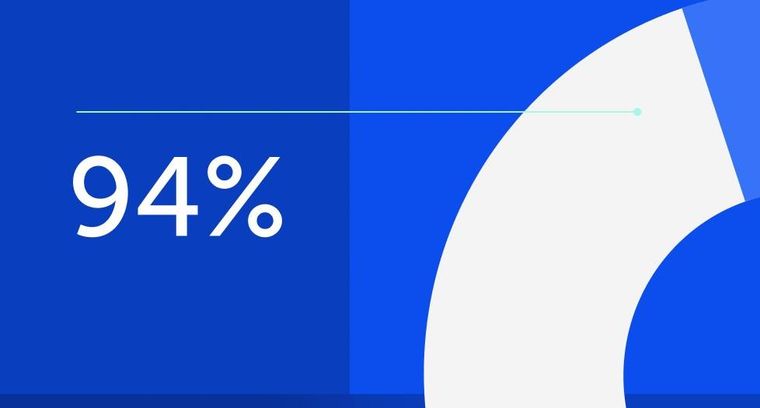
94% of researchers rate our articles as excellent or good
Learn more about the work of our research integrity team to safeguard the quality of each article we publish.
Find out more
ORIGINAL RESEARCH article
Front. Chem., 31 March 2025
Sec. Polymer Chemistry
Volume 13 - 2025 | https://doi.org/10.3389/fchem.2025.1552814
This article is part of the Research TopicInnovative Flame Retardant Materials: Balancing Efficiency, Safety, and SustainabilityView all articles
Polylactic acid (PLA) and acrylonitrile-butadiene-styrene (ABS) are the most commonly used filaments in 3D printing. To enable filament materials to withstand higher stresses, PLA and ABS are often blended (PLA/ABS). In this work, the co-pyrolysis and combustion properties of PLA/ABS blends of various ratios (75%/25%, 50%/50%, and 25%/75%) were analyzed. Thermogravimetric analysis showed that the catalytic pyrolysis of the blends became more intense as the proportion of PLA in PLA/ABS increased. Cone calorimetry tests indicated that the pyrolysis of ABS determines the peak heat release rate of the PLA/ABS blend. The higher amount of PLA allows the blend to pyrolyze at lower temperatures and the combustion reaction becomes more violent. The theoretical heat of combustion was calculated by correlating the average and maximum HRR with the heat flux through theoretical analysis. The theoretical heat of combustion obtained from the maximum HRR data is more reliable than from the average HRR data. This study has implications for the efficient utilization and fire protection of materials based on PLA/ABS.
To develop a polymer with superior properties for the dynamic market, polymer blending is recognized as a cost-effective and flexible method (Vadori et al., 2017). This approach leverages the complementary properties of various polymers, thereby enhancing the overall performance of blends (Haaparanta et al., 2013). It particularly improves their thermal resistance, flame retardancy, and electrical insulation (Hong et al., 2024). Despite these performance enhancements, research on the thermal stability and combustion properties of polymer blends remains limited, indicating a need for further investigation to fully understand and optimize these polymer blends.
Amidst the dwindling petrochemical resources and escalating environmental pollution (Rochman et al., 2013), biodegradable materials have garnered significant attention in recent years. Polylactic acid (PLA) is a biodegradable and renewable thermoplastic polymer (Scaffaro et al., 2018). PLA exhibits inherent high brittleness, low ultimate elongation, and slow crystallization kinetics, which constrain its widespread application (Al-Itry et al., 2012). The blending of PLA with flexible polymers represents an effective strategy to ameliorate these limitations. Some studies have focused on blends such as PLA/polycarbonate (Lin et al., 2015), PLA/Poly (butylene succinate) (Zhao et al., 2021), and PLA/poly (butylene adipate-co-terephthalate) (Signori et al., 2009). In these studies, both the thermal degradation properties and mechanical properties of these blends were found to be improved compared to the PLA. High-elasticity polymers, such as ABS (Acrylonitrile-Butadiene-Styrene), can substantially improve the fracture toughness of PLA (Dhinesh et al., 2019). When considering tensile strength alone, PLA/ABS (mass ratio of 80%/20%) exhibits superior performance. The incorporation of 20% ABS enhances the blend’s ductility, surpassing the properties of PLA. Flexural test results indicate that an ABS-PLA material with a 50%/50% composition, arranged in alternating layers, demonstrates improved strength compared to single-layer configurations. Research on PLA/ABS primarily concentrates on mechanical properties, while the pyrolytic and combustion behaviors have been less investigated. The low limiting oxygen index (LOI) values for both PLA and ABS polymers suggest a high fire hazard (Jia et al., 2020; Liu et al., 2011), indicating that PLA/ABS blends are highly susceptible to ignition and pose a significant fire safety concern under specific environmental conditions. Therefore, the study of the pyrolytic and combustion behaviors of PLA/ABS could offer valuable data support and guidance for fire safety strategies related to the blend. In a previous study (Wu et al., 2022), the co-pyrolysis kinetics and combustion behavior of PLA/ABS (mass ratio of 50%/50%) were initially investigated. The results showed that PLA promoted the depolymerizations of ABS, thereby enhancing the flammability of the blend. Thus, the study on the pyrolytic and combustion behaviors of PLA/ABS with different ratios is of prospective interest.
This study presents an investigation into the thermal decomposition behavior of PLA/ABS blends with varying ratios at different heating rates, utilizing thermogravimetric analysis. (TGA) The study aims to explore the influence of the PLA to ABS ratio on the pyrolysis characteristics of the blend. Furthermore, the combustion characteristics of PLA/ABS blends with different ratios are analyzed under various radiation heat fluxes (20, 30, and 40 kW/m2) employing a cone calorimeter. Thermal decomposition characteristics of PLA/ABS blends were determined using a cone calorimeter, yielding key parameters including ignition time (TTI), mass loss rate (MLR), heat release rate (HRR), and effective heat of combustion (EHC). Correlation analyses were conducted between heat flux density and these characteristic parameters.
PLA (4032D) and ABS (8391) were manufactured by Nature Works Co., Ltd., United States and Shanghai Gaoqiao Petrochemical Co., Ltd. The PLA/ABS sample preparation formulations are shown in Table 1. The molten mixture of PLA and ABS was blended using a QE-70A type compacting machine from Wuhan Qien Technology Development Co., Ltd. The mixing process was carried out for 4 min at 200°C and 60 rpm. The molten mixture was taken out and then hot-pressed into a standard sample of 100 mm × 100 mm × 3 mm (thickness) at 10 MPa and 180°C for 4 min using a Yangzhou Yuanfeng Experimental Machinery Factory YF-8017 plate vulcanizing machine. For comparison, pure PLA and ABS samples were prepared in the same way.
The thermal decomposition behaviors of the five samples at different heating rates were investigated using the STA6000 simultaneous thermal analyzer from PerkinElmer, United States. The PLA and ABS samples were ground into powder and then weighed approximately 10 mg of powder, placed in an Al2O3 crucible for the TGA experiment. The experiments were carried out in a high-purity nitrogen atmosphere. The TGA curves were obtained for each sample at heating rates of 5, 10, and 15°C/min, from room temperature to 600°C. The TG experiments were reproducible with an uncertainty of less than 5% (Li et al., 2013).
The combustion behaviors of the five samples were recorded using a cone calorimeter from Motis Fire Technology Co., Ltd. Prior to the cone calorimetry tests, all samples were conditioned in a controlled environment at room temperature (25°C) and a relative humidity of 50% for at least 48 h to ensure consistent initial moisture content. This conditioning process helps to minimize variability in the test results due to differences in sample moisture levels. The 100 mm × 100 mm × 3 mm sample was wrapped in aluminum foil and placed in a holder with insulating wool on the back according to the ISO 5660-1 test standard. The sample was then placed horizontally at a distance of 25 mm from the cone heater. The radiation heat fluxes were 20, 30, and 40 kW/m2, respectively. A radiation heat flux of 30 kW/m2 represents the growth phase of a real fire, while a heat flux of 20–40 kW/m2 is typical in a building fire (Chen et al., 2015b). The critical heat flux, ignition temperature, heat of vaporization, and heat of combustion significantly influence the fire hazard and thermal decomposition processes (Chen et al., 2015a). The cone calorimeter was calibrated before each experiment which was repeated three times to ensure reproducibility (Schartel et al., 2005).
Figure 1 shows the TG and derivative thermogravimetry (DTG) plots for the five samples. From Figure 1, there is only one mass loss stage during the pyrolysis of pure PLA and ABS, which is consistent with the literature (Mandal et al., 2018; Balart et al., 2019). Three PLA/ABS blends exhibit two main stages of mass loss, and the DTG curve has two peaks corresponding to the pyrolysis stages of PLA and ABS. However, ABS makes up a relatively small proportion of P3A1 and its main degradation process is overlap with PLA, resulting in an insignificant second peak. As these two phases of PLA/ABS are derived from PLA and ABS, the TGA data of pure PLA and ABS are compared to the PLA/ABS and are listed in Table 2. In Table 2, the initial temperature of pyrolysis with a total mass loss of 1 wt%, the temperature at maximum MLR in the first and second stages and the completion temperature of pyrolysis when the MLR is close to 0 are defined as Ti, Tm1, Tm2 and Tf, respectively. The residues at 600°C are also listed in Table 2.
Figure 1. TG curves of (a) 5°C/min, (c) 10°C/min and (e) 15°C/min, and DTG curves of (b) 5°C/min, (d) 10°C/min and (f) 15°C/min for the five samples.
For heating rates of 5°C/min, the Ti, Tm1 and Tf for P1A0 were 310, 362°C and 378°C, respectively, with a residue of 0.66 wt% at 600°C, as shown in Figure 1 and Table 2. For P3A1, the Ti, Tm1 and Tf were 314, 355°C and 478°C, respectively, resulting in a residue of 2.52 wt% at 600°C. For P1A1, it has a Ti of 315°C, the first and second peaks of DTG appear at 352°C and 390°C respectively, and Tf at 479°C, with a residue of 2.53 wt% at 600C. For P1A3, which has a Ti of 316°C, the first and second peaks of DTG appear at 349°C and 396°C respectively, and Tf at 499°C, with a residue of 1.55 wt% at 600°C. P0A1 has Ti, Tm2 and Tf of 360, 409°C and 502°C respectively, with a residue of 1.03 wt% at 600°C.
From the data in Figure 1; Table 2, the Ti of PLA/ABS is similar to that of PLA. With the addition of ABS, the second maximum MLR and the Tm2 of the mixture tend to increase. This is primarily attributed to the higher thermal stability of ABS. The variation is more significant in that the residue at 600°C is higher for PLA/ABS samples than for PLA and ABS. With an increasing percentage of PLA content, the residue increased. The residue amounts of samples P3A1, P1A1 and P1A3 at 600°C were 1.49 wt%, 1.50 wt% and 0.52 wt% higher than those of ABS, respectively. This suggests that the presence of PLA in PLA/ABS may have catalyzed the reaction and promoted the formation of char.
If there is no interaction between the two plastics, the theoretical mass (WT) is obtained from the mass of pyrolysis alone and the mass ratio of the component in the blend (Kai et al., 2017). It is calculated as:
where W1 and W2 represent the mass loss of PLA and ABS respectively at a given time under the same pyrolysis conditions. X1 and X2 represent the corresponding mass ratios of PLA and ABS. The dashed line in Figure 2 shows the theoretical curve calculated using Equation 1. The difference between experimental and theoretical curves for different heating rates is shown in Figure 2D for the blends. The relevant TGA data for the experimental and theoretical curves are summarized in Table 3. The theoretical and experimental TGA curves do not exactly overlap, while the experimental mass decreases more rapidly. As can be seen from Figure 2; Table 3, the maximum differences in the TGA curves for P3A1, P1A1 and P1A3 were within 10.2%–22.3%, 10.1%–20.6% and 10.2%–19.8%, respectively, at different heating rates. This indicates a large difference between co-pyrolysis and the sum of individual pyrolysis steps.
Figure 2. A comparison of theoretical (T) and experimental (E) TG and DTG curves for PLA/ABS blends: (a) P3A1, (b) P1A1, (c) P1A3 and (d) Δmmax.
Comparing the peak temperatures in the DTG curves, it can be inferred that the thermal stability of the blends is reduced to some degrees compared to the raw samples. The higher the amount of ABS greater the difference between theoretical and experiment at mass loss curves, and the more obvious the mutual synergistic between PLA and ABS. Theoretically, the DTG of different proportions of PLA/ABS blends will have two peaks that vary proportionally, according to Equation 1. However, as can be seen in Figure 2, the amplitude and temperature of the experimental DTG peaks for ABS in the blends are lower than the theoretical values. The higher the PLA content, the less pronounced the DTG peak of ABS. This indicates that the thermal degradation reaction of ABS in the blend occurs at lower temperatures compared to pure ABS. This suggests that the presence of PLA promotes the pyrolysis of ABS, thereby advancing the onset of its thermal degradation. The difference in PLA and ABS content leads to a variation in the temperature range over which decomposition occurs. The interaction between PLA and ABS results in a synergistic effect on pyrolysis, which is more pronounced than the theoretical results. Specifically, the peak temperature corresponding to PLA pyrolysis decreases more significantly as the ABS content increases. This suggests that ABS not only lowers the maximum MLR temperature of PLA but also enhances the overall pyrolysis process, leading to a more vigorous reaction. These findings provide novel insights into the synergistic interactions between PLA and ABS, highlighting the importance of considering component interactions in polymer blends.
Pyrolysis of materials represents the initial stage of combustion, and the combustion characteristics of the material are crucial for fire modeling and fire safety design (Chen et al., 2015b; Wu et al., 2022). The presence of PLA catalyzed the pyrolysis of ABS, as evidenced by TGA experiments. Therefore, combustion experiments were carried out using a cone calorimeter. Table 4 lists the values of the relevant parameters of TTI, peak of MLR (p-MLR), average of MLR (a-MLR), peak heat release rate (PHRR), maximum average rate of heat emission (MARHE), total heat release (THR) and EHC for the five samples. Correlation analyses were conducted between heat flux density and these characteristic parameters in turn as follows.
TTI indicates the degree of fire hazard and flammability of solid combustibles (Quintiere, 2006; Luche et al., 2011; Luche et al., 2012; Quang Dao et al., 2013). Figure 3 shows a diagram of TTI versus radiation heat flux for the five samples. As shown in Figure 3a; Table 4, the TTI decreases with increasing radiation heat flux. With the same radiation heat flux, the TTI of blends with different ratios of PLA and ABS decreases as the percentage of ABS increases. This is mainly attributed to the fact that PLA is more difficult to ignite.
According to Janssens, (1991), the reciprical (1/TTI)n for TTI is firstly related to the heat flux using different values of n. n is the coefficient, n = 0.55 and one corresponding to thermally thick and thermally thin solids, respectively. In the present work, none of the sample sizes were thicker than 3 mm. The samples were identified as thermally thin solids and therefore n = 1. The correlation coefficient R2 was obtained using the least squares method in the correlation equation. The lines fitted to the reciprical TTI versus heat flux for n = 1 are shown in Figure 3b. The correlation between conversion TTI and heat flux is shown in Table 5. The qe'' indicates the radiation heat flux (kW/m2).
According to the theory of Quintiere et al. and Luche et al. (Quintiere, 2006; Luche et al., 2011; Luche et al., 2012), the value of critical heat flux (CHF) can theoretically be calculated by
The value of the intercept of the fitted line with the X-axis (hboxIntercept) in Figure 3b is generally considered to be the theoretical critical heat flux (qcr'') using Equation 2. Then the values of qcr'' for the P1A0, P3A1, P1A1, P1A3 and P0A1 are 12.7, 12.6, 12.6, 13.0 and 13.5 kW/m2, respectively. Delichatsios et al. (Delichatsios et al., 2003; Chen et al., 2016) proposed that the minimum heat flux (qmin'') and qcr'' conform to Equation 3.
Then, the qmin” can theoretically be calculated as 18.1, 18, 18, 18.5 and 19.3 kW/m2, respectively. The ignition temperature of samples can be obtained using Equation 4 from the literature (Chen et al., 2019).
where
In this work, the TTI for the five samples of P1A0, P3A1, P1A1, P1A3 and P0A1 were calculated to be 688, 687, 687, 692 and 701 K based on Equation 4 using a MATLAB program.
The MLR (Chen et al., 2019; Chen et al., 2014) is the rate of mass loss during the vaporization and combustion of a solid or liquid fuel. MLR can be used to profile the decomposition rate of a sample and assess its fire risk. Figure 4 demonstrates the MLR versus time for the five samples with radiation heat flux.
Figure 4. Plots of MLR vs. time for the five samples at: (a) 20 kW/m2, (b) 30 kW/m2 and (c) 40 kW/m2.
From Figure 4, the p-MLR and the a-MLR increase with increasing heat flux. According to the literature (Rhodes and Quintiere, 1996), the transient MLR can be expressed as Equation 5:
where
Both the
where C is a constant. Figure 5 shows the p-MLR and a-MLR as a function of heat flux. Figure 5a shows a good linear fit of the p-MLR to the heat flux. The linear relationship between a-MLR and heat flux is not so well shown in Figure 5B. The correlation is expressed as a relationship as shown in Table 6.
The latent heat of vaporization L of the specimen is the inverse of the slope of the fitted straight line according to Equation 6; Figures 4, 5; Table 6. The fitted lines of p-MLR with heat fluxes for P1A0, P3A1, P1A1, P1A3 and P0A1 calculated Lp of 1.32, 1.05, 1.22, 1.49 and 1.43 MJ/kg, respectively. The fitted lines of a-MLR with heat fluxes for P1A0, P3A1, P1A1, P1A3 and P0A1 calculated La of 3.58, 2.88, 3.79, 5.88 and 6.17 MJ/kg, respectively. The La calculated for the same sample a-MLR is much larger than the Lp calculated for the p-MLR. This may be caused by the fact that the whole thermal decomposition process of PLA, ABS and PLA/ABS cannot be considered as steady-state or quasi-steady-state combustion. The a-MLR cannot be considered as strictly following the linear relationship with a heat flux of Equation 7. These resulted in poor confidence in La calculated from the fitted lines of a-MLR and heat flux (Chen et al., 2015b). Therefore, the heat of vaporization Lp calculated from the fitted line of p-MLR and heat flux was used in this study for subsequent analysis.
The HRR of a sample characterizes the rate at which heat is released by the sample burning, which is considered to be the most important variable in fire risk assessment (Carpenter and Janssens, 2005). Figure 6 shows a plot of HRR versus time for the five samples at different heat fluxes.
As seen in Figure 6; Table 4, pure P1A0 starts to burn after ignition and reaches a plateau between 160 and 250 s, followed by a gradual decrease in HRR values to 0 under radiation heat flux conditions of 20 kW/m2. P3A1, P1A1, P1A3 and P0A1 burn faster on ignition. P3A1 reaches a PHRR of 608 kW/m2 at 182 s. P1A1, P1A3 and P0A1 have similar curve shapes and similar PHRR values. The PHRRs for these three samples are 738, 758 and 732 kW/m2 respectively. This means that the percentage of ABS determines the PHRR of PLA/ABS. The PLA/ABS blend gives a similar HRR to that of pure ABS when the PLA content is 50%.
As shown in Figure 7, the PHRR and MARHE increased with increasing heat flux for the five samples. The transient HRR can also be obtained from the transient MLR and the theoretical heat of combustion of the sample in addition to the heat of oxygen consumption method (Quintiere, 2006):
where
The p-MLR and a-MLR are linearly related to the heat flux, as shown in section 3.2.2Mass Loss Rate. The HRR is proportional to MLR for a given sample when the
where C1 is a constant. As shown in Equation 8, the
Based on Equation 8; Table 7, the
If there is no interaction between the components of the blend, a combination of Equation 1; Equation 8 is obtained from the ratio of the heat released from the combustion of the sample alone to the mass of the components in the blend. This equation is expressed as
The theoretical HRRs for the five samples were calculated from Equation 9, as shown by the dashed lines in Figure 8a. Figure 8b shows the value of ΔHRRmax/PHRRE for different samples at three radiation heat fluxes. As shown in Figure 8a, the theoretical and experimental HRR curves do not exactly overlap, while the experimental sample has a faster rise in HRR and a higher PHRR. This indicates that PLA and ABS are more than just the sum of the two burnings separately in the combustion process. From Figure 8b, the ratio ΔHRRmax/PHRRE of P3A1, P1A1 and P1A3 are in the ranges of 34%–35%, 27%–34% and 16%–27% at different radiant heat fluxes. The sample P3A1 has the largest difference in the cone calorimetry. The presence of a small amount of ABS in the blend causes a more pronounced enhancement of the pyrolysis and combustion processes, leading to a higher HRR compared to theoretical results. As the percentage of ABS in the blend increases, the difference between experiment and theory decreases. This is the opposite of the enhanced pyrolysis-promoting effect of PLA/ABS as ABS increases as per Section 3.1 Co-pyrolysis behaviors. This indicates that the degree of burning of the mixture cannot be deduced from the degree of a pyrolytic reaction of the mixture alone. The reason for this opposite trend may be because the more PLA there is in the TGA tests, the lower the temperature corresponding to the second peak reflecting ABS pyrolysis relative to the theoretical value. PLA catalyzes the pyrolysis of ABS in the lower temperature region, resulting in a more vigorous combustion reaction. These results reveal the significant influence of component interactions on the combustion behavior of PLA/ABS blends, providing new insights into their thermal degradation mechanisms.
Figure 8. A comparison of theoretical (T) and experimental (E) HRR for PLA/ABS blends: (a) the HRR curve for P3A1 at 20 kW/m2 and (b) ΔHRRmax/PHRRE.
THR is the total heat energy released when a solid combustible sample burns. EHC represents the actual heat released per unit mass of the sample burned (Santoni et al., 2015). THR and EHC can be calculated using Equations 10, 11 below.
where tend to denote the end time of combustion (s). The Δm is the sample mass loss at the ignition end of combustion (g). Figure 9 shows the THR and EHC histograms for the five samples at three radiation heat fluxes. The results show that the THR values increase uniformly with the proportion of ABS components in the mixture. The THR of the same sample remains almost constant with increasing radiation heat flux. This indicates that THR is an intrinsic property of the sample. The THR of a mixture corresponds to the percentage of each substance. Similar to THR, EHC increases uniformly as the percentage of ABS components in the mixture increases. The EHC value for the same sample remains almost constant with increasing radiation heat flux. The small difference between the values may be due to incomplete combustion, which is strongly influenced by the amount of oxygen in the combustion zone.
The average EHC for P1A0, P3A1, P1A1, P1A3 and P0A1 at the three different heat fluxes were 18, 20, 23, 26 and 29 MJ/kg respectively according to Figure 9; Table 4. This is close to the theoretical EHC as reported earlier in Section 3.2.3 Heat release rates of 15.73, 21.15, 19.20, 22.18 and 21.14 MJ/kg for P1A0, P3A1, P1A1, P1A3 and P0A1 respectively. The average EHC of PLA (18 MJ/kg) is almost identical to the theoretical heat of combustion (19 MJ/kg) obtained with an oxygen bomb calorimeter. The average EHC of the ABS (29 MJ/kg) differs somewhat from the theoretical heat of combustion (39 MJ/kg) obtained with an oxygen bomb calorimeter. This difference can be attributed to incomplete combustion due to insufficient oxygen during combustion. The average EHC for five samples at the three different heat fluxes is much greater than the theoretical heat of combustion deduced from the MARHE data of 8.17, 7.73, 9.28, 10.69 and 11.05 MJ/kg for P1A0, P3A1, P1A1, P1A3 and P0A1, respectively. This could further indicate that the entire thermal decomposition of the sample in this study cannot be considered a steady-state phase. Based on this study, the average HRR data may not be used to estimate the theoretical heat of combustion. Instead, the peak HRR data can be used to obtain relatively accurate theoretical heats of combustion for the thermal decomposition of the five samples.
This study investigates the co-pyrolysis and combustion properties of PLA/ABS blends using TGA and cone calorimetry. The results indicate that PLA catalyzes the pyrolysis of ABS in blends, leading to a more vigorous combustion reaction. The presence of ABS in the blend enhances the thermal degradation of PLA, resulting in a significant synergistic effect on HRR and THR. The kinetic analysis shows that the interaction between PLA and ABS accelerates the degradation process, particularly at lower temperatures. These findings have implications for the efficient utilization and fire protection of PLA/ABS blends. Future work will focus on further exploring the mechanisms of these interactions and improving the mechanical properties of PLA/ABS blends.
The datasets presented in this article are not readily available because the dataset has been provided in the manuscript. Requests to access the datasets should be directed to ZmVpLnhpYW9Ad2h1dC5lZHUuY24=.
XW: Formal Analysis, Methodology, Writing – original draft. YY: Conceptualization, Writing – original draft. YZ: Data curation, Writing – original draft. KL: Funding acquisition, Supervision, Writing – review and editing. FX: Supervision, Validation, Writing – review and editing.
The author(s) declare that financial support was received for the research and/or publication of this article. This work was supported by the National Natural Science Foundation of China (NSFC) under Grant No. 52376123 and the Fundamental Research Funds for the Central Universities (104972024JYS0061) and Science and Technology Program of Department of Transport of Hubei Province (No. 2023-121-1-5).
The authors declare that the research was conducted in the absence of any commercial or financial relationships that could be construed as a potential conflict of interest.
The authors declare that no Generative AI was used in the creation of this manuscript.
All claims expressed in this article are solely those of the authors and do not necessarily represent those of their affiliated organizations, or those of the publisher, the editors and the reviewers. Any product that may be evaluated in this article, or claim that may be made by its manufacturer, is not guaranteed or endorsed by the publisher.
Al-Itry, R., Lamnawar, K., and Maazouz, A. (2012). Improvement of thermal stability, rheological and mechanical properties of PLA, PBAT and their blends by reactive extrusion with functionalized epoxy. Polym. Degrad. Stab. 97, 1898–1914. doi:10.1016/j.polymdegradstab.2012.06.028
Balart, R., Garcia-Sanoguera, D., Quiles-Carrillo, L., Montanes, N., and Torres-Giner, S. (2019). Kinetic analysis of the thermal degradation of recycled acrylonitrile-butadiene-styrene by non-Isothermal thermogravimetry. Polymers 11, 281. doi:10.3390/polym11020281
Carpenter, K., and Janssens, M. (2005). Using heat release rate to assess combustibility of building products in the cone calorimeter. Fire Technol. 41, 79–92. doi:10.1007/s10694-005-6390-z
Chen, R. Y., Lu, S. X., Li, C. H., and Lo, S. M. (2016). Experimental study on ignition and combustion characteristics of fibre-reinforced phenolic composite. Key Eng. Mater. 707, 13–22. doi:10.4028/www.scientific.net/kem.707.13
Chen, R., Lu, S., Li, C., Ding, Y., Zhang, B., and Lo, S. (2015a). Correlation analysis of heat flux and cone calorimeter test data of commercial flame-retardant ethylene-propylene-diene monomer (EPDM) rubber. J. Therm. Analysis Calorim. 123, 545–556. doi:10.1007/s10973-015-4900-x
Chen, R., Lu, S., Li, C., Li, M., and Lo, S. (2015b). Characterization of thermal decomposition behavior of commercial flame-retardant ethylene–propylene–diene monomer (EPDM) rubber. J. Therm. Analysis Calorim. 122, 449–461. doi:10.1007/s10973-015-4701-2
Chen, R., Lu, S., Zhang, B., Li, C., and Lo, S. (2014). Correlation of rate of gas temperature rise with mass loss rate in a ceiling vented compartment. Chin. Sci. Bull. 59, 4559–4567. doi:10.1007/s11434-014-0479-z
Chen, R., Xu, X., Zhang, Y., Lu, S., and Lo, S. (2019). Characterization of ignition and combustion characteristics of phenolic fiber-reinforced plastic with different thicknesses. J. Therm. Analysis Calorim. 140, 645–655. doi:10.1007/s10973-019-08903-4
Delichatsios, M., Paroz, B., and Bhargava, A. (2003). Flammability properties for charring materials. Fire Saf. J. 38, 219–228. doi:10.1016/s0379-7112(02)00080-2
Dhinesh, S. K., Prakash, S. A., Kumar, K. L. S., and Megalingam, A. (2019). Study on flexural and tensile behavior of PLA, ABS and PLA-ABS materials. Mater. Today Proc. 45, 1175–1180. doi:10.1016/j.matpr.2020.03.546
Haaparanta, A.-M., Järvinen, E., Cengiz, I. F., Ellä, V., Kokkonen, H. T., Kiviranta, I., et al. (2013). Preparation and characterization of collagen/PLA, chitosan/PLA, and collagen/chitosan/PLA hybrid scaffolds for cartilage tissue engineering. J. Mater. Sci. Mater. Med. 25, 1129–1136. doi:10.1007/s10856-013-5129-5
Hong, X., Li, Y., Zheng, Y., and Li, Q. (2024). Constructing a biomass flame retardant for fire-safe, thermal management, and compressive strength application of polybutylene adipate terephthalate/polylactic acid foams. Adv. Industrial Eng. Polym. Res. doi:10.1016/j.aiepr.2024.12.003
Hopkins, D., and Quintiere, J. G. (1996). Material fire properties and predictions for thermoplastics. Fire Saf. J. 26, 241–268. doi:10.1016/s0379-7112(96)00033-1
Janssens, M. (1991). Piloted ignition of wood: a review. Fire Mater. 15, 151–167. doi:10.1002/fam.810150402
Janssens, M., Kimble, J., and Murphy, D. (2003). Computer tools to determine material properties for fire growth modeling from cone calorimeter data. Fire Mater. 8, 377–387.
Jia, Y.-W., Zhao, X., Fu, T., Li, D.-F., Guo, Y., Wang, X.-L., et al. (2020). Synergy effect between quaternary phosphonium ionic liquid and ammonium polyphosphate toward flame retardant PLA with improved toughness. Compos. Part B Eng. 197, 108192. doi:10.1016/j.compositesb.2020.108192
Kai, X., Li, R., Yang, T., Shen, S., Ji, Q., and Zhang, T. (2017). Study on the co-pyrolysis of rice straw and high density polyethylene blends using TG-FTIR-MS. Energy Convers. Manag. 146, 20–33. doi:10.1016/j.enconman.2017.05.026
Knurr, B. J., and Hauri, J. F. (2020). An alternative to recycling: measurement of combustion enthalpies of plastics via bomb calorimetry. J. Chem. Educ. 97, 1465–1469. doi:10.1021/acs.jchemed.0c00076
Li, K. Y., Pau, D. S. W., Hou, Y. N., and Ji, J. (2013). Modeling pyrolysis of charring materials: determining kinetic properties and heat of pyrolysis of medium density fiberboard. Industrial and Eng. Chem. Res. 53, 141–149. doi:10.1021/ie402905z
Lin, L., Deng, C., Lin, G.-P., and Wang, Y.-Z. (2015). Super toughened and high heat-resistant poly(lactic acid) (PLA)-based blends by enhancing interfacial bonding and PLA phase crystallization. Industrial and Eng. Chem. Res. 54, 5643–5655. doi:10.1021/acs.iecr.5b01177
Liu, Y., Yi, J., and Cai, X. (2011). Effect of a novel intumescent retardant for ABS with synergist Al(H2PO2)3. Polym. Bull. 67, 361–374. doi:10.1007/s00289-011-0482-3
Luche, J., Mathis, E., Rogaume, T., Richard, F., and Guillaume, E. (2012). High-density polyethylene thermal degradation and gaseous compound evolution in a cone calorimeter. Fire Saf. J. 54, 24–35. doi:10.1016/j.firesaf.2012.08.002
Luche, J., Rogaume, T., Richard, F., and Guillaume, E. (2011). Characterization of thermal properties and analysis of combustion behavior of PMMA in a cone calorimeter. Fire Saf. J. 46, 451–461. doi:10.1016/j.firesaf.2011.07.005
Mandal, D. K., Bhunia, H., and Bajpai, P. K. (2018). Thermal degradation kinetics of PP/PLA nanocomposite blends. J. Thermoplast. Compos. Mater. 32, 1714–1730. doi:10.1177/0892705718805130
Quang Dao, D., Luche, J., Richard, F., Rogaume, T., Bourhy-Weber, C., and Ruban, S. (2013). Determination of characteristic parameters for the thermal decomposition of epoxy resin/carbon fibre composites in cone calorimeter. Int. J. Hydrogen Energy 38, 8167–8178. doi:10.1016/j.ijhydene.2012.05.116
Quintiere, J. G. (2006). A theoretical basis for flammability properties. Fire Mater. 30, 175–214. doi:10.1002/fam.905
Quintiere, J. G., and Rangwala, A. S. (2004). A theory for flame extinction based on flame temperature. Fire Mater. 28, 387–402. doi:10.1002/fam.835
Rhodes, B. T., and Quintiere, J. G. (1996). Burning rate and flame heat flux for PMMA in a cone calorimeter. Fire Saf. J. 26, 221–240. doi:10.1016/s0379-7112(96)00025-2
Rochman, C. M., Browne, M. A., Halpern, B. S., Hentschel, B. T., Hoh, E., Karapanagioti, H. K., et al. (2013). Classify plastic waste as hazardous. Nature 494, 169–171. doi:10.1038/494169a
Santoni, P.-A., Romagnoli, E., Chiaramonti, N., and Barboni, T. (2015). Scale effects on the heat release rate, smoke production rate, and species yields for a vegetation bed. J. Fire Sci. 33, 290–319. doi:10.1177/0734904115591176
Scaffaro, R., Lopresti, F., Marino, A., and Nostro, A. (2018). Antimicrobial additives for poly(lactic acid) materials and their applications: current state and perspectives. Appl. Microbiol. Biotechnol. 102, 7739–7756. doi:10.1007/s00253-018-9220-1
Schartel, B., Bartholmai, M., and Knoll, U. (2005). Some comments on the use of cone calorimeter data. Polym. Degrad. Stab. 88, 540–547. doi:10.1016/j.polymdegradstab.2004.12.016
Signori, F., Coltelli, M.-B., and Bronco, S. (2009). Thermal degradation of poly(lactic acid) (PLA) and poly(butylene adipate-co-terephthalate) (PBAT) and their blends upon melt processing. Polym. Degrad. Stab. 94, 74–82. doi:10.1016/j.polymdegradstab.2008.10.004
Vadori, R., Misra, M., and Mohanty, A. K. (2017). Statistical optimization of compatibilized blends of poly(lactic acid) and acrylonitrile butadiene styrene. J. Appl. Polym. Sci. 134. doi:10.1002/app.44516
Walters, R. N., Hackett, S. M., and Lyon, R. E. (2000). Heats of combustion of high temperature polymers. Fire Mater. 24, 245–252. doi:10.1002/1099-1018(200009/10)24:5<245::aid-fam744>3.0.co;2-7
Wu, X., Bourbigot, S., Li, K., and Zou, Y. (2022). Co-pyrolysis characteristics and flammability of polylactic acid and acrylonitrile-butadiene-styrene plastic blend using TG, temperature-dependent FTIR, Py-GC/MS and cone calorimeter analyses. Fire Saf. J. 128, 103543. doi:10.1016/j.firesaf.2022.103543
Keywords: PLA, ABS, co-pyrolysis, thermogravimetric, cone calorimeter, combustion characteristics
Citation: Wu X, Yang Y, Zhan Y, Li K and Xiao F (2025) Co-pyrolysis and combustion characteristics of polylactic acid and acrylonitrile-butadiene-styrene: insights into interactions, kinetics and synergistic effects. Front. Chem. 13:1552814. doi: 10.3389/fchem.2025.1552814
Received: 29 December 2024; Accepted: 18 March 2025;
Published: 31 March 2025.
Edited by:
Fei Liu, Jiangnan University, ChinaReviewed by:
Svetlana Tretsiakova, Ulster University, United KingdomCopyright © 2025 Wu, Yang, Zhan, Li and Xiao. This is an open-access article distributed under the terms of the Creative Commons Attribution License (CC BY). The use, distribution or reproduction in other forums is permitted, provided the original author(s) and the copyright owner(s) are credited and that the original publication in this journal is cited, in accordance with accepted academic practice. No use, distribution or reproduction is permitted which does not comply with these terms.
*Correspondence: Kaiyuan Li, a3lsaUB3aHV0LmVkdS5jbg==; Fei Xiao, ZmVpLnhpYW9Ad2h1dC5lZHUuY24=
Disclaimer: All claims expressed in this article are solely those of the authors and do not necessarily represent those of their affiliated organizations, or those of the publisher, the editors and the reviewers. Any product that may be evaluated in this article or claim that may be made by its manufacturer is not guaranteed or endorsed by the publisher.
Research integrity at Frontiers
Learn more about the work of our research integrity team to safeguard the quality of each article we publish.