- 1School of Mechanical Engineering, Chongqing Three Gorges University, Chongqing, China
- 2Department of Quantitative Analysis, College of Business Administration, King Saud University, Riyadh, Saudi Arabia
- 3Department of Mathematics and Statistics, Hazara University, Mansehra, Pakistan
This study investigates the significance of single-walled (SWCNTs) and multi-walled (MWCNTs) carbon nanotubes with a convectional fluid (water) over a vertical cone under the influences of chemical reaction, magnetic field, thermal radiation and saturated porous media. The impact of heat sources is also examined. Based on the flow assumptions, the fundamental flow equations are modeled as partial differential equations (PDEs). Using the appropriate transformation, the PDEs are converted to ordinary differential equations and then solved via RK4 in MATLAB. To confirm the results, a comparison is made with a previously investigated problem, finding good agreement. The emerging dimensionless physical parameters impact on the flow problem is determined through graphs and tables. Analysis reveals a dual solution for the suction and injection parameter. Therefore, stability examination is implemented to confirm a stable solution. The aim of the study is to analyze SWCTs and MWCTs in a vertical cone with stability to establish that only the first solution is reliable. The analysis here signifies that large volume fractions can be substituted to increase the nanofluid movement. The mathematical model and graphical demonstration indicate that the velocity of MWCNTs is higher than SWCNTs. Moreover, the local skin friction, rate of heat transfer, and Nusselt and Sherwood numbers improve with Biot number.
1 Introduction
Heat transmission is crucial for both machine performance and material choice. The biological sciences, thermoregulation, bio-heat transfer activities, and blood circulation all greatly benefit from heat transmission. Every biological and mechanical process eventually loses efficiency because it generates heat; regular heat removal from a system is required to maximize its effectiveness. Nanofluids (NFs) are novel substances which can regulate heat conduction. Water, polymerization, engine oil, and various lubricants are examples of common fluids that have lower heating conductivity than solids. Increasing the heat conductivity of such fluids is as simple as adding a certain quantity of solid particles. Nanomaterials are small particles, typically 1–100 nm in size; their resulting fluid is known as “nanofluid”. Choi and Eastman (1995a; 1995b) first recommended the creation of NFs. Xuan and Li (2000) discussed developments in NF heat transmission. To analyze the movement of NFs, Buongiorno (2006) derived a model that included thermophoresis and Brownian motion dynamics. Many singularities, including the reduction or augmentation of the network’s thermal magnitude, the buildup of microchannels, the miniaturization of the entire structure, and minimum clogging, may be better understood using NFs. The electromagnetic dipole impact on Williamson NF under heat was studied by Khan et al. (2020a); they also investigated entropy production on magneto-fluid under robin restrictions with dissipation (Khan et al., 2020b).
Memon et al. (2022) and Abu-Bakr et al. (2022) discuss the larger body of work on heat transmission using NFs. Because of its extensive uses in industry, research, and engineering, heat-mass transfer has attracted much scholarly attention. It is crucial for raising the threshold for final product quality and finds use in ferromagnetic medication targeting and the cooling process of electronic gadgets, among other chemical and pharmacological processes. Hayat et al. (2017a) studied the computational analysis of carbon nanotubes (CNTs) with slip conditions. Hayat et al. (2017b) investigated homogeneous as well as heterogeneous influences in fluid movement with joule heating. Hussain et al. (2022) reported the slip and joule effects in NF over stretched plate. Similarly, Hayat et al. (2019) examined Jeffrey NF in Darcian flow with heat source and melting effects. Other practical uses include insulation, the storage of thermal energy, the extraction and utilization of fossil fuels, the paper sector, food preparation, the inclusion of oxygen, drying porous solids, dialysis treatment, underground energy dissemination, and the restoration of geothermal energy. Peristaltic movement, heat transmission, mass transportation, and chemical processes were all investigated by HinanS et al. (2012).
CNTs have malleable strengths ranging 11–63 GPa and an ultra-high Young’s modulus of roughly 1 TPa—extraordinary mechanical qualities. The elimination of heat is currently of importance to the electronics sector as it strives to achieve higher levels of degenerative power. In order to create future generations of ICs and 3D technological devices, we must determine which materials offer the best heat transfer properties. A CNT is a man-made cylinder made from a rolled-up strip of graphene that can be either a single- or multi-well structure. CNTs with only one hole and a diameter of 0.4–3 nm are called “single-wall carbon nanotubes” (SWCNTs), whereas CNTs with multiple wells and a diameter of 0.4–30 nm are called “multi-wall carbon nanotubes” (MWCNTs). CNTs are employed in a wide variety of industries, including water purification, healthcare, nanotechnology battery production, superconductivity, electronics, recycling, transplantation, solar energy storage, and biological sensors. Using Maxwell hypothesis, Xue (2005) provided a model for thermal conduction that shows the effect of space-dispersed CNTs in a spinning tube. When the liquid heat is 25°C, the heating capacity of the CNTs-based nanofluid is enhanced by up to 30%; at 40°C, the augmentation rises to 79%. Khan (2023a) used ferro nanoparticles to examine the agnetized Williamson NF. The unsteady thermal mass transfer unmagnetized Sutterby NF was studied by Azeem Khan (2022). The radioactive impact in Eyring–Powell fluid comprising gyrotactic microorganisms was described by Khan (2023b). A computational approach was developed for thermally Eyring–Powell fluid exposed to biological convection behavior (Anjum et al., 2022). Waqas et al. (2022) studied the ferromagnetic Casson NF that comprises stratifications in bio-convection movement.
The heat transmission rates of MWCNTs suspended in filtered water across a horizontal heated tube were experimentally investigated by Amrollahi et al. (2010); for a nanotube volume fraction of 0.25%, they found a 33–40% increase in the laminar heat transmission coefficient. The thermal properties of convectional (water) CNT NF was experimentally established to be improved by 100%–250% by Rashmi et al. (2011). Thermophysical characteristics and the general efficacy of MWCNT oil-depending NF movement across helically wrapped tubes was reported by Pakdamana et al. (2012), who also noted an increase in thermal efficiency when the volume friction of suspended CNTs was 0.1%, 0.2%, or 0.4%. Heat transmission along with pressure drop of CNT-convectional (water) NF through a flat cylindrical tube using distilled water as base fluid was inspected by Wang et al. (2013). Using several types of nanoparticles, Akbar et al. (2023a) investigated the peristaltic motion of magnetized tiny fluids. The heat transfer of a magnetized elastic liquid through entropy impact was studied by Akbar et al. (2023b). Using a non-uniform structure, Maraj et al. (2023) investigated NF in peristaltic mobility. Similarly, Akbar et al. (2024) examined thermal properties in microchannels using copper and silver nanotechnology in micropolar liquid. The heat phenomenon in Eyring–Powell fluid across an extensible sheet was observed by Alghamdi et al. (2024).
The fields of biomedical science, optics, magnetic cell segregation, silk float separations, nonlinear optics, heat exhaustion, drug administration, and optical grates are a few applications of magnetic NFs, in which liquid and magnetic characteristics coexist. There has been much research into movement and heat mass transportation using magnetic NFs (Hayat et al., 2011; Chamkha and Rashad, 2014; Sudarsana Reddy and Chamkha, 2016a; Sudarsana Reddy and Chamkha, 2016b; Tasawar et al., 2015). Heatline analysis was provided by Khan et al. (2015) to investigate heat transportation using inclined heated surface containing CuO-water-based NF. Numerical analysis conducted by Selimefendigil and Oztop (2016a) on Al2O3 and CuO-water-based NF in an vertical heated cavity found that heat transportation upsurges with the volume fraction of nano-size particles. Magnetized mixed conduction heat exchange improvement of CuO-based NF over a lid-driven chamber was studied by Selimefendigil and Oztop (2016b), who discovered that the absolute magnitude of average heat transmission rises from 1 to 100 when the Richardson number grows. Heat transmission was shown to decrease with increasing Hartman number in natural porous chamber flow containing CuO NF (Miroshnichenko et al., 2016; Oztop et al., 2017).
According to Amrollahi et al. (2010), Rashmi et al. (2011), Pakdamana et al. (2012), Wang et al. (2013), and Akbar et al. (2023a), there is no research on the inspiration of radiation effect on the SWCNT and MWCNT NF flowing in an upward cone via porous media with heat source and convective boundary conditions enclosing heat mass transportation with stability analysis. This study aims to investigate the significance of SWCNTs and MWCNTs in convectional fluid (water) over a vertical cone under the influences of chemical reaction, magnetism, thermal radiation, and drenched porous media. The impact of heat is also examined. Based on the flow molds, the fundamental flow characteristics are modeled in term of partial differential equations (PDEs). Using the appropriate transformation, the PDEs are dimentionalized in terms of conventional derivatives (ordinary differential equations) and then solved via RK4 in MATLAB. The present analysis reveals the dual solution for the suction and injection parameter. Therefore, an immovability investigation is conducted to confirm which solution is stable. This study is analyzes SWCTs and MWCNTs in vertical cones with stability to establish that only the first solution is reliable. Solar systems, refinement systems, pharmaceutical materials, and thermal electrodes are the immediate applications of this analysis.
2 Mathematical analysis
Laminar flow is studied in two dimensions across a porous vertical cone containing single and multiple CNTs based on an aqueous nanofluid movement with anomalous thermal performance (Figure 1). Table 1 demonstrates the thermophysical features of the base fluid (water) and CNTs. The x-axis of the selected geometry coincides with the path of flow through the cone’s surface. The unknown temperature
The leading flow equations in the occurrence of chemical, suction, injection, radiation, porous matrix, and heat mass transfer are described in Equations 1–6 by, Amrollahi et al. (2010), Rashmi et al. (2011), Pakdamana et al. (2012), Wang et al. (2013), and Akbar et al. (2023a):
with boundary conditions
Here,
The thermal boundary conditions applied to a surface or contact in a system where convection is the primary mode of heat transmission are known as “convective boundary conditions”. The movement of a fluid and a solid surface to transfer heat is the main concern in setting a convective boundary condition. A common description of convective heat transport at a boundary is provided by Newton’s law of cooling.
Here,
Neglecting higher-order terms, we derive
By substituting Equation 8 in Equation 7, We get, Equation 9,
Thermal conductivity
Introducing the similarity transformations:
where
The corresponding boundary constraints are
Prime signifies a derivative with respect to
The physical quantities of interests are Equation 15,
3 RK4 solution and validation
The numerical solution was obtained for the modeled mathematical problem (17)–(20) via fourth-order Runge–Kutta (RK4). The first order ordinary differential equations are obtained in dimensionless form by using the new variables. The boundary conditions are transformed as well. The Prandtl number is fixed as 6.2 for the water, as the model is water-based SWCNTs and MWCNTs. The value of NVF varies 0.1–0.3 (
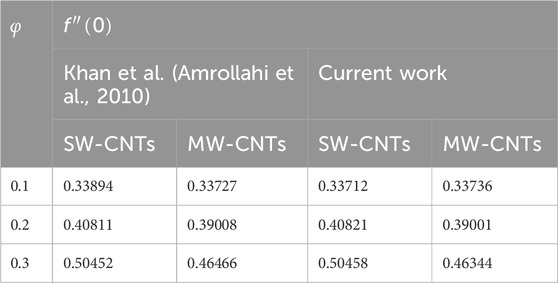
Table 2. Confirmation of the present study by comparison of
4 Stability analysis
We are here interested in obtaining the second solution for the various values of
with boundary conditions:
The new similarity transformation is defined by introducing new parameter
Using Equation 22 in Equations 17–21, we obtain
The corresponding boundary constraints are
The stability explanation is attained by the steady movement
Here,
Using Equation 27 and Equations 23–26, we obtain
The corresponding boundary constraints are
The steady state solution for
The corresponding boundary constraints are
5 Results and discussion
This study aims to investigate the impact of single-walled (SWCNTs) and multi-walled (MWCNTs) carbon nanotubes with convectional fluid (water) over a perpendicular cone beneath the influences of chemical species, magnetism, thermal radiation, and drenched permeable media. The impact of heat is also examined. Constructed on the flow norms, the fundamental flow characteristics are modeled in terms of partial differential equations (PDEs). Using the appropriate transformation, the PDEs are denationalized in terms of conventional derivatives (ordinary differential equations) and then solved via RK4 in MATLAB.
The mathematical framework given in Equations 10–13 with Equation 14 presented multiple solutions on behalf of some evolving constraints. Figure 2A demonstrates the sensations of double solutions—reliable (first solution) and unreliable (second solution). Consequently, an immovability examination is executed to determine a reliable solution. Equation 35, as well as linearized Equations 32–34, were numerically solved using RK4 MATLAB software. Figure 2A shows the lowest eigenvalues

Figure 2. (A) Smallest eigenvalues
Figures 2B and C confirm the effects of the volume fraction parameter (VFP) verses suction factor
The impact of radiation and volume fraction parameters on the Sherwood number and LSF is depicted in Figures 2D and E, respectively, along both suction and injection parameters. It is apparent that dual solutions occurred for both the Sherwood number and LSF. However, no solution exists for
We found that the VFP increased the NN in both the first and second solutions (Figure 2F). It is significant that increasing the nanoparticles’ VFP enhances heat transportation efficiency. The influence of the Biot number on the NN is demonstrated in Figure 2G. Here, in both first and second solution, the NN increases with a higher Biot number.
The distributions of velocity, temperature, and concentration of nanofluid (NF) (water base), including SWCNTs and MWCNTs, for different values of VFP are shown in Figures 3–5. In both cases, the velocity outlines decreased as VFP increased. It is important to note that for MWCNTs, the velocity of the fluid is significantly degraded in comparison to the SWCNT-water-based NFs. As VFP increases, the humidity and concentration profiles of both NFs slow. We also found that MWCNTs demonstrate greater thermal boundary layer thickness (TBLT) retardation than SWCNTs. Nevertheless, SWCNT NF experiences a significantly greater decrease in solutal boundary layer width than MWCNT NF. The impact of magnetic factor
6 Conclusion
We here examine the heat transfer behavior and chemical interactions on the movement of water-based nanofluids (NFs) including single- (SWCNT) and multiple- walled (MWCNT) carbon nanotubes (CNTs) across an upward cone inserted into a porous material under a convection boundary constraints. The system of ordinary differential equations is numerically solved via RK4. Hydrodynamic, thermal, and solutal boundary layers are studied, and the effects of varying relevant parameters are shown graphically. The present analysis reveals the dual solution for the suction and injection parameter, and stability analysis is performed to confirm which solution is stable. The aim of this study is to analyze SWCNTs and MWCNTs in a vertical cone with stability to established that only the first solution is reliable. A table presentation displays the outcomes of LSF, heat transfer rate, NN, SN, and concentration. It is found that in both nanofluids, the heat transmission rate is a growing function of
6.1 Future suggestions
This model’s usefulness is rather limited because it depends solely on a two-dimensional flow arrangement that includes conventional thermal and mass boundary circumstances. Still, the inquiry would be useful for engineering purposes if conducted in three dimensions via the passive control technique and includes a convection heating/melting heat exchange mechanism along with stability assentation.
Data availability statement
The original contributions presented in the study are included in the article/supplementary material; further inquiries can be directed to the corresponding authors.
Author contributions
HX: writing–review and editing and writing–original draft. FA: writing–review and editing and methodology. EI: writing–review and editing, supervision, and formal analysis. WK: writing–review and editing and software.
Funding
The author(s) declare financial support was received for the research, authorship, and/or publication of this article. Researchers Supporting Project number (RSPD2025R1060), King Saud University, Riyadh, Saudi Arabia.
Conflict of interest
The authors declare that the research was conducted in the absence of any commercial or financial relationships that could be construed as a potential conflict of interest.
Publisher’s note
All claims expressed in this article are solely those of the authors and do not necessarily represent those of their affiliated organizations, or those of the publisher, the editors, and the reviewers. Any product that may be evaluated in this article, or claim that may be made by its manufacturer, is not guaranteed or endorsed by the publisher.
References
Abu-Bakr, A. F., Kanagawa, T., and Abu-Nab, A. K. (2022). Analysis of doublet bubble dynamics near a rigid wall in ferroparticle nanofluids. Case Stud. Therm. Eng. 34, 102060. doi:10.1016/j.csite.2022.102060
Akbar, N. S., Akhtar, S., Maraj, E. N., Anqi, A. E., and Homod, R. Z. (2023b). Heat transfer analysis of MHD viscous fluid in a ciliated tube with entropy generation. Math. Methods Appl. Sci. 46 (10), 11495–11508. doi:10.1002/mma.7906
Akbar, N. S., Mehrizi, A. A., Rafiq, M., Habib, M. B., and Muhammad, T. (2023a). Peristaltic flow analysis of thermal engineering nano model with effective thermal conductivity of different shape nanomaterials assessing variable fluid properties. Alexandria Eng. J. 81, 395–404. doi:10.1016/j.aej.2023.09.027
Akbar, N. S., Rafiq, M., Muhammad, T., and Alghamdi, M. (2024). Electro osmotically interactive biological study of thermally stratified micropolar nanofluid flow for Copper and Silver nanoparticles in a microchannel. Sci. Rep. 14 (1), 518. doi:10.1038/s41598-023-51017-z
Alghamdi, M., Akbar, N. S., Zamir, T., and Muhammad, T. (2024). Double layered combined convective heated flow of Eyring-Powell fluid across an elevated stretched cylinder using intelligent computing approach. Case Stud. Therm. Eng. 54, 104009. doi:10.1016/j.csite.2024.104009
Amrollahi, A., Rashidi, A. M., Lotfi, R., Meibodi, M. E., and Kashefi, K. (2010). Convection heat transfer of functionalized MWNT in aqueous fluids in laminar and turbulent flow at the entrance region. Int. Commun. Heat. Mass Transf. 37, 717–723. doi:10.1016/j.icheatmasstransfer.2010.03.003
Anjum, N., Khan, W. A., Hobiny, A., Azam, M., Waqas, M., and Irfan, M. (2022). Numerical analysis for thermal performance of modified Eyring Powell nanofluid flow subject to activation energy and bioconvection dynamic. Case Stud. Therm. Eng. 39, 102427. doi:10.1016/j.csite.2022.102427
Azeem Khan, W. (2022). Impact of time-dependent heat and mass transfer phenomenon for magnetized Sutterby nanofluid flow. Waves random complex media, 1–15. doi:10.1080/17455030.2022.2140857
Buongiorno, J. (2006). Convective transport in nanofluids. Heat. Mass Transf. 128, 240–250. doi:10.1115/1.2150834
Chamkha, A. J., and Rashad, A. M. (2014). Unsteady heat and mass transfer by MHD mixed convection flow from a rotating vertical cone with chemical reaction and Soret and Dufour effects. Can. J. Chem. Eng. 92, 758–767. doi:10.1002/cjce.21894
Choi, S. U. S., and Eastman, J. A. (1995a). Enhancing thermal conductivity of fluids with nanoparticles, San Francisco. ASME Int. Mech. Eng. Congr. Expo., 12–17.
Choi, S. U. S., and Eastman, J. A. (1995b). Enhancing thermal conductivity of fluid with nanofluids.
Hayat, T., Hussain, Z., Alsaedi, A., and Hobiny, A. (2017a). Computational analysis for velocity slip and diffusion species with carbon nanotubes. Results Phys. 7, 3049–3058. doi:10.1016/j.rinp.2017.07.070
Hayat, T., Hussain, Z., Farooq, M., and Alsaedi, A. (2017b). Homogeneous and heterogeneous reactions effects in flow with Joule heating and viscous dissipation. J. Mech. 33 (1), 77–86. doi:10.1017/jmech.2016.71
Hayat, T., Qasim, M., and Mesloub, S. (2011). MHD flow and heat transfer over permeable stretching sheet with slip conditions. Int. J. Numer. Methods Fluids 66, 963–975. doi:10.1002/fld.2294
Hayat, T., Shah, F., Hussain, Z., and Al-Saedi, A. (2019). Darcy Forchheimer flow of Jeffrey nanofluid with heat generation/absorption and melting heat transfer. Therm. Sci. 23, 3833–3842. doi:10.2298/tsci171222314h
HinanS, H. T., Asghar, S., and Hendi, A. A. (2012). Influence of compliant walls on peristaltic motion with heat/mass transfer and chemical reaction. Int. J. Heat. Mass Transf. 55, 3386–3394. doi:10.1016/j.ijheatmasstransfer.2012.02.074
Hussain, Z., Bashir, Z., and Anwar, M. S. (2022). Analysis of nanofluid flow subject to velocity slip and Joule heating over a nonlinear stretching Riga plate with varying thickness. Waves Random Complex Media, 1–17. doi:10.1080/17455030.2022.2124468
Khan, A., Zaman, G., and Rahman, G. (2015). Hydromagnetic flow near a non-uniform accelerating plate in the presence of magnetic field through porous medium. J. Porous Media 18, 801–809.
Khan, W. A. (2023a). Significance of magnetized Williamson nanofluid flow for ferromagnetic nanoparticles. Waves Random Complex Media, 1–20. doi:10.1080/17455030.2023.2207390
Khan, W. A. (2023b). Dynamics of gyrotactic microorganisms for modified Eyring Powell nanofluid flow with bioconvection and nonlinear radiation aspects. Waves Random Complex Media, 1–11. doi:10.1080/17455030.2023.2168086
Khan, W. A., Waqas, M., Chammam, W., Asghar, Z., Nisar, U. A., and Abbas, S. Z. (2020a). Evaluating the characteristics of magnetic dipole for shear-thinning Williamson nanofluid with thermal radiation. Comput. Methods Programs Biomed. 191, 105396. doi:10.1016/j.cmpb.2020.105396
Khan, W. A., Waqas, M., Kadry, S., Asghar, Z., Abbas, S. Z., and Irfan, M. (2020b). On the evaluation of stratification-based entropy optimized hydromagnetic flow featuring dissipation aspect and Robin conditions. Comput. Methods Programs Biomed. 190, 105347. doi:10.1016/j.cmpb.2020.105347
Maraj, E. N., Shah, S. I., Akbar, N. S., and Muhammad, T. (2023). Thermally progressive Particle-Cu/Blood peristaltic transport with mass transfer in a Non-Uniform Wavy Channel: closed-form exact solutions. Alexandria Eng. J. 74, 453–466. doi:10.1016/j.aej.2023.05.056
Memon, A. A., Murtaza, S., Memon, M. A., Bhatti, K., Haque, M., and Ali, M. R. (2022). Simulation of thermal decomposition of Calcium Oxide in water with different activation energy and the high Reynolds number. Complexity 2022, 3877475. doi:10.1155/2022/3877475
Merkin, J. H. (1986). On dual solutions occurring in mixed convection in a porous medium. J. Eng. Math. 20, 171–179. doi:10.1007/bf00042775
Miroshnichenko, I. V., Sheremet, M. A., Oztop, H. F., and Al-Salem, K. (2016). MHD natural convection in a partially open trapezoidal cavity filled with a nanofluid. Int. J. Mech. Sci. 119, 294–302. doi:10.1016/j.ijmecsci.2016.11.001
Oztop, H. F., Sakhrieh, A., Abu-Nada, E., and Al-Salem, K. (2017). Mixed convection of MHD flow in nanofluid filled and partially heated wavy walled lid-driven enclosure. Int. Commun. Heat. Mass Transf. 86, 42–51. doi:10.1016/j.icheatmasstransfer.2017.05.011
Pakdamana, M. F., Akhavan-Behabadi, M. A., and Razi, P. (2012). An experimental investigation on thermo-physical properties and overall performance of MWCNT/heat transfer oil nanofluid flow inside vertical helically coiled tubes. Exp. Therm. Fluid Sci. 40, 103–111. doi:10.1016/j.expthermflusci.2012.02.005
Rashmi, W., Ismail, A. F., Sopyan, I., Jameel, A. T., Yusof, F., Khalid, M., et al. (2011). Stability and thermal conductivity enhancement of carbon nanotube nanofluid using gum Arabic Arabic. J. Exp. Nanosci. 6, 567–579. doi:10.1080/17458080.2010.487229
Selimefendigil, F., and Oztop, H. F. (2016a). Conjugate natural convection in a cavity with a conductive partition and filled with different nanofluids on different sides of the partition. J. Mol. Liq. 216, 67–77. doi:10.1016/j.molliq.2015.12.102
Selimefendigil, F., and Oztop, H. F. (2016b). Analysis of MHD mixed convection in a flexible walled and nanofluids filled lid-driven cavity with volumetric heat generation. Int. J. Mech. Sci 118, 113–124. doi:10.1016/j.ijmecsci.2016.09.011
Sudarsana Reddy, P., and Chamkha, A. J. (2016b). Soret and Dufour effects on MHD convective flow of Al2O3–water and TiO2–water nanofluids past a stretching sheet in porous media with heat generation/absorption with heat generation/absorption. Adv. Powder Technol. 27, 1207–1218. doi:10.1016/j.apt.2016.04.005
Sudarsana Reddy, P., and Chamkha, A. J. (2016b). Influence of size, shape, type of nanoparticles, type and temperature of the base fluid on natural convection MHD of nanofluids type and temperature of the base fluid on natural convection MHD of nanofluids. Alex. Eng. J. 55, 331–341. doi:10.1016/j.aej.2016.01.027
Tasawar, H., Rashid, M., Maria, I., and Ahmed, A. (2015). Magnetohydrodynamic (MHD) flow of Cu-water nanofluid due to a rotating disk with partial slip. AIP Adv. 5, 067169. doi:10.1063/1.4923380
Wang, J., Zhu, J., Zhang, X., and Chen, Y. (2013). Heat transfer and pressure drop of nanofluids containing carbon nanotubes in laminar flows. Exp. Therm. Fluid Sci. 44, 716–721. doi:10.1016/j.expthermflusci.2012.09.013
Waqas, M., Khan, W. A., Pasha, A. A., Islam, N., and Rahman, M. M. (2022). Dynamics of bioconvective Casson nanoliquid from a moving surface capturing gyrotactic microorganisms, magnetohydrodynamics and stratifications. Therm. Sci. Eng. Prog. 36, 101492. doi:10.1016/j.tsep.2022.101492
Weidman, P. D., Kubitschek, D. G., and Davis, A. (2006). The effect of transpiration on self-similar boundary layer flow over moving surfaces. Int. J. Eng. Sci. 44, 730–737. doi:10.1016/j.ijengsci.2006.04.005
Xuan, Y. M., and Li, Q. (2000). Heat transfer enhancement of nanofluids. Int. J. Heat. Fluid fl 21, 58–64. doi:10.1016/S0142-727X(99)00067-3
Keywords: numerical investigation, dual solution, stability analysis, nanofluid, thermal radiation, solutal boundary layer, chemical performance, heat source
Citation: Xu H, Awwad FA, Ismail EAA and Khan W (2025) Mathematical model and stability of SWCNT- and MWCNT-based nanofluid flow with thermal and chemically reactive effects inside a porous vertical cone. Front. Chem. 12:1463778. doi: 10.3389/fchem.2024.1463778
Received: 12 July 2024; Accepted: 30 September 2024;
Published: 14 January 2025.
Edited by:
Robert W. Góra, Wrocław University of Science and Technology, PolandReviewed by:
Yanping Liu, Zhejiang Ocean University, ChinaZakir Hussain, University of Baltistan, Pakistan
Copyright © 2025 Xu, Awwad, Ismail and Khan. This is an open-access article distributed under the terms of the Creative Commons Attribution License (CC BY). The use, distribution or reproduction in other forums is permitted, provided the original author(s) and the copyright owner(s) are credited and that the original publication in this journal is cited, in accordance with accepted academic practice. No use, distribution or reproduction is permitted which does not comply with these terms.
*Correspondence: Haihua Xu, eHVoYWlodWEyMDI0QDE2My5jb20=; Waris Khan, d2FyaXNraGFuNzU4QHlhaG9vLmNvbQ==)