- State Key Laboratory of Heavy Oil Processing, China University of Petroleum-Beijing at Karamay, Karamay, China
At present, the problem of global warming is becoming increasingly serious, and one of the main culprits is the increasing amount of carbon dioxide emissions. Although the traditional carbon capture technologies can reduce the concentration of CO2 in the atmosphere, it has a series of problems such as high energy consumption, high cost, low efficiency or unfriendly environment. Hydrate-based carbon dioxide separation are considered to be a technology with great application and development prospects. Compared with the traditional method of carbon dioxide separation, the hydrate method has the advantages of simple process, low energy consumption and environmental friendliness. This review introduces the advantages of hydrate method compared with traditional carbon capture technologies, expounds the theory of carbon dioxide capture by hydrate, and the strengthening and improvement techniques of hydrate method, including thermodynamic promoter, kinetic promoter and mechanical reinforcement, and introduces the practical application of hydrate method in various fields.
1 Introduction
1.1 Research background
The emission of greenhouse gases caused by human activities is the main cause of global temperature rise, and global warming seriously threatens human survival. Carbon dioxide is one of the main gases that cause the greenhouse effect. According to the statistics and predictions of the United Nations Intergovernmental Panel on Climate Change (IPPC), Carbon dioxide emissions from human activities will reach 35.8 billion tons in 2023. By 2,100, the concentration of carbon dioxide in the atmosphere may reach 570 ppm, which will cause the global average temperature to rise by about 1.9°C (Xie et al., 2019). Therefore, controlling the emission of greenhouse gases has become an urgent matter for all countries in the world. To prevent the exacerbation of the greenhouse effect, a series of clean energy sources, e.g., solar energy, wind energy, and biomass fuels, are being developed as substitutes for fossil fuels. However, these clean energy sources cannot yet replace fossil energy to meet our needs. Fossil energy will still be the main energy source for our daily life and industrial production in the future. Therefore, further research and development on carbon dioxide capture, separation and storage will be a vital method to address current development and environmental issues.
1.2 Capture of carbon dioxide
The capture of carbon dioxide refers to the process of capturing and separating carbon dioxide from the gas mixture, and then store it permanently, thereby reducing the content of carbon dioxide in the atmosphere (Li, 2014). The separation of carbon dioxide is generally divided into three categories: pre-combustion capture, post-combustion capture, and oxyfuel combustion capture. Currently, the most widely used method in industry is post-combustion. The traditional carbon dioxide capture methods mainly include physical adsorption, absorption and membrane separation technology (Madejski et al., 2022).
1.2.1 Adsorption
Gas adsorption include physical adsorption and chemical adsorption. There are two kinds of physical adsorption methods: pressure swing adsorption and temperature swing adsorption (Zhang, 2014). The main difference between the two is: one is to change the pressure, and the other is to change the temperature. Moreover, temperature swing adsorption is considered to be more suitable for post-combustion CO2 capture (Gutierrez-Ortega et al., 2022), while pressure swing adsorption is more suitable for pre-combustion CO2 capture (Abd et al., 2023). Under specific pressure and temperature conditions, solid adsorbents selectively adsorb carbon dioxide to their pores, cracks or surfaces. Common solid adsorbents include activated carbon, zeolite, etc. Activated carbon materials are low in cost and high in thermal stability. In recent years, the research on the preparation and modification of activated carbon for CO2 capture has gradually become a hot spot. Biomass activated carbon for CO2 capture mainly uses KOH as the activator. Shi and Liu (2021) synthesized two kinds of nitrogen-doped activated carbon by microwave/KOH activation and thermal/KOH activation, to separate CO2 from flue gas. By comparison, it was found that the nitrogen-doped activated carbon activated by microwave/KOH have developed pore structure and abundant active functional groups, resulting in high CO2 adsorption capacities. Owing to the strong corrosiveness, long activation time and complicated processing technology of KOH, other types of activators have been developed to replace it. Li and Xiao (2019) prepared a dual pore structure activated carbon with both micropores and mesopores from rice husk charcoal by leaching with K2CO3, and its specific surface area, micropore volume and mesopore volume were 1,097 m2/g, 0.34 cm3/g and 0.49 cm3/g respectively, showing excellent CO2 adsorption capacity and good CO2 selectivity.
The chemisorption of CO2 is achieved by forming active sites on the surface of the adsorbent to increase the selectivity of CO2 molecules (Lee et al., 2011). So far, the commonly used chemical adsorbents are amines and metal oxides. Solid amine adsorbents have the properties of excellent adsorption performance, simple regeneration process, and environmentally friendly equipment (Wang et al., 2022), and have good development prospects. However, the amine functionalization of most carriers may block the micropores, hinder the diffusion of CO2 (Figure 1), and even lead to a decrease in the pore volume and specific surface area of the adsorbent, thereby affecting the adsorption-desorption kinetics of CO2 (Yan et al., 2022). Compared with other chemical adsorbents, metal oxides have advantages in stability, low toxicity and high economic benefit (Azmi, Ruhaimi, and Aziz, 2020). Alkaline earth metal oxides, e.g., magnesium oxide and calcium oxide, are widely used in the CO2 absorption process (Khdary et al., 2022). However, since these oxides will generate some by-products during the adsorption process, the adsorption capacity of CO2 decreases greatly with the increase of cycle times (Cho et al., 2018).
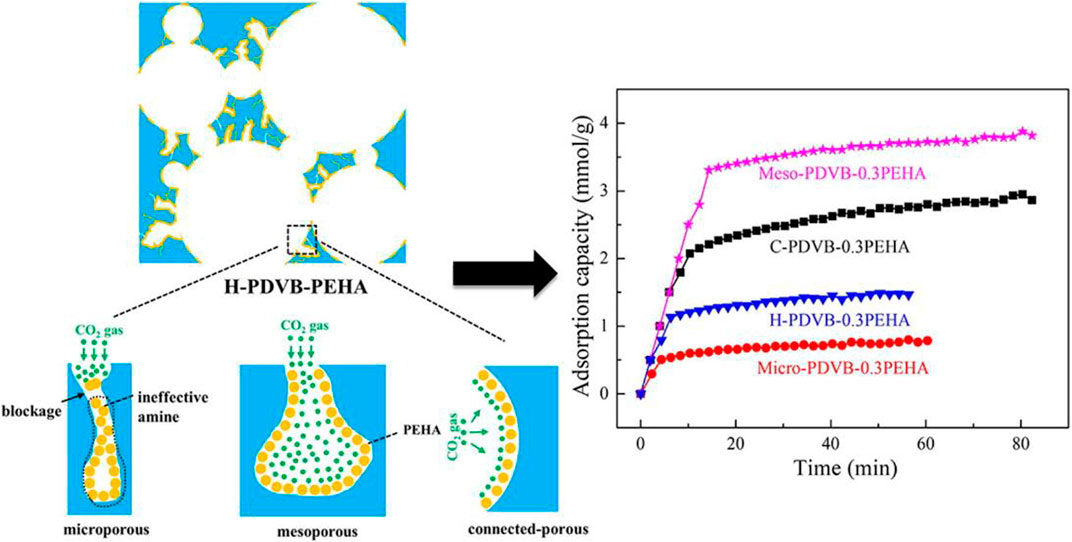
Figure 1. Diffusion of CO2 molecules in different pore structure of hierarchically porous monoliths (Lee et al., 2011).
The advantage of the adsorption method lies in the reuse of the adsorbent. But the separation of carbon dioxide by the adsorption method has higher requirements on the selectivity and capacity of the adsorbent than others, and there is also significant room for improvement in terms of separation efficiency.
1.2.2 Absorption
The absorption method is divided into biological absorption, physical absorption and chemical absorption. Bio-absorption refers to the use of plants to absorb carbon dioxide in the atmosphere through photosynthesis. The physical absorption method refers to the pressure dependent solubility of carbon dioxide in solvent, e.g., water, and methanol, to capture carbon dioxide (Zong et al., 2016). In recent years, ionic liquids with high molecular weight, deep eutectic solvents and some polymers with various functional groups have been proved to be satisfactory physical absorbents for CO2 (Li et al., 2022). Chemical absorption method refers to the use of the acidic gas properties of carbon dioxide to react with weakly alkaline liquid solvents or solid substrates to absorb and separate carbon dioxide from the gas mixture (Xiao et al., 2022). Chemical absorption could be divided into two steps (Madejski et al., 2022). In the first step, the gas mixture react with the absorbent to capture CO2. The second step is to transfer the reaction solution to the stripping tower to regenerate CO2 at high temperature (Figure 2). The advantage of the absorption method is that the solvent can be recycled and carbon dioxide gas with high purity can be obtained, but its cost is high and the solvent consumption is large. Mohamadi-Baghmolaei et al. used adsorption to remove acid gases from mixed gases (Mohamadi-Baghmolaei et al., 2021). Although good separation effect was achieved, the process energy consumption accounted for nearly half of the process cost. Changing the operating conditions and improving the process have become an urgent step for absorption method.
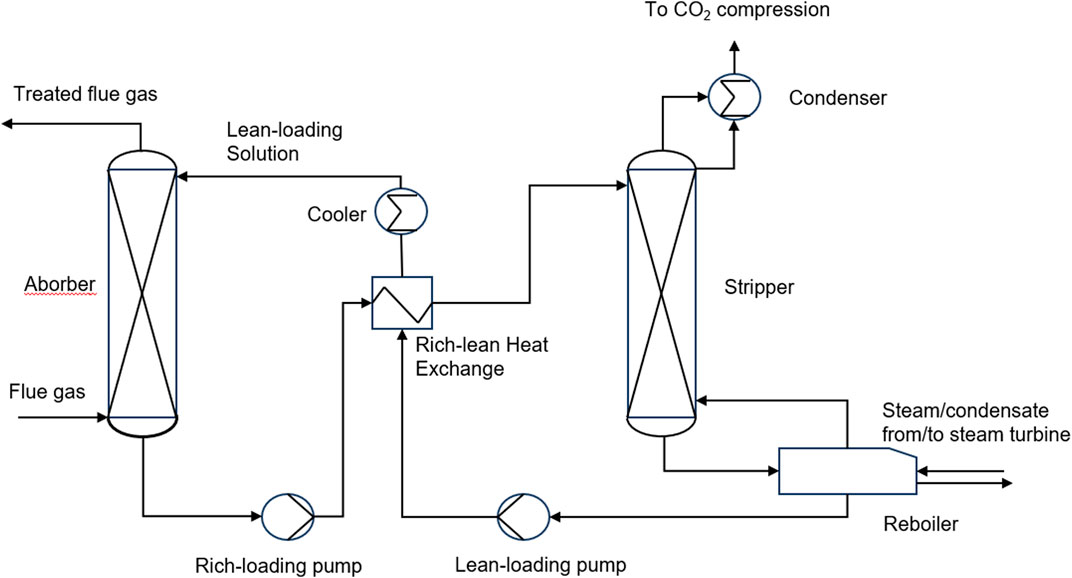
Figure 2. Schematic of a basic chemical absorption process for CO2 capture (Wang et al., 2017).
1.2.3 Cryogenic separation technology
Cryogenic separation technology is based on the difference in the phase transition properties of the components during a series of compression, cooling, and expansion processes to realize separation (Xu et al., 2012). CO2 cryogenic separation technology uses the characteristics of desublimation or condensation of each component of the mixed gas to separate liquid or solid CO2 (Figure 3). The cryogenic separation technology is relatively simple, and the separated CO2 gas has higher purity and easier to transport. Compared with other separation technologies, it is more environmentally friendly and non-corrosive. It can also remove other polluting gases e.g., sulfur oxides, mercury, and nitrogen oxides, etc. (Nandakishora, Sahoo, and Murugan, 2022) Cryogenic separation technology has a relatively mature industrial foundation and is easy to expand to industrial scale. However, the extremely low temperature, large energy consumption and high investment cost of equipment required for CO2 gas condensation process limit its development (Shen et al., 2022; Baena-Moreno et al., 2019). Zhang et al. proposed a hybrid system combining cryogenic separation carbon capture and liquid air energy storage (CS-LAES), which can increase the CO2 capture rate to 99.97%, but it still requires huge energy consumption. It can be seen that there is still a long way to go before cryogenic separation technology is widely used in industrialization (Zhang et al., 2024).
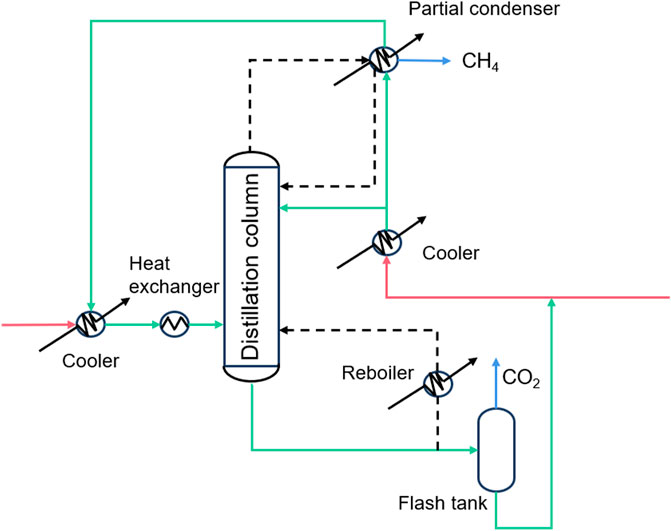
Figure 3. Schematic of cryogenic separation technology (Song et al., 2019).
1.2.4 Membrane separation technology
The membrane separation method is mainly based on the different diffusion rate and relative permeability of various gas molecules in the membrane material, so as to achieve the separation effect (Figure 4). During the membrane separation process, the pressure difference on both sides of the membrane is the driving force for gas molecules to pass through the membrane. When the pressure difference on both sides of the membrane reaches a certain value, the gas molecules with high relative permeability pass through the membrane preferentially (Guo et al., 2023) to realize the separation of gas mixture. Inorganic membranes, metal membranes, polymer membranes and solid-liquid membranes have been developed to separate CO2. The well-known gas transport mechanisms of CO2 separation membranes include the solution diffusion mechanism, enhanced transport mechanism, and molecular sieve mechanism. The separation of CO2 gas by polymer usually follows a simple solution diffusion mechanism. Because of the unique chemical structure of CO2 molecules, the reversible chemical reaction between base groups and CO2 promotes the transport of CO2 between membranes. This mechanism is called the promoted transport mechanism (Sandru et al., 2022). The molecular sieve mechanism means that the membrane material allows small molecules to pass through and intercepts large molecules. This mechanism usually exists in the transmission process of micro-porous membrane materials (Ma et al., 2020). PIM is a common gas separation membrane, which is widely used for CO2 capture in the mixed gas of coal-fired and gas-fired power plants due to its unique microporous structure (Pasichnyk et al., 2023). However, PIM is fragile and will seriously age after long-term use (Gao et al., 2021). The gas separation selectivity will also be greatly reduced. The membrane separation process is relatively simple, easy to operate, and low in energy consumption. However, the cost of membrane materials used in this process is high, and the treatment, dehydration, and filtration are usually required before the separation of carbon dioxide, and the purity of the final carbon dioxide obtained is not high.
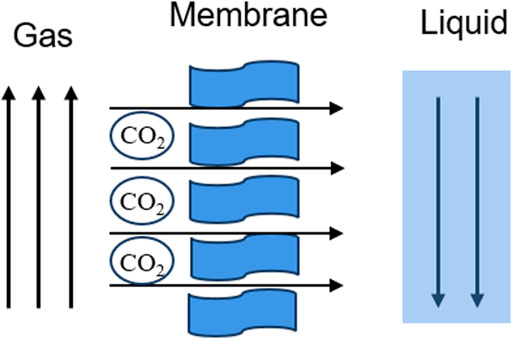
Figure 4. Schematic of membrane separation technology (Guo et al., 2023).
1.2.5 High-pressure supersonic separation technology
Supersonic separation is a physical separation method with no pollution, low energy consumption and high efficiency (Arinelli et al., 2017). The theory of this technology is that the mixed gas is cooled and condensed into droplets through a supersonic nozzle, and then a vortex generator is used to generate a vortex to push the droplets to the wall to form a liquid film (Figure 5). The liquid film will be separated from the liquid outlet, thus reducing the proportion of condensable components in the mixture (Jiang et al., 2018). This technology provides a new idea for decarbonization, and the key of the new idea is carbon condensation in supersonic nozzles. In general, the non-equilibrium condensation characteristics in supersonic expanding flows are stronger than the coupling between the flow field and CO2 condensation. In recent years, some scholars have simulated the feasibility of this method through numerical simulation and other methods. The simulation results show that this method has certain feasibility, but there is still a lack of simulation and experimental research on supercritical CO2 (Ding et al., 2023).
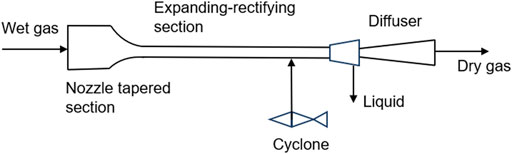
Figure 5. Structure of supersonic separator (Jiang et al., 2018).
1.2.6 Electrochemical carbon capture technology
Electrochemical carbon capture technology is a traditional carbon capture technology that emerged in the last century (Wang F et al., 2024). At present, electrochemical carbon capture technology has been widely used in various fields, mainly through redox active carriers or pH to achieve CO2 capture (alkaline) and recovery (acidic) (Zhu et al., 2023). Some active carriers, e.g., quinones, can bind and release CO2 in the redox state to achieve CO2 capture and recovery. By electrochemical carbon capture technology with controlled pH, salt or water electrolysis is used to separate alkaline and acidic solutions for CO2 absorption. Compared with other traditional methods (absorption, adsorption, etc.), electrochemical carbon capture has advantages of higher energy efficiency, flexibility and sustainability. However, it still has shortcomings of low capture rate, and it is still in the theoretical stage. With the deepening of research and the expansion of application scope, it is expected to achieve industrial application in the future (Rahimi et al., 2022).
The use of these methods to capture carbon dioxide poses numerous problems, e.g., high energy consumption, uneconomical, unfriendly environment and low purity (Table 1). Compared with the above-mentioned traditional capture processes, the hydrate capture and storage of carbon dioxide has the advantages of simple process, low cost, and environmental friendliness.
2 Hydrate-based CO2 capture and separation
2.1 Gas hydrate and the theories
Gas hydrate is a clathrate compound, which is a cage-shaped crystal formed by small gas molecules and water at a certain temperature and pressure (Figure 6). The host water molecules form cage frame structures through hydrogen bonds, and gas molecules enter the cage structure to interact with the host molecules through van der Waals force to obtain a relatively stable non-stoichiometric crystal. There are three kinds of hydrate crystal structures discovered so far, which are type I, type II and type H (Warzinski and Holder, 1998). The separation of compound gas mixture is to use different gases to form hydrates with different degrees of difficulty, so as to achieve the separation effect.
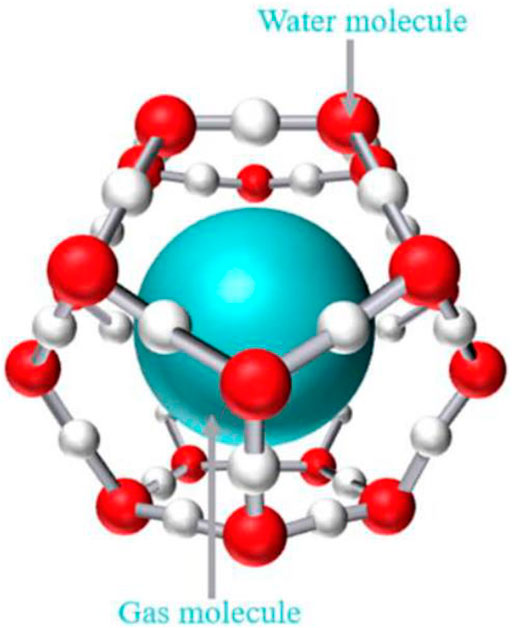
Figure 6. Schematic diagram of gas hydrate (Fu et al., 2022).
The significant advantages of hydrate based gas separation (HBGS) technology are large gas storage capacity, reversibility of hydrate formation and decomposition processes. Therefore, the hydrate based gas separation technology has been considered as a promising CO2 capture technology (Li et al., 2024). During the capture process, the CO2 molecules are small and non-polar molecules, which results in the CO2 molecules being conducive to occupying the large cage. Compared with remaining gases in the mixture, the phase equilibrium pressure of CO2 hydrate at room temperature is lower than 10 MPa (Hassanpouryouzband et al., 2020), resulting in a significantly lower formation pressure of CO2 hydrate, which makes it have a higher affinity for the occupation of suitable cages in the hydrate crystal. The pure CO2 gas can be collected by dissociating the formed CO2 hydrate cage during the release process, while the water is returned to the liquid.
2.2 Phase equilibrium conditions of gas hydrate
The thermodynamic properties of hydrates have important research value in the field of oil and gas development and utilization, and the phase equilibrium conditions of hydrates are the key factors for the formation of hydrates. In the process of petroleum development and processing, mass transfer processes between phases are common, mainly including rectification, extraction, absorption, etc. When two phases are in contact, material exchange occurs between phases until the temperature, pressure, composition and other properties of each phase no longer change, and this state is the phase equilibrium state (Guo, 2002). When the separation of gas mixture based on hydrate method is conducted, due to the difference in the affinity between different guest molecules and water, one gas is enriched in the hydrate phase, and other gases enter the gas phase, and then the gas is recovered through hydrate decomposition (Sun et al., 2023). Common thermodynamic models used to predict hydrates include vdW-P model and Chen-Guo model. The vdW-P model derives the thermodynamic model of natural gas hydrate on the basis of the Langmuir gas isotherm adsorption theory (Naghibzade et al., 2015). The Chen-Guo model proposed a two-step mechanism for the formation of gas hydrate: 1) the quasi-chemical reaction process of forming basic hydrate; 2) the adsorption process of smaller gas molecules in the linked cavities of basic hydrate (Chen and Guo, 1998). This model establishes a simpler hydrate model, and in the temperature range from 273.4 K to 290.15 K, Chen-Guo model is more accurate than vdW-P model in predicting hydrate phase equilibrium (Zhang F Y et al., 2022).
In the CO2 capture process, CO2 is usually separated from the gas mixture. For multi-component mixed systems, grasping the phase equilibrium conditions is the key factor to achieve gas separation. Lee et al. (2016) used the state equation to simulate the phase equilibrium of carbon dioxide-rich mixed gas hydrates. This method is also applicable to the mixed gases including methane, ethane, propylene and nitrogen, and can be used for the calculation of two-phase and three-phase equilibrium systems. Sun et al. (2023) studied the mixing of three impurity gases (i.e., H2S, N2O, SO2) with CO2 gas at different concentrations. By comparing the hydrate phase abundance ratio and the mole fraction of CO2, it was found that impurity gases can be effectively eliminated at low concentrations. After separation, as the concentration of impurity gas increases, the abundance ratio and mole fraction of CO2 in the hydrate phase decrease significantly, which promotes the formation of CO2 hydrate to a certain extent. When the best concentration of impurity gas is 5%. One advantage of the hydrate method for separating CO2 gas is that the obtained CO2 hydrate can be used as a method for storing CO2. To ensure that CO2 could be stably stored in the hydrate state for a long time, it is vital to investigate the phase equilibrium conditions of CO2 hydrate. Kyung et al. (2014) studied the influence of marine environmental factors on the phase equilibrium of CO2 hydrate, obtained the three-phase equilibrium of CO2 hydrate in the presence of electrolytes, soil minerals and common organic matter in the seabed environment. The change of thermodynamic equilibrium conditions provides an important reference value for the seabed storage of CO2.
2.3 Enhanced methods for gas mixture separation based on hydrate technology
2.3.1 Gas hydration separation in pure water system
The research of separating various gas mixtures based on hydrate phase equilibrium principle has been relatively mature. As early as 2006, Park et al. (2006) measured the hydrate phase equilibrium of CO2-N2-H2O ternary system in silica gel pores. As shown in Figure 7 (Park et al., 2006), at a specific temperature, the H-Lw-V three-phase equilibrium curve moves to high pressure with the decrease of CO2 concentration in gas phase. Solid-state nuclear magnetic resonance spectrum shows that the mixed hydrate structure is SI type, and CO2 molecules mainly occupy 51,262 cages. After three cycles of hydrate formation and dissociation, the CO2 concentration in the product can be as high as 96%. In 2016, Wang et al. (2016) studied the multistage separation of CH4/CO2 gas mixture based on hydrate method, which was carried out under different initial pressures. When the initial pressure is 4, 5 and 6 MPa, the proportion of CH4 increases from 72.24% to 97.22% and 97.14% after 4, 5 and 7 stage separation, respectively. The above research have confirmed the feasibility of gas mixture separation by hydrate method. However, the high operating pressure and low temperature seriously hindered the industrial development of this technology.
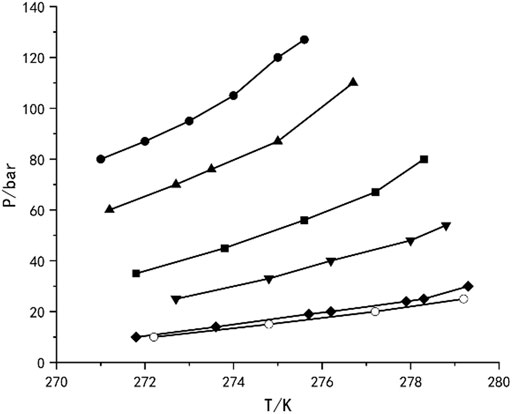
Figure 7. Hyrate phase equilibria for ternary N2+CO2+H2O mixturs of various CO2 compositions in 30.0 nm silica gel pores,and pure CO2+H2O mixture in bulk water:10 mol% CO2(●), 17 mol% CO2(▲), 35 mol% CO2(■), 50 mol% CO2(▼), 100 mol% CO2(◆), and 100 mol% CO2 in bulk water (○).
Different from pure component gases, the phase equilibrium of the mixed system is greatly affected by the gas composition, especially the mixed system containing CO2 (Nguyen et al., 2022). CO2 is easily soluble in water, and the composition in the equilibrium state is actually lower than the composition of the raw gas. The water-to-gas molar ratio affects the hydrate phase equilibrium by affecting the equilibrium gas composition, thereby affecting gas separation. Hydrate formation kinetics and separation efficiency are also one of the key factors in gas separation, which are directly related to the efficiency of HBGS process (Kim and Sa, 2023). In addition, the hydrate method also faces the problems of how to decrease energy consumption and improve separation selectivity, hydration rate, efficiency and hydrate stability. Recent years, researchers have studied the mechanical and chemical additives methods to enhance hydrate technology, and have achieved some success (Table 2).
2.3.2 Strengthening hydrate technology with chemical additives
2.3.2.1 Kinetic promoter
There are two main ways to strengthen hydrate technology: kinetic strengthening and thermodynamic strengthening. Both of them strengthen hydration technology by increasing the dynamic and thermodynamic differences between different gas molecules. The greater the difference has, the better the separation effect. Kinetic enhancement is achieved by increasing the difference of hydration rate and induction time between guest molecules. In the current hydrate research experiments, kinetic enhancement is generally achieved by adding kinetic promoters. There are various chemical reagents that can be used as kinetic hydrate promoters, e.g., some amino acid and surfactants, which can form micelles with solubilization in aqueous solution and promote separation. Zhang G et al. (2022) studied the capture of CO2 by different kinds of amino acid aqueous solutions through microchannel mass transfer, and found that all kinds of amino acid salt solutions have good capture effect on CO2, with sodium glycine aqueous solution has the best capture effect. Deng et al. (2023) added fluorinated graphene with superhydrophobic nanostructure and surfactant sodium dodecyl sulfate (SDS) into the aqueous solution to promote the formation of CO2 hydrate. The results shows that graphene with superhydrophobic nanostructure can effectively promote the nucleation of CO2 hydrate and realize the continuous growth of hydrate. SDS can excellently improve the gas-liquid mass transfer efficiency and promote the dissolution of CO2. Liu et al. (2022) compared the promoting effect of SDS and L-methionine (L-Met) on CO2 hydrate formation and found that L-Met (0.1 wt%) promoted CO2 hydrates formation significantly with a gas uptake in CO2 hydrate five times more than SDS at the same concentration. The combination of fluorinated graphene and SDS greatly promotes the carbon storage performance of hydrate. In addition to the above two kinds of common kinetic promoters, graphene oxide (GO) has been studied in CO2 hydrate formation as the new kinetic promoter. Wang Y J et al. (2024) investigated the significant role of graphene oxide (GO) in enhancing the dynamic behaviors of post-combustion CO2 via the hydrate formation and found that the induction of GO increased the amount of gas transfer, and shortened the induction time for the hydrate nucleation at the gas-liquid interface. In the latest research, researchers tried to combine kinetic promoters with other additives, which can not only effectively promote hydrate formation and improve gas separation efficiency, but also make up for the shortcomings of traditional single kinetic promoters. Li et al. proposed an innovative idea of coupling Mg with amino acids to promote the formation of CO2 hydrate (Li et al., 2024). Experiments verified that the corrosion of Mg assisted hydrate nucleation, greatly shortened the time of CO2 hydrate nucleation, and proved that this method of promoting hydrate formation by coupling Mg with amino acids can also be applied to flue gas separation and hydrogen storage. Liu et al. tried to combine L-methionine, an environmentally friendly kinetic promoter, with low-dose tetrahydrofuran (THF), a thermodynamic promoter, and confirmed the synergistic mechanism of the coupling of kinetic and thermodynamic promoters in the process of CO2 hydrate formation, which provides guidance for the development of new environmentally friendly promoters (Liu et al., 2023).
2.3.2.2 Thermodynamic promoter
Thermodynamic enhancement is achieved by temperature, pressure and other aspects. Thermodynamic promoters (e.g., THF (tetrahydrofuran), TBAB (tetra-n-butyl ammonium bromide), CP (cyclopentane), etc.) are usually added to enhance the separation effect by increasing the phase equilibrium difference between different gases (Zheng et al., 2019). Figure 8 (Majid et al., 2021) is a graph of hydrate equilibrium movement caused by adding thermodynamic hydrate inhibitor and promoter. The hydrate equilibrium curve depends on the gas composition and the promoter concentration. Promoter molecules participate in hydrate formation and are trapped by hydrate cages at low or high pressure, thus reducing the equilibrium conditions for hydrate formation. Yang et al. (2017) carried out the formation and dissociation characteristics of CO2/N2 hydrate under the condition of 19% THF, and found that 19% THF can promote hydrate formation by increasing hydrate formation rate and reducing equilibrium conditions. This discovery also confirmed that adding hydrate thermodynamic promoter makes hydrate formation conditions milder. Hydrate thermodynamic promoter can moderate the pressure condition as well as the temperature condition of hydrate formation. Zhou et al. (2018) measured the phase equilibrium conditions of CO2 hydrate formation with the TBAB concentration of 0.1–4.0 mol% at the pressure of 1.4–4.5 MPa. The results showed that when TBAB was added, the equilibrium temperature at constant pressure shifts 1–14 K to a milder condition. Since the thermodynamic promoter is directly involved in Yu et al. (2020) hydrate formation, many kinds of hydrates will be formed when separating the gas mixture. Yu et al. analyzed the separation effect of CP with different volume concentrations and gas-liquid ratios on CO2 in coal gasification combined cycle syngas, and the highest recovery ratio of CO2 was 98.8%. Meanwhile, the development of new separation technology based on the thermodynamic characteristics of hydrate has also been a hot research topic in recent years. Chen J L et al. (2020) proposed a new method of hydrate thermal-mass coupling, which uses the enthalpy of formation and dissociation of TBTA (tert-butyl trichloroacetylidene ester)/CO2 hydrate to reduce the energy consumption of CO2 separation, and explores the continuous separation of CO2, thus solving the problem of difficult heat transfer in gas-liquid mixed system in the traditional hydrate separation process.
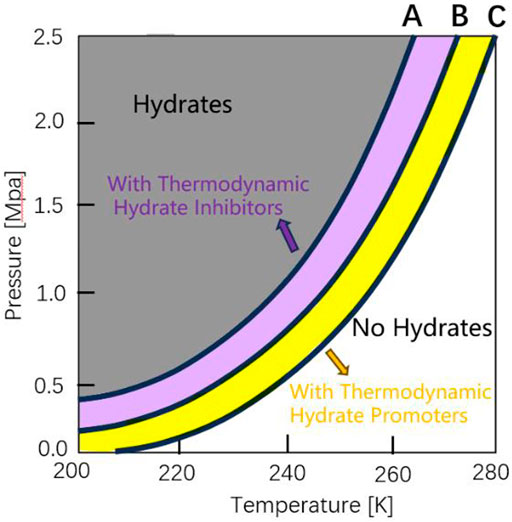
Figure 8. Example of hydrate equilibrium no THI/THP, curve (B) shift as a result of the addition of thermodynamic hydrate inhibitors (THIs, curve (A) or thermodynamic hydrate promoters (THPs, curve (C).
2.3.2.3 Nanoparticle additives
Besides the thermodynamic and kinetic additives mentioned above, nanoparticles can also promote the formation of hydrate. Nanoparticles have good thermal conductivity, and can promote to mass transfer by enhancing gas-liquid disturbance during hydrate formation (Cheng et al., 2021). In addition, the high specific surface area of nano-materials can reduce the surface tension of gas-liquid interface, increase the dissolution rate of CO2 and promote the formation of hydrate (Nashed et al., 2018). Khanmohammadian et al. (Khanmohammadian et al., 2023) used silica nanoparticles as promoter to separate CO2 from CO2/CH4 mixed gas in the presence of potassium hydroxide. The research shows that silica nanoparticles can promote the consumption, separation and recovery of mixed gas. Besides nonmetallic nanoparticles, metal nano-particles can also be used as hydrate promoters. Said et al. (2020) prepared an aluminum nano-fluid for CO2-CH4 hydrate formation process. The results showed that the added aluminum nano-particles can enhance gas dissolution and promote hydrate formation, and the best gas capture effect could be achieved at 0.3 wt%.
2.3.3 Mechanical reinforcement
In addition to the chemical promotion methods mentioned above, there are also physical promotion methods during the hydrate formation process, namely, mechanical reinforcement, including stirring, bubbling and spraying.
2.3.3.1 Stirring
Stirring is the most common mechanical promotion method. In the stirred system, the gas-liquid contact area is greatly increased, which makes the hydrate formation rate improve rapidly. As early as 2007, Hao et al. (2007) compared the temperature and reaction rate of methane hydrate synthesis with or without stirrer, and confirmed that intermittent stirring can enhance the heat and mass transfer performance of hydrate compound form process, effectively shorten the hydrate induction time. The suitable stirring speed at 5 MPa pressure is 320 rpm and the stirring time is 30 min, which provides a reference idea for further improving the storage capacity and formation rate of hydration process. However, with the formation of hydrate, the viscosity of slurry increases, which hinders the rotation of the stirring paddle (Fidel-Dufour et al., 2006). In the experiment of Linga et al. (2012) the hydrate in the stirring tank grew rapidly in the first 3 hours. And with the increase of hydrate amount, mixing becomes more and more difficult. The reaction stops after 60 h, and the final hydrate conversion ratio is only 74%. In order to solve this problem, in recent years, a new mechanical method, i.e., reciprocating impact method, has been developed. Reciprocating impact can make hydrate grow multiple times, promote the hydrate formation rate, and improve gas absorption amount. Xiao et al. (2018) used reciprocating impact instead of traditional stirring to promote hydrate formation by continuously impacting hydrate blocks with high pore moisture content, as shown in Figure 9. In the reciprocating impingement reactor, the water conversion ratio reaches more than 80% within 4 h, which is much higher than that of conventional stirring.
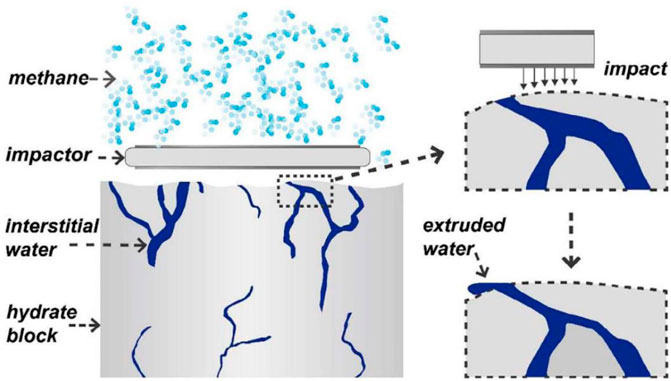
Figure 9. Sketch diagram of extruding interstitial water by reciprocating impact after bulk hydrate has formed.
2.3.3.2 Bubbling
Bubble column is a traditional industrial reactor used in gas-liquid reaction system. In industry, multi-stage separation of gas mixture is usually achieved by utilizing the countercurrent flow between gas and slurry in a bubble tower and the continuous updating of the gas-liquid contact interface. Lv et al. (2012) developed a large bubble column reactor in the industrial production of methane hydrate and the reactor has the following three characteristics. First, it does not need water circulation and saves the energy consumed by pumping water. Second, the gas is automatically introduced into water under the action of pressure difference. Last but not least, bubbles rise for a long time in the liquid phase, and hydrate is almost completely formed. The bubble column reactor effectively increases the gas-liquid contact area and significantly improves heat and mass transfer (Lang et al., 2010). Due to the movement of bubbles, the formation rate of hydrate on its surface is relatively high, the generated hydrate shell is not easy to break, and bubbles with hydrate shell cannot merge into large bubbles, which hinders the further formation of hydrate (Luo et al., 2007). According to this, Kar and Bahadur (2023) simulated the formation process of CO2 hydrate in bubble column, and the results are shown in Figure 10. Bubbles with diameter less than 100 μm were the key to improve the growth rate of hydrate, and increasing the reactor pressure could further improve the maximum theoretical separation efficiency of gas mixture.
2.3.3.3 Spraying
Spray reactor is another common reactor for gas-liquid reaction system, which increases the gas-liquid contact area by spraying water into the continuous gas phase region (Rehman and Lal, 2022). Without stirring device, the tiny droplets move at a high speed under high pressure jet and react with gas molecules to form hydrate. Murakami et al. (2009) carried out laboratory experiments on hydrate formation by using jet impingement device, which proved for the first time that jet device could be used in hydrate formation process. However, due to the existence of pressure difference, hydrate particles will grow in the gas flow loop, resulting in pipeline blockage. Li et al. (2010) explored the factors of rapid formation of CO2 hydrate in spray device, and found that higher initial pressure, i.e., driving force of nozzle, is favorable for promote the formation of hydrate, boost hydrate particles changing from spherical to branched shapes, and the circulating water pipeline will not be blocked by spraying small hydrate particles into gas phase. But with the increase of driving force, the total heat produced by hydrate formation will also increase. In order to overcome the problem of rapid increase in temperature in the spray reactor caused by heat release during hydrate formation, Partoon et al. (2018) were inspired by the direct contact heat exchanger, improved the design of nozzle and added quenching pipeline in the spray reactor to alleviate the unstable heat distribution in the reactor, and higher heat transfer rate can be achieved by the direct contact between heat flow and cold flow (Figure 11).
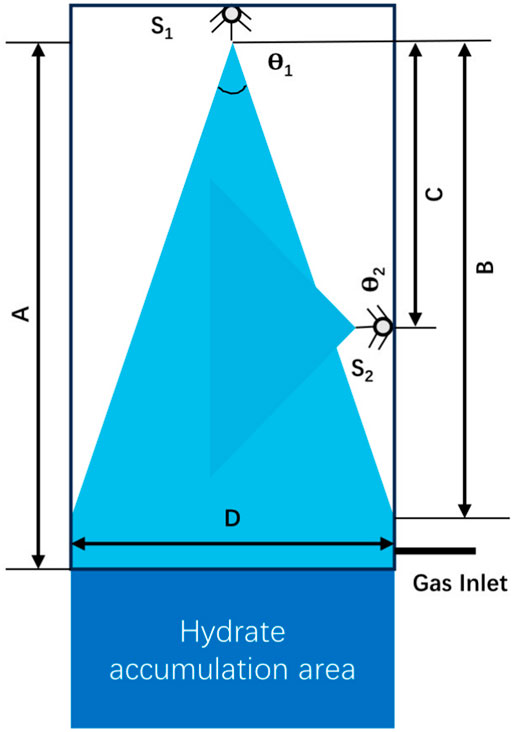
Figure 11. The geometry of main and quench spray nozzles. S1: Main spray nozzle with θ1 narrow spray angle, S2: Quench spray nozzle with θ2 wide spray angles, A: Gas dominate length, B: No wall contact length, C: Quench distance from main spray.
2.3.4 Hydrate membrane technology
Hydrate membrane technology is a new type of gas separation technology, which uses the different permeability of different gas molecules through the membrane to separate gases. The driving force for gas passing through hydrate membrane mainly comes from the pressure difference between the two sides of the membrane. The newly developed hydrate membrane technology directly uses aqueous solution itself to form films. Substances, e.g., cyclopentane (CP) and tetrahydrofuran (THF), can form hydrate without the participation of gas molecules when the temperature of their aqueous solution is higher than zero degrees Celsius. Compared with the previous membrane technology, it greatly speeds up the formation rate of hydrates, increases the effective area of the membrane, and improves the separation efficiency. In addition, cyclopentane and other chemical substances can form membranes under normal pressure, which reduces the energy consumption in the experimental process. Fan et al. (2020) introduced membrane separation technology on the basis of hydrate separation of carbon dioxide, and used porous media on the membrane to adsorb carbon dioxide, which greatly improved the capture rate of carbon dioxide gas. Zhang Y Q et al. (2022) separated H2 by using different diffusion rates of mixed gas components through THF hydrate membrane. The experimental results show that only H2 can pass through the clathrate hydrate membrane with the thickness of 5 mm, while CH4 and CO2 in the gas mixture are prevented.
3 Application of hydrate method to capture carbon dioxide
Carbon dioxide is an easily hydrated gas. When mixed with other gases, it can be captured by hydrate. Separation of carbon dioxide by hydrate method is mainly divided into two steps: 1) first, carbon dioxide enters the cage structure of water molecules under high pressure and low temperature to form hydrate; 2) the formed cage hydrate structure is broken at low pressure and high temperature, and carbon dioxide is released, thus realizing separation. During the above operation, other gases which are not easy to be captured by the cage structure of water molecules are separated after the end of the first process. At present, several kinds of gas mixture involved in the field of CO2 separation and capture mainly include natural gas mainly composed of CO2/CH4, syngas tail gas mainly composed of CO2/H2 and flue gas mainly composed of CO2/N2. Due to the difference of composition and properties of the gas mixture, separation conditions of CO2 by hydrate method are also different. In natural gas CH4/CO2, the hydration pressure of the difficult-to-hydrate gas CH4 is twice as high as that of the easily-hydrated gas CO2 at 273.15 K. In the syngas tail gas (H2/CO2 gas mixture), the hydration pressure of the difficult-to-hydrate gas H2 is 200 times that of the easily-hydrated gas CO2 at 273.15 K. And in the flue gas mainly composed of N2/CO2, the hydration pressure of difficult-to-hydrate gas N2 is 12 times that of easily-hydrated gas CO2 at 273.15 K (Chen Z et al., 2020). Hydrate formation pressure of different gases at 273 K are shown in Table 3 (Wang et al., 2013).
3.1 Capture of carbon dioxide from natural gas
CH4 hydrate is usually synthesized at high pressure and low temperature, which the formation pressure is much higher than that of CO2 hydrate. According to this property, CO2 in natural gas can be separated. Gambelli et al. (2019) analyzed the hydrate method for separating natural gas and synthesized CH4 hydrate and CO2 hydrate at different pressures, and obtained hydrates with extremely high yields, which confirmed the feasibility of CO2/CH4 gas separation by using the hydrate method. As early as 2009, some scholars studied the subject of purifying natural gas by hydrate method. The results showed that the CO2 content was reduced from 25% to 16%, which confirmed that gas hydrate method can be used to purify natural gas (Van Denderen et al., 2009). However, this process of separating CO2/CH4 gas mixture by hydrate crystallization is very difficult. To solve this problem, Ricaurte et al. (2013) studied the influence of additives on hydrate formation, and found that when THF and SDS were mixed, the hydrate formation rate was the highest. In recent years, the research on CO2 storage mainly focuses on replacing the natural gas hydrate in the seabed with CO2. When carbon dioxide gas is injected into natural gas reservoir and reacts with methane, it can not only obtain a large amount of methane gas, but also store carbon dioxide gas stably for a long time. The disadvantage of this method is that usually takes a long time and consumes a lot of energy, and further improvement is needed in the follow-up development.
3.2 Capture of carbon dioxide from the tail gas of synthetic gas
Synthesis gas is a common intermediate raw gas in the processes of chemical industry, which is usually produced under high pressure. Its main components are H2, CO, CH4 and CO2. Under normal pressure, H2 hydrate require extremely low temperature to maintain a stable state (Mao et al., 2002). Compared with H2 hydrate, the formation conditions of CO2 hydrate are milder. The addition of hydrate promoters is usually employed to realize the high selectivity of H2O/CO2 gas mixture. Research has found that the clathrate hydrates constructed by tetra-n-butylammonium bromide (TBAB) and H2O molecules can capture gas molecules. The small hydrate cages constructed by the anions of TBAB solution capture small molecular gas, while the cations enters the large cages (Shimada et al., 2003). Cai et al. (2023) established a prediction model for the thermodynamic conditions of hydrate formation in the TBAB-containing aqueous solution system, and carried out experimental verification. The predicted value obtained were in good consistency with the experimental data, providing a theoretical basis for gas separation. Fukumoto et al. (2015) studied the dissociation conditions of H2 + CO2 smiclathrate hydrate formed with TBAB, TBAC, TBAF, TBPB, and TBNO3 salts, and found that CO2/H2 gas mixture could reach a high selectivity under the condition of moderate salt concentration.
3.3 Capture of carbon dioxide from flue gas
The flue gas generated by the combustion of fossil fuels contains a large amount of CO2 gas. It is reported that the CO2 emitted by power plants accounts for about 41% of the global CO2 emissions (Khatib, 2012). One of the important ways to achieve the carbon peaking is to capture CO2 from flue gas. The pressure difference between CO2 and N2 to form hydrate is much smaller than that between CO2 and H2. Theoretically, it is not difficult to capture CO2 from flue gas (Wang et al., 2013). The separation of CO2 gas from the flue gas based on the hydrate method has become a highly promising technology at present, and the capture ratio of this separation process has been verified to reach 99% (Mondal et al., 2012). However, to achieve industrialization, it is necessary to solve the problem of huge operating costs caused by compressing the gas to a pressure that forms hydrates. Hassanpouryouzband et al. (2019) proposed a new method for capturing CO2, injecting flue gas directly into water-bearing or ice-bearing sediments, integrating CO2 capture into a simple process, and significantly reducing the cost of carbon capture and storage. The CO2 efficiency of this method can reach 92% under certain conditions, which proves the feasibility of the hydrate method to capture CO2 gas from flue gas. Since the formation conditions of N2 hydrate are more severe than CO2 hydrate, a new technology of simulation has been developed, which is usually used to imitate the hydrate formation process to obtain the detailed requirements of hydrate formation (Lu et al., 2022). Kan et al. (2021) developed a new numerical simulation method, investigating the technology of injecting CO2/N2 into the actual permafrost hydrate reservoir to realize natural gas collection and CO2 sequestration by continuous injection-production model. The relationship between the storage rate and the CO2 content and pressure in the injected gas provides a basis for the practical application of CO2 storage and natural gas extraction. Zhang G et al. (2022) simulated the effects of different concentrations of dodecyl ammonium chloride (DTAC) solutions on the formation of CO2/N2 hydrate. Based on the simulation results, the higher the concentration of DTAC, the faster the hydrate formation rate, which lay a foundation for improving the carbon capture kinetics and separation performance based on hydrate.
3.4 Carbon capture and desalination
In recent years, with the continuous growth of the world population, the shortage of water resources and the high concentration of CO2 in the atmosphere have increasingly become a “double crisis” with great threat worldwide (Gautam et al., 2022). Carbon capture and seawater desalination based on hydrate have emerged as the times require. Industrially produced CO2 gas and seawater are injected into the hydrate reactor together. Under certain temperature and pressure conditions, water molecules form a cage structure around the CO2 molecules to generate hydrates. The hydrate dissociates under certain conditions to obtain CO2 gas and freshwater (Babu et al., 2020). However, factors such as the slow kinetics of hydrate formation have hindered the development of this technology. Gautam et al. found that salinity can inhibit the formation of hydrates, and adding thermodynamic promoters to the system can effectively increase the rate of hydrate formation (Gautam et al., 2022). This discovery provides a new insight for integrated carbon capture and seawater desalination of hydrates. Abulkhair et al. experimentally studied the effect of CO2-containing mixed gas hydrate formation on seawater desalination (Abulkhair et al., 2023). The results showed that the mixed gas hydrate formation can be used to treat produced water with low energy consumption according to the water recovery rate, removal efficiency, conductivity and other results. Montazeri et al. proposed the use of CO2 nanobubbles (NBs) as a sustainable kinetic promoter for the hydrate desalination process (Montazeri et al., 2024). The results confirmed that the memory effect of CO2 NBs played an important role in the desalination and effectively improved the desalination rate and ion removal rate, have provided ideas for further development of seawater desalination with natural salt solutions. These studies have shown that hydrate carbon capture and seawater desalination technology has broad application prospects. However, this technology still has problems such as high energy consumption and high cost. If it is to be applied to large-scale industrialization, it still needs to overcome some challenges.
4 Conclusion and prospect
In this paper, several common methods of CO2 capture are summarized, among which the capture of CO2 based on hydrate has become a promising technology because of its low cost and environmental friendliness. Moreover, we review the effect of various hydrate promoters on the hydrate formation process, e.g., kinetic promoters, thermodynamic promoters and nanoparticle additives. The reaction device is also crucial to the capture of CO2 based on hydrate method. Stirring, bubbling and spraying can promote hydrate formation. CO2 capture in industry is mainly carried out from three aspects: natural gas, syngas tail gas and flue gas. With the further implementation of the carbon emission policy, the study of capturing carbon dioxide will continue to intensify in the future. While reducing carbon dioxide emissions from the source, finding a simpler, more economical and environmentally friendly method of capturing CO2 requires researchers to invest more efforts. It is believed that with the improvement of science and technology, the problem of CO2 capture will eventually be properly solved.
Author contributions
JP: Writing–original draft. JC: Writing–review and editing. JW: Writing–review and editing. ZL: Funding acquisition, Supervision, Writing–review and editing. NL: Funding acquisition, Supervision, Writing–review and editing. JK: Writing–review and editing.
Funding
The author(s) declare that financial support was received for the research, authorship, and/or publication of this article. Financial support from the Research Foundation of China University of Petroleum-Beijing at Karamay (XQZX20230017), “Tianchi Talent” Recruitment Program, Karamay Science and Technology Plan Project (20222023hjcxrc0008), CNPC Innovation Found (2023DQ02-0503), National Natural Science Foundation of China (52204061), Xinjiang Tianshan Innovation Team (2022TSYCTD0002), Xinjiang Uygur Region“One Case, One Policy” Strategic Talent Introduction Project (XQZX20240054) are gratefully acknowledged.
Conflict of interest
The authors declare that the research was conducted in the absence of any commercial or financial relationships that could be construed as a potential conflict of interest.
Publisher’s note
All claims expressed in this article are solely those of the authors and do not necessarily represent those of their affiliated organizations, or those of the publisher, the editors and the reviewers. Any product that may be evaluated in this article, or claim that may be made by its manufacturer, is not guaranteed or endorsed by the publisher.
References
Abd, A. A., Othman, M. R., Shamsudin, I. K., Helwani, Z., and Idris, I. (2023). Biogas upgrading to natural gas pipeline quality using pressure swing adsorption for CO2 separation over UiO-66: experimental and dynamic modelling assessment. Chem. Eng. J. 453, 139774. doi:10.1016/j.cej.2022.139774
Abulkhair, H., Nallakukkala, S. I., Moujdin, A., Almatrafi, E., Bamaga, O., Alsaiari, A., et al. (2023). Desalination of produced water via CO2 + C3H8 hydrate formation. Sep. Purif. Technol. 315, 123711. doi:10.1016/j.seppur.2023.123711
Arinelli, L. O., Trotta, T. A. F., Teixeira, A. M., De Medeiros, J. L., and Araújo, O. Q. F. (2017). Offshore processing of CO2 rich natural gas with supersonic separator versus conventional routes. J. Nat. Gas. Sci. Eng. 46, 199–221. doi:10.1016/j.jngse.2017.07.010
Azmi, A. A., Ruhaimi, A. H., and Aziz, M. A. A. (2020). Efficient 3-aminopropyltrimethoxysilane functionalised mesoporous ceria nanoparticles for CO2 capture. Mater. Today Chem. 16, 100273. doi:10.1016/j.mtchem.2020.100273
Babu, P., Nambiar, A., Chong, Z. R., Daraboina, N., Albeirutty, M., Bamaga, O. A., et al. (2020). Hydrate-based desalination (HyDesal) process employing a novel prototype design. Chem. Eng. Sci. 218, 115563. doi:10.1016/j.ces.2020.115563
Baena-Moreno, F. M., Rodriguez-Galan, M., Vega, F., Vilches, L. F., Navarrete, B., and Zhang, Z. E. (2019). Biogas upgrading by cryogenic techniques. Environ. Chem. Lett. 17 (3), 1251–1261. doi:10.1007/s10311-019-00872-2
Cai, J., Wang, X., Tang, H., Chen, G., and Sun, C. (2023). Prediction of the phase equilibrium of semi-clathrate hydrate in TBAB aqueous solution. J. Chem. Ind. Eng. 74 (01), 408–415. doi:10.11949/0438-1157.20221178
Chen, G. J., and Guo, T. M. (1998). A new approach to gas hydrate modelling. Chem. Eng. J. 71 (2), 145–151. doi:10.1016/S1385-8947(98)00126-0
Chen, J. L., Xiao, P., Zhang, D. X., Chen, G. J., Sun, C. Y., Ma, Q. L., et al. (2020). Adsorption-Hydration sequence method for methane storage in porous material slurry. Front. Chem. 8, 294. doi:10.3389/fchem.2020.00294
Chen, Z., Fang, J., Xu, C., Xia, Z., Yan, K., and Li, X. (2020). Carbon dioxide hydrate separation from Integrated Gasification Combined Cycle (IGCC) syngas by a novel hydrate heat-mass coupling method. Energy 199, 117420. doi:10.1016/j.energy.2020.117420
Cheng, Z., Xu, H., Wang, S., Liu, W., Li, Y., Jiang, L., et al. (2021). Effect of nanoparticles as a substitute for kinetic additives on the hydrate-based CO2 capture. Chem. Eng. J. 424, 130329. doi:10.1016/j.cej.2021.130329
Cho, M. S., Lee, S. C., Chae, H. J., Kwon, Y. M., Lee, J. B., and Kim, J. C. (2018). Characterization of new potassium-based solid sorbents prepared using metal silicates for post-combustion CO2 capture. Process Saf. Environ. 117, 296–306. doi:10.1016/j.psep.2018.05.010
Deng, Z., Fan, S., Wang, Y., Lang, X., Li, G., Liu, F., et al. (2023). High storage capacity and high formation rate of carbon dioxide hydrates via super-hydrophobic fluorinated graphenes. Energy 264, 126045. doi:10.1016/j.energy.2022.126045
Ding, H., Zhang, Y., Dong, Y., Wen, C., and Yang, Y. (2023). High-pressure supersonic carbon dioxide (CO2) separation benefiting Carbon Capture, Utilisation and Storage (CCUS) technology. Appl. Energy 339, 120975. doi:10.1016/j.apenergy.2023.120975
Fan, S., You, L., Lang, X., Wang, Ya., Li, W., Liu, Y., et al. (2020). Separation and capture carbon dioxide by clathrate-hydrate membranes: a review. Huagong Jinzhan 39 (04), 1211–1218. doi:10.16085/j.issn.1000-6613.2019-1292
Fidel-Dufour, A., Gruy, F., and Herri, J. (2006). Rheology of methane hydrate slurries during their crystallization in a water in dodecane emulsion under flowing. Chem. Eng. Sci. 61 (2), 505–515. doi:10.1016/j.ces.2005.07.001
Fu, L., Ren, Z., Si, W., Ma, Q., Huang, W., Liao, K., et al. (2022). Research progress on CO2 capture and utilization technology. J. CO2 Util. 66, 102260. doi:10.1016/j.jcou.2022.102260
Fukumoto, A., Sales Silva, L. P., Paricaud, P., Dalmazzone, D., and Fürst, W. (2015). Modeling of the dissociation conditions of H2 + CO2 semiclathrate hydrate formed with TBAB, TBAC, TBAF, TBPB, and TBNO3 salts. Application to CO2 capture from syngas. Int. J. Hydrogen Energy 40 (30), 9254–9266. doi:10.1016/j.ijhydene.2015.05.139
Gambelli, A. M., Castellani, B., Nicolini, A., and Rossi, F. (2019). Gas hydrate formation as a strategy for CH4/CO2 separation: experimental study on gaseous mixtures produced via Sabatier reaction. J. Nat. Gas. Sci. Eng. 71, 102985. doi:10.1016/j.jngse.2019.102985
Gao, Z., Wang, Y., Wu, H., Ren, Y., Guo, Z., Liang, X., et al. (2021). Surface functionalization of Polymers of Intrinsic Microporosity (PIMs) membrane by polyphenol for efficient CO2 separation. Green Chem. Eng. 2 (1), 70–76. doi:10.1016/j.gce.2020.12.003
Gautam, R., Kumar, S., Sahai, M., and Kumar, A. (2022). Solid CO2 hydrates for sustainable environment: application in carbon capture and desalination. Mater. Today Proc. 67, 609–615. doi:10.1016/j.matpr.2022.05.494
Guo, B., Mao, S., Chen, X., Wang, D., Ye, N., Yang, J., et al. (2023). Enhanced process on membrane-based for capturing carbon dioxide in flue gas. Available at: https://d.wanfangdata.com.cn/patent/CN113491929B/en.
Guo, T. (2002). Multivariate gas-liquid equilibrium and distillation. Beijing: Petroleum Industry Press.
Gutierrez-Ortega, A., Nomen, R., Sempere, J., Parra, J. B., Montes-Morán, M. A., and Gonzalez-Olmos, R. (2022). A fast methodology to rank adsorbents for CO2 capture with temperature swing adsorption. Chem. Eng. J. 435, 134703. doi:10.1016/j.cej.2022.134703
Hao, W., Wang, J., Fan, S., and Hao, W. (2007). Study on methane hydration process in a semi-continuous stirred tank reactor. Energy Convers. Manag. 48 (3), 954–960. doi:10.1016/j.enconman.2006.08.007
Hassanpouryouzband, A., Joonaki, E., Farahani, M., Takeya, V. S., Ruppel, C., Yang, J., et al. (2020). Gas hydrates in sustainable chemistry. Chem. Soc. Rev. 49 (15), 5225–5309. doi:10.1039/c8cs00989a
Hassanpouryouzband, A., Yang, J., Yang, B., Yang, E., Yang, V., and Yang, B. (2019). Geological CO2 capture and storage with flue gas hydrate formation in frozen and unfrozen sediments: method development, real time-scale kinetic characteristics, efficiency, and clathrate structural transition. ACS Sustain. Chem. Eng. 7 (5), 5338–5345. doi:10.1021/acssuschemeng.8b06374
Jiang, W., Bian, J., Wu, A., Gao, S., Yin, P., and Hou, D. (2018). Investigation of supersonic separation mechanism of CO2 in natural gas applying the discrete particle method. Chem. Eng. Process. 123, 272–279. doi:10.1016/j.cep.2017.11.019
Kan, J. Y., Sun, Y. F., Dong, B. C., Yuan, Q., Liu, B., Sun, C. Y., et al. (2021). Numerical simulation of gas production from permafrost hydrate deposits enhanced with CO2/N2 injection. Energy 221, 119919. doi:10.1016/j.energy.2021.119919
Kar, A., and Bahadur, V. (2023). Analysis of coupled heat and mass transfer during gas hydrate formation in bubble column reactors. Chem. Eng. J. 452, 139322. doi:10.1016/j.cej.2022.139322
Khanmohammadian, E., Mohammadi, M., Hashemi, R., Eslami, S., and Ehsani, M. R. (2023). Improvement of gas hydrate-based CO2 capture from CH4/CO2 mixture using silica and modified silica nanoparticles in the presence of potassium hydroxide. Fuel 334, 126458. doi:10.1016/j.fuel.2022.126458
Khatib, H. (2012). IEA world energy outlook 2011-A comment. Energy Policy 48, 737–743. doi:10.1016/j.enpol.2012.06.007
Khdary, N. H., Alayyar, A. S., Alsarhan, L. M., Alshihri, S., and Mokhtar, M. (2022). Metal oxides as catalyst/supporter for CO2 capture and conversion, review. Catalysts 12 (3), 300. doi:10.3390/catal12030300
Kim, K., and Sa, J. (2023). Advanced pre-combustion CO2 capture by clathrate hydrate formation with water-to-gas molar ratio optimization. Sep. Purif. Technol. 310, 123135. doi:10.1016/j.seppur.2023.123135
Kyung, D., Lee, K., Kim, H., and Lee, W. (2014). Effect of marine environmental factors on the phase equilibrium of CO2 hydrate. Int. J. Greenh. Gas. Con. 20, 285–292. doi:10.1016/j.ijggc.2013.11.013
Lang, X., Fan, S., and Wang, Y. (2010). Intensification of methane and hydrogen storage in clathrate hydrate and future prospect. J. Nat. Gas. Chem. 19 (3), 203–209. doi:10.1016/S1003-9953(09)60079-7
Lee, D., Jin, Y., Jung, N., Lee, J., Lee, J., Jeong, Y. S., et al. (2011). Gravimetric analysis of the adsorption and desorption of CO2 on amine-functionalized mesoporous silica mounted on a microcantilever array. Environ. Sci.Technol. 45 (13), 5704–5709. doi:10.1021/es200680v
Lee, J. H., Kim, S. H., Kang, J. W., and Lee, C. S. (2016). Modeling gas hydrate-containing phase equilibria for carbon dioxide-rich mixtures using an equation of state. Fluid Phase Equilib. 409, 136–149. doi:10.1016/j.fluid.2015.09.026
Li, G., Liu, D. P., Xie, Y. M., and Xiao, Y. (2010). Study on effect factors for CO2 hydrate rapid formation in a water-spraying apparatus. Energy and Fuels 24 (8), 4590–4597. doi:10.1021/ef100417y
Li, M., and Xiao, R. (2019). Preparation of a dual pore structure activated carbon from rice husk char as an adsorbent for CO2 capture. Fuel Process. Technol. 186, 35–39. doi:10.1016/j.fuproc.2018.12.015
Li, X. B. (2014). Research progress on carbon dioxide capture and separation technology. Guangdong Huagong 41 (5), 115–116. doi:10.3969/j.issn.1007-1865.2014.05.060
Li, Y., Dai, M., Chen, X. H., Yang, Y. P., Yang, M., Huang, W. J., et al. (2022). Synergetic effect and mechanism between propylene carbonate and polymer rich in ester and ether groups for CO2 physical absorption. J. Clean. Prod. 336, 130389. doi:10.1016/j.jclepro.2022.130389
Li, Y., Yin, Z., Rao, Y., Lu, H., Xu, C., Liu, X., et al. (2024). Ultrarapid CO2 hydrate nucleation and growth enabled by magnesium coupled with amino acids as a promoter. Energy and Fuels 38 (17), 16543–16554. doi:10.1021/acs.energyfuels.4c01776
Li, Y. H., Xu, C. G., Li, X. S., and Chen, Z. Y. (2024). Basic research progress on marine CO2 hydrate sequestration. J. Chem. Ind. Eng., 1–16. doi:10.11949/0438-1157.20240554
Linga, P., Daraboina, N., Ripmeester, J. A., and Englezos, P. (2012). Enhanced rate of gas hydrate formation in a fixed bed column filled with sand compared to a stirred vessel. Chem. Eng. Sci. 68 (1), 617–623. doi:10.1016/j.ces.2011.10.030
Liu, X., Li, Y., Chen, G., Chen, D., Sun, B., and Yin, Z. (2023). Coupling amino acid with THF for the synergistic promotion of CO2 hydrate micro kinetics: implication for hydrate-based CO2 sequestration. ACS Sustain. Chem. Eng. 11 (15), 6057–6069. doi:10.1021/acssuschemeng.3c00593
Liu, X., Ren, J., Chen, D., and Yin, Z. (2022). Comparison of SDS and L-Methionine in promoting CO2 hydrate kinetics: implication for hydrate-based CO2 storage. Chem. Eng. J. 438, 135504. doi:10.1016/j.cej.2022.135504
Lu, Y., Wang, H., Li, Q. P., Lv, X., Ge, Y., Zhang, L. X., et al. (2022). CO2 storage behavior via forming hydrate from N2/CO2 gas mixtures in the presence of initial SI CO2 hydrate seeds. Chem. Eng. J. 450, 138001. doi:10.1016/j.cej.2022.138001
Luo, Y. T., Zhu, J. H., Fan, S. S., and Chen, G. J. (2007). Study on the kinetics of hydrate formation in a bubble column. Chem. Eng. Sci. 62 (4), 1000–1009. doi:10.1016/j.ces.2006.11.004
Lv, Q. N., Li, X. S., Xu, C. G., and Chen, Z. Y. (2012). Experimental investigation of the formation of cyclopentane-methane hydrate in a novel and large-size bubble column reactor. Ind. Eng. Chem. Res. 51 (17), 5967–5975. doi:10.1021/ie202422c
Ma, C. H., Wang, M., Wang, Z., Gao, M., and Wang, J. X. (2020). Recent progress on thin film composite membranes for CO2 separation. J. CO2 Util. 42, 101296. doi:10.1016/j.jcou.2020.101296
Madejski, P., Chmiel, K., Subramanian, N., and Kuś, T. (2022). Methods and techniques for CO2 capture: review of potential solutions and applications in modern energy technologies. Energies 15 (3), 887. doi:10.3390/en15030887
Majid, A. A. A., Worley, J., and Koh, C. A. (2021). Thermodynamic and kinetic promoters for gas hydrate technological applications. Energy and Fuels 35 (23), 19288–19301. doi:10.1021/acs.energyfuels.1c02786
Mao, W. L., Mao, H. K., Goncharov, A. F., Struzhkin, V. V., Guo, Q. Z., Hu, J. Z., et al. (2002). Hydrogen clusters in clathrate hydrate. Science 297 (5590), 2247–2249. doi:10.1126/science.1075394
Mohamadi-Baghmolaei, M., Hajizadeh, A., Zahedizadeh, P., Azin, R., and Zendehboudi, S. (2021). Evaluation of hybridized performance of amine scrubbing plant based on exergy, energy, environmental, and economic prospects: a gas sweetening plant case study. Energy 214, 118715. doi:10.1016/j.energy.2020.118715
Mondal, M. K., Balsora, H. K., and Varshney, P. (2012). Progress and trends in CO2 capture/separation technologies: a review. Energy 46 (1), 431–441. doi:10.1016/j.energy.2012.08.006
Montazeri, S. M., Kalogerakis, N., and Kolliopoulos, G. (2024). CO2 nanobubbles as a novel kinetic promoter in hydrate-based desalination. Desalination 574, 117296. doi:10.1016/j.desal.2024.117296
Murakami, T., Kuritsuka, H., Fujii, H., and Mori, Y. H. (2009). Forming a structure-H hydrate using water and methylcyclohexane jets impinging on each other in a methane atmosphere. Energy and fuels 23 (3), 1619–1625. doi:10.1021/ef800880f
Naghibzade, S. A., Kahrizi, H., and Soleimani Mehr, A. (2015). Comparison of different equations of state in a model based on VdW-P for prediction of CO2 hydrate formation pressure in Lw-H-V phase and a new correlation to degrade error of the model. J. Nat. Gas. Sci. Eng. 22, 292–298. doi:10.1016/j.jngse.2014.11.035
Nandakishora, Y., Sahoo, R. K., and Murugan, S. (2022). A comparative study of modified linde and cryogenic cooling for CO2 separation. Int. J. Energy Res. 46 (3), 2840–2857. doi:10.1002/er.7348
Nashed, O., Partoon, B., Lal, B., Sabil, K. M., and Shariff, A. M. (2018). Review the impact of nanoparticles on the thermodynamics and kinetics of gas hydrate formation. J. Nat. Gas. Sci. Eng. 55, 452–465. doi:10.1016/j.jngse.2018.05.022
Nguyen, N. N., La, V. T., Huynh, C. D., and Nguyen, A. V. (2022). Technical and economic perspectives of hydrate-based carbon dioxide capture. Appl. Energy 307, 118237. doi:10.1016/j.apenergy.2021.118237
Park, J., Seo, Y. T., Lee, J. W., and Lee, H. (2006). Spectroscopic analysis of carbon dioxide and nitrogen mixed gas hydrates in silica gel for CO2 separation. Catal. Today 115 (1-4), 279–282. doi:10.1016/j.cattod.2006.02.059
Partoon, B., Sabil, K. M., Lau, K. K., Lal, B., and Nasrifar, K. (2018). Production of gas hydrate in a semi-batch spray reactor process as a means for separation of carbon dioxide from methane. Chem. Eng. Res. Des. 138, 168–175. doi:10.1016/j.cherd.2018.08.024
Pasichnyk, M., Stanovsky, P., Polezhaev, P., Zach, B., Šyc, M., Bobák, M., et al. (2023). Membrane technology for challenging separations: removal of CO2, SO2 and NOx from flue and waste gases. Sep. Purif. Technol. 323, 124436. doi:10.1016/j.seppur.2023.124436
Rahimi, M., Khurram, A., Hatton, T. A., and Gallant, B. (2022). Electrochemical carbon capture processes for mitigation of CO2 emissions. Chem. Soc. Rev. 51 (20), 8676–8695. doi:10.1039/d2cs00443g
Rehman, A., and Lal, B. (2022). Gas hydrate-based CO2 capture: a journey from batch to continuous. Energies 15 (21), 8309. doi:10.3390/en15218309
Ricaurte, M., Dicharry, C., Broseta, D., Renaud, X., and Torre, J. P. (2013). CO2 removal from a CO2–CH4 gas mixture by clathrate hydrate formation using THF and SDS as water-soluble hydrate promoters. Ind. Eng. Chem. Res. 52 (2), 899–910. doi:10.1021/ie3025888
Said, S., Mohamed, B., and Jean-Michel, H. (2020). Investigation of the effects of Al nanoparticles on CO2 separation from natural gas using gas hydrates. Energy Sources Part A 42 (19), 2333–2345. doi:10.1080/15567036.2019.1651426
Sandru, M., Sandru, E. M., Ingram, W. F., Deng, J., Stenstad, P. M., Deng, L. Y., et al. (2022). An integrated materials approach to ultrapermeable and ultraselective CO2 polymer membranes. Science 376 (6588), 90–94. doi:10.1126/science.abj9351
Shen, M. H., Tong, L. G., Yin, S. W., Liu, C. P., Wang, L., Feng, W. J., et al. (2022). Cryogenic technology progress for CO2 capture under carbon neutrality goals: a review. Sep. Purif. Technol. 299, 121734. doi:10.1016/j.seppur.2022.121734
Shi, S., and Liu, Y. X. (2021). Nitrogen-doped activated carbons derived from microalgae pyrolysis by-products by microwave/KOH activation for CO2 adsorption. Fuel 306, 121762. doi:10.1016/j.fuel.2021.121762
Shimada, W., Ebinuma, T., Oyama, H., Kamata, Y., Takeya, S., Uchida, T., et al. (2003). Separation of gas molecule using tetra-n-butyl ammonium bromide semi-clathrate hydrate crystals. JJAP Part 2-Letters 42 (2A), L129–L131. doi:10.1143/JJAP.42.L129
Song, C., Liu, Q., Deng, S., Li, H., and Kitamura, Y. (2019). Cryogenic-based CO2 capture technologies: state-of-the-art developments and current challenges. Renew. Sust. Energy Rev. 101, 265–278. doi:10.1016/j.rser.2018.11.018
Sun, N. R., Li, Y. J., Qiu, N. X., Francisco, J. S., and Du, S. Y. (2023). Effects of X (X = H2S, SO2 and N2O) mole fractions on adsorption behavior and phase equilibrium properties of CO2 + X mixed gas hydrate. J. Mol. Liq. 380, 121661. doi:10.1016/j.molliq.2023.121661
Van Denderen, M., Ineke, E., and Golombok, M. (2009). CO2 removal from contaminated natural gas mixtures by hydrate formation. Ind. Eng. Chem. Res. 48 (12), 5802–5807. doi:10.1021/ie8017065
Wang, F., Fu, S. F., Guo, G., Jia, Z. Z., Luo, S. J., and Guo, R. B. (2016). Experimental study on hydrate-based CO2 removal from CH4/CO2 mixture. Energy 104, 76–84. doi:10.1016/j.energy.2016.03.107
Wang, F., Mu, J. C., Lin, W. J., Cao, Y. H., Wang, Y. H., Leng, S., et al. (2024). Post-combustion CO2 capture via the hydrate formation at the gas-liquid-solid interface induced by the non-surfactant graphene oxide. Energy 290, 130177. doi:10.1016/j.energy.2023.130177
Wang, S. Y., Liu, H. R., and Chen, S. X. (2022). A strategy to synthesis amine-functional Poly(Divinylbenzene)HIPEs with controllable porous structure for effective CO2 adsorption. Fuel 322, 124120. doi:10.1016/j.fuel.2022.124120
Wang, Y., Zhao, L., Otto, A., Robinius, M., and Stolten, D. (2017). A review of post-combustion CO2 capture technologies from coal-fired power plants. Energy Procedia 114, 650–665. doi:10.1016/j.egypro.2017.03.1209
Wang, Y. H., Lang, X. M., and Fan, S. S. (2013). Hydrate capture CO2 from shifted synthesis gas, flue gas and sour natural gas or biogas. J. Energy Chem. 22 (1), 39–47. doi:10.1016/S2095-4956(13)60004-2
Wang, Y. J., Han, F. Z., Zhao, L. L., Lu, Y. H., Ma, M., Wang, K., et al. (2024). CO2 capture and electrocatalytic reduction to formate: a comprehensive review. Chin. Sci. Bull., 1–16. doi:10.1360/tb-2024-0424
Warzinski, R. P., and Holder, G. D. (1998). Gas clathrate hydrates. Energy and Fuels 12, 189–190. doi:10.1021/ef980007q
Xiao, P., Yang, X. M., Sun, C. Y., Cui, J. L., Li, N., and Chen, G. J. (2018). Enhancing methane hydrate formation in bulk water using vertical reciprocating impact. Chem. Eng. J. 336, 649–658. doi:10.1016/j.cej.2017.12.020
Xiao, X. Y., Gu, J. P., Liang, W. S., Yu, Q., and Tang, M. F. (2022). Application of carbon dioxide capture, storage and utilization technology. Guangzhou Huagong 50 (3), 26–29. doi:10.3969/j.issn.1001-9677.2022.03.009
Xie, W. J., Xu, C. G., and Li, X. S. (2019). Research advances on hydrate-based CO2 separation and capture. ANRE 7 (3), 277–286. doi:10.3969/j.issn.2095-560X.2019.03.011
Xu, G., Li, L., Yang, Y. P., Tian, L. H., Liu, T., and Zhang, K. (2012). A novel CO2 cryogenic liquefaction and separation system. Energy 42 (1), 522–529. doi:10.1016/j.energy.2012.02.048
Yan, H. Y., Zhang, G. J., Xu, Y., Zhang, Q. Q., Liu, J., Li, G. Q., et al. (2022). High CO2 adsorption on amine-functionalized improved macro-/mesoporous multimodal pore silica. Fuel 315, 123195. doi:10.1016/j.fuel.2022.123195
Yang, M. J., Zhou, H., Wang, P. F., Li, N., and Song, Y. C. (2017). Hydrate-based CO2 capture from flue gas in constant pressure process with the presence of THF. Proc. 9th ICAE. 142, 3939–3943. doi:10.1016/j.egypro.2017.12.300
Yu, Y. S., Zhang, Q. Z., Li, X. S., Chen, C., and Zhou, S. D. (2020). Kinetics, compositions and structures of carbon dioxide/hydrogen hydrate formation in the presence of cyclopentane. Appl. Energy 265, 114808. doi:10.1016/j.apenergy.2020.114808
Zhang, F. Y., Bhatia, S. K., Wang, B., Chalermsinsuwan, B., and Wang, X. L. (2022). Experimental and numerical study on the kinetics of CO2–N2 clathrate hydrates formation in silica gel column with dodecyltrimethylammonium chloride for effective carbon capture. J. Mol. Liq. 363, 119764. doi:10.1016/j.molliq.2022.119764
Zhang, G., Li, J., Liu, G. H., Yang, H. W., and Huang, H. L. (2022). Applicability research of thermodynamic models of gas hydrate phase equilibrium based on different equations of state. RSC Adv. 12 (25), 15870–15884. doi:10.1039/D2RA00875K
Zhang, L., Ye, K., Wang, Y., Han, W., Xie, M., and Chen, L. (2024). Performance analysis of a hybrid system combining cryogenic separation carbon capture and liquid air energy storage (CS-LAES). Energy 290, 129867. doi:10.1016/j.energy.2023.129867
Zhang, Y. Q., Zhu, C. Y., Chu, C. Y., Fu, T. T., and Ma, Y. G. (2022). Mass transfer and capture of carbon dioxide using amino acids sodium aqueous solution in microchannel. Chem. Eng. Process 173, 108831. doi:10.1016/j.cep.2022.108831
Zhang, Z. Z. (2014). Adsorptive separation of carbon dioxide. Tianjin: Tianjin University. doi:10.7666/d.D322090
Zheng, J. N., Cheng, F. B., Li, Y. P., Lü, X., and Yang, M. J. (2019). Progress and trends in hydrate based desalination (HBD) technology: a review. Chin. J. Chem. Eng. 27 (9), 2037–2043. doi:10.1016/j.cjche.2019.02.017
Zhou, X. B., Long, Z., He, Y., Shen, X. D., and Liang, D. Q. (2018). Phase equilibria and the crystallographic properties of TBAB–CO2 semiclathrate hydrates. J. Chem. Eng. Data 63 (5), 1249–1255. doi:10.1021/acs.jced.7b00884
Zhu, P., Wu, Z. Y., Elgazzar, A., Dong, C. X., Wi, T. U., Chen, F. Y., et al. (2023). Continuous carbon capture in an electrochemical solid-electrolyte reactor. Nature 618 (7967), 959–966. doi:10.1038/s41586-023-06060-1
Keywords: hydrate, capture of CO2, separation of gas mixture, chemical promoter of hydrate, mechanical promotion of hydrate
Citation: Pei J, Chen J, Wang J, Li Z, Li N and Kan J (2024) CO2 capture technology based on gas hydrate method: a review. Front. Chem. 12:1448881. doi: 10.3389/fchem.2024.1448881
Received: 14 June 2024; Accepted: 07 October 2024;
Published: 17 October 2024.
Edited by:
Jianhua Zhang, Victoria University, AustraliaReviewed by:
Shuanshi Fan, South China University of Technology, ChinaZhenyuan Yin, Tsinghua University, China
Copyright © 2024 Pei, Chen, Wang, Li, Li and Kan. This is an open-access article distributed under the terms of the Creative Commons Attribution License (CC BY). The use, distribution or reproduction in other forums is permitted, provided the original author(s) and the copyright owner(s) are credited and that the original publication in this journal is cited, in accordance with accepted academic practice. No use, distribution or reproduction is permitted which does not comply with these terms.
*Correspondence: Zhi Li, bGl6QGN1cGsuZWR1LmNu; Nan Li, bGluYW5AY3Vway5lZHUuY24=