- School of Engineering, Newcastle University, Newcastle upon Tyne, United Kingdom
Free-radical polymerization of styrene conducted in a spinning disc reactor (SDR) results in significant increases in conversion in one disc pass, equivalent to a few seconds of residence time, with little change in the number average and weight average molecular weights and polydispersity compared to a SDR feed pre-polymerized in a batch reactor. Results of our experimental studies are presented in this paper and a rationale, based on simulation studies, is offered to explain these observations. It is shown that phenomena such as large increases in conversion that do not impact on molecular weights and molecular weight distribution is a result of a simultaneous increase in both the initiator decomposition rate and the propagation rate. The increases in these rate constants, predicted by our modeling studies, provide the driving forces that characterize a polymerization process in a SDR reactor, with the centrifugal force having different degrees of influence on individual reaction steps. This is attributed to different molecular sizes being involved in each of the polymerization reaction steps. The highest impact is observed on the initiator decomposition rate constant, as this reaction step involves a small molecule. Lesser impact is observed on the propagation rate constant, as this reaction step involves interaction of one small molecule and one large reactive species, whilst no or very small effect is seen in the case of the termination rate constant as large reactive species are involved. Developed constant variance model was used to estimate reaction parameters at different temperatures (i.e., initiator efficiency f, rate constants kd, kp, and kt) from the acquired experimental data in order to estimate activation energy (Ea) and pre-exponential factor (A) in a SDR. Data analysis at various SDR operating temperatures suggested activation energy for the styrene polymerization in the SDR as 40.59 ± 1.11 kJ mol−1.
Introduction
Polymerization of styrene and many other commercial monomers such as acrylics and vinyls is usually carried out on a commercial scale by free-radical polymerization technique (Odian, 1991; Su, 2013). Increasing market competitiveness has led to a drive to develop innovative polymer processes which would not only improve product quality and reduce manufacturing time, but be more responsive to market needs, more energy efficient and operate under safe conditions. Furthermore, there is also a tendency to move away from traditional batch processes to continuous processes capable of achieving higher heat and mass transfer rates by orders of magnitude than the conventional batch reactors (Reay et al., 2008; Boodhoo and Harvey, 2013a). These reactors are able to provide appropriate mixing environment for improving product quality, reducing reaction times and enhancing selectivity (Boodhoo and Harvey, 2013b). It is well-documented that a reactor's mixing characteristics affect conversion of monomer as well as molecular weight distribution (Kolhapure et al., 2005), but thorough understanding of underlying interaction between mixing and polymerization is still the subject of numerous studies (Xu et al., 2017), both experimental (Erdogan et al., 2002) and numerical (Inglès et al., 2013; Xie et al., 2016).
One example of reactors suitable for polymerization reactions is a thin film spinning disc reactor (SDR) developed and extensively studied at Newcastle University over the years (Jachuck and Ramshaw, 1994). Centrifugal forces, created by disc rotation, produce thin (50–300 μm), highly sheared films which exhibit significant enhancements in the heat and mass transfer rates (Lim, 1980; Aoune and Ramshaw, 1999). Numerous surface waves in the thin film provide an ideal environment for a high degree of mixing, altogether making this type of reactor suitable for performing fast, exothermic and mass transfer limited reactions. This reactor has been shown to improve reaction rates as well as selectivity when used as a catalytic reactor (Vicevic et al., 2004, 2007) and significantly improve control and rates of polymerization reactions (Boodhoo and Jachuck, 2000a; Vicevic et al., 2006a,b). Properties of polymers heavily depend upon molecular weight distributions and polydispersity index and so it is very important to control these parameters (Whitfield et al., 2019). Previous research has shown that significant reduction in reaction times and improvement in product quality can be achieved when styrene (Boodhoo et al., 2006), dicarboxylic acid and diols (Boodhoo and Jachuck, 2000b), and acrylates (Vicevic et al., 2006a) are polymerized using the SDR technology. In spite of the extensive investigations into polymerizations in the SDR, there is currently limited understanding of the actual kinetics of the polymerization process. An earlier work attempted to provide a speculative explanation for the increased polymerization rates by considering the theory of centrifugal field effects on the extension of the polymer chains and the resulting impact on each of the polymerization steps (Boodhoo et al., 2002). In the present investigation, we aim to provide more definitive understanding of the polymerization kinetics through simulation studies validated by experiments in the SDR.
Materials and Methods
Batch Reactor Experimental Procedure (Pre-polymerization)
In order to establish a conversion-time profile for pre-polymers used as feed to the SDR, batch styrene polymerizations were performed in a 250 cm3 agitated vessel. Benzoyl peroxide (BPO) (Merck, with 25% water) was used as an initiator and was re-crystallized from ethanol prior to reaction. Styrene monomer (99%) and toluene as a solvent (99%) were obtained from Aldrich. Samples were taken and analyzed using Gel Permeation Chromatography (GPC) to assess conversion and molecular weight properties. GPC was calibrated using Poly(Styrene) standards obtained from Polymer Laboratories. Conversion was obtained using LC-GC software which was calibrated by samples of known monomer/polymer concentrations. Viscosity and shear rate data were experimentally obtained by a cone and plate Bohlin Visco 88 BV Viscometer.
The batch reaction was carried out at chosen temperature (75–90°C), using ranges of monomer [M] (50–83%w/w) and initiator concentrations [I] (0.8–1.75%w/w), until the desired conversion was achieved. The pre-polymer so formed was used immediately as a feed for the SDR studies.
Spinning Disc Reactor Experimental Procedure
Pre-polymerized feed containing monomer, polymer and initiator, prepared in a batch reactor (as described above) until desired initial conversion was reached, was transferred on the center of a 300 mm diameter SDR (as schematically shown in Figure 1) by means of a gear pump. The top surface of the disc was made of brass and had grooves machined into it (Jachuck and Ramshaw, 1994). The disc was equipped with heating and cooling facilities. Once the feed is introduced to the center of the disc, centrifugal forces created by disc rotation force the liquid to flow over the disc surface in the form of very thin film. On reaching the edge of the disc, the liquid is thrown off the surface and hits the cold walls of the stationary housing before being collected for analysis.
The experiments were designed in order to assess kinetic parameters. The experimental variables were: the disc temperature (75–90°C), disc rotational speed (500–1,500 rpm), feed flow rate (4–9 cm3s−1), and pre-polymer feed conversion (10–54%). The conversion and molecular weight properties (Mn, Mw, and polydispersity index, PDI) were obtained by GPC.
Results and Discussion
Starting from different pre-polymer conversions achieved in a batch reactor, increases in conversion gained upon transfer to the SDR are given in Figure 2. It is immediately noticeable that when a higher conversion pre-polymer was used (i.e., 54%), single SDR pass increased conversion much more than when a lower conversion feed was utilized (i.e., 10%). Observed increases in conversion in a SDR were in the range 2–11%, depending upon the experimental conditions.
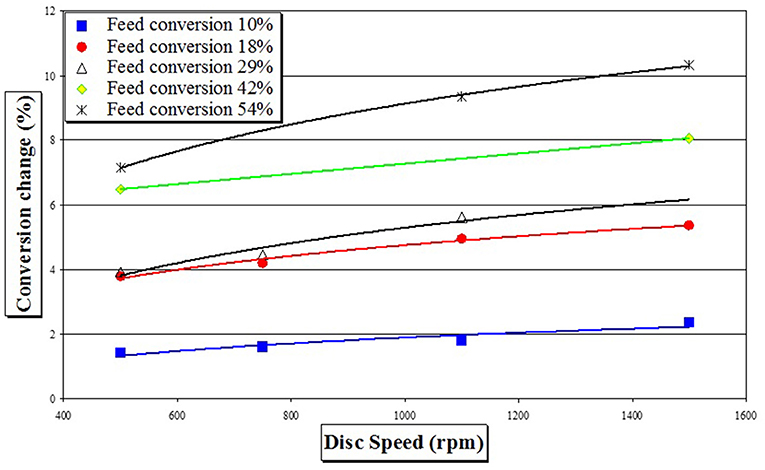
Figure 2. Increase in monomer conversion as a function of feed pre-polymerisation conversion and disk rotational speed (change in conversion of styrene is a measure for a single SDR pass at temperature of 90°C and feed flow rate of 6 cm3 s−1).
Figure 3 depicts these results in comparison to a batch process carried out at the same temperature (90°C). Batch data points are approximated by a smooth line as a guide for the eye and do not represent actual data. Smoothed line is applied to other Figures for the same reason (2–4, 6–8), however data points are also offered.
Looking at the set of data obtained for a single rotational speed and a single feed flow (e.g., 1,500 rpm, Figure 4) it is apparent that the gel effect observed in the later stages of the batch process, characterized by the S-shaped curve after 120 min of polymerization time, is largely suppressed in a SDR, as already speculated by Boodhoo et al. (2002). Same Figure 4 demonstrates time savings of up to 50 min (depending on pre-polymerized feed conversion) gained by a single pass on a SDR and evaluates utilization of nine passes on a SDR, whereby a time saving of 2 hours appears achievable. A multi-pass SDR study conducted by Moghbeli et al. (2009) showed that considerable increases in conversion were indeed observed, but molecular weights and PDI slightly decreased, most probably due to chain scission of the long polymer chains subjected to the high shear forces.
As previously mentioned, on the surface of the SDR thin, highly sheared films are formed, which are associated with high mixing intensities, high shear rates as well as plug flow characteristics. Boodhoo et al. (2002) suspected that the shear forces may initially lead to disentanglement of pre-polymer chains, hence causing a reduction in the viscosity of the polymer mix by shear thinning, more pronounced at higher polymer concentrations and molecular weights. Growing polymers are expected to experience a certain degree of extension as the polymerizing film travels radially outward on the spinning disc under the influence of the centrifugal force whilst monomer molecules would find enhanced access to the active, propagating polymer chains (Boodhoo et al., 2002). Lowering of viscosity by shear thinning, as demonstrated in Figure 5, supports this theory, further shedding light on excellent mixing characteristics within the thin film relevant to maintaining high initiator efficiency, even at high monomer conversions.
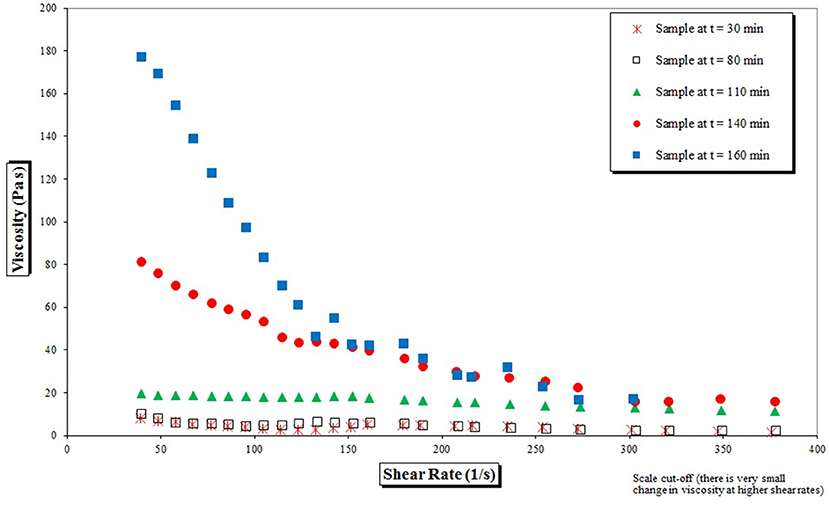
Figure 5. Viscosity changes with the increase of shear rate for the batch reaction samples taken at every 10 min until t = 160 min.
The shear thinning theory put forward by Boodhoo et al. (2002) seems even more plausible when the applied shear rate effects on polymer viscosity are considered, as illustrated in Figure 6 for batch reaction samples taken every 10 min.
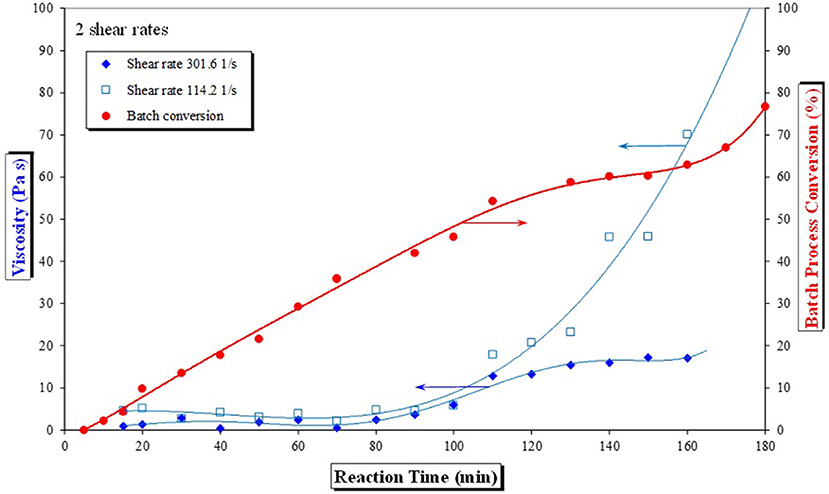
Figure 6. Batch reaction profile and sample viscosities at shear rates of 114.2 and 301.6 s−1 (initial conditions T = 90°C, 83% wt/wt monomer, 1.4% wt/wt BPO).
Looking at the influence of two specific shear rates (114.2 and 301.6 s−1) on material viscosity at certain reaction times, as shown in Figure 6, it can be seen that at such shear rates, viscosity of the material does not change significantly until conversion reaches about 40% (at reaction time of ~80–100 min). At that point viscosity of the reaction mixture starts to increase dramatically and mixing plays very important role in the degree of polymerization (as in any other mass transfer limited reaction). The higher the shear rate, the material becomes easier to handle, i.e., the shear thinning effect is more evident. This clearly demonstrates that increasing shear has a large influence on the measured polymer viscosity, more so for more viscous samples.
In addition, shear rates in a stirred tank are typically very non-uniform, whereby at the tip of the impeller very high shear rates may be obtained whilst away from the impeller shear rate may be very low. In the thin SDR film, in contrast, the shear rate will be more uniform due to the thin film being formed (Vicevic et al., 2007) and this is the reason why the SDR performance exceeds that of a batch reactor particularly when a higher viscosity material is used due to a strong mixing action within the polymer film.
Residence Time and Shear Rate in the SDR
Two important variables that govern progress of any reaction in a SDR are disc residence time and shear rate. Residence time on a smooth horizontal rotating disc surface can be estimated from the centrifugal model using the following equation (Dobie et al., 2013):
The effect of residence time, as calculated by the above equation, on experimentally measured styrene conversion in the SDR for different pre-polymer feeds can be seen in Figure 7.
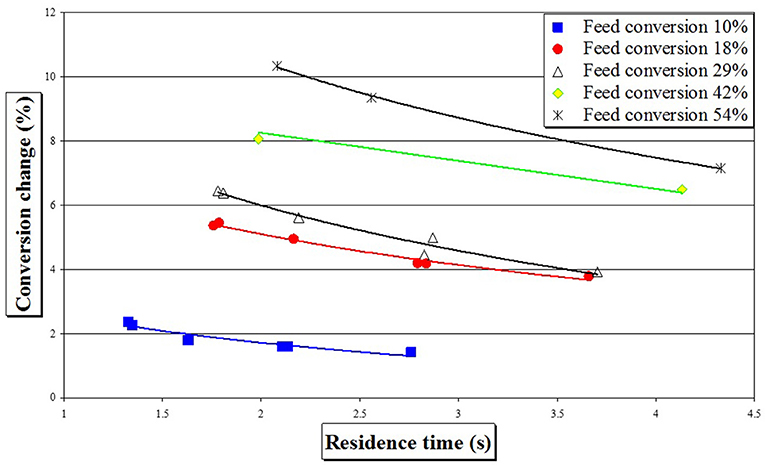
Figure 7. Conversion change with residence time for free-radical styrene polymerization after one SDR pass at 90°C and feed flow rate of 6 cm3 s−1.
It can be noted that an increase in residence time does not result in an increase in conversion, as would be expected in kinetically controlled reactions. Rather, the opposite effect is evident from Figure 7 for the range of feed conversions studied (10–54%) whereby higher conversion changes are achieved at lower residence times. This suggests that the polymerization in the SDR is not kinetically controlled and change in conversion in the SDR is influenced by another parameter, other than the residence time, namely shear rate which is discussed below.
Considering the SDR operating conditions which give rise to lower residence time it can be seen that, at constant flow rate, higher rotational speed of the disc is required whereby high centrifugal forces are generated, causing very thin, highly sheared and therefore highly mixed films to flow on the disc surface. Shear rates within the film may be estimated according to the following equation (Leneweit et al., 2000; Vicevic et al., 2007):
By plotting conversion change in one SDR pass as a function of shear rate (Figure 8), it is evident that styrene polymerization in the SDR is a shear rate dependent reaction, as would be expected for a mass transfer limited reaction. The effect of shear rate on the rate of styrene polymerization may be further assessed by developing an empirical model using all the acquired experimental data.
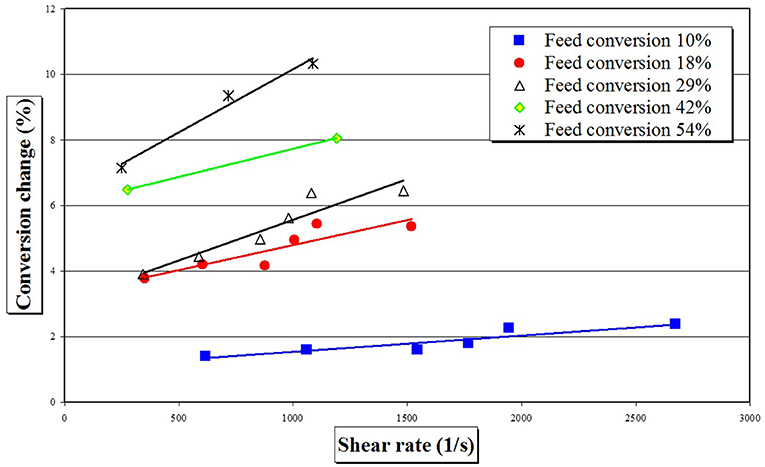
Figure 8. Conversion dependency upon shear rate for free-radical styrene polymerisation after one pass in the SDR for different pre-polymer feeds at temperature of 90°C and feed flow rate of 6 cm3 s−1.
Empirical Model (Shear Rate Model)
Using the regression analysis tool in Microsoft Excel, overall polymerization rate (Rpol) in the SDR can be presented in terms of shear rate, reaction temperature, monomer and initiator concentrations. Following model equation can be drawn within the limited experimental conditions as stated previously in the experimental procedures section:
Validation of the model equation was performed by comparing the obtained experimental values of polymerization rate (monomer uptake rate) and values obtained by Equation (3), as shown in Figure 9, which demonstrates that empirical model is in good agreement with experimental data. Statistical analysis was conducted in Minitab.

Figure 9. Confidence interval (CI) and prediction interval (PI) for linear regression of experimental and model polymerization rate data (all rate units in mol dm−3 s−1).
From the empirically calculated values it can be seen that styrene polymerization in the SDR follows first order kinetics with respect to styrene concentration and 0.52 order in respect to initiator concentration, as typically expected for this reaction (Odian, 1991). Polymerization in the SDR is not highly influenced by temperature and the reasons for this will be elaborated in section Modeling Results. The empirical equation confirms the already stated view that the reaction is substantially dependent on the shear rate used.
Modeling Results
Spinning Disc Reactor (SDR): Background
It has been reported that polymerization of styrene with benzoyl peroxide (BPO) as an initiator and in the presence of small quantities of toluene as a solvent in a spinning disc reactor results in significant increase in conversion, while number average (Mn) and weight average molecular weight (Mw) stay approximately unchanged (Boodhoo, 1999; Boodhoo and Jachuck, 2000a). There has been interest in explaining these results in terms of the underlying mechanistic behavior (Boodhoo et al., 2002). It has been indicated that the overall termination rate constant may be decreasing during the spinning disc polymerization stage. Furthermore, an increase in the polymerization rate in the SDR that does not impact on the molecular weights or polydispersity is believed to be a consequence of the gel effect being suppressed in the SDR (Boodhoo et al., 2002) which is what we have observed as well. Leveson et al. (2003) performed numerical investigations into the kinetics of a free-radical polymerization in a SDR. It was shown that if conventional systems operate with an increased propagation rate constant or reduced termination rate constant, significant increases in conversion could be achieved. It was also suggested that increases in molecular weights are controlled by chain transfer to initiator. However, we believe that phenomenon of high conversion increase whilst maintaining molecular weights/polydispersity is due to simultaneous increase in both initiator decomposition rate and propagation rate. The reasoning behind this view will be explained further in the remaining sections.
Proposed Model
Experimentally observed trends recorded in the SDR polymerization of styrene with BPO as an initiator are mathematically analyzed using previously reported methods (Novakovic et al., 2004). For the majority of experimental data, results of mathematical analysis indicate that in the studied polymerization process in a SDR number of smaller polymer chains is increasing. At the same time conversion is increasing significantly, i.e., number of monomer molecules consumed on the disc surface is high, much higher than the number of monomer molecules consumed in the batch reactor under the same conditions. There are two steps in the polymerization process in which monomer molecules are consumed, namely the initiation step (Equation 4) and propagation step (Equation 5):
Monomers can also be consumed by transfer to another monomer:
Therefore, the rate of monomer disappearance, which is synonymous with the rate of polymerization, can be presented as:
The number of monomer molecules reacting in the initiation step and the transfer to monomer step is by far smaller than the number of molecules in the propagation step (Odian, 1991), resulting in the monomer disappearance rate being defined by the rate of propagation:
As can be seen from Equation (8), the rate of propagation can be increased by increasing propagation rate constant kp, concentration of growing radicals [M·], or monomer concentration [M]. By considering experimental data with the same initial conditions applied to all experimental runs without any external changes during the course of reaction (constant monomer concentration), the effect of the former two variables, that is, increases in the free-radical concentration (Case study 1, section Case Study 1: Increase of Free Radicals Concentration) and in the propagation rate constant (Case study 2, section Case Study 2: Effect of Changes in Propagation Rate Constant) can be analyzed.
In order to visualize the free-radical polymerization in the SDR, a detailed polymerization model that will be used for process simulation is proposed.
The rate of decomposition of initiator in batch model (Odian, 1991) is:
Another reaction where initiator can be consumed is transfer to initiator:
So that the rate of initiator decomposition then becomes:
The rate of monomer disappearance is given as the sum of the rates of propagation and transfer to monomer:
In addition, since the propagation rate constant for all the polymerization steps are the same (Odian, 1991), the rate of propagation is defined by Equation (8), whilst the rate of transfer to monomer can be presented as:
Therefore, Equation (12) can be written as:
As reaction time in a SDR is very short (1–5 s), steady state assumption cannot be applied. Free radicals are produced in the initiation step (by initiator decomposition) and consumed in the termination step. Hence the concentration of the free radicals in time can be followed as:
If transfer to solvent is also considered, then the following is applicable to the polymerization system:
The kinetic chain length can then be calculated according to the following equation:
Thus, the rate of production of macromolecules can be presented as:
It is not known which termination mechanism (coupling or disproportion) is taking place in the SDR environment, but a very interesting study by Mohammadi et al. (2014) suggests that termination by coupling is a dominating termination mechanism in the SDR. Given that only one termination rate constant was available from the literature, it is assumed that the main mechanism of termination is by coupling (Odian, 1991). The calculated termination rate constant is therefore assumed to be equal to the termination rate constant by coupling:
where The extent (conversion) of the reaction is then calculated as:
Moments (first and second order) are presented in Equations (21) and (22) below (Villermaux and Blavier, 1984a,b). In the case of transfer to monomer, solvent and initiator:
Overall rate of moment growth in the polymerization mixture can then be presented as:
It was shown (Villermaux and Blavier, 1984a,b) that following approximation can be applied:
With the overall rate of moment growth in the polymerization mixture being given by:
The number average molecular weight is calculated as:
and the weight average molecular weight as:
Polydispersity is then calculated as:
For a comparison, we used rate constants estimated for a batch process (Vicevic et al., 2006b) (used here as a feed to SDR). In a batch process modeling study the expressions for the kinetic rate constants and the value for initiator efficiency, f, that are appropriate for styrene polymerization with BPO as an initiator have been taken from literature (Biesenberger and Sebastian, 1983; Berger and Meyerhoff, 1989; Buback, 1995; Moad and Solomon, 1995).
The values for kd, kp, and kt were calculated according to the temperature that were to be used in the batch reactor. In the modeling of the SDR these values were taken as the initial values, as the SDR temperature was kept the same as in the batch reactor. For the case analysis in the next section, the temperature is set at 90°C, and initial rate constants are taken as (Novakovic, 2004):
It appears that the centrifugal force produced on the rotating disc surface causes an increase in rate constants. Following that hypothesis, it seems rational to expect higher impact on reactions involving smaller molecules, i.e., highest increase might be expected on initiator decomposition rate constant as this reaction involves small molecules (BPO molecules), significant but smaller increases might be expected in propagation rate constant as this reaction involves one small molecule (monomer, styrene) and one big molecule (growing chain species) and very small or no impact at all might be expected to be seen in the termination rate constant as termination involves reacting two large molecules (growing chain species). This rationale will be explored in detail in further sections (Case Study 1: Increase of Free Radicals Concentration to Case Study 4: Effect of Simultaneous Increase in Propagation Rate Constant and Initiator Decomposition Rate Constant in the Presence of Initiator Efficiency Increase) by using the proposed model in gPROMS and examining how the changes in kinetic parameters would influence polymerization reaction. The model was used to estimate rate constants for all the polymerization steps using previously presented data. Selected results are shown in this article. Using the available data for different reactor temperatures, obtained rate constants results were used to calculate activation energy for each step of the reaction.
Case Study 1: Increase of Free Radicals Concentration
To obtain higher concentration of the free radicals in the system, the rate of initiator decomposition has to be increased. The rate of production of the free radicals via initiator decomposition can be presented as:
Or in terms of rate expression:
From Equation (32) can be seen that increase in initiator decomposition rate occurs if either of these parameters is increased: initiator efficiency f, decomposition rate constant kd (section case study 1a: Effect of changes in initiator decomposition rate constant below), or initiator concentration [I]. Again, by keeping the initiator concentration constant, the possibilities for increases in decomposition rate of initiator are limited to increasing initiator efficiency or/and decomposition rate constant. Increase in initiator efficiency f is limited by maximum value of one, which refers to having all radicals that are formed in decomposition step available for starting polymer chains.
Case Study 1a: Effect of Changes in Initiator Decomposition Rate Constant
Initiator decomposition rate constant is believed to be changing, more specifically increasing, in the free-radical polymerization process in the SDR. Effect of increase in decomposition rate constant value was simulated using the proposed model and run in gPROMS simulation. Numerical results of the simulation for the residence time 5 s are presented in Table 1. It can be seen that increase in initiator decomposition rate constant results in the decrease in molecular weights but increase in polydispersity and conversion.
Case Study 2: Effect of Changes in Propagation Rate Constant
Propagation rate constant is believed to be increased in the free-radical polymerization process in the SDR. Effect of changes in propagation rate value was simulated in the proposed model and run in gPROMS. Numerical results of the simulation for the residence time 5 s, which is approximately time of one run on the SDR, are presented in Table 2.
From Table 2 it can be seen that the large increase in conversion is gained by increasing propagation rate constant by over fifty times. It can also be observed that, as a consequence, molecular weights are also greatly increased and their distribution is significantly broadened.
Case Study 3: Effect of Simultaneous Changes in Propagation Rate Constant and Initiator Decomposition Rate Constant At Constant Initiator Efficiency
Simultaneous changes in the propagation rate constant and the initiator decomposition rate constant will be made in this analysis. Overall increase in conversion of 10% in 5 s for the case of free-radical polymerization of styrene with benzoyl peroxide as initiator and in the presence of toluene as a solvent, at 90°C will be taken as the reference point.
Polymerization processes, in the batch reactor and in the SDR, starting from the time zero are compared. Rate constants in the case of polymerization in the SDR are fitted to obey trends observed in experimental data. The criteria to be fulfilled include:
1. Number average molecular weight of the SDR product to be similar with number average molecular weight of the simulated polymerization process in a batch;
2. Weight average molecular weight of the SDR product to be similar with weight average molecular weight of the simulated polymerization process in a batch;
3. Increase in conversion on SDR to be 10% in 5 s.
To satisfy the listed conditions, initiator decomposition rate constant should be increased 225.5 times whilst propagation rate constant should be increased 8.5 times . Using the available data, actual values for number and weight average molecular weight of SDR feed and product were used to fit the corresponding rate constants. Experimentally determined number average molecular weights of the SDR feed and product were mainly between 18,000 and 20,000 g mol−1, while weight average molecular weights were mainly between 28,000 and 31,000 g mol−1.
Case Study 4: Effect of Simultaneous Increase in Propagation Rate Constant and Initiator Decomposition Rate Constant in the Presence of Initiator Efficiency Increase
Initial values of parameters used are as in the previous examples. Here, it is assumed that initiator efficiency in the process on SDR is reaching maximum value, i.e., fmax = 1. Initiator decomposition and propagation rate constants are fitted to satisfy results gained experimentally, as previously described.
New parameters estimated by gPROMS simulation which satisfy experimental data are: , and .
Termination Rate Constant
Decrease in termination rate constant would indeed lead to increase in monomer conversion while increasing molecular weights significantly, as suggested by some authors (Boodhoo et al., 2002; Leveson et al., 2003). However, if transfer to initiator (or any other species in the system i.e., monomer, solvent, and polymer) is present, molecular weights would be decreased and by that these two effects (i.e., decrease in termination rate constant and increase in transfer to available species) would be theoretically possible to fit and create impression of high increase in conversion without changing molecular weights. Previous modeling study of the free-radical polymerization of styrene in a batch reactor showed that this was not the case (Novakovic et al., 2003b).
Therefore, having molecular weights at all times between predicted limits in the case of termination only by coupling and termination only by disproportion, i.e., with no obvious transfer influencing polymerization in a batch reactor, it would be highly unlikely that extremely high transfer occurs in a spinning disc reactor.
By entering experimental values for conversion, residence time, viscosity, and molecular weights in the proposed model (in gPROMS), software was able to estimate rate constants values independently that gave best agreement with the experimental data. It is interesting to note that, in all of the simulations performed, virtually no change was observed in the estimated values of termination rate constant, kt. Some of these results can be seen in the following sections (Influence of Change in Disc Rotational Speed on Change in Rate Constant and Activation Energy).
Influence of Change in Disc Rotational Speed on Change in Rate Constant
Experimental data available for the same initial conditions suggested that there is a small trend of increase of conversion with increasing disc rotational speed, as was observed earlier in Figure 2. This trend can be explained by having rate constants as a function of disc rotational speed. Using the experimental data obtained at feed flow rate of 6 cm3 s−1, disc temperature of 90°C, pre-polymerization conversion of 10%, monomer and initiator concentrations 83 and 1.4%w/w, respectively, it is possible to evaluate rate constants using the developed modeling method. Results are presented in Table 3. These simulation studies predict simultaneous increases in rate constants kd and kp as the disc spins at a higher rate, whilst there was no change in the value of kt (compared neither to pre-polymerized SDR feed nor as a function of rotational speed).
Activation Energy
The developed model was also used to estimate rate constants kd, kp, and kt at different reaction temperatures in order to evaluate activation energies for each polymerization step in a SDR. Modeling results are presented in Table 4.
Activation energies in the SDR determined using the data obtained by the gPROMS simulation, as seen in Table 4, were estimated as: ; which are smaller than corresponding batch values. There was no change in Eat values as compared to a batch reactor (). Overall activation energy was therefore calculated as 40.59± 1.11 kJ mol−1. Available literature suggest that this value is 94.6 kJ mol−1 (Odian, 1991). The experimental overall activation energy (Odian, 1991) for the batch reaction performed as part of our investigations (Vicevic et al., 2006b) was estimated as 90 kJ mol−1, which shows good agreement with the value reported in the literature. Low activation energy in a SDR indicates that influence of temperature on polymerization reaction is less significant than in conventional equipment (i.e., batch reactor). This further reinforces our findings given by empirical model equation (Equation 3) that showed negligible effect that temperature had on the styrene polymerization in a SDR.
Based on values given in Table 4, the Arrhenius equations for each of the rate constants in the SDR (temperature interval 75–90°C) may be expressed as follows:
Conclusions
Significant increases in conversion while molecular weights and by that polydispersity remain almost unchanged during course of polymerization in SDR is explained by increase in propagation and initiator decomposition rate simultaneously. Our studies have shown that explanations offered in earlier work (Boodhoo et al., 2002; Leveson et al., 2003) are not feasible. Mathematical analysis of the formation of molecule sizes on the spinning disc reactor showed that for majority of experimental data available results of mathematical analysis indicate that in the SDR polymerization process there is an increase in the number of smaller polymer chains formed on the disc (Novakovic et al., 2003a). The significant increase in conversions in very short residence times (of up to 5 s) indicate a rapid increase in monomer consumption. A detailed simulation model is proposed and steps in polymerization process in which monomer molecules are consumed are analyzed. It was shown that there are three possible explanations to satisfy the experimentally observed trends in conversion. All reactions considered feasible for the system analyzed were included in the gPROMS simulation (i.e., transfer to monomer, initiator, and solvent). Steady state assumption was not applied because of the very short residence times experienced by the polymerizing system in the SDR.
Batch process with no changes in initial rate constants was simulated under initial conditions applied on SDR and, according to molecular weights obtained in our experiments, rate constants in SDR simulation were fitted to maintain close values of molecular weights to those achieved in a batch and at the same time to produce high conversion. It was seen that it is possible to achieve desired increase in conversion in required time and to maintain initial molecular weights by simultaneously increasing propagation rate constant and initiator decomposition rate constant while initiator efficiency is kept constant at 0.8.
Results presented here suggest that centrifugal forces produced on rotating disc surface influence increase in rate constants. As expected, highest impact is observed for reactions involving smaller molecules. Highest increase is present in initiator decomposition rate constant (~200 times) as this reaction involve decomposition of small molecule (benzoyl peroxide), smaller increase exists in propagation rate constant (up to 10 times) as this reaction involves interaction of one small molecule (monomer, styrene) and one big molecule (growing polymer chain) and no discernible change was seen in the termination rate constant as termination reaction involves interaction of two large molecules (grown polymer chains).
Further investigated was influence of change in disc speed on rate constants. Summary analysis of selected data showed that rate constants (initiator decomposition and propagation rate constant) are increasing with increasing agitation speed.
Finally, analysis of the data at various SDR operating temperatures allowed us to estimate overall activation energy for the styrene polymerization in the SDR as 40.59± 1.11 kJ mol−1.
Data Availability Statement
The raw data supporting the conclusions of this article will be made available by the authors, without undue reservation.
Author Contributions
MV collected and analyzed the experimental data and prepared and reviewed the manuscript. KN did modeling and analysis of the data and prepared and reviewed the manuscript. KB designed the experiments, collected, prepared and analyzed the data, and reviewed the manuscript. All authors developed the concept together, contributed to the article, and approved the submitted version.
Conflict of Interest
The authors declare that the research was conducted in the absence of any commercial or financial relationships that could be construed as a potential conflict of interest.
Acknowledgments
This paper stems from a couple of past projects funded by the EPSRC, UK. The authors are grateful for their financial support over the years.
Supplementary Material
The Supplementary Material for this article can be found online at: https://www.frontiersin.org/articles/10.3389/fceng.2021.661498/full#supplementary-material
References
Aoune, A., and Ramshaw, C. (1999). Process intensification: heat and mass transfer characteristics of liquid films on rotating discs. Int. J. Heat Mass Transf. 42, 2543–2556. doi: 10.1016/S0017-9310(98)00336-6
Berger, K. C., and Meyerhoff, G. (1989). “Propagation and termination constants in free-radical polymerisation,” in Polymer Handbook, 3 Edn, eds J. Brandrupt and Immergut (New York, NY: Wiley-Intercsience), II/67–II/79.
Biesenberger, J. A., and Sebastian, D. H. (1983). Principles of Polymerization Engineering. New York, NY: John Wiley.
Boodhoo, K., and Harvey, A. (2013a). Process Intensification for Green Chemistry: Engineering Solutions for Sustainable Chemical Processing. Chichester: John Wiley & Sons Ltd. doi: 10.1002/9781118498521
Boodhoo, K., and Harvey, A. (2013b). Process Intensification Technologies for Green Chemistry: Engineering Solutions for Sustainable Chemical Processing. (Chichester: Wiley).
Boodhoo, K. V. K. (1999). Spinning Disc Reactor for Polymerisation of Styrene. (Ph.D. thesis). University of Newcastle upon Tyne, Newcastle upon Tyne. United Kingdom.
Boodhoo, K. V. K., Dunk, W. A. E., and Jachuck, R. J. (2002). Influence of centrifugal field on free-radical polymerisation kinetics. J. Appl. Polym. Sci. 85, 2283–2286. doi: 10.1002/app.10847
Boodhoo, K. V. K., Dunk, W. A. E., Vicevic, M., Jachuck, R. J., Sage, V., Macquarrie, D. J., et al. (2006). Classical cationic polymerization of styrene in a spinning disc reactor using silica-supported BF3 catalyst. J. Appl. Polym. Sci. 101, 8–19. doi: 10.1002/app.22758
Boodhoo, K. V. K., and Jachuck, R. J. (2000a). Process intensification: spinning disc reactor for styrene polymerisation. Appl. Thermal Eng. 20, 1127–1146. doi: 10.1016/S1359-4311(99)00071-X
Boodhoo, K. V. K., and Jachuck, R. J. J. (2000b). Process intensification: spinning disc reactor for condensation polymerisation. Green Chem. 2, 235–244. doi: 10.1039/b002667k
Buback, M. (1995). Critically evaluated rate coefficients for free-radical polymerisation. I propagation rate coefficient for styrene. Macromol. Chem. Phys. 196, 3267–3280. doi: 10.1002/macp.1995.021961016
Dobie, C. G., Vicevic, M., and Boodhoo, K. V. K. (2013). An evaluation of the effectiveness of continuous thin film processing in a spinning disc reactor for bulk free-radical photo-copolymerisation. Chem. Eng. Process. 71, 97–106. doi: 10.1016/j.cep.2013.03.011
Erdogan, S., Alpbaz, M., and Karagöz, A. R. (2002). The effect of operational conditions on the performance of batch polymerization reactor control. Chem. Eng. J. 86, 259–268. doi: 10.1016/S1385-8947(01)00183-8
Inglès, X., Pallares, J., Larre, M. T., Méndezb, L., and Grau, F. X. (2013). Experimental and numerical study of turbulent mixing in a model of a polymerization reactor. J. Indus. Eng. Chem. 19, 1251–1256. doi: 10.1016/j.jiec.2012.12.025
Jachuck, R. J. J., and Ramshaw, C. (1994). Process intensification - heat-transfer characteristics of tailored rotating surfaces. Heat Recov. Syst. 14, 475–491. doi: 10.1016/0890-4332(94)90051-5
Kolhapure, N. H., Fox, R. O., Dai,ß, A., and Mähling, F.-O. (2005). PDF simulations of ethylene decomposition in tubular LDPE reactors. AIChE J. 51, 585–606. doi: 10.1002/aic.10378
Leneweit, G., Fröse, D., Roesner, K. G., Koehler, R., and Scheffler, A. (2000). Shear degradation and deformation of polysaccharides in thin liquid film flow on a rotating disk. Polym. Degrad. Stabil. 70, 283–297. doi: 10.1016/S0141-3910(00)00128-2
Leveson, P., Dunk, W. A. E., and Jachuck, R. J. (2003). Numerical investigation of kinetics of free-radical polymerization on spinning disk reactor. J. Appl. Polym. Sci. 90, 693–699. doi: 10.1002/app.12762
Lim, S. T. (1980). Hydrodynamics and Mass Transfer Processes Associated with the Absorption of Oxygen in Liquid Films Flowing Across a Rotating Disc. (Ph.D. thesis). Newcastle University, United Kingdom.
Moad, G., and Solomon, D. H. (1995). Chemistry of Free-Radical Polymerisation. Oxford: Pergamon-Elsevier Science Ltd.
Moghbeli, M. R., Mohammadi, S, and Alavi, S. M. (2009). Bulk free-radical polymerization of styrene on a spinning disc reactor. J. Appl. Polym. Sci. 113, 709–715. doi: 10.1002/app.30138
Mohammadi, Y., Pakdel, A. S., Saeb, M. R., and Boodhoo, K. (2014). Monte Carlo simulation of free radical polymerization of styrene in a spinning disc reactor. Chem. Eng. J. 247, 231–240. doi: 10.1016/j.cej.2014.03.013
Novakovic, K. (2004). Data Analysis and Modelling of a Polymerisation Process on Spinning Disc Reactor. (Ph.D. thesis). University of Newcastle upon Tyne, Newcastle upon Tyne, United Kingdom.
Novakovic, K., Martin, E., and Morris, J. (2004). Mathematical analysis of the formation of molecule sizes on a spinning disc reactor. Macromol. Symp. 216, 195–208. doi: 10.1002/masy.200451219
Novakovic, K., Martin, E. B., and Morris, A. J. (2003a). “Mathematical analysis of the formation of molecule sizes on a spinning disc reactor,” in 8th Pacific Polymer Conference, (Bangkok) 90.
Novakovic, K., Martin, E. B., and Morris, A. J. (2003b). “Modelling of the free radical polymerization of styrene with benzoyl peroxide as initiator,” in European Symposium on Computer Aided Process Engineering-13, 815–820. doi: 10.1016/S1570-7946(03)80217-1
Reay, D. A., Ramshaw, C., and Harvey, A. P. (2008). Process Intensification: Engineering for Efficiency, Sustainability and Flexibility. Oxford: Butterworth-Heinemann.
Su, W. F. (2013). “Radical chain polymerization,” in Principles of Polymer Design and Synthesis eds B. Carpenter, P. Ceroni, B. Kirchner, A. Koskinen, K. Landfester, J. Leszczynski, et al. (Berlin, Heidelberg: Springer), 137–183. Available online at: https://link.springer.com/book/10.1007/978-3-642-38730-2#about. doi: 10.1007/978-3-642-38730-2_7
Vicevic, M., Boodhoo, K. V. K., and Scott, K. (2007). Catalytic isomerisation of α-pinene oxide to campholenic aldehyde using silica-supported zinc triflate catalysts. II. Performance of immobilised catalysts in a continuous spinning disc reactor. Chem. Eng. J. 133, 43–57. doi: 10.1016/j.cej.2006.12.003
Vicevic, M., Jachuck, R. J. J., Scott, K., Clark, J. H., and Wilson, K. (2004). Rearrangement of α-pinene oxide using a surface catalysed spinning disc reactor (SDR). Green Chem. 6, 533–537. doi: 10.1039/B404191G
Vicevic, M., Novakovic, K., Boodhoo, K. V. K., and Morris, A. J. (2006a). 17th International Congress of Chemical and Process Engineering, CHISA 2006. Prague, Czech Republic, 27-31 August 2006. Prague.
Vicevic, M., Novakovic, K., Boodhoo, K. V. K., and Morris, A. J. (2006b). Process Intensification and Innovation Process (PI)2 Conference II Cleaner, Sustainable, Efficient Technologies for the Future. Christchurch, New Zealand, 24-29 September 2006. Christchurch.
Villermaux, J., and Blavier, L. (1984a). Free radical polimerization engineering—I a new method for modeling free radical homogeneous polymerization reactor. Chem. Eng. Sci. 39, 87–99. doi: 10.1016/0009-2509(84)80133-5
Villermaux, J., and Blavier, L. (1984b). Free radical polymerization engineering—II modeling of homogeneous polymerization of styrene in a batch reactor, influence of initiator. Chem. Eng. Sci. 39, 101–110. doi: 10.1016/0009-2509(84)80134-7
Whitfield, R., Truong, N. P., Messmer, D., Parkatzidis, K., Rolland, M., and Anastasaki, A. (2019). Tailoring polymer dispersity and shape of molecular weight distributions: methods and applications. Chem. Sci. 10, 8724–8734. doi: 10.1039/C9SC03546J
Xie, L., Zhu, L. T., and Luo, Z.-H. (2016). Computational fluid dynamics simulation of multiscale mixing in anionic polymerization tubular reactors. Chem. Eng. Technol. 39, 857–864. doi: 10.1002/ceat.201500628
Xu, C.-Z., Wang, J.-J., Gu, X.-P., and Feng, L.-F. (2017). CFD modeling of styrene polymerization in a CSTR. Chem. Eng. Res. Design 125, 46–56. doi: 10.1016/j.cherd.2017.06.028
Nomenclature
Keywords: kinetics, styrene, poly(styrene), free-radical polymerization, spinning disc reactor, process intensification
Citation: Vicevic M, Novakovic K and Boodhoo K (2021) Free-Radical Polymerization of Styrene: Kinetic Study in a Spinning Disc Reactor (SDR). Front. Chem. Eng. 3:661498. doi: 10.3389/fceng.2021.661498
Received: 30 January 2021; Accepted: 17 March 2021;
Published: 21 April 2021.
Edited by:
Vincenzo Russo, University of Naples Federico II, ItalyReviewed by:
Johan Paul Wärnå, Åbo Akademi University, FinlandRiccardo Tesser, University of Naples Federico II, Italy
Copyright © 2021 Vicevic, Novakovic and Boodhoo. This is an open-access article distributed under the terms of the Creative Commons Attribution License (CC BY). The use, distribution or reproduction in other forums is permitted, provided the original author(s) and the copyright owner(s) are credited and that the original publication in this journal is cited, in accordance with accepted academic practice. No use, distribution or reproduction is permitted which does not comply with these terms.
*Correspondence: Marija Vicevic, bWFyaWphLnZpY2V2aWMxQG5ld2Nhc3RsZS5hYy51aw==
†These authors have contributed equally to this work and share first authorship