- 1Commissariat à l’Energie Atomique et aux Energies Alternatives (CEA), DES, ISEC, DMRC, Univ. Montpellier, Marcoule, France
- 2Institute of Process Engineering, Johannes Kepler University of Linz, Linz, Austria
- 3Department of Chemical Engineering, Tsinghua University, Beijing, China
- 4Department of Applied Science and Technology, Polytechnic University of Turin, Turin, Italy
- 5Rheinland-Pfälzische Technische Universität (RPTU) Kaiserslautern-Landau, Technical University of Kaiserslautern, Kaiserslautern, Germany
Editorial on the Research Topic
Solvent extraction pathways to sustainable industrial processes: new solvents, modelling, and design method
Introduction
The supply of strategic elements is a major challenge for securing the decarbonation of transports and energy. The tension is particularly strong on those required to capture and store intermittent energy sources (Li, Ni, Co, Dy, Nd, Pr), and on those allowing to ensure a stable base production of low carbon energy (U, Pu).
One of the necessary conditions for the deployment of these technologies is to ensure the sustainable and economically viable production of the required materials, with the high grades specified. Most of these elements are currently extracted from mines, with the need to reduce the environmental impact. Alternately, as the demand increases, new types of resource are considered, both in nature, as brines, and through the collecting and recycling of used batteries, wind turbines magnets, etc. One difficulty with these less conventional resources is the significant dilution of the elements of interest in many other components, often with similar chemical properties, which makes their separation difficult. There is therefore an urgent and crucial need to develop new processes and technologies.
Solvent extraction is particularly suitable for separating and purifying complex mixtures to the quality required by energy applications, and will play a major role in the environmental transition. However, even if it is today a major and mature separation process in many industrial sectors, the transposition of current knowledge and technologies to the new challenges linked to securing the supply of strategic elements for the decarbonization of transport and energy is not straightforward, not least because of the specificities of recycled inputs. In addition, the deployment of new extraction systems, with improved selectivity and recovery rates, and contactors, capable of handling both these new extractants and the intrinsic variability of the inputs, must be rapid and have minimal economic and environmental impact. This is not compatible with large-scale pilot experiments, as was the case until the late 90s, for the development of the existing industrial solvent extraction units, and requires new models to be developed.
Towards new extraction systems
Today, intensive research is devoted to the discovery of new extraction systems, whether solvents or adsorbents, with improved capacity, selectivity and kinetics. This is particularly crucial in the case of lithium, demand for which is growing exponentially, and selective extraction of which is hampered by the high salinity of Li-containing brines and/or high alkalinity of battery leach liquors (Zhang et al.).
Based on molecular or even atomic-scale simulations, the mechanisms leading to ions extraction can be studied and better understood, and may lead to the design of “taylorized” molecules. The deployment of microfluidics and automated plateforms will also enable rapid screening of molecules and testing of their performance in a wide range of chemical environments and compositions, with a minimal environmental footprint, which is particularly relevant in the nuclear industry. Investigating combination of co-solvents and the role of the diluent, non-considered so far, are among the current trends of research, with evidence of valuable synergistic effects and/or with the aim of mitigating the risk of 3rd phase accident, which are detrimental to solvent extraction processes.
By pushing back the limits and focusing on the colloid scale, the use of hydrotropes is envisaged to propose innovative separation processes. Hydrotropes can be used as a diluent substitute with, in the case of rare earth ions, a significant reduction in the contribution of the complexation term in the extraction energy, or as a substitute for the extractant itself, enabling the development of an even more direct recycling route based solely on leaching and precipitation (El Maangar et al.).
Towards more efficient contactors and processes
Implementing these promising extraction systems in industrial processes is not straightforward. New extraction systems are usually tested on a small scale in beakers or small mixer-settlers. However, actual performance in industrial contactors can deviate considerably from that measured in small, uniform devices. The main factor influencing the efficiency of a solvent extraction process is the area of the contact zone between the two phases, through which mass transfer takes place. Despite the long-standing implementation of industrial liquid-liquid processes, and although our knowledge of the associated physical phenomena continues to advance, the prediction of the drop size distribution, a fortiori across scale, remains a challenge. Existing scaling rules are based on empirical parameters that are difficult to transpose to new chemical systems, at the risk of oversizing equipment.
Our knowledge of the complex, multi-scale physical and chemical phenomena responsible for drop breakage and coalescence continues to advance, paving the way for the development of predictive emulsification models (Figure 1). In the field of liquid-liquid extraction, machine learning can also help bridge the gap between fundamental research and industry needs. Image processing algorithms have improved considerably and are now capable of detecting droplets and quantifying the interfacial area under conditions closed to the industrial conditions, for example in concentrated and colored media (Bana et al.), thus adding valuably to the current database. At the same time, algorithms combining these data and physical knowledge are being used to revise existing models and sizing rules for given equipment, such as extraction columns (Palmtag et al.).
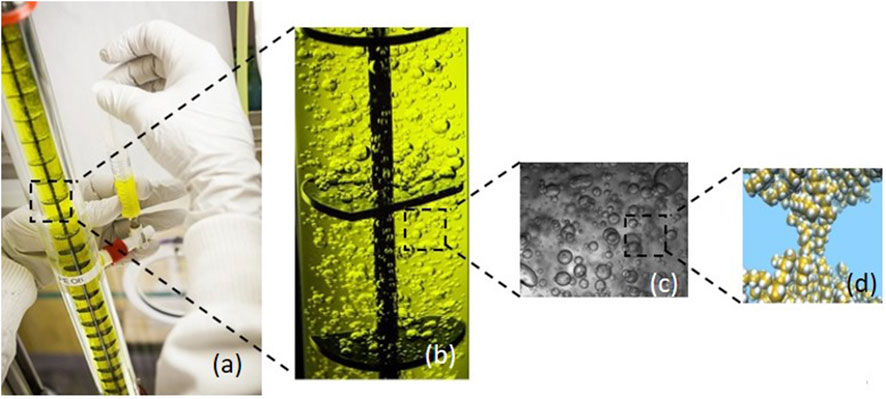
Figure 1. Multi-scale R&D on liquid-liquid extraction processes [credit: (A, B) Photo Sébastien Le Couster; (C, D) CEA ISEC].
Finally, recycling units needs to be flexible to adapt to input variability. This calls for appropriate on-line instrumentation and efficient process control algorithms (Vanel et al.).
Aim of the Research Topic
Developing and scaling up more selective, flexible and sustainable extraction processes is an ambitious challenge, at the interface of many scientific and technical disciplines. But it is also a challenge that new experimental and numerical tools are helping to meet efficiently, by federating advances in usually disconnected fields of research (chemistry, interface science, physics, fluid mechanics, etc.), and accelerating their implementation in the industry. This Research Topic of articles reviews recent advances in these research fields, to provide a factual and forward-looking picture of the development of tomorrow’s sustainable industrial extraction processes.
Author contributions
SC: Conceptualization, Project administration, Supervision, Writing–original draft, Investigation, Methodology, Writing–review and editing. MH: Conceptualization, Investigation, Validation, Visualization, Writing–review and editing. GL: Validation, Visualization, Writing–review and editing. AB: Writing–review and editing, Validation, Visualization. H-JB: Conceptualization, Investigation, Methodology, Validation, Visualization, Writing–review and editing.
Funding
The author(s) declare that no financial support was received for the research, authorship, and/or publication of this article.
Conflict of interest
The authors declare that the research was conducted in the absence of any commercial or financial relationships that could be construed as a potential conflict of interest.
Generative AI statement
The author(s) declare that no Generative AI was used in the creation of this manuscript.
Publisher’s note
All claims expressed in this article are solely those of the authors and do not necessarily represent those of their affiliated organizations, or those of the publisher, the editors and the reviewers. Any product that may be evaluated in this article, or claim that may be made by its manufacturer, is not guaranteed or endorsed by the publisher.
Keywords: solvent extraction (SE), recycling and materials, modelling and simulation, multiphase processes, hydrotrope
Citation: Charton S, Hlawitschka M, Luo G, Buffo A and Bart H-J (2024) Editorial: Solvent extraction pathways to sustainable industrial processes: new solvents, modelling, and design method. Front. Chem. Eng. 6:1539379. doi: 10.3389/fceng.2024.1539379
Received: 04 December 2024; Accepted: 09 December 2024;
Published: 17 December 2024.
Edited and reviewed by:
Chuan-Yu Wu, University of Surrey, United KingdomCopyright © 2024 Charton, Hlawitschka, Luo, Buffo and Bart. This is an open-access article distributed under the terms of the Creative Commons Attribution License (CC BY). The use, distribution or reproduction in other forums is permitted, provided the original author(s) and the copyright owner(s) are credited and that the original publication in this journal is cited, in accordance with accepted academic practice. No use, distribution or reproduction is permitted which does not comply with these terms.
*Correspondence: Sophie Charton, c29waGllLmNoYXJ0b25AY2VhLmZy