- 1Department of Civil Engineering, National University of Skills (NUS), Tehran, Iran
- 2Scientific and Technological Complex “Digital Engineering in Civil Engineering”Peter the Great St. Petersburg Polytechnic University St. Petersburg, Saint Petersburg, Russia
- 3Moscow State University of Civil Engineering, Moscow, Russia
- 4Department of Construction Technologies and Structural Materials, Peoples’ Friendship University of Russia, Moscow, Russia
This review aims to provide a comprehensive analysis of the difference between 3D printed concrete (3DPC) and 3D printing reinforced concrete (3DPRC) technologies, as well as potential future paths for these technologies based on current consolidated approaches. Although 3D printed reinforced concrete technology attempts to strengthen reinforced concrete using 3D printing technologies with polymer ingredients, 3D printed concrete technology concentrates on printing concrete for building concrete structures. In recent years, both technologies have advanced rapidly and become a global research innovation hotspot due to their advantages over traditional construction technology, such as high building efficiency, low labor costs, and less construction waste. Unfortunately, there are several issues with 3DPC and 3DPRC technologies, including competing rheological requirements, integrating hurdles, inadequate interlayer bonding, and anisotropic properties of the material that result in lacking structural performance. The findings of the investigation discuss research gaps and theoretical possibilities for future development in both 3D printing technologies, which can advance concrete technology and safeguard structures under various loads. In the present study, two distinct 3D printing technologies are analyzed, along with their respective uses in material and structural engineering. Additionally, the advantages, methods, and materials utilized for the two types of 3D printing technology are described, and the difficulties and solutions associated with using 3D printed concrete in real-world projects are demonstrated. None of the earlier investigations examined the differences between these two technologies. Although 3DPRC technologies aim to strengthen concrete by incorporating various forms of 3D printed technology, 3DPC technology has been studied for its mechanical qualities and concrete rheology. Meanwhile, engineers in 3D printed concrete technologies try to improve large-scale 3D printers and the mechanical properties of printed concrete, while 3D printing reinforced concrete engineers try to design new patterns of 3D reinforcing patterns due to the improved mechanical properties of concrete. The present study examines the differences between 3DPC and 3DPRC technologies.
1 Introduction
Current limitations like the lack of skilled labor, resource depletion, and safety concerns have had a major impact on the growth of the construction sector as a result of the rapid rate of urbanization and industrialization. The development of technology for 3D printed concrete (3DPC) and 3D printing reinforced concrete (3DPRC) gives engineers and researchers in the building sector new ideas. It has been proven that 3DPC and 3DPRC have significantly influenced civil engineering and concrete structures, respectively (Hematibahar et al., 2024a). Although a few investigations concentrated on 3D printed reinforced concrete, others examined the topic of 3D printed concrete. Both technologies have advantages as well as disadvantages. 3D printed concrete is known as a transformative technology that can change the housing shortage and enable innovative architectural designs. Studies have validated mechanical property testing, including compressive, tensile, and flexural strength, or increased correlation between other conventional test methods and rheometer results. Other studies investigated 3D printing tools through a robot arm or the economic effect of full-scale 3D printed concrete homes (Abdalla et al., 2021; Hu et al., 2024; Park et al., 2024; Phuong Bao et al., 2024). Another example of 3DPRC is the case of cement mortar and reinforced concrete materials with different patterns of 3D printing technology. In this technology, materials are roughly printed through a fused deposition modeling (FDM) technique. Most printing materials are polymers, such as acrylonitrile butadiene styrene (ABS) or polylactic acid (PLA). Thus, the strengthening of concrete with 3D printing is a modern technology that can improve the strength and ductility of concrete or observe the energy of reinforced concrete under various types of loading (Chajec and Šavija, 2024; Xu et al., 2024a; Xu et al., 2024b). In general, 3DPC technology today is looking for generalities in construction, while 3DPRC is at the beginning of scientific research and looking for details in construction materials.
The current study begins with 3D concrete technology. 3D printed concrete focusses on concrete with high mechanical properties in a free form without any concrete mold. Reinforced 3D printing attempts to change the rebar with 3D printing materials. Adding reinforced 3D printing also aims to convert concrete’s strain-softening properties to strain-hardening ones. In 1997, Joseph Pegna utilized additive manufacturing to print concrete layer by layer for the first time. Behrokh Khoshnevis then employed 3DPC technology, namely, contour crafting (CC), using cement materials to create large-scale 3D constructions (Khoshnevis, 2004; Rouhana et al., 2014). The nozzle mechanism could be oriented at different angles to construct different buildings (Khoshnevis and Dutton, 1998; Buswell et al., 2007; Kazemian et al., 2017; Vergara et al., 2017). The primary advantage of this technique is that concrete may be 3D printed in freeform geometry without the need for formwork. Therefore, materials of 3D printed concrete must have suitable fluidity and good standing properties before and after extrusion (Lim et al., 2012; Zhang et al., 2018c).
In the process of printing concrete, the bed is covered by dry powder sprayed with water, and the concrete is printed layer by layer (Lowke et al., 2018). The potential of the printer and mortar material mix to extrude uniformly layer by layer is one of the most crucial aspects of this process. In 3DPC printer technology, vibration and low pressure are transferred from the pipeline to the nozzle to print concrete and mortar (Arosio et al., 2007; Cordeiro et al., 2016; Bani Ardalan et al., 2017; da Silva et al., 2017; Saw et al., 2017). Some studies investigated the use of geopolymers such as fly ash to make concrete green and environmentally friendly (Panda et al., 2017; Paul et al., 2018). Unlike ordinary Portland cement, geopolymer 3D printed concrete has not yielded stress and low viscosity (Favier et al., 2014). The slump test is the easiest test to use to understand the workability of concrete. The simplest laboratory test for determining whether concrete is workable is the slump test (ASTM C143/C143M-03, 2003); Tay et al. (2019a) present a new protocol for slump and slump-flow testing for measuring the pumping ability of concrete.
Different types of materials can improve the mechanical properties of 3D printed concrete. Some chemical and mineral materials are affected by the mechanical properties of concrete, rheology, etc. For example, superplasticizers as accelerators can change the long-term strength of 3D printed concrete. There are different types of accelerators, such as earth metals, carbonates, hydrates, and inorganic salts. One of the most important materials is sulfoaluminate cement (SAC), which can make ettringite in concrete (Lossier, 1946; Prudˆ encio, 1998; Souza et al., 2020b; Souza et al., 2020a). Superplasticizers can change the viscosity of mortar, setting retarders, and workability (Malaeb et al., 2019). Hua Shang Tengda Ltd. is a Chinese building company that presented a new type of 3D printed concrete with extruded steel rebar as concrete reinforced. This rebar can extrude rebar inside the 3D printed concrete in both the vertical and horizontal directions.
Some studies suggested replacing the recycled aggregates with natural aggregates in 3DPC. For example, Evangelista and de Brito (2007) proposed using not more than 30%0 recycled fine aggregates. Different studies show that when the mixture design is suitable for recycled sand, the design can be reasonable for 3D printing technology (Jiang et al., 2019; Le et al., 2012).
Adding fibers to concrete can improve its mechanical and durability properties (Momeni et al., 2024; Vatin et al., 2024). Some researchers investigated using rebar to improve the flexural strength of reinforced 3D printed concrete structures. In addition, other studies investigated a special type of “permanent formwork” that is cast with conventional concrete (Lim et al., 2012). Further studies have investigated adding different types of fibers to 3D printed concrete. For example, Panda et al. (2017) added different types of short glass fibers (3 mm, 6 mm, and 8 mm) at 0.25% and 1% in 3DPC, which improves the mechanical properties. Current studies attempt to change the cement material powder with fine aggregates (0.1–100 μm), and the extruding layer thickness was approximately 100 μm (Xia and Sanjayan, 2016). In another example, Hambach and Volkmer (2017) added basalt and carbon fibers to 3D print fibers in 3D printed concrete and found that flexural strength improved. Polyethylene (PE) fibers can increase the mechanical properties and can increase the energy and fiber bridging effect in 3D printed concrete (Yu et al., 2018). The strain-softening effect was observed after the post peak of concrete when steel fiber was added to 3D printed concrete (Bos et al., 2019). Faludi et al. (2015) added cast concrete to 3D printing, which used less energy than usual. Prasittisopin et al. (2019) improved the thermal performance of 3D printed concrete structures. According to Lpez-Mesa et al. (2009), the environmental effect was reduced by 12% when 3D printed concrete was used instead of the in situ cast concrete process. Several studies examined reinforced 3D printed concrete using continuous fiber-reinforced polymers (FRP). For example, Zeng et al. (2024) reinforced concrete with 3D printed continuous fiber reinforced thermoplastic polymers (CFRTPs). They found that when CFRTPs were added to 3D printed concrete, the flexural strength increased by more than 100%, and strain behavior changed to strain hardening. Yan et al. (2024) examined 3D printing cylindrical of ultra-high performance concrete (UHPC) with reinforcing FRP wrapping. They found that adding FRP wrapping reduced the large defects. Feng et al. (2015) warped 3D printed concrete with glass FRP (GFRP). They found that cylindrical 3D printed concrete warped with GFRP increased by more than 179%. Sun et al. (2021) examined the bonding strength of 3DPRC with basalt fiber-reinforced polymers (BFRP). According to their results, the slip corresponding to the peak bond stress is between 0.48 mm and 1.46 mm. Moreover, the peak bond strength was more than 0.24–0.65 MPa. Park et al. (2020) studied 3D printing reinforced concrete beams with steel and FRP to improve their flexural strength. They found that 3DPRC has a flexural strength of 10.4 kN, and steel-rebar-reinforced 3DPC has a flexural strength of 26.6 kN.
Luo et al. (2022) analyzed the auxetic tube to cover the cylinder concrete under compressive strength. The compressive strength of auxetic improves the concrete when the auxetic tube covers the concrete. Poisson’s ratio and the thickness of the stainless tube can improve the mechanical properties of the concrete cylinder.
The second part of the article is a review of the literature on 3D printed reinforced concrete. The significant improvement of 3DPRC is the increase of mechanical properties such as compressive and flexural strength, in addition to the change of “strain softening” to “strain hardening” to flexural load displacement. Some studies improve mechanical properties such as flexural strength, while the strain behavior has not changed due to the nature of the polymer as a 3D printing material to harden and increase compressive strength (Lao et al., 2024; Li et al., 2024; Zhu et al., 2024). According to the study results, the geometry of 3D reinforcements is the most important factor that is exclusive to this technology, and creativity in reinforced concrete is the greatest advantage of this technology, although the optimization pattern of 3D printed structures has been widely studied. For example, truss, gyroid, and lattice structures perform well under compressive and flexural loads (Nguyen-Van et al., 2022; Skoratko et al., 2022). The lattice structure has many advantages. Auxetic patterns can improve flexural and tensile strength in addition to compressive strength when used as reinforcement in cementitious material. One advantage of the auxetic structure pattern is a negative Poisson ratio (Chen et al., 2023; Xu and Savija, 2024). This behavior can significantly increase the properties of reinforced concrete. Miller et al. (2012) manufactured 3D printed auxetic fibers with a −6.8 negative Poisson ratio and a 30% volume fraction of fiber. Zahra and Dhanasekar (2017) used auxetic foam to reinforce the cement matrix. They understood that auxetic foam can reduce the brittleness of the cement matrix. According to the studies, when reinforced 3D printed auxetic patterns are used in reinforced concrete, confinement effect, stability, shear resistance, and ductility improved (Tzortzinis et al., 2022; Zhong et al., 2022). Many reinforced 3D printed concrete and auxetic material studies are attempts to change strain softening to strain hardening. Xu and Savija (2023) presented a 3D printing method to change the strain softening of concrete to strain hardening. They filled an auxetic polymer shell with cement mortar and found that uniaxial compressive strength improves and changes stress-strain to strain hardening.
This study compares and contrasts two modern concrete construction technologies. 3D concrete printing technology strives to improve the mechanical properties of concrete printing, concrete types, and reduce construction time. In general, 3DPC technology focuses on constructing concrete structures. Meanwhile, 3DPRC technology attempts to add different patterns through 3D printing technology using different materials such as PLA or ABS to increase the flexural strength and ductility of concrete reinforcement. In general, 3D printing plays the role of reinforcement in concrete structures for 3DPRC, while 3DPC plays a large role in building construction. This study analyzes and compares both technologies to prevent mistakes by engineers when choosing and using these disciplines.
2 Existing 3D printed concrete and 3D printing reinforced concrete technologies
3DPC technology focuses on concrete printing through concrete printers and can build structures without concrete formwork, reduce construction time, reduce the number of workers, etc., while 3DPRC technology tries to improve concrete and cementitious materials through reinforced concrete through 3D printing technology, such as fused deposition modeling (FDM) and the use of different polymer materials.
2.1 3D printed concrete technology
2.1.1 Technological aspects
3DPC technology starts with a digital 3D model and “sliced layers” processes and changes file formats to standard tessellation language (STL). Next, the printing process starts, and the structure is completed in the “final element” process (Figure 1) (Pessoa et al., 2021).
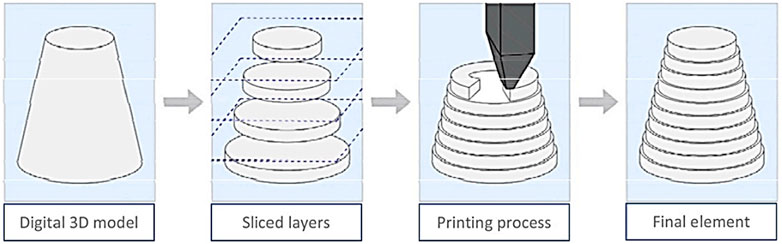
Figure 1. Process of 3D printed concrete technology [based on Pessoa et al. (2021)].
Three-dimensional concrete technologies are designed by software and later converted to the printing process. The printing parameters must be defined with regard to printed concrete. The nozzle opening and layer height are defined according to the thickness as well as the geometric complexity. If the nozzle opening is smaller, the fluidity should be higher (Malaeb et al., 2019). There are two types of nozzles, round and flat, for installing concrete. In the case of round nozzles, because of the smaller gaps between the layers, the bond between them is weaker, but sometimes, some types of round nozzles tend to create smoother and thicker layers. The flat nozzle creates thicker layers and improves mechanical resistance, and the shape of the building is improved due to the rectangular opening (Figure 2A, B shows different opening thicknesses) (Liu et al., 2020). Anisotropic properties are another aspect of 3D printed concrete. When the load is applied in the z direction, the compressive strength increases, and in the x and y directions, the tensile strength increases due to the bond strength between the layers, which is related to viscosity, content level, and time interval (Paul et al., 2018) (Figures 2C–E). Sanjayan et al. (2018) found that the moisture level between the layers is probably the main factor affecting the interlayer adhesion and is related to the compressive and tensile strength.
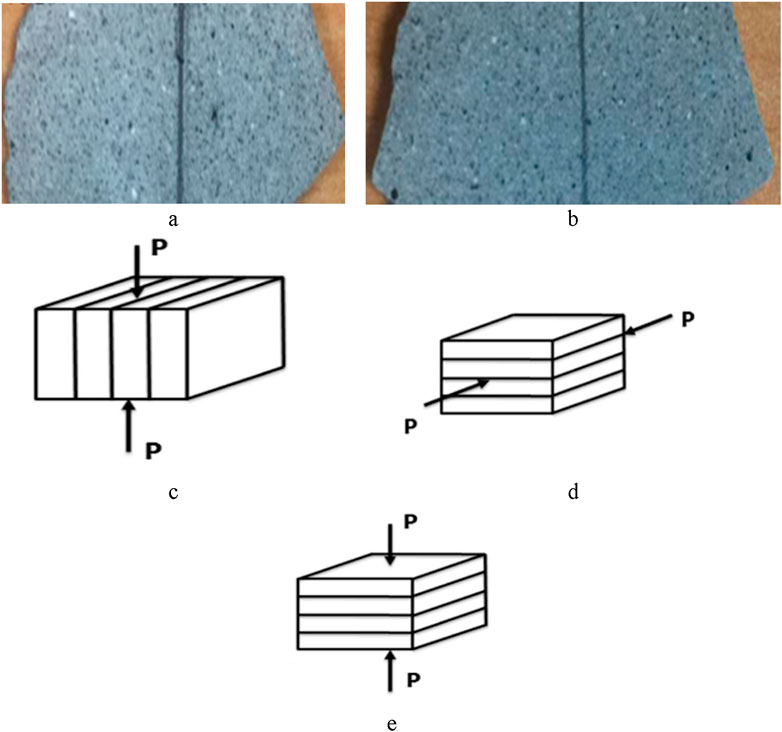
Figure 2. 3D printing methodology: (A) and (B) Different thicknesses of opening [based on Liu et al. (2020)], (C) Loading in the X-direction [based on Paul et al. (2018)], (D) Loading in the Y-direction [based on Paul et al. (2018)], and (E) Loading in the Z-direction [based on Paul et al. (2018)].
In 3D printed concrete, there are disadvantages such as cracking due to shrinkage, cold bonding due to filament interlock, nozzle blockage, and layers of different widths and heights. Shrinkage cracking is usually caused by high temperature, low humidity, and other environmental conditions. The cold joint problem is due to the rapid hydration process. Nozzle clogging disorder occurs due to the high aggregate content and low flexibility of 3D printed concrete. According to the literature review, the 3D printed concrete is environmentally friendly concrete due to the elimination of formworks and the reduction of labor (Labonnote et al., 2016; De Schutter et al., 2018).
2.1.2 Material properties
Various new studies present new methods. For example, Dvorkin et al. (2024) examined fine aggregates to make 3D printed concrete. They added mineral additives and slag-alkaline binders to concrete. According to the results, the maximum compressive strength was between 7.6 MPa and 18.7 MPa after 1 day. It should be mentioned that the thickness of each layer is a maximum of 4 cm. Figure 3 shows the layers and concrete 3D printing fabrication.
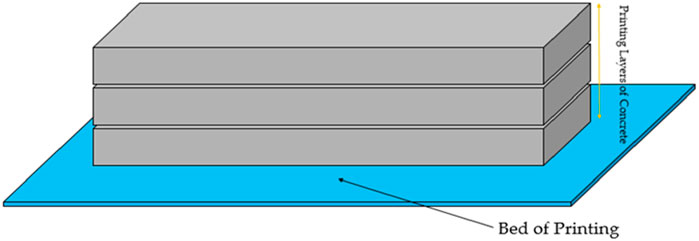
Figure 3. 3D printing sample test based on Dvorkin et al. (2024).
Jiang et al. (2024) analyzed different patterns and paths, such as crosswise, vertical, arched, and diagonal. They found that arched path 3D printed concrete had the best flexural strength (more than 30% improvement compared to other samples) due to the bond between filaments. They used cement, sand, silica fume, and fly ash. Mechanical property results show that arched flexural and compressive strengths are 6.3 MPa and 12.4 MPa, respectively.
3D printed concrete using Portland cement yielded compressive strength of 20 Mpa and 60 Mpa and bending strength between 3 Mpa and 10 Mpa (Higgins and Bailey, 1976; Birchall et al., 1981; Ni and Wang, 2000). Moreover, adding rebar and reinforcement can improve tensile strength and ductility (Khoshnevis et al., 2006; Mechtcherine et al., 2019. Asprone et al. (2018) used a 3D printed concrete beam with steel bars. They found that 3D-printed concrete beams reinforced with steel rebar provide an initial stiffness comparable to that of fully reinforced concrete beams. Some researchers have analyzed the internal voids for post-replacement of reinforcements, and this strategy can be used to improve the tensile and flexural strengths of structures in the assembly of prefabricated components (Lim et al., 2012). Another strategy is using fibers instead of steel rebar reinforcement. Some research shows that 3D printed concrete fiber reinforcement can achieve high mechanical properties similar to 3D printed concrete steel rebar reinforcement (Zollo, 1997; Senff et al., 2014; Senff et al., 2015). Many types of fibers, such as basalt, glass, steel, carbon, etc., are used to improve the mechanical properties such as toughness, ductility, fatigue resistance, impact resistance, and especially the tensile strength of the building structure (Hamedanimojarrad et al., 2012; Yazıcı et al., 2013; Yoo et al., 2013; Mukhametrakhimov, 2022; Kuznetsov et al., 2023; Hemant et al., 2007). There are many aspects, such as fiber orientation, aspect ratio, size, type, and volume fraction, to improving 3D printed concrete strength (Grünewald, 2011). Higher aspect ratio fibers had higher post-crack strength when the aspect ratio ranged from 30 to 150 (Yazıcı et al., 2007; Michels et al., 2013; Malaszkiewicz, 2017).
Some successful mix properties are shown in Table 1, which illustrates that the best sand size is larger than 1.7 mm, and the best rice husk ash size is larger than 0.075 mm and smaller than 2–7
Fibers on 3D printed concrete can affect the workability, shrinkage, and mechanical properties. For example, adding 1% of steel fiber to 3D printed concrete when cement was 483 g, the aggregates were 1,074 g, the silica fume was 268 g, and the superplasticizer was more than 10.7 g increases the compressive strength more than 109 MPa (Pham et al., 2020). Some studies show that when more than 1% polyethylene (PE) fibers were added, the compressive strength increased by more than 27.3 MPa, when the cement was 1,000 g, the aggregates were g, the water-to-binder percentage was 35%, and the superplasticizer was 1.28 g (Xiao J. et al., 2021). Adding polypropylene (PP) fibers to 3D printed concrete increases the compressive strength to more than 60.5 MPa. In this mixture, the cement was 562 g, the silica fume was more than 81.4 g, the aggregates were 1,144 g, and the superplasticizer was more than 4 g (van den Heever et al., 2022). According to studies, when 1.5% of polyvinyl alcohol (PVA) fiber was added to 3D printed concrete, when silica fume was 110 g, the cement was 1,000 g, the aggregates were 1,330 g, and the superplasticizer was 11 g, the flexural and compressive strengths were 10.81 MPa and 45.05 MPa (Zhang and Aslani, 2021).
According to Table 4, steel, polyethylene (PE), polypropylene (PP), polyvinyl alcohol (PVA), and glass fibers can improve flexural and compressive strengths. For example, Singh et al. (2022) found that when fibers that were 13 mm long and 200
Fiber orientation and fiber position are important in 3D printed concrete. Isotropic distribution and orientation of fibers can change the strength of 3D printed concrete (Grünewald, 2011). The length, type, stiffness, and flexibility of fibers are other important factors. The best aspect ratio range is from 30 to 150; fiber orientation is usually vertical, horizontal, or random distribution (Tattersall, 1991; Banfill et al., 2006; Ferrara et al., 2007; Martinie et al., 2010; Cao et al., 2017; Hambach and Volkmer, 2017; Malaszkiewicz, 2017; Güneyisi et al., 2019). When fiber orientation was changed to horizontal alignment, the flexural strength increased by more than 120 MPa (Hambach et al., 2016). Further studies analyzed different types and new methods in 3DPC technology. Bai et al. (2021) examined desert sand (small size), river-sediment ceramist sand (medium size), and recycled concrete (large size) as aggregates in 3D printed concrete. According to this investigation, adding this type of aggregate reduced the cementitious matrix shrinkage. The best flow velocity was 2.3–3.5 mm/s, and the expanded diameter was 160–210 mm/s.
2.1.3 Technology applications
Some studies focused on large-scale 3D printed concrete buildings. For example, Lowke et al. (2021) studied the rheological properties, the concrete flow rate, and the nozzle displacement velocity. They found that limestone suspension as the carrier liquid reduced the cost and controlled the rheological properties. They found a new method for 3D printed injection with materials such as artificial coral. The printing method was a robot-guided nozzle, and variables included the cross-sectional area of the nozzle. They found that this technology is the best technique for printing truss-type bridges.
Some concrete 3D printers are made for large-scale printing. Zhang et al. (2018a) designed a 3D printer for large-scale printing of concrete with a robotic arm (Figure 4A). Keating et al. (2017) developed a new method compound arm for 3D printed concrete at the Massachusetts Institute of Technology (MIT) (Figure 4B). Figure 3 shows that the tanker carries the materials, and fine aggregates are suitable for these types of 3D concrete printers. Mechtcherine et al. (2019) designed a new type of 3D concrete printer that is based on the concrete truck. According to Figure 4C, this type of 3D printed concrete is a mobile site that can pump 3D printed concrete with coarse aggregate concrete to make large-scale buildings. Figure 4D is a large style delta that was developed by the WASP Company. A disadvantage of this 3D printed concrete printer is mobility because this printer needs to be assembled for building construction. Figure 4E illustrates a 3D concrete printer developed by Tongji University and the Chinese Green Print Company. The height of the printer is 10 m, and the printer was moved by rail. In this printer, the maximum material size was 15 mm in the on-site construction project.
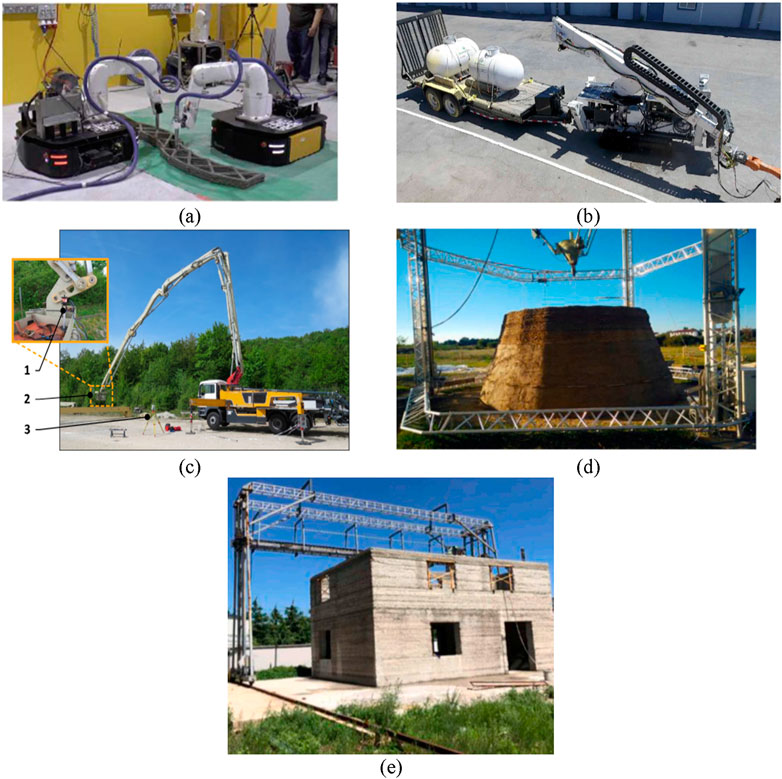
Figure 4. 3D printed concrete for constructions based on Xiao et al. (2021a). (A) Basic arm robotic based on Zhang et al. (2018a), (B) tanker base 3D printer (MIT) based on Science (Keating et al. (2017), (C) mobile base 3D printer based on Mechtcherine et al. (2019), (D) WASP Company 3D printer rails, and (E) Chinese Green Print Company.
The Southeast University and Nanjing Institute for Intelligent Additive Manufacturing developed a new method to design prefabricated and assembled 3D printed concrete particles such as walls, beams, columns, and slabs on-site. Figure 4 shows the 3D-printer technology that can build a 5.15 m high, 286 m2 building in Nanjing, China. The compressive and flexural strengths are more than 44.6 MPa and 7.4 MPa (He et al., 2020).
2.2 3D printing reinforced concrete technology
2.2.1 Technological aspects
Currently, many studies attempt to reinforce concrete with 3D printing technology like fused deposition modeling (FDM). This type of study tries to add different 3D printing patterns to reinforce concrete. Unlike 3DPC technology, 3DPRC technology uses FDM technology to print reinforced concrete and improve the mechanical properties of concrete.
The most important tools for 3D printing using the FDM method are nozzles, filaments, hot ends, heating blocks, etc. There are two main types of printing methods, direct drive and Bowden. In the direct drive method, the filament moves the filament toward the heating block, and while in the Bowden method, the gears send the string through the Bowden tube to the heating block (Fernandez-Vicente et al., 2016; Bhagia et al., 2021). The nozzle temperature is higher than the PLA melting temperature. The pure PLA melting temperature is more than 180°C–230°C, the semi-melting point temperature of PLA is 150°C–165°C (Tm), and the glass transition temperature is 55°C–65°C (Tg) (Fambri and Migliaresi, 2010; Abeykoon et al., 2020).
Rosewitz et al. (2019) used different 3D printed patterns fabricated by FDM technology and polylactic acid (PLA) as material to reinforce cement mortar. They found that some 3D printing patterns are suitable to improve the flexural strength, and the application of this type of reinforced technology printing is using the beam to reinforce. Salazar et al. (2020) used a 3D printing lattice with PLA and acrylonitrile butadiene styrene (ABS) materials to reinforce cement mortar. They understood that the most important factor of adding a 3D printing lattice as reinforcement to cement mortar is improving the strain hardening. The best application of their work was improving the resistance of concrete and cement mortar against earthquake loads. Hao et al. (2023) investigated using a 3D printed lattice to reinforce cubes and prisms. They understand that reinforced samples increase the compressive strength by more than 71.36%. Using polymer to reinforce cement mortar can improve the durability of concrete and be suitable. Tzortzinis et al. (2022) added 3D printing with hexagon auxetic lattice geometry in cement mortar to understand the compressive strength of reinforced concrete. The compressive strength increased by more than 140%. They understand that using 3D-printing steel fabrication is suitable for resistance structures under cyclic and dynamic loadings. Hematibahar et al. (2023) studied the effect of 3D printing hyperbolic shell structures to reinforce ultra-high performance concrete. They found that 3D printing hyperbolic shell structures can improve the ductility of concrete. Chiadighikaobi et al. (2024a) found that when a 3D printed truss was added to high-performance concrete, the flexural strength improved (Table 3).
At an installation, molds are usually printed, and then concrete is cast into the mold. Molds are prepared according to the design methods of each experiment. Commonly, the structure is first printed using the 3D printing method, then placed into the mold, and finally, concrete is installed into the molds (Table 4).
2.2.2 Material properties
Xu and Savija (2024) analyzed the 3D printed fabrication by PLA as an auxetic shape. They analyzed four types of auxetic shapes: re-entrant (RE), rotating-square (RS), chiral (CR), and missing-rib (MR). According to their results, when RS auxetic structures were added to the cement matrix, the compressive strength increased by more than 18.5%, and ductility decreased by more than 32.2% (Figure 5).
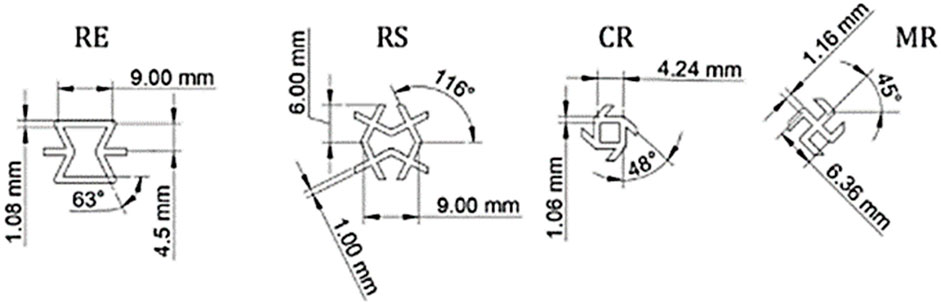
Figure 5. Different patterns of auxetic shapes [based on Xu and Savija (2024)].
Bol et al. (2024) studied the effect of auxetic added to cement matrix. According to the results, plateau stiffness and strength are approximately 120 MPa and 3 MPa, respectively. They found that when auxetic materials were used, the strain-hardening properties improved by 40% under compression loading. Zhang et al. (2022) introduced a new method to improve the mechanical properties of auxetic materials when added to the cement matrix. They first fabricated chiral lattices with and without circular holes. According to the results, auxetic material with circular holes shows improved load-bearing capacity. Novel chiral lattice composites improved volume fraction by more than 0.1 and 0.5. The investigations show that when different types of materials are used as reinforcement, the mechanical properties of concrete will change. Furthermore, the application of 3DPRC technology is very broad.
2.2.3 Technology applications
Different FDM properties are related to the mechanical properties of 3D printing fabrication. The experiments illustrate that the mechanical properties of cement matrix will change when the geometry and material properties of 3D printing fabrication will change. For example, Wan et al. (2023b) used additive manufacturing to print vascular networks with PVA materials. According to their experiments, the vascular tube made using wax-coated PVA material can dissolve when the proxy resin is injected into the vascular tube as a self-healing material. Finally, the four-point bending test shows the good performance of the proxy resin as a self-healing cement matrix. Similarly, Wan et al. (2023a) analyzed a new method to print vascular tubes via fused filament fabrication (FFF) technology. The resin is injected into the 3D-printed vascular network, the vascular network is dissolved, and the resin self-heals (Table 5).
3 Mechanical behavior of 3DPC and 3DPRC
3.1 Mechanical properties of 3D printed concrete
It is difficult to combine computational modeling and additive manufacturing technology to create new materials and produce 3D printed objects with high dimensional accuracy and high mechanical properties in various industries such as biomedicine, aerospace, automotive, and energy. According to previous research, fresh flowability at the time of extrusion affects the mechanical properties of 3DPC technology (Pal et al., 2014; Seidel and Zaeh, 2018; Wolfs et al., 2018). Various studies show that when silica fume is added to concrete, calcium silicate hydrate (C-S-H) is formed during hydration. C-S-H improves the durability and mechanical properties of concrete, thus creating a bond between layers of 3D printed concrete (Zhang et al., 2018b; Hosseini et al., 2019; Al-Muhit and Sanchez, 2020). According to the geometry of 3D printed concrete, the interface bond between layers and different types of reinforcement, the mechanical properties, and the failure modes of 3D printed concrete are different from conventional concrete. Therefore, there is not yet a design theory for concrete 3D printing. Table 6 shows many parameters, such as design patterns, height of layer patterns, etc., for different studies (Salet et al., 2018; Suiker, 2018; Wolfs and Suiker, 2019).
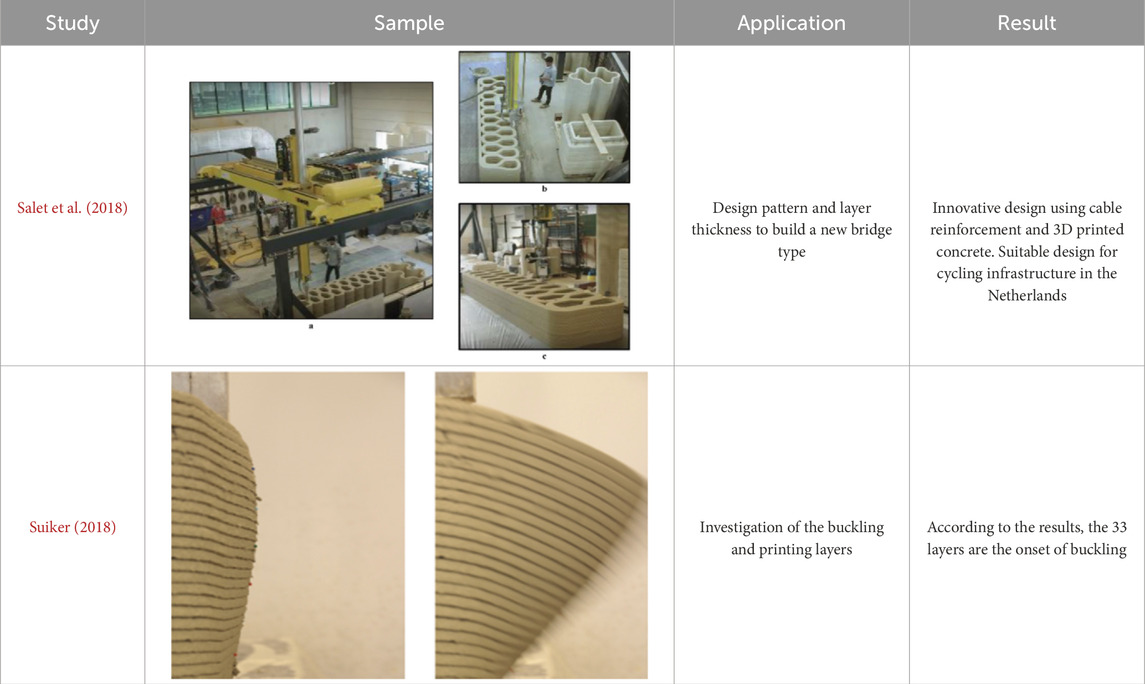
Table 6. Effect of geometry on the mechanical properties and applications of 3D printed concrete structures.
One important factor in improving the mechanical properties of 3D printed concrete is the distribution of fine aggregates between cement and water. Due to adding the fine aggregates, the nozzle must be so narrow for these sizes to overcome the size of extrusion aggregates (Rushing et al., 2017). Unlike other types of 3D printed concrete, different studies show that concrete with recycled aggregate and industrial waste to replace natural sand had lower concrete mechanical properties (Ma et al., 2018; Xiao et al., 2020). Another important factor is the mixture properties of concrete. According to the research, the compressive strength of 3D printed concrete is less than that of cast concrete with the same composition. Therefore, when the compression of 3D printed concrete printers is reduced, the strength-loss coefficient is used to find the reduction of compressive strength. As a sample, when F-class fly ash and silica fume are added to concrete, they help to decrease the coefficient of strength-loss (Nerella et al., 2019). For example, the water-to-binder ratio and surface moisture condition are two important factors that change the mechanical properties. Results illustrated that although water surface free water is an essential issue in concrete printing, adding more water to concrete due to bonding the cement matrix will weaken the compressive strength of concrete (Papachristoforou et al., 2018; Sanjayan et al., 2018; Keita et al., 2019). Another factor related to tensile and compressive strengths is anisotropic properties. When concrete is printed in the anisotropic direction, the resistance between the layers increases. Another issue is the time interval between printed strings and speed. If the time interval was short, the walls might collapse, and if the time interval was long, the bond between the layers would weaken (Table 7) (Buswell et al., 2018; Paul et al., 2018).
Finally, various research shows that although the addition of fibers, additive powder, and different types of aggregates may improve the strength of concrete, the geometry of the structure, the method of mixing concrete, the ratio of water to binder, etc., can improve the strength of concrete.
There are different applications for 3DPC technologies. Table 7 illustrates the opportunities and challenges of 3DPC technology in construction. The largest challenges in 3DPC technology are improving the strength of the building, flowability, thermal and acoustic behavior, and the rheology of concrete. Other challenges are related to controls of layers, layer properties, and designing large-scale printers.
Using 3DPC technology has numerous benefits. For instance, there are opportunities to increase the usage of recycled materials while reducing building time, carbon footprint, labor requirements, and construction and operation expenses. One of the main benefits of using 3DPC technology over traditional construction methods is that it allows for faster construction than the traditional construction of blocks and mortar.
Figure 6 illustrates the differences between classical construction and 3D printed concrete construction. In terms of economics, it is a zero-waste, low labor cost, and faster and more accurate way to create complicated members. According to Table 8, 3D printed concrete can be used in various structures such as bridges, bus stations, architectural issues, on-site construction buildings, and reinforced 3D printed concrete. Considering Table 9, the common application of 3DPC technology is reducing the construction time and supporting building structures in different forms and designs.
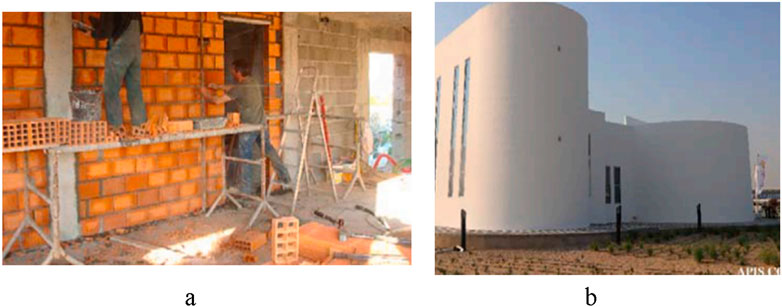
Figure 6. Differences between classical and 3D printed concrete building [based on Pessoa et al. (2021)]: (A) Classical construction and (B) 3D printed concrete [based on Apis Cor. Groundbreaking project: a collaborative project with Dubai municipality (2019)].
3.2 Mechanical properties of 3DPRC
One important factor to improve the strength of 3DPRC is the use of auxetic material. Auxetic materials are known to be energy absorbent and have negative Poisson ratios (Evans, 1991). Evans et al. (1991) were the first to call this type of material “auxetic.” Lakes (1987) achieved a −0.7 Poisson ratio for the first time. Auxetic materials have high mechanical properties such as shear resistance, indentation resistance, potential energy, absorption capacity, and fracture resistance (Table 10) (Lakes, 1993; Evans and Alderson, 2000; Hou et al., 2015; Hu et al., 2019; Li and Rudykh, 2019; Wang, 2019).
Due to the desirable mechanical properties of auxetic materials, many researchers are attracted to the use of these types of materials to improve the mechanical properties of concrete. Zhong et al. (2022) reinforced concrete with auxetic material for energy absorption performance and low density. They used alloy auxetic material to reinforce concrete. They understood that concrete reinforced with auxetic material improves the peak of compressive strength. GÖDEK et al. (2023) studied the effect of 3D concrete printed with different patterns of reinforced cement matrix. They analyzed honeycomb and triangular patterns printed by PLA, ABS, and polyethylene terephthalate glycol (PETG) as materials. They found that when the honeycomb pattern is used with different materials, the load deflection becomes deflection hardening. In another investigation on 3DPRC, Barri et al. (2023) reinforced a conductive cement matrix with auxetic polymer lattices. In this process, the cement is made conductive with graphite powder, with electrical contact between the layers under mechanical stress. The system of auxetic polymer networks achieved more than 15% compressibility cycle loading improvement.
Many studies on reinforced 3D printed concrete have found that when concrete is reinforced with 3D printed polymer, the flexural strength may increase. Another positive effect of adding 3D printed polymer to concrete is changing the strain behavior in terms of strain softening and strain hardening.
For example, when Katzer and Szatkiewicz (2020) reinforced cement mortar with honeycomb and found that the height-to-thickness ratio was high, the flexural strength increased to more than 6 kN, and the strain behavior changed to strain hardening. In another example, Salazar et al. (2020) reinforced UHPC with a 3D printing lattice produced with polymers. The results show that when lattice structure was added to UHPC, the flexural strength improved, and the strain behavior of the beam transferred to strain hardening. Other studies show different results. For example, when Hematibahar et al. (2023) reinforced high-performance concrete (HPC) with a 3D printing shell structure, although the flexural deformation of the beam improved compared to the control samples, the flexural strength decreased, and flexural strain changed to strain softening. In another example, UHPC was reinforced with 3D printing trusses. The authors understood that the flexural improved while the behavior of the beam changed to strain softening (Chiadighikaobi et al., 2024a). Reinforced 3D printed concrete can increase flexural strength. This type of reinforcement can sometimes change strain to strain softening or strain hardening. Differences between concrete reinforced with 3D printing and concrete with steel rebar are mostly related to the strain behavior of concrete beams. The concrete reinforced with steel rebar can change the strain behavior to strain hardening. For example, Belay et al. (2024) compared the concrete reinforced with steel rebar and GFRP and BFRP. They found when concrete was reinforced with different types of rebar, the strain behavior changed to strain hardening. Another study indicated that when concrete was reinforced with steel rebar, the flexural strain behavior changed to strain hardening (Imjai et al., 2024). The differences between reinforced concrete beams and reinforced 3D printed concrete are usually in terms of the strain-hardening behavior of reinforced concrete through steel and rebar types.
4 Discussion
The most important difference between 3DPC and 3DPRC is the difference between the applications of these two technologies. 3DPC technology is related to casting concrete in different ways to achieve the highest mechanical properties, whereas 3DPRC tries to improve the mechanical properties of concrete structural elements. 3DPRC tries to improve the deflection of concrete to the hardening phase.
As an example of 3DPC, Vaitkevicius et al. (2018) created a new binder to improve the compressive strength of 3D printed concrete to 50 MPa over 28-day curing periods. They used cement, silica fume, glass powder, gypsum, and sand (0/2 mm). In their mixture design, the water/cement ratio was 0.46, and the hydration temperature was 36.75
Figure 7 illustrates the differences between 3DPC and 3DPRC technology. 3DPC technology attempts to increase the response to the challenge of population increase by building 3D prefabricated concrete structures and improving the properties of structural materials, and the current technology has a more general view of 3D printing reinforced concrete (Figure 7A). By increasing the mechanical properties of concrete, 3DPRC technology paves its way into the world of civil engineering as new research (Figure 7B).
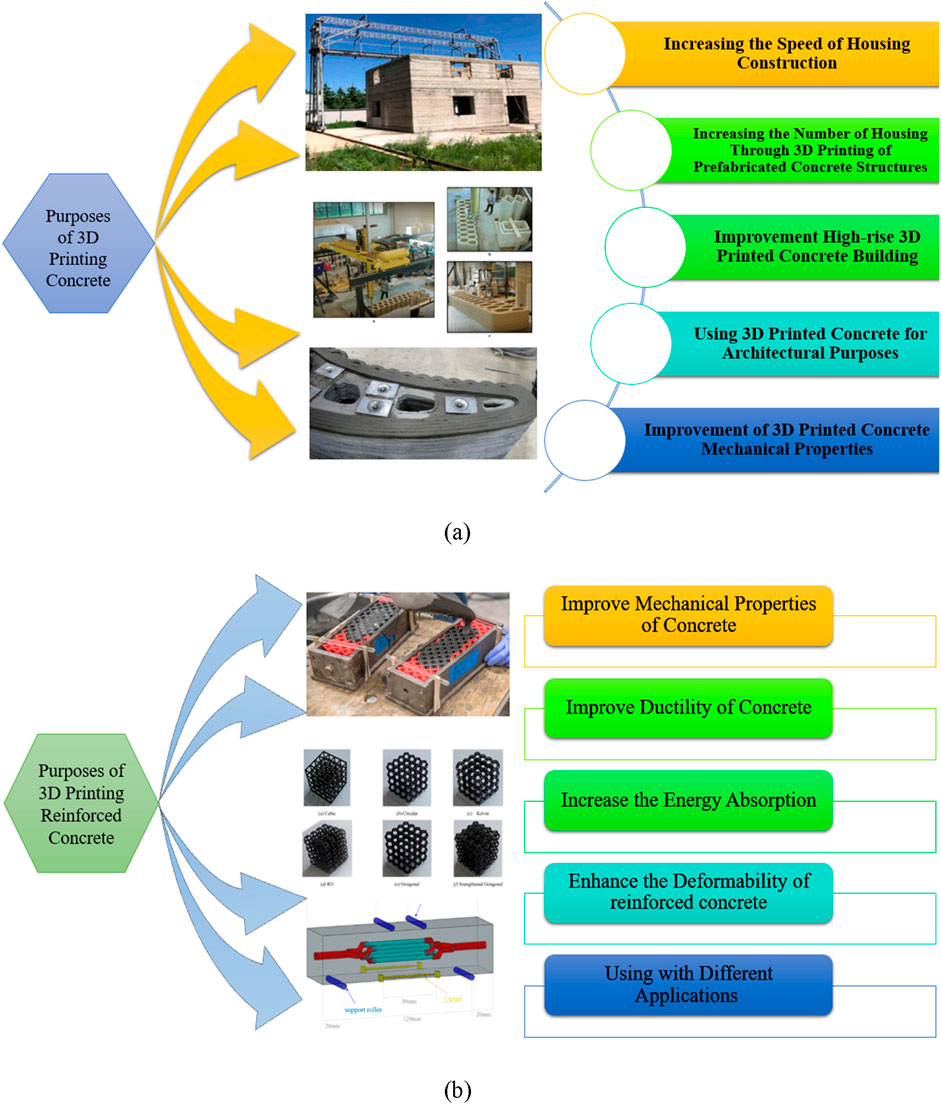
Figure 7. Comparison between (A) 3D printed concrete technology and (B) 3D printing reinforced concrete technology.
This research shows that researchers use machine learning and artificial intelligence (AI) to predict the mechanical properties of 3DPC and 3DPRC. Another proposal is to combine 3DPC and 3DPRC and use machine learning and artificial intelligence to predict the mechanical properties and mix design. The design is 3D printed concrete with a 3D printing reinforced concrete reinforced pattern (Hematibahar et al., 2022; Hematibahar et al., 2024b; Chiadighikaobi et al., 2024b).
5 Conclusion
This study analyzed two types of 3D printing technology in concrete technology. Both types of 3DPC technologies help to protect buildings and structures. 3D concrete printers can extrude and print concrete without the need for molds. This technology attempts to print large-scale buildings with high-strength materials and mortars. The reviewed studies employ diverse concrete types and components, which include various types of aggregates in varying sizes. Furthermore, 3D printing has the advantage of not affecting the environment because it replaces the need for casting. Many researchers have studied the mixture of concrete, rheology, flow ability, printability, etc. Finally, 3DPC technology allows for the construction of large-scale concrete structures.
Unlike 3DPC technology, 3DPRC attempts to improve the strain hardening of concrete and cement matrix reinforced by 3D printing structures. When 3DPRC is added to cement materials, the mechanical properties improve. In this way, different types of patterns have different effects on the cement matrix and concrete. For example, auxetic materials improve the strain hardening of concrete. The main results are listed below:
• Both types of 3D printing technologies can improve concrete technology and protect buildings under different loadings.
• Concrete with 3DPRC technology has better mechanical qualities under various loading conditions, including dynamic and seismic loadings.
• 3D printed concrete can make any concrete structure with a variety of designs and different concrete mixing methods. This method can protect various aspects of buildings from an environmental point of view.
• In this study, it is suggested that researchers investigate the 3DPRC columns, the response of 3D printing reinforced concrete structures with seismic dampers, and increasing the scale of experiments due to the rapid progress in this scientific field. In addition, the combination of 3DPC and 3DPRC technology is a possible proposal.
Author contributions
KM: conceptualization, data curation, formal analysis, software, and writing–original draft. NV: funding acquisition, conceptualization, investigation, methodology, project administration, resources, validation, visualization, and writing–review and editing. MH: conceptualization, writing–original draft, data curation, formal analysis, investigation, methodology, and writing–review and editing. TG: conceptualization, data curation, formal analysis, investigation, software, validation, and writing–review and editing.
Funding
The author(s) declare financial support was received for the research, authorship, and/or publication of this article. The research is partially funded by the Ministry of Science and Higher Education of the Russian Federation as part of the World-class Research Center program Advanced Digital Technologies (contract No. 075–15-2022-311 dated 04/20/2022).
Conflict of interest
The authors declare that the research was conducted in the absence of any commercial or financial relationships that could be construed as a potential conflict of interest.
Publisher’s note
All claims expressed in this article are solely those of the authors and do not necessarily represent those of their affiliated organizations, or those of the publisher, the editors and the reviewers. Any product that may be evaluated in this article, or claim that may be made by its manufacturer, is not guaranteed or endorsed by the publisher.
References
Abdalla, H., Parvez Fattah, K., Abdallah, M., and K. Tamimi, A. (2021). Environmental footprint and economics of a full-scale 3D-printed house. Sustainability 13, 11978. doi:10.3390/su132111978
Abeykoon, C., Sri-Amphorn, P., and Fernando, A. (2020). Optimization of fused deposition modeling parameters for improved PLA and ABS 3D printed structures. Int. J. Lightweight Mater. Manuf. 3, 284–297. doi:10.1016/j.ijlmm.2020.03.003
Al-Muhit, B., and Sanchez, F. (2020). Nano-engineering of the mechanical properties of to bermorite 14 Å with graphene via molecular dynamics simulations. Constr. Build. Mater 233, 117237. doi:10.1016/j.conbuildmat.2019.117237
Arosio, F., Castoldi, L., Ferlazzo, L., and Forzatti, P. (2007). Influence of solfonated melamine formaldehyde condensate on the quality of building blocks production by extrusion of cement–clay pastes. Appl. Clay Sci. 35, 85–93. doi:10.1016/j.clay.2006.06.004
Asprone, D., Auricchio, F., Menna, C., and Mercuri, V. (2018). 3D printing of reinforced concrete elements: technology and design approach. Constr. Build. Mater 165, 218–231. doi:10.1016/j.conbuildmat.2018.01.018
ASTM C143/C143M-03 (2003). Standard Test Method for Slump of Hydraulic Cement Concrete. American Society for Testing and Materials (ASTM), 4
Bai, G., Wang, L., Ma, G., Sanjayan, J., and Bai, M. (2021). 3D printing eco-friendly concrete containing under-utilised and waste solids as aggregates. Cem. Concr. Compos. 120, 104037. doi:10.1016/j.cemconcomp.2021.104037
Banfill, P. F. G., Starrs, G., Derruau, G., McCarter, W. J., and Chrisp, T. M. (2006). Rheology of low carbon fibre content reinforced cement mortar. Cem. Concr. Compos. 28, 773–780. doi:10.1016/j.cemconcomp.2006.06.004
Bani Ardalan, R., Joshaghani, A., and Hooton, R. D. (2017). Workability retention and compressive strength of self-compacting concrete incorporating pumice powder and silica fume. Constr. Build. Mater 134, 116–122. doi:10.1016/j.conbuildmat.2016.12.090
Barri, K., Zhang, Q., Kline, J., Lu, W., Luo, J., Sun, Z., et al. (2023). Multifunctional nanogenerator-integrated metamaterial concrete systems for smart civil infrastructure. Adv. Mater 35, 2211027. doi:10.1002/adma.202211027
Belay, A. A., Krassowska, J., and Kosior-Kazberuk, M. (2024). Comparative performance analysis of small concrete beams reinforced with steel bars and non-metallic reinforcements. Appl. Sci. 3957, 3957. doi:10.3390/app14103957
Bhagia, S., Bornani, K., Agrawal, R., Satlewal, A., Durkovicˇ, J., Lagana, R., et al. (2021). Critical review of FDM 3D printing of PLA biocomposites filled with biomass resources, characterization, biodegradability, upcycling and opportunities for biorefineries. Appl. Mater. Today. 24, 101078. doi:10.1016/j.apmt.2021.101078
Birchall, J. D., Howard, A. J., and Kendall, K. (1981). Flexural strength and porosity of cements. Nature 289, 388–390. doi:10.1038/289388a0
Bol, J. M. R., Xu, Y., and Šavija, B. (2024). Printing path-dependent two-scale models for 3D printed planar auxetics by material extrusion. Addit. Manuf. 89, 104293. doi:10.1016/j.addma.2024.104293
Bos, F. P., Bosco, E., and Salet, T. A. M. (2019). Ductility of 3D printed concrete reinforced with short straight steel fibers. irtual Phys. Prototyp. 14, 160–174. doi:10.1080/17452759.2018.1548069
Buswell, R. A., De Silva, W. R. L., Jones, S. Z., and Dirrenberger, J. (2018). Cement and Concrete Research 3D printing using concrete extrusion: a roadmap for research. Cem. Concr. Res. 112, 37–49. doi:10.1016/j.cemconres.2018.05.006
Buswell, R. A., Soar, R. C., Gibb, A. G. F., and Thorpe, A. (2007). Freeform construction: mega-scale rapid manufacturing for construction. Automation Constr. 16, 224–231. doi:10.1016/j.autcon.2006.05.002
Cao, M., Xu, L., and Zhang, C. (2017). Rheological and mechanical properties of hybrid fiber reinforced cement mortar. Constr. Build. Mater 171, 736–742. doi:10.1016/j.conbuildmat.2017.09.054
Chajec, A., and Šavija, B. (2024). The effect of using surface functionalized granite powder waste on fresh properties of 3D-printed cementitious composites. J. Build. Eng. 97, 110707. doi:10.1016/j.jobe.2024.110707
Chen, M., Yao, X., Zhu, L., Yin, L., Xiong, Y., and Hu, N. (2023). Geometric design and performance of single and dual-printed lattice-reinforced cementitious composite. Cem. Concr. Compos. 143, 105266. doi:10.1016/j.cemconcomp.2023.105266
Chiadighikaobi, P. C., Hasanzadeh, A., Hematibahar, M., Kharun, M., Mousavi, M. S., A. Stashevskaya, N., et al. (2024a). Evaluation of the mechanical behavior of high-performance concrete (HPC) reinforced with 3D-Printed trusses. Results Eng. 22, 102058. doi:10.1016/j.rineng.2024.102058
Chiadighikaobi, P. C., Hematibahar, M., Kharun, M., A. Stashevskaya, N., and Camara, K. (2024b). Predicting mechanical properties of self-healing concrete with Trichoderma Reesei Fungus using machine learning. Cogent Eng. 11, 2307193. doi:10.1080/23311916.2024.2307193
Chu, S., Li, L., and Kwan, A. (2021). Development of extrudable high strength fiber reinforced concrete incorporating nano calcium carbonate. Addit. Manuf. 37, 101617. doi:10.1016/j.addma.2020.101617
Cordeiro, G. C., de Alvarenga, L. M. S. C., and Rocha, C. A. A. (2016). Rheological and mechanical properties of concrete containing crushed granite fine aggregate. Constr. Build. Mater. 111, 766–773. doi:10.1016/j.conbuildmat.2016.02.178
da Silva, M. A., Pepe, M., de Andrade, R. G. M., Pfeil, M. S., and Toledo Filho, R. D. (2017). Rheological and mechanical behavior of High strength steel fiber-river gravel self compacting concrete. Constr. Build. Mater. 150, 606–618. doi:10.1016/j.conbuildmat.2017.06.030
De Schutter, G., Lesage, K., Mechtcherine, V., Nerella, V. N., Habert, G., and Agusti Juan, I. (2018). Vision of 3D printing with concrete — technical, economic and environmental potentials. Cem. Concr. Res. 112, 25–36. doi:10.1016/j.cemconres.2018.06.001
Ding, T., Xiao, J., Zou, S., and Yu, J. (2021). Flexural properties of 3D printed fibre-reinforced concrete with recycled sand. Constr. Build. Mater. 288, 123077. doi:10.1016/j.conbuildmat.2021.123077
Dvorkin, L., Marchuk, V., Mróz, K., Maroszek, M., and Hager, I. (2024). Energy-efficient mixtures suitable for 3D technologies. Appl. Sci. 14, 3038. doi:10.3390/app14073038
Evangelista, L., and de Brito, J. (2007). Mechanical behaviour of concrete made with fine recycled concrete aggregates. Cem. Concr. Compos. 29, 397–401. doi:10.1016/j.cemconcomp.2006.12.004
Evans, K. E. (1991). Auxetic polymers: a new range of materials. Endeavour 4, 170–174. doi:10.1016/0160-9327(91)90123-s
Evans, K. E., and Alderson, A. (2000). Auxetic materials: functional materials and structures from lateral thinking. Adv. Mater 12, 617–628. doi:10.1002/(sici)1521-4095(200005)
Evans, K. E., Nkansah, M. A., Hutchinson, I. J., and Rogers, S. C. (1991). Molecular network design. Nature 353, 124. doi:10.1038/353124a0
Faludi, J., Bayley, C., Bhogal, S., and Iribarne, M. (2015). Comparing environmental impacts of additive manufacturing vs traditional machining via life-cycle assessment. Rapid Prototyp. J. 21, 14–33. doi:10.1108/rpj-07-2013-0067
Fambri, L., and Migliaresi, C. (2010). Crystallization and thermal properties. Poly(Lactic acid): synthesis, structures, properties, processing, and applications. John, 113–124. doi:10.1002/9780470649848.ch9
Favier, A., Hot, J., Habert, G., Roussel, N., and de Lacaillerie, J. B. D. E. (2014). Flow properties of MK-based geopolymer pastes. A comparative study with standard Portland cement pastes. Soft Matter 10, 1134–1141. doi:10.1039/c3sm51889b
Feng, P., and Meng, X.Zhang (2015). Mechanical behavior of FRP sheets reinforced 3D elements printed with cementitious materials. Compos. Struct. 134, 331–342. doi:10.1016/j.compstruct.2015.08.079
Fernandez-Vicente, M., Calle, W., Ferrandiz, S., and Conejero, A. (2016). Effect of infill parameters on tensile mechanical behavior in desktop 3D printing. Addit. Manuf. 3, 183–192. doi:10.1089/3dp.2015.0036
Ferrara, L., Park, Y.-D., and Shah, S. P. (2007). A method for mix-design of fiber-reinforced self-compacting concrete. Cem. Concr. Res. 37, 957–971. doi:10.1016/j.cemconres.2007.03.014
Furet, B., Poullain, P., and Garnier, S. (2019). 3D printing for construction based on a complex wall of polymer-foam and concrete. Addit. Manuf. 28, 58–64. doi:10.1016/j.addma.2019.04.002
Gödek, E., Evi̇k, S., and Özdi̇lli̇, O. (2023). Pattern and filament optimization for 3D-printed reinforcements to enhance the flexural behavior of cement-based composites. J. Sustain. Constr. Mater. Technol. 8, 47–56. doi:10.47481/jscmt.1207739
Grünewald, S. (2011). “Fibre reinforcement and the rheology of concrete,” in Woodhead Publishing Series in Civil and Structural Engineering, Understanding the Rheology of Concrete (Woodhead Publishing), 229–256. doi:10.1016/B978-0-85709-028-7.50009-1
Güneyisi, E., Atewi, Y. R., and Hasan, M. F. (2019). Fresh and rheological properties of glass fiber reinforced self-compacting concrete with nanosilica and fly ash blended. Constr. Build. Mater. 211, 349–362. doi:10.1016/j.conbuildmat.2019.03.087
Hambach, M., Moller, H., Neumann, T., and Volkmer, D. (2016). Portland cement paste with aligned carbon fibers exhibiting exceptionally high flexural strength (>100 MPa). Cem. Concr. Res. 89, 80–86. doi:10.1016/j.cemconres.2016.08.011
Hambach, M., and Volkmer, D. (2017). Properties of 3D-printed fiber-reinforced Portland cement paste. Cem. Concr. Compos 79, 62–70. doi:10.1016/j.cemconcomp.2017.02.001
Hamedanimojarrad, P., Adam, G., Ray, A., Thomas, P., and Vessalas, K. (2012). Development of shrinkage resistant microfibre-reinforced cement-based composites. Open Eng. 2, 289–295. doi:10.2478/s13531-011-0065-y
Hao, W., Liu, J., and Kanwal, H. (2023). Compressive properties of cementitious composites reinforced by 3D printed PA 6 lattice. Polym. Test. 117, 107811. doi:10.1016/j.polymertesting.2022.107811
He, Y., Zhang, Y., Zhang, C., and Zhou, H. (2020). Energy-saving potential of 3D printed concrete building with integrated living wall. Energy Build. 222, 110110. doi:10.1016/j.enbuild.2020.110110
Hemant, Y. L., Dhonde Thomas, B., Hsu, T. C., and Vogel, J. (2007). Fresh and hardened properties of self-consolidating fiber-reinforced concrete. Mater. J. 104 (5), 491–500.
Hematibahar, M., Hasanzadeh, A., Ivanovich Vatin, N., Kharun, M., and Shooshpasha, I. (2023). Influence of 3D-printed reinforcement on the mechanical and fracture characteristics of ultra high performance concrete. Results Eng 19, 101365. doi:10.1016/j.rineng.2023.101365
Hematibahar, M., Hasanzadeh, A., Kharun, M., Beskopylny, A. N., Stel’makh, S. A., and Shcherban’, E. M. (2024a). The influence of three-dimensionally printed polymer materials as trusses and shell structures on the mechanical properties and load-bearing capacity of reinforced concrete. Materials 17, 3413. doi:10.3390/ma17143413
Hematibahar, M., Ivanovich Vatin, N., A. Alaraza, H., Khalilavi, H., and Kharun, M. (2022). The prediction of compressive strength and compressive stress-strain of basalt fiber reinforced high-performance concrete using classical programming and logistic map algorithm. Materials, 6975. doi:10.3390/ma15196975
Hematibahar, M., Kharun, M., Beskopylny, A., Stel’makh, S., Shcherban, E., and Razveeva, I. (2024b). Analysis of models to predict mechanical properties of high-performance and ultra-high-performance concrete using machine learning. J. Compos. Sci. 8, 287. doi:10.3390/jcs8080287
Higgins, D. D., and Bailey, J. E. (1976). Fracture measurements on cement paste. J. Mater. Sci. 11, 1995–2003. doi:10.1007/BF02403347
Hosseini, E., Zakertabrizi, M., Korayem, A. H., and Xu, G. (2019). A novel method to enhance the interlayer bonding of 3D printing concrete: an experimental and computational investigation. Cem. Concr. Compos 99, 112–119. doi:10.1016/j.cemconcomp.2019.03.008
Hou, S. J., Liu, T. Q., Zhang, Z. D., Han, X., and Li, Q. (2015). How does negative Poisson’s ratio of foam filler affect crashworthiness? Mater Des. 82, 247–259. doi:10.1016/j.matdes.2015.05.050
Hu, J., Xu, X., Cao, C., Tian, Z., Ma, Y., Sun, X., et al. (2024). Vibration position detection of robot arm based on feature extraction of 3D lidar. Sensors 24, 6584. doi:10.3390/s24206584
Hu, L. L., Zhou, M. Z., and Deng, H. (2019). Dynamic indentation of auxetic and non-auxetic honeycombs under large deformation. Compos Struct. 207, 323–330. doi:10.1016/j.compstruct.2018.09.066
Imjai, T., Aosai, P., Garcia, R., Raman, S. N., and Chaudhary, S. (2024). Deflections of high-content recycled aggregate concrete beams reinforced with GFRP bars and steel fibres. Eng. Struct. 312, 118247. doi:10.1016/j.engstruct.2024.118247
Jiang, J., Zhou, W., Gao, Y., Wang, L., Wang, F., Chu, H. Y., et al. (2019). Feasibility of manufacturing ultra-high performance cement-based composites (UHPCCs) with recycled sand: a preliminary study. Waste Manag. 83, 104–112. doi:10.1016/j.wasman.2018.11.005
Jiang, X., Li, Y., Yang, Z., Li, Y., and Xiong, B. (2024). Harnessing path optimization to enhance the strength of three-dimensional (3D) printed concrete. Buildings 14, 455. doi:10.3390/buildings14020455
Katzer, J., and Szatkiewicz, T. (2020). Effect of 3D printed spatial reinforcement onFlexural characteristics of conventional mortar. Materials 13, 3133. doi:10.3390/ma13143133
Kazemian, A., Yuan, X., Cochran, E., and Khoshnevis, B. (2017). Cementitious materials for construction-scale 3D printing: laboratory testing of fresh printing mixture. Constr. Build. Mater. 145, 639–647. doi:10.1016/j.conbuildmat.2017.04.015
Keating, S. J., Leland, J. C., Cai, L., and Oxman, N. (2017). Toward site-specific and self-sufficient robotic fabrication on architectural scales. Robotics 2, eaam8986. doi:10.1126/scirobotics.aam8986
Keita, E., Bessaies-Bey, H., Zuo, W., Belin, P., and Roussel, N. (2019). Weak bond strength between successive layers in extrusion-based additive manufacturing: measurement and physical origin. Cem. Concr. Res. 123, 105787. doi:10.1016/j.cemconres.2019.105787
Khoshnevis, B. (2004). Automated construction by contour crafting—related robotics and information technologies. Autom. Constr. 13, 5–19. doi:10.1016/j.autcon.2003.08.012
Khoshnevis, B., and Dutton, R. (1998). Innovative rapid prototyping process makes large sized, smooth surfaced complex shapes in a wide variety of materials. Mater. Technol. 13, 53–56. doi:10.1080/10667857.1998.11752766
Khoshnevis, B., Hwang, D., Yao, K. T., and Yeh, Z. (2006). Mega-scale fabrication by contour crafting. Int. J. Ind. Syst. Eng. 1, 301. doi:10.1504/IJISE.2006.009791
Kuznetsov, D. V., Klyuev, S. V., Ryazanov, A. N., Sinitsin, D. A., Pudovkin, A. N., Kobeleva, E. V., et al. (2023). Dry mixes on gypsum and mixed bases in the construction of low-rise residential buildings using 3D printing technology. Constr. Mater. Prod. 6, 1–5. doi:10.58224/2618-7183-2023-6-6-5
Labonnote, N., Rønnquist, A., Manum, B., and Rüther, P. (2016). Additive construction: state-of-the-art, challenges and opportunities. Autom. Constr. 72, 347–366. doi:10.1016/j.autcon.2016.08.026
Lakes, R. (1987). Foam structures with a negative Poisson’s ratio. Science 235, 1038–1040. doi:10.1126/science.235.4792.1038
Lakes, R. (1993). Advances in negative Poisson’s ratio materials. Adv. Mater 5, 293–296. doi:10.1002/adma.19930050416
Lao, J.-C., Ma, R.-Y., Xu, L.-Y., Li, Y., Shen, Y.-N., Yao, J., et al. (2024). Fly ash-dominated high-strength engineered/strain-hardening geopolymer composites (HS-EGC/SHGC): influence of alkalinity and environmental assessment. J. Clean. Prod. 447, 141182. doi:10.1016/j.jclepro.2024.141182
Le, T. T., Austin, S. A., Lim, S., Buswell, R. A., Gibb, A. G., and Thorpe, T. (2012). Mix design and fresh properties for high-performance printing concrete. Mater. Struct. 45, 1221–1232. doi:10.1617/s11527-012-9828-z
Li, J., and Rudykh, S. (2019). Tunable microstructure transformations and auxetic behavior in 3D-printed multiphase composites: the role of inclusion distribution. Compos B Eng. 172, 352–362. doi:10.1016/j.compositesb.2019.05.012
Li, Q.-H., Luo, A.-M., Huang, B.-T., Wang, G.-Z., and Xu, S.-L. (2024). Bond behavior between steel bar and strain-hardening fiber-reinforced cementitious composites under fatigue loading. Eng. Struct. 314, 118354. doi:10.1016/j.engstruct.2024.118354
Lim, S., Buswell, R. A., Le, T. T., Austin, S. A., Gibb, A. G. F., and Thorpe, T. (2012). Developments in construction-scale additive manufacturing processes. Autom. Constr. 21, 262–268. doi:10.1016/j.autcon.2011.06.010
Liu, Z., Li, M., Tay, Y. W. D., Weng, Y., Wong, T. N., and Tan, M. J. (2020). Rotation nozzle and numerical simulation of mass distribution at corners in 3D cementitious material printing. Addit. Manuf. 34, 101190. doi:10.1016/j.addma.2020.101190
Lossier, H. (1946). Cements with controlled expansions and their applications to prestressed concrete. J. Estructural 24, 503–534.
Lowke, D., Dini, E., Perrot, A., Weger, D., Gehlen, C., and Dillenburger, B. (2018). Particle-bed 3D printing in concrete construction – possibilities and challenges. Cem. Concr. Res. 112, 50–65. doi:10.1016/j.cemconres.2018.05.018
Lowke, D., Vandenberg, A., Pierre, P., Thomas, A., Kloft, H., and Hack, N. (2021). Injection 3D concrete printing in a carrier liquid - underlying physics and applications to lightweight space frame structures. Cem. Concr. Compos. 124, 104169. doi:10.1016/j.cemconcomp.2021.104169
Lpez-Mesa, B., Tomßs, A., and Gallego, T. (2009). Comparison of environmental impacts of building structures with in situ cast floors and with precast concrete floors. Build. Environ. 44, 699e712. doi:10.1016/j.buildenv.2008.05.017
Luo, C., Ren, R., Han, D., Zhang, X. G., Zhong, R., Zhang, X. Y., et al. (2022). A novel concrete-filled auxetic tube composite structure: design and compressive characteristic study. Eng. Struct. 268, 114759. doi:10.1016/j.engstruct.2022.114759
Ma, G., Li, Z., and Wang, L. (2018). Printable properties of cementitious material containing copper tailings for extrusion based 3D printing. Constr. Build. Mater 162, 613–627. doi:10.1016/j.conbuildmat.2017.12.051
Malaeb, Z., AlSakka, F., and Hamzeh, F. (2019). “3D concrete printing: machine design, mix proportioning, and mix comparison between different machine setups,” in 3D concr. Print. Technol. (Elsevier), 115–136. doi:10.1016/B978-0-12-815481-6.00006-3
Malaszkiewicz, D. (2017). Influence of polymer fibers on rheological properties of cement mortars. Open Eng. 7, 228–236. doi:10.1515/eng-2017-0029
Marchment, T., and Sanjayan, J. (2020). Mesh reinforcing method for 3D concrete printing. Automation Constr. 109, 102992. doi:10.1016/j.autcon.2019.102992
Martinie, L., Rossi, P., and Roussel, N. (2010). Rheology of fiber reinforced cementitious materials: classification and prediction. Cem. Concr. Res. 40, 226–234. doi:10.1016/j.cemconres.2009.08.032
Mechtcherine, V., Nerella, V. N., Will, F., Näther, M., Otto, J., and Krause, M. (2019). Large-scale digital concrete construction – CONPrint3D concept for on-site, monolithic 3D-printing. Autom. Constr. 107, 102933. doi:10.1016/j.autcon.2019.102933
Michels, J., Christen, R., and Waldmann, D. (2013). Experimental and numerical investigation on postcracking behavior of steel fiber reinforced concrete. Eng. Fract. Mech. 98, 326–349. doi:10.1016/j.engfracmech.2012.11.004
Miller, W., Ren, Z., Smith, C. W., and Evans, K. W. (2012). A negative Poisson’s ratio carbon fibre composite using a negative Poisson’s ratio yarn reinforcement. Compos. Sci. Technol. 72, 761–766. doi:10.1016/j.compscitech.2012.01.025
Momeni, K., Ivanovich Vatin, N., Hematibahar, M., and Gebre, T. (2024). Repair overlays of modified polymer mortar containing glass powder and composite fibers-reinforced slag: mechanical properties, energy absorption, and adhesion to substrate concrete. Front. Built Environ. 10, 1479849. doi:10.3389/fbuil.2024.1479849
Mukhametrakhimov (2022). Investigation of plasticizing additives based on polycarboxylate esters on the properties of concretes formed by 3d printing. Constr. Mater. Prod. 5, 42–58. doi:10.58224/2618-7183-2022-5-5-42-58
Muthukrishnan, S., Kua, H. W., Yu, L. N., and Chung, J. K. (2020). Fresh properties of cementitious materials containing rice husk ash for construction 3D printing. J. Mater. Civ. Eng. 32, 04020195. doi:10.1061/(asce)mt.1943-5533.0003230
Nerella, V. N., Hempel, S., and Mechtcherine, V. (2019). Effects of layer-interface properties on mechanical performance of concrete elements produced by extrusion-based 3D-printing. Constr. Build. Mater 205, 586–601. doi:10.1016/j.conbuildmat.2019.01.235
Nguyen-Van, V., Choudhry, N. C., Panda, B., Xuan, H. N., and Tran, P. (2022). Performance of concrete beam reinforced with 3D printed Bioinspired primitive scaffold subjected to three-point bending. Automation Constr. 134, 104060. doi:10.1016/j.autcon.2021.104060
Ni, H.-G., and Wang, J.-Z. (2000). Prediction of compressive strength of concrete by neural networks. Cem. Concr. Res. 30, 1245–1250. doi:10.1016/S0008-8846(00)00345-8
Pal, D., Patil, N., Zeng, K., and Stucker, B. (2014). An integrated approach to additive manufacturing simulations using physics based, coupled multiscale process modeling. J. Manuf. Sci. Eng. 136. doi:10.1115/1.4028580
Panda, B., Paul, S. C., and Tan, M. J. (2017). Anisotropic mechanical performance of 3D printed fiber reinforced sustainable construction material. Mater. Lett. 209, 146–149. doi:10.1016/j.matlet.2017.07.123
Papachristoforou, M., Mitsopoulos, V., and Stefanidou, M. (2018). Evaluation of workability parameters in 3D printing concrete. Procedia Struct. Integr. 10, 155–162. doi:10.1016/j.prostr.2018.09.023
Park, K., Hojati, M., Nazarian, S., and Duarte, J. P. (2020). Experimental testing and finite element modeling of 3D-printed reinforced concrete beams. Available at: https://www.researchgate.net/publication/340393925 (Accessed June 21 2024)
Park, K., Memari, M., Hojati, M., Radlińska, A., Pinto Duarte, J., and Nazarian, S. (2024). Effects of anisotropic mechanical behavior on nominal moment capability of 3D printed concrete beam with reinforcement. Buildings 14, 3175. doi:10.3390/buildings14103175
Paul, S. C., Tay, Y. W. D., Panda, B., and Tan, B. (2018). Fresh and hardened properties of 3D printable cementitious materials for building and construction. Arch. Civ. Mech. Eng. 18, 311–319. doi:10.1016/j.acme.2017.02.008
Pessoa, S., Guimaraes, A. S., Lucas, S. S., and Simoes, N. (2021). 3D printing in the construction industry - a systematic review of the thermal performance in buildings. Renew. Sustain. Energy Rev. 141, 110794. doi:10.1016/j.rser.2021.110794
Pham, L., Tran, P., and Sanjayan, J. (2020). Steel fibres reinforced 3D printed concrete: influence of fibre sizes on mechanical performance. Constr. Build. Mater 250, 118785. doi:10.1016/j.conbuildmat.2020.118785
Phuong Bao, T. M., Yeakleang, M., Abdelouhab, S., and Courard, L. (2024). Testing mortars for 3D printing: correlation with rheological behavior. Materials 17, 5002. doi:10.3390/ma17205002
Pimentel Tinoco, M., Gouvêa, L., de Cássia Magalhães Martins, K., Dias Toledo Filho, R., and Aurelio Mendoza Reales, O. (2023). The use of rice husk particles to adjust the rheological properties of 3D printable cementitious composites through water sorption. Constr. Build. Mater 365, 130046. doi:10.1016/j.conbuildmat.2022.130046
Prasittisopin, L., Jiramarootapong, P., Pongpaisanseree, K., and Snguanyat, C. (2019). Lean manufacturing and thermal enhancement of single-layered wall of additive manufacturing (AM) structure. ZKG Int 4, 64–74.
Prudˆencio, L. R. J. (1998). Accelerating admixtures for shotcrete. Cem. Concr. Compos. 20, 213–219. doi:10.1016/s0958-9465(98)80007-3
Rosewitz, J. A., Ashouri Choshali, H., and Rahbar, R. (2019). Bioinspired design of architected cement-polymer composites. Cem. Concr. Compos. 96, 252–265. doi:10.1016/j.cemconcomp.2018.12.010
Rouhana, C. M., Aoun, M. S., Faek, F. S., Eljazzar, M. S., and Hamzeh, F. R. (2014). The reduction of construction duration by implementing contour crafting (3D printing). 22nd Annu. Conf. Int. group lean Constr. Underst. Improv. Proj. based Prod., 1031–1042.
Rushing, T. S., Al-Chaar, G., Eick, B. A., Burroughs, J., Shannon, J., Barna, L., et al. (2017). Investigation of concrete mixtures for additive construction. Rapid Prototyp. J. 23, 74–80. doi:10.1108/rpj-09-2015-0124
Salazar, B., Aghdasi, P., Williams, I., Ostertag, C., and Taylor, H. (2020). Polymer lattice-reinforcement for enhancing ductility of concrete. Mater. Des. 196, 109184. doi:10.1016/j.matdes.2020.109184
Salet, T. A. M., Ahmed, Z. Y., Bos, F. P., and Laagland, H. L. M. (2018). Design of a 3D printed concrete bridge by testing. Virtual Phys. Prototyp. 13, 222–236. doi:10.1080/17452759.2018.1476064
Samad, N. A. I. A., Abdullah, S. R., Ibrahim, M., Shahidan, S., and Ismail, N. (2022). Initial properties of 3D printing concrete using rice husk ash (RHA) as partial cement replacement. IOP Conf. Ser. Earth Environ. Sci. 1022, 012055. doi:10.1088/1755-1315/1022/1/012055
Sanjayan, J. G., Nematollahi, B., Xia, M., and Marchment, T. (2018). Effect of surface moisture on inter-layer strength of 3D printed concrete. Constr. Build. Mater 172, 468–475. doi:10.1016/j.conbuildmat.2018.03.232
Saw, H. A., Villaescusa, E., Windsor, C., and Thompson, G. (2017). Surface support capabilities of freshly sprayed fibre reinforced concrete and safe re-entry time for underground excavations. Tunn. Undergr. Space Technol. 64, 34–42. doi:10.1016/j.tust.2017.01.005
Seidel, C., and Zaeh, M. F. (2018). Multi-scale modelling approach for contributing to reduced distortion in parts made by laser-based powder bed fusion. Procedia CIRP 67, 197–202. doi:10.1016/j.procir.2017.12.199
Senff, L., Modolo, R. C. E., Silva, A. S., Ferreira, V. M., Hotza, D., and Labrincha, J. A. (2014). Influence of red mud addition on rheological behavior and hardened properties of mortars. Build. Mater. 65, 84–91. doi:10.1016/j.conbuildmat.2014.04.104
Senff, L., Modolo, R. C. E., Tobaldi, D. M., Ascençao, G., Hotza, D., Ferreira, V. M., et al. (2015). The influence of TiO2 nanoparticles and poliacrilonitrile fibers on the rheological behavior and hardened properties of mortars. Constr. Build. Mater 75, 315–330. doi:10.1016/j.conbuildmat.2014.11.002
Shakor, P., Nejadi, S., and Paul, G. (2019). A study into the effect of different nozzles shapes and fibre-reinforcement in 3D printed mortar. Materials 12, 1708. doi:10.3390/ma12101708
Singh, A., Liu, Q., Xiao, J., and Lyu, Q. (2022). Mechanical and macrostructural properties of 3D printed concrete dosed with steel fibers under different loading direction. Constr. Build. Mater 323, 126616. doi:10.1016/j.conbuildmat.2022.126616
Skoratko, A., Szatkiewicz, T., Katzer, T., and Jagoda, M. (2022). Mechanical properties of mortar beams reinforced by gyroid 3D printed plastic spatial elements. Cem. Concr. Compos. 134, 104809. doi:10.1016/j.cemconcomp.2022.104809
Souza, M. T., Onghero, L., Nunes Correa, M. A., Selhorst, M., Dias, A., Longuini Repette, W., et al. (2020a). Novel low-cost shrinkage-compensating admixture for ordinary Portland cement. Constr. Build. Mater 230, 117024. doi:10.1016/j.conbuildmat.2019.117024
Souza, M. T., Onghero, L., Repette, W. L., Raupp Pereira, F., and de Oliveira, A. P. N. (2020b). Sustainable cement with Al-anodizing waste: evaluating reactivity and feasibility as a shrinkage-compensating admixture. J. Build. Eng. 30, 101233. doi:10.1016/j.jobe.2020.101233
Suiker, A. S. J. (2018). Mechanical performance of wall structures in 3D printing processes: theory, design tools and experiments. Int. J. Mech. Sci. 137, 145–170. doi:10.1016/j.ijmecsci.2018.01.010
Sun, X., Gao, C., and Wang, H. (2021). Bond performance between BFRP bars and 3D printed concrete. Constr. Build. Mater. 269, 121325. doi:10.1016/j.conbuildmat.2020.121325
Sun, X., Zhou, J., Wang, Q., Shi, J., and Wang, H. (2022). PVA fibre reinforced high-strength cementitious composite for 3D printing: mechanical properties and durability. Addit. Manuf. 49, 102500. doi:10.1016/j.addma.2021.102500
Tay, D. Y. W., Qian, Y., and Tan, M. J. (2019a). Printability region for 3D concrete printing using slump and slump flow test. Compos. Part B 174, 106968. doi:10.1016/j.compositesb.2019.106968
Tay, Y. W. D., Li, M. Y., and Tan, M. J. (2019b). Effect of printing parameters in 3D concrete printing: printing region and support structures. J. Mater. Process. Tech 271, 261–270. doi:10.1016/j.jmatprotec.2019.04.007
Tzortzinis, G., Gross, A., and Gerasimidis, S. (2022). Auxetic boosting of confinement in mortar by 3D reentrant truss lattices for next generation steel reinforced concrete members. Extreme Mech. Lett. 52, 101681. doi:10.1016/j.eml.2022.101681
Vaitkevicius, V., Šerelis, E., and Kerševicius, V. (2018). Effect of ultra-sonic activation on early hydration process in 3D concrete printing technology. Constr. Build. Mater. 169, 354–363. doi:10.1016/j.conbuildmat.2018.03.007
van den Heever, M., du Plessis, A., Kruger, J., and van Zijl, G. (2022). Evaluating the effects of porosity on the mechanical properties of extrusion-based 3D printed concrete. Cem. Concr. Res. 153, 106695. doi:10.1016/j.cemconres.2021.106695
Vatin, N. I., Hematibahar, M., and Gebre, T. (2024). Impact of basalt fiber reinforced concrete in protected buildings: a review. Front. Built Environ. 10. doi:10.3389/fbuil.2024.1407327
Vergara, E. C., Aguirregabiria, B. L., Pérez, J. M. L., and Vacarezza, G. O. (2017). Innovative free-form glass fiber reinforced concrete (GRC) panel. Rev. la Construcción 16, 479–488. doi:10.7764/RDLC.16.3.479
Wan, Z., Xu, Z., and Šavija, B. (2023a). Influence of printing direction on 3D-printed vascular based self-healing cementitious composites. MATEC Web Conf. 378, 02027. doi:10.1051/matecconf/202337802027
Wan, Z., Zhang, Y., Xu, Y., and Savija, B. (2023b). Self-healing cementitious composites with a hollow vascular network created using 3D-printed sacrificial templates. Eng. Struct. 289, 116282. doi:10.1016/j.engstruct.2023.116282
Wang, Z. (2019). Recent advances in novel metallic honeycomb structure. Compos B Eng. 166, 731–741. doi:10.1016/j.compositesb.2019.02.011
Wolfs, R. J. M., Bos, F. P., and Salet, T. A. (2018). Early age mechanical behaviour of 3D printed concrete: numerical modelling and experimental testing. Cem. Concr. Res. 106, 103–116. doi:10.1016/j.cemconres.2018.02.001
Wolfs, R. J. M., and Suiker, A. S. J. (2019). Structural failure during extrusion-based 3D printing processes. Int. J. Adv. Manuf. Technol. 104, 565–584. doi:10.1007/s00170-019-03844-6
Xia, M., and Sanjayan, J. (2016). Method of formulating geopolymer for 3D printing for construction applications. Mater. Des. 110, 382–390. doi:10.1016/j.matdes.2016.07.136
Xiao, J., Zou, S., Ding, T., Duan, Z., and Liu, Q. (2021a). Fiber-reinforced mortar with 100% recycled fine aggregates: a cleaner perspective on 3D printing. J. Clean. Prod. 319, 128720. doi:10.1016/j.jclepro.2021.128720
Xiao, J., Zou, S., Yu, Y., Wang, Y., Ding, T., Zhu, Y., et al. (2020). 3D recycled mortar printing: system development, process design, material properties and on-site printing. J. Build. Eng. 32, 101779. doi:10.1016/j.jobe.2020.101779
Xiao, L., Ji, G., Zhang, Y., Ma, G., Mechtcherine, V., Pan, J., et al. (2021b). Large-scale 3D printing concrete technology: current status and future opportunities. Cem. Concr. Compos. 122, 104115. doi:10.1016/j.cemconcomp.2021.104115
Xu, Y., Meng, Z., Bol, R. J. M., and Savija, B. (2024a). Spring-like behavior of cementitious composite enabled by auxetic hyperelastic frame. Int. J. Mech. Sci. 275, 109364. doi:10.1016/j.ijmecsci.2024.109364
Xu, Y., and Savija, B. (2023). 3D auxetic cementitious-polymeric composite structure with compressive strain-hardening behavior. Eng. Struct. 294, 116734. doi:10.1016/j.engstruct.2023.116734
Xu, Y., and Savija, B. (2024). Auxetic cementitious composites (ACCs) with excellent compressive ductility: experiments and modeling. Mater. and Des. 237, 112572. doi:10.1016/j.matdes.2023.112572
Xu, Y., Wan, Z., and Savija, B. (2024b). Elevating mechanical performance of cementitious composites with surface-modified 3D-Printed polymeric reinforcements. Dev. Built Environ. 19, 100522. doi:10.1016/j.dibe.2024.100522
Yan, Z., Zeng, J., Zhuge, Y., Liao, J., Zhou, J., and Ma, G. (2024). Compressive behavior of FRP-confined 3D printed ultra-high performance concrete cylinders. J. Build. Eng. 83, 108304. doi:10.1016/j.jobe.2023.108304
Yazıcı, S., Arel, H. S., and Tabak, V. (2013). The effects of impact loading on the mechanical properties of the SFRCs. Constr. Build. Mater 68–72, 68–72. doi:10.1016/j.conbuildmat.2012.11.095
Yazıcı, S., Inan, G., and Tabak, V. (2007). Effect of aspect ratio and volume fraction of steel fiber on the mechanical properties of SFRC. Constr. Build. Mater 21, 1250–1253. doi:10.1016/j.conbuildmat.2006.05.025
Yossef, , and Chen, (2015). Applicability and limitations of 3d printing for civil structures. Proceedings of the 2015 conference on autonomous and robotic construction of infrastructure, ames, iowa. Available at: https://dr.lib.iastate.edu/handle/20.500.12876/13657
Yoo, D.-Y., Park, J.-J., Kim, S.-W., and Yoon, Y.-S. (2013). Early age setting, shrinkage and tensile characteristics of ultra high performance fiber reinforced concrete. Constr. Build. Mater 41, 427–438. doi:10.1016/j.conbuildmat.2012.12.015
Yu, K. Q., Yu, J. T., Dai, J. G., Lu, Z. D., and P. Shah, S. (2018). Development of ultra-high performance engineered cementitious composites using polyethylene (PE) fibers. Constr. Build. Mater. 158, 217–227. doi:10.1016/j.conbuildmat.2017.10.040
Zahra, T., and Dhanasekar, M. (2017). Characterisation of cementitious polymer mortar – auxetic foam composites. Constr. Build. Mater 147, 143–159. doi:10.1016/j.conbuildmat.2017.04.151
Zeng, J., Yan, Z., Jiang, Y., and Li, P. (2024). 3D printing of FRP grid and bar reinforcement for reinforced concrete plates: development and effectiveness. Compos. Struct. 335, 117946. doi:10.1016/j.compstruct.2024.117946
Zhang, X., Li, M., Lim, J. H., Weng, Y., Tay, Y. W. D., Pham, H., et al. (2018a). Large-scale 3D printing by a team of mobile robots. ConStruct 95, 98–106. doi:10.1016/j.autcon.2018.08.004
Zhang, X. G., Rena, X., Jiang, W., Zhang, X. Y., Luo, C., Zhang, Y., et al. (2022). A novel auxetic chiral lattice composite: experimental and numerical study. Compos. Struct. 282, 115043. doi:10.1016/j.compstruct.2021.115043
Zhang, Y., and Aslani, F. (2021). Development of fibre reinforced engineered cementitious composite using polyvinyl alcohol fibre and activated carbon powder for 3D concrete printing. Constr. Build. Mater. 303, 124453. doi:10.1016/j.conbuildmat.2021.124453
Zhang, Y., Yang, T., Jia, Y., Hou, D., Li, D., Jiang, J., et al. (2018b). Molecular dynamics study on the weakening effect of moisture content on graphene oxide reinforced cement composite. Chem. Phys. Lett. 708, 177–182. doi:10.1016/j.cplett.2018.08.023
Zhang, Y., Zhang, Y., Liu, G., Yang, Y., Wu, M., and Pang, B. (2018c). Fresh properties of a novel 3D printing concrete ink. Constr. Build. Mater. 174, 263–271. doi:10.1016/j.conbuildmat.2018.04.115
Zhang, Y., Zhang, Y. S., She, W., Yang, L., Lin, G. J., and Yang, Y. G. (2019). Rheological and harden properties of the high-thixotropy 3D printing concrete. Constr. Build. Mater 201, 278–285. doi:10.1016/j.conbuildmat.2018.12.061
Zhong, R., Ren, X., Zhang, X. Y., Luo, C., Zhang, L., and Xie, Y. M. (2022). Mechanical properties of concrete composites with auxetic single and layered honeycomb structures. Constr. Build. Mater. 322, 126453. doi:10.1016/j.conbuildmat.2022.126453
Zhu, J.-X., Weng, K.-F., Huang, B.-T., Xu, L.-Y., and Dai, J.-G. (2024). Ultra-High-Strength Engineered Cementitious Composites (UHS-ECC) panel reinforced with FRP bar/grid: development and flexural performance. Eng. Struct. 302, 117193. doi:10.1016/j.engstruct.2023.117193
Keywords: 3D printing concrete, 3D printing reinforced concrete, auxetic, concrete, protect building
Citation: Momeni K, Vatin NI, Hematibahar M and Gebre TH (2025) Differences between 3D printed concrete and 3D printing reinforced concrete technologies: a review. Front. Built Environ. 10:1450628. doi: 10.3389/fbuil.2024.1450628
Received: 17 June 2024; Accepted: 18 November 2024;
Published: 06 January 2025.
Edited by:
Walid Mansour, Kafrelsheikh University, EgyptReviewed by:
Marialuigia Sangirardi, University of Oxford, United KingdomNahla Hilal, University of Fallujah, Iraq
Copyright © 2025 Momeni, Vatin, Hematibahar and Gebre. This is an open-access article distributed under the terms of the Creative Commons Attribution License (CC BY). The use, distribution or reproduction in other forums is permitted, provided the original author(s) and the copyright owner(s) are credited and that the original publication in this journal is cited, in accordance with accepted academic practice. No use, distribution or reproduction is permitted which does not comply with these terms.
*Correspondence: Nikolai Ivanovich Vatin, dmF0aW5AbWFpbC5ydQ==