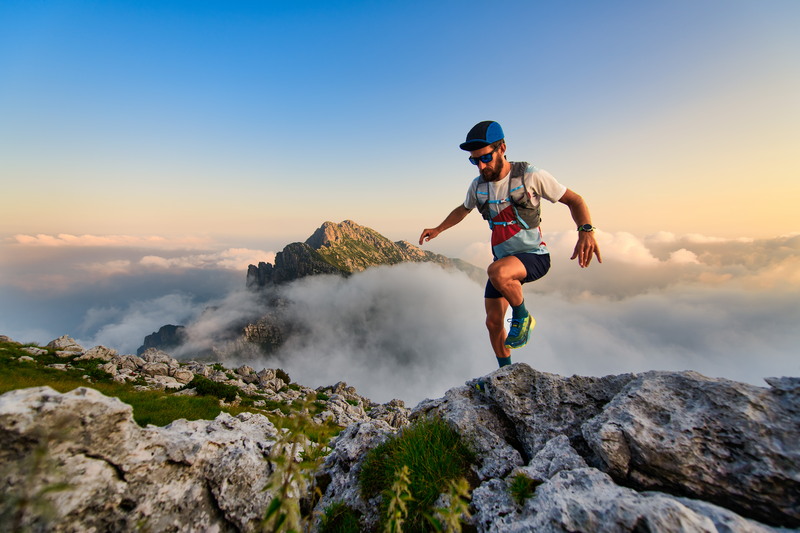
94% of researchers rate our articles as excellent or good
Learn more about the work of our research integrity team to safeguard the quality of each article we publish.
Find out more
REVIEW article
Front. Chem. Eng. , 03 March 2023
Sec. Separation Processes
Volume 5 - 2023 | https://doi.org/10.3389/fceng.2023.1066091
This article is part of the Research Topic Membrane Engineering and Process Intensification View all 5 articles
Carbon monoxide (CO) is an important gas required for various industrial processes. Whether produced directly from syngas or as part of by-product gas streams, valorization of CO streams will play an important role in the decarbonization of industry. CO is often generated in mixtures with other gases such as H2, CO2, CH4, and N2 and therefore separation of CO from the other gases is required. In particular, separation of CO from N2 is difficult given their similar molecular properties. This paper summarizes the current state of knowledge on the four processes for separation of CO from gas mixtures: cryogenic purification, absorption, adsorption and membrane separation. Particular emphasis is placed on technical processes for industrial applications and separation of N2 and CO. Cryogenic processes are not suitable for separation of CO from N2. Absorption developments focus on the use of ionic liquids to replace solvents, with promising progress being made in the field of CO solubility in ionic liquids. Advancements in adsorption processes have focused on the development of new materials however future work is required to develop materials that do not require vacuum regeneration. Membrane processes are most promising in the form of solid state and mixed matrix membranes. In general, there is limited development beyond lab scale for new advancements in CO separation from gas streams. This highlights an opportunity and need to investigate and develop beyond state-of-the-art processes for CO separation at industrial scale, especially for separation of CO from N2.
To achieve large scale decarbonization, or even re-carbonization (i.e., substituting fossil-derived carbon with biomass-derived or circular carbon) in industry, CO2 and CO utilization will play a key role (Gabrielli et al., 2020). This means the conversion of CO2 and CO to various chemicals, either thermochemically or electrochemically. Currently, industrial quantities of CO are required for various processes, including Fisher-Tropsch synthesis, methanol production, hydroformylation, and phosgene and acetic acid production (Evans et al., 2018). These large quantities of CO are primarily produced from syngas derived from biomass and fossil fuels, through Steam Methane Reforming (SMR), Partial Oxidation (POX) or Autothermal Reforming (ATR) (Bierhals, 2001). On smaller scales, CO production is possible electrochemically with the eCOs™ system from Haldor-Topsoe (Topsoe, 2017). In some industries, CO can be a significant component of by-product gas streams (e.g., from blast furnaces in steel production). These gas streams are currently valorized through combustion for electricity production, generation of steam or to satisfy internal heating demands. In addition to iron and steel industries (Van Dijk et al., 2018), this valorization pathway is common for titanium, silicon carbide, and carbon black production.
Purification of CO is necessary, whether produced directly thermochemically or electrochemically, or as a by-product of another process, because CO is always produced with of H2, CO2, H2O, CH4, and N2. Depending on the conversion process, direct utilization of the mixed gas stream can be hampered, in particular by the presence of N2, due to reduced partial pressure of the reactive components. This effect is exacerbated if a recycle is introduced. There is also a potential economic drawback from the use of N2-rich feed as larger compressors reactors and separation systems are required. Therefore, the separation of CO from other gases is important industrially in syngas processing; in particular, CO separation from N2 is important for separating the energy from low value residual streams in industry. Therefore, this paper focuses on the separation of CO from N2.
Chemical engineering separation principles show that molecular properties and, by extension, bulk properties (vapor pressure, absorptivity, solubility, diffusivity) can be used to formulate ways of separating a gas mixture. A large difference in the molecular properties of the different gases can indicate a separation method. Key molecular properties of gases, such as molecular weight, polarizability, Van der Waals volume, Van der Waals area, molecular shape, dipole moment, dielectric constant, electric charge, radius of gyration, and electron configuration (de Haan et al., 2013) are shown in Table 1. Due to the many similar properties of CO and N2, it is very challenging to separate these gases and, after other gases have been separated, CO and N2 typically remain.
TABLE 1. Molecular properties of gases (Data sourced from Linstrom, 1997; Yaws, 2015; Uhlig and Keyes, 1933).
The bulk properties of gases that can be exploited to facilitate separation of CO and N2 are vapor pressure and the affinity of CO in forming π-complexation bonds. These properties allow for direct separation of CO from N2 via four main processes: cryogenics, absorption, adsorption and facilitated membrane separation. An overview of advancements in these technologies is necessary, since the last review on this topic was done more than 25 years ago (Dutta and Patil, 1995).
Although there are other reviews on CO-N2 separation, these papers focus solely on materials (Evans et al., 2018) and lack a process technology element, which is key to industrial application. Furthermore, indirect methods of separation of CO and N2 are considered out of scope for this review, for example chemical looping (Flores-Granobles and Saeys, 2022), or the water gas shift reaction to produce H2 from the CO (van Dijk et al., 2018) and subsequent separation of the H2 from the N2 using pressure swing adsorption or membranes.
The goal of this paper is to systematically review the four main processes for direct CO-N2 separation, i.e., cryogenic purification, absorption, adsorption and membrane separation, with specific attention to process technologies for industrial applications.
Cryogenic purification exploits the vapor pressure difference between gas components at very low temperatures. The principle of exploiting vapor pressure differences is the most mature in terms of industrial application. Cryogenic purification is deployed in multiple industrial applications such as Air Separation Units, Natural Gas Treating, Ethylene Purification and in commercial CO production from natural gas.
Based on the literature review, publications on cryogenic separation of CO are limited to the design of a cryogenic distillation column for CO-H2 separation (Li et al., 2018). No references exist for the separation of CO from relatively high concentrations of N2 by cryogenic purification. Processes for the separation of CO from syngas mixtures are known and commercially deployed. The concept is to cool the gas mixture to a point where one component condenses while the other components stay in the vapor phase. With the normal boiling point of CO being −191.52°C and that of N2 being −195.75°C (Table 1), cryogenics are required. Originally, syngas-CO separation processes were developed to operate at higher pressures, where the boiling point difference between CO and N2 is small. The design is tailored towards higher pressure since most reformers operate at elevated pressures based on techno-economic trade-offs. The high pressure operation means that the cryogenic separation systems are not suitable for mixtures with high N2 content (>5 mol%). A major limitation of the cryogenic processes is the deep cleaning required to remove components that freeze and block pipework and equipment. This includes common species such as CO2 and H2O.
The current cryogenic purification processes for the production of CO can be divided into two types: the partial condensation process and the methane wash process.
The process flow diagram of a partial condensation process is shown in Figure 1. The heat exchangers shown in the process are indicative of heating or cooling and, in the actual process, these are fully integrated. The process functions by first cooling the gas mixture to −193.15°C at an inlet pressure of 30–40 bar (Bierhals, 2001) (i.e., typical operating pressure of a SMR or POX reactor). CH4 and CO are the first species to condense at these temperature and are removed in SEP-01. The liquid product from SEP-01 is reduced in pressure and fed to a second vessel, SEP-02, where any dissolved H2 is removed. This hydrogen-rich gas is compressed and recycled. The liquid phase from the second separator SEP-02 is again reduced in pressure and fed to a CO/CH4 separation tower (SEP-04). If there is a lot of CH4 in this liquid mixture, a CH4-CO separation column can be introduced prior to increasing the temperature. The H2-rich gas phase from the first separation vessel (SEP-01) is cooled to −203.15°C to condense out any remaining CO. If there is little N2 in the feed, the only remaining gas will be the hydrogen. This hydrogen is passed through a heat exchanger to increase its temperature. The refrigeration is provided by expanding a part of the H2-rich stream in a turbine and using CO-rich product coming from the second liquid separator.
FIGURE 1. Process flow diagram of a partial condensation process for separation of CO-CH4-H2 mixture. Adapted from Dutta and Patil (1995) with permission from Elsevier.
Variations of the process can be found for gas mixtures with low CH4 content where the CO/CH4 separation tower (SEP-04) is avoided (Bierhals, 2001). There are numerous variations depending on how the heat integration is performed and the amount of energy extracted from the hydrogen. However, essentially, the separation is between a mixture of CO and H2.
The methane wash variant of cryogenic purification functions by exploiting the high solubility of CO in CH4. The process can consist either one or two methane wash stages, the process flow diagram for both are shown in Figures 2, 3. Note that the heat exchangers shown are indicative of heating or cooling, and are fully integrated with each other in the real process to minimize external cooling duty.
FIGURE 2. Process flow diagram of a single-stage methane wash process. Adapted from Bierhals (2001) with permission from John Wiley and Sons.
FIGURE 3. Process flow diagram of a two-stage methane wash process. Adapted from Dutta and Patil (1995) with permission from Elsevier.
The single-stage methane wash process is shown in Figure 2. The feed stream is at a pressure of 40 bar and is cooled to −181.15°C (Bierhals, 2001), this condenses out most of the CO and CH4 and this mixture is subsequently fed to an absorber column. In the column, a methane wash removes CO to ppm levels, and the remaining H2 stream with 1%–1.5% CH4 exits the top of the column. This hydrogen-rich stream is expanded in a gas turbine to recover energy, and after heat recovery is sent to the battery limits. The liquid product from the bottom of the absorption tower is increased in temperature and reduced in pressure (to 1 or 2 bars) and fed to the splitter column. Liquid methane is recovered at the bottom and is pumped and recycled, with part of the recycle being expanded for cooling and use as fuel. The CO-rich product is recovered from the top of the column at a purity between 97%–99%. Part of the CO-rich product is compressed and cooled in the reboiler of the splitter column; this stream is further cooled before being flashed. The liquid CO is used as reflux in the splitter column.
The two-stage methane wash is shown in Figure 3. Feed gas is cooled and then washed with liquid methane in the wash column, where almost all of the CO is absorbed, leaving behind a H2-rich product that contains ppm levels of CO and is saturated with CH4 at concentrations of 2%–3%. The hydrogen-rich stream is increased in temperature and sent to the battery limits. The liquid methane product from the wash column contains dissolved CO and also H2. This H2 is removed by first heating and flashing the stream in a flash column. In order to limit the loss of CO, a second methane wash is used in the flash column. The gas product from the flash column is sent to battery limits for use as fuel. The liquid product is heated and flashed again, this time with the aim of ‘regenerating’ the liquid methane to recover the CO. This is done in the splitter column, which is essentially a distillation column with vapor recompression and heat integration. The column produces a light product (CO) which is compressed and part of it is sent to the battery limits and the remainder is used as a heat source for the reboiler. After further cooling of the CO stream, it is flashed, with the liquid becoming a reflux for the splitter column. The heavy product (CH4) is withdrawn as a liquid from the bottom and is pumped, cooled and used in the wash column and flash column. Part of the liquid methane, after heat recovery, is sent to the battery limits as fuel.
The cryogenic-pressure swing adsorption hybrid processes refer to patents but not operating processes, and involves a combination of Pressure Swing Adsorption (PSA) and partial condensations to separate CH4, H2, and CO mixtures. Similar to the previous cryogenic processes, there is no indication of nitrogen is presence in these gas mixtures. Figure 4 shows the first Cryogenic-PSA hybrid process. In this process a hydrogen PSA is used to separate the feed gas into a H2 product and a CO-rich tail gas. This tail gas is separated using partial condensation process to produce a H2-rich stream, a CO-rich stream and a mixed steam. The H2-rich stream is combined with the H2 stream from the PSA. The CO-rich stream exists as a product and the mixed stream is used as fuel outside of the separation process (Fabian, 1993).
Figure 5 shows the second Cryogenic-PSA hybrid process. In this process, the feed gas is fed first into a cryogenic separation, specifically a partial-condensation process which produces a H2 rich stream, a mixed stream mainly consisting CH4 and a CO-rich stream. The H2 rich stream is sent to a PSA for further purification, the mixed stream is used as fuel outside of the separation process and the CO-rich stream exists as a product. The PSA separates the H2-rich stream in a purified H2 stream and a tail gas. The purified H2 stream exits as a product and the tail gas is used as fuel outside of the separation process (Trott, 2013).
Absorption processes exploit the difference in affinity of one or more gases to a liquid. This affinity can be in the form of solubility of a molecule or through a chemical interaction between a target gas and a functional component in the liquid. The target molecules are absorbed into the liquid volume and desorbed in a consecutive step through change of pressure and/or temperature.
In the case of physical absorption, the molecules remain inert within the solvent. The driving force for this process is a high partial pressure during the absorption and a reduced pressure during the desorption. In case of chemical absorption, the molecules absorb into the solvent and react with the solvent. Because this process is exothermic a higher temperature is needed in the desorption step. Chemical absorption is generally preferred for separation processes at low partial pressures as it often has a more favorable equilibrium (de Haan et al., 2013). In both physical and chemical absorption, the properties of the solvent play a critical role. The solubility of the target species relative to other species will dictate the degree of separation and the size of the process units. While solvent stability will determine the need for pre-treatment and viscosity will determine both column hydrodynamics and the energy required for pumping. Therefore, the solvent properties are critical for an absorption process.
Examples of industrial absorption processes are the separation of acid gases (CO2, H2S) from flue gases using chilled methanol [Rectisol™, Linde and Lurgi (Linde, 2020)] and Selexol™ [UOP (UOP LLC, 2009)] as physical solvents. The same separation can also be achieved using chemical solvents such as monoethanolamine or other Amines (Koytsoumpa et al., 2015).
The state of the art CO absorption technology is COpure by Costello (R. C. Costello and Assoc. Inc, 2020), which is a successor of COSORB I and II by Tenneco and KTI (Keller and Schendel, 1988). It utilizes CuAlCl4 in toluene as a chemical solvent (Go et al., 2019). The CO is selectively absorbed by binding reversibly with the Cu+ ion (Hogendoorn et al., 1995). The process flow diagram is shown in Figure 6. After the absorber, the rich solvent is flashed to desorb the physically absorbed components such as H2 and only the chemically-absorbed CO is sent to the stripper column. The process is able to separate CO with a purity of 98% and recovery of 99% (R. C. Costello and Assoc. Inc, 2020). Go et al. (2019) modelled the process and concluded that a minimum CO concentration of 0.16 kmol/m3 is required to reach a removal rate of >99%. The equilibrium relationship for the absorption reaction of the predecessor, COSORB, indicates that the absorption can be assumed as instantaneous in regards to mass transfer (Hogendoorn et al., 1995). The sensitivity of the solvent towards impurities such as H2O and H2S leads to an extensive cleaning process prior to the COpure process to avoid harmful side reactions, like production of HCl, and absorbent degradation.
FIGURE 6. Process diagram of the COpure-process . Adapted from R.C. Costello & Assoc. Inc. (2020), Courtesy of R.C. Costello & Assoc., Inc.
Ionic Liquids (IL) are compounds consisting completely of ions with melting point below 100°C. Multiple authors have claimed that ionic liquids are preferred compared to conventional solvents due to their thermal stability and non-volatility. The developments of ionic liquids for CO-N2 separation has focused on solvent characterizing (density, viscosity, etc.) and performance improvement (CO solubility, N2 solubility, etc.), the performance improvements are outlined below. The use of ILs is not limited to absorption, some authors have proposed the use of ILs in supported ionic liquid membranes (SILM) (David et al., 2012; Zarca et al., 2017a; Zarca et al., 2017b), this is covered in the next subsequent section of this paper.
The first screening of ionic liquid for CO separation was performed by (Ohlin et al., 2004), where 37 ionic liquids and some organic solvents were evaluated, and 1-butyl-3-methylimidazol-3-ium ([bmim][Tf2N]) appeared to the most promising. Since then a number of other assessment have also been carried out on [bmim]-based ionic liquids (Raeissi et al., 2013; Lei et al., 2014). The absorption of CO into 1-hexyl-3-methylimidazolium chlorocuprate ([hmim][Cl]) with and without added CuCl has been studied (David et al., 2012). The addition of CuCl increased the absorption of CO without increasing the absorption of N2 leading to the conclusion that it makes the IL selective towards CO. Carbanion-functionalized ionic liquids were reported by to have higher absorption capacity (Tao et al., 2017) and more fundamental work was carried out to evaluate IL containing Cu+ (Repper et al., 2017). The more recent addition is the use of copper-(I) doped deep eutectic solvents (Cui et al., 2021), which show even higher solubilities for CO. However, the authors do not report N2 solubility and therefore the selectivity cannot be determined. An overview of the CO solubilities for various ILs and non-IL solvents are shown in Figure 7 (Tao et al., 2017; Liu et al., 2019; Cui et al., 2021). The figure shows that over the last 2 decades the CO solubilities of ILs have increased by two orders of magnitude, however, the CO solubility of the COpure process is not yet matched. Therefore, further material development work is required to increase the CO solubility while maintaining low N2 solubility. Furthermore, current search and assessments focus on material properties such as solubility, rate of reaction and viscosity. In order to accurately assess the suitability of a solvent for scale-up, a process study must be undertaken to evaluate the overall energy consumption. This is particularly true for the developments that would require the separation system to operate at higher pressures.
Membrane separation functions by introducing a barrier that is able to selectively let CO pass while limiting or preventing the passage of other species. This creates two streams, one rich in CO and another dilute in CO. An example membrane unit process is shown in Figure 8, which differentiates the following streams: feed, retentate, permeate and sweep. The feed gas contains the gas mixture for separation and is at high pressure when the pressure difference is used as the driving force for the separation. It has been shown that an electrical field could substitute the pressure difference in certain gas separations (Winnick, 1990). The retentate is the stream containing the components that did not pass through the membrane. The permeate is the stream that permeates through the membrane. The sweep gas is often used to remove the permeated gas and maintain a lower concentration on the permeate side. The sweep gas is selected to be easily separable from the retentate and not be permeable through the membrane.
FIGURE 8. Membrane Separation of CO (red and black) and N2 (green) with the aid of a sweep gas (blue).
The parameters used to quantify the performance of a membrane are the flux through the membrane and the selectivity of the membrane towards a specific species. The flux is measured in units of volume or mass per unit time per surface area of membrane. The selectivity quantifies the relative difference in permeabilities (how easily a component passes through the membrane) of the different components. Selectivity is unitless while permeability is measured in units of mol m/m2/s/Pa. A membrane with a high permeability and selectivity is ideal for a separation.
Membrane separations can be classified based on the type of membrane, driving force and module design (i.e., the number and topology of membrane units) (Kluiters, 2004). The membrane material can be polymeric, inorganic or metallic. The actual membrane material may be supported by a carrier to provide mechanical strength while maintaining a thin selective membrane layer. Given the physical similarities between CO and N2, membranes based on physical separation such as nanofiltration or microporous membranes cannot be used. Instead, facilitated transport membranes are used.
In the majority of membrane gas separation technologies, the membrane is the solid phase membrane. However, it is also possible to construct the membrane of a liquid phase. Liquid membranes come in different types (Ola and Matsumoto, 2017), the type applicable for gas separation are supported liquid membranes (SLM). SLMs consist a liquid phase supported by impregnation of a microporous membrane or in some cases chemically bound to the solid support.
Membrane separation for CO is not currently at commercial scale and therefore no state of the art is present. However, at smaller scales, CO separation membranes are pressure-driven membranes and the most successful membrane systems transport the CO across using facilitated transported (FT) as well as molecular diffusion (Dutta and Patil, 1995). Facilitated transport refers to the concept of selectively and reversibly binding the CO to a molecule in the liquid phase and allowing this molecule to travel to the other side of the membrane, where the CO is then released due a lower CO partial pressure. In the case of electrochemical driven separation, (Terry et al., 1995), report the use of acidic chloride electrolyte to facilitate transport.
The liquid phase selected for use in FT SLM needs to have a low vapor pressure at process conditions, be selective to absorption of CO and regenerate under low CO partial pressure. Historically, research has focused on a prophyrinatoiron (II) complex and a solution of CuCl and VCl3 dissolved in DMSO and 2-pyrrolindodone. The challenges with these materials is their lack of long-term stability and their tendency to leak and evaporate. More recently (David et al., 2012) have explored the use of imidazolium-based ionic liquid with chloride anion [Rmim][Cl] as the immobilized liquid phase and Cu+ as the active phase to allow facilitated transport.
The reported advantages are the low vapour pressure of ionic liquids, high solubility of CuCl and thermal stability. However, the disadvantages are similar to their predecessor, i.e., extreme sensitivity to water and the tendency to convert from Cu+ to Cu2+. The work was also extended to study the effect of H2 permeation to produce a mixture of CO and H2 (Zarca et al., 2014). This was built upon by (Feng et al., 2019) to use a different ionic liquid and active species, namely 1-ethyl-3-methylimidazolium tetrafluoroborate ([emim][BF4]) as the ionic liquid and AgBF4 as the active species. This is the first reported use of AgBF4 for CO separation. The results showed improved permeation rates and selectivity between CO/N2 ranging from 1 to 9. Finally, (Tu et al., 2019), have also evaluated the use of protic chlorocuprate ionic liquids (PCILs) for absorption and membrane applications; the results indicate high absorption capacities and permeation, making them a potential candidate for SLM and absorption.
The most significant development reported in membranes for CO separation is by (Park et al., 2019a; Kim et al., 2021) who detail the development of solid membranes for CO separation. The membrane is a mixed matrix membrane (MMM), which are made of an discrete phase (an inorganic material) which are incorporated into a continuous phase (a polymeric matrix). The anticipated advantage being that MMMs will significantly separation performance with limited loss in membrane flexibility. The MMMs developed for CO separation were produced with a silver component (AgBF4) stabilized with MgO-Nanosheeets to allow facilitated transport. The reported selectivity of CO/N2 ranges from 2 to 16. The solid membranes that used silver for FT have the highest CO permeance and selectivity. As promising as these results are, the selectivity must be understood as theoretical selectivity calculated based on permeance data. When multi-component mixtures are tested for long durations, the selectivity obtained can be significantly lower due to multi-component diffusion effects that do not manifest themselves in single component permeation experiments. Therefore, it is important that further validation using multi-component gases is performed.
Separation by adsorption is based on one of three effects: steric, kinetic or equilibrium. Steric effects refer to separation based on physical size, where a molecule is able to enter the adsorbent due to its size and shape. This is generally applicable for separation with molecular sieves and zeolite. Kinetic separation functions on the principle of differences in diffusion rates of different molecules, where some molecules are able to move through rapidly, while others are slowed and kept inside the bed. Again, the similarities between CO and N2 prevent the use of steric or kinetic differences as the separation principle. Finally, equilibrium separation occurs due to affinity of the target molecule to the adsorbent (Yang, 1987). The specific mechanism of affinity depends on the target molecule for separation. In the case of CO separation, the first-used sorbents exploited differences in Van der Waals interactions. Later adsorbents relied on the ability of CO to form π-complexation bonds with transition metals from the d-block. CO can be reacted to form a π-complexation bond with Cu+ Ag+ Fe2+ Pd0 Zn2+ and Co2+. However only Cu+ has a sufficiently high rate constant to design an economically viable system (David et al., 2012).
An adsorption process requires multiple beds to operate continuously. The state of the bed goes from being saturated in CO to being lean in CO. The method of regeneration further differentiates the different types of adsorption processes. The regeneration can be done with a change in temperature, pressure or a combination of both. This is referred to as temperature swing or pressure swing adsorption. A typical pressure swing adsorption process involves a bed undergoing some the following steps: adsorption, de-pressurization, regeneration, re-pressurization. In order to improve the overall performance, additional steps such as a purge and rinse step maybe added. In terms of CO separation, the strong π-complexation bond requires vacuum to enable efficient separation. Therefore this is referred to as Vacuum Pressure Swing Adsorption (VPSA).
CO separation with adsorption was first demonstrated in the 1980s by Kawasaki Steel and Osaka Oxygen Industries in Japan for the production of CO rich gas from basic oxygen furnace gas, which typically contains 55–60 mol% CO, 12–18 mol% CO2, 0.1–0.2 mol% O2 and the remainder N2 (Dutta and Patil, 1995). This plant exploits the difference in Van der Waal interactions of the components of the gas. However, since CO2 and H2O interact more strongly with the sorbents than CO, a two stage process is used. The first stage uses activated carbon or silica gel and the second stage uses a Na-type mordenite. CO purity of 98% and CO recovery of 45% have been reported.
Higher CO purity and CO recovery is possible using a sorbent that is able to form π-complexation bonds with CO. In 1986 a pilot plant was constructed at Kakogawa Works of Kobe Steel and additional commercial plants were built in 1989 and 1990 (Kasuya and Tsuji, 1991). These plants use activated alumina impregnated with carbon for mechanical stability as a carrier and copper compounds (CuCl2, CuCl) as the active chemisorption species. The functional species that enables separation is the Cu+ ion. This is, however, not very stable and in the presence of H2O will breakdown to Cu2+which is not active for CO adsorption. This necessitates the requirement of a clean-up system prior to the CO VPSA. The original pilot plants have reported CO purities of up to 99.9% and recovery of 90%.
The VPSA bed undergoes a number of steps to achieve the separation, as shown in Figure 9. The steps are adsorption, purging, desorption and re-pressurization. In the adsorption step, the column is fed at a pressure of 300 kPa and the CO is selectively adsorbed by the sorbent and the CO lean gas exits as rest gas. This step is stopped prior to CO breakthrough (i.e., before CO is detected in the Rest Gas). At the end of the adsorption the void spaces in the column will be filled with feed gas composition and, if regenerated directly, the CO purity will be low. Therefore a purging step is used. CO-rich product gas is used to purge the column with the outlet gas of the purge step being used for re-pressurization of the column at lower pressure. Next the column is regenerated by decreasing the pressure to vacuum between 6 and 13 kPa. The produced CO is sent towards the product gas holder. The final step is to increase the pressure back up to adsorption pressure and this is done partly with the help of the purge step product and the feed gas.
FIGURE 9. Steps of VPSA for CO separation. Adapted from Kasuya and Tsuji (1991) with permission from Elsevier.
The bulk of research around CO separation with adsorption is focused on improving existing sorbent material or developing new sorbents. Table 2 provides an overview of the adsorption material research from 1973 to 2020. The core of the research still focuses on using Cu+ ions as the active species. Recently, more attention has been given to Metal Organic Frameworks (MOFs) because of their ability to be tuned to achieve different functionalities; an overview of MOFs for CO separation is available (Evans et al., 2018). Further to this, a wide ranging screening of sorbent material for CO/CO2 separation was done by (Wilson et al., 2020) which identified that high density silica gel and H-Y are the best adsorbents for bulk separation of CO2 due to their selectivity and capacity. This implies that for binary CO/CO2 mixtures, these materials are suitable for CO purification, but no conclusion can be drawn for CO-N2 separation.
Most literature on adsorbents for CO uses metrics such as capacity and selectivity to rank their performance. However, it has been shown that these metrics alone are poor indicators of sorbent performance because the energy consumption should be accounted for, as well as the fully cyclic (multicolumn) system performance in terms of adsorption-regeneration performance (Rajagopalan et al., 2016). Only a handful of authors (Gao et al., 2018; Tao et al., 2021; Oh et al., 2022) have attempted to quantify performance in a pressure swing adsorption model. We propose that a simple model such as that presented by (Maring and Webley, 2013), when applied to characterize the performance of a VPSA system, can provide a wealth of information. As part of this review, we have recreated this model for CO and N2 separation in MATLAB; the source code for the model is available online (James, 2022).
The simplified model assumes that the PSA process consists of only three steps: Blowdown, Repressurization & Feed. The blowdown step is assumed to start with the column fully saturated at feed composition, temperature and pressure. During the blowdown step, the column pressure is reduced to produce the heavy product (i.e., CO). If a pressure lower than atmospheric is specified, the work required is assumed to be provided by a vacuum pump operating with an isentropic efficiency of 75%. During the repressurization, the feed gas is fed until the column is at feed pressure. Then the column is fed with the feed until conditions match the start of the blowdown. During the repressurization step, if the feed pressure is above atmospheric pressure, a compressor is assumed to be used with an isentropic efficiency of 75%. In all steps, it is assumed a gas and solid are in equilibrium is. It is also assumed that the PSA operates adiabatically (which is close to industrial practice).
Multiple sorbents are available with varying degrees of available data. For this illustrative comparison, we have selected CuCl on activated carbon (CuCul-AC) (Gao et al., 2018) and 45 wt% Cu(I)-doped MIL-100(Fe) (Vo et al., 2019) due to the availability of consistent temperature-dependent data set.
The isotherm parameters are shown in Table 3 and the sorbent properties are shown in Table 4. The isotherm parameters have been regressed from the published experimental data. The isotherm model selected is the Langmuir competitive adsorption between CO and N2, as shown by Eq. 1, where
Furthermore, for the case of the 45Cu(I)@MIL-100(Fe), no N2 isotherm adsorption data was measured; therefore, it has been assumed that the sorbent is only selectively towards CO. In the simulation, the inlet feed pressure is 5 bar, and temperature is 30°C. The feed CO and N2 concentrations of 35% and 65%, respectively, have also been specified. The only variable that is manipulated is the blowdown pressure; this is varied between 1 bar and 0.01 bar. The results purities and corresponding recoveries are shown in Figure 10.
Figure 10 shows the effect of reducing blowdown pressure on CO purity (top left), CO recovery (top right), specific work (bottom left) and working capacity (bottom right). The CO recovery and CO purity increase for both materials as the blowdown pressure is reduced. A lower blowdown pressure means that the sorbent is better regenerated and more CO is recovered. Since the adsorption capacity of the nitrogen is significantly lower than the adsorption of CO, as a deeper regeneration occurs, no nitrogen is left to desorb; thereby a deeper regeneration results in a higher CO purity. When comparing the two sorbent materials, we can see that the CO purity is significantly higher due to the assumption of no N2 adsorption on the 45Cu(I)@MIL-100(Fe). The validity of this assumption remains to be evaluated experimentally; literature studies with other MIL-100(Fe) adsorbents have shown small but not negligible capacities for nitrogen (Ben-Mansour, et al., 2018; Wang and Yu, 2021). However, the total energy consumption of the two is comparable, with the working capacity (which will eventually influence the CAPEX) of the 45Cu(I)@MIL-100(Fe) being higher. The working capacity is higher even though the maximum equilibrium loading of CO is lower for the MOF than the CuCul-AC. This is likely due to the assumption of no N2 adsorption in the case of 45Cu(I)@MIL-100(Fe). Using simple PSA models such as the one proposed can provide the ability to study the influence of such assumptions. Something not easily done with simple metrics. Therefore, such comparisons are key when developing sorbents, a comparison lacking in current literature.
Significant progress has been made in the 27 years since the last review of CO-N2 separation. However, there are still developments required before CO-N2 separation can be widely deployed. Of the different technologies, it is not possible to identify which of these holds the largest promise or to state applicability area depending on required performance. Therefore, additional work in comparative techno-economic analysis (TEA) is required. In current research spanning absorption, adsorption and membranes, material developments are addressed thoroughly and show significant progress. However, there is a gap between material research and process development, where very few of the reviewed research evaluates the impact of the new material and their parameters on the overall separation process. Therefore, in general, all material developments should include a process design and evaluation to guide their development trajectory.
Cryogenic separation of CO-N2 is the area with the least new developments. Based on the technological aspects, it does not seem to be suitable for further development. However, this must be verified with a comparative TEA.
The use of absorption has made excellent progress in terms of solvent development with new solvents showing two orders of magnitude increase in CO solubility compared to solvents from 20 years ago. However, this is still an order of magnitude lower than the state of the art. Therefore, the material development focus should be on increasing CO solubility. In terms of the process design, specific attention should be paid to the influence of solvent viscosity and gas per-treatment requirements.
Solid state membrane development have also shown remarkable material development progress. However, many assessments are limited to single-component permeation experiments. In order to correctly quantify performance, multi-component, long-duration tests must be done. This is crucial since multi-component selectivity can be lower due to multi-component diffusion effects. The bulk of current research with membranes has thus far exploited the use of pressure differences as a driving force with one article demonstrating the use of acidic chloride electrolyte to facilitate transport. It is known that electrical fields can be used to replace pressure difference as driving force for some gas separations (Winnick, 1990). Recent successes of this approach in the area of CO2 separation (Ghezel et al., 2017) (Sharifian et al., 2020) indicate that this could also be a suitable method to advance CO separation.
A further unexplored area is the use of direct electrochemical separation. Facilitated transport relies on a carrier agent (Cu+/Cu2+) that is modulated between the two states. Given that CO exhibits an electrical dipole moment, it is possible to act directly on it without a carrier agent. An example of such a process would be a system which operates cyclically, where the first step separates CO by exploiting the dipole moment of the gas to selectivity adsorb it onto a charged surface and in a second step the electrical field is disabled and the gas is released. In theory such a system should be possible although no such work has been reported.
Adsorption is commercially available for CO-N2 separation and the material developments show some promising new developments. However, the tolerance to impurities and overall performance is limited. In future developments, a material which is more resilient to impurities and can be operated at more energy efficient operating points could be more advantageous even at lower selectivity and/or capacity. Materials previously disregarded due to low capacity but that exhibit favorable characteristics could form a new line of research. An example are pillared interlayered clays (PILC), which were explored for low temperature olefin-paraffin separation, another difficult separation that employs π-bonds. It was found that at these low temperatures, PILC did not have sufficiently high adsorption ratios compared to the reference CuCl/γ-Al2O3. However, a favorable feature of the PILC isotherms was having the steep portion above the Henry’s region of the isotherm, allowing a higher working capacity (Cheng and Yang, 1995). This would indicate that such material could be used without the need for vacuum.
Separation of CO is an important topic that, due to the energy transition, is gaining momentum. This is particularly relevant for Iron & Steel as well as other metal industries where carbon is part of the chemistry. The major methods of CO separation are cryogenics, absorption, adsorption and facilitated membrane separation. In general cryogenic processes are not suitable for CO-N2 separation and there is also little development work in this area.
In the area of absorption most of the focus lies on replacing the traditional benzene or toluene solvent with ionic-based solvents that are doped with copper-(1). Ionic liquids have traditionally had limited solubility in the low pressure region, however, recent advances have resulted in CO solubility in ionic liquids reaching the same order of magnitude as traditional benzene and toluene based solvents. The research is still academic and development into pilot and demonstration scale processes remain to be seen.
The ionic liquids used to replace solvents for absorption are also studied for membrane application in the form of Supported Liquid Membranes. SLMs are developing in parallel to IL but with no development trajectory beyond lab scale due to potential issues in holding the liquid membranes. A more promising direction is the use solid state membranes that have recently shown high permeance and selectivity. These mixed matrix membranes need to be further tested with multi-component gases to assess their feasibility for scaling-up.
In terms of adsorption, there is little development work in the area of process configuration and a significant amount of research focused on new materials. Material research currently focuses on separation processes at low temperature using vacuum regeneration and utilizing Cu+ as the functional species. The main drawback of such a process is the need for extensive clean up prior to the VPSA due to the instability of the Cu+ species and the high energy cost of creating a vacuum for regeneration. These issues present an opportunity for future work in materials that are stable and can separate CO without the requirement for vacuum. Furthermore, material research should be coupled with process design and the assessment of the material should rely on more than simply one parameter such as absolute capacity.
JJ and LL wrote the original draft. HD and JB reviewed and edited the manuscript. All authors contributed to the article and approved the submitted version.
This work was undertaken as part of the Steel2Chemicals project which is partly funded by TKI-Energie under the Toeslag voor Topconsortia voor Kennis en Innovatie (TKI’s) of the Ministry of Economic Affairs and Climate Policy, Netherlands.
We would like to thank Jayaram Ganesan for his contribution the PSA and VPSA Modelling work.
JJ, LL, HD, and JB were employed by the company TNO Sustainable Technologies for Industrial Processes.
All claims expressed in this article are solely those of the authors and do not necessarily represent those of their affiliated organizations, or those of the publisher, the editors and the reviewers. Any product that may be evaluated in this article, or claim that may be made by its manufacturer, is not guaranteed or endorsed by the publisher.
Ben-Mansour, R., Qasem, N. A., and Habib, M. A. (2018). Adsorption characterization and CO2 breakthrough of MWCNT/Mg-MOF-74 and MWCNT/MIL-100 (Fe) composites. Int. J. Energy Environ. Eng. 9 (2), 169–185. doi:10.1007/s40095-018-0260-1
Beyer, H. K., Jacobs, P. A., and Uytterhoeven, J. B. (1979). Chemisorption of carbon monoxide and hydrogen on AgNa mordenite. J. Chem. Soc. Faraday Trans. 1 Phys. Chem. Condens. Phases 75, 109. doi:10.1039/f19797500109
Bierhals, J. (2001). “Carbon monoxide,” in Ullmann's encyclopedia of industrial Chemistry (Hoboken, New Jersey: Wiley Online Library).
Bloch, E. D., Hudson, M. R., Mason, J. A., Chavan, S., Crocellà, V., Howe, J. D., et al. (2014). Reversible CO binding enables tunable CO/H2 and CO/N2 separations in metal-organic frameworks with exposed divalent metal cations. J. Am. Chem. Soc. 136, 10752–10761. doi:10.1021/ja505318p
Cheng, L. S., and Yang, R. T. (1995). Monolayer cuprous chloride dispersed on pillared clays for olefin-paraffin separations by ?-complexation. Adsorption 1, 61–75. doi:10.1007/bf00704146
Cho, K., Kim, J., Beum, H. T., Jung, T., and Han, S. S. (2018). Synthesis of CuCl/Boehmite adsorbents that exhibit high CO selectivity in CO/CO2 separation. J. Hazard. Mater. 344, 857–864. doi:10.1016/j.jhazmat.2017.11.037
Cho, K., Kim, J., Park, J.-H., Jung, T., Beum, H. T., Cho, D.-W., et al. (2019). High CO adsorption capacity, and CO selectivity to CO2, N2, H2, and CH4 of CuCl/bayerite adsorbent. Microporous Mesoporous Mater. 277, 142–148. doi:10.1016/j.micromeso.2018.10.010
COSTELLO, R.C. and ASSOC. INC (2020). COPure carbon monoxide purification technology [online]. Available: https://www.rccostello.com/copure.html [Accessed 13 May 2020].
Cui, G., Jiang, K., Liu, H., Zhou, Y., Zhang, Z., Zhang, R., et al. (2021). Highly efficient CO removal by active cuprous-based ternary deep eutectic solvents [HDEEA] [Cl] + CuCl + EG. Sep. Purif. Technol. 274, 118985. doi:10.1016/j.seppur.2021.118985
David, O. C., Zarca, G., Gorri, D., Urtiaga, A., and Ortiz, I. (2012). On the improved absorption of carbon monoxide in the ionic liquid 1-hexyl-3-methylimidazolium chlorocuprate. Sep. Purif. Technol. 97, 65–72. doi:10.1016/j.seppur.2012.02.015
Deng, S. G., and Lin, Y. S. (1995). Sol-gel preparation and properties of Alumina adsorbents for gas separation. AIChE J. 41, 559–570. doi:10.1002/aic.690410314
Dutta, N. N., and Patil, G. S. (1995). Developments in CO separation. Gas Sep. Purif. 9, 277–283. doi:10.1016/0950-4214(95)00011-y
Evans, A., Cummings, M., Decarolis, D., Gianolio, D., Shahid, S., Law, G., et al. (2020). Optimisation of Cu+ impregnation of MOF-74 to improve CO/N2 and CO/CO 2 separations. RSC Adv. 10, 5152–5162. doi:10.1039/c9ra10115b
Evans, A., Luebke, R., and Petit, C. (2018). The use of metal–organic frameworks for CO purification. J. Mater. Chem. A 6, 10570–10594. doi:10.1039/c8ta02059k
Fabian, R. (1993). “Process for obtaining high-purity hydrogen and high-purity carbon monoxide Japan patent application 39667,”. US4999177A (United States: Dairen Chemical Corp).
Feng, S., Wu, Y., Luo, J., and Wan, Y. (2019). AgBF4/[emim] [BF4] supported ionic liquid membrane for carbon monoxide/nitrogen separation. J. Energy Chem. 29, 31–39. doi:10.1016/j.jechem.2018.02.004
Flores-Granobles, M., and Saeys, M. (2022). Dynamic pressure-swing chemical looping process for the recovery of CO from blast furnace gas. Energy Convers. Manag. 258, 115515. doi:10.1016/j.enconman.2022.115515
Förster, H., and Witten, U. (1989). Studies on interaction of carbon monoxide with transition metal ION-exchanged zeolites A. Stud. Surf. Sci. Catal. 49, 1053. doi:10.1016/S0167-2991(08)61992-8
Gabrielli, P., Gazzani, M., and Mazzotti, M. (2020). The role of carbon capture and utilization, carbon capture and storage, and biomass to enable a net-zero-CO2 emissions chemical industry. Industrial Eng. Chem. Res. 59, 7033–7045. doi:10.1021/acs.iecr.9b06579
Gao, F., Wang, S., Wang, W., Duan, J., Dong, J., and Chen, G. (2018). Adsorption separation of CO from syngas with CuCl@AC adsorbent by a VPSA process. RSC Adv. 8, 39362–39370. doi:10.1039/c8ra08578a
Gao, F., Wang, Y., and Wang, S. (2016a). Selective adsorption of CO on CuCl/Y adsorbent prepared using CuCl2 as precursor: Equilibrium and thermodynamics. Chem. Eng. J. 290, 418–427. doi:10.1016/j.cej.2016.01.054
Gao, F., Wang, Y., Wang, X., and Wang, S. (2016b). Selective CO adsorbent CuCl/AC prepared using CuCl 2 as a precursor by a facile method. RSC Adv. 6, 34439–34446. doi:10.1039/c6ra03116a
Ghezel, H., Jolly, S., Patel, D., and Steen, W. (2017). Electrochemical membrane technology for carbon dioxide capture from flue gas. Energy Procedia 108, 2–9. doi:10.1016/j.egypro.2016.12.183
Go, Y. T., Yoon, Y. S., Lee, I. B., and Lee, S. Y. (2019). Mathematical modeling and simulation of carbon monoxide absorption column for blast furnace gas and Linz–Donawitz gas separation by CoSoRB process. J. Chem. Eng. Jpn. 52, 439–446. doi:10.1252/jcej.18we259
Hogendoorn, J. A., Van Swaaij, W. P. M., and Versteeg, G. F. (1995). The absorption of carbon monoxide in COSORB solutions: Absorption rate and capacity. Chem. Eng. J. Biochem. Eng. J. 59, 243–252. doi:10.1016/0923-0467(94)02959-8
Huang, H. Y., Padin, J., and Yang, R. T. (1999). Comparison of πcomplexations of ethylene and carbon monoxide with Cu+ and Ag+. Industrial Eng. Chem. Res. 38, 2720–2725.
Huang, Y. (1973). Selective adsorption of carbon monoxide and complex formation of cuprous-ammines in Cu(I)Y zeolites. J. Catal. 30, 187–194. doi:10.1016/0021-9517(73)90065-1
Iyuke, S. E., Mohamad, A. B., Daud, W. R. W., Kadhum, A. A. H., Fisal, Z., and Shariff, A. M. (2000). Removal of CO from process gas with Sn-activated carbon in pressure swing adsorption. J. Chem. Technol. Biotechnol. 75, 803–811. doi:10.1002/1097-4660(200009)75:9<803::AID-JCTB283>3.0.CO;2-G
James, J. G. J. (2022). Sorbent screening model [online]. MATLAB central file exchange. Available: https://www.mathworks.com/matlabcentral/fileexchange/107604-sorbent-screening-model [Accessed March 2022].
Kasuya, F., and Tsuji, T. (1991). High purity CO gas separation by pressure swing adsorption. Gas Sep. Purif. 5, 242–246. doi:10.1016/0950-4214(91)80031-y
Keller, A., and Schendel, R. (1988). The use of COSORB II to recover HIgh purity carbon monoxide from a feed gas. Denver, Colorado: AICHE Summer Meeting.
Kim, H., Sohail, M., Yim, K., Park, Y. C., Chun, D. H., Kim, H. J., et al. (2019). Effective CO 2 and CO separation using [M 2 (DOBDC)] (M = Mg, Co, Ni) with unsaturated metal sites and excavation of their adsorption sites. ACS Appl. Mater. Interfaces 11, 7018–7021. doi:10.1021/acsami.8b20450
Kim, N. U., Kim, J.-H., Park, B. R., Kim, K. C., and Kim, J. H. (2021). Solid-state facilitated transport membrane for CO/N2 separation based on PHMEP-co-PAA comb-like copolymer: Experimental and molecular simulation study. J. Membr. Sci. 620, 118939. doi:10.1016/j.memsci.2020.118939
Koytsoumpa, E.-I., Atsonios, K., Panopoulos, K., Karellas, S., Kakaras, E., and Karl, J. (2015). Modelling and assessment of acid gas removal processes in coal-derived SNG production. Appl. Therm. Eng. 74, 128–135. doi:10.1016/j.applthermaleng.2014.02.026
Lei, Z., Dai, C., Yang, Q., Zhu, J., and Chen, B. (2014). UNIFAC model for ionic liquid-CO (H2) systems: An experimental and modeling study on gas solubility. AIChE J. 60, 4222–4231. doi:10.1002/aic.14606
Li, M. L., Zhuo, Y. G., Wei, X. P., and Wu, X. R. (2018). Column design for cryogenic CO-H2 separation process. Huaxue Gongcheng/Chemical Eng. (China) 46, 18–22. doi:10.3969/j.issn.1005-9954.2018.02.005
Li, S., Yang, H., and Zhang, D. (2013). Enrichment of CO from syngas with Cu(I)Y adsorbent by five-bed VPSA. Front. Chem. Sci. Eng. 7, 472–481. doi:10.1007/s11705-013-1351-4
LINDE (2020). RECTISOL® wash [online]. Available: https://www.linde-engineering.com/en/process-plants/hydrogen_and_synthesis_gas_plants/gas_processing/rectisol_wash/index.html [Accessed 13 May 2020].
Linstrom, P. (1997). NIST Chemistry WebBook. Maryland, United States: National Institute of Standards and Technology. NIST Standard Reference Database 69.
Liu, W., Pan, X. M., Wang, J., Zhao, B. Y., and Xie, Y. C. (2001a). Study on adsorption of CO on CuCl modified Y zeolites. Acta Chim. Sin. 59, 1021–1025.
Liu, X. Q., Ma, Z. F., Mei, H., and Yao, H. Q. (2001b). Rare Earth complex adsorbent for carbon monoxide-nitrogen separation and its pressure swing adsorption characteristics. Gao Xiao Hua Xue Gong Cheng Xue Bao/Journal Chem. Eng. Chin. Univ. 15, 323–327.
Liu, Y. M., Tian, Z., Qu, F., Zhou, Y., Liu, Y., and Tao, D. J. (2019). Tuning ion-pair interaction in cuprous-based protic ionic liquids for significantly improved CO capture. ACS Sustain. Chem. Eng. 7. doi:10.1021/acssuschemeng.9b02540
Maring, B. J., and Webley, P. A. (2013). A new simplified pressure/vacuum swing adsorption model for rapid adsorbent screening for CO2 capture applications. Int. J. Greenh. Gas Control 15, 16–31. doi:10.1016/j.ijggc.2013.01.009
Oh, H., Lee, S., Beum, H. T., Kim, J., Kim, J., Lee, S.-Y., et al. (2022). CO recovery from blast furnace gas by vacuum pressure swing adsorption process: Experimental and simulation approach. J. Clean. Prod. 346, 131062. doi:10.1016/j.jclepro.2022.131062
Ohlin, C. A., Dyson, P. J., and Laurenczy, G. (2004). Carbon monoxide solubility in ionic liquids: Determination, prediction and relevance to hydroformylation. Chem. Commun. 2004, 1070–1071. doi:10.1039/b401537a
Ola, P., and Matsumoto, M. (2017). Supported ionic liquid membranes for metal separation. IntechOpen Journals 2017. doi:10.5772/65754
Park, C. H., Lee, J. H., Kim, N. U., Kong, C.-I., Kim, J.-H., and Kim, J. H. (2019a). Solid-state facilitated transport of carbon monoxide through mixed matrix membranes. J. Membr. Sci. 592, 117373. doi:10.1016/j.memsci.2019.117373
Park, Y., Moon, D. K., Park, D., Mofarahi, M., and Lee, C. H. (2019b). Adsorption equilibria and kinetics of CO2, CO, and N2 on carbon molecular sieve. Sep. Purif. Technol. 212, 952–964. doi:10.1016/j.seppur.2018.11.069
Peng, J., Xian, S., Xiao, J., Huang, Y., Xia, Q., Wang, H., et al. (2015). A supported Cu(I)@MIL-100(Fe) adsorbent with high CO adsorption capacity and CO/N2 selectivity. Chem. Eng. J. 270, 282–289. doi:10.1016/j.cej.2015.01.126
Raeissi, S., Florusse, L. J., and Peters, C. J. (2013). Purification of flue gas by ionic liquids: Carbon monoxide capture in [bmim] [Tf 2 N]. AIChE J. 59, 3886–3891. doi:10.1002/aic.14125
Rajagopalan, A. K., Avila, A. M., and Rajendran, A. (2016). Do adsorbent screening metrics predict process performance? A process optimisation based study for post-combustion capture of CO2. Int. J. Greenh. Gas Control 46, 76–85. doi:10.1016/j.ijggc.2015.12.033
Reed, D. A., Xiao, D. J., Gonzalez, M. I., Darago, L. E., Herm, Z. R., Grandjean, F., et al. (2016). Reversible CO scavenging via adsorbate-dependent spin state transitions in an iron(II)–Triazolate metal–organic framework. J. Am. Chem. Soc. 138, 5594–5602. doi:10.1021/jacs.6b00248
Repper, S. E., Haynes, A., Ditzel, E. J., and Sunley, G. J. (2017). Infrared spectroscopic study of absorption and separation of CO using copper(<span style="font-variant:small-caps;">i</span>)-containing ionic liquids. Dalton Trans. 46, 2821–2828. doi:10.1039/C6DT04816A
Sethia, G., Dangi, G. P., Jetwani, A. L., Somani, R. S., Bajaj, H. C., and Jasra, R. V. (2010). Equilibrium and dynamic adsorption of carbon monoxide and nitrogen on ZSM-5 with different SiO2/Al2O3 ratio. Sep. Sci. Technol. 45, 413–420. doi:10.1080/01496390903417990
Sharifian, R., Vermaas, D., Digdaya, I., Xiang, C., and Wagterveld, R. (2020). Electrochemical carbon dioxide capture to close the carbon cycle. Energy Environ. Sci. 14, 781–814. doi:10.1039/d0ee03382k
Sun, S., Wu, Y. Y., Luo, S. Z., Chu, W., and Ni, H. Z. (2011). Absorbent of CuCl/NaY prepared by direct reduction and the application for adsorption of CO and separation for CO/H2 mixture gas. Gaodeng Xuexiao Huaxue Xuebao/Chemical J. Chin. Univ. 32, 1794–1798.
Tamon, H., Kitamura, K., and Okazaki, M. (1996). Adsorption of carbon monoxide on activated carbon impregnated with metal halide. AIChE J. 42, 422–430. doi:10.1002/aic.690420212
Tao, D. J., Chen, F. F., Tian, Z. Q., Huang, K., Mahurin, S. M., Jiang, D. E., et al. (2017). Highly efficient carbon monoxide capture by carbanion-functionalized ionic liquids through C-site interactions. Angew. Chem. Int. Ed. Engl. 56, 6947–6951. doi:10.1002/ange.201701919
Tao, L. R., You, Y. Y., and Liu, X. J. (2021). Numerical studies of CO separation and enrichment from blast furnace gas by using a CuCl/Y fixed bed. Ironmak. Steelmak. 48, 1187–1199. doi:10.1080/03019233.2021.1948314
Terry, P. A., Walis, H. J., Noble, R. D., and Koval, C. A. (1995). Electrochemically modulated complexation process for gas removal and concentration. AIChE J. 41, 2556–2564. doi:10.1002/aic.690411206
Trott, T. (2013). “Method and plant for generating a H2 product stream and a CO product stream,”. Germany patent application.
Tu, Z.-H., Zhang, Y.-Y., Wu, Y.-T., and Hu, X.-B. (2019). Self-enhancement of CO reversible absorption accompanied by phase transition in protic chlorocuprate ionic liquids for effective CO separation from N2. Chem. Commun. 55, 3390–3393. doi:10.1039/C9CC00089E
Uhlig, H. H., and Keyes, F. G. (1933). The dependence of the dielectric constants of gases on temperature and density. J. Chem. Phys. AIP Publishing 1, 155. doi:10.1063/1.3247827
Van Dijk, H. A. J., Cobden, P. D., Lukashuk, L., Van, L., Lundqvist, M., Manzolini, G., et al. (2018). Stepwise project: Sorption-enhanced water-gas shift technology to reduce carbon footprint in the iron and steel industry. Johns. Matthey Technol. Rev. 62, 395–402. doi:10.1595/205651318x15268923666410
Vo, T. K., Bae, Y.-S., Chang, B.-J., Moon, S.-Y., Kim, J.-H., and Kim, J. (2019). Highly CO selective Cu(I)-doped MIL-100(Fe) adsorbent with high CO/CO2 selectivity due to π complexation: Effects of Cu(I) loading and activation temperature. Microporous Mesoporous Mater. 274, 17–24. doi:10.1016/j.micromeso.2018.07.024
Wang, M., and Yu, F. (2021). High-throughput screening of metal-organic frameworks for water harvesting from air. Colloids Surfaces A Physicochem. Eng. Aspects 624, 126746. doi:10.1016/j.colsurfa.2021.126746
Wilson, S. M. W., Kennedy, D. A., and Tezel, F. H. (2020). Adsorbent screening for CO2/CO separation for applications in syngas production. Sep. Purif. Technol. 236, 116268. doi:10.1016/j.seppur.2019.116268
Winnick, J. (1990). Electrochemical membrane gas separation. Chemical Engineering Progress 86, 41–46.
Wu, Y., Chen, Z., Li, B., Xing, J., Liu, H., Tong, Y., et al. (2019). Highly selective adsorption of CO over N2 on CuCl-loaded SAPO-34 adsorbent. J. Energy Chem. 36, 122–128. doi:10.1016/j.jechem.2019.07.013
Xie, Y., Yang, G., Qiu, J., Tong, X., Liu, J., Luo, B., et al. (1993). Highly efficient adsorbent for separation of carbon monoxide. Stud. Surf. Sci. Catal. 80, 737. doi:10.1016/S0167-2991(08)63583-1
Xie, Y., Zhang, J., Qiu, J., Tong, X., Fu, J., Yang, G., et al. (1997). Zeolites modified by CuCl for separating CO from gas mixtures containing CO2. Adsorption 3, 27–32. doi:10.1007/bf01133004
Xue, C., Hao, W., Cheng, W., Ma, J., and Li, R. (2019). Effects of pore size distribution of activated carbon (AC) on CuCl dispersion and CO adsorption for CuCl/AC adsorbent. Chem. Eng. J. 375, 122049. doi:10.1016/j.cej.2019.122049
Yang, R. T. (1987). “Chapter 2 - adsorbents and adsorption isotherms,” in Gas separation by adsorption processes. Editor R. T. YANG (Oxford, United Kingdom: Butterworth-Heinemann).
Yaws, C. L. (2015). The Yaws handbook of physical properties for hydrocarbons and chemicals. Oxford, [England]: Gulf Professional Publishing is an imprint of Elsevier.
Yoon, T.-U., Kim, M. J., Kim, A.-R., Kang, J. H., Ji, D., and Bae, Y.-S. (2020). Cu-impregnated metal-organic frameworks for separation and recovery of CO from blast furnace gas. J. Industrial Eng. Chem. 87, 102–109. doi:10.1016/j.jiec.2020.03.019
Zarca, G., Ortiz, I., and Urtiaga, A. (2014). Facilitated-transport supported ionic liquid membranes for the simultaneous recovery of hydrogen and carbon monoxide from nitrogen-enriched gas mixtures. Chem. Eng. Res. Des. 92, 764–768. doi:10.1016/j.cherd.2013.12.021
Zarca, G., Ortiz, I., Urtiaga, A., and Llovell, F. (2017b). Accurate thermodynamic modeling of ionic liquids/metal salt mixtures: Application to carbon monoxide reactive absorption. AIChE J. 63, 3532–3543. doi:10.1002/aic.15790
Zarca, G., Ortiz, I., and Urtiaga, A. (2017a). Novel solvents based on thiocyanate ionic liquids doped with copper(I) with enhanced equilibrium selectivity for carbon monoxide separation from light gases. Sep. Purif. Technol. 196, 47. doi:10.1016/j.seppur.2017.06.069
Zhou, Y., Shen, Y., Fu, Q., and Zhang, D. (2017). CO enrichment from low-concentration syngas by a layered-bed VPSA process. Industrial Eng. Chem. Res. 56, 6741–6754. doi:10.1021/acs.iecr.7b00229
Keywords: CO separation, adsorption, absorption, CCU, steel, membranes
Citation: James J, Lücking LE, van Dijk HAJ and Boon J (2023) Review of technologies for carbon monoxide recovery from nitrogen- containing industrial streams. Front. Chem. Eng. 5:1066091. doi: 10.3389/fceng.2023.1066091
Received: 10 October 2022; Accepted: 17 January 2023;
Published: 03 March 2023.
Edited by:
Rahul Anantharaman, SINTEF Energy Research, NorwayReviewed by:
Rui P. P. L. Ribeiro, New University of Lisbon, PortugalCopyright © 2023 James, Lücking, van Dijk and Boon. This is an open-access article distributed under the terms of the Creative Commons Attribution License (CC BY). The use, distribution or reproduction in other forums is permitted, provided the original author(s) and the copyright owner(s) are credited and that the original publication in this journal is cited, in accordance with accepted academic practice. No use, distribution or reproduction is permitted which does not comply with these terms.
*Correspondence: Jurriaan Boon, anVycmlhYW4uYm9vbkB0bm8ubmw=
Disclaimer: All claims expressed in this article are solely those of the authors and do not necessarily represent those of their affiliated organizations, or those of the publisher, the editors and the reviewers. Any product that may be evaluated in this article or claim that may be made by its manufacturer is not guaranteed or endorsed by the publisher.
Research integrity at Frontiers
Learn more about the work of our research integrity team to safeguard the quality of each article we publish.