- National Renewable Energy Laboratory, Golden, CO, United States
Mass timber construction is widely considered a promising alternative construction method to reduce buildings’ total life-cycle carbon emissions because wood is a carbon sink. Cross-laminated timber (CLT) panels, manufactured by gluing lumber layers with grains at right angles, are potential low-carbon alternatives to carbon-intensive concrete and steel construction. However, most environmental impact assessment studies do not consider variation in transportation impacts within the CLT supply chain when calculating life-cycle impacts. This study investigates the embodied primary energy and the global warming potential (GWP) of CLT supply chain decisions regarding the type of timber species used, the U.S. region it is sourced from, and the location of the CLT mill. Longer transport distances in the supply chain for timber and CLT panels can contribute as much as 923 MJ/m2 (20%) of the embodied primary energy of a CLT building, and the use of a higher-density timber species increases this contribution to 1246 MJ/m2 (24%), with most of that energy derived from fossil energy sources. For perspective, the GWP of a building whose CLT panels and timber have been transported by truck over 6,000 km (252–270 kgCO2/m2) is greater than the GWP of an equivalent reinforced concrete (RC) building (245 kgCO2/m2). Thus, factors like the location of CLT processing facilities and the type of timber species can significantly impact the overall life-cycle assessment and, if chosen appropriately, can mitigate the environmental impacts of CLT construction.
1 Introduction
Building construction and operation consume 37% (about 135 EJ) of global energy and represent 38% of global carbon dioxide emissions (13.2 Gt CO2) (International Energy Agency, 2023). Since 1990, buildings’ emissions have increased by 50%, and are projected to maintain an upward trajectory in the coming years (Cabeza et al., 2022). As the floor area of buildings is expected to double by 2060 relative to 2017, it is imperative that the per unit emissions of buildings be reduced to realize a decarbonized future (McCulloch et al., 2017).
For existing buildings, operational emissions dominate life-cycle emissions, but energy efficient building technologies can help reduce these operational emissions over time (Vahidi et al., 2021). As more energy efficient buildings are constructed, addressing embodied carbon emissions (emissions due to the production of building materials and construction) will become a priority for decarbonization (United Nations Environment Programme, 2021). Röck et al. (2020) estimated the embodied emissions share to be 20%–25% of life-cycle emissions on average and 45%–50% for highly energy-efficient buildings. For extremely energy efficient buildings, this share could be higher than 90%, and is expected to keep increasing across the building stock. Similarly, a review of the literature showed embodied energy could be 10%–60% of total energy consumption of a building for a lifespan of more than 50 years (Ibn-Mohammed et al., 2013). Additionally, as the majority of embodied emissions are locked into the building’s life-cycle emissions as soon as the building is constructed, addressing these emissions with urgency in anticipation of growth in construction is key to meeting climate goals (United Nations Environment Programme, 2021; Cabeza et al., 2022).
Building materials production and construction account for 11% of global carbon emissions (Architecture 2030, 2021, Accessed: 2021). Currently, concrete and steel are the primary materials used in commercial buildings in North America. Steel production is a particularly carbon intensive process; concrete is not as carbon intensive by weight but is required in large amounts for building construction (United Nations Environment Programme, 2018). The use of low-carbon materials for construction is an important strategy to reduce embodied emissions of buildings (Akbarnezhad and Xiao, 2017). Low carbon materials can include earthen materials (e.g., adobes, rammed earth, compressed earth blocks) and wood (Akbarnezhad and Xiao, 2017; Cabeza et al., 2022). Recently, the extensive use of wood for mid- and high-rise buildings has been made possible by advancements in mass timber technology (Himes and Busby, 2020), and the global use of this technology for new mid-rise urban residential construction can store up to 0.68 Gt of carbon annually (Churkina et al., 2020).1
One of the primary mass timber construction components, CLT panels are being increasingly considered to replace carbon intensive construction materials. CLT is a wood panel system that has high strength, dimensional stability, and the ability to resist high compressive forces, rendering itself a competitive alternative to mid-to high-rise RC construction (Evans, 2018). The timber used in CLT construction is considered a renewable resource, and the environmental impacts of CLT buildings are often compared to RC construction. To measure the environmental impacts of different building construction types and to better understand the sources of those impacts, a life-cycle analysis (LCA) can be performed. An LCA includes the impacts of processing raw materials and manufacturing of the construction products required in the building, the transportation of those products, and the construction of the building.
CLT panels are manufactured by gluing together alternating lumber board layers with their grains at right angles, ensuring equal strength in all directions (Karacabeyli and Douglas, 2013). The timber used to make the lumber board is usually softwood (Douglas fir, Hem fir, southern pine, Ponderosa pine, Lodgepole pine, etc.), although yellow poplar, a hardwood species, is also used (Karacabeyli and Douglas, 2013). After reaching a certain age and/or diameter, the timber is logged and transported from the forest to a sawmill, where it is sawed, dried, and planed into lumber boards. The lumber boards are then transported to the CLT mill, where the manufacturing process involves additional drying (12% ± 3% final moisture content (Karacabeyli and Douglas, 2013)), layup of the lumber boards, and adhesive application. The thickness of the boards can vary (0.675–2 inches), and various adhesives (e.g., polyurethane, melamine, phenol-based) are used for gluing the panels (Karacabeyli and Douglas, 2013). The panels are then cured, pressed, finished, packaged, and transported by truck to the building construction site.
Impacts from each of these phases can be estimated in LCA studies. LCA studies of CLT often consist of two types of analyses: 1) cradle-to-construction-gate analysis (Robertson et al., 2012; Chen et al., 2019; Greene et al., 2023), which includes the phases A1 to A5 (Figure 1), and 2) cradle-to-grave analysis, which includes the phases A, B, and C, and is an analysis from raw material extraction to end of life of the product (Dodoo et al., 2014; Guo et al., 2017; Rajagopalan and Kelley, 2017; Chiniforush et al., 2018; Andersen et al., 2022; Dodoo et al., 2022; Duan et al., 2022; Al-Najjar and Dodoo, 2023; Duan, 2023; Greene et al., 2023; Shin et al., 2023). Supply chain impacts, if included, would be captured in phase A. These studies use the Cumulative Energy Demand (CED) and Tool for Reduction and Assessment of Chemicals and Other Environmental Impacts (TRACI) methods to measure various LCA impacts, including the cumulative energy demand and the GWP impact, among others. Choosing different system boundaries will result in different embodied primary energy estimates. In some instances, CLT buildings had a lower cradle-to-grave (phases A–C) embodied primary energy when compared to RC buildings (Guo et al., 2017; Duan et al., 2022) and even other timber construction systems (e.g., beam-and-column, pre-fabricated modular buildings) (Dodoo et al., 2014). However, when considering a cradle-to-construction-gate system boundary (A1–A5), CLT building construction embodied energy was nearly double that of an RC building (Robertson et al., 2012) and marginally more than a functionally equivalent concrete building (Liang et al., 2020). Generally, CLT buildings result in lower carbon dioxide emissions compared to RC buildings (Hammond and Jones, 2011; Mallo and Espinoza, 2014; Moncaster et al., 2018; Lolli et al., 2019; Andersen et al., 2022; Duan et al., 2022; Duan, 2023) and steel-framed buildings (Greene et al., 2023). When considering the production and construction phases, CLT buildings can have less than half the embodied carbon of functionally equivalent concrete and steel buildings (Hammond and Jones, 2011) and half the embodied carbon of glue-laminated timber buildings (Lolli et al., 2019).
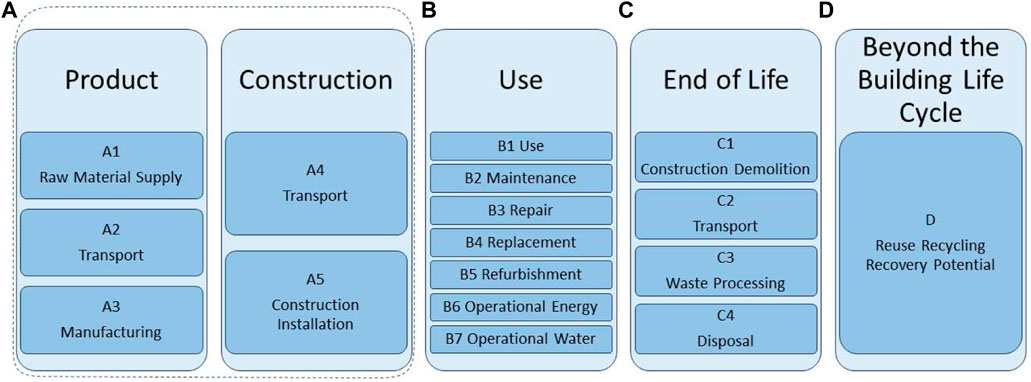
FIGURE 1. Life-cycle phases of a building. The dotted line indicates the life-cycle phases considered in this paper.
However, few studies consider the logistics of manufacturing CLT panels and the impact of distances traveled for transporting materials and products. Chen et al. (2019) considered four case studies with different locations of sawmills and CLT mills in western Washington and determined that the species mix and transportation distances for the lumber and CLT panel significantly impact the carbon dioxide emissions of the CLT panels. The lighter Sitka spruce species, when compared to a heavier mix of 50% Douglas fir and Western hemlock, reduced the GWP by 29%. Similarly, in a case with a 440 km transportation distance from the sawmill to the CLT mill and 322 km from the CLT mill to the building site, transportation contributed 20% of the total GWP (Chen et al., 2019). Liang et al. (2020) performed a sensitivity analysis on the transportation distances for CLT panels and concluded that sourcing across the United States could result in a global warming impact four times greater than if the timber was sourced within the state. Hemmati et al. (2022) performed an LCA on the A4 stage (transport of panels from manufacturer to building site) and concluded that emissions from panel transportation increase in the order of marine, rail, and road transport, but did not evaluate more than one site location scenario.
In the literature, the importance of supply chain aspects in calculating the environmental impact of CLT is evident; however, additional research is needed to analyze their impacts in detail. Different timber species are grown in different areas across the United States, and the difference in the processing inputs—including the type and amount of fuels used in the trucks and machinery, the fraction of the timber co-products used as fuel, and the electricity grid mix of the region—can also affect the embodied primary energy and GWP impacts of CLT construction. These regional variations in timber forestry were not considered in the current CLT impacts literature. Additionally, mass timber is a technology specifically catering to dense urban regions, some of which are longer distances (more than 1,000 km) from timber producing regions than considered in relevant literature. In this study, we develop a Python-based open-source model of the impacts of sourcing decisions for CLT that can model construction supply chain scenarios for buildings across the U.S. The tool offers the flexibility to model species selection, growth locations, and transport options among others to serve as a resource for sustainable planning of the CLT supply chain for practitioners. We also use this tool to model four scenarios that show the impacts of cross-country versus local transport of CLT panels for processing and construction, as well as the effects of sourcing timber for CLT from two major wood producing regions, the Pacific Northwest (PNW) and Southeast (SE).
2 Materials and methods
2.1 Overview
A comparative LCA on a CLT building and an RC building using Cumulative Energy Demand (CED) estimates the embodied primary energy, and the Tool for Reduction and Assessment of Chemicals and Other Environmental Impacts (TRACI) life-cycle impact assessment methods estimates the GWP, among other environmental impacts, of the buildings. The building selected from the tool database for the case represented here was a 12-story, 8,360-m2 floor area CLT designed by LEVER Architecture for mixed use as an office and apartment building in Portland, Oregon. This building and its functionally equivalent RC building, designed by the same company, were also used in another comparative LCA (Liang et al., 2020). The functional unit of analysis was 1 m2 of floor area.
After the initial LCA (A1–A5) of the buildings was completed, it was extended to include four scenarios (A–D), varying the timber source region, timber species, mill location, and building location, as outlined in Table 1. The PNW region accounted for 27% of the nation’s softwood lumber production in 2012, 95% of which was Douglas fir (Milota and Puettman, 2019). Southern pine mills accounted for 49% of the U.S. softwood lumber production in 2012. Southern pine primarily consists of one or more similar species of longleaf, loblolly, and slash pines (Milota and Puettman, 2020). Given the contribution of the PNW and SE regions to the total softwood lumber production in the United States, these regions were selected as sourcing locations in the four scenarios. CLT mill locations were selected based on reports of planned and existing manufacturing facilities (Huang et al., 2019; Milliken, 2019; Sterling Solutions, 2019). Combining these mill locations and different building site locations, the scenarios outlined in Table 1 were chosen to reflect possible realistic transportation distances in the U.S. CLT supply chain.
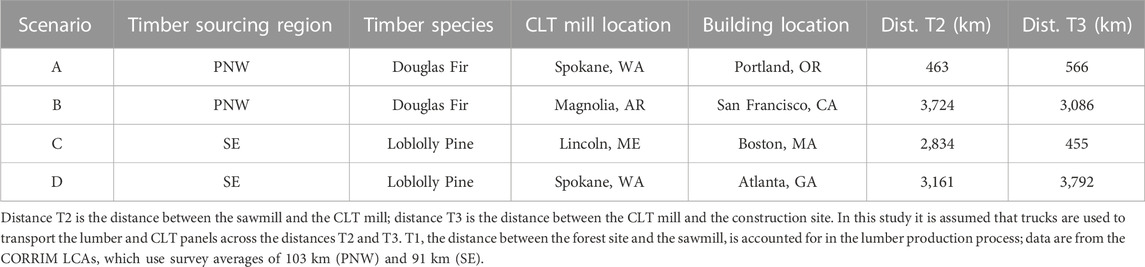
TABLE 1. Region from where timber is sourced (PNW vs. SE), locations of sawmills, CLT mills, and the building for the scenarios considered.
To model the scenarios, the user-interactive Python tool accepts input parameters that include the timber species to be used as well as the locations of the CLT mill and the building site. The tool also allows the user to select one of several CLT building configurations stored in the tool’s database, from which it estimates the bill of materials (BOM) for the building. The tool then calculates the embodied primary energy and GWP for the CLT building and a functionally equivalent RC concrete building. LCA processes from the U.S. Life Cycle Inventory (Federal LCA Commons, 2012) database and the Datasmart life-cycle inventory (LCI) package (Long Trail Sustainability, 2019) are used in the analysis. The system boundary for all analyses includes the life-cycle phases A1–A5, which corresponds to a cradle-to-construction-gate analysis, as shown in Figure 1.
2.2 Buildings LCA
The Python tool has a stored database consisting of a number of proposed or constructed CLT buildings in the United States and Canada, and two RC buildings. The database stores the floor area and the corresponding amount of materials mentioned in the BOM of the buildings. The BOMs have been compiled from either peer-reviewed publications or environmental product declarations for both CLT buildings and RC buildings (Ochsendorf et al., 2011; Huang et al., 2019; Liang et al., 2020). With the assumption that the quantity of each material is directly proportional to the required floor area input by the user, the tool calculates the updated BOM for both of the buildings. The life cycle impact assessment results per unit of each material stored are in the tool’s database. The material amounts from the BOM, along with the tool’s database, are used to get the mid-point life-cycle impacts. The A4 phase transportation distances of all materials except CLT were compiled and averaged from other published reports and environmental product declarations, or assumed to be 300 km if no information for the material was found (Ochsendorf et al., 2011; Bowick, 2014; Bowick, 2015; Bowick, 2016; Bowick, 2018a; Bowick, 2018b). Assumptions about the material and energy inputs for on-site construction processes—including operation of machinery using diesel, electricity, and gasoline, which form phase A5 of the LCA—were made by analyzing data in published reports about the CLT (Bowick, 2014; Bowick, 2015; Bowick, 2016; Bowick, 2018a; Bowick, 2018b) and RC buildings (Junnila and Horvath, 2003; Yan et al., 2010; Zhan et al., 2018).
2.3 LCA of cross-laminated timber
Based on the user inputs and the corresponding BOM, the volume of CLT required for the building is calculated. CORRIM has published cradle-to-gate (A1–A3) LCAs for softwood lumber produced in the PNW, SE, Inland Northwest (INW), and North Central (NC) regions of the United States (Milota and Puettman, 2019; Milota and Puettman, 2020; Puettmann, 2019a; Puettmann, 2019b). The comprehensive and regionally specific analysis takes into account the differences in these regions (e.g., in the density of timber species, local transportation distances for transporting logs, fertilizers used, forestry practices) using data obtained from surveys on local forestry operations and sawmills. CORRIM LCAs’ system boundary includes the phase from greenhouse operations to the planer mill, where the lumber is packaged and ready to be sent to the CLT mill. Data from these LCAs are directly used in the tool to model the lumber production process.
The CLT manufacturing process is modeled based on the LCA published by Katerra, a construction products company, to analyze the impacts of CLT produced in their facility in Spokane, Washington (Huang et al., 2019). In the Katerra facility, the lumber is first fed into the kiln for further drying, after which it is finger jointed, sorted according to the size, lay-ed up for adhesive application, and following the application of the adhesive and finishing, sent for packing. The baseline material and energy inputs required per m3 of CLT were considered. The material and energy inputs required for packaging the CLT were estimated from the CORRIM LCA on CLT (Milota and Puettman, 2019; Milota and Puettman, 2020).
Transportation processes (A2 and A4) in the CLT supply chain are modelled as shown in Figure 2. T1, the transportation distance of logged timber to the sawmill and a part of the LCA phase A1, is accounted for in the CORRIM processes (Milota and Puettman, 2019; Milota and Puettman, 2020). The CORRIM surveys found averages of about 100 km for all regions. T2, the transportation distance for processed lumber from the sawmill to the CLT mill, and T3, the transportation distance for the CLT panels from the CLT mill to the construction site, are variable depending on the location of the CLT mill and the building. It is assumed that trucks are used to transport the lumber and CLT panels across the T2 and T3 distances. The locations of the CLT mill and the building site are added by the user of the tool.
Lumber processing is a mature and widespread industry in the United States, and it is difficult to ascertain in which particular sawmill the timber used in CLT manufacturing was processed, which makes modeling the T2 distance a challenge. To overcome this issue, the following process was used to generate estimated T2 distances for each given timber species and state combination. A geo-spatial data set from the U.S. Department of Agriculture (USDA) Forest Service, mapping timber species to resource locations, was used to get the geographical coordinates of the timber resources (Ruefenacht et al., 2008). Sawmill locations were obtained from a USDA data set of wood processing mills (Prestemon et al., 2005). For every region, CORRIM specifies the average distance a log travels to the sawmill. Based on the selected timber species and the preferred sourcing state, the tool maps the CLT resources available in the state and selects the sawmills within 200 km specified by CORRIM. The tool uses the Google Maps API to compute these distances. The average of the distance between the selected sawmills and the CLT mill is used to compute the T2 distance. The final transportation T3 distance, from the CLT mill to the building site, is also computed by the Google Maps API, based on the CLT mill and building locations input by the user. The T2 and T3 distances generated by the tool for the scenarios A to D are in Table 1. The model code and supporting data are publicly available on GitHub.
3 Results
Table 2 compares the cradle-to-construction-gate (A1–A5) life-cycle impacts for embodied primary energy and GWP for the CLT building in scenario A and the RC building on a per-m2 basis. The embodied primary energy from phases A1–A5 of a CLT building is higher than the RC building by 6.1%. The major contributors to the embodied primary energy for the CLT building are non-renewable fossil energy, followed by renewable biomass energy. Other energy impact categories account for less than 17% of the total embodied primary energy. The higher embodied primary energy of a CLT building can be attributed primarily to renewable biomass energy, which is consumed 1,600% more in a CLT building than the RC building. 64% of this renewable biomass energy is consumed in the production of softwood lumber, which is a raw material in CLT panels manufacturing. The drying of lumber to a moisture content of 19%, as required by grading rules for lumber, is the process that consumes almost all of the renewable biomass energy (Milota and Puettman, 2019; Milota and Puettman, 2020). However, this study found that the embodied fossil energy per unit floor area of a CLT building is 21% lower than that of the RC building. This is important to note because non-renewable fossil energy accounts for 85% of the A1–A5 embodied primary energy in an RC building, and 63% in a CLT building. The CLT building also has a 50% less GWP per m2 of floor area when compared to the RC building. Of the total embodied primary energy of the CLT building, CLT manufacturing adds up to about 8%. When only the life-cycle impacts of the CLT panels are considered, CLT manufacturing contributes to 16% of the A1–A3 embodied primary energy of CLT panels, where the major contributors to embodied energy are the manufacturing of primer used in the gluing process (22%) and the natural gas consumption in the layup process (15%).
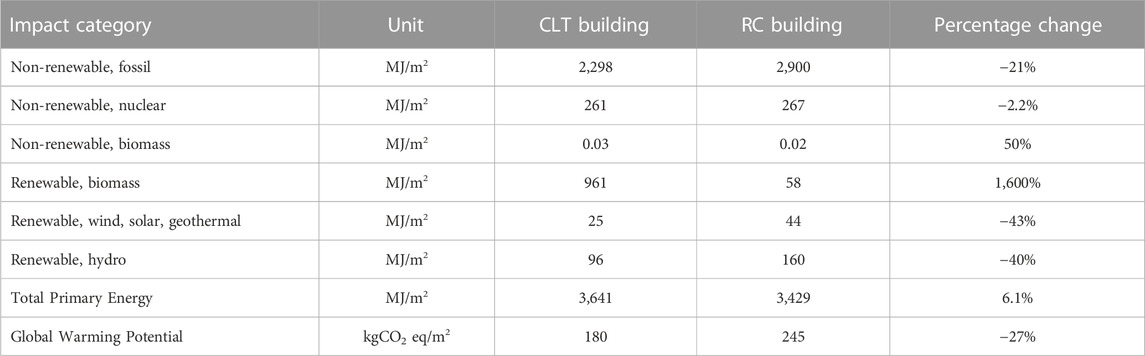
TABLE 2. Cradle-to-gate life-cycle impacts per m2 of floor area for a CLT building (Scenario A) and an RC building.
For both buildings, a major part of the total A1–A5 primary energy, about 94% for the CLT building and 81% for the RC building, is consumed by the time the materials reach the factory gate (A1–A3) (Figures 3, 4A). Transportation of sawn lumber (A2) and CLT panels (A4) for the CLT building account for 4% of the total A1–A5 embodied primary energy in scenario A, where the transportation distances are 463 km and 566 km for the respective phases, the lowest among the four scenarios. For phase A5, on-site construction energy consumption required is 2% of the total embodied energy. Conversely, for an RC building, on-site construction energy accounts for 16% of the total embodied primary energy.
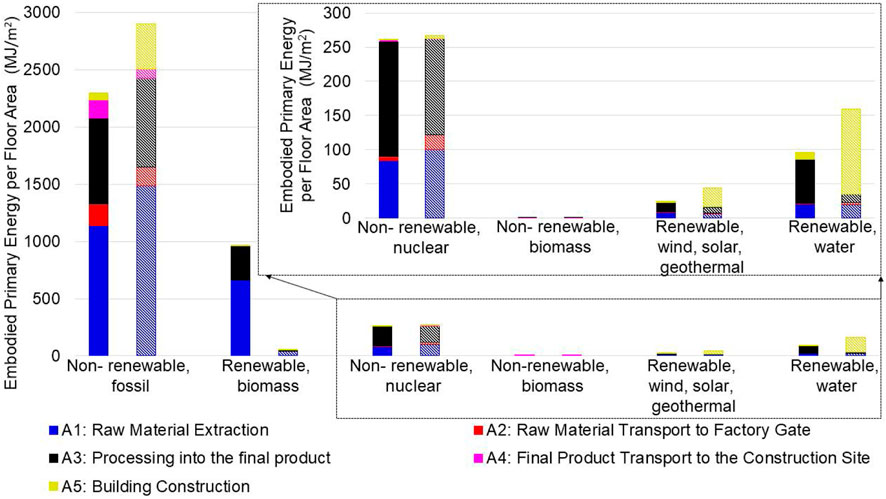
FIGURE 3. Phase-wise life-cycle impacts for a CLT building and an RC building for scenario A. For each life-cycle impact, the columns describe the CLT building impacts (left) and the RC building impacts (right, texture). Inset in the top right corner shows more detail of the last four categories. Background data for this figure can be found in Supplementary Tables S1–S5.
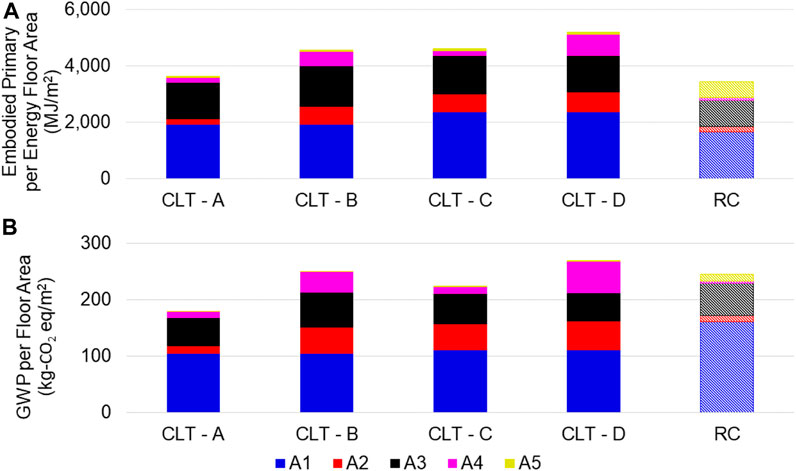
FIGURE 4. (A) Embodied primary energy per floor area for the CLT building scenarios and the RC building for life-cycle phases A1–A5. (B) Phase-wise GWP per floor area for the CLT building scenarios and the RC building for life-cycle phases A1–A5.
Figure 3 shows the segmentation of cradle-to-gate embodied primary energy by life-cycle phase and energy type. The total embodied primary energy of the RC building is less than the CLT building (Table 2), but the non-renewable fossil embodied energy is higher. Phases A1 and A3 are the major contributors to the non-renewable fossil energy in the RC building, and the same applies for the CLT building in scenario A, where the lumber and CLT transportation distances are the lowest among the four cases. Using trucks, lumber transportation (A2) and CLT panel transportation (A4) combined make up as much as 6% of the embodied fossil energy of the CLT building. About 7% of the embodied fossil energy in the CLT building is attributed to transporting all the required materials from the gate of the factory to the building site. About half of this is consumed in the transportation of the panels from the CLT mill to the building site itself.
Given the lower transportation distances between sites in scenario A, the impacts of transportation are not pronounced. However, for higher transportation distances, especially in scenarios B and D, where CLT panels are transported by truck across the United States before reaching their destination, the energy consumption in transportation is more pronounced (Figure 4A). In all figures, the impacts for phases A2 and A4 include the impacts resulting from transportation of all required inputs for the building, and not just the CLT panels. The relative contributions of the transportation of CLT panels to the total embodied primary energy of the CLT building are shown in Figure 5A. The higher transportation distances of CLT panels in scenarios B and D yield total embodied primary energy considerably higher than the RC building, as shown in Figure 4A. The use of the heavier loblolly pine species found in the SE United States was the reason for scenario D having an even greater embodied primary energy, even though scenarios B and D had comparable transportation distances for the panels. Similarly, Figure 4B shows that the GWP impact of the CLT building in scenarios B and D exceeds that of the RC building; thus, the low-carbon advantage for the CLT building, which was observed in scenario A, is no longer present. Additionally, Figure 4A shows that the embodied energy from phase A1 is higher for scenarios C and D than scenarios A and B, which can be attributed to the difference in the inputs to lumber processing in sawmills in the PNW and SE.
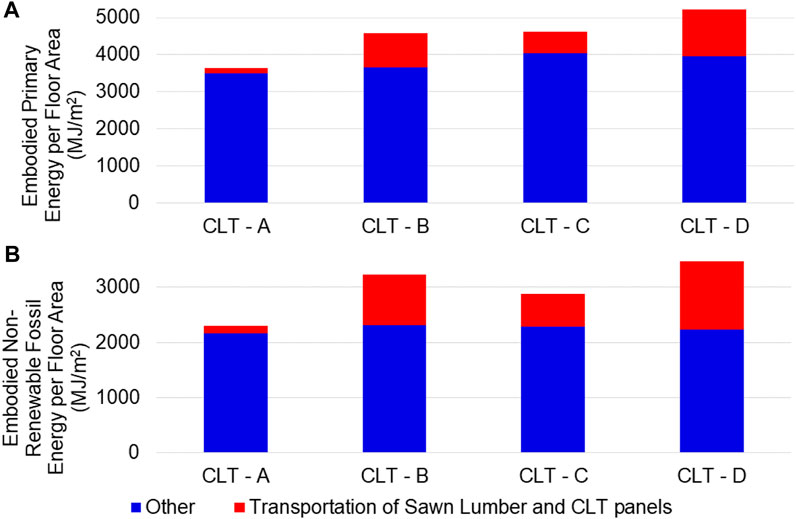
FIGURE 5. (A) Share of transportation of sawn lumber and CLT panels in the total embodied primary energy of the CLT buildings for life-cycle phases A1–A5. (B) Share of transportation of sawn lumber and CLT panels in the total non-renewable fossil embodied energy of the CLT buildings for life-cycle phases A1–A5.
Figure 5A shows the contribution of the transport of lumber and CLT panels to the A1–A5 embodied primary energy of the four CLT building scenarios. In scenario A, the transportation of lumber and CLT panels is a negligible percentage of the total embodied primary energy. However, in scenarios B, C, and D, the embodied energy due to transportation accounts for as much as 20%, 13%, and 24% of the A1–A5 embodied primary energy in the CLT building. This is further amplified when only the embodied fossil energy is considered. Figure 5B shows that in scenario A, the contribution of the transport of CLT panels is 6%, but increases to 28%, 20%, and 35% for scenarios B, C, and D, respectively. Similarly, the contributions of lumber and panel transportation to the GWP of the CLT buildings is 5.7% for scenario A (Supplementary Table S1), and increases to 27%, 19%, and 34% for scenarios B (Supplementary Table S2), C (Supplementary Table S3), and D (Supplementary Table S4), respectively. Thus, as discussed before, the transportation distances for the lumber and panels, as well as the weight of the species used, impact the embodied primary energy of the CLT building. More importantly, decisions that affect these factors can help in reducing the embodied fossil energy of the CLT building.
4 Discussion
CLT has generated interest in the North American architecture, engineering, and construction community for its potential to reduce the environmental impact of new construction. In a survey of CLT experts, more than 70% agreed that CLT has the potential to be an environmentally-friendly substitute for steel, concrete, or masonry, while others said that adoption will most likely vary from region to region (Mallo and Espinoza, 2014). A number of studies have discussed the environmental impacts of CLT, with several finding that CLT buildings have a lower GWP than comparable RC buildings (Hammond and Jones, 2011; Mallo and Espinoza, 2014; Cadorel and Crawford, 2018; Moncaster et al., 2018; Lolli et al., 2019), whereas the conclusions for embodied energy vary between studies. However, these studies do not consider the wide range of material sourcing options that could substantially change environmental impact. This study fills that gap by considering the impacts of supply chain scenarios on the embodied primary energy and the resulting GWP of CLT construction.
The total A1–A5 embodied primary energy per unit floor area of the CLT building scenarios ranged from 3,641 MJ/m2 to 5,213 MJ/m2, always higher than the 3429 MJ/m2 for a RC building (Table 2 and Supplementary Table S4). However, the embodied fossil energy per floor area of the CLT building in Scenario A was lower than the RC building. This is due to the extensive use of materials like steel and concrete in the RC building, which require fossil-fuel-intensive production methods and a fossil-fuel-intensive construction process. The renewable wind, solar, geothermal, and hydro-power embodied energies was also found to be lower in the CLT building. This difference can be attributed to 1) the assumptions about electricity use and requirements (see Section 2.2) in on-site construction, where the CLT building required 4 kWh/m2 of electricity compared to 52 kWh/m2 for the RC building, and 2) the electricity generation asset mix at the construction site in Oregon. These assumptions about the construction phase caused differences in results with other published studies and explain the low percentage of total A1–A5 embodied energy from the construction phase in the CLT building (2%) as compared to the RC building (16%).
Our results indicate the importance of transportation of CLT panels and lumber, the species used, and the lumber processing specific to the region where they are sourced from in the CLT supply chain. These factors can result in as much as a 49% higher A1–A5 embodied primary energy for a CLT building than an RC building. The embodied primary energy per unit floor area of the CLT building scenarios ranged from 1.04 (scenario A, Supplementary Table S1) to 1.49 (scenario D, Supplementary Table S4) times that of an RC building. Longer transportation distances also increase the embodied fossil energy of the building. The A1–A5 embodied fossil energy of a CLT building is lower than an RC building when the CLT supply chain spans across a state or a neighbouring state, with T2 and T3 transportation distances less than 600 km. However, when the locations for sourcing lumber, processing it into CLT, and the ultimate destination of the building under construction stretch across the contiguous United States (Scenarios B and D), the embodied fossil energy impacts surpasses that of an RC building (Supplementary Tables S2, S4, S5).
The lumber species used in CLT can also impact the embodied energy of transportation and the sawmill processing energy. Scenarios B and D in this study have similar transportation distances (Table 1), but the transportation energy consumption of scenario D is higher than B due to the higher density of the loblolly pine species found in the SE (Figure 5). Additionally, Scenarios C and D have a higher embodied energy from phase A1 compared to scenarios A and B, due to differences in the inputs for processing the raw timber into lumber in the sawmills in the PNW and SE. For example, processing lumber in sawmills in the PNW contributes 493 MJ/m3 to the embodied non-renewable fossil energy and 2,431 MJ/m3 to the embodied renewable biomass energy, which is less than the 677 MJ/m3 and 3,769 MJ/m3 for the SE sawmills (Milota and Puettman, 2019; Milota and Puettman, 2020).
In terms of GWP, this study found that the impact of the CLT building in Scenario A (180 kgCO2eq/m2) was less than the RC building (245 kgCO2eq/m2). Like embodied energy, the GWP also increased with transportation distances for the lumber and panels, surpassing the GWP of the RC building in scenarios B and D. Additionally, using a less dense Sitka spruce species instead of a heavier mix of 50% Douglas fir and Western hemlock also reduced the GWP. The reduction in the GWP of lumber transportation for scenario B compared to scenario D was 11%. This difference is primarily attributed to Douglas fir being 34% less dense than loblolly pine, as the T2 transportation distances for scenario B and D were similar.
The results of this study were also compared to other CLT studies. For the embodied energy, the scenario A results were similar to Dodoo et al. (2014) (3233 MJ/m2) and Liang et al. (2020) (2,868 MJ/m2), but results for scenarios B, C, and D were higher than the literature values. The comparatively higher embodied primary energy for these scenarios could be due to a few reasons. First, the tool modelled realistic cross-country supply chains for CLT and thus, the transportation distances used in this study were greater than other studies. Second, the material and energy inputs data used for lumber production and processing was taken from the detailed and regionally specific CORRIM studies. The GWP impacts found in this study were also similar to the results of Liang et al. (2020), and similar to the observations in that study, the GWP increased for higher transportation distances. Guo et al. (2017) concluded that a comparable 11-story CLT building would remove 96.9 kg CO2/m2 from the atmosphere; however, because biogenic carbon was not considered in this study, a comparison to their findings cannot be made.
The findings from this study highlight the importance of considering the impacts of CLT manufacturing and construction from a systems perspective. We find that when the transportation distances increase, the GWP and embodied primary energy impacts of the CLT building exceed that of the RC building. Using a heavier timber species like Loblolly pine compared to Douglas fir for manufacturing CLT also increases the GWP impact of CLT construction. This does not, however, mean that species density is the only factor to be considered to increase the sustainability of CLT buildings, as other factors—the availability of species in different regions, impacts of commercial forestation of a certain species on the land, economics of forest products, and land use impacts on local communities—were not considered in this study. However, if the carbon storing properties of wood are included in the assessment, the GWP of the CLT buildings will likely decrease. The study indicates that factors such as the location of CLT processing facilities and the type of timber species used for manufacturing, if chosen appropriately, can play an important role in mitigating the environmental impacts of CLT construction. Although upfront supply chain factors might be options to reduce the life-cycle environmental impact, there is additional potential to further reduce the impact of materials on CLT construction if we are able to consider the end-of-life fate of these materials in the calculation. However, how end-of-life considerations might affect the economics of CLT construction, and how policy might influence CLT construction material disposition choices at end-of-life, remains to be studied.
5 Conclusion
Buildings contribute significantly to global energy use and GHG emissions; as building area increases, this share is projected to increase. Recent research has focused on increasing the operational energy efficiency of buildings and achieving net-zero emissions building operations. Buildings have become more efficient in their operational phase as a result, to the point where embodied energy and carbon have emerged as critical to decarbonization. Concrete and steel, materials that have high embodied energy and carbon, have been traditionally used to construct mid- and high-rise buildings. Mass timber has emerged as a potential low embodied carbon alternative for mid- and high-rise construction.
We identified the need to analyze the uncertainty around the embodied energy and carbon of mass timber buildings by considering timber properties, locations of processing, local forestry activities, and sourcing options. We created an open-source Python-based tool that allows users to calculate the embodied energy and carbon for a given timber building by taking into account the amount of timber required, the species used, its weight and moisture content, and the location of timber, saw mills, CLT mills, and the constructed building. Thus, users can employ this tool to accurately describe the impacts on embodied carbon of their upstream choices in the supply chain, and thus make informed decisions that minimize the embodied energy and carbon of buildings.
Our results indicate that the embodied energy of the mass timber building was higher than an equivalent RC building. However, the CLT building requires less fossil fuel-derived energy and can have lower embodied carbon than the RC building. If cross-country transportation is required, the embodied fossil energy use and embodied carbon of the CLT building surpasses that of the RC building. Additionally, lower density tree species reduce transportation emissions by lowering the tonnage to be transported. However, species with the required prices, properties, and aesthetics might not always be available closer to a building construction site. Differences in forestry activities across the country also result in different embodied energy and carbon for timber grown in particular regions. Certain regions of the country do not have enough timber resources to spur the development of a timber industry. In such regions, optimizing all supply chain decisions is not always possible. Our tool can be used to assess a variety of options for such regions. Future modeling efforts for the tool could include adding end-of-life considerations for CLT panels and how these considerations might affect construction economics and embodied energy and carbon impacts of CLT buildings.
Data availability statement
Publicly available datasets were analyzed in this study. The data and model can be found at: https://github.com/NREL/CLT-LCA-Tool.
Author contributions
SA: Conceptualization, Data curation, Formal Analysis, Investigation, Methodology, Resources, Software, Validation, Visualization, Writing–original draft, Writing–review and editing. OG: Conceptualization, Methodology, Writing–review and editing. SH: Conceptualization, Methodology, Writing–review and editing. HG: Conceptualization, Funding acquisition, Methodology, Project administration, Supervision, Writing–review and editing. CH: Conceptualization, Funding acquisition, Methodology, Project administration, Resources, Supervision, Writing–review and editing.
Funding
The authors declare financial support was received for the research, authorship, and/or publication of this article. Funding for this project was provided by the U.S. Department of Energy Office of Energy Efficiency and Renewable Energy Building Technologies Office.
Acknowledgments
This work was authored by the National Renewable Energy Laboratory, operated by Alliance for Sustainable Energy, LLC, for the U.S. Department of Energy (DOE) under Contract No. DE-AC36-08GO28308. The U.S. Government and the publisher, by accepting the article for publication, acknowledges that the U.S. Government retains a nonexclusive, paid-up, irrevocable, worldwide license to publish or reproduce the published form of this work, or allow others to do so, for U.S. Government purposes. The authors appreciate the thoughtful reviews of Deanna Cook, Emily Newes, and Dan Bilello.
Conflict of interest
The authors declare that the research was conducted in the absence of any commercial or financial relationships that could be construed as a potential conflict of interest.
Publisher’s note
All claims expressed in this article are solely those of the authors and do not necessarily represent those of their affiliated organizations, or those of the publisher, the editors and the reviewers. Any product that may be evaluated in this article, or claim that may be made by its manufacturer, is not guaranteed or endorsed by the publisher.
Author disclaimer
The views expressed in the article do not necessarily represent the views of the DOE or the U.S. Government.
Supplementary material
The Supplementary Material for this article can be found online at: https://www.frontiersin.org/articles/10.3389/fbuil.2023.1321340/full#supplementary-material
Footnotes
1This scenario assumes that 90% of new construction is timber and 79.1 m2 of floor area per capita is required.
References
Akbarnezhad, A., and Xiao, J. (2017). Estimation and minimization of embodied carbon of buildings: a review. Buildings 7, 5. doi:10.3390/buildings7010005
Al-Najjar, A., and Dodoo, A. (2023). Modular multi-storey construction with cross-laminated timber: life cycle environmental implications. Wood Material Sci. Eng. 18, 525–539. doi:10.1080/17480272.2022.2053204
Andersen, J. H., Rasmussen, N. L., and Ryberg, M. W. (2022). Comparative life cycle assessment of cross laminated timber building and concrete building with special focus on biogenic carbon. Energy Build. 254, 111604. doi:10.1016/j.enbuild.2021.111604
Bowick, M. (2014). The lafarge innovation Hub, Edmonton, AB: an environmental building declaration according to EN 15978 standard. Ottawa, ON, Canada: Athena Sustainable Materials Institute. Tech. rep.
Bowick, M. (2015). Wood innovation and design centre, Prince George, BC: an environmental building declaration according to the EN 15978 standard. Ottawa, ON, Canada: Athena Sustainable Materials Institute. Tech. rep.
Bowick, M. (2016). Design building, University of Massachusetts: an environmental building declaration according to EN 15978 standard. Amherst: Athena Sustainable Materials Institute. Tech. rep.
Bowick, M. (2018a). Brock commons tallwood house, University of British Columbia: an environmental building declaration according to EN 15978 standard. Athena Sustainable Materials Institute Tech. rep.
Bowick, M. (2018b). Ponderosa commons cedar house, University of British Columbia: an environmental building declaration according to EN 15978 standard. Athena Sustainable Materials Institute Tech. rep.
Cabeza, L. F., Bai, Q., Bertoldi, P., Kihila, J., Lucena, A. F., Mata, E., et al. (2022). Climate change 2022: mitigation of climate change, chapter 9: buildings (accepted draft). Intergovernmental Panel on Climate Change Tech. rep.
Cadorel, X., and Crawford, R. (2018). “Life cycle analysis of cross laminated timber in buildings: a review,” in Proceedings of 52nd International Conference of the Architectural Science Association, Melbourne, Australia (The Architectural Science Association and RMIT University), 107–114.
Chen, C. X., Pierobon, F., and Ganguly, I. (2019). Life cycle assessment (LCA) of cross-laminated timber (CLT) produced in western Washington: the role of logistics and wood species mix. Sustainability 11, 1278. doi:10.3390/su11051278
Chiniforush, A. A., Akbarnezhad, A., Valipour, H., and Xiao, J. (2018). Energy implications of using steel-timber composite (STC) elements in buildings. Energy Build. 176, 203–215. doi:10.1016/j.enbuild.2018.07.038
Churkina, G., Organschi, A., Reyer, C. P. O., Ruff, A., Vinke, K., Liu, Z., et al. (2020). Buildings as a global carbon sink. Nat. Sustain. 3, 269–276. doi:10.1038/s41893-019-0462-4
Dodoo, A., Gustavsson, L., and Sathre, R. (2014). Lifecycle primary energy analysis of low-energy timber building systems for multi-storey residential buildings. Energy Build. 81, 84–97. doi:10.1016/j.enbuild.2014.06.003
Dodoo, A., Nguyen, T., Dorn, M., Olsson, A., and Bader, T. K. (2022). Exploring the synergy between structural engineering design solutions and life cycle carbon footprint of cross-laminated timber in multi-storey buildings. Wood Material Sci. Eng. 17, 30–42. doi:10.1080/17480272.2021.1974937
Duan, Z. (2023). Impact of climate change on the life cycle greenhouse gas emissions of cross-laminated timber and reinforced concrete buildings in China. J. Clean. Prod. 395, 136446. doi:10.1016/j.jclepro.2023.136446
Duan, Z., Huang, Q., Sun, Q., and Zhang, Q. (2022). Comparative life cycle assessment of a reinforced concrete residential building with equivalent cross laminated timber alternatives in China. J. Build. Eng. 62, 105357. doi:10.1016/j.jobe.2022.105357
Evans, L. (2018). Cross laminated timber: taking wood buildings to the next level. American Wood Council, reThink Wood, FPInnovations. Tech. rep.
Federal LCA Commons (2012). U.S. Life cycle inventory database. Washington, DC, United States: U.S. Department of Agriculture. Tech. rep.
Greene, J. M., Hosanna, H. R., Willson, B., and Quinn, J. C. (2023). Whole life embodied emissions and net-zero emissions potential for a mid-rise office building constructed with mass timber. Sustain. Mater. Technol. 35, e00528.doi:10.1016/j.susmat.2022.e00528
Guo, H., Liu, Y., Meng, Y., Huang, H., Sun, C., and Shao, Y. (2017). A comparison of the energy saving and carbon reduction performance between reinforced concrete and cross-laminated timber structures in residential buildings in the severe cold region of China. Sustainability 9, 1426. doi:10.3390/su9081426
Hammond, G., and Jones, C. (2011). Embodied carbon: the inventory of carbon and energy (ICE). Bracknell, United Kingdom: University of Bath, BSRIA.
Hemmati, M., Messadi, T., and Gu, H. (2022). Life cycle assessment of cross-laminated timber transportation from three origin points. Sustainability 14, 336. doi:10.3390/su14010336
Himes, A., and Busby, G. (2020). Wood buildings as a climate solution. Dev. Built Environ. 4, 100030. doi:10.1016/j.dibe.2020.100030
Huang, M., Chen, C. X., Pierobon, F., Ganguly, I., and Simonen, K. (2019). Life cycle assessment of katerra’s cross-laminated timber (CLT) and catalyst building final report. Seattle, WA, United States: University of Washington. Tech. rep.
Ibn-Mohammed, T., Greenough, R., Taylor, S., Ozawa-Meida, L., and Acquaye, A. (2013). Operational vs. embodied emissions in buildings—a review of current trends. Energy Build. 66, 232–245. doi:10.1016/j.enbuild.2013.07.026
International Energy Agency (2023). Tracking buildings. Paris, France: International Energy Agency. Tech. rep.
Junnila, S., and Horvath, A. (2003). Life-cycle environmental effects of an office building. J. Infrastructure Syst. ⓒ ASCE 9, 157–166. doi:10.1061/(asce)1076-0342(2003)9:4(157)
Karacabeyli, E., and Douglas, B. (2013). CLT handbook: cross-laminated timber. Pointe-Claire, QC, Canada: U.S. Department of Agriculture, Forest Service, Forest Products Laboratory, Binational Softwood Lumber Council.
Liang, S., Gu, H., Bergman, R., and Kelley, S. (2020). Comparative life-cycle assessment of a mass timber building and concrete alternative. Wood Fiber Sci. 52, 217–229. doi:10.22382/wfs-2020-019
Lolli, N., Fufa, S. M., and Kjendseth Wiik, M. (2019). An assessment of greenhouse gas emissions from CLT and glulam in two residential nearly zero energy buildings. Wood Material Sci. Eng. 14, 342–354. doi:10.1080/17480272.2019.1655792
Mallo, M. F. L., and Espinoza, O. A. (2014). Outlook for cross-laminated timber in the United States. BioResources 9, 7427–7443. doi:10.15376/biores.9.4.7427-7443
McCulloch, S., Masanet, E., Dulac, J., Abergel, T., West, K., Dockweiler, S., et al. (2017). Energy technology perspectives 2017: catalysing energy technology transformations. International Energy Agency. Tech. rep.
Milota, M., and Puettman, M. (2019). Life cycle assessment for the production of Pacific Northwest softwood lumber. Consortium for Research on Renewable Industrial Materials. Tech. rep.
Milota, M., and Puettman, M. (2020). Life cycle assessment for the production of Pacific Northwest softwood lumber. Consortium for Research on Renewable Industrial Materials. Tech. rep.
Moncaster, A., Pomponi, F., Symons, K., and Guthrie, P. (2018). Why method matters: temporal, spatial and physical variations in LCA and their impact on choice of structural system. Energy Build. 173, 389–398. doi:10.1016/j.enbuild.2018.05.039
Ochsendorf, J., Norford, L. K., Brown, D., Durschlag, H., Hsu, S. L., Love, A., et al. (2011). Methods, impacts, and opportunities in the concrete building life cycle. Cambridge, MA, United States: Massachusetts Institute of Technology. Tech. rep.
Prestemon, J., Pye, J., Barbour, J., Smith, G., Ince, P., Steppleton, C., et al. (2005). U.S. Wood-using mill locations - 2005. Washington, DC, United States: U.S. Forest Service. Tech. rep.
Puettmann, M. (2019a). CORRIM report: life cycle assessment for the production of Inland Northwest softwood lumber. Consortium for Research on Renewable Industrial Materials. Tech. rep.
Puettmann, M. (2019b). CORRIM report: life cycle assessment for the production of Northeast - Northcentral softwood lumber. Consortium for Research on Renewable Industrial Materials. Tech. rep.
Rajagopalan, N., and Kelley, S. S. (2017). Evaluating sustainability of buildings using multi-attribute decision tools. For. Prod. J. 67, 179–189. doi:10.13073/FPJ-D-16-00028
Robertson, A. B., Lam, F. C. F., and Cole, R. J. (2012). A comparative cradle-to-gate life cycle assessment of mid-rise office building construction alternatives: laminated timber or reinforced concrete. Buildings 2, 245–270. doi:10.3390/buildings2030245
Röck, M., Saade, M. R. M., Balouktsi, M., Rasmussen, F. N., Birgisdottir, H., Frischknecht, R., et al. (2020). Embodied GHG emissions of buildings – the hidden challenge for effective climate change mitigation. Appl. Energy 258, 114107. doi:10.1016/j.apenergy.2019.114107
Ruefenacht, B., Finco, M., Nelson, M., Czaplewski, R., Helmer, E., Blackard, J., et al. (2008). National forest type dataset. Salt Lake City, UT, United States: U.S. Forest Service. Tech. rep.
Shin, B., Chang, S. J., Wi, S., and Kim, S. (2023). Estimation of energy demand and greenhouse gas emission reduction effect of cross-laminated timber (CLT) hybrid wall using life cycle assessment for urban residential planning. Renew. Sustain. Energy Rev. 185, 113604. doi:10.1016/j.rser.2023.113604
United Nations Environment Programme (2018). 2018 Global status report: towards a zero-emission, Efficient and Resilient buildings and construction sector. United Nations Environment Programme. Tech. rep.
United Nations Environment Programme (2021). 2021 global status report for buildings and construction: towards a zero-emission, efficient and resilient buildings and construction sector. Nairobi: United Nations Environment Programme. Tech. rep.
Vahidi, E., Kirchain, R., Burek, J., and Gregory, J. (2021). Regional variation of greenhouse gas mitigation strategies for the United States building sector. Appl. Energy 302, 117527. doi:10.1016/j.apenergy.2021.117527
Yan, H., Shen, Q., Fan, L., wang, Y., and Zhang, L. (2010). Greenhouse gas emissions in building construction: a case study of One Peking in Hong Kong. Build. Environ. 45, 949–955. doi:10.1016/j.buildenv.2009.09.014
Keywords: low-energy buildings, low-carbon building construction, mass timber, climate change, life cycle assessment, embodied carbon, embodied energy
Citation: Atnoorkar S, Ghatpande OA, Haile SL, Goetsch HE and Harris CB (2024) Carbon intensity of mass timber materials: impacts of sourcing and transportation. Front. Built Environ. 9:1321340. doi: 10.3389/fbuil.2023.1321340
Received: 13 October 2023; Accepted: 30 November 2023;
Published: 19 January 2024.
Edited by:
Soon Poh Yap, University of Malaya, MalaysiaReviewed by:
Arslan Akbar, City University of Hong Kong, Hong Kong SAR, ChinaHussein Ibrahim, Anglia Ruskin University, United Kingdom
Copyright © 2024 Alliance for Sustainable Energy, LLC. This is an open-access article distributed under the terms of the Creative Commons Attribution License (CC BY). The use, distribution or reproduction in other forums is permitted, provided the original author(s) and the copyright owner(s) are credited and that the original publication in this journal is cited, in accordance with accepted academic practice. No use, distribution or reproduction is permitted which does not comply with these terms.
*Correspondence: Chioke B. Harris, Y2hpb2tlLmhhcnJpc0BucmVsLmdvdg==