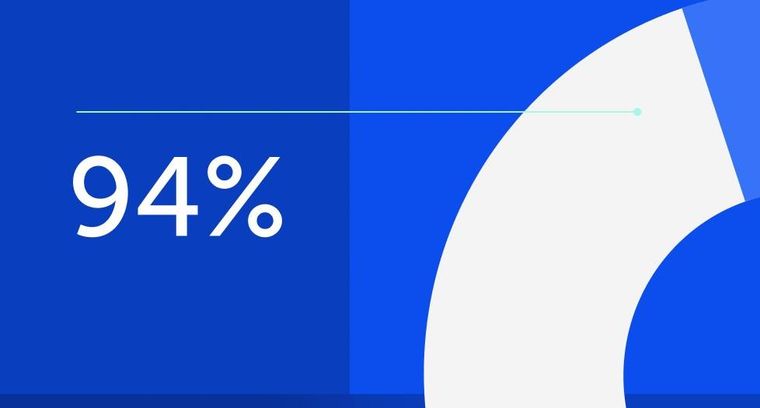
94% of researchers rate our articles as excellent or good
Learn more about the work of our research integrity team to safeguard the quality of each article we publish.
Find out more
ORIGINAL RESEARCH article
Front. Built Environ., 28 May 2021
Sec. Sustainable Design and Construction
Volume 7 - 2021 | https://doi.org/10.3389/fbuil.2021.648220
This article is part of the Research TopicProperties of Smart and Sustainable Building MaterialsView all 5 articles
The purpose of the work reported in this paper is to assess the performance of recycled ultra-high durability concrete (R-UHDC), produced using different fractions of recycled aggregate obtained from crushed ultra-high durability concrete (UHDC), as a substitute for the natural aggregate. Four different recycled ultra-high durability concrete (R-UHDC) mixes were designed and manufactured with a reference mix based on the natural aggregate and three mixes with the natural aggregate replaced using recycled UHDC according to two percentage replacement values (50 and 100%). The effect of environmental degradation of the recycled parent concrete was also addressed, using recycled aggregates subjected to accelerated carbonation (replacement percentage equal to 50%). The work has been conducted in the framework of the activities of the Horizon 2020 ReSHEALience Project in ultra-high durability concrete. One key objective of the project was to formulate the concept and experimentally validate the performance of ultra-high durability concrete for structures and infrastructures exposed to extremely aggressive scenarios. The ReSHEALience consortium has defined UHDC as a “strain-hardening (fiber-reinforced) cementitious material with functionalizing micro- and nano-scale constituents especially added to deliver high durability in the cracked state under extremely aggressive exposure conditions.” In this context, the research was conducted to investigate the potential of recycling the UHDC mixes, developed and validated in previous research and employing them as a partial or even total replacement of the natural fine aggregate in the production of new UHDC. This supports the cradle-to-cradle approach in life cycle engineering applications. The research confirmed the effective regeneration of new UHDC based on the recycled aggregate obtained from crushed UHDC, attaining the required rheological characteristics, mechanical properties (compressive strength, flexural strength, and toughness), and durability performance (chloride penetration resistance, chloride migration, water capillary suction, and resistivity). This work is intended as the first step toward the sustainability assessment of the end of life of UHDC materials and structures and the potential of recycled UHDC for new structures and retrofit structural applications.
The construction industry accounts for about 6% of the world GDP (and up to 8% in developing countries) and generates a total revenue of about 10 trillion USD with 3.6 trillion USD added value (Ferrara, 2019). The construction sector employs directly 100 million people worldwide and has an enormous societal impact. The sector is responsible for contributing, through innovation-led growth, to build up a carbon-neutral society and economy, as is also presented in the intended goals of the European Commission.
The construction industry is currently the largest consumer of raw materials and resources and, as such, also one of the largest contributors to carbon dioxide emissions, mainly coming from the operational life of buildings and structures. It is also one of the largest producers of waste, with construction and demolition waste (CDW) accounting for 30 to 40% of the solid waste produced worldwide (Akhtar and Sarmah, 2018; López Ruiz et al., 2020). One of the main reasons for the high share in both CO2 emissions and waste production can be identified in the need to renovate the building stock in developed countries as well as population growth and urbanization in developing countries (Zhang et al., 2019). Buildings and infrastructures in most cities in Europe as well as in the United States have been (re)built in the 50s and 60s and nowadays turn out to be inadequate, from both an energy point of view (poor insulation, obsolete if not insufficient equipment and installations) and from a structural point of view, mainly due to degradation of materials and reduced structural performance. This is a consequence of durability issues, exacerbated by the change in use as well as worsening exposure conditions, but also due to lack of compliance with evolving structural performance demands, e.g., in seismic zones and/or extreme actions including accidental events, such as impact and blast loadings, as a result of changing societal behavior and expectations. The aforementioned factors, including also the need to upgrade the infrastructure to comply with new (urban) mobility models, imply that a large amount of waste is generated at the end of life of buildings through demolition processes, which may be difficult to dispose of in an efficient and environmentally compliant manner (Alba-Rodríguez et al., 2017).
In view of the above, the construction sector contributes to land degradation, carbon and greenhouse gas emissions, water pollution, high energy consumption, and resource depletion. The environmental impact relates to the extensive industrial chain of the construction sector, with a wide range of related upstream and downstream industries, also involving heavy cross-sectorial industrial linkages. As a direct consequence of this, the largest share in the environmental footprint of construction interventions is represented by construction materials (Zhang et al., 2019), with cement and concrete contributing to the largest share, since concrete, and cement as its main constituent, is the mostly used construction material in the world (Scrivener et al., 2018).
The huge production of solid waste from the construction industry also results in problems related to transportation and storage of CDW before processing and disposal to landfill sites. These problems arise especially because of the presence of different types of materials, including steel, concrete, glass, ceramics, and hazardous materials, including asbestos and mercury whose chemical characteristics present difficulties in handling at landfill sites and in treatment facilities. Concrete contributes through the largest share, representing, for example, 67% of the total CDW in the United States. In the European Union (EU), construction and demolition activities generate 850 million tonnes of construction and demolition waste (CDW) per year, and CDW generation across the EU member states is correlated with their respective national construction sector turnover, population, and gross domestic product (Villoria Sáez and Osmani, 2019).
There is an increased awareness about the need to effectively address the high resource consumption and waste generation through construction and demolition. The Waste Framework Directive 2008/98/EC (WFD) provides a general framework for waste management, setting definitions for member states of the EU (European Parliament, 2008). The WFD introduces a detailed clarification of the “waste hierarchy,” which makes prevention the top waste management priority, followed by preparation for reuse, recycling, and recovery with landfilling being the least desirable option. It also requires that responsible authorities in all European member states establish one or more waste management plans (WMPs) covering their entire geographical territory. Member states are required to implement measures to recover a minimum of 70% (by weight) of non-hazardous CDW (excluding soils) by 2020. In this regard, the study cited above (Villoria Sáez and Osmani, 2019) reveals that Europe as a whole has achieved the target of recovery for the year 2020, including backfilling. However, though 15 member states have already reached the 70% recovery target set in the Waste Framework Directive, there are still 11 member states that need to improve their recovery performance in order to achieve the EU target, with the recovery rate varying from 10 to 95% among the member states.
In this context, the construction sector is actively promoting initiatives to address resource consumption and waste generation through the exploitation of CDW in recycling, which could reduce both waste disposal and also demands on the use of natural resources (Borg et al., 2018).
The demand for the construction aggregate (which topped 45 billion tons worldwide in 2017) is expected to increase up to 66 billion tons, in 5 years. Replacing part or all of the natural aggregate needed to produce concrete with recycled aggregates (RAs) obtained from crushed CDW presents an effective solution that is employed to achieve the goals of the EU Directive 2008/98/EC. The process of transforming CDW into RAs in specialized recycling facilities has been in place for several years, gaining special relevance after the Second World War (Behera et al., 2014; Nováková and Mikulica, 2016). Recycled aggregate concrete (RAC) can be effectively used for both structural and non-structural applications. However, RA use is limited not only to concrete mix design and production but also to other applications such as pavement sub-base, roadway construction, backfilling, and other cement-based composites (Silva et al., 2019). RAs can be divided into recycled concrete aggregate, recycled brick aggregate, and recycled mixed aggregates. Nevertheless, when compared to other recycled aggregate types, the recycled concrete aggregate is the most extensively used RA in construction, with leading organizations developing specifications for its application (Chen et al., 2019).
Standards and legislations on the use of recycled aggregates in concrete are evolving with minimum requirements for its application including minimum percentage of crushed concrete, minimum bulk density, and maximum absorption capacity (Chen et al., 2019; Bai et al., 2020). This implies the development of an integrated approach as a part of the recycling process, including the crushing of demolished concrete, and treatments applied including the removal of contaminants, screening and sorting, and a thorough and “tailored” characterization of the materials in order to transform the waste into a product fit for use. The main difference between natural and recycled aggregates refers to the presence of the mortar attached to the latter, which creates an old interface transition zone (ITZ) intrinsically weaker because of the presence of pores as well as cracks created during the crushing process. As a result, when compared to natural aggregates, RAs have higher water absorption, lower density, lower crushing strength, and lower abrasion resistance. The volume of the attached mortar varies from 20 to 65% of the particle volume, according to the size of the aggregate (Behera et al., 2014). It has been reported that (Bai et al., 2020) the attached mortar content increases with the decrease in the particle size, most likely as a consequence of the crushing process that is more effective in removing the attached mortar when dealing with larger size particles. The absorption capacity of the recycled aggregates increases with the increase in the content of attached mortar.
The properties of RAC are globally affected by the replacement ratio of recycled to natural aggregates, but also by the performance of the parent concrete from which RAs are obtained. The different extents and nature of ITZs are also responsible for the overall performance differences between RAC and conventional concrete produced with natural aggregates.
The presence of porous-adhered mortar with its high porosity and water absorption capacity may result in reduced workability and fresh-state performance for the same w/c ratio. This can be compensated for by pre-soaking the aggregates and/or adjusting the added water to account for the increase in water absorption of the RAs (Behera et al., 2014; Berredjem et al., 2020; Kapoor et al., 2020).
The replacement of natural aggregates with recycled aggregates has also been shown to affect the mechanical performance of RAC, with compressive strength being more sensitive than flexural and tensile strengths. Reported reduction in compression strength can reach up to 30%, for 100% replacement ratio, whereas replacement ratios up to 40% have been reported not to lead to significant reduction in compressive strength. The reduction in mechanical properties can be mitigated through control of the grading of the RAs and high strength of the parent concrete, which, containing larger amounts of un-hydrated cement at the interlayer level, may also lead to improvements in the RAC strength when small proportions of RAs are incorporated (Behera et al., 2014). The influence of the RA content on the modulus of elasticity, drying shrinkage, and creep deformation of RAC has been reported as significantly higher than that on strength properties because of the combined effect of higher porosity of the ITZ, higher paste, and mortar content due to the attached mortar and lower stiffness and strength of the aggregates (Liu et al., 2011). The use of mineral admixtures and supplementary cementitious materials has proven effective in addressing these properties of RAC (Lima et al., 2013; Pedro et al., 2018).
These techniques have been demonstrated as being effective in mitigating the negative effects on durability of RAC, in terms of reduced resistance to chloride penetration, sulfate attack, carbonation penetration, and freeze–thaw cycles, attributed to the reasons outlined above (Zhu et al., 2016; Guo et al., 2018; Ma et al., 2019; Berredjem et al., 2020). The presence of higher CSH gel in RAC, because of higher binder content in the attached mortar, can also contribute to chloride binding (Guo et al., 2018).
Moreover, techniques have been proposed to enhance the removal of the attached mortar (Shaban et al., 2019), which include microwave heating and particle shaping. In the former, the rapid heating of the outer layer results in thermal gradients that cause up to 50% of the attached mortar to be spalled out, whereas through the latter, accelerated RA particles (up to 100 m/s) strike each other, causing the removal of up to 90% of the attached mortar after a few treatment cycles. Techniques to improve the quality of the adhered mortar have also been validated and include pre-soaking of the aggregates in suspensions consisting of cement slurry (proven effective in improving the freeze–thaw resistance), polymer or sodium silicate solutions deemed to increase the density, and also slurries of fly ash, metakaolin, silica fume, ground granulated blast furnace slag, and nano-silica (Luo et al., 2019). Carbonation of RAs has been also investigated as a means to improve the quality of the adhered mortar, through the deposition of the carbonation products in the pores (Ma et al., 2019). In all the aforementioned cases, as witnessed by the results reviewed by Pedro et al. (Pedro et al., 2018), the improvement of the RA properties also resulted in improved durability of the recycled aggregate concrete (RAC), with reference to water and chloride permeability, carbonation resistance, freeze–thaw resistance, and shrinkage cracking potential.
The feasibility of employing recycled aggregates as a replacement of natural aggregates in concrete materials and structures has to address technical aspects as highlighted and also economic and environmental considerations, including additional waste generated through the same recycling process (Zhang et al., 2019; Martínez-Lage et al., 2020).
In general, literature on recycled aggregate concrete refers to the RA originating from normal concrete structural applications. High-strength concrete (HSC) and high-performance concrete (HPC) refer to new technologies with little if any consideration for their exploitation for recycling applications especially for HPC and ultra-high performance concrete (UHPC). This is due, on the one hand, to the still limited share of UHPC as compared to ordinary concrete in the construction industry, though UHPC applications are increasing, e.g., in bridge construction and repair, in China, North America, and several European countries (Shi and Chen, 2018). Moreover, one of the UHPC market–driving concepts is its enhanced durability (so far mainly claimed in the un-cracked state because of the highly compact matrix and seldom proven in cracked structural service scenarios) (Al-Obaidi et al., 2020). This would imply longer structural service life and hence lower availability of UHPC materials and structural elements in a recycling framework. On the other hand, from an engineering point of view, it is worth considering that the expected longer service life of UHPC structures and infrastructures may, at a certain stage during their lifespan, no longer comply with the needs of owners and stakeholders. Urban and infrastructure design concepts are moreover likely to move from an “additional” model toward a “circular” one, which would imply that when the need for a new building/structure/infrastructure facility arises, the old one is dismantled and a new one, which is better fit for purpose, is built in its place rather than adding to or incorporating in the original structure. This is already in some way foreseen in modern structural design codes, which cover in a comprehensive manner the use of cement-based construction materials and end-of-life options for disassembly already at the design stage with a view to facilitate reuse and/or recycling of the original components and materials for new applications in a manner that minimizes the environmental and social impacts. This inspires the challenging option for the assessment of the potential of recycling UHPC, intended as an option for regenerating these materials with no loss in performance, resulting in their full re-use without compromising architectural and structural applications.
In this context, the activity of the Horizon 2020 ReSHEALience Project (GA 760824) is worth analyzing, one of whose goals has been to formulate the concept and experimentally validate the performance of ultra-high durability concrete for structures and infrastructures exposed to extremely aggressive scenarios. It has been hence considered appropriate to address the recycling potential of the conceived, formulated, and validated UHDC mixes in a cradle-to-cradle approach in engineering applications, with the purpose of regenerating the parent UHDC into recycled UHDC.
The ReSHEALience Project consortium has defined UHDC as a “strain-hardening (fiber-reinforced) cementitious material with functionalizing micro- and nano-scale constituents especially added to obtain high durability in the cracked state under extremely aggressive exposure conditions” (Ferrara et al., 2019). The peculiar composition of UHDC mixes, which features high cement and binder contents, the adoption of only fine aggregate fractions, and low water/binder ratios, makes them interesting candidates for recyclability. The likely potential presence of high amounts of anhydrous particles of binding materials in the old ITZ (Zhang et al., 2018; Wang et al., 2019; Qian et al., 2020) may make the same ITZ potentially reactive with interesting impacts on the mechanical and durability performance of the R-UHDC material made by employing the recycled UHDC as an aggregate substituting the natural sand aggregate. At the same time, the mix-design characteristics, which foresee the presence of the sole fine fraction of aggregates and steel fibers, may pose likewise peculiar technological challenges in crushing the parent material and sorting the resulting particles to be recycled.
The research activity reported in this paper was performed by the University of Malta, a partner in the Horizon 2020 ReSHEALience Project responsible for recycling of UHDC, in collaboration with Politecnico di Milano. The UHDC was designed and developed by the University of Malta and applied in the retrofitting and strengthening of the reinforced concrete water tower in the Valletta Grand Harbour. The research focused on the possibility of recycling the specific UHDC mix produced and validated for the aforementioned pilot project application, employing it as a partial and even total replacement of natural sand in the production of new UHDC. Recycled aggregate fraction 0/2 was produced from UHDC through crushing and milling and the separation of fibers using magnetic equipment purposely developed for this research. The crushed material was characterized and blended as the recycled aggregate for the production of new UHDC. The research was intended also to verify the properties of the material in the fresh state, mechanical properties (compressive strength, flexural strength, and toughness), and durability performance (chloride penetration resistance, chloride migration, water capillary suction, and resistivity). Furthermore to the exploitation of crushed UHDC, the research addressed also the effect of the partial replacement of natural aggregates using recycled aggregates subjected to accelerated aging, where the parent recycled UHDC aggregate was exposed to accelerated carbonation.
This work is also intended as the first step toward the sustainability assessment of the recycled UHDC in new and retrofit structural applications, by addressing not only the exploitation of the material as a replacement of natural aggregates but also its potential for partial replacement of cement because of the peculiar characteristics of the ITZs of parent UHDC and assessing its potential foreseeable full-scale applications through an LCA framework. This latter aspect has been regarded as out of scope of this study, also due to lack of comprehensive data considering the pioneering nature of this study.
UHDC samples were used as the parent material for recycling, consisted of the same reference UHDC mix, and were produced 4 months prior to the production of recycled aggregate UHDC (Figure 1), which featured an average compressive strength of 150 MPa.
In order to fragment the UHDC samples and produce the recycled fine aggregates, standard mechanical treatment (SMT) was conducted using a jaw crusher (Pascal Engineering) operating at a power of 750 W. Jaw crushers tend to leave higher levels of cement paste adhered to recycled aggregates. The grain size distribution varies, influencing the compaction efficiency, friction characteristics, and interlocking behavior of the aggregates. A high content of residual cement matrix in the recycled aggregate fraction may result in high porosity and increased water absorption. Repeated crushing was hence required in order to reach the finer size aggregate required to produce UHDC and in order to completely separate the steel fibers from the concrete matrix. After crushing the material, which included the fine recycled crushed aggregate and steel fibers, it was processed using the purposely constructed magnetic separator to remove steel fibers. After separation, the recycled aggregate was sieved on a 2 mm sieve, and all the retained material was put aside and crushed again until a 0–2 mm portion was obtained. All the 0–2 mm material was stored for eventual processing and blending into the new recycled aggregate for use in this research.
The removal of the steel fibers from the crushed concrete presents a challenge in the case of crushed UHDC. A new machine based on a magnetic separator with conveyor belts was constructed for this purpose and used to effectively separate the steel fibers from the concrete matrix (Figure 2). The equipment produced for the purpose of this research serves as a pilot for full-scale UHDC recycling.
A portion of blended recycled aggregate was carbonated using an accelerated carbonation chamber (Borg, 2014) (Figure 3). The recycled aggregate was subjected to carbonation in order to study the effects of carbonation of the parent material as occurring in structures due to natural aging on the performance of R-UHDC. The aggregate carbonation protocol was set such that the aggregate was prepared in containers and spread in aluminum trays over a thickness of 10 mm, to minimize the reactions between the materials and ensure adequate exposure to CO2. The containers were placed in a carbonation chamber at a temperature of 25°C and a relative humidity of 65% (concrete carbonation occurs at a relative humidity in the range 40–70%) and exposed to industrial grade 95% pure CO2 at 100% concentration. During the carbonation process, the temperature in the chamber was kept constant at 25°C, while relative humidity was controlled by means of a water storage tank equipped with a heating device with the relative humidity set at 65 ± 5%. A period of 12 h was set for carbonation at 100% CO2 concentration, preceded by 6.5 h of pre-conditioning in the same chamber. This preconditioning was necessary since the hermetic carbonation chamber with a 192 L volume required a 6.5-h period to reach the total CO2 concentration through a pre-calculated flow rate of approximately 8 ml/s. The CO2 concentration of 100% was chosen in order to accelerate the carbonation within a reasonable limit of time.
FIGURE 3. (A) Schematic representation and (B) actual experimental setup used for accelerated carbonation of the crushed aggregate at the University of Malta (Borg, 2014).
The recycled UHDC aggregates were tested in order to characterize the material through particle size distribution, water absorption, specific gravity, and density. Once the original UHDC was crushed and processed as presented above, a sieve analysis was performed on the crushed material and sorting and blending of the aggregate were performed such that a grain size distribution curve as close as possible to the one of the natural fine aggregate used in the original UHDC was obtained.
The particle size distribution of the natural aggregates used for the preparation of the concrete samples was determined according to standard EN 933-1, and the aggregate samples were sieved on 2 mm, 1 mm, 600 μm, 300 μm, 150 μm, 125 μm, 75 μm, 63 μm, 45 μm, 32 μm, and <32 μm sieves (Figure 4). The particle size distribution of the recycled aggregate obtained after crushing is presented in Figure 5. The PSD curve was compared to that of the natural aggregate used in UHDC, and the recycled UHDC aggregate fractions were blended in order to optimize the particle size distribution and to obtain the desired aggregate grading (labeled Blended RAs and used in this investigation).
FIGURE 5. Grain size distribution of natural and recycled aggregates (as crushed and with modified particle size distribution for the blended recycled aggregate).
Physical properties of both natural and recycled UHDC were determined in order to characterize the material. In particular, the particle density (apparent, saturated surface dry, and dry), the water absorption in accordance with EN 1097-6:2000, the density of the fine recycled aggregate using the density bottle method, and the true density obtained using the helium pycnometer (Quantachrome) were measured. These results obtained for recycled aggregates are presented in Table 1 and are in general similar to and in the same range of the apparent density of the employed natural aggregate, which is equal to 2.66 g/cm3. In detail, it can be observed that the recycled aggregate, including the carbonated aggregate, has a similar density to the natural aggregate. The EN 1097-6 method indicates a lower density for the recycled blended aggregate but higher for the carbonated blended aggregate. The three methods employed yield quite similar results, and the lower values obtained when using the helium pycnometer method can be explained by the intrinsic feature of the method, based on a gas with very low atomic dimensions.
The water absorption of the recycled UHDC aggregates and its evolution with time were determined starting at 0.5 up to 24 h (Figures 6A,B). The water absorption test results confirm the higher absorption of recycled aggregates but also indicate a reduction in water absorption of carbonated aggregates owing to the pore filling by the precipitation of calcium carbonate. This also relates to the higher density determined for the carbonated aggregate. Moreover, higher absorption was noted for the blended aggregate (RA), with particle size distribution similar to that of the natural aggregate. The amount of the absorbed water depends primarily on the abundance and continuity of the pores in the particles, whereas the rate of absorption depends on the size and continuity of these pores, with additional influence of secondary factors, such as the particle size. The particle blending performed to bring the recycled aggregate to a particle size distribution equal to that of the natural aggregate, having increased the 0.3–0.6 mm fraction, may have also led to an increase in particles with a higher volume of attached mortar, which could explain the results obtained.
FIGURE 6. Water absorption of recycled aggregates vs. time: before blending (A) and after blending and carbonation, as compared to natural aggregates (B).
The UHDC mix composition assumed as a reference in this study and presented in Table 2 has been formulated and validated at the University of Malta (Borg, 2019), in the framework of the Horizon 2020 ReSHEALience Project to be employed in the retrofitting of the column support structures of the elevated water tank in the Valletta Grand Harbour, one of the pilot demonstration projects (Ferrara et al., 2019). The mix also represented the starting point for durability enhancing functionalization through synergy between the crystalline admixture and alumina nanoparticles or nanocellulose fibrils and crystals to upgrade the UHPC concept to UHDC (Cuenca et al., 2021).
In order to address the recycling potential of UHDC to regenerate the recycled UHDC (R-UHDC), a large amount of specimens used in the material concept and characterization stage have been used as the parent material to produce the recycled aggregate for the production of R-UHDC mixes with mix designations as presented in Table 2. These mixes were based on different replacement levels of natural aggregates: 0% as a reference (the parent material) and 50% RCA and 100% RCA by weight of aggregate together with 50% carbonated RCA.
The concrete mix proportions were designed to achieve the R-UHDC with a constant water-to-binder ratio for all mixtures (Borg, 2019). The constituents of the mix, namely, the cement, natural sand, and recycled aggregate, were weighed in a dry condition and mixed in a laboratory high-speed pan mixer, with precise constituent measurements and mixed in accordance with the mix protocol, presented in Table 3. The different absorption capacities of natural and recycled aggregates were obviously taken into account to bring aggregates in saturated surface dry conditions. After casting, all specimens prepared to determine mechanical and durability properties were covered with a plastic sheet in order to avoid moisture loss. After that, the specimens were kept at room temperature for 24 h and then demolded and transferred to the curing tank (20±°C) until test dates, covering a period of 120 days for most tests.
The workability of UHDC and R-UHDC was assessed through the slump flow test (the slump flow diameter and the time for the flow to reach a 500 mm spread diameter, t500), with all the mixes targeted to self-compacting consistency in the fresh state. The results, shown in Figure 7, highlight a marginal reduction in the slump flow diameter, whereas an increase in terms of viscosity of the mix is observed through the t500 test attributed to the increase in recycled aggregate and therefore higher roughness and surface area of the particles. This increased flow hindrance is also confirmed by some reduction in homogeneity detected by visual observation of the flown material (Figure 8). Anyway, as a whole, the measured fresh properties indicate that recycled UHDC can be suitably produced, maintaining the desired self-compacting performance, with consistent flow properties where the required flow characteristics were obtained without segregation of the constituents nor bleeding. For the higher recycled vs. natural aggregate replacement ratios, lower workability could be compensated for by using an additional superplasticizer.
The mechanical properties of UHDC and R-UHDC mixes were determined at 7, 28, 56, 90, and 120 days. To determine the hardened concrete density, compressive strength, and flexural strength of concrete, prisms of size 160 × 4 × 40 mm were prepared. For each mix, three specimens were tested in flexure and compression tests were then performed on the (six) broken halves, as per EN 1015-2019; average values and related scattering are reported in the following sections.
As expected, the density decreases generally as the replacement percentage increases, with such a decrease anyway being quite low (on the order of 5%) (Figure 9). This may be due to the high compactness of the parent reference mix as well as to the grain size distribution curve of the aggregate employed. The carbonation of the recycled aggregates, due to the filling of the recycled aggregate pores by means of carbonation products, yielded a density comparable to the one of the reference mix and higher than that of the R-UHDC at the same 50% recycled vs. natural aggregate substitution rate (Fernandezbertos et al., 2004; Zhang et al., 2015; Xuan et al., 2016; Fang et al., 2017; Liang et al., 2019).
The development of the compressive strength with time was measured for all the investigated mixes throughout the test period up to 120 days. The three R-UHDC mixes with 50% RA, 50% carbonated aggregate, and 100% RA showed consistent and comparable results to the reference UHDC (Figure 10). A trend of higher strength for the R-UHDC mixes is consistently observed with an increase in compressive strength with the recycled aggregate in particular even for larger percentage substitution of the natural aggregate. This can be attributed to the increased presence of un-reacted cement particles in the finer portion of the recycled aggregate. This can be justified through the contribution of the presence of un-hydrated binder fraction in the old ITZ of the recycled aggregate fraction to promoting further reactivity, as confirmed through higher strength gains also in the early stages (Figure 10). The effect of the accelerated carbonation of the aggregates does not seem to yield significant differences, especially in the intermediate/longer curing regimes, where the effect of the delayed hydration of the older un-hydrated paste may easily overcome the effect of the higher porosity of the recycled aggregate particles. It is furthermore worth remarking that compressive strength tests performed on specimens containing only recycled aggregates after 120 days of curing in water provided an average compressive strength equal to 193 N/mm2 (with a 6.4 N/mm2 standard deviation on four specimens), thus showing evidence of continuing hydration, though quite moderate, even at quite long curing times.
Replacement of natural sand with recycled UHDC aggregates does not substantially alter the flexural strength capacity and its development over time, this being mainly attributable to the effects of the dispersed fiber reinforcement (Figure 11). The cement hydration effect of the recycled aggregate particles is confirmed in the consistent flexural strength results for R-UHDC over the curing period. Variations are attributable to the random fiber composite during casting that has a considerable impact on flexural strength determination. This can also explain the lower performance of the mixes containing only recycled aggregates, where the higher viscosity may have also hindered the homogeneous dispersion of the fibers in the specimens.
Additional flexural fracture tests were performed at 56 days on 160 × 40 × 40 mm prisms, after having cut an 8 mm deep notch at mid-span to localize the fracture and to be able to measure the crack mouth opening displacement (CMOD) and obtain the complete nominal flexural stress vs. CMOD curve. Tests were performed under a displacement control speed of 0.5 μm/s. The results reported in Figure 12 confirm the possibility of obtaining deflection-hardening UHDC mixes employing recycled UHDC as a partial or even total replacement of natural fine aggregates, highlighting not only the predominant influence of the fibers and of their dispersion in the test specimens on the flexural performance but also the negligible influence of longer curing times on the fiber–matrix bond and hence on the overall mechanical performance of the investigated fiber-reinforced cementitious composites, coherent with the abundant literature on the topic Lo Monte and Ferrara (2020).
In order to determine the durability performance of UHDC and R-UHDC based on recycled aggregates (Singh and Singh, 2018), tests were performed including direct methods for the determination of durability including capillary suction, rapid chloride ion penetration test (RCPT), and non-steady-state chloride migration coefficient, together with indirect methods including vacuum saturation porosity. In addition, the surface resistivity and ultrasonic pulse velocity (UPV) were determined. Tests were conducted, unless otherwise reported, at 28, 56, and 120 days.
The vacuum saturation test was used to measure the permeable porosity of ϕ100 mm × h 50 mm cylindrical samples. The test setup consists of a vacuum desiccator, and the test basically consists in the vacuum saturation of the samples in the dedicated desiccator for 3 h. The specimens were covered with water and allowed under vacuum for an additional hour. The specimens were retained in water for approx. 20 h, and the saturated surface dry mass and the buoyant mass were then determined. Finally, the samples were placed in an oven for a period not less than 48 h at a temperature of 105 ± 5°C, such that the oven dry weight did not vary by more than 0.1% between successive readings taken 24 h apart. As for all saturation techniques, the permeable porosity of concrete is calculated based on the concept of weight gain due to water absorption and weight loss because of buoyancy.
Higher vacuum saturation porosity was registered for R-UHDC compared to the reference UHDC (Figure 13). The increase with respect to the reference mix upon increasing replacement of natural aggregates with recycled ones is more prominent, especially when moving from 50 to 100% replacement ratios, most likely also due to the reduced performance in the fresh state that may have hindered the compactness of the specimens as cast. It is worth remarking that, due to the anyway self-compacting characteristics of the mixes, specimens were not vibrated. A moderate reduction in the open porosity is observed upon continued curing, somewhat higher for the mixes containing higher percentage of recycled aggregates, as a further confirmation of the delayed hydraulic activity that the paste layers attached to the natural sand particles may still possess. The results for the mix with 50% replacement with carbonated recycled aggregates seem to contradict this trend, though it lies within the experimental range. The porosity at 120 days confirms the trend of decreasing porosity with time for all mixes, leveling off the difference for the R-UHDC when compared to the reference mix.
Sorptivity tests were performed at different aging times on prismatic beam specimens as per EN 13057 (EN 13057, 2002). The 160 × 40 × 40 mm3 prism specimens employed for these tests were first oven-dried at 40°C until constant mass and then kept in the lab (25°C and 60% RH) for 24 h to reach an equilibrium with the test environment before performing the sorptivity tests. For this purpose, the lateral surface of the prisms was sealed up to 20 mm depth with a silicon layer and the specimens were put in a water basin resting on two edge supports, in such a way that a 5 mm head over the bottom-exposed surface of the prism was always maintained. The water uptake was then measured, by weighing the specimens, at intervals over a 24 h period and by plotting the water gain vs. the square root of time. The sorption coefficient was calculated as the slope of the stable part of the curve, expressed in [kg/(m2 h0.5)].
A low capillary sorption was noted for all samples with recycled aggregates, with a clear decrease with aging time (Figure 14). A similar trend as for the porosity is noted: the sorptivity coefficient shows scant variation for the mix with 50% replacement of recycled aggregate and a slight increase for the mix with 100% replacement, whereas the specimens made with the mix containing 50% carbonated recycled aggregates featured an increase in the capillary water absorption at 56 days, differences being leveled off upon longer curing. The results are coherent with the general trend of higher porosity being reported, which is associated with more and more interconnected capillary pores and the higher water absorption of recycled aggregates (see also the correlation between the two indicators reported in Figure 15).
The concrete electrical resistivity has been determined for cylindrical samples with reference to AASHTO TP 95-11 (AASHTO TP 95, 2014). This test method, meant to provide a rapid indication of their resistance to the penetration of chloride ions, has a distinct advantage in that it is rapid and easy to perform, with the measurements being conducted on the surface of the cylindrical sample. In the case of mixes with such a high fiber content as the ones herein investigated, the correlation with chloride penetration resistance could be questioned, whereas the method may still be considered useful as an indicator of the quality and homogeneity of the cast specimens. When the information is transferred to real scale casting, it would relate to good surface quality as an indirect indicator of potential durability as well as surface quality. Besides measurements at 28 and 56 days, long-term performance was measured by performing the tests at 300 days (longer testing age was due to restrictions incurred in the meantime due to the COVID-19 pandemic).
The measured values of the surface resistivity (Figure 16) allow for the classification of the mixes, depending on whether the values at 28, 56, or 300 days are considered as featuring low (21–37 kΩcm), very low (37–254 kΩcm), or negligible (> 254 Ωcm) susceptibility to chloride penetration. This confirms the material performance, due to the peculiar mix composition and through prolonged hydration of the cement, further enhanced in the case of the mixes with recycled aggregates through the hydraulic activity of the paste layer surrounding the recycled aggregate particles.
While the mix with carbonated recycled aggregates still presented a minor exception at 28 days, the possibility of maintaining the same high durability characteristics of the parent mix upon replacing natural aggregates with recycled ones obtained by crushing the same parent material is confirmed. Moreover, while test results at 28 and 56 days do not show significant differences between the reference mix and the mixes based on recycled aggregates, long-term test data confirm the same trend reported above with reference to a slight increase in porosity for R-UHDC when compared to the reference mix, likely due as above to higher viscosity in the fresh state that could have hindered homogenous compaction and dispersion of the constituents.
The ultrasonic pulse velocity (UPV) test relies on an ultrasonic pulse with 50-kHz frequency transmitted from an electro-acoustic transducer (P wave). The UPV test results, which are numerically coherent with what is expected and reported in the literature for UHPC materials with the measured strength performance, confirm the trend already noted for vacuum saturation permeable porosity, sorption coefficient, and hardened concrete density results as referring to the relative performance of different mixes (Figure 17). They also highlight once again the possibility of obtaining, even when integrally replacing natural aggregates with recycled ones, the concrete with a performance as high as the reference one.
The RCPT test was conducted on all mixtures at the ages of 28, 56, and 120 days, according to the procedure described in ASTM C1202 (2012). The results, presented in terms of charge in coulombs for the different testing ages, in Figure 18 indicate a quite significant improvement with time in the performance of the recycled UHDC samples when compared to the reference mix. As a matter of fact, ASTM C1202 indicates that a value of charge between 100 and 1,000 coulombs reflects a “very low” chloride ion penetration. The mix with carbonated recycled aggregates, whose resistance to chloride ingress at 56 days is higher, upon longer aging features performances absolutely comparable with other mixes containing recycled aggregates. A continued trend of lower charge is observed at 120 days for all mixes, in particular for the R-UHDC mixes.
Chloride migration tests were performed according to the NordTest method NT Build 492 (1999). In these tests, cylindrical samples of ϕ100 mm × 50 mm thickness were analyzed at different aging times; 28, 56, and 120 days. At the end of the test, the chloride penetration depth was measured with a 0.1 M silver nitrate solution sprayed on the split halves of the cylinder specimens and results were elaborated to calculate the non-steady-state chloride migration coefficient (Figure 19). The good performance of the mixes with recycled aggregates as compared to the reference one was confirmed, since in all cases the investigated mixes featured values of this durability indicator corresponding to excellent durability in the un-cracked state. The chloride ion penetration front indicated a penetration of chloride ions during the test limited to a few millimeters in all cases, in most cases barely visible, actually requiring a microscope to be able to detect and determine it (Figure 20). The microscope images in Figure 20 also show that the fibers immediately close to the exposed surface were severely corroded but that the effect of chloride penetration during the test is limited only to the surface and along the fiber with neither penetration nor corrosion of fibers observed beyond the surface layer, further corroborating very recent literature findings (Marcos Meson et al., 2017).
FIGURE 20. Chloride migration coefficient test indicating the chloride penetration depths in different representative samples from each mix [scale bar: 1 mm divisions with 0.5 mm sub-divisions].
In general, both the chloride penetration results and the chloride migration coefficient results obtained indicate good durability performance of R-UHDC when compared to those obtained for the reference UHDC mix, with clear improved performance over time, further supporting the potential of recycling UHPC/UHDC materials for own self-regeneration with no loss of performance.
A pointwise correlation of the calculated values of the apparent chloride diffusion coefficient vs. the measured porosity would not yield a clear relationship. It is anyway worth remarking that the aforementioned values, all below 10−12 m2/s, clearly denote a very high durability of the produced and investigated materials, comparable to the best high-performance and ultra-high performance concrete so far investigated and reported in the literature (Djerbi et al., 2008).
The effects and contribution of the possible un-hydrated cementitious material in the recycled aggregates employed in R-UHDC mixes were assessed through TGA/DTA using Mettler Toledo TGA/DSC 1. Mass loss calculations and the integration of DTG and heat flux peaks were carried out. Up to 400°C, the loss may be attributed to the expelled capillary water and interlayer water in concrete constituents. Desorption of chemically bound water from portlandite (C-H) takes place in the range of 400–500°C, which significantly affects the mass, followed by de-carbonation above 600°C. The higher the loss in water content bound in Ca(OH)2, the coarser the pore structure and the loss in compressive strength, with the increase in permeability of the specimen.
A similar response for UHDC and recycled UHDC was observed as indicated in Figure 21, but with higher mass loss in the case of all R-UHDC samples and especially for the R-UHDC with 100% replacement rate as indicated in Figure 21. This corroborates the assumption above, recalled to explain the somewhat better gain in performance with time of mixes containing recycled aggregates, obtained from the parent UHDC mixes. The samples incorporating 50% carbonated recycled aggregates show high peak in the presence of the decomposition of the carbonate phases, highlighting the effectiveness of the accelerated carbonation process. It is furthermore worth highlighting that all the samples containing recycled aggregates feature a higher peak in correspondence with the temperature of the carbonate phase decomposition. This can be, once again, rightly attributed to the presence of binder materials attached to the sand particles in the recycled aggregate share, which could have undergone some natural carbonation even during the four-month open-air exposure in which they were left in the lab before the crushing and recycling process started.
The possibility of recycling ultra-high performance/ultra-high durability concrete has been assessed, employing it as a partial or even total replacement of natural aggregates (sand) to produce a material featuring the same mechanical performance and durability characteristics of the parent material. To the authors’ knowledge, the information about recycled UHPC is still scantly available in the literature due to the relative novelty of this broad category of advanced cementitious composites, mainly with reference to their full-scale structural applications, which still have not reached the end of their intended service life, and therefore, the case of their disposal and re-use has not yet been presented. The topic has been herein addressed, as a part of the wider activity of the ReSHEALience Project, funded by the European Commission in the framework of the Horizon 2020 research and innovation programme (GA 760824). The project is thoroughly validating, also through six full-scale pilots, the use of ultra-high durability concrete, meant as a “strain-hardening (fiber-reinforced) cementitious material with functionalizing micro- and nano-scale constituents especially added to obtain high durability in the cracked state under extremely aggressive exposure conditions.”
In a cradle-to-cradle approach to the intended engineering applications and with the purpose of regenerating the same parent UHDC, the present study has clearly and constantly verified the required level of mechanical performance (compressive strength, flexural strength, and toughness) and durability performance (chloride penetration resistance and water capillary uptake) of selected UHDC mix compositions.
The possibility of replacing, even totally, the natural sand with the crushed recycled parent material has been confirmed with no loss in both mechanical and durability performance, even presenting possible improvements, thanks to the positive effect of the delayed hydraulic activity of the cement/binder paste layer surrounding the original natural sand particles. The effects of aging of the parent material before its crushing and recycling has also been investigated through accelerated carbonation of the recycled aggregate. While the “maintenance” of the mechanical performance, in terms of both compressive and flexural strengths, has been confirmed, irrespective of the state of the recycled aggregates (carbonated or non-carbonated), the values obtained for durability indicators in mixes with recycled carbonated aggregates confirm a trend of improved performance.
In view of the improved performance of UHDC based on recycled UHDC as the aggregate for part or full substitution of the aggregate, a relevant development of the study would be the possible exploitation of the recycled sand as a partial replacement of the cement/binder content, thus contributing to further enhancing the environmental impact of this broad category of cement-based construction materials, which is otherwise characterized by a high cement and binder content in their mix composition. This would also pave the way toward a rational and solid assessment of the environmental and economic benefits of the proposed technology, which has to be performed through a comprehensive LCA/LCC procedure, for which available information is anyway still not absolutely sufficient and would require further focused effort from the different actors of the whole value chain of the concrete science, technology, and construction sector.
The original contributions presented in the study are included in the article/Supplementary Material, and further inquiries can be directed to the corresponding authors.
LF and RB procured funds, defined the concept of experimental plan, analyzed the data, and wrote and revised the text. RB, EC, MN, FS and RG performed experimental tests and contributed to text writing and revision and data processing.
The authors declare that the research was conducted in the absence of any commercial or financial relationships that could be construed as a potential conflict of interest.
The research activity reported in this paper has been performed in the framework of the ReSHEALience Project (Rethinking coastal defence and Green-Energy Service infrastructures through enHancEd-durAbiLIty high-performance cement-based materials) that has received funding from the European Union’s Horizon 2020 research and innovation programme under Grant Agreement No. 760824. The information and views set out in this publication do not necessarily reflect the official opinion of the European Commission.
AASHTO TP 95 (2014). Standard Method of Test for Surface Resistivity Indication of Concrete’s Ability to Resist Chloride Ion Penetration
Akhtar, A., and Sarmah, A. K. (2018). Construction and Demolition Waste Generation and Properties of Recycled Aggregate concrete: A Global Perspective. J. Clean. Prod. 186, 262–281. doi:10.1016/j.jclepro.2018.03.085
Al-Obaidi, S., Bamonte, P., Luchini, M., Mazzantini, I., and Ferrara, L. (2020). Durability-Based Design of Structures Made with Ultra-high-Performance/Ultra-high-durability Concrete in Extremely Aggressive Scenarios: Application to a Geothermal Water Basin Case Study. Infrastructures 5 (11), 102–144. doi:10.3390/infrastructures5110102
Alba-Rodríguez, M. D., Martínez-Rocamora, A., González-Vallejo, P., Ferreira-Sánchez, A., and Marrero, M. (2017). Building Rehabilitation versus Demolition and New Construction: Economic and Environmental Assessment. Environ. Impact Assess. Rev. 66, 115–126. doi:10.1016/j.eiar.2017.06.002
ASTM C1202 (2012). Standard Test Method for Electrical Indication of Concrete’s Ability to Resist Chloride Ion Penetration
Bai, G., Zhu, C., Liu, C., and Liu, B. (2020). An Evaluation of the Recycled Aggregate Characteristics and the Recycled Aggregate concrete Mechanical Properties. Construction Building Mater. 240, 117978. doi:10.1016/j.conbuildmat.2019.117978
Behera, M., Bhattacharyya, S. K., Minocha, A. K., Deoliya, R., and Maiti, S. (2014). Recycled Aggregate from C&D Waste & its Use in concrete - A Breakthrough towards Sustainability in Construction Sector: A Review. Construction Building Mater. 68, 501–516. doi:10.1016/j.conbuildmat.2014.07.003
Berredjem, L., Arabi, N., and Molez, L. (2020). Mechanical and Durability Properties of concrete Based on Recycled Coarse and fine Aggregates Produced from Demolished concrete. Construction Building Mater. 246, 118421. doi:10.1016/j.conbuildmat.2020.118421
Borg, R. P. (2019). The Mechanical and Durability Performance of Ultra High Durability Concrete, SBE 19 Malta. in Proceedings. International Conference, 21st – 22nd November 2019, Proceedings. SBE Malta, ISBN 978-99957-1-612-7, ISBN 978-99957-1-613-4 (ebook)
Borg, R. P., Hajek, P., and Fernandez Ordonez, D. (2018). Sustainable Concrete: Materials and Structures. Proceedings of Fib Conference: Sustainable Concrete: Materials and Structures, Materials Science and Engineering. IOP Conf. Ser. 442. doi:10.1088/1757-899X/442/1/011001
Borg, R. P. (2014). Sustainable Concrete; Application of Waste Materials in concrete and Self-Compacting concrete”. UK: Unpublished Thesis, University of Sheffield
Chen, W., Jin, R., Xu, Y., Wanatowski, D., Li, B., Yan, L., et al. (2019). Adopting Recycled Aggregates as Sustainable Construction Materials: A Review of the Scientific Literature. Construction Building Mater. 218, 483–496. doi:10.1016/j.conbuildmat.2019.05.130
Cuenca, E., Mezzena, A., and Ferrara, L. (2021). Synergy between Crystalline Admixtures and Nano-Constituents in Enhancing Autogenous Healing Capacity of Cementitious Composites under Cracking and Healing Cycles in Aggressive Waters. Construction Building Mater. 266, 121447. doi:10.1016/j.conbuildmat.2020.121447
Djerbi, A., Bonnet, S., Khelidj, A., and Baroghel-bouny, V. (2008). Influence of Traversing Crack on Chloride Diffusion into concrete. Cement Concrete Res. 38 (6), 877–883. doi:10.1016/j.cemconres.2007.10.007
EN 13057 (2002). Products and Systems for the protection and Repair of concrete Structures - Test Methods - Determination of Resistance of Capillary Absorption
Fang, X., Xuan, D., and Poon, C. S. (2017). Empirical Modelling of CO2 Uptake by Recycled concrete Aggregates under Accelerated Carbonation Conditions. Mater. Structures 50 (4). doi:10.1617/s11527-017-1066-y
Fernandezbertos, M., Simons, S., Hills, C., and Carey, P. (2004). A Review of Accelerated Carbonation Technology in the Treatment of Cement-Based Materials and Sequestration of CO2. J. Hazard. Mater. 112 (3), 193–205. doi:10.1016/j.jhazmat.2004.04.019
Ferrara, L. (2019). High Performance Fibre Reinforced Cementitious Composites: Six Memos for the XXI century Societal and Economical Challenges of Civil Engineering. Case Stud. Construction Mater. 10, 16. doi:10.1016/j.cscm.2019.e00219
Ferrara, L., Bamonte, P., Falcó, C. S., Animato, F., Pascale, C., Tretjakov, A., et al. (2019). An Overview on H2020 Project “Reshealience”. in Proceeding IABSE Symposium, towards a Resilient Built Environment Risk and Asset Management, Guimarães, Portugal, 184–191.
Guo, H., Shi, C., Guan, X., Zhu, J., Ding, Y., Ling, T.-C., et al. (2018). Durability of Recycled Aggregate concrete - A Review. Cement and Concrete Composites 89, 251–259. doi:10.1016/j.cemconcomp.2018.03.008
Kapoor, K., Singh, S. P., Singh, B., and Singh, P. (2020). Effect of Recycled Aggregates on and Hardened Properties of Self-Compacting concrete. Mater. Today Proc. doi:10.1007/s11356-021-14213-w
Liang, C., Pan, B., Ma, Z., He, Z., and Duan, Z. (2019). Utilization of CO2 Curing to Enhance the Properties of Recycled Aggregate and Prepared concrete: A Review. Cement and Concrete Composites 105, 103446. doi:10.1016/j.cemconcomp.2019.103446
Lima, C., Caggiano, A., Faella, C., Martinelli, E., Pepe, M., and Realfonzo, R. (2013). Physical Properties and Mechanical Behaviour of concrete Made with Recycled Aggregates and Fly Ash. Construction Building Mater. 47, 547–559. doi:10.1016/j.conbuildmat.2013.04.051
Liu, Q., Xiao, J., and Sun, Z. (2011). Experimental Study on the Failure Mechanism of Recycled concrete. Cement Concrete Res. 41 (10), 1050–1057. doi:10.1016/j.cemconres.2011.06.007
Lo Monte, F., and Ferrara, L. (2020). “Tensile Behaviour Identification in Ultra-high Performance Fibre Reinforced Cementitious Composites: Indirect Tension Tests and Back Analysis of Flexural Test Results”. Mater. Structures. 53, 1–12. doi:10.1617/s11527-020-01576-8
López Ruiz, L. A., Roca Ramón, X., and Gassó Domingo, S. (2020). The Circular Economy in the Construction and Demolition Waste Sector – A Review and an Integrative Model Approach. J. Clean. Prod. 248. doi:10.1016/j.jclepro.2019.119238
Luo, Z., Li, W., Tam, V. W. Y., Xiao, J., and Shah, S. P. (2019). Current Progress on Nanotechnology Application in Recycled Aggregate concrete. J. Sustain. Cement-Based Mater. 8 (2), 79–96. doi:10.1080/21650373.2018.1519644
Ma, Z., Tang, Q., Yang, D., and Ba, G. (2019). Durability Studies on the Recycled Aggregate Concrete in China over the Past Decade: A Review. Adv. Civil Eng. 2019, 1-19. 10.1155/2019/4073130
Marcos Meson, V., Michel, A., Solgaard, A. O. S., and Fischer, G. (2017). Corrosion Resistance of Steel Fibre Reinforced concrete – A Literature Review. Cement Concrete Res. 103, 1–20. doi:10.1016/j.cemconres.2017.05.016
Martínez-Lage, I., Vázquez-Burgo, P., and Velay-Lizancos, M. (2020). Sustainability Evaluation of Concretes with Mixed Recycled Aggregate Based on Holistic Approach: Technical, Economic and Environmental Analysis”. Waste Manage. 104, 9–19. doi:10.1016/j.wasman.2019.12.044
Nováková, I., and Mikulica, K. (2016). Properties of Concrete with Partial Replacement of Natural Aggregate by Recycled Concrete Aggregates from Precast Production. Proced. Eng. 151, 360–367. doi:10.1016/j.proeng.2016.07.387
NT Build 492 (1999). Concrete, Mortar and Cement-Based Repair Materials: Chloride Migration Coefficient from Non-steady-state Migration Experiments.
Pedro, D., de Brito, J., and Evangelista, L. (2018). Durability Performance of High-Performance concrete Made with Recycled Aggregates, Fly Ash and Densified Silica Fume. Cement and Concrete Composites 93, 63–74. doi:10.1016/j.cemconcomp.2018.07.002
Qian, D., Yu, R., Shui, Z., Sun, Y., Jiang, C., Zhou, F., et al. (2020). A Novel Development of green Ultra-high Performance concrete (UHPC) Based on Appropriate Application of Recycled Cementitious Material. J. Clean. Prod. 261, 121231. doi:10.1016/j.jclepro.2020.121231
Scrivener, K. L., John, V. M., and Gartner, E. M. (2018). Eco-efficient Cements: Potential Economically Viable Solutions for a low-CO2 Cement-Based Materials Industry. Cement Concrete Res. 114, 2–26. doi:10.1016/j.cemconres.2018.03.015
Shaban, W. M., Yang, J., Su, H., Mo, K. H., Li, L., and Xie, J. (2019). Quality Improvement Techniques for Recycled Concrete Aggregate: A Review. Act 17 (4), 151–167. doi:10.3151/jact.17.151
Shi, C., and Chen, B. (2018). Ultra High Performance Concrete Materials and Structures. Proceedings of the 2nd International Conference, Fuzhou, China (UHPCRILEM pubs. PRO), 129, 832+xxiii
Silva, R. V., de Brito, J., and Dhir, R. K. (2019). Use of Recycled Aggregates Arising from Construction and Demolition Waste in New Construction Applications. J. Clean. Prod. 236, 117629. doi:10.1016/j.jclepro.2019.117629
Singh, N., and Singh, S. P. (2018). Evaluating the Performance of Self Compacting Concretes Made with Recycled Coarse and fine Aggregates Using Non Destructive Testing Techniques. Construction Building Mater. 181, 73–84. doi:10.1016/j.conbuildmat.2018.06.039
Villoria Sáez, P., and Osmani, M. (2019). A Diagnosis of Construction and Demolition Waste Generation and Recovery Practice in the European Union. J. Clean. Prod. 241. doi:10.1016/j.jclepro.2019.118400
Wang, X., Yu, R., Shui, Z., Song, Q., Liu, Z., Bao, M., et al. (2019). Optimized Treatment of Recycled Construction and Demolition Waste in Developing Sustainable Ultra-high Performance concrete. J. Clean. Prod. 221, 805–816. doi:10.1016/j.jclepro.2019.02.201
Xuan, D., Zhan, B., and Poon, C. S. (2016). Assessment of Mechanical Properties of concrete Incorporating Carbonated Recycled concrete Aggregates. Cement and Concrete Composites. 65, 67–74. doi:10.1016/j.cemconcomp.2015.10.018
Zhang, H., Ji, T., Zeng, X., Yang, Z., Lin, X., and Liang, Y. (2018). Mechanical Behavior of Ultra-high Performance concrete (UHPC) Using Recycled fine Aggregate Cured under Different Conditions and the Mechanism Based on Integrated Microstructural Parameters. Construction Building Mater. 192, 489–507. doi:10.1016/j.conbuildmat.2018.10.117
Zhang, J., Shi, C., Li, Y., Pan, X., Poon, C. S., and Xie, Z. (2015). Performance Enhancement of Recycled concrete Aggregates through Carbonation. ASCE J. Mater. Civil Eng. 27 (11). doi:10.1061/(asce)mt.1943-5533.0001296
Zhang, L., Liu, B., Du, J., Liu, C., and Wang, S. (2019). CO2 Emission Linkage Analysis in Global Construction Sectors: Alarming Trends from 1995 to 2009 and Possible Repercussions. J. Clean. Prod. 221, 863–877. doi:10.1016/j.jclepro.2019.02.231
Zhang, Y., Luo, W., Wang, J., Wang, Y., Xu, Y., and Xiao, J. (2019). A Review of Life Cycle Assessment of Recycled Aggregate concrete. Construction Building Mater. 209, 115–125. doi:10.1016/j.conbuildmat.2019.03.078
Keywords: ultra-high performance concrete, ultra-high durability concrete, recycled aggregated concrete, durability, circular economy, ReSHEALience
Citation: Borg RP, Cuenca E, Garofalo R, Schillani F, Nasner ML and Ferrara L (2021) Performance Assessment of Ultra-High Durability Concrete Produced From Recycled Ultra-High Durability Concrete. Front. Built Environ. 7:648220. doi: 10.3389/fbuil.2021.648220
Received: 31 December 2020; Accepted: 04 May 2021;
Published: 28 May 2021.
Edited by:
Prannoy Suraneni, University of Miami, United StatesReviewed by:
Ivan Ignjatović, University of Belgrade, SerbiaCopyright © 2021 Borg, Cuenca, Garofalo, Schillani, Nasner and Ferrara. This is an open-access article distributed under the terms of the Creative Commons Attribution License (CC BY). The use, distribution or reproduction in other forums is permitted, provided the original author(s) and the copyright owner(s) are credited and that the original publication in this journal is cited, in accordance with accepted academic practice. No use, distribution or reproduction is permitted which does not comply with these terms.
*Correspondence: Ruben Paul Borg, cnViZW4ucC5ib3JnQHVtLmVkdS5tdA==; Liberato Ferrara, bGliZXJhdG8uZmVycmFyYUBwb2xpbWkuaXQ=
Disclaimer: All claims expressed in this article are solely those of the authors and do not necessarily represent those of their affiliated organizations, or those of the publisher, the editors and the reviewers. Any product that may be evaluated in this article or claim that may be made by its manufacturer is not guaranteed or endorsed by the publisher.
Research integrity at Frontiers
Learn more about the work of our research integrity team to safeguard the quality of each article we publish.