- 1Vel Tech Rangarajan Sagunthala R&D Institute of Science and Technology, Chennai, Tamil Nadu, India
- 2Department of Biosciences, Saveetha School of Engineering, Saveetha Institute of Medical and Technical Sciences, Chennai, India
- 3Gazi University Faculty of Engineering, Department of Mechanical Engineering, Ankara, Türkiye
- 4Department of Machining, Assembly and Engineering Metrology, Faculty of Mechanical Engineering, VSB-Technical University of Ostrava, Ostrava, Czechia
Recent advancements in concrete technology focus more on increasing strength than durability. Concrete with good durability will withstand adverse conditions like frost, chloride penetration, sulfate assault, alkali-aggregate reaction, steel corrosion, etc., which will lower the strength of the concrete. Strength is vital, but so is durability. The present study examined and discussed the durability parameters of conventional concrete made with geopolymer aggregate (GPA) as a partial substitute for natural aggregate. Strength studies in this research found that the optimal level of substitution for natural coarse aggregate by GPA was 100% replacement to produce the performing concrete. Replacement of natural coarse aggregate by geopolymer aggregate exhibits 9%–15% higher compressive strength than natural aggregate concrete. The findings reveal that concrete with 100% geopolymer aggregate exhibits a compressive strength increase of 9%–15% over that of concrete made with natural aggregates. Ultrasonic pulse velocity measurements for geopolymer aggregate concrete range between 4 km/s and 4.5 km/s, indicating good quality according to IS specifications. Additionally, Rebound Hammer test results further support the enhanced quality of geopolymer aggregate concrete. However, the porosity of geopolymer aggregates results in a sorptivity that is 10%–30% higher than that of natural aggregate concrete. Despite this, the increased resistance to acid and sulfate attacks is noted, attributed to the strong bonding between geopolymer aggregates and the cement matrix.
1 Introduction
The search for durable and sustainable construction materials has been key to architectural and engineering progress. For over a century, traditional concrete made from Portland cement, water, and natural aggregates has been the foundation of modern construction. Its widespread use shows its versatility and strength, crucial for supporting various structures in our built environment. However, as the construction industry faces a growing need for sustainability and resilience, the limitations of conventional concrete have become more evident. Traditional concrete faces significant challenges, primarily related to its environmental impact and durability. The production of Portland cement, a major component of traditional concrete, is responsible for approximately 8% of global CO2 emissions (Seneviratne et al., 2021). This carbon footprint, coupled with the material’s vulnerability to severe conditions such as acid and sulfate attacks, underscores the urgent need for more sustainable and robust alternatives (Gunasekara et al., 2018). As infrastructure ages and extreme weather events become more frequent, the quest for construction materials that can withstand these stresses while minimizing environmental harm has gained momentum. The evolution of construction materials has been a cornerstone of advancing infrastructure and architecture throughout history (Seneviratne et al., 2021). Traditional concretes, despite their widespread use and benefits, present significant limitations, particularly concerning environmental impact and durability under severe conditions. The production of conventional Portland cement, a primary component of traditional concrete, is responsible for a substantial portion of global carbon dioxide emissions. Additionally, traditional concretes often struggle to maintain their integrity in harsh environments, leading to increased maintenance costs and reduced structural longevity (Mesgari et al., 2023).
To address these challenges, the field of materials science has seen a growing interest in alternative materials, notably geopolymers. Geopolymers are inorganic polymers that form long-range, covalently bonded, non-crystalline networks. These materials, which can be synthesized from industrial by-products such as slag, fly ash, and other aluminosilicate materials, offer a promising solution due to their lower carbon footprint and superior durability characteristics. Landmark studies have significantly shaped the current understanding of geopolymers. Subsequent research by researchers demonstrated the enhanced mechanical properties and chemical resistance of geopolymer materials (Seneviratne et al., 2022). More recent studies have focused on optimizing the formulation and curing processes of geopolymers to further improve their performance and applicability in construction. Despite these advancements, there remain gaps in the comprehensive understanding and application of geopolymers, particularly in their use as aggregate materials for non-destructive testing (NDT) in construction (Thomas et al., 2022; Poloju and Sinivasu, 2021). This study aims to bridge these gaps by exploring the potential of geopolymer slag aggregates in NDT applications. By leveraging the unique properties of geopolymers, this research seeks to enhance the sustainability and resilience of construction materials, paving the way for more environmentally friendly and robust infrastructure solutions.
Based on existing research and laboratory experience, it is observed that the amount of conventional coarse aggregate is less than the production of lightweight aggregate. When considering potential environmental pollution due to the collection of waste byproducts, slag, and fly ash, which influence environmental degradation associated with conventional coarse aggregate quarrying, the increase in lightweight aggregate cost becomes insignificant. Through the widespread use of GGBS, a country can enhance its international ‘Carbon Credits,’ a notable achievement with invaluable environmental benefits (Guides, 2019). The production of geopolymer aggregates (Geopolymer aggregate) involves a specific procedure. The primary raw material for GPA synthesis is GGBS, which is the foundational agglomeration component. This agglomeration process is achieved by combining GGBS with an alkaline solution, including sodium silicate and sodium hydroxide. These dry components, encompassing GGBS and the alkaline solution, undergo thorough mixing using a mortar mixer to ensure an even distribution of the constituents throughout the mixture. Manufactured Geopolymer stones made of slag and alkaline solution were crushed 3 days after casting and sieved into different sizes under oven curing conditions, as shown in Figure 1. In light of the significant environmental disturbances caused by excavating aggregates, there is an urgent need to minimize the reliance on excavated aggregates. Consequently, the quest for a replacement for traditional aggregates becomes essential. Geopolymer demonstrates exceptional binding properties, making it a promising avenue for investigating alternatives to conventional aggregates. The purpose of using geopolymer aggregate in concrete is to give comparable properties with conventional concrete and also eliminate the problem of GGBS disposal. The main reasons for research are to prepare geopolymer aggregates using the geopolymer technique and to find mechanical, nondestructive testing and durability properties of artificial geopolymer coarse aggregate concrete.
2 Materials and experimental investigation
Conventional concrete utilizes crushed blue granite stone as coarse aggregate. This section elaborates on using a novel geopolymer artificial coarse aggregate (GPA) in geopolymer artificial coarse aggregate concrete. It concisely overviews the mix proportions, alkaline solutions preparation, and geopolymer coarse aggregate production process. GPA’s physical and mechanical properties are also presented alongside those of traditional aggregate. Due to limited knowledge of geopolymer pastes and mortars and the absence of codal provisions, a trial and error approach was employed to obtain the most economical GPA capable of replacing conventional aggregate (Gunasekara et al., 2017; Gunasekera et al., 2017).
The primary objectives of the initial laboratory work are to familiarize with the production of slag-based geopolymer concrete mix and understand the fundamental mixture proportioning of geopolymer aggregate concrete mix. Drawing from previous research on geopolymer concrete, the following ranges were chosen for components of geopolymer aggregate concrete mixtures (Almadani et al., 2022). The optimum ratio of alkaline solution, which consists of sodium silicate and sodium hydroxide by mass, falls within the range of 0.4–2.5, according to prior studies. This ratio was standardized at 0.5 for all mixes in this research, primarily because the sodium silicate solution is more cost-effective than sodium hydroxide. Molarity of sodium hydroxide (NaOH) solution, which ranges from 8 M to 16 M, was considered. To achieve the required molarity of NaOH (e.g., 8 M), it is necessary to take 8 × 40 = 320 g of NaOH pellets and dilute them in water to obtain 1 L of 8 M NaOH solution. The ratio of alkaline activator solution to slag, by mass, is varied to 0.3, 0.35, and 0.4. The amount of additional water needed is determined by implementing standard slump and compaction factor tests. A consistent slump value of 90–120 mm and a compaction factor of 0.9 is maintained throughout the study. In Ordinary Portland Cement (OPC), mixed water undergoes a chemical reaction, binding aggregates. Conversely, in geopolymer concrete containing GGBS, no such chemical reaction occurs. Additionally, a chemical reaction in geopolymer concrete generates water expelled from the binder.
Water content in geopolymer concrete plays a crucial role in fresh and hardened concrete, as laboratory experience shows (Almadani et al., 2022). Tests were performed to examine the properties of GPA and GPAC in order to compare with conventional coarse aggregate and normal concrete, respectively. Various test programs used in this work are explained below.
2.1 Cement
In the present work, OPC 53 grade cement. The physical properties of cement mentioned in Table 1 were evaluated as per IS 4031–1988.
2.2 Ground granulated blast furnace slag
JSW Steel in Andhra Pradesh provided GGBS, which was employed in this study. Physical attributes of GGBS were assessed in compliance with IS: 12,089 standards as listed in Table 2.
2.3 Fine aggregate
The experimental work used a locally obtained M-sand passing through a 4.75 mm sieve. The grading curve for conventional fine aggregate is shown in Figure 2. Table 3 shows the properties of fine aggregate assessed using IS: 2,386–1963.
Properties of fine aggregate were evaluated according to requirements outlined in IS: 2,386–1963, shown in Table 3.
2.4 Coarse aggregate
The following tests were used to determine the properties of conventional coarse aggregate and GPA, as shown in Table 4.
As shown in Table 5, a mixed design was prepared to analyze the mechanical and durability properties between geopolymer aggregate concrete and conventional concrete. A W/C ratio of 0.45 is maintained evenly in all concrete mixtures.
2.5 Tests for concrete
2.5.1 Compressive strength of concrete
The compressive strength of concrete plays a vital role in mechanical strength properties to identify its design strength. A civil engineering structure’s performance depends on concrete compressive strength. Concrete compressive strength is highly important in building structures (Joseph and Mathew, 2023). The strength of concrete can be determined by concrete grade, grading size of aggregate, shape, surface texture, water-cement ratio, and dosage of superplasticizer characteristics (Chindaprasirt et al., 2017). In the current research, M25 grade concrete was prepared for the cube of dimensions 150 mm × 150 mm × 150 mm, cured for 28 days at room temperature, and tested for its compressive strength. Following IS: 516–1959 norms, a compressive strength test was carried out.
2.5.2 Stress-strain relationship
As per IS 516: 1959, the stress-strain relationship between ordinary concrete and GPA concrete was determined at 28 days of curing. The dimensions of the cylinder specimen used for this test are 150 mm in diameter and 300 mm in height. Cube strength test gives realistic concrete strength properties when compared with split tensile strength of concrete. The cylinder is less affected by end restraints by the platen. Cylinder gives more uniform results than concrete cube strength. Cylinder gives appropriate test results to identify the stress-strain relationship of concrete. Structural member load direction simulates cylinder condition. Three cylinders were cast for every concrete mix. Stress-strain relationships and a schematic diagram of the specimen are shown in Figures 3, 4, respectively. According to ASTM C469, the modulus of elasticity of concrete can be calculated (Demir et al., 2001).
2.5.3 Ultrasonic pulse velocity test
Ultrasonic pulse velocity test can be conducted according to IS 13311 (Part I): 1992 specifications. An electro-acoustical transducer generates an ultrasonic pulse that undergoes multiple reflections within the concrete. The transducer detects the fastest longitudinal waves, which helps to determine homogeneity, cracks, voids’ presence, and overall concrete quality (Hart et al., 2005). The formula for ultrasonic pulse velocity is provided below. Interpretation of test results is shown in Table 6 below. Ultrasonic pulse velocity (V) = Path length (L)/Transit time (T). Ultrasonic Pulse Velocity (UPV) test is an effective method for assessing the integrity of concrete, including geopolymer aggregate concrete, by measuring the speed at which ultrasonic sound waves travel through the material. The test operates by emitting high-frequency ultrasonic pulses into the concrete using a transducer and then detecting the waves with a receiver transducer positioned on the opposite side. The time taken for these pulses to traverse the concrete is recorded, and the resulting pulse velocity provides insights into the material’s quality. A higher pulse velocity generally indicates that the concrete is dense, well-bonded, and free of significant internal defects such as cracks or voids, which disrupt the wave’s speed. For geopolymer aggregate concrete, which differs in composition and properties from traditional concrete, the UPV test helps verify that the material has been properly mixed and cured, ensuring it meets the required standards of strength and durability. Additionally, the UPV test can detect variations in pulse velocity, which might reveal inconsistencies in curing or internal defects. Importantly, the non-destructive nature of the UPV test allows for the assessment of concrete integrity without damaging the structure, making it an invaluable tool for evaluating the performance and longevity of geopolymer aggregate concrete structures.
2.5.4 Rebound hammer test
Rebound hammer test (RH) is performed according to IS 13311 (Part I): 1992. This test determines the compressive strength of concrete using rebound numbers and assesses the uniformity and quality of concrete (Kim and Lee, 2011). It can be used to compare the quality of one concrete element with another. The Rebound Hammer Test (RH) is a useful method for assessing the integrity of geopolymer aggregate concrete by measuring surface hardness, which is indirectly related to the material’s compressive strength. In this test, a spring-loaded hammer strikes the concrete surface, and the distance it rebounds is recorded as a rebound number. Although the RH test does not measure the speed of sound through the material like the Ultrasonic Pulse Velocity (UPV) test, it provides important information about the concrete’s surface quality. A higher rebound number typically indicates a harder surface and thus better compressive strength and overall integrity. For geopolymer aggregate concrete, which can have different surface properties compared to traditional concrete, the RH test helps estimate strength and uniformity by evaluating surface hardness. Variations in rebound numbers can signal inconsistencies in surface quality, which might arise from issues with mixing, curing, or the properties of the geopolymer aggregates. The test also allows for comparing different sections of a structure to identify areas that may need further investigation. Its non-destructive nature and quick application make the Rebound Hammer Test a practical and effective tool for evaluating the quality and structural integrity of geopolymer aggregate concrete, ensuring it meets the required standards for durability and performance.
The durability properties of concrete were determined using the following laboratory experiments.
2.5.5 Rapid chloride penetration test
RCPT (Rapid Chloride Penetration Test) is conducted as per ASTM C 1202. Both conventional concrete and geopolymer aggregate concrete are tested using this method. The test uses cylinder slices with a diameter of 100 mm and a height of 50 mm. Slices are cut from larger 100 mm diameter by 300 mm high cylinders prepared for each mix, resulting in six smaller cylinders. The RCPT setup is shown in Figure 5. By ASTM C 1202 (Zaetang et al., 2015), chloride permeability limits are detailed in Table 7. To ensure the credibility and reproducibility of research involving the Rapid Chloride Penetration Test (RCPT) for both conventional and geopolymer aggregate concrete, a meticulous experimental setup and adherence to standardized procedures are essential. According to ASTM C 1202, the test is conducted using cylindrical concrete samples with a diameter of 100 mm and a height of 50 mm, which are cut from larger cylinders of 100 mm diameter and 300 mm height. The RCPT setup involves placing these cylindrical slices into a test cell filled with sodium chloride (NaCl) and sodium hydroxide (NaOH) solutions, with electrodes on either side of the sample connected to a power supply that applies a constant voltage, typically 60 V. This setup drives chloride ions through the concrete, allowing measurement of their penetration rate. For reliable results, it is crucial that the concrete samples are properly cured and preconditioned by soaking in water before testing. The test should be conducted under controlled temperature and humidity conditions to prevent variability. Methodological innovations include ensuring precise cutting of samples to maintain uniformity, regular calibration of the electrolyte solutions and power supply, and replicating tests to improve data reliability. Including control samples of known permeability also helps validate the test setup. Detailed documentation of test conditions and a thorough comparison of results with established chloride permeability limits are essential for accurate interpretation and reporting. These practices collectively enhance the validity and reproducibility of RCPT research for both conventional and geopolymer aggregate concrete.
2.5.6 Sorptivity test
The standard method for measuring the water absorption rate of hydraulic cement concrete is a sorptivity test. It determines sorptivity by tracking the mass increase of a concrete specimen due to capillary absorption over time with one surface exposed to water. This test follows ASTM C 1585–04 (American Society for Testing and Materials, 2012a). The cylinder specimens used were 100 mm in diameter and 50 mm in height, cut from 100 mm × 300 mm cylinders. To ensure the credibility and reproducibility of research on the water absorption rate of hydraulic cement concrete, the sorptivity test, following ASTM C 1585–04, is meticulously conducted using specific procedures and conditions. The test involves preparing cylindrical concrete specimens with a diameter of 100 mm and a height of 50 mm, which are cut from larger 100 mm by 300 mm cylinders. These specimens are first cured under standard conditions to achieve the necessary hydration and strength. Before testing, the specimens are preconditioned by drying to a constant mass, ensuring that any observed weight gain during the test is due to water absorption. During the sorptivity test, one surface of each specimen is exposed to water, while the other surfaces are sealed to prevent moisture intrusion. The water exposure setup is carefully maintained to ensure that water is absorbed only through the exposed surface. Testing is performed in a controlled environment where temperature and humidity are kept constant to avoid external influences on the absorption rate. Methodological innovations, such as using high-precision digital balances for accurate mass measurements and continuously monitoring weight changes at regular intervals, enhance the accuracy of the results. Detailed documentation of all procedures, including test conditions and measurement data, further supports the reproducibility of the research. By adhering to these rigorous practices, the sorptivity test provides reliable and consistent data on the concrete’s water absorption properties, which is crucial for assessing its durability and performance. It is oven-dried for 24 h at 110°C and cooled to room temperature for 24 h before testing. Water absorption was measured at various intervals, and average sorptivity was calculated. Specimens used for the test are shown in Figure 6.
Calculations are done by using the following equation. Absorption, denoted as ‘I,’ is calculated by dividing the change in mass by-product of the specimen cross-sectional area and density of water used in the test (American Society for Testing and Materials, 2001b)
Where I = Absorption in mm
mt = Change in specimen mass in grams at time t
a = specimen exposed area in mm2
d = water density in g/mm3
2.5.7 Acid resistance test
Concrete’s ability to resist acidity is crucial for sewer systems due to the acidic nature of sewage water. In this study, acid resistance tests were performed as per ASTM C1898-20 using water with 5% sulfuric acid (H2SO4) by weight, following Manju’s (2017) method (American Society for Testing and Materials, 2007). The pH of the water was continuously monitored with a portable digital pH meter and maintained by periodically adding concentrated sulfuric acid. Cube specimens measuring 100 mm × 100 mm × 100 mm were cured in H2SO4 solution for about 28 days. Cube specimens were weighed with a balance accurate to 1 g. It is immersed in acidic water for 28 days. Specimens are removed, wiped dry, and weighed again. They were then tested for compressive strength. Percentage loss in weight and compressive strength is calculated. To ensure the credibility and reproducibility of research on concrete’s resistance to acidity, particularly for sewer systems exposed to acidic sewage water, a well-defined experimental setup and rigorous methodology are essential. Acid resistance tests were conducted following ASTM C1898-20 and adapted from Manju’s (2017) method, using a 5% sulfuric acid (H2SO4) solution by weight. Concrete cubes with dimensions of 100 mm × 100 mm × 100 mm were initially cast and cured under standard conditions. Once cured, these cubes were immersed in the sulfuric acid solution for 28 days. Throughout the immersion period, the pH of the solution was continuously monitored with a portable digital pH meter, and the pH was maintained by periodically adding concentrated sulfuric acid to ensure consistency. After immersion, the cubes were carefully removed, wiped dry, and weighed with a precision balance accurate to 1 g. The percentage loss in weight was calculated, and the cubes were then tested for compressive strength using a compression testing machine to measure their load-bearing capacity. Innovations in this methodology included precise pH control, careful measurement of weight changes, and detailed documentation of all procedures, which collectively enhance the accuracy and reproducibility of the results. This approach ensures that the findings accurately reflect the concrete’s resistance to acidic environments, making it highly relevant for applications such as sewer systems.
3 Results and discussions
3.1 Compressive strength of concrete
Figure 7 shows compressive strength graphical presentation values of M25 grade concrete with replacement levels of GPA from 0% to 100% at 25% increment.
This study underscores the advantages of using geopolymer aggregates in concrete, showing that a 100% replacement of natural coarse aggregates with geopolymer aggregates results in a 9%–15% increase in compressive strength. Additionally, the ultrasonic pulse velocity measurements, ranging from 4 km/s to 4.5 km/s, confirm that geopolymer aggregate concrete meets high-quality standards as per IS specifications. Rebound Hammer test results further support the improved quality of concrete with geopolymer aggregates. While these aggregates enhance concrete’s resistance to acid and sulfate attacks due to their strong bonding with the cement matrix, their increased porosity results in 10%–30% higher sorptivity and greater chloride ingress, which may impact long-term durability. The practical applications of geopolymer aggregate concrete are promising. It is particularly suitable for mass concreting projects, foundation works, and the construction of retaining walls, roads, dams, and breakwater blocks. By substituting natural coarse aggregates with geopolymer aggregates, it is possible to reduce waste, lessen the environmental impact of aggregate extraction, and address the increasing demand for coarse aggregates in expanding construction activities. However, the study also reveals limitations. The increased sorptivity and chloride ingress associated with geopolymer aggregates may affect the concrete’s long-term performance. Future research should focus on addressing these concerns by exploring ways to optimize the porosity of geopolymer aggregates and their impact on chloride penetration. Long-term durability studies are essential to evaluate the performance of geopolymer concrete over time and under various environmental conditions. Additionally, further investigations should aim to refine mix designs, improve cost-effectiveness, and validate laboratory findings through field trials and pilot projects. These steps will enhance the practical application of geopolymer aggregates and solidify their role as a sustainable alternative to natural coarse aggregates in the construction industry (American Society for Testing and Materials, 2006).
3.2 Ultrasonic pulse velocity of concrete
Ultrasonic pulse velocity values of M25 concrete grade with replacement levels by GPA from 0% to 100% at 25% increment are plotted as a graph, as shown in Figure 8.
The study’s findings on pulse velocity provide valuable insights into the quality of concrete, highlighting that regardless of variations in the water-cement ratio and the level of geopolymer aggregate (GPA) replacement, the pulse velocities consistently fall within the range of 4–4.5 km/s. According to IS specifications, this range is indicative of good quality concrete. The consistency in pulse velocities across different concrete mixes suggests that the inclusion of GPA does not adversely affect the concrete’s uniformity or the absence of internal flaws. When comparing these results with previous research, it is evident that the pulse velocities observed for GPA concrete align with those reported for natural aggregate concrete, suggesting that GPA exhibits comparable rheological properties. Existing studies on pulse velocity and aggregate types (American Society for Testing and Materials, 2001a; American Society for Testing and Materials, 2013; American Society for Testing and Materials, 2012c) have shown that aggregate content and type significantly influence pulse velocity. The alignment of pulse velocities for GPA with those for natural aggregates supports the inference that GPA can effectively replicate the performance characteristics of traditional aggregates in terms of concrete quality. The implications of these findings are significant. The ability of GPA to achieve pulse velocities within the acceptable range for good quality concrete demonstrates its potential as a viable alternative to natural aggregates, particularly in applications where concrete quality is critical. This finding is important for validating the use of GPA in construction, especially as the demand for sustainable materials grows. However, the study should address any anomalies or unexpected outcomes in more detail. For instance, if there were any variations in pulse velocity that were not anticipated, exploring these deviations could provide insights into specific interactions between GPA and the cement matrix. Additionally, a thorough discussion on how these findings align with or challenge existing theories would enrich the analysis. This could involve comparing the observed pulse velocities with those from other studies that used different types of aggregates or varying mix designs. To enhance the robustness of the findings, future research should include a more detailed statistical analysis. This would involve calculating confidence intervals and significance levels to substantiate the claims about pulse velocity and its correlation with concrete quality. Such an analysis would help confirm the reliability of the results and provide a clearer understanding of the performance of GPA in concrete applications.
3.3 Rebound number of concrete
Rebound numbers of M25 grade concrete with replacement levels by GPA from 0% to 100% at a 25% increment are plotted in the form of a bar chart, as shown in Figure 9.
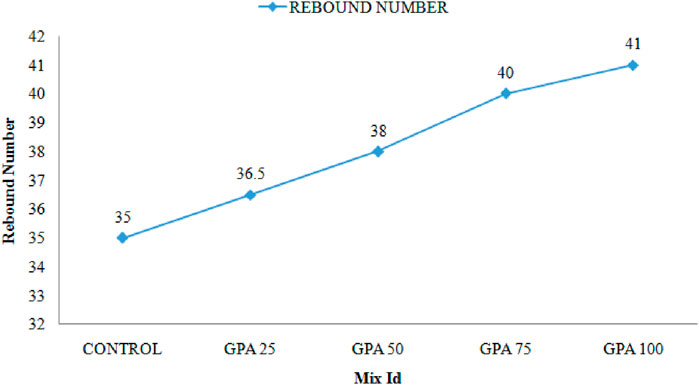
Figure 9. Rebound numbers of M25 grade concrete with various levels of replacement by GPA aggregate.
The rebound hammer test is instrumental in evaluating the quality, uniformity, and strength of concrete, and the results from this study are particularly revealing. Figure 10 demonstrates that rebound numbers for M25 concrete, regardless of the level of geopolymer aggregate (GPA) replacement, remain relatively consistent. This consistency suggests that the inclusion of GPA does not negatively affect the concrete’s surface hardness and strength. In fact, the rebound hammer test indicates an overall improvement in concrete quality with GPA, especially notable at the 100% replacement level. This finding is significant because it implies that GPA can effectively maintain or even enhance concrete’s surface properties, making it a viable alternative to natural aggregates without compromising performance. The improvement at the 100% replacement level particularly highlights GPA’s potential for large-scale construction projects, contributing to more sustainable practices by reducing reliance on natural resources.
However, while the rebound numbers are generally positive, it is crucial to address any anomalies or unexpected results observed in the study. For instance, if there were any variations in rebound numbers not anticipated, these should be thoroughly investigated to understand their causes. Such variations might be due to differences in the texture or composition of the geopolymer aggregates or inconsistencies in the mixing process. Understanding these factors is essential for explaining why GPA may enhance performance in some instances but not others. To further substantiate these findings, future research should include a more detailed statistical analysis, such as calculating confidence intervals and significance levels. This would provide a clearer understanding of the reliability of the rebound numbers and the impact of GPA on concrete quality. Additionally, extending the research to long-term durability tests would offer insights into how GPA concrete performs over time, helping to validate the short-term improvements observed and assess the overall benefits and challenges of using geopolymer aggregates in concrete applications. By addressing these aspects, the study can offer a more comprehensive understanding of GPA’s role in enhancing concrete quality and its practical implications in the construction industry.
3.4 Relation between compressive strength and rebound number
The rebound cement grade, aggregate shape, surface characteristics, and moisture content in concrete significantly influence the rebound number. The compressive strength of concrete is expressed as the exponential function of rebound number (Rn). Figure 10 presents plots of rebound number versus compressive strength. These graphs show that plots for natural aggregate concrete and geopolymer aggregate concrete are closely aligned, indicating excellent agreement and suggesting that the quality of geopolymer aggregate concrete is comparable to conventional concrete. From the graphs, the following equations are derived:
For natural aggregate concrete with
Results obtained from non-destructive tests, namely, the UPV test and rebound hammer test, prove the compatibility of geopolymer aggregate in concrete.
3.5 Sorptivity test
Figure 11 presents a detailed analysis of the absorption characteristics of concrete with varying levels of geopolymer aggregate (GPA) replacement. By graphing absorption values against the square root of time, the experimental setup allows for the calculation of sorptivity values from the slope of the absorption curve. This method provides a quantitative basis for comparing the absorption properties of different concrete types. The results indicate a significant reduction in sorptivity with the addition of GPA, particularly at the 100% replacement level, where the minimum recorded sorptivity value is 0.1062, reflecting a reduction of approximately 47.9% compared to the control sample.
The implications of these findings are substantial. The marked decrease in sorptivity with 100% GPA replacement highlights the ability of geopolymer aggregates to significantly enhance concrete’s resistance to water absorption. This improvement is critical as reduced water absorption leads to increased durability and longevity of concrete structures by mitigating the risks associated with water-related damage, such as corrosion and freeze-thaw cycles. The enhanced water resistance of GPA100 demonstrates its effectiveness in improving the functionality and lifespan of concrete, making it a valuable material for applications where moisture control is crucial.
3.6 Acid resistance test
Test results furnish an exhaustive synopsis of experimental configuration and outcomes about acid resistance of concrete made with geopolymer aggregate (GPA). Results describe weight reduction and GPA compressive strength concrete specimens immersion in 30 days of solutions containing 3% H2SO4 and HCl. These results provide significant insights into the material’s behavior in acidic environments. Variations in weight and strength reductions of GPA concrete specimens are visually represented in Figure 12, facilitating the comparison and interpretation of experimental results. Additionally, the visual representation of data is enhanced by distinctions in strength and weight reductions for both acidic solutions, which are depicted in Figure 12. Text underscores that incorporation of GPA into concrete substantially enhances its resistance to acid, leading to reduced percentage losses in both strength and weight when compared to control specimens. This discovery implies that the performance of GPA concrete is comparable to, if not superior to, that of conventional concrete and GGBS-based aggregate concrete that have been examined in corrosive environments.
Nevertheless, it is worth mentioning that although GPA concrete exhibits enhanced resistance to acids, its reduced structural compactness diminishes its effectiveness as a barrier against exposure to H2SO4 and HCl. Consequently, weight and compressive strength deficits become more pronounced following the 30 day exposure phase. In general, the results of this study emphasize the durability and feasibility of GPA concrete as an alternative material in acidic surroundings. Additionally, they emphasize the significance of incorporating structural attributes when evaluating its operational effectiveness.
3.7 Sulphate resistance test
Results on weight loss and reduction in compressive strength of geopolymer aggregate concrete specimens after 30 days of immersion in 3% sodium sulfate solution. Visual representations of variations in weight and strength decrease, respectively, are presented in Figure 13. A significant observation is presented concerning the progression of strength in GPA concrete as opposed to conventional concrete (CC). In contrast to a modest 6% increase in strength observed in GPA concrete, conventional concrete demonstrates a substantial 63% increase in strength during 28 days. This implies that the ultimate strength of GPA concrete is achieved quicker than conventional concrete. In addition, the text presents data regarding the decrease in weight and compressive strength noted in GPA concrete specimens after a 30 day immersion in a 3% sodium chloride solution. Fluctuations in weight and strength reductions are visually represented in Figure 13. Notwithstanding slight fluctuations in weight spanning from 0.4% to 1.35% throughout exposure, conventional concrete specimens undergo a substantial decline in strength of approximately 12.2%. GPA concrete specimens, on the other hand, exhibit virtually no discernible decline in strength. The results of this study emphasize the exceptional longevity and robustness of GPA concrete, specifically when exposed to corrosive chemical surroundings, thereby establishing its viability as a dependable building material (American Society for Testing and Materials, 2002; Singh and Siddique, 2013).
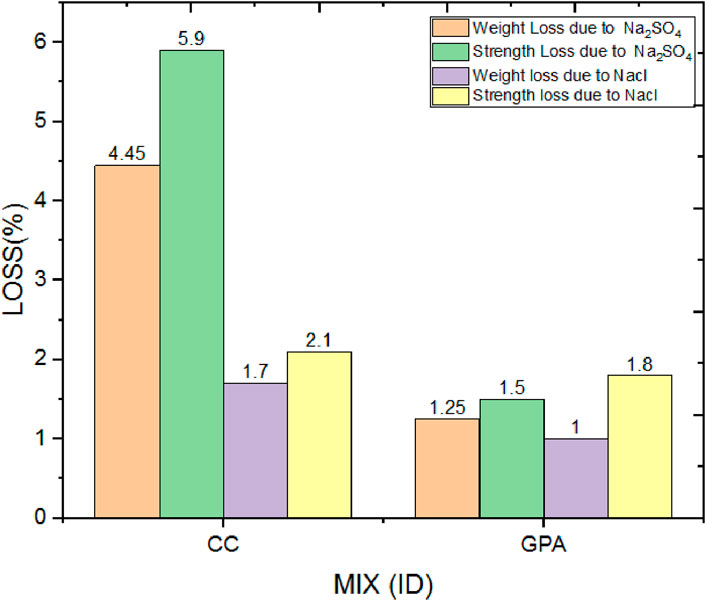
Figure 13. Weight loss and strength loss of GPA100 on exposure to sodium sulfate and sodium chloride solution.
3.8 Rapid chloride penetration
The extent of chloride penetration in different grades of conventional aggregate concrete and GPA concrete was studied using the Rapid Chloride Penetration Test (RCPT). Concrete permeability is influenced by its internal pore structure, which depends on the hydration level of the cementitious materials. Figure 14 shows that while chloride penetration is slightly higher in geopolymer aggregate concrete, the values remain within the permissible limits of ASTM C 1202. The increased chloride penetration is attributed to the porous structure formed by the steel slag aggregate, which permits more chloride ions to infiltrate the surrounding matrix. Iron particles in the geopolymer aggregate also boost electrical conductivity, leading to a higher electric current passing through GPA concrete (Lee et al., 2020; Topark-Ngarm et al., 2021; Topark-Ngarm et al., 2015). The extent of chloride ion ingress depends on the grade of concrete and material properties. As shown in Figure 14, chloride penetration decreases over time for both GPA100 concrete and conventional concrete. This reduction is due to the lower water-cement ratio in higher-grade concrete.
4 Conclusion
This research underscores the advantages of using geopolymer aggregates in concrete, showing that a 100% replacement of natural coarse aggregates with geopolymer aggregates results in a 9%–15% increase in compressive strength. Additionally, the ultrasonic pulse velocity measurements, ranging from 4 km/s to 4.5 km/s, confirm that geopolymer aggregate concrete meets high-quality standards as per IS specifications. Rebound Hammer test results further support the improved quality of concrete with geopolymer aggregates. While these aggregates enhance concrete’s resistance to acid and sulfate attacks due to their strong bonding with the cement matrix, their increased porosity results in 10%–30% higher sorptivity and greater chloride ingress, which may impact long-term durability. The practical applications of geopolymer aggregate concrete are promising. It is particularly suitable for mass concreting projects, foundation works, and the construction of retaining walls, roads, dams, and breakwater blocks. By substituting natural coarse aggregates with geopolymer aggregates, it is possible to reduce waste, lessen the environmental impact of aggregate extraction, and address the increasing demand for coarse aggregates in expanding construction activities.
However, the study also reveals limitations. The increased sorptivity and chloride ingress associated with geopolymer aggregates may affect the concrete’s long-term performance. Future research should focus on addressing these concerns by exploring ways to optimize the porosity of geopolymer aggregates and their impact on chloride penetration. Long-term durability studies are essential to evaluate the performance of geopolymer concrete over time and under various environmental conditions. Additionally, further investigations should aim to refine mix designs, improve cost-effectiveness, and validate laboratory findings through field trials and pilot projects. These steps will enhance the practical application of geopolymer aggregates and solidify their role as a sustainable alternative to natural coarse aggregates in the construction industry.
Data availability statement
The original contributions presented in the study are included in the article/supplementary material, further inquiries can be directed to the corresponding author.
Author contributions
TU: Conceptualization, Data curation, Formal Analysis, Funding acquisition, Investigation, Methodology, Project administration, Resources, Software, Supervision, Validation, Visualization, Writing–original draft, Writing–review and editing. MV: Conceptualization, Data curation, Formal Analysis, Funding acquisition, Investigation, Methodology, Project administration, Resources, Software, Supervision, Validation, Visualization, Writing–original draft, Writing–review and editing. SS: Conceptualization, Data curation, Formal Analysis, Funding acquisition, Investigation, Methodology, Project administration, Resources, Software, Supervision, Validation, Visualization, Writing–original draft, Writing–review and editing. RC: Conceptualization, Data curation, Formal Analysis, Funding acquisition, Investigation, Methodology, Project administration, Resources, Software, Supervision, Validation, Visualization, Writing–original draft, Writing–review and editing.
Funding
The authors declare financial support was received for the research, authorship, and/or publication of this article. The authors extend their appreciation to King Saud University for funding this work through the Researchers Supporting Project number (RSP 2024R164), King Saud University, Riyadh, Saudi Arabia. This article was co-funded by the European Union under the REFRESH−Research Excellence For Region Sustainability and Hightech Industries project number CZ.10.03.01/00/22_003/0000048 via the Operational Programme Just Transition and has been done in connection with project Students Grant Competition SP2024/087 “Specific Research of Sustainable Manufacturing Technologies” financed by the Ministry of Education, Youth and Sports and Faculty of Mechanical Engineering VSB-TUO. The article has been done in connection with the project Students Grant Competition SP2024/087 “Specific Research of Sustainable Manufacturing Technologies,” financed by the Ministry of Education, Youth and Sports and Faculty of Mechanical Engineering VSB-TUO.
Conflict of interest
The authors declare that the research was conducted in the absence of any commercial or financial relationships that could be construed as a potential conflict of interest.
Publisher’s note
All claims expressed in this article are solely those of the authors and do not necessarily represent those of their affiliated organizations, or those of the publisher, the editors and the reviewers. Any product that may be evaluated in this article, or claim that may be made by its manufacturer, is not guaranteed or endorsed by the publisher.
References
Almadani, M., Razak, R. A., Abdullah, M. M., and Mohamed, R. (2022). Geopolymer-based artificial aggregates: a review on methods of producing, properties, and improving techniques. Materials 15 (16), 5516. doi:10.3390/ma15165516
American Society for Testing and Materials (2001a). Standard test method for resistance to degradation of small-size coarse aggregate by abrasion and impact in the Los Angeles machine. West Conshohocken, PA: ASTM International. ASTM C131-96.
American Society for Testing and Materials (2001b). Standard test method for unit weight and voids in aggregate. West Conshohocken, PA: ASTM International. ASTM C29/C29M-97a.
American Society for Testing and Materials (2002). Standard test method for pulse velocity through concrete. West Conshohocken, PA: ASTM International. ASTM C597-09.
American Society for Testing and Materials (2006). Standard test method for Sieve analysis of fine and coarse aggregates. West Conshohocken, PA: ASTM International. ASTM C136-06.
American Society for Testing and Materials (2007). Standard test method for density, relative density (specific gravity), and absorption of coarse aggregate. West Conshohocken, PA: ASTM International. ASTM C127-07.
American Society for Testing and Materials (2012a). Standard specification for coal fly ash and raw or calcined natural pozzolan for use in concrete. West Conshohocken, PA: ASTM International. ASTM C618- 12a.
American Society for Testing and Materials (2012b). Standard test method for density and void content of hardened pervious concrete. West Conshohocken, PA: ASTM International.
American Society for Testing and Materials (2012c). Standard test method for slump of hydraulic-cement concrete. West Conshohocken, PA: ASTM International. ASTM C143/C143M-12.
American Society for Testing and Materials (2013). Standard specification for concrete aggregates. ASTM C33/C33M-13: Book of Standards.
Chindaprasirt, P., Chareerat, T., and Sirivivatnanon, V. (2017). Workability and strength of coarse high calcium fly ash geopolymer. Cem. Concr. Compos. 29 (3), 224–229. doi:10.1016/j.cemconcomp.2006.11.002
Demir, I., Hughes, R. E., and DeMaris, P. J. (2001). Formation and use of coal combustion residues from three types of power plants burning Illinois coals. Fuel 80 (11), 1659–1673. doi:10.1016/S0016-2361(01)00028-X
Guides, E. J. (2019). Effect of coarse aggregate size on the compressive behaviour of geopolymer concrete. Eur. J. Environ. Civ. Eng. 23 (6), 693–709. doi:10.1080/19648189.2017.1304276
Gunasekara, C., Setunge, S., and Law, D. W. (2017). Long-term mechanical properties of different fly ash geopolymers. ACI Struct. J. 114 (3). doi:10.14359/51689454
Gunasekara, C., Setunge, S., Law, D. W., Willis, N., and Burt, T. (2018). Engineering properties of geopolymer aggregate concrete. J. Mater. Civ. Eng. 30 (11). doi:10.1061/(ASCE)MT.1943-5533.0002501
Gunasekera, C., Setunge, S., and Law, D. W. (2017). Correlations between mechanical properties of low-calcium fly ash geopolymer concretes. J. Mater. Civ. Eng. 29 (9), 04017111. doi:10.1061/(ASCE)MT.1943-5533.0001916
Hart, B. R., Powell, M., Fyfe, W., and Ratanasthien, B. (2005). Geochemistry and mineralogy of fly-ash from the mae moh lignite deposit, Thailand. Energy sources. 17 (1), 23–40. doi:10.1080/00908319508946069
Joseph, B., and Mathew, G. (2023). Influence of aggregate content on the behavior of fly ash based geopolymer concrete. Sci. Iran. 19 (5), 1188–1194. doi:10.1016/j.scient.2012.07.006
Kim, H., and Lee, H. (2011). Use of power plant bottom ash as fine and coarse aggregates in high-strength concrete. Constr. Build. Mater. 25 (2), 1115–1122. doi:10.1016/j.conbuildmat.2010.06.065
Kumar, T. U., and Kumar, M. V. (2023). Microstructure characteristics of geopolymer aggregate concrete on the effect of liquid/slag ratio. J. Build. Pathology Rehabilitation 8 (2), 104. doi:10.1007/s41024-023-00348-5
Lee, H. K., Kim, H. K., and Hwang, E. A. (2020). Utilization of power plant bottom ash as aggregates in fiber-reinforced cellular concrete. Waste Manage 30 (2), 274–284. doi:10.1016/j.wasman.2009.09.043
Mesgari, S., Akbarnezhad, A., and Xiao, J. Z. (2023). Recycled geopolymer aggregates as coarse aggregates for Portland cement concrete and geopolymer concrete: effects on mechanical properties. Constr. Build. Mater. 10, 117571. doi:10.1016/j.conbuildmat.2019.117571
Poloju, K. K., and Sinivasu, K. (2021). Influence of GGBS and alkaline ratio on compression strength of geopolymer concrete. SPAST Abstr. 21 (01), 1. doi:10.1149/10701.8897ecst
Rajamane, N. P. J., Annie, P., and Ambily, P. S. (2019). Properties of ground granulated blast-furnace slag (GGBS) and its utilization in concrete. Journal of Sustainable Cement-Based Materials 8, 107–123. doi:10.14359/51732823
Seneviratne, C., Gunasekara, C., Law, D. W., Setunge, S., and Robert, D. (2021). Long-term mechanical properties of geopolymer aggregate concrete. ACI Struct. J. 118 (5). doi:10.14359/51732823
Seneviratne, C., Gunasekara, C., Law, D. W., Setunge, S., and Robert, D. (2022). Creep, shrinkage and permeation characteristics of geopolymer aggregate concrete: long-term performance. Archives Civ. Mech. Eng. 20, 140–145. doi:10.1007/s43452-020-00119-w
Shankar, S., and Joshi, H. R. (2014). Comparison of concrete properties determined by destructive and non-destructive tests. J. Inst. Eng. 10 (1), 130–139. doi:10.3126/jie.v10i1.10889
Singh, M., and Siddique, R. (2013). Effect of coal bottom ash as partial replacement of sand on properties of concrete. Resour. Conserv. Recycl. 72, 20–32. doi:10.1016/j.resconrec.2012.12.006
Thomas, B. S., Yang, J., Bahurudeen, A., Chinnu, S. N., Abdalla, J. A., Hawileh, R. A., et al. (2022). Geopolymer concrete incorporating recycled aggregates: a comprehensive review. Clean. Mater. 1, 3. doi:10.1016/j.clema.2022.100056
Topark-Ngarm, P., Chindaprasirt, P., and Sata, V. (2015). Setting time, strength, and bond of high-calcium fly ash geopolymer concrete. J. Mater. Civ. Eng. 27 (7), 04014198. doi:10.1061/(ASCE)MT.1943-5533.0001157
Topark-Ngarm, P., Sata, V., and Chindaprasirt, P. (2021). “Workability and strength of high calcium geopolymer concrete cured at room temperature,” in Annual concrete conference 7, rayong, Thailand. doi:10.1016/j.cemconcomp.2006.11.002
Keywords: durability, geopolymer aggregate, nondestructive testing, compressive strength, bonding
Citation: Udhaya Kumar T, Vinod Kumar M, Salunkhe S and Cep R (2024) Evaluation of non-destructive testing and long-term durability of geopolymer aggregate concrete. Front. Built Environ. 10:1454687. doi: 10.3389/fbuil.2024.1454687
Received: 25 June 2024; Accepted: 16 September 2024;
Published: 02 October 2024.
Edited by:
Mucteba Uysal, Yıldız Technical University, TürkiyeReviewed by:
Jingjie Wei, Missouri University of Science and Technology, United StatesBeyza Fahriye Aygün, Istanbul University-Cerrahpasa, Türkiye
Heydar Dehghanpour, Istanbul Aydın University, Türkiye
Copyright © 2024 Udhaya Kumar, Vinod Kumar, Salunkhe and Cep. This is an open-access article distributed under the terms of the Creative Commons Attribution License (CC BY). The use, distribution or reproduction in other forums is permitted, provided the original author(s) and the copyright owner(s) are credited and that the original publication in this journal is cited, in accordance with accepted academic practice. No use, distribution or reproduction is permitted which does not comply with these terms.
*Correspondence: Sachin Salunkhe, c2FjaGluc2FsdW5raGVAZ2F6aS5lZHUudHI=