- 1National Technical University of Ukraine “KPI”, Kyiv, Ukraine
- 2Department of Transformation of Structure of Fuel and Energy Complex, General Energy Institute of NAS of Ukraine, Kyiv, Ukraine
- 3Institute of Sustainable Building Materials and Engineering Systems, Riga Technical University, Riga, Latvia
Improving the comfort of living and/or working conditions in buildings usually requires an increase in the consumption of energy and building materials, e.g., for thermal modernization, and thus additional economic costs. It is also important to note that this does not always lead to a reduction in overall emissions of pollutants into the environment, taking into account emissions at all stages of the production and use of energy and materials for energy efficiency and comfort in buildings. The paper is devoted to the problems of modelling energy supply systems for buildings, including methods and means of simulating thermal regimes of buildings and their engineering systems, as well as methods and means of modelling the operating modes of heat pumps that can be used in such systems for a coordinated improvement of energy efficiency and indoor climatic conditions in buildings. Based on the developed mathematical models, the dynamic modes of building energy supply systems are studied and recommendations for improving their efficiency are given. The dynamic models of the energy supply system is implemented in the MATLAB/Simscape software environment and the possibilities (schemes) of detailing the components of different types of sources are shown. The obtained results were verified by means of energy models created in the widely used software product EnergyPlus. It was found that, according to the quasi-steady-state method, the deviation of the energy consumption does not exceed 13% and is about 5% in dynamic modes. The possibilities of using a gas boiler and a heat pump as the most common sources of individual energy supply systems for buildings are investigated. It was found that the heat pump has a more flexible load level control. Its use can reduce the instantaneous power value by up to 40%, but the frequency of switching on the pump is much higher (about 4 times) compared to the gas boiler. If the energy sources produce the same amount of energy, the heat pump keeps the temperature within the set range more efficiently, avoiding overheating. In general, the presented energy dynamic building model and its software implementation allow a wide range of researchers to simulate different energy supply systems to ensure proper energy efficiency and indoor climate in a building.
1 Introduction
The buildings sector, with a share of about 35%, is the largest consumer of total energy consumption in the world, surpassing the contribution of the transport and industrial sectors. In particular, buildings consume around 40% of total energy consumption in the EU and the US, with a corresponding share of CO2 emissions of 36%. This share is projected to grow by 50% by 2050 compared to 2013 figures (Jradi, 2020). It is clear that requirements for the energy efficiency of buildings and their energy supply systems will constantly increase in accordance with the principles of the low-carbon transition to a green economy (Kovalko et al., 2022). In addition to energy efficiency, it is necessary to note several other important factors that determine the quality of climatic conditions in the premises of buildings, such as temperature and air pollution, where non-compliance with sanitary standards significantly worsens the health of workers and residents of buildings. The most common sources of pollution include industrial technologies, cooking, and the use of low-quality building materials (Zaporozhets et al., 2023). All these factors are interdependent, requiring careful study and subsequent optimal coordination to achieve energy and environmental goals.
The level of energy consumption in buildings is reduced in various directions and depends on a number of factors, such as thermal insulation of enclosing structures, management of engineering energy supply systems, climatic conditions, etc. Therefore, a comprehensive approach is essential to analyze the combined impact of these factors and establish the potential for energy resource savings. The assessment of the energy efficiency of a building is carried out on the basis of mathematical modeling. Currently, such models are implemented in the form of software packages – computer software suites. Most software products are based on grid models that combine a set of physically dependent elements, offering a structured framework to simulate energy flows and interactions within buildings. Models built on the equations of physical processes and/or simulation modeling are referred to as “white-box” models, which provide detailed and accurate predictions of building energy dynamics. Simulation modeling involves representing the model as an algorithm and computer program, enabling the reproduction of the object’s behavior. Building Energy Modeling (BEM) is a powerful tool for predicting a building’s energy consumption and estimating energy savings relative to a standard baseline (Kon et al., 2024). It has been shown to be particularly effective for dynamic temperature control in district heating systems (Han et al., 2024), demonstrating its potential for enhancing the energy performance of buildings under varied climatic conditions. Energy-efficient renovation of existing buildings and their HVAC systems has also been emphasized as a critical area for improving energy consumption and achieving sustainability goals. Practical, market-ready solutions to enhance energy efficiency in buildings through renovation measures, providing valuable insights for professionals in this field are highlighted in Cholewa et al. (2022).
The objective of the study is to develop a methodological framework and an energy dynamic model of a building implemented on the MATLAB/Simulink software platform, as well as to model in detail the capabilities of various building energy supply systems to ensure adequate energy efficiency and indoor climate improvement by addressing real-world operational complexities.
The novelty of the study is determined by the systematic solution to the problem of ensuring comfortable living conditions in the building due to the dynamic modes of operation of energy supply sources. The research also provides a justification for using various energy supply sources for buildings, taking into account the dynamic characteristics of the building envelope and engineering systems, as well as the operational features of controllers under variable climatic and internal conditions. This approach ensures the maintenance of comfortable indoor air temperatures under real operating conditions, highlighting its adaptability for existing buildings rather than theoretical designs.
Unlike EnergyPlus, which is tailored primarily for design purposes, the proposed MATLAB/Simulink model considers the inertia of engineering systems, adaptability to operating conditions, and sources of heat supply. This allows the model to account for features of existing buildings, such as system contamination, temperature variability across rooms (it is not always a uniform 20°C), and other factors characteristic of real-world operation. By capturing these differences in room temperatures and system behavior, the MATLAB/Simulink model offers a more practical and realistic representation of building performance under diverse operational scenarios.
The practical relevance of this study lies in equipping designers and practicing engineers with a methodological framework that improves the efficiency and quality of building energy supply systems. The proposed approach enables more informed decision-making to optimize energy efficiency and indoor comfort, taking into account the unique challenges of real-world conditions.
2 Literature review
There are many dynamic software products available for assessing building energy consumption. TRNSYS is a versatile tool frequently used for simulating complex energy systems, including renewable energy applications (Bae et al., 2021). MATLAB/Simulink is particularly effective for creating dynamic models of building energy systems, enabling detailed analysis of thermal and energy flows (Lu et al., 2021). EnergyPlus is widely employed for simulating building energy performance, particularly for analyzing energy efficiency and optimizing system designs (Deshko et al., 2021a). However, poor temperature regulation in indoor spaces remains a common issue in heating and cooling systems, particularly in residential buildings located in countries with cold and temperate climates, such as those in Europe (Deshko et al., 2023). The mechanisms of dynamic regulation of indoor air temperature using a centralized control system are analyzed in paper (Alibabaei et al., 2017). For residential buildings with autonomous heating sources, the choice of heat source and the peculiarities of their operation require separate consideration of several influential factors (Deshko et al., 2021b).
Most existing building energy supply technologies are based on the use of heat sources with high exergy values, however, directly within buildings, energy with relatively low exergy is needed to create thermal comfort, corresponding to temperature levels within 18°C–20°C. As a result, a significant portion of high-quality energy is lost. Currently, a new direction has emerged in the field of heating and cooling – low-exergy buildings (Hinkelman et al., 2023).
Models of heat pump units (HPUs) can be developed by considering the physical processes occurring in the objects, referred to as physics-based models, or by processing experimental data, referred to as data-based models (Goyal et al., 2019). Physics-based models rely on formalizing physical processes, which can be approached in several ways (Afram et al., 2018). In the simplest approach, the object is considered as having characteristics that do not change along the coordinates, also known as an object with concentrated parameters. To account for the dynamics of phase transition zone changes, the moving boundary method is commonly applied (Grald and MacArthur, 1992).
In Yao et al. (2013), a model of the dynamic processes of a chiller as an object with concentrated parameters was developed. Based on the physical approach, a system of nonlinear first-order differential equations is initially formed, then these equations are linearized, and as a result, the model is represented in the state space. The adequacy of the eQuest model was confirmed by a series of experiments with a chiller using R-134a refrigerant. Compared to experimental data, the modeling results error does not exceed 10%.
Later, in the studies Yao et al. (2015), the authors proposed a model of chiller dynamics based on the moving boundary method to account for transient processes during phase transitions. In the compressor and expansion valve models, inertia was not considered due to its negligible influence. The accuracy of the model was evaluated through experiments, with errors in most cases not exceeding 10%.
The authors (Sanama and Xia, 2021) proposed a methodology for modeling transient processes in vapor compression systems based on the finite volume method. It is shown that increasing the discretization step improves the calculation accuracy. It is indicated that the modeling accuracy can be enhanced by considering changes in mass flow rate in the expansion valve and compressor during system startup, evaluating the dependency of heat transfer coefficients in heat exchangers on the phase state, as well as by accounting for pressure losses in the condenser and evaporator.
In Husmann and Aschemann (2022), based on the finite volume method, three types of models are proposed for evaluating transient processes in vapor compression refrigeration systems. In the first, baseline model, the most general conditions of mass and energy balance equations in the evaporator and condenser are considered. In the second model, pressure losses in the heat exchangers are not taken into account. The third model further simplifies the calculation of working fluid mass flow rates in the cells through linear interpolation. It is shown that the second model yields practically the same results as the baseline model but reduces the computation time. However, the third model significantly deteriorates the accuracy of the obtained data compared to the baseline model.
In Voloshchuk et al. (2023), based on the mathematical description of physical phenomena, a model of dynamic processes in an air-to-water heat pump system with a capacity of 10 kW and using R-134a refrigerant was developed and implemented in the MATLAB software package. It was found that the investigated transient processes can be approximated by first-order aperiodic links. Their transfer coefficients and time constants, which vary within 3 … 5 s, and time lags, if present, ranging from 0.5 … 3 s, were determined. It was determined that under different initial conditions, the transfer coefficients of most transient processes change, indicating the nonlinearity of the control object.
In Sangi et al. (2019), the authors proposed a combination of the moving boundary method and discretization method to create a dynamic model of a geothermal heat pump system (GHP) with vertical and horizontal ground heat exchangers in the Modelica package. Two types of such GHP systems were investigated: one utilizing an intermediate ground heat exchanger to supply heat to the evaporator and another using the ground heat exchanger as the evaporator. The GHP system was studied as part of a building heating system. Exergy analysis conducted within the research revealed that the geothermal GHP system using a ground heat exchanger as the evaporator is more efficient compared to the traditional system. Additionally, it was demonstrated that the vertical ground heat exchanger-evaporator is characterized by better performance than the horizontal one.
In Artuso et al. (2021), a numerical model of a reversible heat pump system (HP) using CO2 as the working fluid is presented. The model was developed using the Simcenter AMESim v.17 package. When comparing the calculated data with experimental results, it was found that the maximum error (+5.0%) occurs for the heat flow in the gas cooler. The developed simulation model was used to investigate the operation of the HP system in combination with a hot water storage tank for heating and domestic hot water supply purposes. The potential for achieving a higher coefficient of performance (COP) in the domestic hot water production mode due to the lower temperature of the incoming water is demonstrated.
In the article Li et al. (2017), a dynamic model of cooling systems is developed, which includes models of a chiller, a chilled water pipeline, and a fan coil unit. To simplify, a new parameter called “cooling capacity of the working body” is introduced in the study. Regularities in the change of this parameter during dynamic processes for two common control strategies on the chiller side (on/off switching and changing the chilled water temperature) are obtained and confirmed through experiments and field tests. Based on the model, the dynamics of the change in air inlet temperature are calculated, and it is shown that the root mean square deviation of the obtained data compared to the experiments is 0.43°C and 0.16°C, respectively.
In the article Choi et al. (2021), a model of transient processes in a heat pump dryer was developed based on the finite volume method. It was shown that compared to experimental values, the error in calculating parameters based on the model does not exceed 6.1%. Using the developed simulation model, the dynamic behavior and productivity of the heat pump unit (HPU) were analyzed when changing operating modes and the length of the heat exchanger. The operating mode with a higher compressor rotation frequency showed the potential to increase the moisture extraction rate (MER) by 16.5% due to reduced drying time. However, reducing the compressor rotation frequency leads to a 34.8% increase in the specific MER due to reduced energy consumption. With an increase in the length of the heat exchanger from 80% to 120%, the MRC increased by 10%, and the SMRC increased by 14%. Additionally, with an increase in compressor rotation frequency, the optimal length of the heat exchanger for achieving maximum productivity also increases.
In work Garcia et al. (2018), a comparison of the impact of refrigerants R134a and R1234yf on transient processes in the evaporator, which uses water as a secondary heat carrier, is presented. The dynamic model with distributed parameters includes the laws of thermodynamics, heat, and mass transfer taking into account empirical relationships cited in the literature to consider the degree of dryness, pressure drop, and heat exchange in the two-phase flow. Experimental studies were conducted on a stationary refrigeration unit with a capacity of 3 kW under constant condensation conditions but with changes in evaporation temperature and compressor rotation frequency to verify the accuracy of the model. It was shown that the error in determining the evaporation temperature was within ±1°C. Comparison of transient processes with working fluids R134a and R1234yf under conditions of step disturbance of their mass flow rates showed no significant difference between the dynamic characteristics of the unit.
In the article Borodinecs et al. (2024a), an evaluation of HVAC system efficiency in office buildings was conducted using a data-driven approach integrated with building performance simulation software. The authors examined the control strategy of an office building equipped with a constant air volume (CAV) HVAC system and a regularly controlled air handling unit (AHU), aiming to enhance energy efficiency while maintaining a balance between occupant comfort and energy consumption. The study demonstrated that close monitoring of indoor parameters by building operators, coupled with corresponding adjustments to the HVAC system, can achieve energy savings of up to 16%. Based upon these insights, the paper suggests integrating data-driven and dynamic simulation methods into building management system models to optimize HVAC systems, enhance energy efficiency, and support carbon neutrality objectives.
In work Borodinecs et al. (2024b), a framework for optimizing office building operations through continuous dynamic energy simulations was presented, utilizing digital twins for enhanced building performance management. Using OpenStudio, an open-source platform for building energy modeling, the study demonstrated the creation and editing of digital twins, incorporating detailed modeling of building components and systems, historical data to accurately represent building geometry, materials, schedules, and HVAC systems. The study showed that digital twins, integrated with machine learning algorithms and connected to building management systems, can automate optimal building control strategies, thereby reducing energy consumption and improving occupant comfort. The potential of digital twins lies in their ability to simulate future building conditions and optimize system settings, contributing significantly to the sustainability goals of the wider EU.
The literature review highlights that the use of MATLAB/Simulink is highly suitable for detailed studies of building energy supply systems and sources. The integration of dynamic energy models for buildings and energy supply sources, developed in the MATLAB/Simscape environment, enables adaptation of the models to real operating conditions and management regimes for energy systems. Furthermore, the growing prevalence of heat pumps in autonomous heating systems of residential buildings underscores the need for a comprehensive analysis of various energy supply sources to ensure both energy efficiency and proper indoor climate conditions.
The aim of this research is to model the dynamic modes of integrated energy supply systems for buildings located in regions with sharply continental climates. The objectives of the study are as follows:
1. Develop a dynamic energy model of the building in the MATLAB/Simscape environment;
2. Validate the dynamic energy model;
3. Perform energy modeling of the building using a gas boiler as a heating source;
4. Perform energy modeling of the building using a heat pump as a heating source;
5. Analyze the results and provide recommendations.
The research hypothesis posits that the energy efficiency level of buildings is determined by the consumption of final or primary energy. For regions with sharply continental climates, optimizing energy supply sources must not only account for potential energy savings but also ensure maximum comfort for residents under varying operating conditions.
3 Study area
3.1 Object of the test modelling
To investigate the energy characteristics of the building, an energy model of a typical two-room apartment of modern economy-class construction in Ukraine was created using the MATLAB/Simscape software.
The two-room apartment is located on the fourth floor of a five-story residential building constructed in 2016. The total area of the apartment premises is 49.44 square meters, with a ceiling height of 2.7 m (see Figure 1). The apartment’s windows are oriented towards the east (E) and west (W) sides of the world, as well as a solid outer wall facing north (N). The fenestration elements are made of double-chamber energy-saving insulated glass units with argon filling. The load-bearing part of the external walls is made of red hollow bricks measuring 0.4 m, with insulation of 0.05 m of mineral wool. The ventilation is natural with an air exchange rate of 0.6 h−1. Hourly climatic data from a typical year of the International Weather for Energy Calculation (IWEC) weather file (International weather for energy calculations, 2024) were used in the study (see Figure 2).
3.2 General features of the model
To investigate the energy characteristics of the building, an energy model of a typical two-room apartment of modern economy-class construction was created based on the MATLAB/Simscape software product. The dynamic model in the MATLAB environment was created using subsystems of Simulink tools, which in turn utilize Simscape. With Simscape, which allows for the rapid creation of models of physical systems within the Simulink environment, a model of physical components based on physical connections was developed, directly integrated with modeling block diagrams. The MATLAB software environment enables the design of control systems taking into account the physical system in Simulink. The software product considers the inertial characteristics of enclosures and building systems, as well as the dynamics of climate data variability. At the output, the software product provides the ability to obtain air temperature, radiation temperature of surfaces, loads on the heating/cooling and ventilation (HVAC) system, and more (Lu et al., 2021).
In Figure 3, the energy supply scheme of the apartment (Figure 3A) and the interconnection of rooms/zones of the apartment (Figure 3B) in Simulink are shown. The specific settings of the building’s heating system are presented in Lu et al. (2021).
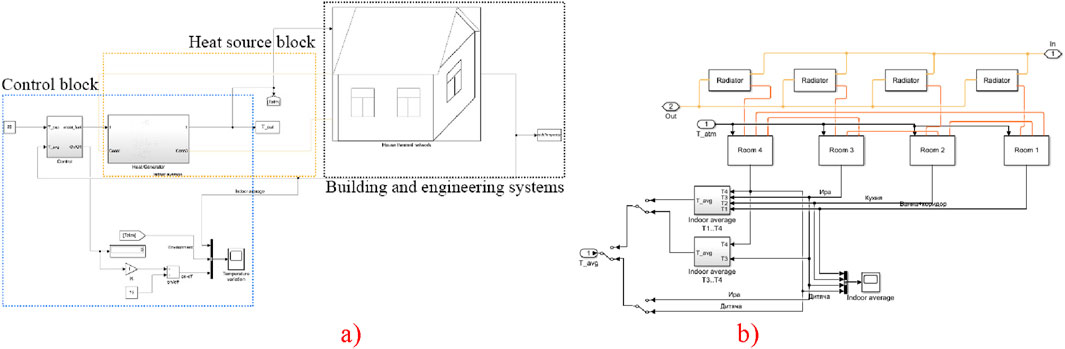
Figure 3. Block diagram of the apartment heating system model and thermal connections between building zones (A) the energy supply scheme of the apartment; (B) the interconnection of rooms/zones of the apartment.
3.3 A model of an alternative heating system for the building using a heat pump
The development of the model was carried out under the following simplifications:
• It is assumed that the expansion of the working fluid in the expansion valve is isenthalpic;
• The mass flow rate of the working fluid is constant in all components of the heat pump;
• The mass of the working fluid in the condenser and evaporator remains constant during the transient process;
• The temperatures of the heat carriers of the low-potential heat source and the heat consumer change linearly;
• Pressure losses in the components are insignificant and can be neglected;
• Superheating of the working fluid vapor in the evaporator is absent;
• Supercooling of the working fluid condensate in the condenser is absent.
The energy balance equation of the working fluid in the condenser:
where:
The energy balance equation for the water heated in the condenser:
where:
The energy balance equation for the working fluid in the evaporator:
where the same parameters apply to the evaporator respectively.
The energy balance equation for the air being cooled in the evaporator:
where the same parameters apply to the evaporator respectively.
The heat transfer coefficient of the air evaporator (finned heat exchanger) was determined in relation to its external surface. The heat transfer in the air-side evaporator, modeled using Equation 5, quantifies the relationship between the heat transfer coefficient and the external surface of the finned heat exchanger.
where:
For the condenser, a plate heat exchanger is provided, where the heat transfer coefficient is determined by the formula. Equation 6 is applied to define the heat transfer coefficient in the plate heat exchanger of the condenser, incorporating thermal conductivity, plate thickness, and heat transfer areas.
where:
The values of the heat transfer coefficients of the working fluid in the evaporator and condenser were taken according to the recommendations provided in Zhang et al. (2019), Longo (2008), Kedzierski et al. (2015), Shafiq et al. (2023), Posew et al. (2009).
The flow rate of the working fluid in the heat pump was determined from the dependency:
where:
ρCM,in, density of the working fluid at the compressor inlet, kg/m3
It is assumed that there is no transient process in the compressor. Then the energy balance of this component will take the form Kinab et al. (2010), Sanaye et al. (2013). The energy dynamics of the compressor are governed by Equation 8, which models the energy balance through specific enthalpy changes across the compressor.
where:
where:
Equation 9 further refines the energy balance by introducing the relationship between isentropic efficiency and specific enthalpy changes. The volumetric (
Equation 11 integrates volumetric and isentropic efficiencies, establishing a combined framework for evaluating the compressor's overall energy conversion efficiency.
where:
The assumption of constant enthalpy expansion in the expansion valve is captured by Equation 12, simplifying the analysis of thermodynamic behavior in the valve’s operation. The expansion valve is calculated at constant enthalpy:
where:
The thermophysical properties of the working fluids used in the investigated heat pump were determined using the Coolprop program (Deshko et al., 2021c).
The structural diagram of the dynamic model of the investigated heat pump system, developed in the Simulink environment, is shown in Figure 4.
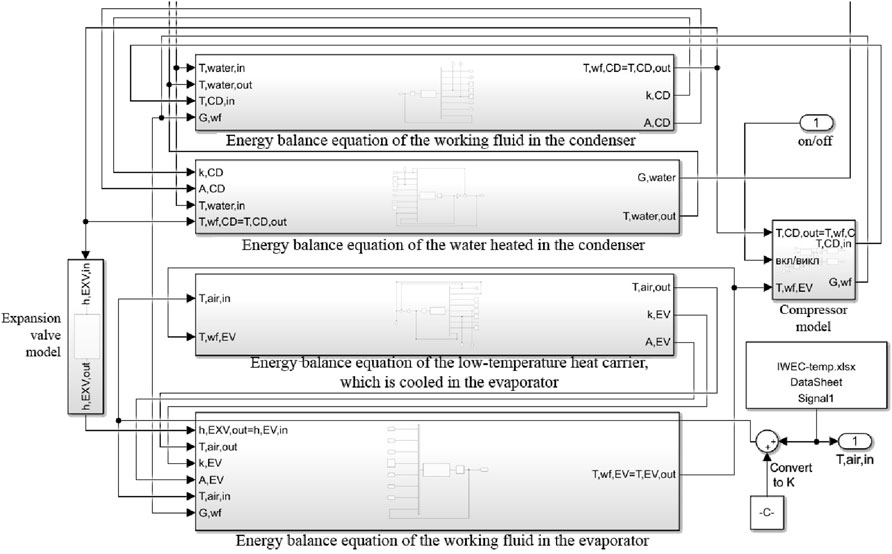
Figure 4. Structure of the dynamic model of exergetic analysis of the heat pump system in the Simulink environment.
This model can be represented as consisting of individual blocks, each of which represents separate models of such components: compressor, condenser, expansion valve, and evaporator. In the created dynamic models of each component of the investigated heat pump system, corresponding equations were used. The implementation of the developed model as a whole enables obtaining the dynamics of changes in a whole range of parameters (pressures, temperatures, flow rates, enthalpies, etc.) of the installation at characteristic points. Figures 5–9 provide a more detailed view of individual blocks of the developed dynamic model.
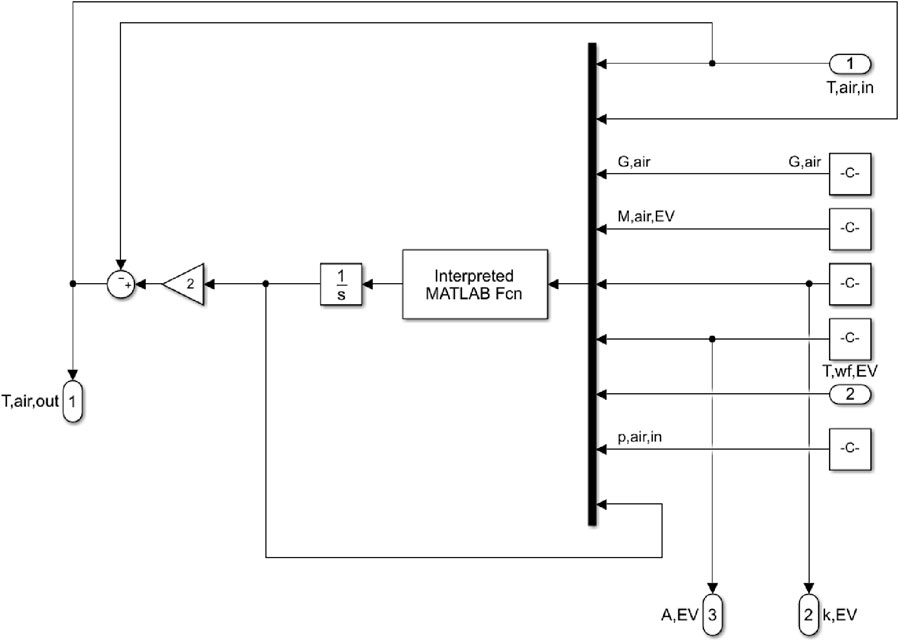
Figure 5. Block diagram for studying the dynamics of changes in coolant temperature in the evaporator.
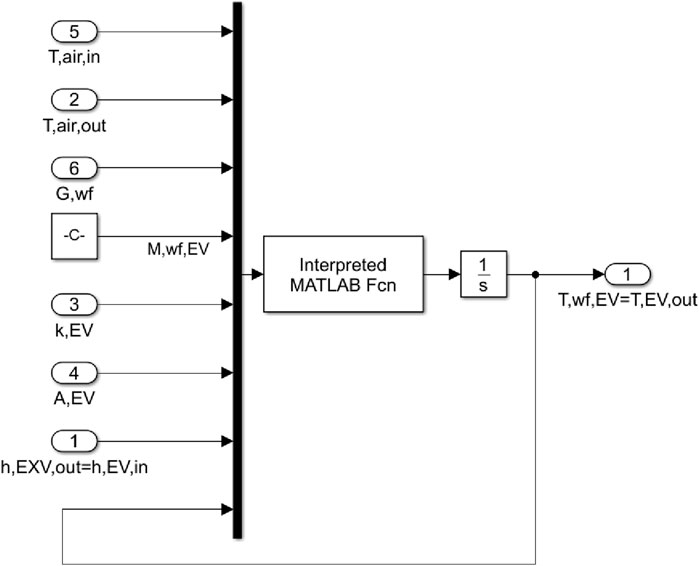
Figure 6. Block diagram of the model created in the Simulink environment for calculating the change in temperature of the working fluid evaporated in the evaporator.
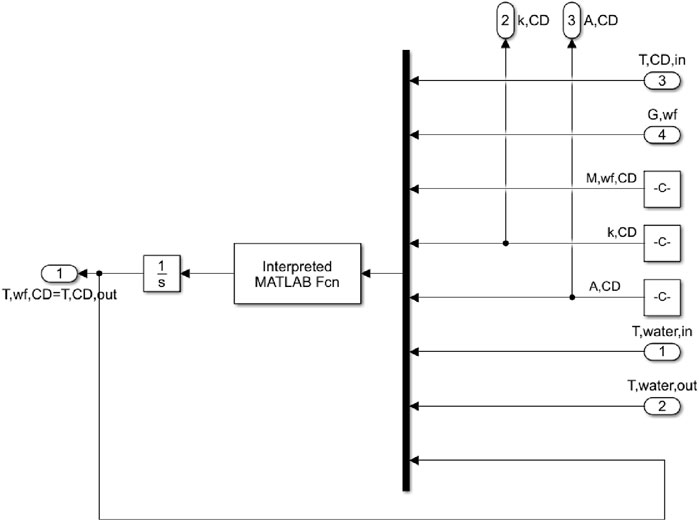
Figure 8. Block diagram of the model created in the Simulink environment for calculating the dynamics of the temperature of the working fluid condensing in the condenser.
The Simulink model developed for studying the dynamics of the temperature change of the low-temperature heat source, cooled in the evaporator, has the structure shown in Figure 5.
According to Equation 4, this model calculates the temperature of the low-temperature heat carrier at the outlet of the evaporator (
• Flow rate of the low-temperature heat source – air (
•Temperature of the low-temperature heat carrier at the inlet of the evaporator (
•Heat transfer coefficient in the evaporator (
•Heat transfer area in the evaporator region (
•Temperature of the working fluid in the evaporator region (
•Pressure of the low-temperature heat source at the inlet of the evaporator (
The enthalpies of air at the inlet and outlet of the evaporator
Developed in the Simulink environment, the dynamic model for investigating the dynamics of the working fluid temperature change evaporated in the evaporator is presented in Figure 6. According to Equation 3, this model calculates the temperature of the working fluid in the evaporator area (
•Working fluid flow rate through the evaporator (
•Enthalpy of the working fluid at the inlet of the evaporator, which is equal to the enthalpy of the working fluid at the outlet of the expansion valve (
•Heat transfer coefficient in the evaporator area (
•Heat transfer area in the evaporator area (
•Air temperature at the inlet of the evaporator (
•Air temperature at the outlet of the evaporator (
•Mass of the working fluid in the evaporator area (
The enthalpies of the working fluid at the outlet of the evaporator
The structural diagram of the dynamic compressor model is shown in Figure 7. This model allows modeling two compressor parameters:
•The temperature of the working fluid at the outlet of the compressor, which is equal to the temperature of the working fluid at the inlet of the condenser (
•The flow rate of the working fluid through the compressor and, consequently, through other components of the HVAC system (
To determine the temperature at the outlet of the compressor (
•The temperature of the working fluid evaporated in the evaporator and then supplied to the compressor (
•The pressure of the working fluid at the outlet of the compressor (
To determine the flow rate of the working fluid (
A dynamic model developed in the Simulink environment for calculating the temperature dynamics of the working fluid condensing in the condenser is presented in Figure 8. According to Equation 1, this model calculates the temperature of the working fluid in the condenser region (the boiling temperature
•Working fluid flow rate through the condenser (
•Temperature of the working fluid at the inlet of the condenser (
•Heat transfer coefficient in the condenser region (
•Heat transfer area in the condenser region (
•Temperatures of the water at the inlet and outlet of the condenser, respectively (
•The mass of the working fluid in the condenser region (
The enthalpies of the working fluid at the inlet and outlet of the condenser
Developed in the Simulink environment, the dynamic model for investigating the dynamics of water temperature change at the outlet of the condenser has the structure depicted in Figure 9. In this case, Equation 2 was used, which is coded in the m-file and embedded in the Interpreted MATLAB Function block. The input parameters used to solve the equation are as follows:
•Water flow rate through the condenser (
•Water temperature at the inlet and outlet of the condenser (
•Heat transfer coefficient in the condenser (
•Heat transfer area in the condenser region (
•Working fluid temperature in the condenser region (
•Water pressure at the inlet of the condenser (
•Water mass in the condenser region (
The enthalpies of water at the inlet and outlet of the condenser,
4 Engineering calculations
An individual gas-fired boiler and an air-to-water heat exchanger were chosen to compare different sources of heat supply for the building. The room air temperature control is based on the averaged values of rooms 3 and 4 (living rooms). The controller is set to maintain the temperature within the range of 19.5°C–20°C. Justification of the installation location and the number of temperature control sensors is provided in Energy Efficiency of Buildings (2022). The heat carrier flow rate in the heating system circuit for both considered heating source options is the same and amounts to 0.998 kg/s.
For the design conditions, the selection of heating devices was carried out based on a mathematical model created in the MATLAB software environment, taking into account the type of heating devices, their area, mass, and thermal inertia characteristics. Under the design conditions the outside air temperature of −22°C was assumed with no solar heat gains. The indoor air temperature is set at 20°C. It was determined that the power of the heating devices in the rooms of the apartment is as follows: bedroom 1/room 4 – 500 W, bedroom 2/room 3 – 1,200 W, kitchen/room 2 – 880 W, common areas (corridor, bathroom)/room 1—320 W.
To verify the mathematical model of the apartment created in the MATLAB software environment, a comparison was conducted using the quasi-steady-state method. The test results are provided in Deshko et al. (2021c). Validation of the apartment model was performed in accordance with DSTU 9190:2022 (Energy Efficiency of Buildings, 2022), the national standard of Ukraine for assessing building energy efficiency and certification. The quasi-steady-state model, based on DSTU 9190:2022, treats the apartment as a single zone and accounts for the thermal storage properties of only the external envelope. In contrast, the dynamic model created in MATLAB incorporates the thermal storage properties of both internal and external enclosures individually.
From an annual perspective, the difference between the simulation results using constant air temperature in the apartment for the two models is 13% during the heating period (October–April). The dynamic model created in MATLAB was selected as the reference due to its higher accuracy. A larger discrepancy was observed during the shoulder seasons (October and April), with differences around 30 kWh, while for colder months, the differences ranged from 80 to 140 kWh.
Additionally, to verify the mathematical model of the apartment created in the MATLAB software environment, a comparison was made with simulation results obtained using the EnergyPlus software environment (EnergyPlus energy simulation software official website, 2024). Both MATLAB and EnergyPlus grid dynamic models consider the thermal inertia properties of each building enclosure separately. EnergyPlus is a specialized software product widely used for energy efficiency modeling and design purposes. However, it does not account for hydraulic operating modes of water heating systems, such as system contamination or imbalance, which are typical issues for existing buildings in Ukraine and several post-Soviet countries. In the building model created in EnergyPlus, similar to the MATLAB model, thermophysical properties of the building envelope, hourly climatic variations, temperature regimes in building zones, heating device types, and energy supply sources were specified. The calculations are based on dynamic energy balances for each considered zone, taking into account heat transfer between apartment zones. A comparison of the capabilities of MATLAB and EnergyPlus is presented in Table 1.
In real practice, the control of maintaining the specified air temperature in the apartment can be carried out by the values of the air temperature in representative rooms; for a compact typical housing, it is 1-2 points of installation of air temperature control sensors, according to the readings of which the controller sends a signal to the boiler to turn it ON/OFF. Typically, the sensors are installed in the rooms where the residents are spending most of their time, i.e., in the bedrooms or living room. This study looks at four different options for installing temperature sensors, specifically: 1) average reading from two sensors in room4 and room 3, respectively; 2) in room 4; 3) in room 3; 4) average reading from four sensors in each room, respectively. The results of the model calculation are shown in Figure 10.
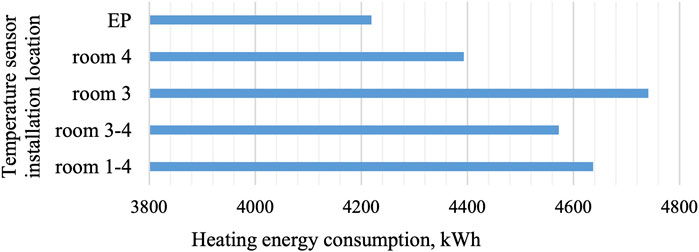
Figure 10. Heat energy consumption for apartment space heating (Lu et al., 2021). Room 1–4, air temperature control sensor installed in rooms 1–4; room 3–4, sensor in rooms 3–4; room 3, sensor in room 3; room 4, sensor in room 3–4; EP, simulation in EnergyPlus software.
From Figure 10 it follows that with the quantitative regulation of heating and the absence of inertia in the heating devices according to the mathematical model created in EnergyPlus software environment, we have the lowest result of heat consumption for heating needs of the building. For the conditions of Ukraine, it is typical to use ON/OFF controllers for autonomous heating systems, so depending on the number and location of temperature control sensors, the temperature in the premises may vary ± 3% (Lu et al., 2021). Research Lu et al. (2021) suggests that with quantitative regulation of heating and the absence of inertia in heating devices according to the mathematical model created in the EnergyPlus software environment, we have the lowest heat consumption result for heating the building. The deviation of the simulation results in MATLAB compared to those in EnergyPlus is 4%–10%, depending on the heating month (Lu et al., 2021). Model verification was carried out in the case of using an autonomous gas boiler. Under these control conditions, the average load on the gas boiler is: sensors in all rooms – 1,073 W; in rooms 3 and 4 – 1,058 W; in room 3 – 1,100 W; in room 4 – 1,010 W; in EnergyPlus – 965 W. (Lu et al., 2021).
The comfortable indoor air temperature of 20°C is set so that the heating power of the heating devices in the apartment rooms is as follows: bedroom 1/room 4 – 500 W, bedroom 2/room 3 – 1,200 W, kitchen/room 2 – 880 W, common areas (corridor, bath)/room 1 – 320 W. (Lu et al., 2021).
The study evaluates the use of a heat pump as an alternative to using a gas boiler for heating a multi-story apartment building.
The heat pump has more flexible regulation, and the load level on the heating system depends on the required amount of thermal energy at a given moment. The use of a heat pump allows reducing the instantaneous power value to 40%, but the frequency of pump activation is significantly higher (about 4 times).
Figure 11 shows the monthly energy consumption for heating purposes. As it is seen, the amount of thermal energy produced by monthly a heat pump and a gas boiler is almost the same.
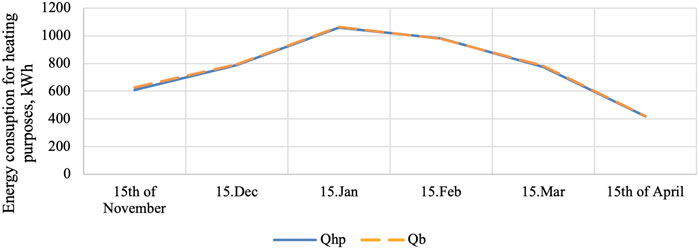
Figure 11. Monthly energy consumption of the heating system. Qhp, the amount of consumed thermal energy produced by the heat pump; Qb, the same, gas boiler.
Significant fluctuations in room air temperature are observed at the beginning and end of the heating season, which can be attributed to high solar activity during daytime hours in the transitional periods between seasons, leading to heating system shutdown. Due to passive heating (sunlight), the room air temperature temporarily reaches up to 23°C. Figure 12 shows the average monthly air temperatures in representative rooms for two different heating sources.
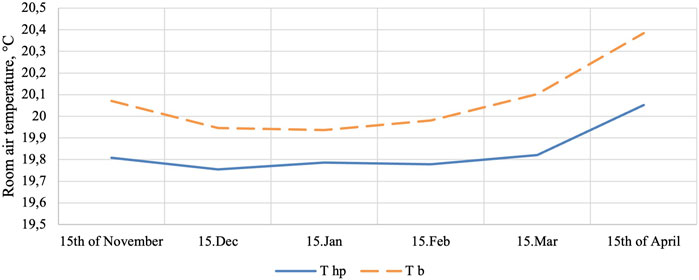
Figure 12. Average monthly indoor air temperature provided by different heating sources. Тhp, indoor air temperature maintained by the heat pump; Tb, the same, gas boiler.
As it is seen, with the same amount of energy produced by heat sources for heating purposes, the heat pump better maintains the set level of air temperature in the room and prevents overheating.
Figure 13 shows the hourly average air temperature across all rooms in the apartment.
Due to different room occupancy schedules, heat flows between rooms and various orientations, different temperatures are observed across all rooms, and the average temperature fluctuation across all rooms exceeds the setpoint on the controller (19.5°C … 20°C), which should correspond to the temperature in representative rooms (bedrooms 1 and 2). In the cold period of the year (December–January), this discrepancy is smaller, with an average deviation of about 0.2°C, while for the transitional period (October, April), it is around 0.4°C.
5 Discussion
Improving energy efficiency while simultaneously enhancing comfortable climatic conditions for living and working in buildings is a multifaceted problem without a straightforward solution. Increased comfort often necessitates higher energy or material consumption, leading to additional economic costs and potentially higher overall emissions of pollutants, considering all stages of energy and material production and use.
Dynamic modeling has proven to be one of the most effective tools for addressing this challenge. By simulating the dynamic behavior of systems, it is possible to evaluate the advantages and disadvantages of specific systemic improvements in energy management, enabling mutually agreed improvements in energy efficiency and indoor climatic conditions. Unlike pre-defined libraries in most developed software products, which limit the analysis of structural components of energy sources in transient modes, this study developed an energy-dynamic model implemented in the MATLAB/Simscape software environment. This model allows for detailed analysis of components for different energy supply sources.
The results of this research are demonstrated using an energy-dynamic grid model of a typical residential building, verified against models created in commonly used software such as EnergyPlus. The deviation in energy consumption using the quasi-steady-state method did not exceed 13%, while comparisons with the dynamic model created in EnergyPlus showed deviations of about 5%. Validation was performed using an autonomous gas boiler, where the average load under control conditions ranged between 965 W and 1,100 W depending on the location and number of air temperature control sensors. For compact residential spaces, temperature regulation is typically achieved using 1–2 sensors placed in representative rooms. However, variations of ±3% in indoor temperature may occur depending on the placement of these sensors, which reflects common practices in Ukraine for autonomous heating systems with ON/OFF controllers.
This study explored the use of gas boilers and heat pumps as the most common sources for individual energy supply systems in buildings. Over an annual period, both systems demonstrated similar energy needs, with specific energy consumption for heating ranging from 8 kWh/m2 during the shoulder season to 25 kWh/m2 in the coldest month (January). However, the heat pump demonstrated superior flexibility in adjusting system load levels to account for variable internal and external conditions. While a heat pump can reduce instantaneous power by up to 40%, its switching frequency is approximately four times higher than that of a gas boiler. The dynamic modeling approach employed in this study facilitated a comprehensive evaluation of energy processes in the building, particularly the ability of different energy supply sources to maintain comfortable indoor air temperatures under varying conditions. Notably, for the same energy output, the heat pump system was better at maintaining the set indoor air temperature and avoiding overheating.
6 Weak points
One notable limitation of the dynamic modeling approach in MATLAB/Simulink is the computational speed when scaling up the heat pump model. The simulation of a typical year for a single apartment required nearly 7 days to complete. This limitation highlights the need for further optimization of the model or integration of more efficient computational techniques, such as neural networks or artificial intelligence, to improve simulation time without compromising accuracy.
7 Conclusion
The results of this study underline the practical value of dynamic modeling for assessing the energy consumption and indoor temperature characteristics of residential buildings. The developed MATLAB/Simscape energy-dynamic model provides a valuable tool for analyzing the performance of various energy supply sources and automation systems under real-world conditions.
It was shown that, despite similar annual energy consumption, heat pumps outperform gas boilers in maintaining consistent indoor air temperatures while offering more flexible load adjustments. These findings provide a basis for optimizing energy supply systems in buildings located in regions with sharply continental climates.
Future research will focus on accelerating calculations in MATLAB models by incorporating neural networks and artificial intelligence, which will enhance the applicability and efficiency of dynamic energy modeling.
Data availability statement
The original contributions presented in the study are included in the article/supplementary material, further inquiries can be directed to the corresponding authors.
Author contributions
IB: Conceptualization, Investigation, Writing–original draft, Writing–review and editing. DB: Writing–original draft, Writing–review and editing, Data curation, Methodology, Software. TE: Conceptualization, Methodology, Writing–original draft. ON: Conceptualization, Methodology, Writing–original draft. VV: Conceptualization, Methodology, Writing–original draft. AP: Funding acquisition, Writing–review and editing.
Funding
The author(s) declare financial support was received for the research, authorship, and/or publication of this article. This work was supported by NATO Science for Peace and Security Programme under grant number G6245.
Conflict of interest
The authors declare that the research was conducted in the absence of any commercial or financial relationships that could be construed as a potential conflict of interest.
Generative AI statement
The author(s) declare that no Generative AI was used in the creation of this manuscript.
Publisher’s note
All claims expressed in this article are solely those of the authors and do not necessarily represent those of their affiliated organizations, or those of the publisher, the editors and the reviewers. Any product that may be evaluated in this article, or claim that may be made by its manufacturer, is not guaranteed or endorsed by the publisher.
References
Afram, A., Fung, A. S., Janabi-Sharifi, F., and Raahemifar, K. (2018). Development and performance comparison of low-order black-box models for a residential HVAC system. J. Build. Eng. 15, 137–155. doi:10.1016/j.jobe.2017.11.021
Alibabaei, N., Fung, A. S., Raahemifar, K., and Moghimi, A. (2017). Effects of intelligent strategy planning models on residential HVAC system energy demand and cost during the heating and cooling seasons. Appl. Energy 185, 29–43. doi:10.1016/j.apenergy.2016.10.062
Artuso, P., Tosato, G., Rossetti, A., Marinetti, S., Hafner, A., Banasiak, K., et al. (2021). Dynamic modelling and validation of an air-to-water reversible R744 heat pump for high energy demand buildings. Energies 14, 8238. doi:10.3390/en14248238
Bae, Y., Bhattacharya, S., Cui, B., Lee, S., Li, Y., Zhang, L., et al. (2021). Sensor impacts on building and HVAC controls: a critical review for building energy performance. Adv. Appl. Energy 4, 100068. doi:10.1016/j.adapen.2021.100068
Borodinecs, A., Paļčikovskis, A., Krūmiņš, A., Zajecs, D., and Lebedeva, K. (2024a). Assessment of HVAC performance and savings in office buildings using data-driven method. Clean. Technol. 6, 802–813. doi:10.3390/cleantechnol6020041
Borodinecs, A., Paļčikovskis, A., Krūmiņš, A., and Lebedeva, K. (2024b). Optimizing office building operations: a framework for continuous dynamic energy simulations in decision-making for efficiency. Front. Built Environ. 10. doi:10.3389/fbuil.2024.1405182
Choi, J., Lee, D., Park, M. H., Lee, Y., and Kim, Y. (2021). Effects of compressor frequency and heat exchanger geometry on dynamic performance characteristics of heat pump dryers. Energy 235, 121391. doi:10.1016/j.energy.2021.121391
Cholewa, T., Balaras, C. A., Kurnitski, J., Siuta-Olcha, A., Dascalaki, E., Kosonen, R., et al. (2022). “Energy efficient renovation of existing buildings for HVAC professionals,” in REHVA guidebook No. 32. Federation of European heating, ventilation and air conditioning associations (REHVA).
Deshko, V., Bilous, I., Biriukov, D., and Yatsenko, O. (2021a). Transient energy models of housing facilities operation. Rocz. Ochr. Srodowiska 23, 539–551. doi:10.54740/ros.2021.038
Deshko, V., Bilous, I., Sukhodub, I., and Yatsenko, O. (2021b). Evaluation of energy use for heating in residential building under the influence of air exchange modes. J. Build. Eng. 42, 103020. doi:10.1016/j.jobe.2021.103020
Deshko, V., Bilous, I., and Biriukov, D. (2021c). Modeling of unsteady temperature regimes of autonomous heating systems. J. New Technol. Environ. Sci. 3, 91–99. doi:10.53412/jntes-2021-3-1
Deshko, V., Bilous, I., and Maksymenko, O. (2023). Impact of heating system local control on energy consumption in apartment buildings. Rocz. Ochr. Srodowiska 25, 77–85. doi:10.54740/ros.2023.009
Energy Efficiency of Buildings (2022). Method for calculating energy Consumption for heating, cooling, ventilation, lighting, and hot water supply, DSTU 9190:2022. Kyiv: State Research Institute of Building Сonstructions.
EnergyPlus energy simulation software official website (2024). Available at: https://energyplus.net/.
Garcia, J., Ali, T., Duarte, W. M., Khosravi, A., and Machado, L. (2018). Comparison of transient response of an evaporator model for water refrigeration system working with R1234yf as a drop-in replacement for R134a. Int. J. Refrig. 91, 211–222. doi:10.1016/j.ijrefrig.2018.04.026
Goyal, A., Staedter, M. A., and Garimella, S. (2019). A review of control methodologies for vapor compression and absorption heat pumps. Int. J. Refrig. 97, 1–20. doi:10.1016/j.ijrefrig.2018.08.026
Grald, E. W., and MacArthur, J. W. (1992). A moving-boundary formulation for modeling time-dependent two-phase flows. Int. J. Heat Fluid Flow 13, 266–272. doi:10.1016/0142-727X(92)90040-G
Han, D., Kalantari, M., and Rajabifard, A. (2024). The development of an integrated BIM-based visual demolition waste management planning system for sustainability-oriented decision-making. J. Environ. Manag. 351, 119856. doi:10.1016/j.jenvman.2023.119856
Hinkelman, K., Anbarasu, S., and Zuo, W. (2023). Exergy-based ecological network analysis for building and community energy systems. Energy Build. 303, 113807. doi:10.1016/j.enbuild.2023.113807
Husmann, R., and Aschemann, H. (2022). Dynamic modeling of a vapor compression cycle. IFAC-Papers Line 55, 523–528. doi:10.1016/j.ifacol.2022.09.148
International weather for energy calculations. (2024): Available at: https://Energyplus.Net/Weather-Location/Europe_wmo_region_6/UKR.
Jradi, M. (2020). Dynamic energy modelling as an alternative approach for reducing performance gaps in retrofitted schools in Denmark. Appl. Sci. 10, 7862. doi:10.3390/app10217862
Kedzierski, M. A., Brown, J. S., and Koo, J. (2015). Performance ranking of refrigerants with low global warming potential. Sci. Technol. Built Environ. 21, 207–219. doi:10.1080/10789669.2014.974479
Kinab, E., Marchio, D., Rivière, P., and Zoughaib, A. (2010). Reversible heat pump model for seasonal performance optimization. Energy Build. 42, 2269–2280. doi:10.1016/j.enbuild.2010.07.007
Kon, O., Yuksel, B., and Karaoglan, A. D. (2024). Modeling the relationship between outdoor meteorological data and energy consumptions at heating and cooling periods: application in a university building. Numer. Algebra, Control Optim. 14 (1), 59–79. doi:10.3934/naco.2022021
Kovalko, O., Eutukhova, T., and Novoseltsev, O. (2022). Energy-related services as a business: eco-transformation logic to support the low-carbon transition. Energy Eng. 119 (1), 103–121. doi:10.32604/EE.2022.017709
Li, W., Chu, Y., Xu, P., Yang, Z., Ji, Y., Ni, L., et al. (2017). A transient model for the thermal inertia of chilled-water systems during demand response. Energy Build. 150, 383–395. doi:10.1016/j.enbuild.2017.05.078
Longo, G. A. (2008). Refrigerant R134a condensation heat transfer and pressure drop inside a small brazed plate heat exchanger. Int. J. Refrig. 31, 780–789. doi:10.1016/j.ijrefrig.2007.11.017
Lu, G., Zhou, X., Yan, J., and Yan, G. (2021). A temperature and time-sharing dynamic control approach for space heating of buildings in district heating system. Energy 221, 119835. doi:10.1016/j.energy.2021.119835
Mateu-Royo, C., Navarro-Esbrí, J., Mota-Babiloni, A., Amat-Albuixech, M., and Molés, F. (2019). Thermodynamic analysis of low GWP alternatives to HFC-245fa in high-temperature heat pumps: HCFO-1224yd(Z), HCFO-1233zd(E) and HFO-1336mzz(Z). Appl. Therm. Eng. 152, 762–777. doi:10.1016/j.applthermaleng.2019.02.047
Mateu-Royo, C., Sawalha, S., Mota-Babiloni, A., and Navarro-Esbrí, J. (2020). High temperature heat pump integration into district heating network. Energy Convers. Manag. 210, 112719. doi:10.1016/j.enconman.2020.112719
Posew, K., Laohalertdecha, S., and Wongwises, S. (2009). Evaporation heat transfer enhancement of R-134a flowing inside smooth and micro-fin tubes using the electrohydrodynamic technique. Energy Convers. Manag. 50, 1851–1861. doi:10.1016/j.enconman.2009.02.003
Sanama, C., and Xia, X. (2021). Transient state modelling and experimental investigation of the thermal behavior of a vapor compression system. Math. Problems Eng. 2021, 1–14. doi:10.1155/2021/9941451
Sanaye, S., Chahartaghi, M., and Asgari, H. (2013). Dynamic modeling of gas engine driven heat pump system in cooling mode. Energy 55, 195–208. doi:10.1016/j.energy.2013.03.074
Sangi, R., Jahangiri, P., and Müller, D. (2019). A combined moving boundary and discretized approach for dynamic modeling and simulation of geothermal heat pump systems. Therm. Sci. Eng. Prog. 9, 215–234. doi:10.1016/j.tsep.2018.11.015
Shafiq, Q. N., Liaw, J. S., and Wang, C. C. (2023). A comprehensive review on the nucleate/convective boiling of low-GWP refrigerants: alternatives to HFC refrigerants. Processes 11, 468. doi:10.3390/pr11020468
Voloshchuk, V. A., Nekrashevych, O. V., Bohza, M. S., and Hikalo, P. V. (2023). Dynamic characteristics of an air-source heat-pump system. Sci. notes Taurida Natl. V.I. Vernadsky Univ. Ser. Tech. Sci. 2, 36–44. doi:10.32782/2663-5941/2023.3.2/07
Yao, Y., Huang, M., and Chen, J. (2013). State-space model for dynamic behavior of vapor compression liquid chiller. Inter. J. Refrig. 36, 2128–2147. doi:10.1016/j.ijrefrig.2013.05.006
Yao, Y., Wang, W., and Huang, M. (2015). A state-space dynamic model for vapor compression refrigeration system based on moving-boundary formulation. Int. J. Refrig. 60, 174–189. doi:10.1016/j.ijrefrig.2015.07.027
Zaporozhets, A., Babak, V., Kostenko, G., Sverdlova, A., Dekusha, O., and Kornienko, S. (2023). Some features of air pollution monitoring as a component of the microclimate of the premises. Syst. Res. Energy 4 (75), 65–73. doi:10.15407/srenergy2023.04.065
Zhang, J., Kærn, M. R., Ommen, T., Elmegaard, B., and Haglind, F. (2019). Condensation heat transfer and pressure drop characteristics of R134a, R1234ze(E), R245fa and R1233zd(E) in a plate heat exchanger. Int. J. Heat Mass Transf. 128, 136–149. doi:10.1016/j.ijheatmasstransfer.2018.08.124
Nomenclature
Subscripts and superscripts
air air
CD condenser
CM compressor
EV evaporator
is isentropic
in inlet
out outlet
vol volumetric
s displacement
w plate
water water
wf working fluid
Greek symbols
Keywords: energy modeling, building, energy supply system, energy efficiency, comfortable temperature
Citation: Bilous I, Biriukov D, Eutukhova T, Novoseltsev O, Voloshchuk V and Prozuments A (2025) Energy efficiency and indoor climatic conditions in buildings: dynamic modeling for systemic improvement. Front. Built Environ. 10:1502794. doi: 10.3389/fbuil.2024.1502794
Received: 27 September 2024; Accepted: 30 December 2024;
Published: 29 January 2025.
Edited by:
Gabriele Lobaccaro, Norwegian University of Science and Technology, NorwayReviewed by:
Giovanni Ciampi, Università degli Studi della Campania Luigi Vanvitelli, ItalyTomasz Cholewa, Lublin University of Technology, Poland
Copyright © 2025 Bilous, Biriukov, Eutukhova, Novoseltsev, Voloshchuk and Prozuments. This is an open-access article distributed under the terms of the Creative Commons Attribution License (CC BY). The use, distribution or reproduction in other forums is permitted, provided the original author(s) and the copyright owner(s) are credited and that the original publication in this journal is cited, in accordance with accepted academic practice. No use, distribution or reproduction is permitted which does not comply with these terms.
*Correspondence: Oleksandr Novoseltsev, YW5vdm9zNzczQHVrci5uZXQ=