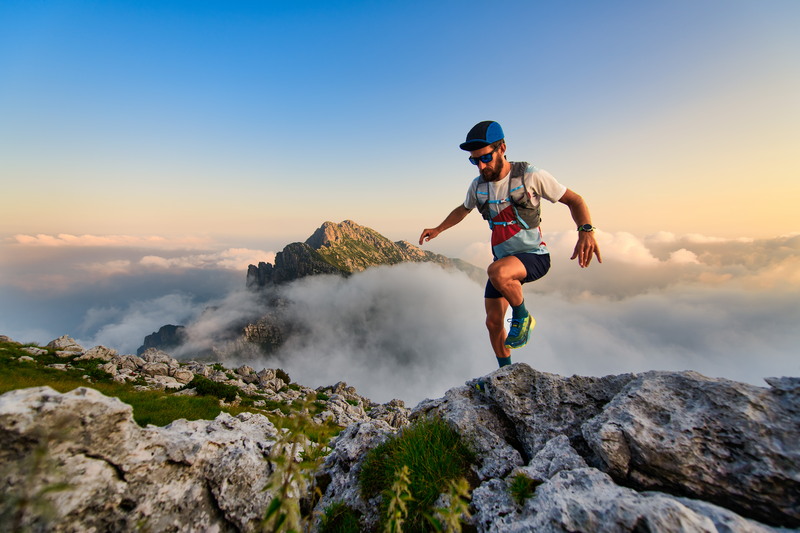
95% of researchers rate our articles as excellent or good
Learn more about the work of our research integrity team to safeguard the quality of each article we publish.
Find out more
REVIEW article
Front. Chem. , 26 May 2021
Sec. Solid State Chemistry
Volume 9 - 2021 | https://doi.org/10.3389/fchem.2021.685789
This article is part of the Research Topic Advances in Tribochemistry View all 8 articles
Over the decades, the application of mechanical force to influence chemical reactions has been called by various names: mechanochemistry, tribochemistry, mechanical alloying, to name but a few. The evolution of these terms has largely mirrored the understanding of the field. But what is meant by these terms, why have they evolved, and does it really matter how a process is called? Which parameters should be defined to describe unambiguously the experimental conditions such that others can reproduce the results, or to allow a meaningful comparison between processes explored under different conditions? Can the information on the process be encoded in a clear, concise, and self-explanatory way? We address these questions in this Opinion contribution, which we hope will spark timely and constructive discussion across the international mechanochemical community.
Chemical transformations initiated by mechanical energy appear to be the first reactions that humans learned to induce and control, even before thermal reactions were possible. In fact, the first combustion reactions were produced through mechanical action: by percussion or by friction, i.e. they were mechanochemical or tribochemical, if modern terminology were used. Throughout human history, mechanically induced chemical reactions have accompanied many significant technological advances. For example, since the discovery of black powder in ca. 220 B.C.E., explosives have allowed the advent of mining and have facilitated the construction of cities and infrastructures. More recently, the continued development of mechanochemistry promises to revolutionize the chemical industry, providing synthetic routes devoid of environmentally harmful solvents (James et al., 2012; Baláž et al., 2013). The potential for mechanochemistry to have paradigm-changing impact across the chemical sciences has placed the field amongst IUPAC’s ‘10 chemical innovations that will change our world’ (Gomollón-Bel, 2019).
The earliest written record of a mechanochemical transformation seems to be that by Theophrastus of Eresus, in his book “On Stones” of ca. 315 B.C.E (Takacs, 2000). Theophrastus describes the reduction of cinnabar to mercury through grinding using a copper mortar and pestle. Although grinding and milling were used extensively over the centuries for the processing of grains, minerals, and even pharmaceuticals, mention of mechanochemical processes in scientific literature did not reappear until the 19th century. These early reports include those by Faraday (1820) on the dehydration of crystal hydrates (Heinicke, 1984; Takacs, 2013), Carey-Lee (1866) on the decomposition of silver, gold, and mercury halides on grinding (Carey-Lea, 1892; Carey-Lea, 1894), and by both Ling and Baker (1893) (Heinicke, 1984; Takacs, 2013) and Flavitsky (Flavitsky, 1902; Flavitsky, 1909) who described organic chemical reactions upon grinding. The attention of mechanochemical investigation soon expanded to a wide range of material types, and explored an array of phenomena including the initiation of explosives by impact and friction (Bowden et al., 1947; Bowden and Gurton, 1949; Fox, 1975; Aduev et al., 1999), and the mechanical decomposition of polymers (Butyagin, 1971; Polukhina and Baramboim, 1975; Oprea, 1979; Sohma, 1989; Delogu et al., 2017). Similarly, mechanochemical investigation into areas including the chemical processes accompanying mining, metallurgy, and the manufacturing of various oxide and chalcogenide materials became a prominent direction of research (Senna, 1993; Butyagin, 1994; Boldyrev, 1996; Fernández-Bertran, 1999; Steinike and Tkáčová, 2000; Senna, 2001; Epelak, 2002; Boldyrev, 2006; Buyanov et al., 2009; Šepelák et al., 2012; Šepelák et al., 2013), expanding toward the preparation and processing of fine chemicals and pharmaceuticals (Baba et al., 1990; Kuzuya et al., 1991; Otsuka et al., 1994; Dubinskaya, 1999; Kondo, 2000; Boldyrev, 2004; Otsuka et al., 2011). The 20th century represents a period of remarkable development of the fundamental aspects of mechanochemistry and of significant progress in scaling mechanochemical reactions toward real-world industrial applications. Although progress in mechanochemistry through the 20th century was dominated by studies of metals, inorganic compounds, materials, and catalysts, significant advances were also made in the mechanochemistry of organic polymers and drug compounds and formulations (Boldyrev and Avvakumov, 1967; Butyagin, 1994; Boldyrev, 1996; Fernández-Bertran, 1999; Steinike and Tkáčová, 2000; Watanabe et al., 2001; Watanabe et al., 2002; Watanabe et al., 2003; Boldyrev, 2004; Boldyrev, 2006; Buyanov et al., 2009). A number of dedicated texts on the historical development of mechanochemistry are available elsewhere (Boldyrev and Tkáčová, 2000; Takacs, 2013; Boldyrev, 2018).
To date, mechanochemical approaches being applied to transformations from across the chemical sciences have been reported, spanning from the synthesis of inorganic and organic compounds [including those as complex as peptides (Hernández et al., 2017; Maurin et al., 2017)] through to the preparation of large porous frameworks such as metal-organic frameworks [MOFs(Stolar et al., 2017; Stolar and Užarević, 2020; Wang et al., 2020; Zhou et al., 2020; Głowniak et al., 2021; Stolar et al., 2021)]. Moreover, the scale of mechanochemical reactions has ranged from the mechanical manipulation of single atoms and molecules (predominantly, synthetic and natural polymers) using atomic force microscopy (Kaupp, 2009; Ribas-Arino and Marx, 2012; Makarov, 2016; Li et al., 2017) to the induction of reactions in multi-component inorganic and organic powder mixtures in ball milling reactors or extruders (Iwasaki et al., 2010; Am Ende et al., 2014; Oliveira et al., 2017; Andersen and Mack, 2018b; Egleston et al., 2020). Alongside synthetic covalent chemical reactions, a wide range of supramolecular assemblies have been also prepared by mechanical treatment, including cocrystals and salts (Myz et al., 2009; Weyna et al., 2009; Friščić, 2012; Myz et al., 2012; Braga et al., 2013; Hasa et al., 2015), as well as non-covalently bound mechano-composites such as drug delivery devices comprising active pharmaceutical ingredients with excipients (Shakhtshneider et al., 2007; Shakhtshneider et al., 2014a; Shakhtshneider et al., 2014b; Lomovsky et al., 2017; Ogienko et al., 2018; Bychkov et al., 2019; Adekenov et al., 2020; Skripkina et al., 2020). Moreover, many organic mechanochemical syntheses have been successfully scaled-up (Iwasaki et al., 2010; Am Ende et al., 2014; Crawford et al., 2017; Trofimova et al., 2018; Stolar et al., 2019; Baláž et al., 2020; Crawford et al., 2020; He et al., 2020; Titi et al., 2020; Stolar et al., 2021), offering a direct route to translate mechanochemical synthesis toward industrial scale applications. It can be therefore expected that many industrial syntheses will be soon conducted mechanochemically, alongside the long-standing technologies of inorganic mechanosynthesis and of powder processing e.g. in the pharmaceutical, pulp-paper, mining, explosives, and food processing industries.
Indeed, this enormous range of applications for mechanochemical preparations demands that the processes which govern their transformation must be equally diverse, as shown in the hierarchical diagram in Figure 1. There is some elegance to this complexity: many of the processes which govern mechanochemical reactions of complex systems can be largely deconstructed into some combination of the elementary processes which occur in simpler systems. For example, mechanical treatment of a single powder particle will still involve geometric distortion of its molecular substituents (Haruta et al., 2019), and there remains the potential for molecular or atomic electronic excitation/emission processes to occur. This behavior is clear for example in high pressure experiments of molecular solids, wherein mechanical action of the bulk lattice yields geometric (Fabbiani et al., 2005) and electronic distortions (Poręba et al., 2019) or excitations (Tulip and Bates, 2009) at the molecular or atomic level(Boldyreva, 2019; Katrusiak, 2019; Zakharov and Boldyreva, 2019). The dynamical stressing (compression or shearing) of solids can also cause chemical species within the solid state to approach each other at high velocities, akin to molecular collisions in fluids. Such dynamical interactions can occur either within a single particle (Landerville et al., 2009; Zhang et al., 2015; Steele et al., 2020), or at inter-particle contacts (Ferguson et al., 2019). These solid state “molecular collisions” have been suggested as the origin of slip-induced “hot spots” (Zhang et al., 2008; Zhang et al., 2015; Zhang et al., 2018), or even covalent bond formation (Engelke and Blais, 1994).
FIGURE 1. Hierarchical representation of the major effects (gray) of mechanical action on different systems, ranging from single molecules to multi-phase solid powder mixtures (gold).
That said, with increasing complexity of the system, many more and new pathways exist by which mechanical action can exert influence. This hierarchical phenomenology is again exemplified by the study of high-pressure phenomena in molecular solids. Mechanical force not only affects molecular geometry but can also influence the intermolecular non-covalent interactions, leading to changes in crystal packing (polymorphism). By manipulating crystal packing, mechanical force thus offers a route to modify bulk physical properties such as lattice stability, melting temperatures, and compressibility. Thus, although many of the elementary stages of a solution-based chemical reaction may still apply to mechanochemical reactions, many additional elementary stages must be also considered to fully account for the mechanism of mechanochemical transformations. Regardless of the exact elementary processes involved, mechanical action drives the system out of equilibrium, which may involve a classical phase transition (Drebushchak et al., 2011) or via some other transient metastable state (Butyagin, 1971). This intermediate state can endure e.g. under continuous mechanical action and provide modified tribological properties (Prentice et al., 2020; Reddyhoff et al., 2021), or relax when the mechanical perturbation is released to yield a reaction product (Boldyrev, 2006). Owing to the significant kinetic barriers in solid state reactions, this reaction product may not be always the most thermodynamically stable one (i.e. the global minimum of the system), but it will always be the most accessible product under the given mechanochemical conditions (Lin and Nadiv, 1979). Identifying, understanding, predicting, and ultimately controlling these pathways leading to the mechanical manipulation of matter is crucial, should mechanochemical approaches ever become equally controllable as the well-developed aspects of solution and gas-phase reactivity.
Deconvolution of these complex phenomena requires the use of a common language which allows the effective communication of the process being discussed. Only in this way can we hope for a concerted and coherent effort towards elucidating mechanochemical reaction mechanisms and driving forces, and therefore gain control over these reactions to make them possible to reproduce and scale. Despite decades of mechanochemical research, the need to agree on using certain terms, on how to define accurately and unambiguously the experimental procedures, and how to present the results have been not widely seen as necessary until very recently. For almost a century, the mechanochemical community remained relatively small, although it covered a diverse range of fields. Researchers knew not only the scientific research of the others but often knew each other personally. The basics of mechanochemistry, as well as the experimental and computational protocols were discussed regularly in original publications, and at many dedicated mechanochemical seminars and conferences. The developments in the field were regularly summarized in thoroughly detailed monographs and reviews, that have now become seminal (Thießen, 1965; Avvakumov, 1972; Boldyrev, 1972; Boldyrev, 1983; Heinicke, 1984; Tkáčová, 1989; Avvakumov et al., 2001; Suryanarayana et al., 2001; Delogu et al., 2004a; Boldyrev, 2006; Butyagin, 2006; Zyryanov, 2008; Buyanov et al., 2009). The foundation of the International Mechanochemical Association (IMA) (International Mechanochemical Association, 2020) under the guide of IUPAC in 1989, was an important event that marked the formation of a mature scientific community with a common language and a clear vision of the scientific field.
As an increasing number of groups have begun in recent years to enter the field of mechanochemistry independently of IMA, the quickly growing community has since become scientifically heterogeneous. In contrast to its original composition, the mechanochemical community is now becoming enriched with researchers from very different backgrounds and expertize, many of them being originally experts not in the solid-state, but in solution-based chemistry. This diversification in its membership has brought with it many new and exciting research challenges, leading to a much greater impact of mechanochemistry than ever before. Yet one cannot ignore the fact that with diversification of the community comes an expanding breadth of specialized scientific languages. As a consequence, the heterogenous community may not always understand each other effectively, or may become increasingly unaware of the mechanochemical knowledge that has been accumulated in early publications, that itself can be perceived as being written in “another scientific language”. There is the real danger that the lack of use of a common scientific language can prevent the community from meeting the challenge of constructing the “Tower of Mechanochemistry”, as it did millennia ago in relation to the Tower of Babel.
Anthropologists argue that humankind evolved due to our capacity to conceive abstract phenomena and communicate these phenomena through complexity of language. In this light, it is no wonder that philosophers have attached such significance to the selection and connotation of words. In Plato’s famous dialogue Cratylus, he argues: “a name is an instrument of teaching and of distinguishing natures, as the shuttle is of distinguishing the threads of the web” (Plato, 1961). The chemical sciences have followed true to Plato’s logic. Chemical reactions are denoted according to the type of energy used to initiate a chemical reaction, their nature is revealed through their name: thermo-chemistry, electro-chemistry, magneto-chemistry, photo-chemistry, and radiation-chemistry. Thus, adequately naming a chemical reaction requires an elementary understanding of the underlying chemical and physical processes.
In the early 20th century, Ostwald (Ostwald, 1919) noted reports that existing nomenclature in the chemical sciences did not fully represent the true nature of all observed chemical reactions, for Carey-Lea demonstrated a unique outcome of thermal- and mechanochemical reactions in metal halides (Carey-Lea, 1892; Carey-Lea, 1894). Correspondingly, Ostwald introduced in his 1919 textbook the term mechanochemistry to describe reactions in any state of aggregation which are initiated by mechanical force (impact and friction). A more specific term—tribochemistry—was subsequently proposed to denote only those chemical and physico-chemical changes which occur in solids in response to mechanical energy (Heinicke, 1970). The term tribochemistry was used widely throughout the 20th century in relation to processes that occur on grinding, ball milling, comminution, friction, wear, rubbing, and lubrication of solids. With growing diversity of tribochemical reactions, daughter terms became commonplace to facilitate more accurately the communication of the scientific work. These words included tribocatalysis, triboelectrochemistry, tribosorption, tribodiffusion, tribocorrosion, tribotechnology, tribomechanics, tribogalvanics, and tribometallurgy, each introducing specific subfields of tribology, the science uniting tribochemistry and tribophysics (Thiessen et al., 1966; Thiessen, 1974; Heinicke, 1984; Holmberg and Erdemir, 2017). A primary aim for introducing these “tribo” terms in addition to Ostwald’s term “mechanochemistry”, was to separate solid-state mechanochemistry from mechanically induced processes that occur in single molecules or liquids. In this way, physical phenomena induced by mechanical action in solids or at their surfaces, including phenomena like mechanical mixing and comminution, were to be denoted with a “tribo” prefix. All other mechanically induced phenomena were instead to be defined by a prefix “mechano”.
Despite growing popularity of tribological nomenclature, analogous terms prefixed by “mechano” remained in the literature as synonyms also for processes involving solids, including: mechanochemistry, mechanocatalysis, mechanocorrosion, and mechanotechnology. Moreover, the term mechanical alloying was introduced to define the process of forming intermetallic compounds and alloys by mechanical treatment of solid components, many of which could not be accessed by any other way than mechanical treatment (Suryanarayana et al., 2001; Benjamin and Volin, 1974; Koch, 1989; El-Eskandarany, 2020). Mechanical alloying processes are of great practical importance, which may account for the extensive publications of mechanical alloying studies and, consequently, of the very wide usage of this term in the scientific literature. The nomenclature regarding the mechanical manipulation of single molecules has remained much simpler. Only terms prefixed by “mechano” have been commonly used when discussing transformations of single-molecules induced by mechanical stretching of bonds, e.g. using an AFM cantilever (Kaupp, 2009; Ribas-Arino and Marx, 2012; Makarov, 2016; De Bo, 2018; Zhang et al., 2017; Beyer and Clausen-Schaumann, 2005), or when investigating biochemical and biophysical processes (Keller and Bustamante, 2000; Kushwaha and Peterman, 2020; Boocock et al., 2021). Figure 2 gives an idea of the relative frequencies of how the usage of different terms has changed with time. Tribology—the term introduced by Jost (Jost, 1990) in the 1960s—remains by far the most popular term to date, while mechanochemistry is much less used than tribology, or mechanical alloying. While the organic chemistry community appears to favor the term mechanochemistry, the terms tribology and tribochemistry are more popular amongst chemical engineers and the materials science community (Huq et al., 2020; Moshkovich et al., 2020; Moshkovich and Rapoport, 2020; Rosenkranz et al., 2020; Rosenkranz et al., 2021). In addition, the term mechanical activation is widely used in relation to thermal reactions that are facilitated by mechanical pre-treatment (Pavljukhin et al., 1983; Pavlyukhin et al., 1984; Boldyrev, 1996; Šepelák et al., 1996; Boldyrev, 1998; Boldyrev, 2006; Kumar et al., 2019; Singla et al., 2020).
FIGURE 2. The number of papers in Scopus each year in which the terms related to chemical reactions of solids induced by mechanical treatment are used in the title, abstract or as keywords.
What is in a name? That which we call a rose by any other name would smell as sweet. This famous phrase by W. Shakespeare serves an important lesson for science: the physical world does not depend on our description of it. Of course, our choice of nomenclature has no influence on the physical reality of chemical reactions. This nomenclature does, however, influence on our understanding, communication, and formulation of scientific principles. Nature is indifferent to our terminology. Scientists, in contrast, are prisoners to nomenclature. Without consistent and precise definition of scientific concepts, “the rose” may not smell as sweet.
Discussions of nomenclature in science has a long history. Most famous, perhaps, are the classifications of species proposed by Charles Darwin. The taxonomic classification of life demonstrates Plato’s reflection of a name in understanding the properties and connections between entities. Similar ontological classifications have been popular in chemistry throughout its history. For example, chemists routinely classify interatomic interactions according to an abstract definition of bond order: single, double, triple, etc. This precise nomenclature allows scientists to directly and unambiguously describe a characteristic of a molecule directly by the type of bond. Recently, a standard set of bond descriptions were suggested to define particular types of molecular interactions (Arunan et al., 2011; Desiraju et al., 2013; Aakeroy et al., 2019). Standardizing nomenclature has long been the focus of the IUPAC. More broadly, ensuring that well-defined and well-classified ontologies exist throughout the sciences is becoming increasingly recognized as the route to ensure Findable, Accessible, Interoperable, and Reusable (FAIR) scientific data (Hall and McMahon, 2016; Wilkinson et al., 2016).
So, what is in a name? Would that which we call “mechanochemistry” by any other name behave the same? Of course, the physical principles which govern mechanochemical reactions will behave independent of our chosen nomenclature, but will the conceptual constructions we use to rationalize, discuss, and direct scientific research be so resilient? The idea of complementing the term mechanochemistry by the term tribology (tribochemistry + tribophysics), to focus more on transformations involving solids (Jost, 1990), is clear and justified. In practice, the more general term mechanochemistry appears to survive. Moreover, it is increasingly used as a complete synonym of tribology, also when describing ball milling, grinding, and friction (Thiessen, 1986). This hazy nomenclature would not create much problem if it were always straightforward to identify which mechanically induced physical processes in solids were responsible for the chemical processes of bond cleavage and formation. This, however, is not the case. Defining accurately by its name the nature of a mechanically induced transformation has serious implications for the type and importance of physical processes which must be considered when seeking to understand mechanochemical transformations. Moreover, it is critically important to consider that molecules in the solid state cannot immediately react with one-another. Instead, some solid-state phenomenon must first occur which allows collisions not at the level of particles but at the level of molecules and atoms. The nature of this preliminary phenomenon depends on whether the reaction is mechano or tribochemical. For example, whereas mixing and comminution may be dominant preliminary phenomena in mechanochemical reactions, electrostatic charging or generation of defects certainly dominate many tribochemical reactions (Boldyrev, 2006). Hence, focus on chemical equilibria presented in terms of solution chemistry, where “one molecule transforms into another molecule”, are grossly oversimplified and neglect many of the critical physical phenomena which separates mechano/tribochemistry from solution chemistry.
Important phenomena such as triboelectric charging (Matsusaka et al., 2010; Cezan et al., 2019) and the mechanical generation of exposed surfaces (Belenguer et al., 2016; Schneider-Rauber et al., 2021) or defects are equally likely to occur in inorganic, organic, and polymeric compounds. It is probable that such phenomena involving defect formation (Boldyrev, 1973; Yelsukov et al., 2013) play a central role in most solid-state mechanochemical transformations, even if they are often overlooked and subsumed by explanations of “mere mixing”. Mechanically generated defects can range from radicals and the isomerization of molecules to extended stacking faults, dislocations, and the formation of shear-induced structures (e.g. shear bands). For example, it is known that grinding initially leads to particle size reduction (Lampronti et al., 2021), and ultimately (after a critical grinding or comminution limit is achieved) to the accumulation of defects within the solid structure (Boldyrev et al., 1996). This change in stress relaxation mechanism can lead to deep mechanical activation thereby greatly affecting the reactivity of the solid. Such effects have been suggested as being responsible for the extended induction periods observed in some mechanochemical reactions (Belenguer et al., 2019b). Mechanical treatment of a solid can also lead to the formation of mesophases, wherein superstructures within the phase become disordered to different degrees. Although this phenomenon appears to be more common in organic solids (Rybin et al., 2014; Descamps and Willart, 2016b; Shalaev et al., 2016; Rybin et al., 2019), it draws analogies to the mechanochemistry of inorganic compounds as well. For example, mechanical treatment can induce disordering of different sublattices such as the disordering or re-ordering of metal cations between octahedral and tetrahedral positions in spinels (Pavlyukhin et al., 1984; Tkáčová et al., 1996; Šepelák et al., 1996; Sepelak et al., 1997; Šepelák et al., 2007; Harris and Šepelák, 2018), or of Al and Si in aluminosilicates (Mackenzie et al., 2000). These mesophases can accompany the step-wize disordering, amorphization, and overall structural transformations in solids exposed to mechanical action.
Why then is the term mechanochemistry gaining more and more popularity? An intrinsic problem with applying the term tribochemistry in the specific sense as originally proposed—as opposed to the previously existing term mechanochemistry—is that we must know the mechanism of the process. Specifically, the term tribochemistry should only be used if it is truly a solid-state reaction. This is not obvious, especially for organic compounds, even if we start with solids (Rothenberg et al., 2001; Tumanov et al., 2017). In many cases, the transformation itself, including chemical synthesis, likely occurs in a fluid phase; the possible origin of this fluid phase can be diverse (Figure 3). This is quite often the case for ball milling, grinding in a mortar, or processing in an extruder a mixture of solid organic compounds (Boldyreva, 2013). Generally, the origin of this fluid phase can be classified as being intrinsic or extrinsic to the reacting system itself. Intrinsic origins include melting (or contact melting) (Saratovkin and Savintcev, 1941; Gerasimov and Boldyrev, 1996; Urakaev and Boldyrev, 2000a; Boldyrev and Tkáčová, 2000; Chadwick et al., 2007; Michalchuk et al., 2014; Humphry-Baker et al., 2016; Fandiño et al., 2020; Haneef and Chadha, 2020), sublimation of solids (Kuroda et al., 2004; Mikhailenko et al., 2004), or dehydration/desolvation (Losev and Boldyreva, 2014) which result from the excess heating of mechanical impacts or bulk heating during mechanical treatment. Where a solids’ glass transition temperature is above the milling temperature, one can consider also the formation of transient amorphous phases (Descamps and Willart, 2016a). It has become very common to explicitly add liquid to a powder mixture to facilitate mechanochemical transformations, a process dubbed liquid assisted grinding (LAG) (Bowmaker et al., 2009; Bowmaker, 2013; Sarmah et al., 2019). This is an obvious extrinsic origin of a fluid phase. Even where researchers do not explicitly add liquid, the powder may “grab” liquid from the environment in a process dubbed inadvertent liquid assisted grinding (IA-LAG) (Tumanov et al., 2017).
FIGURE 3. The potential origins of fluid phases in mechanochemical systems can be broadly classified as intrinsic and extrinsic, depending on whether they initiate within the solid phases or not.
Although the exact role of fluid phases in reactions that are assumed to occur in the solid state is not yet fully understood, various roles can be considered. The added fluid phase can certainly influence the mobility of material (by improving rheology, or by completely transferring the process into a solution or a melt) (Boldyreva, 2013; Lapshin et al., 2021). Additional to its influence on material mobility, melting can also drive erosion in microparticle impact (Hassani-Gangaraj et al., 2018), or can hinder impact-induced adhesion (Hassani-Gangaraj et al., 2017; Lapshin et al., 2021). A fluid, irrespective of its origin, can create hydrothermal conditions (Temuujin et al., 1998a; Boldyrev, 2002), can modify the mechanical properties of the solids via the Ioffe (Ioffe, 1936), Roscoe (Roscoe, 1934), or Rehbinder (Rehbinder, 1947) effects (i.e. the altering of bulk mechanical properties through surface modification) (Zhang et al., 2020; Dang et al., 2021), may influence triboelectric phenomena (Matsusaka et al., 2010), and can alter the relative stability of product phases through the selective stabilization of surfaces (Belenguer et al., 2018; Belenguer et al., 2019a). In many of these cases the process can and should be classified as tribochemical. However, where the process in fact occurs in the fluid phase, it can be no longer classified as tribochemical, nor does it unambiguously qualify to be denoted as a “dry” mechanochemical reaction.
By considering the possible intrinsic origins of fluid phases it becomes clear that some compounds are more likely to give rise to tribochemical transformations. For example, solids with high melting temperatures (primarily inorganic solids) will not melt or sublime during ball milling and therefore will most likely react tribochemically. In contrast, materials with low melting temperatures (e.g. most organic or coordination compounds) which are likely to melt during or as a result of mechanical treatment cannot be even strictly classified as mechanochemical, though tribochemical effects (e.g. electrostatic charging) may still be of importance at the elementary (molecular) level (Bowden and Gurton, 1949; Kajdas, 2013). This represents a critical difference between inorganic and organic “solid state” transformations under mechanochemical action (Boldyreva, 2013).
It follows from the above discussion that a reaction in a mechanochemical reactor that starts with solid reactants may not in fact be mechanochemical or tribochemical at all. This is the case when the chemical or physical transformation itself is not related directly to the absorption of the mechanical energy input. For volatile compounds, the solid reactants do not even require physical contact and can remain separated in space (Kuroda et al., 2004). In this particular case, the reaction is, strictly speaking, neither mechano-, nor tribochemical. In most reactions, however, no visible transformation is observed unless the compounds are treated in a mechanical apparatus. Yet, in many such cases the reaction is not mechanochemical, but thermal in nature; the role of the mechanical processing is limited to facilitating the mobility of the solid reactants, bringing them into contact with each other and/or by removing the solid products which are formed at the surface of the powder particles. Such processes are largely responsible for the success of new mechanochemical reactors such as the Resonant Acoustic Mixer (RAM) (Anderson et al., 2014; Michalchuk et al., 2018a; Titi et al., 2020). One could term such reactions as “mixing assisted thermal reactions”, as opposed to mechanochemical reactions. This can be taken as an analogue of stirred solution-phase reactions, wherein stirring does not cause the reaction, but simply facilitates the thermal reaction by driving mass transport.
These “mixing assisted thermal reactions” differ from “classical” thermal reactions in a few critical ways. “Classical” thermal reactions in solid mixtures (e.g. in high temperature solid-state synthesis) involve the heating of pre-mixed powders, wherein the powder remains largely unperturbed during the reaction. In contrast, reactions of thermal origin that occur during mechanical treatment are accompanied by dynamically changing local compositions (e.g. from mixing) and fluctuations in particle stress regimes. The mixing can be accompanied by the reduction of particle size (comminution), or changes in their agglomeration state. Together, these phenomena of macroscopic motion of particles, comminution or agglomeration, and the potential for strain-induced dissolution of one phase into another (Vasil’ev et al., 2006; Vasil’ev et al., 2009; Vasil’ev and Lomaev, 2011; Vasil’ev, 2012; Butyagin, 1984; Butyagin, 2005) yields intimate mixing across lengths of scale. One must also keep in mind that many solid + solid reactions are exothermic, since no entropy is gained during the reaction. Correspondingly, if the mechanical treatment is itself accompanied by significant heat evolution, mechanically initiated self-sustaining thermal processes become possible (Takacs, 1998; Bakhshai et al., 2002; Takacs, 2002; Delogu et al., 2004b; Maglia et al., 2004; Delogu and Takacs, 2014; Humphry-Baker et al., 2016). It follows that when mechanical mixing results in a chemical transformation, it is not clear a priori if the mechanical treatment of particles themselves plays a significant role, or if the particles are “merely brought into contact”. Regardless, any “mixing assisted thermal reaction” will be to a large extent governed by macrokinetics, i.e. heat and mass transfer processes (Urakaev and Boldyrev, 2000a; Urakaev and Boldyrev, 2000b; Delogu et al., 2003; Lapshin et al., 2021).
This thermodynamic feature—that solid + solid reactions are exothermic—raises an interesting question: do all mechanochemical reactions in fact have thermal mechanisms? When mechanical energy (U) is exerted on a system, some of the energy is absorbed by the material (e.g. as work, w) and the rest is released as heat (q): U = q + w. Using this rule for the conservation of energy, the amount of energy absorbed by the mechanically treated powder has been approximated by measuring the bulk temperature of the reaction vessel (Butyagin, 1967). What energy is then responsible for the transformation, the work or the heat? It is in fact the answer to this very question that distinguishes a mechanochemical transformation from a thermal transformation. Where the absorbed mechanical energy is itself responsible for the transformation (i.e. a mechanochemical reaction), the surrounding temperature has only indirect influence on the reaction. Once the transformation has occurred, excess energy is emitted from the system also as heat. Where a new product forms, for example in a multi-phase reaction, this can often take the form of exothermic nucleation. Although proving whether a reaction is thermo or mechanochemical can be challenging, a number of clear examples can be given, including the dark dimerization of aromatic compounds at high pressures (Engelke and Blais, 1994; Politov et al., 2010; Friedrich et al., 2020), the classic examples of the decomposition of metal halides by Carey Lea (Carey-Lea, 1892; Carey-Lea, 1894), the decomposition of alkali metal nitrates, bromates, and chlorates, which give different products and follows inverted trends upon heating and mechanical action (Boldyrev, 1972; Boldyrev et al., 1972; Urakaev et al., 1977; Boldyrev and Heinicke, 1979), or oxidation of gold by carbon dioxide (Thiessen et al., 1970). The relations between mechanochemical and thermochemical nature of the reactions can be compared with a situation when light and temperature act on a sample simultaneously. One can imagine a thermochemical reaction conducted in the presence of light: the mechanism does not become photochemical simply because light is present, it remains thermochemical. On the other hand, during a photochemical reaction, wherein the photon is absorbed, the reaction occurs on an excited state potential energy surface, and following relaxation, excess vibrational energy is emitted as heat. The heat is simply a byproduct of the photochemical transformation; one would not call such a reaction thermochemical.
It is therefore clear that many so-called “mechanochemical reactions” are not encompassed by the current IUPAC definition, which states that a mechanochemical process is “a chemical reaction that is induced by the direct absorption of mechanical energy” (Mechano-Chemical Reaction, 2009). Such distinctions, although semantic, play an important role when considering the types of physical phenomena which may play a role in driving the observed reaction. For example, effects of adiabatic compression, or the generation of vibronically excited states are unlikely to play a role in “mixing-assisted thermal reactions.” On the other hand, slow nucleation and crystal growth—which presumably dominate such thermal reactions—are very different from the fast cooperative interfacial propagation processes which can be expected for “true” mechanochemical reactions in which mechanical energy is directly transferred into high-level vibrational or electronic excitations (Coffey and Toton, 1982; Dlott and Fayer, 1990; Tokmakoff et al., 1993; Luty et al., 2002; Eckhardt, 2006; Michalchuk et al., 2018b; Michalchuk et al., 2019a; Michalchuk et al., 2021).
Selecting a proper term for a process involving solids that occurs in response to mechanical action is thus intrinsically challenging; the correct term can be only given after the mechanism for the reaction has been established. Even for fluids, deciding on the term “tribochemistry” or “mechanochemistry” may be not always straightforward. Not only can mechanical treatment convert solids to fluids, but it can also convert fluids to solids. Shearing of fluids (e.g. lubricants) often yields rigid supramolecular structures, which can inversely affect fluid properties such as viscosity (Apóstolo et al., 2019). Compression of fluids ultimately leads to their solidification. The solidification of long chain alkanes at relatively low pressures imposes serious implications for their lubricating effects. In certain examples such as mixtures of squalene with poly-
This vague borderline between “solid-state” and “fluid-state” processes under mechanical action only exacerbates the problem of defining the correct terminology to refer to a process involving mechanical action. Moreover, there is significant likelihood that many reactions will need to be reclassified as our understanding of the mechanisms of mechanochemical reactions expands. To paraphrase N. Copernicus, we know what we know, but we do not yet know what we do not know. This reality is of course impractical and indeed superfluous for most researchers who are more interested in the outcome of mechanical treatment rather than in the detailed mechanism of the transformation. What is important, however, is that the process can be reproduced by others based on the original, recorded description. This requires effective and accurate communication of the mechanochemical protocol used, with meaningful descriptions of all the parameters that are known to influence mechanochemical reactions. Hence, although we cannot know a priori how a seemingly “solid + solid” reaction will occur, we can know for sure how we treat the sample and analyze the outcome. It is also important to determine and record the appearance and state of the sample at the start and end of our treatment. It is this information rather than a name itself that must be reported and controlled as carefully as possible. Only in such a way can we hope to identify under what conditions solids react, and how to implement this technology most effectively.
If we define a reaction as thermochemical, it is sufficient to indicate the temperature at which it occurs. If the reaction is not isothermal, a protocol of modifying the temperature with time is required. For a photochemical reaction, energy, polarization, the intensity of light, the spatial characteristics of the irradiation (uniform, local, one-sided, etc.) must be defined. In contrast, where irradiation is discontinuous, the duration and frequency of light pulses must be stated.
For a mechanochemical transformation the type of mechanical action, experimental conditions, the composition and appearance of samples are much broader than for a thermal, or a photochemical reaction (Figure 4). In fact, the very questions as to “how we treat a sample” and “in what state the reactant and product phases exist” are not easily defined. Increasingly, new features are being identified to be crucial for determining the reaction pathway of mechanochemical transformations. For example, the ability for starting reagents to exist in different solid forms (polymorphs, polyamorphs, particles of different size and shape) is unique to the solid state. However, the starting forms of the solid reactants are often not reported in literature, under the assumption that they will be modified by treatment anyway. However, a starting polymorph can play a non-negligible role in determining the outcome of a mechanochemical transformation (Bouvart et al., 2018). Evidence has suggested also that the particle sizes of reagent materials can influence the mechanochemical transformation (Michalchuk et al., 2017). Similarly, the presence of unobservable contaminants (seeds) (Fischer et al., 2016) or crystal defects (Boldyrev et al., 1979) can be critical to the success or failure of a mechanochemical transformation. It is without doubt that more influential parameters will become known with further studies of mechanochemical reactions. At present we can only make every effort to record and describe as many parameters as possible regarding mechanochemical transformations and remain ready to adapt to new developments as they emerge.
FIGURE 4. Representation of the breadth of mechanical actions which are frequently used in mechanochemistry. (A) A broad classification of the types of mechanical action encountered in mechanochemical reactions. (B) Examples of common devices under each category.
The type of mechanical action used to promote mechanochemical transformations has a clear influence on its outcome (Michalchuk et al., 2013; Tumanov et al., 2014). This has become increasingly important owing to the rapidly expanding repertoire of mechanochemical reactors. These range from the original mortar and pestle and ball milling (e.g. planetary and vibratory) to twin screw extrusion (TSE), Resonant Acoustic Mixing (RAM), diamond anvil cell (DAC) technologies, and atomic force microscopy (AFM). The choice of mechanochemical reactor has significant influence on how the stress is applied to the sample in the first place (Figure 4).
The temporal evolution of mechanical action can be regarded as a first parameter to consider when distinguishing mechanochemical regimes of treatment. If a shock wave or a single pulse (e.g. a drop hammer, a knife, a gun, or a jet mill) is used, there is a single excitation event, followed by relaxation of the material via various channels (Figure 5A) (Boldyrev, 2006) For example, this is important in the case of the mechanochemistry of explosives (Michalchuk et al., 2019a), wherein the mechanical impact is suggested to induce super-heating of lattice phonons (Dlott, 1999), which ultimately yields a chemical response via dynamical metallization (Michalchuk et al., 2018b). Chemical transformations at a crack tip fall also into this category. As the crack propagates through the material, the exceptional transient stresses generated at the crack tip induce highly metastable states which, after the crack dissipates, relax through chemical recombination (Gilman, 1960; Gilman and Tong, 1971; Gilman, 1996; Gilman, 1998; Urakaev, 2007; Urakaev, 2008). During explosive initiation and detonation, chemical changes may in fact precede heat, such that the process is athermal and thus truly mechanochemical (Gilman and During, 2006). The rate of crack propagation (akin to the magnitude of a shock wave in explosives) dictates the magnitude of metastability and can even influence the relaxation product, i.e. the chemical products of the mechanochemical decomposition (Urakaev et al., 1977; Urakaev and Boldyrev, 2000).
FIGURE 5. Different influence of mechanical action on solids. (A) Flow diagram for the formation and subsequent relaxation of stress which are involved in mechanochemical reactions in solids, adapted from Ref (Boldyrev, 2006) (B) Schematic representation of the breadth of mechanical actions experienced in different types of mechanochemical reactors. (I) Combination of impact with shear/friction in various types of ball mills and attritors: (from left to right) rotational mill, attritor-stirring ball mill, vibration mill and planetary mill). (II) Dominated by impact in: (from left to right) pin mill, fall hammer, jet mill. (III) Dominated by shear/friction: (from left to right) mortar and pestle, rolling mill, and extruder. Figure adapted from Ref (Lapshin et al., 2021).
Typically, treatment of a sample by a single mechanical pulse is used in model studies, when the details of the effect of the mechanical action on the sample are studied—light, electron, radicals, or gas emission, heat evolution, propagation of the deformation wave, generation of phonons, a hot spot formation, etc. For example, the effect of controlled single impacts on the decomposition of silver oxalate to form Ag nanoparticles has been recently investigated by Delogu and colleagues (Torre et al., 2020). Studies on single pulses are particularly well suited for the in situ study of fast transformations, and indeed form the basis of safety technologies e.g. in testing explosives (c.f. the BAM Fall Hammer or the Rotter Impact Device).
If the mechanical action is long-lived, however, the relaxation event is altered, and the complexity of the problem increases. Long-lived action can itself be divided as being continuous or pulsed. In the former, the stress is applied and maintained. The stress must relax on a so-called force-modified potential energy surface (FM-PES), which can be significantly different than the surface of the fully relaxed material. Moreover, the rate at which the stress is applied can influence on the effective FM-PES upon which relaxation occurs (Fisch et al., 2015). Atomic force microscopy (AFM) can be used to stretch continuously a selected bond in a molecule. AFM and other dedicated stretching or bending device can be also used to deform a macroscopic object—a single crystal, a polycrystalline sample, a polymeric fiber—elastically or plastically. It can be used to study physical and chemical transformations in such strained samples (Boldyreva and Sidelnikov, 1987; Gutman, 1998; Rusanov et al., 2004; Chizhik et al., 2018). Alternatively, one can subject a sample to hydrostatic compression (a small amount in a diamond anvil cell, or a larger amount in a large volume press) and study either the transformations induced by compression itself, or the effect of compression on thermal, or photochemical transformations (Zakharov and Boldyreva, 2019; Galica et al., 2020).
Most devices are based on repeated mechanical treatment of samples in the form of pulses. In the case of repetitive dynamic stressing, relaxation of the stress occurs on the unstressed PES. However, depending on the intensity, pulse shape, duration and frequency of pulses, the relaxation may not be complete. This offers a potential means to accumulate energy with successive pulses (Butyagin, 1971; Belenguer et al., 2019b). Additionally, the relaxation channel (Figure 5A) can change during the course of the reaction, for example as the result of reduction in particle size toward the grinding limit (Boldyrev et al., 1996). The rate of pulsing can vary significantly, from e.g. 30 Hz in a conventional ball mill to tens of kHz using ultrasound radiation (Zhou et al., 2020). The types of mechanical action can be also different, including impact, shear stress, friction, rubbing, and cleavage, or any combination thereof, Figure 5B. Moreover, different types of action can be applied to fractions of the sample located at different sites within the same milling jar (Michalchuk et al., 2013), or can vary between successive pulses. The type and variability of mechanical action does not depend only on the choice of the mechanoreactor, but also on 1) the protocol of operation for the mechanochemical reactor (Zyryanov, 2008), 2) the nature of the sample (e.g. its rheology) (Hutchings et al., 2017; Michalchuk et al., 2017), 3) the presence of additives (e.g. liquids, polymers), and 4) the nature the milling bodies (Michalchuk et al., 2019b) (e.g. their material, mass, density, size and the total number). Each new pulse can interact with the same particle in potentially different geometry, or with another particle altogether. Under such dynamic stressing conditions, little is understood about what mechanical processes actually occur, and even less is understood about how to control them. Customized mechanochemical reactors which mimic specific types of mechanical action have been constructed in attempts to minimize the variation between reaction sites and successive impulses, and to monitor step-by-step the evolution of systems under consistent and repetitive stress (Tumanov et al., 2011; Tumanov et al., 2014). By using such customized mechanochemical reactors it has been possible to attempt to rationalize the outcome of more complex commercial mechanochemical reactors, such as ball mills or attritors (Michalchuk et al., 2013; Michalchuk et al., 2014). It is likely that at different stages (comminution, mixing, generating defects, reaction itself) effective mechanochemical transformations require that a sample be processed in different machines which are optimized for these particular phenomena. Developing customized mechanochemical reactors to simulate and study systematically mechanochemical transformations under idealized mechanical action is exceptionally important to rationalize how and why mechanical treatment exerts its effects. To this end, new mechanochemical reactors capable of probing at the nanoscopic level the evolution of solids exposed to mechanical treatment are being also envisioned (Thiessen, 2016).
Identifying the type of mechanical regime, and indeed the type of mechanical action is not obvious but in exceptional circumstances. In the general case, no sharp boundaries exist between the regimes of mechanical treatment. For example, in ball milling experiments the powder is constantly relocating through the jar. Consequently, the frequency and intensity of pulsed loadings is not constant. Indeed, an apparently “repetitive dynamic” regime may be in fact more accurately described by “single pulse” regime of reactivity. In contrast, if powder is tableted during impact, material remains under some compression. Moreover, when tableted, both the type of mechanical impact (e.g. from free impacts to restricted impacts) or potential for shear (e.g. particles against the jar walls) are greatly affected. Hence, when tableting occurs the regime of mechanical treatment changes unexpectedly. The stochastic and time-dependent formation of “reactive” and “unreactive” contacts, which are affected by mixing, can be also unpredictable. For example, in a two-phase reaction, only mechanical treatment of contacts which involve both phases (i.e. a heterogeneous contact) will react. In contrast, homogeneous contacts will not undergo reaction. Thus, the relaxation of mechanical stress depends also on the structure of the inter-particle contacts, which vary unpredictably with time. Even if one starts with treating a single phase (for example, when a polymorphic transition, an amorphization, or a decomposition are studied), as soon as the product starts being formed, the system becomes at least “binary”, or may contain an even larger number of unique phases. Correspondingly, each successive impact may strike already reacted material, rather than the remaining unreacted particles. This has dramatic consequences on the kinetics of the transformation (Michalchuk et al., 2018c). Even such “single phase” mechanochemical transformations turn out to be strongly controlled by macrokinetics, i.e., mass and heat transfer, comminution, mixing and aggregation (Delogu et al., 2003).
A true designation of a mechanochemical (or tribochemical) reaction requires a thorough understanding of its mechanism. In all but a few cases, this understanding is far from being achieved (The Breadth of Mechanochemistry). We must therefore ask the question: Is an understanding of the mechanism a prerequisite to garnering control over potentially mechanochemical reactions at all? We might not need to know what exactly is occurring, but we must understand collectively what actions are being done, and how to describe these actions amongst the community. The strategies being used across the domains of mechanochemical reactions must be effectively communicated. Only in this case can the community pool knowledge and ultimately achieve the mechanistic understanding required to develop robust and meaningful names. This need to develop a common language in reporting science has been crucial for example in progressing the field of crystallography. The creation of a Crystallographic Information File (CIF) (Hall et al., 1991) facilitated the deposition and automatic processing, visualization and validation of crystallographic structural data. Additionally, the CIF format facilitated the wide adoption of common standards for good practices in the collection and processing of structural data by highlighting to researchers which experimental parameters must be controlled and reported, such that anyone can validate and reproduce the results (Brown and McMahon, 2002; Brown and McMahon, 2006; Vaitkus et al., 2021). During its inception, researchers understood that the field remained in development, both in terms of technology and in understanding which parameters were required for the effective communication of crystallographic data. Hence, the CIF file was established to be dynamic and “naturally evolving”. The process continues still, including increasingly difficult cases such as structural data from powder diffraction, for modulated structures, and only very recently expanding to include high-pressure data (Dziubek, 2020). This situation is very similar to that which faces mechanochemistry today.
It is certain that no universal set of parameters or nomenclature can span the entirety of mechanochemical research. The diversity in mechanical action, stressing regimes, phases present in the system as reactants, additives, reactor materials, or inadvertently penetrating water or impurities, to list just a few parameters that need to be controlled, are too diverse. Yet, this is again synonymous with crystallography, wherein different diffractometer set-ups, collection strategies, sample types, all require a specific set of parameters to be recorded. It is instead likely that effective communication of mechanochemical sciences must evolve to include as many standard parameters (e.g. additives and reactant composition) as possible, whilst allowing the flexibility to dictate mechano-reactor specific information.
A significant step in this direction to standardize nomenclature is credited to Hanusa et al., Figure 6 (Rightmire and Hanusa, 2016). The addition of energy into chemical reaction schemes is easily denoted for traditional methods. For example, the photochemical activation is denoted by
FIGURE 6. Symbol proposed for mechanochemical activation by Hanusa et al. (Rightmire and Hanusa, 2016).
This symbol represents an excellent step toward realizing the need to discern clearly transformations resulting from mechanical treatment from those initiated by thermal, photo, or electrochemical stimuli. However, despite its popularity, the “three ball” symbol appears to have drawbacks when it is supposed to be used as a universal denotation for mechanically induced reactions.
Culturally, the symbol coincides with that of an ancient religious symbol that has existed since prehistory and is found throughout the world. A nearly identical symbol was subsequently adopted as the symbol for the “Banner of Peace”, symbolizing the protection of cultural property in times of war (Roerich Pact, 1935).
As was illustrated in the previous Sections, mechanochemistry differs from other branches of chemical science in that there exist many ways in which the mechanical action can be applied to the system. These different mechanical actions frequently yield different results. Material treated in a vibratory ball mill will be subjected to very different mechanical forces than the same powder treated in a planetary ball mill. Treatment in an extruder, jet mill, or in the rolling mill will be even more different. A single symbol cannot be therefore sufficient to define a general regime of mechanical treatment. Moreover, the presentation of milling balls is not relevant for example in many organic syntheses wherein excellent and scalable results were obtained not by impact in ball mills, but by shear in mortars, extruders, or rollers (Crawford and Casaban, 2016; Andersen and Mack, 2018b; Stolar et al., 2019; Ali El-Remaily et al., 2020; Crawford et al., 2020; Margetić and Štrukil, 2020). In fact, a vast majority of efficient and scalable mechanochemical types of treatment are “ball free” (ultrasonic, RAM, TSE, jet milling, pin milling, rolling-milling, grinding in a mortar, to name just a few).
The specific reactivity of materials under different types of mechanical action has been known for decades. Most famous, perhaps, is the reactivity of energetic materials, whose friction and impact sensitivities can differ enormously. Correspondingly, specialists in energetic materials research make explicit effort to ensure that the type of mechanical action is reported alongside the magnitude of perturbing energy; this reporting and testing procedure has been internationally standardised (UNECE, 2009). It is not surprising to find that the behavior of other organic systems is also mechanoreactor-dependent. For example, in the case of the “piroxicam + succinic acid” system, a co-crystal is formed from the two components on repetitive impacts by a falling ball (Tumanov et al., 2014). On the contrary, piroxicam: succinic acid co-crystal decomposes into the components on grinding when friction dominates (Tumanov et al., 2014). Uninterrupted ball milling of a mixture of glycine and malonic acid gives a different product as compared with the outcome of a treatment that is interrupted intermittently and where the sample is mixed manually (Michalchuk et al., 2013; Michalchuk et al., 2014). The work by Belenguer and colleagues demonstrates clearly how the selective choice of ball milling protocol can be used to target with great reproducibility the polymorphic form of organic solids (Belenguer et al., 2018; Belenguer et al., 2019a). The epsilon-polymorph of chlorpropamide can be transformed into the alfa-polymorph only on cryogrinding at the liquid nitrogen temperature, whereas no transformation is observed on ball-milling at room temperature (Drebushchak et al., 2011). Mechanical treatment of the beta-, gamma-, delta-polymorphs of chlorpropamide gives different products, depending on the choice of the starting form, the type of treatment (grinding in a mortar, simulated impact and shear, or during ball milling) and the presence of a small liquid additive (Bouvart et al., 2018). Liquid assisted Resonant Acoustic Mixing of carbamazepine and nicotinamide gives different products depending on the magnitude of acceleration (Michalchuk et al., 2018a). Such examples are not limited to organic reactions. For example, depending on the rate of crack propagation in crystalline nitrates and chlorates, different products are formed on their mechanolysis (i.e. mechanochemical bond rupture and formation of radicals) (Urakaev et al., 1977). The dissolution rate of quartz in hydrofluoric acid was also shown to depend critically on the type of mechanical treatment, with vibratory milling yielding slower dissolution kinetics than jet milling (Heinicke, 1984). Similar effects are observed for the formation of a Zn—fumarate metal-organic framework, which forms the tetrahydrate upon intense treatment in a SPEX-8000 mill, but a pentahydrate upon restricted impact treatment or laboratory vibratory ball milling (Strobridge et al., 2010; Tumanov et al., 2012). The rate of mechanochemical synthesis of inorganic solids has been also shown to depend critically on the choice of mechanochemical reactor. For the synthesis of aluminosilicate geopolymers from 1:1 layer-lattice minerals, planetary ball milling at 400 rpm using a sample: milling media mass ratio of 1:50 (3 mm diameter ZrO2 balls) took 20 h of mechanical treatment. Instead, this reaction took only 15 min using a more energetic vibratory ball mill with a tungsten carbide bowl and rings (MacKenzie et al., 2007).
It is thus increasingly clear that many often-over-looked parameters can influence on a mechanochemical transformation. Additional to the choice of mechanoreactor (Tumanov et al., 2014), this includes the initial polymorphic form (Bouvart et al., 2018), the inclusion of additives (solid, liquid, or gaseous) (Fischer et al., 2016; Hasa et al., 2016; Belenguer et al., 2018), the bulk temperature of the mechanoreactor (Andersen and Mack, 2018a), the atmosphere in which the reaction occurs (Tumanov et al., 2017), the rate of mechanical stressing (Michalchuk et al., 2018a), the mass and material of the milling balls and jars (Kulla et al., 2019; Michalchuk et al., 2019b; Germann et al., 2020). Certainly, many additional and unsuspected parameters can also exert significant influence over control in mechanochemistry.
Despite this, modern mechanochemical literature typically describes the applied mechanical action in general terms. For example, transformations are often described as occurring under “ball milling conditions”; in many recent papers the mechanochemical reactions are denoted with a general symbol as in Figure 6. The onus thus remains on the careful reader to identify the type of mechanoreactor, and subsequently the main type of mechanical action being applied. This information can be given in a concise form in the Experimental, or, even more difficult to see immediately, in Supplementary Material. A considerable amount of crucial information is therefore not immediately visible, even if available in the publication. In the absence of a “check list” indicating all the important experimental details that must be reported, it is also not uncommon that crucial information is missing. This is often the case, when mechanochemical work is being reported and published in general interest chemistry, physical chemistry, synthetic organic chemistry journals, rather than in the specialized solid-state, materials science, chemical engineering, or tribochemistry journals.
We propose a demonstrative model for a more elaborate, albeit concise, description of a mechanochemical reaction. It is our hope that such a pictographic “nomenclature” will facilitate clarity of communication whilst encouraging researchers to share vital information regarding mechanochemical syntheses. Inspired by the standard elemental symbols used on the periodic table, the example nomenclature emphasis is on the type of mechanical action, which is placed at the center of the symbol. Additional parameters which are currently known to affect the outcome of mechanochemical transformations are indicated systematically in the surrounding space, Figure 7. Such a formalism could make great strides toward ensuring comparable, consistent, and reproducible reporting of mechanochemical reactions.
FIGURE 7. Mechanochemistry at a glance. Left: Schematic representation of the structure of the proposed mechanochemical reaction symbol. Types of symbols see Table 1. Right: Example of the symbolic representation of a mechanochemical reaction performed in a vibratory ball mill for 20 min at 30 Hz under LAG conditions using ACN at 45°C under N2 atmosphere.
In this representation, parameters are given that are known to affect the results of a reaction. These include:
Additive: a solid, liquid, or polymer that is added to the mixture, in order to facilitate the physical transformation, and may or may not be chemically involved in the transformation. This includes processes such as liquid assisted grinding (LAG), ionic liquid assisted grinding (ILAG), polymer assisted grinding (POLAG), and the addition of polymer to affect rheology. We suggest that the symbol contains a short acronym to label the additive, for example acetonitrile—ACN.
Temperature: In cases where the vessel temperature is explicitly controlled (either heating or cooling), the temperature can be indicated here. We suggest that the temperature is denoted alongside the associated symbol.
Known chemical reactant: In addition to denoting the additive, any species which are known to be chemically involved in the reaction should be denoted. This includes catalysts, also in the cases where the milling bodies act as catalysts themselves. We suggest that a short acronym be added to label the reactant species, for example 1,8-Diazabicyclo [5.4.0] undec-7-ene—DBU.
Atmosphere: An indication as to the atmosphere within the milling vessel should also be specified. This may be ambient atmosphere (atm), dry air (dry), or any other atmospheric conditions.
Primary mechanical action: A symbol should be selected to best represent the type of mechanical action being implemented. Additional information regarding reaction time and mechanoreactor conditions (e.g. frequency) should also be given.
These suggestions extend significantly the idea that has been recently expressed in the literature that at least the catalyst which is important for a mechanocatalysis must be added to the symbol of the mechanical treatment (Pickhardt et al., 2020).
To facilitate the consistent use of this system, we have established a preliminary set of suggested symbols, Table 1. The set of symbols can be easily extended e.g. for new types of mechanoreactors or additives.
TABLE 1.. Potential symbols to be used for each major type of mechanical action and experimental conditions.
Let us consider a few examples to illustrate, how much clearer experimental conditions can be at a first glance if we use these pictographic descriptions.
As a first example, we compare the frequently used mechanochemistry symbol (Figure 6) to the alternative nomenclature proposed here, with a simple ball mill grinding cocrystal formation, Figure 8 (Michalchuk et al., 2017). In the original nomenclature, no additional information is visible as to the experimental conditions. In contrast, the proposed new graphical nomenclature immediately allows the reader to identify this as a vibratory ball milling reaction at 30 Hz for 20 min, under atmospheric conditions. The LAG conditions are also visible in the new reaction, in which the water originates from the OAD. Similarly, examples of bottom-up mechanochemical synthesis (BUMS) of inorganic nanoparticle formation are being increasingly common (Rak et al., 2014; Rak et al., 2016; de Oliveira et al., 2020a; de Oliveira et al., 2020b; de Oliveira et al., 2020c). BUMS involve a number of critical processing features, including the addition of reducing agent and stabilizers alongside the mechanochemical conditions. The use of pictographic nomenclature makes immediately clear the use of planetary ball milling for BUMS of Au nanoparticles from HAuCl4, Figure 8B (Moores, 2018).
FIGURE 8. (A, B) Comparison of a simple vibratory ball milling co-crystal formation. (A) The original nomenclature (Michalchuk et al., 2017) and (B) the proposed nomenclature. (C–D) Comparison of nomenclature for the BUMS of Au nanoparticles by planetary ball milling with (C) original nomenclature and (D) recast using the proposed pictograms. Note the choice of planetary milling is only clear in the latter.
It is next worth considering a more complex reaction—that of the vibratory ball milling-induced disulfide exchange reaction, Figure 9 (Belenguer et al., 2019b). In the original publication, the ball milling reaction was denoted as in Figures 9A,B. The catalyst (here DBU) is shown above the reaction arrow, as well as the LAG conditions in ACN. No further information is given as to the nature of the energy source, the physical state of the dbu, the atmospheric conditions or any temperature control. Instead, the readers must find this information for themselves. All of this information is instead visible pictorially using the proposed general nomenclature for mechanochemical reactions, Figures 9C,D. It is immediately evident that the reaction is conducted by vibratory ball milling at 30 Hz under atmospheric conditions, over 30 min for LAG and 45 min for neat grinding (NG), and in the presence of liquid DBU. Furthermore, it is obvious that the two reactions differ only in the presence (or not) of the liquid additive, ACN. Hence, with little extra effort, an enormous amount of additional information (much of which was not present in the original manuscript) is now immediately accessible to the reader. This simplicity of the pictographic representation is equally applicable to inorganic reactions, such as the double salt metathesis between KI and CsCl under vibratory ball milling conditions, Figure 9E (Ban et al., 2017; Lampronti et al., 2021).
FIGURE 9. (A–D) Reaction schemes for the mechanochemical disulfide bond formation. (A, B) adapted from literature, Ref (Belenguer et al., 2019b). (C, D) The same reactions using the proposed general symbols for mechanochemistry. (E) Reaction schemes for ionic exchange in inorganic salts in a vibrational mill (Lampronti et al., 2021).
An additional feature that is missing from current mechanochemical literature is a schematic approach to denote the type of additive being used. This is of primary concern when comparing the effect of the common approaches of LAG, ILAG and POLAG. To demonstrate the strength of the proposed nomenclature, we selected representative examples of each method and show the immediate recognition of these three concepts, schematically, Figure 10. Without the need to deeply consider the text, or indeed understand the physical nature of the additive, the reader is immediately aware how these three vibratory ball milling reactions differ.
FIGURE 10. Using the proposed nomenclature to describe mechanochemical transformations with different types of additives. (A) An example of liquid assisted grinding formation of Ce based framework (Wilke et al., 2018) (B) An example of ionic liquid assisted grinding for the formation of caffeine + glutaric acid cocrystals (Mukherjee et al., 2018) (C) An example of polymer assisted grinding for the formation of phenazine + mesaconic acid cocrystals (Hasa et al., 2015).
Variation in temperature is also readily visible through use of the proposed nomenclature. This can be exemplified by the effects of cryo-temperatures on milling of
FIGURE 11. (A) Using the proposed nomenclature to describe mechanochemical transformations that differ according to temperature. (B) An illustration of the change in molecular conformations on cooling, which is reversible without a mechanical treatment, but is preserved (interlocked) after the molecular layers have been shifted on cryogrinding. (C) The self-sustaining mechanosynthesis of TiB2 under planetary and vibratory ball milling conditions.
The need to specify explicitly the type of mechanical action within mechanochemical protocol is exemplified by the co-crystal formation of piroxicam and succinic acid, Figure 12A (Tumanov et al., 2014). The use of the triple milling ball symbol of Figure 12A would be wholly insufficient in such cases. The differing effects of friction and impact are instead captured explicitly within the proposed system, and a reaction scheme based upon this nomenclature allows immediate recognition of this important mechanochemical phenomenon. The difference in mechanochemical reactivity of energetic materials is also exemplary of the need to make clear the type of mechanical action being applied. Ammonium perchlorate, for example, initiates ca. 5 J mechanical impact, but remains insensitive (i.e. up to 360 N) when exposed to friction, Figure 12B (Roberts and Royle, 1991).
FIGURE 12. Using the proposed nomenclature to describe mechanochemical transformations that differ according to mechanoreactor. (A) Shearing action leads to dissociation of the 2:1 piroxiam:succinic acid cocrystal phase into its coformers, whereas impact action on powder of the coformers leads to formation of the cocrystal. (B) Difference in mechanical reactivity of ammonium perchlorate to impact and friction.
The material of the milling jar and milling bodies can be important for the kinetics, the product composition (Germann et al., 2020) and apparent stability (Kulla et al., 2019), and the very possibility of a transformation on ball-milling. They can act as catalysts of the transformations of the powders which are hit by the balls. Such examples of mechanocatalysis have been documented both for inorganic (Grätz et al., 2020; Li et al., 1999; Chen et al., 2000) and organic (Pickhardt et al., 2020; Haley et al., 2016; Sawama et al., 2018; Cook et al., 2013; Chen et al., 2015; Vogt et al., 2021; Ardila‐Fierro and Hernández, 2021) compounds. For example, the oxidative coupling of tetrahydroisoquinolines with nitromethane by vibratory ball milling with solid additive DDQ was facilitated by using Cu milling balls as catalyst rather than adding another catalytic material to the reaction mixture, Figure 13A (Su et al., 2011). Similarly, the ball milling material can play an important role in the treatment of inorganic phases, as in the case of the polymorphic transformation of Bixbyite (Y2O3) under planetary ball milling conditions. When milled using steel balls, a monoclinic phase is formed, whereas the Fluorite structure is obtained when ZrO2 milling bodies are used, Figure 13B (Begin-Colin et al., 1995). Also the mechanochemical formation of carbon allotropes (fullerenes, carbon nanotubes, carbon onion structures, etc.), which is known to be catalyzed by iron and iron alloys (Zhang et al., 2011; Zhang et al., 2012; Zhang et al., 2014; Velasquez et al., 2016), can be sensitive to the choice of mill (Güler and Evin, 2015), or the substitution of steel milling balls and jar for another material (Surov, 2004). Interestingly, the substitution of steel for ZrO2 seemed to have no significant effect on the mechanochemical synthesis of graphene oxide by neat ball milling of pristine graphite (Mahmoud et al., 2018). In all cases involving organic and inorganic reagents, these small details regarding the milling conditions can be again readily observed using the pictographic nomenclature.
FIGURE 13. Visualizing the effects of milling ball material on mechanochemical reactions. (A) Using the Cu milling balls as catalyst for an oxidative coupling reaction. (B) The formation of two unique polymorphic forms of Y2O3 depending on the material of milling balls during planetary ball milling.
Mechanochemical techniques have now been applied to an enormous array of materials syntheses, well beyond what can be covered here. For example, mechanochemical covalent chemical reactions have been reported (Andersen and Mack, 2018b; Bolm and Hernández, 2019; Tan and García, 2019), spanning classical condensation (Haferkamp et al., 2019) or cyclization (Andersen and Mack, 2017) reactions through to metal-catalyzed (Pickhardt et al., 2020) or piezocatalyzed reactions (Kubota et al., 2019). Regarding inorganic materials, syntheses and modifications have been described for hydrated oxides (MacKenzie et al., 1999; Mehrotra et al., 2016; Alex et al., 2020), mixed oxides and ceramics (Balaz et al., 1994; Mackenzie et al., 2000; Temuujin et al., 2000; MacKenzie and Barneveld, 2006), silicates (Temuujin et al., 1998a; Temuujin et al., 1998b; MacKenzie et al., 2007), and high entropy alloys (Kumar et al., 2017; Balcerzak et al., 2019; Kamalakannan et al., 2019), amongst many others. We note that the pictographic representation is equally applicable to any reactions that occur as a result of mechanical action from across all aspects of chemical reactivity, Figure 14. Comparison of the pictographic representations for mechanochemical transformations of very different chemical species reveals immediately the diverse conditions required. It is readily apparent that inorganic compounds tend to be prepared using long duration planetary ball milling conditions under controlled atmospheres, whereas soft materials are prepared by gentler mechanical conditions and often benefit from the addition of liquid additives. Hence, not only does this pictographic representation allows rapid identification of experimental conditions being reported, but also offers a facile approach to identifying trends in experimental conditions successfully applied across the chemical and materials sciences. We therefore expect this clear and concise approach for representing mechanochemical transformations to facilitate new generalisations of mechanochemistry toward targeted and rapid design of new materials and molecular syntheses.
FIGURE 14. Pictographic representation of literature mechanochemical reactions for a diverse selection of chemical systems, including planetary milling of alloys (Wang and Qin, 2003; Enayati et al., 2004), metal oxides (Stößer et al., 2013), and nitrides (Nash et al., 2016) (e.g. hexagonal boron nitride h-BN converting to defect laden hexagonal boron nitride dh-BN), vibratory ball milling of metal organic frameworks (Batzdorf et al., 2015), and Resonant Acoustic Mixing cocrystal synthesis (Michalchuk et al., 2018a).
The mechanochemical community has expanded significantly in recent years. Throughout most of the 20th century, mechanochemistry was the focus of a smaller and relatively homogeneous scientific community of predominantly solid-state scientists. Now, the community of mechanochemists has flourished, incorporating experts from a wide range of scientific backgrounds. To date, membership in the mechanochemistry field includes researchers from all branches of chemistry, physics, materials sciences, pharmaceutical sciences, biological sciences, and engineering. Many of the newcomers are themselves trained experts in solution or gas phase reactivity, thereby bringing with them many unique viewpoints on phenomena of chemical reactivity. The diversification of the mechanochemical community has triggered new, challenging and fundamentally important scientific questions and has led to mechanochemistry achieving more global impact than ever before.
Mechanochemistry today is understood to include much more than what is strictly defined by IUPAC as a “chemical reaction that is induced by the direct absorption of mechanical energy” (Mechano-Chemical Reaction, 2009). The term mechanochemistry has grown to include any transformation that is observed during or after any type of mechanical treatment, regardless of the exact role of the mechanical action. Moreover, the term mechanochemistry is applied equally to transformations which occur upon stretching of single molecules, through to transformations within and between solids (including those which involve fluid intermediate states). Any transformation that is somehow facilitated by mechanical energy, or reactions that result from thermal- or photochemically induced stress and strain in a solid [the chemomechanochemical effect (Boldyrev, 2018)] seem now to be denoted as “mechanochemical”. Thermal or photochemical transformations in solids which have been mechanically pre-treated are similarly denoted as being “mechanically activated”, and hence also fall within the current paradigm of mechanochemistry (Boldyrev, 2018; Galwey, 2020; Shields et al., 2020).
With this growing diversity of the community and the phenomena being explored comes a confusion of scientific languages on the scale of the Tower of Babel. Terminologies and jargon used by experts from one discipline are often misunderstood by experts from a different background. Similarly, much of the over a century’s worth of research in mechanochemistry that is written in the scientific language of 20th century mechanochemical pioneers remains largely incomprehensible to many who enter the field. Moreover, many of these original works have been not digitalized, and are thus not easily accessible until recently. Advances in modern digital technology have made these precious papers and their translations available via online platforms, thereby allowing the global community to stand on the shoulders of the ancestral mechanochemical giants. Despite these digital advances, there is still a large miscommunication between the established and emerging mechanochemistry communities. Many well-documented phenomena are unfortunately being regularly re-discovered, with many new terminologies being coined to describe them.
Although in principle, science does not care how it is called, this has the knock-on effect of hindering how the scientific community can discuss, communicate, interpret, search the literature, and hence progress its collective understanding of the field. For example, many who accomplish an organic synthesis in a mechanical device do not realize that they in fact deal not only with a chemical transformation, but with a plethora of tribochemical phenomena. By considering only one aspect of the whole, one risks to miss the elegance that nature has laid before us. For an elephant investigated in parts by blind men may be easily mistaken for a rope, a leaf, or a wall. In this same way, the strict isolation of tribo- and mechanochemistry exists only in the minds of humans.
The growing interest in the mechanochemistry of organic compounds has revealed many new parameters which must be controlled to successfully achieve the reproducible mechanosynthesis of molecules and materials. These new parameters are of course in addition to those that were traditionally considered in tribochemistry and inorganic mechanochemistry. Parameters which are presently known to influence mechanochemical transformations include: the starting polymorph; the size and shape of particles; the type of mechanical action; the atmosphere under which the reaction has occurred; the presence and quantities of additives (solids, liquids, gases, polymers) even if they may not obviously participate in the reaction; the presence of catalysts, including those present as the materials of the milling bodies or reactors. Moreover, the specific parameters associated with the type of mechanical actions (e.g. revolutions per minute in twin screw extrusion or planetary ball milling, or frequency in ball milling, or the number, size and mass of the balls) are certainly important in defining the reaction. Yet, many such parameters are often overlooked, remain unreported, or are difficult to identify in literature reports.
Although efforts at unraveling the mechanistic aspects and driving forces of mechanochemical research are without doubt of central importance, effective communication of protocol and processes do not require such an understanding. It might not be possible to classify unambiguously a reaction as “mechanochemical”, “tribochemical” or “mechanically facilitated thermochemical” without this mechanistic understanding, but we can still impose clarity of communication when reporting our results. Following the successful example of the Crystallographic Information File (CIF), we demonstrate how adopting a standard format for reporting experimental conditions can help ensure that important parameters are both monitored and controlled. Such agreements on the type of information that needs to be presented and how it should be presented so that it is clear to all on first glance, are crucial to unify the community and drive fundamental developments in the field of mechanochemistry.
We believe this opinion piece will spark timely and productive discussion across the ever growing and diversifying mechanochemistry community. All symbols displayed in this text are available free of charge for those who wish to use them. Additional pictograms and information will certainly become important as new features of control over mechanochemical reactions emerge, and we as a community must be ready to adapt our nomenclature and standard of practice to accommodate this.
As mechanochemistry becomes an increasingly integral part of efforts to develop environmentally benign strategies for chemical and industrial processes, it is timely to make efforts to unite the dynamic community behind common concepts and definitions in scientific language, and terminology. Only in doing so can we hope to avoid the potential downfall of the “Tower of Babel” and construct a coherent and robust “Tower of Mechanochemistry”. It is only by uniting the community that we can collectively obtain knowledge as, in the words of N. Copernicus, “to know that we know what we know, and that we do not know what we do not know, that is true knowledge.”
A library of the pictograms used in this study are available free of charge from https://opus4.kobv.de/opus4-bam/frontdoor/index/index/docId/52329
All authors listed have made a substantial, direct, and intellectual contribution to the work and approved it for publication.
The authors declare that the research was conducted in the absence of any commercial or financial relationships that could be construed as a potential conflict of interest.
As the founding president of the IMA (VB) and as members of the IMA and COST Action CA18112, the authors acknowledge support of the ongoing efforts of both organisations to develop a global community of mechanochemists. The authors are grateful to many significant and seminal contributions to the field of mechanochemistry by many remarkable scientists, upon whose shoulders the current field stands. EB acknowledges the financial support from RFBR (Grant 19-29-12026-MK).
ACN, Acetonitrile; AFM, Atomic Force Microscopy; BAM, Bundesanstalt für Materialforschung und -prüfung; BUMS, Bottom Up Mechanochemical Synthesis; CIF, Crystallographic Information File; DAC, Diamond Anvil Cell; DBU, 1,8-Diazabicyclo[5.4.0]undec-7-ene; DDQ, 2,3-Dichloro-5,6-dicyano-1,4-benzoquinone; FAIR, Findable, Accessible, Interoperable, Reusable; FM-PES, Force-Modified Potential Energy Surface; GPa, Giga Pascal; IA-LAG, Inadvertent Liquid Assisted Grinding; IUPAC, International Union of Pure and Applied Chemistry; ILAG, Ionic liquid assisted grinding; IMA, International Mechanochemical Association; LAG, Liquid Assisted Grinding; LVP, Large Volume Press; MOF, Metal-Organic Framework; NG, Neat Grinding; OAD, Oxalic acid dihydrate; PES, Potential Energy Surface; POLAG, Polymer Assisted Grinding; PVP, Polyvinylpyrrolidone; RAM, Resonant Acoustic Mixing or Resonant Acoustic Mixer; RPM, Revolutions per minute; TSE, Twin Screw Extrusion.
Aakeroy, C. B., Bryce, D. L., Desiraju, G. R., Frontera, A., Legon, A. C., Nicotra, F., et al. (2019). Definition of the Chalcogen Bond (IUPAC Recommendations 2019). Pure Appl. Chem. 91 (11), 1889–1892. doi:10.1515/pac-2018-0713
Adekenov, S. M., Zhabayeva, А. N., and Baisarov, G. М. (2020). Water-Soluble Substances of Arglabin. Eurasian Chem. Tech. J. 22 (3), 205. doi:10.18321/ectj971
Aduev, B. P., Aluker, É. D., Belokurov, G. M., Zakharov, Y. A., and Krechetov, A. G. (1999). Explosive Decomposition of Heavy-Metal Azides. J. Exp. Theor. Phys. 89 (5), 906–915. doi:10.1134/1.558931
Alex, T. C., Kailath, A. J., and Kumar, R. (2020). Al-Monohydrate (Boehmite) to Al-Trihydrate (Bayerite/Gibbsite) Transformation during High-Energy Milling. Metall. Mater. Trans. B 51, 443–451. doi:10.1007/s11663-020-01771-6
Ali El-Remaily, M. A. E. A. A., Soliman, A. M. M., and Elhady, O. M. (2020). Green Method for the Synthetic Ugi Reaction by Twin Screw Extrusion without a Solvent and Catalyst. ACS Omega 5 (11), 6194–6198. doi:10.1021/acsomega.0c00369
Am Ende, D. J., Anderson, S. R., and Salan, J. S. (2014). Development and Scale-Up of Cocrystals Using Resonant Acoustic Mixing. Org. Process. Res. Dev. 18 (2), 331–341. doi:10.1021/op4003399
Andersen, J., and Mack, J. (2018a). Insights into Mechanochemical Reactions at Targetable and Stable, Sub‐ambient Temperatures. Angew. Chem. Int. Ed. 57 (40), 13062–13065. doi:10.1002/anie.201805263
Andersen, J., and Mack, J. (2018b). Mechanochemistry and Organic Synthesis: From Mystical to Practical. Green. Chem. 20 (7), 1435–1443. doi:10.1039/c7gc03797j
Andersen, J. M., and Mack, J. (2017). Decoupling the Arrhenius Equation via Mechanochemistry. Chem. Sci. 8 (8), 5447–5453. doi:10.1039/C7SC00538E
Anderson, S. R., am Ende, D. J., Salan, J. S., and Samuels, P. (2014). Preparation of an Energetic-Energetic Cocrystal Using Resonant Acoustic Mixing. Propellants, Explosives, Pyrotechnics 39 (5), 637–640. doi:10.1002/prep.201400092
Apóstolo, R. F. G., Tsagkaropoulou, G., and Camp, P. J. (2019). Molecular Adsorption, Self-Assembly, and Friction in Lubricants. J. Mol. Liquids 277, 606–612. doi:10.1016/j.molliq.2018.12.099
Ardila‐Fierro, K. J., and Hernández, J. G. (2021). Sustainability Assessment of Mechanochemistry by Using the Twelve Principles of Green Chemistry. ChemSusChem, 14. doi:10.1002/cssc.202100478
Arunan, E., Desiraju, G. R., Klein, R. A., Sadlej, J., Scheiner, S., Alkorta, I., et al. (2011). Definition of the Hydrogen Bond (IUPAC Recommendations 2011). Pure Appl. Chem. 83 (8), 1637–1641. doi:10.1351/PAC-REC-10-01-02
Avvakumov, E. G. (1972). Mechanochemical Methods of Activation of Chemical Processes. Novosibirsk: Nauka.
Avvakumov, E. G., Senna, M., and Kosova, N. V. (2001). Soft Mechanochemical Synthesis: A Basis for New Chemical Technologies. 1st ed. New York: Kluwer Academic Publishers.
Baba, K., Takeichi, Y., and Nakai, Y. (1990). Molecular Behavior and Dissolution Characteristics of Uracil in Ground Mixtures. Chem. Pharm. Bull. 38 (9), 2542–2546. doi:10.1248/cpb.38.2542
Bakhshai, A., Pragani, R., and Takacs, L. (2002). Self-propagating Reaction Induced by Ball Milling in a Mixture of Cu2O and Al Powders. Metall. Mat Trans. A. 33 (11), 3521–3526. doi:10.1007/s11661-002-0339-3
Baláž, M., Achimovičová, M., Baláž, P., Dutková, E., Fabián, M., Kováčová, M., et al. (2020). Mechanochemistry as a Versatile and Scalable Tool for Nanomaterials Synthesis: Recent Achievements in Košice, Slovakia. Cur. Opin. Green Sus. Chem. 24, 7–13. doi:10.1016/j.cogsc.2019.12.007
Baláž, P., Achimovičová, M., Baláž, M., Billik, P., Cherkezova-Zheleva, Z., Criado, J. M., et al. (2013). Hallmarks of Mechanochemistry: From Nanoparticles to Technology. Chem. Soc. Rev. 42 (18), 7571. doi:10.1039/c3cs35468g
Balaz, P., Briancin, J., Bastl, Z., Medvecky, L., and Sepelak, V. (1994). Properties of Mechanochemically Pretreated Precursors of Doped BaTiO3 Ceramics. J. Mater. Sci. 29, 4847–4851. doi:10.1007/BF00356532
Balcerzak, M., Kawamura, K., Bobrowski, R., Rutkowski, P., and Brylewski, T. (2019). Mechanochemical Synthesis of (Co,Cu,Mg,Ni,Zn)O High-Entropy Oxide and its Physicochemical Properties. J. Elec Materi 48 (11), 7105–7113. doi:10.1007/s11664-019-07512-z
Ban, V., Sadikin, Y., Lange, M., Tumanov, N., Filinchuk, Y., Černý, R., et al. (2017). Innovative In Situ Ball Mill for X-Ray Diffraction. Anal. Chem. 89 (24), 13176–13181. doi:10.1021/acs.analchem.7b02871
Batzdorf, L., Fischer, F., Wilke, M., Wenzel, K.-J., and Emmerling, F. (2015). Direct In Situ Investigation of Milling Reactions Using Combined X-Ray Diffraction and Raman Spectroscopy. Angew. Chem. Int. Ed. 54 (6), 1799–1802. doi:10.1002/anie.201409834
Begin-Colin, S., Le Caër, G., Zandona, M., Bouzy, E., and Malaman, B. (1995). Influence of the Nature of Milling Media on Phase Transformations Induced by Grinding in Some Oxides. J. Alloys Comp. 227 (2), 157–166. doi:10.1016/0925-8388(95)01596-5
Belenguer, A. M., Cruz-Cabeza, A. J., Lampronti, G. I., and Sanders, J. K. M. (2019a). On the Prevalence of Smooth Polymorphs at the Nanoscale: Implications for Pharmaceuticals. CrystEngComm 21 (13), 2203–2211. doi:10.1039/C8CE02098A
Belenguer, A. M., Lampronti, G. I., Cruz-Cabeza, A. J., Hunter, C. A., and Sanders, J. K. M. (2016). Solvation and Surface Effects on Polymorph Stabilities at the Nanoscale. Chem. Sci. 7 (11), 6617–6627. doi:10.1039/C6SC03457H
Belenguer, A. M., Lampronti, G. I., De Mitri, N., Driver, M., Hunter, C. A., and Sanders, J. K. M. (2018). Understanding the Influence of Surface Solvation and Structure on Polymorph Stability: A Combined Mechanochemical and Theoretical Approach. J. Am. Chem. Soc. 140 (49), 17051–17059. doi:10.1021/jacs.8b08549
Belenguer, A. M., Michalchuk, A. A. L., Lampronti, G. I., and Sanders, J. K. M. (2019b). Understanding the Unexpected Effect of Frequency on the Kinetics of a Covalent Reaction under Ball-Milling Conditions. Beilstein J. Org. Chem. 15, 1226–1235. doi:10.3762/bjoc.15.120
Benjamin, J. S., and Volin, T. E. (1974). The Mechanism of Mechanical Alloying. MT 5 (8), 1929–1934. doi:10.1007/BF02644161
Beyer, M. K., and Clausen-Schaumann, H. (2005). Mechanochemistry: The Mechanical Activation of Covalent Bonds. Chem. Rev. 105 (8), 2921–2948. doi:10.1021/cr030697h
Boldyrev, V. (1983). Experimental Methods in the Mechanochemistry of Inorganic Solids. Treatise Mater. Sci. Tech. 19 (B), 185–223. doi:10.1016/b978-0-12-341842-5.50008-1
Boldyrev, V. V., Avvakumov, E. G., Harenz, H., Heinicke, G., and Strugova, L. I. (1972). Zur Tribochemischen Zersetzung von Alkali-Bromaten und -Nitraten. Z. Anorg. Allg. Chem. 393 (2), 152–158. doi:10.1002/zaac.19723930209
Boldyrev, V. V., and Avvakumov, E. G. (1967). Mechanochemistry of Inorganic Solids. Russ. Chem. Rev. 40 (10), 847.
Boldyrev, V. V., Bulens, M., and Delmon, B. (1979). The Control of the Reactivity of Solids. Amsterdam, New York: Elsevier Scientific Publishing.
Boldyrev, V. V. (1972). Facteurs Cinetiques qui Determinent la Specificite des Processus Mecanochimiques dans les Systemes Inorganiques. Kinet. Kataliz. 13 (6), 1411–1421.
Boldyrev, V. V., and Heinicke, G. (1979). Reaktionsursachen in der Tribochemie. Z. Chem. 19 (10), 353–362. doi:10.1002/zfch.19790191002
Boldyrev, V. V. (2002). Hydrothermal Reactions under Mechanochemical Action. Powder Tech. 122, 247–254. doi:10.1016/S0032-5910(01)00421-1
Boldyrev, V. V. (1998). Mechanical Activation and its Application in Technology. Msf 269-272, 227–234. doi:10.4028/www.scientific.net/msf.269-272.227
Boldyrev, V. V. (2004). Mechanochemical Modification and Synthesis of Drugs. J. Mater. Sci. 39, 5117–5120. doi:10.1023/B:JMSC.0000039193.69784.1d
Boldyrev, V. V. (2018). Mechanochemical Processes with the Reaction-Induced Mechanical Activation. Chemo-Mechanochemical Effect. Russ. Chem. Bull. 67 (6), 933–948. doi:10.1007/s11172-018-2162-z
Boldyrev, V. V. (1996). Mechanochemistry and Mechanical Activation. Msf 225-227, 511–520. doi:10.4028/www.scientific.net/MSF.225-227.511
Boldyrev, V. V. (2006). Mechanochemistry and Mechanical Activation of Solids. Russ. Chem. Rev. 75 (3), 177–189. doi:10.1070/rc2006v075n03abeh001205
Boldyrev, V. V. (2018). Mechanochemistry in Siberia. Her. Russ. Acad. Sci. 88 (2), 142–150. doi:10.1134/s1019331618020016
Boldyrev, V. V., Pavlov, S. V., and Goldberg, E. L. (1996). Interrelation between Fine Grinding and Mechanical Activation. Int. J. Mineral. Process. 44, 181–185. doi:10.1016/0301-7516(95)00028-310.1016/b978-0-444-82440-0.50018-3
Boldyrev, V. V., and Tkáčová, K. (2000). Mechanochemistry of Solids: Past, Present, and Prospects. J. Mater. Synth. Process. 8 (3/4), 121–132. doi:10.1023/A:1011347706721
Boldyrev, V. V. (1973). Topochemistry of the Thermal Decomposition of Solid Substances. Russ. Chem. Rev. 42 (7), 515–528. doi:10.1070/RC1973v042n07ABEH002655
Boldyreva, E. (2013). Mechanochemistry of Inorganic and Organic Systems: What Is Similar, what Is Different? Chem. Soc. Rev. 42 (18), 7719. doi:10.1039/c3cs60052a
Boldyreva, E. V. (2019). “High Pressure Crystallography: Elucidating the Role of Intermolecular Interactions in Crystals of Organic and Coordination Compounds,” in Understanding Intermolecular Interactions in the Solid State: Approaches and Techniques. Editor D. Chopra (Royal Society of Chemistry), 32–97.
Boldyreva, E. V., and Sidelnikov, A. A. (1987). The Effect of Mechanical Stress on the Rate of the Bending of the [Co(NH3)5NO2]Cl(NO3) Crystals in the Course of Linkage Nitro-Nitrito Photoisomerization. Proc. Sib. Acad. Sci. Ussr, Chem. 5, 139.
Bolm, C., and Hernández, J. G. (2019). Mechanochemistry of Gaseous Reactants. Angew. Chem. Int. Ed. 58 (11), 3285–3299. doi:10.1002/anie.201810902
Boocock, D., Hino, N., Ruzickova, N., Hirashima, T., and Hannezo, E. (2021). Theory of Mechanochemical Patterning and Optimal Migration in Cell Monolayers. Nat. Phys. 17 (2), 267–274. doi:10.1038/s41567-020-01037-7
Bouvart, N., Palix, R.-M., Arkhipov, S. G., Tumanov, I. A., Michalchuk, A. A. L., and Boldyreva, E. V. (2018). Polymorphism of Chlorpropamide on Liquid-Assisted Mechanical Treatment: Choice of Liquid and Type of Mechanical Treatment Matter. CrystEngComm 20 (13), 1797–1803. doi:10.1039/C7CE02221B
Bowden, F. P., and Gurton, O. A. (1949). Initiation of Solid Explosives by Impact and Friction: The Influence of Grit. Proc. R. Soc. Lond. A. 198 (1054), 337–349. doi:10.1098/rspa.1949.0105
Bowden, F. P., Stone, M. A., and Tudor, G. K. (1947). Hot Spots on Rubbing Surfaces and the Detonation of Explosives by Friction. Proc. R. Soc. Lond. A. 188 (1014), 329–349. doi:10.1098/rspa.1947.0012
Bowmaker, G. A., Hanna, J. V., Skelton, B. W., and White, A. H. (2009). Solvent-Assisted Solid-State Synthesis: Separating the Chemical from the Mechanical in Mechanochemical Synthesis. Chem. Commun. 16, 2168. doi:10.1039/b822370j
Bowmaker, G. A. (2013). Solvent-Assisted Mechanochemistry. Chem. Commun. 49 (4), 334–348. doi:10.1039/C2CC35694E
Braga, D., Maini, L., and Grepioni, F. (2013). Mechanochemical Preparation of Co-crystals. Chem. Soc. Rev. 42 (18), 7638. doi:10.1039/c3cs60014a
Brown, I. D., and McMahon, B. (2002). CIF: The Computer Language of Crystallography. Acta Crystallogr. Sect B 58 (3), 317–324. doi:10.1107/S0108768102003464
Brown, I. D., and McMahon, B. (2006). The Crystallographic Information File (CIF). Data Sci. J. 5 (19), 174–177. doi:10.2481/dsj.5.174
Butyagin, P. Y. (1971). Kinetics and Nature of Mechanochemical Reactions. Russ. Chem. Rev. 40 (11), 901–915. doi:10.1070/RC1971v040n11ABEH001982
Butyagin, P. Y. (1994). Problems in Mechanochemistry and Prospects for its Development. Russ. Chem. Rev. 63 (12), 965–976. doi:10.1070/rc1994v063n12abeh000129
Butyagin, P. Y. (1984). Structural Disorder and Mechanochemical Reactions in Solids. Russ. Chem. Rev. 53 (11), 1025–1038. doi:10.1070/RC1984v053n11ABEH003138
Butyagin, P. Y. (2005). The Kinetics and Energy Balance of Mechanochemical Transformations. Phys. Solid State. 47 (5), 856–862. doi:10.1134/1.1924845
Butyagin, P. Y. (1967). The Nature of the Mechanical Degradation of Polymethylmethacrylate. Polym. Sci. U.S.S.R. 9 (1), 149–158. doi:10.1016/0032-3950(67)90336-x
Buyanov, R. A., Molchanov, V. V., and Boldyrev, V. V. (2009). Mechanochemical Activation for Resolving the Problems of Catalysis. KONA 27 (0), 38–54. doi:10.14356/kona.2009007
Bychkov, A., Podgorbunskikh, E., Bychkova, E., and Lomovsky, O. (2019). Current Achievements in the Mechanically Pretreated Conversion of Plant Biomass. Biotechnol. Bioeng. 116 (5), 1231–1244. doi:10.1002/bit.26925
Carey-Lea, M. (1892). IV. Disruption of the silver haloid molecule by mechanical force. The London, Edinburgh, and Dublin Phil. Mag. J. Sci. 34, 46–50. doi:10.1080/14786449208620163
Cezan, S. D., Nalbant, A. A., Buyuktemiz, M., Dede, Y., Baytekin, H. T., and Baytekin, B. (2019). Control of Triboelectric Charges on Common Polymers by Photoexcitation of Organic Dyes. Nat. Commun. 10 (1), 276. doi:10.1038/s41467-018-08037-5
Chadwick, K., Davey, R., and Cross, W. (2007). How Does Grinding Produce Co-crystals? Insights from the Case of Benzophenone and Diphenylamine. CrystEngComm 9 (9), 732. doi:10.1039/b709411f
Chen, L., Bovee, M. O., Lemma, B. E., Keithley, K. S. M., Pilson, S. L., Coleman, M. G., et al. (2015). An Inexpensive and Recyclable Silver-Foil Catalyst for the Cyclopropanation of Alkenes with Diazoacetates under Mechanochemical Conditions. Angew. Chem. Int. Ed. 54 (38), 11084–11087. doi:10.1002/anie.201504236
Chen, X. H., Yang, H. S., Wu, G. T., Wang, M., Deng, F. M., Zhang, X. B., et al. (2000). Generation of Curved or Closed-Shell Carbon Nanostructures by Ball-Milling of Graphite. J. Cryst. Growth 218 (1), 57–61. doi:10.1016/S0022-0248(00)00486-3
Chizhik, S., Sidelnikov, A., Zakharov, B., Naumov, P., and Boldyreva, E. (2018). Quantification of Photoinduced Bending of Dynamic Molecular Crystals: From Macroscopic Strain to Kinetic Constants and Activation Energies. Chem. Sci. 9 (8), 2319–2335. doi:10.1039/C7SC04863G
Coffey, C. S., and Toton, E. T. (1982). A Microscopic Theory of Compressive Wave‐induced Reactions in Solid Explosives. J. Chem. Phys. 76 (2), 949–954. doi:10.1063/1.443065
Cook, T. L., Walker, J. A., and Mack, J. (2013). Scratching the Catalytic Surface of Mechanochemistry: A Multi-Component CuAAC Reaction Using a Copper Reaction Vial. Green. Chem. 15 (3), 617. doi:10.1039/c3gc36720g
Crawford, D. E., and Casaban, J. (2016). Recent Developments in Mechanochemical Materials Synthesis by Extrusion. Adv. Mater. 28 (27), 5747–5754. doi:10.1002/adma.201505352
Crawford, D. E., Miskimmin, C. K. G., Albadarin, A. B., Walker, G., and James, S. L. (2017). Organic Synthesis by Twin Screw Extrusion (TSE): Continuous, Scalable and Solvent-free. Green. Chem. 19 (6), 1507–1518. doi:10.1039/C6GC03413F
Crawford, D. E., Porcheddu, A., McCalmont, A. S., Delogu, F., James, S. L., and Colacino, E. (2020). Solvent-Free, Continuous Synthesis of Hydrazone-Based Active Pharmaceutical Ingredients by Twin-Screw Extrusion. ACS Sust. Chem. Eng. 8 (32), 12230–12238. doi:10.1021/acssuschemeng.0c03816
Dang, J., Zhang, H., An, Q., Ming, W., and Chen, M. (2021). Surface Modification of Ultrahigh Strength 300M Steel under Supercritical Carbon Dioxide (scCO2)-Assisted Grinding Process. J. Manufacturing Process. 61, 1–14. doi:10.1016/j.jmapro.2020.11.001
De Bo, G. (2018). Mechanochemistry of the Mechanical Bond. Chem. Sci. 9 (1), 15–21. doi:10.1039/C7SC04200K
de Oliveira, P. F. M., Michalchuk, A. A. L., Buzanich, A. G., Bienert, R., Torresi, R. M., Camargo, P. H. C., et al. (2020b). Tandem X-Ray Absorption Spectroscopy and Scattering for In Situ Time-Resolved Monitoring of Gold Nanoparticle Mechanosynthesis. Chem. Commun. 56, 10329–10332. doi:10.1039/D0CC03862H
de Oliveira, P. F. M., Michalchuk, A. A. L., Marquardt, J., Feiler, T., Prinz, C., Torresi, R. M., et al. (2020a). Investigating the Role of Reducing Agents on Mechanosynthesis of Au Nanoparticles. CrystEngComm 22 (38), 6261–6267. doi:10.1039/d0ce00826e
de Oliveira, P. F. M., Torresi, R. M., Emmerling, F., and Camargo, P. H. C. (2020c). Challenges and Opportunities in the Bottom-Up Mechanochemical Synthesis of Noble Metal Nanoparticles. J. Mater. Chem. A. 8 (32), 16114–16141. doi:10.1039/D0TA05183G
Delogu, F., Deidda, C., Mulas, G., Schiffini, L., and Cocco, G. (2004a). A Quantitative Approach to Mechanochemical Processes. J. Mater. Sci. 39 (16/17), 5121–5124. doi:10.1023/B:JMSC.0000039194.07422.be
Delogu, F., Gorrasi, G., and Sorrentino, A. (2017). Fabrication of Polymer Nanocomposites via Ball Milling: Present Status and Future Perspectives. Prog. Mater. Sci. 86, 75–126. doi:10.1016/j.pmatsci.2017.01.003
Delogu, F., Mulas, G., Schiffini, L., and Cocco, G. (2004b). Mechanical Work and Conversion Degree in Mechanically Induced Processes. Mater. Sci. Eng. A 382 (1–2), 280–287. doi:10.1016/j.msea.2004.05.047
Delogu, F., Orrù, R., and Cao, G. (2003). A Novel Macrokinetic Approach for Mechanochemical Reactions. Chem. Eng. Sci. 58 (3–6), 815–821. doi:10.1016/S0009-2509(02)00612-7
Delogu, F., and Takacs, L. (2014). Mechanochemistry of Ti-C Powder Mixtures. Acta Materialia 80, 435–444. doi:10.1016/j.actamat.2014.08.036
Descamps, M., and Willart, J.-F. (2016b). “Some Facets of Molecular Disorder in Crystalline and Amorphous Pharmaceuticals,” in Disordered Pharmaceutical Materials. Editor M. Descamps (Weinheim, Germany: Wiley-VCH Verlag GmbH & Co. KGaA), 1–56. doi:10.1002/9783527652693.ch1
Descamps, M., and Willart, J. F. (2016a). Perspectives on the Amorphisation/Milling Relationship in Pharmaceutical Materials. Adv. Drug Deliv. Rev. 100, 51–66. doi:10.1016/j.addr.2016.01.011
Desiraju, G. R., Ho, P. S., Kloo, L., Legon, A. C., Marquardt, R., Metrangolo, P., et al. (2013). Definition of the Halogen Bond (IUPAC Recommendations 2013). Pure Appl. Chem. 85 (8), 1711–1713. doi:10.1351/PAC-REC-12-05-10
Dlott, D. D., and Fayer, M. D. (1990). Shocked Molecular Solids: Vibrational up Pumping, Defect Hot Spot Formation, and the Onset of Chemistry. J. Chem. Phys. 92 (6), 3798–3812. doi:10.1063/1.457838
Dlott, D. D. (1999). Ultrafast Spectroscopy of Shock Waves in Molecular Materials. Annu. Rev. Phys. Chem. 50 (1), 251–278. doi:10.1146/annurev.physchem.50.1.251
Drebushchak, T. N., Ogienko, A. A., and Boldyreva, E. V. (2011). 'Hedvall Effect' in Cryogrinding of Molecular Crystals. A Case Study of a Polymorphic Transition in Chlorpropamide. CrystEngComm 13 (13), 4405. doi:10.1039/c1ce05189j
Dubinskaya, A. M. (1999). Transformations of Organic Compounds under the Action of Mechanical Stress. Russ. Chem. Rev. 68 (8), 637–652. doi:10.1070/RC1999v068n08ABEH000435
Dziubek, K. F. (2020). Data Preservation in Pressure Measurement. J. Phys. Conf. Ser. 1609, 012002. doi:10.1088/1742-6596/1609/1/012002
Eckhardt, C. J. (2006). Mechanochemistry: The Last Energetic Frontier. Mol. Crystals Liquid Crystals 456 (1), 1–14. doi:10.1080/15421400600786249
Egleston, B. D., Brand, M. C., Greenwell, F., Briggs, M. E., James, S. L., Cooper, A. I., et al. (2020). Continuous and Scalable Synthesis of a Porous Organic Cage by Twin Screw Extrusion (TSE). Chem. Sci. 11 (25), 6582–6589. doi:10.1039/D0SC01858A
El-Eskandarany, M. S. (2020). Mechanical Alloying: Energy Storage, Protective Coatings, and Medical Applications. Elsevier Science.
Enayati, M. H., Sadeghian, Z., Salehi, M., and Saidi, A. (2004). The Effect of Milling Parameters on the Synthesis of Ni3Al Intermetallic Compound by Mechanical Alloying. Mater. Sci. Eng. A 375-377, 809–811. doi:10.1016/j.msea.2003.10.060
Engelke, R., and Blais, N. C. (1994). Chemical Dimerization of Crystalline Anthracene Produced by Transient High Pressure. J. Chem. Phys. 101 (12), 10961–10972. doi:10.1063/1.467846
Epelak, V. (2002). Nanocrystalline Materials Prepared by Homogeneous and Heterogeneous Mechanochemical Reactions. Ann. de Chim. Sci. des Materiaux 27 (6), 61–76. doi:10.1016/S0151-9107(02)90015-2
Fabbiani, F. P. A., Allan, D. R., Parsons, S., and Pulham, C. R. (2005). An Exploration of the Polymorphism of Piracetam Using High Pressure. CrystEngComm 7 (29), 179. doi:10.1039/b418976k
Fandiño, O. E., Reviglio, L., Linck, Y. G., Monti, G. A., Marcos Valdez, M. M., Faudone, S. N., et al. (2020). Novel Cocrystals and Eutectics of the Antiprotozoal Tinidazole: Mechanochemical Synthesis, Cocrystallization, and Characterization. Cryst. Growth Des. 20 (5), 2930–2942. doi:10.1021/acs.cgd.9b01435
Ferguson, M., Moyano, M. S., Tribello, G. A., Crawford, D. E., Bringa, E. M., James, S. L., et al. (2019). Insights into Mechanochemical Reactions at the Molecular Level: Simulated Indentations of Aspirin and Meloxicam Crystals. Chem. Sci. 10 (10), 2924–2929. doi:10.1039/C8SC04971H
Fernández-Bertran, J. F. (1999). Mechanochemistry: an Overview. Pure Appl. Chem. 71 (4), 581–586. doi:10.1351/pac199971040581
Fisch, M., Lanza, A., Boldyreva, E., Macchi, P., and Casati, N. (2015). Kinetic Control of High-Pressure Solid-State Phase Transitions: A Case Study on L-Serine. J. Phys. Chem. C 119 (32), 18611–18617. doi:10.1021/acs.jpcc.5b05838
Fischer, F., Greiser, S., Pfeifer, D., Jäger, C., Rademann, K., and Emmerling, F. (2016). Mechanochemically Induced Conversion of Crystalline Benzamide Polymorphs by Seeding. Angew. Chem. Int. Ed. 55 (46), 14281–14285. doi:10.1002/anie.201607358
Flavitsky, F. M. (1909). Organic Mechanochemistry, In Proceedings of the First Mendeleev Congress on General and Applied Chemistry (St. Petersburg, 205.
Fox, P. G. (1975). Mechanically Initiated Chemical Reactions in Solids. J. Mater. Sci. 10 (2), 340–360. doi:10.1007/bf00540358
Friedrich, A., Collings, I. E., Dziubek, K. F., Fanetti, S., Radacki, K., Ruiz-Fuertes, J., et al. (2020). Pressure-Induced Polymerization of Polycyclic Arene-Perfluoroarene Cocrystals: Single Crystal X-ray Diffraction Studies, Reaction Kinetics, and Design of Columnar Hydrofluorocarbons. J. Am. Chem. Soc. 142 (44), 18907–18923. doi:10.1021/jacs.0c09021
Friščić, T. (2012). Supramolecular Concepts and New Techniques in Mechanochemistry: Cocrystals, Cages, Rotaxanes, Open Metal–Organic Frameworks. Chem. Soc. Rev. 41 (9), 3493. doi:10.1039/c2cs15332g
Galica, T., Konieczny, K. A., and Turowska-Tyrk, I. (2020). Structural Transformations in Crystals Induced by Radiation and Pressure. Part 9. The Photochemical Behaviour of Cinnamic Acids of Stack Architecture - Comparative Analysis. J. Photochem. Photobiol. A: Chem. 386, 112119. doi:10.1016/j.jphotochem.2019.112119
Galwey, A. K. (2020). Thermal Reactions Involving Solids: A Personal View of Selected Features of Decompositions, Thermal Analysis and Heterogeneous Catalysis. J. Therm. Anal. Calorim. 142 (3), 1123–1144. doi:10.1007/s10973-020-09461-w
Gerasimov, K. B., and Boldyrev, V. V. (1996). On Mechanism of New Phases Formation during Mechanical Alloying of Ag-Cu, Al-Ge and Fe-Sn Systems. Mater. Res. Bull. 31 (10), 1297–1305. doi:10.1016/0025-5408(96)00114-6
Germann, L. S., Arhangelskis, M., Etter, M., Dinnebier, R. E., and Friščić, T. (2020). Challenging the Ostwald Rule of Stages in Mechanochemical Cocrystallisation. Chem. Sci. 11, 10092–10100. doi:10.1039/D0SC03629C
Gilman, J., and During, J. (2006). During Detonation Chemistry May Precede Heat. Mater. Sci. Tech. 22 (4), 430–437. doi:10.1179/174328406X86056
Gilman, J. J. (1998). Fast, Faster, and Fastest Cracks. Phil. Mag. Lett. 77 (2), 79–82. doi:10.1080/095008398178633
Gilman, J. J., and Tong, H. C. (1971). Quantum Tunneling as an Elementary Fracture Process. J. Appl. Phys. 42 (9), 3479–3486. doi:10.1063/1.1660757
Gomollón-Bel, F. (2019). Ten Chemical Innovations that Will Change Our World: IUPAC Identifies Emerging Technologies in Chemistry with Potential to Make Our Planet More Sustainable. Chem. Int. 41 (2), 12–17. doi:10.1515/ci-2019-0203
Grätz, S., Oltermann, M., Vogt, C. G., and Borchardt, L. (2020). Mechanochemical Cyclodehydrogenation with Elemental Copper: An Alternative Pathway toward Nanographenes. ACS Sust. Chem. Eng. 8 (20), 7569–7573. doi:10.1021/acssuschemeng.0c02223
Güler, Ö., and Evin, E. (2015). Effect of Milling Type on Formation of Carbon Nanostructures. Fullerenes, Nanotubes and Carbon Nanostructures 23 (5), 463–470. doi:10.1080/1536383X.2013.874343
Głowniak, S., Szczęśniak, B., Choma, J., and Jaroniec, M. M. (2021). Toward Green Synthesis of Metal–Organic Frameworks. Mater. Today 27. doi:10.1016/j.mattod.2021.01.008
Haferkamp, S., Paul, A., Michalchuk, A. A. L., and Emmerling, F. (2019). Unexpected Polymorphism during a Catalyzed Mechanochemical Knoevenagel Condensation. Beilstein J. Org. Chem. 15, 1141–1148. doi:10.3762/bjoc.15.110
Haley, R. A., Zellner, A. R., Krause, J. A., Guan, H., and Mack, J. (2016). Nickel Catalysis in a High Speed Ball Mill: A Recyclable Mechanochemical Method for Producing Substituted Cyclooctatetraene Compounds. ACS Sust. Chem. Eng. 4 (5), 2464–2469. doi:10.1021/acssuschemeng.6b00363
Hall, S. R., Allen, F. H., and Brown, I. D. (1991). The Crystallographic Information File (CIF): A New Standard Archive File for Crystallography. Acta Cryst. Sect A. 47 (6), 655–685. doi:10.1107/S010876739101067X
Hall, S. R., and McMahon, B. (2016). The Implementation and Evolution of STAR/CIF Ontologies: Interoperability and Preservation of Structured Data. Data Sci. J. 15 (3), 1–15. doi:10.5334/dsj-2016-003
Haneef, J., and Chadha, R. (2020). Sustainable Synthesis of Ambrisentan - Syringic Acid Cocrystal: Employing Mechanochemistry in the Development of Novel Pharmaceutical Solid Form. CrystEngComm 22 (14), 2507–2516. doi:10.1039/C9CE01818B
Harris, V. G., and Šepelák, V. (2018). Mechanochemically Processed Zinc Ferrite Nanoparticles: Evolution of Structure and Impact of Induced Cation Inversion. J. Magnetism Magn. Mater. 465, 603–610. doi:10.1016/j.jmmm.2018.05.100
Haruta, N., de Oliveira, P. F. M., Sato, T., Tanaka, K., and Baron, M. (2019). Force-Induced Dissolution of Imaginary Mode in Mechanochemical Reaction: Dibenzophenazine Synthesis. J. Phys. Chem. C 123 (35), 21581–21587. doi:10.1021/acs.jpcc.9b05582
Hasa, D., Carlino, E., and Jones, W. (2016). Polymer-Assisted Grinding, a Versatile Method for Polymorph Control of Cocrystallization. Cryst. Growth Des. 16 (3), 1772–1779. doi:10.1021/acs.cgd.6b00084
Hasa, D., Schneider Rauber, G., Voinovich, D., and Jones, W. (2015). Cocrystal Formation through Mechanochemistry: From Neat and Liquid-Assisted Grinding to Polymer-Assisted Grinding. Angew. Chem. Int. Ed. 54 (25), 7371–7375. doi:10.1002/anie.201501638
Hassani-Gangaraj, M., Veysset, D., Nelson, K. A., and Schuh, C. A. (2018). Melt-Driven Erosion in Microparticle Impact. Nat. Commun. 9 (1), 5077. doi:10.1038/s41467-018-07509-y
Hassani-Gangaraj, M., Veysset, D., Nelson, K. A., and Schuh, C. A. (2017). Melting Can Hinder Impact-Induced Adhesion. Phys. Rev. Lett. 119 (17), 175701. doi:10.1103/PhysRevLett.119.175701
He, X., Deng, Y., Zhang, Y., He, Q., Xiao, D., Peng, M., et al. (2020). Mechanochemical Kilogram-Scale Synthesis of Noble Metal Single-Atom Catalysts. Cel Rep. Phys. Sci. 1 (1), 100004. doi:10.1016/j.xcrp.2019.100004
Hernández, J. G., Ardila-Fierro, K. J., Crawford, D., James, S. L., and Bolm, C. (2017). Mechanoenzymatic Peptide and Amide Bond Formation. Green. Chem. 19 (11), 2620–2625. doi:10.1039/C7GC00615B
Holmberg, K., and Erdemir, A. (2017). Influence of Tribology on Global Energy Consumption, Costs and Emissions. Friction 5 (3), 263–284. doi:10.1007/s40544-017-0183-5
Humphry-Baker, S. A., Garroni, S., Delogu, F., and Schuh, C. A. (2016). Melt-Driven Mechanochemical Phase Transformations in Moderately Exothermic Powder Mixtures. Nat. Mater 15 (12), 1280–1286. doi:10.1038/nmat4732
Huq, N., Rosenkranz, A., Shah, R., and Woydt, M. (2020). Tribology Meets Sustainability. Ind. Lubrication Tribol. doi:10.1108/ILT-09-2020-0356
Hutchings, B. P., Crawford, D. E., Gao, L., Hu, P., and James, S. L. (2017). Feedback Kinetics in Mechanochemistry: The Importance of Cohesive States. Angew. Chem. Int. Ed. 56 (48), 15252–15256. doi:10.1002/anie.201706723
International Mechanochemical Association (2020). International Mechanochemical Association. Imamechanochemical.com.
Ioffe, A. F. (1936). Report on the Activity of the Institute of Technical Physics. Usp. Fiz. Nauk 16, 847–871. doi:10.3367/ufnr.0016.193607c.0847
Iwasaki, T., Yabuuchi, T., Nakagawa, H., and Watano, S. (2010). Scale-up Methodology for Tumbling Ball Mill Based on Impact Energy of Grinding Balls Using Discrete Element Analysis. Adv. Powder Tech. 21 (6), 623–629. doi:10.1016/j.apt.2010.04.008
James, S. L., Adams, C. J., Bolm, C., Braga, D., Collier, P., Friščić, T., et al. (2012). Mechanochemistry: Opportunities for New and Cleaner Synthesis. Chem. Soc. Rev. 41 (1), 413–447. doi:10.1039/c1cs15171a
Kajdas, C. (2013). “General Approach to Mechanochemistry and its Relation to Tribochemistry,” in Tribology in Engineering. Editor H. Pihtili (InTech). doi:10.5772/50507
Kamalakannan, R., Ganesan, G. N., Selvaganesan, J., Gowtham, K., and Dheenathayalan, B. (2019). Mechanochemical Synthesis and Sintering of AlCrFeNiZn High Entrophy Alloy. India: American Institute of Physics: Tamilnadu, 030019. doi:10.1063/1.5117962
Katrusiak, A. (2019). Lab in a DAC - High-Pressure Crystal Chemistry in a Diamond-Anvil Cell. Acta Crystallogr. Sect B 75 (6), 918–926. doi:10.1107/S2052520619013246
Kaupp, G. (2009). Mechanochemistry: The Varied Applications of Mechanical Bond-Breaking. CrystEngComm 11 (3), 388–403. doi:10.1039/B810822F
Keller, D., and Bustamante, C. (2000). The Mechanochemistry of Molecular Motors. Biophysical J. 78 (2), 541–556. doi:10.1016/S0006-3495(00)76615-X
Koch, C. C. (1989). Materials Synthesis by Mechanical Alloying. Annu. Rev. Mater. Sci. 19, 121–143. doi:10.1146/annurev.ms.19.080189.001005
Kondo, S.-I. (2000). A Design and Development of Novel Polymeric Prodrugs Prepared by Mechanochemical Solid-State Polymerization. YAKUGAKU ZASSHI 120 (12), 1337–1346. doi:10.1248/yakushi1947.120.12_1337
Kubota, K., Pang, Y., Miura, A., and Ito, H. (2019). Redox Reactions of Small Organic Molecules Using Ball Milling and Piezoelectric Materials. Science 366 (6472), 1500–1504. doi:10.1126/science.aay8224
Kulla, H., Becker, C., Michalchuk, A. A. L., Linberg, K., Paulus, B., and Emmerling, F. (2019). Tuning the Apparent Stability of Polymorphic Cocrystals through Mechanochemistry. Cryst. Growth Des. 19 (12), 7271–7279. doi:10.1021/acs.cgd.9b01158
Kumar, A., Dhekne, P., Swarnakar, A. K., and Chopkar, M. K. (2017). Analysis of Si Addition on Phase Formation in AlCoCrCuFeNiSix High Entropy Alloys. Mater. Lett. 188, 73–76. doi:10.1016/j.matlet.2016.10.099
Kumar, R., Kumar, S., Alex, T. C., and Singla, R. (2019). Mapping of Calorimetric Response for the Geopolymerisation of Mechanically Activated Fly Ash. J. Therm. Anal. Calorim. 136, 1117–1133. doi:10.1007/s10973-018-7736-3
Kuroda, R., Higashiguchi, K., Hasebe, S., and Imai, Y. (2004). Crystal to Crystal Transformation in the Solid State. CrystEngComm 6 (76), 463. doi:10.1039/b408971e
Kushwaha, V. S., and Peterman, E. J. G. (2020). The Temperature Dependence of Kinesin Motor-Protein Mechanochemistry. Biochem. Biophysical Res. Commun. 529 (3), 812–818. doi:10.1016/j.bbrc.2020.06.004
Kuzuya, M., Sakata, H., Kondo, S., and Noguchi, A. (1991). Mechanochemical Solid State Reactions of Natural Products for Medicinal Use Containing Hydroxyanthraquinone Derivatives. Yakugaku Zasshi 111 (11), 665–671. doi:10.1248/yakushi1947.111.11_665
Lampronti, G. I., Michalchuk, A., Mazzeo, P. P., Belenguer, A., K. M. Sanders, J., Emmerling, F., et al. (2021). Changing the Game of Time Resolved X-Ray Diffraction on the Mechanochemistry Playground by Downsizing. ChemRxiv. doi:10.26434/chemrxiv.14034623.v1
Landerville, A. C., Oleynik, I. I., and White, C. T. (2009). Reactive Molecular Dynamics of Hypervelocity Collisions of PETN Molecules. J. Phys. Chem. A. 113 (44), 12094–12104. doi:10.1021/jp905969y
Lapshin, O. V., Boldyreva, E. V., and Boldyrev, V. V. (2021). Role of Mixing and Milling in Mechanochemical Synthesis (Review). Russ. J. Inorg. Chem. 66 (3), 433–453. doi:10.1134/S0036023621030116
Li, Y. B., Wei, B. Q., Liang, J., Yu, Q., and Wu, D. H. (1999). Transformation of Carbon Nanotubes to Nanoparticles by Ball Milling Process. Carbon 37 (3), 493–497. doi:10.1016/S0008-6223(98)00218-8
Li, Y., Wen, J., Qin, M., Cao, Y., Ma, H., and Wang, W. (2017). Single-Molecule Mechanics of Catechol-Iron Coordination Bonds. ACS Biomater. Sci. Eng. 3, 979–989. doi:10.1021/acsbiomaterials.7b00186
Lin, I. J., and Nadiv, S. (1979). Review of the Phase Transformation and Synthesis of Inorganic Solids Obtained by Mechanical Treatment (Mechanochemical Reactions). Mater. Sci. Eng. 39 (2), 193–209. doi:10.1016/0025-5416(79)90059-4
Liu, X., and Pulham, C. R. (2020). Pressure-Induced Phase Separation of Miscible Liquids: 1 : 1 N-Pentane/Iso-Pentane. CrystEngComm 22, 8251–8255. doi:10.1039/D0CE01335H
Lomovsky, O. I., Lomovskiy, I. O., and Orlov, D. V. (2017). Mechanochemical Solid Acid/Base Reactions for Obtaining Biologically Active Preparations and Extracting Plant Materials. Green. Chem. Lett. Rev. 10 (4), 171–185. doi:10.1080/17518253.2017.1339832
Losev, E. A., and Boldyreva, E. V. (2014). The Role of a Liquid in “Dry” Co-Grinding: a Case Study of the Effect of Water on Mechanochemical Synthesis in a "L-Serine-Oxalic Acid" System. CrystEngComm 16 (19), 3857–3866. doi:10.1039/C3CE42321B
Luty, T., Ordon, P., and Eckhardt, C. J. (2002). A Model for Mechanochemical Transformations: Applications to Molecular Hardness, Instabilities, and Shock Initiation of Reaction. J. Chem. Phys. 117 (4), 1775–1785. doi:10.1063/1.1485968
MacKenzie, K. J. D., and Barneveld, D. V. (2006). Carbothermal Synthesis of β-Sialon from Mechanochemically Activated Precursors. J. Eur. Ceram. Soc. 26 (1–2), 209–215. doi:10.1016/j.jeurceramsoc.2004.10.004
MacKenzie, K. J. D., Brew, D. R. M., Fletcher, R. A., and Vagana, R. (2007). Formation of Aluminosilicate Geopolymers from 1:1 Layer-Lattice Minerals Pre-treated by Various Methods: A Comparative Study. J. Mater. Sci. 42, 4667–4674. doi:10.1007/s10853-006-0173-x
Mackenzie, K. J. D., Temuujin, J., Jadambaa, T., Smith, M. E., and Angerer, P. (2000). Mechanochemical Synthesis and Sintering Behaviour of Magnesium Aluminate Spinel. J. Mater. Sci. 35, 5529–5535. doi:10.1023/A:1004839108758
MacKenzie, K. J. D., Temuujin, J., and Okada, K. (1999). Thermal Decomposition of Mechanically Activated Gibbsite. Thermochim. Acta 327, 103–108. doi:10.1016/s0040-6031(98)00609-1
Maglia, F., Anselmi-Tamburini, U., Deidda, C., Delogu, F., Cocco, G., and Munir, Z. A. (2004). Role of Mechanical Activation in SHS Synthesis of TiC. J. Mater. Sci. 39 (16/17), 5227–5230. doi:10.1023/B:JMSC.0000039215.28545.2f
Mahmoud, A. E. D., Stolle, A., and Stelter, M. (2018). Sustainable Synthesis of High-Surface-Area Graphite Oxide via Dry Ball Milling. ACS Sust. Chem. Eng. 6 (5), 6358–6369. doi:10.1021/acssuschemeng.8b00147
Makarov, D. E. (2016). Perspective: Mechanochemistry of Biological and Synthetic Molecules. J. Chem. Phys. 144 (3), 030901. doi:10.1063/1.4939791
Margetić, D., and Štrukil, V. (2020). “Recent Advances in Mechanochemical Organic Synthesis,” in Organic Synthesis (IntechOpen). doi:10.5772/intechopen.90897
Matsusaka, S., Maruyama, H., Matsuyama, T., and Ghadiri, M. (2010). Triboelectric Charging of Powders: A Review. Chem. Eng. Sci. 65 (22), 5781–5807. doi:10.1016/j.ces.2010.07.005
Maurin, O., Verdié, P., Subra, G., Lamaty, F., Martinez, J., and Métro, T.-X. (2017). Peptide Synthesis: Ball-Milling, in Solution, or on Solid Support, what Is the Best Strategy? Beilstein J. Org. Chem. 13, 2087–2093. doi:10.3762/bjoc.13.206
Mechano-Chemical Reaction (2009). “Mechano-Chemical Reaction,” in IUPAC Compendium of Chemical Terminology. NC: IUPAC: Research Triagle Park. doi:10.1351/goldbook.MT07141
Mehrotra, S. P., Alex, T. C., Greifzu, G., and Kumar, R. (2016). Mechanical Activation of Gibbsite and Boehmite: New Findings and Their Implications. Trans. Indian Inst. Met. 69 (1), 51–59. doi:10.1007/s12666-015-0633-6
Michalchuk, A. A. L., Hemingway, J., and Morrison, C. A. (2021). Predicting the Impact Sensitivities of Energetic Materials through Zone-Center Phonon Up-Pumping. J. Chem. Phys. 154 (6), 064105. doi:10.1063/5.0036927
Michalchuk, A. A. L., Hope, K. S., Kennedy, S. R., Blanco, M. V., Boldyreva, E. V., and Pulham, C. R. (2018a). Ball-free Mechanochemistry: In Situ Real-Time Monitoring of Pharmaceutical Co-Crystal Formation by Resonant Acoustic Mixing. Chem. Commun. 54 (32), 4033–4036. doi:10.1039/C8CC02187B
Michalchuk, A. A. L., Rudić, S., Pulham, C. R., and Morrison, C. A. (2018b). Vibrationally Induced Metallisation of the Energetic Azide α-NaN3. Phys. Chem. Chem. Phys. 20 (46), 29061–29069. doi:10.1039/C8CP06161K
Michalchuk, A. A. L., Trestman, M., Rudić, S., Portius, P., Fincham, P. T., Pulham, C. R., et al. (2019a). Predicting the Reactivity of Energetic Materials: An Ab Initio Multi-Phonon Approach. J. Mater. Chem. A. 7 (33), 19539–19553. doi:10.1039/C9TA06209B
Michalchuk, A. A. L., Tumanov, I. A., and Boldyreva, E. V. (2019b). Ball Size or Ball Mass - what Matters in Organic Mechanochemical Synthesis? CrystEngComm 21 (13), 2174–2179. doi:10.1039/C8CE02109K
Michalchuk, A. A. L., Tumanov, I. A., and Boldyreva, E. V. (2013). Complexities of Mechanochemistry: Elucidation of Processes Occurring in Mechanical Activators via Implementation of a Simple Organic System. CrystEngComm 15 (32), 6403. doi:10.1039/c3ce40907d
Michalchuk, A. A. L., Tumanov, I. A., and Boldyreva, E. V. (2018c). The Effect of Ball Mass on the Mechanochemical Transformation of a Single-Component Organic System: Anhydrous Caffeine. J. Mater. Sci. 53 (19), 13380–13389. doi:10.1007/s10853-018-2324-2
Michalchuk, A. A. L., Tumanov, I. A., Drebushchak, V. A., and Boldyreva, E. V. (2014). Advances in Elucidating Mechanochemical Complexities via Implementation of a Simple Organic System. Faraday Discuss. 170, 311–335. doi:10.1039/C3FD00150D
Michalchuk, A. A. L., Tumanov, I. A., Konar, S., Kimber, S. A. J., Pulham, C. R., and Boldyreva, E. V. (2017). Challenges of Mechanochemistry: Is In Situ Real-Time Quantitative Phase Analysis Always Reliable? A Case Study of Organic Salt Formation. Adv. Sci. 4 (9), 1700132. doi:10.1002/advs.201700132
Mikhailenko, M. A., Shakhtshneider, T. P., and Boldyrev, V. V. (2004). On the Mechanism of Mechanochemical Synthesis of Phthalylsulphathiazole. J. Mater. Sci. 39 (16/17), 5435–5439. doi:10.1023/B:JMSC.0000039261.66084.a3
Moores, A. (2018). Bottom up, Solid-Phase Syntheses of Inorganic Nanomaterials by Mechanochemistry and Aging. Curr. Opin. Green Sust. Chem. 12, 33–37. doi:10.1016/j.cogsc.2018.05.004
Moshkovich, A., Lapsker, I., Laihtman, A., and Rapoport, L. S. (2020). Friction, Wear and Deformed Structure of Ag and Ni under Early Stages of Scratching. Wear 462-463, 203510. doi:10.1016/j.wear.2020.203510
Moshkovich, A., and Rapoport, L. S. (2020). Effect of Stacking-Fault Energy on the Deformed Structures and Work Hardening of Ag and Ni after Scratching during Early Loading Stage. J. Materi Eng. Perform. 29 (11), 7231–7238. doi:10.1007/s11665-020-05228-4
Mukherjee, A., Rogers, R. D., and Myerson, A. S. (2018). Cocrystal Formation by Ionic Liquid-Assisted Grinding: Case Study with Cocrystals of Caffeine. CrystEngComm 20 (27), 3817–3821. doi:10.1039/C8CE00859K
Myz, S. A., Shakhtshneider, T. P., Fucke, K., Fedotov, A. P., Boldyreva, E. V., Boldyrev, V. V., et al. (2009). Synthesis of Co-crystals of Meloxicam with Carboxylic Acids by Grinding. Mendeleev Commun. 19 (5), 272–274. doi:10.1016/j.mencom.2009.09.014
Myz, S. A., Shakhtshneider, T. P., Tumanov, N. A., and Boldyreva, E. V. (2012). Preparation and Studies of the Co-crystals of Meloxicam with Carboxylic Acids. Russ. Chem. Bull. 61 (9), 1798–1809. doi:10.1007/s11172-012-0248-6
Nash, D. J., Restrepo, D. T., Parra, N. S., Giesler, K. E., Penabade, R. A., Aminpour, M., et al. (2016). Heterogeneous Metal-Free Hydrogenation over Defect-Laden Hexagonal Boron Nitride. ACS Omega 1 (6), 1343–1354. doi:10.1021/acsomega.6b00315
Ogienko, A. G., Myz, S. A., Ogienko, A. A., Nefedov, A. A., Stoporev, A. S., Mel’gunov, M. S., et al. (2018). Cryosynthesis of Co-crystals of Poorly Water-Soluble Pharmaceutical Compounds and Their Solid Dispersions with Polymers. The "Meloxicam-Succinic Acid" System as a Case Study. Cryst. Growth Des. 18 (12), 7401–7409. doi:10.1021/acs.cgd.8b01070
Oliveira, P. F. M., Haruta, N., Chamayou, A., Guidetti, B., Baltas, M., Tanaka, K., et al. (2017). Comprehensive Experimental Investigation of Mechanically Induced 1,4-Diazines Synthesis in Solid State. Tetrahedron 73 (16), 2305–2310. doi:10.1016/j.tet.2017.03.014
Oprea, C. V. (1979). Mechanochemical Degradation of Polymers. Polym. Mech. 14, 783–792. doi:10.1007/BF00860088
Ostwald, W. (1919). Die Chemische Literatur Und Die Organisation Der Wissenschaft. Leipzig, Germany: Akademie-Verlag.
Otsuka, M., Matsuda, Y., Hsu, J., Fox, J. L., and Higuchi, W. I. (1994). Mechanochemical Synthesis of Bioactive Material: Effect of Environmental Conditions on the Phase Transformation of Calcium Phosphates during Grinding. Bio-Medical Mater. Eng. 4 (5), 357–362. doi:10.3233/BME-1994-4502
Otsuka, M., Matsumoto, T., and Kaneniwa, N. (2011). Effects of the Mechanical Energy of Multi-Tableting Compression on the Polymorphic Transformations of Chlorpropamide. J. Pharm. Pharmacol. 41 (10), 665–669. doi:10.1111/j.2042-7158.1989.tb06337.x
Park, Y. H., Hashimoto, H., Abe, T., and Watanabe, R. (1994). Mechanical Alloying Process of Metal-B (M ≡ Ti, Zr) Powder Mixture. Mater. Sci. Eng. A 181-182, 1291–1295. doi:10.1016/0921-5093(94)90849-4
Pavljukhin, Y. T., Medikov, Y. Y., and Boldyrev, V. V. (1983). Magnetic and Chemical Properties of Mechanically Activated Zinc and Nickel Ferrites. Mater. Res. Bull. 18, 1317–1327. doi:10.1016/0025-5408(83)90038-7
Pavlyukhin, Y. T., Medikov, Y. Y., and Boldyrev, V. V. (1984). On the Consequences of Mechanical Activation of Zinc and Nickel Ferrites. J. Solid State. Chem. 53 (2), 155–160. doi:10.1016/0022-4596(84)90089-6
Pickhardt, W., Grätz, S., and Borchardt, L. (2020). Direct Mechanocatalysis: Using Milling Balls as Catalysts. Chem. Eur. J. 26 (57), 12903–12911. doi:10.1002/chem.202001177
Politov, A. A., Chupakhin, A. P., Tapilin, V. M., Bulgakov, N. N., and Druganov, A. G. (2010). To Mechanochemical Dimerization of Anthracene. Crystalline Phenanthrene under High Pressure and Shear Conditions. J. Struct. Chem. 51 (6), 1064–1069. doi:10.1007/s10947-010-0163-3
Polukhina, L. M., and Baramboim, N. K. (1975). Intensity of Mechanical Action and Mechanical Degradation of Rigid Polymers. Polym. Mech. 9 (2), 323–325. doi:10.1007/BF00855062
Poręba, T., Ernst, M., Zimmer, D., Macchi, P., and Casati, N. (2019). Pressure-Induced Polymerization and Electrical Conductivity of a Polyiodide. Angew. Chem. Int. Ed. Engl. 58 (20), 6625–6629. doi:10.1002/ange.20190117810.1002/anie.201901178
Prentice, I. J., Liu, X., Nerushev, O. A., Balakrishnan, S., Pulham, C. R., and Camp, P. J. (2020). Experimental and Simulation Study of the High-Pressure Behavior of Squalane and Poly-α-Olefins. J. Chem. Phys. 152 (7), 074504. doi:10.1063/1.5139723
Radev, D. D., and Klisurski, D. (1994). Properties of TiB2 Powders Obtained in a Mechanochemical Way. J. Alloys Comp. 206 (1), 39–41. doi:10.1016/0925-8388(94)90008-6
Rak, M. J., Friščić, T., and Moores, A. (2016). One-Step, Solvent-free Mechanosynthesis of Silver Nanoparticle-Infused Lignin Composites for Use as Highly Active Multidrug Resistant Antibacterial Filters. RSC Adv. 6 (63), 58365–58370. doi:10.1039/C6RA03711A
Rak, M. J., Saadé, N. K., Friščić, T., and Moores, A. (2014). Mechanosynthesis of Ultra-small Monodisperse Amine-Stabilized Gold Nanoparticles with Controllable Size. Green. Chem. 16 (1), 86–89. doi:10.1039/C3GC41827H
Reddyhoff, T., Ewen, J. P., Deshpande, P., Frogley, M. D., Welch, M. D., and Montgomery, W. (2021). Macroscale Superlubricity and Polymorphism of Long-Chain N-Alcohols. ACS Appl. Mater. Inter. 13 (7), 9239–9251. doi:10.1021/acsami.0c21918
Rehbinder, P. (1947). New Physico-Chemical Phenomena in the Deformation and Mechanical Treatment of Solids. Nature 159 (4052), 866–867. doi:10.1038/159866a0
Ribas-Arino, J., and Marx, D. (2012). Covalent Mechanochemistry: Theoretical Concepts and Computational Tools with Applications to Molecular Nanomechanics. Chem. Rev. 112 (10), 5412–5487. doi:10.1021/cr200399q
Rightmire, N. R., and Hanusa, T. P. (2016). Advances in Organometallic Synthesis with Mechanochemical Methods. Dalton Trans. 45 (6), 2352–2362. doi:10.1039/C5DT03866A
Roberts, T. A., and Royle, M. (1991). “Classification of Energetic Industrial Chemicals for Transport,” in Hazards 11 IChemE Symposium Series (Institute for Chemical Engineering), 191–208.
Roerich Pact (1935). Treaty on the Protection of Artistic and Scientific Institutions and Historic Monuments. U.S. Committee of the Blue Shield. www.uscbs.org/1935-roerich-pact.html.
Roscoe, R. (1934). Strength of Metal Single Crystals. Nature 133, 912. doi:10.1038/133912b010.1038/133912a0
Rosenkranz, A., Costa, H. L., Baykara, M. Z., and Martini, A. (2021). Synergetic Effects of Surface Texturing and Solid Lubricants to Tailor Friction and Wear - A Review. Tribol. Int. 155, 106792. doi:10.1016/j.triboint.2020.106792
Rosenkranz, A., Liu, Y., Yang, L., and Chen, L. (2020). 2D Nano-Materials beyond Graphene: From Synthesis to Tribological Studies. Appl. Nanosci 10 (9), 3353–3388. doi:10.1007/s13204-020-01466-z
Rothenberg, G., Downie, A. P., Raston, C. L., and Scott, J. L. (2001). Understanding Solid/Solid Organic Reactions. J. Am. Chem. Soc. 123 (36), 8701–8708. doi:10.1021/ja0034388
Rusanov, A. I., Uriev, N. B., Eryukin, P. V., Movchan, T. G., and Esipova, N. E. (2004). Effect of the Strain Sign in Corrosion under Stress. Mendeleev Commun. 14 (2), 58–59. doi:10.1070/MC2004v014n02ABEH001875
Rybin, D. S., Konygin, G. N., Arsentyeva, I. P., and Sharafutdinova, D. R. (2019). Deformation-Induced Formation of Nanostructures in Molecular Crystals. Mater. Today Proc. 12, 97–101. doi:10.1016/j.matpr.2019.03.073
Rybin, D. S., Konygin, G. N., Porsev, V. E., Yelsukov, E. P., Arsentyeva, I. P., and Boldyrev, V. V. (2014). Deformation-Induced Structural Transformations in Molecular Crystals. Acta Phys. Pol. A. 126 (4), 1014–1018. doi:10.12693/APhysPolA.126.1014
Saratovkin, D. D., and Savintcev, P. A. (1941). The Formation of a Fluid Phase at the Contacts of Solids Forming an Eutectic. Proceed Acad. Sci. USSR 33, 303.
Sarmah, K. K., Rajbongshi, T., Bhuyan, A., and Thakuria, R. (2019). Effect of Solvent Polarity in Mechanochemistry: Preparation of a Conglomerate vs. Racemate. Chem. Commun. 55 (73), 10900–10903. doi:10.1039/C9CC05687D
Sawama, Y., Yasukawa, N., Ban, K., Goto, R., Niikawa, M., Monguchi, Y., et al. (2018). Stainless Steel-Mediated Hydrogen Generation from Alkanes and Diethyl Ether and its Application for Arene Reduction. Org. Lett. 20 (10), 2892–2896. doi:10.1021/acs.orglett.8b00931
Schneider-Rauber, G., Arhangelskis, M., Bond, A. D., Ho, R., Nere, N., Bordawekar, S., et al. (2021). Polymorphism and Surface Diversity Arising from Stress-Induced Transformations - the Case of Multicomponent Forms of Carbamazepine. Acta Crystallogr. Sect B 77 (1), 54–67. doi:10.1107/S2052520620015437
Senna, M. (2001). Recent Development of Materials Design through a Mechanochemical Route. Int. J. Inorg. Mater. 6. doi:10.1016/S1466-6049(01)00060-5
Senna, M. (1993). Incipient Chemical Interaction between Fine Particles under Mechanical Stress - a Feasibility of Producing Advanced Materials via Mechanochemical Routes. Solid State Ionics 63-65, 3–9. doi:10.1016/0167-2738(93)90078-H
Šepelák, V., Bégin-Colin, S., and Le Caër, G. (2012). Transformations in Oxides Induced by High-Energy Ball-Milling. Dalton Trans. 41 (39), 11927. doi:10.1039/c2dt30349c
Šepelák, V., Bergmann, I., Feldhoff, A., Heitjans, P., Krumeich, F., Menzel, D., et al. (2007). Nanocrystalline Nickel Ferrite, NiFe2O4: Mechanosynthesis, Nonequilibrium Cation Distribution, Canted Spin Arrangement, and Magnetic Behavior. J. Phys. Chem. C 111 (13), 5026–5033. doi:10.1021/jp067620s
Šepelák, V., Düvel, A., Wilkening, M., Becker, K.-D., and Heitjans, P. (2013). Mechanochemical Reactions and Syntheses of Oxides. Chem. Soc. Rev. 42 (18), 7507. doi:10.1039/c2cs35462d
Sepelak, V., Tkacova, K., Boldyrev, V. V., and Becker, K.-D. (1997). Mechanically Induced Cation Redistribution in ZnFe2O4 and its Thermal Stability. Physica B: Cond. Mat. 234–236, 617–619. doi:10.1016/S0921-4526(96)01061-7
Šepelák, V., Tkácová, K., Boldyrev, V. V., and Steinike, U. (1996). Crystal Structure Refinement of the Mechanically Activated Spinel-Ferrite. Mater. Sci. Forum 228–231, 783–788. doi:10.4028/www.scientific.net/MSF
Shakhtshneider, T. P., Danède, F., Capet, F., Willart, J. F., Descamps, M., Myz, S. A., et al. (2007). Grinding of Drugs with Pharmaceutical Excipients at Cryogenic Temperatures. J. Therm. Anal. Calorim. 89 (3), 699–707. doi:10.1007/s10973-006-7958-7
Shakhtshneider, T. P., Myz, S. A., Boldyreva, E. V., Nizovskii, A. I., and Kumar, R. (2014a). Core-Shell Mechanocomposites of Drugs with Inorganic Oxides and Hydroxides. Acta Phys. Pol. A. 126 (4), 1019–1024. doi:10.12693/APhysPolA.126.1019
Shakhtshneider, T. P., Myz, S. A., Nizovskii, A. I., Kalinkin, A. V., Boldyreva, E. V., Alex, T. C., et al. (2014b). Effect of the Selected Inorganic Carriers on the Properties of Mechanocomposites with Drugs. Dokl Chem. 456 (2), 98–102. doi:10.1134/S0012500814060044
Shalaev, E., Wu, K., Shamblin, S., Krzyzaniak, J. F., and Descamps, M. (2016). Crystalline Mesophases: Structure, Mobility, and Pharmaceutical Properties. Adv. Drug Deliv. Rev. 100, 194–211. doi:10.1016/j.addr.2016.04.002
Shields, D. J., Karothu, D. P., Sambath, K., Ranaweera, R. A. A. U., Schramm, S., Duncan, A., et al. (2020). Cracking under Internal Pressure: Photodynamic Behavior of Vinyl Azide Crystals through N2 Release. J. Am. Chem. Soc. 142 (43), 18565–18575. doi:10.1021/jacs.0c07830
Singla, R., Alex, T. C., and Kumar, R. (2020). On Mechanical Activation of Glauconite: Physicochemical Changes, Alterations in Cation Exchange Capacity and Mechanisms. Powder Tech. 360, 337–351. doi:10.1016/j.powtec.2019.10.035
Skripkina, T. S., Podgorbunskikh, E. M., and Lomovsky, O. I. (2020). Designing Core-Shell Materials Using Humic Acids. IOP Conf. Ser. Mater. Sci. Eng. 733, 012041. doi:10.1088/1757-899X/733/1/012041
Sohma, J. (1989). Mechanochemistry of Polymers. Prog. Polym. Sci. 14 (4), 451–596. doi:10.1016/0079-6700(89)90004-X
Steele, B. A., Goldman, N., Kuo, I.-F. W., and Kroonblawd, M. P. (2020). Mechanochemical Synthesis of Glycine Oligomers in a Virtual Rotational Diamond Anvil Cell. Chem. Sci. 11 (30), 7760–7771. doi:10.1039/D0SC00755B
Steinike, U., and Tkáčová, K. (2000). Mechanochemistry of Solids - Real Structure and Reactivity. J. Mater. Synth. Process. 8 (3/4), 197–203. doi:10.1023/A:1011364110355
Stolar, T., Batzdorf, L., Lukin, S., Žilić, D., Motillo, C., Friščić, T., et al. (2017). In Situ Monitoring of the Mechanosynthesis of the Archetypal Metal-Organic Framework HKUST-1: Effect of Liquid Additives on the Milling Reactivity. Inorg. Chem. 56 (11), 6599–6608. doi:10.1021/acs.inorgchem.7b00707
Stolar, T., Lukin, S., Tireli, M., Sović, I., Karadeniz, B., Kereković, I., et al. (2019). Control of Pharmaceutical Cocrystal Polymorphism on Various Scales by Mechanochemistry: Transfer from the Laboratory Batch to the Large-Scale Extrusion Processing. ACS Sust. Chem. Eng. 7 (7), 7102–7110. doi:10.1021/acssuschemeng.9b00043
Stolar, T., Prašnikar, A., Martinez, V., Karadeniz, B., Bjelić, A., Mali, G., et al. (2021). Scalable Mechanochemical Amorphization of Bimetallic Cu−Zn MOF-74 Catalyst for Selective CO2 Reduction Reaction to Methanol. ACS Appl. Mater. Inter. 13 (2), 3070–3077. doi:10.1021/acsami.0c21265
Stolar, T., and Užarević, K. (2020). Mechanochemistry: an Efficient and Versatile Toolbox for Synthesis, Transformation, and Functionalization of Porous Metal-Organic Frameworks. CrystEngComm 22 (27), 4511–4525. doi:10.1039/D0CE00091D
Stößer, R., Feist, M., Willgeroth, C., Emmerling, F., Menzel, M., and Reuther, H. (2013). The “Quiet Goldschmidt”-A Mechanochemical, Thermoanalytical, and Spectroscopic Study of Selected Steps of the Aluminothermic Reaction. J. Solid State. Chem. 202, 173–190. doi:10.1016/j.jssc.2013.02.032
Strobridge, F. C., Judaš, N., and Friščić, T. (2010). A Stepwise Mechanism and the Role of Water in the Liquid-Assisted Grinding Synthesis of Metal-Organic Materials. CrystEngComm 12 (8), 2409. doi:10.1039/c003521a
Su, W., Yu, J., Li, Z., and Jiang, Z. (2011). Solvent-Free Cross-Dehydrogenative Coupling Reactions under High Speed Ball-Milling Conditions Applied to the Synthesis of Functionalized Tetrahydroisoquinolines. J. Org. Chem. 76 (21), 9144–9150. doi:10.1021/jo2015533
Surov, D. V. (2004). Investigation of Structural Changes in Graphite during Mechanochemical Treatment and Annealing. Novosibirsk: MSc, Novosibirsk State University.
Suryanarayana, C., Ivanov, E., and Boldyrev, V. V. (2001). The Science and Technology of Mechanical Alloying. Mater. Sci. Eng. A 304-306, 151–158. doi:10.1016/S0921-5093(00)01465-9
Takacs, L. (1998). Combustion Phenomena Induced by Ball Milling. Mater. Sci. Forum 269-272, 513–522. doi:10.4028/www.scientific.net/MSF.269-272.513
Takacs, L. (2000). Quicksilver from Cinnabar: The First Documented Mechanochemical Reaction? JOM 52 (1), 12–13. doi:10.1007/s11837-000-0106-0
Takacs, L. (2002). Self-Sustaining Reactions Induced by Ball Milling. Prog. Mater. Sci. 47 (4), 355–414. doi:10.1016/S0079-6425(01)00002-0
Takacs, L. (2013). The Historical Development of Mechanochemistry. Chem. Soc. Rev. 42 (18), 7649. doi:10.1039/c2cs35442j
Tan, D., and García, F. (2019). Main Group Mechanochemistry: from Curiosity to Established Protocols. Chem. Soc. Rev. 48, 2274–2292. doi:10.1039/C7CS00813A
Temuujin, J., MacKenzie, K. J. D., Jadambaa, T., Namjildorj, B., Olziiburen, B., Smith, M. E., et al. (2000). Effect of Mechanochemical Treatment on the Synthesis of Calcium Dialuminate. J. Mater. Chem. 10 (4), 1019–1023. doi:10.1039/a909888g
Temuujin, J., Okada, K., and MacKenzie, K. J. D. (1998b). Characterization of Aluminosilicate (Mullite) Precursors Prepared by a Mechanochemical Process. J. Mater. Res. 13 (8), 2184–2189. doi:10.1557/JMR.1998.0305
Temuujin, J., Okada, K., and MacKenzie, K. J. D. (1998a). Role of Water in the Mechanochemical Reactions of MgO-SiO2 Systems. J. Solid State. Chem. 138, 169–177. doi:10.1006/jssc.1998.7768
Thiessen, K. P. (1986). On the Origin of Increased Activity in Mechanochemistry of Solids. J. Chim. Phys. 83, 717–724. doi:10.1051/jcp/1986830717
Thiessen, K. P. (2016). Tribochemistry versus Nano-Tribology. I. Theoretical Considerations on Making a Tandem Nanoscope. Eur. Chem. Bull. 5 (10), 420–422. doi:10.17628/ECB.2016.5.420
Thiessen, K. P. (1974). Tribogalvanik - ein neues Anwendungsgebiet der Tribochemie. Z. Chem. 14 (4), 135–141. doi:10.1002/zfch.19740140403
Thiessen, P. A., Heinicke, G., and Schober, E. (1970). Zur tribochemischen Umsetzung von Gold und CO2 mit Hilfe radioaktiver Markierung. Z. Anorg. Allg. Chem. 377, 20–28. doi:10.1002/zaac.19703770104
Thiessen, P. A., Meyer, K., and Heinicke, G. (1966). Grundlagen der Tribochemie. Abh. Dtsch. Akad. Wiss.
Thießen, P. A. (1965). Physikalisch-Chemische Untersuchungen Tribomechanischer Vorgänge (Fragestellung, Ergebnisse, Aussichten). Z. Chem. 5, 162–171. doi:10.1002/zfch.19650050503
Titi, H. M., Do, J.-L., Howarth, A. J., Nagapudi, K., and Friščić, T. (2020). Simple, Scalable Mechanosynthesis of Metal-Organic Frameworks Using Liquid-Assisted Resonant Acoustic Mixing (LA-RAM). Chem. Sci. 11 (29), 7578–7584. doi:10.1039/D0SC00333F
Tkáčová, K., Šepelák, V., Števulová, N., and Boldyrev, V. V. (1996). Structure–Reactivity Study of Mechanically Activated Zinc Ferrite. J. Solid State. Chem. 123 (1), 100–108. doi:10.1006/jssc.1996.0157
Tokmakoff, A., Fayer, M. D., and Dlott, D. D. (1993). Chemical Reaction Initiation and Hot-Spot Formation in Shocked Energetic Molecular Materials. J. Phys. Chem. 97 (9), 1901–1913. doi:10.1021/j100111a031
Torre, F., Barra, P., Pia, G., Delogu, F., and Porcheddu, A. (2020). Microscopic Kinetic Information from Ag Oxalate Mechanochemistry in Ball Drop Experiments. Mater. Lett. 267, 127525. doi:10.1016/j.matlet.2020.127525
Trofimova, E. G., Podgorbunskikh, E. M., Skripkina, T. S., Bychkov, A. L., and Lomovsky, O. I. (2018). Scaling of the Mechano-Chemical Process of Production of Silicon Chelates from Plant Raw Materials. Bulgar. Chem. Commun. 50 (K), 45–48.
Tulip, P. R., and Bates, S. P. (2009). Pressure-Induced Metallization of a Single-Component Molecular Crystal. J. Phys. Chem. C 113 (44), 19310–19316. doi:10.1021/jp906442x
Tumanov, I. A., Achkasov, A. F., Boldyreva, E. V., and Boldyrev, V. V. (2012). About the Possibilities to Detect Intermediate Stages in Mechanochemical Synthesis of Molecular Complexes. Russ. J. Phys. Chem. 86 (6), 1014–1017. doi:10.1134/S003602441206026X
Tumanov, I. A., Achkasov, A. F., Boldyreva, E. V., and Boldyrev, V. V. (2011). Following the Products of Mechanochemical Synthesis Step by Step. CrystEngComm 13 (7), 2213. doi:10.1039/c0ce00869a
Tumanov, I. A., Achkasov, A. F., Myz, S. A., Boldyreva, E. V., and Boldyrev, V. V. (2014). Different Effect of Impact and Shear Mechanical Treatment on Mechanochemical Cocrystallization of Piroxicam and Succinic Acid. Dokl Chem. 457 (2), 154–159. doi:10.1134/S0012500814080059
Tumanov, I. A., Michalchuk, A. A. L., Politov, A. A., Boldyreva, E. V., and Boldyrev, V. V. (2017). Inadvertent Liquid Assisted Grinding: a Key to “Dry” Organic Mechano-Co-Crystallisation? CrystEngComm 19 (21), 2830–2835. doi:10.1039/C7CE00517B
UNECE (2009). Recommendations on the Transport of Dangerous Goods - Manual of Tests and Criteria (New York: ST/SG/AC.10/11/Rev.6; United Nations).
Urakaev, F. Kh., Boldyrev, V. V., Pozdnyakov, O. F., and Regel’, V. R. (1977). Studying Mechanism of Mechanochemical Decomposition of Solid Inorganic Compounds. Kinetika i Kataliz 18 (2), 350–358.
Urakaev, F. K., and Boldyrev, V. V. (2000). Correlation between the Yield of Volatile Products and the Characteristics of the Propagation of Cracks in Crystals. Russ. J. Phys. Chem. A. 74 (8), 1339–1344.
Urakaev, F. K., and Boldyrev, V. V. (2000a). Mechanism and Kinetics of Mechanochemical Processes in Comminuting Devices. Powder Tech. 107, 93–107. doi:10.1016/S0032-5910(99)00175-8
Urakaev, F. K., and Boldyrev, V. V. (2000b). Mechanism and Kinetics of Mechanochemical Processes in Comminuting Devices. Powder Tech. 107, 197–206. doi:10.1016/S0032-5910(99)00200-4
Urakaev, F. K. (2007). Mechanodestruction of Minerals at the Crack Tip (Overview): 1. Experiment. Phys. Chem. Minerals 34 (5), 351–361. doi:10.1007/s00269-007-0153-y
Urakaev, F. K. (2008). Mechanodestruction of Minerals at the Crack Tip (Overview): 2. Theory. Phys. Chem. Minerals 35 (4), 231–239. doi:10.1007/s00269-008-0216-8
Vaitkus, A., Merkys, A., and Gražulis, S. (2021). Validation of the Crystallography Open Database Using the Crystallographic Information Framework. J. Appl. Cryst. 54 (2), 661–672. doi:10.1107/S1600576720016532
Vasil’ev, L. S. (2012). Kinetics of the Formation of Supersaturated Solid Solutions upon Mechanical Alloying: I. General Scheme of Interaction of Diffusion Fluxes upon Plastic Deformation of Multiphase Nanomaterials. Phys. Met. Metallogr. 113 (8), 733–741. doi:10.1134/S0031918X12080133
Vasil’ev, L. S., Lomaev, I. L., and Elsukov, E. P. (2009). Kinetics of Dissolution of Phases upon Deformation of Nanostructured Metals and Alloys. Phys. Met. Metallogr. 107 (2), 141–150. doi:10.1134/S0031918X09020057
Vasil’ev, L. S., Lomaev, I. L., and Elsukov, E. P. (2006). On the Analysis of the Mechanisms of the Strain-Induced Dissolution of Phases in Metals. Phys. Met. Metallogr. 102 (2), 186–197. doi:10.1134/S0031918X06080102
Vasil’ev, L. S., and Lomaev, I. L. (2011). Structural Transformations, Distribution of Nonequilibrium Vacancies, and Anomalous Diffusion in Plastically Deformed Metals and Alloys upon Mechanical Alloying. Phys. Met. Metallogr. 111 (1), 1–12. doi:10.1134/S0031918X11010145
Velasquez, M., Batiot-Dupeyrat, C., Gallego, J., Fernández, J. J., and Santamaria, A. (2016). Synthesis of Carbon Nano-Chains from Glycerol-Ethanol Decomposition over Ni-Fe Alloy Catalyst. Diamond Relat. Mater. 70, 105–113. doi:10.1016/j.diamond.2016.10.019
Vogt, C. G., Oltermann, M., Pickhardt, W., Grätz, S., and Borchardt, L. (2021). Bronze Age of Direct Mechanocatalysis: How Alloyed Milling Materials Advance Coupling in Ball Mills. Adv. Energ. Sustain. Res. 2, 2100011. doi:10.1002/aesr.202100011
Wang, L., and Qin, X. Y. (2003). The Effect of Mechanical Milling on the Formation of Nanocrystalline Mg2Si through Solid-State Reaction. Scripta Materialia 49 (3), 243–248. doi:10.1016/S1359-6462(03)00241-0
Wang, Z., Li, Z., Ng, M., and Milner, P. J. (2020). Rapid Mechanochemical Synthesis of Metal-Organic Frameworks Using Exogenous Organic Base. Dalton Trans. 49 (45), 16238–16244. doi:10.1039/D0DT01240H
Watanabe, T., Hasegawa, S., Wakiyama, N., Kusai, A., and Senna, M. (2003). Comparison between Polyvinylpyrrolidone and Silica Nanoparticles as Carriers for Indomethacin in a Solid State Dispersion. Int. J. Pharmaceutics 250 (1), 283–286. doi:10.1016/S0378-5173(02)00549-5
Watanabe, T., Ohno, I., Wakiyama, N., Kusai, A., and Senna, M. (2002). Stabilization of Amorphous Indomethacin by Co-Grinding in a Ternary Mixture. Int. J. Pharmaceutics 241 (1), 103–111. doi:10.1016/S0378-5173(02)00196-5
Watanabe, T., Wakiyama, N., Usui, F., Ikeda, M., Isobe, T., and Senna, M. (2001). Stability of Amorphous Indomethacin Compounded with Silica. Int. J. Pharmaceutics 226 (1–2), 81–91. doi:10.1016/S0378-5173(01)00776-1
Weyna, D. R., Shattock, T., Vishweshwar, P., and Zaworotko, M. J. (2009). Synthesis and Structural Characterization of Cocrystals and Pharmaceutical Cocrystals: Mechanochemistry vs Slow Evaporation from Solution. Cryst. Growth Des. 9 (2), 1106–1123. doi:10.1021/cg800936d
Wilke, M., Akhmetova, I., Rademann, K., and Emmerling, F. (2018). Mechanochemical Synthesis of Cerium(IV)-Phosphonates. J. Mater. Sci. 53 (19), 13733–13741. doi:10.1007/s10853-018-2507-x
Wilkinson, M. D., Dumontier, M., Aalbersberg, I. J., Appleton, G., Axton, M., Baak, A., et al. (2016). The FAIR Guiding Principles for Scientific Data Management and Stewardship. Sci. Data 3 (1), 160018. doi:10.1038/sdata.2016.18
Yelsukov, E. P., Ul’yanov, A. L., Protasov, A. V., Porsev, V. E., Rybin, D. S., and Kolodkin, D. A. (2013). Deformation-Induced Structural Transformations in Si and the Initial Stage of Mechanical Alloying of Si and Fe. Colloid J. 75 (3), 261–266. doi:10.1134/S1061933X13030058
Zakharov, B. A., and Boldyreva, E. V. (2019). High Pressure: A Complementary Tool for Probing Solid-State Processes. CrystEngComm 21 (1), 10–22. doi:10.1039/C8CE01391H
Zhang, C., Jiao, F., and Li, H. (2018). Crystal Engineering for Creating Low Sensitivity and Highly Energetic Materials. Cryst. Growth Des. 18 (10), 5713–5726. doi:10.1021/acs.cgd.8b00929
Zhang, C., Li, J., Liu, E., He, C., Shi, C., Du, X., et al. (2012). Synthesis of Hollow Carbon Nano-Onions and Their Use for Electrochemical Hydrogen Storage. Carbon 50 (10), 3513–3521. doi:10.1016/j.carbon.2012.03.019
Zhang, C., Li, J., Shi, C., He, C., Liu, E., and Zhao, N. (2014). Effect of Ni, Fe and Fe-Ni Alloy Catalysts on the Synthesis of Metal Contained Carbon Nano-Onions and Studies of Their Electrochemical Hydrogen Storage Properties. J. Energ. Chem. 23 (3), 324–330. doi:10.1016/S2095-4956(14)60154-6
Zhang, C., Li, J., Shi, C., Liu, E., Du, X., Feng, W., et al. (2011). The Efficient Synthesis of Carbon Nano-Onions Using Chemical Vapor Deposition on an Unsupported Ni-Fe alloy Catalyst. Carbon 49 (4), 1151–1158. doi:10.1016/j.carbon.2010.11.030
Zhang, C., Wang, X., and Huang, H. (2008). π-Stacked Interactions in Explosive Crystals: Buffers against External Mechanical Stimuli. J. Am. Chem. Soc. 130 (26), 8359–8365. doi:10.1021/ja800712e
Zhang, J., Mitchell, L. A., Parrish, D. A., and Shreeve, J. N. M. (2015). Enforced Layer-By-Layer Stacking of Energetic Salts towards High-Performance Insensitive Energetic Materials. J. Am. Chem. Soc. 137 (33), 10532–10535. doi:10.1021/jacs.5b07852
Zhang, Y., Wang, Y., Lü, J. T., Brandbyge, M., and Berndt, R. (2017). Mechanochemistry Induced Using Force Exerted by a Functionalized Microscope Tip. Angew. Chem. Int. Ed. Engl. 56, 11769–11773. doi:10.1002/anie.201704940
Zhang, Z., Yao, P., Li, X., Wang, J., Huang, C., Zhu, H., et al. (2020). Grinding Performance and Tribological Behavior in Solid Lubricant Assisted Grinding of Glass-Ceramics. J. Manufacturing Process. 51, 31–43. doi:10.1016/j.jmapro.2020.01.020
Zhou, X., Miao, Y., Suslick, K. S., and Dlott, D. D. (2020). Mechanochemistry of Metal-Organic Frameworks under Pressure and Shock. Acc. Chem. Res. 53 (12), 2806–2815. doi:10.1021/acs.accounts.0c00396
Keywords: mechanochemistry, tribochemistry, mechanical alloying, tribology, mechanical activation, nomenclature, mechanochemical pictographs
Citation: Michalchuk AAL, Boldyreva EV, Belenguer AM, Emmerling F and Boldyrev VV (2021) Tribochemistry, Mechanical Alloying, Mechanochemistry: What is in a Name?. Front. Chem. 9:685789. doi: 10.3389/fchem.2021.685789
Received: 25 March 2021; Accepted: 03 May 2021;
Published: 26 May 2021.
Edited by:
Lev S. Rapoport, Holon Institute of Technology, IsraelReviewed by:
Kenneth John MacKenzie, MacDiarmid Institute for Advanced Materials and Nanotechnology, New ZealandCopyright © 2021 Michalchuk, Boldyreva, Belenguer, Emmerling and Boldyrev. This is an open-access article distributed under the terms of the Creative Commons Attribution License (CC BY). The use, distribution or reproduction in other forums is permitted, provided the original author(s) and the copyright owner(s) are credited and that the original publication in this journal is cited, in accordance with accepted academic practice. No use, distribution or reproduction is permitted which does not comply with these terms.
*Correspondence: Elena V. Boldyreva, ZWJvbGR5cmV2YUB5YWhvby5jb20=, ZWJvbGR5cmV2YUBjYXRhbHlzaXMucnU=; Adam A. L. Michalchuk, YWRhbS5taWNoYWxjaHVrQGJhbS5kZQ==
Disclaimer: All claims expressed in this article are solely those of the authors and do not necessarily represent those of their affiliated organizations, or those of the publisher, the editors and the reviewers. Any product that may be evaluated in this article or claim that may be made by its manufacturer is not guaranteed or endorsed by the publisher.
Research integrity at Frontiers
Learn more about the work of our research integrity team to safeguard the quality of each article we publish.