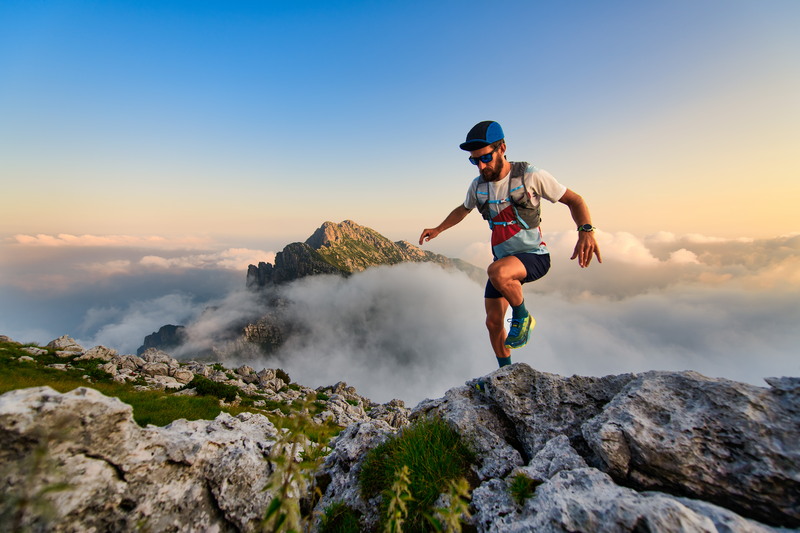
95% of researchers rate our articles as excellent or good
Learn more about the work of our research integrity team to safeguard the quality of each article we publish.
Find out more
SPECIALTY GRAND CHALLENGE article
Front. Ceram. , 14 February 2023
Sec. Ceramics Processing
Volume 1 - 2023 | https://doi.org/10.3389/fceic.2023.1136720
How important are ceramic materials in today’s world? Certainly, very! Every sector of technology, science and common life would not be what it is without the presence of ceramics. Probably, this depends on the very meaning of ceramic; for example, according to the definition proposed by ASTM International (ASTM C1145-19, 2019), an advanced ceramic material is a highly engineered, high performance, predominately non-metallic and inorganic, material having specific functional attributes. But if we think about it, this implies that everything that is not a metal or a polymer is a ceramic material! From aeronautics to space applications, from advanced mechanics to sensors, from automotive to energy systems, from medicine to electronics, from telecommunications to safety devices, from kitchenware to constructions, from optics to nuclear power, ceramic materials are everywhere (Carter and Norton, 2013).
About 25,000 years ago our ancestors had learned to produce ceramic manufacts starting from very fine powders collected from specific clayey sediments (Vandiver et al., 1989); these, suitably mixed with water, could shape objects which, once heated to relatively high temperature, turned out to be very hard, almost like stones. Therefore, the basics of ceramic processing (i.e., powders, slurries or pastes, firing) have been known since ancient times. However, the development of innumerable applications in diverse sectors, especially in the last century, has prompted the development of process technologies obtaining ceramic materials with specific shapes, dimensions and functions requirements, all while keeping an attentive eye on the use of resources, above all, energy.
Most ceramic materials are currently produced starting from powders and the final material characteristics strongly depend on the starting particles. There are now countless ceramic powders available on a commercial level, but new compositions and sizes, especially at the nanometric level, are still a subject of research to propose new forming technologies and achieve different properties and ever higher performances.
In recent years, there has been a trend to use nanometric powders (i.e., with sizes smaller than about 100 nm) for the production of ceramics. As a result, this decreases the sintering temperatures, and obtains materials with a reduced grain size resulting in numerous advantages in terms of properties, especially mechanical, magnetic, electrical and optical (Gleiter, 1989). For the majority of ceramic materials, the sintering onset is definitely lower when nano-particles are used (around 0.2–0.4 Tm, where Tm is the melting point of the compound) with respect to conventional micrometric powders (0.5–0.8 Tm) (Groza, 1999; Hahn, 1993). Nevertheless, if the densification mechanisms when coarse or micrometric powders are used are absolutely known and therefore controllable (Rahaman, 2017), using nano-powders results in many aspects that are not yet understood both from a theoretical and a practical point of view. Among these, the problem of agglomeration, which has decidedly negative effects in the creation of the green body and on densification because of an adverse effect on the packing homogeneity. In addition, questions remain regarding the sintering mechanisms at the nanometric scale.
The characteristics of ceramic powders like shape, size, state of agglomeration depend on the synthesis method. For the production of advanced ceramics some desirable properties are required like micrometric size, equiaxial shape, high chemical and mineralogical purity, no agglomeration (or soft agglomeration). This has led to the development of a number of bottom-up techniques (referring to chemical synthesis approaches) currently preferred, especially for nano-powders, over top-down processes, which basically refer to mechanical methods of comminution. Chemical synthesis techniques are also fundamental, if not unique, in the production of very pure or composite particles made up of complex compounds such as mixed oxides (Biesuz et al., 2016; Palmero, 2015; Tyrpekl et al., 2019), perovskites (Kulkarni et al., 2019; Yin et al., 2019) or high entropy compounds (Oses et al., 2020; Rost et al., 2015; Spiridigliozzi et al., 2022a).
Two innovative research areas, linked to an increasing environmental awareness are the production of powders from natural sources (Cestari et al., 2021) or waste materials. In the former case, there is the possibility to incorporate specific trace elements during the synthesis to obtain improved biocompatibility in the case of scaffolds or implants (Kim et al., 2014; Rocha et al., 2005). The trend towards the reuse of inorganic materials is certainly not new, but the ever-increasing use of devices and components made up of rare or very expensive compounds pushes us to find efficient solutions for the recovery of substances in the form of powders that can re-feed the production cycle (Ciez and Whitacre, 2019; Sarner et al., 2022; Yenesew et al., 2023; Yu et al., 2019).
Forming techniques, such as the creation of suspensions or mixtures to be used in pressing; slip and tape casting; extrusion and additive manufacturing processes, represent a fundamental research sector for the creation of new devices and components.
A first aspect concerns the production of well deflocculated suspensions or homogeneous mixtures especially when nanometric powders are used. It is well known that the homogeneity and density of the final ceramic depend on the capability of the starting particles to rearrange during sintering at high temperature and this is strongly accounted for by the quality of the green compact (Rahaman, 2017).
In most cases the process involves the assembling of a suspension (viscous or plastic) where the powder is adequately dispersed in a solvent thanks to the addition of deflocculant (Shanefield, 2013). In general, organic products are used, since they do not remain in the final material after opportune heating. Also, when nano-particles are used, the increase in specific surface area requires higher amounts of dispersant. However, this can cause defects in the final material, and compounds with superior deflocculant properties and higher tendency to be homogeneously removed upon heating are increasingly in demand. The same issues regard the other processing additives (binder, plasticizer, wetting agent etc.) needed for the specific shaping method, from pressing to casting, from gelation to injection moulding. One additional aspect is related to the production of composites where powders with different shape and composition must be homogeneously dispersed (Moreno, 2020).
There is no doubt that, in recent years, the ceramic materials sector has witnessed a growth in shaping techniques based on additive manufacturing (AM) or, more simply, 3D printing. Additive manufacturing is a technology which allow to produce objects layer by layer starting from a 3D digital model produced by computer-aided design (CAD). It has rapidly developed due to the capacity to generate very complex shapes with high precision and minimum material waste.
3D printing techniques applied to ceramics can produce dense or porous objects although most of the technologies are applied to create porous components, because of the possibility to reproduce the desired structure with precise geometrical control of size, shape and amount of pores; the superior capacity to obtain fine interlaced structures, and the availability of other simpler routes for the manufacture of dense objects.
Basically, two different groups of AM technologies can be identified: the single-step ones (also called direct processes), where parts are fabricated in a single operation and the shape and basic material properties are achieved simultaneously, and the multi-step processes (or indirect processes), where the parts are fabricated in successive operations, the first typically providing the geometric shape and the following consolidating the part to the intended material properties (Deckers et al., 2014).
The only AM direct processes used to produce ceramics are direct energy deposition and powder bed fusion, which includes selective laser melting (SLM) or sintering (SLS). Here a thermal energy (such as a laser) selectively melts or sinters specific regions of a power bed (Deckers et al., 2014). Several issues arise given the huge specific volume variation upon sintering and melting; the stresses generated by the consolidation of successive layers, and residual porosity (Zocca et al., 2015).
More numerous are the AM indirect techniques used for the production of ceramic materials. These range from Direct Inkjet Printing (DIP) to Fused Deposition (FD) and robocasting, from stereolithography (SL) to Laminated Object Modelling (LOM) and Binder Jetting (BJ), just to cite the most common. In the former (DIP, FD and robocasting), a slurry or a thermoplastic filament filled with ceramic particles are deposited layer by layer through a moving printing head or nozzle. In SL, different ceramic-containing slurry layers are scanned by UV radiation, which polymerizes the suspension. Tape cast layers are successively cut and stacked in LOM technology. A liquid bonding agent is selectively deposited to join powder materials in Binder jetting. De-binding and sintering are then always required to consolidate the ceramic powder in all these AM techniques (Zocca et al., 2015). The choice of the solvent/thermoplastic resin or binder, the flowability and packing density of the powder in BJ, and the adhesion among the green layers in LOM represent critical issues. Additional aspects regarding the ceramic solid loading in the slurry or resin filament which, in principle must be maximized to limit the volume difference between the printed body and the final component.
In general, it is still not trivial to produce a green body with specific microstructure and homogeneity by using AM techniques.
Sintering is something inherent in ceramics. The term “ceramic” itself derives from an ancient Greek word, keramos (κεραμοσ) which means “product from clay”, “vase”, “amphora”; in turn, keramos is strictly connected with a Sanskrit root, which meant “to burn”. Therefore, the intrinsic meaning of ceramic is “burnt Earth.” Nowadays, sintering indicates a decidedly broader concept, not strictly related to ceramic materials.
Although sintering has accompanied human beings for about twenty thousand years, the process based on the heating of suitably compacted powders to produce compact ceramic artefacts did not significantly change until the 19th century with the first pressure-assisted sintering experiments, progenitors of the technique currently known as hot pressing (Wollaston, 1829). The early 1900s saw an explosion of ideas that could make sintering more energy efficient with the use of electromagnetic fields, electric currents or radiation like microwaves (Chaffee, 1939; Lux, 1906). Some research activities also began towards the 1960s aimed at favouring the densification of the powders using pressurized steam (Aitken, 1960; Eastman and Cutler, 1966).
But we had to get to 2010 to witness a real explosion of research for the development of new sintering techniques, for example, flash sintering (FS), cold sintering (CS) and ultrarapid high-temperature sintering (UHS).
Flash sintering was discovered in 2010 by R. Raj and co-workers (Cologna et al., 2010). It is activated when an electric field is applied to a ceramic green body as it is heated in a conventional furnace. At a specific combination of temperature and electric field, the ceramic “flashes,” a sudden increase of the body conductivity is recorded and rapid densification (in a few seconds or minutes) occurs together with a bright glowing emission (Biesuz et al., 2020; Biesuz and Sglavo, 2019). The flash takes placed when a certain power dissipation is reached, which triggers a thermal runaway of Joule heating responsible for very high heating rates (around 103°C–104°C/min). But additional athermal effects have been observed, for example, the alteration of the electronic and structural features of the ceramic together with its electrochemical properties (Biesuz and Sglavo, 2019; Biesuz and Sglavo, 2020). Although the flash event was primarily investigated for ceramics sintering, numerous flash-like processes have recently emerged and could develop further, for example, flash synthesis (Jesus et al., 2016), flash joining (Biesuz et al., 2019), and flash softening (McLaren et al., 2018).
A particularly fascinating area is that of the athermal phenomena generated due to the extreme heating conditions during the flash, which could allow in the future the tailoring of the crystallization kinetics to obtain unexpected microstructures. Some of the anomalous features produced by the flash can be retained also when the field is turned off, leading to unconventional properties in flashed ceramics like a modified band gap, grain boundary and surface elemental segregations, enhanced photoluminescence, formation of line defects and staking faults (Biesuz and Sglavo, 2020). It is not just a dream to think that soon flash processes could be used to modify the atomic or electronic structure of ceramics and produce new, unimagined properties.
Very recently, flash sintering has been successfully applied to conductive ceramics (like tungsten carbide) (Mazo et al., 2022a; Mazo et al., 2022b) and such results could open very interesting possibilities also in ultra-high temperature carbides and borides, which are typically difficult to densify.
Cold sintering is another very new and intriguing consolidation process for ceramics. It was introduced by K. Randall and co-workers in 2016 (Guo et al., 2016; Guo et al., 2018; Maria et al., 2017). It resembles the geological formation of rocks and a ceramic powder is densified with the aid of a liquid phase under high pressure and limited heating conditions (below 350°C). A multitude of ceramics has been successfully consolidated by cold sintering to produce piezoelectrics, dielectrics, bioceramics, batteries (Galotta and Sglavo, 2021). There is no doubt that cold sintering represents one of the most promising technologies for consolidating ceramic materials, especially from the point of view of an ecological transition, given the possibility of drastically reducing sintering times and consequently energy costs.
However, the physical and chemical mechanisms underlying the densification process need further investigation, so to optimize the production processes and select appropriate materials and shapes.
In 2020, another innovative technique, called Ultra-fast High temperature Sintering (UHS) was proposed by Wang et al. (2020). The green sample is sandwiched between two carbon felts which are kept in an inert atmosphere and Joule-heated by a current flow. This allows a uniform temperature distribution, high heating and cooling rates (up to 104°C/min), and very high maximum temperature (up to 3,000°C). The ultrahigh heating rate enables ultrafast sintering, with times typically in the order of about 10 s. The short processing time prevents volatile evaporation and undesirable interdiffusion at the interfaces of multilayer structures. The UHS process is also compatible with 3D printed articles and additional advantages regard the possibility to inhibit grain coarsening (Kermani et al., 2021; Wang et al., 2020), control lithium content, by limiting the evaporation in solid state electrolytes (Wang et al., 2020), and stabilize specific phases at room temperature (Biesuz et al., 2021; Spiridigliozzi et al., 2022b).
Ceramics’ processing represents a still strongly expanding research area, driven by the need to respond to requests for new materials with specific properties and processes with lower environmental impact and reduced energy consumption.
Starting from this, the role of Frontiers in Ceramics and of the Processing section is clear: collecting contributions of high quality fundamental and applied research related to the processes used to fabricate ceramics, also with reference to industrial practices, from the synthesis of starting powders to the realization of final components and devices, also including the processes’ analysis by modelling and numerical simulations. One should find in the “Processing” section of Frontiers in Ceramics opportune references to better clarify the phenomena underlying the traditional production techniques; improve and make fabrication techniques more efficient and versatile to obtain diverse compositions and microstructures, and to discover new production routes, from additive manufacturing to innovative sintering methodologies.
The author confirms being the sole contributor of this work and has approved it for publication.
The author declares that the research was conducted in the absence of any commercial or financial relationships that could be construed as a potential conflict of interest.
All claims expressed in this article are solely those of the authors and do not necessarily represent those of their affiliated organizations, or those of the publisher, the editors and the reviewers. Any product that may be evaluated in this article, or claim that may be made by its manufacturer, is not guaranteed or endorsed by the publisher.
Aitken, E. A. (1960). Initial Sintering Kinetics of Beryllium Oxide. Journal of the American Ceramic Society 43 (12), 627–633. doi:10.1111/j.1151-2916.1960.tb13631.x
Biesuz, M., Dell’Agli, G., Spiridigliozzi, L., Ferone, C., and Sglavo, V. M. (2016). Conventional and field-assisted sintering of nanosized Gd-doped ceria synthesized by co-precipitation. Ceramics International 42 (10), 11766–11771. doi:10.1016/j.ceramint.2016.04.097
Biesuz, M., Galotta, A., Motta, A., Kermani, M., Grasso, S., Vontorová, J., Tyrpekl, V., Vilémová, M., and Sglavo, V. M. (2021). Speedy bioceramics: Rapid densification of tricalcium phosphate by ultrafast high-temperature sintering. Materials Science and Engineering: C 127, 112246. doi:10.1016/j.msec.2021.112246
Biesuz, M., Grasso, S., and Sglavo, V. M. (2020). What’s new in ceramics sintering? A short report on the latest trends and future prospects. Current Opinion in Solid State and Materials Science 24 (5), 100868. doi:10.1016/j.cossms.2020.100868
Biesuz, M., Saunders, T. G., Grasso, S., Speranza, G., Sorarù, G. D., Campostrini, R., Sglavo, V. M., and Reece, M. J. (2019). Flash joining of conductive ceramics in a few seconds by flash spark plasma sintering. Journal of the European Ceramic Society 39 (15), 4664–4672. doi:10.1016/j.jeurceramsoc.2019.07.036
Biesuz, M., and Sglavo, V. M. (2019). Flash sintering of ceramics. Journal of the European Ceramic Society 39 (2–3), 115–143. doi:10.1016/j.jeurceramsoc.2018.08.048
Biesuz, M., and Sglavo, V. M. (2020). Beyond flash sintering: How the flash event could change ceramics and glass processing. Scripta Materialia 187, 49–56. doi:10.1016/j.scriptamat.2020.05.065
Carter, C. B., and Norton, M. G. (2013). “Ceramic materials: Science and engineering,” in Ceramic Materials: Science and Engineering. doi:10.1007/978-1-4614-3523-5
Cestari, F., Agostinacchio, F., Galotta, A., Chemello, G., Motta, A., and Sglavo, M.V. (2021). Nano-Hydroxyapatite Derived from Biogenic and Bioinspired Calcium Carbonates: Synthesis and In Vitro Bioactivity. Nanomaterials 11 (2), 264. doi:10.3390/nano11020264
Ciez, R. E., and Whitacre, J. F. (2019). Examining different recycling processes for lithium-ion batteries. Nature Sustainability 2 (2), 148–156. doi:10.1038/s41893-019-0222-5
Cologna, M., Rashkova, B., and Raj, R. (2010). Flash Sintering of Nanograin Zirconia in <5 s at 850°C. Journal of the American Ceramic Society 93 (11), 3556–3559. doi:10.1111/j.1551-2916.2010.04089.x
Deckers, J., Vleugels, J., and Kruth, J. P. (2014). Additive manufacturing of ceramics: A review. Journal of Ceramic Science and Technology 5, 245–260. doi:10.4416/JCST2014-00032
Eastman, P. F., and Cutler, I. B. (1966). Effect of Water Vapor on Initial Sintering of Magnesia. Journal of the American Ceramic Society 49 (10), 526–530. doi:10.1111/j.1151-2916.1966.tb13156.x
Galotta, A., and Sglavo, V. M. (2021). The cold sintering process: A review on processing features, densification mechanisms and perspectives. Journal of the European Ceramic Society 41 (16), 1–17. doi:10.1016/j.jeurceramsoc.2021.09.024
Gleiter, H. (1989). Nanocrystalline materials. Progress in Materials Science 33 (4), 223–315. doi:10.1016/0079-6425(89)90001-7
Groza, J. R. (1999). Nanosintering. Nanostructured Materials 12 (5–8), 987–992. doi:10.1016/S0965-9773(99)00284-6
Guo, H., Baker, A., Guo, J., and Randall, C. A. (2016). Cold sintering process: A novel technique for low-temperature ceramic processing of ferroelectrics. Journal of the American Ceramic Society 99 (11), 3489–3507. doi:10.1111/jace.14554
Guo, J., Zhao, X., Herisson De Beauvoir, T., Seo, J., Berbano, S. S., Baker, A. L., et al. (2018). Recent progress in applications of the cold sintering process for ceramic–polymer composites. Advanced Functional Materials 28 (39), 1801724. doi:10.1002/adfm.201801724
Hahn, H. (1993). Microstructure and properties of nanostructured oxides. Nanostructured Materials 2 (3), 251–265. doi:10.1016/0965-9773(93)90152-2
Jesus, L. M., Silva, R. S., Raj, R., and M’Peko, J.-C. (2016). Electric field-assisted ultrafast synthesis of nanopowders: a novel and cost-efficient approach. RSC Advances 6 (109), 107208–107213. doi:10.1039/C6RA18734J
Kermani, M., Dong, J., Biesuz, M., Linx, Y., Deng, H., Sglavo, V. M., Reece, M. J., Hu, C., and Grasso, S. (2021). Ultrafast high-temperature sintering (UHS) of fine grained α-Al2O3. Journal of the European Ceramic Society 41 (13), 6626–6633. doi:10.1016/j.jeurceramsoc.2021.05.056
Kim, B.-S., Kang, H. J., Yang, S.-S., and Lee, J. (2014). Comparison of in vitro and in vivo bioactivity: cuttlefish-bone-derived hydroxyapatite and synthetic hydroxyapatite granules as a bone graft substitute. Biomedical Materials 9 (2), 025004. doi:10.1088/1748-6041/9/2/025004
Kulkarni, S. A., Mhaisalkar, S. G., Mathews, N., and Boix, P. P. (2019). Perovskite Nanoparticles: Synthesis, Properties, and Novel Applications in Photovoltaics and LEDs. Small Methods 3 (1), 1800231. doi:10.1002/smtd.201800231
Lux, J. (1906). Improved manufacture of electric incandescence lamp filaments from tungsten or molybdenum or an alloy thereof. GB Patent 27 (002).
Maria, J.-P., Kang, X., Floyd, R. D., Dickey, E. C., Guo, H., Guo, J., et al. (2017). Cold sintering: Current status and prospects. Journal of Materials Research 32 (17), 3205–3218. doi:10.1557/jmr.2017.262
Mazo, I., Molinari, A., and Sglavo, V. M. (2022a). Electrical resistance flash sintering of tungsten carbide. Materials & Design 213, 110330. doi:10.1016/j.matdes.2021.110330
Mazo, I., Molinari, A., and Sglavo, V. M. (2022b). Effect of pressure on the electrical resistance flash sintering of tungsten carbide. Journal of the European Ceramic Society 42 (5), 2028–2038. doi:10.1016/j.jeurceramsoc.2022.01.017
McLaren, C. T., Heffner, W. R., Raj, R., and Jain, H. (2018). AC electric field-induced softening of alkali silicate glasses. Journal of the American Ceramic Society 101 (6), 2277–2286. doi:10.1111/jace.15387<
Moreno, R. (2020). Better ceramics through colloid chemistry. Journal of the European Ceramic Society 40 (3), 559–587. doi:10.1016/j.jeurceramsoc.2019.10.014
Oses, C., Toher, C., and Curtarolo, S. (2020). High-entropy ceramics. Nature Reviews Materials 5 (4), 295–309. doi:10.1038/s41578-019-0170-8
Palmero, P. (2015). Structural ceramic nanocomposites: A review of properties and powders’ synthesis methods. NanomaterialsMDPI AG 5 (2), 656–696. doi:10.3390/nano5020656
Rahaman, M. N. (2017). Ceramic Processing. Second Edition. Boca Raton, FL: CRC Press. doi:10.1201/9781315157160
Rocha, J. H. G., Lemos, A. F., Agathopoulos, S., Valério, P., Kannan, S., Oktar, F. N., and Ferreira, J. M. F. (2005). Scaffolds for bone restoration from cuttlefish. Bone 37 (6), 850–857. doi:10.1016/j.bone.2005.06.018
Rost, C. M., Sachet, E., Borman, T., Moballegh, A., Dickey, E. C., Hou, D., Jones, J. L., Curtarolo, S., and Maria, J.-P. (2015). Entropy-stabilized oxides. Nature Communications 6 (1), 8485. doi:10.1038/ncomms9485
Sarner, S., Schreiber, A., Menzler, N. H., and Guillon, O. (2022). Recycling Strategies for Solid Oxide Cells. Advanced Energy Materials 12 (35), 2201805. doi:10.1002/aenm.202201805
Shanefield, D. J. (2013). Organic additives and ceramic processing: with applications in powder metallurgy, ink, and paint. 2nd edition. Kluwer Academic Publishers.
Spiridigliozzi, L., Dell’Agli, G., Callone, E., Dirè, S., Campostrini, R., Bettotti, P., Bortolotti, M., Speranza, G., Sglavo, V. M., and Biesuz, M. (2022a). A structural and thermal investigation of Li-doped high entropy (Mg, Co, Ni, Cu, Zn)O obtained by co-precipitation. Journal of Alloys and Compounds 927, 166933. doi:10.1016/j.jallcom.2022.166933
Spiridigliozzi, L., Dell’Agli, G., Esposito, S., Rivolo, P., Grasso, S., Sglavo, V. M., and Biesuz, M. (2022b). Ultra-fast high-temperature sintering (UHS) of Ce0.2Zr0.2Y0.2Gd0.2La0.2O2−δ fluorite-structured entropy-stabilized oxide (F-ESO). Scripta Materialia 214, 114655. doi:10.1016/j.scriptamat.2022.114655
Tyrpekl, V., Markova, P., Dopita, M., Brázda, P., and Vacca, M. A. (2019). Cerium Oxalate Morphotypes: Synthesis and Conversion into Nanocrystalline Oxide. Inorganic Chemistry 58 (15), 10111–10118. doi:10.1021/acs.inorgchem.9b01250
Vandiver, P. B., Soffer, O., Klima, B., and Svoboda, J. (1989). “The Origins of Ceramic Technology at Dolni Vestonice, Czechoslovakia Science,” in Reprint Series, 246.
Wang, C., Ping, W., Bai, Q., Cui, H., Hensleigh, R., Wang, R., Brozena, A. H., Xu, Z., Dai, J., Pei, Y., Zheng, C., Pastel, G., Gao, J., Wang, X., Wang, H., Zhao, J.-C., Yang, B., Zheng, X., Luo, J., and Hu, L. (2020). A general method to synthesize and sinter bulk ceramics in seconds. http://science.sciencemag.org/.
Wollaston, W. H. (1829). I. The Bakerian Lecture.—On a method of rendering platina malleable. Philosophical Transactions of the Royal Society of London 119, 1–8. doi:10.1080/14786442908675048
Yenesew, G. T., Quarez, E., LE GAL LA SALLE, A., Nicollet, C., and Joubert, O. (2023). Recycling and characterization of end-of-life solid oxide fuel/electrolyzer ceramic material cell components. Resources, Conservation and Recycling 190, 106809. doi:10.1016/j.resconrec.2022.106809
Yin, W.-J., Weng, B., Ge, J., Sun, Q., Li, Z., and Yan, Y. (2019). Oxide perovskites, double perovskites and derivatives for electrocatalysis, photocatalysis, and photovoltaics. Energy & Environmental Science 12 (2), 442–462. doi:10.1039/C8EE01574K
Yu, J., Wang, X., Zhou, M., and Wang, Q. (2019). A redox targeting-based material recycling strategy for spent lithium ion batteries. Energy & Environmental Science 12 (9), 2672–2677. doi:10.1039/C9EE01478K
Keywords: ceramics processing, sintering, colloidal processes, AM technologies, 3D printing, flash sintering, cold sintering, ultra-fast high temperature sintering
Citation: Sglavo VM (2023) Grand challenges in ceramics processing. Front. Ceram. 1:1136720. doi: 10.3389/fceic.2023.1136720
Received: 03 January 2023; Accepted: 26 January 2023;
Published: 14 February 2023.
Edited and reviewed by:
Ping Xiao, The University of Manchester, United KingdomCopyright © 2023 Sglavo. This is an open-access article distributed under the terms of the Creative Commons Attribution License (CC BY). The use, distribution or reproduction in other forums is permitted, provided the original author(s) and the copyright owner(s) are credited and that the original publication in this journal is cited, in accordance with accepted academic practice. No use, distribution or reproduction is permitted which does not comply with these terms.
*Correspondence: Vincenzo M. Sglavo, dmluY2Vuem8uc2dsYXZvQHVuaXRuLml0
Disclaimer: All claims expressed in this article are solely those of the authors and do not necessarily represent those of their affiliated organizations, or those of the publisher, the editors and the reviewers. Any product that may be evaluated in this article or claim that may be made by its manufacturer is not guaranteed or endorsed by the publisher.
Research integrity at Frontiers
Learn more about the work of our research integrity team to safeguard the quality of each article we publish.