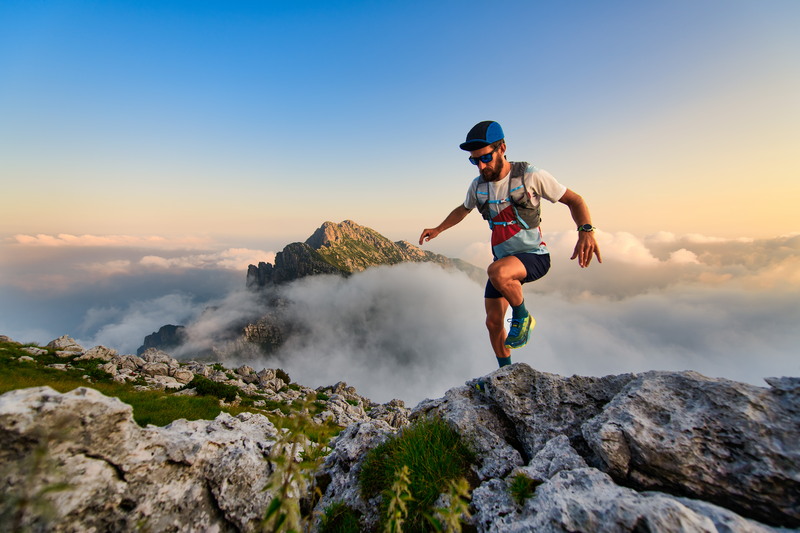
95% of researchers rate our articles as excellent or good
Learn more about the work of our research integrity team to safeguard the quality of each article we publish.
Find out more
TECHNOLOGY AND CODE article
Front. Bioeng. Biotechnol.
Sec. Tissue Engineering and Regenerative Medicine
Volume 13 - 2025 | doi: 10.3389/fbioe.2025.1530126
This article is part of the Research Topic State-of-art of 3D Printing and Bioprinting Technology in various domains of Biomedicine, Tissue Engineering and Regenerative Medicine View all 12 articles
The final, formatted version of the article will be published soon.
You have multiple emails registered with Frontiers:
Please enter your email address:
If you already have an account, please login
You don't have a Frontiers account ? You can register here
Decompressive hemicraniectomy (DC) is a procedure used to treat elevated, therapy-refractory intracranial pressure. Despite the severity of the underlying pathology, selected patients quickly regain mobility and are at risk of secondary injury due to the post-craniotomy defect. A 3D-printed helmet offers a quickly available and safe solution. Up to now, postoperative CT scans have been used as a template for helmet construction. In this study, we present an alternative helmet construction using a non-invasive 3D scan (ArtecLeo, Artec3D), which is used to capture craniometrics data, plan the shape of the helmet, and compare it with routinely performed CT scans. A significant difference in defect displacement between supine scans and standing or sitting scans is evident, which is quantified.We included six patients who underwent decompressive craniectomy due to therapyrefractory elevation of intracranial pressure as a consequence of following pathologies: large intracerebral hemorrhage, large cerebral infarction, sever traumatic brain injury and poor grade subarachnoid hemorrhage. All patients underwent 3-D scan and subsequently, a helmet was created to cover the craniectomy area.A surface heat-map comparison was performed to demonstrate the differences between the data obtained by 3-D scan (lying and sitting position) and CT-scan. Furthermore, the heat-map demonstrates the frontal and posterior surface difference between CT-scan and sitting position. Comparing the lying position 3-D scan and CT-scan, we were able to demonstrate a tissue shift, mainly in cranial and frontal areas.We demonstrated that non-invasive 3D-scan (Artec3D) is a feasible alternative to scan the head of the patients after DHC in order to construct a 3D-printed Helm. According to the heat-map analysis, it seems to be more reliable data assessment method in independently moving patients.
Keywords: 3D printing, Additive manufacturing, Custom medical devices, Neurosurgery, 3D imaging
Received: 18 Nov 2024; Accepted: 18 Mar 2025.
Copyright: © 2025 Kropla, Wach, Winkler, Grunert, Güresir and Vychopen. This is an open-access article distributed under the terms of the Creative Commons Attribution License (CC BY). The use, distribution or reproduction in other forums is permitted, provided the original author(s) or licensor are credited and that the original publication in this journal is cited, in accordance with accepted academic practice. No use, distribution or reproduction is permitted which does not comply with these terms.
* Correspondence:
Fabian Kropla, Department for Neurosurgery, University Hospital Leipzig, Leipzig, 04103, Lower Saxony, Germany
Disclaimer: All claims expressed in this article are solely those of the authors and do not necessarily represent those of their affiliated organizations, or those of the publisher, the editors and the reviewers. Any product that may be evaluated in this article or claim that may be made by its manufacturer is not guaranteed or endorsed by the publisher.
Research integrity at Frontiers
Learn more about the work of our research integrity team to safeguard the quality of each article we publish.