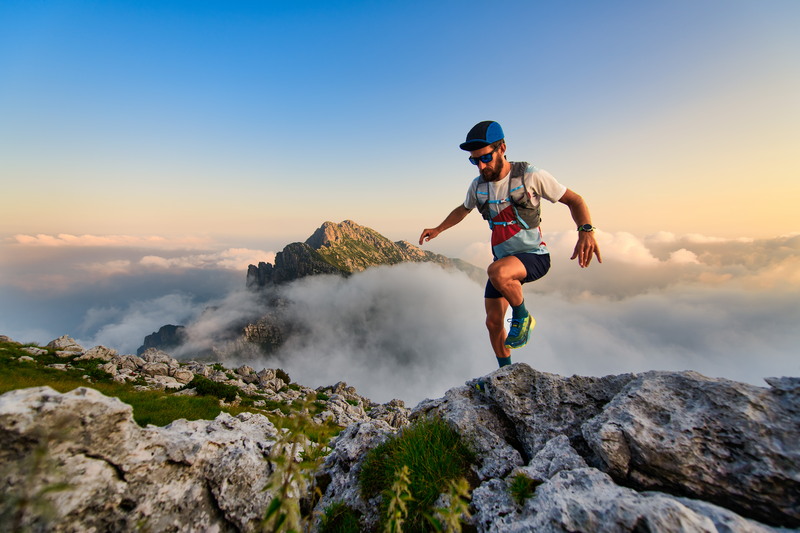
95% of researchers rate our articles as excellent or good
Learn more about the work of our research integrity team to safeguard the quality of each article we publish.
Find out more
ORIGINAL RESEARCH article
Front. Built Environ. , 03 November 2022
Sec. Indoor Environment
Volume 8 - 2022 | https://doi.org/10.3389/fbuil.2022.1062255
This article is part of the Research Topic Design of Efficient and Healthy Buildings View all 6 articles
Furniture emits various VOCs (Volatile Organic Compounds) and formaldehyde (HCHO) into the indoor air. These indoor air pollutants can cause SBS (Sick Building Syndrome), such as sickness, headache, dizziness, nausea, drowsiness, and loss of concentration. This paper aims to provide essential data for improving indoor air quality by identifying the characteristics of the emission of VOCs and HCHO according to the characteristics of raw materials and finishing methods for furniture materials. As a methodology, a small chamber experiment was conducted with eight different test pieces with different base materials compositions and surface finishing methods. VOCs and HCHO were collected and analyzed by GC/MS (Gas Chromatography/Mass Spectrometry) and HPLC (High-Performance Liquid Chromatography). The result showed that the TVOC in the composite material differed according to the retention period of the raw material. HCHO preferentially affects the processing method and the storage period after molding rather than the retention period of raw materials. TVOC emission was lower when the surface finishing method was applied, like paint finish. HCHO emission was getting lower when the adhesive was used during molding. Furniture applied to new houses is installed indoors in the form of finished products (composite materials). It was confirmed that the emission amount from furniture was generally higher than that of the general interior finishing material. Not only using eco-friendly raw materials, securing a specific retention period for raw materials, selecting eco-friendly processing methods, securing a particular retention period after molding, and post-construction management (ventilation and bake-out) should be done through a comprehensive evaluation of furniture.
As environmental pollution in UAE (United Arab Emirates) becomes more serious, interest in breathing air is gradually increasing (Jung and Awad, 2021a; Jung et al., 2021). Since the residents in Dubai, UAE, spend more than 90% of their time indoors due to scorching desert weather and no clear transitions between different seasons, the IAQ (indoor air quality) we breathe is emerging as a critical factor (Awad and Jung, 2021; Jung and Awad, 2021b). Indoors, heat, CO2 (carbon dioxide), dust, and VOCs (Volatile Organic Compounds) emitted from the metabolism and activities of residents, various interior finishing materials, furniture, and cooking utensils are the causes of indoor environmental pollution (Dudareva et al., 2013; Hasager et al., 2021). Moreover, the interior finishing materials composed of complex compounds are increasing (Jeon et al., 2020). The use of various kinds of chemical substances is growing to improve the durability of materials, plastering effect, and convenience of work (Kang et al., 2013). In particular, interior finishing materials and furniture emit various VOCs into the indoor air (Shin and Jo, 2012). These contaminants can cause sickness, headache, dizziness, nausea, drowsiness, and loss of concentration in residents, causing SBS (Sick Building Syndrome), which can seriously deteriorate health (Ghaffarianhoseini et al., 2018). The effects of each toxic substance on the human body are shown in Table 1.
Moreover, due to the harsh natural environment, SBS is increasing faster than in any other country (Araki et al., 2020). As the demands for a high living standard increase, various interior finishing materials have been developed and installed (Lee et al., 2013). Therefore, interior finishing materials used in interior fit-out have been replaced with materials that do not emit harmful substances, such as processed products such as plywood and particle board using adhesives from natural materials, plastics, synthetic resins, and composite materials (Lee et al., 2013; Akadiri, 2015). However, this trend played a significant role in increasing the diversity and usability of interior finishing materials. Still, these products are pollutants that emit harmful substances, such as VOCs, into the air (Liang et al., 2014).
Many previous studies have reported that furniture with complex chemicals had a negative impacts on indoor air quality (Kim et al., 2010a; Liu et al., 2015a; Xiong et al., 2019). To effectively improve indoor air quality this study aims to provide essential data for improving indoor air quality by identifying the characteristics of the emission of VOCs and formaldehyde (HCHO) according to the characteristics of raw materials and finishing methods for furniture materials. The paper aims to identify the characteristics of the emission of hazardous chemicals according to the difference in raw materials used for furniture and understand the characteristics of the emission of harmful chemicals according to the difference in surface finishing methods of composite materials used for furniture.
In this study, the factors for releasing hazardous chemicals should be identified by examining the characteristics of the test samples’ raw materials and surface materials.
It is made by molding and hot-pressing wood fiber as the primary material and bonding it with a synthetic resin adhesive (Simon et al., 2020). It is classified as IB (Insulation Board) with a density of less than 0.35 g/cm3, MDF (Medium Density Fiberboard) with a density of less than 0.35 g/cm3–0.85 g/cm3, and HB (Hard Fiberboard) with a density of 0.85 g/cm3 or more (Schieweck and Bock, 2015). MDF is the most used among them and can be produced from 3.0 to 30 mm thick (Gabriel et al., 2015). MDF has a uniform fiber distribution over the entire thickness and a dense structure, so complex machining can be performed without the face or side rupture. It is used for side molding or surface processing for tabletops, doors, and drawer fronts (Ulker et al., 2021).
PB (Particle Board) is a composite of a cut and crushed piece of wood and a synthetic resin adhesive (Jiang et al., 2017). It refers to a plate-shaped product, formed and hot-pressed, with a density of 0.5 g/cm3–0.8 g/cm3, and is mainly used for the body of furniture (Sun et al., 2020).
The adhesive used for molding HB is a liquid urea resin-based adhesive. A urea resin adhesive is a liquid product mainly composed of synthetic resin made from urea and formaldehyde (HCHO) (Ghani et al., 2018). Melamine and phenols may also be used. As mentioned above, it can be seen that the primary pollutant generation in raw materials is formaldehyde (HCHO) (Younesi-Kordkheili et al., 2016). Therefore, EPA (Environmental Protection Agency) in the United States classifies the above materials according to the amount of formaldehyde (HCHO) emission since 2018 (Wi et al., 2020) (Table 2).
A veneer is a wooden board of uniform thickness (0.2 mm) produced from logs, shards, and incineration ash by rotary cutting and slicing (Jozwiak and Czajka, 2013). There are two types of veneer: dry and wet. In the case of the dry type, it is not harmful as it is a naturally processed veneer, but in the case of the wet type, a large amount of formaldehyde (HCHO) is released by preservative treatment with formalin in an undried state (Cai et al., 2020). In the wet processing method using veneer as the primary material, MDF and PB are mainly used as raw materials. It is used after applying an adhesive to the veneer, heat-treating it, and then polishing and painting the surface. In this experiment, a test sample prepared by wrapping veneer on the raw material of HB was used (Loh et al., 2011). The adhesive applied at this time was a polyurethane-based hot melt adhesive.
LPM makes patterned paper by Gravure printing on paper (Liu and Zhu 2014). This refers to the resin sheet for molding impregnated with melamine resin in this patterned paper. The raw material is an environmentally friendly material using paper and has excellent abrasion resistance and scratch resistance. LPM (Low-Pressure Melamine Impregnated Paper) is known as low-pressure melamine because it is adhesively molded at a lower pressure (10–20 kg/cm2) compared to HPM (High-Pressure Melamine) molding process (Kim et al., 2010b). LPM is thinner than HPM. The resin impregnated in the patterned paper is eluted by high temperature and heat pressure without a separate adhesive and is adhered to by magnetic adhesion. As for the processing method, after impregnating the melamine resin on the patterned paper, it is cured through a curing machine, pressed on the substrate, and adhered to by hot pressing with a hot press for LPM bonding (Chen et al., 2020). In this experiment, LPM-processed specimens on PB were used.
A PVC sheet is made by mixing PVC as a raw material with a stabilizer, plasticizer, and pigment (Franck et al., 2014). It is widely used as an interior finishing material for building interiors because of its easy processability and mass production (Gallego et al., 2013). However, harmful substances such as toxic gas, Dioxin (C4H4O2), are generated during combustion (Zhang et al., 2015). On the other hand, a PP sheet is made of PP as raw material and has a soft texture like paper. It has no harmful ingredients such as plasticizers, heavy metals, and formaldehyde (HCHO) and is widely used as a non-toxic furniture and surface finishing material for doors and windows (Salem et al., 2012). They are usually used as finishing materials for wrapping. After applying the adhesive on the PB or HB, spread the sheet paper, heat it, and cure it. For the sample used in this experiment, a sample piece wrapped on PB using polyurethane-based PVC sheets and EVA hot melt adhesives for PP sheets were used.
UV paint absorbs ultraviolet rays (250–400 nm) from light, becomes reactive, and hardens in a short time, and it has the advantage of improving productivity (Konwar et al., 2012). The general painting process using U.V paint is to grind the base material, apply U.V wood sealer and U.V sanding sealer, and apply D.S. (Direct Shining) painting as a topcoat (Shah and Li, 2019). This coating method can be a high glossy or matte finish. The characteristic of this coating method is that it has a fast curing speed and is not limited by the pot life (Truffier-Boutry et al., 2017).
Water-based paint is paint using water as a solvent (Chang et al., 2011). Generally, it refers to a paint mixed with a water-soluble aqueous solution such as casein, gelatin, and starch. The water-based paint used in this experiment was developed to apply to furniture materials directly (Xiong et al., 2013). By applying water-based paint directly to the raw material and realizing a pattern simultaneously, the product set to block the generation of various harmful substances was used without adhesives to attach vinyl or paper patterns of existing materials (Schieweck and Bock, 2015). The base material is polished in the water-based painting process using the above paints, and the water-based painting to strengthen the hiding power and the U.V painting to strengthen the smoothness are performed sequentially. It performs water-based coating of the base coat, middle coat, and top coat to produce patterns and colors and applies UV paint twice on the top (de Gennaro et al., 2015). For the test pieces used in this experiment, samples finished with UV, and water-based coating on PB was used.
The test piece is a composite material (molding material) in which raw materials, adhesives, and surface materials were applied in the same way as the most commonly used furniture materials used for the interior of the apartment building (Schieweck and Bock, 2015; Kaunelienė et al., 2016; Liang et al., 2021).
In this study, the test pieces are classified into the wrapping type, which wraps the test piece using an adhesive on the raw material, LPM type, which heats the test piece without additional glue; and painting type (Liu et al., 2015b; Zhou et al., 2019). The wrapping type is the test piece TP3, TP4, TP5, and TP6, composed of raw material, adhesive, and surface material. The test pieces TP1 and TP2 are LPM types consisting of raw material and LPM sheets. In addition, the coating type, test pieces TP7 and TP8, has a composition of raw material and paint (Wei et al., 2012; Wang et al., 2021). Table 3 shows the design of the specimen for furniture, the date of manufacture, and the start date of the test.
The composition of each test piece is prepared by applying different surface materials to PB, namely, PVC sheet, LPM, UV coating, water-based coating, and PP sheet (Xiong et al., 2019). In addition, a test piece is prepared by processing a veneer on HB (Table 4). For the test pieces applied in this experiment, raw materials and surface materials with different days after import (retention period) are used (Cheng et al., 2018). In the case of PB, mainly used for furniture, samples were used 30 days after import and 20 days after production for LPM, PP, PVC, UV, and water-based paints (Lin et al., 2009). For HB, 6 months, and for the surface material, veneer, 70 days old raw materials are used (Guo et al., 2000).
To make the composition and retention period of the composite material of each test piece the same as the construction situation of the apartment, it is manufactured from raw materials that have passed the same manufacturing process and storage period at room temperature as the finished furniture product (Yu and Crump, 2003; Kolari et al., 2012).
A small chamber system is used to test the amount of VOCs and HCHO on the test piece to be applied in this experiment, and the configuration is shown in Figure 1.
For VOCs and HCHO measurements, the blank concentration was measured before the input of the sample into the chamber, and the generation amount was calculated on day one and day seven after the input of the sample (Yrieix et al., 2010; Katsoyiannis et al., 2012; Wang et al., 2020a). Experimental conditions were set at a constant temperature and humidity room temperature of 25°C and RH (Relative Humidity) of 50% (Wang et al., 2020b). The input air in the chamber was maintained at a temperature of 25°C and an RH of 50%, and the number of ventilation 0.5 times/h was maintained (Kim et al., 2011). The sample loading factor was 2.2 m2/m3 (the area of the test piece was 0.044 m2), and the TVOC and HCHO emission intensity were calculated according to the EPA IAQ test method (air change rate: 0.5 ± 0.05 per hour) (Kim et al., 2010b; Salem et al., 2012). The emission intensity of each test piece for analysis is the average value of 3 times repeated measurements for each specimen for TP1, TP2, TP5, TP6, TP7, and TP8. TP3 and TP4 were used as the average of the values measured once since the retention period before manufacturing of HB (Hard Fiberboard was 180 days. The emission intensity was calculated as shown in Eqn 1 below.
SERa = Emission amount per unit area of specimen (mg/m2h)Ct = Contaminant concentration in the small chamber at time t (mg/m3)t = Elapsed time after the start of the testA = surface area of the specimen (m2)Q = Flow rate in a small chamber (m3/h)n = Number of ventilation (times/h)V = Volume of a small chamber (m3)L = Sample load factor (m2/m3)q = Flow rate per unit area (m3/m2h)
VOCs collection and analysis were performed according to the EPA IAQ test method. For the collection of VOCs, an adsorption tube filled with Tenax TA 200 mg was connected to a flow sampling pump to collect a total of 3.5 l of air in the chamber at 167 ml/min (An et al., 2011). For the analysis of VOCs target substances contained in standard samples and test pieces, ATD-400 (Perkin Elmer, United Kingdom) is directly connected to the GC column by GC/MS (Gas Chromatography/Mass Spectrometry, HP6890/5973N) was used (Yali et al., 2018). The analysis conditions of GC/MS were HP-1 capillary column. The column flow was 1 ml/min, and the column temperature rate reached 60°C within 5 min, and after that, it was allowed to rise to 260°C by 5°C every 5 min (Suzuki et al., 2014). The ion source temperature of MS was set to 260°C and used for analysis.
HCHO was collected using an LpDNPHS10L cartridge (Supelco Inc., United States) to contain carbonyl compounds (Huang et al., 2013). To remove the interference caused by Ozone (O3), an O3 scrubber was connected in front of the LpDNPH S10L cartridge, and the sample was collected by connecting it to a flow sampling pump (Salem et al., 2012). At this time, a total of 7.0 l of collected air in the chamber was collected at 167 ml/min, and the collected samples were stored in a cool and dark place until extraction (Böhm et al., 2012). For the extraction of the analytical sample, the DNPH-carbonyl derivative formed by reacting with DNPH was extracted with 5 ml of HPLC-grade acetonitrile, and analysis was performed immediately (He et al., 2012). The analysis for HCHO was performed using HPLC (High-Performance Liquid Chromatography, Shimadzu) and fixed at a maximum wavelength of 360 nm.
The difference and characteristics of the emission of hazardous substances due to the difference in raw materials were identified using composite materials manufactured with the same finishing method for raw materials with different HCHO emission grades. Figure 2; Figure 3 show the specimens of PB + LPM type composite material that were molded after holding the raw material for a short period (less than 30 days) and HB + Veneer type composite material after storage for an extended period (more than 30 days). The emission intensity of TVOC and HCHO at 1 day and 7 days in the chamber are shown.
PB (HCHO 0.5 mg/l) and PB (HCHO 1.5 mg/l) with different emission grades of HCHO were used as composite test pieces (TP1 and TP2) subjected to LPM processing. In the case of PB, less than 30 days after the import was used, and in the case of LPM, composite test pieces were prepared with 20 days. The experiment was started 10 days after sample preparation.
As shown in Figure 2, the results confirmed that the difference in the emission of TVOC was demonstrated according to the grade of raw materials. In particular, there is a tendency to increase the amount of release from the 7 days old sample compared to the 1 day old sample. This shows a different aspect from the tendency of toxic substances emitted from general building materials to decrease over time.
The cause is considered to be due to the characteristics of the LPM processing and finishing method. LPM finish requires a cooling period for a certain period (usually 28 days or more) after molding by hot pressing due to the nature of the production. However, this experiment’s cooling time was not provided to secure a relatively equal retention period after molding with other specimens. It was used in the investigation when 10 days had elapsed after molding. It is judged that the emission characteristics of harmful substances continuously increase during the test period.
In other words, in the case of LPM finishing, it was found that securing a sufficient curing period in consideration of the production process’s characteristics after the product’s completion is most important. This means regulating the number of building materials generated and managing procedures based on product processing characteristics is essential.
On the other hand, in the case of HCHO, it was confirmed that the amount of HCHO generated was very low in the case of LPM finishing, and the difference in emission amount between grades was found to be minute.
The difference and characteristics of the emission amount of TVOC and HCHO were evaluated for composite specimens (TP3 and TP4) in which the surface finish of the veneer was wrapped in HB of 0.5 mg/l and 1.5 mg/l grades of HCHO emission. HB was manufactured using long-term storage for 6 months after import and veneer for about 70 days. The experiment was started 3 days after sample preparation.
As shown in Figure 2, TVOC in the HB + Veneer type test piece with a long retention period of the raw material does not offer a significant difference in the amount generated due to the difference between 0.5 mg/l and 1.5 mg/l of HB, and the emission intensity is also low. In the case of using raw materials with a long storage period, it was found that the difference in grades of raw materials did not affect the amount of TVOC generated after molding.
On the other hand, HCHO shows a relatively high emission amount compared to PB + LPM, which is the above-mentioned short-term storage material. The HB (HCHO 0.5 mg/l) test piece showed higher HCHO emission than HB (HCHO 1.5 mg/l). In the case of HB + Veneer test pieces, HB had an extended retention period of more than 6 months after production, so the amount of release was expected to be small. However, rather than the case of PB + LPM 30 days after import, the emission amount is much higher. In other words, the emission characteristics of HCHO are inconsistent with the general decrease trend due to the grade of raw materials or the retention period, unlike the case of TVOC. This may point to the following causes.
First, LPM finishing is a method that adheres to self-adhesive according to the process and does not use an additional adhesive. In the case of veneer, it is judged that it is caused by the difference in the adhesive processing method. In other words, even if raw materials are preserved for a long time and stable release of harmful substances is achieved, the amount of release may be high due to the influence of the adhesive used for product molding. This suggests the importance of using adhesives containing HCHO as the main component in the product processing method.
Second, the higher emission in HB (HCHO 0.5 mg/l) than in HB (HCHO 1.5 mg/l) in the same veneer finish is pointed out as the cause of the possibility of a general error (uncertainty) that does not ensure stability (adhesion.) in the manufacturing process of the molded product.
Third, it can be seen that there is a possibility that the product may have been affected by the retention period after molding. In the case of the PB + LPM composite, it was applied to the test 10 days after sample preparation. However, since the HB + veneer composite was used for the test 3 days after sample preparation, the possibility is also pointed out due to the difference in the amount of natural emission at room temperature.
Using samples prepared by different surface finishing methods for PB (1.5 mg/l of HCHO), which is the same grade of HCHO emission, the difference and characteristics of the release of harmful substances due to the difference in the surface finish are identified.
As shown in Table 2, in the case of LPM (TP2) processing on raw material PB (1.5 mg/l of HCHO), wrapping PVC (TP5) and PP sheet (TP6), UV coating (TP7), water coating (TP8)), the emission characteristics for TVOC and HCHO were analyzed for five composite test pieces, including the case of surface finishing method.
Figure 4 and Figure 5 show the number of hazardous chemical emissions due to the difference in surface finishing methods for PB (1.5 mg/l of HCHO) with a short retention period of raw materials (less than 30 days). The measured value is the emission intensity when 7 days have elapsed after the sample was put into the chamber.
As a result of the experiment, the emission amount of TVOC showed the lowest emission amount in the order of LPM > PVC sheet > PP sheet > water-based coating > UV coating finish. In the case of HCHO, PVC sheet > PP sheet > LPM > water-based coating > UV coating showed the lowest.
In the case of TVOC, there was a clear difference in emission amount between the case of thermal processing, such as PP and PVC wrapping and LPM processing, and the sample produced by the finishing method of painting.
In particular, in the case of water-based coating and UV coating finishing methods, VOCs substances have the property of volatilizing quickly at room temperature. It is judged that the release of hazardous chemicals was carried out in the natural state, such as drying during the manufacturing and transport processes until the test start date.
On the other hand, the amount of release of HCHO was vastly different depending on whether or not adhesive was used in processing the composite material. It was confirmed that there were fewer cases of LPM and painted finish without glue than the case of wrapping PVC and PP sheets using adhesive during processing.
Both TVOC and HCHO showed low emissions in the case of water-based coating and UV coating. In addition, there is a difference in the amount of emission between the water-based coating and UV coating, which can also be considered a reason for the difference in raw materials or process between the above-described test pieces. However, in this experiment, not only this but also the difference in the degree of natural volatilization caused by the difference in the elapsed days from the sample preparation to the start date of the experiment is analyzed as the cause. As shown in Table 4, the test started at 3 days for the water-based coating sample and 16 days for the UV-coated example after sample preparation. It is judged that the UV coating sample exhibited more natural dissipation.
This experiment result is reviewed according to the BIFMA (Business and Institutional Furniture Manufacturing Association) Certification standard, which implements the certification system for building materials in Dubai (Bellingar and Benden, 2015). Currently, BIFMA Certification provides emission standards for furniture materials such as this sample.
In this study, the evaluation was conducted according to the BIFMA Certification criteria considering that furniture materials are also expressed in many surface areas in the same interior space as other general materials.
As shown in Table 5, according to the BIFMA Certification standard, the UV paint sample is of’ Excellent’ grade in the case of the test piece of this composite material. The PVC sheet, LPM, P.P sheet, and water-based coating were judged as “General” grade. In the case of water-based coating, which showed a relatively low emission, it was graded as “General” and showed a very high emission of VOCs overall.
In particular, in the case of HCHO, for all test pieces, the grade was “Good” or “Excellent”, but it was judged as a shallow grade due to the high emission of VOCs.
Also, in the case of BIFMA Certification, the emission standards for wooden office furniture are presented except for wooden furnishings for dormitories and wooden furniture used in schools, libraries, and laboratories.
In the case of a small chamber, the emission amount of HCHO after 7 days is regulated to be 0.125 mg/m2h or less, and the emission amount of VOCs to be 0.4 mg/m2h or less. Again, only UV coating finishing materials were found to meet the emission standards for hazardous chemicals for BIFMA Certification.
In the case of a small chamber, the emission amount of HCHO after 7 days is regulated to be 0.125 mg/m2h or less, and the emission amount of VOCs to be 0.4 mg/m2h or less. Again, only UV coating finishing materials were found to meet the emission standards for hazardous chemicals for BIFMA Certification.
In the current situation where many general materials such as flooring, wallpaper, and ceiling materials are receiving the “Excellent” grade of BIFMA Certification, this study shows a relatively large amount of emission from wood furniture.
In the current construction situation of apartments, it is common for general furniture to be constructed as built-in wardrobes. Built-in furniture is a material that occupies a specific surface area, such as wallpaper and flooring. The fact that it is a pollutant that accounts for a considerable proportion of indoor air pollution compared to other building finishing materials has already been revealed in many previous studies. Therefore, the above result, which dissipates more emissions per unit area than other building materials, indicates that improvement of furniture materials is urgently needed.
Also, in the case of furniture, it is common to use drawers and doors in a closed state in everyday life. It is more exposed to the risk of continuously releasing internal harmful substances over time than other building materials.
In the case of other finishing materials, they are open on the surface, so natural reduction by ventilation is taking place. However, in the case of households, it is judged that it is necessary to induce the behavior of discharging harmful substances by voluntary actions.
Therefore, in the case of furniture, there is an inevitability that low emissions of certain harmful substances should be prioritized before interior construction.
This study aims to identify the characteristics of the number of harmful emissions due to differences in raw materials and surface finishing methods for basic furniture materials.
First, the conclusions based on analyzing the emission characteristics of hazardous chemicals by applying the same finishing method to raw materials PB and HB, which have different HCHO emission grades, are as follows.
It was confirmed that the amount of TVOC generation in the composite material has a difference in the influence of the raw material grade according to the retention period of the raw material. When the retention period of raw materials was less than 30 days, the difference in emission amount for the different raw materials, such as PB + LPM (1.88 mg/m2h) and HB + Adhesive + Veneer (0.05 mg/m2h) was clearly shown. There was no significant difference in the case of raw materials with a long storage period of 6 months or more. The amount of HCHO generated is preferentially affected by the processing method during molding (processing) of the composite material and the storage period after molding rather than the raw materials’ grade and retention periods such as PB + LPM (0.011 mg/m2h) and HB + Adhesive + Veneer (0.033 mg/m2h).
Second, the characteristics of the emission amount according to the difference in surface finishing method for raw materials with the same dissipation grade of HCHO are as follows.
The generation of TVOC is based on a method in which the surface processing method of the composite material is continuously released through a thermal processing process such as PB + PVC (0.998 mg/m2h), PB + LPM (1.847 mg/m2h), PB + Water-based Paint (0.492 mg/m2h), PB + PP (0.965 mg/m2h), and PB + UV Paint (0.001 mg/m2h). However, the surface finishing method that volatilizes for a short period, such as painting finish (0.002 mg/m2h), is advantageous for indoor applications because generation is low. HCHO emission was affected by the construction method related to the use of adhesives during molding in the case of composites.
Third, general building materials such as wallpaper and flooring are classified as eco-friendly by classifying the complete molded product (composite material). However, emission intensity standards for composite materials or finished products are not provided for furniture. Only standards for HCHO emission grade are presented for a limited number of raw materials.
Furniture applied to new houses is installed indoors in the form of finished products (composite materials). In this study, as a result of testing using the composite material having the composition of the finished product, it was confirmed that the emission amount was generally higher than that of the general material standards (TVOC: less than 0.1 mg/m2h, HCHO: less than 0.015 mg/m2h).
Even when other interior finishing materials are applied as eco-friendly materials, it was found that the current kitchen, shoe cabinet, and general furniture have a greater risk of emissions than any other building materials at the time when they are built in the form of built-in wardrobes.
Fourth, eco-friendly raw materials should be used to secure the eco-friendliness of furniture materials as finished products. Furthermore, the entire process, such as securing a specific retention period for raw materials, selecting eco-friendly processing methods, securing a particular retention period after molding, and post-construction management (ventilation and bake-out), should be done through a comprehensive evaluation.
The proposal of an effective material retention period and construction method for each stage requires a process of securing reliability through subsequent future studies with repeated experiments based on the results of this study.
The original contributions presented in the study are included in the article/supplementary material, further inquiries can be directed to the corresponding author.
All authors contributed significantly to this study. CJ and MS identified and secured the example buildings used in the study. The data acquisition system and sensors were designed and installed by CJ and MS. MS was responsible for data collection. Data analysis was performed by CJ. The manuscript was compiled by CJ and reviewed by MS All authors have read and agreed to the published version of the manuscript.
The authors would like to express their gratitude to Ajman University for APC support and to the Healthy and Sustainable Buildings Research Center at Ajman University for providing an excellent research environment.
The authors declare that the research was conducted in the absence of any commercial or financial relationships that could be construed as a potential conflict of interest.
All claims expressed in this article are solely those of the authors and do not necessarily represent those of their affiliated organizations, or those of the publisher, the editors and the reviewers. Any product that may be evaluated in this article, or claim that may be made by its manufacturer, is not guaranteed or endorsed by the publisher.
Akadiri, P. O. (2015). Understanding barriers affecting the selection of sustainable materials in building projects. J. Build. Eng. 4, 86–93. doi:10.1016/j.jobe.2015.08.006
An, J. Y., Kim, S., and Kim, H. J. (2011). Formaldehyde and TVOC emission behavior of laminate flooring by structure of laminate flooring and heating condition. J. Hazard. Mater. 187 (1-3), 44–51. doi:10.1016/j.jhazmat.2010.08.086
Araki, A., Ketema, R. M., Bamai, Y. A., and Kishi, R. (2020). “Aldehydes, volatile organic compounds (VOCs), and health,” in Indoor environmental quality and health risk toward healthier environment for all (Singapore: Springer), 129–158.
Awad, J., and Jung, C. (2021). Evaluating the indoor air quality after renovation at the greens in Dubai, united Arab Emirates. Buildings 11 (8), 353. doi:10.3390/buildings11080353
Bellingar, T. A., and Benden, M. E. (2015). New ANSI/BIFMA standard for testing of educational seating. Ergonomics Des. 23 (2), 23–27. doi:10.1177/1064804613513899
Böhm, M., Salem, M. Z., and Srba, J. (2012). Formaldehyde emission monitoring from a variety of solid wood, plywood, blockboard and flooring products manufactured for building and furnishing materials. J. Hazard. Mater. 221, 68–79. doi:10.1016/j.jhazmat.2012.04.013
Cai, T., Zhang, P., Shen, X., Huang, E., Shen, X., Shi, J., et al. (2020). Synthesis of Pt-loaded NiFe-ldh nanosheets on wood veneer for efficient gaseous formaldehyde degradation. ACS Appl. Mat. Interfaces 12 (33), 37147–37154. doi:10.1021/acsami.0c09016
Chang, Y. M., Hu, W. H., Fang, W. B., Chen, S. S., Chang, C. T., and Ching, H. W. (2011). A study on dynamic volatile organic compound emission characterization of water-based paints. J. Air & Waste Manag. Assoc. 61 (1), 35–45. doi:10.3155/1047-3289.61.1.35
Chen, F., Shen, J., and Xia, X. (2020). Effect of the surface finishing methods on particleboard volatile organic compounds and formaldehyde emission. BioResources 15 (3), 5450–5463. doi:10.15376/biores.15.3.5450-5463
Cheng, K., Hao, W. W., Yi, P., Zhang, Y., and Zhang, J. Y. (2018). Volatile organic compounds emission from Chinese wood furniture coating industry: Activity-based emission factor, speciation profiles, and provincial emission inventory. Aerosol Air Qual. Res. 18 (11), 2813–2825. doi:10.4209/aaqr.2018.02.0044
de Gennaro, G., Loiotile, A. D., Fracchiolla, R., Palmisani, J., Saracino, M. R., and Tutino, M. (2015). Temporal variation of VOC emission from solvent and water based wood stains. Atmos. Environ. 115, 53–61. doi:10.1016/j.atmosenv.2015.04.021
Dudareva, N., Klempien, A., Muhlemann, J. K., and Kaplan, I. (2013). Biosynthesis, function and metabolic engineering of plant volatile organic compounds. New Phytol. 198 (1), 16–32. doi:10.1111/nph.12145
Franck, U., Weller, A., Röder, S. W., Herberth, G., Junge, K. M., Kohajda, T., et al. (2014). Prenatal VOC exposure and redecoration are related to wheezing in early infancy. Environ. Int. 73, 393–401. doi:10.1016/j.envint.2014.08.013
Gabriel, M., Behn, C., and Roffael, E. (2015). Influence of fibre preparation method and wood species on the VOC-emissions from MDF boards. Int. Wood Prod. J. 6 (2), 79–83. doi:10.1179/2042645315y.0000000002
Gallego, E., Roca, F. J., Perales, J. F., and Guardino, X. (2013). Experimental evaluation of VOC removal efficiency of a coconut shell activated carbon filter for indoor air quality enhancement. Build. Environ. 67, 14–25. doi:10.1016/j.buildenv.2013.05.003
Ghaffarianhoseini, A., AlWaer, H., Omrany, H., Ghaffarianhoseini, A., Alalouch, C., Clements-Croome, D., et al. (2018). Sick building syndrome: Are we doing enough? Archit. Sci. Rev. 61 (3), 99–121. doi:10.1080/00038628.2018.1461060
Ghani, A., Ashaari, Z., Bawon, P., and Lee, S. H. (2018). Reducing formaldehyde emission of urea formaldehyde-bonded particleboard by addition of amines as formaldehyde scavenger. Build. Environ. 142, 188–194. doi:10.1016/j.buildenv.2018.06.020
Guo, H., Murray, F., and Wilkinson, S. (2000). Evaluation of total volatile organic compound emissions from adhesives based on chamber tests. J. Air & Waste Manag. Assoc. 50 (2), 199–206. doi:10.1080/10473289.2000.10464006
Hasager, F., Bjerregaard, J. D., Bonomaully, J., Knap, H., Afshari, A., and Johnson, M. S. (2021). “Indoor air quality: Status and standards,” in Air pollution sources, statistics and health effects. London, United Kingdom: IntechOpen Limited, 135–162.
He, Z., Zhang, Y., and Wei, W. (2012). Formaldehyde and VOC emissions at different manufacturing stages of wood-based panels. Build. Environ. 47, 197–204. doi:10.1016/j.buildenv.2011.07.023
Huang, S., Xiong, J., and Zhang, Y. (2013). A rapid and accurate method, ventilated chamber C-history method, of measuring the emission characteristic parameters of formaldehyde/VOCs in building materials. J. Hazard. Mater. 261, 542–549. doi:10.1016/j.jhazmat.2013.08.001
Jeon, J., Park, J. H., Wi, S., Yun, B. Y., Kim, T., and Kim, S. (2020). Field study on the improvement of indoor air quality with toluene adsorption finishing materials in an urban residential apartment. Environ. Pollut. 261, 114137. doi:10.1016/j.envpol.2020.114137
Jiang, C., Li, D., Zhang, P., Li, J., Wang, J., and Yu, J. (2017). Formaldehyde and volatile organic compound (VOC) emissions from particleboard: Identification of odorous compounds and effects of heat treatment. Build. Environ. 117, 118–126. doi:10.1016/j.buildenv.2017.03.004
Jozwiak, M., and Czajka, M. (2013). Investigation on VOC emissions from pine plywood. Annals of Warsaw University of Life Sciences-SGGW. Forestry and Wood Technology. 83, 29–31.
Jung, C., and Awad, J. (2021). Improving the IAQ for learning efficiency with indoor plants in university classrooms in ajman, united Arab Emirates. Buildings 11 (7), 289. doi:10.3390/buildings11070289
Jung, C., Awad, J., Mahmoud, N. S. A., and Salameh, M. (2021). An analysis of indoor environment evaluation for the Springs development in Dubai, UAE. Open House International 46 (4). doi:10.1108/OHI-11-2020-0165
Jung, C., and Awad, J. (2021). The improvement of indoor air quality in residential buildings in Dubai, UAE. Buildings 11 (6), 250. doi:10.3390/buildings11060250
Kang, D. H., Choi, D. H., Yeo, M. S., and Kim, K. W. (2013). Evaluation of VOC emission and sorption characteristics of low-VOC adhesive-bonded building materials. J. adhesion Sci. Technol. 27 (5-6), 683–698. doi:10.1080/01694243.2012.690661
Katsoyiannis, A., Leva, P., Barrero-Moreno, J., and Kotzias, D. (2012). Building materials. VOC emissions, diffusion behaviour and implications from their use. Environ. Pollut. 169, 230–234. doi:10.1016/j.envpol.2012.04.030
Kaunelienė, V., Prasauskas, T., Krugly, E., Stasiulaitienė, I., Čiužas, D., Šeduikytė, L., et al. (2016). Indoor air quality in low energy residential buildings in Lithuania. Build. Environ. 108, 63–72. doi:10.1016/j.buildenv.2016.08.018
Kim, J. A., Kim, S., Kim, H. J., and Kim, Y. S. (2011). Evaluation of formaldehyde and VOCs emission factors from paints in a small chamber: The effects of preconditioning time and coating weight. J. Hazard. Mater. 187 (1-3), 52–57. doi:10.1016/j.jhazmat.2010.10.094
Kim, K. W., Kim, S., Kim, H. J., and Park, J. C. (2010). Formaldehyde and TVOC emission behaviors according to finishing treatment with surface materials using 20 L chamber and FLEC. J. Hazard. Mater. 177 (1-3), 90–94. doi:10.1016/j.jhazmat.2009.09.060
Kim, S., Choi, Y. K., Park, K. W., and Kim, J. T. (2010). Test methods and reduction of organic pollutant compound emissions from wood-based building and furniture materials. Bioresour. Technol. 101 (16), 6562–6568. doi:10.1016/j.biortech.2010.03.059
Kolari, P., Bäck, J., Taipale, R., Ruuskanen, T. M., Kajos, M. K., Rinne, J., et al. (2012). Evaluation of accuracy in measurements of VOC emissions with dynamic chamber system. Atmos. Environ. 62, 344–351. doi:10.1016/j.atmosenv.2012.08.054
Konwar, U., Karak, N., and Jana, T. (2012). Vegetable oil‐based highly branched polyester modified epoxy based low VOC high solid industrial paint. J. Appl. Polym. Sci. 125 (S2), E2–E9. doi:10.1002/app.35370
Lee, E., Allen, A., and Kim, B. (2013). Interior design practitioner motivations for specifying sustainable materials: Applying the theory of planned behavior to residential design. J. Interior Des. 38 (4), 1–16. doi:10.1111/joid.12017
Liang, W., Yang, C., and Yang, X. (2014). Long-term concentrations of volatile organic compounds in a new apartment in Beijing, China. Build. Environ. 82, 693–701. doi:10.1016/j.buildenv.2014.10.016
Liang, X., Sun, X., Lu, Q., Ren, L., Liu, M., Su, Y., et al. (2021). VOC emission inventory of architectural coatings and adhesives for new buildings in China based on investigated and measured data. Atmos. Environ. 245, 118014. doi:10.1016/j.atmosenv.2020.118014
Lin, C. C., Yu, K. P., Zhao, P., and Lee, G. W. M. (2009). Evaluation of impact factors on VOC emissions and concentrations from wooden flooring based on chamber tests. Build. Environ. 44 (3), 525–533. doi:10.1016/j.buildenv.2008.04.015
Liu, X., Mason, M. A., Guo, Z., Krebs, K. A., and Roache, N. F. (2015). Source emission and model evaluation of formaldehyde from composite and solid wood furniture in a full-scale chamber. Atmos. Environ. 122, 561–568. doi:10.1016/j.atmosenv.2015.09.062
Liu, Y., Zhou, X., Wang, D., Song, C., and Liu, J. (2015). A prediction model of VOC partition coefficient in porous building materials based on adsorption potential theory. Build. Environ. 93, 221–233. doi:10.1016/j.buildenv.2015.06.025
Liu, Y., and Zhu, X. (2014). Measurement of formaldehyde and VOCs emissions from wood-based panels with nanomaterial-added melamine-impregnated paper. Constr. Build. Mater. 66, 132–137. doi:10.1016/j.conbuildmat.2014.05.088
Loh, Y. F., Paridah, M. T., Hoong, Y. B., and Yoong, A. C. C. (2011). Effects of treatment with low molecular weight phenol formaldehyde resin on the surface characteristics of oil palm (Elaeis quineensis) stem veneer. Mater. Des. 32 (4), 2277–2283. doi:10.1016/j.matdes.2010.11.014
Salem, M. Z., Böhm, M., Srba, J., and Beránková, J. (2012). Evaluation of formaldehyde emission from different types of wood-based panels and flooring materials using different standard test methods. Build. Environ. 49, 86–96. doi:10.1016/j.buildenv.2011.09.011
Schieweck, A., and Bock, M. C. (2015). Emissions from low-VOC and zero-VOC paints–Valuable alternatives to conventional formulations also for use in sensitive environments? Build. Environ. 85, 243–252. doi:10.1016/j.buildenv.2014.12.001
Shah, K. W., and Li, W. (2019). A review on catalytic nanomaterials for volatile organic compounds VOC removal and their applications for healthy buildings. Nanomaterials 9 (6), 910. doi:10.3390/nano9060910
Shin, S. H., and Jo, W. K. (2012). Volatile organic compound concentrations, emission rates, and source apportionment in newly-built apartments at pre-occupancy stage. Chemosphere 89 (5), 569–578. doi:10.1016/j.chemosphere.2012.05.054
Simon, V., Uitterhaegen, E., Robillard, A., Ballas, S., Véronèse, T., Vilarem, G., et al. (2020). VOC and carbonyl compound emissions of a fiberboard resulting from a coriander biorefinery: Comparison with two commercial wood-based building materials. Environ. Sci. Pollut. Res. 27 (14), 16121–16133. doi:10.1007/s11356-020-08101-y
Sun, S., Zhao, Z., and Shen, J. (2020). Effects of the manufacturing conditions on the VOCs emissions of particleboard. BioResources 15 (1), 1074–1084. doi:10.15376/biores.15.1.1074-1084
Suzuki, M., Akitsu, H., Miyamoto, K., Tohmura, S. I., and Inoue, A. (2014). Effects of time, temperature, and humidity on acetaldehyde emission from wood-based materials. J. Wood Sci. 60 (3), 207–214. doi:10.1007/s10086-014-1397-z
Truffier-Boutry, D., Fiorentino, B., Bartolomei, V., Soulas, R., Sicardy, O., Benayad, A., et al. (2017). Characterization of photocatalytic paints: A relationship between the photocatalytic properties–release of nanoparticles and volatile organic compounds. Environ. Sci. Nano 4 (10), 1998–2009. doi:10.1039/c7en00467b
Ulker, O. C., Ulker, O., and Hiziroglu, S. (2021). Volatile organic compounds (VOCs) emitted from coated furniture units. Coatings 11 (7), 806. doi:10.3390/coatings11070806
Wang, H., Zheng, J., Yang, T., He, Z., Zhang, P., Liu, X., et al. (2020). Predicting the emission characteristics of VOCs in a simulated vehicle cabin environment based on small-scale chamber tests: Parameter determination and validation. Environ. Int. 142, 105817. doi:10.1016/j.envint.2020.105817
Wang, Y., Wang, H., Tan, Y., Liu, J., Wang, K., Ji, W., et al. (2021). Measurement of the key parameters of VOC emissions from wooden furniture, and the impact of temperature. Atmos. Environ. 259, 118510. doi:10.1016/j.atmosenv.2021.118510
Wang, Y., Yang, T., He, Z., Sun, L., Yu, X., Zhao, J., et al. (2020). A general regression method for accurately determining the key parameters of VOC emissions from building materials/furniture in a ventilated chamber. Atmos. Environ. 231, 117527. doi:10.1016/j.atmosenv.2020.117527
Wei, W., Zhang, Y., Xiong, J., and Li, M. (2012). A standard reference for chamber testing of material VOC emissions: Design principle and performance. Atmos. Environ. 47, 381–388. doi:10.1016/j.atmosenv.2011.10.051
Wi, S., Kim, M. G., Myung, S. W., Baik, Y. K., Lee, K. B., Song, H. S., et al. (2020). Evaluation and analysis of volatile organic compounds and formaldehyde emission of building products in accordance with legal standards: A statistical experimental study. J. Hazard. Mater. 393, 122381. doi:10.1016/j.jhazmat.2020.122381
Xiong, J., Chen, F., Sun, L., Yu, X., Zhao, J., Hu, Y., et al. (2019). Characterization of VOC emissions from composite wood furniture: Parameter determination and simplified model. Build. Environ. 161, 106237. doi:10.1016/j.buildenv.2019.106237
Xiong, J., Wang, L., Bai, Y., and Zhang, Y. (2013). Measuring the characteristic parameters of VOC emission from paints. Build. Environ. 66, 65–71. doi:10.1016/j.buildenv.2013.04.025
Yali, S., Jun, S., Shen, X., and Jiankun, Q. (2018). Effect of panel area-volume ratio on TVOC released from decorative particleboards. W&FS. 50 (2), 132–142. doi:10.22382/wfs-2018-015
Younesi-Kordkheili, H., Pizzi, A., and Niyatzade, G. (2016). Reduction of formaldehyde emission from particleboard by phenolated kraft lignin. J. Adhesion 92 (6), 485–497. doi:10.1080/00218464.2015.1046596
Yrieix, C., Dulaurent, A., Laffargue, C., Maupetit, F., Pacary, T., and Uhde, E. (2010). Characterization of VOC and formaldehyde emissions from a wood based panel: Results from an inter-laboratory comparison. Chemosphere 79 (4), 414–419. doi:10.1016/j.chemosphere.2010.01.062
Yu, C. F., and Crump, D. R. (2003). Small chamber tests for measurement of VOC emissions from flooring adhesives. Indoor Built Environ. 12 (5), 299–310. doi:10.1177/142032603035502
Zhang, M., Buekens, A., Jiang, X., and Li, X. (2015). Dioxins and polyvinylchloride in combustion and fires. Waste Manag. Res. 33 (7), 630–643. doi:10.1177/0734242x15590651
Keywords: furniture, formaldehyde (HCHO), VOCs, surface finish methods, retention period
Citation: Sherzad M and Jung C (2022) Evaluating the emission of VOCs and HCHO from furniture based on the surface finish methods and retention periods. Front. Built Environ. 8:1062255. doi: 10.3389/fbuil.2022.1062255
Received: 05 October 2022; Accepted: 25 October 2022;
Published: 03 November 2022.
Edited by:
Roberto Alonso González-Lezcano, CEU San Pablo University, SpainReviewed by:
Susana Hormigos-Jimenez, University of the Balearic Islands, SpainCopyright © 2022 Sherzad and Jung. This is an open-access article distributed under the terms of the Creative Commons Attribution License (CC BY). The use, distribution or reproduction in other forums is permitted, provided the original author(s) and the copyright owner(s) are credited and that the original publication in this journal is cited, in accordance with accepted academic practice. No use, distribution or reproduction is permitted which does not comply with these terms.
*Correspondence: Chuloh Jung, Yy5qdW5nQGFqbWFuLmFjLmFl
Disclaimer: All claims expressed in this article are solely those of the authors and do not necessarily represent those of their affiliated organizations, or those of the publisher, the editors and the reviewers. Any product that may be evaluated in this article or claim that may be made by its manufacturer is not guaranteed or endorsed by the publisher.
Research integrity at Frontiers
Learn more about the work of our research integrity team to safeguard the quality of each article we publish.