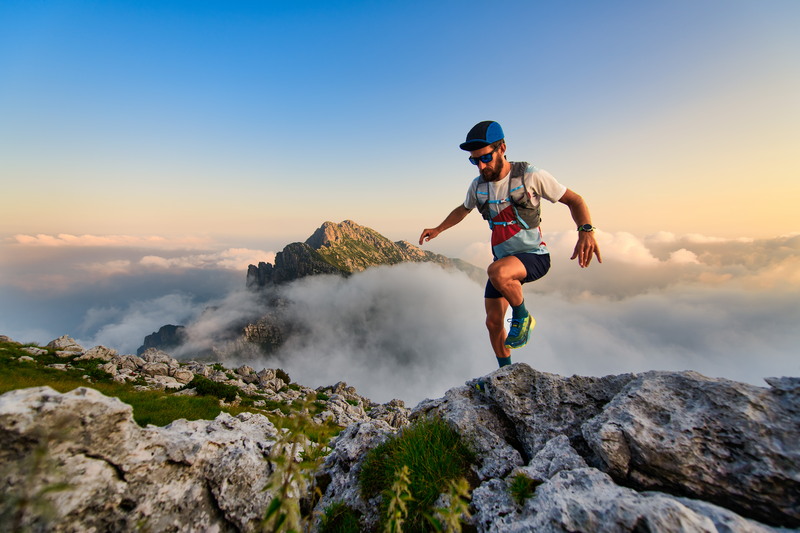
95% of researchers rate our articles as excellent or good
Learn more about the work of our research integrity team to safeguard the quality of each article we publish.
Find out more
ORIGINAL RESEARCH article
Front. Chem. , 15 September 2022
Sec. Supramolecular Chemistry
Volume 10 - 2022 | https://doi.org/10.3389/fchem.2022.1008884
Petrochemical excess sludge, as hazardous solid waste, poses a great threat to the environment and is difficult to dispose of in an economic and environmentally friendly way. A new alternative of using the petrochemical excess sludge to prepare ceramsite is proposed. The relationship between the sintering behavior of dried excess sludge, including the composition, temperature, fluxing agent, and pore-forming agent addition, and the properties of ceramsite is investigated. The properties of ceramsite are primarily affected by the sintering temperature and the addition of a fluxing agent. Ceramsite with a sintering-expanded surface is prepared. Also, its water absorption is quite low, indicating an improvement in densification due to sintering. Moreover, the leaching toxicity of the heavy metals in the dried excess sludge and prepared ceramsite is also investigated. It reveals the feasibility of ceramsite preparation by sintering petrochemical excess sludge.
The petrochemical industry brings about a great deal of energy and convenience for the development of human beings. Meanwhile, the petrochemical industry also produces a large quantity of solid waste, which induces a great environmental hazard to human beings if not properly disposed of (Abouelnasr and Isam, 2008; Elektorowicz and Habibi, 2005; Heidarzadeh et al., 2010; Begum et al., 2013; Hu et al., 2015; Qin et al., 2017; Fabio et al., 2018; Moško et al., 2018). For instance, an annual production of more than one million tons of petrochemical oily waste from a variety of sources, including crude oil tank bottoms, oil/water separators, and on-site wastewater treatment plants, is generated by the petrochemical industry in China (Hu et al., 2013). Among the solid oily waste produced, the excess sludge as an inevitable by-product from the petrochemical on-site wastewater treatment plant accounts for the largest portion. For instance, a ten-million-ton oil refinery plant produces about 10,000 m3/a excess sludge, and a one-million-ton ethylene plant produces more than 40,000 m3/a excess sludge.
The petrochemical excess sludge is a complicated mixture containing different quantities of waste mineral oil, such as benzene, xylene, pyrene, and petroleum hydrocarbon; heavy metals such as Pb, V, and Ni; and mineral matter. Some of the chemicals are toxic, carcinogenic, and mutagenic. Therefore, excess sludge is referred to as one kind of hazardous solid waste in most cases (Guo et al., 2019). Due to its adverse nature, a variety of methods have been applied to treat petrochemical excess sludge, such as thermal drying, pyrolysis, incineration, or landfills at hazardous waste sites (Elektorowicz and Habibi, 2005; Hu et al., 2013; Guo et al., 2019). However, these technologies have problems such as secondary pollution, especially the disposal of residue fly ash after incineration, and land occupation of the landfill treatment.
A similar occurrence is that excess sludge in the municipal wastewater treatment plant is becoming a critical environmental threat due to the treatment required for the enormous increase in the volume of wastewater (Bruno et al., 2022). Among the various treatment approaches for municipal excess sludge, ceramsite prepared from excess sludge, a kind of lightweight aggregate, has been reported and commercialized (Furlani et al., 2011; Li et al., 2018; Liao and Huang, 2012; Wang et al., 2008). For instance, Wang et al. investigated the sintering behavior of dried excess sludge and the related sintering mechanisms (Wang et al., 2008).
In contrast, the ignition loss ratio of the petrochemical excess sludge is between 80% and 90%. This is much higher than that of municipal excess sludge, which is between 40% and 70%. In other words, the content of ash after thermal incineration of the petrochemical excess sludge, which is expected to form the main crystalline matter of the ceramsites, is lower than that of municipal excess sludge. In addition, the content of alkali and alkaline-earth metals in the petrochemical excess sludge is lower than that of municipal excess sludge. The main function of the alkali and alkaline-earth metals during the preparation of ceramsites is to reduce the melting point and thus to prepare the targeted product at a relatively low temperature (Wang et al., 2008).
However, there have been no reports about the preparation of ceramsite from the petrochemical excess sludge. If the petrochemical excess sludge can be used to prepare the ceramsite, the excess sludge can be comprehensively utilized and the ash that would be produced from the incineration of excess sludge is solidified to be the component of ceramsites, which is finally vitrified at ceramsite. The amount of ash or heavy metal that can be extracted from the environment can be dramatically decreased. In addition, the high content of organic matters that would vaporize at a high temperature can generate many pores and be beneficial to the preparation of ceramsites during sintering.
Therefore, the aim of this work is to study the sintering characteristics and behavior of excess sludge produced from the petrochemical wastewater plant under varying sintering conditions, such as different compositions and temperatures. Also, during the sintering, reactions and transformations occur between the silicate and the associated minerals, which result in the formation of various crystalline phases. All, of these transformations and products play a critical role in the properties of ceramsite (Moško et al., 2018; Wang et al., 2008). Thus, the phase and microstructure transformations are also investigated using X-ray diffraction and scanning electron microscopy. Moreover, the leaching behavior of typical heavy metals is included in this article to discuss the environmental safety of the as-prepared products.
The petrochemical excess sludge used in this study was acquired from a petrochemical wastewater treatment plant in Qingdao, China. The excess sludge was first dewatered mechanically via plate-frame pressure filtration, dried in a baking oven at a temperature of 85°C until the weight did not change, and then powdered with a ball mill until it could pass through a 150 mesh sieve. The clay was bought from Shandong Haoyao Co., Ltd. The fluxing agent Na2O (in the form of Na2CO3, analytical grade) and pore-forming agent Fe2O3 were bought from Sinopharm Chemical Reagent Co., Ltd. The powdered excess sludge, clay, and other additions were first thoroughly blended. Spherical specimens with a diameter of around 20 mm were prepared by wet rolling, dried, and subsequently sintered in an electric kiln with sintering temperatures ranging from 1,150 to 1200°C for 15 min. A ramp rate of 15 °C/min and temperature preservation at 350°C for 15 min were used.
The major chemical compositions of excess sludge and the clay, including Si, Al, Ca, Fe, Mg, K, Na, and P, were analyzed using an X-ray fluorescence spectrometer (XRF, Thermo Fisher Scientific ARL QUANT'X EDXRF) after sintering at 1200°C for 15 min, and expressed in the form of oxide. X-ray diffraction (XRD, Bruker D8 Advance) using 40 mA and 40 kV Cu Kα radiation was used for the research of crystalline phases in sintered products. The crystalline phases were examined by comparing the positions of the Bragg peaks with the data files of the Joint Committee on Powder Diffraction Standards (JCPDS). The microstructural morphology was recognized using a scanning electron microscope (SEM, JSM-6460LV).
The leaching toxicity of trace hazardous elements, including Ni, Cd, Pb, Cr, Cu, and V, in excess sludge and sintered product was determined by horizontal vibration extraction procedure (HVEP) according to HJ/T 299-2007 and GB 5085.3-2007 of China (GB5085, 2007; HJ/T299, 2007; Chen et al., 2022). The chosen samples were roughly crushed and pulverized in a laboratory grinding machine for 5 min and then dried in an oven at 80°C until reaching a constant weight. Leaching of the heavy metals: 150 g of pulverized ceramsite was placed in a Teflon bottle. Then, an acid solution with a pH of 3.2 (configured by a mixture of concentrated sulfuric acid and concentrated nitric acid with a mass ratio of 2:1) was added into the Teflon bottle to maintain the liquid–solid ratio (L:kg) of 10:1. The bottle was then fixed in a flip-type shaker and shaken at a speed of 30 r/min for 20 h. After the oscillation, the leachate was collected and stored under cold conditions. The elemental concentration was measured by inductively coupled plasma mass spectrometry (ICP-MS, Thermo Fisher iCAP 7000).
The values of 24 h water absorption and bulk density were obtained as follows:
According to the study conducted by Riley (Riley, 2006), the theoretical composition to prepare the ceramsite is SiO2, 55%–77%;、A12O3, 10%–25%;、other compositions (including K2O、CaO、Fe2O3、MgO、Na2O), 8%–25%. XRF was conducted to analyze the chemical composition of the excess sludge after sintering at 1200°C for 15 min as shown in Table 1. The content of Al2O3 is 41.6%, relatively higher than that of SiO2, which is 28.6% in excess sludge. This is contrary to the theoretical demand of SiO2 being much higher than that of Al2O3 if the material is expected to be used to prepare the sintering-expanded ceramsite (Riley, 2006; Liao and Huang, 2012). The total content of ceramsite structure-forming agents in the excess sludge, mainly including SiO2 and Al2O3, reaches 70.2%, which is also not sufficient to prepare the sintering-expanded ceramsite (Liao and Huang, 2012). More importantly, the total content of the alkali and alkaline-earth oxide in excess sludge, including CaO, MgO, K2O, and Na2O, is lower than that in the clay and municipal sludge (Wang et al., 2008). Especially, the key fluxing agent of K2O and Na2O is not detected, which could influence the melting point considerably. It suggests a higher melting point if the excess sludge is meant to be used to prepare the sintering-expanded ceramsite.
TABLE 1. Chemical composition of excess sludge produced in a petrochemical wastewater treatment plant and clay after sintering at 1200°C for 15 min (wt%).
The XRD pattern of the sintered excess sludge at 1200°C for 15 min is displayed in Figure 1. The main diffraction peak is attributed to SiO2 and MgAl2O4 phases, while some peaks cannot be identified accurately. The SEM morphology of the sintered excess sludge at 1200°C for 15 min is displayed in Figure 2, which consists of many 30 μm spherical particles.
The ignition loss of the dried excess sludge after sintering at 1200°C for 15 min is as high as 86%. That is to say, the easily volatile component of the dried excess sludge treated at elevated temperatures is quite high. This implies that the excess sludge cannot be individually employed to prepare the sintering-expanded ceramsite due to the large ignition loss ratio of the petrochemical excess sludge.
Due to the high content of the easily volatile component in excess sludge as aforementioned, the excess sludge cannot be individually utilized to prepare ceramsite. Some materials comprising high content of SiO2 and Al2O3 must be supplemented in order to regulate the chemical composition of the excess sludge. In this study, clay was selected because of its high content of ceramsite structure-forming composition and its wide usage in ceramsite preparation. Therefore, the mixture containing 80 wt% clay and 20 wt% dried excess sludge was first employed to prepare the ceramsite at a sintering temperature of 1200°C.
The as-prepared product has a solid outer surface. However, the ceramsite does not show any evidence of surface melting or volume expansion. That is to say, the sintering-expanded ceramsite is not prepared. This is mainly because the sintering temperature is too low to make the ceramsite crystal phase molten due to the low content of the alkali and alkaline-earth oxide in excess sludge, which primarily functions in reducing the melting point (Wang et al., 2008). The XRD pattern in Figure 3 displays the main crystalline phase including quartz (SiO2), mullite, and aluminum phosphate (AlPO4). This is quite different from the original phase of the excess sludge as shown in Figure 1, indicating some kinds of chemical changes have occurred.
FIGURE 3. XRD pattern of the prepared ceramsite made of 80 wt% clay and 20 wt% dried excess sludge at a sintering temperature of 1200°C.
Due to the nonmelting surface as verified above, another chemical agent must be supplemented to the mixture of excess sludge and clay in order to reduce the melting temperature and thus prepare the sintering-expanded ceramsite. Therefore, the influence of the fluxing agent Na2O (in the form of Na2CO3) on the property of ceramsite was investigated by the addition of different contents of fluxing agent Na2O to the mixture of clay and excess sludge. The content of the dried excess sludge is 20 wt%. The fluxing agent is 5 wt%, 10 wt%, and 15 wt%, respectively. The remaining is clay. Then, the mixture is subject to sintering at 1200°C for 15 min.
The image of the prepared ceramsites with different contents of fluxing agent Na2O is displayed in Figure 4, showing a completely different surface and cross-sectional image. The ceramsite prepared with a 5% fluxing agent shows a melting surface and hard cover. The ceramsite prepared with a 10% fluxing agent shows a white cover, while the cross-section of the ceramsite shows the formation of bubbles, same as the ceramsite prepared with a 5% fluxing agent. It is noted that the ceramsite prepared with a 15% fluxing agent, which is supposed to decrease the melting temperature most significantly, shows a completely different color. Also, it does not show evidence of the melting phenomenon and bubble formation. In summary, the mixture with the addition of 10% and 15% fluxing agents fails to prepare the ceramsite.
FIGURE 4. Image of the prepared ceramsite with different contents of (A) 5%, (B) 10%, and (C) 15% Na2O at 1200°C for 15 min.
The XRD pattern of the as-prepared ceramsite with the addition of a 5% fluxing agent is displayed in Figure 5. The principal crystalline diffraction peaks identified in the prepared ceramsite are attributed to SiO2, AlPO4, and anorthite (CaAl2Si2O8, i.e., CaO·Al2O3·2SiO2), which indicated that some reaction occurred. As displayed above, the diffraction peak of the prepared ceramsite with the addition of fluxing agent Na2O is also dissimilar to that of the prepared ceramsite without the addition of fluxing agent Na2O identified in Figure 3. The mullite phase is recognized in the prepared ceramsite without the addition of fluxing agent Na2O, while the CaAl2Si2O8 phase is identified in the prepared ceramsite with the addition of fluxing agent Na2O, whose melting point is about 1130°C. This is the indication of chemical reactions occurring during the sintering of the mixed raw material. It is speculated that the addition of a slight amount of fluxing agent changes the chemical reactions and can noticeably reduce the melting temperature compared with that without the addition of fluxing agent, which can thus effectively improve the ceramsite quality and lower the sintering temperature.
FIGURE 5. XRD pattern of the prepared ceramsite with the addition of 5 wt% Na2O at 1200°C for 15 min.
Figure 6A shows the microstructure of the cross-section of the prepared ceramsite with the addition of 5 wt% Na2O examined by SEM. Bubbles are generated with the addition of fluxing agent Na2O, and the diameter of the large bubble is about 0.4 mm. The bubble is relatively separate from each other and is not interconnected. The surface of the bubble is relatively smooth. Therefore, the existence of the bubble indicates that melting occurs and the bubble expands to increase the size of the ceramsite due to the bloating effect (Riley, 2006). Such bloating effect causes the lightweight property of the ceramsite, and the bulk density of the ceramsite is about 1.06 g/cm3. The outer surface of the ceramsite is shown in Figure 6B, which displays a dense melting phenomenon to cover the whole surface. This is why the 24 h water absorption rate is quite low at about 1.4%. The prepared ceramsite could be used as construction material. Compared with the relatively low ceramsite preparation temperature of 1080°C from the municipal excess sludge, the high preparation temperature of 1200°C from petrochemical excess sludge can be attributed to the low content of the fluxing agent, including CaO, MgO, K2O, and Na2O.
FIGURE 6. SEM image of (A) the cross-section and (B) the outer surface of the prepared ceramsite with the addition of 5 wt% Na2O at 1200°C for 15 min.
As verified above, the ceramsite prepared at a high temperature of 1200°C displays a melting surface and expanded bubbles due to the slight addition of the fluxing agent Na2O. Therefore, a lower temperature to prepare ceramsite was investigated in order to reduce the sintering temperature and verify the influence of temperature on the property of the prepared ceramsite.
The XRD pattern of the prepared ceramsites at different temperatures from 1150oC to 1200°C is displayed in Figure 7. The main crystalline peaks identified in the prepared ceramsite are attributed to SiO2, AlPO4, and CaAl2Si2O8, which is almost the same even though a different temperature is applied. The peak of CaAl2Si2O8 becomes relatively stronger as the temperature increases.
FIGURE 7. XRD pattern of the prepared ceramsite at different temperatures: (A) 1150°C, (B) 1175°C, and (C) 1200°C.
Figure 8 shows the microstructure of the cross-section of the prepared ceramsite at different temperatures. When the sintering temperature is 1150°C, some pores are formed; their perimeter is not smooth, and the bubble is not shaped. As the sintering temperature increases to 1175°C, the bubbles form evidently and their perimeter is smooth, as shown in Figure 8B. As the preparation temperature further increases to 1200°C, the bubble size becomes larger in general. Therefore, the high temperatures of 1175oC and 1200°C is necessary to prepare the sintering-expanded ceramsite.
FIGURE 8. SEM image of the prepared ceramsite at different temperatures: (A) 1150°C, (B) 1175°C, and (C) 1200°C.
As above verified, the ceramsite prepared with the addition of the appropriate amount of the fluxing agent displays a melting surface and bubble formation. However, the generated bubble is not sufficiently big enough. According to the literature (Liao and Huang, 2012), Fe2O3 can increase the size of the ceramsite bubbles due to the formation of CO or CO2 gas from the chemical reactions between Fe2O3 and carbon.
Therefore, the influence of the pore-forming agent on the property of ceramsite was investigated by the addition of the pore-forming agent Fe2O3 in order to increase the size of the bubbles generated during the sintering. The amount of Fe2O3 addition is set to be 4 wt% of the total weight of the original composition. The photo of the prepared ceramsite is shown in Figure 9, which displays a dark red color different from that of the ceramsite without the addition of a pore-forming agent. Also, a slight addition of Fe2O3 could obviously increase the bubble size of the ceramsite, whose size can be as big as about 4 mm. The SEM image of the generated bubble is displayed in Figure 10, which is relatively larger than that of the ceramsite prepared without the addition of the pore-forming agent. The density of the prepared ceramsite is about 0.95 g/cm3, smaller than that prepared without the addition of a pore-forming agent due to the increased size of the bubbles. The XRD pattern of the as-prepared ceramsite is shown in Figure 11, which shows that the main diffraction peaks are attributed to SiO2, AlPO4, CaAl2Si2O8, and Fe2O3.
FIGURE 9. Photo of the prepared ceramsite with the addition of pore-forming agent Fe2O3 at 1200°C for 15 min.
FIGURE 10. SEM image of the prepared ceramsite with the addition of pore-forming agent Fe2O3 at 1200°C for 15 min.
FIGURE 11. XRD pattern of the prepared ceramsite with the addition of pore-forming agent Fe2O3 at 1200°C for 15 min.
As known, excess sludge contains some amount of organic matter and heavy metals, which is why it is considered hazardous solid waste in most cases. When the excess sludge is used to prepare ceramsite, the organic matter is completely destroyed due to the high temperature employed to prepare ceramsites during sintering. The hazardous factor of the ceramsite product is the heavy metal leaching toxicity. Therefore, the leaching toxicity of the original dried excess sludge and the as-prepared ceramsite is investigated according to China identification standards for hazardous wastes—identification for extraction toxicity (GB5085, 2007; HJ/T299, 2007). The investigated samples are as follows: the dried excess sludge, the ceramsite prepared from the mixture of excess sludge and clay, the ceramsite prepared with the addition of fluxing agent, and the ceramsite prepared with the addition of pore-forming agent. As seen in Table 2, the leaching toxicity of the heavy metals, including Ni, Cd, Pb, Cr, Cu, and V, in the dried excess sludge is high, although the leaching toxicity of the heavy metals is still lower than that of China Standard. When the excess sludge is used to prepare ceramsite, the leaching toxicity of the heavy metals in the prepared ceramsite decreases to a large extent. For instance, the leaching toxicity of the heavy metal Pb decreases to 0.01 mg/L, far lower than that of the dried excess sludge, which means the heavy metals are fixed in the ceramsite. The heavy metal leaching concentration decreases due to the combined effect of physical coating and chemical binding. This is also supported by the SEM image in Figure 6, which shows a dense structure due to the melting phenomenon which can prevent the leaching of heavy metals.
TABLE 2. Leaching toxicity of heavy metals of the dried excess sludge and the typically prepared ceramsite (mg/L).
The petrochemical excess sludge is applied to prepare ceramsite. The properties of ceramsite are primarily influenced by the addition of fluxing agent and the sintering temperature. The dried excess sludge cannot be alone adopted to prepare ceramsite due to the high content of the volatile component. The sintering-expanded ceramsite is not prepared when the dried excess sludge is mixed with clay. The slight addition of fluxing agent, Na2O, can reduce the melting temperature and prepare the sintering-expanded ceramsite, while an excess amount of fluxing agent can be detrimental to the preparation of ceramsite. Furthermore, the slight addition of a pore-forming agent, Fe2O3, can improve the bubble size and therefore reduce the bulk density of ceramsite. A temperature of 1200°C is necessary in order to prepare ceramsite, while a low temperature cannot expand ceramsite. In short, the optimal conditions for the preparation of ceramsite are as follows: dried excess sludge, 20 wt%; clay 71, wt%; Na2O, 5 wt%; and Fe2O3, 4 wt%. The leaching toxicity of the heavy metals is greatly reduced when the excess sludge is subject to sintering. Also, the leaching concentrations of the sintered products are all in compliance with China Identification Standard for hazardous wastes. Based on the abovementioned study, the petrochemical excess sludge can be used to prepare ceramsite in a resourceful way.
The original contributions presented in the study are included in the article/supplementary material; further inquiries can be directed to the corresponding author.
ZL, ZZ, and HZ came up with the conception and directed the study. ZL and HZ carried out the experiments. XL and ZL performed the statistical analysis. ZL and SZ drafted the article and the final approved version to be published. All authors gave the final approval for publication and agreed to be held accountable for the work performed therein.
This study was financially supported by the National Key R&D Program of China (No. 2018YFC1803300) and the Technology Development Program of SINOPEC, China (Grant No. 316005).
ZL, HZ, XL, HZ, ZZ, and SZ were employed by SINOPEC Research Institute of Safety Engineering Co., Ltd.
All claims expressed in this article are solely those of the authors and do not necessarily represent those of their affiliated organizations, or those of the publisher, the editors, and the reviewers. Any product that may be evaluated in this article, or claim that may be made by its manufacturer, is not guaranteed or endorsed by the publisher.
Abouelnasr, D., and Isam, Z. (2008). Treatment and recovery of oil-based sludge using solvent extraction. Soc. Pet. Eng. 2008, 245–251. doi:10.2118/118179-MS |
Begum, S. S., Gandhimathi, R., Ramesh, S. T., and Nidheesh, P. V. (2013). Utilization of textile effluent wastewater treatment plant sludge as brick material. J. Mat. Cycles Waste Manag. 15, 564–570. doi:10.1007/s10163-013-0139-4 |
Bruno, L. R., Claúdia, M. A., Eralci, M. T., Romildo, J. R., Leonardo, G. V., Ailton, J. T., et al. (2022). Carbon quantum dots: An environmentally friendly and valued approach to sludge disposal. Front. Chem. 10. doi:10.3389/fchem.2022.858323 | |
Chen, R. H., Pan, Z. L., Chu, S. Y., Xiao, J. B., Weng, R. G., Da, Q. Y., et al. (2022). Optimize the preparation of novel pyrite tailings based non-sintered ceramsite by plackett-burman design combined with response surface method for phosphorus removal. Front. Chem. 10, 850171. doi:10.3389/fchem.2022.850171 | |
Elektorowicz, M., and Habibi, S. (2005). Sustainable waste management: Recovery of fuels from petroleum sludge. Can. J. Civ. Eng. 32 (1), 164–169. doi:10.1139/l04-122 |
Fabio, M., Claudio, T., Piero, S., Osvalda, S., and Roberto, S. (2018). Modelling oxy-pyrolysis of sewage sludge in a rotary kiln reactor. Fuel 231, 468–478. doi:10.1016/j.fuel.2018.05.094 |
Furlani, E., Tonello, G., Maschio, S., Aneggi, E., Minichelli, D., Bruckner, S., et al. (2011). Sintering and characterisation of ceramics containing paper sludge, glass cullet and different types of clayey materials. Ceram. Int. 37, 1293–1299. doi:10.1016/j.ceramint.2010.12.005net/ast.68.120 |
Gb5085, (2007) Identification standards for hazardous wastes- Identification for extraction toxicity. Beijing: National Standard of China.
Guo, L., Zhang, H. Z., Jiang, X. Y., Wang, Y., Liu, Z. W., Fang, S. P., et al. (2019). Classification and disposal strategy of excess sludge in the petrochemical industry. Appl. Sci. (Basel). 9, 1186–1199. doi:10.3390/app9061186 |
Heidarzadeh, N., Gitipour, S., and Abdoli, M. A. (2010). Characterization of oily sludge from a Tehran oil refinery. Waste Manag. Res. 28 (10), 921–927. doi:10.1177/0734242X09345794 | |
HJ/T299, (2007). Solid waste-extraction procedure for leaching toxicity-sulphuric acid & nitric acid method. Beijing: Chinese Environmental Protection Industry Standard.
Hu, G. J., Li, J. B., and Hou, H. B. (2015). A combination of solvent extraction and freeze thaw for oil recovery from petroleum refinery wastewater treatment pond sludge. J. Hazard. Mat. 283, 832–840. doi:10.1016/j.jhazmat.2014.10.028 | |
Hu, G. J., Li, J. B., and Zeng, G. M. (2013). Recent development in the treatment of oily sludge from petroleum industry: A review. J. Hazard. Mat. 261 (13), 470–490. doi:10.1016/j.jhazmat.2013.07.069 | |
Li, T. P., Sun, T. T., and Li, D. X. (2018). Preparation, sintering behavior, and expansion performance of ceramsite filter media from dewatered sewage sludge, coal fly ash, and river sediment. J. Mat. Cycles Waste Manag. 20, 71–79. doi:10.1007/s10163-016-0547-3 |
Liao, Y. C., and Huang, C. Y. (2012). Glass foam from the mixture of reservoir sediment and Na2CO3. Ceram. Int. 38, 4415–4420. doi:10.1016/j.ceramint.2012.01.080 |
Moško, J., Pohořelý, M., Zach, B., Svoboda, K., Durda, T., Jeremias, M., et al. (2018). Fluidized bed incineration of sewage sludge in O2/N2 and O2/CO2 atmospheres. Energy fuels. 32, 2355–2365. doi:10.1021/acs.energyfuels.7b02908 |
Qin, L. B., Han, J., Chen, W. S., Wang, G. G., Luo, G. Q., and Yao, H. (2017). Simultaneous removal of SO2 and PAHs by adding calcium-based additives during sewage sludge incineration in a fluidized bed incinerator. J. Mat. Cycles Waste Manag. 19, 1061–1068. doi:10.1007/s10163-017-0592-6 |
Riley, C. M. (2006). Relation of chemical properties to the bloating of clays. J. Am. Ceram. Soc. 34 (4), 121–128. doi:10.1111/j.1151-2916.1951.tb11619.x |
Keywords: excess sludge, ceramsite, fluxing agent, sintering behavior, leaching characteristics
Citation: Liu Z, Zhang H, Lin X, Zhang H, Zhang Z and Zhang S (2022) Investigations on the preparation of ceramsite from petrochemical excess sludge. Front. Chem. 10:1008884. doi: 10.3389/fchem.2022.1008884
Received: 01 August 2022; Accepted: 24 August 2022;
Published: 15 September 2022.
Edited by:
Huacheng Zhang, Xi'an Jiaotong University, ChinaReviewed by:
Jiabin Zhou, Southwest Petroleum University, ChinaCopyright © 2022 Liu, Zhang, Lin, Zhang, Zhang and Zhang. This is an open-access article distributed under the terms of the Creative Commons Attribution License (CC BY). The use, distribution or reproduction in other forums is permitted, provided the original author(s) and the copyright owner(s) are credited and that the original publication in this journal is cited, in accordance with accepted academic practice. No use, distribution or reproduction is permitted which does not comply with these terms.
*Correspondence: Shucai Zhang, emhhbmdzYy5xZGF5QHNpbm9wZWMuY29t
Disclaimer: All claims expressed in this article are solely those of the authors and do not necessarily represent those of their affiliated organizations, or those of the publisher, the editors and the reviewers. Any product that may be evaluated in this article or claim that may be made by its manufacturer is not guaranteed or endorsed by the publisher.
Research integrity at Frontiers
Learn more about the work of our research integrity team to safeguard the quality of each article we publish.