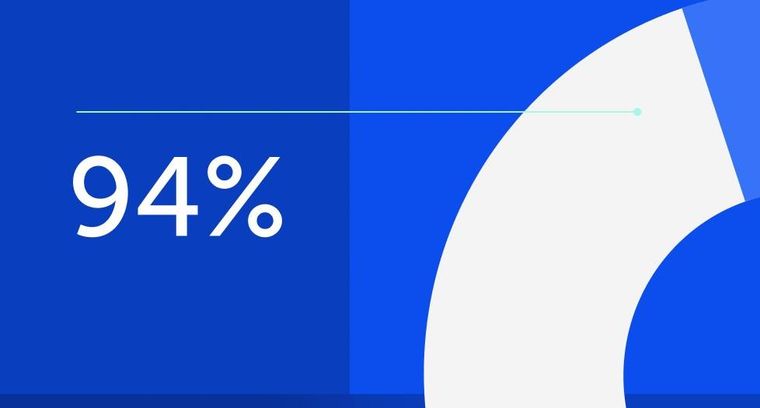
94% of researchers rate our articles as excellent or good
Learn more about the work of our research integrity team to safeguard the quality of each article we publish.
Find out more
SYSTEMATIC REVIEW article
Front. Built Environ., 31 March 2025
Sec. Sustainable Design and Construction
Volume 11 - 2025 | https://doi.org/10.3389/fbuil.2025.1535626
This article is part of the Research TopicPeople, Process, Product, and Policy: Exploring the Nexus For The Sustainable Digital Transformation Of The Construction IndustryView all articles
Background and Objective: Additive Manufacturing (AM), driven by digital 3D design data, is a transformative technology that holds significant potential to revolutionize the construction industry. Its untapped capacity to optimize material utilization, enhance design flexibility, and substantially reduce greenhouse gas (GHG) emissions emplaces it as key enabler to sustainable construction. Although being adopted in biomedical, aerospace, and automotive industries, AM remains underexplored in construction. This study systematically evaluates the role of AM in advancing sustainable construction, particularly its impact on reducing GHG emissions.
Materials and methods: Systematic research was conducted using resourceful methodologies. These are to include PRISMA meta-analysis, Cochrane Collaboration, EPPI-Reviewer 4, VOSviewer, and Databases with Search Engines. The tools were employed to synthesize, organize, and to deduce relevant materials and literature, facilitating comparative analyses of AM and traditional (conventional) subtractive manufacturing (TSM). The systematic review essentially concentrates on metrics such as design process efficiency, cost-effectiveness, production rates, and material sustainability. Furthermore, on diverse AM techniques, and materials, to include concrete, composites, and polymers, being evaluated for their potential to mitigate carbon emissions.
Results: Quantitatively, the results connote that AM can better enhance energy efficiency by up to 60%, reduce material waste by 90%, and cushioned to lower GHG emissions by 80%, while achieving labour and cost savings of 50%–60%, and sustainability by 75% in specific design standards. Furthermore, AM enables the production of complex geometrical designs that are unfeasible with conventional methods, improving both structural and mechanical performance, and sustainability.
Conclusion: This study expounds the environmental, social and economic benefits of AM, providing highly valuable insights to further incorporate AM to contemporary construction as viable alternative solutions, and sustainable supplements to TSM. Additive manufacturing innovations are deduced to be well positioned as significant strategic driver for eco-friendly built environment, supporting global efforts toward carbon neutrality and sustainable urban developments.
• Cuts wastes by 90%, GHG emissions to 80%, and boosts sustainability by 75%.
• Holistic reduction in material, design, process, and labour costs by 60% aggregate.
• Enables innovative and complex designs unattainable by conventional techniques.
• Superior efficacy in economic costs, material and construction utilities on sustainability metrics.
• Incorporates AM 3DP to Industry “X.0” for eco-friendly built environment.
Sustainable development (SD) is a well-framed conceptual initiatives aimed at fulfilling contemporary social goals while promoting economic development, all without endangering environmental quality for present and future generations. The advent of the industrial revolution, combined with increasing energy consumption, material usage in production, and improper recycling practices, has opposed the implementation of the relevant initiatives. The Sustainable Development Goals (SDGs) serve as a framework for achieving a better and sustainable future for humanity in addressing the contemporary challenges. Global warming and climate change, driven by greenhouse gas (GHG) emissions, particularly carbon dioxide (CO2), are major critical global challenges (Gür, 2022). These concerns significantly impair the attainment of Sustainable Development Goals (SDGs), with particularly severe implications on SDG 8 (Decent Work and Economic Growth) and SDG 9 (Industry, Innovation, and Infrastructure), which set essential global targets for sustainability. The critical concerns of anthropogenic GHG emissions can be effectively addressed through intentional and targeted efforts. The consequences of GHGs on a global scale are largely associated with the built environment in both residential and industrial areas (Gür, 2022; Holechek et al., 2022; Caineng et al., 2022). Based on the World Meteorological Organization (WMO’s) global climate report for 2020, the average worldwide temperature has increased by almost 1.2°C compared to the time preceding industrialization (Holechek et al., 2022; Caineng et al., 2022).This indicates a rapid temperature increase than anticipated (Zhang L. et al., 2023). The commitment of international frameworks, such as the Paris Agreement of 2015, adopted by over 200 countries, is specifically significant in this research undertaking. The primary objective of the accord is to prevent global warming from exceeding a tolerable limit of 1.50°C (Spring and Cirella, 2022). The built environment, where human activity is most concentrated is heavily impacted by hazardous pollution, particularly CO2 emissions, have far-reaching and catastrophic consequences on the planet and its ecosystems (Manisalidis et al., 2020; Oladunni et al., 2024). These hazardous pollutions are often a result of waste disposal and/or combustion after the product end life. Product life cycle consists of five distinct stages, which involves the accounts of energy consumption, energy use, and energy wastage that do not contribute to optimal energy efficiency, along with the generation of GHG emissions (Sousa and Bogas, 2021; Hao et al., 2020; Oladunni and Olanrewaju, 2022). These stages are the production of materials, the manufacturing process, distribution, usage, and disposal. During the material production phase, various techniques are employed to transform raw materials into a form suitable for manufacturing. Innovative research into manufacturing techniques, materials, and product design drives industry evolution. To achieve sustainability targets, there are significant motivations to develop and deploy innovative manufacturing processes. Manufacturing processes can be classified into five main categories: subtractive, joining, dividing, transformative and additive (Oladunni and Olanrewaju, 2022; Newman et al., 2015). Compared to traditional (conventional) production methods, AM has more adjustable process parameters and a stronger connection between material qualities and parameters. AM procedures vary based on material preparation, layer creation, phase transition, and material type, with application requirements. Traditional subtractive technology involves removing layers of material to get a particular geometry. Subtractive technologies were subject to significant modification. The use of 3D complex surface modeling software has displaced conventional code generation methods like G and M codes. CNC machines are highly automated through the integration of CAD and CAM technologies, enabling advanced applications in AM design (Flynn et al., 2016). The manufacturing phase is characterized by a series of processes forming the production chain, starting with the creation of the digital model and culminating in post-processing. The distribution phase includes the transportation and packaging of the finished product. The usage phase encompasses all activities related to the operation. Finally, the disposal phase commences after the usage phase concludes. Together, these production phases as applicable to AM, when managed under proper scrutiny, contribute significantly to the reduction of GHG emissions. These stages, which encompass various industries including construction, present three primary challenges of sustainability, namely,: environmental, economic, and social costs (Zhang L. et al., 2023). The building industry, for instance, is responsible for 38% of greenhouse gas emissions, 40% of organic waste, and 12% of portable water consumption (Xiao et al., 2015). The anticipated increase in the urban population, which is projected to reach 68% of the global total by 2050, is expected to result in an expansion and intensification of the urban carbon footprint and impacts (Wang D. et al., 2022). The development of numerous projects within the built environment will inevitably result in the extensive use of building materials, such as concrete and cement, leading to significant economic, social, and environmental impacts on ecosystems, the total environment, and human populations (Nodehi and Mohamad Taghvaee, 2022; Habert et al., 2020). Specifically, these consequences will be evident in areas such as housing, transportation, and other essential infrastructure demands (Çimen, 2021; Shehata et al., 2022a). Methodically, this research systematically reviews the potential real-world applications of AM technologies in the construction industry, with the aim to reduce GHG emissions and promote an eco-friendly built environment. Therefore, the study emphatically reinstate the utilization of Additive Manufacturing (AM) over the conventional Traditional Manufacturing (TM) technology in order to address sustainability concerns. It also explores the application of 3D printing (3DP) in concrete production within the context of Industry 4.0 and 5.0. Additionally, it examines the economic implications of using additive materials. The research further examines the classification of 3D printing techniques and their application in the development of environmentally sustainable infrastructures, specifically buildings, with the view to lowering GHG emissions. In the breadth of thorough assessments of a multi-(inter)-disciplinary approach, no study of this fashion and match exists to the tune of the reduction in GHG emissions. Nevertheless, the existing studies have limitations in terms of not considering the incorporation of the 3DP methods, built environment, energy consumption, and construction industry in the build-up of new components and infrastructures (Belaïd, 2022; Oladunni et al., 2022). The primary aim of this study is to effectively address the conditions necessary for a sustainable built environment using additive manufacturing methods, while also considering the social and economic costs associated with achieving sustainability targets. It is imperative that relevant industries, particularly the construction industry, develop and implement innovative and efficient technologies to mitigate GHG emissions in the built environment. Some of the key terminologies associated with the research topic are presented in Table 1.
A systematic review is an analysis of the available evidence in a specific field of study based on a clearly defined queries or questions, employing a methodical approach to identify, select, objectively appraise, and synthesize all relevant studies. Novel or emerging research topics typically gain significance from a holistic conceptualisation and synthesis of literature studies. In this context, the term “systematic” refers to transparent, thorough and complete, comprehensive and lengthened approach in reviewing of studies for possibly novel research domains (Mengist et al., 2020; Gough et al., 2017; Page et al., 2021). This should follow a pre-defined plan. This review adhered to the procedural steps and guidelines as established by Gough et al. (2017) at the Evidence for Policy and Practice Information and Co-ordinating Centre (EPPI-Centre), a research division at the Institute of Education, University College London, United Kingdom (Mengist et al., 2020), along with the Preferred Reporting Items for Systematic Reviews and Meta-Analyses (PRISMA) (Gough et al., 2017) and the Cochrane Collaboration 2018 (Gough et al., 2017). The EPPI-Reviewer four tool is a software for research synthesis adopted for implementation of multiple functions which include the storage of downloaded studies, screening, and data extraction (Page et al., 2021). This is as demonstrated with originality in this study in both Figures 1A, B respectively. In contrast to conventional reviews, a systematic literature review is more stringent and clearly delineated method for examining literature in a certain research domain area.
Figure 1. (A) Diagrammatic framework for implementation of the systemic review. (B) Supportive PRISMA 2020 flow chart on AM selection process for the novel systematic review.
The following research questions are part of the queries that guided the originality of this review.
(Q.1) What are the current advancements in sustainable additive manufacturing technologies applicable to the construction industry?
(Q.2) How do different additive manufacturing processes contribute to sustainability and carbon footprint in construction industry?
(Q.3) What are the challenges and barriers for sustainable additive manufacturing practices in the construction industry?
(Q.4) How can the integration of additive manufacturing with current construction practices lead to overall sustainable reduction in GHG emissions?
A comprehensive examination of the scientific literature is conducted by utilizing various sources of research bibliographic databases such as Google Scholar, Scopus, Science Direct, Frontiers, Springer Link, MDPI, Web of Science, Wiley Online Library, Taylor & Francis, others, and the Google Search Engine with some of the search key techniques and terms as provided (Supplementary Appendix 1, 2), following search operators (phrase searching, truncation, brackets, closeness and adjacency or with proximity). In addition, Boolean operators (i.e., AND/OR) were also employed to integrate keyword searches. The method of intensification by utilizing the reference lists from relevant studies also provides links to other studies in this systematic review. The original searches were carried out with the purpose of utilizing keywords related to the research topic, abstract, or author keywords, while keeping the aim of the research on focus. The primary subject areas discussed in the article include additive manufacturing, 3D printing, traditional manufacturing, GHG and carbon emissions, built environment, concrete manufacture, quality, and then production technology. These concepts are used individually and in combination throughout the investigation. The selection of articles is based on their distinctive research, peer assessments, and comprehensive coverage mainly of the English language. It is essential to emphasize that the research conducted in this study primarily relies on peer-reviewed publications. However, to strengthen the credibility of the research findings, secondary sources such as conference proceedings, books and book chapters, academic theses, organisation and websites databases were incorporated.
As presented in Figure 1A, additionally supported by Figure 1B is the PRISMA 2020 flow diagram of systematic research review (Mengist et al., 2020), after undergoing a thorough screening process, a total of 250 articles were selected, for further comprehensive analyses till 73 masterpieces are scrutinized and studied in line with the drawn key search terms. The main objective of the analysis is to assess the environmental, product developments, economic and social impacts of additive manufacturing technologies in construction industry for sustainability of the built environment. The purpose of analysing these papers is to emphasize the current state of research on the sustainability and environmental impact of additive manufacturing (AM).
Much of the research works used for this research study are conducted within a span of 7 years, intentionally purposed to be for recent versions. A further examination is conducted by thoroughly reviewing the major content of the papers, primarily using the following four basic criteria.
i. At least one of 3D printing, traditional and subtractive manufacturing, building technology, and energy consumption with respect to GHG (CO2) emissions, as well as additive manufacturing development phases based on economic and environmental sustainability assessments.
ii. Exempt any 3D printing technologies (unless absolutely necessary) that are used for purposes unrelated to construction and the built environment.
iii. Incorporate design elements, components and structures, as well as construction-related materials and printing.
iv. Include projects, investments, economic and policy implications in line with sustainability of additive manufacturing.
The data obtained through inclusion criteria of the studies utilizing the Standard EPPI-Reviewer Application are systematically arranged and analysed to address the basic research questions, an approach of configurative synthesis (Mengist et al., 2020; Gough et al., 2017). VOSviewer an instrument for scientific landscape is used to draw the linkages for the background of the research field. These organized interlinked networks as provided in Figures 2–4 respectively, can be retrieved as being labelled using the software application. The literature review process involved a thorough screening procedure where abstracts are examined, and publications are excluded if they did not pertain to additive manufacturing (AM) and/or three-dimensional printing (3D), which are relevant to the intricate structure of the built environment. More so, articles were excluded if they lacked rationales of the main topic or failed to offer measurable evaluations on any of the following: AM, traditional manufacturing (TM), subtractive manufacturing (SM), energy consumption, GHG emissions, sustainability, and efforts to mitigate global warming due to climate change in the context of additive manufacturing strategies and solutions for construction processes, as well as in their product developments. The network diagram in Figure 2 depicts the linkages between numerous essential background efforts in additive manufacturing that are expanding to new research niches (Page et al., 2021; Garritty et al., 2021; Thomas et al., 2010). The deep dark green circles represent the closed interrelationships among these works.
This research primarily aims to provide in-depth assessments of possible advances in additive manufacturing for construction purposes, adhering to systematic strategies to mitigate GHG emissions for sustainability. It focuses on technological advancements, sustainable processes and materials, barriers to adoption, economic costs, and policy implications, then elaborates on these advances to reach conclusion. The study also takes into cognizant the inclusion of conventional methods, envisaging comparative analyses, thereby demonstrating its real-world applications. The study sought to contribute valuable insights for practitioners, policymakers, stakeholders, and entrepreneurs, cushioning efforts in optimizing material, process, and energy utilization while attaining product efficacy to reduce GHG emissions in the construction industry. Through these inquiries, hence the elaborated research findings are subsequently presented.
By striking a balance between environmental, economic, and social challenges, the construction industry obliged to place emphasis on sustainability (Wong and Hernandez, 2012; Lima et al., 2021). Policymakers and stakeholders in the construction industry, together with their investors, have sought to address global climate change concerns by adopting energy management and sustainability strategies, exploring innovative possibilities for process, material, design and application.
The economic, social, and environmental effects of a manufacturing technique can support businesses to thrive and progress toward sustainability. This is particularly applicable to countries seeking to enhance their manufacturing capabilities relative to the achievements of countries with minimal environmental impacts despite accounting for large production scale. The AM technologies does not only aid in lowering social and economic costs but also have the potential to drive corporate growth and boost profits. For quite a few years, this has brought dynamism in the construction processes; from traditional (subtractive) to hybrid and recently for some cases to fully additive manufacturing techniques of complex construction projects (Ahmed Ali et al., 2020; Pragana et al., 2021). The way additive manufacturing technologies operate is by using digital 3D design data to build up a component in layers by depositing material to produce an item. In contrast, subtractive manufacturing techniques function by taking material out of the workpiece (Page et al., 2021). The removal of material can be accomplished by heat, friction, erosion, or sharp tools (Grabowska et al., 2022). AM offers a greater degree of design autonomy due to its capability to produce complex design from a unit machining task (Al Rashid et al., 2020). Additive manufacturing utilizes several production techniques to offer a diverse range of technologies that are possibly valuable to the construction industry in its quest of environmental sustainability. Subtractive or traditional techniques deplete natural resources, produce non-recyclable construction waste, consume significant amounts of energy, and pose risks to workers’ occupational health and safety (Wong and Hernandez, 2012). To overcome these challenges, 3DP technology is blended as an environmentally friendly construction technique. According to the systematic research, 3DP significantly reduces the negative impacts on the environment (Tabassum et al., 2023; Lima et al., 2021). The limited use of construction materials, waste elimination, reduced energy consumption, and increased manufacturing efficiency all contribute to the reduction in GHG emissions. The rapid growth of AM technologies is driven by research efforts focused on building cost-effective items, expanding material options, and leveraging the complexity advantage to meet wide range of application needs. In addition, 3D printing positively impacts the environment by generating less noise and improving air quality (Ahmed Ali et al., 2020; Pragana et al., 2021; Dilberoglu et al., 2021). Analogously, advanced techniques and technologies are used to include many materials, such as cement, sand, clay, hard plastic, elastomers, and more, into a single print formulation. The network map in Figure 3 illustrates the linkages between various critical research keywords for sustainable additive manufacturing that are broadening to new research niches (Jayawardane et al., 2023), with each specific colour representing the closed interrelationships among these works.
The design flexibility provided by AM is found to yield significant economic benefits. However, there are a few limitations from an industry standpoint. The ease to design intricate shapes that are difficult to obtain makes it unnecessary for additive manufacturing to conform to the fabrication and assembly of traditional manufacturing processes (Tabassum et al., 2023; Gu et al., 2021; Muñoz et al., 2021). The American Society for Testing and Materials (ASTM) has performed an essential function in improving standardization and certification of Additive Manufacturing (AM) processes, such as 3D printing standards and certifications (Wang Y. et al., 2021; Waqar et al., 2023a). Initially, AMs are considered as amorphous machines, but with the involvement of ASTM, Quality Assurance (QA) and Quality Control (QC) strategies have been developed to enhance standardization and ensure consistent quality in industrial certification of AM-3DP processes (Westphal and Seitz, 2022; Hegab et al., 2023). In contrast, the mechanical properties of an AM part may be adversely affected by the size, orientation, sharpness, and position of flaws (located within joints, exterior surfaces, or critical parts of the structure). The same problems apply to TM production as well: porosity, cracks, inclusions, voids, balling, and rough surface quality. In fact, within this disadvantaged minor context, they are nearly the same and due to advancement, AM technologies appear to be a preference. Early on in AM, it is assumed that TSM can produce machined parts with high accuracy and little complexity, whereas AM is thought to lose geometric complexity in return for lower tolerance and better overall quality. Sequences of manufacturing and laboratory advancements, however, point to the opposite condition. By printing entire parts in a single print, the sophisticated advantage of AM has made it possible to do away with the need for forging and joining, which is a great advantage over TM (Khan et al., 2021a; Ahmed, 2023). Due to the level of preliminary assessments, it is imperative to know that AM system has more dependent variables than TM (Kawalkar et al., 2022; Vora and Sanyal, 2020). AM offers a unique characterisation made possible by 3D scanning, together with fast design adaptation with no lead time compared to traditional manufacturing processes (Chen Z. et al., 2022; Lee et al., 2021). An outstanding benefit of AM is its ability to provide tooling and fixturing to complement traditional manufacturing methods (Yang et al., 2020; Sanicola et al., 2020). Utilizing AM enables the production of tooling and fixturing at a lower cost with greater speed compared to traditional methods (Lee et al., 2021). Commonly used items now manufactured with a mass customisation manufacturing approach include Invisalign brace moulds made by Align Technologies with AM Stereolithography printers (Jandyal et al., 2022). The complex geometry, internal lattice structure, surface finish, layer orientation and topology optimization, all contribute to the mechanical aptitude of an AM part (Lee et al., 2021; Zhang and Liou, 2021). Furthermore, each AM printer requires calibration and customization of the printer parameters, sometimes specific to certain types of designs, constructions and buildings (Ingarao and Priarone, 2020; Iqbal et al., 2020). As synthesised for this systematic research, and in alignment with the operating or closely applicable ASTM standards, Table 2 outlines both technical and economic requirements for itemized product to be built up by additive manufacturing process while Table 3 presents the significant merits of AM technologies over the conventional manufacturing technologies.
Table 2. AM -TM technical and economic factors for selection (Wong and Hernandez, 2012; Kawalkar et al., 2022; Vora and Sanyal, 2020).
Table 3. Significant merits of AM and TM technologies for construction industry (Sepasgozar et al., 2020; Praveena et al., 2022; Vaneker et al., 2020).
The construction industry can be highly perilous, ranking among the most hazardous industries, globally. Nonetheless, interlinking it with industry X.0 could make the AM technology a better fit and make human far more productive. Traditional methods utilize natural resources, produce non-reusable building wastes, require substantial quantities of energy, and pose risks to the occupational health and safety of workers in the construction sites (Guzzi and Tibbitt, 2020; Vasco, 2021). The 3DP technology has been introduced as an environmentally friendly construction strategy to address these concerns. Based on the reviewed literature, it is widely accepted that 3DP effectively minimizes detrimental effects on the environment (Go and Hart, 2016; Meng et al., 2020; Arefin et al., 2021). The deployment of industry 4.0 and 5.0 technologies (X.0) to 3D printing for construction results in the mitigation of GHG emissions by limiting the utilization of construction materials, removing waste, reducing energy consumption, and increasing production efficiency (Deneault et al., 2021; Kumar and Sathiya, 2021). Furthermore, the materials utilized for printing have the potential to be recycled and repurposed as a 3D printing mortar that possesses excellent tensile qualities when combined with cement (Vafadar et al., 2021; Khan et al., 2022; Mohamed et al., 2023). Polylactic acid (PLA) is a human-centric commonly used material in 3D printing. It is both biodegradable and recyclable, and it improves the life cycle assessments of reducing GHG emissions by no more than 1.5°C (Xu et al., 2020; Qaidi et al., 2022). The environmental impact of 3D printing in the evolutionary era of juxtaposing industry 4.0 and 5.0 for optimal outputs has positive effects on the society (Shuaib et al., 2021). One example is that 3D printers generate minimal noise and contribute to better air quality (Fraga-Lamas et al., 2021; Singh et al., 2021). Curved walls in structures can decrease the required space and minimize the amount of material used. The construction industry significantly contributes to the global consumption of energy and diverse forms of raw materials, accounting for approximately 50% of the world’s steel production and 30% of its GHG emissions (Ding et al., 2020). The construction industry has relatively been slow to embrace new technology and has not seen a huge, disruptive shift, despite being the big user of raw materials, hence, it is in many ways unsustainable. Concrete is the most frequently used material in the built environment (Çimen, 2021; Xiao et al., 2021a; Skibicki et al., 2022). Advanced manufacturing techniques that are commonly utilized in the production industry are increasingly being exported for use in construction and architectural applications. The building industry is becoming significantly impacted by digital technologies, which have played a crucial role in shaping its landscape during the Fourth and Fifth Industrial Revolution, also known as “Industry 4.0 and 5.0” (Zhang H. et al., 2023). The rapid advancement of smart sensors and wearable gadgets is driving the creation of a smart operator workspace, known as the Industry 4.0 paradigm (Lee et al., 2024; Elbadawi et al., 2021). The industry 4.0 paradigm empowers workers to address manufacturing complexity by complementing and expanding their capabilities and skills, rather than replacing them. The Industry 4.0 & 5.0 interwoven specializes in the concept of Human-Cyber-Physical Systems (HCPS) and adaptive automation, leveraging automation to create a human-automation symbiosis (Rojek et al., 2021; Dobrzyńska et al., 2021). Human-centric smart construction process thrives at using automation-aided system toward human-automation symbiosis framework for socially sustainable workforce. It is evidently novel for both real estate and transportation infrastructure to be constructed, designed, and maintained to inculcate cutting-edge technologies, which include the Internet of Things (IoT), Artificial Intelligence (AI), and in some cases, Machine Learning (ML). These among others to include incremental sheet forming and composite fabrication techniques. However, in contrast to other sectors, the construction industry has been notably slow to embrace new technologies and has yet to undergo a significant, disruptive transformation. It is essential to recognize that each individual human being, on average, consumes approximately one (1) tonne (Conejo et al., 2020) of concrete annually (Conejo et al., 2020; Bos et al., 2022). In terms of non-water substances, no other material is ingested to such an immense extent. Given the substantial volume of concrete consumed, even small reductions in GHG emissions per ton of manufactured concrete can have global significant impacts (Kuittinen et al., 2023). Thus, in line with industry 5.0, the industry is being presented with the justification for implementing 3D Concrete Printing (3DCP) and smart manufacturing technologies (de Almeida Barbosa Franco et al., 2022). The network diagram in Figure 4 with the intelligence of “Connected Papers” reveals the linkages between various key background research for additive manufacturing with industry 4.0 and 5.0 (X.0) that are spreading to new research domains (Peruzzini et al., 2020). The deep-dark green circles reflect the closed links between these publications. Figure 5 depicts the evolution era of 3DP as can be employed to concrete printing with the involvement of industrial stages as labelled. The emergence of mechanization, electric, information, intelligent, and symbiotic are correlated to the strata of industrial age of Industry 1.0, 2.0, 3.0, and 4.0 and 5.0 with their combination (X.0) (Sun et al., 2020; Wang B. et al., 2022; Pantano et al., 2020), respectively as depicted.
The process of building up objects by layering materials according to digital 3D model design data is typically known as 3D print of additive manufacturing. In some instances, this method is also referred to as 3D printing (3DP) technology as specified by the ASTM standards (Sun et al., 2020). In recent times, additive manufacturing has undergone significant improvements owing to its capacity to form intricate and customized items that are previously unfeasible using conventional techniques (Chen Z. et al., 2022). As a result, it demonstrates its suitability for real-world production applications that goes beyond just prototyping. 3DP technology as collection of techniques that build components layer by layer is generally divided into seven primary categories, based on the process used to create each layer (Coffetti et al., 2022). These categories are: photopolymerization, extrusion, sheet lamination, beam deposition, direct write and printing, powder bed binder jet printing, and powder bed fusion. Adopting 3DP has several advantages for sustainability, which include its ability to maximize time, reduce the shortage for skilled labour, and create complex structures while also promoting the reduction of GHG emissions in the built environment relative to the selection of process techniques, with the right composition material use (Coffetti et al., 2022; Mohamad et al., 2022). Only in recent years has the progress of additive manufacturing to produce 3D concrete and other housing components opened new perspectives and essential possibilities for the construction industry. Additive manufacturing distinguishes itself from traditional subtractive technologies in three distinct ways: (a) its capacity to produce complex structures through the benefit of high geometric freedom; (b) the reduced reliance on traditional conventional formwork and labour force, thereby reducing overall production costs; and (c) enhanced productivity in the construction of simple structures compared to the local formwork technique (Coffetti et al., 2022). Due to its exceptional durability, strength, accessibility, design versatility, and fire resistance, 3D printing (3DP) in concrete has attracted significant attention from researchers for applications in the built environment (Jayawardane et al., 2023; Mohamad et al., 2022). A comprehensive examination of AM in terms of global sustainability reveals its potential to reduce carbon dioxide emissions by 130.5–525.5 million tons and overall primary energy consumption by 2.54–9.30 EJ by the year 2025 (Wong and Hernandez, 2012). Despite the widespread acknowledgment of the advantages for 3D printing, there is a significant lack of research into the environmental impacts of AM technologies with respects to the sustainability of the built environment (Flower and Sanjayan, 2007). Traditional manufacturing processes have significant drawbacks compared to AM, hence the rationale for the emergence for 3DP technology. In contrast to conventional manufacturing, additive manufacturing (AM) relies on a unique set of key resources. Notably, the main AM equipment and auxiliary sub-systems efficiently use energy, making it a key feature for sustainability. Additionally, AM with regards to sustainability; materials consumed less power, this include both main and secondary components, comprising metal powders and polymer filaments, support structures, protective gases (argon and nitrogen, for example,), and cooling water (Pragana et al., 2021). For instance, it is simple to produce pieces with complicated geometries and lightweight materials. AM has recently found more usage in the construction industry, in addition to its extensive use in the aerospace, automotive, medical, and dental fields. AM is a promising technology with significant potential; however, it still faces critical challenges related to sustainability, reliability, productivity, robustness, material constraints, and quality, which hinder its full adoption in the construction industry. With continued research, these challenges can be effectively addressed. Concrete is a fundamental component in the construction industry, both domestically and internationally. It is a versatile material that can be used in a wide range of building projects due to its exceptional structural properties and functionalities, both on and off-site (Bos et al., 2016; Mehrpouya et al., 2019). Table 4 presents some real-world examples of construction projects conducted using AM/3D printing technologies.
AM is a valuable design instrument that can be adapted to create a wide range of shapes and forms applicable to all segments of building construction, sometimes at a relatively low economic cost. Concrete is produced by mixing cement, fine and coarse aggregates, mineral additives, and water to form hydrated compound. Traditionally, wooden or metal formwork is used to create basic concrete geometries incurring more design cost (Anastasiades et al., 2021). In contrast to other industries and sectors, such as the manufacturing sector, construction technology has remained markedly static to the introduction of new eco-friendly technologies (Moavenzadeh, 2022; Jung et al., 2022). The production of concrete has become increasingly involved with the creation of customized, irregular structures, this suggests that the traditional design process, with its inherent limitations, is no longer sufficient to meet customers’ demands of contemporary construction. The utilization of AM technology has the potential to significantly improve sustainability by reducing GHG emissions majorly CO2, and the economic production costs on mass scales (Wong and Hernandez, 2012). The AM market growth has demonstrates substantial expansion over the past two and half decades. Beginning with a value of $295 million in 1992, the industry has grown to a staggering $5.1 billion in 2017 (Teixeira et al., 2023). Starting from consumer-grade desktop 3D printers to high-volume industrial additive manufacturing equipment, huge developments have been visible in every category (Ibrahim et al., 2022; Bazli et al., 2023). The market is projected to worth between $230 and $550 billion by 2025. Estimates place the direct part manufacture of medical and aerospace components at $100–200 billion, consumer goods being the key driver of growth is predicted to improve from $100 to 300 billion, being the key drivers of this growth (Tarhan and Şahin, 2019). This phenomenal rise reflects a 25.4% compound annual revenue growth rate for all AM products and services worldwide (de Souza et al., 2024). One of such innovative technology that shows promise in this regard is three-dimensional printing (3DP) for concrete buildings. The 3DP technologies have proven to be efficient in decreasing building material consumption by up to 60%, labour by 80%, construction time by 70%, and economic costs by 30% per square meter of construction (Jipa and Dillenburger, 2022; Suhaily et al., 2013). Among its advantages are the freedom to create complex geometries, reduced material with energy consumption, environmentally friendly material options, minimal waste generation, high recycling potential, and cost-effectiveness. 3DP has the potential to revolutionize the construction industry and play a significant role in achieving sustainability targets (Kang et al., 2020). Khajavi et al. (Fan and Fu, 2017) have studied the potential influence of AM technology on the organization of spare parts supply chains. While technology has made progress in terms of material advancement and scalability, its overall project cost remains a significant concern. Nevertheless, these challenges have encouraged the development of the niche. On the other hand, the environmental impact and life cycle assessment of 3DP technology for building remain largely unexplored in every phase, including design, process technology, and material selection (Gupta et al., 2019; Lipson and Kurman, 2013) for the development of its market growth. 3DP presents means by which the carbon emissions present in the built environment can be reduced through the minimization of embodied and operational energies. Given the extensive range for managing economic cost and accessibility of renewable energy sources, the integration of additive manufacturing (AM) in the construction industry greatly enhances the potential for minimizing the GHG impact on the environment. Unlike subtractive manufacturing techniques, AM involves layering the constituent materials using a computer-controlled cutting edge tool with production management control, resulting in a physical product that replicates the digital three-dimensional model of the desired object at a feasible costs (Khan et al., 2021a; Xiao et al., 2021b).
There are seven main types of additive manufacturing (AM) processes. These are Directed Energy Deposition (DED), Selective Laser Sintering (SLS), Laminated Objective Manufacturing (LOM), Binder Jetting (BJ), Powder Bed Fusion (PBF), Stereolithography (SLA), and Material Extrusion (ME) (Augustyn, 2016; Lund et al., 2019). The distinctive characteristics of these technologies are in the manner of layer deposition and the utilized materials. As widely sourced for this systematic research (from Supplementary Appendix 1, 2), the basic features of 3D printing technologies for industries in addition to construction are concisely presented in Table 5. Product modelling, layer and orientation design, printing with appropriate design parameters, and post-processing for geometric final finish are all components of an additive manufacturing process. Arcam in Sweden, Electro Optical Systems in Germany, and MCP Tooling Technologies in the United Kingdom are some of the companies that fall into this category. Stratasys in Israel, 3D Systems, Z Corporation, and Optomec Inc. in the United States are all included in this group of companies (Batikha et al., 2022). The use of AM technology as demonstrated, can create components from digital designs using wide range of materials and complex structures, which can possibly be deployed in the construction industry. Following available sources on the seven types of AM, there are two main techniques (applicable to any other technique) for rapid development of a large-scale 3D concrete printing (3DCP) technology: (1) binder jetting and (2) material deposition method. Building any complicated structure by adding tiny layers of material on top of each other is the fundamental bedrock for both approaches, which nonetheless depend on the general layer-by-layer technique. Any of the two processes starts by generating 3D computer-aided design (CAD) model which is then sliced into multiple 2D layers and printed incrementally using designated material to produce the object as programmed in the CAD-aided machine.
One method of three-dimensional printing called binder jetting involves depositing layer on layer to a powder bed to produce an object (Khajavi et al., 2014). The build tray is covered with a small coating of powder material, binder is ejected in droplet form. The technique requires layering material powder and gradually adhering 2D cross sections of the required component. This cycle proceeds till the entire 3D product are completely formed. The unbound raw material is retained within the confined container and serves as a base for subsequent production. After the printing process, the unbound material can be extracted from the print bed with a vacuum cleaner which can then be recycled and used for the next printing operation. Voxeljet and Monolite UK Ltd (D-Shape) collaborated on developing a technique for 3D printing of large-scale components used in the architectural and building sectors (Yao et al., 2020; Abu-Ennab et al., 2022). Figure 6 shows a typical binder jet system. Powder is applied to each layer of the part using a counter-rotating roller. The liquid binding agent is then jetted into the powder bed by an inkjet printhead, culminating in the layer’s 2D pattern.
Figure 6. System schematic diagram of 3D print process for binder jetting (Abu-Ennab et al., 2022).
Material deposition method (MDM) for building is a 3D printing technique that sequentially applies material according to the designated CAD model comparable to fused deposition modeling (FDM) (Jiménez et al., 2019). FDM machines are similar to conventional polymer processing machines that utilize extrusion technology. The main reliance of FDM technology is on thermoplastic filament as material substitute. The printer head comprises a heating element, extruder, and nozzle, which are heated to a temperature range of 150°C–250°C. This elevated temperature allows for the extrusion and deposition of thermoplastic material, enabling the creation of both 2D layers and 3D printed objects. To achieve the required shape without distortion, the extruded material has to be sufficiently strong to hold itself and the weight of each successive layer. The following are a couple of automated systems that utilize MDM as the main concrete printing process: (a) Contour crafting and (b) Stick dispenser.
As depicted in Figure 7A, the extruded polymer unit functions as a bead, resulting in swelling effects that necessitate appropriate heat distribution for accurate part printing. Before being deposited, the filament may undergo buckling or structural failure, emphasizing the significance of precise control over the FDM process (as further demonstrated in Figure 7B. It is essential to consider the capacity of the extruded material to maintain a precise diameter, shape, and structure during the printing process, more especially for the case of building (mixing of concrete) construction. FDM machines have a singular head configuration and the capability to print just one material system at elevated temperatures. Leveraging a polymer-based composite material system that is compatible as a filament enables the printing of composite mixes, leading to the creation of a composite product. Alternatively, the act of strengthening material can be accomplished by utilizing an external system, such as a human-autonomous robot system, to carry out the printing process. Dual head FDM printers enhance material mix production by printing two different element systems concurrently. These printers can print using support structures. It is also suitable for printing multilayer and skeleton composites. Using both printer heads concurrently can result in at least a 50% boost in time-efficiency, making it an ideal alternative for small-sized, multi-component fabrication using FDM (Jiménez et al., 2019).
Figure 7. (A) FDM process material schematic flow and (B) Typical FDM-3DP machine with fixed print bed redesign from (Srivastava et al., 2022; Salmi, 2021).
The printed house is a modern construction created by layering materials in a digital file format to create a real-size 3DCP model. Hence in addressing the concerns of sustainability, multitasking construction is a significant improvement in automated construction technology. With this in notion, it is expected that 3D concrete printed models and real-sized houses will create a serene ecosystem with neutral or practically zero carbon emissions.
Figure 8 illustrates the fundamental principles that can be followed in the 3DP process of AM. The principles outlines the procedural stages required for forming a three dimensional printed object using 3DP concrete technology. The materials used in modeling AM components for building construction depend on their intended purposes, these among others can include options such as clay, composites, polymers, ceramics, cement, concrete, and metals. AM has rapidly transformed manufacturing in numerous ways, moving design and production to a level where it is available to everyone to be easily adopted for routine production activities. Previously, numerous unique AM projects such as dwellings, houses, barriers, and electronic gadgets for built environment were printed (Ashima et al., 2021; Craveiro et al., 2019). By the diagrammatic presentation of Figure 9, It can be seen that the AM design process incorporates multiple important performance factors. According to ISO/ASTM52910:2018, AM design has three general stages (Gibson et al., 2021; Shakor et al., 2022). The first stage involves evaluating the part, tool, or product under consideration. The AM process technique is required to adapt to the object or set of objects based on the required parameters. Hence, material selection comes in. After applying all conditions and limitations to the requirements, ranging from material specificity, shape, size, and mechanical properties, bearing into account the functional decomposition and integration, then optimization process can possibly start. Initial selection includes necessary components and starts system entity specification. One further determination is the involvement of specifying the entire production process for each characteristic, including the arrangement of the separate manufacturing procedures, potentially utilizing suggested 3D printing production methods. Each voxel of the part will need to have its material and attributes designated. The material features, such as type, form, thickness and density, require to be clearly identified. Inclusively, the transitions within different materials in different regions of the objects must also be characterized (Lee et al., 2021; Ziaee and Crane, 2019). These optional possibilities are limited and constrained to additive manufacturing technologies to allow material assembly or grading within a product. AM simulators have not been advanced enough to cater for all the designs concerns of average designers.
In this respect, AM has undergone assessments in consideration of its energy usage with the potential to minimize GHG emissions in the built environment. Additive Manufacturing comes with many improved features over TM processes, this includes being more environmentally friendly and better suited in pursuit for climate change, adaptation and mitigation phenomenon. Production industry requires loads of energy, this consequently leads to massive waste and emissions. The demands are to downward adjust the GHG emissions in limiting the progression of global warming. The technologies used for AM are, namely, 3D printing, 3D scanning, and related autonomous and customized software (Daminabo et al., 2020; Dickson et al., 2020). The continued adoption of additive manufacturing (AM) technology in various industries, such as automotive, aerospace, and medical, demonstrates the established status of 3D printing in the built environment. In the construction industry, numerous processes have been developed to date, ranging from printing specific components to the complete production of entire structures, from the foundation to the roof, layer by layer. (Mazzanti et al., 2019). A key advantage of 3D printing in generative architecture is its ability to incorporate multiple components into a single piece, eliminating the need for downstream assembly and optimizing product specifications. Furthermore, its integration streamlines the entire rough building process. Figure 10 shows the comparison between traditional construction techniques and additive manufacturing of 3DP construction. As shown, human resources are involved in several stages of conventional building, which is time-consuming and costly. In addition, the completed product generates a substantial amount of building waste. 3D printing relies on computer-aided design (3D CAD) and eliminates the quest for tooling, dies, or fittings (Nadarajah, 2018). Hence, the system of 3DP minimizes manual operations, labor requirements, and material waste.
Figure 10. Process of conventional manufacturing of building over additive manufacturing of 3DP (Nadarajah, 2018).
More parts for construction as projected have the potential to be produced using 3D printing technology, which would greatly increase the versatility and effectiveness of mass production of even complex components. It is imperative to add that AM components produced by designers can explore varied materials leveraging regenerative designs for greater potential. In addition, cloud modeling can be adopted to assess material fatigue, measure stress, simplify design and further enhance engineering processes (Çetin et al., 2021). AM techniques cut off the demand for iterative physical prototyping, this conserves time, resources, energy and wastes. These economies, in contrast, are often thought of to be environmentally friendly for the reduction of carbon and GHG emissions in the construction industry. It is confirmed that 3DP saves energy and provides a long life cycle because conventional construction is a complicated process that is labour and equipment intensive (Arefin et al., 2021). In comparison, 3DP can be controlled by intelligent buildings operation and cloud servers. Construction industry being the backbone of global economy, accounts for almost 13% of global gross domestic product (GDP) (Martínez-García et al., 2021; Thompson et al., 2016; Jacob et al., 2018). In accordance with World Economic reports, the concerned industry engages well over 100 million individuals globally and just like other manufacturing industries also focused on increasing production efficiency whilst maintaining cost and quality. Among the contributing factors of excess labour impeding production efficiency are the lack of automation and slow adoption to new technology which is part of the fourth industrial revolution commonly known as “Industry 4.0” (Kumar and Sathiya, 2021; Kalkal et al., 2021; Javaid et al., 2021b). The integration of cutting-edge technologies like building information modelling (BIM), modular integrated construction, the Internet of Things (IoT), artificial intelligence (AI), and smart production combined with 3D printing has significantly advanced the construction industry as well as real estate and other built infrastructures. To build, renovate, and maintain these structures, digital data technologies have been essential (Pessoa et al., 2021; Tay et al., 2017).
The production of Ordinary Portland Cement (OPC) on a large scale can result in substantial emissions of greenhouse gases, which often exacerbate global warming (Borowski, 2021). It is estimated that for every ton of OPC produced, 1.5 tons of limestone can be extracted, and approximately 0.5 tons of CO2 are released to the atmosphere (Bajpayee et al., 2020; Teweldebrhan et al., 2022). These emissions can have detrimental effects on the environment and contribute to the persistent challenges of climate change. The constraints associated with the utilization of OPC in AM processes are primarily attributed to its inherent properties. One of which is that OPC can be highly energy demanding, this results in intensive GHG, largely CO2 emissions (Bajpayee et al., 2020; Issa, 2021). The effect can be significantly minimized with the addition of certain substances. Moreover, the benefits of utilizing high-grade concrete for 3D printing are critical, as its high strength and lightweight properties make it technically ideal for earthquake resistance (Wang et al., 2020). Furthermore, it is significant to note that production of OPC presents approximately 5%–7% of the total GHG emissions, making it the fourth largest contributor after petroleum products, coal, and natural gas (Malik et al., 2022).
One of the primary aims of scientific and technical experts is to supplement ordinary Portland cement with sustainable alternatives known as geopolymers (Baduge et al., 2022). The main benefit of printing geopolymer is its rapid curing property, which greatly enhances the ease of construction without requiring any extra chemical accelerators. Fly ash (FA), silica fume, and ground granulated blast furnace slag, which are derived from industrial wastes, are the primary constituents of geopolymers (Sawhney et al., 2020). The choice of binder for printable geopolymers, such as FA and slag, can have a significant impact on the component aggregate properties, including the amount of various alkali activators utilized. The FA are the waste produce of coal fired thermal power plants as being investigated by Neupane (2022). Geopolymers offer a significant environmental advantage due to their reduced carbon emissions during the production process. The research and further development of geopolymer have received significant attention in the past decade (Naqi and Jang, 2019; Khan M. M. H. et al., 2021). The materials are designed to enhance construction techniques to be environmentally friendly in lowering GHG emissions. As per recent studies, Australia is on the lead in the deployment of the geopolymer technology on real world applications in the built environment (Prakasan et al., 2020), this can be enhanced in the reduction GHG emissions as required for the construction industry (Weng et al., 2020).
Though previous assessments of 3D printing techniques in construction have focused on broad technical and material development considerations, there is a need to further evaluate these methods in terms of cost and practical applications of the mix geopolymer (Jayawardane et al., 2023; Rehman and Kim, 2021; Ayub et al., 2021). Nevertheless, it is essential to assess the approach to energy use, environmental impacts, and the potential benefits of adapting geopolymer mixes to mitigate GHG emissions in the construction industry, which pose a significant threat to the built environment. Considering the social, economic, and environmental impacts of global warming and climate change, confronting these increasingly intertwined complex challenges demands that the built environment adopt AM techniques as a vital prerequisite to achieving environmental sustainability (Singh and Middendorf, 2020). Based on Table 6 presentation, which details the proportional contributions of key chemical compounds to GHG emissions, implementing measures to limit the use of conventional manufacturing techniques and adopting 3D printing in the construction industry can substantially aid in the efforts to reduce GHG emissions.
Table 6. Contribution and sources of greenhouse gas emissions in built environment (Gupta, 2021).
Three-dimensional (3D) printing construction technology have been more developed and transferred into real-world applications; nonetheless, the disparity in market demands between large-scale 3D printing and laboratory-scale 3D printing remains limited. In 3D printing as to apply in construction (Xiao et al., 2021b), the computer-aided design (CAD) model is cut into 2-D layers, which are then deposited by the printer to form the model. To further investigate the advantages of AM over traditional manufacturing (TM) in terms of reducing greenhouse gas emissions in built environment for concrete printing, it is necessary to conduct a comprehensive examination of the fundamental processes of AM. The three primary components of additive manufacturing technologies for concrete printing that have been scientifically documented are (a) printing procedures (b) materials, and (c) requisite specifications (Garritty et al., 2021; Ye et al., 2021). When it comes to the fabrication of concrete structures, the implementation of 3D printing technology in the construction industry adheres to the same principles as its technicality in other 3D printing applications (Xiao et al., 2021b; Chen S. et al., 2022; Li et al., 2022). The method is comprised of three basic stages: the process of 3D printing, the construction of slicing and tool paths, and the use of CAD for the result. Cutting is performed on the CAD model to divide it into layers of varying heights. In the following step, the printing route of the layer is transformed into a G-code file. The application of 3D concrete printing technology necessitates the use of concrete with distinct and specific attributes (Ye et al., 2021; Shehata et al., 2022b; Bedarf et al., 2021). These combinations are formulated based on three main material parameters: pumpability, extrudability, and buildability. Pumpability refers to the ability to be pumped, extrudability refers to the ability to be extruded, and buildability refers to the ability to withstand the load of consecutive printed layers without failing (Wang J. et al., 2021). The characteristics of consistency, cohesiveness, stability, and phase separation likelihood under pressure all work together to coordinate pumpability and extrudability. Device key parameters, including green strength, youthful age elastic modulus, dynamic shear yield stress, and static shear yield stress, play a crucial role in determining the optimal composition for a constructible 3D concrete printing process (Niaki et al., 2019). The set parameters favourably adjust by time function due to hydration of cement as affected by the curing conditions. The open time of workability, printability window, thixotropy, layer bond strength, and printing time gap are other essential factors for 3D printing concrete. Furthermore, printing time interval, layer shape and environmental factors impacting on the surface qualities also affect the layer bond strength, and the adhesion (Tay et al., 2022; Xiao et al., 2021c).
Additive manufacturing technologies utilize other methods with respect to the material states of matter, such as liquids, solids, powders and gasses. One method of liquid-based additive manufacturing is vat polymerization, which involves the use of light-activated polymerization to selectively cure liquid photopolymers in a vat (Shahrubudin et al., 2019). The Stereolithography apparatus (SLA) is a popular method of vat polymerization, as it utilizes an ultraviolet (UV) laser beam to scan the surface of a liquid monomer and solidify it into a polymer (Karakurt and Lin, 2020; Zhang et al., 2019). The layers, which are composed of square pixels called voxels, are displayed one at a time on a digital light projector screen in direct light processing (DLP) (Hou et al., 2021). Similarly, the 3SP method involves scanning, spinning, and selective photocuring. Each layer of photopolymer is solidified using the laser’s ultraviolet beam as it rapidly scans in the X direction while moving the laser in the Y direction (Paritala et al., 2023). By positioning an oxygen-permeable window beneath the UV image projection plane and establishing a “dead zone” between the window and the polymerizing component, the continuous liquid interface production (CLIP) process is carried out (Xiao et al., 2019). The polymer is cured by photocentricity polymer printing, which uses an LCD rather than a laser. Using a nozzle, the plastic filament is extruded and deposited layer by layer using FDM (Fused Deposition Modelling), also referred to as FFF (Fused Filament Fabrication), along a predefined path (Shim et al., 2020; Geng et al., 2020). Using many jets on a building platform, Multi-Jet Modelling (MJM) blends ultra-thin layers of photopolymer materials before curing them with UV light. Figure 11 illustrates the state-of-the-art methods and shows the cutting-edge of these processes.
For this printing technique to be effective it is required to determine the ideal mix of printing needs and the printing properties of the materials (Bedarf et al., 2021; Piedra-Cascón et al., 2021). The technology utilized to produce concrete in 3D printing often involves either gantry-based or robotics-based systems. In the latter, the printing head is coupled to a robot and two peristaltic pumps, with one pump delivering the concrete material and the other serving as an accelerator (Dilberoglu et al., 2021). The printing head and the two pumps are controlled by a microcontroller, making the entire process highly precise. In contrast, a gantry-based printer utilizes a hose from the mixer that is attached to the printer head, which is managed using a four-degree freedom mechanism. The printing head in this case is equipped with a nozzle, which can be made of steel and is available in different sizes and shapes (Baumgartner et al., 2020). Due to its effect on interlayer bonding and compressive strength, the nozzle is a crucial part of 3DP (Lakkala et al., 2023). There are two main types of nozzles: screw and plunger types (Li et al., 2019). Common shapes for nozzle graphics include circles, ellipses, and rectangles (Tabassum et al., 2023; Gallego-Schmid et al., 2020; Joensuu et al., 2020). The concrete printing process typically employs trowels in contour crafting to achieve a high level of smoothness, which is a key factor in the production of concrete structures (Pazhamannil and Govindan, 2021). There are several popular 3D printing technologies used in concrete construction, including extrusion printing, Powder Jetting, and 3D printed formwork. Each of these methods has its own unique advantages and disadvantages, making it important to select the appropriate method for the specific application (Lipkowitz et al., 2022). Following the inputs from a CAD tool, the extrusion printing method (EPM) and the binder jetting method (BJM) are commonly utilized. It is pertinent to note that the concrete used for 3D printing applications has a more substantial positive impact on the environment, which contributes to the reduction of greenhouse gas emissions (Dilberoglu et al., 2021; Cano-Vicent et al., 2021). The development of sustainable 3DP concrete technology presents a major technological challenge that involves minimizing the ecological impact of the material through the reduction of cement content in the concrete mixture. The creation of concrete is attributed to the combination of water, fine and coarse aggregates, mineral additives, and cement.
Through the process of hydration, a viscous paste is formed for the bound mixture. While research on printable concrete is still in its early stages, there is currently no established standard for composition. The size of the printable mortar produced by 3D printing is limited due to the nozzle size and printing resolution used, which affects the compressive strength and formation of bulk concrete. By substituting SCM for Portland cement, the characteristics of printable concrete in its fresh and hardened states are improved, resulting in better performance of the final printed product. Unlike conventional concrete, which requires a higher amount of water, 3D printing concrete requires less water due to its rapid setting, low slump, and high strength. Additives such as accelerators, retarders, and superplasticizers are used to control the workability of printed concrete. These components are added to the mixture to regulate the workability of printed concrete (Vyavahare et al., 2020).
Geopolymer concrete technology involves the use of an alkali-based compound known as geopolymer, which is responsible for activating amorphous alumino silicate materials (Dilberoglu et al., 2021; Nematollahi et al., 2017; Assi et al., 2020). Amorphous alumino silicate minerals, such as FA, natural zeolite, and blast furnace slag (BFS) are commonly employed in geopolymer concrete production to minimize the impact on the environment (Prabhakar et al., 2021). Sodium hydroxide is frequently utilized as alkali activator in the production of geopolymers, which are renowned for their diminished environmental footprint (Li et al., 2020; Heidarnezhad and Zhang, 2022). Sodium hydroxide and sodium silicate are the primary components of geopolymers, their employment leads to the reduction in both waste and GHG emissions (Shobeiri et al., 2021). The utilization of geopolymer concrete diminishes the demand for Portland cement, consequently minimizing the environmental impact when compared to traditional OPC concrete (Heidarnezhad and Zhang, 2022). Studies in the relevant literature indicate that geopolymer concrete generally has a lower global warming impact than OPC-based concrete (Miclette et al., 2022; Bard et al., 2018; à Moungam et al., 2017; Chen et al., 2021).
The utility of bootstrapping statistical analysis (BSA) in the context of project management to assess overall project success (OPS) as conducted by Waqar et al. (2023b), which encompasses five dimensions: economic cost, time, quality, safety, and the environment is relevant for this systematic research review. As illustrated in Figure 12, the stages of material functionality, creativity, standardization, and sustainability (along with their relative contributions) significantly play critical role in the successful execution and completion of 3D printing construction projects in the built environment.
Figure 12. Path coefficients for 3D printing construction project completion (Waqar et al., 2023b).
AM technologies enable precise control over material composition and microstructure, this premise is validly applicable to construction industry. Lightweight lattice structures made from recycled PET composites often demonstrate high strength-to-weight ratios to enhance their applicability (Patel et al., 2023; Pal et al., 2021). Systematic assessments demonstrates the feasibility of using lignin-based resins in stereolithography (SLA), highlighting their potential as a sustainable photopolymer (Behera et al., 2024). The assimilation of natural fibres such hemp, jute, and bamboo into bio-based matrices can be more functional using AM techniques. In such case, fibre orientation is controlled to enhance anisotropic properties for structural applications in FDM printing of PLA reinforced with bamboo fibres to achieve improved tensile strength and biodegradability (Ismail et al., 2022). Pellet-based 3DCP AM systems augment this capability by processing recycled feedstock without additional compounding procedures. Extrusion-based AM using rPET demonstrates high-quality prints with minimal degradation of mechanical properties (Patel et al., 2023). Recycled polymers combined with additives or reinforcements can match the performance of raw materials. Upcycling waste coffee grounds into bio-composite filaments of FDM demonstrates potential for eco-friendly designs (Rivera et al., 2023). Topology optimization algorithms can be incorporated into the design process to ensure the efficient use of bio-based or recycled inputs. Multi-material printing in 3DP AM facilitates the integration of diverse materials into singular structure. This capability is essential for hybridizing bio-based composites with synthetic reinforcements to enhance adhesion in recycled composites composed of heterogeneous materials. Failed prints and post-production wastes can be shredded and reprocessed to reduce the demand for raw materials. A closed-loop process using recycled polypropylene enabled the production of building components with reduced environmental footprints (Patel et al., 2023). Consequently, this systematic research delineates significant material innovations capacitated by AM highlighting biobased, recycled, and advanced composites that conform to the concepts of circular economy and carbon mitigation. The materials not only leverage industrial byproducts and renewable resources but also enhance the performance, durability, and sustainability of construction components. Table 7 concisely provides detailed process categorization of AM material innovations, highlighting their environmental impacts, application, potentials, and roles in reducing the carbon footprint of the built environment.
The construction industry is known to have significantly contribute to global GHG emissions, accounts for an immense share of embodied and operational carbon emissions during the lifecycle of buildings. Recent improvements in structural optimization and automation in construction have demonstrated potential in mitigating environmental impacts by boosting material efficiency, minimizing waste, and improving overall sustainability (Patel et al., 2023; Pal et al., 2021). Structural optimization is a computational technique utilized to design structures that attain optimal performance within specified constraints (Behera et al., 2024; Ismail et al., 2022). When this technology is being applied to modular construction, the technique reinstates to improve strength, efficiency, and sustainability of prefabricated components. Modular construction involves fabricating building modules in a controlled off-site environment and assembling them on-site, offering a streamlined efficient alternative to conventional construction techniques. Research studies on modular construction reinforce the environmental benefits of prefabrication, including less waste generation and faster construction timelines (Rivera et al., 2023; Afzal et al., 2023). Within this framework, topology optimization is employed to optimize material distribution for optimal strength-to-weight ratios, whilst shape optimization modifies component geometries to enhance load-bearing efficiency. Material optimization additionally enhances sustainability by integrating low-carbon materials, which include recycled steel or geopolymer concrete, to reduce embodied carbon (Cucuzza et al., 2024; Olivo et al., 2024).
Automation in construction, driven by advanced technologies such as robotics, artificial intelligence (AI), and Building Information Modeling (BIM) under the frameworks of Industry 4.0 and 5.0, as stipulated in this investigation, is revolutionizing the traditionally labour-intensive industry. This transformation enhances efficiency, precision, and sustainability while lowering GHG emissions in the built environment (Qiang et al., 2023). Automating repetitive tasks such as bricklaying and welding, robotics enhances precision and significantly reduces material waste. Similarly, 3D printing enables the direct fabrication of components or entire structures using sustainable materials, significantly reducing offcuts and waste. BIM further optimizes construction processes by facilitating precise planning and resource allocation, leading to reduced material waste and improved project outcomes. These jointly, the technologies address inefficiencies and environmental challenges in the construction industry. Incorporating structural optimization with automation amplifies their potential to reduce GHG emissions across the building lifecycle. Modular structures benefit from optimization techniques to create efficient designs, while automation enhances the speed and accuracy of their assembly (Afzal et al., 2023; Qiang et al., 2023). Collectively, these approaches enable transition to circular economy in construction industry where materials can be reused or recycled at the end the lifecycle of a building, which further lower emissions. Furthermore, optimized and automated systems facilitate the incorporation of renewable energy technologies, such as photovoltaic panels and energy-efficient HVAC systems into building designs (Hussein et al., 2021; Rosso et al., 2022). As these methods scale, they contribute significantly to meeting global climate targets by reducing emissions at both the embodied and operational phases of the building lifecycle.
AM as transformative technology in the construction industry, offers solutions to mitigate GHG emissions and enhance sustainability. Incorporating analytical formulations optimize AM processes by improving material efficiency, energy savings, and structural performance. Advanced slicing algorithms and toolpath optimization models minimize material waste, energy use, and printing time. Thermal energy models and structural analysis frameworks ensure efficiency and durability, reducing lifecycle emissions (Khan et al., 2021c). Sustainability metrics, such as material utilization efficiency (MUE) and energy efficiency indices (EEI), quantify and improve environmental performance, while frameworks for GHG emissions calculation emphasize localized manufacturing benefits. Unified optimization models integrate emissions reduction, material efficiency, and structural optimization, positioning AM as a sustainable alternative for greener infrastructure development (Afzal et al., 2023; Khan et al., 2021c; Bhattacherjee et al., 2021b).
The mathematical formulations in Table 8 as deduced from the systematic research, establish a robust background for modeling and analysing the essential features of additive manufacturing (AM) in the construction industry, further consisting of precise geometric modeling and slicing (
The regulatory standards and policies play crucial role in driving the adoption of additive manufacturing (AM) in the construction industry. By ensuring safety, quality, and sustainability, these measures support the scalability of AM technologies. This, in turn, can lead to a substantial reduction in GHG emissions in the evolving built environment. The following are the essential functions of regulatory standards and policies in advancing the application of additive manufacturing for construction in the built environment.
AM technologies employed in construction have to conform to established safety requirements to prevent accidents, safeguard personnel, and preserve the integrity of the constructed structures. Safety regulations can guarantee that materials utilized in additive manufacturing are appropriate for construction applications and that procedures are executed adhering to health and safety wise. The American Society for Testing and Materials (ASTM) and other organizations have formulated specific standards for 3D printing materials, such as ASTM F42 for 3D print, which delineate regulations for material properties, quality control, and safety in construction applications. The European Committee for Standardization (CEN) is developing guidelines for 3D printing in construction to ensure safety and structural integrity in buildings and infrastructure projects such that it will be eco-friendly.
Regulatory frameworks can foster innovation in additive manufacturing by establishing clear pathways for the development and certification of novel materials and construction methods. A stable regulatory framework allows companies to innovate with AM technologies while ensuring that construction quality and performance adhere to national and international requirements. Adhering to standards ensures the reliability and reproducibility of AM output across diverse projects and locations, hence facilitating efforts for GHGs abatement. As construction involving 3D print projects become more complex and customized, standardization of practices for materials, testing, and construction methods becomes more imperative. The ISO/ASTM 52900 standard for AM processes establishes a uniform terminology, materials, and procedures, fostering greater adoption in construction.
Government policies can support to lower entry barriers into construction enterprises that seek to adopt additive manufacturing by offering aids on licensing requirements, consequently facilitating the integration of AM into their operations without concerns of legal or financial repercussions. Governments can create funding opportunities or incentives, such as tax refunds and stimulus, subsidies, or grants, to motivate industries to invest in AM technologies. Public-private partnerships can support novel projects that facilitate the development and testing of regulatory frameworks 3D printing that would enhance GHGs abatement.
Certifications are essential to ensure that AM processes and items utilized in building and construction adhere to established safety, performance, and durability standards, while also facilitating GHGs reduction exercises. The explicit requirements about certification and assurance instil credibility among stakeholders, including engineers, contractors, architects, and material suppliers, concerning the items and technologies employed. The International Code Council (ICC) in the United States has initiated the formulation of regulations for the application of AM in construction via its Evaluation Service (ICC-ES) and other entities, thus ensuring that AM construction parts can be certified as compliant with local building codes.
Environmental policies can facilitate the adoption of sustainable additive manufacturing technologies in construction by setting standards for waste minimization, energy efficiency, and the utilization of environmentally friendly materials thereby enhancing the abatement of GHGs. The regulatory standards can set objectives for carbon emissions reductions, promoting the adoption of additive manufacturing to develop more sustainable, resource-efficient constructions. For instance, the European Union establishes regulations mandating that buildings adhere to energy efficiency requirements, and additive manufacturing technology can contribute to lowering energy consumption during construction, hence mitigating GHG emissions in the built environment.
Policies can enhance the integration of AM technologies with other digital tools and platforms utilized in construction, such as Building Information Modeling (BIM). Regulations that promote data exchange and standardization can facilitate compatibility among various systems and optimize construction operations. The regulatory standards on data formats, intellectual property rights, and interoperability can allow for smoother collaboration across industries, enhancing the adoption of AM.
A primary concern in construction involves the legal and liability considerations that emerge with the adoption of new technologies such as additive manufacturing. Policies and standards can delineate responsibilities, ensuring that accountability for structural collapse, safety violations, or non-compliance with regulations is unequivocal. The insurance companies and regulators may collaborate to formulate policies that address the unique difficulties associated with AM, thereby comforting stakeholders.
Explicit regulations, requirements, and standards are essential for fostering public confidence in the dependability and safety of AM technologies. Regulatory bodies can establish criteria to ensure additive manufacturing techniques are both innovative and accountable and eco-friendly for GHG abatement, thereby enhancing their acceptance among the public and industry experts. When countries such as the United States, the United Kingdom, and China implement government-sanctioned standards for additive manufacturing in building, they indicate to the public that these technologies adhere to stringent safety and quality regulations. This approach can be adapted also for developing economies. For better grasp, the role of regulatory standard and policies are here presented in Table 10.
As an emerging technological process in construction, AM demonstrates significant potential to improve sustainability, reduce costs, optimize energy use, and substantially mitigate GHG emissions. Consequently, it enhances the built environment, making it more eco-friendly and sustainable. This case study evaluates the environmental and economic impacts of additive manufacturing, reiterating its potential for adaptation in the construction industry as a superior alternative to conventional subtractive methods. The analysis accentuates more on operational and initial costs, energy savings, material efficiency, and the reduction of GHG emissions. This is as presented in the metric of Table 11. As provided in Table 11, it can be seen that AM offers significant savings in material costs (up to 50%) and labour costs (up to 70%) compared to traditional manufacturing methods, while consuming 30%–50% less energy due to more efficient material deposition and reduced operational complexity. AM can achieve up to 90% material efficiency, reducing material waste by up to 70%, and has the potential to cut GHG emissions by 40%–60% through lowering waste, reduced energy use, and even minimized transportation emissions, making it a more sustainable and cost-effective alternative for the construction industry.
This is exemplified in Figure 13 which showcases real-world applications of AM and 3D-printing technologies for constructing main buildings and other housing components, aiming to minimize carbon and greenhouse gas emissions in the built environment (Craveiro et al., 2019; Bos et al., 2016; Dilberoglu et al., 2021), as support, Figure 14 demonstrates the infographics information on clean energy, sustainability with Industry ‘X.0’ on adapting AM technologies in construction industry (Odufuwa et al., 2024; Yitmen et al., 2024).
Figure 13. Real-world AM/3DP applications in construction to reduce emissions. Adapted from Dilberoglu et al. (2021), Craveiro et al. (2019), Bos et al. (2016).
Figure 14. Infographic representation of clean energy, sustainability with Industry X.0 in construction adapted from (Odufuwa et al., 2024; Yitmen et al., 2024).
Drawing on this systematic review, the assessments herein further address prospects for the novel research domain with potential areas of interest that could be investigated in future work.
The following knowledge gaps are envisaged.
1. Limited data specific to construction
i. While AM applications are well-documented in sectors like aerospace and biomedical, there is insufficient empirical data on its direct application and long-term benefits in the construction industry.
ii. Comparative studies between AM and TSM methods often focus on idealized scenarios rather than real-world, large-scale construction projects.
iii. Lack of comprehensive life-cycle analyses specific to AM technologies in construction, including indirect emissions during construction, material production and equipment use.
2. Material limitation and development
i. Although significant advancements have been made in materials such as polymers and composites, the development of construction-specific materials such as durable, eco-friendly concretes for AM are still in their infancy.
ii. Limited research into the recyclability and long-term performance of AM produced components for construction in built environment.
3. Standardization and regulation
i. There is absence of universally accepted standards, guidelines, and certifications for AM processes and materials in the construction industry which can cushion the GHGs abatement measures.
ii. There are regulatory challenges related to safety, structural integrity, and quality control in AM-built eco-friendly structures.
4. Economic viability
i. There are limited cost-benefit analytics studies, particularly in the developing regions, to determine the feasibility of AM integration to construction in order to limit the accounted GHG emissions of the industry.
ii. The high initial investment and operational costs with the rewards (environmental and economic) associated with AM technologies are underexplored in relation to traditional techniques.
5. Social and workforce impacts
i. There have been minor focus on how the widespread adoption of AM technologies can affect the labour markets and skill acquisitions in the construction industry.
ii. There have been potential resistance from stakeholders due to lack of awareness or perceived technological complexity.
As a result of these, the following future perspectives are deduced.
1. Integration of advanced technologies
i. Investigating the synergies between AM and Industry 4.0 technologies such as robotics, IoT, and AI alongside the human-centric approach of Industry 5.0 is essential. The integration can further improve the automation and optimization of construction operations, thereby aiding in the effective reduction of GHG emissions.
ii. The investigation of digital twin technologies to simulate and forecast the performance of AM-built eco-friendly structures.
2. Sustainability and circular economy
i. The research into the application of recycled or bio-based materials designed for additive manufacturing to promote sustainability, subsequently, GHGs abatement.
ii. The development of closed-loop systems where AM processes reuse construction wastes and byproducts as input materials.
3. Hybrid manufacturing approaches
i. The combination of additive manufacturing with conventional traditional and subtractive techniques to develop hybrid operations that leverage the merits of the approaches.
ii. Evaluating the feasibility of employing additive manufacturing for intricate construction components while preserving conventional methods for mass production, contingent upon a thorough assessment of economic and environmental considerations.
4. Policy and standardization framework
i. Developing international standards and policies to regulate additive manufacturing methods in construction while maintaining adherence to sustainability objectives, this particularly as documented in the order of SDG nine and SDG eight to be applied.
ii. Partnership among stakeholders such as government, industry, academia to provide incentive mechanisms for the prompt adoption of additive manufacturing in construction industry.
5. Scaling and accessibility
i. Enhancing additive manufacturing technology for large-scale production in extensive construction projects.
ii. Minimizing the costs and intricacies of additive manufacturing systems to ensure accessibility for small and medium enterprises (SMEs) and developing countries.
6. Long-term impact studies
i. Implementing longitudinal studies to evaluate the longevity, environmental impact, and economic benefits of AM-built structures over time.
ii. The investigation of the consequences of an unchecked additive manufacturing adoption, such as resource and material depletion or alterations in urban planning.
By resolving the captured research gaps and exploring future directions, sustainable additive manufacturing can be more assimilated into the construction industry. This incorporation is supported by the comparative analyses in Figure 15, which are informed by the metrics outlined in Table 11. Figure 15, which presents the comparison metrics further analyzed for greater clarity and detailed in Table 12 as weighted economic implications of a sustainable AM applications in construction industry. This facilitates the shift towards environmentally sustainable practices for GHGs abatement. Table 13 provides more concise knowledge gaps with future perspectives for construction industry, targeted for the reduction of GHG emissions in the built environment. Furthermore, Figure 16 presents the analytical diagrammatic interpretations of Table 9 (for Node A), Table 10 (for Node C), and the subsequent Table 13 (for Node B), all together depict how the systematic research fits in to people, process, product and policy for sustainable design in construction industry. The decision Node A denotes inputs from regulatory, standards and policy. The decision Node B presents the knowledge perspectives as provided in Table 10 while decision Node C is the metric criterion of case-study. Their interactions and interconnections, with appropriate implementations (measures 1–13), are essential determinants for achieving sustainable manufacturing designs for the industry, particularly with effect to the reduction of GHG emissions in the built environment, as here proposed.
Figure 15. Metrics comparison of additive manufacturing with conventional (traditional) manufacturing.
Figure 16. Systems sustainable practices for product-centric design in AM 3DP adaptation for construction.
The section further presents an overview of the detailed identified research endeavours and concerns found from the systematic examination of academic studies and professional practices. Furthermore, it addresses the requirements for AM in the construction industry to mitigate GHG emissions in the built environment. This is accomplished by considering diverse challenges related to technology, the environment, the society, and the economy by proffering more salient recommendations for sustainable future advances.
1. The use of 3D print coupled to other peripherals of an additive manufacturing technology for concrete formations make it possible to create design that are high-performing of diversified designs without exacerbating both economic and environmental costs. Considering this, our quality and production engineering assessments have the potential to make contributions to the reduction of GHG emissions in the built environment.
2. To improve the durability and strength of additive manufacturing materials and processes for construction, it is essential to develop sustainable and long-lasting binders. Binders such as geopolymer and fibers can be utilized with Ordinary Portland Cement (OPC) or as substitutes, thereby contributing to an eco-friendly sustainable built environment.
3. In contrast to traditional conventional techniques, incorporating renewable and clean energy in concrete production through 3D printing with formation of micro-structure of materials can significantly mitigate GHG emissions and enhance energy efficiency.
4. Establishing material hierarchy for climate change initiatives corresponding to their carbon footprint is essential, while also evaluating the potential rebound effects and burden-shifting linked to the negative consequences of GHG emissions and, consequently, global warming.
The incorporation of additive manufacturing in the construction industry presents a viable alternative to traditional subtractive methods. From an economic perspective, additive manufacturing provides reductions in labour and material costs, with possible savings ranging drawn to 60% in specific designed applications. AM technologies offer significant environmental benefits, including up to 60% energy savings compared to conventional methods, up to 90% reduction in material waste, and approximately 80% decrease in GHG emissions under well-designed methodologies. In pursuit of sustainability objectives, AM process control encompasses input-output and product factors to address critical aspects such as environmental impact, energy consumption, waste management, and economic costs. This technology holds considerable potentials for improving the construction industry in reaching sustainability targets in both environmental and economic with the social spheres. The integration of 3D printing in the construction sector is largely dependent on the precision of the printing tasks, the availability of printing materials, the cost of the printing technique, and the duration of printing. These considerations influence the choice of acceptable AM technologies, which include binder jetting, material deposition, stereolithography, fused deposition modeling, inkjet powder printing, selective laser sintering, selective thermal sintering, and contour crafting. Metal-based products can be produced using selective laser sintering, whilst cementitious and ceramic items can be produced with contour crafting, among other feasible approaches. Several benefits have been identified, including design adaptability, reduced labor needs, waste reduction, and decreased energy use, notably for GHG emission mitigation. Identified benefits include less waste, more design flexibility, and reduced manpower. With the current environmental impacts due to increasing GHG emissions emanating from the built environment, sustainable, innovative, and efficient techniques such as 3DCP can be adapted in the construction industry. The study evaluates the viability of 3D printing technology for developing sustainable concrete structures in the built environment to mitigate carbon emissions. It primarily emphasizes the full adaptability of 3D printing technology to enhance the sustainability of the construction industry, with a specific focus on reducing GHG emissions. Future research could explore other building components and segments to identify additional energy and material-saving strategies that further contribute to GHG emissions reduction. Other approaches, such as direct carbon dioxide (CO2) capture and extraction from the atmosphere, can further be investigated in addition to reducing GHG emissions in the construction industry of the built environment. With the advancement of AM technology, its demonstrated benefits are expected to increase substantially, positioning AM as an essential instrument for improving sustainability, cost-efficiency, and eco-friendly construction industry, this in no distant future.
The original contributions presented in the study are included in the article/Supplementary Material, further inquiries can be directed to the corresponding authors.
OJO: Conceptualization, Data curation, Formal Analysis, Investigation, Methodology, Resources, Software, Validation, Visualization, Writing–original draft, Writing–review and editing. CKML: Funding acquisition, Supervision, Validation, Visualization, Writing–review and editing. IDI: Supervision, Validation, Visualization, Writing–review and editing. OAO: Funding acquisition, Supervision, Visualization, Writing–review and editing.
The author(s) declare that no financial support was received for the research, authorship, and/or publication of this article.
In measures, appreciation is extended to PolyU-NAMI 3D Concrete Robotic Printing Research Centre and The Laboratory for Artificial Intelligence in Design for offering short courses, conferences, and presentations during the research exchange collaboration being hosted by the Department of Industrial and Systems Engineering at The Hong Kong Polytechnic University, Hong Kong. Nevertheless, gratitude is extended to the American Society for Testing and Materials (ASTM) for the ICAM 2023 symposia and conferences with sessions for courses and exhibition held in Washington, United States. Altogether, made an invaluable blend of academia, research, innovation, and enterprise.
The authors declare that the research was conducted in the absence of any commercial or financial relationships that could be construed as a potential conflict of interest.
The author(s) declare that no Generative AI was used in the creation of this manuscript.
All claims expressed in this article are solely those of the authors and do not necessarily represent those of their affiliated organizations, or those of the publisher, the editors and the reviewers. Any product that may be evaluated in this article, or claim that may be made by its manufacturer, is not guaranteed or endorsed by the publisher.
The Supplementary Material for this article can be found online at: https://www.frontiersin.org/articles/10.3389/fbuil.2025.1535626/full#supplementary-material
Abu-Ennab, L., Dixit, M., Birgisson, B., and Kumar, P. P. (2022). Comparative life cycle assessment of large-scale 3D printing utilizing kaolinite-based calcium sulfoaluminate cement concrete and conventional construction. Clean. Environ. Syst. 5, 100078. doi:10.1016/j.cesys.2022.100078
Adel, A. (2022). Future of industry 5.0 in society: human-centric solutions, challenges and prospective research areas. J. Cloud Comput. 11 (1), 40. doi:10.1186/s13677-022-00314-5
Afzal, M., Li, R. Y. M., Ayyub, M. F., Shoaib, M., and Bilal, M. (2023). Towards BIM-based sustainable structural design optimization: a systematic review and industry perspective. Sustainability 15 (20), 15117. doi:10.3390/su152015117
Ahmed, G. H. (2023). A review of “3D concrete printing”: materials and process characterization, economic considerations and environmental sustainability. J. Build. Eng. 66, 105863. doi:10.1016/j.jobe.2023.105863
Ahmed Ali, K., Ahmad, M. I., and Yusup, Y. (2020). Issues, impacts, and mitigations of carbon dioxide emissions in the building sector. Sustainability 12 (18), 7427. doi:10.3390/su12187427
Al Rashid, A., Khan, S. A., Al-Ghamdi, S. G., and Koç, M. (2020). Additive manufacturing: technology, applications, markets, and opportunities for the built environment. Automation Constr. 118, 103268. doi:10.1016/j.autcon.2020.103268
Altıparmak, S. C., Yardley, V. A., Shi, Z., and Lin, J. (2022). Extrusion-based additive manufacturing technologies: state of the art and future perspectives. J. Manuf. Process. 83, 607–636. doi:10.1016/j.jmapro.2022.09.032
à Moungam, L. M. B., Mohamed, H., Kamseu, E., Billong, N., and Melo, U. C. (2017). Properties of geopolymers made from fired clay bricks wastes and rice husk ash (RHA)-sodium hydroxide (NaOH) activator. Mater. Sci. Appl. 8 (7), 537–552. doi:10.4236/msa.2017.87037
Anastasiades, K., Goffin, J., Rinke, M., Buyle, M., Audenaert, A., and Blom, J. (2021). Standardisation: an essential enabler for the circular reuse of construction components? A trajectory for a cleaner European construction industry. J. Clean. Prod. 298, 126864. doi:10.1016/j.jclepro.2021.126864
Aramian, A., Razavi, N., Sadeghian, Z., and Berto, F. (2020). A review of additive manufacturing of cermets. Addit. Manuf. 33, 101130. doi:10.1016/j.addma.2020.101130
Arefin, A. M., Khatri, N. R., Kulkarni, N., and Egan, P. F. (2021). Polymer 3D printing review: materials, process, and design strategies for medical applications. Polymers 13 (9), 1499. doi:10.3390/polym13091499
Ashima, R., Haleem, A., Bahl, S., Javaid, M., Mahla, S. K., and Singh, S. (2021). Automation and manufacturing of smart materials in Additive Manufacturing technologies using Internet of Things towards the adoption of Industry 4.0. Mater. Today Proc. 45, 5081–5088. doi:10.1016/j.matpr.2021.01.583
Assi, L. N., Carter, K., Deaver, E., and Ziehl, P. (2020). Review of availability of source materials for geopolymer/sustainable concrete. J. Clean. Prod. 263, 121477. doi:10.1016/j.jclepro.2020.121477
Augustyn, J. (2016). Emerging science and technology Trends: 2016-2045: a synthesis of leading forecasts. Los Angeles, CA: Future Scout.
Ayub, M., Othman, M. H. D., Khan, I. U., Hubadillah, S. K., Kurniawan, T. A., Ismail, A. F., et al. (2021). Promoting sustainable cleaner production paradigms in palm oil fuel ash as an eco-friendly cementitious material: a critical analysis. J. Clean. Prod. 295, 126296. doi:10.1016/j.jclepro.2021.126296
Baduge, S. K., Thilakarathna, S., Perera, J. S., Arashpour, M., Sharafi, P., Teodosio, B., et al. (2022). Artificial intelligence and smart vision for building and construction 4.0: machine and deep learning methods and applications. Automation Constr. 141, 104440. doi:10.1016/j.autcon.2022.104440
Baduge, S. K. S. K., et al. (2021). “Improving performance of additive manufactured (3D printed) concrete: a review on material mix design, processing, interlayer bonding, and reinforcing methods,”, 29. Elsevier, 1597–1609. Structures. doi:10.1016/j.istruc.2020.12.061
Bajpayee, A., Farahbakhsh, M., Zakira, U., Pandey, A., Ennab, L. A., Rybkowski, Z., et al. (2020). In situ resource utilization and reconfiguration of soils into construction materials for the additive manufacturing of buildings. Front. Mater. 7, 52. doi:10.3389/fmats.2020.00052
Bard, J., Cupkova, D., Washburn, N., and Zeglin, G. (2018). Robotic concrete surface finishing: a moldless approach to creating thermally tuned surface geometry for architectural building components using Profile-3D-Printing. Constr. Robot. 2 (1), 53–65. doi:10.1007/s41693-018-0014-x
Batikha, M., Jotangia, R., Baaj, M. Y., and Mousleh, I. (2022). 3D concrete printing for sustainable and economical construction: a comparative study. Automation Constr. 134, 104087. doi:10.1016/j.autcon.2021.104087
Baumgartner, S., Gmeiner, R., Schönherr, J. A., and Stampfl, J. (2020). Stereolithography-based additive manufacturing of lithium disilicate glass ceramic for dental applications. Mater. Sci. Eng. C 116, 111180. doi:10.1016/j.msec.2020.111180
Bazli, M., Ashrafi, H., Rajabipour, A., and Kutay, C. (2023). 3D printing for remote housing: benefits and challenges. Automation Constr. 148, 104772. doi:10.1016/j.autcon.2023.104772
Bedarf, P., Dutto, A., Zanini, M., and Dillenburger, B. (2021). Foam 3D printing for construction: a review of applications, materials, and processes. Automation Constr. 130, 103861. doi:10.1016/j.autcon.2021.103861
Behera, P. K., Dhamaniya, S., Mohanty, S., and Gupta, V. (2024). “Advances in thermoplastic polyurethane elastomers: design, applications and their circularity,” in Advances in thermoplastic elastomers (Elsevier), 407–444. doi:10.1016/B978-0-323-91758-2.00014-3
Belaïd, F. (2022). How does concrete and cement industry transformation contribute to mitigating climate change challenges? Resour. Conservation & Recycl. Adv. 15, 200084. doi:10.1016/j.rcradv.2022.200084
Bhattacherjee, S., Basavaraj, A. S., Rahul, A., Santhanam, M., Gettu, R., Panda, B., et al. (2021a). Sustainable materials for 3D concrete printing. Cem. Concr. Compos. 122, 104156. doi:10.1016/j.cemconcomp.2021.104156
Bhattacherjee, S., Basavaraj, A. S., Rahul, A. V., Santhanam, M., Gettu, R., Panda, B., et al. (2021b). Sustainable materials for 3D concrete printing. Cem. Concr. Compos. 122, 104156. doi:10.1016/j.cemconcomp.2021.104156
Borowski, P. F. (2021). Digitization, digital twins, blockchain, and industry 4.0 as elements of management process in enterprises in the energy sector. Energies 14 (7), 1885. doi:10.3390/en14071885
Bos, F., Wolfs, R., Ahmed, Z., and Salet, T. (2016). Additive manufacturing of concrete in construction: potentials and challenges of 3D concrete printing. Virtual Phys. Prototyp. 11 (3), 209–225. doi:10.1080/17452759.2016.1209867
Bos, F. P., Menna, C., Pradena, M., Kreiger, E., da Silva, W. L., Rehman, A., et al. (2022). The realities of additively manufactured concrete structures in practice. Cem. Concr. Res. 156, 106746. doi:10.1016/j.cemconres.2022.106746
Caineng, Z., Ma, F., Pan, S., Lin, M., Zhang, G., Xiong, B., et al. (2022). Earth energy evolution, human development and carbon neutral strategy. Petroleum Explor. Dev. 49 (2), 468–488. doi:10.1016/S1876-3804(22)60040-5
Cano-Vicent, A., Tambuwala, M. M., Hassan, S. S., Barh, D., Aljabali, A. A., Birkett, M., et al. (2021). Fused deposition modelling: current status, methodology, applications and future prospects. Addit. Manuf. 47, 102378. doi:10.1016/j.addma.2021.102378
Carneau, P., Mesnil, R., Roussel, N., and Baverel, O. (2020). Additive manufacturing of cantilever-From masonry to concrete 3D printing. Automation Constr. 116, 103184. doi:10.1016/j.autcon.2020.103184
Casini, M. (2021). Construction 4.0: advanced technology, tools and materials for the digital transformation of the construction industry. Woodhead Publishing.
Çetin, S., De Wolf, C., and Bocken, N. (2021). Circular digital built environment: an emerging framework. Sustainability 13 (11), 6348. doi:10.3390/su13116348
Chen, K., Wu, D., Xia, L., Cai, Q., and Zhang, Z. (2021). Geopolymer concrete durability subjected to aggressive environments–A review of influence factors and comparison with ordinary Portland cement. Constr. Build. Mater. 279, 122496. doi:10.1016/j.conbuildmat.2021.122496
Chen, S., Ruan, S., Zeng, Q., Liu, Y., Zhang, M., Tian, Y., et al. (2022b). Pore structure of geopolymer materials and its correlations to engineering properties: a review. Constr. Build. Mater. 328, 127064. doi:10.1016/j.conbuildmat.2022.127064
Chen, Z., Han, C., Gao, M., Kandukuri, S. Y., and Zhou, K. (2022a). A review on qualification and certification for metal additive manufacturing. Virtual Phys. Prototyp. 17 (2), 382–405. doi:10.1080/17452759.2021.2018938
Çimen, Ö. (2021). Construction and built environment in circular economy: a comprehensive literature review. J. Clean. Prod. 305, 127180. doi:10.1016/j.jclepro.2021.127180
Classen, M., Ungermann, J., and Sharma, R. (2020). Additive manufacturing of reinforced concrete—development of a 3D printing technology for cementitious composites with metallic reinforcement. Appl. Sci. 10 (11), 3791. doi:10.3390/app10113791
Coffetti, D., Crotti, E., Gazzaniga, G., Carrara, M., Pastore, T., and Coppola, L. (2022). Pathways towards sustainable concrete. Cem. Concr. Res. 154, 106718. doi:10.1016/j.cemconres.2022.106718
Conejo, A. N., Birat, J.-P., and Dutta, A. (2020). A review of the current environmental challenges of the steel industry and its value chain. J. Environ. Manag. 259, 109782. doi:10.1016/j.jenvman.2019.109782
Craveiro, F., Duarte, J. P., Bartolo, H., and Bartolo, P. J. (2019). Additive manufacturing as an enabling technology for digital construction: a perspective on Construction 4.0. Automation Constr. 103, 251–267. doi:10.1016/j.autcon.2019.03.011
Cucuzza, R., Rad, M. M., Domaneschi, M., and Marano, G. C. (2024). Sustainable and cost-effective optimal design of steel structures by minimizing cutting trim losses. Automation Constr. 167, 105724. doi:10.1016/j.autcon.2024.105724
Daminabo, S. C., Goel, S., Grammatikos, S. A., Nezhad, H. Y., and Thakur, V. K. (2020). Fused deposition modeling-based additive manufacturing (3D printing): techniques for polymer material systems. Mater. today Chem. 16, 100248. doi:10.1016/j.mtchem.2020.100248
de Almeida Barbosa Franco, J., Domingues, A. M., de Almeida Africano, N., Deus, R. M., and Battistelle, R. A. G. (2022). Sustainability in the Civil construction sector supported by industry 4.0 technologies: challenges and opportunities. Infrastructures 7 (3), 43. doi:10.3390/infrastructures7030043
Deneault, J. R., Chang, J., Myung, J., Hooper, D., Armstrong, A., Pitt, M., et al. (2021). Toward autonomous additive manufacturing: Bayesian optimization on a 3D printer. MRS Bull. 46, 566–575. doi:10.1557/s43577-021-00051-1
de Souza, E. A., Borges, P. H., Stengel, T., Nematollahi, B., and Bos, F. P. (2024). 3D printed sustainable low-cost materials for construction of affordable social housing in Brazil: potential, challenges, and research needs. J. Build. Eng. 87, 108985. doi:10.1016/j.jobe.2024.108985
Dickson, A. N., Abourayana, H. M., and Dowling, D. P. (2020). 3D printing of fibre-reinforced thermoplastic composites using fused filament fabrication—a review. Polymers 12 (10), 2188. doi:10.3390/polym12102188
Dilberoglu, U. M., Gharehpapagh, B., Yaman, U., and Dolen, M. (2021). Current trends and research opportunities in hybrid additive manufacturing. Int. J. Adv. Manuf. Technol. 113, 623–648. doi:10.1007/s00170-021-06688-1
Ding, T., Xiao, J., Qin, F., and Duan, Z. (2020). Mechanical behavior of 3D printed mortar with recycled sand at early ages. Constr. Build. Mater. 248, 118654. doi:10.1016/j.conbuildmat.2020.118654
Dobrzyńska, E., Kondej, D., Kowalska, J., and Szewczyńska, M. (2021). State of the art in additive manufacturing and its possible chemical and particle hazards—review. Indoor air 31 (6), 1733–1758. doi:10.1111/ina.12853
Elbadawi, M., McCoubrey, L. E., Gavins, F. K., Ong, J. J., Goyanes, A., Gaisford, S., et al. (2021). Harnessing artificial intelligence for the next generation of 3D printed medicines. Adv. Drug Deliv. Rev. 175, 113805. doi:10.1016/j.addr.2021.05.015
Fan, J., Zhang, L., Wei, S., Zhang, Z., Choi, S. K., Song, B., et al. (2021). A review of additive manufacturing of metamaterials and developing trends. Mater. Today 50, 303–328. doi:10.1016/j.mattod.2021.04.019
Fan, M., and Fu, F. (2017). “Introduction: a perspective–natural fibre composites in construction,” in Advanced high strength natural fibre composites in construction (Elsevier), 1–20. doi:10.1016/B978-0-08-100411-1.00001-7
Fawzy, S., Osman, A. I., Doran, J., and Rooney, D. W. (2020). Strategies for mitigation of climate change: a review. Environ. Chem. Lett. 18, 2069–2094. doi:10.1007/s10311-020-01059-w
Flower, D. J., and Sanjayan, J. G. (2007). Green house gas emissions due to concrete manufacture. Int. J. life cycle Assess. 12, 282–288. doi:10.1065/lca2007.05.327
Flynn, J. M., Shokrani, A., Newman, S. T., and Dhokia, V. (2016). Hybrid additive and subtractive machine tools–Research and industrial developments. Int. J. Mach. Tools Manuf. 101, 79–101. doi:10.1016/j.ijmachtools.2015.11.007
Fraga-Lamas, P., Lopes, S. I., and Fernández-Caramés, T. M. (2021). Green IoT and edge AI as key technological enablers for a sustainable digital transition towards a smart circular economy: an industry 5.0 use case. Sensors 21 (17), 5745. doi:10.3390/s21175745
Gallego-Schmid, A., Chen, H.-M., Sharmina, M., and Mendoza, J. M. F. (2020). Links between circular economy and climate change mitigation in the built environment. J. Clean. Prod. 260, 121115. doi:10.1016/j.jclepro.2020.121115
Gao, W., Zhang, Y., Ramanujan, D., Ramani, K., Chen, Y., Williams, C. B., et al. (2015). The status, challenges, and future of additive manufacturing in engineering. Computer-aided Des. 69, 65–89. doi:10.1016/j.cad.2015.04.001
Garritty, C., Gartlehner, G., Nussbaumer-Streit, B., King, V. J., Hamel, C., Kamel, C., et al. (2021). Cochrane Rapid Reviews Methods Group offers evidence-informed guidance to conduct rapid reviews. J. Clin. Epidemiol. 130, 13–22. doi:10.1016/j.jclinepi.2020.10.007
Geng, Z., She, W., Zuo, W., Lyu, K., Pan, H., Zhang, Y., et al. (2020). Layer-interface properties in 3D printed concrete: Dual hierarchical structure and micromechanical characterization. Cem. Concr. Res. 138, 106220. doi:10.1016/j.cemconres.2020.106220
Gibson, I., Rosen, D., Stucker, B., and Khorasani, M. (2021). Binder jetting. Addit. Manuf. Technol., 237–252. doi:10.1007/978-3-030-56127-7_8
Go, J., and Hart, A. J. (2016). A framework for teaching the fundamentals of additive manufacturing and enabling rapid innovation. Addit. Manuf. 10, 76–87. doi:10.1016/j.addma.2016.03.001
Golewski, G. L. (2021). Green concrete based on quaternary binders with significant reduced of CO2 emissions. Energies 14 (15), 4558. doi:10.3390/en14154558
Grabowska, S., Saniuk, S., and Gajdzik, B. (2022). Industry 5.0: improving humanization and sustainability of Industry 4.0. Scientometrics 127 (6), 3117–3144. doi:10.1007/s11192-022-04370-1
Gu, D., Shi, X., Poprawe, R., Bourell, D. L., Setchi, R., and Zhu, J. (2021). Material-structure-performance integrated laser-metal additive manufacturing. Science 372 (6545), eabg1487. doi:10.1126/science.abg1487
Gupta, A. (2021). Investigation of the strength of ground granulated blast furnace slag based geopolymer composite with silica fume. Mater. Today Proc. 44, 23–28. doi:10.1016/j.matpr.2020.06.010
Gupta, V., Nesterenko, P., and Paull, B. (2019). 3D printing in chemical sciences: applications across chemistry. Chromatographia 82, 1733–1734. doi:10.1007/s10337-019-03788-9
Gür, T. M. (2022). Carbon dioxide emissions, capture, storage and utilization: review of materials, processes and technologies. Prog. Energy Combust. Sci. 89, 100965. doi:10.1016/j.pecs.2021.100965
Guzzi, E. A., and Tibbitt, M. W. (2020). Additive manufacturing of precision biomaterials. Adv. Mater. 32 (13), 1901994. doi:10.1002/adma.201901994
Habert, G., Miller, S. A., John, V. M., Provis, J. L., Favier, A., Horvath, A., et al. (2020). Environmental impacts and decarbonization strategies in the cement and concrete industries. Nat. Rev. Earth & Environ. 1 (11), 559–573. doi:10.1038/s43017-020-0093-3
Hao, J. L., Cheng, B., Lu, W., Xu, J., Wang, J., Bu, W., et al. (2020). Carbon emission reduction in prefabrication construction during materialization stage: a BIM-based life-cycle assessment approach. Sci. Total Environ. 723, 137870. doi:10.1016/j.scitotenv.2020.137870
Hegab, H., Khanna, N., Monib, N., and Salem, A. (2023). Design for sustainable additive manufacturing: a review. Sustain. Mater. Technol. 35, e00576. doi:10.1016/j.susmat.2023.e00576
Heidarnezhad, F., and Zhang, Q. (2022). Shotcrete based 3D concrete printing: state of art, challenges, and opportunities. Constr. Build. Mater. 323, 126545. doi:10.1016/j.conbuildmat.2022.126545
Holechek, J. L., Geli, H. M., Sawalhah, M. N., and Valdez, R. (2022). A global assessment: can renewable energy replace fossil fuels by 2050? Sustainability 14 (8), 4792. doi:10.3390/su14084792
Hossain, M. A., Zhumabekova, A., Paul, S. C., and Kim, J. R. (2020). A review of 3D printing in construction and its impact on the labor market. Sustainability 12 (20), 8492. doi:10.3390/su12208492
Hou, S., Duan, Z., Xiao, J., and Ye, J. (2021). A review of 3D printed concrete: performance requirements, testing measurements and mix design. Constr. Build. Mater. 273, 121745. doi:10.1016/j.conbuildmat.2020.121745
Hussein, M., Eltoukhy, A. E., Karam, A., Shaban, I. A., and Zayed, T. (2021). Modelling in off-site construction supply chain management: a review and future directions for sustainable modular integrated construction. J. Clean. Prod. 310, 127503. doi:10.1016/j.jclepro.2021.127503
Ibrahim, I., Eltarabishi, F., Abdalla, H., and Abdallah, M. (2022). 3D Printing in sustainable buildings: systematic review and applications in the United Arab Emirates. Buildings 12 (10), 1703. doi:10.3390/buildings12101703
Ingarao, G., and Priarone, P. C. (2020). A comparative assessment of energy demand and life cycle costs for additive-and subtractive-based manufacturing approaches. J. Manuf. Process. 56, 1219–1229. doi:10.1016/j.jmapro.2020.06.009
Iqbal, A., Zhao, G., Suhaimi, H., He, N., Hussain, G., and Zhao, W. (2020). Readiness of subtractive and additive manufacturing and their sustainable amalgamation from the perspective of Industry 4.0: a comprehensive review. Int. J. Adv. Manuf. Technol. 111, 2475–2498. doi:10.1007/s00170-020-06287-6
Ismail, K. I., Yap, T. C., and Ahmed, R. (2022). 3D-printed fiber-reinforced polymer composites by fused deposition modelling (FDM): fiber length and fiber implementation techniques. Polymers 14 (21), 4659. doi:10.3390/polym14214659
Issa, M. (2021). Additive manufacturing in the engineering and construction industry: development and potentiality. Master's thesis, Barcelona: Universitat Politècnica de Catalunya.
Izdebska-Podsiadły, J. (2022). “Classification of 3D printing methods,” in Polymers for 3D printing (Elsevier), 23–34. doi:10.1016/B978-0-12-818311-3.00009-4
Jacob, A., Windhuber, K., Ranke, D., and Lanza, G. (2018). Planning, evaluation and optimization of product design and manufacturing technology chains for new product and production technologies on the example of additive manufacturing. Procedia Cirp 70, 108–113. doi:10.1016/j.procir.2018.02.049
Jandyal, A., Chaturvedi, I., Wazir, I., Raina, A., and Haq, M. I. U. (2022). 3D printing–A review of processes, materials and applications in industry 4.0. Sustain. Operations Comput. 3, 33–42. doi:10.1016/j.susoc.2021.09.004
Javaid, M., Haleem, A., Singh, R. P., and Suman, R. (2021b). Industrial perspectives of 3D scanning: features, roles and it's analytical applications. Sensors Int. 2, 100114. doi:10.1016/j.sintl.2021.100114
Javaid, M., Haleem, A., Singh, R. P., Suman, R., and Rab, S. (2021a). Role of additive manufacturing applications towards environmental sustainability. Adv. Industrial Eng. Polym. Res. 4 (4), 312–322. doi:10.1016/j.aiepr.2021.07.005
Jayawardane, H., Davies, I. J., Gamage, J., John, M., and Biswas, W. K. (2023). “Sustainability perspectives–a review of additive and subtractive manufacturing,” in Sustainable manufacturing and service economics. doi:10.1016/j.smse.2023.100015100015
Jiang, J., and Ma, Y. (2020). Path planning strategies to optimize accuracy, quality, build time and material use in additive manufacturing: a review. Micromachines 11 (7), 633. doi:10.3390/mi11070633
Jiménez, M., Romero, L., Domínguez, I. A., Espinosa, M. d. M., and Domínguez, M. (2019). Additive manufacturing technologies: an overview about 3D printing methods and future prospects. Complexity 2019. doi:10.1155/2019/9656938
Jipa, A., and Dillenburger, B. (2022). 3D printed formwork for concrete: state-of-the-art, opportunities, challenges, and applications. 3D Print. Addit. Manuf. 9 (2), 84–107. doi:10.1089/3dp.2021.0024
Joensuu, T., Edelman, H., and Saari, A. (2020). Circular economy practices in the built environment. J. Clean. Prod. 276, 124215. doi:10.1016/j.jclepro.2020.124215
Jung, C., Al Qassimi, N., and Sherzad, M. (2022). The comparative analysis of 3D printing technology development for building construction. Int. J. Adv. Res. Technol. Innovation 4 (4), 56–67. doi:10.55057/ijarti.2022.4.4.5
Kalkal, A., Kumar, S., Kumar, P., Pradhan, R., Willander, M., Packirisamy, G., et al. (2021). Recent advances in 3D printing technologies for wearable (bio) sensors. Addit. Manuf. 46, 102088. doi:10.1016/j.addma.2021.102088
Kang, J.-N., Wei, Y.-M., Liu, L.-C., Han, R., Yu, B.-Y., and Wang, J.-W. (2020). Energy systems for climate change mitigation: a systematic review. Appl. Energy 263, 114602. doi:10.1016/j.apenergy.2020.114602
Karakurt, I., and Lin, L. (2020). 3D printing technologies: techniques, materials, and post-processing. Curr. Opin. Chem. Eng. 28, 134–143. doi:10.1016/j.coche.2020.04.001
Kawalkar, R., Dubey, H. K., and Lokhande, S. P. (2022). A review for advancements in standardization for additive manufacturing. Mater. Today Proc. 50, 1983–1990. doi:10.1016/j.matpr.2021.09.333
Khajavi, S. H., Partanen, J., and Holmström, J. (2014). Additive manufacturing in the spare parts supply chain. Comput. industry 65 (1), 50–63. doi:10.1016/j.compind.2013.07.008
Khan, A. H., López-Maldonado, E. A., Alam, S. S., Khan, N. A., López, J. R. L., Herrera, P. F. M., et al. (2022). Municipal solid waste generation and the current state of waste-to-energy potential: state of art review. Energy Convers. Manag. 267, 115905. doi:10.1016/j.enconman.2022.115905
Khan, M. M. H., Havukainen, J., and Horttanainen, M. (2021b). Impact of utilizing solid recovered fuel on the global warming potential of cement production and waste management system: a life cycle assessment approach. Waste Manag. & Res. 39 (4), 561–572. doi:10.1177/0734242X20978277
Khan, S. A., Koç, M., and Al-Ghamdi, S. G. (2021a). Sustainability assessment, potentials and challenges of 3D printed concrete structures: a systematic review for built environmental applications. J. Clean. Prod. 303, 127027. doi:10.1016/j.jclepro.2021.127027
Khan, S. A., Koç, M., and Al-Ghamdi, S. G. (2021c). Sustainability assessment, potentials and challenges of 3D printed concrete structures: a systematic review for built environmental applications. J. Clean. Prod. 303, 127027. doi:10.1016/j.jclepro.2021.127027
Khosravani, M. R., and Reinicke, T. (2020). On the environmental impacts of 3D printing technology. Appl. Mater. Today 20, 100689. doi:10.1016/j.apmt.2020.100689
Krishna, L. S. R., and Srikanth, P. (2021). Evaluation of environmental impact of additive and subtractive manufacturing processes for sustainable manufacturing. Mater. Today Proc. 45, 3054–3060. doi:10.1016/j.matpr.2020.12.060
Kuittinen, M., Zernicke, C., Slabik, S., and Hafner, A. (2023). How can carbon be stored in the built environment? A review of potential options. Archit. Sci. Rev. 66 (2), 91–107. doi:10.1080/00038628.2021.1896471
Kumar, M. B., and Sathiya, P. (2021). Methods and materials for additive manufacturing: a critical review on advancements and challenges. Thin-Walled Struct. 159, 107228. doi:10.1016/j.tws.2020.107228
Lakkala, P., Munnangi, S. R., Bandari, S., and Repka, M. (2023). Additive manufacturing technologies with emphasis on stereolithography 3D printing in pharmaceutical and medical applications: a review. Int. J. Pharm. 5, 100159. X. doi:10.1016/j.ijpx.2023.100159
Lee, C. K. M., Liang, J., Yung, K. L., and Keung, K. L. (2024). Generating TRIZ-inspired guidelines for eco-design using generative artificial intelligence. Adv. Eng. Inf. 62, 102846. doi:10.1016/j.aei.2024.102846
Lee, J.-Y., Nagalingam, A. P., and Yeo, S. (2021). A review on the state-of-the-art of surface finishing processes and related ISO/ASTM standards for metal additive manufactured components. Virtual Phys. Prototyp. 16 (1), 68–96. doi:10.1080/17452759.2020.1830346
Li, C., Wang, H., Liao, X., Xiao, R., Liu, K., Bai, J., et al. (2022). Heavy metal pollution in coastal wetlands: a systematic review of studies globally over the past three decades. J. Hazard. Mater. 424, 127312. doi:10.1016/j.jhazmat.2021.127312
Li, V. C., Bos, F. P., Yu, K., McGee, W., Ng, T. Y., Figueiredo, S. C., et al. (2020). On the emergence of 3D printable engineered, strain hardening cementitious composites (ECC/SHCC). Cem. Concr. Res. 132, 106038. doi:10.1016/j.cemconres.2020.106038
Li, Y., Mao, Q., Li, X., Yin, J., Wang, Y., Fu, J., et al. (2019). High-fidelity and high-efficiency additive manufacturing using tunable pre-curing digital light processing. Addit. Manuf. 30, 100889. doi:10.1016/j.addma.2019.100889
Lima, L., Trindade, E., Alencar, L., Alencar, M., and Silva, L. (2021). Sustainability in the construction industry: a systematic review of the literature. J. Clean. Prod. 289, 125730. doi:10.1016/j.jclepro.2020.125730
Lipkowitz, G., Samuelsen, T., Hsiao, K., Lee, B., Dulay, M. T., Coates, I., et al. (2022). Injection continuous liquid interface production of 3D objects. Sci. Adv. 8 (39), eabq3917. doi:10.1126/sciadv.abq3917
Lund, S., Manyika, J., Woetzel, J., Bughin, J., and Krishnan, M., (2019). Globalization in transition: the future of trade and value chains,
Malhi, G. S., Kaur, M., and Kaushik, P. (2021). Impact of climate change on agriculture and its mitigation strategies: a review. Sustainability 13 (3), 1318. doi:10.3390/su13031318
Malik, A., Haq, M. I. U., Raina, A., and Gupta, K. (2022). 3D printing towards implementing Industry 4.0: sustainability aspects, barriers and challenges. Industrial Robot Int. J. robotics Res. Appl. 49 (3), 491–511. doi:10.1108/IR-10-2021-0247
Manisalidis, I., Stavropoulou, E., Stavropoulos, A., and Bezirtzoglou, E. (2020). Environmental and health impacts of air pollution: a review. Front. public health 8, 14. doi:10.3389/fpubh.2020.00014
Martínez-García, A., Monzón, M., and Paz, R. (2021). “Standards for additive manufacturing technologies: structure and impact,” in Additive manufacturing (Elsevier), 395–408. doi:10.1016/B978-0-12-818411-0.00013-6
Mazzanti, V., Malagutti, L., and Mollica, F. (2019). FDM 3D printing of polymers containing natural fillers: a review of their mechanical properties. Polymers 11 (7), 1094. doi:10.3390/polym11071094
Mehrpouya, M., Dehghanghadikolaei, A., Fotovvati, B., Vosooghnia, A., Emamian, S. S., and Gisario, A. (2019). The potential of additive manufacturing in the smart factory industrial 4.0: a review. Appl. Sci. 9 (18), 3865. doi:10.3390/app9183865
Meng, L., Zhang, W., Quan, D., Shi, G., Tang, L., Hou, Y., et al. (2020). From topology optimization design to additive manufacturing: Today’s success and tomorrow’s roadmap. Archives Comput. Methods Eng. 27, 805–830. doi:10.1007/s11831-019-09331-1
Mengist, W., Soromessa, T., and Legese, G. (2020). Method for conducting systematic literature review and meta-analysis for environmental science research. MethodsX 7, 100777. doi:10.1016/j.mex.2019.100777
Merabet, G. H., Essaaidi, M., Haddou, M. B., Qolomany, B., Qadir, J., Anan, M., et al. (2021). Intelligent building control systems for thermal comfort and energy-efficiency: a systematic review of artificial intelligence-assisted techniques. Renew. Sustain. Energy Rev. 144, 110969. doi:10.1016/j.rser.2021.110969
Miclette, O., Côté, R., Demers, V., and Brailovski, V. (2022). Material extrusion additive manufacturing of low-viscosity metallic feedstocks: performances of the plunger-based approach. Addit. Manuf. 60, 103252. doi:10.1016/j.addma.2022.103252
Miller, S. A., Habert, G., Myers, R. J., and Harvey, J. T. (2021). Achieving net zero greenhouse gas emissions in the cement industry via value chain mitigation strategies. One Earth 4 (10), 1398–1411. doi:10.1016/j.oneear.2021.09.011
Moavenzadeh, F. (2022). “The construction industry,” in Shelter, Settlement & development (Routledge), 73–109. doi:10.4324/9781003271529
Mohamad, N., Muthusamy, K., Embong, R., Kusbiantoro, A., and Hashim, M. H. (2022). Environmental impact of cement production and Solutions: a review. Mater. Today Proc. 48, 741–746. doi:10.1016/j.matpr.2021.02.212
Mohamed, N. H., Khan, S., and Jagtap, S. (2023). Modernizing medical waste management: unleashing the power of the Internet of Things (IoT). Sustainability 15 (13), 9909. doi:10.3390/su15139909
Muñoz, I., Alonso-Madrid, J., Menéndez-Muñiz, M., Uhart, M., Canou, J., Martin, C., et al. (2021). Life cycle assessment of integrated additive–subtractive concrete 3D printing. Int. J. Adv. Manuf. Technol. 112, 2149–2159. doi:10.1007/s00170-020-06487-0
Nadarajah, N. (2018). “Development of concrete 3D printing,” in Master’s thesis. Espoo, Finland: Aalto University.
Naqi, A., and Jang, J. G. (2019). Recent progress in green cement technology utilizing low-carbon emission fuels and raw materials: a review. Sustainability 11 (2), 537. doi:10.3390/su11020537
Nematollahi, B., Xia, M., and Sanjayan, J. (2017). “Current progress of 3D concrete printing technologies,” in ISARC. Proceedings of the international symposium on automation and robotics in construction, 34. IAARC Publications.
Neupane, K. (2022). Evaluation of environmental sustainability of one-part geopolymer binder concrete. Clean. Mater. 6, 100138. doi:10.1016/j.clema.2022.100138
Newman, S. T., Zhu, Z., Dhokia, V., and Shokrani, A. (2015). Process planning for additive and subtractive manufacturing technologies. CIRP Ann. 64 (1), 467–470. doi:10.1016/j.cirp.2015.04.109
Niaki, M. K., Torabi, S. A., and Nonino, F. (2019). Why manufacturers adopt additive manufacturing technologies: the role of sustainability. J. Clean. Prod. 222, 381–392. doi:10.1016/j.jclepro.2019.03.019
Nižetić, S., Djilali, N., Papadopoulos, A., and Rodrigues, J. J. (2019). Smart technologies for promotion of energy efficiency, utilization of sustainable resources and waste management. J. Clean. Prod. 231, 565–591. doi:10.1016/j.jclepro.2019.04.397
Nodehi, M., and Mohamad Taghvaee, V. (2022). Sustainable concrete for circular economy: a review on use of waste glass. Glass Struct. & Eng. 7 (1), 3–22. doi:10.1007/s40940-021-00155-9
Oladunni, O. J., Mpofu, K., and Olanrewaju, O. A. (2022). Greenhouse gas emissions and its driving forces in the transport sector of South Africa. Energy Rep. 8, 2052–2061. doi:10.1016/j.egyr.2022.01.123
Oladunni, O. J., and Olanrewaju, O. A. (2022). Effects of the impact factors on transportation sector’s CO2-eq emissions: panel evaluation on South Africa’s major economies. Atmosphere 13 (10), 1705. doi:10.3390/atmos13101705
Oladunni, O. J., Olanrewaju, O. A., and Lee, C. K. (2024). The Environmental Kuznets Curve (EKC) Hypothesis on GHG emissions: analyses for transportation industry of South Africa. Discov. Sustain. 5 (1), 302. doi:10.1007/s43621-024-00518-6
Olivo, J., Cucuzza, R., Bertagnoli, G., and Domaneschi, M. (2024). Optimal design of steel exoskeleton for the retrofitting of RC buildings via genetic algorithm. Comput. & Struct. 299, 107396. doi:10.1016/j.compstruc.2024.107396
Page, M. J., McKenzie, J. E., Bossuyt, P. M., Boutron, I., Hoffmann, T. C., Mulrow, C. D., et al. (2021). The PRISMA 2020 statement: an updated guideline for reporting systematic reviews. bmj 372, n71. doi:10.1136/bmj.n71
Pal, A. K., Mohanty, A. K., and Misra, M. (2021). Additive manufacturing technology of polymeric materials for customized products: recent developments and future prospective. RSC Adv. 11 (58), 36398–36438. doi:10.1039/D1RA04060J
Pan, Y., and Zhang, L. (2023). Integrating BIM and AI for smart construction management: current status and future directions. Archives Comput. Methods Eng. 30 (2), 1081–1110. doi:10.1007/s11831-022-09830-8
Pantano, M., Regulin, D., Lutz, B., and Lee, D. (2020). A human-cyber-physical system approach to lean automation using an industrie 4.0 reference architecture. Procedia Manuf. 51, 1082–1090. doi:10.1016/j.promfg.2020.10.152
Paolini, A., Kollmannsberger, S., and Rank, E. (2019). Additive manufacturing in construction: a review on processes, applications, and digital planning methods. Addit. Manuf. 30, 100894. doi:10.1016/j.addma.2019.100894
Paritala, S., Singaram, K. K., Bathina, I., Khan, M. A., and Jyosyula, S. K. R. (2023). Rheology and pumpability of mix suitable for extrusion-based concrete 3D printing–A review. Constr. Build. Mater. 402, 132962. doi:10.1016/j.conbuildmat.2023.132962
Patel, K. S., Shah, D. B., Joshi, S. J., and Patel, K. M. (2023). Developments in 3D printing of carbon fiber reinforced polymer containing recycled plastic waste: a review. Clean. Mater. 9, 100207. doi:10.1016/j.clema.2023.100207
Pazhamannil, R. V., and Govindan, P. (2021). Current state and future scope of additive manufacturing technologies via vat photopolymerization. Mater. Today Proc. 43, 130–136. doi:10.1016/j.matpr.2020.11.225
Peruzzini, M., Grandi, F., and Pellicciari, M. (2020). Exploring the potential of Operator 4.0 interface and monitoring. Comput. & Industrial Eng. 139, 105600. doi:10.1016/j.cie.2018.12.047
Pervez, H., Ali, Y., and Petrillo, A. (2021). A quantitative assessment of greenhouse gas (GHG) emissions from conventional and modular construction: a case of developing country. J. Clean. Prod. 294, 126210. doi:10.1016/j.jclepro.2021.126210
Pessoa, S., Guimarães, A. S., Lucas, S. S., and Simões, N. (2021). 3D printing in the construction industry-A systematic review of the thermal performance in buildings. Renew. Sustain. Energy Rev. 141, 110794. doi:10.1016/j.rser.2021.110794
Piedra-Cascón, W., Krishnamurthy, V. R., Att, W., and Revilla-León, M. (2021). 3D printing parameters, supporting structures, slicing, and post-processing procedures of vat-polymerization additive manufacturing technologies: a narrative review. J. Dent. 109, 103630. doi:10.1016/j.jdent.2021.103630
Prabhakar, M. M., Saravanan, A., Lenin, A. H., Mayandi, K., Ramalingam, P. S., and Sethu Ramalingam, P. (2021). A short review on 3D printing methods, process parameters and materials. Mater. Today Proc. 45, 6108–6114. doi:10.1016/j.matpr.2020.10.225
Pragana, J., Sampaio, R. F., Bragança, I., Silva, C., and Martins, P. (2021). Hybrid metal additive manufacturing: a state–of–the-art review. Adv. Industrial Manuf. Eng. 2, 100032. doi:10.1016/j.aime.2021.100032
Prakasan, S., Palaniappan, S., and Gettu, R. (2020). Study of energy use and CO2 emissions in the manufacturing of clinker and cement. J. Institution Eng. India Ser. A 101, 221–232. doi:10.1007/s40030-019-00409-4
Praveena, B., Lokesh, N., Buradi, A., Santhosh, N., Praveena, B., and Vignesh, R. (2022). A comprehensive review of emerging additive manufacturing (3D printing technology): methods, materials, applications, challenges, trends and future potential. Mater. Today Proc. 52, 1309–1313. doi:10.1016/j.matpr.2021.11.059
Qaidi, S., Yahia, A., Tayeh, B. A., Unis, H., Faraj, R., and Mohammed, A. (2022). 3D printed geopolymer composites: a review. Mater. Today Sustain. 20, 100240. doi:10.1016/j.mtsust.2022.100240
Qiang, G., Tang, S., Hao, J., Di Sarno, L., Wu, G., and Ren, S. (2023). Building automation systems for energy and comfort management in green buildings: a critical review and future directions. Renew. Sustain. Energy Rev. 179, 113301. doi:10.1016/j.rser.2023.113301
Rehman, A. U., and Kim, J.-H. (2021). 3D concrete printing: a systematic review of rheology, mix designs, mechanical, microstructural, and durability characteristics. Materials 14 (14), 3800. doi:10.3390/ma14143800
Rivera, M. L., Bae, S. S., and Hudson, S. E. (2023). “Designing a sustainable material for 3D printing with spent coffee grounds,” in Proceedings of the 2023 ACM designing interactive systems conference, 294–311. doi:10.1145/3563657.359598
Röck, M., Saade, M. R. M., Balouktsi, M., Rasmussen, F. N., Birgisdottir, H., Frischknecht, R., et al. (2020). Embodied GHG emissions of buildings–The hidden challenge for effective climate change mitigation. Appl. Energy 258, 114107. doi:10.1016/j.apenergy.2019.114107
Rojek, I., Mikołajewski, D., Macko, M., Szczepański, Z., and Dostatni, E. (2021). Optimization of extrusion-based 3D printing process using neural networks for sustainable development. Materials 14 (11), 2737. doi:10.3390/ma14112737
Rosso, M. M., Cucuzza, R., Marano, G. C., Aloisio, A., and Cirrincione, G. (2022). “Review on deep learning in structural health monitoring,” in Bridge safety, maintenance, management, life-cycle, Resilience and sustainability (CRC Press), 309–315.
Sales, E., Kwok, T. H., and Chen, Y. (2021). Function-aware slicing using principal stress line for toolpath planning in additive manufacturing. J. Manuf. Process. 64, 1420–1433. doi:10.1016/j.jmapro.2021.02.050
Salmi, M. (2021). Additive manufacturing processes in medical applications. Materials 14 (1), 191. doi:10.3390/ma14010191
Sanicola, H. W., Stewart, C. E., Mueller, M., Ahmadi, F., Wang, D., Powell, S. K., et al. (2020). Guidelines for establishing a 3-D printing biofabrication laboratory. Biotechnol. Adv. 45, 107652. doi:10.1016/j.biotechadv.2020.107652
Sathish, K., Kumar, S. S., Magal, R. T., Selvaraj, V., Narasimharaj, V., Karthikeyan, R., et al. (2022). A comparative study on subtractive manufacturing and additive manufacturing. Adv. Mater. Sci. Eng. 2022, 1–8. doi:10.1155/2022/6892641
Sawhney, A., Riley, M., Irizarry, J., and Riley, M. (2020). in Construction 4.0. Editors A. Sawhney, M. Riley, and J. Irizarry.
Sepasgozar, S. M., Shi, A., Yang, L., Shirowzhan, S., and Edwards, D. J. (2020). Additive manufacturing applications for industry 4.0: a systematic critical review. Buildings 10 (12), 231. doi:10.3390/buildings10120231
Shahrubudin, N., Lee, T. C., and Ramlan, R. (2019). An overview on 3D printing technology: technological, materials, and applications. Procedia Manuf. 35, 1286–1296. doi:10.1016/j.promfg.2019.06.089
Shakor, P., Chu, S., Puzatova, A., and Dini, E. (2022). Review of binder jetting 3D printing in the construction industry. Prog. Addit. Manuf. 7 (4), 643–669. doi:10.1007/s40964-021-00252-9
Shehata, N., Mohamed, O., Sayed, E. T., Abdelkareem, M. A., and Olabi, A. (2022a). Geopolymer concrete as green building materials: recent applications, sustainable development and circular economy potentials. Sci. Total Environ. 836, 155577. doi:10.1016/j.scitotenv.2022.155577
Shehata, N., Mohamed, O., Sayed, E. T., Abdelkareem, M. A., and Olabi, A. (2022b). Geopolymer concrete as green building materials: recent applications, sustainable development and circular economy potentials. Sci. Total Environ. 836, 155577. doi:10.1016/j.scitotenv.2022.155577
Shim, J. S., Kim, J.-E., Jeong, S. H., Choi, Y. J., and Ryu, J. J. (2020). Printing accuracy, mechanical properties, surface characteristics, and microbial adhesion of 3D-printed resins with various printing orientations. J. Prosthet. Dent. 124 (4), 468–475. doi:10.1016/j.prosdent.2019.05.034
Shobeiri, V., Bennett, B., Xie, T., and Visintin, P. (2021). A comprehensive assessment of the global warming potential of geopolymer concrete. J. Clean. Prod. 297, 126669. doi:10.1016/j.jclepro.2021.126669
Shuaib, M., Haleem, A., Kumar, S., and Javaid, M. (2021). Impact of 3D Printing on the environment: a literature-based study. Sustain. Operations Comput. 2, 57–63. doi:10.1016/j.susoc.2021.04.001
Singh, N. B., and Middendorf, B. (2020). Geopolymers as an alternative to Portland cement: an overview. Constr. Build. Mater. 237, 117455. doi:10.1016/j.conbuildmat.2019.117455
Singh, R., Gehlot, A., Akram, S. V., Gupta, L. R., Jena, M. K., Prakash, C., et al. (2021). Cloud manufacturing, internet of things-assisted manufacturing and 3D printing technology: reliable tools for sustainable construction. Sustainability 13 (13), 7327. doi:10.3390/su13137327
Skibicki, S., Pułtorak, M., Kaszyńska, M., Hoffmann, M., Ekiert, E., and Sibera, D. (2022). The effect of using recycled PET aggregates on mechanical and durability properties of 3D printed mortar. Constr. Build. Mater. 335, 127443. doi:10.1016/j.conbuildmat.2022.127443
Sousa, V., and Bogas, J. A. J. A. (2021). Comparison of energy consumption and carbon emissions from clinker and recycled cement production. J. Clean. Prod. 306, 127277. doi:10.1016/j.jclepro.2021.127277
Spring, C. R., and Cirella, G. T. (2022). Fostering sustainable development: green energy policy in the European Union and the United States, Human settlements: Urbanization, smart sector development, and future outlook, 101–137.
Srivastava, M., Rathee, S., Patel, V., Kumar, A., and Koppad, P. G. (2022). A review of various materials for additive manufacturing: recent trends and processing issues. J. Mater. Res. Technol. 21, 2612–2641. doi:10.1016/j.jmrt.2022.10.015
Suhaily, S. S., Khalil, H. A., Nadirah, W. W., and Jawaid, M. (2013). “Bamboo based biocomposites material, design and applications,” in Materials science-advanced topics (IntechOpen). doi:10.5772/56057
Sun, C., Wang, Y., McMurtrey, M. D., Jerred, N. D., Liou, F., and Li, J. (2021). Additive manufacturing for energy: a review. Appl. Energy 282, 116041. doi:10.1016/j.apenergy.2020.116041
Sun, S., Zheng, X., Gong, B., Garcia Paredes, J., and Ordieres-Meré, J. (2020). Healthy operator 4.0: a human cyber–physical system architecture for smart workplaces. Sensors 20 (7), 2011. doi:10.3390/s20072011
Tabassum, N., Duarte, J., and Nazarian, S. (2023). Advancing 3D concrete printing for affordable housing: a shape grammar-based approach to print spanning roof structures.
Tarhan, Y., and Şahin, R. (2019). “Developments of 3D concrete printing process,” in International Civil engineering and architecture conference. Trabzon/Turkey.
Tay, Y. W. D., Panda, B., Paul, S. C., Noor Mohamed, N. A., Tan, M. J., and Leong, K. F. (2017). 3D printing trends in building and construction industry: a review. Virtual Phys. Prototyp. 12 (3), 261–276. doi:10.1080/17452759.2017.1326724
Tay, Y. W. D., Ting, G. H. A., Panda, B., Wong, T. N., and Tan, M. J. (2022). Towards net zero in 3DP for building & construction. Mater. Today Proc. 70, 599–602. doi:10.1016/j.matpr.2022.09.610
Teixeira, J., Schaefer, C. O., Rangel, B., Maia, L., and Alves, J. L. (2023). A road map to find in 3D printing a new design plasticity for construction–The state of art. Front. Archit. Res. 12 (2), 337–360. doi:10.1016/j.foar.2022.10.001
Teweldebrhan, B. T., Maghelal, P., and Galadari, A. (2022). Impact of additive manufacturing on maritime transportation: a review. J. Int. Logist. Trade 20, 190–209. ahead-of-print. doi:10.1108/JILT-06-2022-0017
Thomas, J., Brunton, J., and Graziosi, S. (2010). EPPI-Reviewer 4.0: software for research synthesis. EPPI-Centre Software. London: Social Science Research Unit, Institute of Education.
Thompson, M. K., Moroni, G., Vaneker, T., Fadel, G., Campbell, R. I., Gibson, I., et al. (2016). Design for additive manufacturing: trends, opportunities, considerations, and constraints. CIRP Ann. 65 (2), 737–760. doi:10.1016/j.cirp.2016.05.004
Vafadar, A., Guzzomi, F., Rassau, A., and Hayward, K. (2021). Advances in metal additive manufacturing: a review of common processes, industrial applications, and current challenges. Appl. Sci. 11 (3), 1213. doi:10.3390/app11031213
Vaneker, T., Bernard, A., Moroni, G., Gibson, I., and Zhang, Y. (2020). Design for additive manufacturing: framework and methodology. CIRP Ann. 69 (2), 578–599. doi:10.1016/j.cirp.2020.05.006
Vasco, J. C. (2021). “Additive manufacturing for the automotive industry,” in Additive manufacturing (Elsevier), 505–530. doi:10.1016/B978-0-12-818411-0.00010-0
Vora, H. D., and Sanyal, S. (2020). A comprehensive review: metrology in additive manufacturing and 3D printing technology. Prog. Addit. Manuf. 5 (4), 319–353. doi:10.1007/s40964-020-00142-6
Vyavahare, S., Teraiya, S., Panghal, D., and Kumar, S. (2020). Fused deposition modelling: a review. Rapid Prototyp. J. 26 (1), 176–201. doi:10.1108/RPJ-04-2019-0106
Wang, B., Zheng, P., Yin, Y., Shih, A., and Wang, L. (2022c). Toward human-centric smart manufacturing: a human-cyber-physical systems (HCPS) perspective. J. Manuf. Syst. 63, 471–490. doi:10.1016/j.jmsy.2022.05.005
Wang, D., Zhang, T., Guo, X., Ling, D., Hu, L., and Jiang, G. (2022a). The potential of 3D printing in facilitating carbon neutrality. J. Environ. Sci. 130, 85–91. doi:10.1016/j.jes.2022.10.024
Wang, J., Zhang, Y., Aghda, N. H., Pillai, A. R., Thakkar, R., Nokhodchi, A., et al. (2021b). Emerging 3D printing technologies for drug delivery devices: current status and future perspective. Adv. drug Deliv. Rev. 174, 294–316. doi:10.1016/j.addr.2021.04.019
Wang, M., Wang, C. C., Sepasgozar, S., and Zlatanova, S. (2020). A systematic review of digital technology adoption in off-site construction: current status and future direction towards industry 4.0. Buildings 10 (11), 204. doi:10.3390/buildings10110204
Wang, W., Guo, H., Li, X., Tang, S., Li, Y., Xie, L., et al. (2022b). BIM information integration based VR modeling in digital twins in industry 5.0. J. Industrial Inf. Integration 28, 100351. doi:10.1016/j.jii.2022.100351
Wang, Y., Ahmed, A., Azam, A., Bing, D., Shan, Z., Zhang, Z., et al. (2021a). Applications of additive manufacturing (AM) in sustainable energy generation and battle against COVID-19 pandemic: the knowledge evolution of 3D printing. J. Manuf. Syst. 60, 709–733. doi:10.1016/j.jmsy.2021.07.023
Waqar, A., Othman, I., and Pomares, J. C. (2023a). Impact of 3D printing on the overall project success of residential construction projects using structural equation modelling. Int. J. Environ. Res. Public Health 20 (5), 3800. doi:10.3390/ijerph20053800
Waqar, A., Othman, I., and Pomares, J. C. (2023b). Impact of 3D printing on the overall project success of residential construction projects using structural equation modelling. Int. J. Environ. Res. Public Health 20 (5), 3800. doi:10.3390/ijerph20053800
Weng, Y., Li, M., Ruan, S., Wong, T. N., Tan, M. J., Ow Yeong, K. L., et al. (2020). Comparative economic, environmental and productivity assessment of a concrete bathroom unit fabricated through 3D printing and a precast approach. J. Clean. Prod. 261, 121245. doi:10.1016/j.jclepro.2020.121245
Westphal, E., and Seitz, H. (2022). Machine learning for the intelligent analysis of 3D printing conditions using environmental sensor data to support quality assurance. Addit. Manuf. 50, 102535. doi:10.1016/j.addma.2021.102535
Wong, K. V., and Hernandez, A. (2012). A review of additive manufacturing. Int. Sch. Res. notices 2012, 1–10. doi:10.5402/2012/208760
Xiao, J., Ji, G., Zhang, Y., Ma, G., Mechtcherine, V., Pan, J., et al. (2021b). Large-scale 3D printing concrete technology: current status and future opportunities. Cem. Concr. Compos. 122, 104115. doi:10.1016/j.cemconcomp.2021.104115
Xiao, J., Ji, G., Zhang, Y., Ma, G., Mechtcherine, V., Pan, J., et al. (2021c). Large-scale 3D printing concrete technology: current status and future opportunities. Cem. Concr. Compos. 122, 104115. doi:10.1016/j.cemconcomp.2021.104115
Xiao, J., Zou, S., Ding, T., Duan, Z., and Liu, Q. (2021a). Fiber-reinforced mortar with 100% recycled fine aggregates: a cleaner perspective on 3D printing. J. Clean. Prod. 319, 128720. doi:10.1016/j.jclepro.2021.128720
Xiao, W., Zheng, L., Huan, J., and Lei, P. (2015). A complete CAD/CAM/CNC solution for STEP-compliant manufacturing. Robotics Computer-Integrated Manuf. 31, 1–10. doi:10.1016/j.rcim.2014.06.003
Xiao, Y., Shan, B., and Li, Z. (2019). “Recent progress in engineered bamboo development,” in Modern engineered bamboo structures, 3–22. doi:10.1201/9780429434990
Xu, J., Wang, K., Sheng, H., Gao, M., Zhang, S., and Tan, J. (2020). Energy efficiency optimization for ecological 3D printing based on adaptive multi-layer customization. J. Clean. Prod. 245, 118826. doi:10.1016/j.jclepro.2019.118826
Yang, H., Rao, P., Simpson, T., Lu, Y., Witherell, P., Nassar, A. R., et al. (2020). Six-sigma quality management of additive manufacturing. Proc. IEEE 109 (4), 347–376. doi:10.1109/JPROC.2020.3034519
Yao, Y., Hu, M., Di Maio, F., and Cucurachi, S. (2020). Life cycle assessment of 3D printing geo-polymer concrete: an ex-ante study. J. Industrial Ecol. 24 (1), 116–127. doi:10.1111/jiec.12930
Ye, X., Dong, Z., Lu, J., and Li, C. (2021). Thermoeconomic evaluation of double-reheat coal-fired power units with carbon capture and storage and waste heat recovery using organic Rankine cycle. Int. J. Greenh. Gas Control 105, 103247. doi:10.1016/j.ijggc.2020.103247
Yu, M., Robati, M., Oldfield, P., Wiedmann, T., Crawford, R., Nezhad, A. A., et al. (2020). The impact of value engineering on embodied greenhouse gas emissions in the built environment: a hybrid life cycle assessment. Build. Environ. 168, 106452. doi:10.1016/j.buildenv.2019.106452
Zhang, H., Hui, J., Lv, J., Lee, C. H., Yan, Z., Wang, J. j., et al. (2023b). A novel method to combine fused deposition modelling and inkjet printing in manufacturing multifunctional parts for aerospace application. J. Mater. Res. Technol. 24, 4405–4426. doi:10.1016/j.jmrt.2023.04.059
Zhang, J., Wang, J., Dong, S., Yu, X., and Han, B. (2019). A review of the current progress and application of 3D printed concrete. Compos. Part A Appl. Sci. Manuf. 125, 105533. doi:10.1016/j.compositesa.2019.105533
Zhang, L., Ling, J., and Lin, M. (2023a). Carbon neutrality: a comprehensive bibliometric analysis. Environ. Sci. Pollut. Res. 30 (16), 45498–45514. doi:10.1007/s11356-023-25797-w
Zhang, X., and Liou, F. (2021). “Introduction to additive manufacturing,” in Additive manufacturing (Elsevier), 1–31. doi:10.1016/B978-0-12-818411-0.00009-4
Ziaee, M., and Crane, N. B. (2019). Binder jetting: a review of process, materials, and methods. Addit. Manuf. 28, 781–801. doi:10.1016/j.addma.2019.05.031
AM Additive Manufacturing
3DP 3D Printing
ASTM American Society for Testing and Materials
BJ Binder Jetting
DMLS Direct Metal Laser Sintering
DFM Design for Manufacturability
EBM Electron Beam Melting
FDM Fused Deposition Modeling
LENS Laser Engineered Net Shaping
SLA Stereolithography
SLM Selective Laser Melting
SLS Selective Laser Sintering
MM Multi-Material
DP Design for Printability
EAM Energy-Aware Manufacturing
PUE Power Utilization Efficiency
REEM Renewable Energy in Manufacturing
MRS Material Reuse Score
MF Material Footprint
TRL Technology Readiness Level
AIAM Artificial Intelligence for Additive Manufacturing
BioAM Biodegradable Additive Manufacturing
ISO International Organization for Standardization
RoHS Restriction of Hazardous Substances
AMPC Additive Manufacturing Polymer Composites
CMC Ceramic Matrix Composites
PLA Polylactic Acid (biodegradable polymer)
PEEK Polyetheretherketone
HDPE High-Density Polyethylene
BMM Bio-Based Manufacturing Materials
BF Bio-Fillers (Cellulose, Lignin, e.tc.)
PBS Polybutylene Succinate
PGA Polyglycolic Acid
CNT Carbon Nanotubes
AMCC Additive Manufacturing Ceramic Composites
TiN Titanium Nitride Coatings
4DAM 4D Additive Manufacturing
PCMs Phase Change Materials
BIM Building Information Modeling
EPM Electrically Conductive Polymers
HTM High-Temperature Materials
LLM Low-Loss Materials (in electronics)
3DCP 3D Concrete Printing
RPC Reactive Powder Concrete
GGBFS Ground Granulated Blast Furnace Slag
LCC Low-Clinker Concrete
LCA Life Cycle Assessment
CF Carbon Footprint
CE Circular Economy
CC Contour Crafting
EE Energy Efficiency
ESG Environmental, Social, and Governance
GHG Greenhouse Gases
GWP Global Warming Potential
RE Renewable Energy
SDG Sustainable Development Goals
WTE Waste-to-Energy
DfS Design for Sustainability
RRM Renewable Raw Material
RCM Recycled Content Material
PCR Post-Consumer Recycled
EOL End of Life
NREE Non-Renewable Energy Efficiency
EF Environmental Footprint
RSE Resource Savings Efficiency
MLAM Machine Learning in Additive Manufacturing
AMaaS Additive Manufacturing as a Service
SUSAM Sustainable Additive Manufacturing
EHS Environmental, Health, and Safety
AMM Advanced Manufacturing Materials
MMC Metal Matrix Composites
PMMA Polymethyl Mathacrylate
ABS Acrylonitrile Butadiene Styrene
PETG Polyethylene Terephthalate Glycol
BPC Biodegradable Polymer Composites
RCP Recycled Polymer Composites
NFP Natural Fiber Polymers
PHAs Polyhydroxyalkanoates
GRM Graphene-Based Materials
HSS High-Strength Steel
SMA Shape Memory Alloys
SMP Shape Memory Polymers
SAMC Smart Additive Manufacturing Composites
EAP Electroactive Polymers
BCM Biopolymer Ceramic Matrix
ULMs Ultra-lightweight Materials
CAM Concrete Additive Manufacturing
HPC High Performance Concrete
ECC Engineered Cementitious Composites
WBA Wood Based Ashes
SF Silica Fume
Keywords: innovative manufacturing solutions, sustainable additive manufacturing, optimize material utilization, GHG/CO2 emissions mitigation, traditional (subtractive) manufacturing, building information modeling, built environment, sustainability with industry “X.0”
Citation: Oladunni OJ, Lee CKM, Ibrahim ID and Olanrewaju OA (2025) Advances in sustainable additive manufacturing: a systematic review for construction industry to mitigate greenhouse gas emissions. Front. Built Environ. 11:1535626. doi: 10.3389/fbuil.2025.1535626
Received: 27 November 2024; Accepted: 31 January 2025;
Published: 31 March 2025.
Edited by:
Ernest Kissi, Kwame Nkrumah University of Science and Technology, GhanaReviewed by:
Carolina Piña Ramírez, Polytechnic University of Madrid, SpainCopyright © 2025 Oladunni, Lee, Ibrahim and Olanrewaju. This is an open-access article distributed under the terms of the Creative Commons Attribution License (CC BY). The use, distribution or reproduction in other forums is permitted, provided the original author(s) and the copyright owner(s) are credited and that the original publication in this journal is cited, in accordance with accepted academic practice. No use, distribution or reproduction is permitted which does not comply with these terms.
*Correspondence: Oluwole Joseph Oladunni, b2x1am9zZXBoa0BnbWFpbC5jb20=, MjIyOTA2NjVAZHV0NGxpZmUuYWMuemE=
†ORCID: Oluwole Joseph Oladunni, orcid.org/0000-0002-2718-7974
Disclaimer: All claims expressed in this article are solely those of the authors and do not necessarily represent those of their affiliated organizations, or those of the publisher, the editors and the reviewers. Any product that may be evaluated in this article or claim that may be made by its manufacturer is not guaranteed or endorsed by the publisher.
Research integrity at Frontiers
Learn more about the work of our research integrity team to safeguard the quality of each article we publish.