- 1Department of Geography, Philipps-University Marburg, Marburg, Germany
Waste Foundry Sand (WFS) is a byproduct from metal casting processes, often contaminated with heavy metals, acids, and carbon residues. As disposal costs rise, there is growing interest in repurposing WFS as an alternative to traditional aggregates in construction materials such as bricks, tiles, and concrete. However, concerns about the potential leaching of harmful chemicals into soil and groundwater pose significant barriers to its widespread use. By reducing the chemical pollutants, WFS becomes a competitive option for sustainable construction materials. This study aims to address these concerns by developing methods to extract WFS from the production cycle before it exceeds regulatory limits, thereby enhancing its suitability for recycling and reducing disposal costs. We assessed waste foundry sand (WFS) samples from various production cycles, following permissible guidelines, by mixing them with cement in proportions of 1%, 3%, and 5%. Our evaluation focused on their effectiveness as construction materials. The results indicated that the sample with 1% cement slightly exceeded the permissible limits for polycyclic aromatic hydrocarbons (PAHs), whereas the samples with 3% and 5% cement content complied with all regulatory standards. These findings suggest that WFS, particularly when combined with higher cement contents, holds promise as a sustainable construction material. This method not only reduces the need for extensive treatment and reclamation processes but also presents a cost-effective and environmentally friendly approach to managing WFS.
1 Introduction
Effective management of industrial byproducts, such as Waste Foundry Sand (WFS), is imperative for environmental conservation and resource efficiency (Thiruvenkitam et al., 2020; Ashish and Verma, 2021). The foundry industry generates millions of tons of spent materials annually, with WFS constituting a significant portion (Ji et al., 2001; Sabour et al., 2021). In Germany alone, approximately 460,000 tons of WFS are produced each year, often contaminated with heavy metals, acids, and glossy carbon during the production process (Ashish and Verma, 2021; Ahmad et al., 2022).
Historically, efforts to address the challenges of WFS management date back to the late 19th century when industries grappled with disposal issues and environmental concerns (Bagshaw, 1891; Mäsiar et al., 1897). These early endeavors laid the groundwork for subsequent research on WFS utilization, which gained momentum in the late 20th century, driven by growing environmental awareness and regulatory pressures (Riley, 1969; Barnard et al., 1971; Ostrom, 1989; Javed, 1994; Reddi et al., 1996).
According to Matos et al. (2019), foundry sand is a silica sand-based material used in creating molds for both ferrous and non-ferrous metal casting industries. To enhance the casting surface finish, 2%–10% of pulverized coal is added to the mixture (Sithole et al., 2022). When the casting process is complete, the product is removed from the sand mold, and the sand undergoes several steps to prepare it for potential reuse. WFS is generated after several reuse cycles, typically between 5 and 10 cycles (Cioli et al., 2022).
During each reuse cycle, foundry sand is subjected to thermal and mechanical stresses that degrade its properties (Ghosh, 2013; Sappinen et al., 2018; Khan et al., 2021). Contaminants such as metal residues, binders, and other impurities accumulate over time, eventually compromising the quality of the sand for further use in casting molds (Cioli et al., 2022). Consequently, once the sand can no longer meet the required specifications for mold production, it is considered waste foundry sand. Matos et al. (2019) suggested the number of times foundry sand can be reused before it becomes WFS depends on several factors followed by Cioli et al. (2022). Each industry has its own benchmark based on the type of metal being cast and the specific properties of the sand and binders used.
Recent years have seen a surge in research focused on innovative applications and solutions for WFS utilization, driven by the need for sustainable waste management practices (Alves et al., 2014; Mehta, 2024). For instance, the leaching of heavy metals in WFS, such as copper, iron, cadmium, zinc, nickel, and chromium, can damage soil quality and contaminate groundwater (Cioli et al., 2022; Sithole et al., 2022). Therefore, repurposing foundry sand presents a justified and suitable solution for this waste. Noteworthy advancements include the exploration of PozzoCrete as a sustainable alternative in construction applications (Bhimani et al., 2013; Ghosh, 2013; Kshirsagar et al., 2023) and the investigation of WFS as a partial or total replacement for natural sand (Matos et al., 2019; Sithole et al., 2022).
This study presents several novel contributions to the field. We propose developing efficient methods to remove foundry sand from the production line earlier in the production cycle, before WFS parameters exceed guideline values. This early removal minimizes the need for extensive treatment and reclamation processes. By evaluating WFS samples from different production cycles for compliance with regulatory guidelines, we aim to ensure that the sand can be reused safely and effectively. This compliance-focused approach is innovative and essential for practical application. Additionally, our research suggests a cost-effective procedure for the removal and reuse of WFS, which reduces recycling expenses and the environmental burden of landfill disposal.
In light of existing research gaps, the primary objective is to evaluate WFS samples from different production cycles to determine their compliance with regulatory guidelines. Each foundry operation has its own benchmark before sand is classified as WFS. Given the significant environmental concerns and regulatory pressures surrounding WFS disposal, we hypothesize that confirming WFS compliance with regulatory guidelines will enable its feasible removal from foundry operations and reuse as construction material without extensive reclamation processes. This approach aims to achieve environmental alignment and provide a cost-effective procedure for the removal and reuse of WFS, thereby contributing to sustainable waste management practices in the foundry industry.
2 Methodology
2.1 Materials
Waste Foundry Sand (WFS) was procured from three distinct foundries: FRITZ WINTER Eisengießerei GMBH & CO. KG, BUDERUS GUSS GMBH, and WESO-AURORAHÜTTE GMBH. Additionally, Heidelberg Cement CEM III/A 42.5N was used as an additive in various proportions.
2.2 Experimental procedures
The solubility behavior of road construction materials utilizing WFS holds implications for soil chemical properties, intricately tied to eluted characteristics. To analyze the leaching behavior of construction materials using WFS, samples from WESO-AURORAHÜTTE GMBH only were treated as a solid-phase composites, with consideration given to the chemical load values specified by LAGA (LAGA-M20, 2020).
Samples obtained from WESO-AURORAHÜTTE GMBH were divided into three identical portions. The first, second, and third portions were prepared with an additive ratio of P1%, P3%, and P5%, respectively, using Heidelberg Cement CEM III/A 42.5N (refer to Figure 1). The laboratory of Leonhard Weiss GmbH & Co. KG conducted examinations in accordance with DIN 18123 and DIN 1812 to assess the physical properties and compaction (Gruppe, 2016). This step aimed to ensure the suitability and stability of the samples for subsequent analysis.
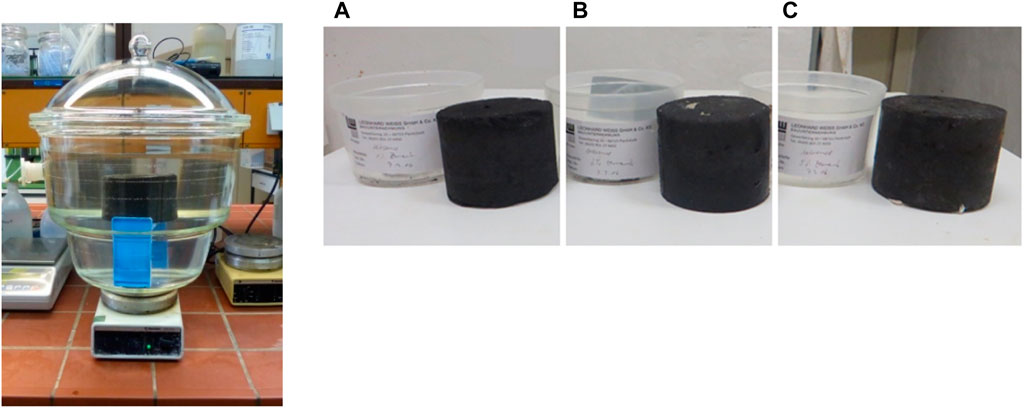
Figure 1. Experimental Setup for Elution Test. Note: In accordance with the LAGA guideline, each sample underwent washing in a glass vessel at a 10:1 ratio of deionized water to solid, left for an elution time of 24 h, and stirred at a rotational speed of approximately 500 rpm (Photo: Vorndran, M.). Note: Different composition prepared in the laboratory of Leonhard Weiss GmbH & Co KG with (A) 1%, (B) 3%, and (C) 5% using Heidelberg Cement CEM III/A 42.5N (Photo: Vorndran, M.).
2.3 Chemical laboratory analysis
Following the meticulous preparation of the samples, a comprehensive chemical laboratory analysis was undertaken to examine the solubility behavior of the chemical composition. Samples were subjected to comprehensive testing to determine the presence and concentration of various organic and inorganic components.
Organic compounds, including Mineral oil hydrocarbons, BTEX (Benzene, Toluene, Ethylbenzene, Xylene), Benzol, Chlorinated hydrocarbons (CHCs), Aldrin, DDT (Dichlorodiphenyltrichloroethane), Phenols, PCB (Total Polychlorinated Biphenyls), PAH (Total Polycyclic Aromatic Hydrocarbons), and Naphthalene, were quantified at Dr. Graser’s laboratory (CLG, 2016). Inorganic parameters such as Antimony, Arsenic, Lead, Cadmium, Chromium, Cobalt, Copper, Molybdenum, Nickel, Mercury, Selenium, Zinc, Tin, Cyanide, and fluoride were conducted with meticulous attention to detail and adherence to stringent quality control measures, ensuring the accuracy and reliability of the results.
To ascertain the maximum permissible value of a substance in accordance with BBodSchV §8 para.1 sentence 2 No.1 (BBodSchV, 1999), three portions of the samples underwent testing in the laboratory of the geography department at Philipps University of Marburg. The elutable organic and inorganic substances from these portions were differentiated. The LAGA protocol guided the treatment sequence as follows: initially, each sample underwent washing in a glass vessel (column) at a deionized water/solid ratio of 10:1. Subsequently, they were allowed an elution time of 24 h while being stirred at a rotational speed of approximately 500 rpm (refer to Figure 1).
2.4 Experimental setup
The solubility behavior of samples was examined to assess compliance with regulatory standards. The chemical properties and analytical results obtained were meticulously processed and are presented in detail in Tables 1, 2 in the subsequent section. The experimental procedure consisted of the following steps:
2.4.1 Sample preparation and filtration
Samples were prepared according to the guidelines outlined in the Revision of the Federal Soil Protection and Contaminated Sites Ordinance BMUB 2015 directive . This involved the preparation of samples and filtration procedures conducted at the laboratory of the geography department at Philipps University of Marburg. The filtration process aimed to isolate the eluates for subsequent chemical analysis (LAGA-33, 2002).
The prescribed procedure only specifies a 2:1 water/solid ratio. In principle, a higher ratio facilitates the dissolution of more substances compared to a lower ratio. The samples were placed on a sieve, maintaining a distance of 5 cm from the bottom of the elution basin to prevent damage. After 24 h, 1 L of eluate was transferred to a glass cylinder. Following a 15-min settling period for coarser particles, the supernatant liquid was decanted and centrifuged at 2000 x g for 30 min, exerting a force equivalent to 2,000 times the gravity at sea level (approximately 9.81 N per kg). Post-centrifugation, the liquid underwent filtration through a 0.45 µm membrane filter.
2.4.2 Chemical analysis
The eluates obtained from the WFS samples were analyzed to determine their chemical properties. The results of the chemical analysis were provided in the laboratory of Dr. Graser (CLG, 2016). Dr. Graser’s laboratory, accredited under DIN ISO 17025, specializes in a wide range of analyses related to environmental substances. The laboratory adheres to rigorous quality assurance measures to ensure accurate and reliable results (refer to Table 3).
3 Analysis and interpretation of results
In essence, the comprehensive analysis and interpretation of results in this study draw from a multidisciplinary perspective, encompassing environmental geochemistry, sedimentary metal indices, and practical applications of metal pollution assessment methodologies. This approach ensures a nuanced understanding of the intricate relationship between element concentration, solubility, and the broader environmental implications, contributing to the advancement of knowledge in this field.
The obtained results underwent a particular analysis to unravel the complex relationship between element concentration and solubility. This analysis was contextualized within relevant standards and guidelines, particularly LAGA M20, to gauge the suitability of road construction materials for recycling and to assess potential environmental impacts. The ensuing discussion delves into solubility patterns, and potential applications of WFS in construction materials.
3.1 Assessment of unbound foundry residual sands
This comprehensive evaluation underscores the significance of these findings in the context of groundwater protection and soil quality. One notable aspect of this analysis is the considerable variation in the number of samples evaluated across various production phases, in accordance with the legal requirements specified in LAGA. The concentrations in both the eluted and solid components of the samples were compared against the Z2 requirements of LAGA M20, ensuring adherence to its maximum permissible values as detailed in Tables 1, 2.
The first sample set (A1) exhibited concentration values within regulatory standards, remaining within the allowable range. PAH compounds in the subsequent sample sets (A1,A2, A3, and A4) were lower than those in the guidelines, consistent with the findings of Ji et al. (2001). However, organic compounds as reported by Zhang et al. (2014), showed high concentration but remined below the permissible levels. This contrast is due to the differentiation in selecting production cycles. In addition, for all sample sets, the allocation values for BTEX and EOX were not negligible. In the subsequent sample sets (A1, A2, and A3) fluoride values generally adhered to the allowable range, with a minor (10%) exceedance noted in A2.4 and a more significant (80%) exceedance in A3.2. Results from earlier production cycles (A1, A2, and A3) showed concentrations below permissible levels. However, in the fourth cycle (A4.1), the solid allocation values of chromium, copper, and nickel surpassed the limits established in 2015 (refer to Table 1).
The fluctuation pattern within the measurement series from all production cycles were evaluated for elute allocation values in accordance with §13 “Evaluation of the measurement results of quality monitoring.” Importantly, all substances met the requirements outlined in the Ordinance on the Specification of Requirements for the Introduction or Discharge of Substances into Groundwater (refer to Table 2). This compliance aligns with the Installation of Replacement Building Materials (IRBM) and the Revision of the Federal Soil Protection and Contaminated Sites Ordinance (BMUB, 2015). However, in the fourth sample set (A4), fluoride concentrations surpassed the permissible limit. These adjustments aim to enhance consistency and clarity in presenting information regarding the sample sets and their concentrations.
Further discussion will delve into the implications of these results and their relevance in the broader context of environmental stewardship (Reimann and Caritat, 2000). underscore the intrinsic flaws of Enrichment Factor (EF)s in environmental geochemistry, shedding light on the complexities involved in interpreting enrichment factors. The EF method assesses the relative enrichment of elements in relation to the reference element and, typically compared to a baseline concentration in the Earth’s crust or background concentration. In selecting a reference element, Zinc (Zn) emerges as a practical choice. Its relative immobility, abundance, and common use in geochemical studies make it a versatile and widely applicable reference. The stability of Zinc compounds, coupled with its resistance to leaching or mobility compared to some other metals, positions it as a robust reference element unaffected by specific geological or environmental processes. Birch, (2023) contributes to this discourse by reviewing and critically assessing sedimentary metal indices employed in gauging anthropogenic changes in coastal environments. Jeong et al. (2020) focus on the assessment of metal pollution in road-deposited sediments and marine sediments around Gwangyang Bay, Korea, providing valuable insights into real-world applications of metal pollution assessment methodologies. Meanwhile, Taylor & McLennan, (1985) provide insights into the composition and evolution of the continental crust, offering a foundational understanding. Given these values, EF will be calculated using the following formula:
The EF is calculated by dividing the concentration of a specific element in the sample (CES) by its concentration in the Background (CEB). This ratio is then divided by the ratio of the concentration of Zinc in the sample (CZS) to its concentration in the Background (CZB).
The average crustal abundance of elements can vary depending on the source and the method of calculation. However, one widely cited source for such estimates are reginal document accordance with BBodSchV – Z2 or the composition of the Earth’s crust as proposed by Clarke 1924. Clarke’s composition values have been refined and updated over the years by various researchers (Taylor, 1964) and organizations (Staudigel et al., 1998).
If EF > 1, it indicates enrichment, suggesting that the element concentration in the sample is higher than what is typically found in the Earth’s crust. If EF = 1, the concentration is similar to the background, and if EF < 1, it suggests depletion.
Based on the data presented in Figure 2, the Enrichment Factor (EF) values for chromium and nickel in the first set of samples (A1.1 to A1.6) are less than 1, indicating that their concentrations are depleted relative to zinc compared to the typical crustal abundances. However, the concentrations of copper and lead are enriched relative to zinc compared to crustal abundances. It is noteworthy that chromium exhibits exceptionally high values, ranging from a maximum of 17.5 mg/kg to a minimum of 1.13 mg/kg, indicating significant variation in its concentration across the samples. However, the situation changes for the second set of samples (A2.1 to A2.6). In this case, the Enrichment Factor (EF) values for the elements examined, as compared to references, indicate depletion relative to zinc when compared to background abundances from Z2. This suggests that the concentrations of these elements in the second set of samples are lower compared to typical crustal levels, particularly in relation to zinc. The third sample set (A3.1, and A3.2) were analyzed not for concentration but for eluted elements in water. Therefore, comparisons based on concentration levels were not considered for this set of samples. In the case of the fourth sample set (A4), none of the elements examined exhibited enrichment factors (EF) below one when compared to the reference values of 103 mg/kg for chromium, 115 mg/kg for nickel, and 31 mg/kg for copper. In line with Cioli et al. (2022), the heavy metals most commonly found in WFS are chromium, nickel, and zinc. These results leave little room for negotiation, indicating that the concentrations of these elements in the fourth cycle are consistently elevated compared to the references.
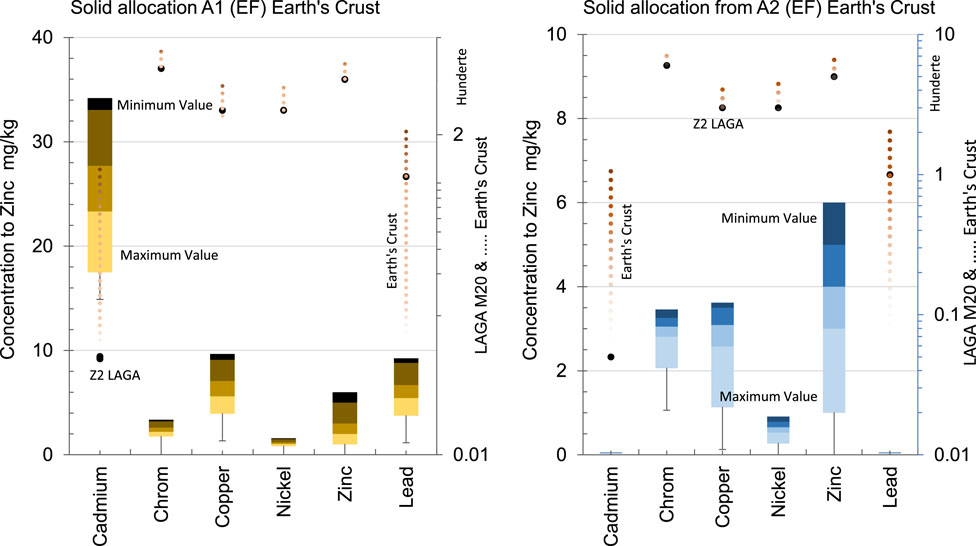
Figure 2. Enrichment Factor of Zinc Concentrations Relative to Earth’s Crust References and Z2 Standards in first and second Production Cycles. The left figure represents the first cycle, and the right figure represents the second cycle.
3.2 Assessment of dissolving properties in bound foundry residual sands
The comprehensive concentrations of both organic and inorganic substances across three distinct WFS scenarios, meticulously documented in Table 3. The following salient observations emerge from this detailed analysis. These result underscore substances deemed of considerable concern in road construction scenarios incorporating WFS.
Inorganic Substances: All concentrations meticulously adhere to the designated (limited) range, meticulously aligning with and surpassing regulatory standards.
Organic Substances in the First Scenario (P1%): A scrupulous evaluation exposes the delineation of two key substance values—polycyclic aromatic hydrocarbons (PAHs; 0.28/0.2 μg/L) and naphthalene (0.31/0.2 μg/L)—exceeding the stipulated allocation range. This revelation resonates with antecedent reports (Susset and Leuchs, 2008), which found PAHs >20 mg/kg. Notably, turbidity in water monitoring, reflective of dissolution tendencies, garners attention due to its low grain binding.
Second (3%) and Third (5%) Scenarios: Results emanating from these scenarios unveil heightened stability, marked by a substantial decrease in turbidity concurrent with escalating cement content. Rigorous investigations underscore the reduction of substances within the diluted samples to levels below the permissible threshold, meticulously aligning with the tenets of BBodSchV.
When comparing the element value to the permissible rate (Figure 3), the concentration of the element in the sample meets regulatory standards and thresholds. This comparison is typically to determine the samples rate is safe for its intended (e.g., road construction propose) use. The permissible rate represents the maximum allowable concentration of the element in the sample.
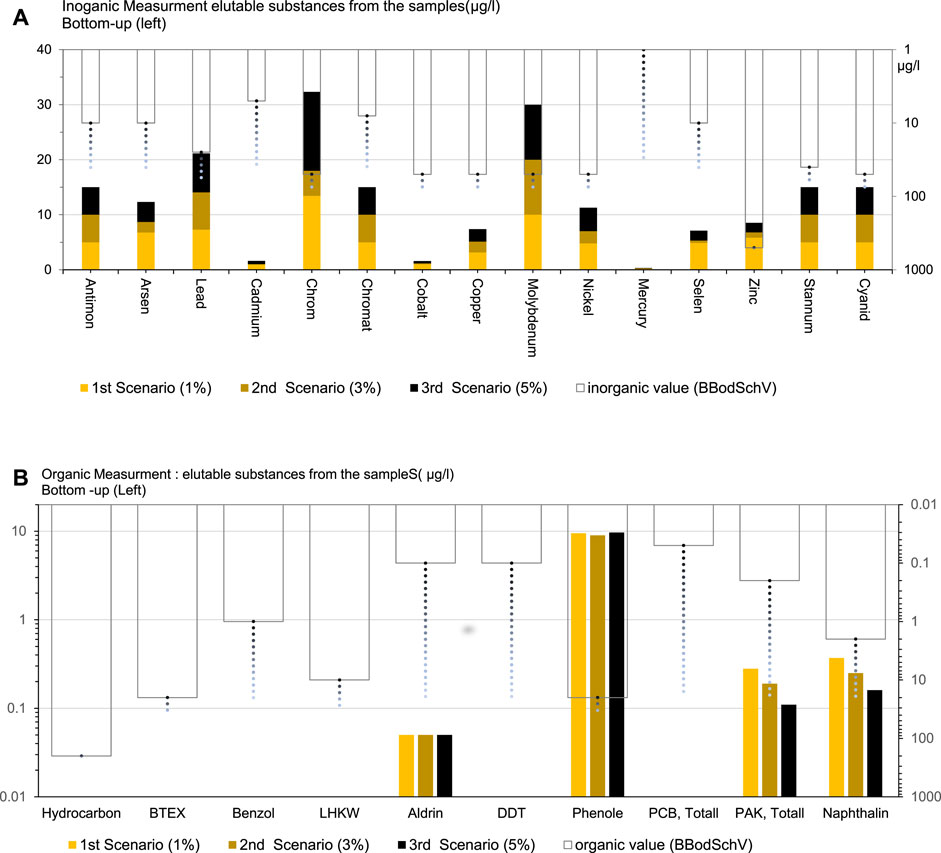
Figure 3. Comparison of Eluted Substance Values for Organic and Inorganic Measurements: Fig. (A) (Inorganic) and Fig. (B) (Organic) show values scaled on the left (bottom-up) and in accordance with Z2 standards on the right (top-down).
Figure 4A, illustrates the stabilization of leaching inorganic substances from WFS through mixing with varying proportions (P1%, P3%, and P5%) of Heidelberg Cement CEM III/A 42.5N. Additionally, raw samples from WESO-AURORAHÜTTE GMBH were analyzed alongside WFS mixed with cement at P1%, P3%, and P5% proportions in line with regulatory guidelines, ensuring that no allocation value exceeds these guidelines.
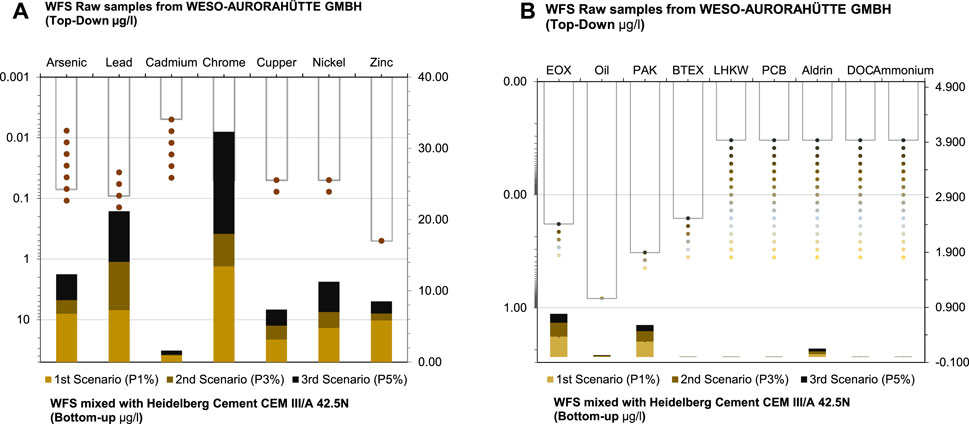
Figure 4. Comparison of Inorganic Fig. (A) and Organic Fig. (B) Substances in WFS Raw Samples vs. WFS Mixed with Heidelberg Cement CEM III/A 42.5N. WFS values are scaled on the right (bottom-up) without additives, and with the proportion of CEM scaled on the left (top-down).
The results reveal notable trends: except for Arsenic and Zinc, all values remained below the allocation value before mixing. Cadmium displayed the highest stabilization, with levels of 0.92 μg/L (P1%), 0.12 μg/L (P3%), and 0.57 μg/L (P5%). Nickel levels were 4.79 μg/L (P1%), 2.24 μg/L (P3%), and 4.26 μg/L (P5%), followed by Lead and Copper. Notably, all mixed portions showed stabilized substance levels.
Upon analysis, scenarios P3% and P5% emerged as strong candidates for mixing WFS with cement due to lower concentrations of potentially harmful elements and relatively stable results. Overall, these findings suggest that increased cement content in scenarios P3% and P5% contributes to a more stable condition, with substances remaining below permissible limits.
As depicted in Figure 4B, the concentrations of most organic compounds in the mixed scenarios (P1%, P3%, P5%) remain consistent with the raw samples. Specifically, EOX, Oil, PAH, and Aldrin show minimal variation between the mixed scenarios and the raw samples. Furthermore, concentrations of BTEX, LHKW, PCB, DOC, and Ammonium are consistently negligible in both the mixed scenarios and the raw samples. Phenol concentrations, however, remain consistent across all scenarios and the raw samples. Based on these analyses, all portions (P1%, P3%, and P5%) appear to be stable candidates for mixing WFS with Cement due to their stabilized concentrations of low potentially harmful elements in line with regulatory standards.
Removing WFS early in the production cycle can significantly reduce the expense of chemical reclamation (Bentz et al., 2012; Ghormley, 2017; Khan and Mahajani, 2024). This early removal minimizes the accumulation of contaminants, thereby decreasing the treatment required to make the WFS suitable for reuse (Gedik et al., 2018). Different manufacturers, such as those producing construction materials, can select WFS that is free from environmental risks and customize its physical properties to suit their specific production needs. Studies have demonstrated the successful application of WFS in various construction materials, showcasing its mechanical properties and environmental safety (Siddique et al., 2010; Khatib et al., 2013; Ferrazzo et al., 2024). For instance, the use of WFS in concrete production has been shown to provide both environmental and performance benefits, supporting its suitability for diverse construction applications (Naik, 2002; Pendhari and Nagarnaik, 2020). Additionally, the influence of particle size distributions on the properties of cement and concrete highlights the ability of manufacturers to tailor WFS to meet specific requirements (Bentz et al., 2012).
For instance, the absence of soil contamination in the selected WFS underscores its suitability for recycling in road construction. Studies have shown that WFS can be effectively used in road and pavement construction without significant environmental risks (Khatib et al., 2013; Morais et al., 2023). The incorporation of appropriate cement content plays a crucial role in shaping the dissolving properties of WFS, thus influencing its environmental sustainability in construction practices. High cement content can immobilize contaminants, reducing the potential for leaching and making the material safer for use (Siddique et al., 2010; Upadhyay et al., 2024).
4 Conclusion
This study represents a significant advancement in understanding the composition of untreated substances within Waste Foundry Sand (WFS) and their potential application in construction materials, addressing a notable gap in current research. Through the analysis of samples from WESO-AURORAHÜTTE GMBH, no detectable release of substances was observed, marking a crucial discovery regarding the behavior of WFS.
A key component of this study was assessing the movement of contaminants through the Waste Foundry Sands cycle. The goal was to remove the foundry sand before it pollutes beyond acceptable guidelines and to save on costs for reclaiming the sand.
We tested different mixes of 1%, 3%, and 5% cement to see how well they prevented contaminants from seeping into the soil and groundwater in case of leaks. By applying a mass ratio of 10:1 (water/solid) and examining the solubility of organic and inorganic substances across three scenarios, it was found that the second (P3% cement content) and third (P5% cement content) scenarios met emplacement requirements. However, the first scenario (P1% cement content) exhibited a slight exceedance of legal thresholds for PAHs (Polycyclic Aromatic Hydrocarbons), according to guidelines from the United States Environmental Protection Agency.
Overall, the results indicate that samples from the second and third scenarios can be safely utilized as recycled products in road construction without significant environmental risks. While organic and inorganic substances generally remained within acceptable concentration ranges, there was a minor fluoride exceedance in the second and third analytical results [A2nd] and [A3rd].
This approach not only addresses the pressing issue of WFS disposal costs but also offers significant environmental benefits by reducing the demand for virgin raw materials and mitigating the environmental impact associated with traditional construction practices. By providing actionable insights for the early removal and reuse of foundry sand, this study contributes to sustainable waste management practices in the foundry industry and promotes the development of eco-friendly construction materials.
5 Future directions
Given the potential significance of this topic, we plan to explore it further in future research endeavors. We aim to conduct economic assessments to evaluate the cost-effectiveness and feasibility of implementing Waste Foundry Sand (WFS)-based construction solutions in real-world scenarios.
Recognizing the need for further investigation and validation, particularly with an individual benchmark for the appropriate production cycles, is essential. Although the current study’s scope limits extensive analysis, expanding the research scope and dedicating additional time to comprehensive data analysis across every industry with planned monitoring are recommended.
This expanded research work could facilitate the identification of spatial patterns and correlations between element concentrations and solubility, utilizing spatial analysis with solubility maps. Future steps may involve developing statistical models to predict solubility based on concentrations of various elements, leveraging machine learning techniques for this purpose.
Continued pursuit of knowledge in these areas is crucial for advancing sustainable practices in waste management and construction material usage.
Data availability statement
The original contributions presented in the study are included in the article/supplementary material, further inquiries can be directed to the corresponding author.
Author contributions
PC: Formal Analysis, Investigation, Supervision, Writing–review and editing, Project administration. MS: Formal Analysis, Investigation, Methodology, Writing–review and editing. MR: Data curation, Formal Analysis, Investigation, Methodology, Resources, Validation, Writing–original draft. MF: Data curation, Formal Analysis, Software, Visualization, Writing–review and editing, Validation.
Funding
The author(s) declare that no financial support was received for the research, authorship, and/or publication of this article.
Conflict of interest
The authors declare that the research was conducted in the absence of any commercial or financial relationships that could be construed as a potential conflict of interest.
Publisher’s note
All claims expressed in this article are solely those of the authors and do not necessarily represent those of their affiliated organizations, or those of the publisher, the editors and the reviewers. Any product that may be evaluated in this article, or claim that may be made by its manufacturer, is not guaranteed or endorsed by the publisher.
References
Ahmad, J., Zhou, Z., Martínez-García, R., Vatin, N. I., de-Prado-Gil, J., and El-Shorbagy, M. A. (2022). Waste foundry sand in concrete production instead of natural river sand: a review. Materials 15 (7), 2365. doi:10.3390/ma15072365
Alves, B. S. Q., Dungan, R. S., Carnin, R. L. P., Galvez, R., and de Carvalho Pinto, C. R. S. (2014). Metals in waste foundry sands and an evaluation of their leaching and transport to groundwater. Water, Air, & Soil Pollut. 225 (5), 1963. doi:10.1007/s11270-014-1963-4
Ashish, D. K., and Verma, S. K. (2021). Robustness of self-compacting concrete containing waste foundry sand and metakaolin: a sustainable approach. J. Hazard. Mater. 401, 123329. doi:10.1016/j.jhazmat.2020.123329
Bagshaw, W. (1891). On the mechanical treatment of moulding sand. Proc. Institution Mech. Eng. 42 (1), 94–107. doi:10.1243/pime_proc_1891_042_012_02
Barnard, P. G., Ritchey, R. A., and Kenworthy, H. (1971). Recovery of chromite and silica from steel foundry waste molding sands. U. S. Dep. Interior 36.
Bentz, D. P., Ferraris, C. F., Galler, M. A., Hansen, A. S., and Guynn, J. M. (2012). Influence of particle size distributions on yield stress and viscosity of cement–fly ash pastes. Cem. Concr. Res. 42 (2), 404–409. doi:10.1016/j.cemconres.2011.11.006
Bhimani, D. R., Pitroda, J., Bhavsar, J. J., Vidyanagar, V., and Vidyanagar–Gujarat–India, V. (2013). Used foundry sand: opportunities fordevelopment of eco-friendly low cost concrete. IJAET 4, 63–66. doi:10.15373/22778179/feb2013/33
Birch, G. F. (2023). A review and critical assessment of sedimentary metal indices used in determining the magnitude of anthropogenic change in coastal environments. Sci. Total Environ. 854, 158129. doi:10.1016/j.scitotenv.2022.158129
BMUB (2015). Bundes-Ministerium für Umwelt, Natur-Schutz, nukleare-Sicherheit und Verbraucher-Schutz.
Cioli, F., Abbà, A., Alias, C., and Sorlini, S. (2022). Reuse or disposal of waste foundry sand: an insight into environmental aspects. Appl. Sci. 12 (13).
Clarke, F. W. (1924). Washington HS the composition of the Earth’s crust. U. S. Dep. Inter. Geol. Surv. 770, 518. doi:10.3133/pp127
CLG (2016). Chemische labor Dr. Graser. Available at: https://www.labor-graser.de/.
Ferrazzo, S. T., de Araújo, M. T., and Consoli, N. C. (2024). Which solution is more sustainable: waste foundry sand stabilized with alkali-activated binder or Portland cement? J. Build. Eng. 84, 108448. doi:10.1016/j.jobe.2024.108448
Gedik, A., Lav, A. H., and Lav, M. A. (2018). Investigation of alternative ways for recycling waste foundry sand: an extensive review to present benefits. Can. J. Civ. Eng. 45 (6), 423–434. doi:10.1139/cjce-2017-0183
Ghormley, S. K. (2017). Life cycle assessment in foundry sand reclamation–comparison of secondary reclamation processes.
Ghosh, A. (2013). Modern sand reclamation technologies for economy, environment friendliness and energy efficiency. 61st Indian Foundry Congress. Available at: https://www.leonhard-weiss.com/.
Jeong, H., Choi, J. Y., and Ra, K. (2020). Assessment of metal pollution of road-deposited sediments and marine sediments around Gwangyang Bay, Korea. Sea J. KOREAN Soc. Oceanogr. 25 (2), 42–53.
Ji, S., Wan, L., and Fan, Z. (2001). The toxic compounds and leaching characteristics of spent foundry sands. Water, Air, Soil Pollut. 132 (3-4), 347–364. doi:10.1023/a:1013207000046
Khan, M. M., and Mahajani, S. M. (2024). Chemical reclamation of waste green foundry sand and its application in core production. Sustain. Chem. Clim. Action 4, 100038. doi:10.1016/j.scca.2024.100038
Khan, M. M., Mahajani, S. M., Jadhav, G. N., Vishwakarma, R., Malgaonkar, V., and Mandre, S. (2021). Mechanical and thermal methods for reclamation of waste foundry sand. J. Environ. Manag. 279, 111628. doi:10.1016/j.jenvman.2020.111628
Khatib, J. M., Herki, B. A., and Kenai, S. (2013). Capillarity of concrete incorporating waste foundry sand. Constr. Build. Mater. 47, 867–871. doi:10.1016/j.conbuildmat.2013.05.013
Kshirsagar, M., Sandbhor, S., Dabir, V., and Kaushik, A. (2023). “Eco-friendly high strength concrete using waste foundry sand and microwave incinerated rice husk ash,” in AIP Conference, LAGA-33. (2002). Länderarbeitsgemeinschaft Abfall. In Richtlinie für das Vorgehen bei physikalischen und chemischen Untersuchungen, China, 26 Jul 2015.
LAGA-M20 (2020). “Verordnung bundesgesetzblatt,” in Anforderungen an die stoffliche Verwertung von mineralischen Abfällen (China: LAGA).
Mäsiar, H., Kasala, J., and Kaloforov, N. (1897). Effect of polyethylene oxide on properties of bentonite foundry mixtures. Archives Foundry Eng. 3310, 69–72.
Matos, P. R., Marcon, M. F., Schankoski, R. A., and Prudêncio, Jr L. R. (2019). Novel applications of waste foundry sand in conventional and dry-mix concretes. J. Environ. Manag. 244, 294–303. doi:10.1016/j.jenvman.2019.04.048
Mehta, V. (2024). Sustainable approaches in concrete production: an in-depth review of waste foundry sand utilization and environmental considerations. Environ. Sci. Pollut. Res. 31 (16), 23435–23461. doi:10.1007/s11356-024-32785-1
Morais, M. d., Levandoski, W. M. K., Reis, J. B., Rosa, F. D., and Korf, E. P. (2023). Environmental and technical feasibility of a waste foundry sand applied to pavement granular layers. Soils Rocks 46 (1), e2023001722. doi:10.28927/sr.2023.001722
Pendhari, A., and Nagarnaik, D. P. (2020). Sustainable concrete by using waste foundry sand and carbon fibre. SSRN Electronic Journal. doi:10.2139/ssrn.3688412
Reddi, L. N., Rieck, G. P., Schwab, A. P., Chou, S. T., and Fan, L. T. (1996). Stabilization of phenolics in foundry waste using cementitious materials. J. Hazard. Mater. 45 (2-3), 89–106. doi:10.1016/0304-3894(95)00083-6
Reimann, C., and Caritat, P. d. (2000). Intrinsic flaws of element enrichment factors (EFs) in environmental geochemistry. Environ. Sci. Technol. 34 (24), 5084–5091. doi:10.1021/es001339o
Riley, G. W. (1969). Recovery of chromite from reclaimed foundry sand. Natural Resources Canada/CMSS/Information Management. doi:10.4095/323903
Sabour, M. R., Derhamjani, G., Akbari, M., and Hatami, A. M. (2021). Global trends and status in waste foundry sand management research during the years 1971-2020: a systematic analysis. Environ. Sci. Pollut. Res. 28, 37312–37321. doi:10.1007/s11356-021-13251-8
Sappinen, T., Orkas, J., and Kronqvist, T. (2018). Thermal reclamation of foundry sands using repurposed sand dryer equipment. Archives Foundry Eng. 18 (4), 99–102. doi:10.24425/afe.2018.125176
Siddique, R., Kaur, G., and Rajor, A. (2010). Waste foundry sand and its leachate characteristics. Resour. Conservation Recycl. 54 (12), 1027–1036. doi:10.1016/j.resconrec.2010.04.006
Sithole, N. T., Tsotetsi, N. T., Mashifana, T., and Sillanpää, M. (2022). Alternative cleaner production of sustainable concrete from waste foundry sand and slag. J. Clean. Prod. 336, 130399. doi:10.1016/j.jclepro.2022.130399
Staudigel, H., Albarede, F., Blichert-Toft, J., Edmond, J., McDonough, B., Jacobsen, S. B., et al. (1998). Geochemical earth reference model (GERM): description of the initiative. Chem. Geol. 145 (3-4), 153–159. doi:10.1016/s0009-2541(97)00141-1
Susset, B., and Leuchs, W. (2008). Stofffreisetzung aus mineralischen Ersatzbaustoffen und Böden: Ermittlung der Quellstärke-Entwicklung und des Rückhalte-und/oder Abbaupotentials mittels Freilandlysimetern und Laborelutionen. Schlussbericht.
Taylor, S. R. (1964). Abundance of chemical elements in the continental crust: a new table. Geochimica cosmochimica acta 28 (8), 1273–1285. doi:10.1016/0016-7037(64)90129-2
Thiruvenkitam, M., Pandian, S., Santra, M., and Subramanian, D. (2020). Use of waste foundry sand as a partial replacement to produce green concrete: mechanical properties, durability attributes and its economical assessment. Environ. Technol. Innovation 19, 101022. doi:10.1016/j.eti.2020.101022
Upadhyay, H. H., Patil, O. E., Jadhav, R. S., Patil, R. S., Ulape, D. P., and Mohite, N. T. (2024). Reclamation of waste sand generated from 3D printer. Int. J. Metalcasting 18 (1), 228–240. doi:10.1007/s40962-023-00991-1
Keywords: waste foundry sand (WFS), construction materials, chemical leaching, recycling, sustainability, in-organic contamination
Citation: Chifflard P, Schütz M, Reiss M and Foroushani MA (2024) Evaluating chemical properties and sustainable recycling of waste foundry sand in construction materials. Front. Built Environ. 10:1386511. doi: 10.3389/fbuil.2024.1386511
Received: 16 February 2024; Accepted: 24 July 2024;
Published: 16 August 2024.
Edited by:
Prannoy Suraneni, University of Miami, United StatesReviewed by:
Markssuel Marvila, Universidade Federal de Viçosa, BrazilCopyright © 2024 Chifflard, Schütz, Reiss and Foroushani. This is an open-access article distributed under the terms of the Creative Commons Attribution License (CC BY). The use, distribution or reproduction in other forums is permitted, provided the original author(s) and the copyright owner(s) are credited and that the original publication in this journal is cited, in accordance with accepted academic practice. No use, distribution or reproduction is permitted which does not comply with these terms.
*Correspondence: Mansour Ahmadi Foroushani, YWhtYWRpZm9Ac3RhZmYudW5pLW1hcmJ1cmcuZGU=
†Present address: Martin Reiss, Hessische Landgesellschaft mbH, Walldorf, Germany