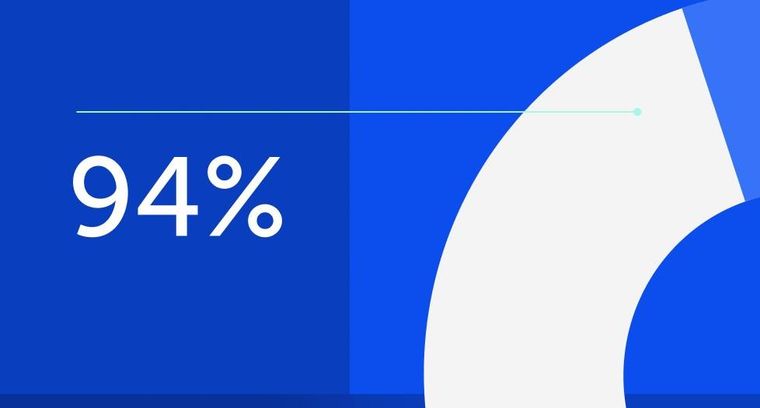
94% of researchers rate our articles as excellent or good
Learn more about the work of our research integrity team to safeguard the quality of each article we publish.
Find out more
ORIGINAL RESEARCH article
Front. Chem. Eng., 01 March 2024
Sec. Materials Process Engineering
Volume 6 - 2024 | https://doi.org/10.3389/fceng.2024.1347342
This article is part of the Research TopicDry Powder Coating in Manufacturing ProcessesView all 6 articles
Triboelectrification of powders and grains is deleterious in a large number of manufacturing operations, due to its adverse effect on process consistency and reliability. To mitigate it, charge neutralisers are commonly employed. However, their selection is often based on trial and error. This study is conducted to systematically examine the influence of the ionic polarity strength of a charge neutraliser, specifically aluminium stearate (AlSt), on charge transfer. AlSt has three types with different numbers of stearate chains, thereby influencing the electron exchange propensity of the molecule. The experiments involved surface-treated glass beads in the sieve size range of 90–150 µm (to make them hydrophilic by acid washing or hydrophobic by silanisation), then coated with the three forms of AlSt (mono-, di- and tri-) for charge mitigation. These coated beads were subjected to aerodynamic dispersion to cause triboelectrification, in order to quantitatively evaluate their charge neutralising effect. The experiments were conducted with four contact surfaces: stainless steel, copper, aluminium, and polytetrafluoroethylene (PTFE). Both acid-washed and silanised glass beads exhibited negative charging against aluminium, copper and stainless steel (typically around 22–44 nC/g), but positive charging against PTFE (around 90 nC/g and 19 nC/g for acid-washed and silanised, respectively), despite having significantly different surface functional groups. A complex trend is observed for the effect of the amount of AlSt present on the surfaces, the type of AlSt and the surface treatment. A relatively good charge reduction behaviour was seen for AlSt-coated acid washed glass beads, but for silanised glass beads, AlSt coating actually increases their charge level.
Triboelectrification, the phenomenon of electric charge transfer through contact and friction is commonly encountered in our daily lives; for example, the electric shock we sometimes experience on moving escalators and the small sparks we see when removing woolly jumpers in low humidity environments. However, this ubiquitous phenomenon can also lead to serious fire and explosion hazards in the manufacturing industry.
Scientists have long been intrigued by triboelectrification and its implications. It poses significant challenges in various industrial operations, particularly in the fields of manufacturing, conveying, handling, and processing of powders and grains. Triboelectrification can cause particles to segregate and adhere to the container walls and upset formulation balance. In extreme cases, it can even lead to fires and explosions, as documented in several studies (Nifuku et al., 1989; Mullarney and Hancock, 2004). Despite these challenges, triboelectrification has also been harnessed for beneficial purposes. One notable application is in the rapidly developing field of Tribo-Electric Nano-Generators (TENG) (Armitage et al., 2022; Mariello, 2022). These devices leverage the principles of triboelectrification to generate electricity, offering a promising avenue for sustainable low power energy production. However, the attention of this work is on the potential risks, for which antistatic agents are commonly used to mitigate charge accumulation. The selection of an effective antistatic agent is often based on trial and error. In this study, we explore the influence of the ionic polarity strength of a charge neutraliser, specifically aluminium stearate (AlSt), on charge transfer. AlSt is a common metallic soap, widely used across various industries due to its versatile properties. It serves as a thickener in paint, a water repellent, and a lubricant. The synthesis process of aluminium stearate results in three different forms: mono-, di-, and tri-stearate, with aluminium di-stearate being the most prevalent. Taghavivand et al. (2021) used the latter to study its effect on reducing wall fouling in fluidised bed reactors, a problem often caused by the build-up of electrostatic charge. Although it was reported that it was not that effective, nevertheless the use of the three forms makes it possible to systematically examine the influence of the polarity strength of the aluminium ion on charge mitigation. The number of alkyl chains present in aluminium stearate imparts different polarity to the aluminium atom, thereby altering its electron transfer characteristics. This makes it very interesting to explore which form of aluminium stearate has the greatest tendency to mitigate triboelectrification.
In this work, acid-washed and silanised glass beads are dry coated with the different forms of AlSt. They are then triboelectrically charged by a method developed in house (Zafar et al., 2018), whereby a small quantity (typically a few mg) is dispersed by an air pressure pulse. In this way the particles get charged to near equilibrium level (Ali and Ghadiri, 2017; Alfano et al., 2021). The particles fall straightaway into a Faraday cage, by which the net charge is measured. This systematic investigation aims to enhance our understanding of the charge mitigating mechanisms of aluminium stearate. The findings could potentially lead to more effective use of this metallic soap as an antistatic agent, thereby improving safety and efficiency in various industrial operations.
The glass beads utilised in this study were made of soda glass, a product commercially known as SiLibeads®, supplied by Sigmund Lindner, Warmensteinach, Germany. The beads have a size range of 90–150 μm, making them suitable for the intended application. Nevertheless, they were sieved again to ensure that they were in the designated sieve size range.
The aluminium mono-stearate was obtained from Merck Life Science (based in Dorset, United Kingdom), while the aluminium di-stearate and aluminium tri-stearate were obtained from Peter Greven (based in Bad Münstereifel, Germany). These differences in the number of alkyl chains could influence the way the different types interact with the treated surfaces, and thus their influence in charge mitigation.
For hydroxylation, glass beads were treated with a mixture of sulphuric acid (H2SO4) at a concentration of 98% and hydrogen peroxide (H2O2) at a volume concentration of 30%, known as Piranha solution. This process produces hydroxyl (-OH) groups on the surfaces, removing contaminants and making them highly hydrophilic. The ratio of these two components in the solution is 3:1. This solution is known for its strong oxidizing properties, which makes it highly effective for the hydroxylation process. The process began by mixing the glass beads with the prepared Piranha solution. The mixture was then left to sit overnight, allowing ample time for the hydroxylation reaction to occur. Following this, the glass beads were filtered and thoroughly rinsed with deionised water. The rinsing was continued until the waste solvent became pH neutral, indicating that all traces of the Piranha solution had been effectively removed. The cleaned and hydroxylated glass beads were then transferred into a sieve with a mesh size smaller than the size of the glass beads, allowing excess water to seep out while retaining the glass beads. The sieve containing the glass beads was then placed in an oven set at a temperature of 90°C. The beads were left to dry in the oven for 2 days.
Sigmacote® solution, supplied by Merck Life Science (Dorset, United Kingdom), is a siliconising reagent, having 1,7-Dichloro-1,1,3,3,5,5,7,7-octamethyltetrasiloxane suspended in heptane. The reagent reacts with the surface silanol (Si-OH) groups on glass, resulting in the formation of a hydrophobic film. The transformation is known as silanisation. In the context of this work, the silanisation process was carried out by immersing the hydroxylated glass beads in the Sigmacote® solution for 1 h, allowing sufficient time for the reaction to take place. After the immersion, the mixture was filtered and rinsed with heptane. This step is crucial as it helps to remove excess silane and hydrochloric acid (HCl), which is a by-product of the reaction, from the glass surface. The end result of this process is a monolayer coverage of silane coating on the surface of the glass beads. This coating alters the properties of the glass beads, making them hydrophobic. Following the rinsing process, the wet cake was left in a fume cupboard to dry. This was done under room temperature conditions and the drying process was allowed to continue overnight. The end result is a batch of glass beads with a hydrophobic silane coating, ready for further use or analysis.
Both the acid-washed and silanised glass beads were subdivided into smaller batches of 40 g to be blended with the three types of aluminium stearate powder. Different amounts of aluminium stearate were weighted and added to the glass beads, producing samples with 0.5 and 3 wt% of aluminium stearate, respectively. The coating process was performed using the Formatrix 4M8-Trix ProCepT high shear mixer, which has a three-bladed impeller that induces mechanical agitation to the glass beads and aluminium stearate mixture, promoting a homogeneous mixing. Following the procedure described by Goh et al. (2021), the glass beads-AlSt mixtures were agitated under an impeller rotational speed of 400 RPM for 20 and 40 min, respectively.
The tribocharging rig, based on the work of Ali and Ghadiri (2017) and Zafar et al. (2018), was used in this work to assess the performance of aluminium mono-, di- and tri-stearates in mitigating the charge built-up on functionalised glass beads. A schematic of the setup is shown in Figure 1. The tribocharging rig makes use of the aerodynamic dispersion unit of Malvern Panalytical Morphologi G3 to induce charge to the particles fed into system. A short pulse of pressurised dry air of 20 ms is released into the dispersion capsule, upon which particles fully are dispersed and experience a large number of collisions against the inner confining walls. This causes charge transfer between the particles and the dispersion capsule, following which the particles exit the dispersion spool and fall into a Faraday cup, where their net charge is measured by a Keithley 6514 electrometer. The dispersion capsule and post-dispersion duct are interchangeable to provide different contact surfaces. In this work, we evaluated the charge mitigating effect of AlSt-coated glass beads against stainless steel, copper, aluminium and polytetrafluoroethylene (PTFE). The sample volume was kept constant at 5 mm3 for each test using a volumetric sampling spoon, and a dispersion pressure of 4 barg was used to disperse them. At least three measurements were made for each sample and an average charge level was calculated.
FIGURE 1. A schematic of the tribocharging rig (left) and a photo of the dispersion spools made of copper, aluminium, PTFE and stainless steel.
Surface modification via acid washing and silanisation changes the surface functional group of the glass beads. It is well known that acid washing hydroxylates the glass surfaces and exposes the -OH groups, while subsequent silanisation process introduces methyl groups (-CH3) which replace the hydroxyl group on the glass surfaces. Having these vastly different surface functional groups, one can therefore expect these treated glass beads to differ in their charging behaviour. The specific charge per unit mass acquired by the surface-treated glass beads when they collide against different materials is shown in Figure 2. Untreated glass beads charge positively against aluminium, copper and PTFE. According to the classical triboelectric series of materials, glass is the most electropositive, followed by aluminium, steel, copper and PTFE (Gooding and Kaufman, 2019; Zou et al., 2020) and this is in agreement with the results obtained here. Interestingly, when charging against stainless steel, untreated glass beads acquire a negative charge. It is worth taking note that carbon steel is more electronegative compared to glass according to the triboelectric series; it was therefore intuitively assumed that stainless steel, while having other components in the alloy mix, should somehow exhibit similar triboelectric charging properties. The result obtained here, albeit slightly unexpected, is not unjustifiable. Unlike steel, stainless steel oxidises and a protective layer of chromium oxide (Cr2O3) is formed on the surface. This metal oxide surface has not been extensively studied in the literature and given a position in the triboelectric series. However, our finding of glass beads charging negatively against stainless steel is not unique. Choi et al. (2020) reported the same observation, where they also found glass beads charged negatively against stainless steel. They also measured the work function of both glass beads and stainless steel and found that the former has a higher work function. When two materials are interacting, the one with lower work function tends to donate electrons to the one with higher work function.
FIGURE 2. Specific charge of untreated, acid-washed and silanised glass beads against aluminium, copper, PTFE and stainless steel.
Acid-washed glass beads charge negatively against aluminium, copper and stainless steel, but positively against PTFE. Based on these results, the exposed hydroxyl groups on the glass surfaces reduce their electropositivity, as indicated by the shift in their relative position (from being the most electropositive to the third in the ranking) in the triboelectric series. The silanised glass beads have very similar triboelectric charging characteristics as compared to acid-washed glass beads, charging negatively against aluminium, copper and stainless steel, but positively against PTFE. The methyl groups appear to have a retarding effect on the chargeability. The only difference is that silanised glass beads charge slightly less compared to acid-washed glass beads against the four materials tested.
In terms of the charge level, whilst both acid-washed and silanised glass beads charge to the same polarity, their charge levels differ. Acid-washed glass beads appear to charge more compared to silanised glass beads regardless of the charge polarity. Against aluminium, acid washing and silanisation both change the polarity of the glass beads and bring their charge level to an almost similar value around −40 nC/g. Against copper, similar behaviour is seen, but the charge level of silanised glass beads is lower than that of acid-washed (−22 vs. −40 nC/g, respectively). Against PTFE, whilst keeping the same polarity, acid washing reduces the charge of glass beads by ∼10% from the untreated case, but for the silanised glass beads the charge level is reduced by ∼80%, down to 19 nC/g. Against stainless steel, both surface treatments actually enhance the charge level of the glass beads from 12 nC/g (untreated case) to around 30 nC/g for silanised and 48 nC/g for acid-washed cases.
For reference, the three forms of AlSt were tested on their own. The specific charge acquired per unit mass of the aluminium stearate powders against different materials is shown in Figure 3. Aluminium mono- and di-stearate charge positively against aluminium, copper and PTFE, but negatively against stainless steel. In contrast, aluminium tri-stearate powder acquires negative charge from aluminium, copper and stainless steel, but a positive charge from PTFE. Looking at the chemical structure of aluminium mono- and di-stearate (Figure 4), aluminium tri-stearate is far more ionic than the other forms of aluminium stearate. Hydroxyl groups absent in aluminium tri-stearate but that is not the case for aluminium mono- and di-stearates. The metal atom and the stearic acid chains of aluminium tri-stearate are held together by ionic bonding. It is therefore speculated that this could have led to the disparity seen in the charge polarity between aluminium tri-stearate and the rest, though further investigation is needed to support this.
FIGURE 3. Specific charge of AlStx (mono-, di- and tri-) against aluminium, copper, PTFE and stainless steel.
The effect of coating acid-washed glass beads with aluminium stearate powders on their chargeability is shown in Figure 5. In general, at 0.5 wt%, all the three aluminium stearate powders show a good level of mitigating effect in the charge acquired by the acid-washed glass beads. Their effect is most prominent when the coated acid-washed glass beads are charged against stainless steel, showing a reduction in specific charge of ∼80%. On PTFE, the presence of aluminium stearate reduces the specific charge of acid-washed glass beads by ∼44%. A change in charge polarity is observed when the coated acid-washed glass beads are charged against aluminium and copper. In the case of aluminium, the level of charge acquired by the coated acid-washed glass beads, albeit of different polarity, is very small. This shows that the addition of aluminium stearate is very effective in retarding the charge transfer between the acid-washed glass beads and aluminium. The same cannot be extended to the case of copper, where the acid-washed glass beads acquire a considerable amount of opposite charge in the presence of aluminium stearate powder. While the difference is not very discernible amongst the three types of aluminium stearate, in most cases the tri-stearate form appears to show the most effective charge mitigating effect in acid-washed glass beads.
FIGURE 5. Specific charge of acid-washed glass beads coated with 0.5wt% (A) and 3wt% (B) of AlStx (mono-, di- and tri-) against aluminium, copper PTFE and stainless steel.
Increasing the concentration of aluminium stearate in acid-washed glass beads does not enhance their charge mitigating properties. In fact, this has an opposite effect where the acid-washed glass beads get even more charged as shown in Figure 5B. At 3 wt%, aluminium mono- and di-stearate exacerbate the specific charge acquired per unit mass of the acid-washed glass beads against aluminium, copper and PTFE. At its extreme, the charge level almost trebles when aluminium mono-stearate is added to the acid-washed glass beads and charged against aluminium. On the other hand, aluminium tri-stearate produces a good degree of charge reduction in the acid-washed glass beads when they are charged against aluminium and stainless steel. Against PTFE, the trend reverses, and the results show that aluminium tri-stearate actually aggravates the charge level of the acid-washed glass beads. In contrast, Aluminium mono-stearate, when added to the acid-washed glass beads at 3 wt%, produces a much better charge reduction effect compared to 0.5 wt% for the PTE case.
The effect of adding aluminium stearate to silanised glass beads on their charging behaviour is shown in Figure 6. While both the acid-washed and silanised glass beads exhibit similar charging tendency as previously discussed, they do not behave the same way when aluminium stearate is added to them. At 0.5 wt%, the silanised glass beads actually acquire higher charge levels in the presence of aluminium stearate for most of the cases. Against aluminium, all three forms of aluminium stearate show varying degrees of charge enhancement effect, with the mono-stearate form at the top of the list, followed by the di-stearate and tri-stearate forms. No change in the charge polarity of the silanised glass beads is observed when aluminium stearate is added to them. The only exception is when the silanised glass beads are coated with aluminium tri-stearate and charged against PTFE, as they charge negatively.
FIGURE 6. Specific charge of silanised glass beads coated with 0.5wt% (A) and 3wt% (B) of AlStx (mono-, di- and tri-) against aluminium, copper PTFE and stainless steel.
A notable increase in the charge acquired by the silanised glass beads is noted for aluminium mono- and distearates when their concentration is increased to 3 wt%. An interesting observation here is that the charge level does not increase much for the case of aluminium tri-stearate. Even though the amount of aluminium-tri-stearate added to the silanised glass beads is almost sixfold of the lower concentration, the charge acquired remain at almost the same level when they are charged against aluminium, copper and stainless steel. While the exact reason is not known, this highlights the special effect of aluminium tri-stearate. However, aluminium tri-stearate performs rather poorly when it is added to the silanised glass beads and charged against PTFE. It actually increases the charge level of the silanised glass beads the most.
To provide a more direct comparison of the charge mitigating effect of aluminium stearate in acid-washed and silanised glass beads, the test results are grouped together as illustrated in Figure 7. At low concentration (0.5 wt%), all the three forms of aluminium stearate reverse the charge polarity of the acid-washed glass beads from negative to positive when they are charged against aluminium. However, for silanised glass beads, while maintaining the same charge polarity, the charge level actually increases when aluminium stearate is added to them. Note that both acid-washed and silanised glass beads charge negatively against aluminium. The fact that aluminium stearate coated acid-washed and silanised glass beads have opposite charge polarity is an indication that the charge transfer mechanism entailed here is a complicated one. The same behaviour is also seen when they are charged against copper. One possible explanation to this behaviour is the restructuring of aluminium stearate molecules on the surface of the acid-washed and silanised glass beads. Aluminium stearate molecules are amphipathic, having a hydrophilic head and hydrophobic tails. The hydrophilic surface of acid-washed glass beads could attract the hydrophilic stearic acid chains of the aluminium stearate and form a structured coating on the surface of the acid-washed glass beads, where the hydrophobic tails are sticking out. On silanised glass beads, where the surfaces are hydrophobic, adherence of the stearic acid chains is favoured, resulting in a coating in which the hydrophilic heads are pointing outwards. Charge transfer happens at the contact interface and the different aluminium stearate coating structures could therefore alter the charge transfer process. Against PTFE, both acid-washed and silanised glass beads charge positively when coated with aluminium stearate. The only exception is the silanised glass beads coated with aluminium tri-stearate which charge negatively against PTFE, a highly surprising result. Against stainless steel, all of them charge negatively. However, a very effective charge reduction is observed in the acid-washed glass beads but not the silanised glass beads.
FIGURE 7. Specific charge of acid-washed and silanised glass beads coated with 0.5wt% of AlStx (mono-, di- and tri) against aluminium, copper, PTFE and stainless steel.
At 3 wt% (Figure 8), both the acid-washed and silanised glass beads are charged negatively against aluminium, contrasting to that of 0.5 wt%. In fact, this behaviour of acquiring the same charge polarity when they were charged against the same material is seen for all the four materials tested. When the concentration of aluminium stearate is high, the surface of the glass beads is heavily covered by it, and hence the charge transfer is potentially dominated by the interaction between the antistatic agent and the contacting surface. In addition, at high concentration, material transfer could also potentially play a vital role in the tribocharging behaviour of the coated glass beads. Nevertheless, whilst both acid-washed and silanised glass beads behave similarly when a high concentration of aluminium stearate is added to them, their behaviour is different from the observations made for pure aluminium stearate powders (Figure 3). Interestingly, when coated at 0.5 wt%, the behaviour of the coated acid-washed glass beads against the four contact materials is similar to the results obtained from dispersing pure aluminium stearate powders. However, at 3 wt%, the trend starts deviating, and the observations made in Figure 3 no longer apply. This is surprising, as one would expect the behaviour of the 3 wt% coated acid-washed glass beads to be more similar to that of the pure aluminium stearate powders. On the other hand, the trend of results of the coated silanised glass beads show no resemblance to the data collected for pure aluminium stearate powders (shown in Figure 3), regardless of the concentration. The experimental data presents a complex pattern of the effect of antistatic agent. Therefore, a first-principle molecular modelling approach based on density functional theory (DFT) could potentially provide valuable insights and help unravel the complex phenomenon observed here.
FIGURE 8. Specific charge of acid-washed and silanised glass beads coated with 3wt% of AlStx (mono-, di- and tri-) against aluminium, copper, PTFE and stainless steel.
The study investigated the effect of three different forms of aluminium stearate (aluminium mono-, di- and tri-stearate) on the charge mitigation of acid-washed and silanised glass beads. This was evaluated using a novel method based on aerodynamic dispersion. The key findings from this study are as follows:
i. Acid-washed glass beads exhibited negative charging against aluminium, copper, and stainless steel, but positive charging against PTFE. Silanised glass beads were found to behave similarly despite a very different surface chemistry.
ii. Pure aluminium mono- and di-stearate charged positively against aluminium, copper, and PTFE, but negatively against stainless steel.
iii. Pure aluminium tri-stearate, an ionic compound, charged negatively against aluminium, copper, and stainless steel, but positively against PTFE.
iv. When present at a concentration of 0.5 wt%, all three types of aluminium stearate reduced the charge acquired by the acid-washed glass beads, with the most significant effect observed against aluminium and stainless steel (most effective when charge against stainless steel, reduction of charge as high as 90% is observed).
v. At a higher concentration of 3 wt% aluminium stearate, the charge level of the acid-washed glass beads actually increased, instead of reducing. However, aluminium tri-stearate still shows good charge mitigating properties for acid-washed glass beads.
vi. None of the three forms of aluminium stearate had any charge reduction effect on the silanised glass beads and increasing the concentration of aluminium stearate exacerbated the charge.
These findings highlight the complexity of the triboelectrification of particulate solids and suggest that a single antistatic agent may not be sufficient to neutralise the tribocharging effect of different particulate solids. The identification of a suitable antistatic agent requires knowledge of the tribocharging properties of the particulate solids against the material of interest, as well as an understanding of the interaction between the particulate solids and the antistatic agent. The method developed here provides a quick evaluation of the effect of antistatic agent on charge mitigation. However, a fundamental understanding is needed to have a predictive capability.
The original contributions presented in the study are included in the article/Supplementary Material, further inquiries can be directed to the corresponding author.
WG: Formal Analysis, Writing–original draft, Writing–review and editing, Data curation, Investigation, Methodology, Supervision. JG: Writing–original draft, Data curation. XJ: Supervision, Writing–review and editing, Investigation. MG: Conceptualization, Methodology, Supervision, Writing–review and editing, Funding acquisition, Project administration.
The author(s) declare financial support was received for the research, authorship, and/or publication of this article. The financial support of the engineering and Physical Sciences Research Council for the project (grant number EP/001766/1) as a part of “Friction: The Tribology Enigma” Programme Grant (www.friction.org.uk) and for the project (EP/X023389/1) as a part of “Modelling, Validation and Application of Triboelectrification” Standard Grant (www.triboelectrification.org) are gratefully acknowledged.
The authors would like to thank Chuks Obi for preparing the test samples. The authors would also like to express their gratitude to Peter Greven for supplying the aluminium stearate powders used in this work.
The authors declare that the research was conducted in the absence of any commercial or financial relationships that could be construed as a potential conflict of interest.
All claims expressed in this article are solely those of the authors and do not necessarily represent those of their affiliated organizations, or those of the publisher, the editors and the reviewers. Any product that may be evaluated in this article, or claim that may be made by its manufacturer, is not guaranteed or endorsed by the publisher.
Alfano, F. O., Di Renzo, A., Di Maio, F. P., and Ghadiri, M. (2021). Computational analysis of triboelectrification due to aerodynamic powder dispersion. Powder Technol. 382, 491–504. doi:10.1016/J.POWTEC.2021.01.011
Ali, M., and Ghadiri, M. (2017). Analysis of triboelectric charging of particles due to aerodynamic dispersion by a pulse of pressurised air jet. Adv. Powder Technol. 28, 2735–2740. doi:10.1016/J.APT.2017.07.026
Armitage, J. L., Ghanbarzadeh, A., Bryant, M. G., and Neville, A. (2022). Investigating the influence of friction and material wear on triboelectric charge transfer in metal–polymer contacts. Tribol. Lett. 70, 46. doi:10.1007/S11249-022-01588-1
Choi, K., Choi, H., and Suzuki, T. (2020). Charging behavior of glass beads using a spiral air type tribocharging apparatus that utilizes a Faraday cup. J. Loss Prev. Process Ind. 65, 104124. doi:10.1016/J.JLP.2020.104124
Goh, W. P., Sanavia, A. M., and Ghadiri, M. (2021). Effect of mixer type on particle coating by magnesium stearate for friction and adhesion modification. Pharmaceutics 13, 1211. doi:10.3390/pharmaceutics13081211
Gooding, D. M., and Kaufman, G. K. (2019). “Tribocharging and the triboelectric series,” in Encycl. Inorg. Bioinorganic Chem. doi:10.1002/9781119951438.eibc2239.pub2
Mariello, M. (2022). Recent advances on hybrid piezo-triboelectric bio-nanogenerators: materials, architectures and circuitry. Nanoenergy Adv. 2, 64–109. doi:10.3390/nanoenergyadv2010004
Mullarney, M. P., and Hancock, B. C. (2004). Improving the prediction of exceptionally poor tableting performance: an investigation into Hiestand’s “special case.”. J. Pharm. Sci. 93, 2017–2021. doi:10.1002/jps.20108
Nifuku, M., Ishikawa, T., and Sasaki, T. (1989). Static electrification phenomena in pneumatic transportation of coal. J. Electrostat 23, 45–54. doi:10.1016/0304-3886(89)90031-4
Taghavivand, M., Sowinski, A., and Mehrani, P. (2021). Triboelectric effects of continuity additives and a silica catalyst support on polyethylene fluidized bed wall fouling. Chem. Eng. Sci. 245, 116882. doi:10.1016/j.ces.2021.116882
Zafar, U., Alfano, F., and Ghadiri, M. (2018). Evaluation of a new dispersion technique for assessing triboelectric charging of powders. Int. J. Pharm. 543, 151–159. doi:10.1016/J.IJPHARM.2018.03.049
Keywords: aluminium stearate, dry coating, triboelectrification, charge modifier, aerodynamic dispersion, functionalised surface
Citation: Goh WP, Guo J, Jia X and Ghadiri M (2024) Influence of type of aluminium stearate on triboelectrification of dry-coated surfaces of functionalised glass beads. Front. Chem. Eng. 6:1347342. doi: 10.3389/fceng.2024.1347342
Received: 30 November 2023; Accepted: 20 February 2024;
Published: 01 March 2024.
Edited by:
Colin Hare, Newcastle University, United KingdomReviewed by:
Fengxian Fan, University of Shanghai for Science and Technology, ChinaCopyright © 2024 Goh, Guo, Jia and Ghadiri. This is an open-access article distributed under the terms of the Creative Commons Attribution License (CC BY). The use, distribution or reproduction in other forums is permitted, provided the original author(s) and the copyright owner(s) are credited and that the original publication in this journal is cited, in accordance with accepted academic practice. No use, distribution or reproduction is permitted which does not comply with these terms.
*Correspondence: Mojtaba Ghadiri, bS5naGFkaXJpQGxlZWRzLmFjLnVr
†Present address: Jiachen Guo, Airworthiness Certification Center, Civil Aviation Administration of China, Beijing, China
Disclaimer: All claims expressed in this article are solely those of the authors and do not necessarily represent those of their affiliated organizations, or those of the publisher, the editors and the reviewers. Any product that may be evaluated in this article or claim that may be made by its manufacturer is not guaranteed or endorsed by the publisher.
Research integrity at Frontiers
Learn more about the work of our research integrity team to safeguard the quality of each article we publish.