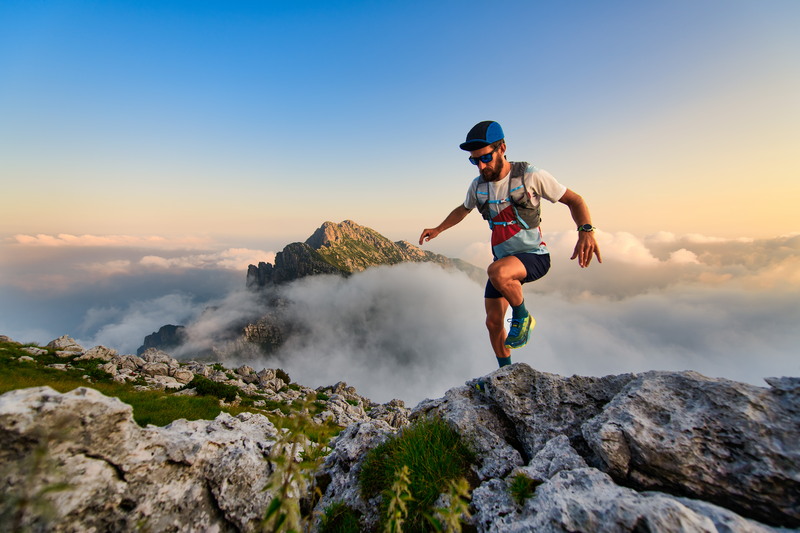
94% of researchers rate our articles as excellent or good
Learn more about the work of our research integrity team to safeguard the quality of each article we publish.
Find out more
EDITORIAL article
Front. Chem. Eng. , 19 March 2024
Sec. Separation Processes
Volume 6 - 2024 | https://doi.org/10.3389/fceng.2024.1391673
This article is part of the Research Topic Artificial Intelligence-Assisted Design of Sustainable Processes View all 6 articles
Editorial on the Research Topic
Artificial intelligence-assisted design of sustainable processes
Process engineering is facing new major challenges as it adapts to the many changes in society driven by the struggle for resources and the need for better ways to use them. For example, process design needs to take into account the developments in material feedstocks (e.g., renewable materials, waste) and energies (e.g., diverse sources, decarbonized), environmental considerations (e.g., carbon, water, biodiversity, chemical pollution of water, air, and soil) and providing new services such as intrant and product flexibility or polygeneration.
To address these challenges, a wide range of technological innovations, in addition to the traditional, well-established functions, such as new materials (e.g., ionic liquids, composite materials, biomolecules), material production techniques (e.g., additive manufacturing), use of non-conventional driving forces (e.g., light or microwave), hybridization of existing functions (e.g., membrane distillation or adsorption bioreactor), and engineering paradigms (e.g., modularization or decentralized production) are offering more possibilities.
To achieve a sustainable design of processes and to balance challenges and opportunities, process designers need therefore to make complex decisions among an expanding set of possibilities at all scales (material, unit operation, process system) in a complex environment.
Fortunately, recent advances in algorithmic techniques, such as artificial intelligence (AI), have gained popularity and applicability and could be used as decision-aiding tools to assist process designers cope with increasing complexity as they face new horizons. The growth in computing capacity and discoveries in cognitive and digital sciences are leading to the popularization of new algorithms for automation and assistance with certain tasks (e.g., optimization, machine learning), discovering new challenges (e.g., molecular design) and multi-criteria decision analysis methods.
AI covers a wide range of techniques at the intersection of the data science and operational research communities. Thus, a broad variety of “intelligent” algorithms could be used, exploiting experiences from reward-driven optimization techniques (global optimization, meta-heuristics, nature-inspired algorithms, etc.) and data-driven learning techniques (Machine Learning, Deep Learning, etc.). Today, AI is being used in the field of chemical engineering to address new molecular separations, reaction pathways, innovative process conceptualization, improving the sustainability of conventional technologies, or re-purposing them for new challenges.
This Research Topic addresses the use of AI -in the general sense of automating decision-making on a complex engineering problem by mimicking intelligent behavior-to achieve sustainable process design. It collects contributions that illustrate different machine-learning approaches that can be purely data-driven or coupled with physics-based approaches and applied at different scales-from product to process-of chemical engineering.
Contributions are grouped into three categories: property prediction, hybrid modeling, and flowsheet generation.
The first set of contributions concerns a popular use of Machine Learning in chemical engineering: the prediction of properties of interest (thermochemical, kinetic, etc.) by data-driven techniques. These approaches can either use data based on experimental measurements or data generated using physics-based numerical simulations. The work by Wang et al., “Predicting xylose yield from prehydrolysis of hardwoods: A machine learning approach”, explores the prediction of a reaction yield, with an application to biomass conversion (e.g., biorefining). A database was established, based solely on experimental samples taken from the literature. The authors used three types of Machine Learning algorithms (ridge regression, support vector regression and artificial neural networks), and compared their predictions with a conventional kinetic model, as such phenomenological models are often limited to specific species and operating regimes.
The study by Komori et al., “Stress Prediction of the Particle Structure of All-Solid-State Batteries by Numerical Simulation and Machine Learning”, deals with the stress at the contact surface between microparticles in all-solid-state batteries, with an application to energy storage (e.g., electric and hybrid vehicles). The authors used a discrete element method to generate 2D images of particle structures and corresponding predictions. A convolutional neural network was used to make predictions from the cross-sectional images. ML prediction compared well with physics-based simulations, and linked the structure of porous materials to stress properties.
The second set of contributions focuses on an emerging hybrid modeling paradigm that combines knowledge-based modeling (often called a white box), and data-driven modeling (often called a black box). The former (white box, often called “first-principle models” in the context of chemical engineering) is based on a fundamental understanding and modeling of physico-chemical phenomena, it exhibits good physical interpretability and extrapolability but offers high model complexity and is computationally intensive. The latter (black box) on the other hand, is based purely on data, has lower model complexity and computational time, but lacks physical interpretability and extrapolability. The two contributions in this second set are both review articles on the use of hybrid modeling in biopharmaceutical processes and predictive maintenance, respectively.
The paper “Hybrid modeling for biopharmaceutical processes: advantages, opportunities, and implementation” by Narayanan et al. deals with the use of such a modeling paradigm for the biopharmaceutical industry. The authors discussed the interest in such a technique for this industry. They introduced the two common architectures for hybridization (serial data/knowledge, or parallel) and reported successful implementations of hybrid models for different types of bioprocesses. A step-by-step sequence for developing hybrid models was also proposed.
The work by Cai et al., “Review of synergy between machine learning and first principles models for asset integrity management”, discusses another aspect of the chemical process industry. The authors presented how hybrid models combining first principles and machine learning models can be applied to asset integrity. In particular, they discussed the interest in improving predictive maintenance, with an emphasis on advanced management in digital twins, and existing software solutions.
The last original contribution relates to another emerging field: the generation of process flowsheets. The use of generative AI for molecular design is an extensive line of work in the literature, that could be a source of inspiration for process flowsheet design.
The paper “Data-driven structural synthesis of supercritical CO2 power cycles” by Nabil et al. deals with the design of innovative power cycles using supercritical CO2 as a working fluid for waste-heat recovery. The authors used Long Short Term Memory networks (common in natural language processing) to generate process flowsheets that exhibit high efficiencies. Initially, the data were random cycles, then the model was fine-tuned using efficient cycle layouts optimized with a physics-based simulator.
TN: Writing–review and editing, Writing–original draft. J-MC: Writing–review and editing. FV: Writing–review and editing.
The authors declare that the research was conducted in the absence of any commercial or financial relationships that could be construed as a potential conflict of interest.
All claims expressed in this article are solely those of the authors and do not necessarily represent those of their affiliated organizations, or those of the publisher, the editors and the reviewers. Any product that may be evaluated in this article, or claim that may be made by its manufacturer, is not guaranteed or endorsed by the publisher.
Keywords: process design, artificial intelligence, machine learning, deep learning, property prediction, hybrid modeling, flowsheet generation
Citation: Neveux T, Commenge J-M and Vermeire F (2024) Editorial: Artificial intelligence-assisted design of sustainable processes. Front. Chem. Eng. 6:1391673. doi: 10.3389/fceng.2024.1391673
Received: 26 February 2024; Accepted: 04 March 2024;
Published: 19 March 2024.
Edited and reviewed by:
Eric Favre, Université de Lorraine, FranceCopyright © 2024 Neveux, Commenge and Vermeire. This is an open-access article distributed under the terms of the Creative Commons Attribution License (CC BY). The use, distribution or reproduction in other forums is permitted, provided the original author(s) and the copyright owner(s) are credited and that the original publication in this journal is cited, in accordance with accepted academic practice. No use, distribution or reproduction is permitted which does not comply with these terms.
*Correspondence: Thibaut Neveux, dGhpYmF1dC5uZXZldXhAZWRmLmZy
Disclaimer: All claims expressed in this article are solely those of the authors and do not necessarily represent those of their affiliated organizations, or those of the publisher, the editors and the reviewers. Any product that may be evaluated in this article or claim that may be made by its manufacturer is not guaranteed or endorsed by the publisher.
Research integrity at Frontiers
Learn more about the work of our research integrity team to safeguard the quality of each article we publish.