- 1Department of Mechanical Engineering, University of Engineering and Technology Lahore, Lahore, Pakistan
- 2Department of Mechanical Engineering, College of Engineering, Prince Mohammad Bin Fahd University, Al-Khobar, Saudi Arabia
- 3Department of Transportation Engineering and Management, University of Engineering and Technology, Lahore, Pakistan
- 4Department of Mechanical Engineering and Technology, GCU Faisalabad, Faisalabad, Pakistan
- 5Department of Mechanical Engineering, Abu Dhabi University, Abu Dhabi, United Arab Emirates
The U.S. Occupational Safety and Health Administration’s (OSHA) most recent estimates show that between 35,000 and 62,000 injuries occur every year due to forklift-related accidents. According to the National Safety Council (NSC) data, approximately 78 fatalities are reported every year. Moreover, manual loading and unloading of heavy items is time-consuming and poses significant risks to workers in small and crowded warehouses. To address these safety and efficiency concerns cost-effectively, an automated robotic forklift prototype was developed. The key features of this industrial robot include full rotational mobility with a zero-degree turning radius, which reduces the time and space required to turn around corners. It can be operated remotely via a mobile phone using Bluetooth or wi-fi. The motion control system, based on the ESP-32 microcontroller, significantly enhances its operational efficiency compared to manual operation. This study evaluates the performance of the robotic forklift prototype, cost-effectiveness, with loading and unloading capabilities as effective solutions to the challenges faced by workers. Additionally, structural analysis using Ansys confirmed that the design can safely withstand forces 60% greater than the intended design load of 50 N. Furthermore, the maximum stress experienced by the fork is 67% below the material yield strength, further demonstrating robustness and reliability. The integration of advanced technology and Eco-friendly design positions this forklift as a viable and sustainable option for improving material handling in various industrial sectors.
1 Introduction
The U.S. Occupational Safety and Health Administration (OSHA) indicates that from 2022 to 23, 205 accidents involving forklifts were recorded, with 128 resulting in fatalities. The National Safety Council (NSC) suggests that approximately 11% of forklifts are involved in some kind of accident each year. The manufacturing industry accounts for the highest percentage of forklift-related fatalities, with a ratio of 42.50%, followed by the construction industry at 23.08% (WarehouseWiz Inc., 2024). Around 75–100 workers lose their lives each year in such accidents, with 36% of these fatalities involving pedestrians (Forklift accident statistics, 2024). Similarly, according to statistical data from the National Labor Inspectorate (NLI) of Poland, on average 90 accidents involving forklift trucks happen annually, resulting in nearly 100 injuries, with 10–15 turning into fatalities (Milanowicz et al., 2018). Similarly, an analysis of forklift-related accidents, injuries, and fatalities in Victoria, Australia from 2000 to 2012 revealed that 50% of incidents were due to collision (Saric et al., 2013). Incidents of forklift accidents resulting in head injury and globe rupture are documented in (Zack et al., 2018; Ono et al., 2024). These statistics highlight the need for enhanced safety measures to reduce the risks involved with forklift operations.
For every production facility, loading, unloading, and transportation of logistics are the main concerns, which also control a significant portion of the accompanying cost (Department of Industrial Engineering et al., 2019). Therefore, proper selection of transportation saves time, and the cost needed (Department of Industrial Engineering et al., 2019; Burinskiene, 2011). Forklifts are one of the most commonly used material handling equipment across various industries due to their efficiency in moving materials and goods (Vivaldini et al., 2010; Sarker et al., 2017). Forklifts also serve as sustainable solutions for indoor material handling in industries (Ferraro et al., 2024). Selection of the most appropriate forklift among many available types depends upon various factors, which include the working environment, type of loading, nature of goods to be transported, and finally the operator’s skills needed (Zajac and Rozic, 2022; Potdukhe, 2019).
The working of a forklift primarily depends on hydraulic systems and internal combustion engines. Hydraulic systems can harm the environment due to potential leaks of oil, causing major complications during transportation. Additionally, they can cause overheating issues and correspondingly wastage of energy, during forklift processes like acceleration and braking (Wang et al., 2017). Conversely, internal combustion engines, as their work is based on fossil fuels, emit an enormous amount of carbon dioxide, contributing to the earth’s temperature rise, global warming, and its associated effects (Raut Shubham et al., 2020; Facchini et al., 2016).
In recent times, due to improved environmental awareness and the Sustainable Development Goals (SDGs) set by the United Nations, electric forklifts are being widely used in the industry and warehouses for logistics handling, instead of traditional ones (Yao et al., 2022). Additionally, the use of an electric forklift also improves its transmission efficiency (Wang et al., 2017). Many researchers have designed and fabricated electric forklifts to meet the industry’s needs (Sequeira et al., 2019; Yadav et al., 2022). Panara et al. (2024) constructed a battery-operated forklift for material handling in the mechanical industry that can be controlled through wired communication.
Conventional forklifts, which depend on manual operations, often lead to operator fatigue and decreased situational awareness, increasing the risk of accidents, especially in crowded and small warehouses (Milanowicz et al., 2018; Choi et al., 2020). As per the statistical data of France, on average 10 workers are killed each year due to accidents involving forklift trucks (Rebelle et al., 2009). To effectively address these issues, automated forklifts have been recommended by researchers as a safer and more efficient alternative (Iinuma et al., 2020; Tamba et al., 2009). This research proposes an algorithm to produce automatic routing for forklift robots (Vivaldini et al., 2009). Abdellatif et al. designed an autonomous forklift using Microsoft Kinect (Abdellatif et al., 2018), capable of lifting materials from sources to target locations while safely avoiding obstacles. Similarly, Bhat et al. developed an advanced autonomous forklift for warehouse use based on a network control system (Bhat et al., 2023). In addition, a small-scale, cost-effective, autonomous forklift was developed for industrial use, capable of carrying loads up to 300 kg (Amio et al., 2024). Auto-guided forklift prototype capable of autonomous navigation, obstacle recognition, and adaptive decision-making was developed in (Thiruchelvam and Pathirana, 2024) and prototypes of automatic material-based vehicles for warehouses, were created and studied to design a system of automated material conveying in Wisedsin (2022).
Although Autonomous forklifts are more efficient, can navigate and handle pallets without operator intervention, and enhance safety in hazardous environments, their high installation and maintenance costs are burdensome for developing countries. To mitigate this issue, semi-automatic forklifts with remote control capabilities have been introduced, reducing the need for highly trained operators and improving the visibility of drivers (Design, 2014; Najmuzzama et al., 2022). Researchers have developed advanced electric forklifts that can be controlled via Wi-fi, radio frequency, or Bluetooth, with remote-controlled options like smartphones being preferred for small warehouses due to their lower cost (Hema Latha et al., 2021; Jagtap et al., 2024). Likewise, Abuzied et al. (2024) designed and simulated a smartphone control and an eco-friendly forklift, that can lift a maximum load of 200 N using a ball screw feed mechanism.
Many improvements are being made in the design of vehicles on which forklifts are mounted to make them more adaptable to the issues of tight spaces, U-turns, parking, and sharp corners (Ali, 2019; Singh et al., 2024). For this purpose, 360-degree rotating vehicles are being designed, which require no extra space for sharp turns or around corners and can operate in narrow paths (Moudgil et al., 2015; Dinesh et al., 2021). By designing these vehicles, we can reduce the problems that occur while handling logistics in small warehouses (Kumar et al., 2020). Similarly, Kasali et al. designed and developed a 360-degree rotating vehicle that can be controlled via mobile phone using Bluetooth having a range of 100 m. This study showed that the vehicle could perform well in tight spaces and easily maneuver around obstacles but there are safety concerns in scenarios of high speed, that need to be addressed for better results (Adedeji et al., 2023). A zero-turning vehicle is developed which takes less time and space as compared to conventional steering mechanisms (Bhui et al., 2024; Soni et al., 2018).
Detailed comparisons among different types of forklifts being operated on batteries, fossil fuel, and fuel cells, have been made by various researchers to check the feasibility of electric and fuel cell-based forklifts over forklifts powered by fossil fuel (Gaines et al., 2008; Elgowainy et al., 2009). The environmental impact of battery-operated and fuel cell-based forklifts is generally lower than that of forklifts powered by internal combustion engines, with the potential for further reduction with some technical improvements (Metzger and Li, 2022; Hosseinzadeh et al., 2013). Hybrid and Hydrogen-powered fuel cell forklifts have been extensively analyzed and tested by several researchers, demonstrating suitability for a wider range of applications (Hsieh et al., 2021; Al-Douri et al., 2023). A similar economic comparison between fuel cell-powered and battery-powered forklifts in Renquist et al. (2012) demonstrates that battery-powered forklifts are less expensive to purchase and simultaneously easy to operate compared to fuel cell-powered forklifts for the facilities considered in the research.
The main purpose of this research is to develop a low-cost, and environmentally friendly forklift that incorporates advanced features to improve operational efficiency and safety for logistics transportation, to reduce the accidents linked with forklift trucks. The operation of this project forklift is based on a rechargeable battery employing a lead screw mechanism and can be controlled remotely via a smartphone using Bluetooth or wi-fi. Other features include a 360-degree rotational capability allowing it to navigate tight spaces and corners with ease. The forklift is equipped with DC motors that drive the wheels and the conveyor belt system on the forks, facilitating the smooth lifting and transfer of goods. Moreover, a cost comparison has been made between electric and diesel-powered forklift prototypes having similar lifting capacities. The primary novelty of this project includes its low cost, smartphone-based remote control to reduce accident risk, 360-degree rotational capability for enhanced cornering, and zero-emission operation for improved environmental sustainability.
2 Materials and methods
Cast iron is being widely used in the industry due to its strength, durability, cost-effectiveness, and easy availability. Therefore, the material selected for the development of this project forklift is cast Iron. The project methodology involves a systematic approach to calculation, selection of components, SolidWorks-based CAD modeling, static structural analysis using Ansys, and fabrication, including cutting, shaping, welding, and ultimately the final assembly. This forklift prototype is designed to handle a total load of 5 kg during operation, demonstrating its practical application in lifting and moving logistics in warehouses.
2.1 Design methodology
To select the appropriate number of components to use for the development of a battery-operated forklift to carry 5 kg of weight, the required amount of torque is calculated for the forward and reverse motion of the vehicle, which comes out to be 0.809 N·m and for 360-degree rotation of the vehicle, the torque required is 1.121 N.m. Similarly, the required torque for the conveyor motion is 0.08829 N.m. Based upon these calculations, Table 1 outlines the specifications of the main components, and the quantity used in the project.
2.2 Hardware description
To ensure the prototype is accessible and easy to operate, an optimally sized supporting frame was designed as shown in Figure 1A. The frame measures 24 inches by 15 inches. A rechargeable battery having 12 V and 7 Ah power, and gear motors with an input torque of 0.01 N·m are used as depicted in Figure 1B. For 360-degree rotation of the wheel, the four geared motors are used that are controlled and regulated by a motor driver. Additionally, it directs the left and right turns of the wheels. The L298N Motor Driver is used in the model as shown in Figure 1C.

Figure 1. Hardware components used in the project: (A) Supporting frame, (B) DC gear motor, (C) Motor Driver L298N, (D) Tire.
The other components used in the project include plastic tires, which are used for 360-degree rotation of the vehicle, having a diameter of 9 inches to ensure proper clearance of the base from the ground and to match the dimensions of the frame structure. In a total of 4 tires used, a single tire is demonstrated in Figure 1D. An electric motor is used that powers the up-and-down movement of the forklift’s fork, delivering the required torque to lift loads to 5 kg. A critical relay switch controls the electrical circuit in the forklift, ensuring safe and efficient operation by regulating the flow of electricity. A Pulse Width Modulation (PWM) controller is used to optimize motor operation in the forklift by rapidly switching it on and off in a series of pulses. This method enables efficient and precise control of speed and torque to perform different operations of the forklift.
More technical details of the project are presented in Table 2. The load center of the project is located at 88.9 mm, with a load capacity of 5–8 kg. The overall length and width of the forklift are 609.6 mm and 381 mm respectively. The forward travel speed of the forklift is 0.5 m/s, and the lifting speed of the fork after carrying weight is 0.25 mm/s. The power rating of the drive motor and lift motor is 60 W.
Forklifts mounted on 360-degree rotating vehicles have gained popularity because they can maneuver in tight spaces and make sharp turns, thereby reducing parking and U-turn issues in small and crowded warehouses. To incorporate this feature in this project as well, a 360-degree rotating vehicle is designed in SolidWorks and then fabricated accordingly.
The Bluetooth module helps to control the vehicle remotely by facilitating communication with Bluetooth-enabled devices such as computers and smartphones. This module has low power consumption, secure, reliable connections, with a communication range of up to 100 m. Its incorporation into the vehicle increases operational flexibility and user convenience, allowing for seamless control and improved maneuverability in tight spaces and in taking turns around corners.
2.3 Forklift control system using ESP-32 microcontroller
The forklift control system is managed and controlled by an ESP-32 microcontroller board, which receives signals via wi-fi or Bluetooth from a smartphone to control the functions and the movement of the forklift. This development board is primarily used for cost-effective, power-efficient, and IoT-based applications.
Arduino code, which is developed using Arduino software, is utilized to establish a connection between the smartphone and the forklift to perform the specific functions as assigned, after receiving commands from a smartphone via Bluetooth (Desai and Vaidya, 2024; Roskam, 2018). Arduino software, which offers a user-friendly programming environment, allows developers to write and upload code to the microcontroller board. Using this software, the control logic, movement patterns, and other features of the forklift can be programmed and tailored to the specific needs (Sonker et al., 2021; Moe San et al., 2019).
In summary, the integration of the EPS-32 microcontroller board as shown in Figure 2, alongside Arduino programming empowers the forklift to be wirelessly controlled and operated via a mobile device. This feature enhances convenience and flexibility in the operation of the forklift.
In addition to the microcontroller board, the loading and unloading operations of this forklift prototype are controlled by a conveyor belt system. This system consisting of two rollers enables the movement of heavy goods between the front and rear positions. The motors responsible for driving the conveyors are powered by rechargeable batteries, ensuring efficient operation while performing different processes. This project prototype has another advantage in that it can be used for both loading and unloading operations with the help of this conveyor belt system.
2.4 CAD modeling and experimental setup
In this research work, SolidWorks is used for modeling the forklift prototype to accurately represent its shape and structure. This CAD model later is used for the detailed evaluation of the structural robustness of the forklift using Ansys. Figure 3 depicts the comprehensive 3D CAD model of the battery-operated forklift. After modeling individual key components of the project such as the robust cast iron frame to ensure sturdy support, 360-degree rotating wheels that facilitate smooth mobility across different surfaces, and efficient lifting mechanisms using a conveyor belt system to carry a load, the final assembly is also completed in SolidWorks. The prototype is powered by a customized electric motor; therefore, the lifting mechanism is capable of handling loads up to 8 kg, against the intended design load of 5 kg.
The final assembly of this project prototype included a rigorous process of integrating various components to ensure proper functionality and performance. This phase commenced with the precise cutting and welding of various structural components, subsequently the installation of the lead screw mechanism and DC motors. The assembly incorporated the ESP-32 microcontroller-based control system for Bluetooth connectivity via mobile phone and the belt conveyor system. Each component was thoroughly tested for alignment and operational accuracy, ensuring that the forklift met the design specifications. The final assembly is first evaluated through a mobile phone to confirm its capability to navigate in tight spaces and around corners which confirms its effectiveness in remote operations, and then finally against the applied load to reaffirm its loading and unloading capacity. This comprehensive testing process resulted in a cost-effective, and environmentally friendly forklift. The labeled final product of this project prototype is shown in Figure 4.
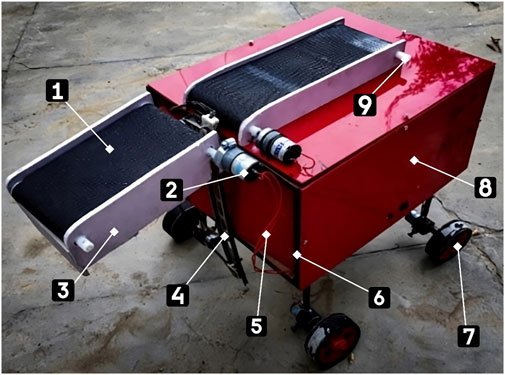
Figure 4. Forklift illustrative drawing of final assembly: 1 – Conveyor belt, 2 – Motor, 3 – Protective guards, 4 – Window motor, 5 – Electric wiring, 6 – Support structure, 7 – Tire, 8 – Chassis, 9 – Roller.
3 Results and discussion
This section presents the in-depth analysis and discussion of this project prototype, which includes simulation and material cost comparison. For a comprehensive understanding of mechanical component behavior under diverse loading conditions, static structural analysis using Ansys is performed and discussed in detail. Cost comparison includes the cost for each component and a cost comparison with diesel-powered forklifts of similar capacity. These results provide insights into the efficiency, cost-effectiveness, and structural integrity of the forklift prototype, contributing to advancements in material handling technology and sustainable industrial practices.
3.1 Structural load response analysis using ansys
To analyze the strength, stability, and safety of this project under different loading conditions, a widely employed static structural module of Ansys software is used Jie et al. (2019). This module works on a finite element analysis (FEA) tool in which precise material properties and boundary conditions are employed, depending on actual scenarios to consider (Hassan et al., 2024; Doçi and Imeri, 2013). This software can also be used to study the service conditions, structural integrity of forklifts, fracture, and failure analysis after many hours of operations (Massone and Boeri, 2010; Figueiredo et al., 2001). Here, the analysis evaluates the structural integrity under different loads ranging from 20 N to 80 N, ensuring compliance with a safe load limit of 50 N or 5 kg weight. Additionally, the forklift’s capacity to handle loads up to 80 N was also verified, demonstrating its capability to safely carry a weight of 8 kg.
3.2 Forklift finite element model and boundary conditions
After selecting and opening the static structural module in Ansys, gray cast Iron material was selected, and relevant properties were assigned to perform analysis as shown in Table 3. The Young’s modulus of the selected material is 1.1 × 1011 Pa, with tensile and compressive yield strengths of 152 MPa and 572 MPa, respectively.
Following the import of forklift geometry, fixed supports were applied to the legs of the fork, and the corresponding load was applied in the downward direction of the forks. Meshing was performed on the model as shown in Figure 5, resulting in the number of Nodes and Elements as 34,850 and 18,679 respectively.
3.3 Deformation analysis of forklift under operational loads
The static structural analysis of the forklift under different load conditions (20 N, 40 N, 60 N, and 80 N) illustrates a linear relationship between applied force and total deformation. As the uniformly distributed force increases, the total deformation proportionally escalates. Specifically, under a 20 N force, the deformation measures 0.000125 m as shown in Figure 6A, increasing consistently with force increments as depicted in Figures 6A–D. At 40 N, the maximum deformation reaches 0.000250 m as depicted in Figure 6B, escalating further to 0.000376 m at 60 N as illustrated in Figure 6C, and culminating at 0.000501 m under an 80 N force as shown in Figure 6D. These results indicate the forklift material and structural design reliably manage increasing loads, maintaining structural integrity while exhibiting linearly increasing deformation.
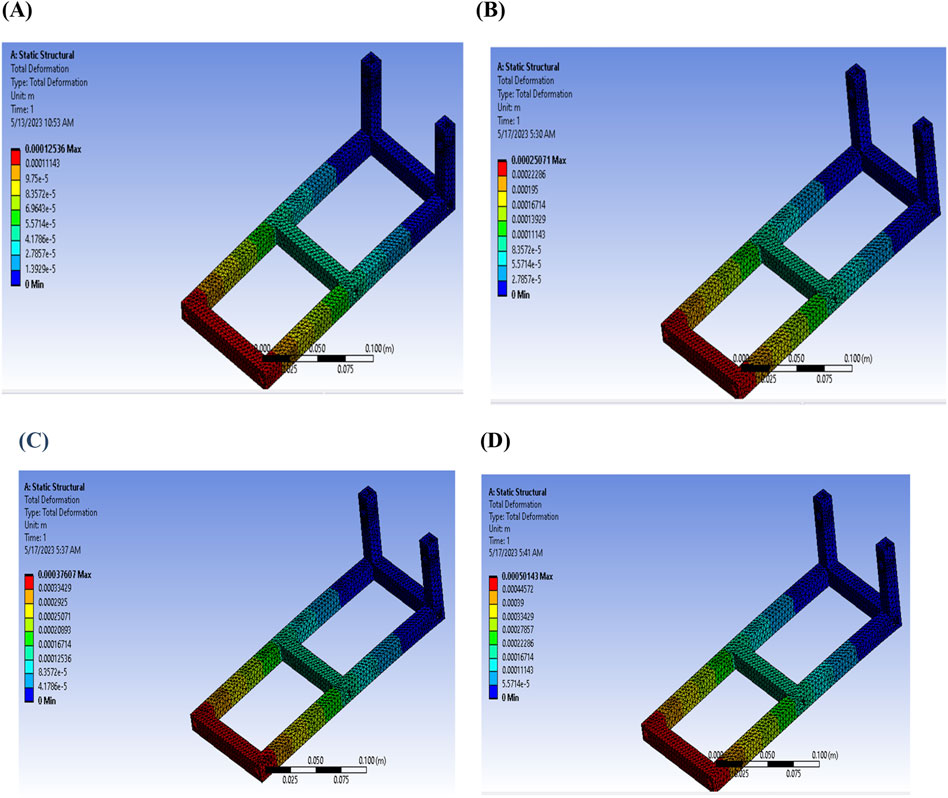
Figure 6. Total deformation at different loading conditions: (A) 20 N, (B) 40 N, (C) 60 N, (D) 80 N.
A graphical representation depicting the relationship between increasing force and total deformation is presented in Figure 7, demonstrating a linear correlation between these factors.
3.4 Evaluation of stress response in forklift under applied loadings
In the subsequent step of the static structural analysis of the forklift, equivalent Von-Mises stresses were calculated under various loading conditions of 20 N, 40 N, 60 N, and 80 N to assess the strength and safety of the prototype.
At a load of 20 N, the maximum stress is approximately 12.5 MPa, while the minimum stress is near zero as shown in Figure 8A, indicating areas with negligible stress. When the load increases to 40 N, the maximum stress nearly doubles to 25.1 MPa, with the minimum stress still close to zero in certain areas as illustrated in Figure 8B. For loads of 60 N and 80 N, the maximum stress further increases to about 37.2 MPa and 50.2 MPa, as depicted in Figures 8C, D respectively, while the minimum stress remains nearly zero. This consistent pattern highlights a predictable and linear increase in stress, graphically represented in Figure 9, reflecting the material’s ability to handle higher loads while maintaining a uniform stress distribution across the forklift. The maximum stress experienced by the fork is about 50 MPa, which is well below the tensile yield strength of 152 MPa. This proves that the material is saved under all applied loads up to 80 N.
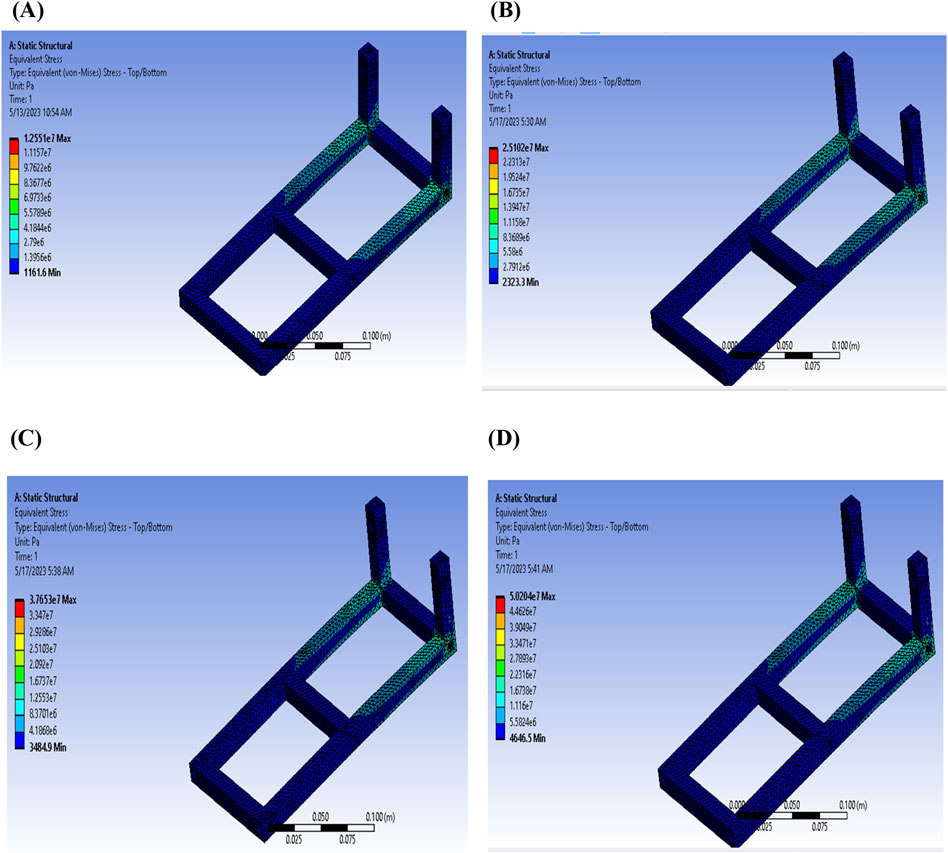
Figure 8. Equivalent stress at different loading conditions: (A) 20 N, (B) 40 N, (C) 60 N, (D) 80 N.
3.5 Comprehensive strain analysis of forklift under simulated loads
In the next phase of static structural analysis, elastic strain values are calculated to ensure the safety, reliability, and optimization of material and structural design. It also helps in understanding material behavior under different loading conditions ranging from 20 N to 80 N.
At a load of 20 N, the maximum equivalent strain is about 0.00012, while the minimum strain is nearly zero, indicating regions with negligible strain. As the load increases to 40 N, the maximum strain approximately doubles to 0.00024 as depicted in Figure 10. At load values of 60 N and 80 N, the maximum strains rise further to around 0.00036 and 0.00048 respectively while the minimum strain continues to be nearly zero at certain regions of the geometry. This consistent pattern demonstrates a predictable and linear increase in strain, reflecting the material’s and structure’s ability to handle higher loads while maintaining uniform strain distribution across the forklift, also graphically represented in Figure 10.
3.6 Structural integrity and factor of safety analysis of forklift
In the final phase of static structural analysis, the factor of safety was evaluated. The factor of safety indicates the margin a structure has before reaching its critical failure point. Figure 11 shows the trends of the factor of safety against force, ranging from 20 N to 80 N. At the force of 20 N, the maximum factor of safety is 15, while the minimum is zero. As the force increases to 40 N, the factor of safety decreases to 10, and it further reduces to 4 at a force value of 80 N. The value of the factor of safety as 9 at the intended design load of 50 N indicates that this project is safe under the specified loading conditions. The graph shows that geometry can easily withstand the load up to 80 N, but at the load value of 90 N, the factor of safety abruptly decreases to 1 which shows that the geometry is no safer at this load value.
The design load for the prototype is approximately 50 N. However, all calculations and graphs demonstrate that this battery-operated forklift prototype can safely withstand an applied force of up to 80 N.
3.7 Detailed comparative analysis of material costs
The total cost of each component used in the project, as well as the overall cost of the project prototype, is calculated and summarized here. The prices are calculated using a conversion factor of 1 USD = 278 PKR. Most of the materials used in the project are readily available in the marketplace (Ismail and Abdu Rahman, 2022; Electric, 2024).
The total cost of the project prototype is $ 89.34, and the detailed distribution of component cost is illustrated in Figure 12, as a pie chart. The 10 DC gear motors used in this project account for $ 5.38 having a share of 6% in the total cost of the project. A wiper motor, priced at $ 16.15, contributes 18.1% to the overall expenditure of the project. The motor driver and battery are priced at $ 1.61 and $ 10.77 respectively. Similarly, the costs of the charger, lifting mechanism, frame, and plastic sheet are $ 5.74, $ 1.79, $ 7.18, and $ 7.18 respectively. The chart indicates that the largest portion of the cost belongs to the mobile application, which accounts for 20.92% of the total cost, enabling remote control of the project via mobile phone. Conversely, the motor driver constitutes the smallest portion of the cost, representing only 1.88% of the total expenditure. Wires, wires board, tires, and lifting mechanism each contribute 2% to the overall project cost.
The comparative analysis between electric and diesel forklifts based on cost, lifting capacity, and power source is presented in Table 4. The estimated price of a diesel forklift is derived from (MHEDA, 2024).
The total cost of this project prototype, having a lifting capacity of 5 kg, is 89.34 $. The estimated and derived price of a diesel forklift having a similar capacity is 813.46 $, which is well above in comparison to this project prototype having an electric power source.
4 Conclusion
This study presents a comprehensive analysis of the fabrication, structural assessment, and operational capabilities of a low-cost, fully rotatable vehicle-mounted forklift. The prototype was meticulously constructed and assembled to ensure optimal functionality. Through systematic testing, including deformation, stress, strain, and factor of safety analyses under different operational loading, the results consistently validate the forklift’s ability to handle a load up to 80 N. The main findings of this research are as follows:
• This project introduces a 360-degree rotating electric forklift, with a traveling speed of 0.5 m/s and load capacity of 5–8 kg, offering a practical, viable, and efficient alternative to traditional diesel-powered forklifts.
• The efficient control system built with an ESP-32 microcontroller, Arduino programming, DC motors, and L298N motor drivers, enhances forklift safety, ensuring secure handling of goods through a mobile phone, particularly in small and crowded warehouses.
• At an approximate cost of 90$, the forklift provides a low-cost and economically feasible option for different industries.
• Static structural analysis using Ansys revealed that the maximum total deformation of 0.5 mm against the extreme load value of 80 N, confirms the design’s safety.
• The maximum stress value recorded was nearly 50 MPa, and a factor of safety value of 9 at the intended design load of 50 N, ensures the forklift’s structural reliability under the operational loads.
Data availability statement
The original contributions presented in the study are included in the article/supplementary material, further inquiries can be directed to the corresponding authors.
Author contributions
AJ: Conceptualization, Data curation, Formal Analysis, Investigation, Writing–original draft, Writing–review and editing. MF: Conceptualization, Funding acquisition, Project administration, Resources, Supervision, Validation, Writing–review and editing. IA: Investigation, Validation, Visualization, Writing–review and editing. NH: Investigation, Validation, Visualization, Writing–review and editing. AM: Data curation, Software, Validation, Visualization, Writing–review and editing. IZ: Investigation, Methodology, Validation, Writing–review and editing. NA: Data curation, Methodology, Software, Validation, Writing–review and editing. MH: Data curation, Validation, Writing–review and editing. MN: Data curation, Visualization, Writing–review and editing. FR: Funding acquisition, Investigation, Resources, Writing–review and editing.
Funding
The author(s) declare that no financial support was received for the research, authorship, and/or publication of this article.
Conflict of interest
The authors declare that the research was conducted in the absence of any commercial or financial relationships that could be construed as a potential conflict of interest.
Generative AI statement
The author(s) declare that no Generative AI was used in the creation of this manuscript.
Publisher’s note
All claims expressed in this article are solely those of the authors and do not necessarily represent those of their affiliated organizations, or those of the publisher, the editors and the reviewers. Any product that may be evaluated in this article, or claim that may be made by its manufacturer, is not guaranteed or endorsed by the publisher.
References
Abdellatif, M., Shoeir, M., Talaat, O., Gabalah, M., Elbably, M., and Saleh, S. (2018). “Design of an autonomous forklift using Kinect,”. Editors P. Tandon, W. Wisnoe, and M. Z. Bin Abdullah, 153. doi:10.1051/matecconf/201815304005Available at: https://www.matec-conferences.org/10.1051/matecconf/201815304005.MATEC Web Conf.
Abuzied, H., Nazih, N., and Sahbel, A. (2024). Design and simulation of eco-friendly smartphone controlled forklift. Heliyon 10 (9), e30682. doi:10.1016/j.heliyon.2024.e30682Available at: https://linkinghub.elsevier.com/retrieve/pii/S2405844024067136.
Adedeji, A. K., Abiodun, Y. A., Shola, E. W., Anthony, O. S., and Gbolahan, O. A. (2023). Design and Development of AKEA: a 360-degree rotating vehicle. Glob. J. Eng. Technol. Adv. 16 (2), 065–074. doi:10.30574/gjeta.2023.16.2.0142Available at: https://gjeta.com/content/design-and-development-akea-360-degree-rotating-vehicle.
Al-Douri, A., Ruiz-Tagle, A., and Groth, K. M. (2023). A quantitative risk assessment of hydrogen fuel cell forklifts. Int. J. Hydrog. Energy 48 (50), 19340–19355. doi:10.1016/j.ijhydene.2023.01.369Available at: https://linkinghub.elsevier.com/retrieve/pii/S0360319923006547.
Ali, D. P. M. (2019). Design and fabrication of 360 degree rotating vehicle. Int. J. Res. Appl. Sci. Eng. Technol. 7 (2), 697–701. doi:10.22214/ijraset.2019.2100Available at: https://www.ijraset.com/fileserve.php?FID=20066.
Amio, F. F., Ahmed, N., Jeong, S., Jung, I., and Nam, K. (2024). Optimizing precision material handling: elevating performance and safety through enhanced motion control in industrial forklifts. Electronics 13 (9), 1732. doi:10.3390/electronics13091732Available at: https://www.mdpi.com/2079-9292/13/9/1732.
Bhat, A., Kai, N., Suzuki, T., Shiroshima, T., and Yoshida, H. (2023). An advanced autonomous forklift based on a networked control system. IFAC-Pap 56 (2), 11444–11449. doi:10.1016/j.ifacol.2023.10.432Available at: https://linkinghub.elsevier.com/retrieve/pii/S2405896323007991.
Bhui, B. S., Gupta, P., Pawar, A., Javed, M., and Magar, V. M. (2024). Development of 3600 rotating vehicle. 3(11).
Burinskiene, A. (2011). The travelling of forklifts in warehouses. Int. J. Simul. Model 10 (4), 204–212. doi:10.2507/ijsimm10(4)4.191Available at: http://www.ijsimm.com/Full_Papers/Fulltext2011/text10-4_204-212.pdf.
Choi, M., Ahn, S., and Seo, J. (2020). VR-Based investigation of forklift operator situation awareness for preventing collision accidents. Accid. Anal. Prev. 136, 105404. doi:10.1016/j.aap.2019.105404Available at: https://linkinghub.elsevier.com/retrieve/pii/S0001457519308346.
Department of Industrial Engineering, School of Engineering Univeristy, D., Damghan, , Iran, , Fazlollahtabar, H., and Smailbašić, A. (2019). FUCOM method in group decision-making: selection of forklift in a warehouse. Decis. Mak. Appl. Manag. Eng. 2 (1), 49–65. doi:10.31181/dmame1901065fAvailable at: https://dmame-journal.org/index.php/dmame/article/view/26.
Dinesh, N., Kumar, V. A., Christon, A. A., Dharshan, B., and Kumar, M. M. (2021). Design and fabrication of 360 degree car parking. Int. J. Eng. Res. 9 (10).
Doçi, I., and Imeri, V. (2013). Dynamic analysis of forklift during load lifting using modeling and simulations. Int. J. Curr. Eng. Technol.
Electric, F. (2024). Diesel forklifts: which one is right for the job? Available at: https://www.tcm.eu/blog/electric-vs.-gas-or-diesel-forklifts-which-one-is-right-for-the-job.
Elgowainy, A., Gaines, L., and Wang, M. (2009). Fuel-cycle analysis of early market applications of fuel cells: forklift propulsion systems and distributed power generation. Int. J. Hydrog. Energy 34 (9), 3557–3570. doi:10.1016/j.ijhydene.2009.02.075Available at: https://linkinghub.elsevier.com/retrieve/pii/S0360319909003644.
Facchini, F., Mummolo, G., Mossa, G., Digiesi, S., Boenzi, F., and Verriello, R. (2016). Minimizing the carbon footprint of material handling equipment: comparison of electric and LPG forklifts. J. Ind. Eng. Manag. 9 (5), 1035. doi:10.3926/jiem.2082Available at: http://www.jiem.org/index.php/jiem/article/view/2082.
Ferraro, S., Leoni, L., Cantini, A., and De Carlo, F. (2024). Analyzing forklift and drone applications in sustainable logistics: a bibliometric review. IFAC-Pap 58 (19), 463–468. doi:10.1016/j.ifacol.2024.09.255Available at: https://linkinghub.elsevier.com/retrieve/pii/S2405896324016847.
Figueiredo, M. V., Oliveira, F. M. F., Gonçalves, J. P. M., De Castro, PMST, and Fernandes, A. A. (2001). Fracture analysis of forks of a heavy duty lift truck. Eng. Fail Anal. 8 (5), 411–421. doi:10.1016/s1350-6307(00)00040-6Available at: https://linkinghub.elsevier.com/retrieve/pii/S1350630700000406.
Forklift accident statistics (2024). Available at: https://www.mccue.com/blog/forklift-accident-statistics
Gaines, L., Elgowainy, A., and Wang, M. (2008). Full fuel-cycle comparison of forklift propulsion systems. Department of Energy US.
Hassan, W. U., Jalal, A., Bilal, M. A., Buzal, M. Z., Asghar, H., and Ali, U. (2024). Parametric analysis of a helical-bladed vertical axis wind turbine. J. Ocean. Eng. Mar. Energy 10 (2), 383–398. doi:10.1007/s40722-024-00318-0Available at: https://link.springer.com/10.1007/s40722-024-00318-0.
Hema Latha, K., Misbahuddin Husaini, S., Saboor Sohail, S. A., and Ahmed Khan, M. (2021). in Design and analysis of a remotely operated mini forklift bot. E3S web conf. Editors S. Tummala, S. Kosaraju, P. Bobba, and S. Singh, 309. Available at: https://www.e3s-conferences.org/10.1051/e3sconf/202130901168.01168
Hosseinzadeh, E., Rokni, M., Advani, S. G., and Prasad, A. K. (2013). Performance simulation and analysis of a fuel cell/battery hybrid forklift truck. Int. J. Hydrog. Energy 38 (11), 4241–4249. doi:10.1016/j.ijhydene.2013.01.168Available at: https://linkinghub.elsevier.com/retrieve/pii/S0360319913003005.
Hsieh, C. Y., Pei, P., Bai, Q., Su, A., Weng, F. B., and Lee, C. Y. (2021). Results of a 200 hours lifetime test of a 7 kW Hybrid–Power fuel cell system on electric forklifts. Energy 214, 118941. doi:10.1016/j.energy.2020.118941Available at: https://linkinghub.elsevier.com/retrieve/pii/S036054422032048X.
Iinuma, R., Kojima, Y., Onoyama, H., Fukao, T., Hattori, S., Nonogaki, Y., et al. (2020). Pallet handling system with an autonomous forklift for outdoor fields. J. Robot. Mechatron. 32 (5), 1071–1079. doi:10.20965/jrm.2020.p1071Available at: https://www.fujipress.jp/jrm/rb/robot003200051071.
Ismail, A. P. E., and Abdu Rahman, R. (2022). An open design for a low-cost open-loop subsonic wind tunnel for aerodynamic measurement and characterization. HardwareX 12, e00352. doi:10.1016/j.ohx.2022.e00352Available at: https://linkinghub.elsevier.com/retrieve/pii/S2468067222000979.
Jagtap, K. S., Londhe, S. D., Khujat, S. M., Koli, P. S., and Desai, A. A. A. (2024). Design and fabrication of battery operated remote control articulated forklift.
Jie, Y., Fa-guo, H., and Xin-jia, Z. (2019). “Manual hydraulic forklift fork analysis based on ANSYS workbench,” in Proceedings of the 2019 4th international conference on intelligent information processing (China China: ACM), 91–95. Available at: https://dl.acm.org/doi/10.1145/3378065.3378083.
Kumar, S., Ranjan, A., Kumar, U., Kumar, D., and Kumar, D. (2020). 360 Degree wheel rotation vehicles;8(6).
Massone, J. M., and Boeri, R. E. (2010). Failure of forklift forks. Eng. Fail Anal. 17 (5), 1062–1068. doi:10.1016/j.engfailanal.2009.12.005Available at: https://linkinghub.elsevier.com/retrieve/pii/S1350630709002933.
Metzger, N., and Li, X. (2022). Technical and economic analysis of fuel cells for forklift applications. ACS Omega 7 (22), 18267–18275. doi:10.1021/acsomega.1c07344
MHEDA (2024). Material handling equipment distributors association: your source for material handling insight your material handling industry association. Available at: https://www.mheda.org/.
Milanowicz, M., Budziszewski, P., and Kędzior, K. (2018). Numerical analysis of passive safety systems in forklift trucks. Saf. Sci. 101, 98–107. doi:10.1016/j.ssci.2017.07.006Available at: https://linkinghub.elsevier.com/retrieve/pii/S092575351630707X.
Moe San, Z. Z., Thike, A., and Min Oo, D. Z. (2019). Electronic forklift by remote control. Int. J. Sci. Eng. Appl. 8 (6), 162–166. Available at: https://ijsea.com/archieve/volume8/issue6/ijsea08061003.pdf.
Moudgil, J., Mengi, S., Chopra, M., and Singh, D. J. (2015). 360° rotating vehicle to overcome the problem of parking space;5(2).
Najmuzzama, K. M., Sharif, K. H., Roshan, M. M. S., Vishal, P., and Gulbarga, M. A. (2022). Universal turning forklift. Eng. Technol. 10, 959–966. doi:10.22214/ijraset.2022.41995
Ono, T., Iwasaki, T., Kato, M., Sakisaka, T., Mori, Y., Nejima, R., et al. (2024). Debilitating ocular globe rupture due to a forklift accident: a case report. Trauma Case Rep. 53, 101081. doi:10.1016/j.tcr.2024.101081Available at: https://linkinghub.elsevier.com/retrieve/pii/S2352644024001043.
Panara, K. S., Mishra, V. R., Patel, A. M., Patel, T. B., and Dhivar, K. R. (2024). Construction of battery operated forklift. 2(4).
Potdukhe, D. P. (2019). Design, construction and testing of two wheel drive forklift. Int. J. Res. Advent Technol. 7 (4), 53–55. Available at: https://www.ijrat.org/downloads/Vol-7/april-2019/PaperID-74201923.pdf.
Raut Shubham, B., Gawade Karan, D., Mane, V. N., More Shubham, N., and Suryavanshi Amol, V.Savitribai Phule Pune University (2020). Design of electric forklift used in small industrial warehouses and workshops. Int. J. Eng. Res. Available at: https://www.ijert.org/design-of-electric-forklift-used-in-small-industrial-warehouses-and-workshops.
Rebelle, J., Mistrot, P., and Poirot, R. (2009). Development and validation of a numerical model for predicting forklift truck tip-over. Veh. Syst. Dyn. 47 (7), 771–804. doi:10.1080/00423110802381216Available at: http://www.tandfonline.com/doi/abs/10.1080/00423110802381216.
Renquist, J. V., Dickman, B., and Bradley, T. H. (2012). Economic comparison of fuel cell powered forklifts to battery powered forklifts. Int. J. Hydrog. Energy 37 (17), 12054–12059. doi:10.1016/j.ijhydene.2012.06.070Available at: https://linkinghub.elsevier.com/retrieve/pii/S036031991201453X.
Roskam, R. (2018). “Development of a forklift for research and education in mechatronics,” in Proceedings of the 2018 2nd international conference on mechatronics systems and control engineering (Amsterdam Netherlands: ACM), 17–21. Available at: https://dl.acm.org/doi/10.1145/3185066.3185070.
Saric, S., Bab-Hadiashar, A., Hoseinnezhad, R., and Hocking, I. (2013). Analysis of forklift accident trends within Victorian industry (Australia). Saf. Sci. 60, 176–184. doi:10.1016/j.ssci.2013.07.017Available at: https://linkinghub.elsevier.com/retrieve/pii/S0925753513001677.
Sarker, A., Amin, S. A., Tamzid, S. M. T. H., and Chisty, N. A. (2017). “Design and implementation of a forklift with dynamic stability,” in 2017 IEEE region 10 humanitarian technology conference (R10-HTC) (Dhaka: IEEE), 658–663. Available at: http://ieeexplore.ieee.org/document/8289045/.
Sequeira, A., Mohammed, S., Kumar, A., Sameer, M., Kareem, Y., and Sachidananda, K. (2019). Design and fabrication of battery operated forklift. J. Eur. Systèmes Autom. 52 (6), 569–574. doi:10.18280/jesa.520604Available at: http://www.iieta.org/journals/jesa/paper/10.18280/jesa.520604.
Singh, A., Kumar, A., Chaudhary, R., and Singh, R. C. (2024). Study of 4 wheel steering systems to reduce turning radius and increase stability.
Soni, A., Ansari, A., Gahlod, P., Tiwari, S., Dohare, K., and Damahe, J. (2018). Design and analysis of 360 degree turning vehicle. SMART MOVES J. IJOSCIENCE 4 (4), 5. doi:10.24113/ijoscience.v4i4.131Available at: http://ijoscience.com/ojsscience/index.php/ojsscience/article/view/131.
Sonker, D. D., Khatri, D. V., Kaur, M. R., and Yadav, M. A. (2021). Bluetooth car controlled using Arduino. Int. J. Adv. Res. Sci. Commun. Technol., 416–420. doi:10.48175/ijarsct-1963Available at: http://ijarsct.co.in/sepi1.html.
Tamba, T. A., Hong, B., and Hong, K. S. (2009). A path following control of an unmanned autonomous forklift. Int. J. Control Autom. Syst. 7 (1), 113–122. doi:10.1007/s12555-009-0114-yAvailable at: http://link.springer.com/10.1007/s12555-009-0114-y.
Vivaldini, K. C. T., Galdames, J. P. M., Becker, M., and Caurin, G. A. P. (2009). Automatic routing of forklift robots in warehouse applications;
Vivaldini, K. C. T., Galdames, J. P. M., Bueno, T. S., Araujo, R. C., Sobral, R. M., Becker, M., et al. (2010). “Robotic forklifts for intelligent warehouses: routing, path planning, and auto-localization,” in 2010 IEEE International Conference on Industrial Technology. Vina del Mar: IEEE, 1463–1468. Available at: http://ieeexplore.ieee.org/document/5472487/.
Wang, L., Zhao, D., Wang, Y., Wang, L., Li, Y., Du, M., et al. (2017). Energy management strategy development of a forklift with electric lifting device. Energy 128, 435–446. doi:10.1016/j.energy.2017.04.012Available at: https://linkinghub.elsevier.com/retrieve/pii/S0360544217305765.
WarehouseWiz Inc. (2024). OSHA forklift accident statistics you need to know. Available at: https://warehousewiz.com/blogs/news/osha-forklift-accident-statistics.
Yadav, J., Vishwakarma, M., Shakir, S. M., Yadav, S., and Rehman, Y. (2022). Design and fabrication of electric forklift. Int. J. Res. Appl. Sci. Eng. Technol. 10 (4), 589–593. doi:10.22214/ijraset.2022.41344Available at: https://www.ijraset.com/best-journal/design-and-fabrication-of-electric-forklift.
Yao, Z., Li, H., and Zhou, L. (2022). Research and development of electric power lifting truck. J. Phys. Conf. Ser. 2218 (1), 012076. doi:10.1088/1742-6596/2218/1/012076Available at: https://iopscience.iop.org/article/10.1088/1742-6596/2218/1/012076.
Zack, F., Blaas, V., and Büttner, A. (2018). Unusual head injury by a forklift vehicle. J. Forensic Leg. Med. 56, 9–11. doi:10.1016/j.jflm.2018.02.024Available at: https://linkinghub.elsevier.com/retrieve/pii/S1752928X18300702.
Zajac, P., and Rozic, T. (2022). Energy consumption of forklift versus standards, effects of their use and expectations. Energy 239, 122187. doi:10.1016/j.energy.2021.122187Available at: https://linkinghub.elsevier.com/retrieve/pii/S036054422102435X.
Keywords: battery-operated forklift, autonomous forklift, 360-degree rotating vehicle, zerodegree turning radius, DC gear motor, ESP-32 motion control System
Citation: Jalal A, Farooq M, Anwer I, Hayat N, Munir A, Zahid I, Akbar NS, Hamza M, Nouman M and Riaz F (2025) Design and development of a low-cost, eco-friendly forklift for sustainable logistics management. Front. Built Environ. 10:1506495. doi: 10.3389/fbuil.2024.1506495
Received: 05 October 2024; Accepted: 10 December 2024;
Published: 06 January 2025.
Edited by:
Kong Fah Tee, King Fahd University of Petroleum and Minerals, Saudi ArabiaReviewed by:
Zhixiong Zeng, Nanjing University, ChinaMonika Chuda-Kowalska, Poznań University of Technology, Poland
Copyright © 2025 Jalal, Farooq, Anwer, Hayat, Munir, Zahid, Akbar, Hamza, Nouman and Riaz. This is an open-access article distributed under the terms of the Creative Commons Attribution License (CC BY). The use, distribution or reproduction in other forums is permitted, provided the original author(s) and the copyright owner(s) are credited and that the original publication in this journal is cited, in accordance with accepted academic practice. No use, distribution or reproduction is permitted which does not comply with these terms.
*Correspondence: Muhammad Farooq, bWZhcm9vcUBwbXUuZWR1LnNh; Fahid Riaz, ZmFoaWQucmlhekBhZHUuYWMuYWU=