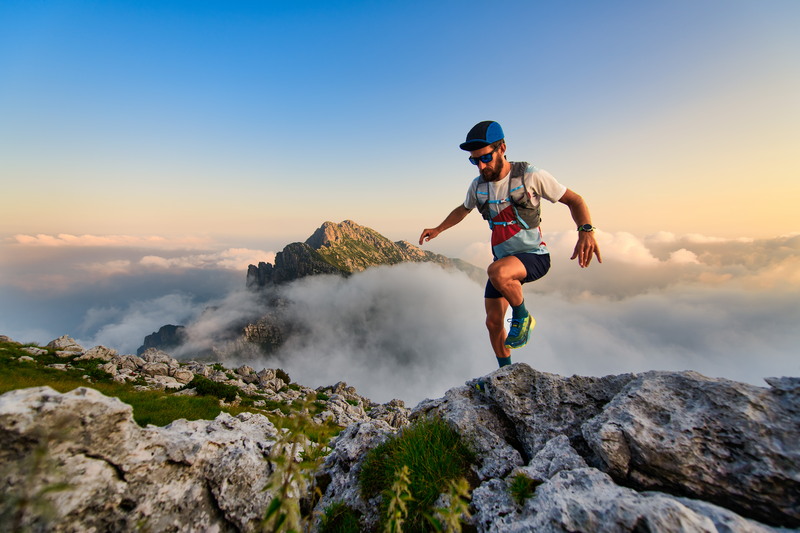
95% of researchers rate our articles as excellent or good
Learn more about the work of our research integrity team to safeguard the quality of each article we publish.
Find out more
ORIGINAL RESEARCH article
Front. Chem. , 03 June 2022
Sec. Inorganic Chemistry
Volume 10 - 2022 | https://doi.org/10.3389/fchem.2022.900962
This article is part of the Research Topic Inorganic Materials for Energy and Environmental Catalysis View all 18 articles
Nitrate pollution is already a global problem, and the electrocatalytic reduction of nitrate is a promising technology for the remediation of wastewater and polluted water bodies. In this work, Co3O4/Ti electrodes were prepared by electrodeposition for the electrocatalytic reduction of nitrate. The morphology, chemical, and crystal structures of Co3O4/Ti and its catalytic activity were investigated. Then, the electrocatalytic nitrate reduction performance of Co3O4/Ti as the cathode was evaluated by monitoring the removal efficiencies of nitrate (NO3−-N) and total nitrogen (TN), generation of reduction products, current efficiency (CE), and energy consumption (EC) at different operating conditions. Under the catalysis of Co3O4/Ti, NO3− was reduced to N2 and NH4+, while no NO2− was produced. After the introduction of chloride ions and IrO2-RuO2/Ti as the anode, NH4+ was selectively oxidized to N2. The removal efficiencies of NO3−-N (at 100 mg/L) and TN after 2 h were 91.12% and 60.25%, respectively (pH 7.0; Cl− concentration, 2000 mg/L; current density, 15 mA/cm2). After 4 h of operation, NO3−-N and TN were completely removed. However, considering the EC and CE, a 2-h reaction was the most appropriate. The EC and CE were 0.10 kWh/g NO3−N and 40.3%, respectively, and electrocatalytic performance was maintained after 10 consecutive reduction cycles (2 h each). The cathode Co3O4/Ti, which is prepared by electrodeposition, can effectively remove NO3−-N, with low EC and high CE.
Nitrate (NO3−) contamination of surface water and groundwater is a global environmental problem associated with increasing populations, and its hazards have attracted much attention (Jasper et al., 2014; Khalil et al., 2016; Serio et al., 2018). The accumulation of plant nutrients such as NO3− and phosphate in water can accelerate eutrophication, a process that increases the biomass of a water body as its biological diversity decreases, for example, due to increases in invertebrates and fish. In the extreme, a state of hypoxia can exist, resulting in the loss of the aquatic ecosystems (Kubicz et al., 2018; Zhang et al., 2021). Although NO3− is chemically stable, it can be microbially reduced to reactive nitrite in the oral cavity and stomach, which has been linked to liver damage, methemoglobinemia, and cancer in animals (Spalding and Exner, 1993; Elmidaoui et al., 2001; Barakat et al., 2020).
Currently, microbial denitrification is widely used for the large-scale remediation of NO3− pollution (Clauwaert et al., 2007; Della Rocca and Belgiorno V Meriç, 2007). Many other methods of NO3− removal have been explored such as reverse osmosis, ion exchange, ammonia stripping, electrodialysis, catalytic reduction, and electrocatalytic reduction (Kapoor and Viraraghavan, 1997; Yang and Lee, 2005; Della Rocca and Belgiorno V Meriç, 2007). Among these techniques, the electrocatalytic reduction of NO3− is a promising and clean technology because the electron reductants neither introduce pollutants nor adversely affect the environment (Garcia-Segura et al., 2018; Gayen et al., 2018).
The mechanism of the electrochemical NO3− reduction reaction (NO3−-RR) involves anodic oxidation and cathodic reduction in which NO3− is reduced to NO2−, NH4+, and N2 on the active sites of the cathode according to Eqs 1–3 (Zhang et al., 2021):
The choice of the cathode material is important in this process. To date, most studies have used high-cost noble metal cathodes, such as Pt, Rh, and Pd, which may limit their commercial application (Taguchi and Feliu, 2007; Yang et al., 2014; Soto-Hernández et al., 2019). Co3O4 is a cost-effective catalyst, and the preparation of a CuO-Co3O4/Ti electrode by the sol-gel method for electrochemical reduction of NO3− was recently reported (Yang et al., 2020). The system demonstrated the complete removal of NO3− after 3 h at a current density of 20 mA/cm2.
NO2− and NH4+ generated at the cathode (Eqs. (1) and (2)) diffuse to the anode where they are adsorbed onto the surface and subsequently oxidized to NO3− and N2 (Eqs. (4) and (5)) (Zhang et al., 2021):
When Cl− is present in the electrolyte, the following reactions also occur at the anode (Eqs. 6–9) (Zhang et al., 2021):
The electrochemical NO3−-RR involves NO3− reduction at the cathode and ammonium nitrogen (NH4+-N) oxidation at the anode. Cl2 generated at the anode (Eq. (6)) immediately forms hypochlorite (Eq. (7)), which selectively oxidizes NH4+ to N2 (Su et al., 2017). Hence, the efficient anodic oxidation of chloride ions is a key requirement for this process, and the anode materials used in the chlor-alkali industry, which obtain Cl2 by electrolysis of sodium chloride, provide a useful reference (Yi et al., 2007). Among these materials, IrO2-RuO2 is a good choice due to its low overpotential, high chlorine selectivity, and long-term stability (Chen et al., 2007). In addition, the electrocatalytic reduction of NO3−-N is also affected by reaction potential, current, solution pH, battery structure, and anode material.
Here, a catalytic cathode was prepared by the in situ electrodeposition of Co3O4 on a titanium substrate (Co3O4/Ti) to obtain improved electrocatalytic performance. IrO2-RuO2/Ti was employed as the anode for the effective removal of NH4+-N and TN. The aim of this study was to obtain simultaneous electrochemical NO3− reduction and oxidation of the in situ-generated NO2− and NH4+ into N2 gas. The morphology and structure of Co3O4/Ti were characterized using conventional methods, and its performance in NO3− removal was evaluated under different operating conditions. The current efficiency (CE) and energy consumption (EC) of the system were also measured to assess its commercial application.
The Ti mesh and Ti plate (99.5% purity, 0.6 mm, 10 mesh) were purchased from Lanruiyinde Electrochemical Materials Co., Ltd. (China). The Pt plate was obtained from Aidahengsheng Co., Ltd., (Tianjin, China). All chemicals were of analytical grade. Potassium nitrate and sodium hydroxide were purchased from Aladdin Biochemical Technology Co., Ltd. (Shanghai, China). Cobalt nitrate hexahydrate, sodium eicosyl, hexachloroiridic acid, and ruthenium (III) chloride were obtained from Macklin Biochemical Technology Co., Ltd. (Shanghai, China). Solutions were prepared using deionized water (>15 MΩ cm) obtained from an Elix® 3 purification system (Millipore, United States). Simulated wastewater was prepared by adding potassium nitrate to deionized water.
Samples of the Ti mesh and Ti plate (3 × 4 cm, 12 cm2) were degreased with NaOH solution (40 wt%) at 95°C for 2 h before etching by boiling in oxalic acid solution (10 wt%) for 2 h. The treated samples were then rinsed with deionized water and stored in ethanol until further use.
As shown in Figure 1, the Co3O4/Ti electrode was prepared using an electrodeposition method. A three-electrode system was employed in a single compartment cell using the pretreated Ti mesh as the cathode, the Pt plate as the anode, and an Ag/AgCl reference electrode. The electrodeposition solution comprised boric acid (0.5 M), cobalt nitrate hexahydrate (0.1 M), and sodium eicosyl sulfonate (2.0 g/L). Following electrodeposition at a current of 0.25 A for 5 min, the electrode was cleaned with deionized water and oven-dried (60°C) before heating at 5°C/min to 500°C (hold 2 h) in a muffle furnace to effect calcination. The treated samples were allowed to cool naturally to room temperature.
The IrO2-RuO2/Ti anode was prepared by using a thermal decomposition method. A mixed solution of hexachloroiridic acid and ruthenium (III) chloride in n-butanol (molar ratio, 2:1) was evenly coated onto the surfaces of the pretreated titanium plate, dried at 105°C for 10 min, and then calcined at 500°C for 15 min. The process was repeated until the weight of the titanium plate increased by about 10 g/cm2. Finally, the electrode was washed with deionized water before use.
Surface morphology and elemental composition were studied by field-emission scanning electron microscopy (SEM) and energy-dispersive X-ray spectroscopy (EDS) on a Phenom ProX system (Thermo Fisher Scientific, United States) at an accelerating voltage of 15 kV. The crystal structure of Co3O4 was examined by X-ray diffraction (XRD) with an X’pert Powder system (Malvern Panalytical, Malvern, UK) using Cu Kα (λ = 1.5406 Å) irradiation.
NO3−-RR tests were performed in a single chamber electrolytic cell (200 ml) using a three-electrode system, with Co3O4/Ti (or Ti as required), Pt plate, and Ag/AgCl as the working, counter, and reference electrodes, respectively. The electrolyte was prepared using Na2SO4 (0.1 M) and different concentrations of NO3−-N (KNO3) as required. Linear sweep voltammetry (LSV), and electrolysis tests were performed in an electrochemical workstation (Metrohm Autolab M204, Switzerland). Prior to the electrochemical test, oxygen was removed by bubbling high-purity N2 through the electrolyte for ≥20 min, and continuously fed during the experiments.
Electrolysis measurements were performed at an optimum current density of 15 mA/cm2, and aliquots of the reaction solutions (2 ml) were removed at predetermined time intervals to measure the concentrations of NO3−-N, NO2−-N, and NH4+-N. The effects of chlorine on NO3−-RR and the stability of the Co3O4/Ti cathode electrode were assessed at a current density of 15 mA/cm2 for 2 h and an initial NO3−-N concentration of 100 mg/L.
During the NO3−-RR, the formation of NO, N2O, and NH3 are negligible, and hence, the generated gaseous products can be considered as N2 (Teng et al., 2018). UV-Vis spectroscopy was used to measure the concentrations of NO3−-N, NO2−-N, NH4+-N, and total nitrogen (TN) (Evolution 201, Thermofisher Scientific Co., Ltd.), and their removal efficiencies were calculated according to Eqs (10)–(12):
where C0(NO3−-N) (mg/L) is the initial concentration of NO3−-N, Ct(NO3−-N) (mg/L) is the concentration of NO3−-N at time t, Ct(NH4+-N) (mg/L) is the concentration of NH4+-N at time t, C0(TN) (mg/L) is the initial concentration of TN, and Ct(TN) (mg/L) is the concentration of TN at time t.
EC was calculated using Eq. 13 (Zhang et al., 2016):
where U is the cell potential (V), I is the current (A), t is the reaction time (h), and V is the volume of reaction solution (L).
The CE for TN removal rates was obtained using Eq. 14:
where M is the molar mass of N (14 g/mol), Q is the amount of electricity passing through the electrode, and n is the number of electrons obtained from the complete reduction of NO3−-N (calculated according to the conversion of NO3− to N, n = 5).
SEM was used to depict the electrode surface morphology of Co3O4/Ti. Figure 2 shows that spherical particles (3–5 μm) of Co3O4 were observed on the surface of Co3O4/Ti at different magnifications, confirming its deposition on the Ti mesh. SEM-EDS elemental mapping of a surface region of the Co3O4/Ti cathode (Figure 3) gave a value of 26.26 atom% for Co, indicating that the element was successfully deposited on the titanium mesh.
Figure 4 shows the XRD patterns of the calcined Co3O4/Ti electrode and their comparison with the reference powder patterns of cubic phase Co3O4 (PDF#42–1467) and Ti (PDF#44–1294). The characteristic peaks observed at 2θ of 35.1°, 38.4°, 40.2°, 53.0°, 62.9°, 70.7°, 76.2°, and 77.4° correspond to (100), (002), (101), (102), (110), (103), (112), and (201) planes of Ti (PDF#44–1294), respectively (Figure 4A). Inspection of the enlarged pattern obtained from the Co3O4/Ti cathode (Figure 4B) showed that the main peaks of Co3O4 at 2θ=31.3°, 36.9°, 44.8°, 59.4°, 65.2°, and 74.1°, correspond to the (220), (311), (400), (511), (440), and (620) planes of Co3O4, respectively. These results were in good agreement with the standard cubic phase (PDF#42–1467).
FIGURE 4. Crystal structure of Co3O4/Ti cathode and comparison with the reference XRD powder patterns: (A) XRD patterns of Ti and Co3O4/Ti cathodes; (B) enlarged XRD patterns of Co3O4/Ti cathode.
LSV was used to evaluate the electrocatalytic performance of the catalysts toward NO3−-RR. Figure 5A shows the LSV curves obtained with Co3O4/Ti and Ti in the presence of NO3−-N. The onset potential for NO3−-RR using the Co3O4/Ti cathode (-0.7 V) was more positive than that using the Ti mesh (-1.0 V), indicating the improved performance with the composite catalyst. From −0.7 to −1.6 V, Co3O4/Ti gave a larger current response at all potentials due to its higher activity toward the NO3−-RR compared with the Ti mesh. Figure 5B shows the effects of increasing NO3−-N (0–500 mg/L) using Co3O4/Ti as the cathode. In the absence of NO3−-N, the onset potential (i.e., for the electrolysis of water to produce H2) was −0.9 V. The addition of NO3− produced a positive shift in the onset potential, and the corresponding current increased with increasing initial NO3−-N due to the enhanced reduction reaction activity.
FIGURE 5. LSV curves illustrating the NO3−-N removal performance of the catalysts (0.1 M Na2SO4, 10 mV/s). (A) Effects of different catalysts at constant initial NO3−-N concentration (100 mg/L). (B) Effects of increasing initial NO3−-N concentrations using the Co3O4/Ti cathode.
To determine the effect of Co3O4 on NO3−RR activity, the NO3−-N (100 mg/L) removal efficiencies of the Co3O4/Ti and Ti mesh cathodes were compared at a current density of 15 mA/cm2 with a Pt plate as the anode (Figure 6). The results showed that the Co3O4/Ti cathode could achieve a NO3−-N removal efficiency of ∼98% in 2 h, compared with 6.4% using the Ti mesh, demonstrating the important role of Co3O4 in improving the performance of NO3−-RR.
FIGURE 6. Removal efficiencies of NO3−-N by the Ti and Co3O4/Ti cathodes (Pt anode; [NO3−-N], 100 mg/L, 150 ml; current density, 15 mA/cm2; pH, 7.0; reaction time, 2 h).
Figure 7A,B show the rate of NO3−-N removal using the Co3O4/Ti cathode and the corresponding fit of the experimental data to first-order kinetics. The increased removal efficiency with increasing current density over 5–15 mA/cm2 could be attributed to enhanced electron transfer on the electrode surface of Co3O4/Ti, which increased the rate of NO3−-RR. However, when the current density was increased from 15 to 20 mA/cm2, the removal efficiency of NO3−-N did not improve significantly. At higher current densities, the competing hydrogen evolution reaction consumes the extra charge, and the NO3−-N removal efficiency decreases. Figure 7C shows that there was good correspondence between the reduction of NO3−-N and the generation of NH4+-N. The reduction products were NH4+-N and N2, while NO2−-N was not detected (Figure 7D).
FIGURE 7. Effects of current density on the NO3−-RR using the Co3O4/Ti cathode (Pt anode; [NO3−-N], 100 mg/L, 150 ml; initial pH, 7.0; reaction time, 2 h): (A) and (B) rate of loss of NO3−-N and the fit of the data to first-order kinetics; (C) rate of generation of NH4+-N; and (D) distribution of the products formed.
The effects of initial NO3−N concentration on its removal efficiency using the Co3O4/Ti cathode and the generation of reduction products are shown in Figure 8. At initial NO3−-N concentrations of <100 mg/L, the removal efficiency of the system was close to 100% at 2 h; and the corresponding reduction products were NH4+-N (60%) and N2. At an initial NO3−-N concentration of 200 mg/L, the removal efficiency decreased to ∼58%, while the NH4+-N generation efficiency increased to ∼79%. Under this condition, the higher initial NO3−-N concentration suppressed the competing hydrogen evolution reaction, thus reducing its charge consumption at the electrode.
FIGURE 8. Effects of different initial NO3−-N concentrations on NO3−-RR using the Co3O4/Ti cathode (Pt anode; reaction solution, 150 ml; current density, 15 mA/cm2; initial pH, 7.0; reaction time, 2 h): (A) and (B) Rate of loss of NO3−-N and the fit of the data to first-order kinetics; (C) generation of NH4+-N; and (D) product distributions.
The main product of electrocatalytic NO3− reduction is NH4+, which is also a contaminant requiring removal. However, in the presence of Cl−, which is widely present in drinking water and industrial water, the active species participating in the oxidative transformation of NH4+-N to N2 at the anode (Eqs 6–9) will increase TN removal. The IrO2-RuO2/Ti electrode is widely employed in the chlor-alkali industry because of its high chlorine evolution performance. To investigate the effects of Cl− on NH4+-N generation and NO3−-N removal, various concentrations of Cl− were presented to a Co3O4/Ti/IrO2-RuO2/Ti NO3−-N removal system (Table 1). As the concentration of Cl− increased from 0 to 2000 mg/L, the removal efficiencies of NO3−-N were all >90%. At 4,000 mg/L Cl−, the removal efficiency decreased to 83.99% due to the oxidation of NH4+ to NO3− by HClO/ClO−. The increase in Cl− concentration increased the amount of HClO/ClO− generated by anodic oxidation to reduce NH4+-N to N2. Hence, NH4+-N generation decreased and TN removal efficiency increased with increasing Cl− concentration. The TN removal efficiency reached 78.1% with negligible NH4+-N generation (0.34%) and without NO2−-N accumulation.
In addition to the initial activity, the long-term performance of a catalyst is an essential requirement for its commercial application. Figure 9 shows the changes in NO3−-N removal and distribution of generated products over 4 h, and 10 consecutive cycles of 2 h each, using the system. At an initial concentration of 100 mg/L, almost all NO3−-N is converted into N2 after 4 h (Figure 9A). After 10 cycles (Figure 9B), the removal efficiencies of NO3−-N (∼90%) and TN remained unchanged.
FIGURE 9. Changes in NO3−-N removal and the distribution of generated products for the Co3O4/Ti/IrO2-RuO2/Ti system ([NO3−-N], 100 mg/L, 150 ml; current density, 15 mA/cm2; pH, 7.0; cycle time, 2 h). (A) Changes over 4 h. (B) Changes over 10 cycles.
EC and CE are key evaluation factors for the commercial electrochemical treatment process (Zeng et al., 2020). The EC and CE under different process conditions using the system were calculated. It can be seen from Figure 10A,B that within 1 h after the start of the reaction, EC is lower and CE is higher than those of the follow-up experiments, but the NO3−-N removal rate is only 58.52%. After 2 h, the NO3−-N removal efficiency reaches 93.39% with an EC of 0.10 kW h/g NO3−-N and a CE of 40.3%. There was no significant improvement in the follow-up, but the EC continued to rise, and the CE continued to decline.
FIGURE 10. Effects of reaction time and initial NO3−-N concentrations on the operational efficiency. (A) and (C) EC; (B) and (D) CE (pH, 7.0; current density, 15 mA/cm2; [Cl−], 2000 mg/L; reaction time, 2 h).
The effect of the initial NO3−-N concentration is demonstrated in Figures 10C,D. As the NO3−-N concentration increased, the EC decreased and CE increased. This can be explained by the increase in the contact area between NO3−-N and the electrode surface with increasing concentrations, which promotes the reduction reaction. From an economic viewpoint, the results indicate that the Co3O4/Ti/IrO2-RuO2/Ti electrocatalytic process is more suitable for wastewater with high concentrations of NO3−. The small amount of NO3− remaining in the electrochemically treated wastewater can be removed by other processes, such as the electrocatalytic removal of NO3−-N, which can be combined with constructed wetlands for wastewater control/remediation.
A Co3O4/Ti electrode was successfully prepared by electrodeposition, and the material showed good electrocatalytic performance toward NO3−-RR. At an initial concentration of 100 mg/L NO3−-N, the removal rate was ∼98% in 2 h (Pt anode; pH, 7.0; current density, 15 mA/cm2). The corresponding generation of NH4+-N was ∼60%, while NO2−-N was not detected. When IrO2-RuO2/Ti was employed as the anode in the presence of Cl− (2000 mg/L), the removal efficiencies for NO3−-N and TN under the same operating conditions were ∼91% and ∼60%, respectively, with an EC of 0.10 kW h/g NO3−-N and a CE of 40.3%. After 4 h of continuous operation, 100% of NO3−-N was converted into N2. In addition, the system could maintain the removal efficiencies of ∼90% and ∼60% for NO3−-N and TN, respectively, after 10 consecutive cycles (2 h each). This work provides a simple preparation method of electrodeposited Co3O4/Ti with good catalytic performance and stability, which provides a new preparation strategy for the Co3O4 catalytic electrode.
The original contributions presented in the study are included in the article/Supplementary Material, further inquiries can be directed to the corresponding author.
CW: conceptualization, methodology, data analysis, and writing—original draft. ZC: data curation. HH: validation. HL: resources and funding acquisition. SW: conceptualization, investigation, and writing—review and editing.
This work was supported by the National Natural Science Foundation of China (grant numbers 51978181, 51808527, 51727812, and 52131003).
The authors declare that the research was conducted in the absence of any commercial or financial relationships that could be construed as a potential conflict of interest.
All claims expressed in this article are solely those of the authors and do not necessarily represent those of their affiliated organizations, or those of the publisher, the editors, and the reviewers. Any product that may be evaluated in this article, or claim that may be made by its manufacturer, is not guaranteed or endorsed by the publisher.
Barakat, A., Mouhtarim, G., Saji, R., and Touhami, F. (2020). Health Risk Assessment of Nitrates in the Groundwater of Beni Amir Irrigated Perimeter, Tadla Plain, Morocco. Hum. Ecol. Risk Assess. Int. J. 26 (7), 1864–1878. doi:10.1080/10807039.2019.1613631
Chen, J., Shi, H., and Lu, J. (2007). Electrochemical Treatment of Ammonia in Wastewater by RuO2-IrO2-TiO2/Ti Electrodes. J. Appl. Electrochem 37 (10), 1137–1144. doi:10.1007/s10800-007-9373-6
Clauwaert, P., Rabaey, K., Aelterman, P., De Schamphelaire, L., Pham, T. H., Boeckx, P., et al. (2007). Biological Denitrification in Microbial Fuel Cells. Environ. Sci. Technol. 41 (9), 3354–3360. doi:10.1021/es062580r
Della Rocca, C., Belgiorno V, , and Meriç, S. (2007). Overview of In-Situ Applicable Nitrate Removal Processes. Desalination J. 204 (1), 46–62. doi:10.1016/j.desal.2006.04.023
Elmidaoui, A., Elhannouni, F., Menkouchi Sahli, M. A., Chay, L., Elabbassi, H., Hafsi, M., et al. (2001). Pollution of Nitrate in Moroccan Ground Water: Removal by Electrodialysis. Desalination J. 136 (1), 325–332. doi:10.1016/s0011-9164(01)00195-3
Garcia-Segura, S., Lanzarini-Lopes, M., Hristovski, K., and Westerhoff, P. (2018). Electrocatalytic Reduction of Nitrate: Fundamentals to Full-Scale Water Treatment Applications. Appl. Catal. B Environ. 236, 546–568. doi:10.1016/j.apcatb.2018.05.041
Gayen, P., Spataro, J., Avasarala, S., Ali, A.-M., Cerrato, J. M., and Chaplin, B. P. (2018). Electrocatalytic Reduction of Nitrate Using Magnéli Phase TiO2 Reactive Electrochemical Membranes Doped with Pd-Based Catalysts. Environ. Sci. Technol. 52 (16), 9370–9379. doi:10.1021/acs.est.8b03038
Jasper, J. T., Jones, Z. L., Sharp, J. O., and Sedlak, D. L. (2014). Nitrate Removal in Shallow, Open-Water Treatment Wetlands. Environ. Sci. Technol. 48 (19), 11512–11520. doi:10.1021/es502785t
Kapoor, A., and Viraraghavan, T. (1997). Nitrate Removal from Drinking Water-Review. J. Environ. Eng. 123 (4), 371–380. doi:10.1061/(asce)0733-9372(1997)123:4(371)
Khalil, A. M. E., Eljamal, O., Jribi, S., and Matsunaga, N. (2016). Promoting Nitrate Reduction Kinetics by Nanoscale Zero Valent Iron in Water via Copper Salt Addition. Chem. Eng. J. 287, 367–380. doi:10.1016/j.cej.2015.11.038
Kubicz, J., Pawełczyk, A., and Lochyński, P. (2018). Environmental Health Risk Posed by Contamination of the Individual Water Wells. Chemosphere 208, 247–256. doi:10.1016/j.chemosphere.2018.05.182
Serio, F., Miglietta, P. P., Lamastra, L., Ficocelli, S., Intini, F., De Leo, F., et al. (2018). Groundwater Nitrate Contamination and Agricultural Land Use: A Grey Water Footprint Perspective in Southern Apulia Region (Italy). Sci. Total Environ. 645, 1425–1431. doi:10.1016/j.scitotenv.2018.07.241
Soto-Hernández, J., Santiago-Ramirez, C. R., Ramirez-Meneses, E., Luna-Trujillo, M., Wang, J-A., Lartundo-Rojas, L., et al. (2019). Electrochemical Reduction of NOx Species at the Interface of Nanostructured Pd and PdCu Catalysts in Alkaline Conditions. Appl. Catal. B Environ. J. 259, 118048.
Spalding, R. F., and Exner, M. E. (1993). Occurrence of Nitrate in Groundwater-A Review. J. Environ. Qual. 22 (3), 392–402. doi:10.2134/jeq1993.00472425002200030002x
Su, L., Li, K., Zhang, H., Fan, M., Ying, D., Sun, T., et al. (2017). Electrochemical Nitrate Reduction by Using a Novel Co 3 O 4/Ti Cathode. Water Res. 120, 1–11. doi:10.1016/j.watres.2017.04.069
Taguchi, S., and Feliu, J. M. (2007). Electrochemical Reduction of Nitrate on Pt(S)[n(111)×(111)] Electrodes in Perchloric Acid Solution. Electrochimica Acta 52 (19), 6023–6033. doi:10.1016/j.electacta.2007.03.057
Teng, W., Bai, N., Liu, Y., Liu, Y., Fan, J., and Zhang, W.-x. (2018). Selective Nitrate Reduction to Dinitrogen by Electrocatalysis on Nanoscale Iron Encapsulated in Mesoporous Carbon. Environ. Sci. Technol. 52 (1), 230–236. doi:10.1021/acs.est.7b04775
Yang, G. C. C., and Lee, H.-L. (2005). Chemical Reduction of Nitrate by Nanosized Iron: Kinetics and Pathways. Water Res. 39 (5), 884–894. doi:10.1016/j.watres.2004.11.030
Yang, J., Sebastian, P., Duca, M., Hoogenboom, T., and Koper, M. T. M. (2014). pH Dependence of the Electroreduction of Nitrate on Rh and Pt Polycrystalline Electrodes. Chem. Commun. 50 (17), 2148–2151. doi:10.1039/c3cc49224a
Yang, M., Wang, J., Shuang, C., and Li, A. (2020). The Improvement on Total Nitrogen Removal in Nitrate Reduction by Using a Prepared CuO-Co3O4/Ti Cathode. Chemosphere 255, 126970. doi:10.1016/j.chemosphere.2020.126970
Yi, Z., Kangning, C., Wei, W., Wang, J., and Lee, S. (2007). Effect of IrO2 Loading on RuO2-IrO2-TiO2 Anodes: A Study of Microstructure and Working Life for the Chlorine Evolution Reaction. Ceram. Int. 33 (6), 1087–1091. doi:10.1016/j.ceramint.2006.03.025
Zeng, Y., Priest, C., Wang, G., and Wu, G. (2020). Restoring the Nitrogen Cycle by Electrochemical Reduction of Nitrate: Progress and Prospects. Small Methods 4, 2000672. doi:10.1002/smtd.202000672
Zhang, X., Wang, Y., Liu, C., Yu, Y., Lu, S., and Zhang, B. (2021). Recent Advances in Non-Noble Metal Electrocatalysts for Nitrate Reduction. Chem. Eng. J. 403, 126269. doi:10.1016/j.cej.2020.126269
Keywords: nitrate removal, electrocatalytic, Co3O4/Ti, reduction, IrO2-RuO2
Citation: Wang C, Cao Z, Huang H, Liu H and Wang S (2022) Electrocatalytic Reduction of Nitrate via Co3O4/Ti Cathode Prepared by Electrodeposition Paired With IrO2-RuO2 Anode. Front. Chem. 10:900962. doi: 10.3389/fchem.2022.900962
Received: 21 March 2022; Accepted: 19 April 2022;
Published: 03 June 2022.
Edited by:
Qingyi Zeng, University of South China, ChinaReviewed by:
Huawei Song, Sun Yat-sen University, ChinaCopyright © 2022 Wang, Cao, Huang, Liu and Wang. This is an open-access article distributed under the terms of the Creative Commons Attribution License (CC BY). The use, distribution or reproduction in other forums is permitted, provided the original author(s) and the copyright owner(s) are credited and that the original publication in this journal is cited, in accordance with accepted academic practice. No use, distribution or reproduction is permitted which does not comply with these terms.
*Correspondence: Sha Wang, d2FuZ3NoYUBjaWdpdC5hYy5jbg==
Disclaimer: All claims expressed in this article are solely those of the authors and do not necessarily represent those of their affiliated organizations, or those of the publisher, the editors and the reviewers. Any product that may be evaluated in this article or claim that may be made by its manufacturer is not guaranteed or endorsed by the publisher.
Research integrity at Frontiers
Learn more about the work of our research integrity team to safeguard the quality of each article we publish.