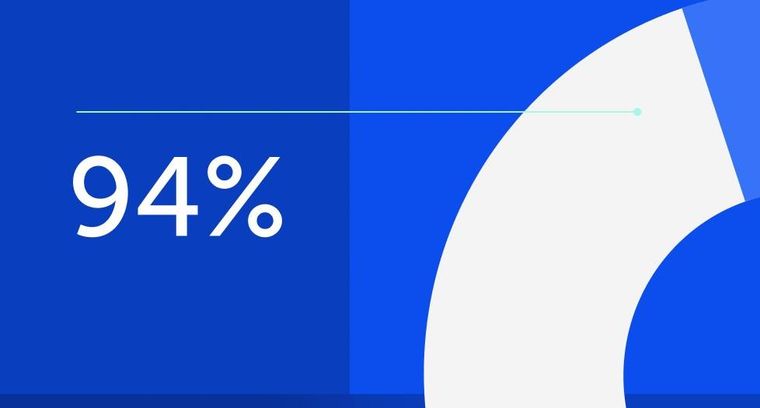
94% of researchers rate our articles as excellent or good
Learn more about the work of our research integrity team to safeguard the quality of each article we publish.
Find out more
ORIGINAL RESEARCH article
Front. Built Environ., 22 May 2023
Sec. Sustainable Design and Construction
Volume 9 - 2023 | https://doi.org/10.3389/fbuil.2023.1194121
Environmental awareness and the need for sustainable construction inspired researchers and practitioners to explore innovative alternatives that might reduce greenhouse gas emissions and energy use related to excessive structural work. One such alternative is the utilization of Fiber-Reinforced Polymer (FRP) bars as a reinforcement in reinforced concrete members. FRP bars possess favorable characteristics like high tensile strength, lightweight and corrosion resistance compared to steel. This feature makes FRP bars a potential solution for utilizing seawater instead of fresh water in concrete mixtures, especially in areas facing a harsh climate and water shortage like the Arabian Peninsula. This paper aims to assess and evaluate the environmental impacts through life cycle assessment of glass fiber-reinforced polymer bars, carbon fiber-reinforced polymer, and steel glass fiber reinforced polymer bars compared to steel bars. Moreover, another LCA was conducted comparing steel-reinforced beams made with desalinated fresh water to GFRP/CFRP reinforced beams made with seawater for the concrete mixture. The results indicate that the GFRP bar performed better than the steel bar in 10 out of 14 categories, while the carbon fiber-reinforced polymer bar performed worse than the steel bar in 10 out of 14 categories. The SGFRP bar had a result between the steel and GFRP bar, outperforming the steel bar in 10 categories. Furthermore, the GFRP beam exhibited better environmental performance than the steel beam in 9 out of 14 categories, while the CFRP beam performed better than the steel beam in 8 categories, attributed to the reduction in reinforcement ratio due to the high tensile strength of CFRP and GFRP bars compared to steel bars. Overall, this study sheds light on the possible environmental advantages of using FRP bars in construction and highlights the importance of sustainable construction practices in minimizing environmental impacts.
Over the past decades, Fiber-reinforced polymer (FRP) composite materials have evolved into economically competitive and structurally practical building materials (Bank, 2006). FRPs are gradually being employed in a broad range of structures, particularly in harsh environments such as the marine environment or in the chemical industry, where metallic profiles require costly maintenance regularly (Hollaway, 2010; Vallée et al., 2013). FRPs are easily manufactured and can be customized to meet performance criteria (Lee and Jain, 2009). They managed to draw a lot of attention in the civil engineering community due to their favorable characteristics, such as their reduced weight in comparison to conventional steel, high tensile strength, anticorrosion characteristics, and high specific stiffness (Teng et al., 2003; Lee and Jain, 2009; Brigante, 2014; Mugahed Amran et al., 2018). FRP composites are mainly formed using glass, aramid, carbon, or basalt fibers embedded in a matrix of polyester, vinyl ester, or epoxy resins (Sbahieh et al., 2022a; 2022b). The fibers generally provide strength and high stiffness, while the role of the resin is to hold the fibers together, transfer forces between fibers, and preserve them (Qureshi, 2022). The application of FRP composites in civil engineering extends from rehabilitating existing structures, which involves strengthening, retrofitting, and repairing the structures, to adapting FRP composites as reinforcement in new projects, either entirely or partially, similar to concrete-FRP structure (Einde et al., 2003; Zaman et al., 2013). FRP composite materials are utilized for both internal reinforcement (bars, tendons, and rods) as well as external reinforcement (sheets, wraps, and laminates) (Gudonis et al., 2014; Sbahieh et al., 2022a). Glass fiber-reinforced polymer (GFPP), basalt fiber-reinforced polymer (BFRP), carbon fiber-reinforced polymer (CFRP), and aramid fiber reinforced polymer (AFRP) are the four most common forms of FRP reinforcement (Sbahieh et al., 2022a; Xian et al., 2022). FRPs typically exhibit linear-elastic tensile stress-strain behavior until failure, known as brittle behavior, which occurs suddenly and without sufficient notice (Harris et al., 1998). GFRP and CFRP are currently the most frequently used reinforcing fiber for polymeric matrix composites (Mugahed Amran et al., 2018; Qureshi, 2022). The key benefits of CFRP over other forms of FRPs are its high tensile strength and elastic modulus, which decrease deformations in CFRP-reinforced parts (Gudonis et al., 2014; Maxineasa and Taranu, 2018). The main benefits of GFRP are its high strength, water resistance, chemical resistance, and low cost. Yet, the fundamental disadvantages of GFRP are its low elastic modulus, limited resistance to alkaline conditions, low fatigue resistance, and low long-term strength due to stress rupture (Gudonis et al., 2014; Maxineasa and Taranu, 2018; Li et al., 2021). CFRP possesses a high elastic modulus, is lightweight, has low conductivity, excellent creep resistance, high fatigue strength, and does not absorb water. Nevertheless, one of the main drawbacks is the remarkably high energy need for manufacturing carbon fibers, which results in expensive costs. They also have anisotropic properties, poor compressive strength, and risk for galvanic corrosion when directly contacting steel (Gudonis et al., 2014; Mugahed Amran et al., 2018; Abbood et al., 2021; Guo et al., 2023).
Steel is frequently utilized as reinforcement in concrete beams to enhance their ductile behavior and give warning before failure. By adding steel reinforcing bars to the concrete beam, the structure gains the ability to deform and absorb energy before failing. This ductile behavior is desirable because it enables the structure to bend and flex without experiencing sudden or catastrophic failure (El-Mogy et al., 2010). On the other hand, the low elongation at break of the FFP bar is a significant concern when it comes to its application in concrete structures. The brittle behavior of FRP materials up to failure may result in inadequate seismic performance and raises questions regarding their ability to distribute loads and moments in beams (El-Mogy et al., 2010). GFRP-reinforced concrete columns expressed linear elastic behavior under seismic loads and had smaller residual displacements than steel-bar reinforced columns (Tavassoli et al., 2015). These findings indicate that FRP RC constructions have a low capacity for energy dissipation during earthquakes. As a result, a new type of hybrid reinforcement bar, Steel-FRP composite bars (SFRP), are recommended, which is made of inner ribbed steel bar with FRP skin over the steel core in order to take advantage of the enhanced durability of FRP while avoiding the linear elastic behavior of FRP bars (Wu et al., 2012; Dong et al., 2016).
Concrete constructions tend to be at risk of deterioration due to steel corrosion (Sbahieh et al., 2022a). One viable alternative is substituting the steel bars with a different type of bars with higher strength compared to steel, like FRP bars (Li et al., 2015). However, It is crucial to remember that FRP bars have a lower elastic modulus compared to steel bars. This indicates that, although FRP bars have a long elastic deformation prior to rupture, their rupture is brittle, which might lead to severe damage to structures (Liu et al., 2019). On the other hand, steel has a plastic nature with high fracture strain, yet its elastic deformation stage usually is not long, and the yield strength is not always high enough (Hearn, 1997). The solution to this problem is to combine the benefits of steel and FRP bars together. The hybrid FRP-steel composite bar system is an effective option for reducing corrosion risk, increasing load-carrying capacity, and resisting sudden catastrophic failure (Mazaheripour et al., 2016; Liu et al., 2019; Rimkus et al., 2019). In the hybrid bar, the steel contributes to ductility and strength, while GFRP provides corrosion resistance and stiffness. The steel-FRP composite bars were tested for reinforcing concrete columns by (Sun et al., 2011) and it was found that Steel-FRP bars have better anti-seismic properties compared to steel-reinforced columns. Steel-GFRP composite bars (SGFRP) display bi-linear curves, along with elastic deformation occurring prior to the steel component yield at the first inflection point. The GFRP remains elastic after this point, while steel experiences plastic deformation. The SGFRP exhibits elastoplastic deformation, and the peak load results from the GFRP component’s rupture. Once the peak load is reached, the GFRP component can no longer bear the load, and the force is carried solely by the steel component. The final plateau is equal to the yield strength of the steel component when steel undergoes plastic flow, and the GFRP component becomes entirely load carrying-free when the steel component reaches its fracture strain (Liu et al., 2019).
Sustainable building materials are essential factors in building’s environmental performance, influencing the structures at different phases throughout their life cycle. As a result, the evaluation and selection of sustainable construction materials such as FRP have been determined depending on the life cycle assessment (LCA) method (Ding, 2013). The life cycle assessment (LCA) is one of the approaches created to measure and understand the environmental effect of a good or service. It examines the environmental effects across the product’s whole life cycle, from the procurement of raw materials (cradle) to manufacture, usage, recycling, and disposal (grave) (Tahir et al., 2022). Few research studies have looked into the environmental impacts of adopting FRP in concrete structures. LCA was conducted comparing BFRP reinforced concrete (RC) beam to steel RC beam (Inman et al., 2017). The findings demonstrate that the BFRP RC beam outperforms the steel RC beam throughout all eighteen environmental impact categories. In another study, it was found through LCA that GFRP/CFRP reinforced seawater sea sand beams had significantly lower environmental impacts than steel-reinforced beams (Dong et al., 2021). The environmental effect of employing BFRP bars in place of steel bars in RC beams was investigated using a life cycle assessment (LCA) (Pavlović et al., 2022). It was reported that BFRP beams outperformed steel beams in 18 midpoint categories. Moreover, the environmental effects of producing basalt fibers were compared to those of ordinary steel fibers using life cycle assessment (Fořt et al., 2021). The results show that, mainly for compressive and flexural strength, basalt reinforcement presents a much reduced environmental intensity per strength unit. Furthermore, it was stated that BFRP, CFRP, and GFRP-reinforced beams used less energy and produced fewer CO2 emissions than steel-reinforced beams (Garg and Shrivastava, 2019).
The supply of freshwater worldwide might be seriously impacted by the increasing growth of the global population as well as the effects of climate change (Nishida et al., 2015). The World Meteorological Organization (WMO) predicts that by 2050, more than five billion people won’t have access to enough clean drinking water (World Meteorological Organization, 2021). Concrete preparation requires 16.6*109m3 of freshwater per year, equivalent to the annual domestic consumption of 145 million Americans in the United States and approximately 18% of global yearly industrial water demand (Miller et al., 2018). Therefore, using a seawater concrete mixture is expected to be most favorable in areas facing water scarcity, like the Arabian peninsula, central Asia, and North Africa (Ebead et al., 2022). Seawater concrete mixture is prepared by substituting the freshwater used to mix the concrete with seawater. The strength and durability of the concrete subjected to seawater might be weakened by the presence of salts in various ratios. Some reports suggest that the average concentration of soluble salts in seawater is 3.5% (Islam et al., 2010). In addition, salts have three different effects on concrete: mechanical (loss of strength), chemical (corrosion of the cement matrix and degradation of the steel reinforcement), and physical (tides and sea waves) (Mangi et al., 2021). The compressive strength increased at early ages (14 days) for samples prepared and cured with seawater, whereas a decrement was observed at ages between 28 and 90 days with a reduction ranging between 3.8% and 14.5% in comparison to the freshwater mixtures (Wegian, 2010), While in another study, (Otsuki et al., 2011), reported that seawater concrete’s long-term compressive strength was a bit higher than that of regular concrete. Concrete tensile strength improved by 10%–20% when cured with seawater (Abdel-Magid et al., 2016). There was no notable change in the flexural strength of concrete beams prepared and cured using seawater in comparison to beams prepared and cured utilizing freshwater (Mangi et al., 2021). However, the reported percentages do not exceed the natural scatter in the mechanical performance of the concrete because of its heterogeneous structure (Jakubovskis et al., 2018).
The durability of FRP-reinforced concrete structures can be compromised by exposure to alkaline or humid and hot environments. Therefore it is crucial to understand the mechanism of degradation in FRP bars to ensure that the design and technical guidance of the FRP bars are optimized for long-term performance and reliability in real-world conditions. (Feng et al., 2022). The major cause of FRP bar durability failure is the degradation of fiber, resin, and the fiber-resin interface (Zhang et al., 2022). When FRP bars come into contact with water or an alkaline environment, the resin initially degrades as a result of plasticizing and hydrolysis (Zhou and Lucas, 1999). The resin degradation leads to a reduction in the load transfer capability of FRP bars, which lowers their tensile strength (Li et al., 2021). The loss of the FRP bar’s resin protection exposes the fiber-resin interface to water and OH−, accompanied by the resin’s macromolecular chains, which quickly deteriorate the fibers (Feng et al., 2022). Fibers deteriorate significantly as a result of OH− etching (for glass and basalt fibers) and Cl− corrosion (only for basalt fibers) (Wang et al., 2017). The fiber-resin interface loses its mechanical biting force and chemical bonding force (Li et al., 2022), eventually leading to the failure of the fiber and resin, deteriorating the FRP bars. Consequently, resin hydrolysis is the predominant cause of FRP bar degradation, followed by debonding of the fiber-resin interface and fiber damage, which ultimately leads to FRP bar failure (Fergani et al., 2018).
The aim of this study is to assess and evaluate the environmental impacts through life cycle assessment (LCA) of anticorrosive materials like glass fiber-reinforced polymer (GFRP) bars, carbon fiber-reinforced polymer (CFRP) bars, and steel-glass fiber-reinforced polymer (SGFRP) bars compared to steel bars. Additionally, another life cycle assessment is conducted for steel-reinforced beams and compared to GFRP/CFRP reinforced beams. In order to reduce the environmental impacts of the reinforced concrete beams and to reduce the use of freshwater in Qatar, seawater was used instead of freshwater from the desalination plant in the concrete mixture after CFRP/GFRP bars were used in the RC beams.
The innovation of this work lies in the comprehensive evaluation of the environmental impacts of several types of reinforcement, such as steel, GFRP, SGFRP, and CFRP, using life cycle assessment. The study also includes the comparison of the environmental impacts of RC beams reinforced with these materials, providing valuable insights for decision-makers and engineers to select suitable materials for sustainable construction. The use of seawater in place of freshwater in the concrete mixture after the incorporation of GFRP/CFRP bars is also an innovative approach toward minimizing the environmental impacts of RC beams and freshwater usage. This study contributes to the development of sustainable construction practices and offers a framework for future studies on assessing environmental impacts in structures.
Three beams are designed in this section; the first is a concrete beam designed according to ACI 318R-14 (ACI 318-14, 2014), casted using desalinated freshwater and reinforced with steel bars and stirrups; the second is a concrete beam made using seawater and reinforced with GFRP bars and stirrups, while the third is a concrete beam casted using seawater and reinforced with CFRP bars and stirrups. The second and third beams were designed according to ACI 440.1R-15 (ACI 440 1R-15, 2015), ACI 440.6M-08 (ACI 440.6M-08, 2008), and ACI 440.5–08 (American Concrete Institute, 2008). The three beams were designed in this study to evaluate their environmental impacts when different types of reinforcement are used. These beams present a real-world example of structural design. They are made up of a single span with a pinned support and roller support at each end. The three beams have a rectangular cross-section of 500*300 mm and a 5 m length, as shown in Figure 1. The three beams are designed to carry the same load with different internal reinforcements due to the different properties of steel, GFRP, and CFRP bars. The dead load and live load were calculated by assuming that the beam is carrying half of the weight of a 4*5 m slab, in addition to the weight of a 3 m height and 25 cm thickness wall surrounding the slab. The dead load and the live load were calculated and decided to be 18 kn/m and 3 kn/m. The beams are mainly comprised of cement, sand, gravel, desalinated freshwater/seawater, and steel/CFRP/GFRP reinforcement. The used sand is produced by crushing granite and has a bulk density of 1550 kg/m3. Gravels make up the majority of coarse aggregate found in concrete, with a bulk density of 1350 kg/m3. Desalinated fresh water from the Ras Abofantas plant in Qatar was used in the steel-reinforced beam, while seawater was used in the GFRP/CFRP beam. The density of the seawater and the desalinated freshwater are 1030 kg/m3 and 1000 kg/m3, respectively. Ordinary Portland cement (OPC) was utilized for casting the three beams, and it has a bulk density of 1440 kg/m3. Standard hot-rolled steel reinforcement bars with a density of 7850 kg/m3 were used as a reinforcement for steel-reinforced beams. GFRP and CFRP reinforcement bars were adopted as an alternative reinforcement in the GFRP/CFRP-reinforced beams. The density of the GFRP bars, CFRP reinforecement bars, and epoxy resin are 1900 kg/m3, 1700 kg/m3, and 1200 kg/m3, respectively. The water-cement ratio was set as 0.45. In order to build the three beams, a specific amount of materials are needed, and they are 416 kg cement, 448 kg sand, 780 kg coarse aggregate, and 187 lite of either seawater or desalinated water. The amount of reinforcement and the dimensions of the beams are presented in Figure 1. The FRP beams were designed using (ACI 440 1R-15, 2015). The beams were checked for crack width, longe term deflection, creep rupture stress, and for shear. The details related to the properties of the used reinforcement bar are presented in Table 1, and the details of the GFRP/CFRP-designed beams are shown in Table 2.
Life cycle assessment is performed to evaluate the environmental impacts of the Carbon/glass fiber-reinforced polymer. A framework to carry out the life-cycle assessment is developed. The assessment will follow the LCA framework established by the International Organization for Standardization, ISO 14040 (ISO 14040, 2006). The LCA of the developed RC beams addresses all the environmental aspects throughout the member’s life cycle, starting from the raw material extraction until the product is ready at the factory or the site. The LCA was carried out using Gabi LCA software to build a system model and evaluate the two scenarios' environmental impacts.
The goal of this study is to assess and evaluate the environmental impacts of CFRP/GFRP/SGFRP compared to steel; therefore, in this research, the following Life cycle assessments were evaluated.
• Cradle-to-gate life cycle assessment to assess the environmental impacts of CFRP/GFRP/SGFRP reinforcing bars compared to steel bars. The functional unit for this LCA was a 1 m long bar with a diameter of 12 mm.
The Steel-FRP composite bar (SGFRP) is made of an inner ribbed steel bar with GFRP skin over the steel core. Figure 2 shows the cross-section of the four studied bars.
• Cradle-to-gate life cycle assessment to study the environmental impacts of CFRP/GFRP reinforced beam made with seawater compared to steel reinforced beam made with desalinated freshwater in Qatar. The functional unit is a 5*0.5*0.3 m beam that can carry the same load with different reinforcement (CFRP/GFRP/steel).
The boundaries of the two systems, including manufacturing steel/CFRP/GFRP/SGFRP bars and all the other components of beams, are presented in Figure 3. The boundaries contain raw materials extraction and manufacturing (epoxy, carbon fiber, glass fiber, sand, gravel, seawater/desalinated water, cement, and CFRP/GFRP/steel bars) for the RC beams and the process of making GFRP/CFRP bars. Both FRP and steel bars are assumed to be imported from the same country, therefore, transporting the bars and the manufactured materials to the factory or the construction site was not included in the boundaries for the comparative LCA.
All inputs taken into account during the evaluation per functional unit are included in the life cycle inventory. The environmental impacts of sand, cement, gravel, steel bar, and seawater were found in the Gabi database. The chosen steel bar production process was based on the blast furnace-basic oxygen furnace (BF-BOF) process due to the fact that the BF-BOF path accounts for over 66% of total crude steel production. In comparison, the EAF path is responsible for around 31%, leaving the BF-open hearth method, which led the steel production industry at the beginning of the twentieth century, with just around 3% (Yang et al., 2014).
Regarding the production of desalinated freshwater in Qatar, a model on Gabi software developed by (Mannan et al., 2019) for producing freshwater from the Ras Abu Fontas plant in Qatar was used to calculate the environmental impact of the desalinated freshwater. However, the production process of CFRP and GFRP bars does not exist in the Gabi database; therefore, a new process was created to perform a full LCA. CFRP and GFRP bars are mainly composed of resin and (glass/carbon) fibers, where fiber content should not be less than 55% (ACI Committee 440, 2000). This parameter differs across manufacturers, so a ratio of 80% fibers and 20% resin was adopted in this study. Epoxy resin is the most used resin for FRP materials (Fiore and Valenza, 2013); thus, it was selected as the matrix for the FRP bars. The process of manufacturing epoxy resin, glass fibers, and carbon fibers can be found in the Gabi database. Germany is the country of origin for epoxy, glass fibers, and carbon fibers. Surface treatments, including sand coating, are estimated to have an energy intensity of 0.3 MJ/kg. The GFRP/CFRP bars were manufactured using the pultrusion process, which has an energy intensity of 3.1 MJ/kg (Suzuki and Takahashi, 2005).
Recipe methodology is the impact assessment method used for this study’s life cycle impact assessment (LCIA). The recipe was founded in 2008 as a result of a collaboration between RIVM, Radboud University Nijmegen, Leiden University, and PRé Sustainability. The major goal of the ReCiPe method is to simplify a large number of life cycle inventory findings to a small number of indicator scores. The relative severity of an environmental impact category is represented by the indicator scores (Huijbregts et al., 2017). The selected environmental impact categories are Climate change (CC), ozone depletion (OD), ionizing radiation (IR), fine particulate matter formation (PMF), Terrestrial acidification (TA), Freshwater eutrophication (FEP), Freshwater ecotoxicity (FET), Human toxicity (HT), Water depletion (WD), Fossil depletion (FD), Metal depletion (MD), Terrestrial ecotoxicity (TE), Marine ecotoxicity (MEC), Marine eutrophication (MEU) and Photochemical oxidant formation (POF). The ReCiPe approach was created after a thorough examination of scientific literature and feedback from stakeholders. The environmental impact categories were chosen due to their relevance to human health, ecosystem quality, and resource availability (Goedkoop et al., 2009). Each category was selected due to a certain impact. Climate change (CC) was included due to the considerable influence of greenhouse gas emissions on global temperatures and the impacts on ecosystems and human health. Ionizing radiation (IR) has the potential to affect human health and the environment. Fine particulate matter formation (PMF) was selected due to the impact of airborne particulate matter on human health and ecosystems. Terrestrial acidification (TA) and freshwater eutrophication (FEP) can potentially influence terrestrial and aquatic ecosystems. Freshwater ecotoxicity (FET) and terrestrial ecotoxicity (TE) have the potential to harm organisms in freshwater and terrestrial ecosystems, respectively. Marine ecotoxicity (MEC) and marine eutrophication (MEU) can possibly harm marine ecosystems. Human toxicity (HT) was selected because of the possible influence of chemicals and pollutants on human health. Water depletion (WD), fossil depletion (FD), and metal depletion (MD) have impact on the availability of resources therefore impacting future generations. Photochemical oxidant formation (POF) was selected because of ground-level ozone’s negative effects on human health and ecosystems (Goedkoop et al., 2009).
This section is divided into two main parts; the first part is the life cycle assessment of GFRP/CFRP/SGFRP bars compared to steel bars, and the second is LCA for CFRP/GFRP reinforced beams compared to steel-reinforced beams.
The results for comparing the environmental impacts of steel bars with glass, steel-glass and carbon FRP bars (1 m long with a 12 mm diameter) are demonstrated in Table 3. The cradle-to-gate life cycle assessment results show that the GFRP bar had the most significant reduction in environmental impact compared to steel and CFRP bars. GFRP bars performed better than the steel bar in ten out of 14 categories, while the CFRP bar had the worse environmental impact in 10 out of 14 categories compared to steel bars. GFRP bar has environmental advantages over steel bars in categories like CC, FD, HT, and WD, with a reduction of 65.6, 54.65, 10.24, and 94.9%, respectively. The CFRP bar had the worst environmental impact score compared to the other reinforcing bars, as shown in Figure 4. In the process of manufacturing CFRP bars, Carbon fibers have the dominant effect compared to epoxy resin production, pultrusion process, and sand coating in all 14 environmental impact categories, where they were responsible for approximately 62%–94% of the impact across the studied categories. Glass fibers had the ruling environmental impact in comparison with epoxy resin in 8 of 14 categories throughout GFRP bar production process, accounting for about 16.8%–90.2% of the total environmental impacts in the selected categories. SGFP bars generally have lower environmental impacts than steel and CFRP bars; however, SGFRP bars have higher environmental impact values when compared to GFRP bars. SGFRP bars can be seen as a compromise between the GFRP and steel, where SGFRP bars have higher tensile strength than steel and have a better ductile behavior compared to the brittle behavior of GFRP.
Although CFRP reinforcement bar has less favorable environmental indicators than steel, SGFRP and GFRP bars, such characteristics do not necessarily exclude their application in concrete structures. The usage of CFRP bars depends on each specific application and the acceptable trade-offs when designing. Furthermore, the high cost of carbon fiber must be addressed while deciding whether to employ CFRP reinforcement bars in concrete structures.
CFRP bars are commonly utilized in projects where weight reduction and durability are important considerations, such as bridge decks and marine structures. The lightweight nature of CFRP bars can minimize energy and transportation expenses during construction, resulting in a reduced carbon footprint overall. Moreover, CFRP bar’s superior strength and corrosion resistance can lead to longer service life and lower maintenance costs. SGFRP bars offer several advantages over other types of reinforcement bars, including high tensile strength, corrosion resistance, and ductile behavior. Additionally, the lower cost of SGFRP compared to CFRP bars makes SGFRP bars an attractive option, making them a cost-effective option for various applications. In conclusion, designers should be able to make informed decisions on the most appropriate type of reinforcement to employ in their projects by examining the benefits and drawbacks of each bar.
This section evaluates the environmental impact of the different components used in GFRP-reinforced beams, CFRP-reinforced beams, and steel-reinforced beams like cement, steel, CFRP, GFRP, sand, gravel, seawater, and desalinated water. Additionally, a comparison was made at the end to assess the different total environmental impacts of the previously mentioned beams.
The environmental performance of a steel-reinforced beam prepared with desalinated fresh water was evaluated in this part without considering transportation for the materials. The environmental impact resulting values of each component of the steel-reinforced beam are presented in Table 4. Cement and steel are the main components affecting the natural environment and having the worst environmental impacts. The steel-reinforced beam’s climate change and human toxicity environmental categories are heavily impacted by the amount of cement utilized in the beam, followed by the negative impact of using the steel bar, as seen in Figure 5. Fossil depletion, water depletion, and metal depletion environmental impact categories are mainly impacted by the effect of steel bar, followed by cement. Cement was responsible for 68.5% of the total impact in the climate change category, while steel, sand, desalinated water, and gravel are responsible for 29.7%, 0.24%, 1%, and 0.6% of the total impact.
In this section, the environmental performance of a seawater-prepared GFRP-reinforced beam was assessed without considering material transportation. Table 5 displays the results for each environmental impact category of the GFRP-reinforced beam components. The primary elements impacting the environment and those with the worst effects on the environment are cement and then followed by GFRP bars. The amount of cement used in the beam significantly influences the GFRP-reinforced beam’s environmental impact categories like climate change, human toxicity, fossil depletion, and water depletion, as shown in Figure 6. In the category of climate change, cement accounted for 88.8% of the overall impact, while GFRP, sand, seawater, and gravel were each responsible for 10.18%, 0.31%, 0.003%, and 0.31% of the total impact, respectively. Cement had the dominant impact in 10 of 14 environmental categories, accounting for 51.8%–92% of the total environmental effects. This scenario proves that using GFRP bars as an internal reinforcement instead of steel bars could reduce the total environmental impact of the reinforced concrete beam. Utilizing GFRP bars instead of steel bars allow the use of seawater instead of desalinated freshwater in the reinforced beams, which reduces the carbon footprint resulting from using water in the concrete mixture by 94.7%.
This section evaluates the environmental performance of a CFRP-reinforced seawater-prepared beam without taking material transportation into account. The outcomes for each category of environmental impact for the CFRP-reinforced beam components are shown in Table 6. Cement and CFRP bars are the two main environmental pollutants, and they also have the worst effects on the environment compared to the other materials used to form the CFRP-reinforced beam. Figure 7 illustrates how the GFRP-reinforced beam’s environmental impact categories, such as climate change, human toxicity, fossil depletion, and water depletion, are greatly influenced by the amount of cement utilized in the CFRP-reinforced beam. Cement made up 71.3% of the entire climate change impact, whereas CFRP, sand, and gravel each contributed 27.6%, 0.25%, and 0.63% of the overall impact, respectively. This case study demonstrates how replacing steel bars with CFRP bars as internal reinforcement might lessen the reinforced concrete beam’s overall environmental effect. CFRP reinforecement bar has a significant negative influence on environmental impact categories related to marine ecotoxicity, water depletion, and fossil depletion, accounting for 65.5%, 86.2%, and 58% of each category’s total impacts, respectively. The influence of cement dominates in 8 categories, and it accounts for 68.8%–80.2% of the total environmental impacts. The use of seawater rather than desalinated freshwater in the reinforced beams is made possible by adopting CFRP bars rather than steel bars, which lowers the carbon footprint associated with using water in the concrete mix by 86.45%.
GFRP/CFRP reinforced beams built with seawater are compared to steel reinforced beams made with desalinated fresh water in this section to assess their respective environmental impacts. The designed beams can carry the same load and have the same dimensions, but they are reinforced differently since GFRP and CFRP have different tensile strengths from steel. Figure 8 compares the environmental impacts of seawater CFRP/GFRP reinforced beams to desalinated freshwater steel-reinforced beams. GFRP-reinforced beam outperformed steel-reinforced beam in 9 out of 14 environmental impact categories, while CFRP-reinforced beam performed better in 8 out of 14 environmental categories compared to the steel-reinforced beam. GFRP-reinforced beams performed better than steel-reinforced beams in categories like climate change, fossil depletion, water depletion, human toxicity, and meatal depletion, with a reduction rate of 22.78%, 36.77%, 94.7%, 6.25%, and 97% respectively. CFRP-reinforced beams outperformed steel-reinforced beams in categories like climate change, human toxicity, water depletion, metal depletion, and terrestrial acidification with a decrease rate of 3.8%, 4.9%, 86.4%, 96.5%, and 30.6%, respectively. Using seawater instead of desalinated freshwater in RC beams did not have a significant environmental impact due to the dominant effect of other materials like cement, steel GFRP, and CFRP. However, utilizing seawater instead of desalinated freshwater reduced the CO2 emissions associated with desalinated water production from 3.98 kgCO2eq to 0.0104 kgCO2eq achieving a reduction rate of 99.7%. Figure 8 presents a comparison between the environmental impacts of steel, GFRP, and CFRP-reinforced beams in 14 categories.
Overall, GFRP and CFRP bars have less environmental impacts than steel bars in most categories, with the exception of a few. However, it's crucial to remember that their environmental impacts could still be significant in specific categories. Thus, the material selection should be based on a comprehensive analysis of the product’s full lifespan, taking into account aspects like cost, performance, and durability in addition to environmental effects.
This paper aims to evaluate the environmental impact through life cycle assessment for CFRP, GFRP, and steel bars; additionally, it assesses their environmental performance when used in reinforced beams experiencing the same load with different reinforcement. Based on the findings and analyses, the following conclusions can be made.
• GFRP reinforcement bars have the lowest environmental impacts compared to steel, SGFRP and CFRP bars, while CFRP bars scored the highest score for environmental influence across 9 out of 14 environmental impact categories. This information could be used to make informed decisions when selecting reinforcement materials for construction projects, taking into consideration both the structural and environmental aspects.
• The climate change environmental impact category, measured as kg CO2eq of the GFRP bars, is 82% lower than that of CFRP, 46% less than SGFRP, and 65.6% lower than the steel bars making GFRP bars the best alternative to reduce the greenhouse gases (GHG) effects. Therefore, GFRP bars are the best alternative for reducing the effects of greenhouse gases compared to other types of reinforcements.
• Carbon fibers have the major influence in the process of producing CFRP bars when compared to epoxy resin in all 14 environmental impact categories, accounting for about 64%–94% of the total impact across the evaluated categories. Furthermore, Glass fibers outscored epoxy resin in 8 of 14 categories throughout the GFRP bar manufacturing phase, accounting for about 17%–90% of the overall environmental impacts in the studied categories. This suggests that alternative materials or production processes that reduce the use of carbon fibers in CFRP bars and glass fibers in GFRP bars could help lessen these reinforcement bars' environmental impact.
• Even though GFRP, SGFRP and steel bars show better environmental performance than CFRP bars in various impact categories, this does not necessarily mean that CFRP bars should be completely excluded from use in concrete structures. The selection of the reinforcement bar material depends on the specific application and design trade-offs that can be made. Therefore, the suitability of CFRP bars should be evaluated on a case-by-case basis, considering the construction project’s specific needs.
• SGFRP bars offer a balance between the environmental impacts of GFRP and steel bars, as they have lower impacts than steel and CFRP bars but higher impacts than GFRP bars. However, SGFRP bars have advantages in terms of their higher tensile strength compared to steel and better ductile behavior compared to GFRP. Therefore, the choice of reinforcement material depends on the designer and the needed properties for the project.
• Cement and steel are the primary environmental pollutants and those with the worst environmental effects caused by the steel-reinforced concrete structural members. Cement accounts for 68.5% of the climate change category of the overall environmental impact of the steel-reinforced beam, while steel accounts for 29.7%. These findings highlight the need for sustainable alternatives to cement and steel in the construction industry to minimize the environmental impact of building structures.
• The proposed study demonstrates that adopting GFRP, SGFRP or CFRP bars as internal reinforcement rather than steel bars is a potential solution for the natural environment. As a result, FRP materials may play an essential part in the construction sector’s attempts to reduce its environmental footprint and hence in the worldwide sustainable act.
• The study suggests that using seawater instead of desalinated freshwater in reinforced concrete beams did not significantly impact the environment. This is because other materials, such as cement, steel, GFRP, and CFRP, dominate the overall environmental impact. However, the study shows that the use of seawater instead of desalinated freshwater can significantly reduce CO2 emissions related to freshwater production, with a reduction rate of 99.7%.
• While CFRP bars have the worst environmental impacts compared to steel, SGFRP, and GFRP bars, they can still be suitable for reinforcement in concrete beams. This is because CFRP-reinforced beams perform better than steel-reinforced beams due to the CFRP bars' lightweight and high tensile strength. However, the selection of reinforcement bars depends on individual applications and allowable design trade-offs, including the consideration of environmental impacts.
• GFRP and CFRP bars have lower environmental impacts compared to steel bars when used as reinforcement in concrete beams. GFRP bars provide a greater reduction in categories like terrestrial acidification, fossil depletion, and water depletion, while CFRP bars have a better performance in reducing the impact of categories like human toxicity and metal depletion. Therefore, the choice of reinforcement material depends on the specific application and the desired environmental outcomes.
• This study utilized the same amount of concrete for the GFRP, CFRP, and steel-reinforced concrete beam scenarios. Since GFRP and CFRP have better tensile strength than conventional steel reinforcement, it is believed that thinner concrete members could be implemented in the GFRP and CFRP scenario. Researchers and manufacturers of FRP materials must develop answers to the challenging issue of recycling composite materials since recycling FRP is crucial for the future in addition to being good for the environment. Cradle-to-grave life cycle assessment studies are required to gain more definitive findings concerning the environmental implications of FRP composites.
• The development of acceptable design and construction guidelines for reinforced concrete beams made of FRP will promote the adoption of these materials in the construction industry. Engineers and builders will have more confidence in adopting FRP in place of conventional materials like steel if clear and accurate guidelines are provided, leading to higher utilization of FRP in construction while possibly lowering the industry’s environmental impact.
• Further technological advancements and mass manufacturing of GFRP and CFRP reinforcement bars are predicted to significantly minimize the environmental effect of the production process, making them the most environmentally friendly substitutes for steel reinforecement bars in concrete beams.
The original contributions presented in the study are included in the article/supplementary material, further inquiries can be directed to the corresponding authors.
Conceptualization, SS and SA-G; methodology, SS and SA-G; software, SS and SA-G; validation, SS, GM, and SA-G; formal analysis, SS and SA-G; investigation, SS and SA-G; resources, SS and SA-G; data curation, SS and SA-G; writing—original draft preparation, SS and SA-G; writing—review and editing, SS, GM, and SA-G; visualization, SS and SA-G; supervision, GM and SA-G; project administration, SA-G; funding acquisition, SA-G. All authors listed have made a substantial, direct, and intellectual contribution to the work and approved it for publication.
This work was made possible through the National Priorities Research Program (NPRP), Qatar grant (NPRP13S-0209-200311) from the Qatar National Research Fund (QNRF), a member of the Qatar Foundation (QF), as well as through extra funding and a scholarship from Hamad Bin Khalifa University (HBKU). Any opinions, findings, conclusions or recommendations expressed in this material are those of the authors and do not necessarily reflect the views of HBKU, QNRF or QF.
The authors declare that the research was conducted in the absence of any commercial or financial relationships that could be construed as a potential conflict of interest.
All claims expressed in this article are solely those of the authors and do not necessarily represent those of their affiliated organizations, or those of the publisher, the editors and the reviewers. Any product that may be evaluated in this article, or claim that may be made by its manufacturer, is not guaranteed or endorsed by the publisher.
Abbood, I. S., Odaa, S. A., Hasan, K. F., and Jasim, M. A. (2021). “Properties evaluation of fiber reinforced polymers and their constituent materials used in structures - a review,” in Materials today: Proceedings (Elsevier Ltd), 1003–1008. doi:10.1016/j.matpr.2020.07.636
Abdel-Magid, T. I., Osman, O. M., Ibrahim, O. H., Mohammed, R. T., Hassan, S. O., and Bakkab, A. A. H. (2016). Influence of seawater in strengths of concrete mix design when used in mixing and curing. KEM 711, 382–389. doi:10.4028/www.scientific.net/kem.711.382
ACI 318-14 (2014). Building code requirements for structural concrete (ACI 318-14). American Concrete Institute.
ACI 440 1R-15 (2015). Guide for the design and construction of structural concrete reinforced with fiber-reinforced polymer (FRP) bars 1st printing. Farmington Hills, MI: American Concrete Institute.
ACI 440.6M-08 (2008). Specification for construction with fiber-reinforced polymer reinforcing bars: An ACI standard. Farmington Hills: American Concrete Institute.
ACI Committee 440 (2000). Specification for carbon and glass fiber-reinforced polymer bar materials for concrete reinforcement. ACI Committee.
American Concrete Institute (2008). Specification for carbon and glass fiber reinforced polymer bar materials for concrete reinforcement. Farmington Hills, MI: American Concrete Institute. Available at: www.concrete.org.
Bank, L. C. (2006). Composites for construction: Structural design with FRP materials. United States of America: John Wiley and Sons.
Brigante, D. (2014). New composite materials. Napoli , Italy: Springer International Publishing Switzerland. doi:10.1007/978-3-319-01637-5
Ding, G. K. C. (2013). “Life cycle assessment (LCA) of sustainable building materials: An overview,” in Eco-efficient construction and building materials: Life cycle assessment (LCA), eco-labelling and case studies (Elsevier Inc.), 38–62. doi:10.1533/9780857097729.1.38
Dong, Z., Wu, G., and Xu, Y. (2016). Experimental study on the bond durability between steel-FRP composite bars (SFCBs) and sea sand concrete in ocean environment. Constr. Build. Mater. 115, 277–284. doi:10.1016/j.conbuildmat.2016.04.052
Dong, S., Li, C., and Xian, G. (2021). Environmental impacts of glass- and carbon-fiber-reinforced polymer bar-reinforced seawater and sea sand concrete beams used in marine environments: An LCA case study. Polymers 13, 154. doi:10.3390/polym13010154
Ebead, U., Lau, D., Lollini, F., Nanni, A., Suraneni, P., and Yu, T. (2022). A review of recent advances in the science and technology of seawater-mixed concrete. Cem. Concr. Res. 152, 106666. doi:10.1016/j.cemconres.2021.106666
Einde, L. V. D., Zhao, L., and Seible, F. (2003). Use of FRP composites in civil structural applications. Constr. Build. Mat. 17, 389–403. doi:10.1016/s0950-0618(03)00040-0
El-Mogy, M., El-Ragaby, A., and El-Salakawy, E. (2010). Flexural behavior of continuous FRP-reinforced concrete beams. J. Compos. Constr. 14, 669–680. doi:10.1061/(ASCE)CC.1943-5614.0000140
Feng, G., Zhu, D., Guo, S., Rahman, M. Z., Jin, Z., and Shi, C. (2022). A review on mechanical properties and deterioration mechanisms of FRP bars under severe environmental and loading conditions. Cem. Concr. Compos. 134, 104758. doi:10.1016/j.cemconcomp.2022.104758
Fergani, H., Di Benedetti, M., Miàs Oller, C., Lynsdale, C., and Guadagnini, M. (2018). Durability and degradation mechanisms of GFRP reinforcement subjected to severe environments and sustained stress. Constr. Build. Mater. 170, 637–648. doi:10.1016/j.conbuildmat.2018.03.092
Fiore, V., and Valenza, A. (2013). “Epoxy resins as a matrix material in advanced fiber-reinforced polymer (FRP) composites,” in Advanced fibre-reinforced polymer (FRP) composites for structural applications (Elsevier), 88–121. doi:10.1533/9780857098641.1.88
Fořt, J., Kočí, J., and Černý, R. (2021). Environmental efficiency aspects of basalt fibers reinforcement in concrete mixtures. Energies 14, 7736. doi:10.3390/en14227736
Garg, N., and Shrivastava, S. (2019). “Environmental and economic comparison of FRP reinforcements and steel reinforcements in concrete beams based on design strength parameter,” in UKIERI concrete congress (Jalandhar (Punjab), India: Dr B R Ambedkar National Institute of Technology).
Goedkoop, M., Heijungs, R., Huijbregts, M., Schryver, A. D., Struijs, J., and van Zelm, R. (2009). A life cycle impact assessment method which comprises harmonised category indicators at the midpoint and the endpoint level.
Gudonis, E., Timinskas, E., Gribniak, V., Kaklauskas, G., Arnautov, A. K., and Tamulėnas, V. (2014). FRP reinforcement for concrete structures: State-of-The-Art review of application and design. Eng. Struct. Technol. 5, 147–158. doi:10.3846/2029882X.2014.889274
Guo, R., Li, C., and Xian, G. (2023). Water absorption and long-term thermal and mechanical properties of carbon/glass hybrid rod for bridge cable. Eng. Struct. 274, 115176. doi:10.1016/j.engstruct.2022.115176
Harris, H. G., Somboonsong, W., and Ko, F. K. (1998). New ductile hybrid FRP reinforcing bar for concrete structures. J. Compos. Constr. 2, 28–37. doi:10.1061/(asce)1090-0268(1998)2:1(28)
Hearn, E. J. (1997). “Simple stress and strain,” in Mechanics of materials (Elsevier), 1, 1–26. doi:10.1016/B978-075063265-2/50002-5
Hollaway, L. C. (2010). A review of the present and future utilisation of FRP composites in the civil infrastructure with reference to their important in-service properties. Constr. Build. Mater. 24, 2419–2445. doi:10.1016/j.conbuildmat.2010.04.062
Huijbregts, M. A. J., Steinmann, Z. J. N., Elshout, P. M. F., Stam, G., Verones, F., Vieira, M. D. M., et al. (2017). ReCiPe 2016 v1.1. RIVM report 2016-0104, 201.
Inman, M., Thorhallsson, E. R., and Azrague, K. (2017). “A mechanical and environmental assessment and comparison of basalt fibre reinforced polymer (BFRP) rebar and steel rebar in concrete beams,” in Energy procedia (Elsevier Ltd), 31–40. doi:10.1016/j.egypro.2017.03.005
Islam, M. S., Islam, M. M., and Mondal, B. C. (2010). Effect of freeze-thaw action on physical and mechanical behavior of marine concrete. J. - Institution Eng. Malays. 71, 53–64.
ISO 14040 (2006). Environmental management — life cycle assessment — principles and framework. Geneva, Switzerland: International Organization for Standardization, 20.
Jakubovskis, R., Kupliauskas, R., Rimkus, A., and Gribniak, V. (2018). Application of FE approach to deformation analysis of RC elements under direct tension. Struct. Eng. Mech. 68, 345–358. doi:10.12989/SEM.2018.68.3.345
Lee, L. S., and Jain, R. (2009). The role of FRP composites in a sustainable world. Clean Technol. Environ. Policy 11, 247–249. doi:10.1007/s10098-009-0253-0
Li, G., Wu, J., and Ge, W. (2015). Effect of loading rate and chemical corrosion on the mechanical properties of large diameter glass/basalt-glass FRP bars. Constr. Build. Mater. 93, 1059–1066. doi:10.1016/j.conbuildmat.2015.05.044
Li, S., Guo, S., Yao, Y., Jin, Z., Shi, C., and Zhu, D. (2021). The effects of aging in seawater and SWSSC and strain rate on the tensile performance of GFRP/BFRP composites: A critical review. Constr. Build. Mater. 282, 122534. doi:10.1016/j.conbuildmat.2021.122534
Li, S., Zhu, D., Guo, S., Xi, H., Rahman, M. Z., Yi, Y., et al. (2022). Static and dynamic tensile behaviors of BFRP bars embedded in seawater sea sand concrete under marine environment. Compos. Part B Eng. 242, 110051. doi:10.1016/j.compositesb.2022.110051
Liu, S., Zhou, Y., Zheng, Q., Zhou, J., Jin, F., and Fan, H. (2019). Blast responses of concrete beams reinforced with steel-GFRP composite bars. Structures 22, 200–212. doi:10.1016/j.istruc.2019.08.010
Mangi, S. A., Makhija, A., Raza, M. S., Khahro, S. H., and Jhatial, A. A. (2021). A comprehensive review on effects of seawater on engineering properties of concrete. Silicon 13, 4519–4526. doi:10.1007/s12633-020-00724-7
Mannan, M., Alhaj, M., Mabrouk, A. N., and Al-Ghamdi, S. G. (2019). Examining the life-cycle environmental impacts of desalination: A case study in the state of Qatar. Desalination 452, 238–246. doi:10.1016/j.desal.2018.11.017
Maxineasa, S. G., and Taranu, N. (2018). “Life cycle analysis of strengthening concrete beams with FRP,” in Eco-efficient repair and rehabilitation of concrete infrastructures (Elsevier), 673–721. doi:10.1016/B978-0-08-102181-1.00024-1
Mazaheripour, H., Barros, J. A. O., Soltanzadeh, F., and Sena-Cruz, J. (2016). Deflection and cracking behavior of SFRSCC beams reinforced with hybrid prestressed GFRP and steel reinforcements. Eng. Struct. 125, 546–565. doi:10.1016/j.engstruct.2016.07.026
Miller, S. A., Horvath, A., and Monteiro, P. J. M. (2018). Impacts of booming concrete production on water resources worldwide. Nat. Sustain 1, 69–76. doi:10.1038/s41893-017-0009-5
Mugahed Amran, Y. H., Alyousef, R., Rashid, R. S. M., Alabduljabbar, H., and Hung, C.-C. (2018). Properties and applications of FRP in strengthening RC structures: A review. Structures 16, 208–238. doi:10.1016/j.istruc.2018.09.008
Nishida, T., Otsuki, N., Ohara, H., Garba-Say, Z. M., and Nagata, T. (2015). Some considerations for applicability of seawater as mixing water in concrete. J. Mat. Civ. Eng. 27, B4014004. doi:10.1061/(ASCE)MT.1943-5533.0001006
Otsuki, N., Furuya, D., Saito, T., and Tadokoro, Y. (2011). Possibility of sea water as mixing water in concrete Singapore, 131–138. Available at: http://cipremier.com/100036021.
Pavlović, A., Donchev, T., Petkova, D., and Staletović, N. (2022). Sustainability of alternative reinforcement for concrete structures: Life cycle assessment of basalt FRP bars. Constr. Build. Mater. 334, 127424. doi:10.1016/j.conbuildmat.2022.127424
Qureshi, J. (2022). A review of fibre reinforced polymer structures. Fibers 10, 27. doi:10.3390/fib10030027
Rimkus, A., Barros, J. A. O., Gribniak, V., and Rezazadeh, M. (2019). Mechanical behavior of concrete prisms reinforced with steel and GFRP bar systems. Compos. Struct. 220, 273–288. doi:10.1016/j.compstruct.2019.03.088
Sbahieh, S., Rabie, M., Ebead, U., and Al-Ghamdi, S. G. (2022a). The mechanical and environmental performance of fiber-reinforced polymers in concrete structures: Opportunities, challenges and future directions. Buildings 12, 1417. doi:10.3390/buildings12091417
Sbahieh, S., Tahir, F., and Al-Ghamdi, S. G. (2022b). Environmental and mechanical performance of different fiber reinforced polymers in beams. Mater. Today Proc. 5, 3548–3552. doi:10.1016/j.matpr.2022.04.398
Sun, Z.-Y., Wu, G., Wu, Z.-S., and Zhang, M. (2011). Seismic behavior of concrete columns reinforced by steel-FRP composite bars. J. Compos. Constr. 15, 696–706. doi:10.1061/(ASCE)CC.1943-5614.0000199
Suzuki, T., and Takahashi, J. (2005). “Prediction of energy intensity of carbon fiber reinforced plastics for mass-produced passenger cars,” in Ninth Japan international SAMPE symposium JISSE-9, 14–19.
Tahir, F., Sbahieh, S., and Al-Ghamdi, S. G. (2022). Environmental impacts of using recycled plastics in concrete. Mater. Today Proc. 62, 4013–4017. doi:10.1016/j.matpr.2022.04.593
Tavassoli, A., Liu, J., and Sheikh, S. (2015). Glass fiber-reinforced polymer-reinforced circular columns under simulated seismic loads. ACI Struct. J. 112. doi:10.14359/51687227
Teng, J. G., Chen, J. F., Smith, S. T., and Lam, L. (2003). Behaviour and strength of FRP-strengthened RC structures: A state-of-the-art review. Proc. Institution Civ. Eng. - Struct. Build. 156, 51–62. doi:10.1680/stbu.2003.156.1.51
Vallée, T., Tannert, T., Meena, R., and Hehl, S. (2013). Dimensioning method for bolted, adhesively bonded, and hybrid joints involving Fibre-Reinforced-Polymers. Compos. Part B Eng. 46, 179–187. doi:10.1016/j.compositesb.2012.09.074
Wang, Z., Zhao, X. L., Xian, G., Wu, G., Singh Raman, R. K., Al-Saadi, S., et al. (2017). Long-term durability of basalt- and glass-fibre reinforced polymer (BFRP/GFRP) bars in seawater and sea sand concrete environment. Constr. Build. Mater. 139, 467–489. doi:10.1016/j.conbuildmat.2017.02.038
Wegian, F. M. (2010). Effect of seawater for mixing and curing on structural concrete. IES J. Part A Civ. Struct. Eng. 3, 235–243. doi:10.1080/19373260.2010.521048
World Meteorological Organization (2021). Wake up to the looming water crisis. Available at: https://public.wmo.int/en/media/press-release/wake-looming-water-crisis-report-warns#:∼:text=In%202020%2C%203.6%20billion%20people,10%20with%20extremely%20low%20levels.
Wu, G., Sun, Z. Y., Wu, Z. S., and Luo, Y. B. (2012). Mechanical properties of steel-FRP composite bars (SFCBs) and performance of SFCB reinforced concrete structures. Adv. Struct. Eng. 15, 625–635. doi:10.1260/1369-4332.15.4.625
Xian, G., Guo, R., Li, C., and Wang, Y. (2022). Mechanical performance evolution and life prediction of prestressed CFRP plate exposed to hygrothermal and freeze-thaw environments. Compos. Struct. 293, 115719. doi:10.1016/j.compstruct.2022.115719
Yang, Y., Raipala, K., and Holappa, L. (2014). “Ironmaking,” in Treatise on process metallurgy (Elsevier), 2–88. doi:10.1016/B978-0-08-096988-6.00017-1
Zaman, A., Gutub, S. A., and Wafa, M. A. (2013). A review on FRP composites applications and durability concerns in the construction sector. doi:10.1177/0731684413492868
Zhang, K., Zhang, Q., and Xiao, J. (2022). Durability of FRP bars and FRP bar reinforced seawater sea sand concrete structures in marine environments. Constr. Build. Mater. 350, 128898. doi:10.1016/j.conbuildmat.2022.128898
Keywords: life-cycle assessment (LCA), fiber-reinforced polymer (FRP), carbon fiber-reinforced polymer “CFRP”, glass fiber-reinforced polymer (GFRP), environmental impacts
Citation: Sbahieh S, Mckay G and Al-Ghamdi SG (2023) A comparative life cycle assessment of fiber-reinforced polymers as a sustainable reinforcement option in concrete beams. Front. Built Environ. 9:1194121. doi: 10.3389/fbuil.2023.1194121
Received: 26 March 2023; Accepted: 09 May 2023;
Published: 22 May 2023.
Edited by:
Aliakbar Gholampour, Flinders University, AustraliaReviewed by:
Viktor Gribniak, Vilnius Gediminas Technical University, LithuaniaCopyright © 2023 Sbahieh, Mckay and Al-Ghamdi. This is an open-access article distributed under the terms of the Creative Commons Attribution License (CC BY). The use, distribution or reproduction in other forums is permitted, provided the original author(s) and the copyright owner(s) are credited and that the original publication in this journal is cited, in accordance with accepted academic practice. No use, distribution or reproduction is permitted which does not comply with these terms.
*Correspondence: Sami G. Al-Ghamdi, c2FtaS5hbGdoYW1kaUBrYXVzdC5lZHUuc2E=
† ORCID: Sami G. Al-Ghamdi, orcid.org/0000-0002-7416-5153
Disclaimer: All claims expressed in this article are solely those of the authors and do not necessarily represent those of their affiliated organizations, or those of the publisher, the editors and the reviewers. Any product that may be evaluated in this article or claim that may be made by its manufacturer is not guaranteed or endorsed by the publisher.
Research integrity at Frontiers
Learn more about the work of our research integrity team to safeguard the quality of each article we publish.