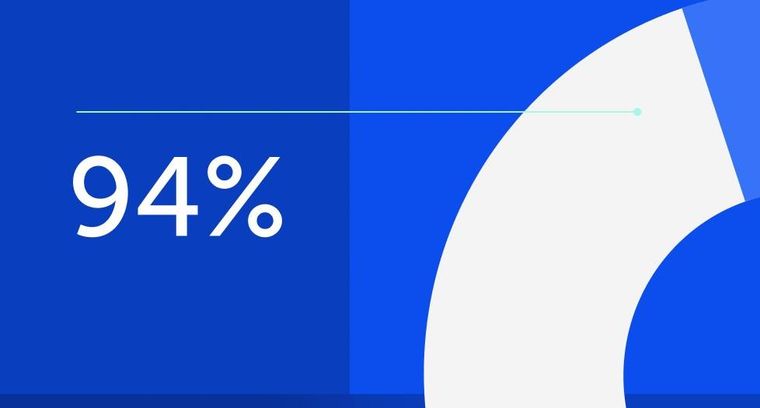
94% of researchers rate our articles as excellent or good
Learn more about the work of our research integrity team to safeguard the quality of each article we publish.
Find out more
ORIGINAL RESEARCH article
Front. Chem., 19 March 2025
Sec. Polymer Chemistry
Volume 13 - 2025 | https://doi.org/10.3389/fchem.2025.1545984
Polymeric shock tubes are now widely used in explosives systems for drilling and mining operations. Most shock tubes on the market consist of three layers of polymer, the first layer being Surlyn 8940 copolymer, the second layer Nucrel 31001 and the outer layer Borostar ME 6053 medium density polyethylene. Surlyn and Nucrel are usually sourced from DuPont, polyethylene from Charlotte Boralis. the main goal in this research is reducing the price of final shock tube and reuse the waste tube of plant (rejected shock tube) with improving the properties of product. For reaching to this goal, using polyethylene blend with available raw materials in the country and mixing them with rework from the shock tube production plant. For this purpose, different proportions of low- and high-Density polyethylene are blend using a twin-screw extruder and finally mixed with some of the factory’s polymer rework. In the first phase, the low-density polyethylene LDPE 020, the high-density polyethylene HDPE HI 0500 and the filler calcium carbonate were blend in a twin-screw extruder and compounded with different percentages of 20/75/5, 30/65/5, 40/55/5 and 47/47/6 percent respectively. In the second phase, the resulting blend was mixed physically with 5, 10 and 15 percent three-layer tube rework (which was crushed with a crusher or pelletizer). The results showed that the 47/47/6 percent mixture had the best composition in terms of the production process, the properties of blend in terms of tensile strength (17/3 MPa), elongation percentage (458%) was suitable. In order to reduce the waste and cost of the product, the best processing results, product properties and costs are obtained when the above composition is mixed with crushed shock tube rework in a ratio of 90/10 (blend/rework). Tensile strength at break was 20/01 MPa and elongation at break was 478%. After evaluating the raw materials and accepting the results, the polymer blends were used on an industrial scale to produce shock tubes. The performance of the resulting shock tubes was then compared using various tests, including mechanical tests, oil penetration resistance, thermal shrinkage (in 60°C: upper 7% and in 80°C: upper 9%), burst strength, thermal aging (before aging:170 N, after aging: N5, N6, N7, N8: upper 170 N), and explosion velocity (upper 1890 m/s). The results showed that by using the polymer blend with rework, the mechanical properties of the shock tubes produced met the standard (tensile strength of more than 170 N/m2 and elongation percentage of more than 220). The results of the oil penetration resistance (45–50 h), burst strength and aging tests also showed that all shock tubes manufactured with the new third layer had acceptable properties and were on the same level as shock tubes made of Boralis polyethylene.
One of the most important developments in the 1960s in the mining, construction and drilling sectors was the industrial development of the shock tube detonator (Yakan-A-Nwai and Mukhopadhyay, 2013a; AyalaCarcedo, 2017; Persson et al., 2018; Himanshu, 2024). In general, explosive systems (blasting systems) used in mining and drilling operations consist of three parts: the detonator, the explosive charge and the energetic charge (Balan and Raj, 2023; Li et al., 2024). The function of the detonator is to emit a signal or wave that activates and sets off the explosive charge. The explosive charge receives the signal and, by amplifying it, causes the energetic charge to explode (Yakan-A-Nwai and Mukhopadhyay, 2013a; AyalaCarcedo, 2017; Himanshu, 2024; Dick et al., 1982). Shock tubes are a type of initiator system. These devices consist of a hollow plastic tube containing explosive powder (see in Figure 1) (Yakan-A-Nwai and Mukhopadhyay, 2013a; Fordham, 2013; Choudhary, 2024; Meyer et al., 2016).
Figure 1. Above side of the shock tube connected to a non-electric explosive detonator (Yakan-A-Nwai and Mukhopadhyay, 2013a) and below side of the shock wave transmission inside the tube by the combustion of explosive powder inside it (Balan and Raj, 2023; Yakan-a-Nwai and Mukhopadhyay, 2013b).
Polymer shock tubes can be divided into three categories depending on the number of layers: single-layer, double-layer and triple-layer (Salehi et al., 2021; Jia et al., 2024; Abedi et al., 2018). Gladden et al. developed a triple-layer shock tube in 2002 (Yakan-a-Nwai and Mukhopadhyay, 2013b; Goncharov, 2023). Gladden et al. used ethylene-Surlyn ionomers for the first layer, which should have good adhesion to explosive powders. For the outer layer, they proposed nylon 6, LDPE and MDPE (Yakan-a-Nwai and Mukhopadhyay, 2013b; Goncharov, 2023). For the middle layer, they also selected polymers with good adhesion to the other two layers (Yakan-a-Nwai and Mukhopadhyay, 2013b; Goncharov, 2023).
In 2013, Christian Yakan et al. used the following compositions for the second layer of a two-layer shock tube (Yakan-A-Nwai and Mukhopadhyay, 2013a; Yakan-a-Nwai and Mukhopadhyay, 2013b):
HDPE/HDPE g MAH: 30/70
HDPE/IONOMER: 30/70
HDPE/ EMA: 30/70
LLDPE/ IONOMER: 30/70
After fabricating the two-layer shock tube, they concluded that the first three compounds, most of which are made of HDPE, have higher burst strength than the last compound, which is made of LLDPE, due to less branching and greater crystallinity.
The sleep time of the HDPE/HDPE g MAH blend was also higher than that of the other blends, with maleic anhydride groups increasing the penetration resistance and thermal resistance of the polymer. High thermal resistance reduces heat transfer from hot oil to the inner layer of the shock tube, and hot oil takes longer to transfer to the inner layer. The blend made from high density polyethylene and ionomer has moderate penetration resistance due to the complex molecular structure of the ionomer, which makes it difficult for organic and inorganic solvents to penetrate it. They also found that the blend of high-density polyethylene and ethylene methacrylate has low penetration resistance and the blend of linear low-density polyethylene has the lowest oil penetration resistance, which is due to the presence of civet branching and consequently more pores in linear low-density polyethylene that allow solvent penetration.
They also found that the breaking strength of the blend of high-performance polyethylene and ethylene methacrylate was higher than that of the others. This is due to the high adhesion of these two compounds to each other. Today, conventional and commercially available shock tubes are available in single-layer, double-layer and triple-layer types. However, high-performance shock tubes usually consist of three polymer layers. The performance characteristics of a triple-layer shock tube are listed in Table 1. The inside of such tubes is coated with a mixture of HMX and aluminum as an explosive powder (Yakan-a-Nwai and Mukhopadhyay, 2013b; Manner et al., 2012). Different types of Surlyn are used to produce the inner layer of this type of shock tube. When selecting the polymer used for the outer layer, polyolefins are usually preferred due to their low price and easy and cheap processability. In this case, the middle layer must be able to create good adhesion between a polar polymer such as Surlyn and a non-polar polymer such as the polyolefins. NUCREL is an ethylene copolymer that is copolymerized with different proportions of acrylic acid or methacrylic acid, depending on the type and grade. In most shock tubes, this copolymer is used as the raw material for the middle layer. However, the price of this copolymer is higher than that of conventional polyolefins, so replacing it with a cheaper polymer with the same performance characteristics can reduce production costs.
Polyolefins are among the most widely used thermoplastics, which are widely used in the packaging, wire and cable, automotive, electronics and other industries due to their low price, good low-temperature processability and easy availability (Parthasarathy et al., 2013; Rajeshwari and Dey, 2014; Graziano et al., 2020; Rajeshwari et al., 2019; Favakeh et al., 2020).
However, some properties of these materials prevent their wider use. In the polymer industry, a material with suitable properties can be obtained by blending and compounding two or more polymers. The properties of the blend resulting from the properties of the individual blend phases in the pure and single state are thus better. Due to the good compatibility of the polyolefin family, the alloying of different polyethylene types with each other has been carried out for years on an industrial and laboratory scale (Rosales et al., 2020; Su et al., 2010; Klimovica et al., 2020; Zhou et al., 2020; Leng et al., 2020). In plants for the production of shock tubes, a large amount of rework is usually generated at the beginning of the production process. The addition of this rework, which contains Surlyn ionomer, interlayer adhesive and three-layer polyethylene, to the polyethylene mixture can increase the modulus and tensile strength of the polyethylene (Rosales et al., 2020; Su et al., 2010).
Ionomer Surlyn 8940 with a density of 0.95 g/cm3 and a melt flow index of 2.8 dg/min containing sodium ions and methacrylic acid groups, as well as Nucrel 31,001 with a density of 0.940 g/cm3 and a melt flow index of 1.3 dg/min containing 9.5 wt% acrylic acid groups, were obtained from DuPont, United States. Medium density polyethylene with trade names HTA002, EXCEES 1327CA, Borstar ME6053 was obtained from Boralis.
It is a type of high density, medium molecular weight polyethylene that is easy to process. This polymer is normally used in coextrusion processes with other polyolefins or alone. Its physical properties are shown in Table 2. In the structure of the shock tube, it is used in the production of the material composition of the outer layer of the shock tube. It accounts for 30% of the weight of this material.
This polymer is a hexane-ethylene copolymer produced with a metallocene catalyst. It has a high modulus and at the same time a high toughness and is therefore ideal for the production of multilayer films. The interesting thing about this material is that no data sheet has been published for it.
This material is a type of medium-density polyethylene that is characterized by its resistance to ultraviolet radiation and its good colourability. This material is manufactured using Borstar’s special technology, which gives it the ability to facilitate processability and molding. The shrinkage of this part during molding, common in polymers, is reduced to a minimum while maintaining mechanical strength. It contains ultraviolet-resistant fillers. Typically, one of Exceed 1327CA and Borstar ME6053 selectively makes up 70% by weight of the outer layer of the shock tube (As seen in Table 3).
Typically, one of the two materials Exceed 1327CA and Borstar ME6053 selectively makes up 70% by weight of the outer layer of the shock tube.
This material is added as a pigment to the polymer mixture mentioned in the previous step. It is a colored low-density polyethylene that is added to the mixture of HTA0200 and Borstar ME6053 by applying color. Its color depends on the user’s choice and varies. Its physical properties are listed in Table 4.
In this research work, based on the study of the properties of different types of polyethylene, two types of low- and high-density polyethylene obtained from Bandar Imam Petrochemical Company were used. The properties of the light polyethylene LDPE020 and heavy polyethylene HDPE HI 0500 used in this study are shown in Tables 5, 6:
Table 5. The characteristics of low density polyethylene LDPE020 and high density polyethylene HDPE HI 0500.
The middle layer is generally an adhesive used to bond the outer and inner layers of the shock tube. Its trade name is Nucrel 31,001 and this material is a type of ethylene-acrylic copolymer containing 9.5% acrylic acid by weight. Its main application is injection molding and coextrusion as an adhesive. Its physical properties are listed in Table 7.
In this study, the Nucrel copolymer was replaced by a blend of polyethylene grafted with maleic anhydride and polypropylene and used as a second layer. Its properties are given in Table 8.
This layer consists of two parts: Polymer and explosive. The polymer part is the main carrier and the aluminum powder and the HMX explosive are the materials that come into contact with the tube. Surlyn 8940 is the actual carrier of the explosive in the shock tube. The trade name of the material is Surlyn 8940, which is a thermoplastic sodium ionomer plastic produced by copolymerization of methacrylic acid in the presence of ethylene so that it contains 14.5%–15.5% methacrylic acid by weight and its acid groups are neutralized by sodium ions. In fact, an acidic salt is formed at the end. Table 9 shows the physical and process properties for identification. The main application of this material is in extrusion molding.
The inner wall of the inner layer of the shock tube is coated with explosive powder. This powder mixture is in micronized form. The powder consists of 92% HMX and 8% aluminum powder.
With the help of a ZSK twin-screw extruder (ZSK MC18 D0/Di:1/55) from Iran Polymer and Petrochemical Institute, low density polyethylene LDPE 020, high density polyethylene HDPE HI0500 and filler were blend as follows:
• 20/75/5%
• 30/65/5%
• 40/55/5%
• 47/47/6%
The three-layer shock tube rework produced in the factory was broken down into 1*3 mm particles using a crushing machine (Pelletizing System COLLIN SP2) (As seen in Figure 2). In the next step, the best compound in terms of process, properties and final price was mixed with shredded three-layer tube rework at 5, 10 and 15 percent respectively using a mixer (Horizontal behsaz polymer 100 Kg) (As seen in Table 10). The specific condition for mixing the best blend with rework:
Figure 2. ZSK twin-screw extruder (Top), Mixer (Bottom) of polymers and Shock Tube three-layer tube rework crushing machine (Left).
RPM: 50
Temperature: 25°C
Time: 1 h.
Stages of adding rework to blend: 3 stage.
The polyethylene control sample was Borostar medium-density polyethylene labeled P8.
After preparing the polymer blends, 100 m shock tubes of each of the formulations were prepared according to the method described by Yakan and Mukhopadhyay (Yakan-A-Nwai and Mukhopadhyay, 2013a). The shock tubes were named according to Table 11.
First, dumbbell-shaped samples of Borstar medium density polyethylene (P8) and samples P1 to P7 were prepared using a injection molding machine available in Iran Polymer and Petrochemical Research Institute according to ASTM 823 standard. Then, 5 dumbbells from each of the samples were subjected to mechanical tensile testing using a SANTAM STM-20 tensile testing machine at a speed of 100 mm/min. In addition, in order to examine the mechanical properties of the manufactured shock tubes and after heat aging, 30 cm long samples were cut from each of the shock tube tubes N1 to N8 and subjected to mechanical tensile testing at a speed of 100 mm/min.
This test was carried out at two temperatures of 60
As explained in the “Mechanical properties” section, for this test a certain number of samples from each of the shock tubes were cut to a length of 30 cm and placed in an oven at 50
When the shock tube is activated, the explosive powder in the inner layer explodes and transmit to the end of the tube until the wave resulting from the explosion of the explosive powder reaches the primer and triggers it. For the shock tube to function properly, it is necessary that the shock wave is only transmitted in the longitudinal direction. Therefore, the tube wall must resist the shock wave entering in the radial direction. This resistance is referred to as bursting strength. To test the bursting strength, three samples of 5 m length were cut from each type of tube. The samples were placed in an oven at 50
Figure 3. Image of two tubes that burst during the burst strength test (Yakan-A-Nwai and Mukhopadhyay, 2013a; Yakan-a-Nwai and Mukhopadhyay, 2013b).
To carry out this test, 300 mL of liquid paraffin oil was poured into a beaker with a volume of 750 mL. Then a certain number of 30 cm long shock tubes, both ends of which were sealed with an ultrasonic device, were placed in a U-shape in the beaker with oil. The middle 10 cm of the tubes came into contact with the paraffin oil. So that the middle 10 cm of the tubes come into contact with the paraffin oil. The beaker was placed in a water bath and the temperature of the water in it was adjusted so that the temperature of the oil bath in the beaker remained constant at 50
As can be seen in Figures 4, 5, when low- and high-density polyethylene are blend in different proportions, there is no significant change in the tensile strength and elongation of these two types of polyethylene as a percentage (Table 12). However, when three-layer shock tube rework is added, there is significant change in the tensile strength and elongation of between without and with rework and the tensile strength of the blend increases by two to four units, which is due to the presence of Surlyn ionomer in the rework, which has high mechanical strength. The elongation percentage of the compound also increases by 10–16 unit, which is due to the presence of Surlyn ionomer in the rework, which has a high elongation percentage.
Figure 4. Tensile strength of Borostar polyethylene, blend of polyethylene compounds and shock tube rework.
Figure 5. Percentage elongation of Borostar polyethylene, blend of polyethylene compounds and shock tube rework.
The result has been showed that there is not no significant difference between various blending in tensile properties of product (Table 13).
Table 13. Result of analysis of variance effect of blending without and with rework in tensile properties.
The result has been showed that there is not significant difference between various blending and using of rework in tensile properties of product.
Polymer fibers and films that are stretched during the manufacturing process shrink when used at high temperatures (Leng et al., 2020; Gupta et al., 1994). Shock tubes are also stretched at various stages of the manufacturing process. In addition, the polymer chains are stretched and aligned in the extruder and as they exit the die. This alignment can improve the mechanical properties, but also leads to thermal shrinkage of the polymer. The results of the linear heat shrinkage test in Figure 6 show that the linear heat shrinkage of N1 – N4 is lower than that of the other shock tubes at both temperatures. At 60
However, samples N5, N6 and N7 exhibit greater thermal shrinkage than the other shock tubes. In ordered polymers, such as polymer fibers, both the amorphous and crystalline regions become ordered (Trznadel and Kryszewski, 1992). As the temperature increases, the polymer chains have the opportunity to escape from some of the induced arrangements. It is in the nature of things that the chains in the crystalline regions need higher temperatures or more time to escape from the arrangements. A polymer with lower crystallinity therefore shows greater thermal shrinkage at the same time and temperature. From this it can be concluded that the higher the crystal content in a particular polymer, the less linear thermal shrinkage this sample will exhibit under the same conditions as the same polymer with lower crystallinity. In addition to polyethylene, samples N5, N6 and N7 also contain a 5 to 15 ionomer compound of Surlyn and polyethylene grafted with maleic anhydride. The grafting of polar groups onto a semi-crystalline polymer chain such as polyethylene leads to a decrease in the sequence of chains that have to be joined together to form a crystal, and thus also in the degree of crystallinity of the polymer. Since the shock tubes produced in samples N5, N6 and N7 contain polar compounds and have a lower crystallinity, this conclusion can probably be used as a reason for the higher heat shrinkage of these three compounds compared to other shock tubes. Overall, the percentage of heat shrinkage of the tubes was within the normal range, i.e., less than 10.
The tensile strength range of high-performance shock tubes is between 170–200 N (Yakan-a-Nwai and Mukhopadhyay, 2013b). The results of the tensile tests show that all shock tubes developed in this work have a tensile strength of more than 170 N. However, the shock tubes N5, N6 and N7 had higher tensile strengths than the other shock tubes. However, this value was not significantly different from that of the other samples, and it can be said that the shock tubes N1 to N4 have mechanical properties and breaking strength of 170–175 N, but when crushed rework is added to the third layer, the breaking strength of the tube increases to over 180 N. As mentioned above, the number of polar groups in Surlyn and PEGMA increases the adhesion between the second and third layers. Despite the higher tensile strength of the polyethylene blend, shock tube N8 has a lower tensile strength than N5, N6 and N7. Figures 7, 8 show that these results also apply to the tensile strength of shock tube. It can therefore be concluded that for the materials that make up the third layer of shock tube, a higher adhesive strength is likely to have a greater effect on improving the mechanical properties of shock tube than better mechanical properties. All shock tubes exploded after leaving the furnace with the help of an electric shocker. This indicates that thermal aging did not affect the explosive properties of the shock tubes. Thermal aging of blend is molecular deterioration as outcome of overheating due to the presence of tertiary hydrogen atoms in the polymer chan. The elevated temperature causes chain scission of the long chain backbone of polymer that react with one another. The mechanical properties of the shock tubes after thermal aging also showed a similar trend to the mechanical properties before thermal aging. However, after thermal aging, the tensile strength of all shock tubes decreased compared to before thermal aging. In addition, the tensile strength of the shock tubes increased.
The occurrence of linear heat shrinkage can affect the mechanical properties of shock tubes. Heat aging creates exactly the same conditions as linear heat shrinkage. The difference is that the samples in this test were stored in an oven at 50
In the case of multi-layer tubes, all layers must have good burst strength. The results of this test for all shock tubes showed that no bursting was detected in the samples, which means that all shock tubes have good burst strength.
The results of the oil penetration resistance test showed that all shock tubes could properly explode after 50 h in a paraffin oil bath at 50
Figure 9 shows the explosion velocity of shock tubes made with the third layer with different compositions. As can be seen, the explosion velocity of all tubes is higher than 1800 m/s. It can be concluded that the third layer has no effect on the explosion velocity of the shock tube and only affects the mechanical properties and resistance to solvent penetration.
1. The results of the mechanical tests show that the addition of three-layer shock tube rework to the LDPE and HDPE blend increases the mechanical tensile strength and the percentage elongation of the finished tube. However, the best percentage of rework is 10%. This is because when the second and third layers are added to the Surlyn tube in the coextruder section, 15% of the coextruder outlet is extruded as filamentous melt, causing the tube to crack during production and stopping the production line, which in turn increases production rework.
2. The use of filler and three-layer tube rework reduces the cost price of the product by 15%.
3. The results show that although the mechanical strength of LDPE and HDPE is similar and that different proportions of these two polymer types do not cause a significant change in mechanical strength, given the low price of HDPE compared to LDPE, increasing the proportion of this material to 3.42 reduces the cost of the compound.
4. The use of a polyethylene blend with factory rework reduces the cost of the product by 35%–45% compared to Borostar. The properties of the finished tube are within the standard range.
5. All shock tubes have been successfully exploded without defects following tests for oil penetration resistance, bursting strength and heat aging.
6. The tensile strength of all shock tubes was within the standard range for high performance shock tubes (more than 170 N). The mechanical properties of the shock tubes did not differ significantly. However, despite the better mechanical properties of Borostar polyethylene in this study compared to the polyethylene alloy, shock tubes N5, N6 and N7 had better mechanical properties than shock tubes N1, N2, N3, N4 and N8. This discrepancy is probably due to the better adhesion of the Surlyn- and PEGMA-containing rework to the second layer of the shock tube.
7. The shock tubes N5, N6 and N7 showed higher linear thermal shrinkage than the shock tubes N1 to N4 at both 60
8. In conclusion, the shock tubes N1, N2, N3, N4, N5, N6 and N7 have similar properties to the shock tube N8, so any of the blends P1, P2, P3, P4, P5, P6 and P7 can be a suitable alternative to Borostar.
The original contributions presented in the study are included in the article/supplementary material, further inquiries can be directed to the corresponding author.
AK: Conceptualization, Data curation, Formal Analysis, Funding acquisition, Investigation, Methodology, Project administration, Resources, Software, Supervision, Validation, Visualization, Writing–original draft, Writing–review and editing. MD: Conceptualization, Data curation, Formal Analysis, Funding acquisition, Investigation, Methodology, Project administration, Resources, Software, Supervision, Validation, Visualization, Writing–original draft, Writing–review and editing. SS: Conceptualization, Data curation, Formal Analysis, Funding acquisition, Investigation, Methodology, Project administration, Resources, Software, Supervision, Validation, Visualization, Writing–original draft, Writing–review and editing. MP: Conceptualization, Data curation, Formal Analysis, Funding acquisition, Investigation, Methodology, Project administration, Resources, Software, Supervision, Validation, Visualization, Writing–original draft, Writing–review and editing.
The author(s) declare that financial support was received for the research, authorship, and/or publication of this article. This research was supported by university of zabol (iran) with grant code (IR-UOZ-GR-5071).
The authors declare that the research was conducted in the absence of any commercial or financial relationships that could be construed as a potential conflict of interest.
The authors declare that no Generative AI was used in the creation of this manuscript.
All claims expressed in this article are solely those of the authors and do not necessarily represent those of their affiliated organizations, or those of the publisher, the editors and the reviewers. Any product that may be evaluated in this article, or claim that may be made by its manufacturer, is not guaranteed or endorsed by the publisher.
Abedi, H. R., Salehi, M., and Shafyei, A. (2018). Multi-layered thermal barrier coatings on BMI polyimide matrix composite. Surf. Coatings Technol. 337, 104–116. doi:10.1016/j.surfcoat.2018.01.007
AyalaCarcedo, F. (2017). Drilling and blasting of rocks. 1st Edn. London: Routledge. 408. doi:10.1201/9781315141435
Balan, G. S., and Raj, S. A. (2023). A review on Shock tubes with multitudinous applications. Int. J. impact Eng. 172, 104406. doi:10.1016/j.ijimpeng.2022.104406
Dick, R. A., Fletcher, L. R., and D’Andrea, D. V. (1982). Explosives and blasting procedures manual. US Department of the Interior, Bureau of Mines.
Favakeh, M., Bazgir, S., and Karbasi, M. (2020). Dynamically vulcanized thermoplastic elastomer nanocomposites based on linear low-density polyethylene/styrene-butadiene rubber/nanoclay/bitumen: morphology and rheological behavior. Iran. Polym. J. 29 (3), 209–217. doi:10.1007/s13726-020-00786-9
Goncharov, V. G. (2023). Thermal and thermodynamic investigations of ceramic and molten salt systems relevant to the development of advanced nuclear reactors. (dissertation/thesis.) Washington State University ProQuest Dissertations and Theses, 30316963.
Graziano, A., Garcia, C., Jaffer, S., Tjong, J., and Sain, M. (2020). Novel functional graphene and its thermodynamic interfacial localization in biphasic polyolefin systems for advanced lightweight applications. Compos. Sci. Technol. 188, 107958. doi:10.1016/j.compscitech.2019.107958
Gupta, V., Radhakrishnan, J., and Sett, S. (1994). Effect of processing history on shrinkage stress in axially oriented poly (ethylene terephthalate) fibres and films. Polymer 35 (12), 2560–2567. doi:10.1016/0032-3861(94)90379-4
Himanshu, V. K., Bhagat, N. K., Vishwakarma, A. K., and Mishra, A. K. (2024). Principles and practices of rock blasting. 1st Edn. Boca Raton: CRC Press. doi:10.1201/9781003461616
Jia, S., Wang, C., Xu, W., Ma, D., and Qi, F. (2024). Experimental investigation on weak shock wave mitigation characteristics of flexible polyurethane foam and polyurea. Def. Technol. 31, 179–191. doi:10.1016/j.dt.2023.06.013
Klimovica, K., Pan, S., Lin, T. W., Peng, X., Ellison, C. J., LaPointe, A. M., et al. (2020). Compatibilization of i PP/HDPE blends with PE-g-i PP graft copolymers. ACS Macro Lett. 9 (8), 1161–1166. doi:10.1021/acsmacrolett.0c00339
Leng, J., Gu, X., Hong, R., and Zhang, J. (2020). Tailored crystalline structure and enhanced impact strength of isotactic polypropylene/high-density polyethylene blend by controlling the printing speed of fused filament fabrication. J. Mater. Sci. 55, 14058–14073. doi:10.1007/s10853-020-04999-4
Li, C., Luo, Y., Deng, H., Zhou, Z., Ning, H., Shang, Y., et al. (2024). Shock tube and kinetic modeling study on high-temperature ignition of ammonia blended with methyl hexanoate. Combust. Flame 266, 113555. doi:10.1016/j.combustflame.2024.113555
Manner, V. W., Pemberton, S. J., Gunderson, J. A., Herrera, T. J., Lloyd, J. M., Salazar, P. J., et al. (2012). The role of aluminum in the detonation and post-detonation expansion of selected cast HMX-based explosives. Propellants, Explos. Pyrotech. 37 (2), 198–206. doi:10.1002/prep.201100138
Parthasarathy, V., Dhanalakshmi, V., and Anbarasan, R. (2013). Thermal, melting and crystallinity behavior of esters grafted LDPE by thermolysis method. Int. J. Plastics Technol. 17, 61–74. doi:10.1007/s12588-013-9047-7
Persson, P.-A., Holmberg, R., and Lee, J. (2018). Rock blasting and explosives engineering. 1st Edn. Boca Raton: CRC Press. doi:10.1201/9780203740514
Rajeshwari, P., and Dey, T. (2014). Thermogravimetric kinetics of degradation of HDPE based MWCNTs reinforced composites. Int. J. Plastics Technol. 18, 294–320. doi:10.1007/s12588-014-9076-x
Rajeshwari, P., Rao, V., and Dey, T. (2019). Depth-sensing indentation and nano-dynamic mechanical properties of aluminum nitride nanoparticles reinforced high density poly-ethylene nanocomposites. Polym. Compos. 40 (1), 240–254. doi:10.1002/pc.24637
Rosales, C., Bernal, C., and Pettarin, V. (2020). Effect of blend composition and related morphology on the quasi-static fracture performance of LLDPE/PP blends. Polym. Test. 90, 106598. doi:10.1016/j.polymertesting.2020.106598
Salehi, M., Mirbagheri, S., and Ramiani, A. J. (2021). Efficient energy absorption of functionally-graded metallic foam-filled tubes under impact loading. Trans. Nonferrous Metals Soc. China 31 (1), 92–110. doi:10.1016/s1003-6326(20)65480-2
Su, R., Wang, K., Zhang, Q., Chen, F., and Fu, Q. (2010). Effect of melt temperature on the phase morphology, thermal behavior and mechanical properties of injection-molded PP/LLDPE blends. Chin. J. Polym. Sci. 28 (2), 249–255. doi:10.1007/s10118-010-9013-1
Trznadel, M., and Kryszewski, M. (1992). Thermal shrinkage of oriented polymers. J. Macromol. Sci. Part C Polym. Rev. 32 (3-4), 259–300. doi:10.1080/15321799208021428
Yakan-A-Nwai, C., and Mukhopadhyay, S. (2013a). An investigation into polyethylene blends for the design of high performance shock tubes. Int. J. Plastics Technol. 17, 24–34. doi:10.1007/s12588-013-9045-9
Yakan-a-Nwai, C., and Mukhopadhyay, S. (2013b). Progressive developments of polymeric shock tubes for initiating systems.
Keywords: blasting systems, shock tube, polymer compound, mechanical properties, low density
Citation: Khalili Gashtroudkhani A, Dahmardeh Ghaleno M, Soltan Abadi S and Pouyani M (2025) Investigating the use of low and high-density polyethylene blends with waste material from three-layer factory tube for the third layer of shock tubes. Front. Chem. 13:1545984. doi: 10.3389/fchem.2025.1545984
Received: 16 December 2024; Accepted: 17 February 2025;
Published: 19 March 2025.
Edited by:
Odda Ruiz de Ballesteros, Department of Chemical Sciences of University of Napoli Federico II, ItalyReviewed by:
Ravichandran Kollarigowda, American Dental Association, United StatesCopyright © 2025 Khalili Gashtroudkhani, Dahmardeh Ghaleno, Soltan Abadi and Pouyani. This is an open-access article distributed under the terms of the Creative Commons Attribution License (CC BY). The use, distribution or reproduction in other forums is permitted, provided the original author(s) and the copyright owner(s) are credited and that the original publication in this journal is cited, in accordance with accepted academic practice. No use, distribution or reproduction is permitted which does not comply with these terms.
*Correspondence: Ali Khalili Gashtroudkhani, YS5raGFsaWxpQGlwcGkuYWMuaXI=; Mohammad Dahmardeh Ghaleno, bW1kYWhtYXJkZWhAdW96LmFjLmly
Disclaimer: All claims expressed in this article are solely those of the authors and do not necessarily represent those of their affiliated organizations, or those of the publisher, the editors and the reviewers. Any product that may be evaluated in this article or claim that may be made by its manufacturer is not guaranteed or endorsed by the publisher.
Research integrity at Frontiers
Learn more about the work of our research integrity team to safeguard the quality of each article we publish.