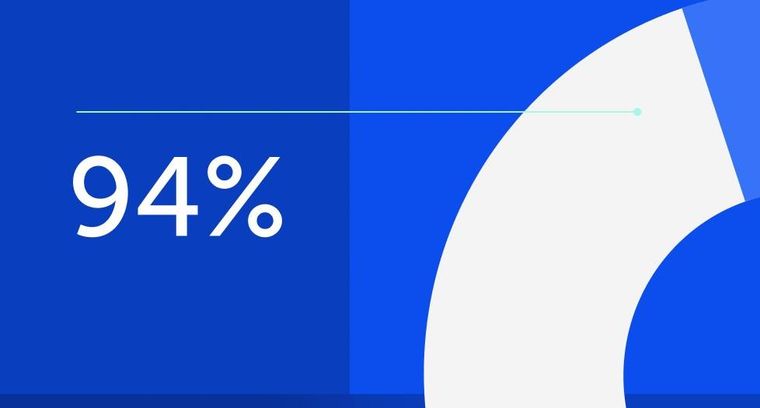
94% of researchers rate our articles as excellent or good
Learn more about the work of our research integrity team to safeguard the quality of each article we publish.
Find out more
REVIEW article
Front. Chem., 17 December 2020
Sec. Nanoscience
Volume 8 - 2020 | https://doi.org/10.3389/fchem.2020.601256
This article is part of the Research TopicMicrobial Fabrication of Nanomaterials and Their ApplicationsView all 9 articles
Nanocellulose is a unique and natural compound extracted from native cellulose using different extraction techniques. Nanocellulose is currently attracting attention due to its excellent properties such as special surface chemistry, exceptional physical and chemical strength, and rich hydroxyl groups for modification. In addition, its significant biological properties, like biodegradability, biocompatibility, and non-toxicity, accompanied by being environmentally friendly, are added advantages. The current review is focused on the lignocellulosic biomass processing methods for nanocellulose production and their usage for eco-friendly and environmental sustainability. We have also described insights into different techniques by which cellulosic materials can be changed into cellulose nanofibers (CNFs) and cellulose nanocrystals (CNCs). Lastly, we further discussed how nano-cellulosic materials are being used in a variety of industries such as the food sector, biomedical hygiene products, health care, water purification, and sensors. In the review, the unique uses of nanocelluloses in the production of nanocomposite materials, like flexible supercapacitor and polymer matrix, toward minimizing the utilization of global fossil energy and environmental pollution are envisaged. Finally, the significant application of nanomaterials in the areas of packaging industries, health and hygienic sector, cosmetics, and other important sectors are discussed. In the aspect of techno-economically feasibility, nano-cellulose-based materials may prove to be outstanding, environment friendly, and mitigate effluent load.
Environmental concerns are growing due to petroleum product usage. Hence, the production of superfine nanoscale efficient compounds from native cellulose is gathering more attention (Thakur and Voicu, 2016). Nanocellulose is a unique and promising natural compound derived from ordinary biomass. It is currently the most environmentally friendly compound that is techno-feasible and cost-effective, and also reduces effluent production (Kalia et al., 2011). Nanocellulose has retained significant attention due to its tremendous functionality i.e., greater surface chemistry, extraordinary biotic possessions, low toxicity, low in cost, lower density, and significant mechanical properties. The quick growth of green and nano-technological sustainability is related to the improvement of different resources and uses (Voicu et al., 2016). For 150 years, cellulose has been regarded as a renewable and biodegradable polymer, which has been used as an energy source and for various value-added products (Park et al., 2019). Previously, many researchers have been innovating bio-based compounds for the reduction of vestige fuel dependency (Mugaanire et al., 2019). Most of the cellulosic materials are utilized by many industries such as fabric, pulp mill, and reagent manufacturing sectors (Farooq et al., 2019). Recently, numerous investigators have been discovering efficient NC resources by using significant waste managing system (Lavoine et al., 2012).
In the global market, the business of fiber and its products is expected to achieve about USD 1.08 billion by 2020 and to continue to increase in value. Therefore, many resources are used for the production of cellulose and nanocellulose products. Among them, agro-waste residues are the most sustainable sources of cellulosic biomass, so various efforts have been prepared to mine cellulosic fiber from waste residues like fruits waste, marine biomass, and wheat straw (Yang et al., 2017). Nanocellulose has been used as filler in various applications and it enhances the physical strength of materials and barrier properties of carboxymethyl cellulose (CMC), chitosan, alginate, and biopolymeric films. Similarly, another study reported that nanocellulose is used in enzyme immobilization, automotive and electric appliances, and sensor devices (Farshchi et al., 2019). Various techniques, such as hydrolysis and physical and biological pretreatment methods, have been used for the production of cellulose fibers. These fibers convert/disintegrate into a crystalline, rod-shaped, and nano-sized units, such as much as micrometers, called Cellulose Nano-Crystal (CNC). However, the nano-sized compound can be produced using a microbial approach called bacterial nanocellulose (BNC) (Wijaya et al., 2019). Numerous studies have reported on Cellulose Nano-Fibril and CNC extraction from different types of sources such as bamboo, cotton, sugar beet, banana rachis, and agricultural waste, including hardwood and softwood (Haldar and Purkait, 2020a). Another report revealed that the powder form of Australian native “spinifex” grass (Triodia pungens) has been processed with an ultra-high pressure homogenization technique for the withdrawal of CNF (Amiralian et al., 2015). Habibi and coworkers in 2010 found that nanoparticles were extracted from the cotton, which has a dimension of 70–300 nm in length and 5–11 nm in width (Habibi et al., 2010). Similarly, Kang et al. reported that corncob wastage of ball milling was used as sources for CNF production through a step mechano-chemical esterification process (Kang et al., 2017). Additionally, Pandey and colleagues in 2015 revealed that the production of CNF through newspaper waste has a significant impact on the ecosystem and is economically important (Pandey et al., 2012). BNC has been extracted by using a bacterial submerged fermentation process. It can be used with several culture mediums, such as carbon source (glucose, agricultural waste, and fructose), nitrogen source (peptone yeast extract), and saccharified food waste. Typically, microorganisms like Gluconacetobacter hansenii, G. xylinus, and Acetobactor sp. are used for the fermentation process. Generally, after the bacterial treatment of cellulose, acid hydrolysis was employed to mine the BNC. However, expected and accurate proportions of BNC depends upon various optimized parameters (Haldar and Purkait, 2020b). Hence, the BNC production rate usually varies between 0.01 and 0.31 g L−1 h−1 (Reiniati et al., 2017). All three nano-celluloses (CNF, CNC, and BNC) have similarities, such as containing a native cellulose I crystal structure, having a great molecular weight, most polymerization properties, and having a significant ultrafine structure that is capable of holding them in water (Castro et al., 2011). Cellulose pretreatment can be done through several methods, like alkaline-acid pretreatment, enzymatic pretreatment, and ionic pretreatment, to remove the unwanted materials and enhance the nano-cellulosic properties. In the alkaline-acid treatment methods, the lignocellulosic compound is processed via alkali chemicals (Gupta et al., 2020a). These methods cause fibrillation and modified the surface properties of native fibers which way-out the hemicellulose, lignin, and waxes (Phanthong et al., 2018). After the chemical and biological purification of native lignin-cellulosic materials, the next methods are the transformation of refined cellulosic component nanosized particles (CNC, CNF, and BNC) through various methods, especially acid hydrolysis and physical treatments (Trache et al., 2016). Characteristics of various nanocellulose derived from lignocellulosic biomass and their applications have been described in Table 1. Various physical processes, like high-pressure homogenizers, microfluidization, cryo-crushing, and high-intensity ultrasonic treatments, are used to convert cellulose fibers into nanofiber materials (Ferrer et al., 2012). Nanocellulose materials are used in the production of bio-components, packaging component, polymer matrix, and antimicrobial barrier or coating materials in the food industry, as well as in the pharmaceutical sectors and most advanced 3D-structural technologies (like tissue or cell culturing process and diagnostic kits). These nanocellulose has been used for the production of nanocomposite materials, like flexible supercapacitor and polymer matrix, as they minimize the utilization of global fossil energy and environmental pollution (Abitbol et al., 2016). The current review focused on the lignocellulosic biomass processing methods for nanocellulose production and their eco-friendly and environmentally sustainable usage.
Table 1. Functional characteristics of various nanocelluloses derived from lignocellulosic biomass and their applications.
Bengt Rånby first described the nanocellulose material as cellulose bundles generating micelles in water solution in 1951 (Chen et al., 2018). Nanocellulose material can be extracted from woody biomass through conventional techniques, releasing the lignin and hemicellulose residues then converting the purified cellulose content into the nanoscale materials (Kargarzadeh et al., 2018). The term “nanocellulose” is roughly categorized into three different varieties: cellulose nanofibers (CNF), cellulose nanocrystals (CNC), and bacterial nanocellulose (BNC). These vary upon their sizes and functionality (Abitbol et al., 2016).
The extraction of cellulose nanofibrils (CNFs) from wood pulp biomass is often done using the TEMPO-mediated oxidation method. Its nanoscale is about 5–60 nm in diameter and many microns in length (Habibi et al., 2010). CNF consists of cellulosic domains i.e., crystalline and amorphous domains. Generally, several resources of native biomass, such as corn husk, rice straw, soft and hardwoods, and banana can be used for obtaining NCF (Farooq et al., 2020). In recent years, there has been only a low level of interest in the commercialization of CNF due to its high-cost production process. But recently, various chemical and enzymatic methods have been introduced for the production of CNF due to cost effective processes (Suopajärvi et al., 2017). The chemical methods, such as 2,2,6,6-tetramethylpiperidine-1-oxyl radical (TEMPO), periodate, and carboxymethylation, are the most used methods for the obtaining of NCF. The endoglucanase enzyme is used for enzymatic pretreatments of cellulosic content and the yielding of CNF materials (Barbash et al., 2017).
CNC is needle-shaped and highly crystalline and produced from cellulose pulp by acid hydrolysis process; through this process amorphous fibrils are dissolved to maintain the crystallinity. These materials contain cellulose moieties which are termed as cellulose nanowhiskers and microcrystalline (Clemons, 2016). The dimension of the yielded CNC is 5 nm in diameter and 20–100 nm in length. Similarly, another study reported that the average dimension obtained was 3–35 nm in diameter and 100–1000 nm in length (Nechyporchuk et al., 2016). Therefore, the NC structure varies depending on cellulosic biomass types and processing methods (Campano et al., 2016). According to Liu in 2014, CNC consists of highly strong material-like structures, such as Young's modulus, which is related to Kevlar material and used in the making of highly robust and tough materials (Liu et al., 2014). For commercialization purposes, many sectors started production and commercialization of CNC due to its tremendous properties. In India, the Indian Council of Agriculture Research produces about 10 kg/day of nanocellulose and commercialized their products in the market (Kumar et al., 2020).
BNC are ribbon-shaped fibers with a usual size of 20–100 nm and are many micrometers in length (Jonoobi et al., 2015). BNC contains fibers with high crystallinity and high polymerization properties. BNC can be obtained through various bacterial strains like Gluconacetobacter xylinus, Aerobacter, Escherichia, Sarcina, and Komagataeibacter. Among these, Gluconacetobacter xylinus is the most widely used strain for the obtaining of BNC nanocellulose. BNC is secreted as an extracellular product from the bacterial fermentation process. Purification of BNC from cellulosic content occurs by the washing of bacterial cellulosic products using 1 M NaOH (Römling and Galperin, 2015). The elemental structure of BNC is quite similar to the high transparency level in comparison to plant-based biomass cellulose. The advantage of BNC is that it does not have unwanted polymers, unlike plant origin cellulose. BNC production from various microorganisms and their biomedical applications are given in Table 2. BNC materials have gathered the most interest in the biomedical field due to their tremendous activity in their nano-cellulosic materials (Jozala et al., 2016).
Nanocellulose can also be obtained from cellulose fibers through several treatment methods (e.g., traditional treatment and enzymatic treatment) of lignocellulosic biomass. The production of nanocellulose is attained by a two-step process. In the first step, the pretreatment process of native cellulose biomass is done which yields treated cellulose fibers. While in the second step, pretreated cellulose fibers are converted into nanocellulose using various routes e.g., high-pressure homogenization, micro fluidization, micro grinding, high-intensity ultra-sonication, electrospinning, and steam explosion. The schematic representation of nanocellulose production is given in Figure 1.
Agro-residue has gained attention as a resource for nanocellulose production. The uses of these waste products are not only based on their availability but also on the conversion of the valuable and high profitable product (nanocellulose) from the non-valuable waste (dos Santos et al., 2013). Moreover, the significant use of agro-waste is good for the ecosystem. As described above, lignocellulosic biomass is high in cellulose and undesired compounds, such as hemicellulose and lignin (Johar et al., 2012; Gupta et al., 2020b). The pretreatment process can be done before the extraction of nanocellulosic materials. To remove the ashes, waxes, and undesired polymers (i.e., hemicelluloses, lignin) and enhance the quality of cellulose, pretreatment process are needed (Gupta et al., 2020c). Also, the pretreatment process improved the fibrillation as well as the conversion of the cellulose fiber into micro/nanofibrils. However, the machine-driven process is a costly procedure due to its high energy consumption during the treatment process (Visanko et al., 2014). The pretreatment process also reduces the energy (from 20, 000 to 30, 000 kWh/ton to 1,000 kWh/ton) needed for the production of nanocellulose. There are several treatment processes, such as alkaline hydrolysis, acid hydrolysis, organosolvent treatment, ionic liquid treatment, and enzymatic treatment, that can be done for nanocellulose production. In the pulp and paper industry, acid-chlorite treatment or bleaching process is mostly used for biomass treatment (Hubbell and Ragauskas, 2010). Hubbell and coworker reported that it can remove most of the organic compounds through the combinatory effect of water and chlorite at optimized values, such as 70–80°C for 4–12 h. After that, the treated cellulose kept over a period minimizes the pH value till an ambient pH level is reached and then the cellulose is dried. Finally, the solid yields are termed as holocellulose (Li et al., 2012). The alkaline treatment, meanwhile, can be done for the removal of the amorphous polymer of an organic compound. These holocellulosic materials were treated with an alkaline chemical, i.e., sodium hydroxide, for a period of 1–5 h, treated with water until ambient pH level is reached, and dried (Abraham et al., 2013). Microbial processing is used for the alteration of cellulose biomass by degrading hemicellulose and lignin components. Various biocatalysts, such as endoglucanase, cellobiohydrolase, and hemicellulose, have been employed for the alteration of cellulose. In the biological method, a biocatalyst acts in either a restrictive hydrolysis process or a specific hydrolysis process of fiber components (Wahlström and Suurnäkki, 2015). The retention time for the enzymatic pretreatment needs to be much higher than in chemical pretreatment. Many researchers have reported that enzyme hydrolysis in combination with the homogenization of softwood cellulose resulted in nanocellulose with a greater aspect ratio that is less aggressive than the acidic treatment (Phanthong et al., 2018). Another study reported that microorganisms prepare cellulose naturally by using simple sugar molecules. Hence, the bioconversion of carbohydrates into cellulose is a multifaceted step and depends on several biocatalysts. Sometimes mutation can occur in the microbes and enhances the thickness of processing media, which is a demerit of this process (Chen et al., 2018). Researchers have studied and reported that a significant quality of cellulose is achieved on carbon sources i.e., glucose, mannitol, and fructose sugars (Islam et al., 2017). Besides traditional pretreatment, enzymes cellulose was found to be an eco-friendly process. Many researchers report that the synergistic effect of enzymes shows an excellent effect on the surface modification of cellulose biomass. Cellulases A and B, such as cellobiohydrolases, act on crystalline cellulose, whereas C- and D-type, i.e., endoglucanases, act on the amorphous cellulose. Cellobiohydrolase I and II are derived from Trichoderma reesei, which combine with cellulose-degrading catalyst and have high polymerization properties (Yarbrough et al., 2017). The BNC are also produced from the fruit and vegetable peels by the action of certain bacterial cells. In this process, vegetable peels are hydrolyzed by the acid hydrolysis and then by the bacterial cell for BNC production. Acid hydrolysis is performed at 10 mL/g liquid/solid ratio with 0.6 M H2SO4 for 2 h at 100°C using K. hansenii GA2016 microorganism. The highest BNC is produced from the kiwifruit and has the highest water holding capacity compared to other BNC (Güzel and Akpinar, 2020). Therefore, vegetable nanocellulose must first be chemically isolated using sequential reagent processing with alkaline solutions at various doses. After the chemical treatment, a physical process must be carried out which would breakdown the cellulose and provide 5–20nm sized nanocellulose (Klemm et al., 2011). The most preferred mechanical process are high pressure homogenization, microfluidizer, waring blender, and grinder (Uetani and Yano, 2011).
Various technologies have been discovered for the isolation of nanocellulose from pretreated cellulose. In these scenarios, the isolation methods are mainly focused on three categories: mechanical extraction, enzymatic hydrolysis, and acid hydrolysis (Anwar et al., 2014). Among these, acid hydrolysis is most widely used for the extraction of nanocellulose from biomass fibers. It is easily hydrolyzed into the disordered regions of cellulose. In this process, sulfuric acid is widely employed for the acid hydrolysis. The mode of action of acid hydrolysis is dispersal of the nanocellulose via sulfate ions during the esterification process (Morais et al., 2013). A major demerit of acid hydrolysis is the generation of water waste during the wash away process of pretreated nanocellulose. TEMPO oxidized cellulose nanofibers consist even with a high aspect ratio and have a broad range of applications, including a gas-barrier film for packaging and nanofiber filling for composite materials (Fukuzumi et al., 2009). Biological hydrolysis can be done using cellulose-digesting enzymes. Generally, a high reaction time is needed during the enzymatic hydrolysis process. However, to overcome this problem a combination of enzymatic and other methods are employed for the digestion and extraction of nanocellulose (Khalil et al., 2014). Moniruzzaman and Ono in 2013 found that the cellulose separated from wood biomass with ionic pretreatment, which enhanced the available exterior zone and then causes bio-catalytic activity to take place. The NC produced by this method has significant crystallinity and high stability as compared to ordinary fibers (Moniruzzaman and Ono, 2013). Many researchers in the 21st century are focused on the factors' optimization for BNC extraction to obtain a significant quality of BNC using traditional media, consisting of sugars at static or agitated operations (Sharma and Bhardwaj, 2019). The novel substrates (often rich in sugars) like sugarcane scum, pineapple waste, and coconut water instead of traditional sugar source can be used for BNC production. The microorganisms, especially bacterial genera like Acetobacter, Bacillus, Sarcina, Rhizobium, Enterobacter, and Klebsiella, are recognized for BNC production. However, gram-negative bacteria such as Gluconacetobacter xylinus, formerly known as Acetobacter xylinum, are the most common bacteria reported for the BNC production (Siró and Plackett, 2010). The extracted cellulose from the Gluconacetobacter xylinus has similar characteristic features to plant cellulose, which is observed using X-ray diffraction technique. The nanocellulose produced from the Gluconacetobacter xylinus have β-1,4-glucan chains and a twisted and ribbon-like structure in the environment. The purity of formed cellulose can be estimated using the cellulose solubility test method. In this method, cupriethylenediamine and sodium hydroxide are used, and complete solubility of cellulose indicates purity level. Therefore, batch and fed-batch methods are used for the static production of BNC through bioreactors. The BNC extraction is directly subjected by its extraction techniques and factors involved during the production process (Gama et al., 2016). BNC production at a commercial scale might be achieved through advanced bioreactor methods. According to Kralisch et al. in 2010, BNC foils were produced with desirable lengths and thicknesses using a horizontal lift reactor at static condition (Kralisch et al., 2010). Recently, Dudey and co-workers used static intermittent fed batch technology for BNC production and reported that they obtained 38 g/l BNC using Komagataeibacter europaeus SGP37 strain in sweet lime pulp waste medium (Dubey et al., 2018). Another type of bioreactor, rotatory biofilm contactor (RBC), was used by Kim et al. in 2007 who reported 5.52 g/l BNC production while using Gluconacetobacter sp. (Kim et al., 2007). Most researchers used substrate-based strategies for BNC production using several microorganisms. However, Son and colleagues in 2001 revealed that, using Acetobactor sp. A9, BNC production improved 4-fold while using ethanol addition as supplemented agents (Son et al., 2001). Kim et al. concluded that the addition of agar in the production media increased the BNC productivity (Kim et al., 2012).
Due to outstanding functionality and being ecologically friendly, nanocellulose is used in many fields such as nanocomposite materials, surface modified materials, and transparent paper with distinct properties. We discussed how nanocellulosic materials are utilized in a variety of sectors such as the nourishment sector, biomedical products, health care, water purification, and sensors. An overview of various applications of extracted nanocellulose is depicted in Figure 2. These nanocellulose have been used for the production of nanocomposite materials like flexible supercapacitor and polymer matrix; they also minimize the utilization of global fossil energy and environmental pollution.
Nanocellulose paper has tremendous physical capacities (transparent, optically clear, and foldable) and is used in electronic appliances, energy capacitors, harvesting devices, and as flexible composite materials (Salas et al., 2014). Nogi et al. in 2009 stated that transparent nanocellulose paper was fabricated from timber powder, and reveal its optically active, excellent physical strength and high modulus (13GPa) (Nogi et al., 2009). Weng and coworkers used simple fabricated graphene-cellulose paper (GCP) membranes as electrodes in the flexible supercapacitors. They found it has the greatest stability of electrical conductivity with only a 6% reduction after being bent 1,000 times (Weng et al., 2011). Similarly, Cui and team reported that the commercial paper sheets utilized in the fabrication of supercapacitors and lithium-ion batteries were coated with carbon nanotube (CNT) ink with the help of sodium dodecylbenzene sulfonate (SDBS) as a surfactant (Jose et al., 2019). Cui's group reported that CNF-based organic solar cells have a power conversion efficiency (PCE) of 0.4%. However, the highest observed PCE of CNF-based solar film was about 4% (Hu et al., 2013).
BNC is considered to be the most unique and cost-efficient natural nanomaterial for health sectors. It has extraordinary applications, such as scaffolds fabrication, wound-dressing, drug delivery applications, diagnostic and biosensors, and the most advanced tissue and cell engineering techniques. There are many biomedical applications of nanocellulose-based materials, most of which are highlighted here.
Nanocellulose that are non-hazardous, renewable, and have significant compatibility excellent durability are often used in pharmaceutical sectors. Hakkarainen and coworker in 2016 extracted nano fibrillated cellulose from bleached birch pulp and used it as wound-dressing and also reported that it has an ecofriendly use with graft systems (Hakkarainen et al., 2016). These dressing materials can be fitted with a wound and simply removed by a patient once the wound has healed (Abitbol et al., 2016). Along with this, cellulose modification is enhanced by cell attachment. For this purpose, in various ways, such as the plasma treatment process, the protein coating process can be done. There are many nanocellulose-based antimicrobial composites, such as silver nanoparticles and lysozyme adopted with special effects. According to Fontana et al. in 1990, BNC-based “BioFill®” material is reported as the most anticipated wound dressing biomaterial in the biomedical field (Fontana et al., 1990). The BNC obtained dressing agents, like Bioprocess, XCell, and Gengiflex®, are commercially found for the treatment of periodontal disease reconstruction applications (Sharma and Bhardwaj, 2019). Similarly, BWD, XCell®, and Xylos formed from biocellulose can be applied for chronic venous leg ulcers (Alvarez et al., 2004).
Nanocellulose is also applied in medical fields as bold vessel replacements, implants of soft tissues, and drug delivery to targeted cells (Jorfi and Foster, 2015). Nowadays, the use of nanocellulose in the drug delivery system has been adopted to monitor the systems. The hydrogel-based nanocellulose has been used as a drug carrier molecule, as it produced the stability of drugs (Gupta et al., 2019). Most of the researchers reported that the BNC-based carrier molecules can be used for the delivery of berberine hydrochloride and berberine sulfate drug delivery system (Huang et al., 2013). Similarly, tetracycline hydrochloride was blended with BNC composite material to be employed for drug delivery in skin dressing applications (Shao et al., 2016). However, the BNC- caffeine material was exploited for both solution and forms of the topical drug delivery application. Similar experiments on BNC-glycerin were conducted by many researchers who concluded the same topical drug delivery application (Silva et al., 2014). But an adverse effect (skin irritating problem) of BNC was found in human beings. Recently, BNC has acted as a biocarrier of 1,3-Dihydroxy-2-Propanone (DHA) for curing vitiligo. The BNC is the most promising biomaterial for the drug delivery system due to its ultrafine 3D nanostructure. Various studies reported that BNC can be responsible for delivering drugs, antibodies, and enzymes to their targeted sites (Abeer et al., 2014).
BNC is noted as a unique scaffold component due to its tremendous characteristics. It can be divided into three scaffolds: BNC membrane scaffolds, BNC bio-composite matrix, and BNC pellicle scaffolds (Lin et al., 2014). BNC-based novel small caliber vascular prosthesis was invented by many researchers (Leitão et al., 2013). The BNC-gelatin materials can be used for the attachment of fibroblast cells. Using polymeric P(3HB-co-4HB) as a matrix, BNC bio-composite scaffold was formed with the help of the freeze-drying method and used for Chinese hamster lung fibroblast cells adhesion (Zhijiang et al., 2012). Another study reported that, BNC has significant efficiency in bone tissue engineering technology. The nanocellulose-based hydrogels have been effective with mesenchymal stem cells (MSC) for 3D culturing. The maintained rates of MSCs cell viability on the cellulose matrix are nearly 90% and have high distribution properties across the gel (Azoidis et al., 2017). Similarly, engineered tissues also required an ECM system for 3D bio-printing. Recently, hydrogels derived from NC have been discovered and employed as scaffolds in the 3D biological system. The BNC tube fabrication was achieved through the use of a polydimethylsiloxane template, which has been applied as artificial blood tubes with improved mechanical strength, huge temperature stability, and compliance concerning in vivo surroundings (Zang et al., 2015).
Diagnostic kits and biosensors are employed for the detection and diagnosis of diseases in clinical experiments. Nowadays, various biosensors have been developed for different applications in biomedical fields. Generally, receptors, antibodies, antigens, and enzymes have been used as active factors for clinical evaluation (Sharma and Bhardwaj, 2019). However, using thiosalicylic acid and 2,2-dithiodipyridine as analytes, BNC-silver nanocomposite matrix has been applied for the biological analysis of surface enhanced Raman scattering (SERS) lamellas (Marques et al., 2008). Similarlythe advanced BNC-Au nanomaterials have been used for the detection of glucose compounds in the human blood serum. Currently, high performance artificial tongues were developed with the help of BNC nano-paper as source (Abbasi-Moayed et al., 2018). These nanopaper-based tongues have advanced biochemical disparity and can be used for the optical sensor array application. Thus, BNC-filtered carbon nanotube composites were developed for the immobilization of electrons within glucose and glucose oxidase (Kim et al., 2013). Additionally, BNC produced from Komagataeibacter sucrofermentans was altered with perchloric acid stabilized magnetic fluid and was applied as a transporter for the immobilization of cells, ligands, and enzymes in biomedical fields (Baldikova et al., 2017).
Nanocomposite materials obtained from nanocellulose consist of a few superior assets, such as high durability and wide-range stability while being low in weight (Abitbol et al., 2016). These nanocomposite materials have been applied in many fields, such as the blades of windmills, lightweight armor, and flexible energy capacitor. Robles et al. in 2016, used nanocomposite materials obtained from PLA and nanocellulose, and concluded that nanocellulose improved the contact between matrix fillers with thermal capability and enhanced crystallinity (Robles et al., 2015). Similarly, Ardanuy et al. reported on a sisal fiber cement composite produced by the CNF and sisal fibers and found 40% enhanced flexural strength as compared to ordinary cement composite (Ardanuy et al., 2012). The introduction of filler in the polymeric material improved the physical and thermal properties of the composite material, as compared to polymeric material alone (Xu et al., 2016).
Various studies have been performed in the last few decades on the uses of nanocellulose in the oil drilling industry. The researchers Saboori et al. and Fereydouni et al. in 2012 found that the nano-scaled carboxymethyl cellulose (CMC) and polyanionic cellulose when used as fluid loss additives (Fereydouni et al., 2012; Saboori et al., 2012). The amphiphobic nanocellulose modified paper was fabricated by Phanthong et al. (2016). For this process, filter paper was coated by nanocellulose and then reacted with trichloro (1H,1H,2H,2H-tridecafluoro-noctyl) silane for deposition of vapor. This paper acted as a repellent to polar as well as non-polar liquids in the ecosystem due to its superhydrophobicity and oleophobicity properties. The biodegradable aerogels are produced from the nanocellulosic materials, consisting of high porosity and negativity charge with excellent adsorption capacity. Similarly, Li and coworkers studied the use of CNC as a rheology convertor. They reported that mud produced from nanocellulose and bentonite water have excellent rheological activity, high-temperature constancy, and low fluid loss (Li et al., 2015). Recently, nano-scale additives used in cement slurry formulation are considered for the enhancement of cement properties. With a high surface area, chemical reactions can be efficiently enhanced and significantly promote the degree of hydration (Ramasamy and Amanullah, 2020).
The high surface area, aspect ratio, rheological behavior, and non-cytotoxic and non-genotoxic properties of vegetable nanocellulose mean it is easy to use in the food sector. This nanocellulose has been widely used in three main applications: as a food stabilizing agent, as a vital food constituent, and as food packaging. It is used as a food packaging application worldwide (Serpa et al., 2016). Nanocellulose is used as a food stabilizing agent for a variety of foods like soy sauce and soup, retort food, dough-based food, and whipping cream by several Japanese companies, such as Daicel, Procter & Gamble, and Asahi Foods Co., Ltd (Winuprasith and Suphantharika, 2015). A recent patent was filed by Yano and co-workers in 2014 who reported that nanocellulose used as a food stabilizer means frozen dessert can retain their shape. Another study revealed that nanocellulose used as dietary fibers have a range of beneficial roles. It can be used in the reduction of risk of chronic diseases like diabetes and cardiacarrest. Additionally, it improved physiological effects, including laxation and blood sugar level (Andrade et al., 2015). Nanocellulose-based film has extraordinary properties of air and oxygen barriers, which protect the food from undesirable entities. The characteristics of nano-based films are similar to natural poly bags. The excellent oxygen tolerance capability of nano-film arises due to the high crystallinity of nanocellulose (Svagan et al., 2016).
Numerous studies on the estimating and fabrication of nanocellulose have been reported by several organizations and industries (Mhd Haniffa et al., 2016). The US Forest Service reported that nanocellulose could add $600billion to the US economy by 2020. A similar study reported that ~1 × 1012 tons of cellulose and its derivatives were produced annually, which accounts for 1.8 × 109 billion USD business by 2020 (Thomas et al., 2020). According to Gama et al. (2016), in the Philippines and Indonesia about 1,500 tons of BNC is produced and commercialized from the nata de coco farms (Gama et al., 2016). Various factors were involved to decrease the BNC production costs, like use of alternative sources, upgrading the scale up process, and the designing of bioreactors. However, the production cost remains a challenge. While in NFC, similar costs are absorbed on the pre-treatment process. The approximate cost of NFC processing from wood pulp is about 0.4 $/kg when using enzymatic pre-treatment approaches and is also reported as cheapest among the other process (Ålander et al., 2017). NFC produced by TEMPO-modified process has been reported as reducing the final processing cost. It has higher greenhouse gas emission during NFC production in comparison with other industries (Moon et al., 2017). Similarly, NCC shares the same expenditures with commercialization production via the sulphuric acid hydrolysis technique. During the NCC processing, a by-product is generated and can be used for bioenergy generation. However, the extra cost and energy are needed for the production of biofuel. Currently, various reports revealed that the cost-effective processes for NCC production are subcritical water processing, hot water pre-extraction, and oxidation techniques. Hence, the commercial price was estimated to be lowered by 18 $/kg for NCC production via using H2SO4 hydrolysis (Bian et al., 2017). According to NanoCrystalline Cellulose, 2019 report, Celluforce is reported as the highest NCC producing plants among commercial aspects, which has a production capacity of ~300 tons annually (NanoCrystalline Cellulose, 2019). Thus, it is challenging to analyze and predict the final cost of nanocellulose but it is estimated at between 7-12 USD/kg of final product (Thomas et al., 2020).
The presence of undesired organic materials, like lignin, hemicellulose, and its derivatives in the lignocellulosic biomass, present a challenge in the production of cellulose. The pre-treatment process is necessary for the removal of all these undesired organic compounds. Due to the time taken, toxic chemicals consumed, and discharged wastewater, the pretreatment process is a complex process. However, the conventional technologies have drawbacks like production of huge wastewater effluent, high energy demand, and long retention time for the production of nanocellulose using the acid hydrolysis process. Hence, enzymatic treatment has the efficient capability to extract out nanocellulose from the cellulosic biomass. Due to the current deand for flexible and sustainable energy devices, there has been a focus on ecological considerations in cellulose production. Certainly, challenges do exist and efficient research outputs are needed to overcome these issues to create innovative materials for sustainable applications. Consequently, more research and environmentally friendly processes are needed for the manufacture and alteration of nanocellulose as well as reaction activity. We presume that research on nanocellulose-based bio-decomposable polymers and porous nanocomposites will continue to grow. We must continue with the development of novel production processes of nanocellulose and its products. Furthermore, nanocellulose products are successfully and significantly expand them-self in upcoming nano-generation.
The main focus of this review was to consider the extraction and application processes of NC from biomass. Nanocellulose is a promising material due to its distinctive functionalities i.e., high strength, low density, transparent, large aspect ratio, etc. The biomass pretreatment is a vital step to remove undesired materials. The BNC is the most preferred choice for drug delivery and pharmaceutical applications. However, for rheological activity, composite and strength additive NFCs would be the superior choice. In the case of reinforcing agents in biomedical applications, NCC is the significant choice. The NC-based conductive materials have been widely applied in the area of energy devices, such as in supercapacitors, solar batteries, and solar plants. Thus, the various materials obtained from CNF, CNC, and BNC would draw interest from various sectors e.g., pharmaceutical, food processing, and antimicrobial activity. Overall, nanocelluloses have multiple uses that can resolve several challenges of modern society and also play a vital role in the future of material science.
GG wrote the first draft of the manuscript. The final draft was read and edited by PS. Both authors listed have made a substantial, direct and intellectual contribution to the work, and approved it for publication.
The authors declare that the research was conducted in the absence of any commercial or financial relationships that could be construed as a potential conflict of interest.
The infrastructural support from the Department of Science and Technology, New Delhi, Govt. of India, through the FIST grant (Grant No. 1196 SR/FST/LS-I/2017/4) and Department of Biotechnology, Government of India (Grant No. BT/PR27437/BCE/8/1433/2018) is duly acknowledged. The Junior Research Fellowship by DBT, Govt. of India to GG, is duly acknowledged.
Ålander, E., Lindgren, K., Johansson, M., and Gimåker, M. (2017). “Towards a more cost-efficient paper and board making using microfibrillated cellulose,” in 7th Nordic Wood Biorefinery Conference (Stockholm: RISE Bioekonomi), 49–54.
Abbasi-Moayed, S., Golmohammadi, H., and Hormozi-Nezhad, M. R. (2018). A nanopaper-based artificial tongue: a ratiometric fluorescent sensor array on bacterial nanocellulose for chemical discrimination applications. Nanoscale 10, 2492–2502. doi: 10.1039/C7NR05801B
Abeer, M. M., Mohd, A. M. C. I., and Martin, C. (2014). A review of bacterial cellulose-based drug delivery systems: their biochemistry, current approaches, and future prospects. J. Pharm. Pharmacol. 66, 1047–1061. doi: 10.1111/jphp.12234
Abitbol, T., Rivkin, A., Cao, Y., Nevo, Y., Abraham, E., Ben-Shalom, T., et al. (2016). Nanocellulose, a tiny fiber with huge applications. Curr. Opin. Biotechnol. 39, 76–88. doi: 10.1016/j.copbio.2016.01.002
Abraham, E., Deepa, B., Pothen, L. A., Cintil, J., Thomas, S., John, M. J., et al. (2013). Environmental friendly method for the extraction of coir fibre and isolation of nanofibre. Carbohydr. Polym. 92, 1477–1483. doi: 10.1016/j.carbpol.2012.10.056
Alvarez, O. M., Patel, M., Booker, J., and Markowitz, L. (2004). Effectiveness of a biocellulose wound dressing for the treatment of chronic venous leg ulcers: results of a single center randomized study involving 24 patients. Wounds 16, 224–233.
Amiralian, N., Annamalai, P. K., Memmott, P., Taran, E., Schmidt, S., and Martin, D. J. (2015). Easily deconstructed, high aspect ratio cellulose nanofibres from Triodia pungens; an abundant grass of Australia's arid zone. RSC Adv. 5, 32124–32132. doi: 10.1039/C5RA02936H
Andrade, D. R. M., Mendonça, M. H., Helm, C. V., Magalhães, W. L., de Muniz, G. I. B., and Kestur, S. G. (2015). Assessment of nano cellulose from peach palm residue as potential food additive: part II: preliminary studies. J. Food Sci. Tech. 52, 5641–5650. doi: 10.1007/s13197-014-1684-0
Anwar, Z., Gulfraz, M., and Irshad, M. (2014). Agro-industrial lignocellulosic biomass a key to unlock the future bio-energy: a brief review. J. Radiat. Res. Appl. Sci. 7, 163–173. doi: 10.1016/j.jrras.2014.02.003
Ardanuy, M., Claramunt, J., Arévalo, R., Parés, F., Aracri, E., and Vidal, T. (2012). Nanofibrillated cellulose (NFC) as potential reinforcement for high performance cement moretar composites. Bioresour. Technol. 7, 3883–3894.
Azoidis, I., Metcalfe, J., Reynolds, J., Keeton, S., Hakki, S. S., Sheard, J., et al. (2017). Threedimensional cell culture of human mesenchymal stem cells in nanofibrillar cellulose hydrogels. MRS Commun. 7, 458–465. doi: 10.1557/mrc.2017.59
Baldikova, E., Pospiskova, K., Ladakis, D., Kookos, I. K., Koutinas, A. A., Safarikova, M., et al. (2017). Magnetically modified bacterial cellulose: a promising carrier for immobilization of affinity ligands, enzymes, and cells. Mater. Sci. Eng. C 71, 214–221. doi: 10.1016/j.msec.2016.10.009
Barbash, V. A., Yaschenko, O. V., and Shniruk, O. M. (2017). Preparation and properties of nanocellulose from organosolv straw pulp. Nanosc. Res. Lett. 12:241. doi: 10.1186/s11671-017-2001-4
Bian, H., Chen, L., Wang, R., and Zhu, J. (2017). Green and low-cost production of thermally stable and carboxylated cellulose nanocrystals and nanofibrils using highly recyclable dicarboxylic acids. J. Vis. Exp. 119:e55079. doi: 10.3791/55079
Campano, C., Balea, A., Blanco, A., and Negro, C. (2016). Enhancement of the fermentation process and properties of bacterial cellulose: a review. Cellulose 23, 57–91. doi: 10.1007/s10570-015-0802-0
Castro, C., Zuluaga, R., Putaux, J. L., Caro, G., Mondragon, I., and Gañán, P. (2011). Structural characterization of bacterial cellulose produced by Gluconacetobacter swingsii sp. from Colombian agroindustrial wastes. Carbohydr. Polym. 84, 96–102. doi: 10.1016/j.carbpol.2010.10.072
Chen, W., Yu, H., Lee, S. Y., Wei, T., Li, J., and Fan, Z. (2018). Nanocellulose: a promising nanomaterial for advanced electrochemical energy storage. Chem. Soc. Rev. 47, 2837–2872. doi: 10.1039/C7CS00790F
Clemons, C. (2016). Nanocellulose in spun continuous fibers: a review and future outlook. J. Renew. Mater. 4, 327–339. doi: 10.7569/JRM.2016.634112
dos Santos, R. M., Neto, W. P. F., Silvério, H. A., Martins, D. F., Dantas, N. O., and Pasquini, D. (2013). Cellulose nanocrystals from pineapple leaf, a new approach for the reuse of this agro-waste. Ind. Crop Prod. 50, 707–714. doi: 10.1016/j.indcrop.2013.08.049
Dubey, S., Singh, J., and Singh, R. P. (2018). Biotransformation of sweet lime pulp waste into high-quality nanocellulose with an excellent productivity using Komagataeibacter europaeus SGP37 under static intermittent fed-batch cultivation. Bioresour. Technol. 247, 73–80. doi: 10.1016/j.biortech.2017.09.089
Farooq, A., Jiang, S., Farooq, A., Naeem, M. A., Ahmad, A., and Liu, L. (2019). Structure and properties of high quality natural cellulose nano fibrils from a novel material Ficus natalensis barkcloth. J. Ind. Text. 1–17. doi: 10.1177/1528083719887533
Farooq, A., Patoary, M. K., Zhang, M., Mussana, H., Li, M., Naeem, M. A., et al. (2020). Cellulose from sources to nanocellulose and an overview of synthesis and properties of nanocellulose/zinc oxide nanocomposite materials. Int. J. Biol. Macromol. 154, 1050–1073. doi: 10.1016/j.ijbiomac.2020.03.163
Farshchi, E., Pirsa, S., Roufegarinejad, L., Alizadeh, M., and Rezazad, M. (2019). Photocatalytic/biodegradable film based on carboxymethyl cellulose, modified by gelatin and TiO2-Ag nanoparticles. Carbohyd. Polym. 216, 189–196. doi: 10.1016/j.carbpol.2019.03.094
Fereydouni, M., Sabbaghi, S., Saboori, R., and Zeinali, S. (2012). Effect of polyanionic cellulose polymer nanoparticles on rheological properties of drilling mud. J. Nanosci. Nanotechnol. 8, 171–174.
Ferrer, A., Filpponen, I., Rodríguez, A., Laine, J., and Rojas, O. J. (2012). Valorization of residual Empty Palm Fruit Bunch Fibers (EPFBF) by microfluidization: production of nanofibrillated cellulose and EPFBF nanopaper. Bioresour. Technol. 125, 249–255. doi: 10.1016/j.biortech.2012.08.108
Fontana, J. D., De Souza, A. M., Fontana, C. K., Torriani, I. L., Moreschi, J. C., Gallotti, B. J., et al. (1990). Acetobacter cellulose pellicle as a temporary skin substitute. Appl. Biochem. Biotechnol. 24, 253–264. doi: 10.1007/BF02920250
Fukuzumi, H., Saito, T., Kumamoto, Y., Iwata, T., and Isogai, A. (2009). Transparent and high gas barrier films of cellulose nanofibers prepared by TEMPO-mediated oxidation. Biomacromolecules 10, 162–165. doi: 10.1021/bm801065u
Gama, M., Dourado, F., and Bielecki, S., (eds.). (2016). Bacterial Nanocellulose: From Biotechnology to Bio-Economy. Amsterdam: Elsevier
Gupta, G. K., Kapoor, R. K., and Shukla, P. (2020b). “Advanced techniques for enzymatic and chemical bleaching for pulp and paper industries,” in Microbial Enzymes and Biotechniques, ed P. Shukla (Singapore: Springer), 43–56. doi: 10.1007/978-981-15-6895-4_3
Gupta, G. K., Mandeep, Liu, H., and Shukla, P. (2019). Pulp and paper industry–based pollutants, their health hazards and environmental risks. Curr. Opin. Environ. Sci. Health 12, 48–56. doi: 10.1016/j.coesh.2019.09.010
Gupta, G. K., Mandeep, and Shukla, P. (2020a). Insights into the resources generation from pulp and paper industry wastes: challenges, perspectives, and innovations. Bioresour. Technol. 297:122496. doi: 10.1016/j.biortech.2019.122496
Gupta, G. K., Mandeep, and Shukla, P. (2020c). “Enzyme engineering techniques for biotechnological applications,” in Microbial Enzymes and Biotechniques, ed P. Shukla (Singapore: Springer), 235–249. doi: 10.1007/978-981-15-6895-4_12
Güzel, M., and Akpinar, Ö. (2020). Preparation and characterization of bacterial cellulose produced from fruit and vegetable peels by Komagataeibacter hansenii GA2016. Int. J. Biol. Macromol. 162, 1597–1604. doi: 10.1016/j.ijbiomac.2020.08.049
Habibi, Y., Lucia, L. A., and Rojas, O. J. (2010). Cellulose nanocrystals: chemistry, self-assembly, and applications. Chem. Rev. 110, 3479–3500. doi: 10.1021/cr900339w
Hakkarainen, T., Koivuniemi, R., Kosonen, M., Escobedo-Lucea, C., SanzGarcia, A., Vuola, J., et al. (2016). Nanofibrillar cellulose wound dressing in skin graft donor site treatment. J. Control. Release 244, 292–301. doi: 10.1016/j.jconrel.2016.07.053
Haldar, D., and Purkait, M. K. (2020a). Lignocellulosic conversion into value-added products: a review. Process Biochem. 89, 110–133. doi: 10.1016/j.procbio.2019.10.001
Haldar, D., and Purkait, M. K. (2020b). Micro and nanocrystalline cellulose derivatives of lignocellulosic biomass: a review on synthesis, applications, and advancements. Carbohydr. Polym. 250:116937. doi: 10.1016/j.carbpol.2020.116937
Hu, L., Zheng, G., Yao, J., Liu, N., Weil, B., Eskilsson, M., et al. (2013). Transparent and conductive paper from nanocellulose fibers. Energy Environ. Sci. 6, 513–518. doi: 10.1039/C2EE23635D
Huang, L., Chen, X., Nguyen, T. X., Tang, H., Zhang, L., and Yang, G. (2013). Nano-cellulose 3D-networks as controlled-release drug carriers. J. Mater. Chem. B 1, 2976–2984. doi: 10.1039/c3tb20149j
Hubbell, C. A., and Ragauskas, A. J. (2010). Effect of acid-chlorite delignification on cellulose degree of polymerization. Bioresour. Technol. 101, 7410–7415. doi: 10.1016/j.biortech.2010.04.029
Islam, M. U., Ullah, M. W., Khan, S., Shah, N., and Park, J. K. (2017). Strategies for costeffective and enhanced production of bacterial cellulose. Int. J. Biol. Macromol. 102, 1166–1173. doi: 10.1016/j.ijbiomac.2017.04.110
Johar, N., Ahmad, I., and Dufresne, A. (2012). Extraction, preparation, and characterization of cellulose fibres and nanocrystals from rice husk. Ind. Crop Prod. 37, 93–99. doi: 10.1016/j.indcrop.2011.12.016
Jonoobi, M., Oladi, R., Davoudpour, Y., Oksman, K., Dufresne, A., Hamzeh, Y., et al. (2015). Different preparation methods and properties of nanostructured cellulose from various natural resources and residues: a review. Cellulose 22, 935–969. doi: 10.1007/s10570-015-0551-0
Jorfi, M., and Foster, E. J. (2015). Recent advances in nanocellulose for biomedical applications. J. Appl. Polym. Sci. 132, 1–19. doi: 10.1002/app.41719
Jose, J., Thomas, V., Vinod, V., Abraham, R., and Abraham, S. (2019). Nanocellulose based functional materials for supercapacitor applications. J. Sci. Adv. Mater. Devices 4, 333–340. doi: 10.1016/j.jsamd.2019.06.003
Jozala, A. F., de Lencastre-Novaes, L. C., Lopes, A. M., de Carvalho Santos-Ebinuma, V., Mazzola, P. G., Pessoa-Jr, A., et al. (2016). Bacterial nanocellulose production and application: a 10-year overview. Appl. Microbiol. Biotechnol. 100, 2063–2072. doi: 10.1007/s00253-015-7243-4
Kalia, S., Kaith, B. S., and Kaur, I. (2011). Cellulose Fibers: Bio- and Nano-Polymer Composites: Green Chemistry and Technology. New York, NY: Springer Science and Business Media. doi: 10.1007/978-3-642-17370-7
Kang, X., Sun, P., Kuga, S., Wang, C., Zhao, Y., Wu, M., et al. (2017). Thin cellulose nanofiber from corncob cellulose and its performance in transparent nanopaper. ACS Sustain. Chem. Eng. 5, 2529–2534. doi: 10.1021/acssuschemeng.6b02867
Kargarzadeh, H., Mariano, M., Gopakumar, D., Ahmad, I., Thomas, S., Dufresne, A., et al. (2018). Advances in cellulose nanomaterials. Cellulose 25, 2151–2189. doi: 10.1007/s10570-018-1723-5
Khalil, H. A., Davoudpour, Y., Islam, M. N., Mustapha, A., Sudesh, K., Dungani, R., et al. (2014). Production and modification of nanofibrillated cellulose using various mechanical processes: a review. Carbohydr. Polym. 99, 649–665. doi: 10.1016/j.carbpol.2013.08.069
Kim, S., Li, H., Oh, I., Kee, C., and Kim, M. (2012). Effect of viscosity-inducing factors on oxygen transfer in production culture of bacterial cellulose. Korean J. Chem. Eng. 29, 792–797. doi: 10.1007/s11814-011-0245-8
Kim, Y. H., Park, S., Won, K., Kim, H. J., and Lee, S. H. (2013). Bacterial cellulose–carbon nanotube composite as a biocompatible electrode for the direct electron transfer of glucose oxidase. J. Chem. Technol. Biotechnol. 88, 1067–1070. doi: 10.1002/jctb.3939
Kim, Y. J., Kim, J. N., Wee, Y. J., Park, D. H., and Ryu, H. W. (2007). Bacterial cellulose production by Gluconacetobacter sp. PKY5 in a rotary biofilm contactor. Appl. Biochem. Biotechnol. 137, 529–537. doi: 10.1007/s12010-007-9077-8
Klemm, D., Kramer, F., Moritz, S., Lindström, T., Ankerfors, M., Gray, D., et al. (2011). Nanocelluloses: a new family of nature-based materials. Angew. Chem. Int. Ed. 50, 5438–5466. doi: 10.1002/anie.201001273
Kralisch, D., Hessler, N., Klemm, D., Erdmann, R., and Schmidt, W. (2010). White biotechnology for cellulose manufacturing—the HoLiR concept. Biotechnol. Bioeng. 105, 740–747. doi: 10.1002/bit.22579
Kumar, V., Pathak, P., and Bhardwaj, N. K. (2020). Waste paper: an underutilized but promising source for nanocellulose mining. Waste Manage. 102, 281–303. doi: 10.1016/j.wasman.2019.10.041
Lavoine, N., Desloges, I., Dufresne, A., and Bras, J. (2012). Microfibrillated cellulose–its barrier properties and applications in cellulosic materials: a review. Carbohydr. Polym. 90, 735–764. doi: 10.1016/j.carbpol.2012.05.026
Leitão, A. F., Silva, J. P., Dourado, F., and Gama, M. (2013). Production and characterization of a new bacterial cellulose/poly (vinyl alcohol) nanocomposite. Materials 6, 1956–1966. doi: 10.3390/ma6051956
Li, J., Wei, X., Wang, Q., Chen, J., Chang, G., Kong, L., et al. (2012). Homogeneous isolation of nanocellulose from sugarcane bagasse by high pressure homogenization. Carbohydr. Polym. 90, 1609–1613. doi: 10.1016/j.carbpol.2012.07.038
Li, M.-C., Wu, Q., Song, K., Qing, Y., and Wu, Y. (2015). Cellulose nanoparticles as modifiers for rheology and fluid loss in bentonite water-based fluids. ACS Appl. Mater. Interfaces 7, 5006–5016. doi: 10.1021/acsami.5b00498
Lin, D., Lopez-Sanchez, P., Li, R., and Li, Z. (2014). Production of bacterial cellulose by Gluconacetobacter hansenii CGMCC 3917 using only waste beer yeast as nutrient source. Bioresour. Technol 151, 113–119. doi: 10.1016/j.biortech.2013.10.052
Liu, D. Y., Sui, G. X., and Bhattacharyya, D. (2014). Synthesis and characterization of nanocellulose-based polyaniline conducting films. Compos. Sci. Technol. 99, 31–36. doi: 10.1016/j.compscitech.2014.05.001
Marques, P. A., Nogueira, H. I., Pinto, R. J., Neto, C. P., and Trindade, T. (2008). Silver-bacterial cellulosic sponges as active SERS substrates. J. Raman Spectrosc. 39, 439–443. doi: 10.1002/jrs.1853
Mhd Haniffa, M. A. C., Ching, Y. C., Abdullah, L. C., Poh, S. C., and Chuah, C. H. (2016). Review of bionanocomposite coating films and their applications. Polymers 8:246. doi: 10.3390/polym8070246
Moniruzzaman, M., and Ono, T. (2013). Separation and characterization of cellulose fibers from cypress wood treated with ionic liquid prior to laccase treatment. Bioresour. Technol. 127, 132–137. doi: 10.1016/j.biortech.2012.09.113
Moon, D., Sagisaka, M., Tahara, K., and Tsukahara, K. (2017). Progress towards sustainable production: environmental, economic, and social assessments of the cellulose nanofiber production process. Sustainability 9:2368. doi: 10.3390/su9122368
Morais, J. P. S., Rosa, M. F., Filho, M. M. S., Nascimento, L. D., Nascimento, D. M., and Cassales, A. R. (2013). Extraction and characterization of nanocellulose structures from raw cotton linter. Carbohydr. Polym. 91, 229–235. doi: 10.1016/j.carbpol.2012.08.010
Mugaanire, I. T., Wang, H., and Sun, J. (2019). Fibrous microcrystalline cellulose from Ficus natalensis barkcloth. Eur. J. Wood Wood Prod. 77, 483–486. doi: 10.1007/s00107-019-01382-2
NanoCrystalline Cellulose (2019). Manufacturing Expert. Montreal, QC: CelluForce. Available online at: https://www.celluforce.com/ (accessed December 9, 2019).
Nechyporchuk, O., Belgacem, M. N., and Bras, J. (2016). Production of cellulose nanofibrils: a review of recent advances. Ind. Crops Prod. 93, 2–5. doi: 10.1016/j.indcrop.2016.02.016
Nogi, M., Iwamoto, S., Nakagaito, A. N., and Yano, H. (2009). Optically transparent nanofiber paper. Adv. Mater. 21, 1595–1598. doi: 10.1002/adma.200803174
Pandey, J. K., Bistamam, M. S. A., and Takagi, H. (2012). Cellulose nano-fibers from waste newspaper. J. Biobased Mater. Bioenergy 6, 115–118. doi: 10.1166/jbmb.2012.1195
Park, N. M., Choi, S., Oh, J. E., and Hwang, D. Y. (2019). Facile extraction of cellulose nanocrystals. Carbohydr. Polym. 223:115114. doi: 10.1016/j.carbpol.2019.115114
Peretz, R., Sterenzon, E., Gerchman, Y., Vadivel, V. K., Luxbacher, T., and Mamane, H. (2019). Nanocellulose production from recycled paper mill sludge using ozonation pretreatment followed by recyclable maleic acid hydrolysis. Carbohydr. Polym. 216, 343–351. doi: 10.1016/j.carbpol.2019.04.003
Phanthong, P., Reubroycharoen, P., Hao, X., Xu, G., Abudula, A., and Guan, G. (2018). Nanocellulose: extraction and application. Carbon Resour. Convers. 1, 32–43. doi: 10.1016/j.crcon.2018.05.004
Phanthong, P, Guan, G., Karnjanakom, S., Hao, X, Wang, Z., Kusakabe, K., et al. (2016). Amphiphobic nanocellulose-modified paper: fabrication and evaluation. RSC Adv. 6, 13328–13334. doi: 10.1039/C5RA24986D
Puangsin, B., Soeta, H., Saito, T., and Isogai, A. (2017). Characterization of cellulose nanofibrils prepared by direct TEMPO-mediated oxidation of hemp bast. Cellulose 24, 3767–3775. doi: 10.1007/s10570-017-1390-y
Ramasamy, J., and Amanullah, M. (2020). Nanocellulose for oil and gas field drilling and cementing applications. J. Petrol. Sci. Eng. 184:106292. doi: 10.1016/j.petrol.2019.106292
Reiniati, I., Hrymak, A. N., and Margaritis, A. (2017). Recent developments in the production and applications of bacterial cellulose fibers and nanocrystals. Crit. Rev. Biotechnol. 37, 510–524. doi: 10.1080/07388551.2016.1189871
Robles, E., Urruzola, I., Labidi, J., and Serrano, L. (2015). Surface-modified nano-cellulose as reinforcement in poly (lactic acid) to conform new composites. Ind. Crops Prod. 71, 44–53. doi: 10.1016/j.indcrop.2015.03.075
Römling, U., and Galperin, M. Y. (2015). Bacterial cellulose biosynthesis: diversity of operons, subunits, products, and functions. Trends Microbiol. 23, 545–557. doi: 10.1016/j.tim.2015.05.005
Saboori, R., Sabbaghi, S., Mowla, D., and Soltani, A. (2012). Decreasing of water loss and mud cake thickness by CMC nanoparticles in mud drilling. Int. J. Nano Dimens. 3, 101–104. doi: 10.7508/IJND.2012.02.002
Salas, C., Nypelö, T., Rodriguez-Abreu, C., Carrillo, C., and Rojas, O. J. (2014). Nanocellulose properties and applications in colloids and interfaces. Curr. Opin. Colloid Interface Sci. 19, 383–396. doi: 10.1016/j.cocis.2014.10.003
Serpa, A., Velásquez-Cock, J., Gañán, P., Castro, C., Vélez, L., and Zuluaga, R. (2016). Vegetable nanocellulose in food science: a review. Food Hydrocoll. 57, 178–186. doi: 10.1016/j.foodhyd.2016.01.023
Shao, W., Liu, H., Wang, S., Wu, J., Huang, M., Min, H., et al. (2016). Controlled release and antibacterial activity of tetracycline hydrochloride-loaded bacterial cellulose composite membranes. Carbohydr. Polym. 145, 114–120. doi: 10.1016/j.carbpol.2016.02.065
Sharma, C., and Bhardwaj, N. K. (2019). Bacterial nanocellulose: present status, biomedical applications, and future perspectives. Mater. Sci. Eng. C 104:109963. doi: 10.1016/j.msec.2019.109963
Silva, N. H., Drumond, I., Almeida, I. F., Costa, P., Rosado, C. F., Neto, C. P., et al. (2014). Topical caffeine delivery using biocellulose membranes: a potential innovative system for cellulite treatment. Cellulose 21, 665–674. doi: 10.1007/s10570-013-0114-1
Siró, I., and Plackett, D. (2010). Microfibrillated cellulose and new nanocomposite materials: a review. Cellulose 17, 459–494. doi: 10.1007/s10570-010-9405-y
Son, H. J., Heo, M. S., Kim, Y. G., and Lee, S. J. (2001). Optimization of fermentation conditions for the production of bacterial cellulose by a newly isolated Acetobacter. Biotechnol. Appl. Biochem. 33, 1–5. doi: 10.1042/BA20000065
Suopajärvi, T., Sirviö, J. A., and Liimatainen, H. (2017). Nanofibrillation of deep eutectic solvent-treated paper and board cellulose pulps. Carbohydr. Polym. 169, 167–175. doi: 10.1016/j.carbpol.2017.04.009
Svagan, A. J., Koch, C. B., Hedenqvist, M. S., Nilsson, F., Glasser, G., Baluschev, S., et al. (2016). Liquid-core nanocellulose-shell capsules with tunable oxygen permeability. Carbohydr. Polym. 136, 292–299. doi: 10.1016/j.carbpol.2015.09.040
Syafri, E., Kasim, A., Abral, H., and Asben, A. (2018). Cellulose nanofibers isolation and characterization from ramie using a chemical-ultrasonic treatment. J. Nat. Fib. 16, 1–11. doi: 10.1080/15440478.2018.1455073
Thakur, V. K., and Voicu, S. I. (2016). Recent advances in cellulose and chitosan based membranes for water purification: a concise review. Carbohydr. Polym. 146, 148–165. doi: 10.1016/j.carbpol.2016.03.030
Thomas, P., Duolikun, T., Rumjit, N. P., Moosavi, S., Lai, C. W., Johan, M. R. B., et al. (2020). Comprehensive review on nanocellulose: recent developments, challenges, and future prospects. J. Mech. Behav. Biomed. Mater. 110:103884. doi: 10.1016/j.jmbbm.2020.103884
Trache, D., Hussin, M. H., Chuin, C. T. H., Sabar, S., Fazita, M. N., Taiwo, O. F., et al. (2016). Microcrystalline cellulose: isolation, characterization, and bio-composites application—a review. Int. J. Biol. Macromol. 93, 789–804. doi: 10.1016/j.ijbiomac.2016.09.056
Uetani, K., and Yano, H. (2011). Nanofibrillation of wood pulp using a high-speed blender. Biomacromolecules 12, 348–353. doi: 10.1021/bm101103p
Visanko, M., Liimatainen, H., Sirviö, J. A., Heiskanen, J. P., Niinimäki, J., and Hormi, O. (2014). Amphiphilic cellulose nanocrystals from acid-free oxidative treatment: physicochemical characteristics and use as an oil–water stabilizer. Biomacromolecules 15, 2769–2775. doi: 10.1021/bm500628g
Voicu, S. I., Condruz, R. M., Mitran, V., Cimpean, A., Miculescu, F., Andronescu, C., et al. (2016). Sericin covalent immobilization onto cellulose acetate membrane for biomedical applications. ACS Sustain. Chem. Eng. 4, 1765–1774. doi: 10.1021/acssuschemeng.5b01756
Wahlström, R. M., and Suurnäkki, A. (2015). Enzymatic hydrolysis of lignocellulosic polysaccharides in the presence of ionic liquids. Green Chem. 17, 694–714. doi: 10.1039/C4GC01649A
Weng, Z., Su, Y., Wang, D. W., Li, F., Du, J., and Cheng, H. M. (2011). Graphene–cellulose paper flexible supercapacitors. Adv. Energy Mater. 1, 917–922. doi: 10.1002/aenm.201100312
Wijaya, C. J., Ismadji, S., Aparamarta, H. W., and Gunawan, S. (2019). Optimization of cellulose nanocrystals from bamboo shoots using response surface methodology. Heliyon 5:e02807. doi: 10.1016/j.heliyon.2019.e02807
Winuprasith, T., and Suphantharika, M. (2015). Properties and stability of oil-in-water emulsions stabilized by microfibrillated cellulose from mangosteen rind. Food Hydrocoll. 43, 690–699. doi: 10.1016/j.foodhyd.2014.07.027
Xu, Q., Chen, C., Rosswurm, K., Yao, T., and Janaswamy, S. (2016). A facile route to prepare cellulose-based films. Carbohydr. Polym. 149, 274–281. doi: 10.1016/j.carbpol.2016.04.114
Yang, X., Wang, X., Liu, H., Zhao, Y., Jiang, S., and Liu, L. (2017). Impact of dimethyl sulfoxide treatment on morphology and characteristics of nanofibrillated cellulose isolated from corn husks. Bioresour. Technol. 12, 95–106. doi: 10.15376/biores.12.1.95-106
Yarbrough, J. M., Zhang, R., Mittal, A., Vander Wall, T., Bomble, Y. J., Decker, S. R., et al. (2017). Multifunctional cellulolytic enzymes outperform processive fungal cellulases for coproduction of nanocellulose and biofuels. ACS Nano 11, 3101–3109. doi: 10.1021/acsnano.7b00086
Zang, S., Zhang, R., Chen, H., Lu, Y., Zhou, J., Chang, X., et al. (2015). Investigation on artificial blood vessels prepared from bacterial cellulose. Mater. Sci. Eng. C 46, 111–117. doi: 10.1016/j.msec.2014.10.023
Keywords: cellulose, flexible supercapacitor, energy harvesting device, nanocellulose, composite materials, water treatment, cellulose nano-fibrils (CNFs), cellulose nano-crystals (CNCs)
Citation: Gupta GK and Shukla P (2020) Lignocellulosic Biomass for the Synthesis of Nanocellulose and Its Eco-Friendly Advanced Applications. Front. Chem. 8:601256. doi: 10.3389/fchem.2020.601256
Received: 31 August 2020; Accepted: 26 November 2020;
Published: 17 December 2020.
Edited by:
Karishma R. Pardesi, Savitribai Phule Pune University, IndiaReviewed by:
Dibyajyoti Haldar, Indian Institute of Technology Guwahati, IndiaCopyright © 2020 Gupta and Shukla. This is an open-access article distributed under the terms of the Creative Commons Attribution License (CC BY). The use, distribution or reproduction in other forums is permitted, provided the original author(s) and the copyright owner(s) are credited and that the original publication in this journal is cited, in accordance with accepted academic practice. No use, distribution or reproduction is permitted which does not comply with these terms.
*Correspondence: Pratyoosh Shukla, cHJhdHlvb3NoLnNodWtsYUBnbWFpbC5jb20=
†Present address: Pratyoosh Shukla, School of Biotechnology, Institute of Science, Banaras Hindu University, Varanasi, India
Disclaimer: All claims expressed in this article are solely those of the authors and do not necessarily represent those of their affiliated organizations, or those of the publisher, the editors and the reviewers. Any product that may be evaluated in this article or claim that may be made by its manufacturer is not guaranteed or endorsed by the publisher.
Research integrity at Frontiers
Learn more about the work of our research integrity team to safeguard the quality of each article we publish.