- 1Hubei Key Laboratory for Processing and Application of Catalytic Materials, Huanggang Normal University, Huangzhou, China
- 2National Engineering Research Center for Compounding and Modification of Polymer Materials, Guizhou, China
Two DOPO-conjugated flame retardants with or without amino terminal groups (DOPO-NH2 and DIDOPO, respectively) were synthesized and incorporated into polyamide 6 (PA6). Results demonstrated the DOPO-NH2 endowed superior thermal, flame retardant and mechanical performances to PA6 composites. With the same loading of 15 wt%, DOPO-NH2 can catalyze the PA6 matrix more effectively and result in more residues at high temperature. The PA6 composites containing DOPO-NH2 exhibited higher LOI (28.0%) compared to 25.0% for the sample containing DIDOPO, and the lower heat release capacity and peak heat release rate. Furthermore, the overall mechanical properties of PA6 composites containing DOPO-NH2 outperformed the samples containing DIDOPO, even superior to that for PA6. Such a significant difference can be mainly attributed to the existence of amino-terminal group, which can interact with carboxyl group in PA6 as confirmed by dynamic mechanical analysis, improving the compatibility between the flame retardant and PA6 matrix.
Introduction
As one class of important engineering plastics, polyamide especially polyamide 6 (PA6) are extensively used in electronical, automobile, and aerospace areas due to high tensile strength, chemical resistance, good electrical insulation and easy processability (Wirasaputra et al., 2016; Vannini et al., 2018; Song et al., 2017). However, the easy flammability greatly limits their application, and flame retardant modification of PA6 becomes an urgent task and is attracting more and more research interests.
Due to the environmental considerations, a variety of halogen-free flame retardants are proposed to flame retard PA6, including phosphorous-containing (Zhi et al., 2011; Tao et al., 2020), nitrogen-based (Cai et al., 2017; Lu et al., 2019), and some organic/inorganic flame retardants (Marneya et al., 2012; Zheng et al., 2020; He et al., 2020). Among these, metal phosphinates are proved to be the most efficient flame retardants for PA6 and has been commercialized as OP serials. Metal phosphinates play their main role in gas phase by releasing PO· free radical scavenger and also catalyze the charring in the condensed phase. Higher than 15 wt% loading of metal phosphinates is generally necessary to pass the UL-94 tests, which will inevitably cause loss in mechanical properties (Zhao et al., 2013; Lin et al., 2018). To further reinforce the flame retardancy and compensate the mechanical loss, inorganic synergists such as OMMT, carbon nanotube, halloysite are combined with metal phosphinates together to flame retard PA6 (He et al., 2017; He et al., 2019; He et al., 2022). In recent years, 9,10-dihydro-9-oxa-10-phosphaphenanthrene-10-oxide (DOPO) conjugated flame retardants have been developed as an effective alternative and exert their flame retardant activity mainly in gas phase (Xie et al., 2017; Koedel et al., 2020; Zhang et al., 2022; Sai et al., 2022). Incorporation of approx. 17 wt.% bridged DOPO derivatives (DiDopoMeo or DiDopoEDA) into PA6 can achieve a V-0 rating at 1 mm thickness (Buczko et al., 2014). In another work, a nitrogen-phosphorus-based DOPO derivative, DTE-DOPO was developed and incorporated to PA6. Compared to the commercially-available Exolit® OP 1230, DTE-DOPO exhibited higher flame-retardant efficiency since lower P content was contained at a similar flame retardant loading, and superior mechanical performances (Butnaru et al., 2015). Therefore, DOPO derivatives exhibit good prospect in flame retarding PA6.
In our previous work, different DOPO derivatives were synthesized and employed to flame retard polylactic acid (PLA) and high-temperature PA (Long et al., 2017; Huang et al., 2018). Results demonstrated the molecular structure of DOPO derivatives played a critical role on the final flame retardant performance. For instance, the increase of aromatic ring in the structure of the flame retardant contributed to the formation of cross-linked structure in the residue of flame retardant polymers during combustion (Long et al., 2017). However, the effect of active terminal group in the molecules on the flame retardant efficiency have not been considered. Numerous researches have proved that active terminal groups such as epoxide or amino groups in flame retardants or flame retardant synergists have strong interaction with amino or carboxyl end-groups of polymer molecules by coupling reaction (Liang et al., 2019; Xu et al., 2019) or hydrogen bonding (Malkappa et al., 2020; Chen et al., 2017). The strong interaction between flame retardants and polymer matrix can improve the interfacial compatibility and promote the uniform dispersion of the flame retardants, which will be beneficial for improving the flame retardancy and thermomechanical or mechanical performance (Zhou et al., 2021b). For example, Malkappa et al. (Liu et al., 2021) found a 37.2% increase in thermomechanical performance and 41.7% and 30.4% decrease in the peak heat and total heat release rates, respectively, when adding 10 wt% poly (cyclotriphosphazene) functionalized α-zirconium phosphate (f-ZrP) nanoplatelets into PA6. Given that the possible strong interaction between −NH2 group of nanofiller and the carbonyl groups of PA6 polymer matrix, it is expected that the fire retardancy efficiency and mechanical performance of DOPO derivatives can be further improved by introducing −NH2 terminal group onto the molecular structure. Therefore, in this article, two DOPO-conjugated flame retardants with similar structures but different terminal groups were incorporated into PA6 to investigate the effect of terminal groups. The thermal stability and flame retardancy were investigated by thermogravimetric analysis (TGA), limited oxygen index (LOI) and microscale combustion calorimetry (MCC). The mechanical performances were evaluated by dynamical rheological analysis (DMA) and tensile testing.
Materials and methods
Materials
PA6 (1013B) were supplied by UBE Co. Ltd (Tokyo, Japan). The DOPO-based flame retardant DIDOPO without amino terminal groups (as shown in Figure 1), was synthesized as previously reported protocols (Long et al., 2017). Briefly, 86.4 g DOPO and 24 g 2-acetonaphthone were dissolved in xylene at 170°C. Then 16 g phosphorus oxychloride was added dropwise to the above solution. After reacting for 8 h, 100 ml isopropyl alcohol was added to the mixture and stirred at 80°C. The obtained solid product was then recrystallized, and washed with isopropyl alcohol repeatedly to obtain the final powder product. 1H NMR (CDCl3): δ 6.9–8.0 (m, 21H), 3.2 (m, 1H), 2.4 (m, 2H). HRMS (m/z): [MH]+ calcd for C32H24O4P2 535. Found: 535.
The DOPO-NH2 with amino terminal groups was synthesized according to our previous work (Wang et al., 2021). Briefly, 38.91 g DOPO and 6.37 g 4, 4′-diaminobenzophenone were mixed. The mixture was then heated to 180°C and stirred for 3 h. After cooling down to 100°C, 150 ml toluene was added into the flask under stirring. The formed precipitate was filtered off and washed with toluene. The obtained solid product was then recrystallized from tetrahydrofuran and the final powder product was obtained. 1H NMR (DMSO-d6): δ5.82–8.06 (m, 24H), 4.92 (s, 4H). HRMS (m/z): [MH]+ calcd for C37H28O4N2P2 627. Found: 627.
The flame retardant PA6 composites consisting of 85 wt% PA6 and 15 wt% flame retardants were prepared by melt compounding in a co-rotating twin screw extruder (CTE 20, Coperion Keya Machinery Manufacturing Co., Ltd., China) at about 210–230°C with the screw speed of 300 r/min and feeding speed of 16 r/min. Then, the modified PA6 composites were further injection-molded into the standard testing bars by an injection molding machine (CJ80MZ2NCII, Zhende Plastic Machinery Factory, China) at 210–230°C. The obtained PA6 composites were designated as PA6/DIDOPO and PA6/DOPO-NH2, respectively.
Characterization
Thermogravimetric analysis (TGA) was carried out by a Q50 instrument (TA Instruments, United States) under nitrogen flow, from ambient temperature to 800°C with a heating rate of 10°C·min−1.
Crystallization and melting behavior were examined using a Q10 differential scanning calorimetry (DSC) (TA Instruments, United States). Samples of about 5–10 mg were heated from 40 to 250°C and held at 250°C for 5 min to erase the thermal history. Then, the samples were cooled to 40°C at a cooling rate of 10°C·min−1. A subsequent heating scan was then recorded at a rate of 10°C·min−1 from 40 to 250°C. The crystallinity was calculated according to the following equation:
where Xc is the crystallinity; ΔHm is the melting enthalpy of the sample in the second heating; ΔH0m is the melting enthalpy of 100% crystalline PA6, which is 190 J/g (Xiao et al., 2017); ϕ is the mass fraction of the flame retardants in the composites.
The LOI test was conducted on a JF-3 oxygen index meter (Jiangning Analytical Instrument Company, Jiangning, China) with sample dimension of 100 mm × 6.5 mm × 3.2 mm according to the standard of ASTM D286377. Microscale combustion calorimetry (MCC) was carried out on a FTT0001 (Fire Testing Technology Ltd., United Kingdom) to determine the flammability properties of the PA6 composites of milligram-sized samples according to ASTM Standard Method D7309. The specimens were thermally decomposed in an oxygenated environment with a heating rate of 1 K s−1.
The rheological behaviors of samples were investigated by using a rheometric analyzer (HAAKE MARSII, Thermo Fisher Scientifc Inc., Newington, Germany) with the diameter of parallel plates 35 mm. The tests were carried out over an angular frequency range of 0.1 to 100 rad s−1 at 175°C using 1% strain. Tensile and flexural strengths of the samples were evaluated using a universal test machine (CMT4104, Shenzhen SANS Testing Machine Co., China) with cross-head speeds of 50 and 2 mm min−1 at room temperature. The notched Izod impact strength was measured according to ASTMD256A using an impact tester ZBC 1400-2. The freeze-fractured surfaces of flame retardant PA6 composites were recorded on a TESCAN MIRA scanning electron microscope (SEM) using 20 kV accelerating voltage. Prior to the measurements, the freeze-fractured surfaces were fractured and sputter-coated with 5 nm gold.
Results and discussion
Thermal stability of polyamide 6/DOPO-conjugated flame retardant composites
According to our previous work, the initial decomposition temperature (T5%) of DOPO is estimated at 249°C, and maximum decomposition temperatures (Tmax) is at 328°C (Wang et al., 2021). From Figure 1 and Table 1, both flame retardants exhibit better thermal stability compared to DOPO. The T5% of DIDOPO under N2 is observed at 363.6°C. The compound decomposes in a single decomposition step with Tmax at 427.3°C and the residues at 650°C is 1.5%. For DOPO-NH2, the T5% and Tmax is 361.2°C and 473.3°C, respectively. Different from DIDOPO, the char yield of DOPO-NH2 at 600°C reaches 23.5%, suggesting the better charring capacity. The TG curves of pure PA6 and PA6 composites in N2 atmosphere are revealed in Figure 2, and the typical data are listed in Table 1. Pure PA6 decomposes in one step process, with the T5% and Tmax at 408.6°C and 478.4°C, respectively, leaving negligible char residues. With the introduction of DIDOPO, the T5% and Tmax decrease and the amounts of char residues increase slightly. For PA6/DOPO-NH2, the amounts of char residues increase more significantly, indicating that DOPO-NH2 with amino terminal groups improves the thermal stability of the char residue at high temperature and promotes the formation of more residues (Zhou et al., 2019).
Differential scanning calorimetry analysis of polyamide 6/DOPO-conjugated flame retardant composites
DSC analysis was conducted to investigate the effect of two flame retardants on the crystallization and melting behaviors of PA6. To erase the previous thermal history of the samples, an initial heating scan was performed. Then the cooling and second heating processes were recorded. As revealed by Figure 3A and Table 2, the crystallization temperature (Tc) of the neat PA6 is located at 190.8°C during the cooling process. From Figure 3B, the melting curve of PA6 presents two peaks where the low temperature peak corresponds to the γ-crystalline form and the high-temperature peak corresponds to the α-crystalline form (Cai et al., 2017). With the incorporation of DIDOPO, the crystallization temperature reduces by about 3°C (187.0°C) and lower melting temperatures (Tm) are observed. Similar decrease in melting temperatures for polymer composites by other DOPO derivatives is previously reported (Butnaru et al., 2015; Jia et al., 2018). The incorporated DIDOPO which acts as a plasticizer is regarded as the main cause. However, the Tc and Tm of PA6/DOPO-NH2 are all higher compared to PA6/DIDOPO. Besides, upon the addition of DIDOPO, the crystallinity (Xc) of PA6/DIDOPO increases compared to the neat PA6 (from 31.8% to 34.7%), while the crystallinity of PA6/DOPO-NH2 is 31.7%. It is considered that for PA6/DIDOPO, the DIDOPO in PA6 acts as a plasticizer and facilitates the movement of polymer molecular chain segments, resulting in the higher crystallinity. While for PA6/DOPO-NH2, the terminal amino groups in DOPO-NH2 can form hydrogen bonding with the PA6 matrix and therefore limit the crystallization process (Wang et al., 2019).
Flame retardancy of polyamide 6/DOPO-conjugated flame retardant composites
The flame retardancy of PA6 and PA6 composites is investigated by LOI tests, and the results are listed in Table 3. PA6 is inherently flammable and the LOI value of 22.0% is obtained. The introduction of DIDOPO and DOPO-NH2 improves the LOI to 25.0% and 28.0%, respectively. Such results indicate that both flame retardants endow PA6 with improved flame retardancy and the flame retardant efficiency of DOPO-NH2 is superior to that of DIDOPO.
Microscale combustion calorimetry (MCC) is one of the most effective bench scale methods to evaluate the combustion properties of polymer materials of milligram-sized samples (Ding et al., 2016). In this work, MCC was employed in order to assess and compare the combustion behavior of different PA6 composites. The heat release rate (HRR) profiles of the PA6 and PA6 composites versus temperature are shown in Figure 4 and the relevant MCC data are listed in Table 3. For neat PA6, the peak heat release rate (pHRR) was 683.1 W g−1 at a temperature of TM = 489.9°C and the heat release capacity (HRC) was about 693 kJ g−1. The presence of DIDOPO in the PA6 causes decrease in TM due to the thermal degradation of DIDOPO or their catalytic degradation effect on PA6 as reflected by the slightly increased residues in TG analysis. In addition, the introduction of DIDOPO results in slightly increased PHRR and HRC (714.7 W g−1 and 732 kJ g−1, respectively). According to references (Buczko et al., 2014; Butnaru et al., 2015), similar phenomenon regarding the increased pHRR for the PA6 formulation containing DiDopoEDA or DTE-DOPO have been reported. It is considered that for these DOPO derivatives, a gas-phase flame inhibition mechanism plays a main role in improving the flame retardancy (Peng et al., 2021; Yang et al., 2021; Huo et al., 2022). On the contrary, the addition of DOPO-NH2 bring about decrease in PHRR and HRC (670.5 W g−1 and 675 kJ g−1), respectively. Therefore, in the present study, it can be concluded that for these DOPO derivatives, a gas-phase flame inhibition mechanism plays a main role in improving the flame retardancy. While for DOPO-NH2 containing sample, besides the flame inhibition in gas phase due to the existence of DOPO groups, the charring effect in condensed should not be excluded (Xue et al., 2021).
Rheological and mechanical properties
To evaluate the influence of the two flame retardants on the rheological behaviors of PA6, rheological measurements were carried out on neat PA6 and PA6 composites. From Figures 5A,B, both storage modulus and complex viscosity of PA6 decrease obviously with the incorporation of DiDOPO in the whole range of measured frequencies. This might indicate the internal plasticizing effect of DiDOPO on the polymer structures, which facilitates the movement of the PA6 molecular chains. For DOPO-NH2 containing samples, although the storage modulus and the complex viscosity decrease compared to neat PA6, the effect is not so profound. In almost the whole frequency range, the storage modulus and complex viscosity of PA6/DOPO-NH2 are higher than that of PA6/DIDOPO. This could be ascribed to the limited motion of the polymer chains due to the interaction between the terminal amino of DOPO-NH2 and carboxyl end groups of PA6 molecules (Wang et al., 2019).
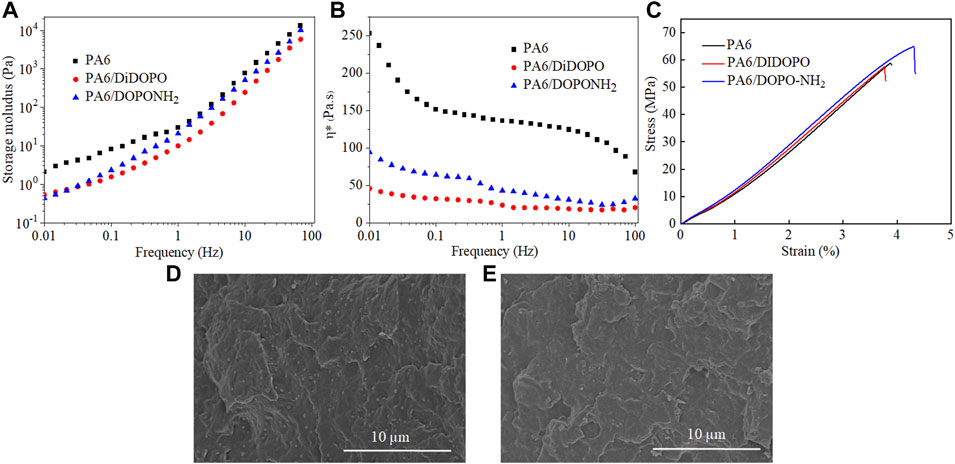
FIGURE 5. Storage modulus (A) and complex viscosity (B) as a function of frequency, and stress-strain curves (C) of PA6 and PA6 composites; SEM images of the fracture of PA6/DIDOPO (D) and PA6/DOPO-NH2 (E) composites after their treatment in liquid N2.
Generally, the mechanical performance of polymer composites are strongly dependent on the interfacial compatibility between the additive and the polymer matrix (Qian et al., 2017; Qian et al., 2019; Liu et al., 2022). The impacts of DIDOPO and DOPO-NH2 on the mechanical properties PA6 matrix are assessed and the results are presented in Figure 5C and Table 4. Upon the loading of DIDOPO, the tensile and flexural strengths of PA6 decrease to 53.2 and 67.8 MPa, respectively, from 58.4 to 71.2 MPa for neat PA6. The elongation at break shows no obvious change. Comparably, in the presence of DOPO-NH2, the tensile and flexural strengths of PA6 composites increase to 63.7 and 81.3 MPa, respectively, even higher than that of untreated PA6. Besides, the strain at break further increased to 4.3% (higher than 3.9% of the untreated PA6).
In addition, PA6/DIDOPO and PA6/DOPO-NH2 composites registered lower impact strength values of 3.5 kJ/m2 and 3.6 kJ/m2, respectively, compared to pristine PA6, suggesting the incorporation of both flame retardants increases the brittleness due to its rigid chemical structure (Zhou et al., 2021a). From SEM images the cryogenic fracture of both PA6 composites, one can distinguish distinct lines of fracture propagation which are associated to an inherent brittleness Figures 5D,E. Similar phenomenon have been observed for PA6/meltable triazine-DOPO by Butnaru et al. (2015). It is considered that a good interfacial compatibility between the flame retardant and PA6 restricts the movement of the chain segments, resulting in a lower toughness. In addition, a few DIDOPO aggregate particles are clearly visible in the fracture surface in PA6/DIDOPO composites but not in PA6/DOPO-NH2 (Figures 5D,E), which can explain why the latter exhibits higher tensile strength and flexural strength than the former.
The results are consistent with the rheological analysis and it is considered that the terminal amino groups play a critical role, which can form strong hydrogen bonding with PA6 molecular chains and enhance the interaction force between PA6 macromolecular chains (Liu et al., 2021). However, the introduced flame retardant particles may act as an energy concentration under impact force, resulting in decrease of impact strength.
Conclusion
In this paper, DIDOPO and DOPO-NH2 with amino terminal groups were used to modify the flame retardancy and mechanical properties of PA6. The flame retardant performance of PA6 containing DOPO-NH2 is superior to that containing DIDOPO. At 5 wt% loading of the additives, the PA6/DOPO-NH2 had a LOI of 28.0% while PA6/DIDOPO show a much lower LOI of 25.0%. Besides, from the MCC test, the PHRR and HRC of PA6/DOPO-NH2 decreased compared to that of pristine PA6, and the PHRR and HRC of PA6/DIDOPO are even higher than of PA6. Furthermore, the overall mechanical performances of PA6 containing DOPO-NH2 are better than the sample containing DIDOPO. Particularly, the tensile strength, flexural strength and elongation at break of PA6 composites containing DOPO-NH2 reach 63.7, 81.3 MPa and 4.3%, respectively, even higher than that of untreated PA6. DSC and rheological analysis suggest that the stronger interaction between DOPO-NH2 and PA6 play a critical role for the property improvement. This work offers an alternative and promising strategy for design and synthesis of more efficient flame retardants.
Data availability statement
The original contributions presented in the study are included in the article/Supplementary Material, further inquiries can be directed to the corresponding author.
Author contributions
JG and WH prepared materials and carried out the experiments. SX and LL helped to characterize materials, and SQ helped to analyze the experimental data. WH supervised the work. All authors contributed to revising the manuscript, approved the final version, and agreed to be accountable for all aspects of this work.
Funding
This work was financially supported by the Natural Science Foundation of China (grant: 52103080) and Doctoral Scientific Fund Project in Huanggang Normal University (2042019029).
Conflict of interest
The authors declare that the research was conducted in the absence of any commercial or financial relationships that could be construed as a potential conflict of interest.
Publisher’s note
All claims expressed in this article are solely those of the authors and do not necessarily represent those of their affiliated organizations, or those of the publisher, the editors and the reviewers. Any product that may be evaluated in this article, or claim that may be made by its manufacturer, is not guaranteed or endorsed by the publisher.
References
Buczko, A., Stelzig, T., Bommer, L., Rentsch, D., Heneczkowski, M., and Gaan, S. (2014). Bridged DOPO derivatives as flame retardants for PA6. Polym. Degrad. Stab. 107, 158–165. doi:10.1016/j.polymdegradstab.2014.05.017
Butnaru, I., Fernández-Ronco, M. P., Czech-Polak, J., Heneczkowski, M., and Bruma, M. (2015). Effect of meltable triazine-DOPO additive on rheological, mechanical, and flammability properties of PA6. Polymers 7, 1541–1563. doi:10.3390/polym7081469
Cai, J., Wirasaputra, A., Zhu, Y., Liu, S., Zhou, Y., and Zhao, J. (2017). The flame retardancy and rheological properties of PA6/MCA modified by DOPO-based chain extender. RSC Adv. 7, 19593–19603. doi:10.1039/C6RA28293H
Chen, Y., Wei, W., Yong, Q., Li, L., Qian, L., and Fei, X. (2017). Terminal group effects of phosphazene-triazine bi-group flame retardant additives in flame retardant polylactic acid composites. Polym. Degrad. Stab. 140, 166–175. doi:10.1016/j.polymdegradstab.2017.04.024
Ding, P., Li, J., and Wang, C. L. (2016). Roles of supermolecule structure of melamine phosphomolybdate in intumescent flame retardant polypropylene composites. J. Anal. Appl. Pyrolysis 119, 139–146. doi:10.1016/j.jaap.2016.03.007
He, W., Song, P., Yu, B., Fang, Z., and Wang, H. (2020). Flame retardant polymeric nanocomposites through the combination of nanomaterials and conventional flame retardants. Prog. Mat. Sci. 114, 100687. doi:10.1016/j.pmatsci.2020.100687
He, W. T., Gao, J., Liao, S. T., Wang, X. X., Qin, S. H., and Song, P. A. (2019). A facile method to improve thermal stability and flame retardancy of polyamide 6. Compos. Commun. 13, 143–150. doi:10.1016/j.coco.2019.04.010
He, W. T., Zhu, H., Xiang, Y. S., Long, L. J., Qin, S. H., and Yu, J. (2017). Enhancement of flame retardancy and mechanical properties of polyamide 6 by incorporating an aluminum salt of diisobutylphosphinic combined with organoclay. Polym. Degrad. Stab. 144, 442–453. doi:10.1016/j.polymdegradstab.2017.09.003
He, W., Xu, H., Song, P., Xiang, Y., and Qin, S. (2022). P, N-decorated halloysite nanotubes for flame retardancy enhancement of polyamide 6/aluminum diethylphosphinate. Polym. Degrad. Stab. 196, 109847. doi:10.1016/j.polymdegradstab.2022.109847
Huang, W. J., He, W. T., Long, L. J., Yan, W., He, M., and Qin, S. H. (2018). Highly efficient flame-retardant glass-fiber-reinforced polyamide 6T system based on a novel DOPO-based derivative: Flame retardancy, thermal decomposition, and pyrolysis behavior. Polym. Degrad. Stab. 148, 26–41. doi:10.1016/j.polymdegradstab.2018.01.008
Huo, S., Sai, T., Ran, S., Guo, Z., Fang, Z., and Wang, H. (2022). A hyperbranched P/N/B-containing oligomer as multifunctional flame retardant for epoxy resins. Compos. Part B Eng. 234, 109701. doi:10.1016/j.compositesb.2022.109701
Jia, L., Zhang, W. C., Tong, B., and Yang, R. J. (2018). Crystallization, mechanical and flame-retardant properties of poly(lactic acid) composites with DOPO and DOPO-POSS. Chin. J. Polym. Sci. 36, 871–879. doi:10.1007/s10118-018-2098-7
Koedel, J., Callsen, C., Weise, M., Puchtler, F., Weidinger, A., and Altstaedt, V. (2020). Investigation of melamine and dopo-derived flame retardants for the bioplastic cellulose acetate. Polym. Test. 90, 106702. doi:10.1016/j.polymertesting.2020.106702
Liang, T. X., Cai, J. N., Liu, S. M., Lai, H. L., and Jq, Z. (2019). Chain extension and synergistic flame-retardant effect of aromatic schiff base diepoxide on polyamide 6/aluminum diethylphosphinate composites. Materials 12, 2217–2234. doi:10.3390/ma12142217
Lin, X. B., Chen, L., Long, J. W., Shuang-Lan, D., and Wang, Y. Z. (2018). A hybrid flame retardant for semi-aromatic polyamide: Unique structure towards self-compatibilization and flame retardation. Chem. Eng. J. 334, 1046–1054. doi:10.1016/j.cej.2017.10.101
Liu, L., Zhu, M., Ma, Z., Xu, X., Seraji, S. M., and Yu, B. (2022). A reactive copper-organophosphate-MXene heterostructure enabled antibacterial, self-extinguishing and mechanically robust polymer nanocomposites. Chem. Eng. J. 430, 132712. doi:10.1016/j.cej.2021.132712
Liu, L., Zhu, M., Shi, Y., Xu, X., Ma, Z., and Yu, B., (2021). Functionalizing MXene towards highly stretchable, ultratough, fatigue- and fire-resistant polymer nanocomposites. Chem. Eng. J. 424, 130338. doi:10.1016/j.cej.2021.130338
Long, L. J., Chang, Q. F., He, W. T., Xiang, Y. S., Qin, S. H., and Yin, J. B., (2017). Effects of bridged DOPO derivatives on the thermal stability and flame retardant properties of poly(lactic acid). Polym. Degrad. Stab. 139, 55–66. doi:10.1016/j.polymdegradstab.2017.03.016
Lu, S., Zhou, W., Yang, M., Chen, G., Chen, X., and Yu, D., (2019). Preparation and flame-retardant mechanism of polyheptazine/PA6 nanocmposites. Polymer 182, 121810. doi:10.1016/j.polymer.2019.121810
Malkappa, K., Bandyopadhyay, J., and Ray, S. S. (2020). Design of poly(cyclotriphosphazene)-functionalized zirconium phosphate nanoplatelets to simultaneously enhance the dynamic mechanical and flame retardancy properties of polyamide 6. ACS Omega 5, 13867–13877. doi:10.1021/acsomega.0c01247
Marneya, D. C. O., Yang, W., Russell, L. J., Shen, S. Z., Nguyen, T., and Yuan, Q., (2012). Phosphorus intercalation of halloysite nanotubes for enhanced fire properties of polyamide 6. Polym. Adv. Technol. 23, 1564–1571. doi:10.1002/pat.3030
Peng, W., Nie, S.-b., Xu, Y.-x., and Yang, W. (2021). A tetra-DOPO derivative as highly efficient flame retardant for epoxy resinsfficient flame retardant for epoxy resins. Polym. Degrad. Stab. 193, 109715. doi:10.1016/j.polymdegradstab.2021.109715
Qian, M., Song, P., Qin, Z., Yan, S., and Zhang, L. (2019). Mechanically robust and abrasion-resistant polymer nanocomposites for potential applications as advanced clearance joints. Compos. Part A Appl. Sci. Manuf. 126, 105607. doi:10.1016/j.compositesa.2019.105607
Qian, M., Sun, Y., Xu, X., Liu, L., Song, P., and Yu, Y., (2017). 2D-alumina platelets enhance mechanical and abrasion properties of PA612 via interfacial hydrogen-bond interactions. Chem. Eng. J. 308, 760–771. doi:10.1016/j.cej.2016.09.124
Sai, T., Ran, S., Guo, Z., Song, P., and Fang, Z. (2022). Recent advances in fire-retardant carbon-based polymeric nanocomposites through fighting free radicals, 1–24. doi:10.1002/sus2.73SusMat
Song, P., Wang, C., Chen, L., Zheng, Y., Liu, L., and Wu, Q., (2017). Thermally stable, conductive and flame-retardant nylon 612 composites created by adding two-dimensional alumina platelets. Compos. Part A Appl. Sci. Manuf. 97, 100–110. doi:10.1016/j.compositesa.2017.02.029
Tao, W., Hu, X., Sun, J., Qian, L., and J, L. (2020). Effects of P–N flame retardants based on cytosine on flame retardancy and mechanical properties of polyamide 6. Polym. Degrad. Stab. 174, 109092. doi:10.1016/j.polymdegradstab.2020.109092
Vannini, M., Marchese, P., Celli, A., Marega, C., and Lorenzetti, C. (2018). Strategy to improve PA6 performances by melt compounding. Polym. Test. 67, 84–91. doi:10.1016/j.polymertesting.2018.02.021
Wang, X., He, W., Long, L., Huang, S., Qin, S., and Xu, G. (2021). A phosphorus- and nitrogen-containing DOPO derivative as flame retardant for polylactic acid (PLA). J. Therm. Anal. Calorim. 145, 331–343. doi:10.1007/s10973-020-09688-7
Wang, X. X., Sun, J., Liu, X., Jiang, S., Zhang, S., and Li, H., (2019). An effective flame retardant containing hypophosphorous acid for poly (lactic acid): Fire performance, thermal stability and mechanical properties. Polym. Test. 78, 105940. doi:10.1016/j.polymertesting.2019.105940
Wirasaputra, A., Zheng, L., Liu, S., Yuan, Y., and Zhao, J. (2016). High-performance flame-retarded polyamide-6 composite fabricated by chain extension. Macromol. Mat. Eng. 301, 614–624. doi:10.1002/mame.201500357
Xiao, Y., Xu, J., Huang, S., and Deng, H. (2017). Effects of α -ZrP on crystallinity and flame-retardant behaviors of PA6/MCA composites. Int. J. Polym. Sci., 1–12. doi:10.1155/2017/6034741
Xie, M. C., Zhang, S. M., Ding, Y. F., Wang, F., Liu, P., and Tang, H. Y., (2017). Synthesis of a heat-resistant DOPO derivative and its application as flame-retardant in engineering plastics. J. Appl. Polym. Sci. 134, 44892–44992. doi:10.1002/app.44892
Xu, M. J., Liu, H. C., Ma, K., Li, B., and Zhang, Z. (2019). New strategy towards flame retardancy through design, synthesis, characterization, and fire performance of a chain extender in polyamide 6 composites. Polym. Eng. Sci. 59, pen.25030–215. doi:10.1002/pen.25030
Xue, Y., Feng, J., Ma, Z., Liu, L., Zhang, Y., and Dai, J., (2021). Advances and challenges in eco-benign fire-retardant polylactide. Mat. Today Phys. 21, 100568. doi:10.1016/j.mtphys.2021.100568
Yang, S., Huo, S., Wang, J., Zhang, B., Wang, J., and Ran, S., (2021). A highly fire-safe and smoke-suppressive single-component epoxy resin with switchable curing temperature and rapid curing rate. Compos. Part B Eng. 207, 108601. doi:10.1016/j.compositesb.2020.108601
Zhang, D., Pei, M., Wei, K., Tan, F., Gao, C., and Bao, D., (2022). Flame-retardant properties and mechanism of polylactic acid-conjugated flame-retardant composites. Front. Chem. 10, 894112. doi:10.3389/fchem.2022.894112
Zhao, B., Chen, L., Long, J. W., Chen, H. B., and Wang, Y. Z. (2013). Aluminum hypophosphite versus alkyl-substituted phosphinate in polyamide 6: Flame retardance, thermal degradation, and pyrolysis behavior. Ind. Eng. Chem. Res. 52, 2875–2886. doi:10.1021/ie303446s
Zheng, T., Xia, W., Guo, J., and Liu, Y. (2020). Modified magnesium hydroxide encapsulated by melamine cyanurate in flame-retardant polyamide-6. J. Polym. Res. 27, 258–268. doi:10.1007/s10965-020-02229-8
Zhi, H., Chen, L., Lin, G. P., Luo, Y., and Wang, Y. Z. (2011). Flame retardation of glass-fibre-reinforced polyamide 6 by a novel metal salt of alkylphosphinic acid. Polym. Degrad. Stab. 96, 1538–1545. doi:10.1016/j.polymdegradstab.2011.03.010
Zhou, Y., Lin, Y., Tawiah, B., Sun, J., Yuen, R. K. K., and Fei, B. (2021a). DOPO-decorated two-dimensional MXene nanosheets for flame retardant, ultraviolet-protective, and reinforced polylactide composites. ACS Appl. Mat. Interfaces 13, 21876–21887. doi:10.1021/acsami.1c05587
Zhou, Y., Tang, R. C., Xing, T., Guan, J. P., Shen, Z. H., and Zhai, A. D. (2019). Flavonoids-metal salts combination: A facile and efficient route for enhancing the flame retardancy of silkfficient route for enhancing the flame retardancy of silk. Ind. Crops Prod. 130, 580–591. doi:10.1016/j.indcrop.2019.01.020
Zhou, Y., Tawiah, B., Noor, N., Zhang, Z., Sun, J., and Yuen, R. K. K., (2021b). A facile and sustainable approach for simultaneously flame retarded, UV protective and reinforced poly(lactic acid) composites using fully bio-based complexing couples. Compos. Part B Eng. 215, 108833. doi:10.1016/j.compositesb.2021.108833
Keywords: terminal group effect, conjugated flame retardant, polyamide 6, flame retardancy, mechanical performance
Citation: Gao J, He W, Xiang Y, Long L and Qin S (2022) Terminal group effects of DOPO-conjugated flame retardant on polyamide 6: Thermal stability, flame retardancy and mechanical performances. Front. Chem. 10:1002569. doi: 10.3389/fchem.2022.1002569
Received: 25 July 2022; Accepted: 06 September 2022;
Published: 28 September 2022.
Edited by:
Haichang Zhang, Qingdao University of Science and Technology, ChinaReviewed by:
Yan Zhang, Zhejiang University, ChinaYuyang Zhou, Soochow University, China
Hui Wang, National Center for Nanoscience and Technology (CAS), China
Siqi Huo, Zhejiang University, China
Copyright © 2022 Gao, He, Xiang, Long and Qin. This is an open-access article distributed under the terms of the Creative Commons Attribution License (CC BY). The use, distribution or reproduction in other forums is permitted, provided the original author(s) and the copyright owner(s) are credited and that the original publication in this journal is cited, in accordance with accepted academic practice. No use, distribution or reproduction is permitted which does not comply with these terms.
*Correspondence: Wentao He, d2VudGFvaGVAYWxpeXVuLmNvbQ==