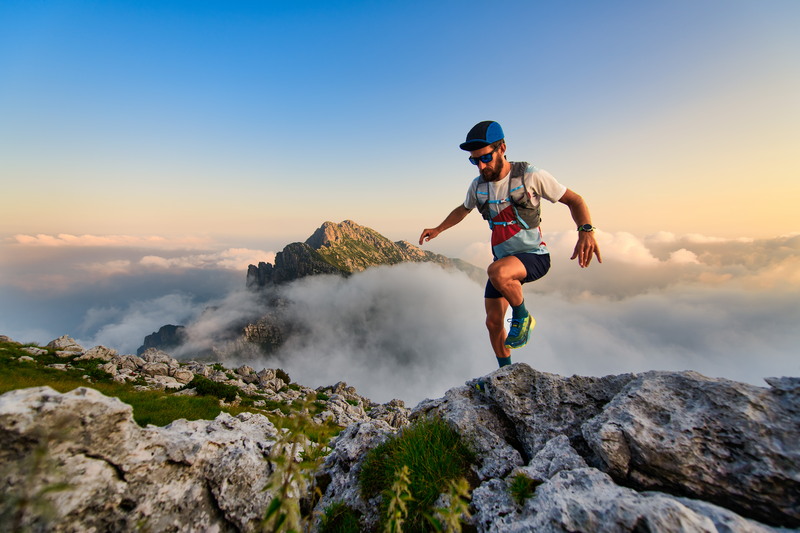
95% of researchers rate our articles as excellent or good
Learn more about the work of our research integrity team to safeguard the quality of each article we publish.
Find out more
REVIEW article
Front. Carbon , 08 May 2024
Sec. Carbon-Based Objects and Devices
Volume 3 - 2024 | https://doi.org/10.3389/frcrb.2024.1339418
Rubber (elastomer) based polymer nanocomposites have attracted wide range of attention from industries and other fields due to its exceptionally good mechanical, thermal and electrical properties. One of the promising candidates of this category is CNT filled rubber nanocomposites. This review throws light on the historical trajectory of development of CNT filled rubber nanocomposites. Various fabrication methods, detailed explanation of reinforcement mechanism in CNT/rubber nanocomposites and the relationship between the structure and properties are reviewed. The next part of the review discusses about the morphological and interface characteristics. An attempt to investigate the versatile mechanical, thermal, and electrical properties also included in the review. The final part of the review includes the applications of CNT filled rubber nanocomposites. Major applications in fields like electronics, sustainable biomedical and EMI shielding are discussed in detail. The review also focuses on the key challenges that arises while incorporating CNTs into rubber matrices.
The versatility of elastomers in industrial sector among various polymers is of considerable significance in the present era due to their high and reversible deformability. Elastomers are broadly used in many sectors, such as automobile engineering, biomedical field, aerospace study, civil applications and so on. But unfilled elastomers show poor properties. Elastomer has been incorporated with various macro and micro fillers to improve the mechanical, thermal. Electrical, barrier and optical properties. Even though incorporation of conventional fillers to rubber improved the performance of rubber-based materials, the emerging potential applications of rubber composites motivated the researchers to think of more efficient fillers that possess multifunctional attributes. Moreover, higher amount of conventional fillers are needed to enhance the overall performance of rubber. Parameters which affect the performance of the rubber materials include volume fraction of fillers and their aspect ratio, processability, proper dispersion of fillers in the polymer matrix, filler-rubber interaction, etc. So, the incorporation of nanofillers in the rubber matrix can impart superior performance for these materials (Thostenson et al., 2005).
The high aspect ratio of nanofillers enables the formation of network formation in the rubber matrix at low filler loading. Rubber-filler interaction is improved by the nanoscale dispersion of fillers in the matrix which leads to the property improvement. Many nanofillers have been extensively examined to achieve extraordinary properties in rubber-based products.
Among various nanofillers Carbon nanotubes (CNTs) have got special attention because of their interesting properties like outstanding mechanical and physical properties, high aspect ratio, low density, tunable electrical conductivity, high modulus and high electrical/thermal properties, biocompatibility, ease of functionalization, etc (Popov, 2004). Because of these outstanding characteristics CNTs have potential applications in supercapacitors, electrode material, thin-film electronics, device modelling, automotive parts, sporting goods, water filters, coatings, actuators, sensors, electromagnetic shields, medicinal and diagnostic substances, drug delivery and biosensing platforms (De Volder et al., 2013).
Figure 1 gives a cumulative idea of the intensive research that is being carried out in the field of CNT/rubber polymer nanocomposites. It gives a graph which shows the number of publications and citations in this dynamic area during the last 24 years. The graph clearly provides the proof of vast research in the field of fabrication of CNT/rubber composites which paved the way to develop exceptionally good materials with superior applications.
Figure 1. Graph showing the total number of publications and citations in the field of CNT/rubber polymer nanocomposites during 1999–2023.
It is seen that, in the earlier times, the extent of research in this field is limited because of the lack of fabrication methods to synthesize polymer nanocomposites. Primary step of modifying elastomeric polymer matrix by incorporating nanomaterials have taken in 1959 itself. But authentic scientific research began in early 1990s. Incorporation of 1D materials like CNTs into elastomers was a milestone movement which leads to the development of conducting materials which found various applications (Akpan et al., 2019). The commercial use of CNT reinforced polymer nanocomposites was first carried out in 1990s. Incorporating CNTs in elastomers create highly durable, flexible, and light weight composites. The exceptional properties of these elastomeric composites encouraged the researchers to develop unique fabrication methods for the fabrication of CNT/rubber composites. Modifications on filler CNTs were also taking place to improve the characteristics. The graph shows that progressive research has taken place from 2004 onwards and resulted an average of 15 publications per year. Within 10 years, the number of publications per annum increased by almost 10 folds. This clearly give the importance and scope of CNT reinforced elastomeric nanocomposites in various fields. The improved mechanical and electrical properties of CNT/rubber composites finds applications in various fields which includes energy harvesting and storage, biomedical and sensing. The ability of these composites to replace conventionally used electrodes in sensing and energy harvesting systems attracted the global attention. Towards 2017 and 2018, a rapid increase in the research have taken place and as a result, huge number of scientific articles depicting the formation, modification and applications have been published (literature shows the publication of approximately 250 articles in 2018 itself). The research is still now progressing to find the unexplored applications of CNT/rubber composites by modifying both the polymer and filler.
CNTs are made of one or more graphene sheets rolled-up to form tubes. Based on number of layers, there are two different types of CNT. Single walled carbon nanotube (SWCNT) comprise a single graphene layer seamlessly wrapped into a cylindrical tube. Multi-walled carbon nanotube (MWCNT) comprise a series of graphene layers wrapped into a cylindrical tube with van der Waals force of attraction between individual tubes. Carbon nanotubes have so many excellent properties, but processing difficulty and the formation of agglomerates in the rubber matrix are the two major concerns in the fabrication of CNT rubber nanocomposites (Xie et al., 2005). Large surface area and van der Waals force of attraction between individual tubes leads to the formation of agglomerates which act as stress concentration centres. CNTs inherently tend to hold together as ropes and bundles due to this van der Waals interactions. So the solubility of CNT in common solvents and the CNT polymer interaction is limited. These drawbacks can be overcome by the proper surface functionalization either by chemical or physical methods. Surface modification improves interfacial linkage, dispersion of CNT and hence chemical reactivity. CNT surface functionalization can be broadly classified into three categories covalent and non-covalent approaches and endohedral filling. Figure 2 represents the various functionalization approaches for CNT.
• Covalent bonds between CNT surface and incoming group.
• Attachment of different chemical groups via non-covalent bonds by using hydrophobicity of CNTs such as hydrogen bonds, π–π interactions, or ionic bonds.
• Inline filling (endohedral) of hollow tubes of CNTs (Encapsulation of Fullerene derivatives, inorganic species, biomolecules etc.).
In covalent functionalization, a covalent bond is formed between functional moieties and carbon skeleton of CNT. This type of functionalization improves the dispersion of CNT in the medium, i.e., polymer or solvent, which enhance wetting or adhesion characteristics and decrease the clusters of CNTs (Koval’chuk et al., 2008). Covalent functionalization is superior to non—covalent functionalization in terms of the stability of functionalization. Effective filler reinforcement is observed in covalently functionalized CNT polymer nanocomposite due to the excellent load transfer between CNT and polymer through these covalent linkages (Yerushalmi-Rozen and Szleifer, 2006). However, in covalent functionalization there is a change the hybridization of carbon atom from sp2 to sp3 and a simultaneous loss of conjugation. This destroys the surface conjugated π network which in turn leads to the reduction in electrical conductivity of CNT. Moreover, creation of defects on the surface of CNT also leads to the loss of inherent mechanical properties of CNT.
One of the major covalent functionalization of CNT is oxidation of CNT by acid treatment. Different combinations of inorganic acids can be used for this type of functionalization. Jun and co-workers made a comparative study of acid functionalization of carbon nanotube via ultrasonic and reflux mechanism. The effects of parameters including type of acids, acid concentrations, treatment methods, operating temperature and treatment duration has been investigated. Results of the study indicated that optimized conditions for the acid functionalization of MWCNTs is by using a concentrated acid mixture of HNO3/H2SO4 (1:3 v/v ratio), via ultrasonication technique. It is also found that sonication method was more efficient for the acid functionalization of CNT than reflux method because of the simplicity for the experimental set up, high yield and desirable properties of CNT (Jun and Mubarak, 2018). Carboxylic acid functional group on CNT surface can be modified by various chemical reactions such as Amidation—Formation of Carbon Nanotube-Acyl Amides (Seo et al., 2017), Ester formation (Hamon et al., 2002), Thiolation (Lim et al., 2003) etc. Fluorination (Adamska and narkiewicz, 2017), Chlorination (Dettlaff-Weglikowska et al., 2002), Hydrogenation (Chen et al., 1998) etc., are some other prominent methods for the covalent functionalization of CNT. Another commonly used for the covalent functionalization of CNT is addition reactions, such as nucleophilic addition, electrophilic addition, free-radical addition, cycloaddition (carbene addition, addition of nitrenes, Diels alder reaction, Azomethine Ylides, Nucleophilic Cyclopropanation), Birch reduction and reductive alkylation (Tasis et al., 2006). In covalent functionalization of CNT by polymers, the long chain polymers assist CNT to dissolve in suitable solvents. Covalent modification by polymers can be either achieved by surface-initiated polymerization, known also as “grafting from” or through “grafting to” methodology (Abousalman-Rezvani et al., 2020).
Covalent functionalization may change the intrinsic properties of CNT and, in turn make them unsuitable for many applications. On the other hand, non-covalent functionalization enhances the solubility of CNT at the same time this preserves the intrinsic attributes of CNT. Non-covalent functionalization is mostly accomplished through supramolecular complexation using a variety of adsorption forces, including the Van der Waals force, hydrogen bonds, electrostatic force, and π-stacking interactions. Non-covalent functionalization means physical wrapping of functional moieties to the CNT surface. This type of functionalization can be operated in milder conditions (Meng et al., 2009).
There are several strategies for the noncovalent functionalization of CNT using polymers 1) Non-covalent functionalization via π—π interactions with conjugated polymers (Tuncel, 2011) 2) Non-covalent functionalization of carbon nanotubes via π—π interactions with polymers bearing pyrene moieties (Lou et al., 2004) 3) Non-covalent functionalization through more π—π interactions 4) Non-covalent functionalization via ionic interactions, 5) Non-covalent functionalization via CH–π interactions, 6) Non-covalent functionalization via OH–π interactions (Bilalis et al., 2014). Functionalization through polymer wrapping is attractive in terms of the homogeneity of the functionalization and stability. It also preserves the intrinsic properties of CNT such as electrical conductivity and mechanical stability, etc. Polymer forms a thermodynamically stable coating on the surface of the CNTs, and it is possible to remove the unbound (free) polymer while leaving the wrapped polymer on the CNT surface (Fujigaya and Nakashima, 2015). Surfactants can be used for the non-covalent functionalization of CNT. Some examples for commonly used surfactant are Sodium dodecyl sulfate (SDS), sodium dodecylbenzene sulfonate (SDBS), sodium cholate (SC), Cetyltrimethylammonium bromide (CTAB), Tween and Triton X, etc (Ponnamma et al., 2014). Ionic liquids have been used for the non-covalent functionalization of CNT. Ionic liquids are green solvents and are considered to improve the CNT dispersibility without the necessity for solid substances or organic solvents. Fukushima et al. used imidazolium based ionic liquid as the dispersant for CNT for the first time (Fukushima and Aida, 2007). Here cationic part of ionic liquid interacts with π electronic surface of CNT by cation—π interaction and hence disperse CNT. The high dielectric constant of ionic liquid prevents the defundling of CNT (Abraham et al., 2016).
The fabrication of Carbon Nanotube (CNT)/elastomer nanocomposites is a cutting-edge area of research that leverages the remarkable properties of carbon nanotubes to enhance the flexibility and resilience of elastomers. The key challenge lies in achieving a uniform dispersion of CNTs within the elastomer matrix, which is addressed through various techniques, including mechanical mixing (e.g., two-roll mill or twin-screw extruder), the use of functionalized CNTs or surfactants, sonication, and three-roll milling. Cross-linking agents are introduced to enhance mechanical properties, and processing techniques such as compression molding, injection molding, and calendaring are employed to shape the nanocomposite into sheets, films, or other desired forms (Sisanth et al., 2017). These nanocomposites have versatile applications across electronics, aerospace, automotive, and biomedical devices, making them materials with wide-ranging potential. The diverse methods for preparing these nanocomposites encompass solution mixing, latex blending, melt mixing, and in-situ polymerization, reflecting the dynamic nature of this field’s ongoing research.
Solution mixing is a highly versatile and widely employed technique for the fabrication of CNT/elastomer nanocomposites. This method hinges on the dispersion of CNTs within a suitable solvent, followed by their subsequent mixing with the elastomer matrix. Solution mixing offers several distinct advantages, including the capability to achieve a high degree of CNT dispersion and meticulous control over nanocomposite properties. The initial step in solution mixing necessitates meticulous materials selection. The choice of CNT type, functionalization, elastomer polymer, and solvent plays a pivotal role in the success of this method. Compatibility between materials is essential to ensure proper dispersion and mixing. Achieving uniform dispersion of CNTs within the solvent is a critical aspect of the solution mixing process. CNTs are prone to agglomeration due to van der Waals forces, rendering their dispersion challenging. To overcome this challenge, researchers often employ ultrasonication, a technique demonstrated in the study. Ultrasonication involves subjecting the CNT-solvent mixture to high-frequency sound waves, effectively breaking down CNT agglomerates and promoting even dispersion. This thorough dispersion is essential for achieving homogeneity in the subsequent mixing step and for the enhancement in properties. Following the achievement of a homogeneous CNT-solvent dispersion, the next step involves gradually introducing this mixture to the elastomer polymer. Gharib, 2018 have introduced an innovative ternary system featuring multi-walled carbon nanotubes (MWCNTs), electron-deficient acceptors, and organic solvents to mitigate the challenges of CNT dispersion and stability. The electron-deficient acceptors serve a dual purpose by disrupting inter-CNT π–π interactions, facilitating debundling and dispersion of MWCNT aggregates, while also acting as stabilizers to prevent re-agglomeration. This approach significantly boosts yield, reducing energy input requirements, and it introduces an environmentally friendly biosolvent, dihydrolevoglucosenone, addressing sustainability concerns associated with CNT processing. In summary, this method offers a promising solution to enhance the utility of CNTs by improving their dispersion, stability, and environmental sustainability. Figure 3 shows the Debundling, Dispersion, and Stability of multi-walled carbon nanotubes Driven by Molecularly Designed Electron Acceptors.
Figure 3. Debundling, Dispersion, and Stability of Multi-walled Carbon Nanotubes Driven by Molecularly Designed Electron Acceptors. (A) Bundled CNT (π - π interaction). (B) Donor-acceptor interaction. (C) Debundled and dispersed CNT stabilized by donor-acceptor interactions.
Numerous efforts have been undertaken to disperse CNTs within natural rubber (NR) matrices, all with the aim of preventing the re-agglomeration of CNTs and their bundles. These endeavors have focused on various key aspects, including mixing procedures (such as melt, solution, and latex mixing), surface functionalization of CNTs using silane coupling agents (both ex-situ and in-situ), the utilization of ionic liquids, and the incorporation of metal nanoparticles. While these approaches have succeeded in reducing the percolation threshold concentration in NR composites, they have generally fallen short in significantly improving the certain properties like electrical conductivities of these composites. The fabrication of rubber/CNT (carbon nanotube) nanocomposites through melt mixing has undergone significant developments in recent years, with a focus on achieving optimal dispersion, introducing innovative additives, and refining process parameters. These advancements are key to enhancing the properties of these nanocomposites, making them attractive for a wide range of applications. Recent advancements in melt mixing for natural rubber/CNT nanocomposites continue to address dispersion challenges, enhance interfacial interactions, and optimize process parameters, further expanding the potential applications of these nanocomposites in various industries (Balasubramanian and Jawahar, 2019). But the progress isn’t limited to natural rubber. Recent works have explored Nitrile Rubber (NBR) and Styrene-Butadiene Rubber (SBR) nanocomposites as well. Recent research utilizes a melt-mixing molding technique and employs styrene ethylene butylene styrene (SEBS) rubber as a flexible material to craft an extremely flexible strain sensor. CNTs are incorporated to establish a conductive network, and the impact of introducing Ag flakes to enhance sensor performance is investigated. The experimental findings reveal the strain-resistance characteristics of the sensor, which boasts an exceptional sensing range of approximately 540% with a gauge factor (GF) of 5.197. The highest observed electrical conductivity has been approximately 10^-1 μS/cm, which is considerably lower than the intrinsic conductivity of pure CNTs, which is around 10^5 S/cm. This disparity is largely attributed to the limited electron tunneling capability when CNTs are encapsulated within an insulating rubber layer (Zhang et al., 2021).
In one of the recent studies the research primarily focuses on the development of NR composites using a combination of CNT and CB fillers. The addition of these fillers was carefully controlled during the mixing process using a two-roll mill, with the goal of achieving optimal filler dispersion in the NR matrix. The aim is to enable CCB particles/aggregates to bridge the CNT encapsulates, ultimately improving the electrical conductivity of NR composites by facilitating electron tunneling, provided the filler conformation within the NR matrix is suitable. The study examines interactions between fillers, as indicated by the Payne effect, wetting ability, relaxation behaviour (thermo-mechanical properties), and electrical conductivity. The study also investigates the relationships between electrical conductivity, dielectric constant, bound rubber layer thickness, and inter-particle gap of CNT. The work supports the melt mixing by altering other factors (Nakaramontri et al., 2017).
Das et al., 2008 have reported a novel mixing approach for achieving a good dispersion of multi-walled carbon nanotubes (MWCNTs) in a rubber blend. In this approach the CNTs were incorporated into a 50:50 blend of solution-styrene-butadiene rubber and butadiene rubber. First, the CNTs were pre-dispersed in ethanol and then this CNT-alcohol suspension was mixed with the rubber blend at elevated temperature. The rubber nanocomposites prepared by such method exhibit significantly enhanced physical properties already at very low nanotube concentrations. Dynamic mechanical analysis indicates that the incorporation of CNTs affects the glass transition behaviour by reducing the height of the tan d peak considerably.
Liu et al. have introduced a novel ultrasonic grinding dispersion method for CNTs using waterjet-produced rubber powder (WPRP) as a carrier. Microscopic examination reveals the formation of a distinctive Xanthium-like structure, where WPRP acts as the central core, and CNTs extend outward like spikes. This unique structure plays a vital role in significantly enhancing the dispersion of CNTs within the natural rubber (NR) matrix, simultaneously reinforcing the bond between WPRP and the NR matrix. Figure 4 represents the scheme of ultrasonic grinding dispersion method for CNTs using waterjet-produced rubber powder (WPRP). As the loading of WPRP increases, the Payne effect observed in CNT/WPRP/NR composites decreases, indicating the effectiveness of the dispersion method. Additionally, the vulcanization characteristics, as represented by MH (maximum torque) and ML (minimum torque) values, along with the crosslinking density, exhibit improvements with higher WPRP loading. However, it’s worth noting that when the WPRP loading is less than 15 phr (parts per hundred rubber), both the scorch time and cure time display a decreasing trend. The research findings highlight the remarkable performance enhancements achieved in CNT/WPRP/NR composites, particularly when loaded with 5 phr WPRP. These composites exhibit a 4% increase in the 300% modulus, a 3% boost in tensile strength, and a 5% reduction in Akron abrasion loss compared to CNT/NR composites (Guo et al., 2023).
Figure 4. Scheme of ultrasonic grinding dispersion method for carbon nanotubes (CNTs) using waterjet-produced rubber powder (WPRP).
In-situ polymerization technique is a conventional method of processing rubber nanocomposites. In this technique CNTs are dispersed into the monomer followed by polymerizing the monomers under the reaction conditions (Coleman et al., 2006). This method involves covalent bonding between functionalized nanotubes and the rubber matrix using various condensation reactions (Spitalsky et al., 2010). Higher loading of CNTs could be easily dispersed in this method resulting in a stronger interaction with the rubber matrix. This method is limited to the preparation of rubber nanocomposites that are insoluble in solvent and thermally unstable. In this technique CNTs are first dispersed in the monomer followed by curing the monomer with the corresponding crosslinking agent under certain conditions. A few CNT-rubbery composites have been fabricated using this method and yielded good results. Poly (trimethyleneterephthalate)-block poly (tetra-methyleneoxide) (PTT-PTMO) segmented copolymer and COOH-functionalized SWCNTs were prepared via this technique with uniform dispersion (<0.5 wt%) and enhanced mechanics 0.05–0.3 wt% by Szymczyk (Szymczyk, 2012). Roslaniec et al., 2003 prepared multiblock polyester elastomers (PEE)/CNTs nanocomposites with enhanced mechanical and thermal properties.
Latex stage compounding is a method used to prepare rubber nanocomposites. In this method, the rubber is first converted into latex, which is then mixed with CNTs to form a nanocomposite (Krainoi et al., 2021). Rubber based nanocomposites have been prepared with single-walled carbon nanotubes (SWNTs) via latex stage mixing method. SWNTs are dispersed in water by ultrasonication and stabilized by the subsequent addition of a surfactant. The stabilized aqueous dispersion of SWNTs is mixed with the corresponding rubber lattices. The addition of CNT is expected to enhance the mechanics of the rubber nanocomposites. Tensile strength and modulus of Natural rubber nanocomposite film containing 2.0 phr (parts per hundred parts of rubber) SWNTs were 56% and 63% relative to pure NR. Electrical percolation threshold concentration of SWNTs in NR was found to be 1.5 phr. Thermal stability of NR is unchanged in presence of SWNTs at low concentrations (Anand K et al., 2009).The mechanical properties of NR nanocomposites filled with CNT by latex stage compounding revealed that the addition of CNT affected the strain-induced crystallization of NR, i.e., CNT enhanced the strain-induced crystallization through the interaction of the CNT network and NR chains (Krainoi and Boonkerd, 2022).
Enhancing Performance and Sustainability, the term “interface” in composite materials denotes the boundary that is formed when reinforcing fillers and the matrix come into contact. This interface is crucial for facilitating interfacial bonding, which, in turn, enables the transfer of loads. On the other hand, the “interphase” represents a distinct region characterized by variations in chemistry, polymer chain mobility, degree of cure, and crystallinity index when compared to the filler or matrix. The size of this interphase in CNT-polymer matrix composites is subject to change and has been reported to extend to approximately 500 nm, depending on the size and dimensions of the fillers. Even when the interfacial region is only a few nanometers thick, it can present significant challenges related to achieving uniform dispersion and distribution, ultimately affecting the mechanical stability and overall performance of the composite material (Kim and Mai, 1998). Interface modification plays a pivotal role in optimizing the performance of elastomer nanocomposites, particularly in the context of natural rubber (NR), Nitrile Butadiene Rubber (NBR), and Styrene-Butadiene Rubber (SBR). Recent research highlights the crucial significance of interfacial modification strategies, offering new dimensions of performance enhancement and sustainability in rubber-based materials. Interface modification is the key to unlock the full potential of elastomer nanocomposites. It involves tailoring the interaction between the reinforcing carbon nanotubes and the elastomer matrix, which profoundly influences material properties. The significance of interfacial modification is multifaceted, interface modification enhances the dispersion and adhesion of carbon nanotubes within the rubber matrix. This results in substantial improvements in tensile strength, tear resistance, and modulus, making these materials ideal for applications requiring robust mechanical properties. Interfacial modification contributes to increased oil resistance in NBR-based nanocomposites. This property is invaluable in industries such as automotive, where oil exposure is a common challenge. SBR-based nanocomposites show remarkable enhancement in abrasion resistance, making them well-suited for applications requiring durability, such as tire manufacturing. Interfacial modification not only enhances performance but also contributes to sustainability. By optimizing the properties of these elastomer nanocomposites, we reduce material waste and extend the lifespan of rubber-based products, aligning with the global demand for eco-friendly solutions (Ning et al., 2018).
The types of interfacial modification used in these studies vary based on the specific needs of the elastomer and the desired property enhancements: These modifications not only enhance material properties but also contribute to sustainability by creating durable, eco-friendly materials. The multifaceted benefits of interface modification underline its pivotal role in meeting the growing demand for high-performance and environmentally conscious solutions in various industries. Interfacial modification in composite materials, such as those involving CNTs and natural rubber (NR), styrene-butadiene rubber (SBR), or synthetic rubber, is essential to enhance the compatibility and overall properties of the composite.
Some common types of interfacial modification techniques used in such composite materials:
➢ Chemical Functionalization: Modifying the surface of CNTs through chemical treatments, such as oxidation or functionalization with specific groups (e.g., -COOH, -NH2), can improve their adhesion to the rubber matrix.
➢ Silane Coupling Agents: Silane coupling agents can be used to form chemical bridges between the CNTs and rubber, improving the interfacial adhesion.
➢ In-situ Polymerization: This involves the in-situ formation of a polymer layer on the CNT surface within the rubber matrix. It helps to improve compatibility and dispersion.
➢ Use of Surfactants: Surfactants can be used to disperse CNTs within the rubber matrix and improve their interaction with the polymer.
➢ Plasma Treatment: Plasma treatment of CNTs or the rubber surface can enhance their compatibility by modifying the surface energy and promoting better adhesion.
➢ Nanocomposite Blending: In addition to surface treatments, simply mixing CNTs with rubber during compounding can lead to some degree of interfacial modification. Proper mixing methods and conditions are crucial.
➢ Melt Mixing: Melt mixing involves processing the CNTs and rubber together at an elevated temperature to improve dispersion and adhesion.
➢ Inclusion of Fillers: Other fillers, such as nanoscale inorganic particles, can be added to enhance the interaction between CNTs and the rubber matrix.
➢ Electrostatic Adsorption: Electrostatic forces can be utilized to enhance the dispersion of CNTs within the rubber matrix.
➢ Layer-by-Layer Assembly: This technique involves the layer-by-layer deposition of oppositely charged polyelectrolytes on CNTs, which can improve their compatibility with the rubber matrix.
➢ Functionalized Rubber Polymers: Using rubber polymers with functional groups compatible with CNTs can improve their interfacial compatibility.
➢ The specific choice of interfacial modification method depends on the desired properties of the composite, the nature of the rubber (NR, SBR, etc.), and the intended application. Experimentation and testing are often required to determine the most effective modification technique for a particular composite.
The multifaceted benefits of these interface modification strategies extend beyond property enhancement, encompassing sustainability and the development of durable materials. This aligns with the growing demand for eco-friendly and high-performance materials in various industries. These advancements pave the way for the development of high-performance, eco-friendly materials with diverse applications across industries. In a study conducted by Ni et al. the objective was to engineer the interface between multi-walled carbon nanotubes (MWCNTs) and natural rubber (NR). This was achieved through a two-step process, involving the use of a silane coupling agent known as bis(3-triethoxysilylpropyl) tetrasulfide (TESPT) to modify the surface of MWCNTs. Subsequently, the silane-modified MWCNTs (s-MWCNTs) were incorporated into the NR matrix through a solvent casting method (Jiang et al., 2011).
CNT-reinforced rubber nanocomposites are a promising class of materials with enhanced mechanical properties. The strength of bonding due to which CNTs are incorporated to polymers plays a significant role in enhancing the mechanical properties of CNT. High aspect ratio of CNTs positively contribute towards the enhancement of mechanical properties of CNT-elastomer composites (Arash et al., 2014). Morphological characteristics of CNTs like their ratio significantly influences the mechanical properties of CNT filled rubber composites. Effective dispersion of CNTs into polymer matrix can be done by functionalization of CNTs. The functionalization can be either covalent or non-covalent. Large surface area of CNTs can provide better interphase spacing between CNTs and polymer matrix which will enhance the mechanical properties. The process of synthesizing CNT filled rubber composites affects the enhancement of mechanical properties. One of the most efficient methods to develop CNT-rubber composites with enhanced mechanical properties are melt mixing method. In brief, fabrication of CNT filled elastomeric composites improve the mechanical properties than the pristine polymer. The properties depend upon the load transfer capability of CNTs, proper surface modification, and the method of dispersion of CNTs in polymer matrix (Dang et al., 2011).
CNTs have exceptional tensile strength, stiffness, and electrical conductivity. CNT alignment can be achieved through various methods, such as mechanical stirring, magnetic field alignment, and electric field alignment. CNT-reinforced rubber nanocomposites have a wide range of potential applications in industries such as automotive, aerospace, and sports. For example, CNT-reinforced rubber tires can offer improved fuel efficiency, traction, and wear resistance. CNT-reinforced rubber aircraft components can provide lightweight and durable materials with enhanced mechanical properties. CNT-reinforced rubber sports equipment can offer improved performance and durability. A significant amount of research has been focused on developing polymer composites reinforced with carbon nanotubes for both functional and structural applications. Despite their potential, the use of CNTs as reinforcements in composites faces challenges. One significant challenge is the difficulty in achieving uniform dispersion of entangled CNTs within the polymer matrix during the manufacturing process. This dispersion issue is more complex compared to conventional fillers like spherical particles and carbon fibers. CNTs have unique properties, including nanometer-scale dimensions and extremely high aspect ratios (greater than 1000). These properties result in an exceptionally large surface area for CNTs. The distribution behavior of fillers in a polymer matrix is strongly influenced by their size and geometry. Micro-scale fillers are evenly distributed throughout the matrix, while CNTs, due to their nanometer-scale properties, do not disperse easily and uniformly within the matrix. The interphase in CNT-polymer matrix composites can be relatively large, up to approximately 500 nm, depending on the size and dimensions of the CNT fillers. Even if the interfacial region is only a few nanometers thick, it can significantly impact the dispersion and distribution of CNTs in the matrix, ultimately affecting the mechanical stability and performance of the composite (Jian and Lau, 2020). Table 1 consolidates the enhancement of different mechanical properties of CNT filled rubber nanocomposites.
A crucial aspect of achieving enhanced mechanical properties in CNT-reinforced rubber nanocomposites is the proper dispersion of CNTs within the rubber matrix. Various dispersion methods, including solution along with their impacts on the final nanocomposite’s mechanical properties. Carbon nanotubes when incorporated into elastomer matrices, can enhance the mechanical properties of the resulting composites. Recent experimental studies have provided valuable insights into the synergistic effects of CNT loading, dispersion, and alignment on the tensile properties and Young’s modulus of various rubber nanocomposites (Mensah et al., 2015). The mechanical properties of CNT-reinforced polymer composites can be significantly enhanced through various functionalization techniques, including both physical and chemical approaches, aimed at improving CNT dispersion and optimizing the CNT interface within the matrix. These strategies contribute to strengthening the interfacial bonding between the CNT reinforcements and the matrix constituents in the composite system. Chemical modification, for instance, plays a vital role in enhancing CNT dispersion and solubility in solvents or polymers, consequently enhancing interaction and reactivity with the matrix through mechanisms such as hydrogen bonding. Many works have been reported where the property of the CNT polymer nanocomposite has been enhanced through various functionalization techniques, including both physical and chemical approaches, aimed at improving CNT dispersion and optimizing the CNT interface within the matrix (Nurazzi N. M. et al., 2021). This chemical treatment often involves the use of strong acids to remove CNT end caps and reduce their length. Oxygenated functional groups, such as carboxylic acids, carbonyl, and hydroxyl groups, are introduced at the tube ends and defect sites of the CNTs during acid treatment. These oxygen-containing groups can undergo further modification with other functional groups, such as amides and thiols (Bahun, 2006). As Norizan et al. highlighted, incorporating chemically functionalized CNTs into the polymer matrix can significantly improve the mechanical properties of CNT-reinforced polymer composites. This approach enables covalent bonding between single-walled carbon nanotubes (SWCNTs) and multi-walled carbon nanotubes (MWCNTs). Chemical functionalization contributes to enhancing the interface between CNTs and the polymer matrix, thereby increasing interfacial strength and improving the load transfer mechanism to the CNTs (Nurazzi NorizanM. et al., 2021).
Understanding the mechanisms behind the mechanical property enhancements in CNT-elastomer composites is essential. Load transfer, percolation, CNT alignment, and dispersion are key factors influencing these properties. The underlying mechanisms that contribute to these improvements include.
➢ Tensile strength enhancement-The incorporation of CNTs into elastomer matrices significantly enhances the tensile strength and modulus of the resulting composite. CNTs possess exceptional tensile strength, often reaching several gigapascals, and act as effective load-bearing agents, leading to improved tensile properties.
➢ Modulus enhancement- CNTs also contribute to modulus enhancement, toughness improvement and fatigue resistance. Fatigue resistance is a critical mechanical property for materials subjected to cyclic loading. CNT-elastomer composites show improved fatigue resistance due to the load transfer capabilities of CNTs and their ability to dissipate energy during cyclic deformation. The fatigue resistance of materials is a critical consideration, especially in applications subject to cyclic loading and deformation. It is the ability of a material to withstand cyclic loading and deformation without experiencing premature failure. In many applications, such as flexible electronics, biomedical devices, and structural components, materials are subjected to repetitive mechanical stresses. Understanding and improving fatigue resistance are essential for ensuring the longevity and reliability of such materials. Several key mechanisms contribute to the enhanced fatigue resistance observed in CNT-elastomer systems like Load Transfer and Reinforcement, Energy Dissipation, Crack Bridging etc., The enhanced fatigue resistance of CNT-elastomer systems are reported in numerous experimental studies. Through measurements of fatigue life, crack propagation rates, and other relevant parameters, researchers have consistently demonstrated the beneficial effects of CNT reinforcement in elastomers. Carbon nanotube-elastomer composites exhibit remarkable fatigue resistance due to several key mechanisms, including load transfer, energy dissipation, and crack bridging. This enhanced fatigue resistance has significant implications for various applications, where materials must endure repetitive mechanical stresses. The experimental evidence supports the effectiveness of CNT reinforcement in improving fatigue performance.
➢Percolation threshold in CNT/rubber systems: The enhancement of tensile properties is particularly pronounced around the percolation threshold, a critical CNT concentration. Below this threshold, CNTs are not interconnected, limiting their reinforcement effect. However, beyond the threshold, a network of CNTs forms, resulting in a significant increase in tensile strength and modulus.
➢ Alignment and dispersion of CNTs in rubber matrices: Proper alignment and dispersion of CNTs within the elastomer matrix play a crucial role in maximizing the enhancement of modulus. Well-aligned and well-dispersed CNTs create efficient load transfer networks, yielding higher modulus values.
➢ Choice of rubber matrix: The choice of elastomer matrix also influences the tensile properties of CNT/elastomer composites. Different elastomers have varying inherent stiffness levels, contributing to the final modulus of the composite (Adamska and Narkie, 2017). Their high intrinsic strength and ability to transfer loads effectively to the elastomer matrix lead to enhanced tensile properties. The reinforcement mechanism involves load-bearing by CNTs and prevention of crack propagation.NR is known for its exceptional elasticity and high elongation at break.
In a work reported by Das et al. the study reports about the preparation of MWCNT containing rubber nanocomposites with a very low loading of carbon nanotubes by a novel technique. In this technique predispersed ethanol mixtures of carbon nanotubes were mixed with rubber blends at elevated temperature using a two-roll mixing mill. In the mixing mill the ethanol vaporises and, simultaneously, the CNTs can be impregnated into the rubber matrix. The rubber matrix is a 50/50 blend of solution-styrene–butadiene rubber (S-SBR) and polybutadiene rubber (BR).
Infrared spectroscopy can be used to get the structural characteristics of polymer nanocomposites from their vibrational properties. Analysis of vibrational spectrum provide information about functional groups on polymer and filler particles, filler dispersion and functionalization, the degree of orientation of both the polymer chains and the reinforcing material (Bokobza, 2017). Muroga et al., 2021 used In-Situ ATR-FTIR Spectroscopy and spectroscopic imaging for real-time simultaneous monitoring of curing reaction and diffusion of the curing agent at fluorine rubber (FKM) nanocomposite surface. The increase and broadenings of the C=O stretching band of the triallyl-isocyanurate (TAIC) curing agent suggested that the reaction rate at the surface was quicker than that of the bulk due to the diffusion and condensation of curing agent at the surface during heating. Results from cross-sectional ATR-FTIR imaging showed the curing agent’s unidirectional migration towards the heated surface of the FKM sample. Additionally, in situ ATR-FTIR imaging revealed that the curing agent did not disperse from the cured condition, indicating that the diffusion stopped once the curing was complete.
Raman spectroscopy is a powerful non-destructive technique to characterize carbon-based materials such as, CNT, carbon black, graphene, etc. It is possible to understand all fundamentals about sp2 carbon atoms in CNT, defects in CNT and the nanotube-nanotube interactions. In CNT/rubber nanocomposites, Raman spectroscopy is used to evaluate the state dispersion of CNT in rubber matrix as well as extent of filler rubber interaction. Bokobza et al. investigated the thermal effects caused by incident laser on the Raman spectrum of CNT/Styrene-Butadiene Rubber (SBR) nanocomposites. Downshifts of D and G frequencies are observed with increased laser power irradiation. By altering the laser excitation’s wavelength, significant impacts are seen. On the other hand, changes in the Raman bands at a specific excitation wavelength are seen by adjusting the laser power density as a result of sample heating during the measurement process (Bokobza and Zhang, 2012). Raman spectroscopy was used to investigate the interfacial interactions between the rubber chains and MWCNTs. Coupling activity of ionic liquids between diene elastomers and multi-walled carbon nanotubes is explored by Das et al., 2009 Here the presence of ionic liquid leads to a shift in the position of G band towards high frequency side. This upward shift is because of the disentanglement of CNT and the improved interaction between CNT and rubber matrix in presence of ionic liquid. Azira et al., 2012 studied the effect of CNT loading on the position of G band in the Raman spectrum of multi-Walled Carbon Nanotubes/Natural Rubber Nanocomposite by wet mixing method. There is a shift in the position of G band for each loading of CNT and this is due to the stress transfer from the matrix to the nanotubes and hence indicates reinforcement of the MWCNTs in the rubber matrix.
Incorporation of nanomaterials into rubber significantly improves the mechanical, thermal, and electrical properties of elastomers. Among the different nanomaterials, carbon nanotubes (CNTs) are found to be potential candidates for improving the electrical properties of rubbers. Incorporation of CNTs into natural rubber not only improves the strength, modulus and hardness but also modifies the electrical conductivity of the composites. Research shows that the efficiency of CNTs is much more superior than that of the carbon black nanomaterials. Easiness of dispersing CNTs can effectively form conducting-pathways. Extent of dispersion of CNTs into the polymer matrix can be described by the solubility parameter. It explains the degree of interaction between materials. A matching solubility parameter between CNTs and polymer is important to achieve lower percolation threshold and high conductivity. Research shows that fluorinated rubber gives a matching solubility parameter with CNTs and thus the resulting composites possess improved electrical conductivity (Ata et al., 2014). The lower percolation threshold value of CNT in elastomer matrix than other nanomaterials is evident, and it makes superior CNT-elastomeric rubber composites to provide superior electrical properties (Balasubramanian and Jawahar, 2019). Studies have shown that a very small volume fraction, say 0.13 of CNT can provide a dielectric permittivity (Ɛ) of 9,000 to the elastomer composites. This value is about 2400 folds higher than that of the pristine elastomer. The reason for this drastic change is the interfacial polarization at the interface of elastomer and CNTs (Shehzad et al., 2015). In rubber- CNT nanocomposites, quantum mechanical tunnelling of electrons occurs between neighbouring CNTs. However, CNTs separated by a thin polymer layer limits the dc conductivity of the CNT network. Thus, a transition from tunnelling to thermal activated hopping need to be taken place to provide better conductivity (Klüppel, 2003). Natural rubber and styrene-butadiene rubber (SBR)-CNT nanocomposites can be prepared at varying filler compositions, say 0–20 phr and the resulting composites exhibit tremendous increase on the electrical conductivity (Bernal-Ortega et al., 2020). Tsuchiya et al., 2011 reported the synthesis of SBR-MWCNT elastomer composite by a novel rotation-revolution method. The resulting composites showed a significant improvement in electrical properties. It is observed that the electrical conductivity of lower loading of MWCNTs depends directly upon frequencies. The conductivities of composites also increase with increase in CNT loading. CNTs form a continuous percolating network in the polymer matrix and hence the composites typically behave as an Ohmic conductor. The electrical permittivity of the composites is found to be independent of the frequency at lower frequency region and increases with increase in concentration of MWCNTs. A comparative study among different types of CNTs (MWCNTs, SWCNTs, etc.,) as fillers are also done with the above composites. For all fillers, the ohmic conductance and dielectric relaxation is much higher at a lower percolation threshold. The conductivity of the composites increased dominantly above the percolation threshold of filler particles. The material behaves as a perfect ohmic conductor whose conductivity is independent of frequency when it contains 3–5 phr of CNT loading (Das et al., 2008).
MWCNTs can be effectively incorporated with silicone rubber by mechanical mixing method. It is seen that the volume resistivity of the prepared composites decreases with increase in CNT loading. When the filler concentration increases, more conducting paths are developed in the polymer matrix which leads to the decrease in electrical resistivity (Katihabwa et., 2011).
Modifications on CNTs can further improve the electrical properties of composites. Li et al., 2020 reported CTAB-functionalized CNT/Natural rubber (NR) composites and the resulting flexible material possesses high EMI shielding persisting and shielding stability. This is because the presence of CTAB along with CNTs provides more conduction pathways and produces better filler-matrix interfaces (Jia et al., 2017). Another material that is used to functionalize CNTs is chitosan. Chitosan modified CNTs can be used to reinforce SBR rubber, and the resulting composites exhibit extremely superior electrical conductivity properties without losing its mechanical properties (Shang et al., 2014). Ionic liquids can also be used to improve the electrical properties of CNT-rubber composites. An imidazolium type ionic liquid (IL) can be mixed with CNTs and incorporated to polychloroprene rubber by melt mixing. Ionic liquid considerably modifies relaxation behaviour of the pristine rubber and leads to increase of the conductivity for the CNT/rubber composites. Ionic liquids offer better dispersion of the CNTs into the polymer matrix (Steinhauser et al., 2012). A liquid metal (LM) like eutectic gallium indium can be incorporated with CNT-rubber composites to improve the electrical and mechanical properties. The prepared material shows improved conductivity by about 328% at 10 vol% of liquid metals without changing mechanical properties. After that, the conductivities are found to get decreased. This may be due to the interference of LMs into the network of CNTs. A polymer like poly (methyl methacrylate) (PMMA) can be blend with natural rubber (NR) and can be incorporated with CNTs which provide improved electrical conductivities. PMMA helps to lower the concentration of CNTs. It is found that for the same amount of MWCNTs, the conductivity of PMMA-NR/MWCNT composite is higher than that of NR/MWCNT composite. Further increase in CNTs can tremendously enhances the conductivity which indicates the formation of conductive networks in NR and PMMA-NR matrices (Salaeh et al., 2020).
Thermal stability of the material is crucial since the spectrum of applications of rubber nanocomposites increases with increased temperature. Research on incorporating thermally stable fillers in the elastomer matrix is conducting frequently. CNT surface can scavenge radical species, and this radical scavenging restricts the chain reaction of polymer degradation (Ata et al., 2017). Numerous studies have been reported on the high thermal stability of CNT elastomer nanocomposites as compared with virgin elastomer.
Dispersibility of CNT in rubber matrix has a significant role in improving the thermal stability of rubber nanocomposites. Shimizu et al., 2020 explored the improved thermal stability of silicone rubber nanocomposites containing well dispersed CNT. Three dispersion methods were tried, direct mixing of CNT with silicone rubber, ultrasonication and wet jet milling. High thermal stability was achieved at 0.5wt% CNT by using the appropriate dispersion method (wet jet milling). Thermal ageing studies have shown that CNT/silicone rubber nanocomposites made using the proper dispersion method may maintain rubbery elasticity after 7 days at 280°C, but virgin silicone rubber becomes embrittled at this temperature just after 1 day.
Surface modification of CNT by acid treatment imparts high thermal stability to CNT filled natural rubber nanocomposites. This is due to the positive effect on CNT dispersion and CNT rubber interfacial interaction after surface modification (Shahamatifard et al., 2023). Large number of investigations have been done on exploring the improved thermal properties of rubber composites by the introduction of functionalized CNT (Atieh, 2011). Subramaniam et al., 2011 studied the thermal degradation of polychloroprene rubber (CR) composites based on unmodified and ionic liquid modified multi-walled carbon nanotubes (MWCNTs) by Thermogravimetric analysis. The enhanced thermal stability of ionic liquid modified CNT based CR nanocomposites because of the interfacial interactions of ionic liquid/modified tubes with CR and the well dispersion of modified CNT in CR matrix.
The unusual high thermal conductivity of CNT makes it as an attractive candidate for fabricating rubber nanocomposites with high thermal conductivity. Katihabwa et al., 2011 studied the effect of CNT loading on the thermal conductivity of silicone rubber nanocomposites prepared by high shear mechanical mixing. It was found that both thermal stability and thermal conductivity substantially improved with CNT loading. Here presence of CNT reduces the thermal degradation of rubber because of the barrier effect as well as decreased polymer chain mobility in presence of CNT. The high thermal conductivity of nanocomposites is because of the high charge transport rate through the channels in CNT. The effect of CNT alignment on the thermal conductivity of natural rubber (NR) is explored by Gao et al. (2017) An AC electric field is applied to induce the orientation and promote the dispersion of CNT. NR composites with aligned CNT have high thermal conductivity as compared with composites with random CNT. This is because of the anisotropy of heat conduction along CNTs axis and a better dispersion of CNTs (Gao et al., 2018).
CNT based nanocomposites possess unique properties and are very promising candidates. They found applications in several fields. Incorporation of CNTs into polymer matrix can improve the mechanical and physical properties of composites. The resulting nanocomposites have high surface area and have small and high-volume pores. It possesses characteristic features like flexibility, stretchability, conductivity and the quality or condition of being strong (Chinnappan et al., 2016). The elastomeric polymer nanocomposites with enhanced properties found applications in several fields and summarized in Figure 5.
The characteristic features that a sensor should possess include low detection limit, high sensitivity, reproducible results, ambient operational conditions, fast response, cost effectiveness and causing no environment hazards. Physical sensors are used to sense stimuli like strain, pressure, and temperature whereas chemical sensors sense the presence of chemical constituents. CNT-elastomer composites-based materials made a breakthrough in the production of stretchable sensors and found applications in various sectors (Pandey et al., 2013). Mainly, physical sensors which can sense properties like change in pressure, strain and temperature can be made utilizing these CNT-elastomeric nanocomposites.
Strain sensors are used to convert mechanical deformations into electrical signals. Strain sensors have found superior applications in various sectors. These include applications in personal healthcare products, robotics, human machine interface and so on. Strain sensors based on CNT nanocomposites possess high stretchability. Several elastomeric polymers can be incorporated to CNT to exhibit wearable sensing applications. Polydimethylsiloxane (PDMS) polymer can be made composites with CNTs through a simple polymerization technique like spin coating and the resulting composites are very stretchable and the method of production is cost effective too. These materials found applications on human skin for skin mountable sensing applications (Nankali et al., 2021). Studies have shown that the efficiency of resulting PDMS-CNT elastomeric nanocomposite highly depend upon factors like temperature. These materials show exceptionally good sensors to track the changes in human body movements and can be used for healthcare inspection. Ecoflex is a type of silicone-based elastomer which found in medical implants and specially functionalised masks. Impregnation of CNTs into Ecoflex forms wearable devices which are biocompatible. These composites found to have high conductivity and experiments were carried out to demonstrate the Joule heating effect. It is seen that a high conductivity is developed in Ecoflex-CNT composites due to Joule heating. The conductivity of the composites was analysed using current-voltage curves. This can find applications in Joule heating devices and tactile sensors which measures information arising from physical interaction with its environment. In human machine interface devices like arm heating devices and touch sensitive sensors, these composites are widely used (Noh and Song, 2022). Well dispersed polymer matrix of SWCNTs (Single walled carbon nanotubes) on vinylidene fluoride-hexafluoropropylene copolymer also produces elastomeric composites with sensing applications. Tsuyoshi Sekitani et al. reported that the polymerization technique is carried out in presence of ionic liquids like 1-butyl-3-methyl imidazolium bis (trifluoromethylsulphonyl)imide. Fluorine rubber-single walled CNT composites produce a pressure-sensitive rubber (PSR). Addition of foaming agent can create porous structures. The resultant composite can withstand a punch pressure of −120 kPa and the time intervals between punches can be also recorded. This shows the possibility of applying these composite materials on force detections or computer game applications (Hsiao et al., 2019). SBR modified with an organic semiconductor like metal free phthalocyanine can be incorporated with CNT and it forms a sandwich-type material. The material can act as shockproof deformable infrared radiation (IR) sensors. The appropriate ratio of SBR and CNT make the devices suitable for bolometric applications (Chani et al., 2023). CNTs can be dispersed to the polymer elastomeric matrix using suitable surfactants. Studies confirm the use of multi-walled carbon nanotubes (MWCNTs) incorporated isoprene rubber composites in oil sensors. Oil sensors effectively sense oil spillage, and it is found that the extent of filler-polymer interactions highly influences the oil detecting capacity of the sensors (Ponnamma et al., 2016). Figure 6 gives an experimental setup which uses elastomer-CNT as a material for oil sensing applications.
Figure 6. Experimental setup for oil sensing on interdigitated electrodes with polyethylene substrate.
Natural rubber (NR) can act as a host for accommodating CNTs (both SWCNTs and MWCNTs) and the formed composites possess a low specific weight. It will be utilized as a prosthetic material for making prosthetic foot for amputees. The addition of MWCNTs in right proportion to the NR make the material to possess high tensile strength, optimum stability and found to be ecofriendly too. The water absorption capacity of CNT-NR composite was found to be ∼0.1%. The material also possesses exceptionally good wear resistance (Medupin et al., 2019).
SWCNT-rubber and graphene-rubber polymer nanocomposites are found to possess wide range of biomedical applications which includes monitoring movements in finger and wrist, analysing carotid pulse and breathing pattern and muscle motion during speech (Abubakre et al., 2023). Other elastomeric systems that are used in animal studies are silicones, fluoro silicones and Poly (styrene-butadiene-styrene). Improvement in corrosion resistance and stability, materials like CNTs are incorporated (Llerena Zambrano et al., 2021).
Reinforcing carboxylated nitrile rubber (XNBR) with CNTs results in composites with excellent shape fixation and shape recovery in progressive cycles. Thus, these materials are widely used as shape memory materials in biomedical fields like general medicine, drug delivery, neuromedicine, orthopedics, regenerative medicine and dentistry (Rokaya et al., 2023). CNT sheets which is wrapped on the stretched styrene (ethylene-butylene)-styrene (SEBS) creates highly stretchable conductive fibers. The resultant composites are also widely used in bio medical fields (Wei et al., 2023). CNT-biomaterial scaffolds are utilised in cardiac tissue regeneration too (Ahadian et al., 2017).
The need for sustainable energy resources is increasing day by day since energy scarcity is experiencing in different parts of the world nowadays. Renewable energy resources like solar energy, energy harvesting methods utilizing piezoelectric materials, thermos electric materials, etc., are of paramount importance in the present era. Polymeric materials are widely utilized for synthesizing different energy harvesting systems. For the development of portable, concise, and unique energy harvesting systems requires the presence of stretchable materials. The insulating properties of polymeric materials can be improved by incorporating nanomaterials like CNTs. CNT based elastomeric materials can be used to fabricate electrodes in batteries and supercapacitors and they exhibit stable electrochemical performance at low strains. The fabrication methods are quite complex and therefore special care should be taken (Li et al., 2021). Development of stretchable acrylate rubber (ACM)/MWCNT electrodes in supercapacitors was reported. The prepared nanocomposites exhibited good stretchability (155%) and conductivity (9.6 S cm−1) at appropriate composition of MWCNT. Another important electrode material for supercapacitors from CNT/poly (dimethylsiloxane) (PDMS) materials were also synthesized (Chen et al., 2014). Nanogenerators are synthesized using CNT elastomer based composites. For example, a nanogenerator is synthesized using PDMS–CNT composite as the bottom electrode. The composites are very stretchable, but the output power was not large (Lee et al., 2014). Synthesis of highly stretchable elastic generator is made possible by incorporating a mixture of MWCNTs dispersed in a silicone rubber and modified by titanates like lead titanate (Jeong et al., 2015). Figure 7A shows the picture of hyper stretchable nanocomposite generator made by incorporating lead magenesio-lead titanate to silicone rubber -CNT nanocomposites. Figure 7B confirms the stretchability of the materials (Noh, 2016).
Figure 7. (A) Schematic picture of the hyper-stretchable nanocomposite generator (SEG) (B) SEG can be stretched and released without damage (C) Generated (i) open-circuit voltage and (ii) short circuit current depending on periodic stretching–releasing cycles at a strain of 200%.
CNT-rubber elastomeric composites are widely applied in EMI shielding applications. Styrene-butadiene rubber (SBR) which is a cost effective synthetic rubber with a suitable ionic liquid embedded MWCNT is reported to possess a shielding effectiveness of 35.06 dB @ 18 GHz. The shielding effectiveness is monitored using a vector network analyser (Abraham et al., 2017). CNTs of different ratios can be effectively incorporated to natural rubber and chlorobutyl rubber to produce materials with superior EMI shielding applications. Studies have shown that the material possess EMI shielding effectiveness of 59 dB at maximum composition of CNTs (Muringayil Joseph et al., 2022). Figure 8 shows diagrammatic representation of the EMI shielding efficiency of SBR- MWCNT composites (Abdeldaym and Elhady, 2022). Single-walled carbon nanotubes as fillers can be introduced to fluorinated rubber and the material exhibits electromagnetic interference (EMI) shielding. This flexible material of suitable thickness could decrease more than 90% of the strength of incident electromagnetic waves (Kato et al., 2017). Abdeldaym et al. investigated the Gamma rays shielding applications of natural rubber latex reinforced with multiwall carbon nanotubes. From the values of linear attenuation coefficients (L) and half-value thickness for NRL/MWCNTs nanocomposite it was concluded that the fabricated material offers promising radiation-shielding properties (Abdeldaym and Elhady, 2022). Several elastomeric polymers - CNT composites were developed to make them a potential candidate for EMI shielding applications as listed in Table 2.
Multi-walled carbon nanotubes (MWCNTs) incorporated styrene-co-butadiene-costyrene (SBS) triblock copolymer matrix possess extremely high elastic and conductive properties. These materials act as superior piezoresistive sensors. They found applications in wearable electronics and computers (Duan et al., 2017).
Rubber-CNT-based nanocomposites are promising candidates for widespread applications in various fields. Properties like thermal and electrical stability made them be applied in oil/fuel hoses and gaskets and microwave, structural applications in the aerospace industry (Mensah et al., 2015). Similarly, dispersing CNT in silicone resin, can develop materials of high water-repellency. These materials were planned to implement as roofing material resistant to snow build-up in regions of high snowfall (Ata et al., 2017).
Addition of CNT to tyres was another experimental breakthrough. CNTs are incorporated with rubbers and the resulting composites were made as tyres. The product exhibited wear resistance, fuel economy and traction control. These factors are credibly influenced by the ratio of CNTs added. It is found that addition of CNT does not change the elasticity of rubber notably. But more studies are required for studying the safety evaluation angle (Nakaramontri et al., 2017).
Carbon nanotube (CNT) filled rubber nanocomposites are materials that combine rubber with carbon nanotubes to enhance their properties. When these two materials are combined, they create a nanocomposite that offers improved mechanical, electrical, thermal, and other properties. Reinforcement of rubber matrices using CNTs can be done using the methods like solution mixing, mechanical mixing, in-situ polymerization, and latex stage compounding. More techniques must be designed to ensure the homogeneous dispersion of CNTs into the rubber matrix. Functionalization of CNT improves the dispersion of CNT and the interfacial interaction between CNT and the rubber matrix. The elastomeric CNT nanocomposites with enhanced properties found applications in several fields such as electronics, sustainable biomedical and EMI shielding, etc.
NK: Writing–original draft, Writing–review and editing. JA: Writing–original draft, Writing–review and editing. MT: Writing–original draft, Writing–review and editing. HV: Writing–original draft, Writing–review and editing. HM: Writing–original draft, Writing–review and editing. ST: Writing–original draft, Writing–review and editing.
The author(s) declare that financial support was received for the research, authorship, and/or publication of this article. DBT-STAR College Scheme, Department of Biotechnology, Govt. of India (No. 102/IFD/ SAN/3988/201-20) dated 29.02.2020.
The authors declare that the research was conducted in the absence of any commercial or financial relationships that could be construed as a potential conflict of interest.
All claims expressed in this article are solely those of the authors and do not necessarily represent those of their affiliated organizations, or those of the publisher, the editors and the reviewers. Any product that may be evaluated in this article, or claim that may be made by its manufacturer, is not guaranteed or endorsed by the publisher.
Abdeldaym, A., and Elhady, M. A. (2022). Preparation and assessment of nanocomposites based on natural rubber latex reinforced with multiwall carbon nanotubes for Gamma rays shielding applications. J. Compos. Mater. 56 (27), 4183–4193. doi:10.1177/00219983221121870
Abousalman-Rezvani, Z., Eskandari, P., Roghani-Mamaqani, H., and Salami-Kalajahi, M. (2020). Functionalization of carbon nanotubes by combination of controlled radical polymerization and “grafting to” method. Adv. Colloid Interface Sci. 278, 102126. doi:10.1016/j.cis.2020.102126
Abraham, J., Arif P, M., Xavier, P., Bose, S., George, S. C., Kalarikkal, N., et al. (2017). Investigation into dielectric behaviour and electromagnetic interference shielding effectiveness of conducting styrene butadiene rubber composites containing ionic liquid modified MWCNT. Polymer 112, 102–115. doi:10.1016/j.polymer.2017.01.078
Abraham, J., Kailas, L., Kailas, L., Kalarikkal, N., George, S. C., and Thomas, S. (2016). Developing highly conducting and mechanically durable styrene butadiene rubber composites with tailored microstructural properties by a green approach using ionic liquid modified MWCNTs. RSC Adv. 6 (39), 32493–32504. doi:10.1039/c6ra01886f
Abraham, J., Thomas, J., Kalarikkal, N., George, S. C., and Thomas, S. (2018). Static and dynamic mechanical characteristics of ionic liquid modified MWCNT-SBR composites: theoretical perspectives for the nanoscale reinforcement mechanism. J. Phys. Chem. B 122 (4), 1525–1536. doi:10.1021/acs.jpcb.7b10479
Abubakre, O. K., Medupin, R. O., Akintunde, I. B., Jimoh, O. T., Abdulkareem, A. S., Muriana, R. A., et al. (2023). Carbon nanotube-reinforced polymer nanocomposites for sustainable biomedical applications: a review. J. Sci. Adv. Mater. Devices 8, 100557. doi:10.1016/j.jsamd.2023.100557
Adamska, M., and Narkiewicz, U. (2017). Fluorination of carbon nanotubes− a review. J. Fluor. Chem. 200, 179–189. doi:10.1016/j.jfluchem.2017.06.018
Ahadian, S., Davenport-Huyer, L., Smith, N., and Radisic, M. (2017). Hybrid carbon nanotube-polymer scaffolds for cardiac tissue regeneration. Microfluid. BioMEMS, Med. Microsystems XV, 10061. SPIE, 11–19.
Akpan, E. I., Shen, X., Wetzel, B., and Friedrich, K. (2019). “Design and synthesis of polymer nanocomposites,” in Polymer composites with functionalized nanoparticles (Elsevier), 47–83.
Anand K, A., Jose T, S., Alex, R., and Joseph, R. (2009). Natural rubber-carbon nanotube composites through latex compounding. Int. J. Polym. Mater. 59 (1), 33–44. doi:10.1080/00914030903172916
Arash, B., Wang, Q., and Varadan, V. K. (2014). Mechanical properties of carbon nanotube/polymer composites. Sci. Rep. 4 (1), 6479. doi:10.1038/srep06479
Ata, S. (2017). Features and application of carbon nanotube and rubber composites. Int. Polym. Sci. Technol. 44 (8), 33–38. doi:10.1177/0307174x1704400807
Ata, S., Mizuno, T., Nishizawa, A., Subramaniam, C., Futaba, D. N., and Hata., K. (2014). Influence of matching solubility parameter of polymer matrix and CNT on electrical conductivity of CNT/rubber composite. Sci. Rep. 4 (1), 7232. doi:10.1038/srep07232
Ata, S., Tomonoh, S., Yamda, T., and Hata, K. (2017). Improvement in thermal durability of fluorinated rubber by the addition of single-walled carbon nanotubes as a thermally stable radical scavenger. Polymer 119, 112–117. doi:10.1016/j.polymer.2017.05.025
Atieh, M. A. (2011). Effect of functionalize carbon nanotubes with amine functional group on the mechanical and thermal properties of styrene butadiene rubber. J. Thermoplast. Compos. Mater. 24 (5), 613–624. doi:10.1177/0892705710397456
Azira, A. A., Hassim, D. H. A. I., Suriani, A. B., Mahmood, M. R., and Mohamad Rusop, M. (2012). Characterization of multi-walled carbon nanotubes/natural rubber nanocomposite by wet mixing method. Nano Hybrids 1, 81–97. doi:10.4028/www.scientific.net/nh.1.81
Bahun, G. J., Wang, C., and Adronov, A. (2006). Solubilizing single-walled carbon nanotubes with pyrene-functionalized block copolymers. J. Polym. Sci. Part A Polym. Chem. 44 (6), 1941–1951. doi:10.1002/pola.21308
Bai, Lu, Bai, Y., and Zheng, J. (2017). Improving the filler dispersion and performance of silicone rubber/multi-walled carbon nanotube composites by noncovalent functionalization of polymethylphenylsiloxane. J. Mater. Sci. 52, 7516–7529. doi:10.1007/s10853-017-0984-y
Balasubramanian, M., and Jawahar, P. (2019). Rubber—CNT nanocomposites. Adv. Nanostructured Compos. Vol. 1, 295–314. Carbon Nanotube and Graphene Composites. doi:10.1201/9781315118406-13
Bernal-Ortega, P., Bernal, M. M., González-Jiménez, A., Posadas, P., Navarro, R., and Valentín, J. L. (2020). New insight into structure-property relationships of natural rubber and styrene-butadiene rubber nanocomposites filled with MWCNT. Polymer 201, 122604. doi:10.1016/j.polymer.2020.122604
Bilalis, P., Katsigiannopoulos, D., Avgeropoulos, A., and Sakellariou, G. (2014). Non-covalent functionalization of carbon nanotubes with polymers. RSC Adv. 4 (6), 2911–2934. doi:10.1039/c3ra44906h
Bokobza, L. (2017). Spectroscopic techniques for the characterization of polymer nanocomposites: a review. Polymers 10, 7–1. doi:10.3390/polym10010007
Bokobza, L., and Zhang, J. (2012). Raman spectroscopic characterization of multiwall carbon nanotubes and of composites. Express Polym. Lett. 6, 601, 608. doi:10.3144/expresspolymlett.2012.63
Chani, M. T. S., Karimov, K. S., Kamal, T., Fatima, N., Rahman, M. M., and Asiri, A. M. (2023). Shockproof deformable infrared radiation sensors based on a polymeric rubber and organic semiconductor H2pc-CNT composite. Polymers 15 (12), 2691. doi:10.3390/polym15122691
Chen, T., Peng, H., Durstock, M., and Dai, L. (2014). High-performance transparent and stretchable all-solid supercapacitors based on highly aligned carbon nanotube sheets. Sci. Rep. 4 (1), 3612. doi:10.1038/srep03612
Chen, Y., Haddon, R. C., Fang, S., Rao, A. M., Eklund, P. C., Lee, W. H., et al. (1998). Chemical attachment of organic functional groups to single-walled carbon nanotube material. J. Mater. Res. 13 (9), 2423–2431. doi:10.1557/jmr.1998.0337
Chinnappan, A., Baskar, C., Kim, H., and Ramakrishna, S. (2016). Carbon nanotube hybrid nanostructures: future generation conducting materials. J. Mater. Chem. A 4 (24), 9347–9361. doi:10.1039/c6ta01717g
Coleman, J. N., Khan, U., Blau, W. J., and Gun’ko, Y. K. (2006). Small but strong: a review of the mechanical properties of carbon nanotube–polymer composites. Carbon 44 (9), 1624–1652. doi:10.1016/j.carbon.2006.02.038
Costa, P., Silva, J., Lanceros-Mendez, S., Alejandro, A.-C., Ansón-Casaos, A., Martinez, M., et al. (2014). Effect of carbon nanotube type and functionalization on the electrical, thermal, mechanical and electromechanical properties of carbon nanotube/styrene–butadiene–styrene composites for large strain sensor applications. Compos. Part B Eng. 61, 136–146. doi:10.1016/j.compositesb.2014.01.048
Dang, Z.-M., Xia, Y.-J., Zha, J.-W., Yuan, J.-K., and Bai, J. (2011). Preparation and dielectric properties of surface modified TiO2/silicone rubber nanocomposites. Mater. Lett. 65 (23-24), 3430–3432. doi:10.1016/j.matlet.2011.07.056
Daniel, S., Joseph, S., Alapat, P. S., Kalarikkal, N., and Thomas, S. (2022). Silver-sandwiched natural rubber/st-LDH/MWCNT hybrid bio-nano-composite system as a high-performing multimedia laminated electromagnetic interference shield through a tripling mechanism. ACS Sustain. Chem. Eng. 10 (45), 14897–14913. doi:10.1021/acssuschemeng.2c04820
Das, A., Stöckelhuber, K. W., Jurk, R., Fritzsche, J., Klüppel, M., and Heinrich, G. (2009). Coupling activity of ionic liquids between diene elastomers and multi-walled carbon nanotubes. Carbon 47 (14), 3313–3321. doi:10.1016/j.carbon.2009.07.052
Das, A., Stöckelhuber, K. W., Jurk, R., Saphiannikova, M., Fritzsche, J., Lorenz, H., et al. (2008). Modified and unmodified multiwalled carbon nanotubes in high performance solution-styrene–butadiene and butadiene rubber blends. Polymer 49 (24), 5276–5283. doi:10.1016/j.polymer.2008.09.031
Das, P., Katheria, A., Ghosh, S., Roy, B., Nayak, J., Nath, K., et al. (2023). Self-healable and super-stretchable conductive elastomeric nanocomposites for efficient thermal management characteristics and electromagnetic interference shielding. Synth. Met. 294 (2023), 117304. doi:10.1016/j.synthmet.2023.117304
Dettlaff-Weglikowska, U., Benoit, J. M., Chiu, P.-W., Graupner, R., Lebedkin, S., and Roth, S. (2002). Chemical functionalization of single walled carbon nanotubes. Curr. Appl. Phys. 2 (6), 497–501. doi:10.1016/s1567-1739(02)00164-5
De Volder, M. F. L., Tawfick, S. H., Baughman, R. H., Hart, A. J., and John Hart, A. (2013). Carbon nanotubes: present and future commercial applications. science 339, 535–539. doi:10.1126/science.1222453
Duan, Z.-Q., Li, T.-P., Yao, K., Xuan, Z.-L., and Liu, Y.-T. (2017). Elastic and conductive MWCNT/SBS nanocomposites as superior piezoresistive sensors. Micro & Nano Lett. 12 (no. 1), 17–19. doi:10.1049/mnl.2016.0578
Fan, M., Li, S., Wu, Lu, Li, L., Qu, M., Nie, J., et al. (2022). Natural rubber toughened carbon nanotube buckypaper and its multifunctionality in electromagnetic interference shielding, thermal conductivity, Joule heating and triboelectric nanogenerators. Chem. Eng. J. 433 (2022), 133499. doi:10.1016/j.cej.2021.133499
Fujigaya, T., and Nakashima., N. (2015). Non-covalent polymer wrapping of carbon nanotubes and the role of wrapped polymers as functional dispersants. Sci. Technol. Adv. Mater. 16 (2), 024802. doi:10.1088/1468-6996/16/2/024802
Fukushima, T., and Aida, T. (2007). Ionic liquids for soft functional materials with carbon nanotubes. Chemistry 13 (18), 5048–5058. doi:10.1002/chem.200700554
Gao, J., He, Y., and Gong, X. (2018). Effect of electric field induced alignment and dispersion of functionalized carbon nanotubes on properties of natural rubber. Results Phys. 9, 493–499. doi:10.1016/j.rinp.2018.02.074
Gao, J., He, Y., Gong, X., and Xu, J. (2017). The role of carbon nanotubes in promoting the properties of carbon black-filled natural rubber/butadiene rubber composites. Results Phys. 7, 4352–4358. doi:10.1016/j.rinp.2017.09.044
Ge, Yi, Zhang, Q., Zhang, Y., Liu, F., Han, J., and Wu, C. (2018). High-performance natural rubber latex composites developed by a green approach using ionic liquid-modified multiwalled carbon nanotubes. J. Appl. Polym. Sci. 135 (38), 46588. doi:10.1002/app.46588
Gharib, D. H., Malherbe, F., and Moulton, S. E. (2018). Debundling, dispersion, and stability of multiwalled carbon nanotubes driven by molecularly designed electron acceptors. Langmuir 34 (40), 12137–12144. doi:10.1021/acs.langmuir.8b02878
Guo, X., Guo, S., Liu, G., Bai, L., Liu, H., Xu, Y., et al. (2023). Improving dispersion of carbon nanotubes in natural rubber by using waterjet-produced rubber powder as a carrier. Polymers 15 (3), 477. doi:10.3390/polym15030477
Hamon, M. A., Hui, H., Bhowmik, P., Itkis, H. M. E., and Haddon, R. C. (2002). Ester-functionalized soluble single-walled carbon nanotubes. Appl. Phys. A Mater. Sci. Process. 74, 333–338. doi:10.1007/s003390201281
Hsiao, F.-R., Wu, I.-F., and Liao, Y.-C. (2019). Porous CNT/rubber composite for resistive pressure sensor. J. Taiwan Inst. Chem. Eng. 102, 387–393. doi:10.1016/j.jtice.2019.05.017
Jeong, C. K., Lee, J., Han, S., Ryu, J., Hwang, G.-T., Park, D. Y., et al. (2015). A hyper-stretchable elastic-composite energy harvester. Adv. Mater. 27 (18), 2866–2875. doi:10.1002/adma.201500367
Jia, L.-C., Yan, D.-X., Yang, Y., Zhou, D., Cui, C.-H., Bianco, E., et al. (2017). High strain tolerant EMI shielding using carbon nanotube network stabilized rubber composite. Adv. Mater. Technol. 2 (7), 1700078. doi:10.1002/admt.201700078
Jian, W., and Lau, D. (2020). Understanding the effect of functionalization in CNT-epoxy nanocomposite from molecular level. Compos. Sci. Technol. 191, 108076. doi:10.1016/j.compscitech.2020.108076
Jiang, H.-X., Ni, Q.-Q., and Natsuki, T. (2011). Design and evaluation of the interface between carbon nanotubes and natural rubber. Polym. Compos. 32 (2), 236–242. doi:10.1002/pc.21040
Joseph, N., Janardhanan, C., and Sebastian, M. T. (2014). Electromagnetic interference shielding properties of butyl rubber-single walled carbon nanotube composites. Compos. Sci. Technol. 101, 139–144. doi:10.1016/j.compscitech.2014.07.002
Jun, L. Y., Mubarak, N. M., Yon, L. S., Bing, C. H., Khalid, M., and Abdullah, E. (2018). Comparative study of acid functionalization of carbon nanotube via ultrasonic and reflux mechanism. J. Environ. Chem. Eng. 6 (5), 5889–5896. doi:10.1016/j.jece.2018.09.008
Katihabwa, A., Wang, W., Jiang, Yi, Zhao, X., Lu, Y., and Zhang, L. (2011). Multi-walled carbon nanotubes/silicone rubber nanocomposites prepared by high shear mechanical mixing. J. Reinf. plastics Compos. 30 (12), 1007–1014. doi:10.1177/0731684410394008
Kato, Y., Horibe, M., Ata, S., Yamada, T., and Hata, K. (2017). Stretchable electromagnetic-interference shielding materials made of a long single-walled carbon-nanotube–elastomer composite. RSC Adv. 7 (18), 10841–10847. doi:10.1039/c6ra25350d
Klüppel, M. "The role of disorder in filler reinforcement of elastomers on various length scales." Filler-reinforced elastomers scanning force microscopy (2003): 1–86.
Koval’chuk, A. A., Shevchenko, V. G., Shchegolikhin, A. N., Aladyshev, A. M., Nedorezova, M., Alla, N., et al. (2008). Effect of carbon nanotube functionalization on the structural and mechanical properties of polypropylene/MWCNT composites. Macromolecules 41 (20), 7536–7542. doi:10.1021/ma801599q
Krainoi, A., and Boonkerd, K. (2022). Novel hybrid natural rubber nanocomposites with carbon nanotube and cellulose nanofiber for strain-sensitive sensor. Industrial Crops Prod. 187 (2022), 115455. doi:10.1016/j.indcrop.2022.115455
Krainoi, A., Johns, J., Kalkornsurapranee, E., and Nakaramontri, Y. (2021). “Carbon nanotubes reinforced natural rubber composites,” in Carbon nanotubes-redefining the world of electronics (London, United Kingdom: IntechOpen).
Krainoi, A., Kummerloewe, C., Nakaramontri, Y., Wisunthorn, S., Vennemann, N., Pichaiyut, S., et al. (2019). Influence of carbon nanotube and ionic liquid on properties of natural rubber nanocomposites. Express Polym. Lett. 13 (4), 327–348. doi:10.3144/expresspolymlett.2019.28
Kueseng, P., Sae-oui, P., and Rattanasom, N. (2013). Mechanical and electrical properties of natural rubber and nitrile rubber blends filled with multi-wall carbon nanotube: effect of preparation methods. Polym. Test. 32 (4), 731–738. doi:10.1016/j.polymertesting.2013.03.002
Lee, J.-H., Lee, K. Y., Gupta, M. K., Kim, T. Y., Lee, D.-Y., Oh, J., et al. (2014). Highly stretchable piezoelectric-pyroelectric hybrid nanogenerator. Adv. Mater. 26 (5), 765–769. doi:10.1002/adma.201303570
Li, C., Chen, H., Zhang, L., and Zhong, J. (2020). Electrical properties of carbon nanotube/liquid metal/rubber nanocomposites. AIP Adv. 10, 10. doi:10.1063/5.0027021
Li, L., Wang, L., Ye, T., Peng, H., and Zhang, Ye (2021). Stretchable energy storage devices based on carbon materials. Small 17 (48), 2005015. doi:10.1002/smll.202005015
Likozar, B., and Major., Z. (2010). Morphology, mechanical, cross-linking, thermal, and tribological properties of nitrile and hydrogenated nitrile rubber/multi-walled carbon nanotubes composites prepared by melt compounding: the effect of acrylonitrile content and hydrogenation. Appl. Surf. Sci. 257 (2), 565–573. doi:10.1016/j.apsusc.2010.07.034
Lim, J. K., Yun, W. S., Yoon, M, Lee, S. K., Kim, C. H., Kim, K., et al. (2003). Selective thiolation of single-walled carbon nanotubes. Synth. Met. 139 (2), 521–527. doi:10.1016/s0379-6779(03)00337-0
Lin, J.-L., Su, S.-M., He, Y.-B., and Kang, F.-Y (2020). Improving thermal and mechanical properties of the alumina filled silicone rubber composite by incorporating carbon nanotubes. New Carbon Mater. 35 (1), 66–72. doi:10.1016/s1872-5805(20)60476-0
Liu, D., Kong, Q.-Q., Jia, H., Xie, L.-J., Chen, J., Tao, Z., et al. (2021). Dual-functional 3D multi-wall carbon nanotubes/graphene/silicone rubber elastomer: thermal management and electromagnetic interference shielding. Carbon 183 (2021), 216–224. doi:10.1016/j.carbon.2021.07.013
Llerena Zambrano, B., Renz, A. F., Ruff, T., Lienemann, S., Tybrandt, K., Vörös, J., et al. (2021). Soft electronics based on stretchable and conductive nanocomposites for biomedical applications. Adv. Healthc. Mater. 10 (3), 2001397. doi:10.1002/adhm.202001397
Lou, X., Daussin, R., Cuenot, S., Duwez, A. S., Pagnoulle, C., Detrembleur, C., et al. (2004). Synthesis of pyrene-containing polymers and noncovalent sidewall functionalization of multiwalled carbon nanotubes. Chem. Mater. 16 (21), 4005–4011. doi:10.1021/cm0492585
Lu, Y. L., Ma, J., Xu, T. Y., Wang, W. C., Jiang, Y., and Zhang, L. Q. (2017). Preparation and properties of natural rubber reinforced with polydopamine-coating modified carbon nanotubes. Express Polym. Lett. 11 (no. 1), 21–34. doi:10.3144/expresspolymlett.2017.4
Luan, W., Wang, Q., Sun, Q., and Lu, Y. (2021). Preparation of CF/Ni-Fe/CNT/silicone layered rubber for aircraft sealing and electromagnetic interference shielding applications. Chin. J. Aeronautics 34 (10), 91–102. doi:10.1016/j.cja.2020.12.040
Maya, M. G., Abraham, J., Arif, P. M., Moni, G., George, J. J., George, S. C., et al. (2020). A comprehensive study on the impact of RGO/MWCNT hybrid filler reinforced polychloroprene rubber multifunctional nanocomposites. Polym. Test. 87, 106525. doi:10.1016/j.polymertesting.2020.106525
Medupin, R. O., Abubakre, O. K., Abdulkareem, A. S., Muriana, R. A., and Abdulrahman, A. S. (2019). Carbon nanotube reinforced natural rubber nanocomposite for anthropomorphic prosthetic foot purpose. Sci. Rep. 9, 20146–20151. doi:10.1038/s41598-019-56778-0
Meng, L., Fu, C., and Lu, Q. (2009). Advanced technology for functionalization of carbon nanotubes. Prog. Nat. Sci. 19 (7), 801–810. doi:10.1016/j.pnsc.2008.08.011
Mensah, B., Kim, H. G., Lee, J. H., Arepalli, S., and Nah, C. (2015). Carbon nanotube-reinforced elastomeric nanocomposites: a review. Int. J. Smart Nano Mater. 6 (4), 211–238. doi:10.1080/19475411.2015.1121632
Muringayil Joseph, T., Mariya, H. J., Haponiuk, J. T., Thomas, S., Esmaeili, A., and Sajadi, S. M. (2022). Electromagnetic interference shielding effectiveness of natural and chlorobutyl rubber blend nanocomposite. J. Compos. Sci. 6 (8), 240. doi:10.3390/jcs6080240
Muroga, S., Takahashi, Yu, Hikima, Y., Ata, S., Kazarian, S. G., Ohshima, M., et al. (2021). Novel approaches to in-situ ATR-FTIR spectroscopy and spectroscopic imaging for real-time simultaneous monitoring curing reaction and diffusion of the curing agent at rubber nanocomposite surface. Polymers 13 (17), 2879. doi:10.3390/polym13172879
Nakaramontri, Y., Pichaiyut, S., Wisunthorn, S., and Nakason, C. (2017). Hybrid carbon nanotubes and conductive carbon black in natural rubber composites to enhance electrical conductivity by reducing gaps separating carbon nanotube encapsulates. Eur. Polym. J. 90, 467–484. doi:10.1016/j.eurpolymj.2017.03.029
Nankali, M., Nouri, N. M., Malek, N. G., and Amjadi, M. (2021). Dynamic thermoelectromechanical characterization of carbon nanotube nanocomposite strain sensors. Sensors Actuators A Phys. 332, 113122. doi:10.1016/j.sna.2021.113122
Ning, N., Mi, T., Chu, G., Zhang, L.-Q., Liu, Li, Tian, M., et al. (2018). A quantitative approach to study the interface of carbon nanotubes/elastomer nanocomposites. Eur. Polym. J. 102, 10–18. doi:10.1016/j.eurpolymj.2018.03.007
Noh, J.-S. (2016). Conductive elastomers for stretchable electronics, sensors and energy harvesters. Polymers 8, 123–124. doi:10.3390/polym8040123
Noh, S., and Song, Y. (2022). Elastic CNT nanocomposites for Joule heating and tactic sensing devices. Mech. Adv. Mater. Struct. 29 (13), 1874–1882. doi:10.1080/15376494.2020.1842950
Nurazzi, N. M., Abdullah, N., Demon, S. Z. N., Halim, N. A., Azmi, A. F. M., Knight, V. F., et al. (2021b). The frontiers of functionalized graphene-based nanocomposites as chemical sensors. Nanotechnol. Rev. 10 (1), 330–369. doi:10.1515/ntrev-2021-0030
Nurazzi, N. M., Sabaruddin, F. A., Harussani, M. M., Kamarudin, S. H., Rayung, M., Asyraf, M. R. M., et al. (2021a). Mechanical performance and applications of cnts reinforced polymer composites—a review. Nanomaterials 11 (9), 2186. doi:10.3390/nano11092186
Pandey, S., Goswami, G. K., Nanda, K. K., and Nanda, *K. (2013). Nanocomposite based flexible ultrasensitive resistive gas sensor for chemical reactions studies. Sci. Rep. 3 (1), 2082. doi:10.1038/srep02082
Ponnamma, D., Sadasivuni, K. K., Thomas, S., Krupa, I., and AlMa'adeed, M. A. A. (2016). Flexible oil sensors based on multiwalled carbon nanotube–filled isoprene elastomer composites. Rubber Chem. Technol. 89 (2), 306–315. doi:10.5254/rct.15.84841
Ponnamma, D., Sung, S. H., Hong, J. S., Thomas, S., Hyun Ahn, K. H., and Varughese, K. (2014). Influence of non-covalent functionalization of carbon nanotubes on the rheological behavior of natural rubber latex nanocomposites. Eur. Polym. J. 53, 147–159. doi:10.1016/j.eurpolymj.2014.01.025
Popov, V. N. (2004). Carbon nanotubes: properties and application. Mater. Sci. Eng. R Rep. 43 (3), 61–102. doi:10.1016/j.mser.2003.10.001
Prasad, R., Pai, A. R., Oyadiji, S. O., Thomas, S., and Parashar, S. K. S. (2022). Utilization of hazardous red mud in silicone rubber/MWCNT nanocomposites for high performance electromagnetic interference shielding. J. Clean. Prod. 377 (2022), 134290. doi:10.1016/j.jclepro.2022.134290
Rokaya, D., Skallevold, H. E., Srimaneepong, V., Marya, A., Shah, P. K., Khurshid, Z., et al. (2023). Shape memory polymeric materials for biomedical applications: an update. J. Compos. Sci. 7 (1), 24. doi:10.3390/jcs7010024
Roslaniec, Z., Broza, G., and Schulte, K. (2003). Nanocomposites based on multiblock polyester elastomers (PEE) and carbon nanotubes (CNT). Compos. Interfaces 10 (no. 1), 95–102. doi:10.1163/156855403763586819
Salaeh, S., Thitithammawong, A., and Salae, A. (2020). Highly enhanced electrical and mechanical properties of methyl methacrylate modified natural rubber filled with multiwalled carbon nanotubes. Polym. Test. 85 (2020), 106417. doi:10.1016/j.polymertesting.2020.106417
Seo, J.-M., Tan, L.-S., and Baek, J.-B. (2017). Defect/edge-selective functionalization of carbon materials by “direct” friedel–crafts acylation reaction. Adv. Mater. 29, 1606317–1606319. doi:10.1002/adma.201606317
Shahamatifard, F., Rodrigue, D., Park, K.-W., Frikha, S., and Mighri, F. (2023). Surface modification of MWCNT to improve the mechanical and thermal properties of natural rubber nanocomposites. Can. J. Chem. Eng. 101 (4), 1881–1896. doi:10.1002/cjce.24566
Shang, S., Gan, L., Yuen, M. C. W., Jiang, S.-X., and Mei Luo, N. (2014). Carbon nanotubes based high temperature vulcanized silicone rubber nanocomposite with excellent elasticity and electrical properties. Compos. Part A Appl. Sci. Manuf. 66, 135–141. doi:10.1016/j.compositesa.2014.07.014
Shehzad, K., Hakro, A. A., Zeng, Y., Yao, S.-H., Xiao-Hong, Y., Mumtaz, M., et al. (2015). Two percolation thresholds and remarkably high dielectric permittivity in pristine carbon nanotube/elastomer composites. Appl. Nanosci. 5, 969–974. doi:10.1007/s13204-015-0403-0
Shimizu, T., Kishi, R., Kobashi, K., Morimoto, T., Okazaki, T., Yamada, T., et al. (2020). Improved thermal stability of silicone rubber nanocomposites with low filler content, achieved by well-dispersed carbon nanotubes. Compos. Commun. 22, 100482. doi:10.1016/j.coco.2020.100482
Sisanth, K. S., Thomas, M. G., Abraham, J., and Thomas, S. (2017). “General introduction to rubber compounding,” in Progress in rubber nanocomposites (Sawston, Cambridge: Woodhead Publishing), 1–39.
Spitalsky, Z., Tasis, D., Papagelis, K., and Galiotis, C. (2010). Carbon nanotube–polymer composites: chemistry, processing, mechanical and electrical properties. Prog. Polym. Sci. 35 (3), 357–401. doi:10.1016/j.progpolymsci.2009.09.003
Steinhauser, D., Subramaniam, K., Das, A., Heinrich, G., and Klueppel, M. (2012). Influence of ionic liquids on the dielectric relaxation behavior of CNT based elastomer nanocomposites. eXPRESS Polym. Lett. 6, 927–936. doi:10.3144/expresspolymlett.2012.98
Subramaniam, K., Das, A., and Heinrich, G. (2011). Development of conducting polychloroprene rubber using imidazolium based ionic liquid modified multi-walled carbon nanotubes. Compos. Sci. Technol. 71 (11), 1441–1449. doi:10.1016/j.compscitech.2011.05.018
Sui, G., Zhong, W., Yang, X., and Zhao, S. (2007). Processing and material characteristics of a carbon-nanotube-reinforced natural rubber. Macromol. Mater. Eng. 292 (9), 1020–1026. doi:10.1002/mame.200700126
Sui, G., Zhong, W. H., Yang, X. P., and Yu, Y. H. (2008). Curing kinetics and mechanical behavior of natural rubber reinforced with pretreated carbon nanotubes. Mater. Sci. Eng. A 485 (1-2), 524–531. doi:10.1016/j.msea.2007.09.007
Szymczyk, A. (2012). Poly (trimethylene terephthalate-block-tetramethylene oxide) elastomer/single-walled carbon nanotubes nanocomposites: synthesis, structure, and properties. J. Appl. Polym. Sci. 126 (3), 796–807. doi:10.1002/app.36961
Tasis, D., Tagmatarchis, N., Bianco, A., and Prato, M. (2006). Chemistry of carbon nanotubes. Chem. Rev. 106 (3), 1105–1136. doi:10.1021/cr050569o
Thostenson, E. T., Li, C., and Chou, T.-W. (2005). Nanocomposites in context. Compos. Sci. Technol. 65 (3-4), 491–516. doi:10.1016/j.compscitech.2004.11.003
Tsuchiya, K., Sakai, A., Nagaoka, T., Uchida, K., Furukawa, T., and Yajima, H. (2011). High electrical performance of carbon nanotubes/rubber composites with low percolation threshold prepared with a rotation–revolution mixing technique. Compos. Sci. Technol. 71 (8), 1098–1104. doi:10.1016/j.compscitech.2011.03.015
Tuncel, D. (2011). Non-covalent interactions between carbon nanotubes and conjugated polymers. Nanoscale 3 (9), 3545–3554. doi:10.1039/c1nr10338e
Wei, L., Wang, S., Shan, M., Li, Y., Wang, Y., Wang, F., et al. (2023). Conductive fibers for biomedical applications. Bioact. Mater. 22 (2023), 343–364. doi:10.1016/j.bioactmat.2022.10.014
Xie, X.-L., Mai, Y.-W., and Zhou, X.-P. (2005). Dispersion and alignment of carbon nanotubes in polymer matrix: a review. Mater. Sci. Eng. R Rep. 49 (4), 89–112. doi:10.1016/j.mser.2005.04.002
Xie, Z., Cai, Y., Zhan, Y., Meng, Y., Li, Y., Xie, Q., et al. (2022). Thermal insulating rubber foams embedded with segregated carbon nanotube networks for electromagnetic shielding applications. Chem. Eng. J. 435 (2022), 135118. doi:10.1016/j.cej.2022.135118
Yang, J., Liao, X., Li, J., He, G., Zhang, Y., Tang, W., et al. (2019). Light-weight and flexible silicone rubber/MWCNTs/Fe3O4 nanocomposite foams for efficient electromagnetic interference shielding and microwave absorption. Compos. Sci. Technol. 181, 107670. doi:10.1016/j.compscitech.2019.05.027
Yerushalmi-Rozen, R., and Szleifer, I. (2006). Utilizing polymers for shaping the interfacial behavior of carbon nanotubes. Soft Matter 2 (1), 24–28. doi:10.1039/b513344k
Keywords: carbon nanotube, rubber, functionalization, reinforcement, interface characteristics, mechanical characteristics, electrical properties
Citation: K. C N, Abraham J, Thomas MG, Vahabi H, Maria HJ and Thomas S (2024) Carbon nanotube filled rubber nanocomposites. Front. Carbon 3:1339418. doi: 10.3389/frcrb.2024.1339418
Received: 16 November 2023; Accepted: 15 February 2024;
Published: 08 May 2024.
Edited by:
Ajit K. Roy, Air Force Research Laboratory, United StatesReviewed by:
Kailu Xiao, Texas A and M University, United StatesCopyright © 2024 K. C, Abraham, Thomas, Vahabi, Maria and Thomas. This is an open-access article distributed under the terms of the Creative Commons Attribution License (CC BY). The use, distribution or reproduction in other forums is permitted, provided the original author(s) and the copyright owner(s) are credited and that the original publication in this journal is cited, in accordance with accepted academic practice. No use, distribution or reproduction is permitted which does not comply with these terms.
*Correspondence: Sabu Thomas, c2FidXRob21hc0BtZ3UuYWMuaW4=
†These authors have contributed equally to this work
Disclaimer: All claims expressed in this article are solely those of the authors and do not necessarily represent those of their affiliated organizations, or those of the publisher, the editors and the reviewers. Any product that may be evaluated in this article or claim that may be made by its manufacturer is not guaranteed or endorsed by the publisher.
Research integrity at Frontiers
Learn more about the work of our research integrity team to safeguard the quality of each article we publish.