uptake of CO2 and options to increase uptake rates in the future by improved process design. Finally, we estimate the overall amount of potential CO2 removal, which could be enabled by this NET in Switzerland, as well as globally, based on current and future figures on concrete recycling and available appropriate sources of biogenic CO2.
The CO2 mineralization value chain (red box, Figure 1) consists of the liquefaction, transport and evaporation of CO2 as well as of the CO2 mineralization plant. The process is embedded into the concrete recycling and reuse value chain. The two components of major relevance for the overall system are the operation of the CO2 mineralization plant and the effect of carbonation on concrete mix designs. All other components of the value chain have been in commercial use since many years. Hence, lab-scale experiments were conducted to investigate the phenomenology of the carbonation process, particularly the effect of grain size and processing time. Moreover, an industrial scale mineralization plant was designed, constructed and operated to demonstrate the technology in a relevant industrial setting. Finally, the carbonated RCA was incorporated in fresh concrete to investigate potential effects of carbonation on the quality of the concrete mix design.
Figure 1. System boundaries of the functional units 1 kg of RCA that are carbonated and 1 m3 of concrete of a specific strength class. Material flows and processes of the virgin concrete (VC) system, the recycling concrete (RC) system and the carbonated recycling concrete (C-RC) system.
RCA is concrete crushed into the size of aggregate and sand. It contains gravel and sand surrounded by cement paste. Two different types of concrete aggregate were used. At lab-scale, 80 liters of concrete (composition according to Supplementary Table 1) were batched by Swiss Federal Laboratories for Material Sciences and Technology (EMPA). In order to mimic RCA, the hardened concrete was crushed, sieved into size fractions and stored in airtight containers until it was used in the experiments.
The daily demand of 120 tons RCA for the industrial scale mineralization plant was supplied by commercially available RCA at the concrete plant Kästli. The origin and composition of this material is unknown, but it is very likely that the concrete was produced with Ordinary Portland cement (CEM I) (Jacobs, 2011) and that it is 60–80 years old. Hence, the same composition for both RCA types was assumed. The material was stored outdoors and weathered in stockpiles for a period of several summer months before it was carbonated in the mineralization plant.
Industrial grade liquefied CO2 (Pangas, >99.5% CO2) sourced from bottles and a CO2 semitrailer was used for the experimental campaigns at lab and industrial scale, respectively. The liquefaction step itself reduces the level of impurities. These remaining impurities are typically oxygen, nitrogen and methane, which act as inert gases and thus have no influence on the process of concrete carbonation.
A lab scale setup was designed and constructed to conduct the laboratory tests. The core of the lab setup is a 850 ml reactor, which can be sealed gas tight. The reactor has a gas inlet at the bottom and a gas outlet at the top. In addition, the reactor is placed on a scale.
The mineralization plant uses two reactor containers with a total volume of 34 m3. One of the reactor containers is placed on a 40 t container balance. The gas injection rate and the gas outlet flow rate of the mineralization plant are measured by a gas flow meter. In addition, the gas outlet concentration is measured by a gas analysis device.
At the beginning of every lab scale experiment, the setup was filled with a few 100 g of RCA. The 850 ml reactor was sealed air tight and the gas inlet and outlet pipes were connected. The experiments were conducted at 20°C and ambient pressure. At time zero, the gas inlet flow was set at 500 mg of CO2 per minute and reduced stepwise to 50, 25, 12 and 6 mg of CO2 per minute. This procedure was followed to minimize the amount of gas exiting the reactor. The weight of the material was measured as a function of time. After 72 h, the gas flow was switched off, the material discharged and the experiment completed.
At industrial scale, a five axles truck loaded the empty reactor container with a hook and traveled to the RCA stock pile. The roof of the container was opened and a wheel loader heaved approximately 20 t of RCA into the reactor container. The roof was closed again and the truck traveled back to the terminal and placed the container on a 40 t balance. The CO2 inlet and outlet pipes were connected and the amount of material was measured on the balance. CO2 was injected for 2 h, while the change in mass of the RCA was recorded by the balance to quantify the uptake of CO2. The initial CO2 injection rate of 180 kg CO2 per hour was stepwise reduced such that the rate of CO2 mineralization was similar to the CO2 feed rate. The carbonation experiment was conducted at ambient temperature and pressure. After 2 h, the injection was stopped and the RCA was discharged.
The amount of CO2 injected can be calculated as:
where is the total amount of CO2 fed into the reactor, at a gas inlet flow rate Fin and a CO2 mole fraction of ; t is the experimental time. The amount of CO2 leaving the system can be calculated as:
where is the total amount of CO2 exiting the reactor through the exiting gas stream, Fout the gas outlet flow rate and the CO2 mole fraction in the exiting gas stream. Moreover, when the RCA is discharged from the reactor containers, the residual CO2 () in the void space ϵ in-between the particles is lost during to the atmosphere; the corresponding amount is calculated as:
where VR is the reactor volume, p the pressure of the gas phase, MCO2 the molar mass of CO2, the CO2 mole fraction in the void space of the particles during the discharge of the material, R the ideal gas constant and T the temperature. The amount of CO2 stored in one batch of material is :
In order to make results better comparable and to mitigate the effect of different material loadings in the reactor, the CO2 mineralized per unit of concrete aggregate is determined as:
where is the mass of RCA filled into the reactor. Moreover, the CO2 storage efficiency can be calculated as:
Part of the RCA was used to test the performance of the carbonated RCA with respect to the non-carbonated RCA in concrete mix designs. For this reason, concrete mix designs with a RCA content of 40% and a cement content of 280, 295 and 315 kg of tpye CEM II B were batched in a 40 liter lab-scale mixer and a 3.5 m3 industrial scale mixer according to SN EN 206. The properties related to strain (SN EN 12350) were measured. Afterwards, the concrete was molded into cubes and cured according to SN EN 12390-2. The compressive strength (SN EN 12390-3), the density (SN EN 12390-7) and the Young's modulus (SN EN 12390-13) were measured at day 28 in an external, certified laboratory.3
The ISO standards (International Organization for Standardization, 2006a,b) define LCA in terms of goal and scope, life cycle inventory, life cycle impact assessment and interpretation of the results. This work follows the regulatory framework. Moreover, a specific guideline for LCA about CCS and CCU technologies can be found elsewhere (Müller et al., 2020a).
The main aim of this paper is to investigate the negative emission potential of a CO2 mineralization value chain in the concrete sector. The environmental performance of the negative emission value chain, which has been demonstrated in the RECARB4 project at scale, will be critically assessed. In addition, results will be extrapolated to the Swiss concrete sector, and the evolution of the current, near- and long-term sink capacity, which is generated by this technology, will be discussed. To this end, we use the well-established method of Life Cycle Assessment (LCA), which aims at quantifying the environmental burdens generated along the entire life cycle—production, use, and end-of-life—of products and services (Guinée and Lindeijer, 2002; Arvanitoyannis, 2008). These burdens (i.e., emissions to air, water bodies, and soil as well as resource consumption) are quantified with reference to a functional unit (FU) to provide a common basis for comparison between different products. The environmental burdens are characterized against indicators that represent damages borne by mid- (e.g., Global Warming) and endpoint (e.g., Human health) recipients, respectively, via cause-effect pathways (e.g., from the emission of a greenhouse gas to the radiative forcing of the atmosphere). Within a product system in an LCA, so-called foreground and background data are distinguished. While foreground data represent energy and material flows as well as emissions associated to the product (chain) investigated, background data represent those exchanges associated with material and energy supply chains not directly investigated, but still relevant, e.g., steel supply for the construction of trucks used for the transport of concrete aggregate. The foreground system and data are discussed in the following sub-sections; as source of background data we use the ecoinvent database, version v3.6, system model “allocation, cut-off by classification” (Wernet et al., 2016).
Figure 1 visualizes the negative CO2 emission chain we investigate by means of LCA. Old concrete infrastructure such as buildings and bridges are dismantled and the demolition concrete is transported to a concrete recycling facility in the vicinity. There, the demolition concrete is crushed into recycling concrete aggregate (RCA) of a specific grain size distribution. Reinforcing steel as well as non-mineral light weight materials such as wood and plastics are sorted out.
The CO2 for the mineralization of the RCA comes from a biogenic source such as a wastewater treatment plant. These plants often produce biogas, consisting mainly of methane and carbon dioxide. To increase the calorific value of biogas, biogas upgrading is conducted whereby CO2 is removed (Angelidaki et al., 2019), which is normally released to the atmosphere. In case of mineralization, the CO2 is collected, liquefied, temporarily stored and finally transported to the mineralization plant located at the concrete recycling facility. This LCA only considers biogenic CO2 from biomass waste, or more precisely from the upgrade of biogas generated via anaerobic digestion of biogenic waste. In line with the background LCA database, this biogenic waste is supplied free of environmental burdens, since those are assigned to the service of treating this waste, or in other words to the agricultural sector generating this waste.
Two mineralization containers filled with RCA are transported next to the process center. The CO2 inlet pipe and the gas discharge pipe are attached to the front walls of the containers. The CO2 tank contains the liquid CO2 which has to be evaporated before it feeds the two containers for the process duration (typically 120 min) at a high flow rate. The CO2 reacts with the cement phase of the RCA to yield calcium carbonate; CO2 uptake is measured. At the end of the process, the carbonated RCA are stockpiled.
The carbonated RCA is used as sand and gravel substitute for the production of concrete. According to SN EN 206, concrete with a secondary aggregate content exceeding 25% is categorized as recycling concrete. The carbonated RCA exhibits a decreased porosity and water absorption compared to regular RCA. The reduction in porosity can be attributed to the formation of CaCO3 in the pore network, which occupies more space than the corresponding cement minerals. This effect may alter the properties of new concrete, which can result in concrete of increased 28-day compressive strength or Young's modulus (Seidemann et al., 2015; Xuan et al., 2016). In such a case, the clinker content can be reduced compared to conventional recycling concrete while still complying with the same quality standards. However, the exact extent of clinker reduction depends on many factors, among which the quality of the primary and secondary material, the concrete mix design and the concrete chemistry. In this work, we demonstrate in a set of material tests that concrete made from carbonated RCA provides the same service as concrete made from regular RCA.
In many locations, it is more convenient to use RCA unbound for instance as a road base material. In the scope of this work, this use is not considered. However, the negative emission value chain and thus the associated environmental impacts do not change in case of different uses.
Global climate change mitigation policies rely on a combination of emission avoidance and negative emissions. Emission avoidance will allow to reduce the emissions by for example reducing the demand for clinker through a more efficient use of cement and concrete (Habert et al., 2020). Although emission avoidance is of key importance, it will not be sufficient to reduce emissions to zero. Negative emissions technologies remove residual emissions from the atmosphere and fix them permanently. Tanzer and Ramírez (2019) established four criteria to determine whether a technology leads to negative CO2 emissions, i.e., permanent removal of CO2 from the atmosphere. The carbonated RCA process chain must comply with such criteria:
1. Physical greenhouse gases are removed from the atmosphere.
2. The biogenic CO2 produced in the biogas upgrader and used for mineralization is normally released as a waste flow into the atmosphere. With the proposed technology, this CO2—originally taken up from the atmosphere by biomass—is stored in concrete aggregate instead of being released back to the atmosphere in a short period of time.
3. The removed gases are stored away from the atmosphere in a manner intended to be permanent.
4. The CO2 reacts with the cement phase contained in RCA to CaCO3. Even extraordinary environmental conditions such as acidic rain (Teir et al., 2006) and temperatures of 100°C do not result in a release of the fixed CO2 into the atmosphere (Villain et al., 2007). The European Court of Justice considers CO2 mineralized to CaCO3 in one of their sentences as per permanently stored (Siwior and Bukowska, 2018). Since the CO2 undergoes a chemical reaction and is fixed as CaCO2 mineral, the concrete aggregate can undergo further recycling loops or it can be landfilled without releasing the fixed CO2 to the atmosphere.
5. Upstream and downstream greenhouse gas emissions associated with the removal and storage process, such as biomass origin, energy use, gas fate, and co-product fate, are comprehensively estimated and included in the emission balance.
6. The mineralization process has neither a significant impact on the upstream nor on the downstream processes, i.e., the use of the material. Thus, only the emissions of the CO2 value chain have to be considered, which is the case in our LCA.
7. The total quantity of atmospheric greenhouse gases removed and permanently stored is larger than the total quantity of greenhouse gases emitted to the atmosphere
8. To determine whether the value chain is net-negative, the GHG emissions of the CO2 supply chain and of the carbonation of RCA have to be smaller than the amount of biogenic CO2 that can be stored. This evaluation is the core element of this work.
This LCA aims to validate different aspects of the negative emission value chain. In a first step, the CO2 sink potential in RCA is analyzed. Thus, 1 kg of RCA carbonated has been chosen as the functional unit. In a further step, the environmental performance of CO2 mineralized recycling concrete (C-RC) has been compared to conventional recycling concrete (RC) and concrete using primary material, virgin concrete (VC). For this comparison, the system boundaries are drawn differently and the functional unit is defined as 1 m3 of concrete of a specific strength class.
Figure 1 illustrates the system boundaries of the two functional units, namely in red for 1 kg of carbonated RCA and in yellow for 1 m3 of concrete. The system boundary of the functional unit 1 kg of carbonated RCA includes only the negative emission value chain from the liquefaction of the CO2 to the carbonation of the RCA. Since the carbonated and regular RCA are chemically identical (less than 1% of difference in their composition), and (as shown later in this paper, see Figure 4) fulfill the same service in the downstream processes, a cradle to gate approach is justified (Müller et al., 2020a).
For the comparison of the three different concrete types the system boundary encompasses the entire value chain of concrete production. The systems of the three different concrete types contain the supply of raw materials such as cement, water, admixtures and aggregate (sand and gravel). The amounts of the raw materials per unit volume of concrete vary between the three different concrete types. A certain amount of the primary material in recycling concrete (RC) and carbonated recycling concrete (C-RC) is substituted with recycled concrete aggregates (RCA). The RC and C-RC systems thus encompass concrete recycling. During this process, reinforcing steel is sorted out and recycled. For C-RC, the recycled concrete aggregates are carbonated with biogenic CO2. The CO2, which is used for carbonation, represents a waste flow of biogas upgrading, which is usually released to the atmosphere. Therefore, in line with the system model of our background database, its supply can be considered as “burden-free.” However, the C-RC system entails liquefaction, transport and evaporation of the CO2 and carbonation of RCA. It can be assumed that the processes after the production of concrete are the same for all three concrete types, since they exhibit equivalent properties. Therefore, the transport of the concrete from the concrete facility to the construction site as well as the construction of new infrastructure and the use-phase were excluded from the system boundaries. Also the demolition of old infrastructure was assumed to be the same for all three concrete types. Furthermore, it was assumed that the distance from the demolition site to the concrete recycling facility is the same as to the landfill site. The transport of demolition concrete was thus excluded from the system boundary.
In general, the electricity demand and material input of the technology and the devices along the CO2 supply chain are based on the fact sheets of the manufacturers. Transportation distances were estimated by analyzing different concrete facilities in Switzerland. The inventory data was first calculated for the functional unit 1 kg of carbonated RCA, and then extrapolated to the functional unit 1 m3 of concrete and compared with the production of conventional recycling concrete and of virgin concrete. Figure 2 represents a flowchart with material and energy flows of the negative emission value chain. The single components of the chain are described in detail in the following sub-sections. A general modeling choice concerns the end-of-life of the infrastructure of the value chain. This infrastructure (see Table 1) is made of steel and it can be assumed that these components are recycled at the end of their lifetimes. According to the used system model of the ecoinvent database in the background (Wernet et al., 2016), recycled materials enter their markets carrying the environmental burdens of recycling activities per default and therefore, scrapping and recycling does not have to be specifically taken into account in our inventories.
Figure 2. Material energy and CO2 flows of the negative emission value chain for the production of 1 kg of carbonated RCA.
Table 1. Life cycle inventory data based on the Ecoinvent data for the main processing steps in respect to the functional unit 1 kg RCA is listed in the table blow.
The process of concrete recycling delivers more than one product or service (i.e., it is an example of joint production): 1) RCA is produced, 2) scrap iron is sorted out, and 3) the recycling of concrete provides a waste treatment service (Grieder et al., 2016) (Supplementary Table 2). In Switzerland, concrete recycling facilities are paid for receiving the demolition concrete. Consequently, the efforts for recycling the concrete are split between the three co-products using economic allocation. The allocation factors and the LCI data for the production of 1 kg of RCA are listed in Supplementary Tables 3, 4, respectively.
RCA is usually stock piled for intermediate storage and afterwards processed by the mineralization plant. Therefore, a wheel loader heaves the RCA from the stock pile into the mineralization container on the truck. The RCA is then transported to the carbonation plant. After the mineralization of CO2, the container with the carbonated aggregates is transported to the silo where the RCA is temporary stored, to be used afterwards as sand and gravel substitute in the concrete production. Then, the truck with the empty container drives back to the stock pile of RCA, to be filled again. Primary materials and non-carbonated RCA are also heaved with a wheel loader from the stock pile into a truck and then transported directly to the silo. If the mineralization process is well integrated into the existing value chain of the concrete facility, the additional transport distance of the carbonated RCA is negligible. It is thus assumed that the logistic efforts for all sorts of sand and aggregates are the same. Different concrete facilities were analyzed to estimate an average transport distance of 1 km for the logistic efforts on site. A diesel fueled EURO 6 lorry, with a gross vehicle weight above 32 metric tons, transports the aggregates. The carbonation container is filled with 20 t of RCA. Further, it has been assumed that the wheel loader, with an hourly diesel consumption of roughly 22 liters, needs 3 min to fill one container.5
The electricity consumption of the liquefaction plant needed to liquefy the CO2 prior to transport is 240 kWh per ton of liquefied CO2.6 It is made of 10 tons of stainless steel and contains 55 kg of the refrigerant R449A.7 A yearly leakage rate of 10% was assumed which is based on the average leakage rate of refrigerating and air conditioning units (Koronaki et al., 2012). It was further assumed that the amount of refrigerant that leaks to the environment is refilled. Over a lifetime of 20 years, 165 kg of refrigerant are required, the initial 55 kg plus 110 kg of leaked refrigerant.
The liquefaction plant serves more than one customer. Therefore, the CO2 output of 270 kg of CO2 per hour was used to calculate the total amount of CO2 that is liquefied over a plant lifetime of 20 years. It was assumed that the plant operates 24 h a day, 365 days a year; to take maintenance into account, the operational hours were reduced by 10%. The amount of stainless steel and refrigerant needed for the liquefaction plant was divided by the output of liquefied CO2 per lifetime (42,574 t) to obtain the specific amount of steel and refrigerant per kg of CO2. This value has then been multiplied by the demand of 7.53 g CO2 per kg RCA to get the amount of steel and refrigerant per kg of RCA. The inventory data of the liquefaction plant is listed in Table 1.
CO2 tanks, which weigh 8 tons each, are used for the storage and transport of the CO2. There is one CO2 tank that stays at the liquefaction plant to be filled with liquid CO2. The other CO2 tanks are located at the concrete facilities. As soon as the mineralization plant runs out of CO2, CO2 from a full tank, charged at the liquefaction plant, is supplied. The CO2 liquefaction operates at a higher CO2 production rate than the CO2 uptake rate at the mineralization plant. Consequently, the CO2 tank at the liquefaction plant supplies CO2 to different concrete facilities. It is assumed that four concrete facilities share one backup tank. Thus, 10 tons of steel or five fourth of a tank are allocated to one concrete facility. A concrete facility can mineralize on average 120 tons of RCA per day. For the assumed CO2 tank lifetime of 20 years, a total amount of 626,400 tons of RCA can be carbonated. Based on that, the amount of steel per kg of RCA was calculated.
An EURO-6 diesel truck transports the CO2 from the liquefaction plant to the mineralization plant. The transportation distance from wastewater treatment plants to concrete facilities located in different agglomerations were measured and an average transportation distance of 10 km was determined. Supplementary Table 5 lists the distances for various Swiss urban areas. The CO2 tank increases the “empty” weight of the truck.8 The vehicle has a driving mass of 36 tons, with a CO2 load of 20 tons. This corresponds to a load factor of 100% (as the vehicle only departs when full), which is adjusted to a 50% average to account for the return trip driven empty.
The inventory data of the CO2 storage and transport components of the chain is listed in Table 1.
For the mineralization, the liquid CO2 has to be evaporated with a reboiler that is made of 243 kg of chromium steel. It is assumed that an atmospheric reboiler can be used from March to October which has an energy consumption of 7.9 kWh per ton of CO2.9 From November to February an electric reboiler has to be used which has a power output of 20 kW and evaporates 180 kg of CO2 per hour. This leads to an electricity consumption of 111.1 kWh per ton of CO2. From mid-December to mid-January the concrete plant undergoes annual maintenance, and thus the reboiler does not operate. Therefore, the electric reboiler runs for 3 months. The evaporation of the CO2 has thus an average energy consumption of 36 kWh per ton of CO2. Table 1 summarizes the inventory data of the evaporation.
The mineralization plant comprises of two mineralization containers, a process center and some connecting pipes. Each mineralization container is made of 3.7 tons of low-alloyed steel. The process center of the mineralization consists of 6 tons of low-alloyed steel. Based on the power output of the different devices of the carbonation plant listed in Supplementary Table 6, a total power output of 2 kW was assumed for the mineralization. Further, it has been assumed that 120 tons of RCA are carbonated per day. Table 1 lists the life cycle inventory data of the mineralizarion plant.
Moreover, the amount of CO2 mineralized per unit of RCA as well as the CO2 storage efficiency are two main process performance indicators, which are required to conduct the LCA. For this purpose, the mineral carbonation plant was operated at industrial scale for several days to collect this data. The results of this campaign are reported in the following section.
The concrete recipe of the virgin concrete is based on an ecoinvent data set.10 Based on the recycling concrete recipe of four different concrete facilities (Supplementary Table 7), a RCA share of 44% was assumed which corresponds to 860 kg/m3. It was further assumed that the remaining 1,095 kg of aggregates are 64% gravel and 36% sand. The aim of a specific concrete mix design is to meet characteristics as specified by the standard. Thus, the objective is to adjust the cement content so that the physical requirements are met. The use of RCA in concrete can alter its properties compared to the use of primary aggregate, which can be traced back to the heterogeneous nature of the material both in terms of chemical composition and of particle size distribution, particle shape and higher water absorption. Consequently, the cement input has to be increased from 290 to 315 kg/m3 to achieve the same material properties (Marinković et al., 2010). As stated above, the mineralization alters the properties of RCA positively, because it densifies the material (Seidemann et al., 2015). Depending on the concrete mix design, this can result in improved physical properties of the corresponding concrete; as a result less cement is needed (Xuan et al., 2016). For the concrete facility Frischbeton Rubigen AG, this improvement could be demonstrated for the concrete type NPK A. The cement content could be reduced to the regulatory minimum using carbonated aggregates. But the extent of cement reduction is subject to significant variations, since concrete plants utilize different raw materials, different cements and different chemical admixtures. Therefore, two different recipes were considered for the carbonated recycling concrete. On the one hand, the worst case (WC) recipe represents the situation where the concrete facility uses carbonated RCA in their recycling concrete without optimizing the concrete mixture. The best case (BC) recipe on the other hand corresponds to a recipe with carbonated RCA and with an optimized concrete mixture that allows a reduction of the cement content to 290 kg/m3, which is the average amount that is used for virgin concrete. The concrete recipes of the three different concrete types (VC, RC, C-RC) are listed in Supplementary Table 8.
The impact assessment regarding impacts on climate change was performed using the indicator Global Warming Potential with a time horizon of 100 years, calculated according to the characterization factors provided by the IPCC 2013 (Stocker, 2014). Additional indicators from the environmental footprint method EF 3.0 (Fazio et al., 2018) were used to quantify environmental burdens beyond impacts on climate change.
In order to quantify the scale of negative emissions, which are enabled by the proposed value chain until 2050, one has to determine the sink capacity of demolition concrete over the upcoming decades and match them with the biogenic CO2 supply. For this reason, projections based on historic data of the corresponding industrial sectors are made.
Historical data about concrete demolition is sparse. However, the historic calcination related CO2 emissions of the Swiss cement sector are known (Boden et al., 2008). These CO2 emissions provide the theoretical maximal CO2 storage potential in the corresponding concrete—since every calcined CaCO3 molecule can bind one CO2 molecule. This theoretical storage potential applies, if the cement is fully hydrated, all cement mineral phases are in solid-liquid equilibrium with the aqueous pore solution and the carbonation time is sufficient for the CO2 to diffuse even to the cement minerals deep inside of the particles. Furthermore, to determine the annual CO2 storage potential in Swiss demolition concrete until 2050, an average service life of a concrete structure of 80 years is assumed. Switzerland has no significant cement trade surplus or deficit (CEMSUISSE, 2020), thus the reported emissions correspond to cement which was afterwards used in concrete within the Swiss national borders. Further, Portland Cement of type 1 with a clinker content of 95% was the main cement type used in the twentieth century (Worrell et al., 2001). To translate the emissions into a concrete output and into amounts of demolition concrete, the RCA composition of the Kästli RCA was assumed to be the same as the one of EMPA, as listed in Supplementary Table 1. Since the objective is to capture future trends, rather than to make very accurate projections, we assumed that the amounts of demolition concrete are constant until 2025, then they grow linearly (see Figure 9).
The three main CO2 sources for negative emission technologies in Switzerland are biogas upgrading, waste incineration and direct air capture (DAC).
Today, CO2 from biogas upgraders is the only biogenic CO2 available in Switzerland in purified form and larger quantities. Swiss biogas plants produced in 2019 roughly 1,000 GWh biogas, and about one third was upgraded to biomethane. Assuming that CO2 accounts for 40 mole % of the biogas, current Swiss biogas upgraders emit about 50,000 t of biogenic CO2 per year. Furthermore, the sector has seen an annual growth in capacity of about 10% in the past 3 years (Stamm, 2019). Moreover, it was estimated that the Swiss biogas upgrading sector can grow to a maximum size of 175,000 t of CO2 per year (Teske et al., 2019). For this reason, the projection considers an annual growth of the sector of 10,000 tons of CO2, starting at 50,000 t of CO2 in 2020, until the technical potential is reached. The annual biogenic CO2 emission of biogas upgraders between 2010 and 2018 were calculated according to the methodology presented at the beginning of this paragraph.
Swiss waste incineration generates about 4 Mt CO2 emissions with a fossil share of roughly 50% (Gross, 2018; Swiss Federal Council, 2021). To access the CO2, CO2 post - combustion capture facilities need to be installed. In such a case, the CO2 capture process would be within the system boundaries of the value chain and thus its environmental impacts would need to be considered; however, these can be expected to be smaller than for DAC, since the CO2 is available at high concentrations, and heat and electricity can be provided by the waste incineration itself (Müller et al., 2020b). The implementation of large scale CCS is currently hindered by the lack of CO2 storage sites. First geologic storage sites accessible to European industries will start their operation in the North Sea around 2025.11,12 First feasibility studies have been conducted, which have identified that a first CO2 capture plant may start its operation at a Swiss waste incinerator between 2025 and 2030.13 Each facility will generate on average 50,000 to 100,000 tons of biogenic CO2 per year—summing up to a total of 1.5 Mt for all Swiss waste incinerators in 2050.
Other than biogas upgraders and waste incinerators, the capacity of DAC is not limited by current point source emissions, which are projected to experience no significant growth in the future. The limitations in DAC are rather related to the access to carbon lean heat and electricity (Deutz and Bardow, 2021).
The results of the lab tests and of the industrial demonstration are presented in this section. They provide input data for the LCA and confirm the key assumptions which have been made.
The results of the lab-scale carbonation experiments are reported in Figure 3. Since particle size plays an important role in carbonation processes, the cumulative mass based particle size distribution of the 0–16 mm RCA after crushing is shown in Figure 3A. One can see, that 50 wt.% of the particles are in the 0–4 mm size fraction, whereas the remaining 50 wt. % are in the 4 to 16 mm size fraction. Figure 3B shows the CO2 uptake of the 0 to 16 mm size fraction (black bold line) in g CO2 per kg of RCA as a function of the carbonation time. At time zero, when the CO2 injection starts, the 0 to 16 mm RCA experiences a rapid increase in mass, reaching 11.5 g CO2 per kg RCA after 2 h and 15.7 g of CO2 per kg RCA after 8 h. As the carbonation progresses, the rate of CO2 mineralization decreases, exhibiting a CO2 uptake of 18.5 g of CO2 per kg RCA after 24 h and 20.8 g of CO2 per kg RCA after 72 h. To understand, why this is the case, one has to consider the underlying physical mechanisms of concrete carbonation. RCA embodies gravel and sand which is surrounded and bound together with cement paste. These cement phases, a porous structure partially saturated with water, consist to a large degree of portlandite, C-S-H, monosulfate type and ettringite type phases (Soler, 2007). As CO2 reaches the surface of the particle, it is absorbed by the pore water, which is in a liquid-solid equilibrium with the cement minerals. The absorbed CO2 speciates to bicarbonate and carbonate ions and triggers the precipitation of the poorly soluble salt CaCO3. As a result, calcium ions are removed from the solution - which triggers further dissolution of the cement minerals and release of more calcium. At some point, the cement minerals are depleted in calcium, and the dissolution process stops. In this initial phase, the mineralization reaction is rate limiting. As the mineralization progresses, the CO2 has to diffuse through a growing layer of already carbonated cement paste to find pore water rich in calcium ions. This effect slows down the rate of CO2 mineralization, as observed in the experimental campaign. Thus, the rate of mineralization is limited by the diffusion of CO2 through the carbonated layers of RCA (Thiery et al., 2013). Within the experimental time, the CO2 uptake curve does not flatten yet, thus indicating that CO2 mineralization continues and the cement minerals carbonation have not reached completion.
Figure 3. (A) The sieve curve is plotted over the particle size. (B) The CO2 uptake of different particle size fractions is plotted over the experimental time. (C) The CO2 uptake relative to the 72 h uptake is plotted over time. Furthermore, the relative contribution of the different size fraction to the total uptake is visualized. The orange dot indicates the current operating point in the industrial plant.
Moreover, the 0 to 16 mm size fraction was sieved in 8 sub fractions and the corresponding results are shown in Figure 3B as a function of carbonation time. All size fractions exhibit the same trend. Initially, they experience a fast CO2 uptake, which slows down with time. Figure 3B shows that the fine material exhibits a more rapid CO2 uptake and in addition can store more CO2 per unit mass of the corresponding particle size within the experimental time. There are two major reasons for this effect. First, smaller particles have a significantly larger surface area per unit mass. Similar to many other processes, the reaction rate is proportional to the surface area of the particles. In case of the larger particles, the CO2 first needs to diffuse through the pore network to carbonate cement phases which are far away from the surface. Second, throughout the crushing process, concrete preferentially breaks along the phase boundaries between the sand and aggregate and cement. Thus, the crushing process leads to a classification of the material - where the finer fractions tend to be rich in hydrated cement, whereas the larger fractions tend to be rich in aggregate (Etxeberria et al., 2007). So far, it has been shown that all particle size fractions mineralize CO2. In a further step, one has to understand which size fractions contribute most to the total CO2 uptake. Depending on the results, one can selectively utilize certain size fractions so as to save reactor volume - or decide to address the concrete aggregate as it leaves the crusher. To quantify the total CO2 uptake per fraction, one can multiply the specific CO2 uptake of the individual fraction reported in Figure 3B with the corresponding weight of the cumulative particle size distribution (Figure 3A). This results in Figure 3C. The black bold line corresponds to the total CO2 uptake of the 0–16 mm size fraction as a function of time relative to the 72 h CO2 uptake. One can see that 55% of the relative uptake are reached after 2 h. This value increases to 77%, respectively, 90% after 8 and 24 h. It is evident that increasing the processing time beyond 24 h does not increase the amount of CO2 stored significantly. Hence, one has to identify if the reactor volume or the amount of RCA is the limiting factor to come up with the best decision about the processing time. The thin lines correspond to the total CO2 uptake of each fraction. Summing up the contributions of the single size fractions gives the thick black line. Moreover, due to their large contribution in mass, the 4–16 mm particles contribute roughly 20% to the total CO2 uptake despite their relatively low specific CO2 uptake.
So far, it has been demonstrated that the investigated process at lab scale can fix CO2 in RCA of commercial nature in industrial applicable processing times. The technology was scaled by 4 orders of magnitude to validate the results at industrial scale. Key figures of the industrial operation are listed in Table 2. The phenomenology at industrial scale was identical to the one at lab scale. The orange dot in Figure 3B indicates the 2 h CO2 uptake of the industrial scale test. It is on average 8.2 g CO2 per kg RCA, which is below the value measured at lab scale. Since the processing time is the time between the start and stop of the injection, one reason for the lower uptake may be that at industrial scale, part of the RCA is submerged in CO2 for a much shorter time, thus reducing the effective carbonation time. Moreover, the material might slightly differ in chemical composition and humidity. Beyond that, the CO2 storage efficiency, i.e., the amount of CO2 stored over the amount of CO2 supplied to the reactor needs to be determined for the LCA. Throughout the industrial operation, on average 2.3% of the CO2 injected was lost, as it was mixed with air initially and thus discharged from the reactor with the exiting gas stream. Moreover, as the RCA is discharged, part of the void space in-between the particles (about 40% of the reactor volume) is filled with a CO2 rich gas. Single measurements have shown, that the CO2 concentration in the gas phase is about 35% at the time of discharge. Assuming ambient conditions (25°C and 0.95 bars for Switzerland), 236 g of CO2 per cubic meter of RCA equivalent to additional 2.7% of the total CO2 supplied to the reactor are lost throughout discharge. This CO2 leakage as such is CO2-neutral, because it comes from a biogenic source. However, it increases the climate impact of the CO2 supply chain. Overall, the CO2 storage efficiency sums up to 95%. The results of the single tests are listed in Supplementary Table 9.
Table 2. The results of the experimental campaign at industrial scale, conducted at ambient conditions are summarized in the table below.
Figure 4 shows the physical properties of hardened concrete batched at lab scale and in the industrial scale mixer. The detailed mix designs are reported in Supplementary Table 10. At lab scale, 40 L of concrete were batched per mix design; at industrial scale, 1000 L of concrete were batched per mix design. The black bar corresponds to the 28-day compressive strength read out at the left y-axis; the orange bar to the 28-day Young's modulus read out at the right y-axis. All mix designs exceed the regulatory required minimum compressive strength of 30 MPa. At lab scale, carbonation clearly increases the compressive strength of the corresponding mix design. This trend can be observed with mix designs using 280 and 315 kg cement per m3 of concrete. Moreover, the mix design incorporating carbonated RCA and using the lower amount of cement exhibits superior physical performance than the reference mix design with the higher cement content. The Young's modulus seems to be affected to a lower degree. The same trends, but less marked, could be confirmed at industrial scale. In this section, it has been shown for specific concrete mix designs, that carbonation can be used to store CO2 but also may reduce the cement consumption of the investigated mix design. In other words, carbonated RCA may replace primary aggregate in concrete mix designs without the need of increasing the cement content. As a result of these findings and in the scope of the LCA, the environmental performance of two mix designs with 290 kg and 315 kg cement per m3 concrete, incorporating carbonated RCA will be benchmarked with primary concrete batched with 290 kg cement per m3 concrete. It is worth noting that the results of the material test are specific to the concrete mix designs investigated and have to be validated for every change in e.g., raw material or grain size distribution.
Figure 4. The compressive strength of concrete of type A after 28 days (black bars, left y-axis) for the reference concrete mix designs incorporating regular RCA and the concrete mix designs incorporating carbonated RCA is plotted for tests conducted at lab and industrial scale. Moreover, the Young's modulus is represented by the orange framed bars (right y-axis). The error bars represent one standard deviation. The Young's modulus (orange bars) can be read out at the right y-axis.
The impacts on climate change in terms of life-cycle GHG emissions of the four sub-processes of the negative emission value chain, namely CO2 liquefaction, transport, evaporation and mineralization, are illustrated in Figures 5, 6. In Figure 5, GHG emissions are grouped in four categories for each sub-process, i.e., infrastructure, electricity demand, refrigerant needs, and transport. The left y-axis indicates the emissions of greenhouse gases per kilogram of RCA, the right y-axis the amount of GHG emissions per ton of CO2 stored. The left panel shows that the ranking of sub-processes in terms of climate impact is CO2 liquefaction first, then transport, mineralization and finally evaporation, with electricity demand being the dominant effect in the case of liquefaction and evaporation, and infrastructure (the steel used to build the relevant CO2 vessels) in the case of transport and mineralization. The right panel shows the results of the left panel in a cumulative way and the positive emissions associated with the four sub-processes in total compared to the corresponding amount of CO2 stored. This shows that the net effect, which is given by the difference between negative and positive emissions, is 936.2 kg CO2,eq. of net negative emissions generated for every ton of CO2,eq. mineralized and stored, or – in other terms – of 6.7 g CO2,eq. for every kg of RCA carbonated.
Figure 5. (Left) The GWP of the sub-processes of the negative emission value chain are visualized along four main process categories. (Right) The cumulative GHG emission of the value chain, including the negative emissions of the mineralization plant.
Figure 6. Sensitivity analysis of different parameters of the LCA regarding impacts on climate change for the RCA. The left axis shows the carbon removal efficiency, i.e., the net amount of CO2 removed from the atmosphere compared to the total amount of CO2 stored. And the right axis indicates the net negative emissions per kg of RCA. The black dot illustrates the reference values. The blue lines in (A–C) indicate the carbon removal efficiency and the CO2 removed per kg RCA as a function of the investigated parameter. In (D), the blue line indicates the carbon removal efficiency, while the red line indicates the amount of CO2 removed per kg RCA.
Figure 6 illustrates the sensitivity of the environmental impacts of the three most impactful categories of GHG emissions on key parameters, namely transport distance (Figure 6A), carbon intensity of electricity (Figure 6B), and lifetime of infrastructure (Figure 6C), thus reflecting the possibly different boundary conditions of each specific implementation of mineralization of CO2 in RCA. Each effect is expressed in terms both of carbon removal efficiency, i.e., the net amount of CO2 removed from the atmosphere compared to the total amount of CO2 stored (left axis) and of net negative emissions (g CO2-eq. per kg RCA carbonated, right axis). Along each curve, a black dot indicates the values representing the reference case considered in this work and used to determine the values plotted in Figure 5. The assumed reference values are listed in Table 3. In panel B, the carbon intensity of electricity of important European countries is also reported. Finally, panel D illustrates the effect of changing (increasing) the CO2 uptake of RCA on the process emissions (minor effect) and on the net negative emissions generated (obviously a major effect). As it can be readily observed, transport distance and infrastructure's lifetime play a minor role when varied within reasonable ranges (panels A and C), whereas the carbon intensity of electricity plays a major role, with a 20% reduction of net negative emissions when the carbon intensity of electricity reaches levels as high as 0.6 kg CO2-eq. per kWh (the reference value that we use is 0.1 kg CO2-eq. per kWh, which refers to today's Swiss consumption mix, including guaranties of origin).
Figure 7 illustrates the GWP of the four different concrete types—which fulfill the same service. The cement is responsible for over 90% of the GHG emission of the corresponding concrete mix design, followed by the primary aggregate and the concrete factory. CO2 mineralized recycling concrete stores around 6 kg of CO2-eq. per m3 of concrete. Thus, CO2 mineralized recycling concrete with an unimproved mix design representing the environmental worst case (C-RC(WC)) emits about 6 kg CO2-eq. less per m3 of concrete than conventional recycling concrete, since the emissions of the negative emission value chain are—in comparison—negligible. However, cement is the main contributor to overall GHG emissions of all concrete types and for the CO2 mineralized concrete with an unimproved mix design a cement demand of 315 kg/m3 was assumed to fulfill the strength requirements. Consequently, it has a higher CO2 footprint than virgin concrete, which requires only 290 kg of cement/m3. However, based on the tests illustrated in Figure 4, it can be assumed that the cement content of CO2 mineralized concrete can be reduced to 290 kg/m3 and that such an optimized concrete mix design (C-RC(BC)) still complies with the same standards. Such C-RC(BC) exhibits the lowest carbon footprint and causes emissions of around 9 kg CO2-eq./m3 of concrete less than virgin concrete and as much as 21 kg CO2-eq./m3 less than conventional recycling concrete. As shown in Figure 8, regarding other life cycle impact assessment indicators such as particulate matter, land and water use, resource use of minerals and metals and ozone depletion, virgin concrete performs worst most of the time and causes the highest burdens. This is due to the higher consumption of the primary aggregates sand and gravel, the extraction of which causes substantial environmental burdens—especially, land, water, and resource use are affected. Differences among the other three concrete mix designs regarding the results for these impact categories are minor.
Figure 7. GWP of 1 m3 of concrete. The dots indicate the absolute GWP of the concrete taking into account the amount of CO2 stored. C-RC(BC), carbonated recycling concrete (best-case); VC, virgin concrete; C-RC (WC), carbonated recycling concrete (worst-case); RC, conventional recycling concrete.
Figure 8. Environmental performance of the four concrete types in other impact categories than GWP per m3 of concrete using the EF 3.0 Method (adapted) V1.00.
The orange line in Figure 9, read out at the left axis, shows the projection of the amounts of Swiss demolition concrete until 2050. At the same time, this line represents the theoretical storage potential read out at the right y-axis. One can see that the amount of demolition concrete remains constant at 5 Mt of demolition concrete per year until 2025, while it will experience a rapid eight-fold growth between 2025 and 2050. The data was cross-validated. Several studies of the federal Swiss office of environment estimate the annual amounts of demolition concrete between 1998 and 2018 to lie in the range from 3 to 9 Mt concrete per year (Haag, 2008; Rubli, 2016; Schneider, 2016). Similar estimates can be found elsewhere (Hoffmann and Jacobs, 2007).
Figure 9. The projected theoretical amount of CO2 that can be permanently removed from the atmosphere is plotted over time (orange curve). Furthermore, evolution of the technological exploitable CO2 sink capacity in demolition concrete (black) and the amount of biogenic CO2 available from biogas (green) upgrading can be read out at the y-axis as a function of time (Boden et al., 2008).
The theoretical sink capacity corresponds to the calcination related emission of the cement, which is embodied in the demolished concrete. This maximum potential is today in the range of 300,000 tons of CO2-eq. per year. This value sees a rapid increase in the upcoming 30 years, reaching an annual theoretical sink capacity of approximately 2.4 Mt of CO2-eq. in 2050. This theoretical sink capacity is technology independent and tells, how much CO2 can be removed from a thermodynamic point of view, assuming that the corresponding technologies do not have any associated emissions.
The technological sink capacity tells, how much CO2 can be permanently removed from the atmosphere in case all demolition concrete is carbonated by the presented technology. In addition, it also considers the GHG emissions associated with the operation of the negative emission value chain—which reduce the potential by 6.4%. This translates into a CO2 removal capacity of about 35,000 t CO2-eq. in 2020, which is represented by the black line in Figure 9. Moreover, carbonation experiments revealed, that the specific CO2 uptake of RCA can potentially be doubled by increasing the processing time from 2 to 24 h (Figure 3), while the CO2 emissions of the value chain are reduced. Thus, this effect is taken into consideration from 2025 onwards, which results in the kink on the black curve of Figure 9.
So far, we have demonstrated the technological elements of the value chain at industrial scale. In addition, the LCA has shown, that negative emissions are generated by operating the value chain already today. In this section, we want to discuss potential short-term improvements of the value chain (perspective 2025) and the role of the system in the perspective of the Swiss climate targets (perspective 2050). Moreover, the regional implementation of the value chain (regional perspective) and the deployment of the technology beyond the Swiss national borders (global perspective) will be discussed.
The presented negative emission value chain was demonstrated for the first time at industrial scale in summer 2020. Thus, the operational environment, namely the upstream and downstream processes are not yet optimized for CO2 storage. In addition, the experience in incorporating carbonated RCA into fresh concrete is still limited. As the technology is increasingly deployed, ancillary processes as well as the technology itself will undergo a steep learning curve.
Advancement in upstream processes and the mineralization technology
In the foreseeable future, a higher level of system integration can be achieved. This is reflected by the fact that the technology may be integrated in existing silo infrastructure which will increase the residence time to 24 h and more. Doing so will double the technologically exploitable storage capacity in concrete aggregate to about 80,000 t of CO2-eq. per year in 2025.
Smaller particles—bigger CO2 uptake?
It seems evident (Figure 3) that finely ground RCA yields the highest CO2 uptake in the given processing time. This is mainly due to the fact that the diffusion distances decrease with decreasing particle size. In theory, the theoretical CO2 uptake potential of 50% of the calcination related emissions (Leemann and Hunkeler, 2016) can be reached within hours—which would result in an uptake of about 30 g CO2 per kg of RCA. However, one has to keep in mind that today, demolition concrete is crushed to serve as sand and aggregate substitute in concrete and other applications. If the material is ground to micrometer size, it cannot fulfill the same service any longer. While a reduction in maximum particle size in the sieve curve down to 4 mm still may be reasonable in order to reuse the RCA as sand, grinding it to powder transforms the RCA into a material which needs to be landfilled. Hence, when maximizing the CO2 uptake, both upstream and downstream implications such as additional processing of the material or the generation of waste have to be added to the system boundary to come up with a qualified decision.
Advancement in concrete mix designs
With evolution and dissemination of more know-how about carbonated RCA, the environmental and physical optimization of concrete mix designs may turn into state of the art by 2025. Ideally, carbonated RCA can replace primary aggregate without compromising the functional performance of the concrete mix design. This will enable a future where concrete mix designs made with carbonated RCA have similar clinker contents as concrete made from primary aggregate. In the case study of this paper, this advancement would avoid another 15 kg CO2-eq. emissions per cubic meter of concrete compared to conventional recycling concrete. As a result, the recycling concrete mix design would exhibit a better GHG emission balance than primary concrete.
The Swiss climate policy target is to reduce net GHG emissions within the Swiss national borders (including international aviation and shipping) from 52.1 Mt CO2-eq. in 2018 to net-zero in 2050. This target should be achieved by a combination of classical emission avoidance, CO2 capture and storage and negative emissions. The Swiss Federal Office of the Environment estimates that 6.8 Mt of negative CO2-eq. emissions will be required in 2050. About 2 Mt of these negative emissions should be generated within the Swiss national borders (Swiss Federal Council, 2021). In comparison to the target sink capacity, the 40 Mt of demolition concrete available in 2050 have a theoretical sink capacity of 2.4 Mt of CO2-eq. The part of the sink capacity, which can be technically exploited with the presented technology is about 0.56 Mt of CO2-eq. per year - and thus can provide about 30% of the required domestic sink capacity. Since current demolition concrete recovery rates are in the range of 85% (Gauch et al., 2016), this target seems to be reachable. To build a carbon sink of the required scale, the integration of the technology into concrete recycling processes needs to start today. Moreover, the CO2 supply chains need to be scaled correspondingly. In particular, the biogas upgrading will reach its limits in supplying sufficient amounts of biogenic CO2 between 2025 and 2030 as it is illustrated by the cross over of the green and the black line in Figure 9. For this reason, it is critical that waste incinerators are retrofitted with CO2 capture units in the upcoming 5–10 years. Moreover, it is key that biomass wastes or residues are utilized as the biogenic carbon source, since they can be considered as free of environmental burdens.
Every urban area in Switzerland usually has biogenic CO2 emitters, e.g., waste water treatment plants or waste incinerators, as well as concrete demolition and a number of concrete recycling facilities as integral part of their industry. Matching supply and demand on a regional level keeps transport distances short and generates regional economic growth, since a new sector is established. Typical biogas upgrading operations generate 1,000–10,000 tons of biogenic CO2, while concrete recycling plants can use and store 350–2,000 tons of CO2 per year. The small scale comes at the benefit of smaller capital costs per installation and the compatibility with existing infrastructure. Furthermore, we could show that the demand for biogenic CO2 matches well with the amounts which could be supplied by biogas upgraders until 2030 (Figure 9). From 2030 on, part of the waste incinerator's CO2 emissions can be fixed in demolition concrete. Moreover, point source CCS was developed for large scale centralized operations, in order to decarbonize cement manufacturing and waste incineration. To enable its operation, the whole value chain needs to be scaled up to the size of megatonnes per year. However, the key elements of the CCS value chain, namely the CO2 capture, liquefaction and transport are also an integral part of the presented negative emission value chain. These synergies will accelerate the large scale deployment of CCS.
In the scope of this work, the environmental performance of a negative emission value chain in the Swiss industrial environment was evaluated. However, similar industrial clusters can be found all around the world. Moreover, sink capacities of many countries, e.g., European countries, the US, Canada, Japan and South Korea, are expected to exhibit similar characteristics to those presented in this work for Switzerland. This is due to the expected large amounts of demolition waste due to aging built stock. It has been shown that the electricity mix is most sensitive in determining the environmental performance of the process. Even for carbon intensive electricity, such as in Germany, the presented value chain has a carbon removal efficiency exceeding 75%. Hence, the presented value chain enables them to activate concrete as one of their carbon sinks. In 2050, the globally available theoretical sink capacity in concrete will reach 500 Mt of CO2-eq. per year (Boden et al., 2008). This study tries to anticipate the key developments of the presented negative emission value chain within the upcoming 30 years. On the large scale, this is challenging, since the industrial environment is facing a rapid transformation, which will impact the operational environment of the value chain. This work is supposed to represent the basis for future evaluations at the overall system level, which will consider interdependencies on the market and within the construction sector. Moreover, as the market penetration increases, re-assessments of the negative emission technology are of critical importance in order to understand systemic changes and to consider further impacts of upscaling the technology.
In the scope of demonstrating a CO2 mineralization plant at industrial scale, a CO2 uptake of 7.2 g CO2 per kg RCA was measured. Concrete material tests confirmed, that carbonated RCA fulfills at least the same service as regular RCA. In addition, lab scale carbonation experiments with a grain size of 0–16 mm RCA revealed that 50% of the CO2 is stored in the 0 to 1 mm particles, which account only for 25% of the mass (Figure 3). Furthermore, this study also revealed that extending the processing time from the current 2 h to more than 24 h can roughly double the amount of CO2 stored.
In addition, the LCA has demonstrated that carbonating recycled concrete aggregates using biogenic CO2 represents an efficient permanent carbon sink to remove CO2 from the atmosphere. The carbon removal efficiency (de Jonge et al., 2019), i.e., the net amount of CO2 removed from the atmosphere compared to the total amount of CO2 stored, of the presented negative emission value chain is about 93.6% in Switzerland. Thus 6.7 g CO2-eq. out of the 7.2 g CO2 stored per kg RCA can be considered as net negative emissions. The remaining 0.5 g CO2 stored per kg RCA compensate for the emissions related to the process, i.e., materials and energy. The value chain is most sensitive toward the carbon intensity of the electricity mix used for liquefaction and evaporation of CO2 and other processes. However, even carbon intensive electricity mixes like in Germany allow to operate the value chain at a carbon removal efficiency exceeding 75%. Since carbonated RCA can provide the same service as regular RCA, an integration of CO2 mineralization in current concrete recycling processes is an effective climate change mitigation measure. The presented negative emission value chain does not cause major environmental burdens. Other environmental impact categories beside impacts on climate change such as particulate matter formation and land use are more sensitive to the use of primary and recycling materials as well as cement than to the negative emissions value chain. The demonstrated negative emission value chain could currently generate annually about 35,000 tons of negative CO2 emission in 5 Mt of demolition concrete within the Swiss national borders, the amounts being limited by the rate of concrete demolition. The technical potential for negative emissions will evolve due to advancements along the value chain to 80,000 t CO2-eq. removed per year in 2025. Until 2030, the required biogenic CO2 can be supplied from biogas upgraders. Afterwards, more and more CO2 needs to be sourced from waste incineration or DAC for full exploitation of the CO2 removal potential via carbonating RCA. Ultimately, the growing amounts of demolition concrete to be expected will allow to store about 560,000 t CO2-eq. in 35 Mt Swiss demolition concrete in 2050, accounting for about 30% of the targeted sink capacity within the Swiss national borders by the Swiss federal office of environment to achieve overall climate neutrality.
The original contributions presented in the study are included in the article/Supplementary Material, further inquiries can be directed to the corresponding author.
LB performed the LCA under the guidance of JT. LB wrote the chapters 3.1–3.4, 5.2, and 5.3. JT wrote parts of the introduction, chapter 2, 3.5, 4.1, 5, and 6. All co-authors were involved on many detailed discussions about the content of the manuscript, reviewing, and editing it.
This analysis was performed within the Swiss Competence Center of Energy Research-Energy and Industrial Processes (SCCER-EIP), from which it received main funding. In addition, this work has partially received financial support from the Kopernikus Project Ariadne (FKZ 03SFK5A), funded by the German Federal Ministry of Education and Research. The pilot demonstrations were financially supported by the Swiss Federal office of Environment (BAFU), the Klimastiftung Schweiz, Neustark AG, and Kästli Bau AG.
JT: Ph.D. student in the Separation Processes Laboratory at ETH Zurich and Co-founder, member of the board and shareholder of the ETH-Spinoff Neustark, which scaled and commercialized the presented value chain. MM: Professor of the Separation Processes Laboratory at ETH Zurich and member of the advisory board of the ETH-Spinoff Neustark.
The remaining authors declare that the research was conducted in the absence of any commercial or financial relationships that could be construed as a potential conflict of interest.
All claims expressed in this article are solely those of the authors and do not necessarily represent those of their affiliated organizations, or those of the publisher, the editors and the reviewers. Any product that may be evaluated in this article, or claim that may be made by its manufacturer, is not guaranteed or endorsed by the publisher.
We would like to acknowledge Marcel Eckstein and Luca Tschurtschenthaler for their efforts in designing, constructing and operating the plant. In addition, Martin Reichen (Kästli Bau AG) for supporting us with the concrete material tests; Daniel Kästli and Bernhard Hirschi to enable the demonstration of the technology on-site of the concrete recycling plant Kästli Bau AG. In addition, we want to thank Theodora Potsi for supporting us in the lab scale carbonation experiments and Daniel Trottmann for constructing and maintaining the lab-scale carbonation setup. Last, but not least, we want to thank Frank Winnefeld for providing 80 L of RCA for our lab-scale study. Moreover, we would like to thank Stephan Pfister for supporting us with his expertise in life cycle assessment.
The Supplementary Material for this article can be found online at: https://www.frontiersin.org/articles/10.3389/fclim.2021.729259/full#supplementary-material
1. ^https://fastcarb.fr/en/home/
2. ^Swiss FOEN environmental technology promotion project 2019 with the aim to demonstrate CO2 mineralization in RCA at scale.
4. ^Swiss FOEN environmental technology promotion project 2019 with the aim to demonstrate CO2 mineralization in RCA at scale.
5. ^The following ecoinvent data set is used as a proxy: “machine operation, diesel, >= 74.57 kW, steady-state” with a diesel consumption of approximately 20.5 l per hour.
6. ^Fact sheet CO2 recovery plant, Hypro Group, 2020.
7. ^The ecoinvent database does not have any data on that specific refrigerant. Thus, the background data of the refrigerant R134a with approximately the same GWP (Makhnatch et al., 2017) was used instead.
8. ^Inventories generated by “carculator_truck,” a LCA tool for heavy-duty vehicles, were used to model a diesel-powered truck (Sacchi et al., 2021).
9. ^Fact sheet Atmosphärischer CO2 Verdampfer, ASCO-Kohlensäure AG 2019.
10. ^Concrete, high exacting requirements CH| concrete production, for building construction, with cement CEM II/B.
11. ^https://northernlightsccs.com/
12. ^https://www.portofrotterdam.com/en/news-and-press-releases/ccs-project-porthos-a-step-closer
Allen, M. R., de Coninck, H., Dube, O. P., Hoegh-Guldberg, O., Jacob, D., Jiang, K., et al. (2018). “Technical Summary,” in Global Warming of 1.5°C. An IPCC Special Report on the Impacts of Global Warming of 1.5°C Above Pre-industrial Levels and Related Global Greenhouse Gas Emission Pathways, in the Context of Strengthening the Global Response to the Threat of Climate Change, Sustainable Development, and Efforts to Eradicate Poverty, eds V. Masson-Delmotte, P. Zhai, H.-O. Pörtner, D. Roberts, J. Skea, P. R. Shukla, A. Pirani, W. Moufouma-Okia, C. Péan, R. Pidcock, S. Connors, J. B. R. Matthews, Y. Chen, X. Zhou, M. I. Gomis, E. Lonnoy, T. Maycock, M. Tignor, and T. Waterfield.
Anderson, K., and Peters, G. (2016). The trouble with negative emissions. Science 354, 182–183. doi: 10.1126/science.aah4567
Angelidaki, I., Xie, L., Luo, G., Zhang, Y., Oechsner, H., Lemmer, A., et al. (2019). “Biogas upgrading: current and emerging technologies,” in Biofuels: Alternative Feedstocks and Conversion Processes for the Production of Liquid and Gaseous Biofuels, (Amsterdam: Elsevier), 817–843.
Arvanitoyannis, I. S. (2008). “Iso 14040: life cycle assessment (lca)-principles and guidelines,” in Waste Management for the Food Industries (Amsterdam), 97–132.
Bednar, J., Obersteiner, M., and Wagner, F. (2019). On the financial viability of negative emissions. Nat. Commun. 10, 1–4. doi: 10.1038/s41467-019-09782-x
Boden, T., Marland, G., and Andres, B. (2008). Switzerland Geogenic Co2 Emissions From Cement Production. Carbon dioxide Information Analysis Center (Oak Ridge National Laboratory).
Colangelo, F., Navarro, T. G., Farina, I., and Petrillo, A. (2020). Comparative lca of concrete with recycled aggregates: a circular economy mindset in europe. Int. J. Life Cycle Assess. 25, 1790–1804. doi: 10.1007/s11367-020-01798-6
Creutzig, F., Breyer, C., Hilaire, J., Minx, J., Peters, G. P., and Socolow, R. (2019). The mutual dependence of negative emission technologies and energy systems. Energy Environ. Sci. 12, 1805–1817. doi: 10.1039/C8EE03682A
de Jonge, M. M., Daemen, J., Loriaux, J. M., Steinmann, Z. J., and Huijbregts, M. A. (2019). Life cycle carbon efficiency of direct air capture systems with strong hydroxide sorbents. Int. J. Greenhouse Gas Control 80, 25–31. doi: 10.1016/j.ijggc.2018.11.011
Deutz, S., and Bardow, A. (2021). Life-cycle assessment of an industrial direct air capture process based on temperature-vacuum swing adsorption. Nat. Energy 6, 203–213. doi: 10.1038/s41560-020-00771-9
Etxeberria, M., Vázquez, E., Marí, A., and Barra, M. (2007). Influence of amount of recycled coarse aggregates and production process on properties of recycled aggregate concrete. Cement Concrete Res. 37, 735–742. doi: 10.1016/j.cemconres.2007.02.002
Fajardy, M., and Mac Dowell, N. (2017). Can beccs deliver sustainable and resource efficient negative emissions? Energy Environ. Sci. 10, 1389–1426. doi: 10.1039/C7EE00465F
Farina, I., Colangelo, F., Petrillo, A., Ferraro, A., Moccia, I., and Cioffi, R. (2020). “Lca of concrete with construction and demolition waste,” in Advances in Construction and Demolition Waste Recycling (Amsterdam: Elsevier), 501–513.
Fazio, S., Castellani, V., Sala, S., Schau, E., Secchi, M., Zampori, L., et al. (2018). Supporting Information to the Characterisation Factors of Recommended ef Life Cycle Impact Assessment Methods. New Models and Differences with ILCD, EUR 28888.
Fuhrman, J., McJeon, H., Doney, S. C., Shobe, W., and Clarens, A. F. (2019). From zero to hero?: Why integrated assessment modeling of negative emissions technologies is hard and how we can do better. Front. Clim. 1:11. doi: 10.3389/fclim.2019.00011
Fuss, S., Lamb, W. F., Callaghan, M. W., Hilaire, J., Creutzig, F., Amann, T., et al. (2018). Negative emissions part 2: costs, potentials and side effects. Environ. Res. Lett. 13, 063002. doi: 10.1088/1748-9326/aabf9f
Gasser, T., Guivarch, C., Tachiiri, K., Jones, C., and Ciais, P. (2015). Negative emissions physically needed to keep global warming below 2 c. Nat. Commun. 6, 1–7. doi: 10.1038/ncomms8958
Gauch, M., Matasci, C., Hincapié, I., Hörler, R., and Böni, H. (2016). Material-und Energieressourcen Sowie Umweltauswirkungen der Baulichen Infrastruktur der Schweiz; empa Materials Science &Technology. St. Gallen.
Geden, O., Peters, G. P., and Scott, V. (2019). Targeting carbon dioxide removal in the european union. Clim. Policy 19, 487–494. doi: 10.1080/14693062.2018.1536600
Geden, O., and Schenuit, F. (2019). Climate Neutrality as Long-Term Strategy: The EU's Net Zero Target and Its Consequences for Member States. Tech. rep., DEU.
Goglio, P., Williams, A. G., Balta-Ozkan, N., Harris, N. R., Williamson, P., Huisingh, D., et al. (2020). Advances and challenges of life cycle assessment (lca) of greenhouse gas removal technologies to fight climate changes. J. Clean Prod. 244:118896. doi: 10.1016/j.jclepro.2019.118896
Grieder, A., Hubler, P., and Poell, M. (2016). Oekobilanz ausgewählter Betonsorten: Schlussbericht-Version 4.1. Tech. rep., Stadt Zürich.
Gross, C. (2018). Faktenblatt CO2 - Emissionsfaktoren für die Berichterstattung der Kantone. Tech. rep., Bundesamt für Umwelt BAFU.
Grubler, A., Wilson, C., Bento, N., Boza-Kiss, B., Krey, V., McCollum, D. L., et al. (2018). A low energy demand scenario for meeting the 1.5 c target and sustainable development goals without negative emission technologies. Nat. Energy 3, 515–527. doi: 10.1038/s41560-018-0172-6
Guinée, J. B., and Lindeijer, E. (2002). Handbook on Life Cycle Assessment: Operational Guide to the ISO Standards, Vol. 7. Luxenburg: Springer Science &Business Media.
Gursel, A. P., Masanet, E., Horvath, A., and Stadel, A. (2014). Life-cycle inventory analysis of concrete production: a critical review. Cement Concrete Composites 51, 38–48. doi: 10.1016/j.cemconcomp.2014.03.005
Haag, M. (2008). Bauabfälle Hochbau in der Schweiz Ergebnisse der Studie 2008. Bern: Bundesamt for Umwelt (BAFU).
Habert, G., Miller, S., John, V., Provis, J., Favier, A., Horvath, A., et al. (2020). Environmental impacts and decarbonization strategies in the cement and concrete industries. Nat. Rev. Earth Environ. 1, 559–573. doi: 10.1038/s43017-020-0093-3
Hafez, H., Kurda, R., Cheung, W. M., and Nagaratnam, B. (2019). A systematic review of the discrepancies in life cycle assessments of green concrete. Appl. Sci. 9, 4803. doi: 10.3390/app9224803
Hoffmann, C., and Jacobs, F. (2007). Recyclingbeton aus Beton-und Mischabbruchgranulat Sachstandsbericht. Zurich: EMPA.
International Organization for Standardization (2006a). Environmental Management - Life Cycle Assessment - Principles and Framework: ISO 14040. Tech. rep.
International Organization for Standardization (2006b). Environmental Management - Life Cycle Assessment - Requirement and Guidelines: ISO 14044. Tech. rep.
Jacobs, F. (2011). Proof of Concrete Quality by' Limiting Values' and/or Tests? Tech. rep., TFB Wildegg.
Knoeri, C., Sanyé-Mengual, E., and Althaus, H.-J. (2013). Comparative lca of recycled and conventional concrete for structural applications. Int. J. Life Cycle Assess. 18, 909–918. doi: 10.1007/s11367-012-0544-2
Kober, T., Bauer, C., Bach, C., Beuse, M., Georges, G., Held, M., et al. (2019). Perspectives of power-to-x technologies in switzerland: A white paper. Technical report, ETH Zurich.
Koronaki, I., Cowan, D., Maidment, G., Beerman, K., Schreurs, M., Kaar, K., et al. (2012). Refrigerant emissions and leakage prevention across europe-results from the realskillseurope project. Energy 45, 71–80. doi: 10.1016/j.energy.2012.05.040
Lagerblad, B. (2005). Carbon Dioxide Uptake During Concrete Life Cycle: State of the art. Stockholm: Swedish Cement and Concrete Research Institute Stockholm.
Leemann, A., and Moro, F. (2017). Carbonation of concrete: the role of CO2 concentration, relative humidity and CO2 buffer capacity. Mater. Struct. 50, 1–14. doi: 10.1617/s11527-016-0917-2
Levasseur, A., Lesage, P., Margni, M., Deschenes, L., and Samson, R. (2010). Considering time in lca: dynamic lca and its application to global warming impact assessments. Environ. Sci. Technol. 44, 3169–3174. doi: 10.1021/es9030003
Lueddeckens, S., Saling, P., and Guenther, E. (2020). Temporal issues in life cycle assessment'a systematic review. Int. J. Life Cycle Assess. 25, 1385–1401. doi: 10.1007/s11367-020-01757-1
Makhnatch, P., Mota-Babiloni, A., Rogstam, J., and Khodabandeh, R. (2017). Retrofit of lower gwp alternative r449a into an existing r404a indirect supermarket refrigeration system. Int. J. Refriger. 76, 184–192. doi: 10.1016/j.ijrefrig.2017.02.009
Marinković, S., Radonjanin, V., Malešev, M., and Ignjatović, I. (2010). Comparative environmental assessment of natural and recycled aggregate concrete. Waste Manag. 30, 2255–2264. doi: 10.1016/j.wasman.2010.04.012
Meyer, V., de Cristofaro, N., Bryant, J., and Sahu, S. (2018). “Solidia cement an example of carbon capture and utilization,” in Key Engineering Materials, Vol. 761 (St. Quentin Fallavier: Trans Tech Publ), 197–203.
Miller, S. A., and Moore, F. C. (2020). Climate and health damages from global concrete production. Nat. Clim. Change 10, 439–443. doi: 10.1038/s41558-020-0733-0
Minx, J. C., Lamb, W. F., Callaghan, M. W., Fuss, S., Hilaire, J., Creutzig, F., et al. (2018). Negative emissions part 1: research landscape and synthesis. Environ. Res. Lett. 13, 063001. doi: 10.1088/1748-9326/aabf9b
Monkman, S., MacDonald, M., Hooton, R. D., and Sandberg, P. (2016). Properties and durability of concrete produced using co2 as an accelerating admixture. Cement Concrete Composites 74:218–224. doi: 10.1016/j.cemconcomp.2016.10.007
Müller, L. J., Kätelhön, A., Bachmann, M., Zimmermann, A., Sternberg, A., and Bardow, A. (2020a). A guideline for life cycle assessment of carbon capture and utilization. Front. Energy Res. 8:15. doi: 10.3389/fenrg.2020.00015
Müller, L. J., Kätelhön, A., Bringezu, S., McCoy, S., Suh, S., Edwards, R., et al. (2020b). The carbon footprint of the carbon feedstock CO2. Energy Environ. Sci. 13, 2979–2992. doi: 10.1039/D0EE01530J
Nemet, G. F., Callaghan, M. W., Creutzig, F., Fuss, S., Hartmann, J., Hilaire, J., et al. (2018). Negative emissions part 3: innovation and upscaling. Environ. Res. Lett. 13, 063003. doi: 10.1088/1748-9326/aabff4
Obrist, M. D., Kannan, R., Schmidt, T. J., and Kober, T. (2021). Decarbonization pathways of the swiss cement industry towards net zero emissions. J. Clean Prod. 288:125413. doi: 10.1016/j.jclepro.2020.125413
Papadakis, V. G., Vayenas, C. G., and Fardis, M. (1989). A reaction engineering approach to the problem of concrete carbonation. AICHE J. 35, 1639–1650. doi: 10.1002/aic.690351008
Papadakis, V. G., Vayenas, C. G., and Fardis, M. N. (1991). Fundamental modeling and experimental investigation of concrete carbonation. Mater. J. 88, 363–373.
Rogelj, J., Luderer, G., Pietzcker, R. C., Kriegler, E., Schaeffer, M., Krey, V., et al. (2015). Energy system transformations for limiting end-of-century warming to below 1.5 c. Nat. Clim. Chang 5, 519–527. doi: 10.1038/nclimate2572
Rosa, L., Reimer, J. A., Went, M. S., and DOdorico, P. (2020a). Hydrological limits to carbon capture and storage. Nat. Sustainabil. 3, 658–666. doi: 10.1038/s41893-020-0532-7
Rosa, L., Sanchez, D. L., Realmonte, G., Baldocchi, D., and D'Odorico, P. (2020b). The water footprint of carbon capture and storage technologies. Renewable Sustainable Energy Rev. 138:110511. doi: 10.1016/j.rser.2020.110511
Rubli, S. (2016). Bauabfälle in der Schweiz - Tiefbau Aktualisierung 2015. Bern: Bundesamt for Umwelt (BAFU).
Runge-Metzger, A. (2018). A Clean Planet for All, a European Strategic Long-Term Vision for a Prosperous, Modern, Competitive and Climate Neutral Economy. European Commission, 1–18.
Sacchi, R., Bauer, C., and Cox, B. L. (2021). Does size matter? the influence of size, load factor, range autonomy, and application type on the life cycle assessment of current and future medium-and heavy-duty vehicles. Environ. Sci. Technol. 5, 5224–5235. doi: 10.1021/acs.est.0c07773
Seidemann, M., Müller, A., and Ludwig, H.-M. (2015). Weiterentwicklung der Karbonatisierung von rezyklierten Zuschlägen aus Altbeton: Abschlussbericht. Tech. rep., Bauhaus-Universität Weimar.
Siwior, P., and Bukowska, J. (2018). Commentary on european court of justice judgement of 19 january 2017 in case c-460/15 schaefer kalk gmbh &co. kg v bundesrepublik deutschland. Environ. Protect. Natural Resour. 29, 25–30. doi: 10.2478/oszn-2018-0011
Soler, J. M. (2007). Thermodynamic Description of the Solubility of CSH Gels in Hydrated Portland Cement. Tech. rep., Posiva Oy, Finland.
Stamm, N. (2019). Schweizerische Statistik der Erneuerbaren Energien. Available online at: https://www.bfe.admin.ch/bfe/de/home/versorgung/erneuerbare-energien/energie-aus-biomasse.html
Stocker, T. (2014). “Climate change 2013: the physical science basis,” in Working Group I Contribution to the Fifth Assessment Report of the Intergovernmental Panel on Climate Change (Cambridge: Cambridge University Press).
Swiss Federal Council (2021). Switzerland's Long-Term Climate Strategy. Available online at: https://www.bafu.admin.ch/bafu/en/home/documentation/news-releases/anzeige-nsb-unter-medienmitteilungen.msg-id-82140.html.
Tanzer, S. E., and Ramírez, A. (2019). When are negative emissions negative emissions?. Energy Environ. Sci. 12, 1210–1218. doi: 10.1039/C8EE03338B
Teir, S., Eloneva, S., Fogelholm, C.-J., and Zevenhoven, R. (2006). Stability of calcium carbonate and magnesium carbonate in rainwater and nitric acid solutions. Energy Convers Manag. 47, 3059–3068. doi: 10.1016/j.enconman.2006.03.021
Terlouw, T., Bauer, C., Rosa, L., and Mazzotti, M. (2021). Life cycle assessment of carbon dioxide removal technologies: a critical review. Energy Environ. Sci. 14, 1701–1721. doi: 10.1039/D0EE03757E
Teske, S., Rüdisüli, M., Bach, C., and Schildhauer, T. (2019). Potentialanalyse Power-to-gas in der Schweiz (version 1.0. 0). Dübendorf: EMPA.
Thiery, M., Dangla, P., Belin, P., Habert, G., and Roussel, N. (2013). Carbonation kinetics of a bed of recycled concrete aggregates: a laboratory study on model materials. Cement Concrete Res. 46:50–65. doi: 10.1016/j.cemconres.2013.01.005
Tollefson, J. (2018). Ipcc says limiting global warming to 1.5 c will require drastic action. Nature 562, 172–173. doi: 10.1038/d41586-018-06876-2
Van Vuuren, D. P., Deetman, S., van Vliet, J., van den Berg, M., van Ruijven, B. J., and Koelbl, B. (2013). The role of negative co 2 emissions for reaching 2 c insights from integrated assessment modelling. Clim. Change 118, 15–27. doi: 10.1007/s10584-012-0680-5
Van Vuuren, D. P., Hof, A. F., Van Sluisveld, M. A., and Riahi, K. (2017). Open discussion of negative emissions is urgently needed. Nat. Energy 2, 902–904. doi: 10.1038/s41560-017-0055-2
Van Vuuren, D. P., Stehfest, E., Gernaat, D. E., Van Den Berg, M., Bijl, D. L., De Boer, H. S., et al. (2018). Alternative pathways to the 1.5 c target reduce the need for negative emission technologies. Nat. Clim. Chang 8, 391–397. doi: 10.1038/s41558-018-0119-8
Vieira, D. R., Calmon, J. L., and Coelho, F. Z. (2016). Life cycle assessment (lca) applied to the manufacturing of common and ecological concrete: a review. Construct. Build. Mater. 124, 656–666. doi: 10.1016/j.conbuildmat.2016.07.125
Villain, G., Thiery, M., and Platret, G. (2007). Measurement methods of carbonation profiles in concrete: Thermogravimetry, chemical analysis and gammadensimetry. Cement Concrete Res. 37, 1182–1192. doi: 10.1016/j.cemconres.2007.04.015
Waisman, H., de Coninck, H., and Rogelj, J. (2019). Key technological enablers for ambitious climate goalsinsights from the ipcc special report on global warming of 1.5°c. Environ. Res. Lett. 14:111001 doi: 10.1088/1748-9326/ab4c0b
Wernet, G., Bauer, C., Steubing, B., Reinhard, J., Moreno-Ruiz, E., and Weidema, B. (2016). The ecoinvent database version 3 (part i): overview and methodology. Int. J. Life Cycle Assess. 21, 1218–1230. doi: 10.1007/s11367-016-1087-8
Wiloso, E., Heijungs, R., Huppes, G., and Fang, K. (2016). Effect of biogenic carbon inventory on the life cycle assessment of bioenergy: challenges to the neutrality assumption. J. Clean Prod. 125, 78–85. doi: 10.1016/j.jclepro.2016.03.096
Worrell, E., Price, L., Martin, N., Hendriks, C., and Meida, L. O. (2001). Carbon dioxide emissions from the global cement industry. Ann. Rev. Energy Environ. 26, 303–329. doi: 10.1146/annurev.energy.26.1.303
Xi, F., Davis, S. J., Ciais, P., Crawford-Brown, D., Guan, D., Pade, C., et al. (2016). Substantial global carbon uptake by cement carbonation. Nat. Geosci. 9, 880–883. doi: 10.1038/ngeo2840
Xuan, D., Zhan, B., and Poon, C. S. (2016). Assessment of mechanical properties of concrete incorporating carbonated recycled concrete aggregates. Cement Concrete Composites 65, 67–74. doi: 10.1016/j.cemconcomp.2015.10.018
Zhang, X., Witte, J., Schildhauer, T., and Bauer, C. (2020). Life cycle assessment of power-to-gas with biogas as the carbon source. Sustain. Energy Fuels 4, 1427–1436. doi: 10.1039/C9SE00986H
Keywords: negative emission technologies (NET), concrete, CO2 mineralization, concrete carbonation, carbon sink, life cycle assessment (LCA), construction
Citation: Tiefenthaler J, Braune L, Bauer C, Sacchi R and Mazzotti M (2021) Technological Demonstration and Life Cycle Assessment of a Negative Emission Value Chain in the Swiss Concrete Sector. Front. Clim. 3:729259. doi: 10.3389/fclim.2021.729259
Received: 22 June 2021; Accepted: 14 September 2021;
Published: 13 October 2021.
Edited by:
Shareq Mohd Nazir, KTH Royal Institute of Technology, SwedenReviewed by:
Jacopo Giuntoli, Independent Researcher, Montecatini Terme, ItalyCopyright © 2021 Tiefenthaler, Braune, Bauer, Sacchi and Mazzotti. This is an open-access article distributed under the terms of the Creative Commons Attribution License (CC BY). The use, distribution or reproduction in other forums is permitted, provided the original author(s) and the copyright owner(s) are credited and that the original publication in this journal is cited, in accordance with accepted academic practice. No use, distribution or reproduction is permitted which does not comply with these terms.
*Correspondence: Marco Mazzotti, bWFyY28ubWF6em90dGlAaXBlLm1hdnQuZXRoei5jaA==
Disclaimer: All claims expressed in this article are solely those of the authors and do not necessarily represent those of their affiliated organizations, or those of the publisher, the editors and the reviewers. Any product that may be evaluated in this article or claim that may be made by its manufacturer is not guaranteed or endorsed by the publisher.
Research integrity at Frontiers
Learn more about the work of our research integrity team to safeguard the quality of each article we publish.