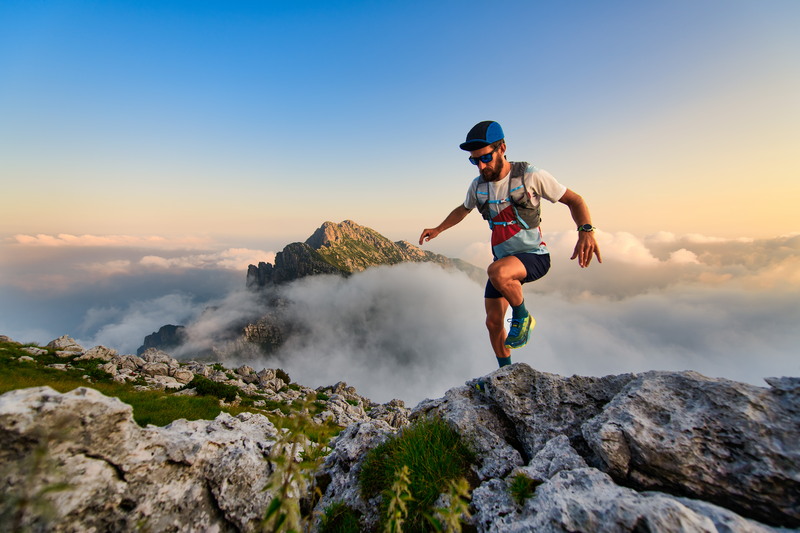
95% of researchers rate our articles as excellent or good
Learn more about the work of our research integrity team to safeguard the quality of each article we publish.
Find out more
ORIGINAL RESEARCH article
Front. Bioeng. Biotechnol.
Sec. Biomaterials
Volume 13 - 2025 | doi: 10.3389/fbioe.2025.1562367
This article is part of the Research Topic Metallic Biomaterials for Medical Applications - Volume II View all 4 articles
The final, formatted version of the article will be published soon.
You have multiple emails registered with Frontiers:
Please enter your email address:
If you already have an account, please login
You don't have a Frontiers account ? You can register here
Metal porous structures are becoming a standard design feature of orthopedic implants such as joint endoprostheses. The benefits of the pores are twofold: 1) help improve the cementless primary stabilization of the implant by increasing osteointegration and 2) reduce the overall stiffness of the metal implant thus minimizing stress-shielding. While the mechanical interaction between porous implants and bone has been extensively investigated via complex numerical and finite element models, scarce is the in-vitro and in-vivo data on the effect of porosity and materials on stress and strain distribution in the implant-bone compound.An integrated numerical and experimental approach was used to investigate the effect of material and porosity on the mechanical interaction in compression between porous metal scaffolds and bovine cortical bone. 18×18×6 mm cuboid samples were cut from fresh-frozen bovine cortical bones. A 9x6x6 cavity was obtained in each sample to allow insertion of CoCrMo porous and full density scaffolds. Digital Image Correlation analysis tracked bone strain during axial compression of the scaffold-bone samples up to bone failure. The experimental strain data were compared to those from finite element analysis (FEA) of the scaffold-bone compound. The effect of scaffold porosity and material - Ti6Al4V and CoCrMo - on bone strain distribution and reactions forces, with respect to full bone samples, was assessed via FEA and an analytical spring-based model of the bone-scaffold compound.The experimental data revealed that the porous scaffold resulted in bone strain closer to that of the intact bone with respect to full density scaffolds. FEA showed that Ti6Al4V scaffolds result in bone strain and reaction forces closer to the those in the intact bone with respect to those in CoCrMo scaffolds. The 1000 µm pores scaffolds resulted significantly more effective in improving reaction forces with respect to the 500 µm pores scaffolds.The present findings confirm that metal porous scaffolds help promote a more uniform distribution to the bone compared to full density implants. Ti6Al4V scaffolds demonstrated a more favorable mechanical interaction compared to CoCrMo. This integrated approach offers valuable insights into the design of orthopedic implants with optimized mechanical and osteointegration properties.
Keywords: porous scaffolds, Bone strain, digital image correlation, Stress shielding, Finite Element Analysis, CoCrMo, Ti6Al4V, Orthopedics
Received: 17 Jan 2025; Accepted: 25 Mar 2025.
Copyright: © 2025 Ramaglia Amadasi, Rogati, Leardini, Liverani and Caravaggi. This is an open-access article distributed under the terms of the Creative Commons Attribution License (CC BY). The use, distribution or reproduction in other forums is permitted, provided the original author(s) or licensor are credited and that the original publication in this journal is cited, in accordance with accepted academic practice. No use, distribution or reproduction is permitted which does not comply with these terms.
* Correspondence:
Giulia Rogati, IRCCS Istituto Ortopedico Rizzoli, Bologna, Italy
Disclaimer: All claims expressed in this article are solely those of the authors and do not necessarily represent those of their affiliated organizations, or those of the publisher, the editors and the reviewers. Any product that may be evaluated in this article or claim that may be made by its manufacturer is not guaranteed or endorsed by the publisher.
Research integrity at Frontiers
Learn more about the work of our research integrity team to safeguard the quality of each article we publish.