- 1School of Physics and Electronic Information/Information College, Huaibei Normal University, Huaibei, China
- 2School of Life Science, Huaibei Normal University, Huaibei, China
In this study, micro/nanoscale LiFePO4/graphene composites are synthesized successfully using a one-step microwave heating method. One-step microwave heating can simplify the reduction step of graphene oxide and provide a convenient, economical, and effective method of preparing graphene composites. The structural analysis shows that LiFePO4/graphene has high phase purity and crystallinity. The morphological analysis shows that LiFePO4/graphene microspheres and micron blocks are composed of densely aggregated nanoparticles; the nanoparticle size can shorten the diffusion path of lithium ions and thus increase the lithium-ion diffusion rate. Additionally, the graphene sheets can provide a rapid transport path for electrons, thus increasing the electronic conductivity of the material. Furthermore, the nanoparticles being packed into the micron graphene sheets can ensure stability in the electrolyte during charging and discharging. Raman analysis reveals that the graphene has a high degree of graphitization. Electrochemical analysis shows that the LiFePO4/graphene has an excellent capacity, high rate performance, and cycle stability. The discharge capacities are 166.3, 156.1, 143.0, 132.4, and 120.9 mAh g−1 at rates of 0.1, 1, 3, 5, and 10 C, respectively. The superior electrochemical performance can be ascribed to the synergy of the shorter lithium-ion diffusion path achieved by LiFePO4 nanoparticles and the conductive networks of graphene.
Introduction
Energy and materials, important pillars of the modern developing society, are closely related to human civilization. Rechargeable lithium-ion batteries, an environmentally friendly and new green energy, have wide applicability in the fields of energy storage and transportation (Song et al., 2018). The ever-increasing demand for high current charge-discharge capability, high energy density, and long service life has driven the development of the lithium battery industry (Zhou et al., 2019). Olivine phase lithium iron phosphate (LiFePO4) is one of the focused cathode materials in lithium-ion batteries (Padhi et al., 1997a,b). It has many superior properties, such as that Fe is low-cost and environmentally benign, that the covalently bonded PO4 groups make the chemical properties more stable and prolong service lifetime, and that it has a high theoretical capacity (170 mAhg−1) and flat voltage plateau (3.45 V vs. Li/Li+). However, LiFePO4 materials have some drawbacks, such as inferior electronic conductivity (ca.10−9–10−10 Scm−1) as well as slow one-dimensional lithium ion diffusion, which is a formidable obstacle to the high performance of lithium-ion batteries (Goodenough and Kim, 2010; Dathar et al., 2011). A considerable number of methods have been adopted with the aim of alleviating the above shortcomings. These methods can be categorized into two main classes: particle size control (Prosini et al., 2003; Zhao et al., 2016) and conductive material coating (Chang et al., 2019; Han et al., 2019; Ma et al., 2019; Tao et al., 2019).
Small particle size can decrease the migration distance of lithium ions from the interior to the surface and increase the diffusion rate (Lim et al., 2008; Hai et al., 2019; Li et al., 2019; Xiao et al., 2019). Various techniques, including solid-state reaction (Zheng et al., 2008), sol-gel (Zhang et al., 2011) hydrothermal (Kiyoshi et al., 2008; Chang et al., 2014), co-precipitation (Park et al., 2003; Wang et al., 2013), and microwave heating (Wang et al., 2007; Beninati et al., 2008; Guo et al., 2010), are adopted to control particle size. Moreover, surface coating with conductive material can increase the electronic conductivity between particles (Wang et al., 2010; Fathollahi et al., 2015; Ahn et al., 2019) and provide paths in all directions for the fast transmission of electrons (Wang et al., 2009; Jang et al., 2011; Fan et al., 2014). Graphene with high electrical conductivity has been adopted to improve the cycling stability and rate capability of cathode material (Ding et al., 2010; Zhou et al., 2011; Shi et al., 2012; Tang et al., 2012; Chen et al., 2018; Wang et al., 2018). Ding et al. (2010) prepared nano-structured LiFePO4/graphene using co-precipitation and sintering at 700°C for 18 h under argon flow. Shi et al. (2012) prepared graphene-wrapped LiFePO4/C using a microwave-assisted hydrothermal method, followed by sintering at 600°C for 2 h under H2/Ar flow. Zhou et al. (2011) first synthesized LiFePO4 nanoparticles by a hydrothermal method and then synthesized LiFePO4/graphene from LiFePO4 nanoparticles and graphene oxide nanosheets by spray-drying and annealing processes. Tang et al. (2012) synthesized LiFePO4/graphene by mixing three-dimensional graphene prepared by chemical vapor deposition and LiFePO4 prepared by solid-state reaction in a N-methyl pyrrolidinone (NMP) suspension. The above experimental methods are very complicated, and most of them require long-term high-temperature treatment and atmosphere protection, which lead to high energy consumption and cost. Additionally, the graphene and active materials agglomerate easily and distribute unevenly. Therefore, simplifying the preparation technology and obtaining a product with a small and homogeneous distribution remain great challenges for preparing LiFePO4/graphene composites. Microwave heating is a convenient, economical, and environmentally friendly route for the preparation of graphene composites in a way that addresses the deficiency of graphene modification. Microwave heating can simplify the reduction step of graphene oxide, as, due to the microwave-absorbing properties of graphene oxide, microwave irradiation can restore it into graphene directly without any reductive agent and atmosphere.
In this work, micro/nanoscale LiFePO4/graphene composites are synthesized successfully using a one-step microwave heating method. The synthesis technique has a decisive influence on the structure, morphology, and electrochemical properties of the LiFePO4 product. Microwave synthesis can save synthesis time; this is because the raw material can absorb microwave energy by itself and convert electromagnetic energy into heat and internal molecular kinetic energy, thus improving the diffusion coefficient and accelerating the reaction rate. Meanwhile, microwave synthesis can lower the synthesis temperature; this is because the electromagnetic field decreases the activation energy of the reaction. Therefore, microwave heating is a rapid and effective synthetic method for preparing a product with small particle size. Furthermore, unlike in complex, multi-step preparation processes, microwave irradiation can restore the graphene oxide into graphene directly without any reductive agent and atmosphere. The synthesized micro/nanoscale LiFePO4/graphene composites with fine particle size and uniform distribution can decrease the migration distance of lithium ions from the interior to the surface and increase the diffusion rate. Meanwhile, graphene wrapping of the surface of LiFePO4 particles can guarantee that the electrons migrate to the active sites quickly. Controlling the particle size and coating with graphene play important roles in the electrochemical performance. The effects of graphene and microwave irradiation on the electrochemical performance of LiFePO4/graphene cathode materials for lithium-ion batteries are further investigated.
Experimental
Preparation of Materials
FeSO4·7H2O (99%), LiOH·H2O (95%), H3PO4 (85%), ethylene glycol, and sucrose were purchased from Sinopharm Chemical Reagent Co. Ltd. Graphene oxide was synthesized from natural graphite powder (325 mesh) using a modified Hummers' method (Kovtyukhova et al., 1999; Stankovich et al., 2007).
The LiFePO4/graphene and LiFePO4/C composites were synthesized via the following steps. FeSO4·7H2O and H3PO4 were dissolved in a mixed solution of de-ionized water and ethylene glycol, and GO suspension was added to the solution. Next, a mixture of LiOH·H2O aqueous solution and GO suspension was added into the mixed solution under constant stirring. The molar ratio of Li:Fe:P is 3:1:1. After stirring for 3 h, the solution was evaporated at 80°C for 12 h. Meanwhile, a separate sample was prepared with the GO suspension replaced by sucrose as the source of carbon, and the previous steps were repeated. Finally, the precursors obtained were pressed into pellets, and then the pellets were placed inside a quartz crucible with a cover to prevent air oxidation. The quartz crucible was put in the middle of the domestic microwave oven, and the precursors were radiated by microwave for 10 min with a maximum power of 1,500 W and a frequency of 2.45 GHz. After microwave irradiation, LiFePO4/graphene and LiFePO4/C composites were obtained, respectively.
Characterization Techniques
The structures of LiFePO4/graphene and LiFePO4/C composites were investigated using an X-ray diffractometer (X'pert PRO, Panalytical, Holland) with Cu Kα radiation operated at 40 kV and 40 mA. The contents of graphene and carbon in the LiFePO4/graphene and LiFePO4/C composites were calculated from TG-DSC (STA449F3, NETZSCH, Germany), which was carried out from room temperature to 700°C under an air atmosphere at a rate of 10°C min−1. The morphologies of LiFePO4/graphene composites were observed using a scanning electron microscope (SEM, JSM-IT300 at 20 kV) and transmission electron microscopy (TEM, JEM2100F Japan at 200 kV). The Raman spectra of LiFePO4/graphene and LiFePO4/C composites were recorded from 100 to 3,200 cm−1 on a Renishaw Raman microprobe (INVIA, China) using a 514.5 nm argon-ion laser at room temperature.
Cell Fabrication and Electrochemical Measurement
The electrochemical behaviors of the LiFePO4/graphene and LiFePO4/C composites were evaluated with 2,025 coin-type batteries. The cathode electrodes were prepared by mixing 80 wt% active materials (LiFePO4/graphene or LiFePO4/C) and 10 wt% carbon black (TIMCAL) with 10 wt% polytetrafluoroethylene (PTFE, Aldrich) in isopropyl alcohol solution (99.5%, Aldrich). A uniform slurry was formed and pasted onto Al foils, dried at 120°C for 12 h, and then cut into circular electrodes with a diameter of 10 mm. Lithium metal (99.9%, Alfa-Aesar) was used as the anode, Celgard polypropylene (Celgard 2400) as the separator, and 1M LiPF6 dissolved in ethylene carbonate and dimethyl carbonate (with a 1:1 volume ratio) as the electrolyte (MERCK KGaA, Germany). The cells were assembled in an argon-filled glove box (Etelux Lab2000, China). Cells were charged and discharged at room temperature using a LAND-CT2001A battery cycler (Wuhan, China) within the voltage range of 2.7–4.2 V (vs. Li+/Li). Cyclic voltammetry (CV) was performed with an Auto Potentiostat 30 system at a scan rate of 0.1 mVs−1 between 2.5 and 4.2 V. Electrochemical impedance spectroscopy (EIS) profiles were obtained at the same open-circuit voltage by applying a 5-mV amplitude of the AC voltage with the frequency ranging from 100 kHz to 0.01 Hz.
Results and Discussion
Phase Structural Analysis
The phase constitution and crystal structure of the synthetic LiFePO4/graphene and LiFePO4/C composites are here investigated. XRD patterns of the composites are shown in Figure 1. It can be seen that there is no noticeable difference between LiFePO4/graphene and LiFePO4/C composites. All the sharp diffraction peaks corresponding to the (200), (101), (210), (011), (111), (211), (301), (311), (121), (410), (221), (401), (112), (222), and (123) planes can be indexed to the orthorhombic olivine-type structure LiFePO4 with the Pnma space group (JCPDS card No. 83-2092) (Wang et al., 2009, 2010), and no excess impurity peaks are observed. The results manifest that the synthetic composites have high crystallinity and purity; this is mainly because microwave synthesis has the advantage of increasing the crystallinity and purity of products. The diffraction pattern of LiFePO4/graphene shows that no diffraction peak of graphene oxide (at around 12°) is observed, proving that the graphene oxide has already been reduced into graphene directly without any reducing agent or atmosphere. This is mainly because the graphene oxide with a large amount of oxygen functional groups on the surface that can absorb microwaves easily, and electromagnetic energy is converted into heat and molecular kinetic energy; the reactive oxygen groups are then exfoliated, and, finally, the graphene oxide is restored into graphene. Also, the introduction of graphene has no effect on the structure of LiFePO4. Moreover, the diffraction pattern of LiFePO4/C shows no diffraction peaks corresponding to residual carbon, indicating that the carbon decomposed from sucrose in the sample exists in an amorphous state.
TG-DSC Analysis
TG-DSC measurement data is used to estimate the graphene and carbon content in the LiFePO4/graphene and LiFePO4/carbon composites, as shown in Figure 2. The pure LiFePO4 can be completely oxidized to Li3Fe2(PO4)3 and Fe2O3 under air flow, and the total weight gain is about 5.07% in theory (Belharouak et al., 2005; Bai et al., 2015). For LiFePO4/graphene and LiFePO4/carbon composites, in the temperature range of 400–600°C, the graphene and carbon are oxidized to CO2 gas, so the amounts of graphene and carbon in the LiFePO4/graphene and LiFePO4/carbon composites are about 1.40 and 10.70%, respectively.
Raman Analysis
Raman scattering spectroscopy was employed to recognize the chemical structure of the LiFePO4/graphene and LiFePO4/C composites; the results are shown in Figure 3. The main vibration modes include internal modes attributable to anions and external modes attributable to the coupled motion of Fe2+ and (Markevich et al., 2011). The modes at 990, 1,058, and 945 cm−1 correspond to the anti-symmetric (ν3) and symmetric (ν1) stretching of the P–O bonds. The modes at 626 and 587 cm−1 correspond to the symmetric (ν2) and anti-symmetric (ν4) bending of the O-P-O angles. The mode at 395 cm−1 corresponds to the lithium cage and oxygen ion breathing cage. The modes in the 100–300 cm−1 range are induced by translation of Fe and coupled translation and vibration of Fe and (Burba and Frech, 2004; Wu et al., 2013). Moreover, there are two obvious D band peaks at around 1,310 cm−1 and a G band at around 1,590 cm−1 (Tuinstra and Koenig, 1970). The D band is induced by a disordered and defective carbon structure in the crystal plane of the short-order sp2 and sp3 carbon. The G band is assigned to the in-plane bond-stretching motion of sp2 carbon atoms. The intensity ratio of the D and G bands (ID/IG) is inversely proportional to the degree of graphitization of carbon materials. The ID/IG in LiFePO4/graphene composites is 1.18, while the ID/IG in LiFePO4/C composites is 1.43. This implies that the graphene has a higher degree of graphitization than the carbon decomposed from sucrose. The higher the degree of graphitization, the better the conductivity of the carbon. A high degree of graphitization is favorable for electron transfer and improves the electrochemical performance of the cathode. Additionally, the strong signals of the graphene (D band and G band) weaken and override the bands of LiFePO4 in the high-frequency region.
Morphological Analysis
SEM images of the graphene oxide and LiFePO4/graphene are shown in Figures 4A–F. Figure 4A shows that the micron-scale graphene oxide sheets aggregate into petal shapes; these sheets can provide implantation sites for the adhesion of reaction particles. Figures 4B,C clearly shows that the LiFePO4/graphene composites are composed of micron-scale spheres and blocks with average dimensions of ~2 μm. In Figures 4D–F, it can be clearly observed that these LiFePO4/graphene microspheres and micron blocks are composed of densely aggregated nanoparticles. This structure forms because the self-heating effect induced by the microwave heating can greatly shorten the reaction time, and the graphene wrapping the surface of LiFePO4 particles can inhibit the growth of grains. Under the action of graphene, the nanoparticles assembled into microspheres and micron blocks. When the highly conductive electrolyte penetrates into the cathode material, the nanoparticles have a high specific surface area, which increases the contact area with the electrolyte. The nanoparticle size can shorten the diffusion paths of electrons and lithium ions and improve the conductivity of the cathode material significantly. Moreover, the micron structure formed by the aggregation of nanoparticles does not collapse during the process of lithium-ion intercalation and deintercalation, which ensures the stability of cathode material in the electrolyte. TEM and HRTEM images of the micron/nanoscale LiFePO4/graphene composite are shown in Figures 4G,H. The ultrathin graphene sheets successfully form an effective conducting network and intrinsically bridge and intimately connect the active LiFePO4 particles. Figure 4H indicates that the graphene sheets around LiFePO4 are highly graphitic. The highly efficient and stable conducting network can give the material desirable electrochemical properties. In the energy spectrum, elements of P, O, Fe, and C are found, as shown in Figure 4I; Li cannot be detected because of its very low atomic weight.
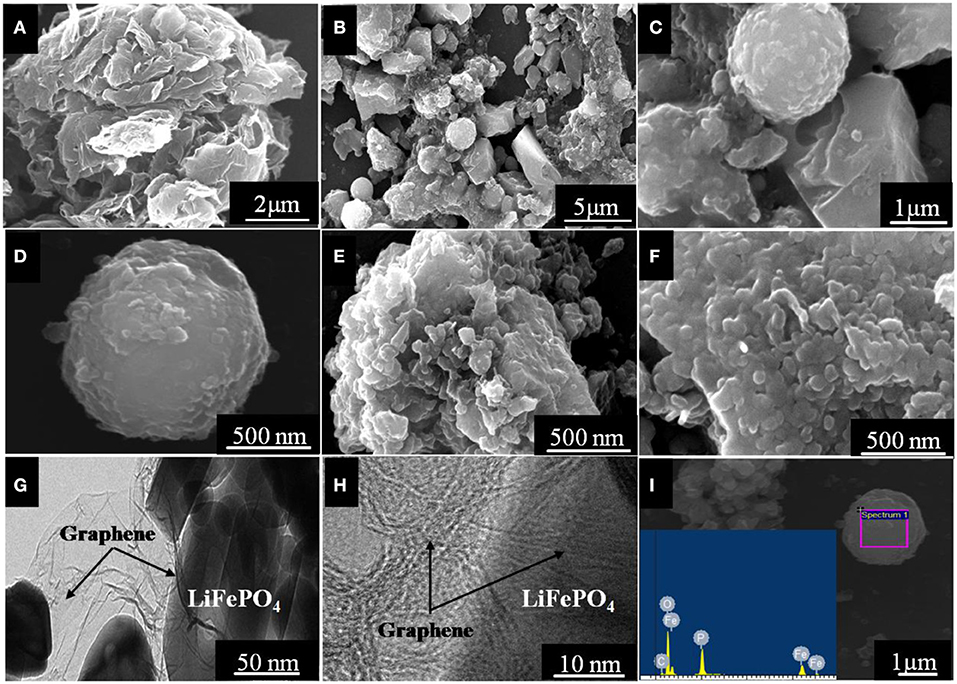
Figure 4. SEM images of the graphene oxide (A) and LiFePO4/graphene (B–F); TEM and HRTEM images of the LiFePO4/graphene composites (G,H); EDS spectra of the LiFePO4/graphene composites (I).
The formation process of the LiFePO4/graphene composites is illustrated in Figure 5. At the initial stage of the reaction, the chemical reaction follows a dissolution–precipitation mechanism. The iron ions, phosphate ions, and lithium ions in the solution react with each other and form agglomerated precipitate on the surface of the graphene oxide sheets, and a large number of active functional groups are adsorbed on the surface of graphene oxide. At the stage of microwave irradiation, the active functional groups, being polar molecules, can absorb microwave easily, and electromagnetic energy is converted into heat and molecular kinetic energy. The temperature increase quickly, the reactive oxygen groups are exfoliated, and, finally, the graphene oxide is restored into graphene. Meanwhile, the precipitated particles adsorbed on the surface of reduced graphene sheets become hot and absorb microwaves quickly, the particles interact with each other, and then crystal nuclei are formed quickly under the action of the microwave electromagnetic field. Finally, under the influence of micron graphene sheets, the crystal nuclei grow, agglomerate, and form microspheres and micron blocks.
Electrochemical Properties Analysis
A schematic diagram of LiFePO4/graphene electrode dynamics is shown in Figure 6. Transportation of electrons and ions (e− and Li+) from their “reservoirs” toward the LiFePO4 particles (Gaberscek et al., 2007; Gaberscek, 2009) is shown as step A. A charge incorporation reaction that involves the transfer of e− and Li+ from the outside into the interior of active particles is shown as step B, and the transport of the lithium component inside the solid active particles (solid-state diffusion) is shown as step C. It can be seen that graphene can provide a high-speed channel for the rapid diffusion of electrons and cause the electrons to reach the reactive site quickly, thus increasing the electronic conductivity of the materials. Meanwhile, the nanoparticles can shorten the transport path of Li+ from the surface to the interior of solid active particles and improve the diffusion coefficient of lithium ions. Moreover, the nanoparticles are surrounded by the micron graphene sheets, and the micron structure guards the stability of the material. Therefore, LiFePO4/graphene composites are expected to have excellent electrochemical performance.
Cyclic voltammetry was performed to investigate the electrochemical kinetics of LiFePO4/graphene and LiFePO4/C cathode materials. Figure 7 shows the CV spectra of the LiFePO4/graphene and LiFePO4/C composites. In the first scan, there is a pair of redox peaks corresponding to the Fe2+/Fe3+ couple (Ding et al., 2010; Zhou et al., 2011). The shapes of redox peaks are low and asymmetrical; this is because, in the first charging and discharging cycle, active materials are not completely saturated by electrolyte, and the pathways of lithium ion insertion and extraction were not completely formed. In the second scan, the current intensity increases, and the shape of the redox peaks becomes more symmetrical and sharper. For LiFePO4/graphene, the potential difference between the oxidation and reduction peaks decreases from 0.27 to 0.26 V, which means that the phase is stabilized in subsequent cycles. Figure 7B shows the CV spectra of LiFePO4/C composites. During the second scan, the potential difference increases from 0.31 to 0.33 V, which proves that detrimental polarization becomes more and more serious. The results show that LiFePO4/graphene composites have very high reversibility and better electrochemical activity.
The polarization of the LiFePO4/C electrode is explained by the electron transfer pathway, as shown in Figure 8A. The carbon is dispersed unevenly, so the electrons cannot reach the entire reactive site where the Li+ ions intercalate. In contrast, for LiFePO4/graphene, due to the one-dimensional Li+ ion mobility in the framework, the graphene can ensure that electrons reach particles from all directions and alleviate the polarization, as shown in Figure 8B. Therefore, the LiFePO4/graphene composites, with well-defined peaks and smaller potential difference, have higher electrochemical reactivity.
The charging and discharging capacity profiles of the LiFePO4/graphene and LiFePO4/C at progressively increasing C rates from 0.1 to 10 C are shown in Figure 9. The cells are cycled in the voltage window of 2.7–4.2 V at room temperature. For LiFePO4/graphene composites, the initial discharge capacity is 166.3 mAhg−1 at 0.1 C, and the discharge capacity decreases to 156.1 mAhg−1 with an increase in the discharge rate to 1 C. At a higher discharge rate of 5 C, the cell delivers a capacity of 132.4 mAhg−1. Even at a 10 C rate, the capacities can reach 120.9 mAhg−1, and a good voltage plateau remains above 3 V. For LiFePO4/C, the discharge capacity is 154.8, 133.8, 121.6, 105.9, and 86.4 mAh g−1 at 0.1, 1, 3, 5, and 10 C rates, respectively. The cycling performances of the LiFePO4/graphene and LiFePO4/C from 0.1 to 10 C are shown in Figure 10. Although for LiFePO4/graphene, the specific capacity decreases with increasing current rate, the capacity retention remains very good for all of the different rates; the discharge capacity retentions are, respectively, 99.5, 99.2, 99.4, 99.1, and 97.1% at 0.1, 1, 3, 5, and 10 C current rates after being cycled 10 times. While for LiFePO4/C, the discharge capacity retentions are, respectively, 97.7, 96.9, 93.0, 87.1, and 79.5% at 0.1, 1, 3, 5, and 10 C current rates. All of the results demonstrate that LiFePO4/graphene composites have better rate performance and cycling stability. This can be attributed to the excellent electrical conductivity of graphene, which can improve the conductivity and stability of materials.
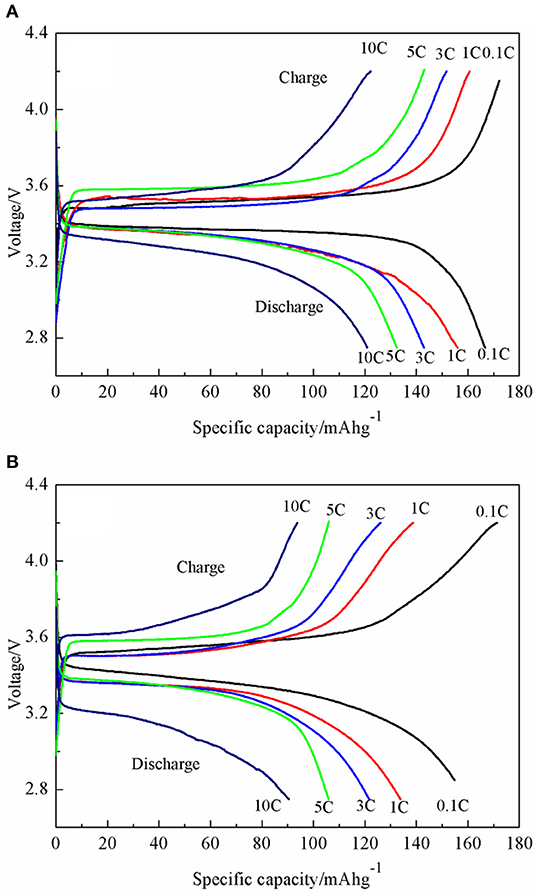
Figure 9. Charge/discharge profiles of LiFePO4/graphene (A) and LiFePO4/C (B) composites at various current rates ranging from 0.1 to 10 C.
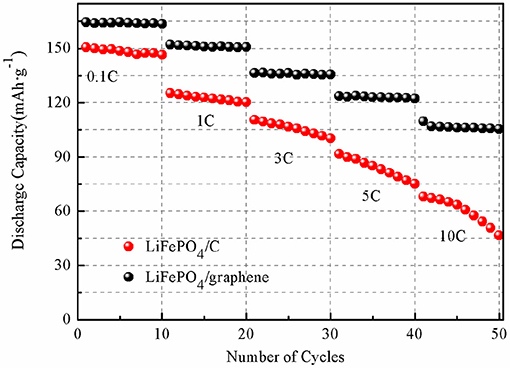
Figure 10. Cycling performances of LiFePO4/graphene (A) and LiFePO4/C (B) composites at various current rates ranging from 0.1 to 10 C.
Electrochemical impedance spectroscopy was used to investigate the electrochemical behaviors of LiFePO4/graphene and LiFePO4/C cathodes. Figure 11A shows the Nyquist plots of the LiFePO4/graphene and LiFePO4/C cathodes. The experimental EIS data is simulated by Zview2.1 software according to the equivalent circuit as shown in Figure 11B. It can be found that all the Nyquist plots present a high-frequency quasi-semicircle, which is related to the migration of the Li+ ions at the electrode/electrolyte interface and the charge transfer process. Meanwhile, a low-frequency sloping line is related to the Warburg impedance of the lithium-ion diffusion in the electrode (Zhang et al., 2011). RS is the internal resistance of the cell and corresponds to the electrodes, electrolyte, and the separator resistance, Rct is associated with the charge-transfer resistance, CPE is associated with the capacitance contributed by the surface of the active material (Guo et al., 2010). The simulation results show that the Rct value of the LiFePO4/graphene cathode is 79 Ω, which is smaller than the 129 Ω value of the LiFePO4/C cathode. The result shows that graphene can reduce the charge transfer resistance of Li-ion insertion and extraction between the electrode/electrolyte and increase the conductivity of the LiFePO4/graphene cathode.
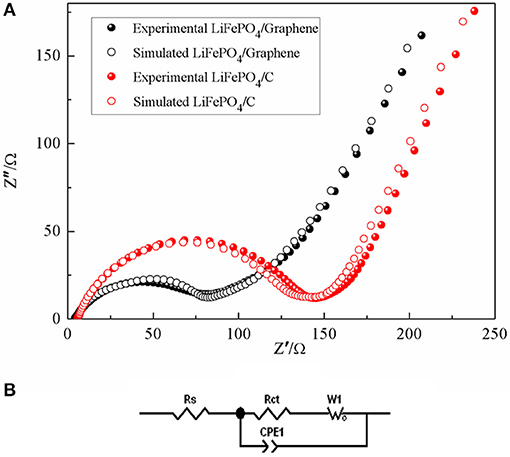
Figure 11. Experimental and simulated electrochemical impedance spectra of LiFePO4/graphene and LiFePO4/C composites (A); equivalent circuit (B).
Conclusion
A LiFePO4/graphene composite was successfully prepared as cathode material through one-step microwave heating. The graphene oxide, which has excellent microwave-absorbing properties, can react with microwaves quickly and be restored into high-quality graphene directly without any reducing agent or atmosphere. The introduction of graphene does not impact the structure of LiFePO4, and LiFePO4 nanoparticles are packed into micron graphene sheets. The graphene network, which has a high degree of graphitization, can provide a high-speed channel for the rapid transfer of electrons and thus increase the electronic conductivity of materials. Meanwhile, the nanoparticles can improve the diffusion coefficient of lithium ions. Moreover, because the nanoparticles are surrounded by the graphene sheets, the micron structure guards the stability of the material. The electrochemical analyses reveal that the LiFePO4/graphene composites have excellent high-rate performance and cycling life. The outstanding electrochemical performance, as well as the fast and efficient method, make this technology commercially viable.
Data Availability Statement
The datasets generated for this study are available on request to the corresponding author.
Author Contributions
SL, PY, and WS performed the experiments. SL, PY, HL, and XZ performed the data analysis. SL and PY wrote the paper. All authors contributed to the theoretical analysis and the general discussion.
Funding
This work was supported by the Program for Quality Engineering at School Level (2017jxcg01), Natural Science Foundation of Anhui Province (1708085QE119), Natural Science Foundation of Anhui Higher Education Institutions of China (KJ2015A314, KJ2017A393), and Collaborative Innovation Center of Advanced Functional Materials (XTZX103732016005).
Conflict of Interest
The authors declare that the research was conducted in the absence of any commercial or financial relationships that could be construed as a potential conflict of interest.
References
Ahn, W., Seo, M. H., Pham, T. K., Nguyen, Q. H., Luu, V. T., Cho, Y., et al. (2019). High lithium ion transport through rGO-wrapped LiNi0.6Co0.2Mn0.2O2 cathode material for high-rate capable lithium ion batteries. Front. Chem. 7:361. doi: 10.3389/fchem.2019.00361
Bai, N. B., Chen, H., Zhou, W., Xiang, K. X., Zhang, Y. L., and Li, C. L. (2015). Preparation and electrochemical performance of LiFePO4/C microspheres by a facile and novel co-precipitation. Electrochim. Acta 167, 172–178. doi: 10.1016/j.electacta.2015.03.163
Belharouak, I., Johnson, C., and Amine, K. (2005). Synthesis and electrochemical analysis of vapor-deposited carbon-coated LiFePO4. Electrochem. Commun. 7, 983–988. doi: 10.1016/j.elecom.2005.06.019
Beninati, S., Damen, L., and Mastragostino, M. (2008). MW-assisted synthesis of LiFePO4 for high power applications. J. Power Sources 180, 875–879. doi: 10.1016/j.jpowsour.2008.02.066
Burba, C. M., and Frech, R. (2004). Raman and FTIR spectroscopic study of LixFePO4 (0 ≤ x ≤ 1). J. Electrochem. Soc. 151, A1032–A1038. doi: 10.1149/1.1756885
Chang, M., Wang, H., Zheng, Y., Li, N., Chen, S., Wan, Y., et al. (2019). Surface modification of hollow microsphere Li1.2Ni1/3Co1/3Mn1/3O2 cathode by coating with CoAl2O4. J. Solid State Electrochem. 23, 607–613. doi: 10.1007/s10008-018-4157-y
Chang, Y. C., Hung, I. M., and Peng, C. T. (2014). Effects of particle size and carbon coating on electrochemical properties of LiFePO4/C prepared by hydrothermal method. J. Mater. Sci. 49, 6907–6916. doi: 10.1007/s10853-014-8395-9
Chen, H., Zhang, B., Zhang, J., Yu, W., Zheng, J., Ding, Z., et al. (2018). In-situ grown SnS2 nanosheets on rGO as an advanced anode material for lithium and sodium ion batteries. Front. Chem. 6:629. doi: 10.3389/fchem.2018.00629
Dathar, G. K. P., Sheppard, D., Stevenson, K. J., and Henkelman, G. (2011). Calculations of Li ion diffusion in olivine phosphates. Chem. Mater. 23, 4032–4037. doi: 10.1021/cm201604g
Ding, Y., Jiang, Y., Xu, F., Yin, J., Ren, H., Zhuo, Q., et al. (2010). Preparation of nano-structured LiFePO4/graphene composites by co-precipitation method. Electrochem. Commun. 12, 10–13. doi: 10.1016/j.elecom.2009.10.023
Fan, Q., Lei, L. X., Xu, X. Y., Yin, G., and Sun, Y. M. (2014). Direct growth of FePO4/graphene and LiFePO4/graphene hybrids for high rate Li-ion batteries. J. Power Sources 257, 65–69. doi: 10.1016/j.jpowsour.2014.01.044
Fathollahi, F., Javanbakht, M., Omidvar, H., and Ghaemi, M. (2015). Improved electrochemical properties of LiFePO4/graphene cathode nanocomposite prepared by one-step hydrothermal method. J. Alloy Compd. 627, 146–152. doi: 10.1016/j.jallcom.2014.12.025
Gaberscek, M. (2009). Towards optimized preparation of cathode materials: how can modeling and concepts be used in practice. J. Power Sources 189, 22–27. doi: 10.1016/j.jpowsour.2008.12.041
Gaberscek, M., Dominko, R., and Jamnik, J. (2007). Is small particle size more important than carbon coating? an example study on LiFePO4 cathodes. Electrochem. Commun. 9, 2778–2783. doi: 10.1016/j.elecom.2007.09.020
Goodenough, J. B., and Kim, Y. (2010). Challenges for rechargeable Li batteries. Chem. Mater. 22, 587–603. doi: 10.1021/cm901452z
Guo, X. F., Zhang, Y. T., Zhan, H., and Zhou, Y. H. (2010). Investigation on the microwave-derived LiFePO4/C cathode material. Solid State Ion. 181, 1757–1763. doi: 10.1016/j.ssi.2010.10.008
Hai, Y., Zhang, Z., Liu, H., Liao, L., Fan, P., Wu, Y., et al. (2019). Facile controlled synthesis of spinel LiMn2O4 porousmicrospheres as cathode material for lithium ion batteries. Front. Chem. 7:437. doi: 10.3389/fchem.2019.00437
Han, Q. G., Zhang, W. Q., Han, Z. W., Wang, F. X., Geng, D., Li, X., et al. (2019). Preparation of PAN-based carbon fiber@MnO2 composite as an anode material for structural lithium ion batteries. J. Mater. Sci. 54, 11972–11982. doi: 10.1007/s10853-019-03751-x
Jang, B. Z., Liu, C. G., Neff, D., Yu, Z. Y., Wang, M. C., Xiong, W., et al. (2011). Graphene surface-enabled lithium ion-exchanging cells: next-generation high-power energy storage devices. Nano. Lett. 11, 3785–3791. doi: 10.1021/nl2018492
Kiyoshi, K., Shohei, K., and Kaoru, D. (2008). Hydrothermal synthesis of LiFePO4 as a cathode material for lithium batteries. J. Mater. Sci. 43, 2138–2142. doi: 10.1007/s10853-007-2011-1
Kovtyukhova, N. I., Ollivier, P. J., Martin, B. R., Mallouk, T. E., Chizhik, S. A., Buzaneva, E. V., et al. (1999). Layer-by-layer assembly of ultrathin composite films from micron-sized graphite oxide sheets and polycations. Chem. Mater. 11, 771–778. doi: 10.1021/cm981085u
Li, Y., Zhang, H., Xiao, Z., and Wang, R. (2019). Flexible Li[Li0.2Ni0.13Co0.13Mn0.54]O2/carbon nanotubes/nanofibrillated celluloses composite electrode for high-performance lithium-ion battery. Front. Chem. 7:555. doi: 10.3389/fchem.2019.00555
Lim, S., Yoon, C. S., and Cho, J. (2008). Synthesis of nanowire and hollow LiFePO4 cathodes for high-performance lithium batteries. Chem. Mater. 20, 4560–4564. doi: 10.1021/cm8006364
Ma, F., Wu, Y. H., Wei, G., Qiu, S., and Qu, J. (2019). Enhanced electrochemical performance of LiNi0.8Co0.1Mn0.1O2 cathode via wet-chemical coating of MgO. J. Solid State Electrochem. 23, 2213–2224. doi: 10.1007/s10008-019-04308-3
Markevich, E., Sharabi, R., Haik, O., Borgel, V., Salitra, G., Aurbach, D., et al. (2011). Raman spectroscopy of carbon-coated LiCoPO4 and LiFePO4 olivines. J. Power Sources 196, 6433–6439. doi: 10.1016/j.jpowsour.2011.03.059
Padhi, A. K., Nanjundaswamy, K. S., and Goodenough, J. B. (1997a). Phospho-olivines as positive electrode materials for rechargeable lithium batteries. J. Electrochem. Soc. 144, 1188–1194. doi: 10.1149/1.1837571
Padhi, A. K., Nanjundaswamy, K. S., Masquelier, C., and Goodenough, J. B. (1997b). Mapping of transition metal redox energies in phosphates with NASICON structure by lithium intercalation. J. Electrochem. Soc. 144, 2581–2586. doi: 10.1149/1.1837868
Park, K.-S., Son, J. T., Chung, H. T., Kim, S. J., Lee, C. H., and Kim, H. G. (2003). Synthesis of LiFePO4 by co-precipitation and microwave heating. Electrochem. Commun. 5, 839–842. doi: 10.1016/j.elecom.2003.08.005
Prosini, P. P., Carewska, M., Scaccia, S., Wisniewski, P., and Pasquali, M. (2003). Long-term cyclability of nanostructured LiFePO4. Electrochim. Acta 48, 4205–4211. doi: 10.1016/S0013-4686(03)00606-6
Shi, Y., Chou, S. L., Wang, J. Z., Wexler, D., Li, H. J., Liu, H. K., et al. (2012). Graphene wrapped LiFePO4/C composites as cathode materials for lithium-ion batteries. J. Mater. Chem. 22, 16465–16470. doi: 10.1039/c2jm32649c
Song, L., Tang, F., Xiao, Z., Cao, Z., and Zhu, H. (2018). Energy storage and thermostability of Li3VO4-coated LiNi0.8Co0.1Mn0.1O2 as cathode materials for lithium ion batteries. Front. Chem. 6:546. doi: 10.3389/fchem.2018.00546
Stankovich, S., Dikin, D. A., Piner, R. D., Kohlhaas, K. A., Kleinhammes, A., Jia, Y. Y., et al. (2007). Synthesis of graphene-based nanosheets via chemical reduction of exfoliated graphite oxide. Carbon 45, 1558–1565. doi: 10.1016/j.carbon.2007.02.034
Tang, Y. F., Huang, F. Q., Bi, H., Liu, Z. Q., and Wan, D. Y. (2012). Highly conductive three-dimensional graphene for enhancing the rate performance of LiFePO4 cathode. J. Power Sources 203, 130–134. doi: 10.1016/j.jpowsour.2011.12.011
Tao, Y., Cao, Y. B., Hu, G. R., Chen, P. W., Peng, Z. D., Du, K., et al. (2019). Effects of vanadium oxide coating on the performance of LiFePO4/C cathode for lithium-ion batteries. J. Solid State Electrochem. 23, 2243–2250. doi: 10.1007/s10008-019-04319-0
Tuinstra, F., and Koenig, J. L. (1970). Raman spectrum of graphite. J. Chem. Phys. 53, 1126–1130. doi: 10.1063/1.1674108
Wang, G. X., Shen, X. P., Yao, J., and Park, J. (2009). Graphene nanosheets for enhanced lithium storage in lithium ion batteries. Carbon 47, 2049–2053. doi: 10.1016/j.carbon.2009.03.053
Wang, L., Huang, Y. D., Jiang, R. R., and Jia, D. Z. (2007). Preparation and characterization of nano-sized LiFePO4 by low heating solid-state coordination method and microwave heating. Electrochim. Acta 52, 6778–6783. doi: 10.1016/j.electacta.2007.04.104
Wang, L., Wang, H. B., Liu, Z. H., Xiao, C., Dong, S. M., Han, P. X., et al. (2010). A facile method of preparing mixed conducting LiFePO4/graphene composites for lithium-ion batteries. Solid State Ion. 181, 1685–1689. doi: 10.1016/j.ssi.2010.09.056
Wang, S. P., Yang, H. X., Feng, L. J., Sun, S. M., Guo, J. X., Yang, Y. Z., et al. (2013). A simple and inexpensive synthesis route for LiFePO4/C nanoparticles by co-precipitation. J. Power Sources 233, 43–46. doi: 10.1016/j.jpowsour.2013.01.124
Wang, Y., Zhen, M., Liu, H., and Wang, C. (2018). Interlayer-expanded MoS2/graphene composites as anode materials for high-performance lithium-ion batteries. J. Solid State Electrochem. 22, 3069–3076. doi: 10.1007/s10008-018-4018-8
Wu, J., Dathar, G. K. P., Sun, C. W., Theivanayagam, M. G., Applestone, D., Dylla, A. G., et al. (2013). In situ Raman spectroscopy of LiFePO4: size and morphology dependence during charge and self-discharge. Nanotechnology 24:424009. doi: 10.1088/0957-4484/24/42/424009
Xiao, H., Huang, X., Ren, Y., Ding, X., and Zhou, S. (2019). Fabrication of Li4Ti5O12@CN composite with enhanced rate properties. Front. Chem. 7:432. doi: 10.3389/fchem.2019.00432
Zhang, Y., Du, P. P., Wang, L. Z., Zhang, A. Q., Song, Y. H., Li, X. F., et al. (2011). Synthesis and electrochemical properties of gyroscope-like lithium iron phosphate/multiwalled carbon nanotubes composites by microwave-assisted sol–gel method. Synthetic Metals 161, 548–551. doi: 10.1016/j.synthmet.2011.01.008
Zhao, N. N., Li, Y. S., Zhao, X. X., Zhi, X. K., and Liang, G. C. (2016). Effect of particle size and purity on the low temperature electrochemical performance of LiFePO4/C cathode material. J. Alloys Compd. 683, 123–113. doi: 10.1016/j.jallcom.2016.04.070
Zheng, J. C., Li, X. H., Wang, Z. X., Guo, H. J., and Zhou, S. Y. (2008). LiFePO4 with enhanced performance synthesized by a novel synthetic route. J. Power Sources 184, 574–577. doi: 10.1016/j.jpowsour.2008.01.016
Zhou, P., Zhang, M., Wang, L., Huang, Q., Su, Z., Li, L., et al. (2019). Synthesis and electrochemical performance of ZnSe electrospinning nanofibers as an anode material for lithium ion and sodium ion batteries. Front. Chem. 7:569. doi: 10.3389/fchem.2019.00569
Keywords: LiFePO4/graphene composite, micro/nanoscale, one step, microwave synthesis, electrochemical performance
Citation: Liu S, Yan P, Li H, Zhang X and Sun W (2020) One-Step Microwave Synthesis of Micro/Nanoscale LiFePO4/Graphene Cathode With High Performance for Lithium-Ion Batteries. Front. Chem. 8:104. doi: 10.3389/fchem.2020.00104
Received: 26 December 2019; Accepted: 04 February 2020;
Published: 25 February 2020.
Edited by:
Kezhen Qi, Shenyang Normal University, ChinaReviewed by:
Jian Zhang, Wuhan University of Technology, ChinaQi Long Guo, Northwest University for Nationalities, China
Copyright © 2020 Liu, Yan, Li, Zhang and Sun. This is an open-access article distributed under the terms of the Creative Commons Attribution License (CC BY). The use, distribution or reproduction in other forums is permitted, provided the original author(s) and the copyright owner(s) are credited and that the original publication in this journal is cited, in accordance with accepted academic practice. No use, distribution or reproduction is permitted which does not comply with these terms.
*Correspondence: Shulong Liu, bGl1c2h1bG9uZzAzMTRAMTYzLmNvbQ==