- 1Process Engineering Advanced Research Lab (PEARL), Department of Chemical Engineering, Polytechnique Montreal, Montreal, QC, Canada
- 2Heirloom, Brisbane, CA, United States
- 3Technology Development Cell (Tech-Cell) Department, Mohammed VI Polytechnic University, Ben Guerir, Morocco
Microwave (MW) heating is rapid, selective, and volumetric, and it is a compelling non-conventional heating approach for driving chemical reactions. The effect of MW irradiation on the kinetics of thermal/catalytic reactions is still under debate. A group of researchers reported that the effect of MW heating on reaction kinetics is highlighted through the non-thermal effects of MWs on kinetic parameters and reaction mechanisms in addition to the thermal effect. However, another group attributed the observations to the thermal effect only. In the present work, we summarized and critically synthesized available information in the literature on the subject. It can be concluded that MW heating has solely the thermal effect on gas-solid reactions, and the variations of kinetic parameters are related to the direct and indirect impacts of that. Temperature measurement limitations, physical structure variation, and non-uniform temperature distribution are the primary sources of the discrepancy in previous studies. In ionic liquid-solid reactions, the presence of electromagnetic fields can affect the movement of ions/polar molecules which can be considered a non-thermal effect of MWs. However, the effect of MW absorption by solid/catalyst, and the formation of hot spots must be taken into account to avoid potential discrepancy. Therefore, further theoretical/experimental studies are required to clarify the effect of MWs on liquid-solid reactions. In addition, developing reliable temperature measurement methods and isothermal reaction domain are required for an accurate kinetic study during MW irradiation.
Introduction
Compared to conventional heating, microwave (MW) heating is an effective heat supply approach for chemical and material processes. Electromagnetic (EM) properties of materials, including permittivity, permeability, penetration depth, and electrical conductivity play critical roles in absorbing MWs and their conversion to thermal energy (Gupta and Leong, 2007; Amini et al., 2021). In the conventional heating of a multi-phase system, an external source supplies heat, and the whole system, including solid particles, gas/liquid, and reactor walls, are at similar temperatures. Therefore, non-desired secondary reactions likely occur in the fluid phase, reducing the desired chemicalsā production rate and process efficiency (Hamzehlouia et al., 2018). In the MW heating approach, however, heat is generated in the body of certain phases (commonly solid particles) owing to the high penetration depth of MWs and their interaction with dielectric material loaded in the reactors. MWs cannot directly heat the gas phase due to their negligible interactions with this phase (Hamzehlouia et al., 2018; Amini et al., 2019). Therefore, a considerable temperature gradient between the solid particles (either inert or catalyst) and fluid suppresses the fluid-phase side reactions, favors the production of desired chemicals, and likely leads to higher selectivity and conversion (Stefanidis et al., 2014; Hamzehlouia et al., 2018; Amini et al., 2019; Robinson et al., 2020). The rapid and selective features of MW heating also decrease the treatment time and energy loss during the process (Gupta and Leong, 2007). The effects of MW irradiation on various multiphase (gas/liquid-solid phases) reaction systems are presented in Table 1.
Despite the applications of MW heating in multiphase systems, its effect on the kinetics of these reactions is still under debate. The main discrepancy is the presence of non-thermal effects, i.e., the interaction of MWs with materials at atomic/subatomic level and electron donation enhancement, in addition to the thermal effects, i.e., selective heating and formation of hotspots. In the present communication, we reviewed the impacts of MW heating on the reaction kinetics of multiphase reactions reported in the literature. We critically compared the experimental procedures in various references to propose the potential sources of discrepancy in the kinetic results.
Kinetics of gas/liquid-solid reactions
According to literature, MW heating has mainly thermal effects on reaction kinetics. For instance, hot spots generated during the MW treatment of solid beds enhance the reaction rate as their temperature is significantly higher than the average bed (or bulk) temperature (Amini et al., 2019; Amini et al., 2021). The hot spots can form microcracks inside the solid materials and enhance internal mass transfer. For instance, MWs selectively heat some components of iron oxide minerals, generating a temperature gradient between different components within an ore particle. Accordingly, micro-cracks are generated throughout the ore, enhancing gas diffusion into the ore, and improving the apparent kinetics of the reduction reaction (Amini et al., 2019).
In some discrepant cases, the non-thermal effect of MWs is also reported as a driving force in accelerating reactions (Hu et al., 2020). For instance, it was reported that a decrease in the activation energy (
where
In the case of
Potential sources of discrepancy
Variations of reaction kinetic parameters in multiphase reactions under MW heating compared to conventional heating have potential reasons, such as reactor diameter/sample amount in a kinetic study (Benzennou et al., 2020a), heating approach (direct or hybrid) (Ren et al., 2022), temperature measurement (Gangurde et al., 2017; Ren et al., 2022), physical structure variation due to materials exposure to MWs (Amini et al., 2019), and interaction of MWs with polar molecules and free radicals (Wan et al., 2022). These sources are discussed below.
Effects of reactor diameter/sample amount and heating approach
The uniform temperature distribution in the reaction domain is essential to increase the accuracy of estimated kinetic parameters. Temperature non-uniformity in the bed is observed on both the macro-scale and micro-scale. The macro-scale temperature gradient of the bed is changed by variation of the sampleās location in the cavity, the ratio of the waveguide to cavity impedances, and materials properties (affecting penetration depth). The main reason for the micro-scale temperature non-uniformity/hot spots is the difference in dielectric properties of materials in the bed (Ramirez et al., 2017; Amini et al., 2021).
Smaller reactor sizes and a few grams of solid mass are preferred to have a more uniform temperature distribution (see Figure 1), while effects of external and internal mass transfer limitations are eliminated/minimized either by increasing gas/liquid velocity or decreasing particle size, respectively (Benzennou et al., 2020a). To provide a uniform temperature distribution, we recommend applying a reactor diameter smaller than 10 mm (around 1/12 of MW wavelength at a frequency of 2.45 GHz), in fixed bed reactors adopted for intrinsic kinetic studies. In addition, employing fluidized bed reactors is another solution for an accurate kinetic study due to minimizing temperature non-uniformity (Farag and Chaouki, 2015; Samih and Chaouki, 2015). Impedance matching between the waveguide and cavity eliminates microwave reflection and minimizes the bedās macro-scale temperature gradient.
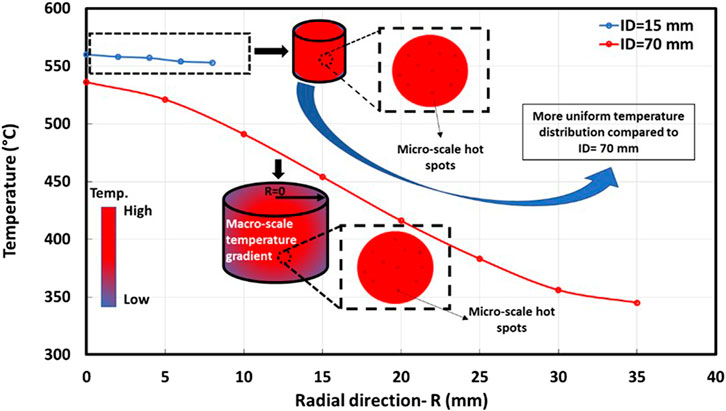
FIGURE 1. Effect of the internal reactor diameter (15 and 70 mm) on temperature distribution in a mixture of paper cups and graphite (adapted from ref. (Benzennou et al., 2020a)).
Heating of materials with weak MW interactions, e.g., plastics and biomass, in MW heating systems is challenging (Ren et al., 2022). Therefore, the hybrid heating approach is typically applied. However, due to variations in dielectric properties, it forms hot spots at MW receptors in the bed. For instance, pyrolysis of 40 g of waste printed circuit board in a MW-thermogravimetric analyzer resulted in both macro- and micro-scale hot spots during MW-assisted hybrid heating (Sun et al., 2012). In addition, MW-assisted pyrolysis of bamboo sawdust in a fixed bed reactor with a diameter of 45 mm (around 1/3 of the MW wavelength at 2.45 GHz) resulted in the formation of macro-scale hot spots (Dong and Xiong, 2014).
Effect of temperature measurement
Most MW reactors work based on temperature control mode, where the sample is heated to and kept at the desired temperature by coupling the feedback from an appropriate temperature measurement technique to the impedance tuner in the MW waveguide (Kappe, 2013; Gangurde et al., 2017). However, accurate temperature measurement of the gas/liquid and solid phases under MW heating is one of the critical issues in kinetic studies (Kappe, 2013; Gangurde et al., 2017). If the temperature is underestimated, the kinetic results show a fake enhancement.
Currently, no technique can accurately measure the gas/liquid and solid local temperatures during MW heating (Nguyen et al., 2020). Various techniques, including grounded and shielded metallic thermocouples (Gangurde et al., 2017), fiber optic probes (Kappe, 2013), IR (Gangurde et al., 2017), polymeric (Gangurde et al., 2017), molecular (Gangurde et al., 2017), and air thermometers (Farag and Chaouki, 2015), as well as radiometry methods (Nguyen et al., 2020), are employed in MW heated reactions. For kinetic studies, we need at least one contact sensor, e.g., thermocouple and fiber optic probe, or some other MW transparent sensors, to track the temperature changes during MW treatment of multiphase systems (Gangurde et al., 2017). Critical remarks regarding different temperature measurement techniques for MW heating systems are summarized in Table 3.
Effect of MWs interactions with polar molecules and free radicals
The activation energy is a characteristic of a chemical reaction implying the minimum required energy to initiate the reaction between reactants. Thus, a deep insight into the interactions (e.g., vibrations, disassociations, etc.) at an atomic scale under MW irradiation is essential to investigate their dependency on MWs. In liquid-solid reactions under MW irradiation, literature reported improvement in the kinetic. However, this improvement can be either due to hot spots formation in presence of solid/catalyst or dipolar/ionic molecules movement. For instance, Patil et al. (Patil et al., 2011) reported that the reaction rate constant for MW-assisted transesterification of oil on Barium oxide (BaO) catalyst is two order of magnitude higher than that for the conventional reaction. Although they provided no discussion/justification, it seems that they ignored the potential interaction between BaO catalyst and MWs that leads to a higher temperature at the catalyst surface compared to the bulk temperature (i.e., hot spot formation). BaO is a non-polar dielectric material with potential defects, including vacancies and interstitials, which couple with MWs to convert its energy into heat (Khujaev et al., 2013). Khujaev et al. (Ekinci et al., 2022) reported that the complete dissolution of BaO in hydrochloride acid under MW irradiation at 385 W takes less than 2.5 min, whereas it requires more than 20 min in conventional heating methods, indicating a significant interaction between MWs and BaO. Accordingly, a higher reaction rate during MW transesterification is attributed to the higher local temperature at the catalyst surface compared to the measured temperature, i.e., the bulk temperature, whereas the catalyst temperature is the same as the bulk temperature during conventional heating (Ekinci et al., 2022).
In liquid-solid MW heating-assisted reaction systems, MWs interactions can potentially affect ions and polar molecules. These interactions might result in a variation of kinetic parameters compared to conventional heating. For instance, the activation energy of Sodium tetrahydridoborate (NaBH4) hydrolysis under MW heating (46.8 kJ/mol) is lower than that obtained under the conventional heating approach (66.9 kJ/mol) (Yang et al., 2020). The authors attributed this to the interaction between MW electric field and OHā ions that accelerate hydrolysis, which was confirmed by a high-level pre-exponential factor (2.08Ć103 L/mol.min) under MW irradiation. In the study by Yang et al. (Benzennou et al., 2020b), accelerating ions under MW heating was also reported. However, the MW absorption capability of the solid/catalyst was ignored in these studies. If the solid absorbs MWs, the improved kinetics in a liquid-solid system under MW irradiation is likely attributed to the formation of hot spots in the solid component, which provides a higher local temperature compared to the bulk. Moreover, the formation of intermediate products with MW interaction, which is locally heated, affected reaction kinetics by their rotation (DomĆnguez et al., 2007).
Unlike the gas phase, which is relatively transparent to MWs, liquid materials containing polar molecules or ions interact with MWs. Accordingly, a liquid ionās dipolar/rotational movement on a solidās surface can change the reaction pathway/mechanism (Yang et al., 2020). However, further theoretical/experimental investigations are needed to study the interaction of ions and polar intermediate with MWs in liquid-solid systems.
Future study
The development of new temperature measurement techniques, preferably non-intrusive ones, e.g., wireless thermometers, for local temperature measurement in MW systems is essential. In addition, the morphology variation of solid materials should be monitored under MW heating processes. Applying computational approaches like density functional theory (DFT), to investigate the effect of EM field on polar molecules in solid-liquid systems and consequently its impact on reaction kinetics/mechanism is an important concept that needs to be covered in future studies.
Conclusion
The effect of MW heating on the kinetic parameters of gas/liquid-solid reactions was reported in the literature. Underestimation and even sometimes overestimation of the reaction temperature in the reaction domain due to hot spots formation at micro and macro scales, and difficulty in measurement of these temperatures are the main sources of discrepancy in MW heating kinetic studies. Therefore, to the best of the authorsā knowledge, there is no evidence in the literature confirming the presence of the non-thermal effect of MWs on the kinetics of gas-solid reactions, by now. Fixed bed reactors with a smaller diameter, e.g., 10 mm or operation under fluidized bed mode are suggested for kinetic studies to avoid noticeable temperature gradients within the reactor. However, changing the morphology of solid materials under MW heating can affect apparent kinetic parameters when the internal mass transfer controls the reaction rate. In liquid-solid systems with ions and polar molecules, electromagnetic fields likely accelerate the moleculeās movement, which might affect the reaction rate. The interaction of MWs with solid/catalyst should also be considered for potential hot spot formation to avoid an inaccurate reaction kinetics evaluation.
Author contributions
KA: Reviewed the literature, write the manuscript, revised the manuscript, discussed and concluded the findings AA: Reviewed the literature, write the manuscript, revised the manuscript, discussed and concluded the findings ML: Reviewed the literature, reviewed the manuscript, revised the manuscript, discussed and concluded the findings. JS: Reviewed the manuscript, revised the manuscript, discussed and concluded the findings. JC: Reviewed the manuscript, discussed and concluded the findings.
Conflict of interest
Author JS was employed by the company Heirloom.
The remaining authors declare that the research was conducted in the absence of any commercial or financial relationships that could be construed as a potential conflict of interest.
Publisherās note
All claims expressed in this article are solely those of the authors and do not necessarily represent those of their affiliated organizations, or those of the publisher, the editors and the reviewers. Any product that may be evaluated in this article, or claim that may be made by its manufacturer, is not guaranteed or endorsed by the publisher.
References
Adnadjevic, B. K., and Jovanovic, J. D. (2012). Kinetics of isothermal ethanol adsorption onto a carbon molecular sieve under conventional and microwave heating. Chem. Eng. Technol. 35, 761ā768. doi:10.1002/ceat.201100153
Amini, A., Latifi, M., and Chaouki, J. (2021). Electrification of materials processing via microwave irradiation : A review of mechanism and applications. Appl. Therm. Eng. 193, 117003. doi:10.1016/j.applthermaleng.2021.117003
Amini, A., Ohno, K., Maeda, T., and Kunitomo, K. (2019). A kinetic comparison between microwave heating and conventional heating of FeS-CaO mixture during hydrogen-reduction. Chem. Eng. J. 374, 648ā657. doi:10.1016/j.cej.2019.05.226
Bai, X., Muley, P. D., Musho, T., Abdelsayed, V., Robinson, B., Caiola, A., et al. (2022). A combined experimental and modeling study of Microwave-assisted methane dehydroaromatization process. Chem. Eng. J. 433, 134445. doi:10.1016/j.cej.2021.134445
Bai, X., Robinson, B., Killmer, C., Wang, Y., Li, L., and Hu, J. (2019). Microwave catalytic reactor for upgrading stranded shale gas to aromatics. Fuel 243, 485ā492. doi:10.1016/j.fuel.2019.01.147
Benzennou, S., Laviolette, J. P., and Chaouki, J. (2020). Kinetic study of microwave pyrolysis of paper cups and comparison with calcium oxide catalyzed reaction. AIChE J. 65, 16471. doi:10.1002/aic.16471
Benzennou, S., Laviolette, J. P., and Chaouki, J. (2020). Microwave effect on kinetics of paper cups pyrolysis. Can. J. Chem. Eng. 98, 1757ā1766. doi:10.1002/cjce.23752
Bi, X. j., Hong, P. j., Xie, X. g., and Dai, S. s. (1999). Microwave effect on partial oxidation of methane to syngas. React. Kinet. Catal. Lett. 66, 381ā386. doi:10.1007/bf02475816
Chen, J., Zhu, J., Xu, W., Chen, Y., and Zhou, J. (2022). Highly efficient H2 and S production from H2 S decomposition via microwave catalysis over a family of TiO2 modified MoxC microwave catalysts. Fuel Process. Technol. 226, 107069. doi:10.1016/j.fuproc.2021.107069
DomĆnguez, A., Fidalgo, B., FernĆ”ndez, Y., Pis, J. J., and MenĆ©ndez, J. A. (2007). Microwave-assisted catalytic decomposition of methane over activated carbon for CO2CO2-free hydrogen production. Int. J. Hydrogen Energy 32, 4792ā4799. doi:10.1016/j.ijhydene.2007.07.041
Dong, Q., and Xiong, Y. (2014). Kinetics study on conventional and microwave pyrolysis of moso bamboo. Bioresour. Technol. 171, 127ā131. doi:10.1016/j.biortech.2014.08.063
Durka, T., Stefanidis, G. D., Van Gerven, T., and Stankiewicz, A. I. (2011). Microwave-activated methanol steam reforming for hydrogen production. Int. J. Hydrogen Energy 36, 12843ā12852. doi:10.1016/j.ijhydene.2011.07.009
Einaga, H., Nasu, Y., Oda, M., and Saito, H. (2016). Catalytic performances of perovskite oxides for CO oxidation under microwave irradiation. Chem. Eng. J. 283, 97ā104. doi:10.1016/j.cej.2015.07.051
Ekinci, A., Åahin, Ć., and Horoz, S. (2022). Kinetics of catalytic hydrolysis of NaBH4 solution: Ni-La-B catalyst. J. Aust. Ceram. Soc. 58, 113ā121. doi:10.1007/s41779-021-00673-3
Farag, S., and Chaouki, J. (2015). A modified microwave thermo-gravimetric-analyzer for kinetic purposes. Appl. Therm. Eng. 75, 65ā72. doi:10.1016/j.applthermaleng.2014.09.038
Fukushima, J., Kashimura, K., Takayama, S., Sato, M., Sano, S., Hayashi, Y., et al. (2013). In-situ kinetic study on non-thermal reduction reaction of CuO during microwave heating. Mat. Lett. 91, 252ā254. doi:10.1016/j.matlet.2012.09.114
Gangurde, L. S., Sturm, G. S. J., Devadiga, T. J., Stankiewicz, A. I., and Stefanidis, G. D. (2017). Complexity and challenges in noncontact high temperature measurements in microwave-assisted catalytic reactors. Ind. Eng. Chem. Res. 56, 13379ā13391. doi:10.1021/acs.iecr.7b02091
Gupta, M., and Leong, W. W. (2007). Microwaves and metals. Singapore: John Wiley & Sons (Asia) Pte Ltd.
Hamzehlouia, S., Shabanian, J., Latifi, M., and Chaouki, J. (2018). Effect of microwave heating on the performance of catalytic oxidation of n-butane in a gas-solid fluidized bed reactor. Chem. Eng. Sci. 192, 1177ā1188. doi:10.1016/j.ces.2018.08.054
Hu, J., Wild, C., Stiegman, A. E., Dagle, R. A., Shekhawat, D., Abdelsayed, V., et al. (2020). Microwave-driven heterogeneous catalysis for activation of dinitrogen to ammonia under atmospheric pressure. Chem. Eng. J. 397, 125388. doi:10.1016/j.cej.2020.125388
Huang, Y., Chiueh, P., Kuan, W., and Lo, S. (2016). Microwave pyrolysis of lignocellulosic biomass : Heating performance and reaction kinetics. Energy 100, 137ā144. doi:10.1016/j.energy.2016.01.088
Kappe, C. O. (2013). How to measure reaction temperature in microwave-heated transformations. Chem. Soc. Rev. 42, 4977ā4990. doi:10.1039/c3cs00010a
Khujaev, S., Vasidov, A., and Markelova, E. A. (2013). Extraction of the 131Cs from neutron irradiated barium oxide under microwave radiation. J. Radioanal. Nucl. Chem. 298, 435ā438. doi:10.1007/s10967-013-2687-4
Liu, Q., He, H., Li, H., Jia, J., Huang, G., Xing, B., et al. (2019). Characteristics and kinetics of coal char steam gasification under microwave heating. Fuel 256, 115899. doi:10.1016/j.fuel.2019.115899
Luo, H., Bao, L., Kong, L., and Sun, Y. (2017). Low temperature microwave-assisted pyrolysis of wood sawdust for phenolic rich compounds: Kinetics and dielectric properties analysis. Bioresour. Technol. 238, 109ā115. doi:10.1016/j.biortech.2017.04.030
Nguyen, H. M., Sunarso, J., Li, C., Pham, G. H., Phan, C., and Liu, S. (2020). Microwave-assisted catalytic methane reforming: A review. Appl. Catal. A General 599, 117620. doi:10.1016/j.apcata.2020.117620
Omran, M., Fabritius, T., Heikkinen, E., Vuolio, T., Yu, Y., Chen, G., et al. (2020). Microwave catalyzed carbothermic reduction of zinc oxide and zinc ferrite : Effect of microwave energy on the reaction activation energy. RSC Adv. 10, 23959ā23968. doi:10.1039/d0ra04574h
Patil, P., Gude, V. G., Pinappu, S., and Deng, S. (2011). Transesterification kinetics of Camelina sativa oil on metal oxide catalysts under conventional and microwave heating conditions. Chem. Eng. J. 168, 1296ā1300. doi:10.1016/j.cej.2011.02.030
Perry, W. L., Datye, A. K., Prinja, A. K., Brown, L. F., and Katz, J. D. (2002). Microwave heating of endothermic catalytic reactions : Reforming of methanol. AIChE J. 48, 820ā831. doi:10.1002/aic.690480416
Pham, T. T. P., Ro, K. S., Chen, L., Mahajan, D., Ji, T., and Ashik, S. U. P. M. (2020). Microwave - assisted dry reforming of methane for syngas production : A review. Environ. Chem. Lett. 18, 23. doi:10.1007/s10311-020-01055-0
Ramirez, A., Hueso, J. L., Mallada, R., and Santamaria, J. (2017). In situ temperature measurements in microwave-heated gas-solid catalytic systems . Detection of hot spots and solid-fluid temperature gradients in the ethylene epoxidation reaction. Chem. Eng. J. 316, 50ā60. doi:10.1016/j.cej.2017.01.077
Ramirez, A., Hueso, J. L., Mallada, R., and Santamaria, J. (2020). Microwave-activated structured reactors to maximize propylene selectivity in the oxidative dehydrogenation of propane. Chem. Eng. J. 393, 124746. doi:10.1016/j.cej.2020.124746
Ren, X., Shanb, M., Zhu, H., Ao, W., Zhang, H., Moreside, E., et al. (2022). Challenges and opportunities in microwave-assisted catalytic pyrolysis of biomass : A review. Appl. Energy 315, 118970. doi:10.1016/j.apenergy.2022.118970
Robinson, B., Caiola, A., Bai, X., Abdelsayed, V., Shekhawat, D., and Hu, J. (2020). Catalytic direct conversion of ethane to value-added chemicals under microwave irradiation. Catal. Today 356, 3ā10. doi:10.1016/j.cattod.2020.03.001
Samih, S., and Chaouki, J. (2015). Development of a fluidized bed thermogravimetric analyzer. AIChE J. 61, 84ā89. doi:10.1002/aic.14637
She-bin, W., Wang, S. b., Zhang, M., Liu, J. y., and Zhou, J. x. (2008). Kinetics of voluminal reduction of chromium ore fines containing coal by microwave heating. J. Iron Steel Res. Int. 15, 10ā15. doi:10.1016/S1006-706X(08)60258-7
Stefanidis, G. D., Munoz, A. N., Sturm, G. S., and Stankiewicz, A. (2014). A helicopter view of microwave application to chemical processes : Reactions , separations , and equipment concepts. Rev. Chem. Eng. 30, 33. doi:10.1515/revce-2013-0033
Sun, J., Wang, W., Liu, Z., Ma, Q., Zhao, C., and Ma, C. (2012). Kinetic study of the pyrolysis of waste printed circuit boards subject to conventional and microwave heating. Energies (Basel) 5, 3295ā3306. doi:10.3390/en5093295
Wan, M., Yue, H., Notarangelo, J., Liu, H., and Che, F. (2022). Deep learning-assisted investigation of electric FieldāDipole effects on catalytic ammonia synthesis. JACS Au 2, 1338ā1349. doi:10.1021/jacsau.2c00003
Xia, X., Zhao, X., Zhou, P., Feng, T., Ma, C., and Song, Z. (2020). Reduction of SO2 to elemental sulfur with carbon materials through electrical and microwave heating methods. Chem. Eng. Process. - Process Intensif. 150, 107877. doi:10.1016/j.cep.2020.107877
Yadav, G. D., and V Borkar, I. (2006). Kinetic modeling of microwave-assisted chemoenzymatic epoxidation of styrene. AIChE J. 52, 1235ā1247. doi:10.1002/aic.10700
Yang, X., Cheng, K., and Jia, G. (2020). Microwave heating and non-thermal effects of sodium chloride aqueous solution. Mol. Phys. 8976, e1662505. doi:10.1080/00268976.2019.1662505
Keywords: microwave irradiation, reaction kinetics, thermal effect, non-thermal effect, temperature measurement, hot spot
Citation: Adavi K, Amini A, Latifi M, Shabanian J and Chaouki J (2022) Kinetic study of multiphase reactions under microwave irradiation: A mini-review. Front. Chem. Eng. 4:1059160. doi: 10.3389/fceng.2022.1059160
Received: 30 September 2022; Accepted: 19 October 2022;
Published: 01 November 2022.
Edited by:
Xinwei Bai, National Energy Technology Laboratory (Leidos), United StatesCopyright Ā© 2022 Adavi, Amini, Latifi, Shabanian and Chaouki. This is an open-access article distributed under the terms of the Creative Commons Attribution License (CC BY). The use, distribution or reproduction in other forums is permitted, provided the original author(s) and the copyright owner(s) are credited and that the original publication in this journal is cited, in accordance with accepted academic practice. No use, distribution or reproduction is permitted which does not comply with these terms.
*Correspondence: Jamal Chaouki, jamal.chaouki@polymtl.ca