- School of Management Technology, Sirindhorn International Institute of Technology, Thammasat University, Bangkadi Muang, Thailand
Project delay has been a phenomenon contending with the construction sector opposing time, cost, and quality. This study develops a model, which is a combination of two mathematical decision-making methods DEMATEL and system dynamics modeling, to investigate the impact of the factors on the entire project schedule. The simulation results reveal the importance of minimizing design error to reduce the project delay at the beginning (or preconstruction stage) of the project. Rework, design changes, and change orders must also be closely monitored during the construction to ensure work productivity and on-time project completion. The results also reveal that experienced designers and the use of updated design technology help reduce design errors, thus enhancing work performance in the long term. As shown in the simulation results, the actual project completion time and magnitude of delay steadily reduce with the project series. This explains the fact that the more the consistency and effectiveness in handling the delay factors as similar projects are performed in turns, the better the project performance in terms of time. Therefore, careful consideration of the delay factors reduces the time lag and delay magnitude in construction projects. Other improvements, such as effective supervision during construction which is a function of experienced supervisors, good project management, and cooperation among key stakeholders, including owners, consultants, and contractors, also assist in reducing the construction delay in the long term.
Introduction
The construction industry is a significant and positively contributing sector that catalyzes socio-economic development both in developed and emerging economies (Venkatesh and Venkatesan 2017; Owusu and Aggrey 2020). It provides essential structures, such as private and public infrastructures and housing, thus fulfilling human’s major requirements (Chimay et al., 2008; Imad et al., 2018; Kirchberger 2018). A colossal amount of capital has been invested in infrastructure projects and programs by many governments to promote the socio-economic development of their countries (Andric et al., 2019). This underscores the fact that the significance of infrastructure, as a product of the construction sector, is highly recognized by extant researchers. The industry plays a key role in the improvement of income per capita, thereby, engaging a significant proportion of the active workforce by creating job opportunities (Malaj and Shuli 2015). The Thai construction sector, for example, has experienced massive growth by completing basic infrastructure projects, fostering the growth of the country’s economy (Prasertrungruang and Hadikusumo 2009). Hicham et al. (2016), in the same way, mentioned that the Moroccan construction industry has immensely contributed to the drastic reduction of the unemployment rate and contributed an average of 6.6% of the gross domestic product (GDP), representing half of the gross fixed capital formation (GFCF). Subramani et al. (2014) claimed that the Indian construction sector has contributed immensely to the improvement of the living standard through massive employment, with 31 million employments, accounting for up to 8% of the GDP. Other economies like Ghana (Boadu et al., 2020), the UAE (Cherian 2020), Malaysia (Memon et al., 2012), among others, are not left out of the positive impacts of the construction sectors. These lead to the magnitude of the global construction industry that comprises 40% of the total GDP and is expected to double within the next 30 years (Solis 2007).
Though having a positive impact on the economy, a common besetting problem and complication of the construction sector are delays that reflect poor project performance (Bertelsen and Sacks 2007; Sambasivan and Soon 2007; Yang and Tsai 2011; Gardezi et al., 2014; Jalal and Yousefi 2017). It is defined as an event resulting in the extension of time to complete specific tasks (Sambasivan and Soon 2007). In Saudi Arabia, only 30% of construction projects were completed within the schedule, and the average time overrun was up to 30% (Assaf and Al-Hejji 2005). Seven out of the ten surveyed projects in Nigeria suffered delays, depicting the fact that delays are a major problem in the Nigerian construction industry as several projects executed in Nigeria are faced with the menace of delay (Ibironke et al., 2013).
As time is a major part of every construction plan and can affect each party’s contractual obligations, delays must be minimized to avoid time and cost overruns (Gardezi et al., 2014; Nahidi et al., 2017). A construction delay is also accompanied by numerous social and economic consequences. Myriads of negative effects of delays have been identified by extant researchers. Tafazzoli and Shrestha (2017), for example, opined that construction delay has a deleterious effect on all triple-bottom lines of sustainability, including social, environmental, and financial. Hassan et al. (2017) concluded that time overrun, cost overrun, reduction in profits for the contractor, losses for the owner due to an extended construction phase, distrust between the owner and contractor, legal disputes between various parties, and total abandonment of the project are direct effects of the delay. Gebrehiwet and Luo (2017) added that overrunning of cost, termination of a contract, arbitration, and litigation are the critical consequences of a delay. Ametepey et al. (2017) stated that a delay results in overrunning of time and cost, delay by the contractor in repayment of loans, disputes, and poor quality of work. Khattri et al. (2016) agreed that disputes, cost overrun, time overrun, abandonment, negotiation, lawsuit, litigation, and total desertion are the effects of a delay.
The quest to assuage the threat of a construction delay, coupled with its negative effects, has necessitated myriads of investigations over the years, which are predominantly directed towards identifying factors responsible for this monumental problem. Tahir et al. (2019), for example, investigated the causes of a delay and cost overrun in Malaysian construction projects, while Gardezi et al. (2014) investigated time extension factors in the Pakistani construction industry. The study results show key delay factors, such as law and order situation, design changes, and improper availability of funds with the client. Other studies on causative factors of construction delay include Alaghari et al. (2007), Sambasivan and Soon (2007), Toor and Ogunlana (2008), Mohammed and Isah (2012), Aziz (2013), Sweis (2013), Samarah and Bekr (2016), Ikechukwu et al. (2017), Kesavan et al. (2017), Durdyev and Hosseini (2018), Imad et al. (2018), Shahsavand et al. (2018), Sepasgozar et al. (2019), and Arantes and Ferreira (2020). Results of these investigations reveal key construction delay factors and their influence scores. Nevertheless, the problem of construction delay still lingers, buttressing the fact that the effective panacea to this monumental problem goes beyond the identification of factors, and there is a need to step up a quest to mitigate this problem.
Therefore, this study is staged to comprehensively explore the dynamics of key delay factors utilizing the Decision-Making Trial and Evaluation Laboratory (DEMATEL) and system dynamics (SD) modeling methods. The study aims to identify the critical factors from myriads of factors mentioned so far by extant studies by making. Many of these factors are direct causes of key factors that eventually lead to delay which are referred to in this study as controlling parameters of delay. This also explains the fact many of these factors lead to delay through some other key parameters. For example, Shamsudeen and Obaju (2016), identified insufficient time and funds, lack of coordination, an unclear scope of work, and designer’s lack of experience as contributing factors of design errors. Shortage of materials and experience are mentioned as causes of design change (Mirshekarlou 2012; Suleiman and Luvara 2016), while inadequate planning and scheduling, complexity in design, the rigidity of consultant are mentioned as causes of the change order in a construction project (Halwatura and Ranasinghe, 2013; Alaryan et al., 2014). Rework is mentioned as the direct effect of poor supervision, omissions, alterations, and poor materials (Mahamid, 2016; Enshassi et al., 2017).
Pertinent delay factors intersecting both developed and developing economies are retrieved from extant studies as a result of an extensive literature review. The collated factors were subjected to experts’ scrutiny and judgment in the Thai construction sector to sort and identify the rampant factors associated with the Thai construction sector. The systematic identification of these controlling parameters is an effective way for project stakeholders to get acquainted with the core factors and the dynamics of these factors for effective decision, thereby, mitigating the threat of construction delay to the barest minimum. The DEMATEL analysis results reveal the influences of these key construction delay factors (controlling parameters) on each other. The system dynamics (SD) modeling approach is then utilized to capture the dynamic behaviors of those key construction delay factors and how they affect the construction schedule so that construction companies can plan for a long-term policy to minimize the construction delay.
Previous Studies
Construction Phases
Rao et al. (2016) opined that construction activities are divided into three phases, namely, preconstruction, construction, and post-construction phases. The preconstruction phase consists of project opening, designing, bidding, and work preparation, while the construction phase (so-called execution phase) transforms work design into a physical structure. The post-construction or closeout phase, on the other hand, is embedded with activities to hand in the project. This final phase has often been neglected, making it difficult to close out the project on time. Even the project that proceeds according to the schedule could falter toward the end due to administrative, technical, or financial reasons (Kaul 2014). Therefore, it is also imperative for project stakeholders to carefully handle activities at this phase to avoid construction delay and cost overrun. Main activities in each phase are listed in Table 1.
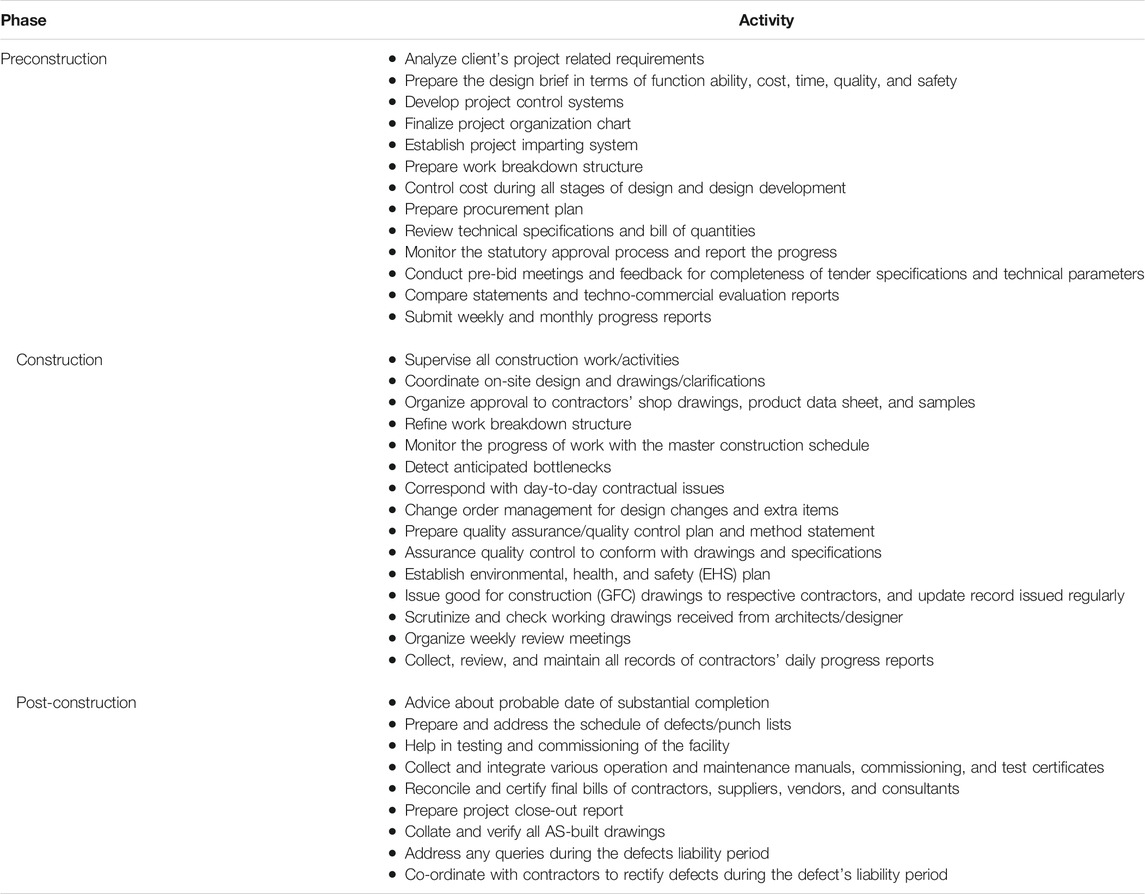
TABLE 1. Main activities in each phase of construction projects (Nikumbh and Pimplikar 2014).
Construction Delay Factors
Construction projects are being stratified into stages to avert besetting risks. However, construction projects are still faced with the menace of time lags, thus debasing project performance. Therefore, myriads of factors responsible for project delays are mentioned in the literature. This study, which is a function of an extensive review of literature, identifies pertinent delay factors intersecting developed and developing economies, as well as the Thai construction industry. Five key delay factors, namely, design error, design change, change orders, rework, and productivity, are considered as key responsible factors in this study. These five key factors are associated with several sub-criteria, also known as independent variables. A total of 27 factors (independent variables) are direct causes of five independent variables, which are referred to as delay-controlling parameters. For example, the design error factor is associated with three variables, namely, communication and coordination, consultant experience, and technology usage. This means that communication and coordination, consultant experience, and technology usage induce design errors causing project delay. The rework factor, on the other hand, consists of two associated variables, namely, supervision and project management.
The Summary of five key construction delay factors (dependent variables) and their total of 27 independent variables is as shown in Table 2.
Research Methodology
Research Flow
The research flow of this study is as shown in Figure 1. A literature review related to construction delay is conducted to examine relevant previous studies on key delay factors. Collected data from experts in the construction industry are then processed with the DEMATEL method to establish and develop the influence weight and diagram of delay factors for SD modeling. The DEMATEL–SD model is established to examine the interrelationships among key delay factors through time. The developed DEMATEL–SD model is simulated and validated through the policy analysis to examine long-term construction delays. The study results are concluded to enhance a better understanding of construction project complexities and identify policies for effective decision making and planning, leading to better construction project performance in terms of time.
The decision-making process is essential in managing a successful organization (Anastasiu 2018). Decision at all stages of a construction project, from the beginning, execution, to closeout stages is imperative to avoid resulting problems that might ensue (Szafranko, 2017). Various decision-making methods are applied to several diverse situations, and therefore, management in construction projects entails a series of decisions. Strategy selection and strategy implementation are the important phases in decision-making processes involved in construction projects. The four major approaches to a decision-making process can be inductive, deductive, development of a benefit matrix, and marginal analyses (Szafranko, 2015). These approaches are different from each other as they can be used separately, in a sequence, or in conjunction with each other (Jajac et al., 2015). For example, Erdogan et al. (2016) adopted the analytic hierarchy process as a decision-making tool for construction management, while Seker and Zavadskas (2017) examined the application of the fuzzy DEMATEL method for analyzing occupational risks on construction projects. Results show that the fuzzy DEMATEL method can evaluate causal factors of occupational hazards by a cause–effect diagram and improve certain measures on a construction site.
The complexities involved in a construction project make the project system difficult. Controlling factors embedded in the process of construction project implementation make the construction project very complex causing colossal challenges to the project control, thus debasing performance. Hierarchical listing of key factors and the cause–effect relationships among the key factors may not be adequate for the holistic investigation of construction delay. Having established the influence weight of these factors, it is also important to comprehensively explore the dynamics of these factors to establish the impact of these factors on the entire project schedule for effective decision and planning to significantly assuage the menace of construction project delay. According to Yu-jing (2012), SD modeling is an effective way to improve performance through effective project control. It has been increasingly advocated by researchers to explore nonlinear and dynamic complexity issues involved in construction management. Maryani et al. (2015), for example, examined an SD approach for modeling construction accidents, while Liu et al. (2019) conducted a critical review on future trends of SD modeling for construction management research. SD modeling involves the integration of methods, combining network analysis, fuzzy logic analysis, discrete event simulation, and agent-based simulation (Liu et al., 2019). It is used in examining the impact of contextual complicated conditions in project planning and control, effectiveness and performance, strategic management, and sustainability (Liu et al., 2019). The role of SD in advancing other decision-making methods to comprehensively explore relationships and dynamics of a system cannot be overemphasized, as it is the ground to establish the impact of parameters on a set-down standard, initiating effective decisions to enhance better project performance.
This study utilizes the DEMATEL and SD modeling methods as the main methodologies to examine long-term construction delay. The study develops a conceptual framework of construction delay from five key construction delay factors (or dependent variables), namely, design error, design change, change orders, rework, and productivity factors, and their associated independent variables. The data collected from experts in the Thai construction industry, as well as secondary data from well-known construction-related literature, are used for the DEMATEL and SD modeling analyses. The importance of each key factor and its influence on the other factors, as a result of the DEMATEL analysis, is examined. A causal loop diagram, based on the DEMATEL analysis results, is developed utilizing the SD modeling approach to better understand the dynamic behavior of those key construction delay factors. The DEMATEL-SD model of construction delay is developed to depict the comprehensive dynamics of delay factors and investigate the impact of each factor on project schedule to enhance the understanding of complex project systems, and effectively plan for construction scheduling to minimize delay in the long term.
Data Collection Method
Information about the degree of influence among the five delay factors was collected from 15 leading experts in the Thai construction sector on the degree of impact of one factor on the other. This number of experts is considered adequate (Kumar and Dash 2016; Tsai et al., 2016; Susanty et al., 2019), since DEMATEL analysis is not an approach premised on the sample size but the judgment of experts with reasonable years of experience in the industry of concern (Hossain et al., 2020). 73% of the experts were males, there were contractors, consultants, and clients of building construction projects, representing 47, 33, and 20% of total responses, respectively. 40% of them were working as engineers, 27% were project managers, architects (20%), and 13% were quantity surveyors on large-scale construction projects. The result revealed that judgmental opinions of the experts used in the DEMATEL-SD analysis are reliable with a Cronbach’s alpha of 0.939, which is greater than the minimum acceptable value of 0.7 (SAS 2007). The developed DEMATEL–SD model considers all three construction phases to thoroughly plan for the construction schedule to minimize construction delay in the long term.
DEMATEL Analysis Method
The DEMATEL analysis was developed to resolve intertwined problematic groups using a mixture of matrices (Shieh et al., 2010; Wu et al., 2010). It is effective in establishing the cause-and-effect relationships in structured models and is an effective method for decision-makers especially in the management field (Kaushik and Somvir 2015). The technique has been applied in many areas over the years. One of the merits of this method is the ability to visualize the interrelationships between factors and enable decision-makers to clearly understand which factors have a mutual influence on others (Singh et al., 2018).
In this study, pertinent steps of DEMATEL are proposed (Shieh et al., 2010; Amiri et al., 2011; Kaushik and Somvir, 2015; Abdullah et al., 2019; Kakha et al., 2019).
• Step 1: Compute the direct-relation (average) matrix A: To assess the relationships between
• Step 2: Normalize the direct-relation matrix A. By normalizing the average matrix A, the normalized direct-relation matrix D can be obtained in which the value of each element in the matrix D is between 0 and 1 (see Eq 2, Eq 3), where
• Step 3: Compute the total-relation matrix T. The total-relation matrix T is an (n × n) matrix and is defined by Eq. 4, where I is the identity matrix.
• Step 4: Calculate the sum of rows (R) and sum of columns (C). In the total-relation matrix T, the sum of rows and the sum of columns are expressed by the vectors R and C, respectively, where the vectors R and C are separately expressed as the sum of rows and sum of columns from the total-relation matrix
• Step 6: Select a threshold value
SD Modeling Analysis Method
SD modeling is used in this study to develop the SD model of construction delay. SD modeling analysis aims at modeling and analyzing the behavior of complex systems in an industrial context (Boateng et al., 2012). It is designed to help decision-makers learn about the structure and dynamics of complex systems, design high-leverage policies for sustained improvement, and speed up successful implementation and changes. It is systematic thinking that enhances the communication of high-level complex information to be disseminated into a simplified circular-loop feedback structure.
The SD approach is based on the concept of a causal loop diagram and is effective in modeling processes that involve changes over time (Ogunlana et al., 2003). Each causal link is assigned a polarity, either positive (+) or negative (−), to indicate how a variable impacts or is impacted by the other variable over time (Sterman et al., 2000). Kim et al. (1999) explained that a positive (+) link indicates that as one variable changes, the next variable changes in the same direction. A negative (−) link, on the other hand, indicates that as one variable changes, the other changes in the opposite direction. A causal loop, on the other hand, can either be reinforcing or balancing based on the number of negative (−) signs. If there are no negative (−) signs or an even number of negative (−) signs, then the loop is reinforcing. Contrary, if there is an odd number of negative (−) signs, then the loop is balancing (Kim et al., 1999).
Another main concept of the SD approach is the stock-flow diagram. Stock is a representation of significant or insignificant accumulations within the system. Flow, on the other hand, signifies the rate of change in the system represented by the inflow (which increases the level of the stock) or outflow (which reduces the stock level). The mathematical relationship between the stock and flow is given in Eq. 8, where
The initial stock does not have to be positive as it may be negative, null, or positive (Chaker et al., 2015). A net flow of stock, also known as the derivative of the stock, is defined as some function of variables and constants. Since most of the system is premised on a feedback structure, the net flow depends on the stock. Therefore, a net flow of a stock is as shown in Eq. 9, where
In this study, the DEMATEL analysis results achieved will be used as input and pathways to the development of the DEMATEL–SD model of construction delay.
Analyses Results
Results of the DEMATEL Analysis
The collated data are analyzed with DEMATEL using MATLAB 2019 software. The direct-relation matrix A of all 15 experts was calculated, as shown in Table 3. The normalized initial direct-relation matrix D is constructed, as shown in Table 4, while total-relation matrix T is described in Table 5.
In this study, the threshold value
Design change factor, on the other hand, is found to have the least influence among the five key construction delay factors. This may be because fewer design errors lead to less rework (the relationship between design error and rework factors, see Figure 2), which in turn, lower design changes (relationship between rework and design change factors, see Figure 2). Rework influences design change and mutually influences design error, change order, and productivity. These reflect complex relationships among the five key construction delay factors. The methodology that can deal with complex systems, such as the SD modeling approach, therefore, should be utilized to fully understand their interrelationships and feedback systems, so that a proper plan could be established in each phase of construction to minimize construction delay and deliver the project on time.
Results of the DEMATEL–SD Model of Construction Delay
The DEMATEL–SD Model of Construction Delay Development
This study utilizes the five key construction delay factors and their associated variables to examine their comprehensive dynamic relationships, and how they affect project schedule using the so-called DEMATEL–SD analysis method. DEMATEL analysis, on one hand, enhances a comprehensive understanding of construction delay factors, their impact levels on construction delay, and their influences on the others. SD modeling, on the other hand, is an effective technique in construction project management with the potential to contribute to decision-making in a complex system. It considers the causal feedback relationships among construction delay factors, and how these factors affect the project schedule. Therefore, the DEMATEL–SD model approach is adopted in this study to effectively capture the dynamic behaviors of construction delay, which are not widely mentioned in past research. It is expected that the study results provide a better understanding of key construction delay factors and their influences on the project schedule, and also assist in developing effective policies to resolve delays and complete the project within the schedule.
Both the primary and secondary data were used for the DEMATEL–SD model development (see Table 6). They were validated before inputting into the model. Model validation is the process of determining whether the model accurately represents the behavior of the system. This process enhances confidence in the model representing the real-life situation it seeks to emulate (Gilkinson and Drangerfield 2013). The process of a system established for the purpose of analyzing a key problem in an organization demands acquiring acceptance from a closely involved set of eligible personnel and possibly affirming that the base case behavior is qualitatively in accordance with the known reported (past) data. The model, which was formulated based on the results obtained from DEMATEL, was subjected to a validation process featuring a league of industrial experts, inviting their opinions and contributions to the model, thus providing a tool that can be adopted to improve the project’s performance.
A group of experts working in leading building construction companies in Bangkok and other provinces in Thailand participated in the validation process. They are top executives, owners, and engineers having more than 20 years of working experience in large-size building construction with an average of 100 million Baht in capital investment and over 100 operators. A preliminary piece of information was shared explaining how the model was developed. This helped the experts understand how the model worked. Experts were asked to review the model and give comments to improve the model. The model was subsequently adjusted based on their recommendation and comments.
The causal loop diagram of the five key construction delay factors, their associated items, and the DEMATEL–SD model of construction delay are as shown in Figures 3, 4. The model depicts the relationships among the five key construction delay factors and their associated items.
In this study, the DEMATEL–SD model of construction delay is scheduled to be completed within 232 weeks, with 23 weeks (162 days) for the preconstruction stage, 200 weeks for the construction stage, and 9 weeks for the post-construction stage (i.e., 209 weeks for the construction and post-construction stages). The planned project tasks are 10,000 units (Wang and Yuan 2017). The preconstruction stage consists of 996 tasks, while the construction and post-construction (closure) stages consist of 9004 tasks.
In a typical design-bid-build system, which is considered in this study, key stakeholders involved at the preconstruction stage include owners and consultants. According to Ham et al. (2018), design error is crucial in the preconstruction stage to minimize delays. Therefore, the model describing the workflow of the project is established by focusing on the preconstruction stage’s design workflow to minimize design errors (i.e., enhance communication, technology usage, and consultant’s experiences, which are two-three items under the design error factor (see Figures 3, 4)). The workflows, considering design changes, change orders, rework, and productivity, are then considered in the construction and post-construction stages to minimize the overall construction delay of the project. The design error is recognized as the key delay factor at the preconstruction stage with a significant effect on rework and the project schedule, as signaled by DEMATEL analysis results. This makes it important to examine the design processes based on the associated sub-criteria (which are communication, experience, and technology usage) and other endogenous variables to minimize the magnitude of design errors before the commencement of the construction processes to save the project from a colossal delay.
In the design error section, the design development rate depends mainly on staff in the designing team, productivity in design, and levels of communication between the design team and other stakeholders (see Figure 4 and Eq. 10).
The effectiveness of the designers also depends on their experiences. In this study, four new designers are considered at the beginning of the project in expectation to complete the design on time. It is also hypothesized that there is a need for one experienced designer to train four new designers (Suslov and Katalevsky 2019). The variable “effective designers,” as shown in Eq. 11, is a value depicting the collation of full-time experienced designers that can work on the design. According to Suslov and Katalevsky (2019) and DEMATEL analysis results, new designers have 80% productivity subjected to improvement by experienced designers.
Design tasks are to be completed by the design team. The number of completed design tasks depends on the error proneness of the designers (i.e., mistakes from designers). According to Love et al. (2008), the design error proneness by expert designers, designers inducted from other projects, and newly recruited designers are 10, 20, and 25%, respectively. In the DEMATEL–SD model, however, the design error at the beginning is set at 20%, assuming that new designers become experienced in 30 days of work.
Butlewski et al. (2014) mentioned that the use of high design technology helps reduce design errors. A reasonable level of accuracy in handling and applying advanced engineering design software debases design errors. Nevertheless, design error always exists. Even if the design system can be operated without human intervention, the chance of design errors is still possible (Busby 2001; Foord and Gulland 2006). Since the owners define and control the project through the consultants, the consultants’ roles are very sensitive in ensuring proper supervision of the design processes to avoid design errors (Kubba 2012). In a typical DBB system, the design processes are concluded before the commencement of the construction process. Therefore, the consultants must facilitate effective communication and provide advanced engineering software to ensure a reasonable level of design accuracy.
The design error (in % of error) is calculated based on Eq. 12. With higher designers’ experience, better communication, and better technology usage, design errors can be reduced, resulting in lower rework and change orders and higher productivity (see Figure 3).
The construction and post-construction phases are scheduled to be completed within 209 weeks in this study. The change order factor relates to the design error factor, as a result of DEMATEL analysis. Fewer design errors, therefore, lead to fewer change orders (see Eq. 13).
Rework is modeled to be associated with supervision and project management (see Figure 3). In addition, the rework factor is also affected by design errors, change orders, and productivity factors, as a result of DEMATEL analysis. These reflect in the “poor project tasks’ completion” in Eq. 14 and “undiscovered rework” in Eq. 15. With better supervision and project management, together with fewer design errors and change orders, the undiscovered rework could be reduced, resulting in high work progress and productivity (see Figure 3). This is consistent with Love et al. (2008) that design error contributes greatly to the total amount of rework experienced in the construction project, which later results in the schedule delay.
Productivity is the key factor in the post-construction phase. Based on the DEMATEL analysis results, this factor was influenced by design errors, rework, and change orders. Once design errors are detected, some completed tasks are to be redone; this reduces productivity. An increase in productivity is achieved once repeated projects are performed. Design errors, change orders, and rework are reduced through experiences, better technology, good project management, high-quality equipment, motivation, and staff encouragement, thus reducing the delay of the whole project (see Figure 3 and Eq. 16).
The early stage of a construction project faces various problems, ranging from frequent changes, low supervision, the inability of staff to adapt to construction processes, and high rework, resulting in poorly completed tasks that lead to delays in project completion. Once the project continues, workers get adapted to the processes, project supervision becomes more effective, and tasks are completed according to the owner’s specification, resulting in the increase of properly completed tasks, thus reducing rework and delay in the construction phase.
The Simulation Results of the DEMATEL–SD Model of Construction Delay
The DEMATEL–SD model of construction delay is simulated, and the simulation results are as shown in Figure 5. With no consideration of five key construction delay factors, the construction companies face a delay of a maximum of 16 weeks, that is, 248 weeks of completion time. This could be seen in the early projects. Once similar projects are performed, and the improvement of the five key delay factors are implemented, the construction companies can reduce the construction delay to meet the deadline of 232 weeks as planned.
A closer examination of the project at the beginning (the first project) reveals that at the end of the 232nd week, the closed tasks are 8,899 out of 10,000 tasks. It is found that the delay in the preconstruction stage results in unfinished closed tasks in the construction and post-construction stages. This early-stage delay comes from the inexperience of designers. Once the projects are repeated, with better technology usage and experienced designers, the design error reduces from 20% to a minimum of 0.47% (as no absolute design error is impossible). Fewer design errors in the preconstruction phase reduce rework, change orders, and design changes in the construction phase, thus increasing productivity in the post-construction phase. Figure 6 shows the delay time of the construction projects. It can be seen that the delay is reduced once the five key construction delay factors are considered and improved.
Model Validation Through Policy Analysis
In this study, the behavior–sensitivity test is referred to as the policy testing analysis. It focuses on the sensitivity of the model’s behavior to changes in parameter values. It is conducted by experimenting with different parameter values and analyzing their impact on the system (Forrester and Senge 1980). It is one of the most effective methods used to build confidence in SD models.
In this study, policy testing is performed to achieve the strategies the construction companies can perform to complete the project on time. As design error is a crucial factor in the preconstruction stage and that this factor depends on the design team and technology used in the design (see Figures 3, 4), the policy testing is then performed by changing the technology usage values, from 0.03 (representing outdated design technology) to 0.07 (representing updated design technology). The results, as shown in Figure 7, reveal that the use of low design technology results in more delay of the whole project, as design changes, rework, and change orders are achieved in the construction stage.
The impact of technology on the design process and the entire project is immense, as low technology input impacts the project schedule negatively. With the optimum value of technology accuracy (i.e., TA @ 0.07), the time lag in delivering the project is reduced compared with other values of technology accuracy (see Figure 7). The impact of reasonable accuracy in technology would make the design processes completed with minimal error, thus contributing significantly to the timely project completion.
Rework is a critical factor in the construction phase, and effective supervision is needed to detect rework at the beginning of the construction. The policy testing is then performed by changing supervision personnel from one to three persons. The results show that with better supervision, the projects can be completed on time (see Figure 8). The increasing value of supervision personnel (
In summary, it is suggested that the construction sector gives considerable attention to technology to alleviate the menace of design errors, thus alleviating the threat of frequent changes, rework, and low productivity. It is also important that project participants embark on effective supervision to debase the problem of rework and enhance project performance and on-time project completion.
Discussion
In this study, the DEMATEL analysis results are adopted to depict the relationships among key construction delay factors and serve as the input for DEMATEL–SD model development. Design error is considered a key delay factor at the preconstruction stage. To minimize design errors, better design techniques should be used, together with enhanced communication and experienced designers. Design errors at the preconstruction phase and changes during construction alter the initial scope of work, and these modifications or alterations necessitate rework, which in turn, affects project quality and completion time. Therefore, it is imperative for project stakeholders to make sure project scope and requirements are clearly spelled out at the early stage of the project to mitigate the threat of design changes, change orders, and rework during the construction. Delay may affect project closure if design errors are not minimized. In addition, closing more tasks demands a high level of effort and cooperation among key stakeholders, including owners, consultants or the design team, and contractors to ensure project completion time. With the concerted efforts of the project staff, the projects experience improved productivity early enough during construction, which in turn, subjugate the menace of errors, changes, and rework. It is, therefore, important for project owners to weigh their financial options before embarking on a construction project to avoid any forms of financial problems. In the course of the project execution, the consultant should effectively oversee the design processes to avoid any ambiguities or complexities in project designs that could make the design complicated for the contractor to implement. The consultant and contactor should also utilize quality equipment and materials in the design and construction. These would avert workers’ absenteeism and frequent equipment breakdown, thus enhancing work performance, productivity, minimizing design errors, change orders, rework, and completing the project on time. This could be seen by the gradual improvement in project performance when similar projects are performed (see Figure 5), subjected to a steady improvement of the key delay factors. The magnitude of delay depicted in Figure 6 further proves that the construction delay can be reduced in the long term through the improvement of key construction delay factors and their associated items, such as technical accuracy, supervision personnel, and points suggested in this study. The time lag in closing a project gradually reduces due to a gradual improvement in handling the controlling factors of delay. This depicts the fact that a better project performance, in terms of time, is a process that evolves over time in subsequent projects as delay factors are consistently being dealt with. Effective supervision, project management, and technology are among key players in dealing with these inhibiting factors.
The DEMATEL–SD integrated system is useful in initiating a panacea to other prevailing problems opposing performance in the construction sector. The model clearly showcases a series of similar projects performed in succession, where a steady delay decline is realized in the project delivery time and delay magnitude through consistent debasement of the threat of the key factors for each succeeding project. This explains the fact that developing subsequent effective measures against these time lag factors improves project performance gradually, as better project performance in terms of time is a phenomenon that evolves in a succession of time. The DEMATEL–SD model, which possesses flexible simulation capacities to test the effects of compelling factors on the overall project scheme as demonstrated in the policy testing section, enhances practical project schedule management effectiveness as project stakeholders could easily examine the influences of key factors on the project schedule. Also, it allows for the assessment of other projects’ performance-inhibiting factor mitigation measures in advance. It helps project stakeholders to easily observe and analyze the effects of the occurrence of delay factors on the system behavior over time. This, in turn, enables stakeholders to identify the key impact and establish corresponding inhibiting measures, if necessary. Furthermore, the integrated model is easy and convenient for project personnel to apply in a practical sense, owing to the realistic nature of the model. The model is robust simulating various construction project-scheduling scenarios because the factors and the feedback relationships are determined based on the exploration of the experiences and analysis prowess of key construction project practitioners. The established encapsulating hierarchical structure of factors, which is a core of the DEMATEL–SD model, is determined based on the impacts of factors on each other, unlike the commonly adopted statistical approaches that do not possess the characteristics of ranking factors based on their impacts on each other. The model’s structure and variables possess the characteristics of being easily fine-tuned to reflect real practices.
As extensive examination and effective management of construction delay-controlling factors are vital to the achievement of better project performance, this study presents a unique way of investigating the menace of project delay. It is distinct from other studies that focus on identifying the causes of the delay. Holistic examination and exploration of the dynamics of key delay factors were carried out throughout the construction project stages. The comprehensive dynamics of the project design cycle, changes during construction, rework, and productivity encapsulated in the integrated work process are critically examined to debase the threat and magnitude of project delay from the preconstruction to post-construction stages of the project as a swift and prompt way of dealing with the project-time lag menace. This study, which lies in its contribution to advancing the body of knowledge of project scheduling and management, has resulted in the development of a mathematical hybrid system that explicitly demonstrates the interactions among construction project delay parameters and reflects the hierarchical and feedback structure of project delay management configuration. The simulation results that are displayed in the figures make it easy for the construction industry and related sectors to understand the complex relationships among key construction delay factors and plan for delay improvement in the long term.
Conclusion
This study adopted a novel approach to proffer a solution to the menace of construction delay that emanates from the preconstruction stage and metamorphosizes into a thriving problem throughout the project. The DEMATEL–SD model is adopted in this study to investigate the relationships among the controlling factors of delay and their impacts on the project schedule over time. The developed model is embedded with several contributing parameters to depict the overall workflow processes. It is found that design errors should be minimized at the beginning of the project to reduce change orders, design changes, and rework during the construction. Minimizing the threat of design error, changes during construction, rework, and steady improvement in productivity reduces the time lag and delay magnitude (as shown in Figures 5, 6, for 20 different projects). Project participants tend to learn from their mistakes in the previous projects to enhance better performance in subsequent projects, as better project performance in terms of time is a process that evolves with time. Minimal design errors achieved by a reasonable level of technical accuracy and experienced designers significantly reduce the magnitude of delay of the whole project. Effective supervision born from experiences and active supervisors help minimize schedule delay through timely detection of rework during the construction. Also, consistent consideration and subjugation of the key delay parameters reduce the schedule delay in the long term.
The consultant, who has been with the owner from the early stage of the project, plays a key role in the design process. The consultant should work assiduously to facilitate a stellar project management system and effective supervision, especially in a situation where the project enjoys adequate financing from the owner.
This study contributes a body of knowledge to the construction industry. The DEMATEL–SD model is developed to analyze the problems of construction delay, showing the dynamics of delay-controlling factors and their impacts on the project schedule over time. The results of the DEMATEL analysis serve as reliable mathematical decision criteria to support SD modeling analysis, forming a hybrid system that can be used to effectively plan and manage the project schedule in the long term. DEMATEL analysis does not only validate the fact that the delay factors are greatly influenced by attributing significant influence values to the factors, but also describes how the SD model could be adopted to comprehensively explore the dynamics of the factors based on the established influence weight of factors and the relationships among them. The integrated model, therefore, describes how the factors at play influence each other to affect the project schedule for project players to realize that the menace of project delay is an intricating system that demands a systemic method to subjugate. Furthermore, the model is successful in generating results that stakeholders confirmed applicable and represent the reality of project outcomes in the construction sector. The robust nature of the model makes it easy to be replicated to address several other pertinent problems of project performance. In such cases, the project players only have to add the responsible factors to the model by determining their interrelationships with the current variables in the system. The study results help decision-makers to better understand the uncertainties and complexities involved in construction projects through the convoluted relationships among delay-controlling factors and their impacts on the project schedule as a modus operandi to alleviate construction delay, thereby attenuating the threat of time and cost overruns in the long term. The project’s actual completion time series and the delay magnitude profiles established in the study describe the importance of dealing with project delay factors for a monotonically increasing better construction project performance to avert the menace of the negative occurrences associated with project delays.
This study focuses on construction projects in Thailand, which is an emerging economy having a similar project environment and characteristics with other developing economies across the globe. Therefore, more research spanning through other developing economies may be carried out. Also, further research could be conducted to advance the SD model to capture an effective panacea to some other opposing problems of the construction sector.
Data Availability Statement
The original contributions presented in the study are included in the article/Supplementary Material; further inquiries can be directed to the corresponding author.
Author Contributions
The authors confirm contribution to the paper as follows: Conceptualization, data collection, and analysis and result interpretation: BA and TC. Draft manuscript preparation: BA. Revision of manuscripts and corrections: TC and BA.
Conflict of Interest
The authors declare that the research was conducted in the absence of any commercial or financial relationships that could be construed as a potential conflict of interest.
Publisher’s Note
All claims expressed in this article are solely those of the authors and do not necessarily represent those of their affiliated organizations, or those of the publisher, the editors, and the reviewers. Any product that may be evaluated in this article, or claim that may be made by its manufacturer, is not guaranteed or endorsed by the publisher.
Acknowledgments
The authors are sincerely grateful to Sirindhorn International Institute of Technology (SIIT), Thammasat University, Thailand, for the provision of enabling environment and adequate facilities that enhance the success of the research.
References
Abbasi, O., Noorzai, E., Jafari, K. G., and Golabchi, M. (2020). Exploring the Causes of Delays in Construction Industry Using a Cause-And-Effect Diagram: Case Study for Iran. J. Architect. Eng. 26 (3), 1–16. doi:10.1061/(asce)ae.1943-5568.0000431
Abdullah, L., Ramli, R., Bakodah, H. O., and Othman, M. (2019). Developing a Causal Relationship Among Factors of E-Commerce: A Decision Making Approach. J. King Saud Uni. Comput. Inf. Sci. 1319 (1578), 1–8. doi:10.1016/J.JKSUCI.2019.01.002
Abeku, D. M., Ogunbode, E. B., Salihu, C., Maxwell, S. S., and Kure, M. A. (2016). Project Management and the Effect of Rework on Construction Works: A Case of Selected Projects in Abuja metropolis, Nigeria. Int. J. Finance Manag. Practic. 4 (1), 2360–7459.
Ahmed, S. M., Azhar, S., Kappagantula, P., and Gollapudi, D. (2003). “Delay in Construction: A Brief Study of the Florida Construction Industry,” in ASC Proceedings of the 39th Conference, Clemenson, South Carolina, April 10–12, 2013, 257–266.
Aibinu, A. A., and Odeyinka, H. A. (2006). Construction Delays and Their Causative Factors in Nigeria. J. Constr. Eng. Manage. 132 (7), 667–677. doi:10.1061/(asce)0733-9364(2006)132:7(667)
Al-Hams, M. F. (2010). Simulation Model of Change Orders and Their Impact on Building Projects Performance in Gaza Strip. Gaza, Palestine: Thesis of Islamic University, 1–194.
Alaghari, W., Kadir, M. R. A., Salim, A., and Ernawati, M. K. (2007). The Significant Factors Causing Delay of Building Construction Projects in Malaysia. Eng. Construct. Architect. Manag. 14, 192–206. doi:10.1108/0969998071073130
Alaryan, A., Emadelbeltagi, E. A., and Dawood, M. (2014). Causes and Effects of Change Orders on Construction Projects in Kuwait. Int. J. Eng. Res. Appl. 4 (7), 1–8. doi:10.5296/ijafr.v4i1.5405
Alavifar, A. H., and Motamedi, S. (2014). “Identification, Evaluation, and Classification of Time Delay Risks of Construction Project in Iran,” in Proceedings of International Conference on Industrial Engineering and Operations Management, Bali, Indonesia, January 7–9, 2014, 919–929.
Ameh, O., and Osegbo, E. E. (2011). Study of Relationship Between Time Overrunand Productivity on Construction Sites. Ijcscm 1 (1), 56–67. doi:10.14424/ijcscm101011-56-67
Ametepey, S. O., Gyadu-Asiedu, W., and Assah-Kissiedu, M. (2017). Causes-effects Relationship of Construction Project Delays in Ghana: Focusing on Local Government Projects. Adv. Hum. Factor Sustain. Urban Plan. Infrastr. Adv.Intelligent Sys. Comput. 600, 84–95. doi:10.1007/978-3-319-60450-3_9
Amiri, M., Salehi Sadaghiyani, J., Payani, N., and Shafieezadeh, M. (2011). Developing a DEMATEL Method to Prioritize Distribution Centers in Supply Chain. msl 1, 279–288. doi:10.5267/j.msl.2010.04.001
Anastasiu, L. (2018). The Decision-Making Process in Construction Project Management by Using the ELECTRE I Method. Int. J. Res. Sci. Manag. 5 (2), 1–14. doi:10.5281/zenedo.1168806
Andric, J. M., Mahamadu, A., Wang, J., Zou, P. X. W., and Zhong, R. (2019). The Cost Performance and Causes of Overrun in Infrastructure Development Projects in Asia. J. Civil Eng. Manag. 25, 203–214. doi:10.3846/jcem.2019.8646
Arantes, A., and Ferreira, L. M. D. F. (2020). A Methodology for the Development of Delay Mitigation Measures in Construction Projects. Prod. Plann. Control. 32 (3), 228–241. doi:10.1080/09537287.2020.1725169
Arantes, A., Silva, P. F., and Ferreira, L. M. D. F. (2015). Delays in Construction Projects – Causes and Impacts. 6th IESM Conference. Seville, Spain: IEEE, 1–6.
Ardila, F., and Francis, A. (2020). Spatiotemporal Planning of Construction Projects: A Literature Review and Assessment of the State of the Art. Front. Built. Environ. 6 (128), 1–13. doi:10.3389/fbuil.2020.00128
Assaf, S. A., and Al-Hejji, S. (2005). Causes of Delay in Large Construction Projects. Int. J. Proj. Manag. 24, 349–357. doi:10.1016/j.ijproman.2005.11.010
Aziz, R. F. (2013). Ranking of Delay Factors in Construction Projects After Egyptian Revolution. Alexandria Eng. J. 52, 387–406. doi:10.1016/j.aej.2013.03.002
Bahra, A. (2019). “What Causes Delays and Cost Overruns on Major Infrastructure Projects,” in Construction Products Association. London: The Building Centre
Bajjou, M. S., and Chafi, A. (2018). Empirical Study of Schedule Delay in Moroccan Construction Projects. Int. J. Constr. Manag.. doi:10.1080/15623599.2018.1484859
Bassa, M., Reta, A., Alyew, A., and Tora, M. (2019). Causes and Effects of Design Change in Building Construction Projects in Three Selected Southern Ethiopia Zone. Int. J. Eng. Res. Technol. 8 (12), 757–761.
Bertelsen, S., and Sacks, R. (2007). “Towards a New Understanding of the Construction Industry and the Nature of its Production,” in Proceedings of IGLC, Michigan, USA, July 15, 2007, 46–56.
Boadu, E. F., Wang, C. C., and Sunindijo, R. Y. (2020). Characteristics of the Construction Industry in Developing Countries and its Implications for Health and Safety: An Exploratory Study in Ghana. Int. J. Environ. Res. Public Health 17, 1–20. doi:10.3390/ijerph17114110
Boateng, P., Chen, Z., and Ogunlana, S. (2012). A Conceptual System Dynamic Model to Describe the Impacts of Critical Weather Conditions in Megaproject of Construction. J.Construct. Proj. Manag. Innovat. 2, 208–224. doi:10.36615/jcpmi.v2i1.22
Busby, J. S. (2001). Error and Distributed Cognition in Design. Des. Stud. 22, 233–254. doi:10.1016/s0142-694x(00)00028-4
Butlewski, M., Kaczmarek, M. J., Misztal, A., and Slawinska, M. (2014). Design Methods of Reducing Human Error in Practice. London: Poznan University of Technology, 1–6. doi:10.1201/b17399-54
Chaker, F., El Manouar, A., and Idrissi, M. A. J. (2015). Towards a System Dynamic Modelling Method Based on DEMATEL. Int. J. Comput. Sci. Informat. Technol. (Ijcsit). 7, 28–40. doi:10.5121/ijcsit.2015.7203
Chandrusa, S., and Basha, M. (2017). Rework Management in Construction Projects and Comparison with Time and Cost. Int. J. Eng. Sci. Comput. 7 (6), 13020–13025.
Cherian, A. (2020). The Construction Industry in the Perspective of an Economic Boost of the United Arab Emirates (UAE). Int. J. Eng. Technol. (Irjet). 7, 270–276.
Chimay, J., Raja, A. R. A., and Mutis, I. J. P. I. (2008). Ontology-based Information and Knowledge Management in Construction. Construct. Innovat. 8, 219–239. doi:10.1108/14714170810888976
Choopojcharoen, T., and Magzari, A. (2012). Mathematics behind System Dynamics. Worcester, Massachusetts: Worcester Polythechnic Institute, 1–102.
Couto, J. P. (2012). Identifying of the Reasons for the Project Design Errors in the Portuguese Construction Industry. Nat. Appl. Sci. 3 (2), 164–170.
Desai, M., and Bhatt, R. (2013). Critical Causes of Delay in Residential Construction Project: Case Study of central Gujarat Region of India. Int. J. Eng. Trend Technol. 4 (4), 762–768.
Durdyev, S., and Hosseini, M. R. (2018). Causes of Delays on Construction Projects: a Comprehensive List. Int. J. Manag. Proj. Bus. 13 (1), 20–46. doi:10.1108/IJMPB-09-2018-0178
Eksander, A. F. Z. (2018). Risk Assessment Influencing Factors for Arabian Construction Projects Using Analytic Hierarchy. Alexandria Eng. J. 57, 4207–4218. doi:10.1016/j.aej.2018.10.018
Enshassi, A., Sundermeier, M., and Zeiter, M. A. (2017). Factors Contributing to Rework and Their Impact on Construction Projects Performance. Int. J. Sustain. Construct. Eng. Technol. 8 (1), 12–33.
Erdogan, S. A., Šaparauskas, J., and Turskis, Z. (2017). Decision Making in Construction Management: AHP and Expert Choice Approach. Proced. Eng. 172, 270–276. doi:10.1016/j.proeng.2017.02.111
European Commission (2018). European Construction Sector Observatory. Ireland: ECSO, 1–33. https://ec.europa.eu/growth/sectors/construction/observatory_en.
Foord, A. G., and Gulland, W. G. (2006). Can Technology Eliminate Human Error. Process Saf. Environ. Prot. 84, 171–173. doi:10.1205/psep.05208
Forrester, J. W., and Senge, P. M. (1980). Tests for Building Confidence in System Dynamics Models. TIMS Stud. Manag. Sci. 14, 209–228.
Fuade, D. F., Rahmawati, Y., and Utomo, C. (2017). Factor of Design Errors in Construction Project. IPTEK J. Proc. Ser. 6, 284–288.
Gardezi, S. S. S., Manarvi, I. A., and Gardezi, S. J. S. (2014). Time Extension Factors in Construction Industry of Pakistan. Proced. Eng. 77, 196–204. doi:10.1016/j.proeng.2014.07.022
Gascuena, N. V., Astor, E. N., del-Burgo, J. F., and Fernandez, J. P. R. (2011). “Factors that Affect the Productivity of Construction Projects in Small and Medium Companies: Analysis of its Impact on Planning,” in Proceedings of 27th Annual ARCOM Conference of Association of Research in Construction and Management, Bristol, UK, September 5–7, 2011, 879–888.
Gebrehiwet, T., and Luo, H. (2017). Analysis of Delay Impact on Construction Project Based on RII and Correlation Coefficient: Empirical Study. Proced. Eng. 196, 366–374. doi:10.1016/j.proeng.2017.07.212
Gilkinson, N. R., and Dangerfield, B. C. (2013). Some Results From a System Dynamics Model of Construction Sector Competitiveness. Manchester: University of Salford, 1–18. doi:10.1016/j.mcm.2011.09.011
Halwatura, R. U., and Ranasinghe, N. P. N. P. (2013). Causes of Variation Orders in Road Construction Projects in Sri Lanka. ISRN Construction Eng. 2013, 1–7. doi:10.1155/2013/381670
Ham, N., Moon, S., Kim, J. H., and Kim, J. J. (2018). Economic Analysis of Design Errors in BIM-Based High Rise Construction Projects: Case Study of Haeundae L Project. J. Construct. Eng. Manag. 144 (6), 1–13. doi:10.1061/(asce)co.1943-7862.0001498
Hassan, A., Hamza, F., Nikhil, M., and Sufyan, S. (2017). A Study in Construction Delays of Residential Structures. Int. Refereed J. Eng. Sci. 6, 42–47.
Hicham, H., Taoufiq, C., and Aziz, S. (2016). “Last Planner System: Implementation in a Moroccan Construction Project,” in Proceedings of 24th Annual Conference of the International Group for Lean Construction, Boston, MA 6, 193–202.
Hickson, B. G., and Ellis, L. A. (2014). Factors Affecting Construction Labor Productivity in Trinidad and Tobago. The J. Assoc. Prof. Eng. Trinidad Tobago. 42 (1), 4–11.
Hossain, M. A., Raiymbekov, D., Nadeem, A., and Kim, J. R. (2019). Delay Causes in Kazakhstan’s Construction Projects and Remedial Measures. Int. J. Constr. Manag.. doi:10.1080/15623599.2019.1647635
Hossain, G. M. S., Huang, W. M. A., and Kaium, W. M. A. (2020). Evaluating Critical success Factors for Adoption Decision of E-Learning Facilities in Bangladesh by Using DEMATEL Approach. Ijeeee 10 (2), 182–204. doi:10.17706/ijeeee.2020.10.2.182-204
Ibironke, O. T., Oladinrin, T. O., Adeniyi, O., and Eboreime, I. V. (2013). Analysis of Non-excusable Delay Factors Influencing Contractors’ Performance in Lagos State, Nigeria. J. Constr. Dev. Cont. 18 (1), 53–72.
Ikechukwu, A. C., Emoh, F. I., and Kelvin, O. A. (2017). Causes and Effects of Cost Overruns in Public Building Construction Projects Delivery, in Imo State, Nigeria. Iosr Jbm 19, 13–20. doi:10.9790/487x-1907021320
Imad, H. U., Akhund, M. A., Ali, T. H., Khoso, A. R., and Siddiqui, F. H. (2018). Time Overrun in Preconstruction Planning Phase of Construction Project. World Acad. Sci. Eng. Technol. Int. J. Civil Environ. Eng. 12, 817–821. doi:10.5281/zenodo.1474483
Jajac, N., Marovi, L., and Hanak, T. (2015). Decision Support for Management of Urban Transport Projects. Gradjevinar 6 (2), 131–141. doi:10.14256/JCE.1160.2014
Jalal, M. P., and Yousefi, E. (2017). An Integrated Expert Model for Delay Management in Construction Projects. KICEM J. Construct. Eng. Proj. Manag., 1–14. doi:10.6106/JCEPM.2017.9.29.001
Jussila, J., and Lähtinen, K. (2019). Effects of Institutional Practices on Delays in Construction - Views of Finnish Homebuilder Families. Housing Stud. 35 (7), 1167–1193. doi:10.1080/02673037.2019.1651831
Kakha, G., Tabasi, S., Jami, M., and Narooei, K. D. (2019). Evaluation of the Impacting Factors on Sustainable Mining Development, Using the Grey-Decision Making Trial and Evaluation Laboratory Approach. Int. J. Eng. 32 (10), 1497–1505. doi:10.5829/IJE.2019.32.10A.20
Karthik, D., and Rao, C. B. K. (2018). The Analysis of Essential Factors Responsible for Loss of Labor Productivity in Building Construction Projects in India. Eng. J. 23 (2), 56–70. doi:10.4186/ej.201923.2.55
Kaul, V. (2014). Excessive Delays in Closeouts Can Be Removed with the Adaptation of Better Practices. Open Access Theses, 1–103.
Kaushik, S., and Somvir, R. (2015). A Method for Research in Library and Information Science. Int. J. Librarian. Admin. 2, 179–185.
Kazaz, A., Ulubeyli, S., and Tuncbilekli, N. A. (2012). Causes of Delays in Construction Projects in Turkey. J. Civil Eng. Manag. 18 (3), 426–435. doi:10.3846/13923730.2012.698913
Keane, P., Sertyesilisik, B., and Ross, A. D. (2010). Variations and Change Orders on Construction Projects. J. Leg. Aff. Dispute Resolut. Eng. Constr. 2 (2), 89–96. doi:10.1061/(asce)la.1943-4170.0000016
Kesavan, M., Gobidan, N., and Dissanayake, P. (2017). Analysis of Factors Contributing Civil Engineering Construction Project Delays in Sri Lankan Building Construction Industries. J. Industr. Eng. Res. 1, 5–11.
Khattri, T., Agarwal, S., Gupta, V., and Pandey, M. (2016). Causes and Effects of Delay in Construction Project. Int. Res. J. Eng. Technol. (Irjet). 3, 564–566.
Khoso, A. R., Khan, J. S., Faiz, R. U., and Akhund, M. A. (2019). Assessment of Change Orders Attributes in Preconstruction and Construction Phase. Civ Eng. J. 5 (3), 616–623. doi:10.28991/cej-2019-03091273
Kirchberger, M. (2018). The Role of the Construction Sector, 146. Helsinki, Finland: United Nation University World Institute for Development Economic Research, 1–17.
Kubba, S. (2012). “Types of Building Contract Agreements,” in Handbook of Green Building Design and Construction. Alexandria, VA: EJCDC, 1–14. doi:10.1016/b978-0-12-385128-4.00014-7
Kumar, A., and Dash, M. K. (2016). “Using DEMATEL to Build Decision Model of Online Reputation Management,” in Fuzzy Optimization and Multi-Criteria Decision Making in Digital Marketing. Hershey, Pennsylvania: IGI Global, 127–146. doi:10.4018/978-1-4666-8808-7.ch006
Larsen, J. K., Shen, G. Q. P., Lindhard, S. M., and Bruce, T. D. (2015). Factors Affecting Schedule Delay, Cost Overrun, and Quality Level in Construction Projects. J. Manag. Eng. 32, 1–29. doi:10.1061/(ASCE)ME.1943-5479.0000391
Lessing, B., Thurnell, D., and Durdyev, S. (2017). Main Factors Causing Delays in Large Construction Projects: Evidence from New Zealand. Jomeino 1 (2), 63–82. doi:10.31039/jomeino.2017.1.2.5
Liu, M., Le, Y., Hu, Y., Xia, B., Skitmore, M., and Gao, X. (2019). System Dynamics Modeling for Construction Management Research: Critical Review and Future Trends. J. Civ. Eng. Manag. 25 (8), 730–741. doi:10.3846/jcem.2019.10518
Love, P. E. D., Edwards, D. J., and Irani, Z. (2008). Forensic Project Management: An Exploratory Examination of the Causal Behavior of Design-Induced Rework. IEEE Trans. Eng. Manage. 55, 234–247. doi:10.1109/tem.2008.919677
Love, P. E. D., Lopez, R., Edwards, D. J., and Goh, Y. M. (2012). Error Begat Error: Design Error Analysis and Prevention in Social Infrastructure Projects. Accid. Anal. Prev. 48, 100–110. doi:10.1016/j.aap.2011.02.027
Love, P. E. D., and Smith, J. (2003). Benchmarking, Benchaction, and Benchlearning: Rework Mitigation in Projects. J. Manage. Eng. 19 (4), 147–159. doi:10.1061/(asce)0742-597x(2003)19:4(147)
Mahamid, I. (2016). Analysis of Rework in Residential Building Projects in Palestine. Jjce 10 (2), 197–208. doi:10.14525/jjce.10.1.3536
Mahamid, I. (2020). Impact of Rework on Material Waste in Building Construction Projects. Int. J. Constr. Manag.. doi:10.1080/15623599.2020.1728607
Malaj, A., and Shuli, I. (2015). Problems and Challenges Facing Today’s Construction Sector in Albania. Acad. J. Interdiscipl. Stud. 4, 572–576. doi:10.5901/ajis.2015.v4n3s1p572
Memon, A. H. (2014). Contractor Perspective on Time Overrun Factors in Malaysian Construction Projects. Int. J. Sci. Environment. Technol. 3, 1184–1192. doi:10.1177/0146167295214010
Maryani, A., Wignjosoebroto, S., and Partiwi, S. G. (2015). A System Dynamics Approach for Modeling Construction Accidents. Proced. Manufacturing 4, 392–401. doi:10.1016/j.promfg.2015.11.055
Memon, A. H., Rahman, I. A., and Aziz, A. A. A. (2012). The Cause Factors of Large Project’s Cost Overrun Survey in the Southern Part of Peninsular Malaysia. Int. J. Real Estate. Stud. 7, 1–15.
Mirshekarlou, B. R. (2012). A Taxonomy for Causes of Changes in Construction. A Thesis to Graduate School of Natural and Applied Sciences of the Middle East Technical University Turkey, 1–149.
Mittal, Y. K., and Paul, V. K. (2018). Identification of Critical Factors for Delay in Metro Rail Projects in India. ijsrtm 6 (1), 30–39. doi:10.18510/ijsrtm.2018.615
Mohammed, K., and Isah, A. D. (2012). Causes of Delay in Nigeria Construction Industry. Interdiscip. J. Contemp. Res. Bus. 4, 785–794.
Moradi, S., Nasirzadeh, F., and Golkhoo, F. (2017). Modelling Labor Productivity in Construction Projects Using Hybrid SD-DES Approach. Scientia Iranica 24 (6), 2752–2761. doi:10.24200/sci.2017.4171
Nahidi, S., Fountas, G., Sarvani, S. P., Sarwar, M. T., and Anastasopoulos, P. (2017). Project Discrepancies in Roadway Construction and Preservation: A Statistical Analysis of Public-Private-Partnership Contract Types in the US. Front. Built. Environ. 3 (15), 1–20. doi:10.3389/fbuil.2017.00015
Najafabadi, E., and Pimplikar, S. S. (2013). The Significant Causes and Effects of Delays in Ghadir 2206 Residential Project. IOSR-JMCE 7 (4), 75–81. doi:10.9790/1684-0747581
Nikumbh, A. R., Pimplikar, S. S., and S.S. Pimplikar, D. (2014). Role of Project Management Consultancy in Construction Project. Iosrjmce 10, 14–19. doi:10.9790/1684-1061419
Ogano, N. O. (2016). A System Dynamics Approach to Managing Project Risks in the Electricity Industry in Sub–saharan Africa. Doctoral Thesis submitted to Graduate School of Technology Management, Faculty of Engineering, Built Environment and Information Technology, University of Pretoria, 1–346.
Ogunlana, S. O., Li, H., and Sukhera, F. A. (2003). System Dynamics Approach to Exploring Performance Enhancement in a Construction Organization. J. Constr. Eng. Manage. 129, 528–536. doi:10.1061/(asce)0733-9364(2003)129:5(528)
Owolabi, J. D., Amusan, L. M., Oloke, C. O., Olusanya, O., Olayeni, T. P., Owolabi, D., et al. (2014). Causes and Effect of Delay on Project Construction Delivery Time. Int. J. Educ. Res. 2 (4), 197–208.
Owusu, P. K., and Aggrey, D. E. G. (2020). Examining the Effect of Project Delays in the Construction Field, A Case Study of Prime Engineering and Service Ghana Limited. Asian J. Appl. Sci. Technol. 4 (3), 129–144. doi:10.38177/ajast.2020.4317
Pawar, A. C., Wagh, S. V., and Bhalerao, N. V. (2016). Factors Causing Delay and Methodology of Ranking for Residential Projects. Int. J. Eng. Res. Technol. 5 (8), 17–28. doi:10.17577/ijertv5is080040
Prasertrungruang, T., and Hadikusumo, B. H. (2009). Study of Factors Influencing the Efficient Management and Downtime Consequences of Highway Construction Equipment in Thailand. J. Constr. Eng. Manage. 135 (1), 2–11. doi:10.1061/(asce)0733-9364(2009)135:1(2)
Rao, G. V. R. S., Silaparasetti, V., and Abbulu, Y. (2016). Occupational Health and Safety Management Vis-À -vis Different Phases of Construction Activities. Int. J. Res. Eng. Technol. 5, 59–67.
Samarah, A., and Bekr, G. A. (2016). Causes of Delay in Public Construction Projects in Jordan. Am. J. Eng. Res. 5, 87–94.
Sambasivan, M., and Soon, Y. W. (2007). Causes and Effects of Delays in Malaysian Construction Industry. Int. J. Project Manage. 25, 517–526. doi:10.1016/j.ijproman.2006.11.007
Sandhyavitri, A. (2019). Stochastic Analyses for Managing Risk of Delay in Duri Oil Construction Projects, Indonesia. Int. J. Constr. Manag.. doi:10.1080/15623599.2019.1644762
SAS (2007). Introduction to SAS. UCLA. Academic Tech. Services, Statistical Consulting Group. Available at: http://www.ats.ucla.edu/stat/sas/notes2.
Seker, S., and Zavadskas, E. K. (2017). Application of Fuzzy DEMATEL Method for Analyzing Occupational Risks on Construction Sites. Sustainability 9, 1–19. doi:10.3390/su9112083
Sepasgozar, S. M. E., Karimi, R., Shirowzhan, S., Mojtahedi, M., Ebrahimzadeh, S., and McCarthy, D. (2019). Delay Causes and Emerging Digital Tools: A Novel Model of Delay Analysis, Including Integrated Project Delivery and PMBOK. Buildings 9 (191), 191–237. doi:10.3390/buildings9090191
Shahsavand, P., Marefat, A., and Parchamijalal, M. (2018). Causes of Delays in Construction Industry and Comparative Delay Analysis Techniques with SCL Protocol. Eng. Construct. Architect. Manag. 25 (2), 1–39. doi:10.1108/ecam-10-2016-0220
Shaik, A. W., Muree, M. R., and Soomro, A. S. (2010). Identification of Critical Delay Factors in Construction, 42. Jamsoro, Pakistan: Sindh University Res. J., 11–14.
Shamsudeen, M., and Obaju, N. B. (2016). Effects of Design Errors on Construction Projects. Int. J. Sci. Eng. Res. 7 (2), 1099–1114.
Shieh, J.-I., Wu, H.-H., and Huang, K.-K. (2010). A DEMATEL Method in Identifying Key Success Factors of Hospital Service Quality. Knowledge-Based Syst. 23, 277–282. doi:10.1016/j.knosys.2010.01.013
Singh, S., Bala, A., Dixit, S., and Varchney, D. (2018). Critical Analysis of Causes of Delay in Residential Construction Projects in India. Int. J. Civil Eng. Technol. 9 (1), 330–345.
Solis, J. L. F. (2007). Towards a Construction Industry Paradigm. College Station: Texas A&M University, 1–35.
Sterman, J. (2000). Business Dynamics: Systems Thinking and Modelling for the Complex World. Boston, MA: McGraw-Hill
Subramani, T., Sruthi, P. S., and Kavitha, M. (2014). Causes of Cost Overrun in Construction. IOSR J. Eng. 4, 1–7.
Suleiman, I. J., and Luvara, V. G. M. (2016). Factors Influencing Change of Design of Building Projects during Construction Stage in Dar-Es-Salaam Tanzania. Int. J. Construct. Eng. Manag. 5 (4), 93–101. doi:10.5923/j.ijcem.20160504.01
Sun, M., and Meng, X. (2009). Taxonomy for Change Causes and Effects in Construction Projects. Int. J. Project Manage. 27, 560–572. doi:10.1016/j.ijproman.2008.10.005
Susanty, A., Sari, D. P., Rinawati, D. I. I., Purwaningsih, R., and Sjawie, F. H. (2019). Policy Making for GSCM Implementation in the Wooden Furniture Industry. Meq 30 (5), 925–944. doi:10.1108/meq-11-2018-0193
Suslov, S., and Katalevsky, D. (2019). Modelling and Simulation Toolset. Evolving Toolbox for Complex Project Management. New York, NY: Taylor & Francis, 417–448.
Sweis, G. J. (2013). Factors Affecting Time Overruns in Public Construction Projects: The Case of Jordan. Int. J. Bus. Manage. 8, 120–129. doi:10.5539/ijbm.v8n23p120
Szafranko, E. (2017). Decision Problems in Management of Construction Projects. IOP Conf. Ser. Mater. Sci. Manage. 251, 1–8. doi:10.1088/1757-899x/251/1/012048
Szafranko, E. (2015). Evaluation of Variant Construction Projects Supported by Expert Opinion System Based on Multi-Criteria Methods. Int. J. New Tech. Sci. Eng. 2 (5), 39–46.
Tafazzoli, M., and Shrestha, P. P. (2017). Investigating Causes of Delay in U.S. Construction Projects. ASC Annu. Int. Conf. Proc. 53, 611–621.
Tahir, M. M., Haron, N. A., Alias, A. H., and Diugwu, I. A. (2019). Causes of Delay and Cost Overrun in Malaysian Construction Industry. Lecture Notes Civ. Eng. 9, 47–57. doi:10.1007/978-981-10-8016-6_5
Toor, S.-U. -R., and Ogunlana, S. (2008). Problems Causing Delays in Major Construction Projects in Thailand. Construction Man. Econ. 26, 395–408. doi:10.1080/01446190801905406
Tsai, S.-B., Huang, C.-Y., Wang, C.-K., Chen, Q., Pan, J., Wang, G., et al. (2016). Using a Mixed Model to Evaluate Job Satisfaction in High-Tech Industries. Plos One 11 (5), e0154071. doi:10.1371/journal.pone.0154071
Vacanas, Y., and Danezis, C. (2018). An Overview of the Risk of Delay in Cyprus Construction Industry. Int. J. Constr. Manag.. doi:10.1080/15623599.2018.1541703
Venkatesh, P. K., and Venkatesan, V. (2017). Delays in Construction Project: A Review of Causes, Need and Scope for Further Research. Malaysia Constr. Res. J. 23 (1), 89–113.
Wang, J., and Yuan, H. (2017). System Dynamics Approach for Investigating the Risk Effects on Schedule Delay in Infrastructure Projects. J. Manag. Eng. 33, 1–13. doi:10.1061/(asce)me.1943-5479.0000472
Wu, H. H., Chen, H. K., and Shieh, J. I. (2010). Evaluating Performance Criteria of Employment Service Outreach Program Personnel by DEMATEL Method. Expert Syst. Appl 37, 219–5223. doi:10.1016/j.eswa.2009.12.068
Yana, A. A. G. A., Rusdhi H.A., H. A., and Wibowo, M. A. (2015). Analysis of Factors Affecting Design Changes in Construction Project with Partial Least Square (PLS). Proced. Eng. 125, 40–45. doi:10.1016/j.proeng.2015.11.007
Yang, J.-B., and Tsai, M.-K. (2011). Computerizing ICBF Method for Schedule Delay Analysis. J. Constr. Eng. Manage. 137, 583–591. doi:10.1061/(asce)co.1943-7862.0000338
Yu-jing, W. (2012). “Application of System Dynamics in Construction Project Planning and Control,” in International Conference on Business Computing and Global Informatization, Shangai, China, October 12–14, 2012, 52–54. doi:10.1109/bcgin.2012.20
Keywords: construction, delay, DEMATEL, preconstruction, post-construction, system dynamics modeling
Citation: Ajayi BO and Chinda T (2022) Impact of Construction Delay-Controlling Parameters on Project Schedule: DEMATEL-System Dynamics Modeling Approach. Front. Built Environ. 8:799314. doi: 10.3389/fbuil.2022.799314
Received: 21 October 2021; Accepted: 17 January 2022;
Published: 10 February 2022.
Edited by:
Samad Sepasgozar, University of New South Wales, AustraliaReviewed by:
Serdar Durdyev, Ara Institute of Canterbury, New ZealandAmir Mahdiyar, University of Science Malaysia, Malaysia
Copyright © 2022 Ajayi and Chinda. This is an open-access article distributed under the terms of the Creative Commons Attribution License (CC BY). The use, distribution or reproduction in other forums is permitted, provided the original author(s) and the copyright owner(s) are credited and that the original publication in this journal is cited, in accordance with accepted academic practice. No use, distribution or reproduction is permitted which does not comply with these terms.
*Correspondence: Babatunde Oluwaseun Ajayi, YmFiYXR1bmRlLm9sdUBkb21lLnR1LmFjLnRo