- 1College of Chemistry and Pharmaceutical Engineering, Huanghuai University, Zhumadian, China
- 2School of Chemical Engineering and Materials, Changzhou Institute of Technology, Changzhou, China
- 3College of Chemistry and Chemical Engineering, Anhui University of Technology, Ma'anshan, China
With the demand of energy and re-utilization of wastes, the renewable lignocellulosic biomass, has attracted increasing and significant attention for alleviating the growing energy crisis and environment problems. As main components of lignocellulosic biomass, lignin, cellulose, and hemicellulose are connected by hydrogen bond to form a compact skeleton structure, resulting the trenchant condition of biomass pyrolysis. Also, pyrolysis products of above three main constituents contain a large amount of oxygenates that cause low heating value, high corrosiveness, high viscosity, and instability. Meanwhile, zeolites are of considerable significance to the conversion of lignocellulosic biomass to desirable chemical products on account of fine shape selectivity and moderate acid sites and strength. Among numerous zeolites, ZSM-5-based catalysts have been most extensively studied, and the acidity and porosity of ZSM-5 can be tuned by changing the content of Si or Al in zeolite. Beyond that, doping of other metal elements, such as Mn, Co, Ni, Ga, Ce, Pt, into ZSM-5 is also an efficient way to regulate the strength and density of acid sites in zeolite precisely. This review focused on the recent investigation of Ni-modified microporous ZSM-5 used in catalytic pyrolysis of lignin and cellulose. The application of metal-modified hierarchical ZSM-5 is also covered.
Introduction
With the rapid development of world economy and the continuous increase of population, human is facing unprecedented energy demand (Department of Economic Social Affairs United Nations, 2019; Energy Information Administration United States, 2019). Petroleum-based resources are currently society's primary source of chemicals and transportation fuels. However, due to limited oil reserves, uneven geographical distribution and environmental motivation to reduce carbon dioxide emissions and other factors, renewable energy such as lignocellulosic biomass has become a promising candidate resource for the production of renewable fuels and chemicals (Huber et al., 2006; Demirbas, 2008; Saxena et al., 2009; Zakzeski et al., 2010). Although fossil fuels continue to meet most of the world's energy demand, renewable energy is the world's fastest growing form of energy and its worldwide consumption will increase by 3% per year between 2018 and 2050 (Energy Information Administration United States, 2019). As carbon-neutral and the most abundant renewable energy resource for production of biofuels and valuable chemicals, biomass energy has attracted great attention, and developed rapidly in the last two decades (Jürgen, 2006; Ragauskas et al., 2006; Chheda et al., 2007; Huber and Corma, 2007). Biomass consists of a mixture of strongly bonded natural polymers such as cellulose (40–50%), hemicelluloses (25–30%), lignin and non-carbohydrate (Zhang et al., 2006; Menon and Rao, 2012). One most recent emerging focus of biomass utilization was the use of bio-oil generated from sustainable biomass feedstocks.
Biomass conversion is generally carried out in two ways: thermochemical decomposition, including gasification, biological carbonization, liquefaction, thermal decomposition (pyrolysis) process, and biological digestion process (essentially microbial digestion and fermentation) (Rocca et al., 1999; Lewandowski et al., 2011). Biomass conversion through thermochemical processes is considered to be a very promising biofuel carrier, because obtained bio-oil can be easily transported, burned directly in a thermal power station or gas turbine, and used in traditional refineries to produce high-quality light hydrocarbon fuels. Fast pyrolysis technology, firstly appeared in the late 1970s, is a promising way to convert biomass into bio-oil, for its high liquid oil production (up to 80% of dry feed) (Bridgwater and Peacocke, 2000; Onay, 2007). Bio-oil has many potential applications in the field of energy including being used for static application, and also can be upgraded to transportation fuel (Bridgwater and Cottam, 1992; Czernik and Bridgwater, 2004; Bridgwater, 2012). However, bio-oil usually presents several shortcomings, among which high water and oxygen content, corrosiveness, heat storage instability, immiscibility with petroleum fuel, high acidity, high viscosity, and low calorific value are main obstacles for its direct application as fuel (Michael, 2008; Park et al., 2011). The major product from non-catalytic fast pyrolysis are acids including linoleic acid, nitrogen containing compounds such as amines, amides, indoles, and pyrroles. Other organic compounds are ketones, alcohols, esters, ethers, phenols, and sugars. Acid is related to the high acidity of bio oil, and ketone is the cause of the instability of bio oil. Ethers and esters will reduce the heating values of bio oil, and nitrogen compounds cause environmental problems. In order to improve fuel quality, the process used must remove oxygen, convert carboxylic acid and other active substances into milder products, and add hydrogen to bio oil (Corma et al., 2007a; Gallezot, 2007; Alonso et al., 2010). Catalytic pyrolysis is the process of pyrolysis with assistance of catalyst and recombination of organic steam obtained from rapid pyrolysis of biomass into a class of compounds under the action of catalysts. Meanwhile, liquid fuels such as aromatic compounds within the gasoline range can be directly pyrolyzed by biomass materials (Chen and Degnan, 1988). However, due to the existence of lignin and hemicellulose structure, it is difficult to transform lignocellulose into liquid fuels by simple chemical or enzymatic hydrolysis, and finally into biofuels. Many pyrolysis parameters, such as temperature, pressure, heating rate, reactor structure, biomass type, particle size, and so on, have been widely studied and summarized (Melligan et al., 2011; Bridgwater, 2012).
Catalysts play an important role in the upgrading of bio-oil (Horne and Williams, 1996; Zhang et al., 2011). The primary catalysts mainly consist of supported noble metals Pt and Pd, transition metals Mo, Ni-Mo, Co-Mo, Ni-W, and Co-W (Viljava et al., 2000; Olivas et al., 2008; Yang et al., 2008). Although the noble metal catalysts have excellent catalytic performance, their high cost limit their large-scale application (Kubičková et al., 2005). To maintain the activity and stability of catalysts modified with metal Co and Ni, sulfurization of these catalysts is necessary during catalysts activation and bio-oil upgrading process, which will result in sulfur pollution of final products (Ryymin et al., 2010). In order to prevent sulfur pollution, it is of great significance to explore the non-sulfurized transition metal catalyst (Hu et al., 2018). ZSM-5 has been widely applied in crude oil refinery and gas adsorption-separation industry due to its strong acidity as well as shape selectivity. ZSM-5 is a kind of crystalline aluminosilicate material, which has unique two-dimensional channel-like pore structure with intersecting channels of ~0.55 nm in diameter favoring hydrocarbons of <10 carbon atoms, good thermal and hydrothermal stability, strong acid resistance, and carbon deposition resistance, adjustable acidity (Brönsted acid sites and Lewis acid sites), excellent shape selectivity, isomerization, hydrodeoxidization, and other catalytic properties (Sharma and Bakhshi, 1991; Chen et al., 2020). It has been successfully used in the hydrolysis of lignocellulose (Corma et al., 2007b; Mortensen et al., 2011; Park et al., 2011). ZSM-5 has also been widely used as a catalyst for biomass pyrolysis, and found to greatly change the composition of bio oil via dramatically reducing oxygenated compounds by deoxidization reactions, increasing aromatic species, and producing more organic matters (bio-oil) which can be upgraded to gasoline and diesel fuel (Vitolo et al., 2001; Cheng and Huber, 2011; Mortensen et al., 2011; Park et al., 2011; Taarning et al., 2011). Oxygen is removed through formation of water due to strong dehydration tendency promoted by the strong acidity of H+-exchanged ZSM-5 (HZSM-5) (Topsøe et al., 1981; Kapustin et al., 1988; Triantafillidis et al., 2001; Lappas et al., 2009). However, the strong acidity of ZSM-5 may lead to the decrease of organic components of bio oil by over-cracking to hydrocarbon, gas, or coke. Therefore, tuning of the acid sites is essential to utilization of catalyst (Huang et al., 2009).
Transition metal dopants are believed to affect the oxygen exclusion pattern by producing more carbon oxides and less water, so that more hydrogen can be incorporated into hydrocarbons. Different metal-modified ZSM-5 catalysts (Ce-ZSM-5, Co-ZSM-5, FeZSM-5, Ga-ZSM-5, HZSM-5, Ni-ZSM-5) have been used in biomass pyrolysis to verify whether these metal promoted low acid zeolites produce higher hydrocarbon yield and less coke than the commercial ZSM-5 catalysts previously tested (Park et al., 2007; French and Czernik, 2010; Valle et al., 2010; Cheng et al., 2012; Neumann and Hicks, 2012). Among them, French and Czernik (2010) studied 40 different catalysts and found that Ni-ZSM-5 catalyst has the highest hydrocarbon yield. The incorporation of transition metals (such as nickel) can increase the yield of aromatics, and they found that the hydrothermal stability of ZSM-5 will be improved by metal impregnation (Valle et al., 2005). Considering the importance of hydrodeoxygenation of bio-oil for biomass utilization and the hydrogenation ability of transition metals such as Ni, this paper mainly reviews the research progress of Ni supported ZSM-5 zeolite in catalytic conversion of biomass, and comprehensively summarizes the following aspects: (1) the catalytic conversion of biomass promoted by single metal Ni supported ZSM-5 in the absence of hydrogen; (2) the promotion of Ni supported ZSM-5 in biomass catalytic conversion in hydrogen atmosphere; (3) the utilization of bimetal supported ZSM-5 composed of Ni and other metals in biomass catalytic conversion.
Ni Modified ZSM-5
The most representative organic compounds in pyrolytic bio-oil can be divided into 13 major functional groups: aromatic hydrocarbons, aliphatic hydrocarbons, phenols, furans, acids, esters, alcohols, ethers, aldehydes, ketones, polyaromatic hydrocarbons (PAHs), nitrogen compounds, and heavier compounds (Iliopoulou et al., 2012). Among them, aromatic hydrocarbon, aliphatic hydrocarbon, and alcohol are considered as ideal biofuel products, and phenols and furans are considered as high value-added chemicals. Carbonyl compounds, such as acids, ketones, aldehydes, ketones, esters, ethers are undesirable products for their relation to corrosiveness, instability and reduce the heating value of bio oils. Other undesirable products includes polyaromatic hydrocarbons and nitrogen compounds due to environmental reasons.
The aromatics produced by catalytic pyrolysis can be divided into two types including (1) monocyclic aromatics (MAHs), such as benzene, toluene, ethylbenzene (EB), xylene, indene and other substituted benzenes as styrene, ethyl-methyl-benzene, etc. (2) polycyclic aromatics (PAHs: naphthalene, anthracene, phenanthrene, fluorene). The metal on ZSM-5 helps to catalyze the formation of monocyclic aromatics and retards the further polymerization of PAHs and other oxygenates, which is a competitive reaction and leads to the formation of PAHs.
The conversion of biomass to bio oil (XA) and selectivity to product i (Si) was defined as:
Where w0 refers to the initial weight of biomass, w1 means the weight of bio oil after catalytic pyrolysis; ni refers to moles of the product i, and ai is the carbon atom numbers for product i.
The addition of Ni metal to ZSM-5 zeolite is believed to promote the conversion of oxygenated and nitrogen compounds to aliphatics and aromatics and improve the hydrothermal stability of the catalyst, due to the synergistic effect of the dehydrogenation activity of nickel and the moderate acid strength of the catalyst (Valle et al., 2010). The formation of aliphatic compounds may be due to the fact that the metal part slows down the reaction between aromatics and other oxygenated compounds during the catalytic pyrolysis, forming alkylated benzene or polycyclic aromatic hydrocarbons (PAHs) (Carlson et al., 2010; Thangalazhy-Gopakumar et al., 2012).
Monometallic Ni-Modified ZSM-5
Huynh et al. (2014) synthesized Ni-ZSM-5 for 4, 12, 21 wt.% Ni loadings. The N2 adsorption studies revealed a steady decline in adsorption capacities with the increase in Ni content, as the N2 adsorbed volume were 94.5, 75.2, 73.4, and 65.4 cm3·g−1 at standard temperature and pressure for 4, 12, 21 wt.% Ni loadings ZSM-5, respectively. This finding could be attributed to pore blocking by the increasing proportion of loaded metal species, which is in consistence with the results of Gayubo et al. (2010). The H2 temperature-programmed reduction (TPR) profile of 21 wt.% Ni-ZSM-5 consists of two peaks at low temperature (350–450°C) and high temperature (500–600°C). There are two possible explanations for this result. One is that nickel oxide can be reduced to two-step reaction as shown in formula (1) and formula (2), as Hadjiivanov et al. (2002) confirmed. The other explanation is the intensities of interaction between Ni2+ and HZSM-5 at different positions are different, which may lead to different reducibility, which is in line with conclusion from Maia et al. (2010). According to the elemental compositions analysis by X-ray photoelectron spectroscopy, the surface Ni/Si ratio decrease from 0.24 to 0.11 during the reduction of 21 wt.% Ni-ZSM-5, and this result may be due to the sintering or migration of Ni into the pore (volume) during reduction. Results from IR spectra of neat and reduced 21 wt.% Ni-ZSM-5 showed that the total acidity remains the same (619 and 588 μmol·g−1 for neat and reduced 21 wt.% Ni-ZSM-5). However, after impregnation with Ni species, the overall Brönsted acidity significantly decreased from 451 to 243 μmol·g−1 whereas the overall Lewis acidity increased from 168 to 345 μmol·g−1. The variation of overall Brönsted acidity and Lewis acidity may be attributed to substitution of protons at Brönsted sites by exchangeable cations, that is Ni2+ (Huynh et al., 2014). The overall Lewis acidity could be produced by dehydration of protonated oxide bridge after high temperature treatment in the calcination or reduction step (Hooff and Roelofsen, 1991). This combination of Brönsted acid sites and Lewis acid sites is more suitable for HDO reaction because the acid center can cleave C-O bond through protonation, while the metal center can activate H2 and reduce aromatic ring.
Catalytic Pyrolysis
Catalytic pyrolysis with cracking catalyst is an emerging technology to directly convert the oxygenated compounds produced in the pyrolysis of biomass into hydrocarbons, so as to improve the quality of bio-oil. Catalytic pyrolysis can be carried out in the atmosphere without high hydrogen pressure, which reduces the operation cost. The volatile oxygenated species in the pyrolysis gas enter into ZSM-5 pores and react with the protons in the active sites through dehydration, decarboxylation, decarbonylation, oligomerization, and dehydrogenation to generate aromatic compounds, carbon monoxide, carbon dioxide, and water.
The results from Huynh et al. revealed that phenol conversion of 14, 82, and 98% were obtained with 4, 12, 21 wt.% Ni-ZSM-5, respectively. For 21 wt.% Ni-ZSM-5, selectivity toward deoxygenated products reached 98%, which included ~88% for cyclohexane and 8% for benzene, indicating that the combination of metal and acid is needed to effectively remove oxygen from phenol. Tuning of the metal sites can provide additional control over the severity of hydrogenation (whether it is an attack on a substituent or aromatic ring system) and selectivity. Iliopoulou et al. (2012) investigated the catalytic upgrading of biomass pyrolysis vapors using different loadings (1, 5, 10 wt.%) Ni-modified commercial equilibrium ZSM-5 diluted with silica-alumina (containing 30 wt.% crystalline zeolite) via typical wet impregnation method. There is no significant loss of surface area at low loadings (1 and 5 wt.%). However, high loading (10 wt.%) results in a 15% decrease of surface area, which is mainly due to the blocking of micropores in ZSM-5 crystal when metal phases are formed (Vitolo et al., 2001). On the other hand, compared with porosity, the effect of metals on the acidity of ZSM-5 zeolite catalyst is more significant. The presence of 1 and 5 wt.% Ni reduced the number of Brönsted acid sites by 40%, and higher loading (10 wt.%) induced further reduction (47 wt.%). The significant decrease of Brönsted acid sites indicated that the acidic protons in ZSM-5 zeolite were exchanged by Ni ions during the dry impregnation process, and the quantity of Lewis was increased by 2–3 times, possibly due to the formation of the corresponding oxide, i.e., NiO, which can serve as Lewis acid center. Basing on X-ray diffraction (XRD) pattern, crystallite size of NiO increases from 28.5 to 39.5 nm for the 5 and 10 wt.% loaded catalyst, while it is difficult to identify the XRD peaks caused by NiO in Ni (1%) ZSM-5 catalyst. For10 wt.% Ni-ZSM-5, the rectangular or cubic NiO particles were highly dispersed on catalysts and showed a mean size of ~40–45 nm.
The results of deoxy-liquefaction of laminaria japonica to liquid oil over Ni-ZSM-5 showed that Ni-ZSM-5 catalyst could increase the liquid oil yield and the contents of aromatics and long-chain alkanes, and decrease the amounts of phenols, other oxygen and nitrogen containing species (Li et al., 2013). Vichaphund et al. (2015) investigate the catalytic pyrolysis of jatropha residues including 59.2% cellulose, 18.0% hemicelluloses, and 22.8% lignin with 3 wt.% Ni-ZSM-5 catalysts. The combination of Ni and acid sites provides an ideal environment for the oligomerization, cyclization, and dehydrogenation of small olefins, and improves the formation rate of aromatic compounds. The main product is toluene with selectivity of 36.4% while the selectivity of benzene is only 10%, owing to the alkylation of benzene and other oxygenated compounds to form alkylated benzene. In addition, the 3 wt.% Ni-ZSM-5 catalysts with different preparation method of ion-exchange and wet impregnation are compared in catalytic pyrolysis of jatropha residues. For ion-exchanged HZSM-5, the MAHs selectivity is 85–88% and PAHs can be reduced to 12–16%, while for impregnated HZSM-5, the MAHs selectivity is 85–90% and PAHs can be reduced to 10–15%.
The upgrading of bio-oil with Ni modified hierarchical ZSM-5 catalyst is also studied, and results showed that the preferential mechanism for O-removal using hierarchically structured Ni-ZSM-5 zeolite catalysts seems to proceed through decarbonylation and decarboxylation reactions at the Lewis acid sites evolved after metal incorporation (Veses et al., 2016). However, the main product in obtained bio-oil is phenols (42.8 wt%). Chen et al. synthesize hierarchical ZSM-5 catalyst by NaOH desilication and HCl treatment and investigate the catalytic pyrolysis of rice straw to aromatics with Ni modified ZSM-5. High yields of aromatics (28%) can be obtained at very low Ni loading (0.1 wt.%), and there is no difference in the selectivity of aromatic products when the amount of Ni added is 0.1, 0.5, or 1.0% (Chen et al., 2018). The study on effect of reaction temperature on conversion of phenol with hierarchical Ni-ZSM-5 shows that the main products were mostly benzene and cyclohexene formed by phenol deoxygenation at low and intermediate temperatures (393 and 423 K) whereas a shift in the reaction pathways occurred at higher temperature (448 K), leading to high slectivity of valuable alkylphenols (mostly cresols and cyclohexylphenols) generated by the occurrence of alkylation reactions catalyzed by the zeolite acid sites (García-Minguillan et al., 2020). The mixture of microporous ZSM-5 and another mesoporous zeolite is also employed for catalytic pyrolysis of biomass. Hu et al. (2020) investigate the catalytic co-pyrolysis of seaweeds and cellulose using mixed ZSM-5 and MCM-41, the yield of main product (furans) is 52.2%, which is higher than that using single ZSM-5 or MCM-41. Because of the interaction between the free radicals of seaweeds/cellulose and ZSM-5/MCM-41, as well as the synergism between the joint channel advantage of mesoporous molecular sieve and the acidity of microporous molecular sieve, the yield and composition of bio oil are improved.
The biomass pyrolysis experiments were performed on a bench-scale fixed bed tubular reactor, and catalytic pyrolysis experiment with NiO was also conducted for comparison (Iliopoulou et al., 2007; Triantafyllidis et al., 2007). Compared with the non-catalytic experiment, all the catalysts reduced the total liquid yield, increased the gas products and coke at the expense of organic yield. This behavior is due to various hydrocarbon conversion reactions, such as cracking, dehydrogenation, and cyclization/aromatization, which are catalyzed by zeolite protonic acid sites. Besides that, water formation was promoted by dehydration/decarboxylation of oxygenated compound on acid sites of ZSM-5 (Lappas et al., 2009). What is needed to point out is that the addition of Ni in to ZSM-5 does not influence the formation of water and leads mainly to increased production of H2 and C2-C6 gaseous hydrocarbons. Iliopoulou et al. (2012) suggested two important reaction routes: (1) bio oil deoxidized by decarboxylation, producing a small amount of water and in situ generating hydrogen; (2) in situ generated hydrogen atoms participate in the hydrogen transfer reaction on NiO atoms, increasing the generation of saturated hydrocarbon through the carbonium intermediate on the acid sites of zeolite. The almost unaffected water production indicates that the oxygen of bio oil compounds is not removed by hydrogen deoxidation, which can be promoted by Ni supported metals, but mainly by decarboxylation reactions. The increase of aromatics may be due to the enhancement of dehydrogenation of Ni metal, and the increase of phenolic content may be related to the decrease of Brönsted acid sites which are covering by Ni metal ions. After pyrolysis experiment, a majority of NiO particles converted to metallic Ni particles which showed smaller spherical or rectangular particles with an average size of ~17 nm, and the catalyst particle were covered by a layer of graphitized carbon, which may be due to the strong dehydrogenation effect of Ni species (related to the formation of coke) during pyrolysis. This is the first report of observation of reduction of Ni oxides to metallic Ni during biomass catalytic pyrolysis. And this result may play an important role in commercial use of Ni-ZSM-5, because the catalyst will continue to circulate between the pyrolysis reactor (reduction of Ni oxides) and the regenerator (oxidization of metal Ni) which is used to burn off char (coke deposited on the catalyst and possibly unreacted biomass). In addition, the in-situ formation of reduced Ni metal phase can also promote the hydrogen transfer reaction using the in situ produced H2 on metallic Ni or external supplied H2 in a hydro-pyrolysis process (Yung et al., 2016). Porosity and acidity of different Ni-ZSM-5 catalysts and their catalytic pyrolysis performance are shown in Table 1.
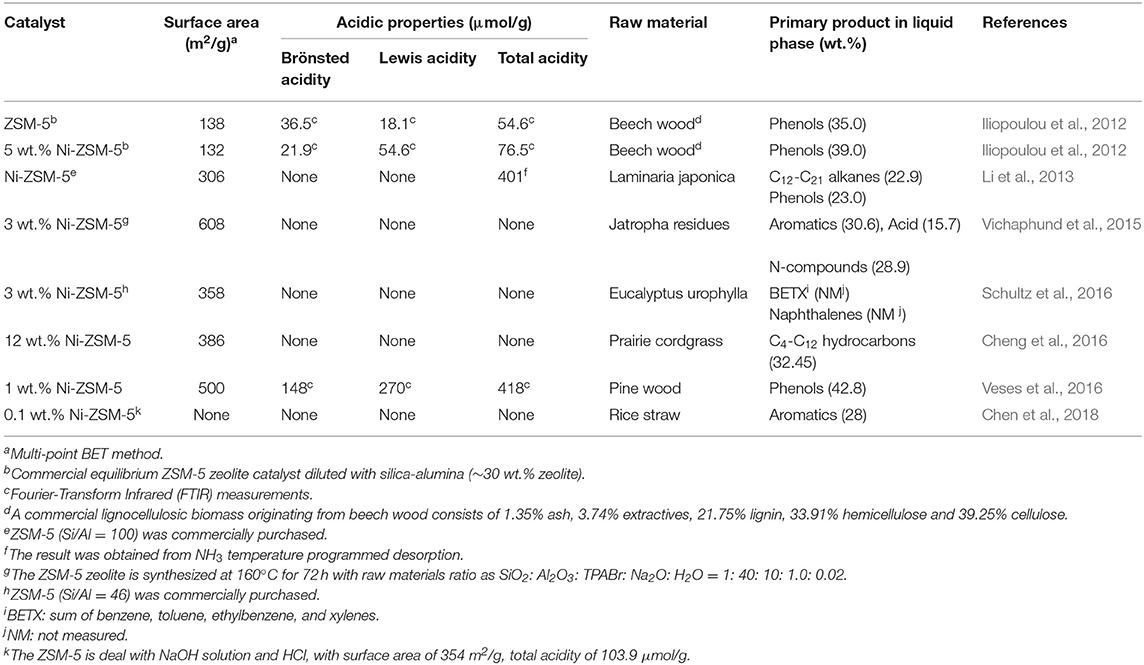
Table 1. Porosity and acidity characteristics of catalysts and catalytic pyrolysis performance of different catalysts.
Catalytic Hydro-Pyrolysis
When hydrogen is added in the pyrolysis process, very active H· radicals will be produced. H· radicals are easy to react to form biomass fragments, while removing oxygen and covering free radicals, thus increasing the hydrocarbons production. Hydro-pyrolysis has been widely used in coal pyrolysis, and the results show that under high hydrogen pressure, cracking, and hydrogenation of bio oil compounds will occur simultaneously (Canel et al., 2005). To study the deoxidization effect of Ni-ZSM-5 catalyst in the process of catalytic hydro-pyrolysis, Thangalazhy-Gopakumar et al. (2012) investigated the catalytic hydro-pyrolysis of pine wood sample (particle size of 149–177 μm) using HZSM-5 and 5 wt.% Ni-HZSM-5 under different hydrogen pressure of 10, 20, 30, and 40 MPa.
For HZSM-5 catalysts, the aromatic yields have no change in the hydrogen pressure of 10–40 MPa, and the catalyst may only play the role of cracking catalyst, not the role of promoting hydrogenation (Pindoria et al., 1998). Lower amounts of the higher molecular weight phenolic compounds and larger amounts of the lighter phenols were observed in the presence of Ni supported ZSM-5 (Melligan et al., 2012). The possible reaction mechanism for the formation of phenols, benzene, toluene, and ethylbenzene is shown in Scheme 1. Compared with ZSM-5 catalyst, Ni-ZSM-5 lowered the ethanoic acid content, and a further decrease of 20% in ethanoic acid was observed after introduction of H2 to the reaction.
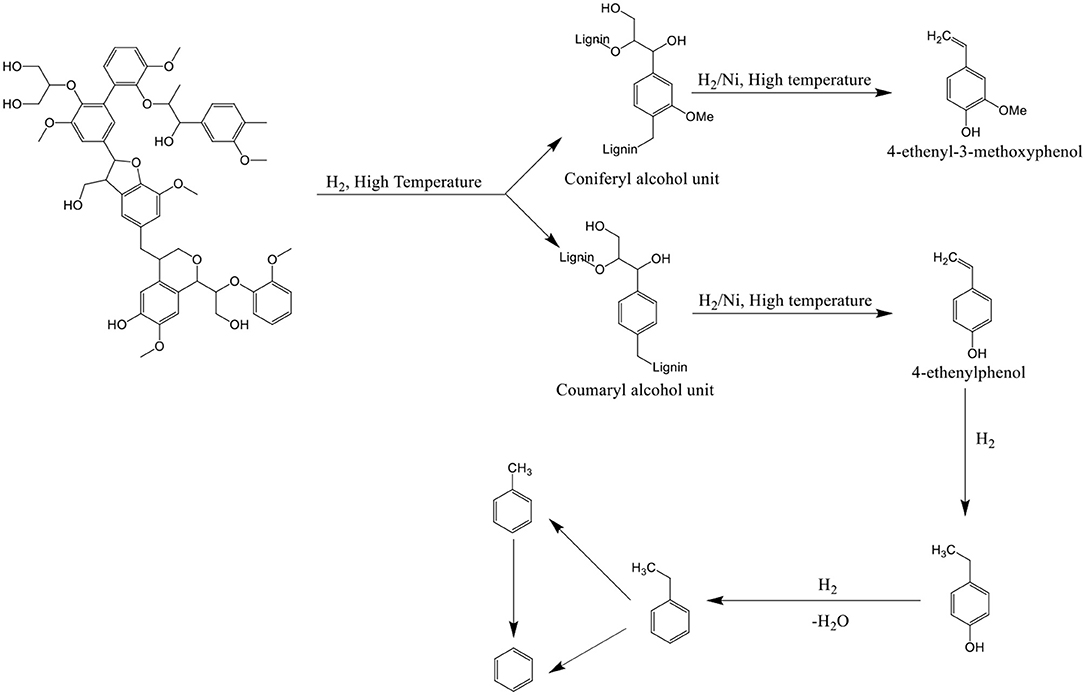
Scheme 1. Possible reaction pathway for lignin, from Melligan et al. (2012).
The hydrodeoxygenation of guaiacol and 2-phenoxy-1-phenylethanol as model compounds of lignin are performed with different Ni loadings (5, 10, 12.5, 15, 20 wt.%) Ni-ZSM-5 under 5 MPa of hydrogen pressure (Barton et al., 2018). Regardless of Ni loading, the conversions of guaiacol are nearly 100% and three main products are 2-methoxycyclohexanol, cyclohexanol, and cyclohexane. But the time required to reach 100% conversion decreased with increased Ni loading. The Ni-ZSM-5 was also used to investigate the hydrodeoxygenation of vegetable oils to liquid alkane fuels, where the selectivity of n-C5-C16 alkane was 71.0% (Na et al., 2012). Porosity and acidity of different Ni-ZSM-5 catalysts and their catalytic hydro-pyrolysis performance are shown in Table 2.
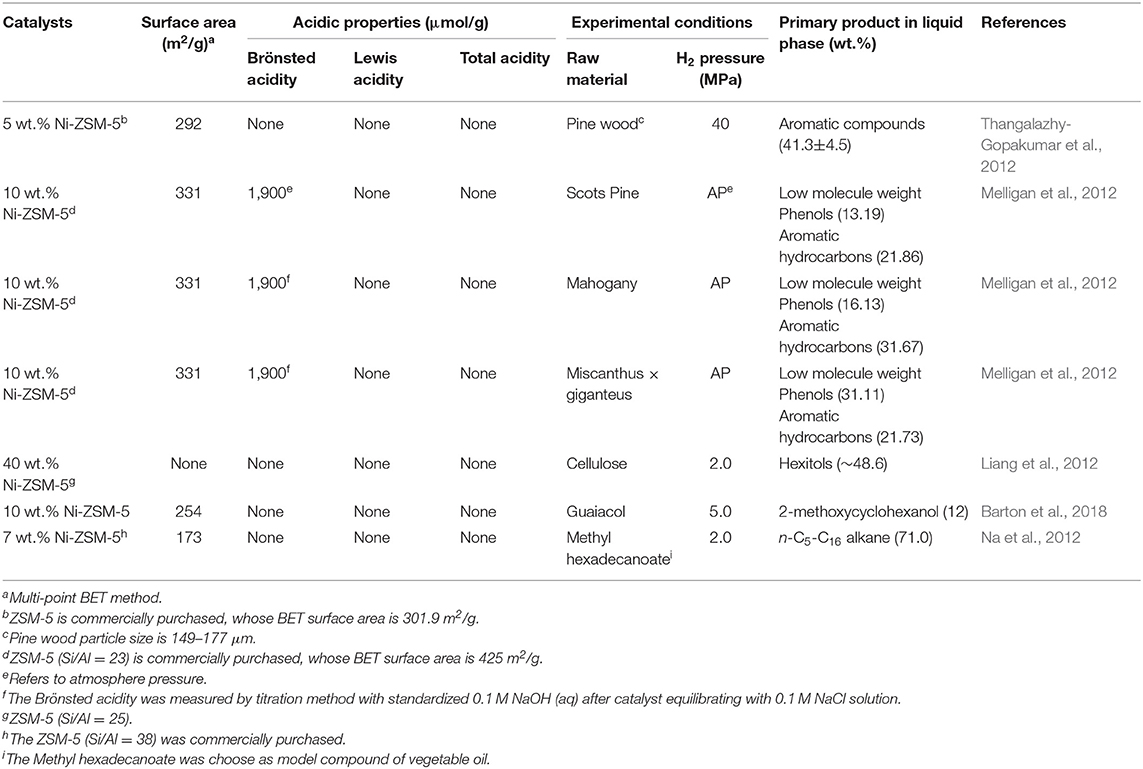
Table 2. Porosity and acidity characteristics of catalysts and catalytic hydro-pyrolysis performance of different catalysts.
Bimetallic Ni Modified ZSM-5
Although the activity of nickel-based catalysts is higher than that of other catalysts, there are still many problems that limit the utilization of Ni-ZSM-5 catalysts, such as carbon deposition. Zhang et al. (2013) observed that 36 wt.% of residue such as coke was deposited on the surface after hydrotreatment. Zhao et al. (2012) observed the deactivation of Ni-ZSM-5 catalysts owing to sintering during the hydrothermal treatment and recycling process as well as partly Ni leaching from the catalyst into water (Zhao et al., 2012). The deactivation of catalysts mainly depends on the zeolite pore structure, acidic properties, reaction temperature, and properties of reactants. The main function of Lewis acid sites is to bind substances to the catalyst surface; Brönsted acid sites is to transfer protons to related compounds to form carbon positive ions, which is considered to be the main reason for coking (Mortensen et al., 2011). The process of carbon deposition is very complex, in which the intramolecular and intermolecular condensation reactions of reactants and/or products play a key role. These condensation reactions usually undergo nearly irreversible second reaction of dehydrogenation or hydrogen transfer to form stable oligomer or graphite carbon, which is difficult to remove from the acid catalyst. Li et al. (2015) investigate the coke deposition on 15 wt.% Ni-ZSM-5 in bio-oil hydrodeoxygenation process under 523–603 K and 2.0 MPa of hydrogen pressure. The results showed that most of the deposited filamentous carbon is converted into carbon-rich flat plate as the temperature rises from 250 to 330°C. The filamentous carbon and carbon-rich flat plate both possess low volatility and solubility and are often retained within pores or on the outer surface of the catalysts, which could potentially block reactant molecules from reaching acid sites and result in catalysts deactivation. The deposition coked at 250°C is soft carbon which is soluble in organic solvents, the deposition coked at 280°C shows that some soluble carbon burned off or is transformed into derivatives with higher molecular weights, the deposition coked at 300°C shows deposited hard coke (or amorphous graphite) which is insoluble in organic solvents, and the deposition coked at 330°C shows deposited graphite or amorphous graphite (Rossetti et al., 2005; Xu et al., 2009). Thermogravimetry analysis of catalysts after hydrodeoxygenation process shows four stages of mass loss from 50 to 250°C, from 250 to 450°C, from 450 to 600°C, and from 600 to 750°C, which corresponds to the loss of moisture, physical absorbents, the formation of soft coke, hard coke, and graphite, respectively.
Bimetallic catalysts often show properties different from those of the corresponding monometallic catalysts (Alonso et al., 2012). Therefore, bimetallic catalysts have also attracted much attention from researchers in recent years. Huynh et al. (2014) discovered that when using monometallic Ni-ZSM-5 and bimetallic Ni-Cu or Ni-Co-ZSM-5 as catalysts, no differences in adsorption capacities were observed irrespective of mono- or bimetallic catalysts with 20 wt.% loading. Thus, the difference of catalytic performance must be related to other reasons besides pore size effect, because all of these samples have similar micropore volumes. After calcination and reduction of Ni-Cu-ZSM-5 and Ni-Co-ZSM-5, Ni-Cu alloy and possible Ni-Co alloy are detected. What should be pointed is that a new phase of NiCo2O2 is detected in the calcined Ni-Co-ZSM-5. During the H2 temperature-programmed reduction (TPR) experiments, the Ni-Cu-ZSM-5 shows lower reduction temperature, possibly due to synergistic interaction between the oxide phases and even physical mixing of NiO and CuO (Carrero et al., 2007; Rogatis et al., 2009), whereas the effect of Co addition to Ni on reducibility is not as strong as that of Cu on Cu-Ni bimetallic precursors. The above TPR results reveal that the addition of Cu and Co promotes the reduction of nickel oxide. For catalytic hydro-pyrolysis of phenol with Ni-Cu-ZSM-5 catalyst, the phenol conversion decreases substantially along with exchange of Ni with Cu, while the selectivity to cyclohexanol increases. Considering the decrease in the number of Ni active sites and acid sites, it can be concluded that the combination of metal and acid sites can effectively remove oxygen from phenol, and tuning of metal sites can provide additional control over the severity and selectivity of hydrogenation. For catalytic hydro-pyrolysis of phenol with Ni-Co-ZSM-5 catalyst, the phenol conversion is complete for 10 wt.% Ni-10 wt.% Co-ZSM-5 and the selectivity toward deoxygenated products (benzene and cyclohexene) is 99.3%, which is probably due to the formation of a NiCo2O4 spinel phase in the catalyst precursor resulting in the high dispersion of metal species. The Ni-Cu biometallic zeolite also is investigated by Kumal et al., where CuNi/zeolite showed better deoxygenation efficiency than mono-metallic catalysts (Cu/zeolite and Ni/zeolite) and produced comparatively higher percentage of aromatic hydrocarbons at 14.3% and aliphatic hydrocarbons at 39.9% (Kumar et al., 2019, 2020).
The addition of noble metals to Ni-ZSM-5 show excellent catalytic performance in hydrogenation of microcrystalline cellulose (Liang et al., 2014). All investigated noble-metal-modified Ni-ZSM-5 gave enhanced hexitols yields in an order of Ir-Ni-ZSM-5 (49.2%) < Ru-Ni-ZSM-5 (55.6%) < Pd-Ni-ZSM-5 (58.9%) < Rh-Ni-ZSM-5 (60.6%) < Pt-Ni-ZSM-5 (76.9%). The TPR results show that the reduction of NiO is promoted by the addition of noble metals, and this promotion is due to hydrogen spillover, i.e., free hydrogen migrates from noble metals to NiO surfaces. The close interaction between platinum clusters and nickel clusters leads to homogeneous reduction, forming Pt-Ni alloy. In addition, the size of metal particles decreases to 13 nm in the presence of Pt, indicating that the addition of Pt results in higher dispersion of Pt-Ni particles, as same as the effect of addition of Ce (Li et al., 2017). The Pt-enriched alloy surface can inhibit the oxidation of nickel and suppress the leaching of active nickel, which leads to excellent hydrothermal stability. Guo et al. (2019) investigate the cleavage C-O ether bond of lignin model compounds (2-methoxyphenyl anisole, 2-(2-methoxyphenoxy)-1-phenylethanol, and 4-phenoxyphenol) over Ni/CaO-ZSM-5 catalyst and conclude that low H2 pressure favored hydrogenolysis, while high H2 pressure favored hydrogenation. Porosity and acidity of different bimetallic Ni-ZSM-5 catalysts and their catalytic hydro-pyrolysis performance are shown in Table 3.
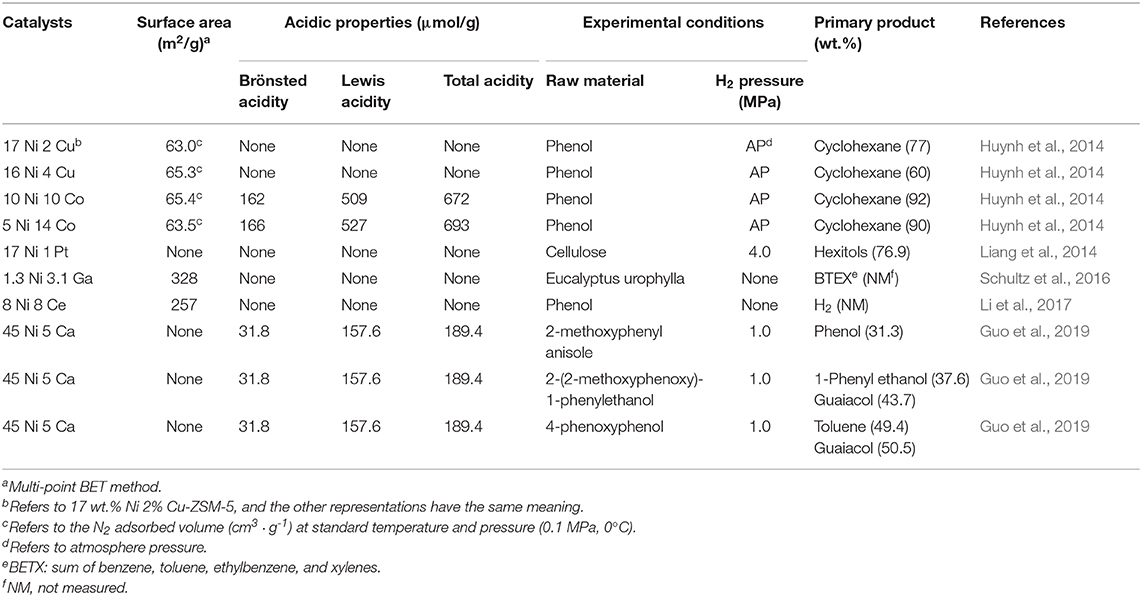
Table 3. Porosity and acidity characteristics of catalysts and catalytic performance of different bimetallic Ni-ZSM-5.
Outlook
Despite the praiseworthy achievements in catalytic pyrolysis and catalytic hydro-pyrolysis of bio oil have been studied extensively, there are still some disadvantages, such as harsh conditions (high temperature and high pressure), the use of molecular H2 as hydrogen donor, and the high cost of developing catalysts (generally noble metal catalyst is needed), low selectivity to target products and low catalyst stability. Special attention should be paid to the stability of bifunctional ZSM-5 catalysts containing different catalytic sites (metal and acid sites), which get deactivated due to different mechanisms. The metal particles on ZSM-5 suffer from leaching out while the ZSM-5 suffers from phase transformation and surface area loss. However, there are limited methods to stabilize each type of catalytic active sites. Though surface functionalization can be used to stabilize ZSM-5 catalyst, it is difficult to prepare bifunctional catalysts by different methods. Considering that improving the stability of catalyst can help to solve the problem of high catalyst cost, further study on the stability of bifunctional sites is needed. It is also necessary to study the long-term operation of continuous reactor system, because the batch reactor used in most studies is not the appropriate choice to evaluate the stability of catalyst. In order to obtain higher quality bio oil, most processes need to add a lot of molecular H2, which is usually obtained from non-renewable resources (such as steam reforming of coal). The use of gaseous hydrogen has brought challenges to the process economy and transportation. More importantly, its low solubility in most solvents requires high operating pressure, which will cause serious safety problems.
Excessive metal loading reduces the acidity and physical properties of ZSM-5, and then reduces the diffusivity and catalytic activity of the reactants. High mesopore content will increase coke formation and catalyst deactivation, so it is necessary to determine the mesoporous content of ZSM-5 and the optimal metal loading. Considering the cost of catalyst, the regeneration of ZSM-5 is still the focus of future research. Co-pyrolysis of biomass needs to be taken into account as an effective way to improve the quality as well as quantity of bio-oil, in which two or more materials will be used as feedstock. In general, the use of catalysts for biomass conversion has achieved valuable results, but there is still much room for us to understand the design of catalysts for the selective preparation of target products from biomass. Therefore, the reasonable design of catalyst is of great significance to the innovation of biomass conversion technology.
Author Contributions
R-QL: conceptualization and supervision. Y-LD and H-QW: investigation and original draft. Q-PK: methodology. MX and PY: review and editing. All authors: contributed to the article and approved the submitted version.
Conflict of Interest
The authors declare that the research was conducted in the absence of any commercial or financial relationships that could be construed as a potential conflict of interest.
Acknowledgments
We are grateful for the support of Henan Province Science and Technology Research and Development Projects (192102210025 and 202102310279); the Key Program for International S&T Cooperation Projects of China from the Ministry of Science and Technology of China (2017YFE0124300); and Anhui Provincial Natural Science Foundation of China (200808M47).
References
Alonso, D. M., Bond, J. Q., and Dumesic, J. A. (2010). Catalytic conversion of biomass to biofuels. Green Chem. 12, 1493–1513. doi: 10.1039/c004654j
Alonso, D. M., Wettstein, S. G., and Dumesic, J. A. (2012). Bimetallic catalysts for upgrading of biomass to fuels and chemicals. Chem. Soc. Rev. 41:8075. doi: 10.1039/c2cs35188a
Barton, R. R., Carrier, M., Segura, C., Garcia, F. J. L., Park, S., Lamb, H. H., et al. (2018). Ni/HZSM-5 catalyst preparation by deposition-precipitation. Part 2. catalytic hydrodeoxygenation reactions of lignin model compounds in organic and aqueous systems. Appl. Catal. A General 562, 294–309. doi: 10.1016/j.apcata.2018.06.012
Bridgwater, A. V. (2012). Review of fast pyrolysis of biomass and product upgrading. Biomass Bioenergy 38, 68–94. doi: 10.1016/j.biombioe.2011.01.048
Bridgwater, A. V., and Cottam, M. L. (1992). Opportunities for biomass pyrolysis liquids production and upgrading. Energy Fuels 6, 113–120. doi: 10.1021/ef00032a001
Bridgwater, A. V., and Peacocke, G. V. C. (2000). Fast pyrolysis processes for biomass. Renew. Sustain. Energy Rev. 4, 1–73. doi: 10.1016/S1364-0321(99)00007-6
Canel, M., Misirlioglu, Z., and Sinag, A. (2005). Hydropyrolysis of a turkish lignite (tuncbilek) and effect of temperature and pressure on product distribution. Energy Convers. Manage. 46, 2185–2197. doi: 10.1016/j.enconman.2004.10.007
Carlson, T. R., Cheng, Y. T., Jae, J., and Huber, G. W. (2010). Production of green aromatics and olefins by catalytic fast pyrolysis of wood sawdust. Energy Environ. Sci. 4, 145–161. doi: 10.1039/C0EE00341G
Carrero, A., Calles, J. A., and Vizcaíno, A. J. (2007). Hydrogen production by ethanol steam reforming over Cu-Ni/SBA-15 supported catalysts prepared by direct synthesis and impregnation. Appl. Catal. A General 327, 82–94. doi: 10.1016/j.apcata.2007.04.030
Chen, H., Cheng, H., Zhou, F., Chen, K., Qiao, K., Lu, X., et al. (2018). Catalytic fast pyrolysis of rice straw to aromatic compounds over hierarchical HZSM-5 produced by alkali treatment and metal-modification. J. Anal. Appl. Pyrol. 131, 76–84. doi: 10.1016/j.jaap.2018.02.009
Chen, N. Y., and Degnan, T. F. (1988). Cheminform abstract: industrial catalytic applications of zeolites. ChemInform 84, 32–41. doi: 10.1002/chin.198826353
Chen, Y., Aanjaneya, K., and Atreya, A. (2020). Catalytic pyrolysis of centimeter-scale pinewood particles to produce hydrocarbon fuels: the effect of catalyst temperature and regeneration. Energy Fuels 34, 1977–1983. doi: 10.1021/acs.energyfuels.9b04314
Cheng, S., Wei, L., and Zhao, X. (2016). Development of a bifunctional Ni/HZSM-5 catalyst for converting prairie cordgrass to hydrocarbon biofuel. Energy Sources 38, 2433–2437. doi: 10.1080/15567036.2015.1065298
Cheng, Y. T., and Huber, G. W. (2011). Chemistry of furan conversion into aromatics and olefins over HZSM-5: a model biomass conversion reaction. ACS Catal. 1, 611–628. doi: 10.1021/cs200103j
Cheng, Y. T., Jae, J., Shi, J., Fan, W., and Huber, G. W. (2012). Production of renewable aromatic compounds by catalytic fast pyrolysis of lignocellulosic biomass with bifunctional Ga/ZSM-5 catalysts. Angew. Chemie 51, 1387–1390. doi: 10.1002/anie.201107390
Chheda, J., Huber, G. W., and Dumesic, J. (2007). Liquid-phase catalytic processing of biomass-derived oxygenated hydrocarbons to fuels and chemicals. Angew. Chemie Int. Ed. 46, 7164–7183. doi: 10.1002/anie.200604274
Corma, A., Huber, G. W., Sauvanaud, L., and Oconnor, P. (2007a). Processing biomass-derived oxygenates in the oil refinery: catalytic cracking (FCC) reaction pathways and role of catalyst. J.Catal. 247, 307–327. doi: 10.1016/j.jcat.2007.01.023
Corma, A., Iborra, S., and Velty, A. (2007b). Chemical routes for the transformation of biomass into chemicals. Chem. Rev. 107, 2411–2502. doi: 10.1021/cr050989d
Czernik, S., and Bridgwater, A. V. (2004). Overview of applications of biomass fast pyrolysis oil. Energy Fuels 18, 590–598. doi: 10.1021/ef034067u
Demirbas, A. (2008). Biofuels sources, biofuel policy, biofuel economy and global biofuel projections. Energy Convers. Manage. 49, 2106–2116. doi: 10.1016/j.enconman.2008.02.020
Department of Economic and Social Affairs United Nations (2019). World Population Prospects. Available online at: https://population.un.org/wpp/
Energy Information Administration and United States (2019). International Energy Outlook. Available online at: https://www.eia.gov/outlooks/ieo/
French, R., and Czernik, S. (2010). Catalytic pyrolysis of biomass for biofuels production. Fuel Process. Technol. 91, 25–32. doi: 10.1016/j.fuproc.2009.08.011
Gallezot, P. (2007). Catalytic routes from renewables to fine chemicals. Catal. Today 121, 76–91. doi: 10.1016/j.cattod.2006.11.019
García-Minguillan, A. M., Briones, L., Serrano, D. P., Botas, J. A., and Escola, J. M. (2020). Shifting pathways in the phenol/2-propanol conversion over the tandem Raney Ni + ZSM-5 catalytic system. Ind. Eng. Chem. Res. 59, 3375–3382. doi: 10.1021/acs.iecr.9b07015
Gayubo, A. G., Alonso, A., Valle, B., Aguayo, A. T., Olazar, M., and Bilbao, J. (2010). Hydrothermal stability of HZSM-5 catalysts modified with Ni for the transformation of bioethanol into hydrocarbons. Fuel 89, 3365–3372. doi: 10.1016/j.fuel.2010.03.002
Guo, J., Ma, Y. L., Yu, J. Y., Gao, Y. J., and Wu, X. Y. (2019). Highly selective cleavage C-O ether bond of lignin model compounds over Ni/CaO-H-ZSM-5 in ethanol. BMC Chem. 13, 1–15. doi: 10.1186/s13065-019-0557-z
Hadjiivanov, K. H., and Knözinger Mihaylov, M. (2002). FTIR study of co adsorption on Ni-ZSM-5. J. Phys. Chem. B 106, 331–338. doi: 10.1021/jp0132782
Hooff, J. H. C. V., and Roelofsen, J. W. (1991). Chapter 7: Techniques of zeolite characterization. Stud. Surf. Sci. Catal. 58, 241–283. doi: 10.1016/S0167-2991(08)63605-8
Horne, P. A., and Williams, P. T. (1996). Upgrading of biomass-derived pyrolytic vapours over zeolite ZSM-5 catalyst: effect of catalyst dilution on product yields. Fuel Energy Abstracts 75, 1043–1050. doi: 10.1016/0016-2361(96)00082-8
Hu, M., Safarifard, V., Doustkhah, E., Rostamnia, S., Morsali, A., Nouruzi, N., et al. (2018). Taking organic reactions over metal-organic frameworks as heterogeneous catalysis. Microporous Mesoporous Mater. 256, 111–127. doi: 10.1016/j.micromeso.2017.07.057
Hu, Y., Wang, H., Lakshmikandan, M., Wang, S., Wang, Q., He, Z., et al. (2020). Catalytic co-pyrolysis of seaweeds and cellulose using mixed ZSM-5 and MCM-41 for enhanced crude bio-oil production. J. Thermal Anal. Calorimetry. doi: 10.1007/s10973-020-09291-w
Huang, J., Long, W., Agrawal, P. K., and Jones, C. W. (2009). Effects of acidity on the conversion of the model bio-oil ketone cyclopentanone on H-Y zeolites. J. Phys. Chem. C 113, 16702–16710. doi: 10.1021/jp905661w
Huber, G. W., and Corma, A. (2007). Synergies between bio- and oil refineries for the production of fuels from biomass. Angew. Chemie Int. Ed. 46, 7184–7201. doi: 10.1002/anie.200604504
Huber, G. W., Iborra, S., and Corma, A. (2006). Synthesis of transportation fuels from biomass: chemistry, catalysts, and engineering. Chem. Rev. 106, 4044–4098. doi: 10.1021/cr068360d
Huynh, T. M., Armbruster, U., Pohl, M. M., Schneider, M., Radnik, J., Hoang, D. L., et al. (2014). Hydrodeoxygenation of phenol as a model compound for bio-oil on non-noble bimetallic nickel-based catalysts. ChemCatChem 6, 1940–1951. doi: 10.1002/cctc.201402011
Iliopoulou, E. F., Antonakou, E. V., Karakoulia, S. A., Vasalos, I. A., Lappas, A. A., and Triantafyllidis, K. S. (2007). Catalytic conversion of biomass pyrolysis products by mesoporous materials: effect of steam stability and acidity of Al-MCM-41 catalysts. Chem. Eng. J. 134, 51–57. doi: 10.1016/j.cej.2007.03.066
Iliopoulou, E. F., Stefanidis, S. D., Kalogiannis, K. G., Delimitis, A., Lappas, A. A., and Triantafyllidis, K. S. (2012). Catalytic upgrading of biomass pyrolysis vapors using transition metal-modified ZSN-5 zeolite. Appl. Catal. B Environ. 127, 281–290. doi: 10.1016/j.apcatb.2012.08.030
Jürgen, O. M. (2006). Production of liquid hydrocarbons from biomass. Angew. Chemie Int. Ed. 45, 696–698. doi: 10.1002/anie.200502895
Kapustin, G. I., Brueva, T. R., Klyachko, A. L., Beran, S., and Wichterlova, B. (1988). Determination of the number and acid strength of acid sites in zeolites by ammonia adsorption: comparison of calorimetry and temperature-programmed desorption of ammonia. Appl. Catal. 42, 239–246. doi: 10.1016/0166-9834(88)80005-8
Kubičková, I., Snåre, M., Eränen, K., Mäki-Arvela, P., and Murzin, D. (2005). Hydrocarbons for diesel fuel via decarboxylation of vegetable oils. Catal. Today 106, 197–200. doi: 10.1016/j.cattod.2005.07.188
Kumar, R., Strezov, V., Kan, T., Weldekidan, H., He, J., and Jahan, S. (2020). Investigating the effect of mono and bimetallic/zeolite catalysts on hydrocarbon production during bio-oil upgrading from ex-situ pyrolysis of biomass. Energy Fuels 34, 389–400. doi: 10.1021/acs.energyfuels.9b02724
Kumar, R., Strezov, V., Lovell, E., Kan, T., Weldekidan, H., He, J., et al. (2019). Bio-oil upgrading with catalytic pyrolysis of biomass using copper/zeolite-nickel/zeolite and copper-nickel/zeolite catalysts. Bioresour. Technol. 279, 404–409. doi: 10.1016/j.biortech.2019.01.067
Lappas, A. A., Bezergianni, S., and Vasalos, I. A. (2009). Production of biofuels via co-processing in conventional refining processes. Catal. Today 145, 55–62. doi: 10.1016/j.cattod.2008.07.001
Lewandowski, W. M., Klugmann-Radziemska, E., Ryms, M., and Ostrowski, P. (2011). Modern methods of thermochemical biomass conversion into gas, liquid and solid fuels. Ecol. Chem. Eng. 18, 39–47.
Li, J., Wang, G., Gao, C., Lv, X., Wang, Z., and Liu, H. (2013). Deoxy-liquefaction of laminaria japonica to high-quality liquid oil over metal modified ZSM-5 catalysts. Energy Fuels 27, 5207–5214. doi: 10.1021/ef4004208
Li, X., Yan, B., Zhang, J., Xu, N., Tao, J., Zhang, R., et al. (2017). Hydrogen production by aqueous phase reforming of phenol derived from lignin pyrolysis over NiCe/ZSM-5 catalysts. Int. J. Hydr. Energy. 43, 649–658. doi: 10.1016/j.ijhydene.2017.09.096
Li, Y., Zhang, C., Liu, Y., Hou, X., Zhang, R., and Tang, X. (2015). Coke deposition on Ni/HZSM-5 in bio-oil hydrodeoxygenation processing. Energy Fuels 29, 1722–1728. doi: 10.1021/ef5024669
Liang, G., Cheng, H., Li, W., He, L., Yu, Y., and Zhao, F. (2012). Selective conversion of microcrystalline cellulose into hexitols on nickel particles encapsulated within ZSM-5 zeolite. Green Chem. 14, 2146–2149. doi: 10.1039/c2gc35685f
Liang, G., He, L., Arai, M., and Zhao, F. (2014). The Pt-enriched PtNi alloy surface and its excellent catalytic performance in hydrolytic hydrogenation of cellulose. ChemSusChem 7, 1415–1421. doi: 10.1002/cssc.201301204
Maia, A. J., Louis, B., Lam, Y. L., and Pereira, M. M. (2010). Ni-ZSM-5 catalysts: detailed characterization of metal sites for proper catalyst design. J. Catal. 269, 103–109. doi: 10.1016/j.jcat.2009.10.021
Melligan, F., Auccaise, R., Novotny, E. H., Leahy, J. J., Hayes, M. H. B., and Kwapinski, W. (2011). Pressurised pyrolysis of miscanthus using a fixed bed reactor. Bioresour. Technol. 102, 3466–3470. doi: 10.1016/j.biortech.2010.10.129
Melligan, F., Hayes, M. H. B., Kwapinski, W., and Leahy, J. J. (2012). Hydro-pyrolysis of biomass and online catalytic vapor upgrading with Ni-ZSM-5 and Ni-MCM-41. Energy Fuels 26, 6080–6090. doi: 10.1021/ef301244h
Menon, V., and Rao, M. (2012). Trends in bioconversion of lignocellulose: biofuels, platform chemicals & biorefinery concept. Progress in Energy Combust. Sci. 38, 522–550. doi: 10.1016/j.pecs.2012.02.002
Michael, S. (2008). Biofuels and biomass-to-liquid fuels in the biorefinery: catalytic conversion of lignocellulosic biomass using porous materials. Angew. Chemie Int. Ed. 47, 9200–9211. doi: 10.1002/anie.200801476
Mortensen, P. M., Grunwaldt, J. D., Jensen, P. A., Knudsen, K. G., and Jensen, A. D. (2011). A review of catalytic upgrading of bio-oil to engine fuels. Appl. Catal. A General 407, 1–19. doi: 10.1016/j.apcata.2011.08.046
Na, S., Qi-Ying, L., Ting, J., Tie-Jun, W., Long-Long, M., Qi, Z., et al. (2012). Hydrodeoxygenation of vegetable oils to liquid alkane fuels over Ni/HZSM-5 catalysts: methyl hexadecanoate as the model compound. Catal. Commun. 20, 80–84. doi: 10.1016/j.catcom.2012.01.007
Neumann, G. T., and Hicks, J. C. (2012). Effects of cerium and aluminum in cerium-containing hierarchical HZSM−5 catalysts for biomass upgrading. Topics Catal. 55, 196–208. doi: 10.1007/s11244-012-9788-0
Olivas, A., Zepeda, T. A., Villalpando, I., and Fuentes, S. (2008). Performance of unsupported Ni(Co, Fe)/MoS2 catalysts in hydrotreating reactions. Catal. Commun. 9, 1317–1328. doi: 10.1016/j.catcom.2007.11.025
Onay, O. (2007). Fast and catalytic pyrolysis of pistacia khinjuk seed in a well-swept fixed bed reactor. Fuel 86, 1452–1460. doi: 10.1016/j.fuel.2006.12.017
Park, H. J., Dong, J. I., Jeon, J. K., Yoo, K. S., Yim, J. H., Sohn, J. M., et al. (2007). Conversion of the pyrolytic vapor of radiata pine over zeolites. J. Indus. Eng. Chem. 13, 182–189.
Park, H. J., Jeon, J. K., Suh, D. J., Suh, Y. W., Heo, H. S., and Park, Y. K. (2011). Catalytic vapor cracking for improvement of bio-oil quality. Catal. Surveys Asia 15, 161–180. doi: 10.1007/s10563-011-9119-7
Pindoria, R. V., Megaritis, A., Herod, A. A., and Kandiyoti, R. (1998). A two-stage fixed-bed reactor for direct hydrotreatment of volatiles from the hydro-pyrolysis of biomass: effect of catalyst temperature, pressure and catalyst ageing time on product characteristics. Fuel 77, 1715–1726. doi: 10.1016/S0016-2361(98)00079-9
Ragauskas, A. J., Williams, C. K., Davison, B. H., Britovsek, G., Cainey, J., Eckert, C. A., et al. (2006). The path forward for biofuels and biomaterials. Science 311, 484–489. doi: 10.1126/science.1114736
Rocca, P. A. D., Cerrella, E. G., Bonelli, P. R., and Cukierman, A. L. (1999). Pyrolysis of hardwoods residues: on kinetics and chars characterization. Biomass Bioenergy 16, 79–88. doi: 10.1016/S0961-9534(98)00067-1
Rogatis, L. D., Montini, T., Cognigni, A., Olivi, L., and Fornasiero, P. (2009). Methane partial oxidation on nicu-based catalysts. Catal. Today 145, 176–185. doi: 10.1016/j.cattod.2008.04.019
Rossetti, I., Bencini, E., Trentini, L., and Forni, L. (2005). Study of the deactivation of a commercial catalyst for ethylbenzene dehydrogenation to styrene. Appl. Catal. A General 292, 118–123. doi: 10.1016/j.apcata.2005.05.046
Ryymin, E. M., Honkela, M. L., Viljava, T. R., and Krause, A. O. I. (2010). Competitive reactions and mechanisms in the simultaneous HDO of phenol and methyl heptanoate over sulphided NiMo/γ-Al2O3. Appl. Catal. A General 389, 114–121. doi: 10.1016/j.apcata.2010.09.010
Saxena, R. C., Adhikari, D. K., and Goyal, H. B. (2009). Biomass-based energy fuel through biochemical routes: a review. Renew. Sustain. Energy Rev. 13, 167–178. doi: 10.1016/j.rser.2007.07.011
Schultz, E. L., Mullen, C. A., and Boateng, A. A. (2016). Aromatic hydrocarbon production from Eucalyptus urophylla pyrolysis over several metal-modified ZSM-5 catalysts. Energy Technol. 5, 196–204. doi: 10.1002/ente.201600206
Sharma, R. K., and Bakhshi, N. N. (1991). Catalytic upgrading of biomass-derived oils to transportation fuels and chemicals. Can. J. Chem. Eng. 69, 1071–1081. doi: 10.1002/cjce.5450690505
Taarning, E., Osmundsen, C. M., Yang, X., Voss, B., Andersen, S. I., and Christensen, C. H. (2011). Zeolite-catalyzed biomass conversion to fuels and chemicals. Energy Environ. Sci. 4, 793–804. doi: 10.1039/C004518G
Thangalazhy-Gopakumar, S., Adhikari, S., and Gupta, R. B. (2012). Catalytic pyrolysis of biomass over H+ZSM-5 under hydrogen pressure. Energy Fuels 26, 5300–5306. doi: 10.1021/ef3008213
Topsøe, N. Y., Pedersen, K., and Derouane, E. G. (1981). Infrared and temperature-programmed desorption study of the acidic properties of ZSM-5-type zeolites. J. Catal. 70, 41–52. doi: 10.1016/0021-9517(81)90315-8
Triantafillidis, C. S., Vlessidis, A. G., Nalbandian, L., and Evmiridis, N. P. (2001). Effect of the degree and type of the dealumination method on the structural, compositional and acidic characteristics of H-ZSM-5 zeolites. Microporous Mesoporous Mater. 47, 369–388. doi: 10.1016/S1387-1811(01)00399-7
Triantafyllidis, K. S., Iliopoulou, E. F., Antonakou, E. V., Lappas, A. A., Wang, H., and Pinnavaia, T. J. (2007). Hydrothermally stable mesoporous aluminosilicates (MSU-S) assembled from zeolite seeds as catalysts for biomass pyrolysis. Microporous Mesoporous Mater. 99, 132–139. doi: 10.1016/j.micromeso.2006.09.019
Valle, B., Alonso, A., Atutxa, A., Gayubo, A. G., and Bilbao, J. (2005). Effect of nickel incorporation on the acidity and stability of HZSM-5 zeolite in the MTO process. Catal. Today 106, 118–122. doi: 10.1016/j.cattod.2005.07.132
Valle, B., Gayubo, A. G., Aguayo, A. T., Olazar, M., and Bilbao, J. (2010). Selective production of aromatics by crude bio-oil valorization with a nickel-modified HZSM-5 zeolite catalyst. Energy Fuels 24, 2060–2070. doi: 10.1021/ef901231j
Veses, A., Puértolas, B., López, J. M., Callén, M. S., Solsona, B., and García, T. (2016). Promoting deoxygenation of bio-oil by metal-loaded hierarchical ZSM-5 zeolites. ACS Sustain. Chem. Eng. 4, 1653–1660. doi: 10.1021/acssuschemeng.5b01606
Vichaphund, S., Aht-Ong, D., Sricharoenchaikul, V., and Atong, D. (2015). Production of aromatic compounds from catalytic fast pyrolysis of jatropha residues using metal/HZSM-5 prepared by ion-exchange and impregnation methods. Renew. Energy 79, 28–37. doi: 10.1016/j.renene.2014.10.013
Viljava, T. R., Komulainen, R. S., and Krause, A. O. I. (2000). Effect of H2S on the stability of CoMo/Al2O3 catalysts during hydrodeoxygenation. Catal. Today 60, 83–92. doi: 10.1016/S0920-5861(00)00320-5
Vitolo, S., Bresci, B., Seggiani, M., and Gallo, M. G. (2001). Catalytic upgrading of pyrolytic oils over HZSM-5 zeolite: behaviour of the catalyst when used in repeated upgrading-regenerating cycles. Fuel 80, 17–26. doi: 10.1016/S0016-2361(00)00063-6
Xu, J., Zhou, W., Wang, J., Li, Z., and Ma, J. (2009). Characterization and analysis of carbon deposited during the dry reforming of methane over Ni/La2O3/Al2O3 catalysts. Chin. J. Catal. 30, 1076–1084. doi: 10.1016/S1872-2067(08)60139-4
Yang, Y. Q., Tye, C. T., and Smith, K. J. (2008). Influence of MoS2 catalyst morphology on the hydrodeoxygenation of phenols. Catal. Commun. 9, 1364–1368. doi: 10.1016/j.catcom.2007.11.035
Yung, M. M., Starace, A. K., Mukarakate, C., Crow, A., Leshnov, M. A., and Magrini-Bair, K. A. (2016). Biomass catalytic pyrolysis on Ni/ZSM-5: effects of nickel pretreatment and loading. Energy Fuels 30, 5259–5268. doi: 10.1021/acs.energyfuels.6b00239
Zakzeski, J., Bruijnincx, P. C. A., Jongerius, A. L., and Weckhuysen, B. M. (2010). The catalytic valorization of lignin for the production of renewable chemicals. Chem. Rev. 110, 3552–3599. doi: 10.1021/cr900354u
Zhang, H., Cheng, Y. T., Vispute, T. P., Xiao, R., and Huber, G. W. (2011). Catalytic conversion of biomass-derived feedstocks into olefins and aromatics with ZSM-5: the hydrogen to carbon effective ratio. Energy Environ. Sci. 4:2297. doi: 10.1039/c1ee01230d
Zhang, X., Wang, T., Ma, L., Zhang, Q., and Jiang, T. (2013). Hydrotreatment of bio-oil over Ni-based catalyst. Bioresour. Technol. 127, 306–311. doi: 10.1016/j.biortech.2012.07.119
Zhang, Y. H. P., Himmel, M. E., and Mielenz, J. R. (2006). Outlook for cellulase improvement: screening and selection strategies. Biotechnol. Adv. 24, 452–481. doi: 10.1016/j.biotechadv.2006.03.003
Keywords: lignocellulose, microporous, Ni-ZSM-5, catalytic pyrolysis, hydro-pyrolysis
Citation: Ding Y-L, Wang H-Q, Xiang M, Yu P, Li R-Q and Ke Q-P (2020) The Effect of Ni-ZSM-5 Catalysts on Catalytic Pyrolysis and Hydro-Pyrolysis of Biomass. Front. Chem. 8:790. doi: 10.3389/fchem.2020.00790
Received: 21 May 2020; Accepted: 28 July 2020;
Published: 25 September 2020.
Edited by:
Hu Li, Guizhou University, ChinaReviewed by:
Yujing Weng, Henan Polytechnic University, ChinaZhibing Shen, Xi'an Shiyou University, China
Copyright © 2020 Ding, Wang, Xiang, Yu, Li and Ke. This is an open-access article distributed under the terms of the Creative Commons Attribution License (CC BY). The use, distribution or reproduction in other forums is permitted, provided the original author(s) and the copyright owner(s) are credited and that the original publication in this journal is cited, in accordance with accepted academic practice. No use, distribution or reproduction is permitted which does not comply with these terms.
*Correspondence: Rong-Qiang Li, cnFsaUBpY2Nhcy5hYy5jbg==; Qing-Ping Ke, cWluZ2tlQGFodXQuZWR1LmNu