- 1School of Marine Science and Technology, Hainan Tropical Ocean University, Sanya, China
- 2School of Iron and Steel, Soochow University, Suzhou, China
Cathode materials made of xLiVPO4F·yLi3V2(PO4)3/C (x:y = 1:0, 2:1, 0:1) are synthesized via a feasible sol-gel method for high-performance lithium-ion batteries. The structures, morphology, and electrochemical properties of the composites are thoroughly investigated. The results show that LiVPO4F/C, Li3V2(PO4)3/C, and 2LiVPO4F·Li3V2(PO4)3/C can be synthesized under 750°C without the formation of impurities. Meanwhile, the unique morphology of the 2LiVPO4F·Li3V2(PO4)3/C composite, which is porous, with nanoflakes adhering to the surface, is revealed. This composite integrates the advantages of LiVPO4F and Li3V2(PO4)3. There are four discharge plateaus near 4.2, 4.1, 3.7, and 3.6 V, and the cathode material delivers high capacities of 143.4, 141.6, 133.2, 124.1, and 117.6 mAh g−1 at rates of 0.1, 0.2, 0.5, 1, and 2 C, respectively. More importantly, the discharge capacity can be almost fully recovered when the discharge rate returns to 0.1 C. The study is highly promising for the development of cathode material for LIBs.
Introduction
With the increasing demand for renewable energy resources, lithium-ion batteries (LIBs) have attracted tremendous attention in recent years (Uddin et al., 2017; Wu et al., 2019; Zheng et al., 2019). As one of the most important parts of LIBs, cathode materials play a critical role in their electrochemical performance (Goodenough and Park, 2013; Nitta et al., 2015; Zheng et al., 2017; Sui et al., 2019a). Recently, various materials have been explored for LIB cathodes, such as olivine-structured materials (LiMPO4, M = Fe, Mn, Co, and Ni) (Li Y. et al., 2019; Vásquez and Calderón, 2019; Wu et al., 2020), layered oxide materials (LiCoO2, LiMnO2, LiNiO2, etc.) (El-Bana et al., 2017; Zhao et al., 2017; Lin et al., 2020), spinel-structured materials (LiMn2O4, LiCo2O4, etc.) (Hariprasad et al., 2016; Abou-Rjeily et al., 2019), tavorite-structured materials (LiFeSO4F, LiVPO4F, etc.) (Kim and Kang, 2017; Hu et al., 2019), and NASICON-structured materials [Li3V2(PO4)3, Li3Fe2(PO4)3, etc.] (Karami and Taala, 2011; Zheng et al., 2016; Jiang, 2018).
Among these materials, LiVPO4F and Li3V2(PO4)3 are especially promising and have drawn attention in recent years. LiVPO4F, which was synthesized by Barker et al. (2003) in 2003 for the first time, is attracting attention due to its high theoretical energy density (655 Wh kg−1) and high working voltage platform (4.2 V vs. Li/Li+) (Gover et al., 2006). The synergistic effect between F− and within the material could enhance the electronegativity and induction property of LiVPO4F, achieving improved electrochemical performance (Huang et al., 2009). For example, Sui et al. (2019b) have prepared spherical LiVPO4F/C by spray drying, and the initial discharge capacity of the synthesized LiVPO4F/C can be as high as 137.9 mAh g−1 at 0.1 C, and discharge capacity remains at 91.4% of the initial capacity after 50 cycles. However, the Li+ diffusion coefficient in LiVPO4F is low, which restricts its application.
Li3V2(PO4)3, a typical NASICON-structured material, allows the insertion and/or extraction of lithium ions from various pathways, and exhibits an outstanding Li+ diffusion coefficient (10−9-10−10 cm2 s−1) (Li R. et al., 2019). In addition, Li3V2(PO4)3 displays a high average operation voltage (4.0 V vs. Li+/Li) and excellent theoretical capacity (197 mAh·g−1) (Zhang et al., 2019). Therefore, it is expected that the combination of Li3V2(PO4)3 with LiVPO4F may enhance the ionic conductivity of cathode material and improve electrochemical performance.
Herein, we synthesized xLiVPO4F·yLi3V2(PO4)3/C cathode material for LIBs via a feasible sol-gel method. Such a design is demonstrated to combine the advantages of LiVPO4F and Li3V2(PO4)3, and it can effectively enhance electronic/ionic conductivity and structural stability. The optimal xLiVPO4F·yLi3V2(PO4)3/C shows a high initial discharge capacity, outstanding rate capability, and proper cycling performance, illustrating that it is a promising cathode material for LIBs.
Experimental Method
Synthesis of LiVPO4F/C: firstly, stoichiometric amounts of H3PO4, V2O5, and citric acid were added into deionized water under stirring, and then ammonia was added into the solution. After stirring at 80°C for 6 h and drying overnight in an oven, the precursor of VPO4 was obtained. The obtained VPO4 was pretreated at 300°C for 4 h under the protection of Ar gas and heated at 750°C for 8 h to prepare VPO4/C. Finally, stoichiometric amounts of the VPO4-based precursor and LiF were mixed and calcined from 690 to 770°C for 1 h under a flowing Ar atmosphere to obtain LiVPO4F/C. All chemical reagents used in this work were analytical grade.
Synthesis of Li3V2(PO4)3/C: stoichiometric amounts of the prepared VPO4 precursor and Li3PO4 were mixed and calcined from 650 to 800°C for 16 h under a flowing Ar atmosphere to obtain Li3V2(PO4)3/C.
Synthesis of 2LiVPO4F·Li3V2(PO4)3/C: Stoichiometric amounts of the prepared VPO4/C, LiF, and Li3PO4 were mixed and calcined at 750°C for 1 h under a flowing Ar atmosphere to obtain 2LiVPO4F·Li3V2(PO4)3/C samples.
Crystallographic information was studied by powder X-ray diffractometer (XRD, Rigaku, Ultima VI). The morphology was observed with a Hitachi SU5000 scanning electron microscope (SEM). The electrodes for electrochemical tests were fabricated with 80 wt.% active material and 20 wt.% additives (PVDF/acetylene black, 1:1). CR2025 button cells were assembled in an Ar-filled glove box. The galvanostatic charge/discharge and the cyclic voltammetry (CV) were characterized with a LAND battery test system and a CHI660D electrochemical workstation, respectively.
Results and Discussion
Figure 1 shows the XRD results of the VPO4/C precursors synthesized at different temperatures. Obvious peaks indexed to V2O3 are observed in the precursor calcined at 650°C. However, these peaks disappear when the calcination temperature is elevated above 700°C. Hence, the precursors synthesized at 700, 750, and 800°C can be confirmed to be amorphous VPO4/C. Meanwhile, the absence of peaks belong to crystalline carbon suggests the amorphous nature of the carbon coating layer.
The morphology of VPO4/C precursors synthesized at various temperatures was also investigated, as shown in Figure 2. Figure 2a suggests that the reactants cannot be completely converted to products at 650°C. Moreover, the pores on the samples are uneven. As the temperature rises to 700°C, the product has a more uniform pore diameter. However, many small particles adhere to the surface of the sample. At 750°C, the pores become most uniform, and the small particles disappear. A serious aggregation occurs when the temperature further increases to 800°C. Therefore, the optimal calcination temperature for VPO4/C precursor is 750°C, which is chosen for the synthesis of xLiVPO4F·yLi3V2(PO4)3/C (x:y = 1:0, 2:1, 0:1).
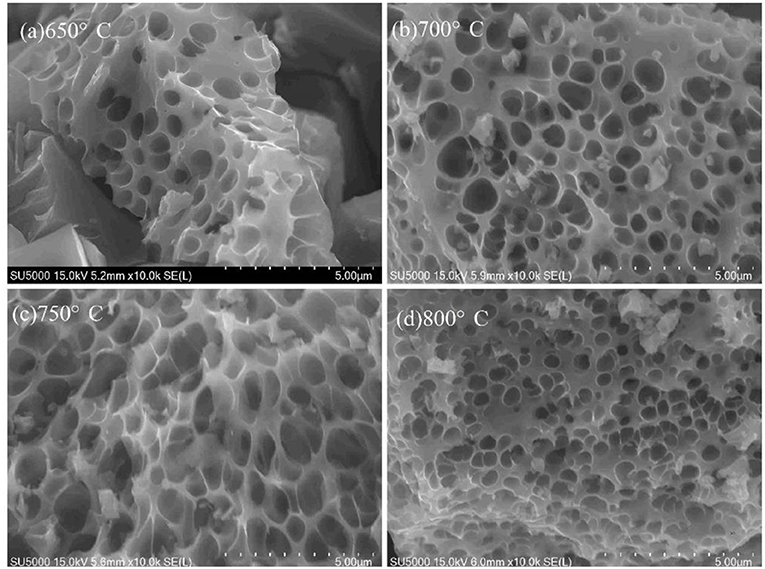
Figure 2. SEM images of the VPO4/C precursors synthesized at different temperatures. (a) 650°C; (b) 700°C; (c) 750°C; (d) 800°C.
XRD patterns of LiVPO4F/C (Figure 3A) and Li3V2(PO4)3/C (Figure 3B) synthesized at different temperatures are shown in Figure 3. As can be seen, the diffraction peaks are stronger and the half-peak width narrower at the higher calcination temperature, indicating that elevated temperature facilitates the crystallization of composites. It can be seen in Figure 3A that the characteristic peaks of Li3V2(PO4)3 and LiF become weaker as the temperature increases and that they completely disappear at 750°C. However, the impurity of Li3V2(PO4)3 reappears when the temperature reaches 770°C, suggesting that an excessive temperature has a detrimental effect on the formation of LiVPO4F. On the contrary, only pure Li3V2(PO4)3 is observed in the temperature range from 650 to 800°C in Figure 3B.
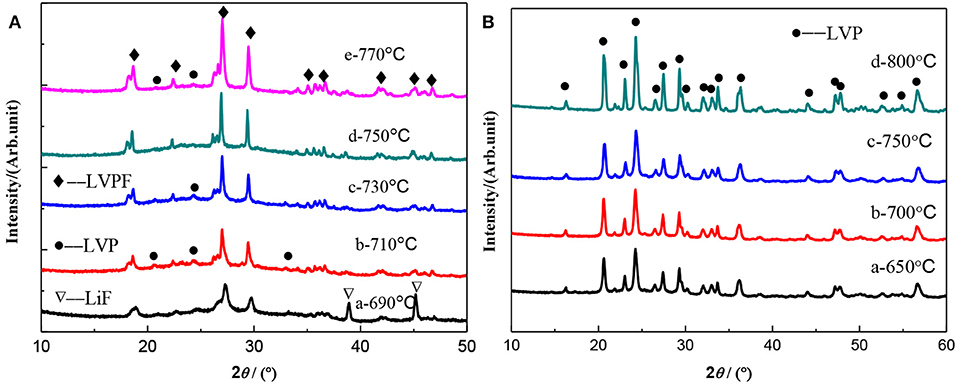
Figure 3. XRD patterns of LiVPO4F/C (A) and Li3V2(PO4)3/C (B) synthesized at different temperatures.
Figure 4 shows SEM images of LiVPO4F/C synthesized at different temperatures. Obviously, the samples obtained at 730 and 750°C possess a porous morphology, and the latter has a more uniform pore diameter. In contrast, those calcined at lower temperatures (690 and 710°C) are not porous, since there are lots of unreacted LiF particles left on the surface of the samples. At 770°C, all pores disappear due to aggregation. Figure 5 shows SEM images of Li3V2(PO4)3/C synthesized at different temperatures. Although the XRD results (Figure 3b) do not show a significant difference between these samples calcined at different temperatures, they can be clearly distinguished from each other in the SEM images, indicating that the porous VPO4/C and Li3PO4 start to react at around 650°C. With an increase in temperature, the particles coarsen since the high temperature can accelerate the growth rate of particles. When calcined at 750°C, the particles display irregular shapes and are uniformly dispersed on the carbon network. As the temperature reaches 800°C, the particles agglomerate seriously. Hence, the optimal calcination temperature for synthesis of LiVPO4F/C and Li3V2(PO4)3/C is 750°C.
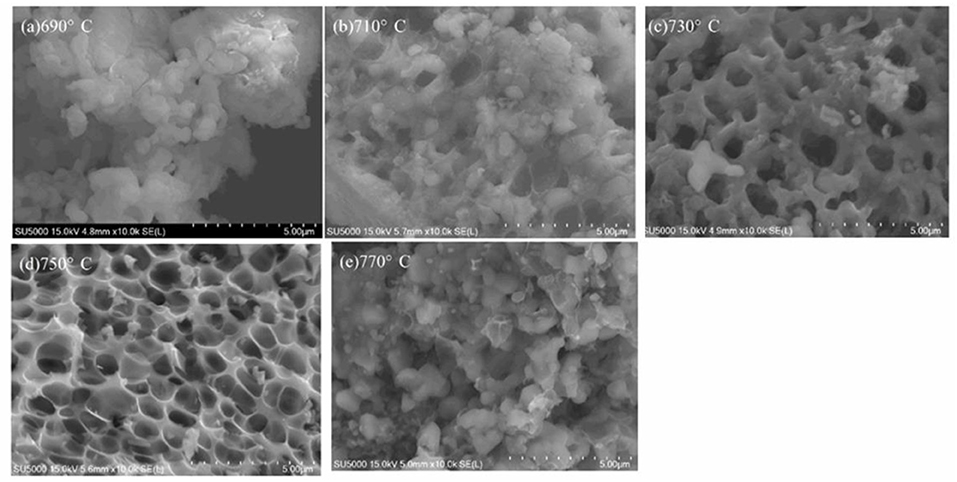
Figure 4. SEM images of LiVPO4F/C synthesized at different temperatures. (a) 690°C; (b) 710°C; (c) 730°C; (d) 750°C; (e) 770°C.
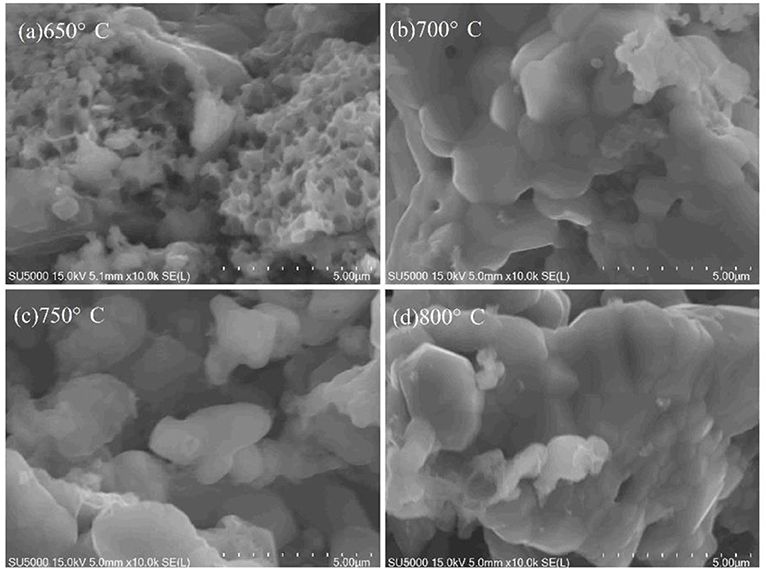
Figure 5. SEM images of Li3V2(PO4)3/C synthesized at different temperatures. (a) 650°C; (b) 700°C; (c) 750°C; (d) 800°C.
Based on the above analysis, 2LiVPO4F·Li3V2(PO4)3/C was chosen to be synthesized at 750°C. The XRD pattern of the as-prepared 2LiVPO4F·Li3V2(PO4)3/C is shown in Figure 6. It can be seen that all diffraction peaks can be indexed to LiVPO4F and Li3V2(PO4)3, and no impurity is detected. Moreover, characteristic peaks of crystalline carbon cannot be spotted, suggesting that carbon is amorphous in the composite.
Figure 7 displays SEM images of the as-prepared 2LiVPO4F·Li3V2(PO4)3/C. The composite is composed of porous particles with a pore diameter of 0.5–2 μm and nanosheets with a thickness of 200–500 nm. Furthermore, the amorphous carbon can be clearly observed. This uniform morphology of this material could facilitate ion transportation.
The electrochemical performance of the as-prepared materials was tested using galvanostatic charge-discharge in the voltage range of 3.0–4.5 V. The initial discharge curves (Figure 8A) and the cycling performances (Figure 8B) of the LiVPO4F/C samples were revealed. The one calcined at 750°C delivers the highest initial discharge capacity of 141.1 mAh g−1 at 0.1 C. After 50 cycles, the remaining capacity can be as high as 125.9 mAh g−1, with a capacity retention of 89.22%. The samples calcined at 690, 710, 730, and 770°C display capacities of 90.4, 114.8, 122.3, and 123.9 mAh g−1 at 0.1 C, respectively. The corresponding capacity retention rates after 50 cycles are 37.30, 50.69, 51.43, and 69.57%. The samples calcined in the ranges of 710–770°C show the characteristic discharge plateaus of LiVPO4F, as well as the characteristic discharge plateaus of Li3V2(PO4)3 around 4.10, 3.68, and 3.58 V. For the sample calcined at 750°C, no diffraction peaks of Li3V2(PO4)3 are detected in the XRD pattern, but it indeed shows the characteristic discharge plateaus. This is due to the very tiny amount of Li3V2(PO4)3 in this sample. Moreover, this sample has a good three-dimensional porous structure, which provides pathways for Li-ion transportation, consequently enhancing the cycling performance.
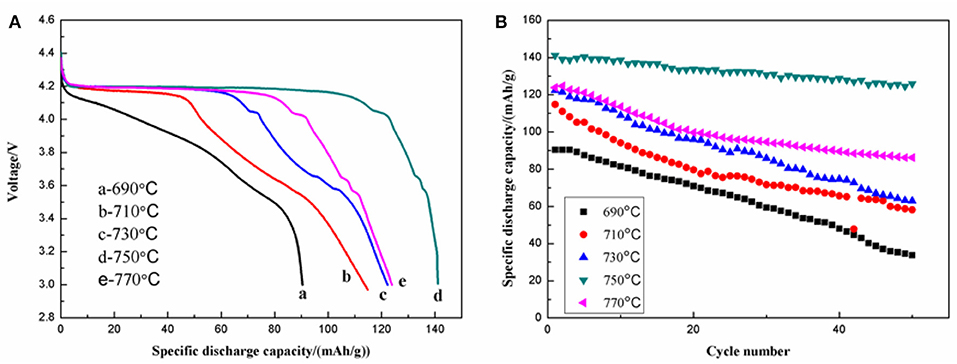
Figure 8. Initial discharge curves (A) and cycling performance (B) of LiVPO4F/C synthesized at different temperatures.
The initial discharge curves at various discharge rates of the LiVPO4F/C samples synthesized at different temperatures are illustrated in Figure 9. The one calcined at 750°C shows a better rate capability than the others. For example, the initial discharge capacities at 0.1, 0.2, 0.5, 1, and 2 C are 141.1, 125.2, 106.3, 87.9, and 71.5 mAh g−1, respectively. The discharge plateau around 4.17 V becomes lower and shorter with an increase in discharge rate, indicating that the high current density enlarges the resistance of the electrochemical reactions.
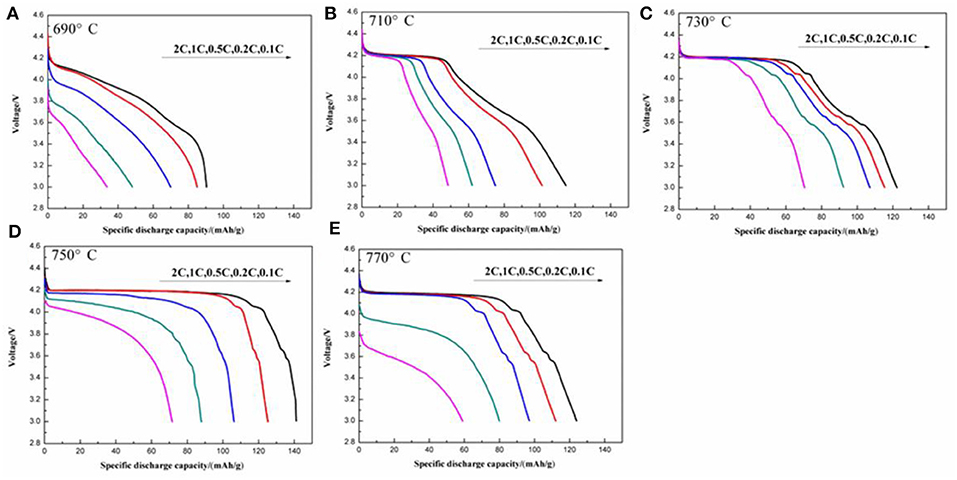
Figure 9. Initial discharge curves at different discharge rates of the LiVPO4F/C synthesized at different temperatures. (A) 690°C; (B) 710°C; (C) 730°C; (D) 750°C; (E) 770°C.
Figure 10 shows the initial discharge curves (Figure 10A) and the cycling performance (Figure 10B) of Li3V2(PO4)3/C. The samples calcined at 650, 700, 750, and 800°C show initial discharge capacities of 95.3, 128.0, 136.1, and 128.5 mAh g−1, respectively. After 50 cycles, the remaining capacities are 55.5, 92.2, 131.9, and 111.4 mAh g−1, with corresponding capacity retentions of 58.2, 72.0, 96.9, and 86.7%. Compared with the samples calcined at 650, 700, and 800°C, the one calcined at 750°C shows more stable discharge plateaus at 4.07, 3.68, and 3.58 V, suggesting suppressed polarization and a more stable structure.
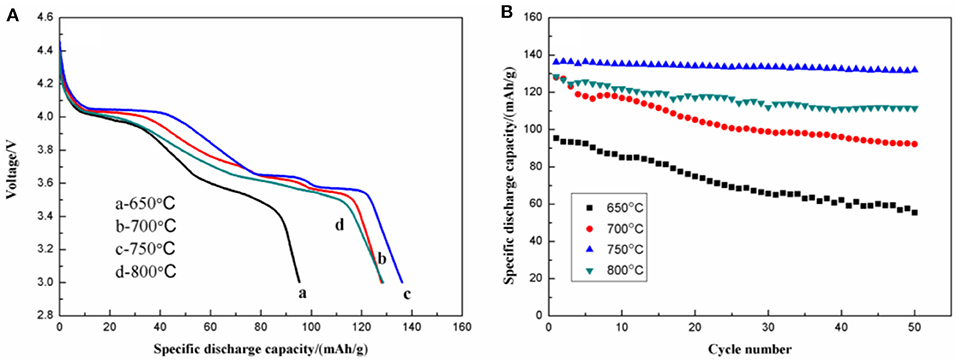
Figure 10. Initial discharge curves (A) and cycling performance (B) of the Li3V2(PO4)3/C synthesized at different temperatures.
Figure 11 shows the initial discharge curves at various discharge rates of the Li3V2(PO4)3/C synthesized at different temperatures. The one calcined at 750°C delivers the highest discharge capacity. When tested under rates of 0.1, 0.2, 0.5, 1, and 2 C, it shows discharge capacities of 136.1, 138.8, 130.2, 124.4, and 115.7 mAh g−1, respectively. Moreover, the discharge plateaus are stable even under higher current density.
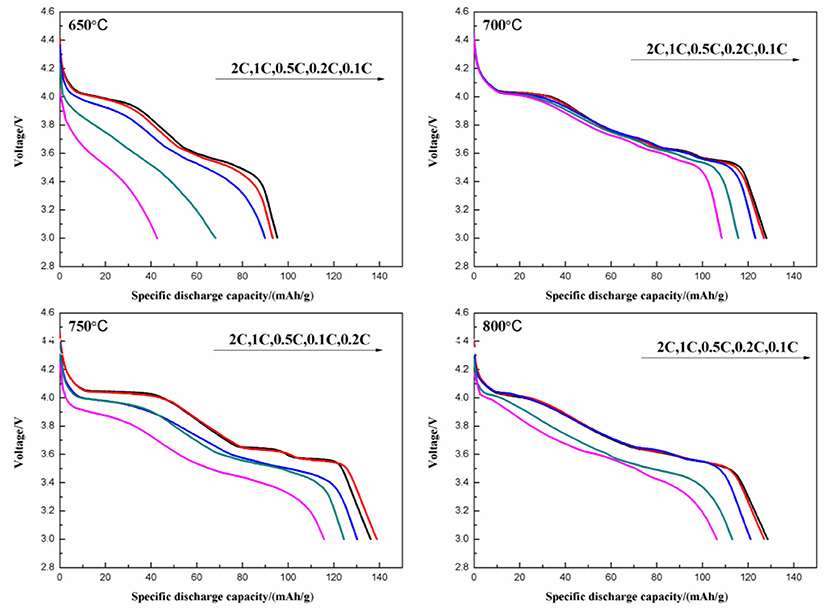
Figure 11. Initial discharge curves at different discharge rates of Li3V2(PO4)3/C synthesized at different temperatures.
Figure 12 shows the electrochemical properties of 2LiVPO4F·Li3V2(PO4)3/C. The initial discharge curves at different discharge rates (Figure 12A) show that this composite delivers a significantly improved electrochemical performance in comparison with LiVPO4F/C and Li3V2(PO4)3/C. For instance, 2LiVPO4F·Li3V2(PO4)3/C has an initial discharge capacity of 143.1 mAh g−1 at 0.1 C (1 C = 156 mA g−1), which is higher than that of the other materials. With an increase in current density, the capacity fading is minor. When tested at 0.2, 0.5, 1, and 2 C, the discharge capacities are 141.6, 133.2, 124.1, and 117.6 mAh g−1, respectively. The discharge curves show four plateaus. The one around 4.2 V is attributed to the discharge of LiVPO4F, and the others around 4.1, 3.7, and 3.6 V are due to the discharge of Li3V2(PO4)3. Figure 12B shows the rate capability of the composite. After being successively tested at 0.1 and 0.2 C for 5 cycles and 0.5, 1, and 2 C for 10 cycles (40 cycles in total), the discharge capacity can be almost fully recovered when the discharge rate returns to 0.1 C.
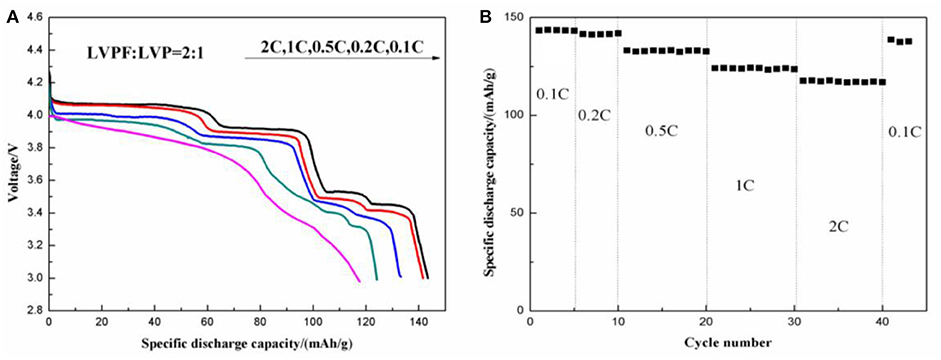
Figure 12. Initial discharge curves at different discharge rates (A) and rate capability (B) of the as-prepared 2LiVPO4F·Li3V2(PO4)3/C.
In order to study the lithiation/delithiation processes of 2LiVPO4F·Li3V2(PO4)3/C, a CV test was implemented; the results are shown in Figure 13. The anodic peaks at 4.22 and 4.44 V and the cathodic peak at 4.08 V correspond to the reversible redox of V3+/V4+ in LiVPO4F. The potential difference is 0.36 V. Moreover, the anodic peaks at 3.62, 3.71, and 4.15 V and the corresponding cathodic ones at 3.51, 3.61, and 3.97 V are due to the multi-step Li-ion extraction/insertion in Li3V2(PO4)3. The potential differences are 0.11, 0.10, and 0.18 V. Apparently, the polarization in Li3V2(PO4)3 is much smaller than that in LiVPO4F. Hence, a moderate amount of Li3V2(PO4)3 could suppress the polarization in the xLiVPO4F·yLi3V2(PO4)3/C composite, consequently enhancing the electrochemical performance.
Conclusions
In summary, xLiVPO4F·yLi3V2(PO4)3/C (x:y = 1:0, 2:1, 0:1) composites were successfully synthesized via a feasible sol-gel method. Our results indicate that the composites are well-crystallized and composed of porous particles. 2LiVPO4F·Li3V2(PO4)3/C outperforms LiVPO4F/C and Li3V2(PO4)3/C due to the synergy between the fluorophosphate and phosphate. This study presents a facile approach in synthesizing xLiVPO4F·yLi3V2(PO4)3/C for high-performance cathode materials of LIBs.
Data Availability Statement
The datasets generated for this study are available on request to the corresponding author.
Author Contributions
SZ, XZ, and JL did the main experiment and wrote the manuscript. JL and YS were involved the discussion of the experiment, revised the manuscript, and made the research plan. XZ assisted in the material synthesis. SZ and YS also provided the financial support.
Funding
This study was supported by the National Natural Science Foundation of China (51774207, 51904194), the Scientific Research Foundation of Hainan Tropical Ocean University (No. RHDRC202002), Prospective Applied Research from the Technological Innovation Project of Key Industry of Suzhou (SYG201931), and the Natural Science Research of Jiangsu Higher Education Institutions of China (19KJB450001).
Conflict of Interest
The authors declare that the research was conducted in the absence of any commercial or financial relationships that could be construed as a potential conflict of interest.
References
Abou-Rjeily, J., Bezza, I., Laziz, N. A., Autret-Lambert, C., Sougrati, M. T., and Ghamouss, F. (2019). High-rate cyclability and stability of LiMn2O4 cathode materials for lithium-ion batteries from low-cost natural β-MnO2. Energy Storage Mater. 26, 423–432. doi: 10.1016/j.ensm.2019.11.015
Barker, J., Saidi, M. Y., and Swoyer, J. L. (2003). Electrochemical insertion properties of the novel lithium vanadium fluorophosphates. J. Electrochem. Soc. 150, A1394–A1398. doi: 10.1149/1.1609998
El-Bana, M. S., El Radaf, I. M., Fouad, S. S., and Sakr, G. B. (2017). Structural and optoelectrical properties of nanostructured LiNiO2 thin films grown by spray pyrolysis technique. J. Alloy. Compd. 705, 333–339. doi: 10.1016/j.jallcom.2017.02.106
Goodenough, J. B., and Park, K. S. (2013). The Li-ion rechargeable battery: a perspective. J. Am. Chem. Soc. 135, 1167–1176. doi: 10.1021/ja3091438
Gover, R. K. B., Burns, P., Bryan, A., Saidi, M. Y., Swoyer, J. L., and Barker, J. (2006). LiVPO4F: A new active material for safe lithium-ion batteries. Solid State Ion. 177, 2635–2638. doi: 10.1016/j.ssi.2006.04.049
Hariprasad, K., Naresh, N., Nageswara Rao, B., Venkateswarlu, M., and Satyanarayana, N. (2016). Preparation of LiMn2O4 nanorods and nanoparticles for lithium-ion battery applications. Mater. Today Proc. 3, 4040–4045. doi: 10.1016/j.matpr.2016.11.070
Hu, G., Gan, Z., Cao, Y., Peng, Z., Lu, Y., and Du, K. (2019). Multi-level carbon co-modified LiVPO4F cathode material for lithium batteries. J. Alloy. Compd. 788, 1146–1153. doi: 10.1016/j.jallcom.2019.02.323
Huang, H., Faulkner, T., and Saidi, M. Y. (2009). Lithium metal phosphates, power and automotive applications. J. Power Sources 189, 748–751. doi: 10.1016/j.jpowsour.2008.08.024
Jiang, S. (2018). Ultrafine Li3V2(PO4)3 crystals adhered to P-doped graphene sheets for electrochemical lithium storage. Solid State Ionics 326, 58–62. doi: 10.1016/j.ssi.2018.09.005
Karami, H., and Taala, F. (2011). Synthesis, characterization and application of Li3Fe2(PO4)3 nanoparticles as cathode of lithium-ion rechargeable batteries. J. Power Sources 196, 6400–6411. doi: 10.1016/j.jpowsour.2011.03.079
Kim, M., and Kang, B. (2017). Highly-pure triplite 3.9V-LiFeSO4F synthesized by a single-step solid-state process and its high electrochemical performance. Electrochim. Acta 228, 160–166. doi: 10.1016/j.electacta.2017.01.073
Li, R., Sun, S., Liu, J., Chen, T., Dai, C., and Ding, F. (2019). From rational construction to theoretical study: Li3V2(PO4)3 nanoplates with exposed {100} facets for achieving highly stable lithium storage. J. Power Sources 442:227231. doi: 10.1016/j.jpowsour.2019.227231
Li, Y., Wang, J., Yao, J., Huang, H., Du, Z., Gu, H., et al. (2019). Enhanced cathode performance of LiFePO4/C composite by novel reaction of ethylene glycol with different carboxylic acids. Mater. Chem. Phys. 224, 293–300. doi: 10.1016/j.matchemphys.2018.12.042
Lin, J., Zeng, C., Wang, L., Pan, Y., Lin, X., Reddy, R. C. K., et al. (2020). Self-standing MOF-derived LiCoO2 nanopolyhedron on Au-coated copper foam as advanced 3D cathodes for lithium-ion batteries. Appl. Mater. Today 19:100565. doi: 10.1016/j.apmt.2020.100565
Nitta, N., Wu, F., Lee, J. T., and Yushin, G. (2015). Li-ion battery materials: present and future. Mater. Today 18, 252–264. doi: 10.1016/j.mattod.2014.10.040
Sui, Y., Chen, W., Tang, S., Wu, L., Wang, B., Li, H., et al. (2019a). Spray-drying synthesis of LiFeBO3/C hollow spheres with improved electrochemical and storage performances for Li-ion batteries. Front. Chem. 7:379. doi: 10.3389/fchem.2019.00379
Sui, Y., Wu, L., Hong, W., Liu, J., Zhang, X., Li, W., et al. (2019b). Synthesis and electrochemical properties of spherically shaped LiVPO4F/C cathode material by a spray drying-roasting method. Rare Met. doi: 10.1007/s12598-019-01340-0
Uddin, M., Alaboina, P. K., and Cho, S. (2017). Nanostructured cathode materials synthesis for lithium-ion batteries. Mater. Today Energy 5, 138–157. doi: 10.1016/j.mtener.2017.06.008
Vásquez, F. A., and Calderón, J. A. (2019). Vanadium doping of LiMnPO4 cathode material: correlation between changes in the material lattice and the enhancement of the electrochemical performance. Electrochim. Acta 325:134930. doi: 10.1016/j.electacta.2019.134930
Wu, L., Zheng, J., Wang, L., Xiong, X., Shao, Y., Wang, G., et al. (2019). PPy-encapsulated SnS2 nanosheets stabilized by defects on a TiO2 support as a durable anode material for lithium-ion batteries. Angew. Chem. Int. Edit. 58, 811–815. doi: 10.1002/anie.201811784
Wu, X., Meledina, M., Tempel, H., Kungl, H., Mayer, J., and Eichel, R. (2020). Morphology-controllable synthesis of LiCoPO4 and its influence on electrochemical performance for high-voltage lithium ion batteries. J. Power Sources 450:227726. doi: 10.1016/j.jpowsour.2020.227726
Zhang, S., Gu, Q., Tan, S., and Zhao, L. (2019). Improved electrochemical properties of the Li3V2(PO4)3 cathode material synthesized from a V(III) precursor. J. Alloy. Compd. 802, 583–590. doi: 10.1016/j.jallcom.2019.06.240
Zhao, H., Wang, J., Wang, G., Liu, S., Tan, M., Liu, X., et al. (2017). Facile synthesis of orthorhombic LiMnO2 nanorods by in-situ carbothermal reduction: promising cathode material for Li ion batteries. Ceramics Int. 43, 10585–10589. doi: 10.1016/j.ceramint.2017.04.158
Zheng, J., Han, Y., Sun, D., Zhang, B., and Cairns, E. J. (2017). In situ-formed LiVOPO4@V2O5 core-shell nanospheres as a cathode material for lithium-ion cells. Energy Storage Mater. 7, 48–55. doi: 10.1016/j.ensm.2016.12.003
Zheng, J., Han, Y., Tang, L., and Zhang, B. (2016). Investigation of phase structure change and electrochemical performance in LiVP2O7-Li3V2(PO4)3-LiVPO4F system. Electrochim. Acta 198, 195–202. doi: 10.1016/j.electacta.2016.03.070
Keywords: lithium-ion batteries, cathode material, LiVPO4F, Li3V2(PO4)3, electrochemical performance
Citation: Zhong S, Zhang X, Liu J and Sui Y (2020) Study on xLiVPO4F·yLi3V2(PO4)3/C Composite for High-Performance Cathode Material for Lithium-Ion Batteries. Front. Chem. 8:361. doi: 10.3389/fchem.2020.00361
Received: 18 February 2020; Accepted: 07 April 2020;
Published: 08 May 2020.
Edited by:
Lingjun Li, Changsha University of Science and Technology, ChinaReviewed by:
Dongliang Yan, Guilin University of Electronic Technology, ChinaJunchao Zheng, Central South University, China
Bin Huang, Guilin University of Technology, China
Copyright © 2020 Zhong, Zhang, Liu and Sui. This is an open-access article distributed under the terms of the Creative Commons Attribution License (CC BY). The use, distribution or reproduction in other forums is permitted, provided the original author(s) and the copyright owner(s) are credited and that the original publication in this journal is cited, in accordance with accepted academic practice. No use, distribution or reproduction is permitted which does not comply with these terms.
*Correspondence: Jiequn Liu, bGl1amllcXVuMjAyMEAxNjMuY29t; Yulei Sui, c3VpeXVsZWlAc3VkYS5lZHUuY24=