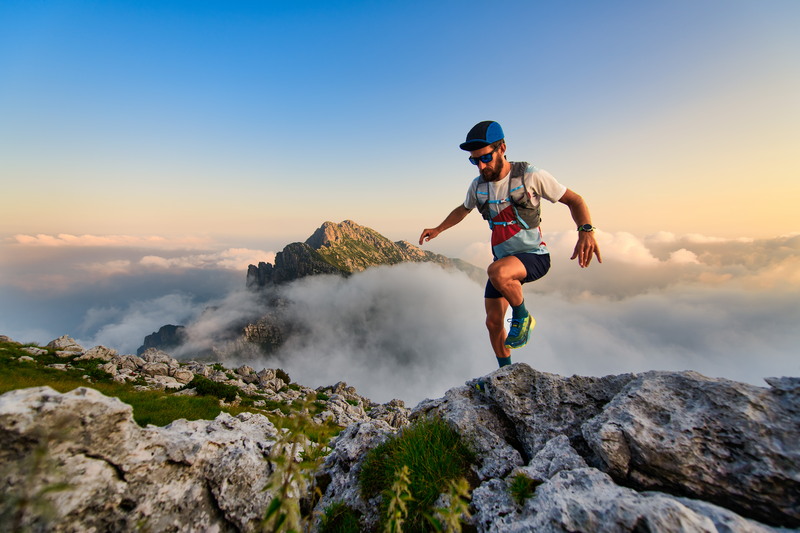
95% of researchers rate our articles as excellent or good
Learn more about the work of our research integrity team to safeguard the quality of each article we publish.
Find out more
ORIGINAL RESEARCH article
Front. Chem. , 22 August 2022
Sec. Green and Sustainable Chemistry
Volume 10 - 2022 | https://doi.org/10.3389/fchem.2022.979353
This article is part of the Research Topic Preparation of Functional Materials and Utilization of Renewable Resources in Green Solvents View all 12 articles
Efficient conversion of biomass-derived 5-hydroxymethylfurfural (HMF) to renewable fuels such as 2,5-dimethylfuran (DMF) and 2,5-dimethyltetrahydrofuran (DMTHF) is of significance for sustainable energy supply. For efficient catalyst design, it is important to understand the catalytic behavior and clarify the influence of physico-chemical properties of catalyst on reaction performance. Herein, to study the structure-activity relationships of monometallic Cu catalysts for HMF hydrogenolysis, a series of Cu/SiO2 catalysts with different physico-chemical properties were prepared and compared for their catalytic performance in HMF hydrogenolysis. It was found that Cu/SiO2-HT-8.5 catalyst prepared by hydrothermal method showed excellent activity in HMF hydrohydrolysis reaction. Under the optimal reaction condition, the total yield of liquid fuels reaches 91.6% with 57.1% yield of DMF and 34.5% yield of DMTHF in THF solvent. Characterizations such as XRD, H2-TPR, N2-adsorption/desorption, TEM and XPS revealed that the Cu particles in the Cu/SiO2-HT-8.5 catalyst have uniform size and high dispersion. The Cu species and the SiO2 support have relatively weak interaction and are easy to be reduced to Cu0, which makes it show excellent activity in the hydrogenolysis of HMF.
Efficient conversion of renewable lignocellulosic biomass to bio-fuels and value-added chemicals is of significance for sustainable energy supply, and reduction of CO2 emissions, as an alternative strategy to many other ways to solve the energy and environmental issues (Jing et al., 2019; Hao et al., 2021; Qin et al., 2021; Li et al., 2022). 5-hydroxymethylfurfural (HMF) is regarded as one of the most versatile platform molecules that can be converted to a variety of biofuels and chemicals, such as levulinic acid (Yan et al., 2015), liquid alkanes (Xia et al., 2014; Nakagawa et al., 2019), 2,5-furandicarboxylic acid and derivatives (Yang et al., 2020; Nakagawa et al., 2021), 2,5-bis(hydroxymethyl)tetrahydrofuran (BHMTHF) (Nakagawa et al., 2017), 1,6-hexanediol (Xiao et al., 2016) and so forth (Gao et al., 2021). 2,5-dimethylfuran (DMF) and 2,5-dimethyltetrahydrofuran (DMTHF) derived from hydrogenolysis of HMF are not only important chemical intermediates, but also serves as high-grade biofuels with high octane number and high energy density (Roman-Leshkov et al., 2007). Moreover, DMF is also employed as a feedstock for the production of p-xylene through the Diels-Alder reaction (Rohling et al., 2018).
The reaction networks for DMF and DMTHF production from HMF contain a series of parallel and consecutive reactions, and therefore it is a challenge to increase the selectivity to the desired products at a complete conversion of HMF (Maki-Arvela et al., 2021). Over the last decade, catalysts based on noble metals (e.g., Pt (Shi et al., 2016), Ru (Zu et al., 2014; Priecel et al., 2018; Feng et al., 2020; Tzeng et al., 2020), Pd (Hu et al., 2021)) and their bimetallics (Requies et al., 2018; Wang et al., 2018; Mhadmhan et al., 2019; Talpade et al., 2019; Pisal & Yadav, 2021) have been extensively explored and proved to be efficient in the hydrogenolysis of HMF to DMF and DMTHF. However, noble metal-based catalysts suffer from the high cost of catalyst preparation, which may limit their large-scale industrial applications.
As an alternative, catalysts based on non-noble transition metals such as Cu, Co and Ni have been widely studied for HMF hydrogenolysis to DMF and DMTHF, with the great majority efforts emphasis on bimetallic catalysts (e.g., Ni-Co (Yang et al., 2015; Yang et al., 2016; Xia et al., 2022), Co-Cu (Guo et al., 2016), Cu-Ni (Zhang Y.-R. et al., 2019; Zhu et al., 2019; Umasankar et al., 2020), Cu-Zn (Zhu et al., 2015; Brzezinska et al., 2020), Ni-Zn (Kong et al., 2017), Co-Fe (Solanki and Rode, 2019) etc.) or bifunctional catalysts that consist of active metal and acidic supports (Shi et al., 2018; Chen N. et al., 2020; Esteves et al., 2020; Guo et al., 2020). For example, Zhu et al. developed an alloyed Cu-Ni encapsulated in carbon catalyst by loading Ni and Cu onto biochar, and the bimetallic Cu-Ni catalyst displayed high catalytic performance for HMF hydrogenolysis to DMF with yield up to 93.5% under the optimized conditions (Zhu et al., 2019). Our group also reported a non-noble bimetallic Ni-Co catalyst with the uniform dispersion of Ni and Co species on the active carbon for hydrogenolysis of HMF, and an excellent yield (up to 95%) of DMF can be obtained at relatively mild conditions (Yang et al., 2016). Very recently, our group reported a unique core-shell structured Co@CoO catalyst for this reaction and afforded the highest productivity among all catalysts reported to date (Xiang et al., 2022).
Earth-abundant Cu-based catalysts are well known for their hydrogenation ability, especially in the field of CO2 hydrogenation (Kattel et al., 2017). From the catalyst design point of view, it is important to understand the catalytic behavior and clarify the influence of physico-chemical properties of metal on reaction performance. However, structure-activity relationships of monometallic non-noble metals (Cu, Co, and Ni) on HMF hydrogenolysis have been rarely explored, especially for Cu-based catalysts (Chen S. et al., 2020).
Herein, to study the structure-activity relationships of monometallic Cu catalysts for HMF hydrogenolysis, a series of Cu/SiO2 catalysts with different physico-chemical properties were prepared and compared for their catalytic performance in HMF hydrogenolysis. The low acidic non-metal oxide SiO2 was chosen as the support to exclude the effect of the acid sites and metal-support interactions as far as possible.
HMF was purchased from Shanghai Mode Pharmaceutical Technology Co., Ltd. Tetrahydrofuran (THF) was purchased from Shanghai Lingfeng Chemical Reagent Co., Ltd. 2,5-dimethylfuran (DMF), tridecane was obtained from Aladdin Reagent (Shanghai) Co., Ltd. SiO2 was obtained from Afaisha Chemical Co. Ltd. All other chemicals and solvents (analytical grade) were purchased from Sinopharm Chemical Reagent Co., Ltd, China. All the chemicals were used without further purification.
Cu/SiO2 catalysts were prepared by three different method, namely excessive impregnation (EI), deposition-precipitation (DP) and hydrothermal (HT) method. For a typical EI method, 1.89 g CuNO3•3H2O was dissolved in 70 ml deionized water, and then 1.0 g SiO2 was added into the solution, stirred at room temperature for 12 h. After that, the suspension was dried at 60°C for 12 h. The obtained precursor was then calcined in static air at 450°C for 4 h, and then reduced in flow 10% H2/Ar mixture at 450°C for 6 h before use. The catalyst was denoted as Cu/SiO2-EI.
For a typical DP method, 1.89 g CuNO3•3H2O was dissolved in 70 ml deionized water, and then silica sol (equivalent to 1.0 g SiO2) was dropped into the solution and stirred for 0.5 h. Then 1.0 mol/L NaOH solution was dropped into the above mixture with stirring, until the pH of the suspension to a set value of 9. Subsequently, the obtained suspension was filtered, washed by deionized water and dried at 60°C for 12 h. The obtained precursor was then calcined and reduced with the same procedure as EI method. The catalysts were denoted as Cu/SiO2-DP.
For a typical HT method, 1.89 g CuNO3•3H2O was dissolved in 70 ml deionized water, and then a certain amount of NH4Cl, NH3·H2O and silica sol (equivalent to 1.0 g SiO2) were added into the solution to reach a set pH value (6.5 or 8.5) and stirred for 0.5 h. After that, the mixture was placed in ultrasonic bath for 0.5 h, and then transferred into a 100 ml Teflon-lined autoclave and aged at 120°C for 4 h. After cooling to room temperature, the suspension was filtered, washed by deionized water and dried at 60°C for 12 h. The obtained precursor was then calcined and reduced with the same procedure as EI method. The catalysts were denoted as Cu/SiO2-HT-6.5 or Cu/SiO2-HT-8.5.
The X-ray diffraction (XRD) patterns of the catalysts were recorded by a Bruker D8 Foucus X-ray diffractometer with Cu Kα radiation (λ = 0.1541 nm) operating at 40 kv and 40 mA. The crystal size was calculated using the Scherrer equation through the Cu 111) diffraction peak.
N2 adsorption-desorption isotherms were measured at −196°C using a Micromeritics ASAP 2020 instrument. The samples were outgassed at 200°C for 6 h before analysis. The specific surface areas were obtained by the Brunauer-Emmett-Teller (BET) method.
H2 temperature programmed reduction (H2-TPR) was performed on a Huasi DAS-7200 automatic chemisorption apparatus. The samples were pretreated with pure Ar at 150°C for 1 h before reduction. After cooling to room temperature, 10% H2/Ar mixture was introduced and the sample tube was heated to 800°C at a heating rate of 10°C/min. TCD was used as the detector to collect signals.
Transmission electron microscopy (TEM) images were taken using a JEOL 2100F microscope operated at an acceleration voltage of 200 kV. The sample was grinded and dispersed in ethanol under supersonic waves, and then dropped on a copper net and dried before use.
The copper content of the catalyst was determined by Agilent 725ES inductively coupled plasma atomic emission spectrometer (ICP-AES).
X-ray photoelectron spectroscopy (XPS) was tested on a Thermo Scientific Escalab 250Xi X-ray photoelectron spectrometer with a monochromatic Al Kα radiation (1,486.6 eV photons). All of the binding energies were calibrated by C 1s and the binding energy of C-C is 284.6 eV.
The hydrogenolysis of HMF was carried out in a batch reactor equipped with a magnetic stirrer. Typically, 0.05 g HMF, 0.05 g catalyst, 100 μL tridecane (internal standard) and 5 ml tetrahydrofuran (THF) were put into a Teflon-lined stainless-steel autoclave (50 ml). After purging with H2 for three times, the reactor was conducted under H2 pressure at the required condition for a desired time with magnetic stirring. After the reaction, the reactor was cooled with ice-water and depressurized carefully. After centrifugation of the catalyst, the liquid products were identified by GC-MS (Agilent 7,890A-5975C) equipped with an HP-5 capillary column and quantitatively analyzed by GC (Agilent GC7890 B) equipped with a flame ionization detector (FID) and an HP-5 capillary column using tridecane as an internal standard. The injector temperature was set at 270°C, and the column temperature was increased from 50 to 200°C with a ramp rate of 10°C/min.
The Cu/SiO2 catalysts were prepared by impregnation (EI), deposition-precipitation (DP) and hydrothermal (HT) methods at different pH value. Figure 1A shows the XRD patterns of various catalysts after calcination. It can be seen that the Cu/SiO2-EI and Cu/SiO2-DP catalysts exhibit diffraction peaks at 35.5°, 38.7°, 48.7°, 53.5°, 61.5° and 66.2°, indexed to (110), (11–1), (111), (20–2), (020) and (11–3) planes of CuO, suggesting the presence of bulk CuO. Interestingly, obvious CuO diffraction peaks were observed for Cu/SiO2-HT-6.5, but none of them was found for Cu/SiO2-HT-8.5, which indicates CuO species were highly dispersed on the latter catalyst. The high dispersion of CuO species on Cu/SiO2-HT-8.5 can be resulted from the calcination of layered copper silicate (Li et al., 2018). These results indicate that the hydrothermal method favors the Cu2+ to complex with surface silanol to form layered copper silicate, leading to high dispersed CuO species after calcination.
FIGURE 1. Physicochemical characterization of Cu/SiO2 catalysts prepared by different method. (A) XRD patterns of Cu/SiO2 catalysts before reduction; (B) XRD patterns of Cu/SiO2 catalysts after reduction; (C) N2 adsorption-desorption isotherm of Cu/SiO2 catalysts; (D) H2-TPR profiles of Cu/SiO2 catalysts.
Figure 1B shows the XRD patterns of various Cu/SiO2 catalysts after reduction. Evident peaks at 43.4°, 50.5° and 74.1° were observed for Cu/SiO2-EI catalyst, assigned to (111), (200) and (220) planes of Cu (Dong et al., 2016). The particle size of Cu of Cu/SiO2-EI was calculated to be ca. 50 nm according to the Cu 111) diffraction peak, which suggests an agglomeration of Cu cluster. The Cu characteristic diffraction peaks can also be clearly found on Cu/SiO2-DP and Cu/SiO2-HT-6.5 catalysts, while no obvious Cu diffraction peaks observed on Cu/SiO2-HT-8.5, indicating the high dispersion of Cu nanoparticles on the latter catalyst. Cu/SiO2-HT-6.5 still exhibits the diffraction peaks at 35.5° (110) and 38.8° (11–1) of CuO, suggesting an incomplete reduction of the catalyst. In addition, Cu/SiO2-DP and Cu/SiO2-HT catalysts all exhibit the diffraction peaks at 36.5°, 42.3° and 61.3°, attributed to the (111), (200) and (220) planes of Cu2O (Wang et al., 2002), indicating the partial reduction of CuO on these catalysts, due to the interactions between CuOx and SiO2.
N2 adsorption/desorption isotherms for the four Cu/SiO2 catalysts are presented in Figure 1C, and the calculated textural properties as well as ICP-AES results are listed in Table 1. All catalysts present the isotherm shape of type IV (IUPAC classification), indicating the existence of mesoporous structure in all cases. There are distinct differences of the textural properties in these catalysts. Cu/SiO2-HT-8.5 possesses the largest BET specific surface area (449 m2g−1) and pore volume (0.92 cm3g−1), while Cu/SiO2-EI shows the smallest ones (48 m2g−1 and 0.09 cm3 g−1, respectively). The large BET specific surface area of Cu/SiO2-HT-8.5 allows the high dispersion of CuOx species on the SiO2 surface, consistent with the XRD results. The Cu contents in Cu/SiO2-EI and Cu/SiO2-HT catalysts analyzed by ICP-AES were close to the set value (33 wt%), whereas only 23 wt% Cu was detected in Cu/SiO2-DP catalyst, which indicates almost a third of Cu content was lost during the DP process.
The reduction features of Cu/SiO2 catalysts were investigated by H2-TPR experiments. As shown in Figure 1D, the H2-TPR profile of Cu/SiO2-EI and Cu/SiO2-DP presents a broad hydrogen consumption peak centered at 275 and 284°C, respectively, which can be attributed to the reduction of bulk CuO (Mo and Kawi, 2014). Significant difference was presented for the reduction peaks of Cu/SiO2-HT prepared at different pH values. Cu/SiO2-HT-6.5 catalyst exhibits two adjacent reduction peaks at 250∼350°C, assigned to the reduction of bulk CuO with multiple sizes. Generally, the reduction peak at high temperature is caused by the reduction of large bulk CuO, and that at low temperature is caused by the reduction of highly dispersed isolated CuO particles (Mo and Kawi, 2014). Cu/SiO2-HT-8.5 shows a single symmetrical reduction peak at 242°C. This indicates that there are well-dispersed CuO species with uniform size on the catalyst, which is consistent with the XRD results. Moreover, different reduction temperature can also reflect the strength of the metal-support interactions (Cui et al., 2016). Cu/SiO2-HT-8.5 exhibit the lowest reduction temperature of CuO, suggesting the weakest interaction between Cu species and SiO2.
The dispersions of the Cu particles in Cu/SiO2 catalysts after reduction were further evaluated by TEM (Figure 2). It can be seen from Figures 2A–C that Cu particles were unevenly dispersed on SiO2 surface for Cu/SiO2-EI, Cu/SiO2-DP and Cu/SiO2-HT-6.5, with the co-existence of both small and large Cu particles. In contrast, it can be clearly seen that Cu particles are uniformly dispersed on the SiO2 support for Cu/SiO2-HT-8.5 (Figure 2D). These results are in well agreement with the XRD and H2-TPR results. Most of the Cu particles are in the rage of 10–15 nm for Cu/SiO2-HT-8.5, as shown in the particle size distribution in Figure 2D. It should be noted that such size (10–15 nm) of Cu particle is relatively small compared to its ultra high Cu loading of 33 wt%. The results reveal that the metal-support interaction adjusted by different preparation method can affect not only the reduction of CuO, but also the dispersion of Cu particles on SiO2 surface.
FIGURE 2. Typical TEM images of Cu/SiO2 catalysts prepared by different method after reduction. (A) Cu/SiO2-EI, (B) Cu/SiO2-DP, (C) Cu/SiO2-HT-6.5, (D) Cu/SiO2-HT-8.5.
The chemical state of Cu species plays a crucial role on the catalytic performance of Cu/SiO2 catalysts for HMF hydrogenolysis. The Cu0 and Cu+ species on the catalyst surface play different roles in catalytic reactions, such as activation of H2 or adsorption of substrate. There are two steps of reaction in HMF hydrogenolysis to DMF, namely the hydrogenation of the side -CH = O groups and the following hydrogenolysis of -CH2-OH groups, which both need the activation of H2 and adsorption of HMF (Zheng et al., 2017). Therefore, XPS and XAES analyses were performed to evaluate the chemical state of Cu species on SiO2 surface. As XPS spectra shown in Figure 3A, all four catalysts display binding energy peaks of Cu 2p3/2 at 932.1∼932.5 eV, which can be attributed to the formation of Cu0 or Cu+ (Liu et al., 2015; Li et al., 2016). In the Cu/SiO2-EI, Cu/SiO2-DP and Cu/SiO2-HT-6.5 catalysts, Cu 2p3/2 has both low binding energy (932.1∼932.3) and high binding energy (933.7∼934.1), indicating that Cu element in these three catalysts exists not only as Cu+ or Cu0, but also as Cu2+ species (Li et al., 2016). In contrast, no high binding energy peak of Cu 2p3/2 was observed in Cu/SiO2-HT-8.5 catalyst, attributed to the disappearance of Cu2+ species after reduction. These XPS results indicate the highest reducibility of Cu/SiO2-HT-8.5, which is in well accordance with H2-TPR results.
FIGURE 3. Cu 2p XPS (A) and Cu LMM XAFS (B) profiles of Cu/SiO2 catalysts prepared by different method after reduction. (a) Cu/SiO2-EI, (b) Cu/SiO2-DP, (c) Cu/SiO2-HT-6.5, (d) Cu/SiO2-HT-8.5.
Since it is difficult to distinguish the Cu0 and Cu+ by XPS spectra, XAES was carried out to determine the surface Cu0 and Cu+ species of the reduced Cu/SiO2 catalysts. All the reduced catalysts exhibit the Auger kinetic energy peaks of Cu LMM at 917.0 and 913.0 eV (Figure 3B), corresponding to Cu0 and Cu+ species, respectively (Zhang Z. et al., 2019). According to the peak area of the kinetic energy peak of Cu LMM XAES spectra, we can calculated the ratio of Cu0/(Cu0+ Cu+) (Table 2). The peak area ratio of surface Cu0/(Cu0+ Cu+) varies from 0.40 to 0.59 as the different synthetic method of Cu/SiO2, with the Cu/SiO2-HT-8.5 catalyst showing the largest proportion of Cu0. It is known that the weaker interaction between Cu species and the support leads to the easier reduction of CuO to Cu0, while the stronger interaction generates more Cu+ species. The largest proportion of Cu0 in Cu/SiO2-HT-8.5 catalyst indicates that the weakest metal-support interaction compared with the other three catalysts, which is consistent with the H2-TPR results.
TABLE 2. Kinetic energy and ratio of Cu0/(Cu0+ Cu+) of Cu/SiO2 catalysts prepared by different method.
The reaction activity of Cu/SiO2 catalysts prepared by different methods in HMF hydrogenolysis is shown in Table 3. HMF was completely converted in all cases, indicating the hydrogenation of HMF to BHMF is easy over Cu-based catalysts. However, the selectivity of the products was obviously different. Among them, the catalyst prepared by over-impregnation method (Cu/SiO2-EI) and deposition precipitation method (Cu/SiO2-DP) gave 2,5-dihydroxymethylfuran (BHMF) as a main product with 83.1 and 84.9% yield, respectively, while the total yields of 2.5-dimethylfuran (DMF) and further hydrogenation product 2.5-dimethyltetrahydrofuran (DMTHF) were less than 10%, suggesting a poor hydrogenolysis activity. In contrast, Cu/SiO2 prepared by hydrothermal method offered a much stronger hydrogenolysis activity with DMF and DMTHF as the majority products, especially for Cu/SiO2-HT-8.5 which achieving the highest activity in HMF hydrohydrolysis with 57.1% yield of DMF and 34.5% yield of DMTHF. It was reported that the activity of Cu-based catalysts in HMF hydrogenolysis is proportional to the specific surface area of the metallic Cu0. The high activity for HMF hydrogenolysis over Cu/SiO2-HT-8.5 catalyst can be attributed to the high Cu dispersion, small Cu particle size and high proportion of Cu0, which is well evidenced by XRD characterization, H2-TPR, TEM images, XPS and XAES spectra.
TABLE 3. Catalytic performance of HMF hydrogenolysis over Cu/SiO2 catalysts prepared by different methods.
The reaction pathway of HMF hydrogenolysis over Cu/SiO2-HT-8.5 was studied by analyzing the product distribution at different reaction time, as shown in Figure 4. It can be seen that HMF has been completely converted when reaction for 2 h, along with a large number of intermediates BHMF (49.8%) and HMMF (11.2%), as well as 23.5% yield of product DMF. This result indicated that the hydrogenation of exocyclic aldehyde group (C=O bond) is a rapid and facile step over Cu/SiO2-HT-8.5 catalyst, confirming the high hydrogenation activity of Cu species. It is noted that no 5-methylfurfural (5-MF) was detected, revealing that HMF was first undergo hydrogenation of aldehyde group to BHMF rather than hydrogenolysis of hydroxyl group to 5-MF. After reaction for 4 h, the yield of DMF gradually increased to 29.8%, with the decrease of BHMF to 41.8% and slight increase of HMMF to 13.0%. Only trace of DMTHF was produced at this time, indicating that the hydrogenolysis of hydroxyl group is much faster than the hydrogenation of furan ring over Cu/SiO2-HT-8.5. As the reaction further extended to 8 h, the yield of DMF continued to increase to 58.6%, with the complete conversion of BHMF and HMMF. At the same time, it is noteworthy that the yield of DMTHF also increased rapidly to 30.2%, as well as a small amount of hydration ring opening products of DMF. When the reaction was further extended to 12 h, the yield of DMF decreased from 58.6 to 49.8%, and the yield of DMTHF further increased to 38.8%, indicating that the further extension of reaction time would promote the cyclic hydrogenation reaction of DMF to DMTHF. During the reaction period, small amount of other by-products (such as BHMTHF, HMMTHF, hexanols etc., denoted by others) were also detected, totally account for ca. 10%。According to the variation tendency of product distribution versus reaction time, the reaction pathways of HMF hydrogenolysis to DMF and DMTHF over Cu/SiO2-HT-8.5 was proposed in Figure 4B.
FIGURE 4. Reaction pathway study of HMF hydrogenolysis over Cu/SiO2-HT-8.5 catalyst. (A) Product distribution of HMF hydrogenolysis at different reaction time; (B) Proposed reaction pathways for HMF hydrogenolysis over Cu/SiO2-HT-8.5 catalyst. Reaction conditions: 0.05 g HMF, 0.05 g catalyst, 100 µL tridecane, 5 ml THF, 200°C, 0.6 MPa.
To further tailor the catalytic performance of Cu/SiO2 for HMF hydrogenolysis, we investigated the influence of reaction temperature and H2 pressure on the reaction performance, as shown in Table 4. When increase the reaction temperature from 180 to 220oC at 0.6 MPa H2 pressure, the yield of DMF first increased from 47.5 to 57.1% and then decreased to 51.0%. According to the detection of the product distribution, lower temperature (180oC) led to the incomplete conversion of intermediate HMMF and higher temperature (220oC) resulted in a small amount of side reaction of DMF to hydration by-products. At the same time, the yield of DMTHF continuously increased from 30.7 to 36% with the increase of reaction temperature, indicating that higher temperature accelerated the reaction rate of furan ring hydrogenation and in favor of the production of DMTHF.
TABLE 4. The effects of temperature and pressure on the conversion of HMF over Cu/SiO2-HT-8.5 catalyst.
When the reaction temperature was fixed at 200oC, the variation of H2 pressure showed that the H2 pressure for HMF hydrogenolysis can be as low as 0.2 MPa, at which a high DMF yield of 66.8% was reached, along with 24.3% yield of DMTHF. This result further confirms the high activity of Cu/SiO2-HT-8.5 catalyst for HMF hydrogenolysis. Increasing of the H2 pressure from 0.2 to 1.4 MPa led to the decrease of the DMF yield from 66.8 to 46.5% with a slight increase of DMTHF, indicating that high H2 pressure in favor of the hydrogenation of furan ring, leading to a decline of DMF yield.
The stability of a catalyst is an important factor to evaluate its prospect for industrial application. Therefore, the cycle stability of Cu/SiO2-HT-8.5 catalyst for HMF hydrohydrolysis was also investigated under the optimal reaction conditions (200oC, 0.6 MPa, 8 h). After the first run, the catalyst was separated from the liquid phase by centrifugation, washed with THF, dried and re-used directly for the second run. No obvious activity loss was found after five successive runs and the total yield of DMF and DMTHF maintain close to the values as the first run (Figure 5), revealing the high stability and recyclability of Cu/SiO2-HT-8.5 catalyst. These results suggest that the high dispersion of Cu species with smaller Cu particle offers not only high activity for HMF hydrogenolysis, but also high catalyst stability.
FIGURE 5. The cycle stability test for HMF hydrogenolysis over Cu/SiO2-HT-8.5 catalyst. Reaction conditions: 0.05 g HMF, 0.05 g catalyst, 100 µL tridecane, 5 ml THF, 200°C, 0.6 MPa, 8 h.
In summary, we have studied the structure-activity relationships of four Cu/SiO2 catalysts prepared by different method for HMF hydrogenolysis. It was demonstrated that Cu/SiO2-HT-8.5 catalyst prepared by hydrothermal method showed the best catalytic activity in HMF hydrohydrolysis reaction. Under the optimal reaction condition, the total yield of liquid fuels reaches 91.6% with 57.1% yield of DMF and 34.5% yield of DMTHF in THF solvent. A combination of multiple characterization revealed that the Cu particles in the Cu/SiO2-HT-8.5 catalyst have uniform size and high dispersion. The Cu species and the SiO2 support have relatively weak interaction and are easy to be reduced to Cu0, which makes it an excellent catalyst for the hydrogenolysis of HMF. This work provides a new possibility for cheap monometallic catalyst design for biomass valorization.
The original contributions presented in the study are included in the article/supplementary material, further inquiries can be directed to the corresponding authors.
HJ: Writing-original draft, Writing-review and editing. QL: Data curation, Visualization. QX: Methodology, Writing-review and editing, Funding acquisition. WH: Writing-review and editing. YW: Conceptualization, Supervision, Writing-review and editing, Funding acquisition.
This work was financially supported by the National Natural Science Foundation of China (No. 21972056 and 21832002), Natural Science Foundation of Zhejiang Province (No. LY21B030008) and Technology Development Project of Jiaxing University.
The authors declare that the research was conducted in the absence of any commercial or financial relationships that could be construed as a potential conflict of interest.
All claims expressed in this article are solely those of the authors and do not necessarily represent those of their affiliated organizations, or those of the publisher, the editors and the reviewers. Any product that may be evaluated in this article, or claim that may be made by its manufacturer, is not guaranteed or endorsed by the publisher.
Brzezinska, M., Keller, N., and Ruppert, A. M. (2020). Self-tuned properties of CuZnO catalysts for hydroxymethylfurfural hydrodeoxygenation towards dimethylfuran production. Catal. Sci. Technol. 10 (3), 658–670. doi:10.1039/c9cy01917k
Chen, N., Zhu, Z., Ma, H., Liao, W., and Lü, H. (2020a). Catalytic upgrading of biomass-derived 5-hydroxymethylfurfural to biofuel 2, 5-dimethylfuran over Beta zeolite supported non-noble Co catalyst. Mol. Catal. 486, 110882. doi:10.1016/j.mcat.2020.110882
Chen, S., Ciotonea, C., De Oliveira Vigier, K., Jérôme, F., Wojcieszak, R., Dumeignil, F., et al. (2020b). Hydroconversion of 5‐hydroxymethylfurfural to 2, 5‐dimethylfuran and 2, 5‐dimethyltetrahydrofuran over non‐promoted Ni/SBA‐15. ChemCatChem 12 (7), 2050–2059. doi:10.1002/cctc.201902028
Cui, Y., Chen, X., and Dai, W.-L. (2016). Continuous heterogeneous hydrogenation of CO2-derived dimethyl carbonate to methanol over a Cu-based catalyst. RSC Adv. 6 (73), 69530–69539. doi:10.1039/c6ra14447k
Dong, F., Ding, G. Q., Zheng, H. Y., Xiang, X. M., Chen, L. F., Zhu, Y. L., et al. (2016). Highly dispersed Cu nanoparticles as an efficient catalyst for the synthesis of the biofuel 2-methylfuran. Catal. Sci. Technol. 6 (3), 767–779. doi:10.1039/c5cy00857c
Esteves, L. M., Brijaldo, M. H., Oliveira, E. G., Martinez, J. J., Rojas, H., Caytuero, A., et al. (2020). Effect of support on selective 5-hydroxymethylfurfural hydrogenation towards 2, 5-dimethylfuran over copper catalysts. Fuel 270, 117524. doi:10.1016/j.fuel.2020.117524
Feng, L., Li, X., Lin, Y., Liang, Y., Chen, Y., Zhou, W., et al. (2020). Catalytic hydrogenation of 5-hydroxymethylfurfural to 2, 5-dimethylfuran over Ru based catalyst: Effects of process parameters on conversion and products selectivity. Renew. Energy 160, 261–268. doi:10.1016/j.renene.2020.06.123
Gao, G., Jiang, Z. C., and Hu, C. W. (2021). Selective hydrogenation of the carbonyls in furfural and 5-hydroxymethylfurfural catalyzed by PtNi alloy supported on SBA-15 in aqueous solution under mild conditions. Front. Chem. 9, 759512. doi:10.3389/fchem.2021.759512
Guo, D., Liu, X., Cheng, F., Zhao, W., Wen, S., Xiang, Y., et al. (2020). Selective hydrogenolysis of 5-hydroxymethylfurfural to produce biofuel 2, 5-dimethylfuran over Ni/ZSM-5 catalysts. Fuel 274, 117853. doi:10.1016/j.fuel.2020.117853
Guo, W., Liu, H., Zhang, S., Han, H., Liu, H., Jiang, T., et al. (2016). Efficient hydrogenolysis of 5-hydroxymethylfurfural to 2, 5-dimethylfuran over a cobalt and copper bimetallic catalyst on N-graphene-modified Al2O3. Green Chem. 18 (23), 6222–6228. doi:10.1039/c6gc02630c
Hao, L., Xia, Q., Zhang, Q., Masa, J., and Sun, Z. (2021). Improving the performance of metal-organic frameworks for thermo-catalytic CO2 conversion: Strategies and perspectives. Chin. J. Catal. 42 (11), 1903–1920. doi:10.1016/s1872-2067(21)63841-x
Hu, B., Warczinski, L., Li, X., Lu, M., Bitzer, J., Heidelmann, M., et al. (2021). Formic acid-assisted selective hydrogenolysis of 5-hydroxymethylfurfural to 2, 5-dimethylfuran over bifunctional Pd nanoparticles supported on N-doped mesoporous carbon. Angew. Chem. Int. Ed. 60 (12), 6807–6815. doi:10.1002/anie.202012816
Jing, Y., Guo, Y., Xia, Q., Liu, X., and Wang, Y. (2019). Catalytic production of value-added chemicals and liquid fuels from lignocellulosic biomass. Chem 5 (10), 2520–2546. doi:10.1016/j.chempr.2019.05.022
Kattel, S., Ramirez, P. J., Chen, J. G., Rodriguez, J. A., and Liu, P. (2017). Active sites for CO2 hydrogenation to methanol on Cu/ZnO catalysts. Science 355 (6331), 1296–1299. doi:10.1126/science.aal3573
Kong, X., Zhu, Y., Zheng, H., Zhu, Y., and Fang, Z. (2017). Inclusion of Zn into metallic Ni enables selective and effective synthesis of 2, 5-dimethylfuran from bioderived 5-hydroxymethylfurfural. ACS Sustain. Chem. Eng. 5 (12), 11280–11289. doi:10.1021/acssuschemeng.7b01813
Li, B. L., Li, L. L., Sun, H., and Zhao, C. (2018). Selective deoxygenation of aqueous furfural to 2-methylfuran over Cu-0/Cu2O center dot SiO2 sites via a copper phyllosilicate precursor without extraneous gas. ACS Sustain. Chem. Eng. 6 (9), 12096–12103. doi:10.1021/acssuschemeng.8b02425
Li, F., Cao, B., Ma, R., Liang, J., Song, H., Song, H., et al. (2016). Performance of Cu/TiO2-SiO2 catalysts in hydrogenation of furfural to furfuryl alcohol. Can. J. Chem. Eng. 94 (7), 1368–1374. doi:10.1002/cjce.22503
Li, X., Li, L., Xia, Q., Hong, S., Hao, L., Robertson, A. W., et al. (2022). Selective electroreduction of CO2 and CO to C2H4 by synergistically tuning nanocavities and the surface charge of copper oxide. ACS Sustain. Chem. Eng. 10 (19), 6466–6475. doi:10.1021/acssuschemeng.2c01600
Liu, H., Huang, Z., Han, Z., Ding, K., Liu, H., Xia, C., et al. (2015). Efficient production of methanol and diols via the hydrogenation of cyclic carbonates using copper–silica nanocomposite catalysts. Green Chem. 17 (8), 4281–4290. doi:10.1039/c5gc00810g
Maki-Arvela, P., Ruiz, D., and Murzin, D. Y. (2021). Catalytic hydrogenation/hydrogenolysis of 5-hydroxymethylfurfural to 2, 5-dimethylfuran. ChemSusChem 14 (1), 150–168. doi:10.1002/cssc.202001927
Mhadmhan, S., Franco, A., Pineda, A., Reubroycharoen, P., and Luque, R. (2019). Continuous flow selective hydrogenation of 5-hydroxymethylfurfural to 2, 5-dimethylfuran using highly active and stable Cu–Pd/reduced graphene oxide. ACS Sustain. Chem. Eng. 7 (16), 14210–14216. doi:10.1021/acssuschemeng.9b03017
Mo, L., and Kawi, S. (2014). An in situ self-assembled core–shell precursor route to prepare ultrasmall copper nanoparticles on silica catalysts. J. Mat. Chem. A 2 (21), 7837. doi:10.1039/c3ta14592a
Nakagawa, Y., Tamura, M., and Tomishige, K. (2019). Recent development of production technology of diesel- and jet-fuel-range hydrocarbons from inedible biomass. Fuel Process. Technol. 193, 404–422. doi:10.1016/j.fuproc.2019.05.028
Nakagawa, Y., Tamura, M., and Tomishige, K. (2017). Supported metal catalysts for total hydrogenation of furfural and 5-hydroxymethylfurfural. J. Jpn. Pet. Inst. 60 (1), 1–9. doi:10.1627/jpi.60.1
Nakagawa, Y., Yabushita, M., and Tomishige, K. (2021). Reductive conversion of biomass-derived furancarboxylic acids with retention of carboxylic acid moiety. Trans. Tianjin Univ. 27, 165–179. doi:10.1007/s12209-021-00284-w
Pisal, D. S., and Yadav, G. D. (2021). Production of biofuel 2, 5-dimethylfuran using highly efficient single-step selective hydrogenation of 5-hydroxymethylfurfural over novel Pd-Co/Al-Zr mixed oxide catalyst. Fuel 290, 119947. doi:10.1016/j.fuel.2020.119947
Priecel, P., Endot, N. A., Cara, P. D., and Lopez-Sanchez, J. A. (2018). Fast catalytic hydrogenation of 2, 5-hydroxymethylfurfural to 2, 5-dimethylfuran with ruthenium on carbon nanotubes. Ind. Eng. Chem. Res. 57 (6), 1991–2002. doi:10.1021/acs.iecr.7b04715
Qin, Y., Guo, J., and Zhao, M. (2021). Metal-Organic framework-based solid acid materials for biomass upgrade. Trans. Tianjin Univ. 27, 434–449. doi:10.1007/s12209-021-00298-4
Requies, J. M., Frias, M., Cuezva, M., Iriondo, A., Agirre, I., Viar, N., et al. (2018). Hydrogenolysis of 5-hydroxymethylfurfural to produce 2, 5-dimethylfuran over ZrO2 supported Cu and RuCu catalysts. Ind. Eng. Chem. Res. 57 (34), 11535–11546. doi:10.1021/acs.iecr.8b01234
Rohling, R. Y., Uslamin, E., Zijlstra, B., Tranca, I. C., Filot, N. A. W., Hensen, E. J. M., et al. (2018). An active alkali-exchanged faujasite catalyst for p-xylene production via the one-pot diels-alder cycloaddition/dehydration reaction of 2, 5-dimethylfuran with ethylene. ACS Catal. 8 (2), 760–769. doi:10.1021/acscatal.7b03343
Roman-Leshkov, Y., Barrett, C. J., Liu, Z. Y., and Dumesic, J. A. (2007). Production of dimethylfuran for liquid fuels from biomass-derived carbohydrates. Nature 447 (7147), 982–985. doi:10.1038/nature05923
Shi, G., Yang, L., Liu, Z., Chen, X., Zhou, J., Yu, Y., et al. (2018). Photocatalytic reduction of CO2 to CO over copper decorated g-C3N4 nanosheets with enhanced yield and selectivity. Appl. Surf. Sci. 427, 1165–1173. doi:10.1016/j.apsusc.2017.08.148
Shi, J., Wang, Y., Yu, X., Du, W., and Hou, Z. (2016). Production of 2, 5-dimethylfuran from 5-hydroxymethylfurfural over reduced graphene oxides supported Pt catalyst under mild conditions. Fuel 163, 74–79. doi:10.1016/j.fuel.2015.09.047
Solanki, B. S., and Rode, C. V. (2019). Selective hydrogenation of 5-HMF to 2, 5-DMF over a magnetically recoverable non-noble metal catalyst. Green Chem. 21 (23), 6390–6406. doi:10.1039/c9gc03091c
Talpade, A. D., Tiwari, M. S., and Yadav, G. D. (2019). Selective hydrogenation of bio-based 5-hydroxymethyl furfural to 2, 5-dimethylfuran over magnetically separable Fe-Pd/C bimetallic nanocatalyst. Mol. Catal. 465, 1–15. doi:10.1016/j.mcat.2018.12.009
Tzeng, T.-W., Lin, C.-Y., Pao, C.-W., Chen, J.-L., Nuguid, R. J. G., Chung, P.-W., et al. (2020). Understanding catalytic hydrogenolysis of 5-hydroxymethylfurfural (HMF) to 2, 5-dimethylfuran (DMF) using carbon supported Ru catalysts. Fuel Process. Technol. 199, 106225. doi:10.1016/j.fuproc.2019.106225
Umasankar, S., Tamizhdurai, P., Santhana krishnan, P., Narayanan, S., Mangesh, V. L., Shanthi, K., et al. (2020). Effect of copper on NiCu bimetallic catalyst supported on SBA-16 for the catalytic hydrogenation of 5-hydroxymethylfurfural to 2, 5-dimethylfuran. Biomass Bioenergy 143, 105868. doi:10.1016/j.biombioe.2020.105868
Wang, W. Z., Wang, G. H., Wang, X. S., Zhan, Y. J., Liu, Y. K., Zheng, C. L., et al. (2002). Synthesis and characterization of Cu2O nanowires by a novel reduction route. Adv. Mat. 14 (1), 67–69. doi:10.1002/1521-4095(20020104)14:1<67::aid-adma67>3.0.co;2-z
Wang, Y., Huang, N.-Y., Shen, J.-Q., Liao, P.-Q., Chen, X.-M., Zhang, J.-P., et al. (2018). Hydroxide ligands cooperate with catalytic centers in metal-organic frameworks for efficient photocatalytic CO2 reduction. J. Am. Chem. Soc. 140 (1), 38–41. doi:10.1021/jacs.7b10107
Xia, J., Gao, D., Han, F., Lv, R. F., Waterhouse, G. I. N., Li, Y., et al. (2022). Hydrogenolysis of 5-hydroxymethylfurfural to 2, 5-dimethylfuran over a modified CoAl-hydrotalcite catalyst. Front. Chem. 10, 907649. doi:10.3389/fchem.2022.907649
Xia, Q.-N., Cuan, Q., Liu, X.-H., Gong, X.-Q., Lu, G.-Z., Wang, Y.-Q., et al. (2014). Pd/NbOPO4 multifunctional catalyst for the direct production of liquid alkanes from aldol adducts of furans. Angew. Chem. Int. Ed. 53 (37), 9755–9760. doi:10.1002/anie.201403440
Xiang, S., Dong, L., Wang, Z.-Q., Han, X., Daeman, L. L., Li, J., et al. (2022). A unique Co@CoO catalyst for hydrogenolysis of biomass-derived 5-hydroxymethylfurfural to 2, 5-dimethylfuran. Nat. Commun. 13, 3657. doi:10.1038/s41467-022-31362-9
Xiao, B., Zheng, M. Y., Li, X. S., Pang, J. F., Sun, R. Y., Wang, H., et al. (2016). Synthesis of 1, 6-hexanediol from HMF over double-layered catalysts of Pd/SiO2 + Ir-ReOx/SiO2 in a fixed-bed reactor. Green Chem. 18 (7), 2175–2184. doi:10.1039/c5gc02228b
Yan, K., Jarvis, C., Gu, J., and Yan, Y. (2015). Production and catalytic transformation of levulinic acid: A platform for speciality chemicals and fuels. Renew. Sustain. Energy Rev. 51, 986–997. doi:10.1016/j.rser.2015.07.021
Yang, C. X., Li, X., Zhang, Z. Z., Lv, B. H., Li, J. C., Liu, Z. J., et al. (2020). High efficient catalytic oxidation of 5-hydroxymethylfurfural into 2, 5-furandicarboxylic acid under benign conditions with nitrogen-doped graphene encapsulated Cu nanoparticles. J. Energy Chem. 50, 96–105. doi:10.1016/j.jechem.2020.03.003
Yang, P., Cui, Q., Zu, Y., Liu, X., Lu, G., Wang, Y., et al. (2015). Catalytic production of 2, 5-dimethylfuran from 5-hydroxymethylfurfural over Ni/Co3O4 catalyst. Catal. Commun. 66, 55–59. doi:10.1016/j.catcom.2015.02.014
Yang, P., Xia, Q., Liu, X., and Wang, Y. (2016). High-yield production of 2, 5-dimethylfuran from 5-hydroxymethylfurfural over carbon supported Ni-Co bimetallic catalyst. J. Energy Chem. 25 (6), 1015–1020. doi:10.1016/j.jechem.2016.08.008
Zhang, Y.-R., Wang, B.-X., Qin, L., Li, Q., and Fan, Y.-M. (2019a). A non-noble bimetallic alloy in the highly selective electrochemical synthesis of the biofuel 2, 5-dimethylfuran from 5-hydroxymethylfurfural. Green Chem. 21 (5), 1108–1113. doi:10.1039/c8gc03689f
Zhang, Z., Wang, C., Gou, X., Chen, H., Chen, K., Lu, X., et al. (2019b). Catalytic in-situ hydrogenation of 5-hydroxymethylfurfural to 2, 5-dimethylfuran over Cu-based catalysts with methanol as a hydrogen donor. Appl. Catal. A General 570, 245–250. doi:10.1016/j.apcata.2018.11.029
Zheng, S., Zhu, K., Li, W., and Ji, Y. (2017). Hydrogenation of dimethyl malonate to 1, 3-propanediol catalyzed by a Cu/SiO2 catalyst: The reaction network and the effect of Cu+/Cu0 on selectivity. New J. Chem. 41 (13), 5752–5763. doi:10.1039/c6nj03960j
Zhu, C., Wang, H., Li, H., Cai, B., Lv, W., Cai, C., et al. (2019). Selective hydrodeoxygenation of 5-hydroxymethylfurfural to 2, 5-dimethylfuran over alloyed Cu−Ni encapsulated in biochar catalysts. ACS Sustain. Chem. Eng. 7 (24), 19556–19569. doi:10.1021/acssuschemeng.9b04645
Zhu, Y., Kong, X., Zheng, H., Ding, G., Zhu, Y., Li, Y.-W., et al. (2015). Efficient synthesis of 2, 5-dihydroxymethylfuran and 2, 5-dimethylfuran from 5-hydroxymethylfurfural using mineral-derived Cu catalysts as versatile catalysts. Catal. Sci. Technol. 5 (8), 4208–4217. doi:10.1039/c5cy00700c
Keywords: 5-hydroxymethylfurfural, 2,5-dimethylfuran, renewable fuels, hydrogenolysis, Cu/SiO2 catalyst
Citation: Jia H, Lv Q, Xia Q, Hu W and Wang Y (2022) Tailoring the catalytic performance of Cu/SiO2 for hydrogenolysis of biomass-derived 5-hydroxymethylfurfural to renewable fuels. Front. Chem. 10:979353. doi: 10.3389/fchem.2022.979353
Received: 27 June 2022; Accepted: 11 July 2022;
Published: 22 August 2022.
Edited by:
Honglei Fan, Chinese Academy of Sciences, ChinaCopyright © 2022 Jia, Lv, Xia, Hu and Wang. This is an open-access article distributed under the terms of the Creative Commons Attribution License (CC BY). The use, distribution or reproduction in other forums is permitted, provided the original author(s) and the copyright owner(s) are credited and that the original publication in this journal is cited, in accordance with accepted academic practice. No use, distribution or reproduction is permitted which does not comply with these terms.
*Correspondence: Qineng Xia, eGlhcWluZW5nMTU5QDE2My5jb20=; Yanqin Wang, d2FuZ3lhbnFpbkBlY3VzdC5lZHUuY24=
†These authors have contributed equally to this work and share first authorship
Disclaimer: All claims expressed in this article are solely those of the authors and do not necessarily represent those of their affiliated organizations, or those of the publisher, the editors and the reviewers. Any product that may be evaluated in this article or claim that may be made by its manufacturer is not guaranteed or endorsed by the publisher.
Research integrity at Frontiers
Learn more about the work of our research integrity team to safeguard the quality of each article we publish.