- 1Department of Materials Science and Engineering, Baise University, Baise, China
- 2Guangxi Novel Battery Materials Research Center of Engineering Technology, Guangxi Key Laboratory of Processing for Non-Ferrous Metallic and Featured Materials, Guangxi Colleges and Universities Key Laboratory of Novel Energy Materials and Related Technology, School of Physical Science and Technology, Guangxi University, Nanning, China
Mg−Li alloy possesses a high hydrogen capacity. However, the hydrogenation and dehydrogenation performances are still far from practical application. In this work, Mg2Si (MS) and graphene (G) were employed together to synergistically improve the hydrogen storage properties of Mg−Li alloy. The structures of the samples were studied by XRD and SEM methods. The hydrogen storage performances of the samples were studied by nonisothermal and isothermal hydrogenation and dehydrogenation, thermal analysis, respectively. It is shown that the onset dehydrogenation temperature of Mg−Li alloy was synergistically reduced from 360°C to 310°C after co-addition of Mg2Si and graphene. At a constant temperature of 325°C, the Mg−Li−MS−G composite can release 2.7 wt.% of hydrogen within 2 h, while only 0.2 wt.% of hydrogen is released for the undoped Mg−Li alloy. The hydrogenation activation energy of the Mg−Li−MS−G composite was calculated to be 86.5 kJ mol−1. Microstructure and hydrogen storage properties studies show that graphene can act as a grinding aid during the ball milling process, which leads to a smaller particle size for the composites. This work demonstrates that coaddition of Mg2Si and graphene can synergistically improve the hydrogen storage properties of Mg−Si alloy and offers an insight into the role of graphene in the Mg−Li−MS−G composite.
1 Introduction
Hydrogen storage remains a big challenge for the large-scale application of hydrogen energy. Solid-sate hydrogen storage based on the reversible dehydrogenation and rehydrogenation reactions of some materials exhibits promising application potential due to its large volumetric density and sound security. Research and development of advanced hydrogen storage materials is of vital importance for the practical application of solid-state hydrogen storage. During the past decades, many light-weight hydrogen storage materials have been discovered and developed (Li et al., 2019a), for example, light binary metal hydrides (Liu et al., 2020a; Liu et al., 2021a; Zhang et al., 2021a; Huang et al., 2021; Jiang et al., 2021; Si et al., 2021), metal aluminum hydrides (Huang et al., 2020; Li et al., 2020; Ren et al., 2021), metal borohydrides (Zhang et al., 2021b; Neves et al., 2021; Wang and Aguey-Zinsou, 2021; Xian et al., 2021), imides and amides (Chao et al., 2020; Chen et al., 2020; Liu et al., 2021b), etc.
As a potential hydrogen storage material, magnesium hydride (MgH2) has attracted considerable interest due to its high gravimetric hydrogen capacity of 7.6 wt.% and the widely availability of Mg. However, the unfavorably high thermal stability and sluggish dehydrogenation kinetics significantly limit its practical application (Luo et al., 2019; Zhang et al., 2020a). Many attempts have been carried out to improve the dehydrogenation and rehydrogeantion properties of MgH2, including alloying (Hardian et al., 2018; Hui et al., 2020; Ali and Ismail, 2021), nanoengineering (Zhang et al., 2020a; Zhang et al., 2021c; Thi Thu et al., 2021), and catalyst addition (Zhong et al., 2018; Li et al., 2019b; Liu et al., 2020b; Zhang et al., 2020b; Ding et al., 2020; Singh et al., 2020; Sun et al., 2020; Wang and Deng, 2020; Yao et al., 2020; Zeng et al., 2020; Zhu et al., 2020; Lu et al., 2021a; Lu et al., 2021b; Liu et al., 2021c; Liu et al., 2021), etc. Li is also a H-absorbing metal and has a hydrogen capacity of 11.5 wt.%. However, the dehydrogenation of LiH requires a very high temperature. Mg−Li alloys were reported to possesses better hydrogen storage performances than metals Mg or Li (Lan et al., 2016; Halim and Ismail, 2017; Wu et al., 2018). However, the dehydrogenation properties of Mg−Li alloys are still very poor for practical applications.
To improve the hydrogen storage performances of MgH2 and LiH, Vajo et al. (Vajo et al., 2004) utilized Si to destabilize MgH2 and LiH. It was shown that the reversibility of the LiH−Si system was improved. The formation of the Mg or Li silicides contributes to the destabilization of MgH2 and LiH. Mg2Si plays an important role in the destabilized MgH2−Si composites. Addition of carbon materials had been considered an effective way to improve the hydrogen storage properties of MgH2 or Mg-based hydrogen storage alloys. Lukashev et al. (Lukashev et al., 2006) prepared a Mg−C composite and demonstrated that MgH2 was destabilized and the hydrogen dehydrogenation and rehydrogenation kinetics were improved. Another work by Zhang et al. (2015) showed that addition of 10 wt.% graphene significantly enhances the dehydrogenation thermodynamics and kinetics of MgH2. Similar results were also reported by Imamura et al. (1999). Besides graphene, carbon black, graphite, and carbon nanotubes all have positive influence on the hydrogen storage performance of MgH2 (Huang et al., 2007). It was suggested that the interaction between MgH2 and carbon materials contributes to the improvement of the hydrogen storage performances of MgH2.
Inspired by the above-mentioned discussions, we performed a systematic investigation on the effects of Mg2Si and graphene on the hydrogenation and dehydrogenation properties of Mg−Li alloys in this work. The following will show that Mg2Si and graphene have synergetic enhancing effect on the dehydrogenation properties of MgH2. Such fundamental investigation may provide useful guidance for the design and development of high-performance Mg−Li alloys.
2 Experimental Details
2.1 Materials Synthesis
To prepare the Mg−Li alloy (Mg77Li23), the powders of Mg (99.5% of purity from Alfa Aesar) and LiH (99.7% of purity from Alfa Aesar) with a molar ratio of Mg77Li23 were first homogeneously mixed and then pressed into plates using a pressure of 20 MPa. The plates were subject to sintering treatment at 500°C for 2 h with a high-vacuum furnace. After that, the plates were mechanically crushed and then mixed with Mg2Si (MS), graphene (G), and Mg2Si + graphene (MS + G), respectively, with a content of 5 wt.%. The mixtures were then ball-milled to prepare various composites, that is Mg77Li23 + 5 wt.% Mg2Si (denoted as Mg−Li−MS), Mg77Li23 + 5 wt.% graphene (denoted as Mg−Li−G), and Mg77Li23 + 5 wt.% (Mg2Si + graphene) (denoted as Mg−Li−MS−G). For comparison, the as-prepared Mg77Li23 alloy was also ball-milled under the same conditions, which denoted as Mg−Li. The ball-to-powder weight ratio was about 40:1, and the milling process was carried out at 300 rpm for 30 h. The preparation of all the samples and their handling were carried out without exposure to air.
2.2 Materials Characterizations
The dehydrogenation/hydrogenation were performed on a Sieverts-type apparatus by a volumetric method. During measurements, the temperature and pressure data were collected by a computer. The amounts of hydrogen desorbed and absorbed were calculated by the ideal gas equation using the obtained temperature and pressure data. The hydrogenation measurements were conducted using an initial hydrogen pressure of 6.0 MPa, and the samples were heated gradually from room temperature to 377°C with a heating rate of 2°C min−1. The isothermal dehydrogenation measurements were started at an initial hydrogen pressure of 1.1 kPa. The nonisothermal dehydrogenation measurements were conducted as the isothermal measurements, with the temperature increased from room temperature to a target temperature using a heating rate of 2°C min−1. To further determin the dehydrogenation behavior of the composites, the fully hydrogenated samples were measured by using a differential scanning calorimeter (Linseis STA PT-1000) with a high-purity hydrogen (99.999%) of 30 mL min−1 as the carrying gas. Powder X-ray diffraction (XRD) measurements were carried out using a Rinku Miniflex-600 diffractometer with Cu-Kα radiation. To avoid exposure to any moisture or oxygen, the samples were sealed with an amorphous membrane in an Ar glovebox prior to measurements. The morphologies of the samples were observed by a scanning electron microscopy (JEOL, JSM-6510).
3 Results and Discussion
Figure 1A shows the XRD pattern of Mg−Li alloy after sintering treatment and the as-received LiH for comparison. It can be seen that only Mg peak is detected, and the peak of LiH disappears in the sintered Mg−Li alloy. Figure 1B displays the expanded XRD pattern of the Mg−Li alloy. The standard XRD peak position of Mg is also displayed for reference. It is shown that the peaks of Mg in the Mg−Li alloy all shift to higher angles, which indicates a shrinkage of the Mg crystal structure according to the Bragg’s equation. This suggests that the Li may has totally dissolved into the Mg lattice to form a solid solution phase of Mg since the atomic radius of Mg is larger than Li. Figure 1C shows the XRD patterns of the as-milled Mg−Li, Mg−Li−MS, Mg−Li−G, and Mg−Li−MS−G composites. It can be seen that Mg phase is detected in all samples. Besides, some minor peaks of the additives (Mg2Si and graphene) remain nearly unchanged in the corresponding milled composites. This means that Mg2Si and graphene do not react with the Mg−Li alloy.
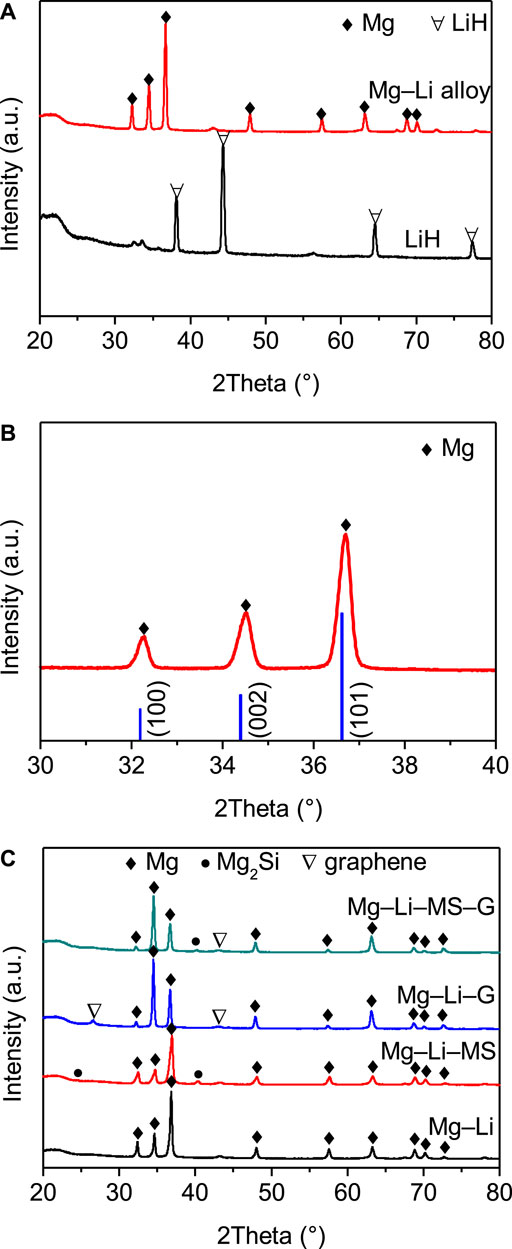
FIGURE 1. (A) XRD patterns of as-received LiH and Mg−Li alloy after sintering treatment; (B) Expanded XRD patterns of Mg−Li alloy after sintering treatment in 2Theta rage 30–40°; (C) XRD patterns of as-milled Mg−Li, Mg−Li−MS, Mg−Li−G, and Mg−Li−MS−G composites.
Figure 2 presents the SEM images of the as-milled Mg−Li, Mg−Li−MS, Mg−Li−G, and Mg−Li−MS−G composites. For the samples without graphene addition, as shown in Figures 2A,B, large particles and the severe agglomeration of small particles can be observed. These large particles are formed from the agglomeration of smaller ones. For the samples with graphene addition, as shown in Figures 2C,D, it is obvious that the particle size is much smaller than the previous two samples, which further indicates the graphene can act as an important grinding aid and significantly improve the milling efficiency.
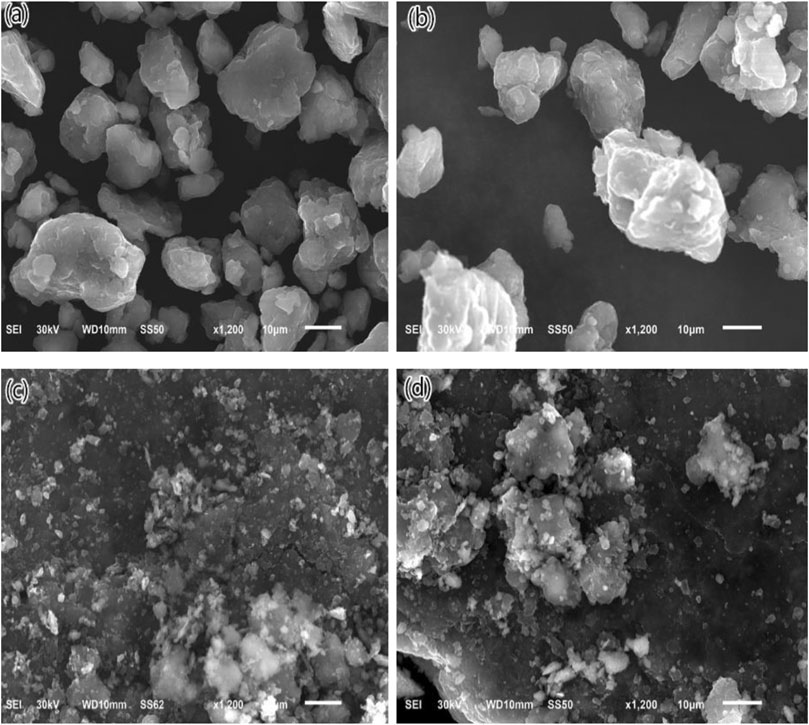
FIGURE 2. SEM images of as-milled Mg−Li (A), Mg−Li−MS (B), Mg−Li−G (C), and Mg−Li−MS−G (D) composites.
To understand the effects of Mg2Si, graphene and Mg2Si + graphene on the hydrogenation/dehydrogenation characteristics of the Mg−Li alloys. The hydrogenation and dehydrogenation curves of the various composites are shown in Figures 3A,B, respectively. The hydrogenations of the composites all start at about 125°C, implying that the starting temperature of the hydrogenation is not affected by addition of Mg2Si or graphene. However, the hydrogenation capacities for samples with graphene (4.1 wt.%) or Mg2Si + graphene (4.4wt.%) addition is slightly lower than the other two samples, which may be due to the fact that the graphene does not absorb any hydrogen under such conditions. The final hydrogenation capacities are 5.9 wt.%, 6.0 wt.%, 4.4 wt.%, and 4.6 wt.% for the Mg−Li, Mg−Li−MS, Mg−Li−G, and Mg−Li−MS−G composites, respectively. Figure 3B displays the dehydrogenation curves of the various composites. The onset dehydrogenation temperatures of the Mg−Li alloys are substantially reduced from 360°C to 300°C, 310°C, and 345°C, respectively, for samples with MS, G or MS + G additions). Obviously, the Mg−Li−G−MS exhibits the lowest onset dehydrogenation temperature among the various composites, which indicates a synergistic improving effect of M2Si and graphene on the dehydrogenation of Mg−Li alloy. The significant improvement in kinetics of the graphene-containing samples may be due to the smaller particle size as shown in Figure 2. The smaller particles will result in more fresh surface exposures, which leads to the improved dehydrogenation performances of Mg−Li alloy. The final dehydrogenation capacities are 5.7 wt.%, 5.6 wt.%, 3.9 wt.%, and 4.5 wt.% for the Mg−Li, Mg−Li−MS, Mg−Li−G, and Mg−Li−MS−G composites, respectively.
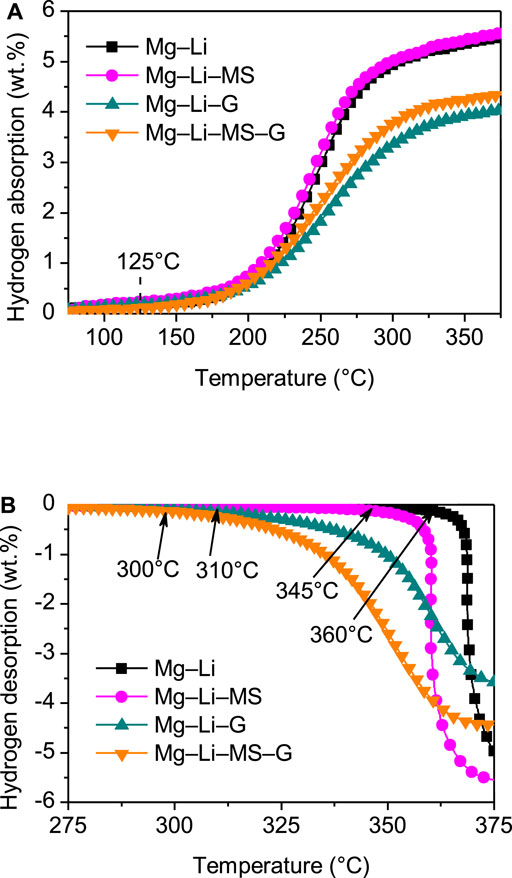
FIGURE 3. Hydrogenation (A) and dehydrogenation (B) curves of the Mg−Li, Mg−Li−MS, Mg−Li−G, and Mg−Li−MS−G composites with a heating rate of 2°C min−1.
To investigate the dehydrogenation kinetics of the various composites, isothermal dehydrogenation measurements were carried out. Figure 4 displays the isothermal dihydrogen curves of the various composites at a constant temperature of 325°C. It is found that the dehydrogenation kinetics of the Mg−Li alloy was significantly improved by the addition of Mg2Si or graphene. Comparatively, the as-milled Mg−Li alloy without additive can hardly release hydrogen at 325°C. After dehydrogenation for 2 h, the dehydrogenation capacity reaches 0.6 wt.%, 2.2 wt.%, and 2.7 wt.% for the Mg−Li−MS, Mg−Li−G, and Mg−Li−MS−G composites, respectively. Obviously, the composite with co-addition of Mg2Si and graphene exhibits the best dehydrogenation kinetics, which also imply a synergistic effect of Mg2Si and graphene on the dehydrogenation of the Mg−Li alloy. It should be noted that the onset dehydrogenation temperature of Mg−Li−MS composite is as high as 345°C shown in Figure 3B; this is because the dehydrogenation needs an induction period. When the composite starts dehydrogenation, the temperature has already increased to 345°C. Therefore, at a constant temperature of 325°C, the composite still can release hydrogen as long as enough reaction time was provided.
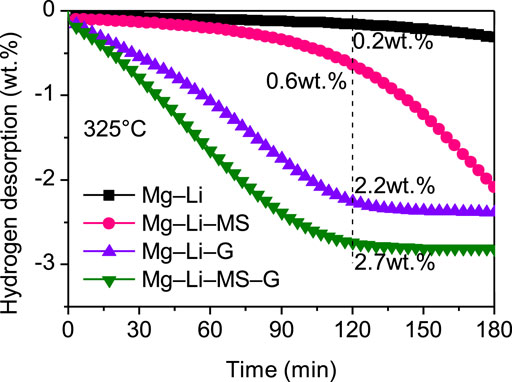
FIGURE 4. Isothermal dehydrogenation curves of the Mg−Li, Mg−Li−MS, Mg−Li−G, and Mg−Li−MS−G composites at a constant temperature of 325°C.
The dehydrogenation performance of the various composites were further studied by thermal analysis. Figure 5 illustrates the DSC curves of the various composites. It is interesting to find that addition of Mg2Si or graphene substantially decreases the peak dehydrogenation temperature of the Mg−Li alloy. For the as-milled Mg−Li alloy, the peak dehydrogenation occurs at 412°C, while for the samples with addition of Mg2Si, graphene or Mg2Si + graphene, their peak dehydrogenation temperatures shift to 395, 391, or 389°C, respectively. The enhance in dehydrogenation kinetics is attributed to the reduction of the particle size. As can be seen in Figure 2, graphene can play a grinding aid role during the mechanical milling, resulting in fine particle size. The smaller particle size can shorten the diffusion path of the hydrogen atom. In other word, the fine particle may reduce the barrier for the diffusion of the hydrogen atoms. As point out in the work by Huang et al. (Huang et al., 2007), the cleavage-decomposed graphite in the composites may intimately interacts with finely divided particles via charge-transfer reactions. Such charge-transfer sites are also responsible for the catalytic activation of hydrogen molecules. Consequently, the dehydrogenation properties of Mg−Li composites were improved.
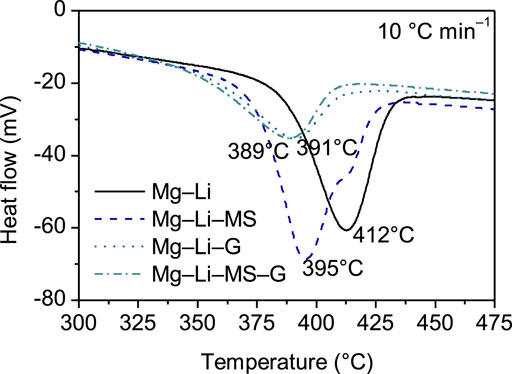
FIGURE 5. DSC curves of the Mg−Li, Mg−Li−MS, Mg−Li−G, and Mg−Li−MS−G composites with a heating rate of 10°C min−1.
The Mg−Li−MS−G composite possesses the best hydrogen storage performances among the various composites. Therefore, the energy barrier was further studied by calculating the activation energy for hydrogenation. Figure 6A shows the hydrogenation curves of the Mg−Li−MS−G composite at different temperatures. A two-step hydrogen absorption process is distinctly observed in the temperature range 275–350°C. In the first step, the hydrogen atoms are quickly absorbed at the particles surface with small increase in temperature. In the second step, the hydrogen atoms start to diffusion in the bulk material, resulting in a lower absorption rate. As the operating temperature increases, the hydrogenation rate is distinctly accelerated. The discrepancy between the first and second steps suggests that the hydrogenation of the Mg−Li−MS−G composite is governed by the diffusion of hydrogen in the bulk material. For the analysis of the apparent activation energy, the Johnson-Mehl-Avrami (JMA) formula is adopted (Avrami, 1939; Kempen et al., 2002). The equation can be written as
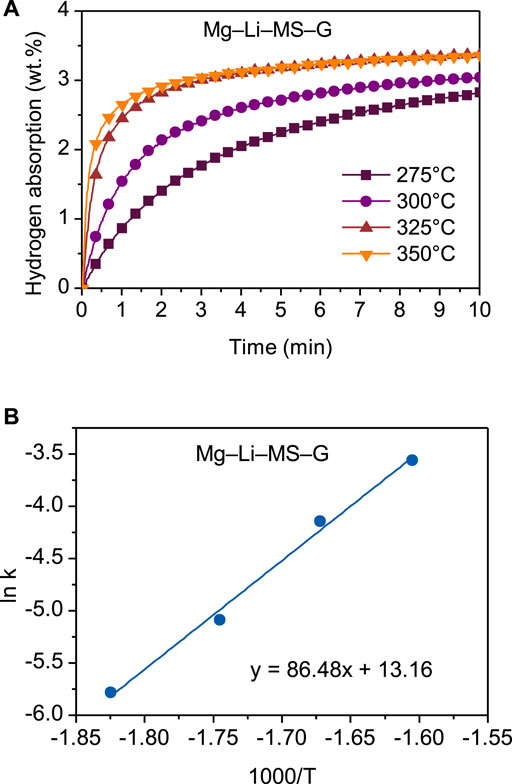
FIGURE 6. Hydrogenation curves under different temperatures (A) and Arrhenius’s plot (B) of the Mg−Li−MS−G composite.
Where α is the fraction already reacted at time t, η is the Avrami exponent, and k is the rate constant. Based on Eq. 1, the temperature-dependent reaction rate exponent, k, can be determined. It should be noted that the data in α range of 0.2–0.8 was selected for fitting by JMA equation. It is well known that the temperature-dependent reaction rate exponent, k, satisfies the Arrhenius equation, which is expressed as follows:
in which A is the pre-exponential factor, Ea is the apparent activation energy, R is the gas constant, and T is the absolute temperature. Figure 6B shows the Arrhenius’s plot for the Mg−Li−MS−G composite. Clearly, the plot of lnk versus 1/T exhibits a good linearity. The apparent activation energy Ea for the Mg−Li−MS−G composite was calculated to be 86.5 kJ mol−1. This is significantly lower than that of Mg/MgH2 (95–130 kJ mol−1) (Fernandez and Sanchez, 2002; Norberg et al., 2011). The reduction of the activation energy contributes directly to the improvement of the hydrogen storage performances of the Mg−Li−MS−G composite.
4 Conclusion
Mg2Si and graphene was utilized to improve the hydrogenation and dehydrogenation performances of the Mg−Li alloy. The hydrogenation of the Mg−Li alloy was not affected by the addition of Mg2Si or graphene. However, the dehydrogenation of the Mg−Li alloy was synergistically improved by co-addition of Mg2Si and graphene. The onset dehydrogenation temperature of Mg−Li alloy was reduced by 50°C after co-addition of Mg2Si and graphene. At 325°C, the Mg−Li−MS−G composite can release 2.7 wt.% of hydrogen within 2 h. The hydrogenation reaction activation energy of the Mg−Li−MS−G composite was calculated to be 86.5 kJ mol−1. Graphene can act as a grinding aid during the ball milling process, which leads to a smaller particle size of the Mg−Li alloy. Detailed enhancing mechanism inside the Mg−Li−MS−G composite needs to be studied further to understand the exact role of Mg2Si and graphene in tailoring the hydrogen storage properties of the Mg−Li alloy.
Data Availability Statement
The raw data supporting the conclusion of this article will be made available by the authors, without undue reservation.
Author Contributions
All authors listed have made a substantial, direct, and intellectual contribution to the work and approved it for publication.
Funding
This work was financially supported by National Natural Science Foundation of China (No. 52001079), and the Natural Science Foundation of Guangxi Province (2019GXNSFBA185004, 2018GXNSFAA281308, 2019GXNSFAA245050).
Conflict of Interest
The authors declare that the research was conducted in the absence of any commercial or financial relationships that could be construed as a potential conflict of interest.
Publisher’s Note
All claims expressed in this article are solely those of the authors and do not necessarily represent those of their affiliated organizations, or those of the publisher, the editors and the reviewers. Any product that may be evaluated in this article, or claim that may be made by its manufacturer, is not guaranteed or endorsed by the publisher.
References
Ali, N. A., and Ismail, M. (2021). Advanced Hydrogen Storage of the Mg–Na–Al System: A Review. J. Magnesium Alloys 9 (4), 1111–1122. doi:10.1016/j.jma.2021.03.031
Avrami, M. (1939). Kinetics of Phase Change. I General Theory. J. Chem. Phys. 7 (12), 1103–1112. doi:10.1063/1.1750380
Chao, P., Bao-Qi, F., Ge, J., Guang-Zhen, L., Zhu, W., Yun-Lei, T., et al. (2020). Cyclic Reaction-Induced Enhancement in the Dehydrogenation Performances of the KNH2-Doped LiNH2 and LiH System. Int. J. Hydrogen Energ. 45 (48), 25927–25934. doi:10.1016/j.ijhydene.2019.09.109
Chen, Y., Sun, X., Zhang, W., Gan, Y., Xia, Y., Zhang, J., et al. (2020). Hydrogen Pressure-dependent Dehydrogenation Performance of the Mg(NH2)2-2LiH-0.07KOH System. ACS Appl. Mater. Inter. 12 (13), 15255–15261. doi:10.1021/acsami.0c00956
Ding, X., Ding, H., Song, Y., Xiang, C., Li, Y., and Zhang, Q. (2020). Activity-Tuning of Supported Co-Ni Nanocatalysts via Composition and Morphology for Hydrogen Storage in MgH2. Front. Chem. 7, 937. doi:10.3389/fchem.2019.00937
Fernandez, J. F., and Sanchez, C. R. (2002). Rate Determining Step in the Absorption and Desorption of Hydrogen by Magnesium. J. Alloys Compd. 340 (1-2), 189–198. doi:10.1016/s0925-8388(02)00120-2
Halim, Yap. F. A., and Ismail, M. (2017). The Hydrogen Storage Properties of Mg-Li-Al Composite System Catalyzed by K2ZrF6. J. Phys. Chem. Sol. 104, 214–220. doi:10.1016/j.jpcs.2017.01.021
Hardian, R., Pistidda, C., Chaudhary, A.-L., Capurso, G., Gizer, G., Cao, H., et al. (2018). Waste Mg-Al Based Alloys for Hydrogen Storage. Int. J. Hydrogen Energ. 43 (34), 16738–16748. doi:10.1016/j.ijhydene.2017.12.014
Huang, Y., An, C., Zhang, Q., Zang, L., Shao, H., Liu, Y., et al. (2021). Cost-Effective Mechanochemical Synthesis of Highly Dispersed Supported Transition Metal Catalysts for Hydrogen Storage. Nano Energy 80, 105535. doi:10.1016/j.nanoen.2020.105535
Huang, Y., Shao, H., Zhang, Q., Zang, L., Guo, H., Liu, Y., et al. (2020). Layer-by-layer Uniformly Confined Graphene-NaAlH4 Composites and Hydrogen Storage Performance. Int. J. Hydrogen Energ. 45 (52), 28116–28122. doi:10.1016/j.ijhydene.2020.03.241
Huang, Z. G., Guo, Z. P., Calka, A., Wexler, D., and Liu, H. K. (2007). Effects of Carbon Black, Graphite and Carbon Nanotube Additives on Hydrogen Storage Properties of Magnesium. J. Alloys Compd. 427 (1), 94–100. doi:10.1016/j.jallcom.2006.03.069
Hui, Y., Guo, S., Yuan, Z., Qi, Y., Zhao, D., and Zhang, Y. (2020). Phase Transformation, Thermodynamics and Kinetics Property of Mg90Ce5RE5 (RE = La, Ce, Nd) Hydrogen Storage Alloys. J. Mater. Sci. Technol. 51, 84–93. doi:10.1016/j.jmst.2020.02.042
Imamura, H., Takesue, Y., Akimoto, T., and Tabata, S. (1999). Hydrogen-absorbing Magnesium Composites Prepared by Mechanical Grinding with Graphite: Effects of Additives on Composite Structures and Hydriding Properties. J. Alloys Compd. 293-295, 564–568. doi:10.1016/s0925-8388(99)00412-0
Jiang, W., Wang, H., and Zhu, M. (2021). AlH3 as a Hydrogen Storage Material: Recent Advances, Prospects and Challenges. Rare Met. 40, 3337–3356. doi:10.1007/s12598-021-01769-2
Kempen, A. T. W., Sommer, F., and Mittemeijer, E. J. (2002). Determination and Interpretation of Isothermal and Non-isothermal Transformation Kinetics: The Effective Activation Energies in Terms of Nucleation and Growth. J. Mater. Sci. 37 (7), 1321–1332. doi:10.1023/a:1014556109351
Lan, Z., Peng, W., Wei, W., Xu, L., and Guo, J. (2016). Preparation and Hydrogen Storage Properties of Mg-Al-Li Solid Solution. Int. J. Hydrogen Energ. 41 (14), 6134–6138. doi:10.1016/j.ijhydene.2015.10.150
Li, J., Wang, S., Du, Y., and Liao, W. (2019b). Catalytic Effect of Ti2C MXene on the Dehydrogenation of MgH2. Int. J. Hydrogen Energ. 44 (13), 6787–6794. doi:10.1016/j.ijhydene.2019.01.189
Li, L., Huang, Y., An, C., and Wang, Y. (2019a). Lightweight Hydrides Nanocomposites for Hydrogen Storage: Challenges, Progress and Prospects. Sci. China Mater. 62 (11), 1597–1625. doi:10.1007/s40843-019-9556-1
Li, Z.-L., Zhai, F.-Q., Qiu, H.-C., Wan, Q., Li, P., and Qu, X.-H. (2020). Dehydrogenation Characteristics of ZrC-Doped LiAlH4 with Different Mixing Conditions. Rare Met. 39 (4), 383–391. doi:10.1007/s12598-016-0711-x
Liu, B., Zhang, B., Yuan, J., Lv, W., and Wu, Y. (2021). Improvement of Hydrogen Dehydrogenation Performance of Lithium Amide Pyrolysis by ball Milling with Magnesium. Int. J. Hydrogen Energ. 46 (35), 18423–18432. doi:10.1016/j.ijhydene.2021.02.207
Liu, H., Lu, C., Wang, X., Xu, L., Huang, X., Wang, X., et al. (2021). Combinations of V2C and Ti3C2 MXenes for Boosting the Hydrogen Storage Performances of MgH2. ACS Appl. Mater. Inter. 13 (11), 13235–13247. doi:10.1021/acsami.0c23150
Liu, X.-S., Liu, H.-Z., Qiu, N., Zhang, Y.-B., Zhao, G-Y., Xu, L., et al. (2021). Cycling Hydrogen Desorption Properties and Microstructures of MgH2–AlH3–NbF5 Hydrogen Storage Materials. Rare Met. 40 (4), 1003–1007. doi:10.1007/s12598-020-01425-1
Liu, H., Ma, H., Zhang, L., Gao, S., Wang, X., Xu, L., et al. (2020). Wet Chemical Synthesis of Non-solvated Rod-like α'-AlH3 as a Hydrogen Storage Material. Front. Chem. 7, 892. doi:10.3389/fchem.2019.00892
Liu, H., Zhang, L., Ma, H., Lu, C., Luo, H., Wang, X., et al. (2021a). Aluminum Hydride for Solid-State Hydrogen Storage: Structure, Synthesis, Thermodynamics, Kinetics, and Regeneration. J. Energ. Chem. 52, 428–440. doi:10.1016/j.jechem.2020.02.008
Liu, J., Ma, Z., Liu, Z., Tang, Q., Zhu, Y., Lin, H., et al. (2020). Synergistic Effect of rGO Supported Ni3Fe on Hydrogen Storage Performance of MgH2. Int. J. Hydrogen Energ. 45 (33), 16622–16633. doi:10.1016/j.ijhydene.2020.04.104
Lu, C., Liu, H., Xu, L., Luo, H., He, S., Duan, X., et al. (2021b). Two-Dimensional Vanadium Carbide for Simultaneously Tailoring the Hydrogen Sorption Thermodynamics and Kinetics of Magnesium Hydride. J. Magnesium Alloys. doi:10.1016/j.jma.2021.03.030
Lu, Z-Y., Yu, H-J., Lu, X., Meng-Chen, S., Wu, F-Y., Jia-Guang, Z., et al. (2021). Two-dimensional Vanadium Nanosheets as a Remarkably Effective Catalyst for Hydrogen Storage in MgH2. Rare Met. 40 (11), 3195–3204. doi:10.1007/s12598-021-01764-7
Lukashev, R. V., Klyamkin, S. N., and Tarasov, B. P. (2006). Preparation and Properties of Hydrogen-Storage Composites in the MgH2-C System. Inorg. Mater. 42 (7), 726–732. doi:10.1134/s0020168506070077
Luo, Q., Li, J., Li, B., Liu, B., Shao, H., and Li, Q. (2019). Kinetics in Mg-Based Hydrogen Storage Materials: Enhancement and Mechanism. J. Magnesium Alloys 7 (1), 58–71. doi:10.1016/j.jma.2018.12.001
Neves, A. M., Puszkiel, J., Capurso, G., Bellosta von Colbe, J. M., Milanese, C., Dornheim, M., et al. (2021). Modeling the Kinetic Behavior of the Li-RHC System for Energy-Hydrogen Storage: (I) Absorption. Int. J. Hydrogen Energ. 46 (63), 32110–32125. doi:10.1016/j.ijhydene.2021.06.227
Norberg, N. S., Arthur, T. S., Fredrick, S. J., and Prieto, A. L. (2011). Size-Dependent Hydrogen Storage Properties of Mg Nanocrystals Prepared from Solution. J. Am. Chem. Soc. 133 (28), 10679–10681. doi:10.1021/ja201791y
Ren, Z., Zhang, X., Gao, M., Pan, H., and Liu, Y. (2021). Research Progress in Ti-Based Catalysts-Modified NaAlH4 Hydrogen Storage Materials. Chin. J. Rare Met. 45 (5), 569–582.
Singh, S., Bhatnagar, A., Shukla, V., Vishwakarma, A. K., Soni, P. K., Verma, S. K., et al. (2020). Ternary Transition Metal alloy FeCoNi Nanoparticles on Graphene as New Catalyst for Hydrogen Sorption in MgH2. Int. J. Hydrogen Energ. 45 (1), 774–786. doi:10.1016/j.ijhydene.2019.10.204
Si, T.-Z., Zhang, X-Y., Feng, J. -J., Ding, X-L., and Li, Y.-T. (2021). Enhancing Hydrogen Sorption in MgH2 by Controlling Particle Size and Contact of Ni Catalysts. Rare Met. 40 (4), 995–1002. doi:10.1007/s12598-018-1087-x
Sun, Z., Lu, X., Nyahuma, F. M., Yan, N., Xiao, J., Su, S., et al. (2020). Enhancing Hydrogen Storage Properties of MgH2 by Transition Metals and Carbon Materials: A Brief Review. Front. Chem. 8, 552. doi:10.3389/fchem.2020.00552
Thi Thu, L., Claudio, P., Van Huy, N., Singh, P., Pankaj, R., Klassen, T., et al. (2021). Nanoconfinement Effects on Hydrogen Storage Properties of MgH2 and LiBH4. Int. J. Hydrogen Energ. 46 (46), 23723–23736. doi:10.1016/j.ijhydene.2021.04.150
Vajo, J. J., Mertens, F., Ahn, C. C., Bowman, R. C., and Fultz, B. (2004). Altering Hydrogen Storage Properties by Hydride Destabilization through Alloy Formation: LiH and MgH2 Destabilized with Si. J. Phys. Chem. B 108 (37), 13977–13983. doi:10.1021/jp040060h
Wang, K., and Deng, Q. (2020). Constructing Core-Shell Co@N-Rich Carbon Additives toward Enhanced Hydrogen Storage Performance of Magnesium Hydride. Front. Chem. 8, 223. doi:10.3389/fchem.2020.00223
Wang, T., and Aguey-Zinsou, K.-F. (2021). Synthesis of Borohydride Nanoparticles at Room Temperature by Precipitation. Int. J. Hydrogen Energ. 46 (47), 24286–24292. doi:10.1016/j.ijhydene.2021.05.001
Wu, H., Sun, Z., Du, J., Ning, H., Guangxu, L. I., Wenlou, W., et al. (2018). Catalytic Effect of Graphene on the Hydrogen Storage Properties of Mg-Li alloy. Mater. Chem. Phys. 207, 221–225. doi:10.1016/j.matchemphys.2017.12.069
Xian, K., Nie, B., Li, Z., Gao, M., Li, Z., Shang, C., et al. (2021). TiO2 Decorated Porous Carbonaceous Network Structures Offer Confinement, Catalysis and thermal Conductivity for Effective Hydrogen Storage of LiBH4. Chem. Eng. J. 407, 127156. doi:10.1016/j.cej.2020.127156
Yao, P., Jiang, Y., Liu, Y., Wu, C., Chou, K.-C., Lyu, T., et al. (2020). Catalytic Effect of Ni@rGO on the Hydrogen Storage Properties of MgH2. J. Magnesium Alloys 8 (2), 461–471. doi:10.1016/j.jma.2019.06.006
Zeng, L., Qing, P., Cai, F., Huang, X., Liu, H., Lan, Z., et al. (2020). Enhanced Hydrogen Storage Properties of MgH2 Using a Ni and TiO2 Co-doped Reduced Graphene Oxide Nanocomposite as a Catalyst. Front. Chem. 8, 207. doi:10.3389/fchem.2020.00207
Zhang, J., Yu, X. F., Mao, C., Long, C. G., Chen, J., and Zhou, D. W. (2015). Influences and Mechanisms of Graphene-Doping on Dehydrogenation Properties of MgH2: Experimental and First-Principles Studies. Energy 89, 957–964. doi:10.1016/j.energy.2015.06.037
Zhang, L., Wang, K., Liu, Y., Zhang, X., Hu, J., Gao, M., et al. (2021a). Highly Active Multivalent Multielement Catalysts Derived from Hierarchical Porous TiNb2O7 Nanospheres for the Reversible Hydrogen Storage of MgH2. Nano Res. 14 (1), 148–156. doi:10.1007/s12274-020-3058-4
Zhang, M., Xiao, X., Luo, B., Liu, M., Chen, M., and Chen, L. (2020b). Superior de/Hydrogenation Performances of MgH2 Catalyzed by 3D Flower-like TiO2@C Nanostructures. J. Energ. Chem. 46, 191–198. doi:10.1016/j.jechem.2019.11.010
Zhang, X., Liu, Y., Ren, Z., Zhang, X., Hu, J., Huang, Z., et al. (2021c). Realizing 6.7 wt% Reversible Storage of Hydrogen at Ambient Temperature with Non-confined Ultrafine Magnesium Hydrides. Energ. Environ. Sci. 14 (4), 2302–2313. doi:10.1039/d0ee03160g
Zhang, X., Zhang, L., Zhang, W., Ren, Z., Huang, Z., Hu, J., et al. (2021b). Nano-synergy Enables Highly Reversible Storage of 9.2 wt% Hydrogen at Mild Conditions with Lithium Borohydride. Nano Energy 83, 105839. doi:10.1016/j.nanoen.2021.105839
Zhang, X. L., Liu, Y. F., Zhang, X., Hu, J. J., Gao, M. X., and Pan, H. G. (2020a). Empowering Hydrogen Storage Performance of MgH2 by Nanoengineering and Nanocatalysis. Mater. Today Nano 9, 100064. doi:10.1016/j.mtnano.2019.100064
Zhong, H.-C., Xu, J.-B., Jiang, C.-H., and Lu, X.-J. (2018). Microstructure and Remarkably Improved Hydrogen Storage Properties of Mg2Ni Alloys Doped with Metal Elements of Al, Mn and Ti. Trans. Nonferrous Met. Soc. China 28 (12), 2470–2477. doi:10.1016/s1003-6326(18)64893-9
Keywords: hydrogen storage, Mg-Li alloy, doping, graphene, Mg2Si
Citation: Huang X, Liu H, Duan X, Lan Z and Guo J (2021) Co-Addition of Mg2Si and Graphene for Synergistically Improving the Hydrogen Storage Properties of Mg−Li Alloy. Front. Chem. 9:775537. doi: 10.3389/fchem.2021.775537
Received: 14 September 2021; Accepted: 28 September 2021;
Published: 13 October 2021.
Edited by:
Feng Luo, East China University of Technology, ChinaReviewed by:
Yongfeng Liu, Zhejiang University, ChinaNoratiqah Sazelee, University of Malaysia Terengganu, Malaysia
Copyright © 2021 Huang, Liu, Duan, Lan and Guo. This is an open-access article distributed under the terms of the Creative Commons Attribution License (CC BY). The use, distribution or reproduction in other forums is permitted, provided the original author(s) and the copyright owner(s) are credited and that the original publication in this journal is cited, in accordance with accepted academic practice. No use, distribution or reproduction is permitted which does not comply with these terms.
*Correspondence: Haizhen Liu, bGl1aHpAZ3h1LmVkdS5jbg==