- Department of Applied Chemistry, Graduate School of Natural Science and Technology, Okayama University, Okayama, Japan
We develop a sequential flow process for the production of monodisperse poly (methyl methacrylate) (PMMA)/polystyrene (PS) composite particles through a soap-free emulsion polymerization of methyl methacrylate (MMA) using the first water-in-oil (W/O) slug flow and a subsequent seeded emulsion polymerization of styrene (St) using the second W/O slug flow. In this process, monodisperse PMMA seed particles are first formed in the dispersed aqueous phase of the first W/O slug flow. Subsequently, removal of the oil phase from the slug flow is achieved through a porous hydrophobic tubing, resulting in a single flow of the aqueous phase containing the seed particles. The aqueous phase is then mixed with an oil phase containing St monomer to form the second W/O slug flow. Finally, monodisperse PMMA/PS composite particles are obtained by a seeded emulsion polymerization of St using the second W/O slug flow. We compared the reaction performance between the slug flow and the batch processes in terms of particle diameter, monomer conversion, particle size distribution, and the number of particles in the system. We found that internal circulation flow within the slugs can enhance mass transfer efficiency between them during polymerization, which results in monodisperse PMMA/PS composite particles with a large particle diameter and a high monomer conversion in a short reaction time, compared to those prepared using the batch process. We believe that this sequential microflow process can be a versatile strategy to continuously produce monodisperse composite particles or core-shell particles in a short reaction time.
Introduction
Polymer/polymer composite particles have been applied to various applications such as coatings (Jiang et al., 2017), reinforced elastomers (Yu et al., 2017), high-impact plastics (Guo et al., 2003), and toughened plastics (Ning et al., 2020) since the functionality of polymer particles can be easily controlled by the combination of polymers and the morphology of polymer particles. In general, polymer/polymer composite particles are prepared via multistep polymerization process using a seeded emulsion polymerization (Cho and Lee, 1985). In a seeded emulsion polymerization, an emulsion or soap-free emulsion polymerization is first conducted to prepare monodisperse polymer particles. Then, part of the polymer particle dispersion is used as a seed solution for a subsequent seeded emulsion polymerization. If there are no micelles in a seed solution, a monomer that diffuses to the seed solution during polymerization is only consumed to grow the seed to the desired size without a new nucleation event. Recently, various morphologies including core-shell (Vatankhah et al., 2020; Watanabe et al., 2020b), Janus (Tang et al., 2010; Chen et al., 2017), hollow (Kobayashi et al., 2007, 2009; Lv et al., 2008), and raspberry-like (Perro et al., 2006; Tolue et al., 2009) structures have been prepared by controlling thermodynamic and kinetic parameters during a seeded emulsion polymerization. Seeded emulsion polymerization has therefore attracted attention as one of the most effective ways to produce polymer composite particles as well as control the morphology of particles. However, it requires a long time to produce polymer/polymer composite particles with a batch process due to time-consuming multiple polymerization steps.
In the last decades, microflow processes have increased tremendous attention in the field of fine chemistry and chemical/bio engineering as an innovative process because of their unique characteristics such as high heat and mass transfer efficiency (Schwalbe et al., 2002; Elvira et al., 2013; Tanimu et al., 2017; Wang and Luo, 2017) and precise control over temperature and reaction time (Mason et al., 2007; Yoshida, 2010). These characteristics of microflow processes originate from their large surface to volume ratio and short diffusion path. Recently, a microreaction technology has been applied to not only organic syntheses but also polymerization reactions. For example, homogeneous polymerization including radical polymerization (Iwasaki and Yoshida, 2005; Iwasaki et al., 2006; Xiang et al., 2019) and controlled/living radical polymerization (Hornung et al., 2011; Tonhauser et al., 2012; Parida et al., 2014) with the use of microflow processes produce polymers with a controlled molar mass and a narrow molar mass dispersity. Heterogeneous polymerization reactions using liquid–liquid multiphase systems such as emulsion polymerization (Yadav et al., 2014; Liu et al., 2017), miniemulsion photopolymerization (Lobry et al., 2014) and suspension polymerization (Liu et al., 2011; Sen et al., 2020) enable the production of polymer particles with various sizes and morphologies in a continuous manner.
Among heterogeneous polymerization reactions using a microflow process, liquid–liquid slug flow has attracted attention as a new polymerization field instead of emulsion drops because a segmented liquid–liquid slug flow can be prepared just by mixing water and oil phases without any surfactant in a microflow reactor and the products after polymerization can be easily collected by a subsequent spontaneous phase separation between water and oil phases at the exit of the reactors. Moreover, when the polymerization proceeds only in the dispersed phase of the slug flow, a thin liquid film of the continuous phase around the dispersed phase prevents solid products formed in the dispersed phase from adhering to the channel wall (Seike et al., 2007). Furthermore, internal circulation flow within the slugs enhances the mixing of reactants in each slug and mass transfer between the liquid–liquid interfaces (Song et al., 2018; Song et al., 2019). In our previous studies, we have shown that a soap-free emulsion polymerization of methyl methacrylate (MMA) using a water-in-oil (W/O) slug flow enhances the rate of polymerization, resulting in poly (methyl methacrylate) (PMMA) particles with a high molar mass (∼1,500 kg mol−1) at a 20-min reaction time (Watanabe et al., 2019). We also found that addition of non-ionic surfactant to the continuous phase of a W/O slug flow prevents formed particles from adhering to the liquid–liquid interfaces and provides polymer particles with a narrow particle size distribution (Watanabe et al., 2020a). This polymerization strategy can be utilized to produce monodisperse polymer particles with a high molar mass in a short reaction time. However, to the best of our knowledge, there are no reports on the continuous production of polymer/polymer composite particles using a sequential microflow process.
In this study, we develop a sequential flow process to prepare monodisperse PMMA/PS composite particles by combining a soap-free emulsion polymerization of MMA using the first W/O slug flow and a subsequent soap-free seeded emulsion polymerization of styrene (St) using the second W/O slug flow. First, to confirm whether a W/O slug flow can be applied to a seeded emulsion polymerization, we demonstrate the seeded emulsion polymerization of St using a W/O slug flow in the presence of seed particles (batch/flow process) (Figure 1A) and compare the reaction performance between the batch/flow and a batch process. Then, we evaluate the effect of seed particle diameter on the reaction performance of the seeded emulsion polymerization using the batch/flow and the batch processes. Finally, we demonstrate a sequential flow (flow/flow) process to prepare PMMA/PS composite particles (Figure 1B) and compare the reaction performance between the sequential flow and the batch processes.
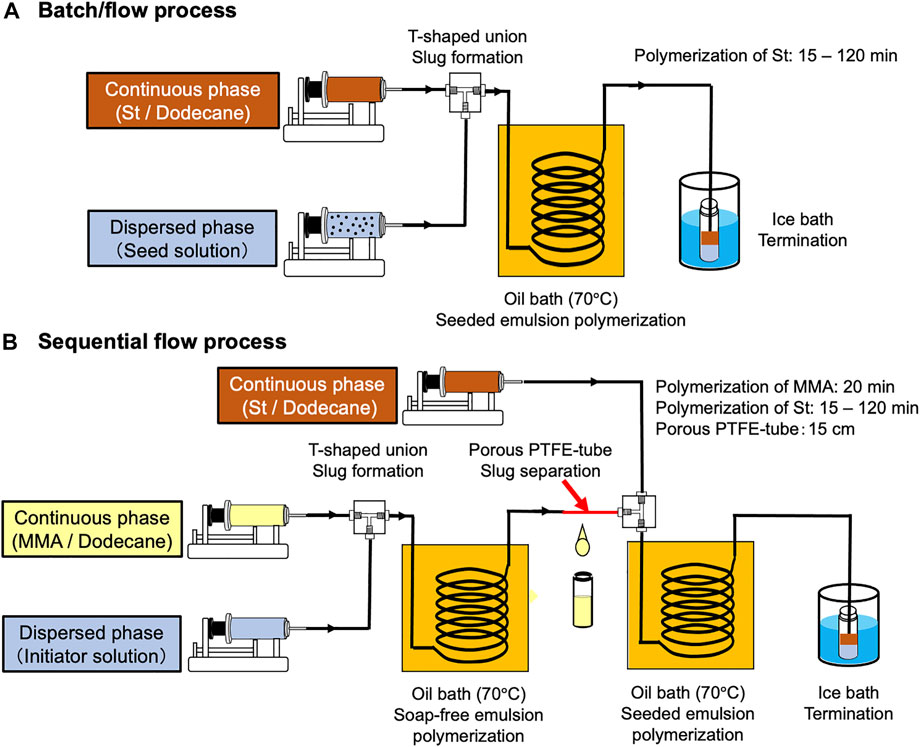
FIGURE 1. Schematic images of the microflow systems to prepare PMMA/PS composite particles (A) Batch/flow process, (B) Sequential flow process.
Materials and Methods
Materials
Methyl methacrylate (MMA, FUJIFILM Wako) and styrene (St, FUJIFILM Wako) were used after purification by distillation under a reduced pressure to remove polymerization inhibitors. Distilled water used in all experiments was produced with a distilled water production system (RFD210TC, ADVANTEC, Japan). Potassium persulfate (KPS) and dodecane were purchased from FUJIFILM Wako and used as received. Span 85, which is an oil-soluble non-ionic surfactant, was purchased from Sigma-Aldrich and used as received.
Fabrication of Microflow System
The microfluidic devices were fabricated by assembling T-shaped poly (1,1,2,2-tetrafluoroethylene) (PTFE) unions (outer diameter 1/16″, GL science) and PTFE tubes (inner diameter: 1 mm and outer diameter: 1/16”, GL science). The inlet PTFE tube having 20 cm-long was connected to syringes (HSW NORM-JECT® Syringe, Henke-Sass, Wolf) placed on syringe pumps (Harvard Pump 33 Dual Syringe Pump, Harvard Apparatus). In the heating zone, the PTFE tubes were coiled helically and dipped in an oil bath (PAIRSTIRRER PS-1000, EYELA) at 70°C. In the case of a batch/flow process, the residence time of the heating zone for the polymerization of MMA was fixed at 20 min with the tube length of 4.8 m. In case of a sequential flow process, the residence time of the heating zone for the first polymerization of MMA was set at 20 min with the tube length of 4.8 m, while that for the second polymerization of St was controlled from 15 to 120 min by changing the tube length from 3.5 to 28 m, respectively. Between the first reaction zone and the second T-shaped PTFE union, a 15 cm-long porous water-oil separator (PTFE filter tube, inner diameter: 1 mm and outer diameter: 2 mm, Kokugo) was set to remove the remaining oil phase from the W/O slug flow. The exit of the outlet tube after polymerization was placed in a collection vial put in an ice bath.
Preparation of PMMA Seed Particles Using a Batch Process
PMMA seed particles were prepared by a soap-free emulsion polymerization of MMA using a batch process. Five mM of KPS was added to 100 ml of distilled water in a 100 ml two-necked flask set in an oil bath and deoxygenated by bubbling with nitrogen for 20 min under stirring. MMA was added to a 50 ml two-necked flask and then deoxygenated by bubbling with nitrogen for 20 min under stirring. The KPS aqueous solution (100 ml) and 2 mol/L of MMA (21.3 ml) were poured into a 300 ml three-necked flask, and polymerization was conducted for 1 h at 480 rpm and 70°C under a nitrogen atmosphere. The resulting suspension was centrifuged three times (himac CF 15R, HITACHI, 13,200 rpm, 10 min, 25°C) to separate and wash the product. The washed product was freeze-dried in a freeze-dryer overnight.
Preparation of PMMA/PS Composite Particles Using a Batch Process in the Presence of Seed Particles
PMMA/PS composite particles were prepared by a seeded emulsion polymerization of St using a batch process in the presence of PMMA seed particles. Initially, a 300 ml three-necked flask equipped with a mechanical stirrer was set in an oil bath and deoxygenated with nitrogen for 20 min. An aqueous solution (100 ml) containing 3.7 mM KPS and 5 g of PMMA particles [Dp = 634 nm, Coefficient of Variance (CV) = 4.1%] were added to a 100 ml two-necked flask, stirred for 1 h, followed by deoxygenated with nitrogen for 20 min. St was added to a 50 ml two-necked flask and then deoxygenated with nitrogen for 20 min. The KPS aqueous solution (100 ml) and St (16.5 ml) were poured into the 300 ml three-necked flask in the oil bath and then polymerization was conducted for 1 h at 480 rpm and 70°C under a nitrogen atmosphere. The products were washed and dried using the same procedure as above.
Preparation of PMMA/PS Composite Particles Using a Batch/Flow Process
PMMA/PS composite particles were prepared by a seeded emulsion polymerization of St using a W/O slug flow in the presence of PMMA seed particles. For a seed solution (W), 3.7 mM of KPS and 5 g of PMMA seed particles (Dp = 634 nm, CV = 4.1%) were added to 100 ml of distilled water and deoxygenated with the same procedure described above. For a monomer solution (O), 10 ml of St and 40 ml of dodecane (the mixture was St/dodecane = 1/4, v/v) and 5 wt% of Span 85 was added to a 50 ml two-necked flask and deoxygenated with the same procedure described above. These solutions were charged into disposable plastic syringes. Both syringes were set on the syringe pump, and the tip of the syringes was connected to the inlet tubes of the microreactor. The solutions were infused into the microreactor with a total flow rate of 184.6 μL min−1, while keeping the volume ratio of oil to water phase constant at 1.0. A W/O slug flow formed at the T-shaped union having a hydrophobic surface traveled downstream and was passed through a reaction region where the tube was immersed in an oil bath at 70°C. Then, polymerization was initiated in the aqueous phase and proceeded during which the slugs was passed through the reaction zone. The reaction time was controlled from 15 to 60 min by changing the length of the tube immersing into the oil bath from 3.5 to 14 m. After the polymerization, the sample solution was collected in a sample vial placed in an ice bath. The collected sample was subsequently phase separated between aqueous and oil phases in the sample vial, and the reaction was quenched. After the upper oil phase was removed from the sample, the products were washed and dried using the same procedure as above.
Preparation of PMMA/PS Composite Particles Using a Batch Process
PMMA/PS composite particles were prepared by a soap-free emulsion polymerization of MMA and a subsequent seeded emulsion polymerization of St using a batch process. Initially, a 100 ml two-necked flask equipped with a mechanical stirrer was set in an oil bath and deoxygenated with nitrogen for 20 min. An aqueous solution (100 ml) containing 5 mM KPS was added to a 100 ml two-necked flask, followed by deoxygenated with nitrogen for 20 min. MMA and dodecane were added to each 50 ml of two-necked flask and then deoxygenated with nitrogen for 20 min. A mixture of MMA/dodecane (MMA/dodecane = 4/1, v/v) was added to a 50 ml two-necked flask. Both the aqueous phase (30 ml) and the mixture of MMA/dodecane (30 ml) were added to the two-necked flask set in the oil bath and the polymerization of MMA was conducted for 20 min at 240 rpm and 70°C under a nitrogen atmosphere. St and dodecane were added to each 50 ml two-necked flask and then deoxygenated with nitrogen for 20 min. After removing the oil phase of the soap-free emulsion polymerization system, a mixture of St/MMA [30 ml, St/dodecane = 4/1 (v/v)] was added to the aqueous solution containing PMMA seed particles and then a seeded emulsion polymerization of St was performed for 15–120 min at 240 rpm and 70°C under a nitrogen atmosphere. The products were washed and dried using the same procedure as above.
Preparation of PMMA/PS Composite Particles Using a Sequential Flow Process
PMMA/PS composite particles were prepared by a soap-free emulsion polymerization of MMA, followed by a seeded emulsion polymerization of St using a W/O slug flow. For an initiator aqueous solution (W), 5 mM of KPS was added to 100 ml of distilled water in a 100 ml two-necked flask and deoxygenated with nitrogen for 20 min. For the first monomer solution (O), 10 ml of MMA and 40 ml of dodecane (the mixture was MMA/dodecane = 1/4, v/v) and 5 wt% of Span 85 was added to a 50 ml two-necked flask and deoxygenated with a nitrogen for 20 min. For the second monomer solution (O), 10 ml of St and 40 ml of dodecane (the mixture was St/dodecane = 1/4, v/v) and 5 wt% of Span 85 was added to 50 ml two-necked flask and deoxygenated with a nitrogen for 20 min. In the first step, to prepare PMMA seed particles, the aqueous and the oil solutions were fed into the microreactor with a total flow rate of 184.6 μL min−1, while keeping the volume ratio of oil to water phase constant at 1.0. A The polymerization was conducted at 70°C for 20 min. Then, the first oil phase of the slug flow was removed through a 15 cm-long porous PTFE tube. Subsequently, the aqueous phase containing PMMA seed particles was mixed with the second oil phase at the second T-shaped union to form W/O slug flow, and polymerization was conducted in an oil bath at 70°C to prepare PMMA/PS composite particles. The reaction time was controlled from 15 to 120 min by changing the length of the tube immersing into the oil bath from 3.5 to 28 m. After the polymerization, the sample solution was collected in a sample vial placed in an ice bath. The collected sample was subsequently phase separated between aqueous phase and oil phase in the sample vial, and the reaction was quenched. After the upper oil phase was removed from the sample, the products were washed and dried using the same procedure as above.
Characterization
The morphology of particles was observed by a scanning electron microscope (SEM, S-4700, Hitachi Ltd., Japan) at a voltage intensity of 2 kV. Before SEM observation, the prepared particles were sputter-coated (E-1030 Ion-Sputter, Hitachi Ltd., Japan) with Pd/Pt for 1 min to reduce the sample charging. Average particle diameter and the size distribution were determined with SEM images by using an image analysis software (WinROOF, Mitani Co., Ltd., Japan). In the image analysis, the size distribution was evaluated as CV that is defined as the ratio of standard deviation to average diameter. The CV values were calculated from the average diameter of 200 particles. Monomer conversion was calculated by the following equation: Monomer conversion (%) = 1—(the amount of unreacted monomer)/(the amount of feed monomer) ×100. To determine the amount of unreacted monomer in the system, the upper oil phase in a collection vial after polymerization was dissolved in hexane (2 ml) that was used as an internal standard. The solution was then analyzed by gas chromatography (GC-14A, Shimadzu Ltd., Japan) equipped with a J&W Scientific 30-m DB-WAX column with a Shimadzu CR51 Chromatopac. The GC conditions were as follows: initial column oven temperature 40°C, initial hold time of the column oven temperature 2 min, heating rate 10°C min−1, final column oven temperature 160°C, final hold time 2 min, detector temperature 250°C, and injector temperature 250°C. Fourier transform infrared (FT-IR) spectra were measured using a FT-IR spectrometer (IRPrestige-21, Shimadzu, Japan). The dried polymer particles were mixed with KBr and pressed to a disk for measurement.
Results
Seeded Emulsion Polymerization of St in the Presence of PMMA Seed Particles
In our previous study, we have reported that a soap-free emulsion polymerization of MMA using a W/O slug flow facilitates the rate of polymerization by high heat transfer in microreactor and enhanced mass transfer between liquid–liquid interface through internal circulation flow, which results in polymer particles with a large diameter and a high molar mass in a short reaction time (Watanabe et al., 2019). However, it is not clear that a slug flow can be applied to a soap-free seeded emulsion polymerization and how the slug flow process affects the reaction performance, compared to a batch process. A general soap-free seeded emulsion polymerization consists of two-step polymerization processes: the first polymerization to prepare seed particles and the second polymerization to prepare composite particles. In the first step, seed polymer particles are prepared by typical soap-free emulsion polymerization. Then, in the second step, the polymerization of the second monomer is performed in the aqueous dispersion of the seed particles. In this step, the second monomer diffuses to the aqueous phase and swells the seed polymer particles. During the polymerization, a nucleation process is prevented and thus the second monomer can be only consumed by the seed polymer particles, which results in the formation of composite particles. In this study, we first demonstrated a seeded emulsion polymerization of St using a W/O slug flow and batch processes in the presence of PMMA seed particles and compared the reaction performance between the processes. It is noted here that the flow rate of the slug flow, the length of the reactor, and the stirring rate for a batch process were determined based on the result of our previous reports (Watanabe et al., 2019; Watanabe et al., 2020a).
The PMMA seed particles (Dp = 634 nm, CV = 4.1%) were prepared by a soap-free emulsion polymerization of MMA using a batch process (Figure 2A). Then, a series of the seeded emulsion polymerization of St in the presence of the seed particles using both the slug flow and the batch processes were conducted for a predetermined reaction time (15, 30, 45, and 60 min). Figures 2B,C show the representative SEM images of PMMA/PS composite particles prepared using the batch/flow and the batch processes at 60-min reaction time. We found that regardless of the process, the diameter of the composite particles was larger than that of the seed particles. Figure 3 shows the representative FT-IR spectra of PMMA seed particles and PMMA/PS composite particles. The spectrum of PMMA/PS composite particles shows the typical characteristic bands for PMMA at 2,994 and 2,951 cm−1 due to aliphatic C–H stretching, 1729 cm−1 due to aliphatic–C=O stretching vibration, and 1,191, 1,151 cm−1 due to C–O–C stretching vibration, and those for PS at 3,026 cm−1 due to aromatic C–H stretching vibration, 1,600 and 1,492 cm−1 due to C=C stretching vibration, and 698 cm−1 –C–H out of plane bending vibration. These results indicate that the seeded emulsion polymerization of St would proceed in both the processes.
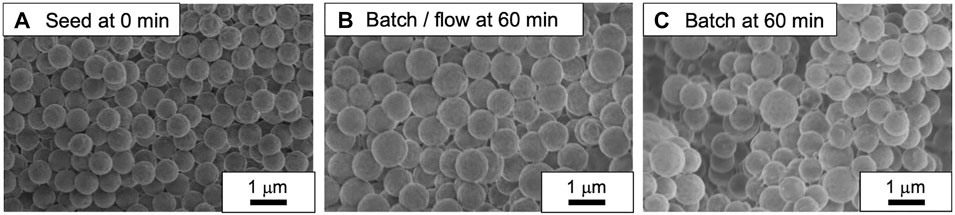
FIGURE 2. (A) PMMA seed particles, (B) PMMA/PS composite particles prepared with the batch/flow process at 60 min, (C) PMMA/PS composite particles prepared with the batch process at 60 min.
Figure 4 shows the comparison of reaction performance using the batch/flow and the batch processes in terms of particle diameter, monomer conversion, their CV value, and the number of particles as a function of reaction time. The particle growth rate and the increase of monomer conversion in the batch/flow process was faster than those in the batch process, as shown in Figures 4A,B, respectively. This tendency was similar to that in the soap-free emulsion polymerization of MMA using a W/O slug flow (Watanabe et al., 2019; Watanabe et al., 2020a). Rapid particle growth and high polymerization rate in the batch/flow process would be due to two effects: high heat transfer efficiency in the microflow reactor and high mass transfer efficiency induced by internal circulation flow within each slug. The model calculation result of the heat transfer in the PTFE tube immersed in an oil bath showed that the temperature of the slug stream can increase from 20 to 70°C in 18 s after the stream entered the heating zone (Supplementary Figure S1). This excellent heat transfer efficiency of the microflow reactor could facilitate the decomposition of initiator molecules and increase the numbers of ionic radicals and growing polymer chains that are absorbed to the seed particles in the dispersed aqueous phase, which results in a high rate of particle growth in the slug flow. Moreover, the internal circulation flow in each slug continuously provides the dispersed aqueous phase with monomer from the continuous oil phase, which would promote the rate of polymerization in the slug flow process.
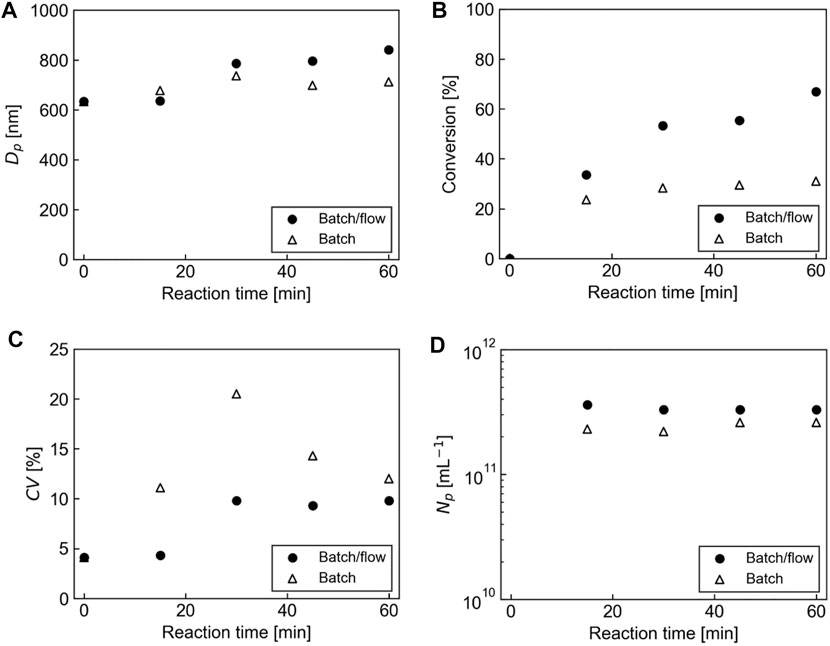
FIGURE 4. Comparison of the reaction performance of the seeded emulsion polymerization of St using the batch/flow and the batch processes. (A) Particle diameter, (B) Monomer conversion, (C) CV value of the particle diameter, (D) The number of particles per unit volume.
Figure 4C shows the change in CV value as a function of reaction time for both processes. Regardless of the process, the CV values showed a tendency to increase with reaction time from 0 to 30 min. After that, in the batch process, the CV values showed a decreasing trend up to 60 min. On the other hand, in the flow process, the CV values maintained almost constant until 60 min. There is a possibility that a small number of large particles formed due to coagulation in the early stage of the polymerization may cause the increase in CV values up to 30 min, and that the CV value decreases or maintains almost constant because the size difference between the large particles and the other particles decreases in the later stage of polymerization. After 60-min polymerization, the CV value of the resulting particles prepared using the batch/flow process was less than 10%, which was slightly lower than those prepared using the batch process.
To confirm the progress of polymerization based on a seeded emulsion polymerization mechanism, we evaluated the number of particles per unit volume as a function of reaction time using the following equation (Lovell and Schork, 2020).
where
Effects of Seed Particle Diameter on a Seeded Emulsion Polymerization of St in the Presence of Seed Particles
To evaluate the effects of seed particle diameter on the reaction performance of the seeded emulsion polymerization of St using the batch/flow and the batch processes, we prepared PMMA seed particles with three different diameters (Dp = 183, 397, and 634 nm) (Figure 5) and performed a seeded emulsion polymerization of St using each seed particle. Figure 6A shows the effect of the PMMA seed particle diameter on the resulting PMMA/PS composite particle diameter as a function of time. In both the processes, regardless of the seed particle diameter, the PMMA/PS composite particle diameter became bigger as a function of reaction time and the particle growth rate in the batch/flow process was slightly higher than that in the batch process. As shown in Figure 6B, the monomer conversion in the batch/flow process was higher than that in the batch process. In addition, the monomer conversion decreased with larger seed particles in both the processes. In this experiment, we added the same weight of seed particles having different diameters to the reaction system. This means that as the seed particle diameter decreases, the number of the seed particles added to the reaction system increases. We thus think that a large number of seed particles with small diameters would consume many monomers per unit time. Therefore, the monomer conversion decreased with large seed particles. Figure 6C shows the effect of the PMMA seed particle diameter on the CV value of the PMMA/PS composite particles as a function of time. There was no clear trend in changes in the CV value of the obtained particles prepared with the seed particles having different diameters, but the CV value of the PMMA/PS composite particles obtained in the batch/flow process was less than 10% and lower than that obtained in the batch process. As shown in Figure 6D, there were no significant changes in the number of particles during the polymerization in both the processes, indicating that a seeded emulsion polymerization was successfully conducted in each condition. These results clearly show that regardless of PMMA seed particle diameter, a seeded emulsion polymerization of St using a batch/flow process provides PMMA/PS composite particles with a high monomer conversion and a narrow particle size distribution, compared to those prepared using a batch process.
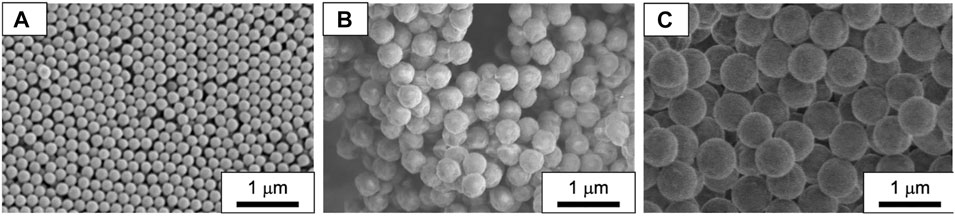
FIGURE 5. SEM images of PMMA seed particles with different diameters. The diameters are (A) 183 nm, (B) 397 nm, and (C) 634 nm.
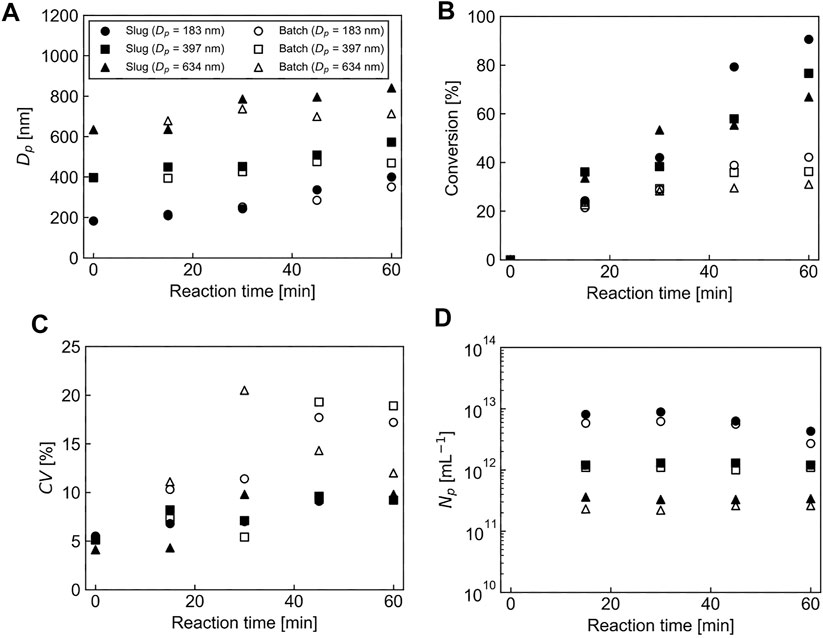
FIGURE 6. Effects of seed particle diameter on the reaction performance of the seeded emulsion polymerization of St using the batch/flow and the batch processes. (A) Particle diameter, (B) Monomer conversion, (C) CV value of the particle diameter, (D) The number of particles per unit volume.
Comparison of Reaction Performance Between Sequential Flow and Batch Processes
We found in the above study that a W/O slug flow can be used as a reaction field to perform a seeded emulsion polymerization of St and that the resulting PMMA/PS composite particles have a large diameter and a narrow particle size distribution in a short reaction time, compared to those prepared using a batch process. We then developed a sequential flow process to produce monodisperse PMMA/PS composite particles in a continuous manner by combining a soap-free emulsion polymerization of MMA using the first W/O slug flow with a subsequent seeded emulsion polymerization of St using the second W/O slug flow. In this process, PMMA seed particles were first prepared by a soap-free emulsion polymerization of MMA using a W/O slug flow. Then, to separate the continuous oil phase from the slug flow, the slug flow was passed through a porous hydrophobic tube (Bannock et al., 2013). The separated aqueous phase was then mixed with the second oil phase containing St monomer to form the second W/O slug flow. Subsequently, PMMA/PS composite particles were prepared by a seeded emulsion polymerization of St in the slug flow.
Figure 7 shows the SEM images of PMMA particles and PMMA/PS composite particles prepared using the sequential flow and the batch processes at different reaction times. It is noted that the SEM images at 0 min describe the PMMA seed particles prepared with a soap-free emulsion polymerization for 20 min using both the processes. The PMMA seed particles prepared using the sequential flow process had about 1.5 times larger diameter than those prepared using the batch process. The time-course observation of the particles during the seeded emulsion polymerization revealed that new particles were not formed in both the processes and that the particle diameter increased as a function of reaction time. As shown in Figure 8A, after the seeded emulsion polymerization for 120 min, there was a significant difference in diameter of the particles between the sequential flow and the batch processes: The diameter of the composite particles prepared using the sequential flow process was 428 nm, which was about 1.7 times larger than that prepared using the batch process. As shown in Figure 8B, monomer conversion in the sequential flow process also increased and reached 97.4% at 120 min, while that in the batch process reached 47.2% at 120 min. Figure 8C shows the CV values of the PMMA/PS composite particles as a function of reaction time. Although the CV values of the resulting particles prepared using the sequential flow varied significantly depending on the reaction time, the value at 120 min was around 9%, indicating that the particles had a relatively monodisperse particle size distribution. The CV values of the resulting particles prepared using the batch process were kept constant around 6% and these values were considerably lower than those in the batch process using as-prepared PMMA seed particles. Figure 8D shows changes in the number of particles in both the processes during the seeded emulsion polymerization. The number of particles in both the processes were kept constant during the polymerization, which strongly suggests that the polymerization proceeded based on a seeded emulsion polymerization mechanism. In the whole reaction time, the number of the particles present in the sequential flow process was significantly smaller than that in the batch process. This is because the diameter of the seed particles formed in the first polymerization in the sequential flow process was significantly larger than that in the batch process and the number of particles in both the processes was then kept almost constant during the second polymerization. Based on these results, we succeeded in the development of a sequential flow process to prepare monodisperse PMMA/PS composite particles in a continuous way and found that the sequential flow process provides reaction field with a high rate of polymerization, resulting in monodisperse PMMA/PS composite particles with a large diameter and a high monomer conversion in a short reaction time, compared to a batch process.
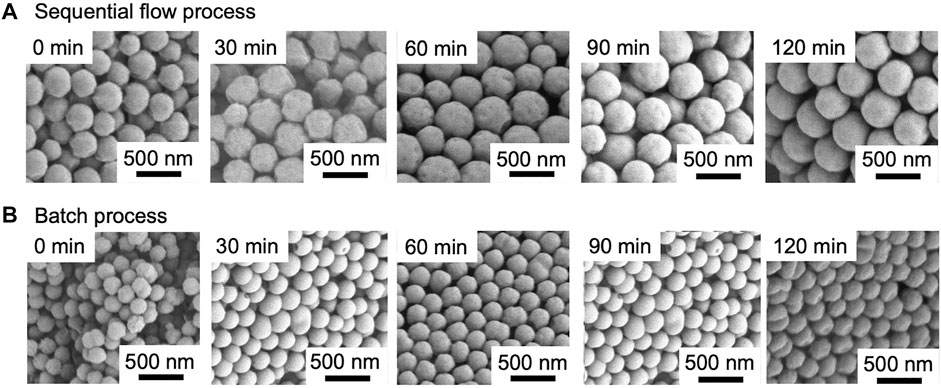
FIGURE 7. SEM images of PMMA/PS composite particles prepared using (A) the sequential flow process and (B) the batch process.
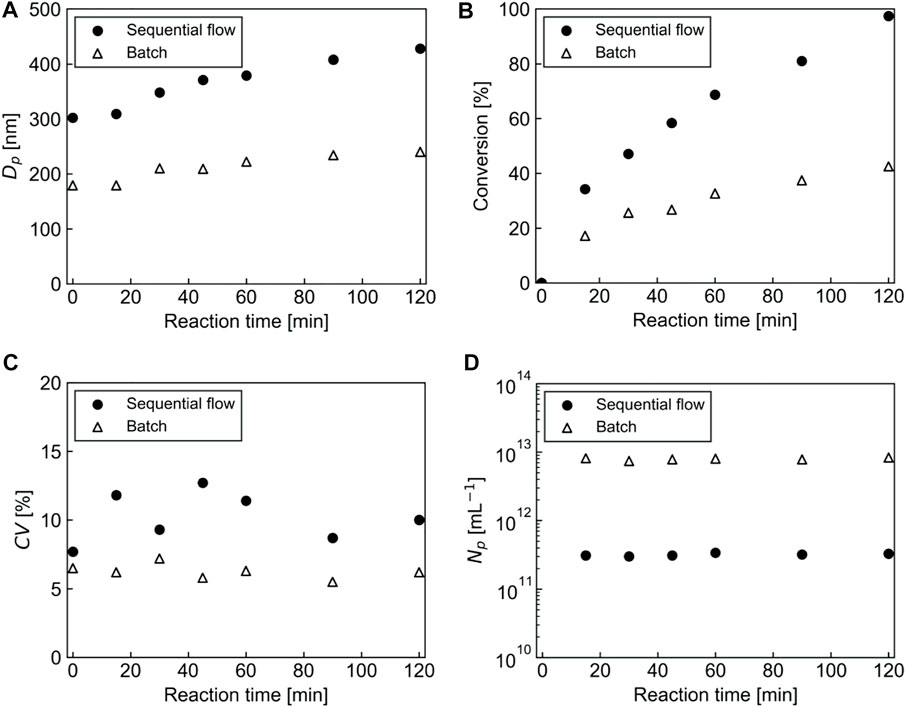
FIGURE 8. Comparison of the characteristics of the seeded emulsion polymerization of St using the sequential flow and the batch processes. (A) Particle diameter, (B) Monomer conversion, (C) CV value of the particle diameter, (D) The number of particles per unit volume. The time at 0 min means the time when the polymerization of St is initiated.
Discussion
Advantage of Slug Flow for Seeded Emulsion Polymerization
Seeded emulsion polymerization has been one of the most versatile ways to design polymer composite particles with various morphologies by controlling thermodynamic and kinetic parameters upon the polymerization. However, the preparation process requires laborious and time-consuming multi-step procedures. Here, as the proof-of-concept study, we demonstrated that a microflow process using a W/O slug flow can be applied to a seeded emulsion polymerization for the preparation of PMMA/PS composite particles (Figure 4). Moreover, we developed a sequential flow process to produce monodisperse PMMA/PS composite particles in a continuous manner by combination of a soap-free emulsion polymerization of MMA and a subsequent seeded emulsion polymerization of St using a W/O slug flow. Specifically, we found that particle growth rate and polymerization rate during both the first seed particle formation step and the second composite particle formation step in the slug flow process are faster than those in the batch process (Figure 8A), and that the sequential flow process results in monodisperse PMMA/PS composite particles having a large diameter and a high monomer conversion in a short reaction time, compared to the batch process (Figure 8C).
The reaction performance of a seeded emulsion polymerization using a sequential flow process is analogue to that of a soap-free emulsion polymerization using a W/O slug flow (Watanabe et al., 2019; Watanabe et al., 2020a) and is related to other reports regarding oxidative polymerization of aniline (Song et al., 2018) and synthesis of polyacrylamide with a high molar mass using a slug flow (Song et al., 2019). Although the detailed mechanism of the enhanced rate of polymerization in a slug flow has not been elucidated from the point of view of quantitative mass transfer analyses and polymerization kinetics, it would derive from two characteristics of a microflow process: high heat transfer efficiency in the narrow width of the microchannel and high mass transfer efficiency induced by internal circulation flow within the slugs.
Limitations on Slug Flow for Seeded Emulsion Polymerization
To enhance the rate of polymerization in a soap-free emulsion polymerization and a seeded emulsion polymerization using a W/O slug flow, it is of importance for the slug flow to be kept stable in the whole reaction time. However, we found that increasing a pressure drop in polymerization systems causes the instability of the slug flow. Specifically, in a seed particle formation step, a slug flow tends to be destabilized when the viscosity of the dispersed phase increases by increasing the number (volume fraction) of the seed particles, which may lead to a decrease in the rate of polymerization and a wide particle size distribution upon a subsequent seeded emulsion polymerization. To circumvent the instability of a slug flow caused by increasing the viscosity of the dispersed phase, it is important to control the number of seed particles formed in the first step by tuning the concentration of initiator and monomer as a pilot study.
Another limitation on slug flow for a seeded emulsion polymerization is the reaction time. In a microflow process, the reaction (residence) time of polymerization can be calculated by the length of a reaction tube divided by a linear flow rate. In general, as increasing the length of the reaction tube or the linear flow rate, the pressure drop in the system increases. Therefore, monomer types that require a long-time reaction are generally difficult to be applied to the slug flow process. When constructing a sequential flow process for the preparation of new polymer composite particles, we must check the required reaction time for each monomer and then determine the basic reaction conditions such as flow rates and the length and diameter of the tubes, based on the pressure drop of the system.
Future Direction of Research About Slug Flow for Composite Particle Synthesis
Despite these limitations, the experimental evidence we have reported shows that a seeded emulsion polymerization using a W/O slug flow has significant advantages. The microflow technology can be potentially used for the rapid production of monodisperse polymer/polymer composite particles with various morphologies in a continuous way by tuning thermodynamics and kinetic parameters of the polymerization systems. In addition, not only polymer particles but also inorganic particles can be utilized for the seed particles and thus inorganic/organic composite particles can be developed using the same procedure, which can be applied to biomedical fields including optical materials, sensors, and diagnosis. Moreover, to consider the industrial application of the microflow process, it will be required to develop a scalable microflow process as well as a continuous monitoring process of the product.
Conclusion
In this study, we have developed a sequential flow process using a W/O slug flow to produce monodisperse PMMA/PS composite particles in a continuous manner. Compared to the current batch process, the W/O slug flow process can enhance the rate of polymerization and produce monodisperse composite particles having a large diameter and a high monomer conversion in a short reaction time. This microflow technology has the exciting potential to the rapid production of polymer/polymer composite particles having various combinations of materials and morphologies, which can be applied to coatings, reinforced materials, optics, sensors, and diagnosis.
Data Availability Statement
The original contributions presented in the study are included in the article/Supplementary Material, further inquiries can be directed to the corresponding author.
Author Contributions
TW and TO designed the experiments and wrote the manuscript. TW, KK, and MM performed the experiments and interpreted the experimental data. TO supervised the whole research. All authors contributed to the article and approved the submitted version.
Funding
TW and TO thank the financial support from the Japan Society for the Promotion of Science (JSPS, Grant-in-Aid for Scientific Research, Nos. JP21K04749 and JP18H01767).
Conflict of Interest
The authors declare that the research was conducted in the absence of any commercial or financial relationships that could be construed as a potential conflict of interest.
Publisher’s Note
All claims expressed in this article are solely those of the authors and do not necessarily represent those of their affiliated organizations, or those of the publisher, the editors and the reviewers. Any product that may be evaluated in this article, or claim that may be made by its manufacturer, is not guaranteed or endorsed by the publisher.
Supplementary Material
The Supplementary Material for this article can be found online at: https://www.frontiersin.org/articles/10.3389/fceng.2021.742447/full#supplementary-material
References
Bannock, J. H., Phillips, T. W., Nightingale, A. M., and deMello, J. C. (2013). Microscale Separation of Immiscible Liquids Using a Porous Capillary. Anal. Methods 5, 4991–4998. doi:10.1039/C3AY41251B
Chen, W.-H., Tu, F., Bradley, L. C., and Lee, D. (2017). Shape-Tunable Synthesis of Sub-micrometer Lens-Shaped Particles via Seeded Emulsion Polymerization. Chem. Mater. 29, 2685–2688. doi:10.1021/acs.chemmater.7b00494
Cho, I., and Lee, K.-W. (1985). Morphology of Latex Particles Formed by Poly(methyl Methacrylate)-Seeded Emulsion Polymerization of Styrene. J. Appl. Polym. Sci. 30, 1903–1926. doi:10.1002/app.1985.070300510
Elvira, K. S., i Solvas, X. C., Wootton, R. C. R., and deMello, A. J. (2013). The Past, Present and Potential for Microfluidic Reactor Technology in Chemical Synthesis. Nat. Chem. 5, 905–915. doi:10.1038/nchem.1753
Guo, T. Y., Tang, G. L., Hao, G. J., Song, M. D., and Zhang, B. H. (2003). Toughening Modification of PS withn-BA/MMA/styrene Core-Shell Structured Copolymer from Emulsifier-Free Emulsion Polymerization. J. Appl. Polym. Sci. 90, 1290–1297. doi:10.1002/app.12752
Hornung, C. H., Guerrero-Sanchez, C., Brasholz, M., Saubern, S., Chiefari, J., Moad, G., et al. (2011). Controlled RAFT Polymerization in a Continuous Flow Microreactor. Org. Process. Res. Dev. 15, 593–601. doi:10.1021/op1003314
Iwasaki, T., and Yoshida, J.-I. (2005). Free Radical Polymerization in Microreactors. Significant Improvement in Molecular Weight Distribution Control. Macromolecules 38, 1159–1163. doi:10.1021/ma048369m
Iwasaki, T., Kawano, N., and Yoshida, J.-i. (2006). Radical Polymerization Using Microflow System: Numbering-Up of Microreactors and Continuous Operation. Org. Process. Res. Dev. 10, 1126–1131. doi:10.1021/op060127u
Jiang, S., Van Dyk, A., Maurice, A., Bohling, J., Fasano, D., and Brownell, S. (2017). Design Colloidal Particle Morphology and Self-Assembly for Coating Applications. Chem. Soc. Rev. 46, 3792–3807. doi:10.1039/c6cs00807k
Kobayashi, H., Miyanaga, E., and Okubo, M. (2007). Preparation of Multihollow Polymer Particles by Seeded Emulsion Polymerization Using Seed Particles with Incorporated Nonionic Emulsifier. Langmuir 23, 8703–8708. doi:10.1021/la7010748
Kobayashi, H., Suzuki, T., Moritaka, M., Miyanaga, E., and Okubo, M. (2009). Preparation of Multihollow Polystyrene Particles by Seeded Emulsion Polymerization Using Seed Particles with Incorporated Nonionic Emulsifier: Effect of Temperature. Colloid Polym. Sci. 287, 251–257. doi:10.1007/s00396-008-1983-y
Liu, Z., Lu, Y., Yang, B., and Luo, G. (2011). Controllable Preparation of Poly(butyl Acrylate) by Suspension Polymerization in a Coaxial Capillary Microreactor. Ind. Eng. Chem. Res. 50, 11853–11862. doi:10.1021/ie201497b
Liu, X., Lu, Y., and Luo, G. (2017). Continuous Flow Synthesis of Polystyrene Nanoparticles via Emulsion Polymerization Stabilized by a Mixed Nonionic and Anionic Emulsifier. Ind. Eng. Chem. Res. 56, 9489–9495. doi:10.1021/acs.iecr.7b02352
Lobry, E., Jasinski, F., Penconi, M., Chemtob, A., Croutxé-Barghorn, C., Oliveros, E., et al. (2014). Continuous-flow Synthesis of Polymer Nanoparticles in a Microreactor via Miniemulsion Photopolymerization. RSC Adv. 4, 43756–43759. doi:10.1039/C4RA06814A
Lovell, P. A., and Schork, F. J. (2020). Fundamentals of Emulsion Polymerization. Biomacromolecules 21, 4396–4441. doi:10.1021/acs.biomac.0c00769
Lv, H., Lin, Q., Zhang, K., Yu, K., Yao, T., Zhang, X., et al. (2008). Facile Fabrication of Monodisperse Polymer Hollow Spheres. Langmuir 24, 13736–13741. doi:10.1021/la802782w
Mason, B. P., Price, K. E., Steinbacher, J. L., Bogdan, A. R., and McQuade, D. T. (2007). Greener Approaches to Organic Synthesis Using Microreactor Technology. Chem. Rev. 107, 2300–2318. doi:10.1021/cr050944c
Ning, N., Liu, W., Hu, Q., Zhang, L., Jiang, Q., Qiu, Y., et al. (2020). Impressive Epoxy Toughening by a Structure-Engineered Core/shell Polymer Nanoparticle. Compos. Sci. Technol. 199, 108364. doi:10.1016/j.compscitech.2020.108364
Parida, D., Serra, C. A., Garg, D. K., Hoarau, Y., Muller, R., and Bouquey, M. (2014). Flow Inversion: An Effective Means to Scale-Up Controlled Radical Polymerization Tubular Microreactors. Macromol. React. Eng. 8, 597–603. doi:10.1002/mren.201400002
Perro, A., Reculusa, S., Bourgeat-Lami, E., Duguet, E., and Ravaine, S. (2006). Synthesis of Hybrid Colloidal Particles: From Snowman-like to Raspberry-like Morphologies. Colloids Surf. A: Physicochem. Eng. Aspects 284-285, 78–83. doi:10.1016/j.colsurfa.2005.11.073
Schwalbe, T., Autze, V., and Wille, G. (2002). Chemical Synthesis in Microreactors. chimia (aarau) 56, 636–646. doi:10.2533/000942902777679984
Seike, Y., Kamio, E., Ono, T., and Yoshizawa, H. (2007). Extraction of Ethyl Ester of Polyunsaturated Fatty Acids by Utilizing Slug Flow Prepared by Microreactor. J. Chem. Eng. Jpn. 40, 1076–1084. doi:10.1252/jcej.07WE144
Sen, N., Shaikh, T., Singh, K. K., Sirsam, R., and Shenoy, K. T. (2020). Synthesis of Polyacrylamide (PAM) Beads in Microreactors. Chem. Eng. Process. - Process Intensif. 157, 108105. doi:10.1016/j.cep.2020.108105
Song, Y., Song, J., Shang, M., Xu, W., Liu, S., Wang, B., et al. (2018). Hydrodynamics and Mass Transfer Performance during the Chemical Oxidative Polymerization of Aniline in Microreactors. Chem. Eng. J. 353, 769–780. doi:10.1016/j.cej.2018.07.166
Song, J., Zhang, S., Wang, K., and Wang, Y. (2019). Synthesis of Million Molecular Weight Polyacrylamide with Droplet Flow Microreactors. J. Taiwan Inst. Chem. Eng. 98, 78–84. doi:10.1016/j.jtice.2018.05.008
Tang, C., Zhang, C., Liu, J., Qu, X., Li, J., and Yang, Z. (2010). Large Scale Synthesis of Janus Submicrometer Sized Colloids by Seeded Emulsion Polymerization. Macromolecules 43, 5114–5120. doi:10.1021/ma100437t
Tanimu, A., Jaenicke, S., and Alhooshani, K. (2017). Heterogeneous Catalysis in Continuous Flow Microreactors: A Review of Methods and Applications. Chem. Eng. J. 327, 792–821. doi:10.1016/j.cej.2017.06.161
Tolue, S., Moghbeli, M. R., and Ghafelebashi, S. M. (2009). Preparation of ASA (Acrylonitrile-styrene-acrylate) Structural Latexes via Seeded Emulsion Polymerization. Eur. Polym. J. 45, 714–720. doi:10.1016/j.eurpolymj.2008.12.014
Tonhauser, C., Natalello, A., Löwe, H., and Frey, H. (2012). Microflow Technology in Polymer Synthesis. Macromolecules 45, 9551–9570. doi:10.1021/ma301671x
Vatankhah, Z., Dehghani, E., Salami-Kalajahi, M., and Roghani-Mamaqani, H. (2020). Seed's Morphology-Induced Core-Shell Composite Particles by Seeded Emulsion Polymerization for Drug Delivery. Colloids Surf. B: Biointerfaces 191, 111008. doi:10.1016/j.colsurfb.2020.111008
Wang, K., and Luo, G. (2017). Microflow Extraction: A Review of Recent Development. Chem. Eng. Sci. 169, 18–33. doi:10.1016/j.ces.2016.10.025
Watanabe, T., Karita, K., Tawara, K., Soga, T., and Ono, T. (2019). Rapid Synthesis of Poly(methyl Methacrylate) Particles with High Molecular Weight by Soap‐Free Emulsion Polymerization Using Water‐in‐Oil Slug Flow. Macromol. Chem. Phys. 220, 1900021. doi:10.1002/macp.201900021
Watanabe, T., Karita, K., and Ono, T. (2020a). Flow Synthesis of Monodisperse Micron-Sized Polymer Particles by Heterogeneous Polymerization Using a Water-In-Oil Slug Flow with a Non-ionic Surfactant. Colloid Polym. Sci. 298, 1273–1281. doi:10.1007/s00396-020-04705-5
Watanabe, T., Nishizawa, Y., Minato, H., Song, C., Murata, K., and Suzuki, D. (2020b). Hydrophobic Monomers Recognize Microenvironments in Hydrogel Microspheres during Free‐Radical‐Seeded Emulsion Polymerization. Angew. Chem. 132, 8934–8938. doi:10.1002/ange.202003493
Xiang, L., Song, Y., Qiu, M., and Su, Y. (2019). Synthesis of Branched Poly(butyl Acrylate) Using the Strathclyde Method in Continuous-Flow Microreactors. Ind. Eng. Chem. Res. 58, 21312–21322. doi:10.1021/acs.iecr.9b03906
Yadav, A. K., Barandiaran, M. J., and De la Cal, J. C. (2014). Effect of the Polymerization Technique and Reactor Type on the Poly(n -butyl Acrylate) Microstructure. Macromol. React. Eng. 8, 467–475. doi:10.1002/mren.201300159
Yoshida, J.-I. (2010). Flash Chemistry: Flow Microreactor Synthesis Based on High-Resolution Reaction Time Control. Chem. Rec. 10, 332–341. doi:10.1002/tcr.201000020
Keywords: emulsion polymerization, seed, composite particles, polymer particles, internal circulation, microreacter, slug flow
Citation: Watanabe T, Karita K, Manabe M and Ono T (2021) Preparation of Monodisperse Poly(Methyl Methacrylate)/Polystyrene Composite Particles by Seeded Emulsion Polymerization Using a Sequential Flow Process. Front. Chem. Eng. 3:742447. doi: 10.3389/fceng.2021.742447
Received: 16 July 2021; Accepted: 19 October 2021;
Published: 02 November 2021.
Edited by:
Yi Cheng, Tsinghua University, ChinaReviewed by:
Shirish Sonawane, National Institute of Technology Warangal, IndiaJun Yue, University of Groningen, Netherlands
Copyright © 2021 Watanabe, Karita, Manabe and Ono. This is an open-access article distributed under the terms of the Creative Commons Attribution License (CC BY). The use, distribution or reproduction in other forums is permitted, provided the original author(s) and the copyright owner(s) are credited and that the original publication in this journal is cited, in accordance with accepted academic practice. No use, distribution or reproduction is permitted which does not comply with these terms.
*Correspondence: Tsutomu Ono, dG9ub0Bva2F5YW1hLXUuYWMuanA=