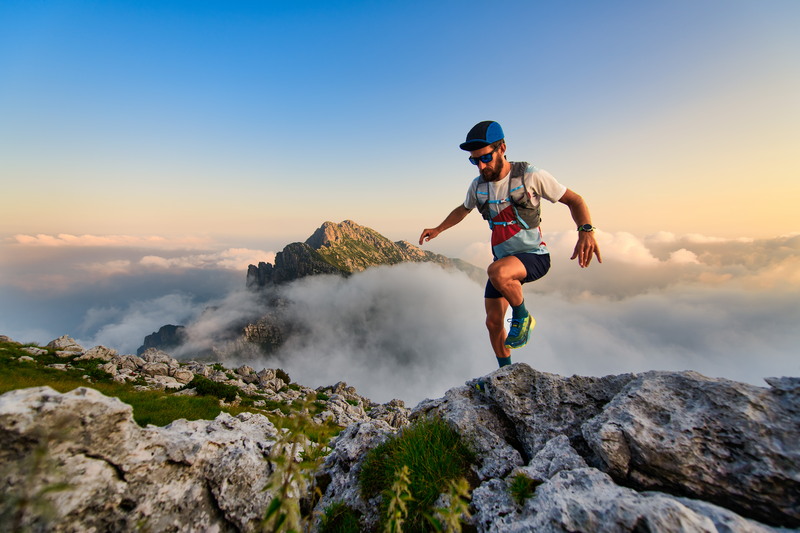
95% of researchers rate our articles as excellent or good
Learn more about the work of our research integrity team to safeguard the quality of each article we publish.
Find out more
ORIGINAL RESEARCH article
Front. Bioeng. Biotechnol.
Sec. Tissue Engineering and Regenerative Medicine
Volume 13 - 2025 | doi: 10.3389/fbioe.2025.1526873
This article is part of the Research Topic Translational development of tailored implants based on new processing approaches and surface modifications for tissue regeneration View all 3 articles
The final, formatted version of the article will be published soon.
You have multiple emails registered with Frontiers:
Please enter your email address:
If you already have an account, please login
You don't have a Frontiers account ? You can register here
In the field of biomedical implants, additively manufactured titanium alloys, particularly Ti-6Al-4V, hold significant potential due to their biocompatibility and mechanical properties. This study focuses on the characterization and modeling of additively manufactured Ti-6Al-4V alloy for dental and maxillofacial implants, emphasizing fatigue behavior, surface modification, and their combined effects on cyto-and osseocompatibility. Experimental methods, including tensile, compression, and fatigue testing, were applied alongside in-silico simulations to assess the long-term mechanical performance of the material. Surface properties were further modified through sandblasting and coating techniques to enhance cell adhesion and proliferation. By using in-vitro methods, the cytocompatibility of the coatings and materials was examined followed by in-vivo tests to determine osseocompatibility. Results demonstrated that appropriate surface roughness and modifications are essential in optimizing osseointegration, while the layer-by-layer additive manufacturing process influenced the fatigue life and stability. These findings contribute to the development of patient-specific implants, optimizing both mechanical integrity and biological integration for enhanced clinical outcomes. This work summarizes the investigations on additively manufactured Ti-6Al-4V alloy of the research unit 5250 "Mechanism-based characterization and modeling of permanent and bioresorbable implants with tailored functionality based on innovative in vivo, in vitro and in silico methods" funded by the Germany Research Foundation (DFG).
Keywords: Additive manufacturing, Ti-6Al-4V alloy, Osseointegration, Dental Implants, Surface modification, Fatigue behavior, Finite element method
Received: 12 Nov 2024; Accepted: 24 Feb 2025.
Copyright: © 2025 Kök, Andreeva, Stammkötter, Reinholdt, Akbas, Jahn, Gamon, Fuest, Teschke, Schäfer, Michael, Koch, Jung, Barbeck, Greuling, Smeets, Hermsdrof, Krastev, Junker, Stiesch and Walther. This is an open-access article distributed under the terms of the Creative Commons Attribution License (CC BY). The use, distribution or reproduction in other forums is permitted, provided the original author(s) or licensor are credited and that the original publication in this journal is cited, in accordance with accepted academic practice. No use, distribution or reproduction is permitted which does not comply with these terms.
* Correspondence:
Hüray Ilayda Kök, Leibniz University Hannover, Hanover, Germany
Disclaimer: All claims expressed in this article are solely those of the authors and do not necessarily represent those of their affiliated organizations, or those of the publisher, the editors and the reviewers. Any product that may be evaluated in this article or claim that may be made by its manufacturer is not guaranteed or endorsed by the publisher.
Research integrity at Frontiers
Learn more about the work of our research integrity team to safeguard the quality of each article we publish.