- 1School of Metallurgy and Environment, Central South University, Changsha, China
- 2College of Chemistry and Chemical Engineering of Xiamen University, Xiamen, China
Lithium-rich manganese-based cathode materials has been attracted enormous interests as one of the most promising candidates of cathode materials for next-generation lithium ion batteries because of its high theoretic capacity and low cost. In this study, 0.5Li2MnO3·0.5LiNi0.5Co0.2Mn0.3O2 materials are synthesized through a solid-state reaction by using different lithium sources, and the synthesis process and the reaction mechanism are investigated in detail. The morphology, structure, and electrochemical performances of the material synthesized by using LiOH·H2O, Li2CO3, and CH3COOLi·2H2O have been analyzed by using Thermo gravimetric analysis (TGA), X-ray diffraction (XRD), Scanning electron microscope (SEM), Transmission electron microscope (TEM), X-ray photoelectron spectroscopy (XPS), and electrochemical measurements. The 0.5Li2MnO3·0.5LiNi0.5Co0.2Mn0.3O2 material prepared by using LiOH·H2O displays uniform morphology with nano particle and stable layer structure so that it suppresses the first cycle irreversible reaction and structure transfer, and it delivers the best electrochemical performance. The results indicate that LiOH·H2O is the best choice for the synthesis of the 0.5Li2MnO3·0.5LiNi0.5Co0.2Mn0.3O2 material.
Introduction
Rechargeable Li-ion batteries (LIBs) play a dominant role in energy storage devices of portable electronic devices and electric vehicles (EVs) for its excellent safety, long cycle life, and high energy density (Armand and Tarascon, 2008; Goodenough and Park, 2013; Zhang Q. et al., 2015, 2016; Li et al., 2017a,b; Zhang et al., 2018). However, the specific energy density of LIBs still cannot meet the demand of EVs owing to lower energy density of cathode material (Whittingham, 2014). At present, classic cathode materials, such as LiFePO4 (Zheng et al., 2008, 2017), LiMn2O4 (Kim et al., 2008), LiCoO2 (Kang et al., 1999), and LiNiaMnbCo1−a−bO2 (Li et al., 2017) etc., offer a reversible discharge capacity less than 200mAh g−1. Recently, lithium-rich manganese-based cathode materials has been attracted enormous interests as a promising cathode material for next-generation LIBs because of high discharge capacity (more than 250mAh g−1) and low cost (Ohzuku et al., 2011).
Lithium-rich manganese-based cathode materials contain double component: one phase of Li2MnO3 with C2/m space group and the other phase of LiMO2 with R-3m space group. Because Mn4+ in Li2MnO3 phase cannot be oxidized any more, it possesses electrochemically inert. However, Li+ and O2 can be extracted from the TM (transition metal) layer and the lattice, respectively, which indicates that the Li2MnO3 phase is activated by initial charging process and forms an irreversible loss of Li2O (Yabuuchi et al., 2011). It is demonstrated that the high capacity of the materials originates from the oxygen escape from Li2MnO3 phase at high voltage (Yabuuchi et al., 2011). In addition, there are so many fatal disadvantages in lithium-rich manganese-based cathode materials, such as severe voltage fading during cycling (Zheng J. et al., 2015; Zhang T. et al., 2016) poor rate performance (Fan et al., 2015; Rozier and Tarascon, 2015; Zhang K. et al., 2015), large initial irreversible capacity, and low initial coulombic efficiency (Bai et al., 2015). Presently, many methods like comprising doping (Dianat et al., 2013; Wang et al., 2013; Li et al., 2014; Zhang H. et al., 2014), coating (Shi et al., 2012, 2013; Gu et al., 2013; Zhang et al., 2013; Zhou et al., 2017; Liu et al., 2018), nano crystallization (Wang et al., 2010), and morphology control (Yang et al., 2013; Remith and Kalaiselvi, 2014) have been proposed to promote the electrochemical performance of the materials.
Generally speaking, the compositions of this kind of material are varied. According to the chemical formula of lithium-rich manganese-based cathode materials, it can be simply written as xLi2MnO3·(1-x)LiMO2(M = Ni, Co, Mn, Ti, Fe, etc.; Ohzuku et al., 2011; Yabuuchi et al., 2011; Bai et al., 2015; Fan et al., 2015; Rozier and Tarascon, 2015; Zheng J. et al., 2015; Zhang T. et al., 2016). Common and representative components of lithium-rich manganese-based materials are 0.5Li2MnO3·0.5LiNi0.5Mn0.5O2 and 0.5Li2MnO3·0.5LiNi1/3Co1/3Mn1/3O2 (Shi et al., 2012, 2013; Dianat et al., 2013; Gu et al., 2013; Wang et al., 2013; Yang et al., 2013; Zhang et al., 2013; Zhang H. et al., 2014; Li et al., 2014; Zhou et al., 2017).
To the best of our knowledge, the presence and content of nickel that improves the cathode capacity (Sun et al., 2005). Zheng Z. et al. (2015) discussed that the roles and the functions of nickel in electrochemical cycling of lithium-rich Mn-based cathode materials. Yang et al. (2017) reported that the Ni substitution at 2c sites not only enhances oxygen stability and delays oxygen loss from the lattice but also suppresses the cation mixing that induces the undesired phase transition. Gao et al. (2017) demonstrated that Li-rich material Li1.2(Ni0.25Co0.25Mn0.5)0.8O2 was prepared by a novel core-shell structure, in which Ni element acts as stabilizing ions to inhibit the Jahn-Teller effect of active Mn3+. Based on the above considerations, lithium-rich manganese-based material 0.5Li2MnO3·0.5LiNi0.5Co0.2Mn0.3O2 is designed for the first time.
In fact, the cathode materials with different morphology and electrochemical performance can be achieved by using different lithium sources (Zhang B. et al., 2014; Cao et al., 2017). In this work, we; try to synthesize 0.5Li2MnO3·0.5LiNi0.5Co0.2Mn0.3O2 materials with nano-size particles by using different lithium sources (LiOH·H2O, Li2CO3 and CH3COOLi·2H2O). The solid state reaction mechanism is investigated and the effects of lithium sources on the morphology, structure and electrochemical performance are clarified.
Experimental
Material Preparation
The 0.5Li2MnO3·0.5LiNi0.5Co0.2Mn0.3O2 cathode material was prepared via solid-state reaction. Analytical grade chemicals NiC4H6O4·4H2O (AR, 99.9%), CoC4H6O4·4H2O (AR, 99.5%), MnC4H6O4·H2O (AR, 99%), and different lithium sources, LiOH·H2O, Li2CO3, and CH3COOLi·2H2O (excess 3.33% molar ratio, AR 95%, AR 98%, AR 99%, respectively), with a stoichiometric amount were mixed thoroughly and ball milled (200 rpm) for 1 h. With an amount of ethanol added, the materials were ball milled (200 rpm) continually for 3 h and dried in an oven at 80°C for 12 h to obtain a uniform mixed precursor. Then the dried precursor was ball milled for 0.5 h and sintered at 900°C for 10 h in air atmosphere to prepare the targeted 0.5Li2MnO3·0.5LiNi0.5Co0.2Mn0.3O2 material. The rate of heating was retained at 5°C min−1. The 0.5Li2MnO3·0.5LiNi0.5Co0.2Mn0.3O2 compounds synthesized by using LiOH·H2O, Li2CO3, and CH3COOLi·2H2O as lithium sources are marked as Sample A, Sample B, and Sample C, respectively.
Sample Characterization
The crystalline structure of 0.5Li2MnO3·0.5LiNi0.5Co0.2Mn0.3O2 was tested by X-ray diffraction (XRD, Rigaku D/maxb) with Cu Kα radiation(λ = 1.54056Å) in the range of 10°-80° with the speed of 5° min−1. The morphology was investigated with scanning electron microscopy (SEM, Philips, FEI Quanta 200 FEG) and transmission electron microscopy (TEM, TECNAI G2 F20, FEI). The sample was examined by Thermo gravimetric/Differential Scanning calorimeter (TG/DSC, SDT Q600) under the air from ambient temperature to 1,000°C at 10°C min−1. X-ray photoelectron spectroscopy (XPS, VG Multilab 2000) was used to observe the chemical valence of the TMs (transition elements Ni, Co, Mn, O) of the sample.
Electrochemical Measurements
Electrochemical measurements of 0.5Li2MnO3·0.5LiNi0.5Co0.2Mn0.3O2 were tested by CR2025 coin-type cells. The positive electrode was operated as slurry by 80% active material (0.5Li2MnO3·0.5LiNi0.5Co0.2Mn0.3O2), 10% acetylene black, 10% polyvinylidene fluoride (PVDF), and N-methylpyrrolidone (NMP) solvent. Then the electrode slurry was cast on aluminum foil and dried at 120°C for 12 h under vacuum atmosphere. Typical active material areal loadings were about 1.2 mg cm−2. The cells were assembled in a filled argon glove box. Lithium metal was used as the anode and the separator was a Celgard 2500. The electrolyte utilized was a 1 M LiPF6 solution by mixtures of ethylene carbonate (EC) and dimethyl carbonate (DMC) with a volume ratio of 1:1. The Galvanostatic charge-discharge measurements were carried out using NEWARE CT-3008 battery testing system (Shenzhen, China) within the voltage range of 2.0–4.8 V at room temperature. Cyclic voltammetry (CV) measurements were conducted using CHI660D Electrochemical Workstation (Shanghai Chen Hua) at 0.1 mV s−1 between 2.0 and 4.8 V. Electrochemical impedance spectroscopy (EIS) of the cell was carried out using CHI660D Electrochemical Workstation (Shanghai Chen Hua) in the frequency range of 0.1 Hz−10 kHz, and the AC voltage was applied as 5 mV.
Results and Discussions
In order to ascertain the optimum temperature for heat treatment and explore the effects of different lithium sources, TG-DSC analyses are done for the precursor in the air. As presented in Figure 1, there are three main stages for weight losses in the TG plots and several endothermic and exothermic peaks in the DSC plot. The temperature range from ambient to about 200°C, the weight loss is the release of hydration water from precursor (Deng et al., 2010). In the region from 200 to 500°C, there is a sharp exothermic peak (Figures 1A,B) or two exothermic peaks (Figure 1C) accompanied by abrupt weight loss observed in DTG/DSC curves, it should be related to the volatilization of crystallized water from MC4H6O4·4H2O(M = Ni, Co, Mn) and the decomposition of precursor. The weight loss of precursor mainly comes from the escape of water and carbon dioxide during the reaction. As the temperature increases from 500 to 1,000°C, weight loss (Figures 1A,C) almost can't be observed in DTG curves. However, a little exothermic peak and a small amount weight loss is observed in DSC curves (Figure 1B) when the temperature reaches 720°C, which corresponding to the melting temperature of lithium carbonate. We think that it attributes to carbon dioxide emission from lithium carbonate (Li2CO3).
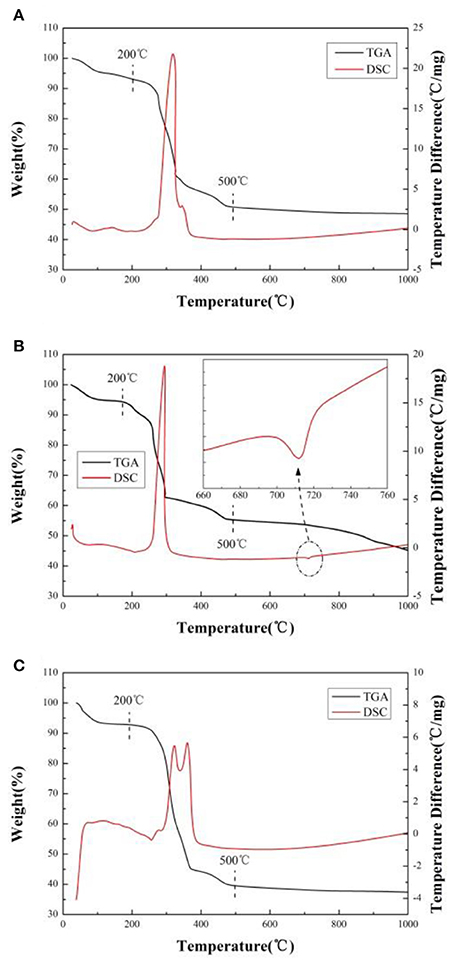
Figure 1. TG-DSC curves of the precursor by using different lithium sources. (A) LiOH·H2O, (B) Li2CO3, (C) CH3COOLi·2H2O.
The mass loss of sample A, B, and C is 51.44, 54.93, and 62.63%, respectively. The weight loss is from the decomposition of precursor and the release of water and carbon dioxide under heating (Cao et al., 2017). The greater the weight losses, the greater the quantity of gas releases (Cao et al., 2017). During the material formation under heat treatment, a large number of gas releases will destroy the primary particle morphology and promote it growth, resulting in aggregation. Because the mass loss of sample A is the least, the average size of particles and uniformity of the sample A should be much better than others. It will be proved in subsequent SEM images (Cao et al., 2017).
The XRD patterns for sample A synthesized at different temperatures are shown in Figure S1. It can be seen that the crystallinity of the samples increases accompanied by temperature increment from 600 to 1,000°C. As the temperature increases to 800°C, there appears a couple of peaks during 20–23° attributed to the super lattice diffraction of the monoclinic Li2MnO3 phase (Gao et al., 2017). With the temperature increasing to 900°C, the diffraction peaks of sample A are well indexed to a hexagonal α-NaFeO2 structure (Seteni et al., 2017). Sample A displays the (006)/(012) and (018)/(110) peaks with a fine splitting, it indicates that it possesses highly ordered good crystallinity layered structure. When the temperature reaches 1,000°C, the peak at 36.5° corresponding to LiMn2O4 with spinel structure. It indicates that LiMn2O4 structure can be formed at higher temperature (Zhang B. et al., 2014). Based on the above analysis, the optimum sintering temperature is chosen as 900°C in this work.
The XRD patterns of the sample A, B and C sintered at 900°C are shown in Figure 2. The peaks of the samples can be indexed to the hexagonal α-NaFeO2 phase (R-3m) and the little peaks from 20 to 23° (Figure 2B) are attributed to Li2MnO3 phase (C2/m). Li2MnO3 phase can be described as the ordering of lithium ions and transition metal ions in the layer for transition metal and the forming of LiMn6 arrangement (Gao et al., 2017). Besides, the two pairs of the (006)/(012) and (018)/(110) peaks are well separation, illustrating that the samples possesses good crystallinity and fine layered structure. Nevertheless, there are a group of minor peaks at 36.5° and 44° of sample C corresponding to LiMn2O4(Fd-3m) of formed under the high temperature. Lattice parameters of 0.5Li2MnO3·0.5LiNi0.5Mn0.3Co0.2O2 are listed in Table 1. The c/a ratios of samples are more than 4.9, it indicates that the material possesses layered characteristics (Zhang M. et al., 2016). The I(003)/I(104) ratios of materials are much larger than 1.2, which indicates that the samples have low cationic mixing (Deng et al., 2010).
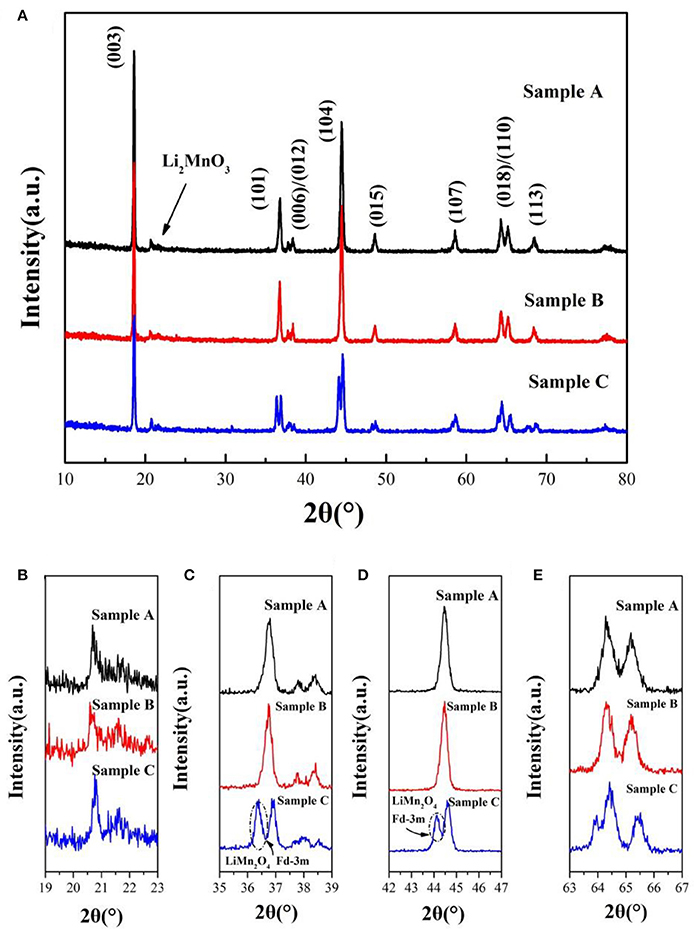
Figure 2. (A) XRD patterns of 0.5Li2MnO3·0.5LiNi0.5Co0.2Mn0.3O2 synthesized at 900°C by using different lithium sources and magnified XRD patterns in the 2θ range of (B) 19°–23°, (C) 35°–39°, (D) 42°–47°, (E) 63°–67°, respectively.
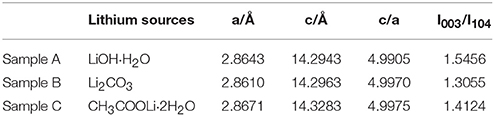
Table 1. Lattice parameters of 0.5Li2MnO3·0.5LiNi0.5Mn0.3Co0.2O2 synthesized by different lithium sources.
The SEM images of 0.5Li2MnO3·0.5LiNi0.5Co0.2Mn0.3O2 layered materials obtained before and after heat treatment are shown in Figure S2. The images of all samples possess morphology of similar aggregation, but sample A and B (Figures S2B,E) synthesized by LiOH·H2O and Li2CO3 have higher homogeneity. The sample C (Figures S2H,I) forms an irregular aggregation of primary particles. As shown in Figures S2B,E, sample A synthesized by LiOH·H2O shows much smaller primary particle sizes compared with other samples. The smaller particle size can shorten the diffusion distance of lithium ions and improve the electrochemical performance of the materials (Cao et al., 2017).
To confirm SEM results, TEM analysis and the Fast Fourier Transform (FFT) are performed, as shown in Figure 3. Sample A composed of 200–300 nm primary particles and the distance of the lattice fringes of particles is calculated to be 0.204 nm, matching well with the d(104) planes, which attributed to layer structure R-3m (Yang et al., 2016). Figures 3C,D show that sample B composed of 300–400 nm primary particles and the lattice spacing are 0.273 and 0.368 nm, corresponding to the planes d(111) and d(−111) of Li2MnO3 phase (C2/m) (Luo et al., 2014). As illustrated in Figures 3E,F, Sample C has severe aggregation although it possesses small primary particles from some regions owing to the destruction of released gas. The distance of the lattice fringes of this material is calculated to be 0.47 nm, corresponding to the d(003) planes of layer structure (Yang et al., 2016).
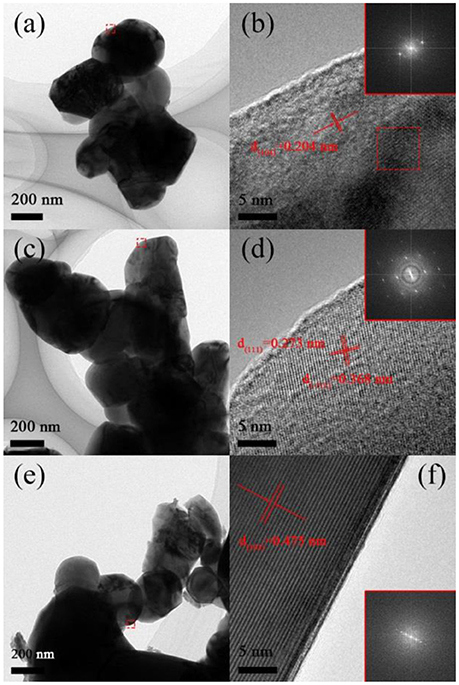
Figure 3. TEM images of (A) Sample A, (C) Sample B, (E) Sample C and HRTEM images of (B) Sample A, (D) Sample B, (F) Sample C.
In order to determine the chemical valence of major elements, the X-ray photoelectron spectra of sample A, B, and C is analyzed and shown in Figure 4. In contrast with the samples, the O 1s, Ni 2p, Co 2p, and Mn 2p peaks have no obvious chemical shift. In Figure 4A, the peak of O 1s located at 529.54 eV can be indexed to the O2− in the lattice of the samples. The Ni 2p3/2 XPS spectra with binding energy of 854.98 eV, corresponding to the Ni 2p3/2 peaks of Ni2+ and Ni3+ located at 854.0 ± 0.2 and 856.0 eV, respectively (Zhang M. et al., 2016). As shown in Figure 4C, the Co 2p3/2 binding energy peaks of the samples centers at 780.20 eV, which is agreed with the binding energy of Co3+ in LiCoO2 (Seteni et al., 2017). The Mn 2p3/2 peaks is 641.94 eV, which is consistent with the value of Mn4+ (Lou et al., 2017). So the chemical valences of O, Ni, Co, and Mn are−2, +2/+3, +3, and +4, respectively, which indicate that lithium sources cause no effect on valence states.
Figure 5A shows the initial charge/discharge curves of the sample A, B, and C at C/10 within the voltage window of 2.0 and 4.8 V. During initial charge, two plateaus from 3.8 to 4.4 V and from 4.4 to 4.6 V are observed for all samples. The plateau from 3.8 to 4.4 V can be accorded with the oxidation of Ni2+/Ni3+ to Ni4+ and Co3+ to Co4+, which is in good agreement with the reversible extraction of Li+ from LiMO2 (M = Ni, Co, Mn) phase (Seteni et al., 2017). Furthermore, the later plateau is attributed to the Li+ and O2− irreversible extraction as Li2O from the inert Li2MnO3 phase, resulting in high irreversible capacity (Yang et al., 2016). When the voltage is from 3.8 to 4.4 V during the first charging cycle, the charging mechanism is written as (Lou et al., 2017),
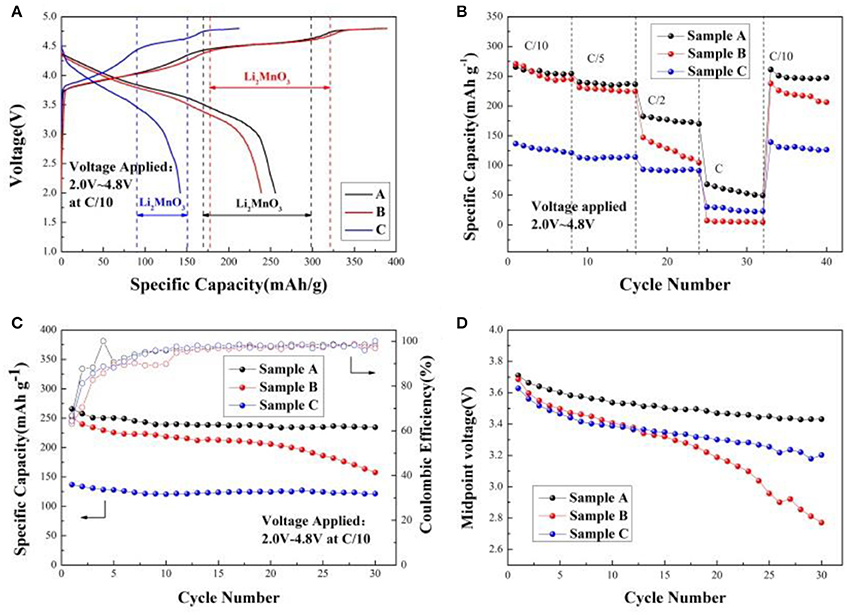
Figure 5. (A) Initial charge/discharge curves of the Sample A, B, and C cathodes at C/10 within 2.0–4.8 V; (B) Rate performance of Sample A, B, and C cathodes; (C) Cycle performance of Sample A, B, and C cathodes at C/10 rate; (D) The decay of midpoint voltage of Sample A, B, and C cathodes at C/10 rate.
When the voltage is from 4.4 to 4.6 V, the charging mechanism is as follows (Lou et al., 2017),
The initial charge/discharge capacity and the coulombic efficiency of the sample A, B, and C are listed in Table 2. Obviously, the discharge capacity of the sample A is much higher than the others. Figure 5B shows rate performance of the Sample A, B, and C at different rates. It can be seen that the discharge capacities of all samples decrease as the rates increased due to the poor conductivity of the material and inert of Li2MnO3 (Seteni et al., 2017). However, the sample A shows much higher rate property because of smaller primary particle, which can shorten the Li+ ions diffusion pathway. The midpoint voltage decay of the samples during cycling at rate of C/10 is shown in Figures 5C,D. The discharge capacities of sample A, B, and C reaches 231.8, 157.7, and 121.0 mAhg−1 after 30 cycles at C/10 rate, with capacity retentions of 88.4, 63.8, and 88.6%, respectively. Figure 5D indicates that sample A holds the most stable voltage from 3.71 to 3.43 V during cycling. However, a sudden drop appears for the midpoint voltage of Sample B after 20 cycles. The results indicate sample A keeps the most stable voltage during cycling.
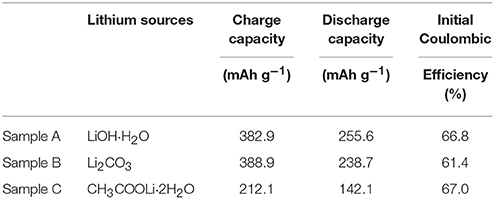
Table 2. Initial charge/discharge capacity and the Coulombic efficiency of the sample A, B, and C cathodes.
Cyclic voltammetry curves of sample A, B, and C for the initial three cycles during the voltage range of 2.0–4.8 V at the scan rate of 0.1 mV s−1 are shown in Figure 6. The CV curves are similar. There are two oxidation peaks and two reduction peaks in the initial cycle. The oxidation peak at about 4.0 V is the oxidation of Ni2+/Ni3+ to Ni4+ and Co3+ to Co4+ with the reversible extraction of Li+ from LiMO2 (M = Ni, Co, Mn) phase (Xiao et al., 2017). The oxidation peak at around 4.6 V corresponds to the Li+ and O2− irreversible extraction from the Li2MnO3 phase. In the following reduction process, the peak at about 3.7 V is the reduction of Ni4+ to Ni2+/Ni3+ and Co4+ to Co3+, and the peak at around 3.2 V related to Li+ insertion into layered MnO2 (Seteni et al., 2017). Besides, the peaks of sample A and B (Figures 6A,B) are higher than sample C, indicated that sample A and B have more steady structure. It is also worth mentioning that, there are two peaks at about 2.9 V and 2.5 V for the sample C (Figure 6C), corresponding to oxidation peak and reduction peak, respectively, related to a small amount of spinel structure (Cao et al., 2017).
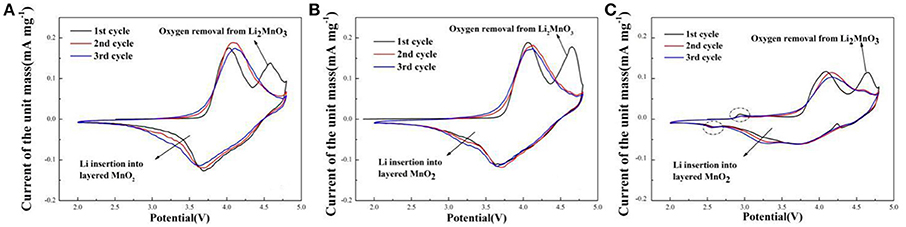
Figure 6. Cyclic voltammetry curves of (A) Sample A (B) Sample B (C) Sample C at the scan rate of 0.1 mV s−1.
Electrochemical impedance spectroscopy (EIS) can be used to investigate the electrode kinetic process of samples A, B, and C. As shown in Figure 7, The EIS plots consist of a semicircle arc and a straight line. The semicircle arc at high frequency region corresponds to the charge transfer process, and the straight line at low frequency region is the lithium diffusion process. The plots are fitted using the electric equivalent circuit model, as shown in Figure 7. The parameters of the equivalent circuit are listed in Table 3. In the equivalent circuit, Rs and Rct represent the solution resistance and charge-transfer resistance, respectively (He et al., 2015). CPE is related to capacitance of the surface layer (Toprakci et al., 2013). ZW represents the Warburg impedance (Xiao et al., 2017) (Z' is the real impedance and Z” is the imaginary impedance). It is observed that the Rs and Rct of sample A (5.39 Ω, 87.93 Ω) are smaller than those of sample B (7.968 Ω, 72.08 Ω) and sample C (27.31 Ω, 120 Ω). The results indicate that the solution resistance and charge-transfer resistance of sample A is the smallest, which mainly because sample A prepared by using LiOH·H2O owns the smaller primary sizes (Cao et al., 2017). Hence, sample A exhibits the best electrochemical properties.
Conclusions
In summary, 0.5Li2MnO3·0.5LiNi0.5Co0.2Mn0.3O2 materials have been successfully synthesized by using three kinds of lithium sources, LiOH·H2O, Li2CO3, and CH3COOLi·2H2O, respectively. The effects of morphology, structure, electrochemical performances of the 0.5Li2MnO3·0.5LiNi0.5Co0.2Mn0.3O2 material prepared by using different lithium sources have been investigated. 0.5Li2MnO3·0.5LiNi0.5Co0.2Mn0.3O2 material prepared by using LiOH·H2O shows the most uniform morphology with the particle diameters of about 200–300 nm and stable layer structure. It delivers the best electrochemical performances with the initial discharge capacity reaching 255.6 mAh g−1 at C/10, and the capacity retention is 88.4% after 30 cycles at C/10. LiOH·H2O is the best choice for the synthesis of 0.5Li2MnO3·0.5LiNi0.5Co0.2Mn0.3O2 material compared with Li2CO3 and CH3COOLi·2H2O.
Author Contributions
All authors listed have made a substantial, direct and intellectual contribution to the work, and approved it for publication.
Conflict of Interest Statement
The authors declare that the research was conducted in the absence of any commercial or financial relationships that could be construed as a potential conflict of interest.
The handling Editor declared a shared affiliation, though no other collaboration, with one of the authors, M-ZL.
Acknowledgments
This study was supported by National Natural Science Foundation of China (Grant No. 51774333, 51604081) and the Innovation-Driven Project of Central South University (NO.2016CX021).
Supplementary Material
The Supplementary Material for this article can be found online at: https://www.frontiersin.org/articles/10.3389/fchem.2018.00159/full#supplementary-material
References
Armand, M., and Tarascon, J. M. (2008). Building better batteries. Nature 451, 652–657. doi: 10.1038/451652a
Bai, Y., Li, Y., Wu, C., Lu, J., Li, H., Liu, Z., et al. (2015). Lithium-rich nanoscale Li1.2Mn0.54Ni0.13Co0.13O2 cathode material prepared by co-precipitation combined freeze drying (CP-Fd) for lithium-ion batteries. Environ. Technol. 3, 843–850. doi: 10.1002/ente.201500030
Cao, K., Shen, T., Wang, K., Chen, D., and Wang, W. (2017). Influence of different lithium sources on the morphology, structure and electrochemical performances of lithium-rich layered oxides. Ceram. Int. 43, 8694–8702. doi: 10.1016/j.ceramint.2017.03.203
Deng, H., Belharouak, I., Wu, H., Dambournet, D., and Amine, K. (2010). Effect of cobalt incorporation and lithium enrichment in lithium nickel manganese oxides. J. Electrochem. Soc. 157, 776–781. doi: 10.1149/1.3418608
Dianat, A., Seriani, N., Bobeth, M., and Cuniberti, G. (2013). Effects of Al-doping on the properties of Li–Mn–Ni–O cathode materials for Li-ion batteries: an ab initio study. J. Mater. Chem. A 32, 9273–9280. doi: 10.1039/c3ta11598d
Fan, J., Li, G., Luo, D., Fu, C., Li, Q., Zheng, J., et al. (2015). Hydrothermal-assisted synthesis of Li-rich layered oxide microspheres with high capacity and superior rate-capability as a cathode for lithium-ion batteries. Electrochim. Acta 173, 7–16. doi: 10.1016/j.electacta.2015.05.028
Gao, S., Yang, T., Zhang, H., Song, D., Shi, X., and Zhang, L. (2017). Improved electrochemical performance and thermal stability of Li-rich material Li1.2(Ni0.25Co0.25Mn0.5)0.8O2 through a novel core-shelled structure design. J. Alloys Compd. 729, 695–702. doi: 10.1016/j.jallcom.2017.09.225
Goodenough, J. B., and Park, K. S. (2013). The Li-ion rechargeable battery: a perspective. J. Am. Chem. Soc. 135, 1167–1176. doi: 10.1021/ja3091438
Gu, M., Belharouak, I., Zheng, J., Wu, H., Xiao, J., Genc, A., et al. (2013). Formation of the spinel phase in the layered composite cathode used in Li-ion batteries. ACS NANO 7, 760–767. doi: 10.1021/nn305065u
He, Z., Wang, Z., Chen, H., Huang, Z., Li, X., Guo, H., et al. (2015). Electrochemical performance of zirconium doped lithium rich layered Li1.2Mn0.54Ni0.13Co0.13O2 oxide with porous hollow structure. J. Power Sources 299, 334–341. doi: 10.1016/j.jpowsour.2015.09.025
Kang, S., Kang, S., Ryu, K., and Chang, S. (1999). Electrochemical and structural properties of HT-LiCoO2 and LT-LiCoO2 prepared by the citrate sol-gel method. Solid State Ionics 120, 155–161.
Kim, D., Muralidharan, P., Lee, H., Ruffo, R., Yang, Y., Chan, C., et al. (2008). Spinel LiMn2O4 nanorods as lithium ion battery cathodes. Nano Lett. 8, 3948–3952. doi: 10.1021/nl8024328
Li, Q., Li, G., Fu, C., Luo, D., Fan, J., and Li, L. (2014). K+-Doped Li1.2Mn0.54Co0.13Ni0.13O2: a novel cathode material with an enhanced cycling stability for Lithium-ion batteries. ACS Appl. Mater. Interfaces 6, 10330–10341. doi: 10.1021/am5017649
Li, S., Li, X., Li, Y., Yan, B., Song, X., and Li, D. (2017a). Superior sodium storage of vanadium pentoxide cathode with controllable interlamellar spacing. Electrochim. Acta 244, 77–85. doi: 10.1016/j.electacta.2017.05.053
Li, S., Li, X., Li, Y., Yan, B., Song, X., Li, L., et al. (2017b). Design of V2O5·xH2O cathode for highly enhancing sodium storage. J. Alloys Compd. 722, 278–286. doi: 10.1016/j.jallcom.2017.06.093
Li, T., Li, X., Wang, Z., and Guo, H. (2017). A short process for the efficient utilization of transition-metal chlorides in lithium-ion batteries: a case of Ni0.8Co0.1Mn0.1O1.1 and LiNi0.8Co0.1Mn0.1O2. J. Power Sources 342, 495–503. doi: 10.1016/j.jpowsour.2016.12.095
Liu, W., Li, X., Xiong, D., Hao, Y., Li, J., Kou, H., et al. (2018). Significantly improving cycling performance of cathodes in lithium ion batteries: the effect of Al2O3 and LiAlO2 coatings on LiNi0.6Co0.2Mn0.2O2. Nano Energy 44, 111–120. doi: 10.1016/j.nanoen.2017.11.010
Lou, M., Zhong, H., Yu, H., Fan, S., Xie, Y., and Yi, T. (2017). Li1.2Mn0.54Ni0.13Co0.13O2 hollow hierarchical microspheres with enhanced electrochemical performances as cathode material for lithium-ion battery application. Electrochim. Acta 237, 217–226. doi: 10.1016/j.electacta.2017.03.201
Luo, D., Li, G., Fu, C., Zheng, J., Fan, J., Li, Q., et al. (2014). A new spinel-layered Li-rich microsphere as a high-rate cathode material for Li-ion batteries. Adv. Energy Mater. 2014:1400062. doi: 10.1002/aenm.201400062
Ohzuku, T., Nagayama, M., Tsuji, K., and Ariyoshi, K. (2011). High-capacity lithium insertion materials of lithium nickel manganese oxides for advanced lithium-ion batteries: toward rechargeable capacity more than 300 mAh g−1. J. Mater. Chem. 21, 10179–10188. doi: 10.1039/c0jm04325g
Remith, P., and Kalaiselvi, N. (2014). Li1.2Mn0.6Ni0.1Co0.1O2 microspheres constructed by hierarchically arranged nanoparticles as lithium battery cathode with enhanced electrochemical performance. Nanoscale 6, 14724–14732. doi: 10.1039/C4NR04314F
Rozier, P., and Tarascon, J. M. (2015). Review-Li-rich layered oxide cathodes for next-generation Li-ion batteries: chances and challenges. J. Electrochem. Soc. 162, A2490–A2499. doi: 10.1149/2.0111514jes
Seteni, B., Rapulenyane, N., Ngila, J. C., Mpelane, S., and Luo, H. (2017). Coating effect of LiFePO4 and Al2O3 on Li1.2Mn0.54Ni0.13Co0.13O2 cathode surface for lithium ion batteries. J. Power Sources 353, 210–220. doi: 10.1016/j.jpowsour.2017.04.008
Shi, S., Tu, J., Mai, Y., Zhang, Y., Gu, C., and Wang, X. (2012). Effect of carbon coating on electrochemical performance of Li1.048Mn0.381Ni0.286Co0.286O2 cathode material for lithium-ion batteries. Electrochim. Acta 63, 112–117. doi: 10.1016/j.electacta.2011.12.082
Shi, S., Tu, J., Tang, Y., Liu, X., Zhang, Y., Wang, X., et al. (2013). Enhanced cycling stability of Li[Li0.2Mn0.54Ni0.13Co0.13]O2 by surface modification of MgO with melting impregnation method. Electrochim. Acta 88, 671–679. doi: 10.1016/j.electacta.2012.10.111
Sun, Y., Myung, S., Kim, M., Prakash, J., and Amine, K. (2005). Synthesis and characterization of Li[(Ni0.8Co0.1Mn0.1)0.8(Ni0.5Mn0.5)0.2]O2 with the microscale core–shell structure as the positive electrode material for lithium batteries. J. Am. Chem. Soc. 127, 13411–13418. doi: 10.1021/ja053675g
Toprakci, O., Toprakci, H., Li, Y., Ji, L., Xue, L., Lee, H., et al. (2013). Synthesis and characterization of xLi2MnO3·(1-x)LiMn1/3Ni1/3Co1/3O2 composite cathode materials for rechargeable lithium-ion batteries. J. Power Sources 241, 522–528. doi: 10.1016/j.jpowsour.2013.04.155
Wang, D., Huang, Y., Huo, Z., and Chen, L. (2013). Synthesize and electrochemical characterization of Mg-doped Li-rich layered Li[Li0.2Ni0.2Mn0.6]O2 cathode material. Electrochim. Acta 107, 461–466. doi: 10.1016/j.electacta.2013.05.145
Wang, Y., Li, H., He, P., Hosono, E., and Zhou, H. (2010). Nano active materials for lithium-ion batteries. Nanoscale 2, 1294–1305. doi: 10.1039/c0nr00068j
Whittingham, M. S. (2014). Ultimate limits to intercalation reactions for Lithium batteries. Chem. Rev. 114, 11414–11443. doi: 10.1021/cr5003003
Xiao, B., Wang, B., Liu, J., Kaliyappan, K., Sun, Q., Liu, Y., et al. (2017). Highly stable Li1.2Mn0.54Co0.13Ni0.13O2 enabled by novel atomic layer deposited AlPO4 coating. Nano Energy 34, 120–130. doi: 10.1016/j.nanoen.2017.02.015
Yabuuchi, N., Yoshii, K., Myung, S., Nakai, I., and Komaba, S. (2011). Detailed studies of a high-capacity electrode material for rechargeable batteries, Li2MnO3-LiCo1/3Ni1/3Mn1/3O2. J. Am. Chem. Soc. 133, 4404–4419. doi: 10.1021/ja108588y
Yang, J., Cheng, F., Zhang, X., Gao, H., Tao, Z., and Chen, J. (2013). Porous 0.2Li2MnO3·0.8LiNi0.5Mn0.5O2 nanorods as cathode materials for lithium-ion batteries. J. Mater. Chem. A 2, 1636–1640. doi: 10.1039/C3TA14228K
Yang, J., Xiao, L., Wei, H., Fan, J., Chen, Z., Ai, X., et al. (2016). Understanding voltage decay in lithium-rich manganese-based layered cathode materials by limiting cutoff voltage. ACS Appl. Mater. Interfaces 8, 18867–18877. doi: 10.1021/acsami.6b04849
Yang, M., Kim, S., Kim, K., Cho, W., Choi, J., and Nam, Y. (2017). Role of ordered Ni atoms in Li layers for Li-rich layered cathode materials. Adv. Funct. Mater. 27:1700982. doi: 10.1002/adfm.201700982
Zhang, B., Ou, X., Zheng, J., Shen, C., Ming, L., Han, Y., et al. (2014). Electrochemical properties of Li2FeP2O7 cathode material synthesized by using different lithium sources. Electrochim. Acta 133, 1–7. doi: 10.1016/j.electacta.2014.03.188
Zhang, H., Qiao, Q., Li, G., and Gao, X. (2014). polyanion-doping for stabilizing Li-rich layered oxides as cathode materials for advanced lithium-ion batteries. J. Mater. Chem. A 2, 7454–7460. doi: 10.1039/C4TA00699B
Zhang, K., Han, X., Hu, Z., Zhang, X., Tao, Z., and Chen, J. (2015). Cheminform abstract: nanostructured Mn-based oxides for electrochemical energy storage and conversion. Chem. Soc. Rev. 44, 699–728. doi: 10.1039/c4cs00218k
Zhang, M., Hu, G., Liang, L., Peng, Z., Du, K., and Cao, Y. (2016). Improved cycling performance of Li2MoO4-inlaid LiNi0.5Co0.2Mn0.3O2 cathode materials for lithium-ion battery under high cutoff voltage. J. Alloys Compd. 673, 237–248. doi: 10.1016/j.jallcom.2016.03.003
Zhang, Q., Chen, H., Luo, L., Zhao, B., Luo, H., Han, X., et al. (2018). Harnessing the concurrent reaction dynamics in active Si and Ge to achieve high performance lithium-ion batteries. Energy Environ. Sci 11, 669–681. doi: 10.1039/C8EE00239H
Zhang, Q., Wang, J., Dong, J., Ding, F., Li, X., Zhang, B., et al. (2015). Facile general strategy toward hierarchical mesoporous transition metal oxides arrays on three-dimensional macroporous foam with superior lithium storage properties. Nano Energy 13, 77–91. doi: 10.1016/j.nanoen.2015.01.029
Zhang, Q., Zhao, B., Wang, J., Chong, Q., Sun, H., Zhang, K., et al. (2016). High-performance hybrid supercapacitors based on self-supported 3D ultrathin porous quaternary Zn-Ni-Al-Co oxide nanosheets. Nano Energy 28, 475–485. doi: 10.1016/j.nanoen.2016.08.049
Zhang, T., Li, J., Liu, J., Deng, Y., Wu, Z., Yin, Z., et al. (2016). Suppressing the voltage-fading of layered lithium-rich cathode materials via an aqueous binder for Li-ion batteries. Chem. Comm. 52, 4683–4686. doi: 10.1039/c5cc10534j
Zhang, X., Belharouak, I., Li, L., Lei, Y., Elam, J., Nie, A., et al. (2013). Structural and electrochemical study of Al2O3 and TiO2 coated Li1.2Ni0.13Mn0.54Co0.13O2 cathode material using ALD. Adv. Energy. Mater. 3, 1299–1307. doi: 10.1002/aenm.201300269
Zheng, J., Han, Y., Sun, D., Zhang, B., and Cairns, E. J. (2017). In situ-formed LiVOPO4@V2O5 core-shell nanospheres as a cathode material for lithium-ion cells. Energy Storage Mater. 7, 48–55. doi: 10.1016/j.ensm.2016.12.003
Zheng, J., Li, X., Wang, Z., Guo, H., and Zhou, S. (2008). LiFePO4 with enhanced performance synthesized by a novel synthetic route. J. Power Sources 184, 574–577. doi: 10.1016/j.jpowsour.2008.01.016
Zheng, J., Xu, P., Gu, M., Xiao, J., Browning, N., Yan, P., et al. (2015). Structure and chemical evolution of Li- and Mn- rich layered cathode material. Chem. Mater. 27, 1381–1390. doi: 10.1021/cm5045978
Zheng, Z., Liao, S., Xu, B., and Zhong, B. (2015). The roles of nickel/manganese in electrochemical cycling of lithium-rich Mn-based nickel cathode materials. Ionics 21, 3295–3300. doi: 10.1007/s11581-015-1575-z
Keywords: lithium-ion battery, lithium-rich manganese-based cathode materials, lithium sources, solid reaction, electrochemical performances
Citation: Wang P-B, Luo M-Z, Zheng J-C, He Z-J, Tong H and Yu W (2018) Comparative Investigation of 0.5Li2MnO3·0.5LiNi0.5Co0.2Mn0.3O2 Cathode Materials Synthesized by Using Different Lithium Sources. Front. Chem. 6:159. doi: 10.3389/fchem.2018.00159
Received: 13 March 2018; Accepted: 20 April 2018;
Published: 15 May 2018.
Edited by:
Qiaobao Zhang, Xiamen University, ChinaReviewed by:
Bo Chen, Nanyang Technological University, SingaporeHuixin Chen, Xiamen Institute of Rare Earth Materials, China
Xifei Li, Xi'an University of Technology, China
Copyright © 2018 Wang, Luo, Zheng, He, Tong and Yu. This is an open-access article distributed under the terms of the Creative Commons Attribution License (CC BY). The use, distribution or reproduction in other forums is permitted, provided the original author(s) and the copyright owner are credited and that the original publication in this journal is cited, in accordance with accepted academic practice. No use, distribution or reproduction is permitted which does not comply with these terms.
*Correspondence: Jun-Chao Zheng, amN6aGVuZ0Bjc3UuZWR1LmNu
†These authors have contributed equally to this work and co-first authors.