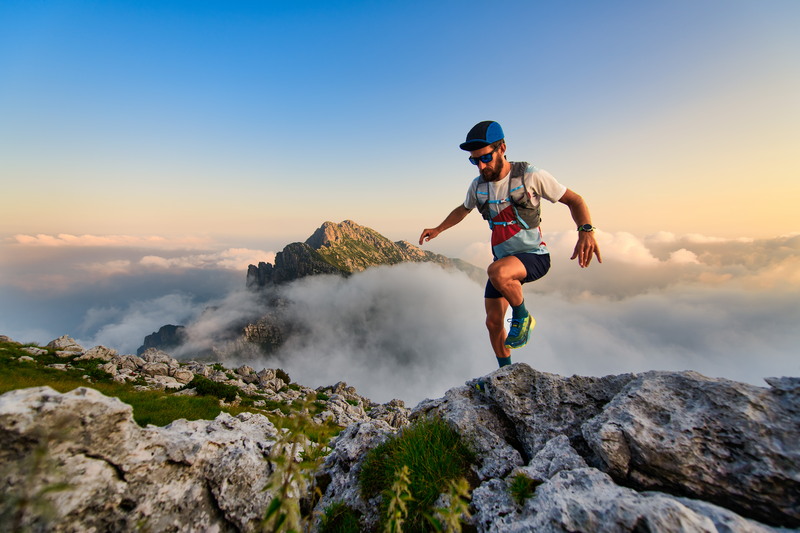
95% of researchers rate our articles as excellent or good
Learn more about the work of our research integrity team to safeguard the quality of each article we publish.
Find out more
BRIEF RESEARCH REPORT article
Front. Bioeng. Biotechnol. , 13 December 2023
Sec. Bioprocess Engineering
Volume 11 - 2023 | https://doi.org/10.3389/fbioe.2023.1324417
This article is part of the Research Topic Biotechnologies to Recover Critical Metals View all 4 articles
The presence of sulfur impurities in complex iron ores represents a significant challenge for the iron mining and steel-making industries as their removal often necessitates the use of hazardous chemicals and energy-intensive processes. Here, we examined the microbial and mineralogical composition of both primary and secondary iron concentrates, identifying the presence of Sulfobacillus spp. and Leptospirillum spp., while sulfur-oxidizing bacteria were absent. We also observed that these concentrates displayed up to 85% exposed pyrrhotite. These observations led us to explore the capacity of Acidithiobacillus thiooxidans to remove pyrrhotite-sulfur impurities from iron concentrates. Employing stirred tank bioreactors operating at 30°C and inoculated with 5·106 (At. thiooxidans cells mL-1), we achieved 45.6% sulfur removal over 16 days. Then, we evaluated packed leaching columns operated at 30°C, where the At. thiooxidans enriched system reached 43.5% desulfurization over 60 days. Remarkably, sulfur removal increased to 80% within 21 days under potassium limitation. We then compared the At. thiooxidans-mediated desulfurization process, with and without air supply, under potassium limitation, varying the initial biomass concentration in 1-m columns. Aerated systems facilitated approximately 70% sulfur removal across the entire column with minimal iron loss. In contrast, non-aerated leaching columns achieved desulfurization levels of only 6% and 26% in the lower and middle sections of the column, respectively. Collectively, we have developed an efficient, scalable biological sulfur-removal technology for processing complex iron ores, aligning with the burgeoning demand for sustainable practices in the mining industry.
Iron ore mining represents the topmost metal extraction activity worldwide, only comparable to the crude petroleum extractive industry. According to the British Geological Survey, iron extraction decreased by 7% from 2017 to 2021, reaching a total of 3.1 billion metric tons (Idoine et al., 2023). This decline aligns with extensive depletion of rich iron ore mines, high iron demand, and exploitation of lower grade iron ores with complex mineralogical composition (Fernández-González et al., 2017). Today, the main iron extracted minerals are hematite (Fe2O3), goethite (α-FeOOH), and magnetite (Fe3O4). Typically, these minerals undergo concentration processes in order to enhance the iron content while minimizing impurities, particularly alkalis, sulfur, and phosphorus.
Steel production currently consumes more than 98% of the mined iron ore. The presence of sulfur impurities in iron ore concentrates, particularly when exceeding 0.05%, can lead to steel brittleness and reduced weldability. Therefore, it is imperative to keep sulfur levels as low as possible (Schrama et al., 2017; Rezvanipour et al., 2018). In this sense, the production of iron concentrate utilizing magnetic concentration of Fe3O4 may result in high sulfur content, primarily due to contamination by pyrrothite (Fe 1-x)S) in the secondary concentrate. Depending on the ore characteristics, including extraction ore and tailings, iron concentrates with varying levels of magnetic sulfur impurities can be produced. The presence of such impurities can result in penalties in iron concentrate sale contracts, with a tolerated sulfur content limit typically set at 0.1% S (Compañía Minera del Pacífico, personal communication). Given these considerations, different approaches have been developed for sulfur impurity removal, including thermal, mechanical, and chemical procedures. One option involves roasting the sulfur content in iron ore using an oxidant, usually oxygen, and heat in a thermal decomposition process. In this operation, sulfur removal is directly related to temperature with significant desulfurization efficiencies achieved above 1,100 C. However, this approach comes with a high carbon footprint, the release of polluting SOx emissions, and changes in ore composition (Abzalov et al., 2008), necessitating different flue gas desulfurization technologies, which incurs significant costs and generate solid waste and wastewater treatment (Xu et al., 2000). Alternatively, the desulfurization of iron ores through flotation leads to a notable loss of valuable minerals. Efforts to enhance efficiency through collector mixtures (Yu et al., 2016) traduce environmental concerns, such as the use of compounds like xanthate (Elizondo-Álvarez et al., 2021). Moreover, the presence of iron ions in solution significantly influences sulfur removal during iron oxide flotation, requiring precise adjustments in each operation to achieve optimal efficiencies (Nakhaei et al., 2019).
A straightforward alternative to iron ore desulfurization involves acid leaching, where the reduction of sulfur content is directly proportional to H2SO4 concentration and reaction time, while inversely related to particle size. This approach can achieve up to 88% sulfur removal using 4M H2SO4, 2-h and particle sizes of 10 microns (Ocheri and Mbah, 2016). Additionally, nitric acid leaching has demonstrated remarkable results, with over 80% sulfur conversion from iron ore at 100°C, residence times exceeding 3-h and particle size of 100 µm or smaller (Rezvani Pour et al., 2016). Unfortunately, these experimental conditions often prove economically impractical for industrial applications. Despite the demonstrated leaching ability of acidophilic bacteria to remove sulfur from various ore minerals (Cismasiu, 2010; Shang et al., 2015), especially pit coals (Cismasiu, 2010; Ghosh et al., 2015; Mishra et al., 2020), this technology remains largely unexplored in the iron and steel-making sector. In this regard, Acidithiobacillus thiooxidans emerges as the most suitable biotechnological option since it is widely recognized for its acidophilic, aerobic, and chemolithoautotrophic features, and notably, it efficiently uses reduced inorganic sulfur compounds as electron donors while producing sulfuric acid in situ (Dopson and Okibe, 2022). These remarkable capabilities offer potential for developing an eco-friendly process to remove sulfur impurities from iron ore concentrates. At. thiooxidans has been industrially utilized for cobalt recovery (Morin and d’Hugues, 2007) and for the biooxidation of refractory gold-bearing ores in the BIONORD® process, using stirred bioreactors (Belyi and Tupikina, 2022). Regarding sulfur-oxidizing capacities, our previous research demonstrated that At. thiooxidans was more prevalent than At. ferrooxidans in mixed cultures (Bobadilla-Fazzini et al., 2011). Additionally, various studies have shown that At. thiooxidans bacteria are the dominant species in acidic environments (Okabe et al., 2007; Jones et al., 2012).
Here, we established a biotechnological procedure to efficiently remove sulfur impurities by inoculating the iron concentrate with A. thiooxidans. Different bioreactor modes demonstrated high desulfurization rates from iron concentrates offering a novel clean technology for the iron industry.
The A. thiooxidans (Bobadilla-Fazzini et al., 2011) used in this study was obtained by enrichment from ore samples from mining regions in Chile. Acidithiobacillus thiooxidans was maintained in batch aerated bubble column reactors at 30 C in basal 9Kmedium (990 mg L−1 (NH4)2SO4, 145 mg L−1 NaH2PO4·H2O, 52 mg L−1 KH2PO4, 100 mg L−1, MgSO4·7H2O, and 21 mg L−1 CaCl2), adjusted to pH 1.6 and containing 10 g L−1 of elemental sulfur as sole energy source.
Four different ore concentrate samples, two primary concentrate samples obtained after two rougher magnetic concentration stages and before the classification for grinding denominated “Iron concentrate sample A” (28.39% iron and 1.096% sulfur) and “Iron concentrate sample B” (40.70% iron and 0.950% sulfur), and two from secondary concentrate coming after grinding, flaking and finisher magnetic stages denominated “Iron concentrate sample C” (62,53% iron and 1.200% sulfur) and “Iron concentrate sample D” (61.70% iron and 0.720% sulfur) from an iron mining process in the Atacama Region of Chile were used. The mineralogical ore composition comprises 40.99, 41.63, 81.67% and 82.78% magnetite, 3.21%, 11.05%, 0.35% and 0.74% pyrite, and 0.58, 0.80, 1.42% and 2.10% pyrrhotite, for samples A, B, C and D, respectively. Remaining minerals correspond to gangue including 19.38%, 16.42%, 7.65% and 3.77% plagioclase, 16.51%, 14.10%, 2.19% and 6.28% quartz, 4.16, 3.55, 0.73 and 1.58 epidote for samples A, B, C and D respectively. All samples were received crushed and sieved with 325 Tyler mesh, which means that all particles were below 0.053 mm. Additionally and for bench-scale assays, a primary iron concentrate composite sample generated by standardized mixture of two primary concentrate samples from the same origin as the previous ones was used as “composite sample” (34.40% iron and 0.780% sulfur), with mineralogical ore composition comprising 72.09% magnetite, 5.56% pyrite and 3.78% pyrrhotite.
Cell number was determined by chamber counting (Thoma Chamber, depth 0.010 mm), counting four fields per sample in triplicate under microscope (Olympus CX31). Strain proportion was determined by specific qPCR determination as previously described (Bobadilla-Fazzini et al., 2011). Briefly, purified genomic DNA was extracted and analyzed with total bacteria 16S rDNA gene region primers (Forward 5′- GTGCCAGCMGCCGCGGTAA -3′, Reverse 5′-CCGTCAATTCCTTTGAGTTT-3′), rusticyanin gene rusB for At. ferrooxidans DSM 16786 (Forward 5′-GGACACCACCTGGAAAAC -3′, Reverse 5′- TCCCTTGTTGGTGTTGATG -3′), 16S rDNA gene for At. thiooxidans (Forward 5′- TAATATCGCCTGCTGTTGAC -3′, Reverse 5′- TTTCACGACAGACCTAATG-3′), 16S rDNA gene for Acidiphilium spp. (Forward 5′- CAACCACGGTCGGGTCAG A-3′, Reverse 5′- TCTCTGACCCGACCGTGG TT-3′), 16S rDNA gene for Leptospirillum spp. (Forward 5′- TGAGGGGACTGCCAGCGAC-3′, Reverse 5′- CTAGACGGGTACCTTGTTAC-3′), 16S rDNA gene for Sulfobacillus spp. (Forward 5′- CGAAGGCGGTGCACTGGCC-3′, Reverse 5′- CAGTGCACCGCCTTCGCCA-3′) and 16S rDNA gene for Ferroplasma spp. (Forward 5′- AGAGTCAACGTCACGAGCTTA-3′, Reverse 5′- AAGCTCGTCAGGTTGACTCT-3′).
To assess the sulfur bioconversion under controlled conditions, 1-L (0.8 L working volume) mechanically agitated bioreactors (BioFlo 110, New Brunswick), including air stripping (0.5 L min−1) and temperature control at 30°C and constant agitation 700 rpm, were carried out with 300 g concentrate L−1 of secondary ore concentrate samples (samples C and D) and at initial biomass of At. thiooxidans of 5·106 (cells mL−1).
From each ore sample, sub-samples of approximately 500 g were obtained after strict protocols to minimize sampling errors. Each sample was agglomerated with water and inoculum at a dose of 106 (cells g−1) and packed in 6 cm diameter 30 cm high acrylic columns fed at a rate of 5 L (h m2) −1 with water adjusted to pH 3.0 and addition of 0.5 g (NH4)2HPO4 L−1. Assays were done from 7 up to 60 days with forty columns in total, divided in four groups of ten columns each. The first two groups of ten columns each with samples A and B included potassium addition (0.006 g KH2PO4 L−1) as part of the feeding solution (condition N/P/K), while the second group was modified without any potassium addition on the feed (condition N/P), replicated for both primary ore samples. All columns were incubated at 30 C under non-sterile conditions in closed circuit, and evaporation was compensated with pure water.
For bench-scale assays, the composite sample was sub-sampled in approximately 22 kg after strict protocols to minimize sampling errors. Each sample was agglomerated with water and inoculum at a dose of 105 or 106 cells g−1 and packed in 15 cm diameter glass columns fed at a rate of 5 L (h m2)−1 with water adjusted to pH 3.0 and addition of 0.5 g (NH4)2HPO4 L−1. Columns of 1 m were operated for 60 days, both without and with aeration from the base with compressed air at a rate of 0.05 m3 (ton h)−1. At the end of each assay, each column was drained and discharged, and the iron ores within the column were separated into three equal sections based on lengths at day 60: upper, middle, and lower sections.
Total iron was determined after iron ore sample dissolution in HNO3/HCl with heat and serially diluted in volumetric flasks for analysis against standard curve by Atomic Absorption Spectrometry (Perkin Elmer Analyst 400) and Fe(II) ions by the o-phenanthroline method (Kolthoff and Sandell, 1963). Concentrate sulfur content was determined before and after magnetic concentration by Davis Test Tube (DTT) using a LECO 844 series combustion sulfur analyzer. Briefly, 0.1 g of ore concentrate sample was placed in a ceramic crucible and heated to 1,600°C in a stream of purified O2. The liberated SO2 was then quantified by titration using a standard KIO3 solution, with measurements taken by a calibrated automatic SO2 titrator (LECO Corp, 2019).
Before treatment, samples were deagglomerated, sieved, and weighed to obtain exact mass proportions. Grain mounts were prepared, by grinding and polishing prior to optical microscopy. Reflected light microscopy was performed using a Zeiss Axio Image M1m and Axiophot in order to identify the main features of each sample. To determine the mineralogical composition, a statistical point counting method was applied using an integration plate, with a metric network of 400 points, including the analysis of the degree of liberation of the sulfur minerals present, counting the points of free sulfides, associated with gangue and grains included in non-metallic gangue.
We first analyzed the presence of native acidophilic microorganisms in the iron ore samples using direct DNA extraction and quantitative PCR (qPCR), following established protocols (Bobadilla-Fazzini et al., 2011). As anticipated, all samples showed high bacteria counts, with no detection of archaea (Table 1). The analysis unveiled that heterotrophic species of the genus Sulfobacillus had low abundance in primary concentrate samples A and B, while autotrophic iron-oxidizing Leptospirillum spp. was present only in one secondary concentrate sample. Mesophilic bacterial genera such as Leptospirillum are widespread due to their reliance on iron oxidation as an energy source. Notably, the detection of Sulfobacillus species is somehow atypical, considering their standard classification as moderate thermophilic and with a mixotrophic lifestyle (Bobadilla-Fazzini et al., 2014). However, Sulfobacillus species can thrive within a temperature range of 20°C and 60°C (Tat’yana et al., 2006), with Sulfobacillus acidophilus, for instance, utilizing ferrous iron as an energy source through autotrophic growth (Norris et al., 1996). Interestingly, mesophilic sulfur-oxidizing Acidithiobacillus bacteria were below the detection limit, suggesting their potential use as agents for sulfur removal through inoculation.
Initial mineralogical composition analysis showed that primary iron concentrates had a higher pyrite content compared to secondary concentrate samples, with the latter exhibiting an enrichment in pyrrhotite abundance. This composition indicates that magnetic concentration is not efficient in removing pyrrhotite, making biological treatment a promising technology for eliminating this sulfur impurity. Detailed optical mineralogical analysis in terms of mineral species liberation degree and associations is summarized in the Supplementary Table S1. Key minerals, namely, magnetite, pyrite, and pyrrhotite are predominantly found in their free form. Moreover, a significant proportion of pyrrhotite is associated with pyrite in primary concentrate samples, while pyrrhotite is linked to gangue in the secondary material. This analysis denotes that the weakly magnetic sulfur fraction present in these iron ore concentrate samples is readily accessible to sulfur-oxidizing acidophilic microorganisms. Further, the association of pyrrhotite with pyrite in primary iron ore concentrates is important, considering the possible catalytic galvanic effect that pyrite may exert on the acceleration of leaching kinetics. This phenomenon is commonly observed in various metal sulfides such as sphalerite (Estrada-De los Santos et al., 2016) and enargite (Ma et al., 2021).
Next, we assessed the sulfur conversion ability of At. thiooxidans in batch-stirred bioreactors using secondary samples C and D to monitor sulfur conversion over time. The bioreactors started with a 300 (g L−1) pulp density and were inoculated to reach a biomass concentration of 5.106 (cells mL−1). Due to the sulfur oxidation activity of At. thiooxidans and native sulfur-oxidizing bacteria in the ores, the pH gradually decreased over time (Figure 1). The bacterial consortium exhibited a sulfur removal rate of 2.4% ± 0.2% day−1 during the first 20 days, reaching a total removal of 45.6% within 16 days (Figure 1A). During this period, we observed minor iron leaching, yielding a low concentration of ∼100 (mg L−1). Initially, ferrous iron species were detected in the first 5 days of culturing. Likely attributable to acid-soluble iron species (Figure 1B). Subsequently, the iron was encountered in the ferric form, which persisted until the end of the process (Figure 1B).
FIGURE 1. Iron ore secondary concentrate sulfur removal kinetic assays in batch stirred bioreactors with sample “C” and sample “D” at 30°C, 300 (g L−1) pulp density with inoculation of At. thiooxidans enriched consortium 5.106 (cells mL−1). (A) Sulfure removal and biomass, (B) Iron content and (C) pH of the desulfurization process
The leaching column bioreactor setup closely resembles heap leaching processes. Thus, subsamples of 500 g of primary iron concentrate samples A and B were agglomerated with water and inoculated with At. thiooxidans at an initial biomass of 106 (cells g−1). Two sets of ten columns each were used for each primary ore sample. A constant feed rate of 5 L (h m2)−1 was maintained, with the addition of 0.5 g L−1 of (NH4)2HPO4 to provide nitrogen and phosphorous (N/P) sources, while avoiding the incorporation of alkali impurities such as sodium and potassium. Based on the nutrient profile previously reported for At. thiooxidans (Denisov et al., 1980) a minimum potassium concentration of (6 mg L−1 of KH2PO4) was included (N/P/K) in ten columns for each sample. The assays ran for 60 days totaling 40 columns, 10 columns for each condition: sample A (N/P), sample A (N/P/K), sample B (N/P), and sample B (N/P/K).
To determine sulfur removal kinetics on both iron concentrate samples, with (N/P) and (N/P/K) addition, columns were drained and discharged at 7, 14, 21, 28, 35, 42, 49, 56 and 60 operation days for each condition separately. Dry samples of treated ores were then analyzed for sulfur removal before (Figure 2A; Figure 2C) and after the Davis Test Tube (DTT) for magnetic concentration (Figure 2B; Figure 2D), as well as soluble iron in order to determine iron loss. Figure 2 illustrates the sulfur impurities removal kinetics for (N/P/K) columns, before and after magnetic concentration. The process initially yielded low sulfur removal before magnetic concentration, indicating sulfur enrichment due to precipitation (Figure 2A). After DTT magnetic concentration, the leaching bioprocess resulted in desulfurization yields 43.5% ± 7.8 at day 60, while the loss of iron in solution reached a maximum value of 4% after treatment for this group of columns (Figure 2B).
FIGURE 2. Sulfur removal and iron loss kinetics in iron primary concentrate samples in leaching columns incubated at 30 C inoculated with At. thiooxidans. (A) N/P/K before magnetic concentration; (B) N/P/K after magnetic concentration; (C) N/P before magnetic concentration and; (D) N/P after magnetic concentration.
A series of column assays were conducted without the addition of potassium to prevent the incorporation of alkali impurities. Figure 2C, D also illustrate the kinetics of sulfur impurities removal for columns of the (N/P) group under potassium limitation. In the absence of magnetic concentration, just a small fraction, less than 5%, of sulfur was removed (Figure 2C). Conversely, with DTT concentration, we achieved a sulfur conversion efficiency of 80% ± 4.4 within 21 days as depicted in Figure 2D. Notably, under potassium-depleted conditions, we observed a higher desulfurization activity, effectively doubling the values attained with potassium-replenished conditions. Figure 2D also highlights the loss of iron in (N/P) columns, which reached a maximum of only 3% after treatment, indicating lower values than those found in columns with potassium addition.
In our final set of experiments, we extended the length of the column bioreactor to 1 m and monitored sulfur removal in primary iron ore concentrates under potassium limitation. We evaluated two initial cell densities, 105 and 106 (At. thiooxidans cells g−1), with and without aeration. The supply of oxygen is a critical parameter for aerobic bacterial activity and has been demonstrated to be important in improving leaching efficiency in standard heap leaching operations (Pradhan et al., 2008). Recent findings also demonstrated that aeration can accelerate pyrrhotite oxidation at an industrial scale (Arpalahti and Lundström, 2019). To gain insight into sulfur bioconversion within different sections of the leaching columns, we drained, discharged, and separated the iron ores within the column in three equal lengths at day 60: upper, middle, and lower. Sulfur conversion was quantified for dry sample analysis before and after DTT treatment. The aerated process reached a maximum sulfur removal of nearly 70% across the entire column when At. thiooxidans was inoculated at 106 cells g−1 (Figure 3A). However, columns without aeration and high initial biomass exhibited low sulfur conversion in the middle and lower part of the column, indicating unfavorable sulfur oxidation activity due to low oxygen availability (Figure 3B). Sulfur removal showed a direct dependence on At. thiooxidans inoculation, as aerated columns with lower biomass (105 cells g−1) removed only 49% of the available sulfur at day 60 (Figure 3C).
FIGURE 3. Sulfur removal assay from primary iron ore composite packed column bench-scale bioreactors (1-m length) with (N/P) addition after 60 days operation. (A) Aerated column with initial At. thiooxidans inoculum 106 (cells g−1). (B) Non-aerated column with initial At. thiooxidans inoculum 106 (cells g−1). (C) Aerated column with initial At. thiooxidans inoculum 105 (cells g−1). (D) Non-aerated column with initial At. thiooxidans inoculum 105 (cells g−1).
The iron mining industry is currently grappling with major challenges, including soaring demand, the depletion of rich iron ore deposits, and a shift toward the exploitation of complex mineralogical iron ores with escalating sulfur impurities. In this study, we successfully established a desulfurization bioprocess using At. thiooxidans in stirred tanks and leaching column bioreactors, achieving 45% and 80% sulfur bioconversion over 20 days of operation, respectively. The pace at which these processes occur is directly correlated with the abundance of microorganisms (Lambert et al., 2014; Tupikina et al., 2014). Based on our results, the higher initial cell density of sulfur-oxidizing bacteria seems to influence the biodesulfurization process in pyrrhotite present in iron concentrates within bench-scale columns. Particularly noteworthy is the observation of enhanced biological sulfur removal under potassium limitation conditions. Inorganic nutrient limitation is known to typically boost the carbon uptake rate and, consequently, the oxidation rate in chemolithoautotrophic (Parro and Moreno-Paz, 2003; Vera et al., 2008), as well as in chemoheterotrophic bacteria (Sulbaran-Bracho et al., 2023).
However, it also exerts a negative impact on biomass formation as this condition can be deleterious for ATP production (Parro and Moreno-Paz, 2003; Vera et al., 2008). Mounting evidence supports the notion that the efficient bacterial sulfur oxidation activities in the leaching process require the development of a complex and orchestrated biofilm matrix. This involves either native or externally introduced acidophiles colonizing the ore surface (Bobadilla-Fazzini, 2014; Dong et al., 2020; Bobadilla-Fazzini and Poblete-Castro, 2021), or relates to the aggregation degree of planktonic cells prior to biofilm formation (Bellenberg et al., 2015; Melaugh et al., 2016; Yavari et al., 2019). Consequently, it is less likely that the improved desulfurization process can be solely attributed to the activity of sulfur-oxidation bacteria. A more plausible explanation lies in the fact that the soluble bioavailable sulfur, existing in intermediate forms between sulfur ion (S2−) and sulfate (SO42−), such as acid-stable tetrathionate (S4O62−), partially precipitates in the presence of potassium ions, thereby hindering more efficient sulfur-oxidizing activity. Thus, the exclusion of potassium ions from the leaching solution appears to be a beneficial strategy for achieving increased sulfur removal yields.
The observed kinetics of magnetic sulfur impurity removal from iron concentrate samples during the inoculation of an enriched culture of At. thiooxidans reveal transformation reactions driven by oxidation catalysis and precipitation phenomena under the given operating conditions. First, the inoculated sulfur-oxidizing microorganisms, operating under potassium limitation, efficiently catalyze the pyrrhotite (here represented as FeS), a magnetic sulfur impurities oxidation:
This process effectively preserves the non-magnetic sulfur compounds such as pyrite (FeS2), while selectively reducing the presence of magnetic sulfur impurities on the iron concentrate. Concurrently, reactions leading to sulfate and/or jarosite precipitation occur, as follows:
These precipitation reactions are pH-dependent and result in the form of precipitates on the surface of the iron concentrate. These precipitates must be mechanically removed via a magnetic concentration process, as exemplified by the Davis Test Tube.
When scaling up the bioleaching process in iron ore-packed columns, we found that cell density and air supply are critical process parameters for attaining high sulfur removal across the entire column with minimal iron loss (Figure 3). The feed solution is initially oxygen-saturated, but oxygen rapidly depletes from the draining solution due to aerobic microbial consumption, making it unavailable further downstream in the process (Lizama, 2001). Additionally, there is a linear correlation between increasing temperature and lower oxygen solubility during bioleaching (Huang et al., 2022) along with air convection and diffusion also decreasing along the length of the column, adversely affecting the oxygen-dependent microbial activity essential for bioleaching and the reaction of oxygen with other iron compounds (Casas et al., 1998; Chen et al., 2022). This phenomenon became particularly evident in columns without forced aeration, where we recorded almost negligible sulfur removal at the bottom of the column (Figure 3).
In conclusion, bioleaching columns that are supplied with compressed air and inoculated with an initial cell concentration of At. thiooxidans at 106 cells g−1 under potassium limitation present the most suitable condition for converting pyrrhotite-sulfur impurities in iron concentrates. This bioprocess emerges as a sustainable alternative to conventional methods that typically involve the use of contaminating chemicals and energy-consuming procedures.
The raw data supporting the conclusion of this article will be made available by the authors, without undue reservation.
RB-F: Conceptualization, Data curation, Formal Analysis, Investigation, Project administration, Writing–original draft. IP-C: Data curation, Formal Analysis, Funding acquisition, Investigation, Resources, Validation, Visualization, Writing–review and editing.
The author(s) declare financial support was received for the research, authorship, and/or publication of this article. Facultad de Ingenieria USACH for financial support that enable publishing open access.
The authors acknowledge the financial support by ANID-PIA-Anillo INACH ACT192057. We also extend our gratitude to Facultad de Ingeniería at Universidad de Santiago de Chile (USACH) for their financial support in enabling open access publication.
The authors declare that the research was conducted in the absence of any commercial or financial relationships that could be construed as a potential conflict of interest.
The author(s) declared that they were an editorial board member of Frontiers, at the time of submission. This had no impact on the peer review process and the final decision.
All claims expressed in this article are solely those of the authors and do not necessarily represent those of their affiliated organizations, or those of the publisher, the editors and the reviewers. Any product that may be evaluated in this article, or claim that may be made by its manufacturer, is not guaranteed or endorsed by the publisher.
The Supplementary Material for this article can be found online at: https://www.frontiersin.org/articles/10.3389/fbioe.2023.1324417/full#supplementary-material
Abzalov, V. M., Sudai, A. V., and Yur’ev, B. P. (2008). Desulfurization in roasting iron-ore pellets. Steel Transl. 38, 1003–1007. doi:10.3103/s0967091208120152
Arpalahti, A., and Lundström, M. (2019). Dual aeration tests with heap leaching of a pyrrhotite-rich pentlandite ore. Hydrometallurgy 185, 173–185. doi:10.1016/j.hydromet.2019.02.018
Bellenberg, S., Barthen, R., Boretska, M., Zhang, R., Sand, W., and Vera, M. (2015). Manipulation of pyrite colonization and leaching by iron-oxidizing Acidithiobacillus species. Appl. Microbiol. Biotechnol. 99, 1435–1449. doi:10.1007/s00253-014-6180-y
Belyi, A. V., and Tupikina, O. V. (2022). “Biooxidation of gold ores in Russia and Kazakhstan,” in Biomining technologies: extracting and recovering metals from ores and wastes (Cham: Springer), 191–208.
Bobadilla-Fazzini, R. A., Cortés, M. P., Maass, A., and Parada, P. (2014). Sulfobacillus thermosulfidooxidans strain Cutipay enhances chalcopyrite bioleaching under moderate thermophilic conditions in the presence of chloride ion. Amb. Express 4, 84–85. doi:10.1186/s13568-014-0084-1
Bobadilla-Fazzini, R. A., Levican, G., and Parada, P. (2011). Acidithiobacillus thiooxidans secretome containing a newly described lipoprotein Licanantase enhances chalcopyrite bioleaching rate. Appl. Microbiol. Biotechnol. 89, 771–780. doi:10.1007/s00253-010-3063-8
Bobadilla-Fazzini, R. A., and Poblete-Castro, I. (2021). Biofilm Formation is crucial for efficient copper bioleaching from bornite under mesophilic conditions: unveiling the lifestyle and catalytic role of sulfur-oxidizing bacteria. Front. Microbiol. 12, 761997. doi:10.3389/fmicb.2021.761997
Casas, J. M., Vargas, T., Martínez, J., and Moreno, L. (1998). Bioleaching model of a copper-sulfide ore bed in heap and dump configurations. Metallurgical Mater. Trans. B 29, 899–909. doi:10.1007/s11663-998-0149-0
Chen, W., Yin, S., and Ilankoon, I. (2022). Effects of forced aeration on community dynamics of free and attached bacteria in copper sulphide ore bioleaching. Int. J. Minerals, Metallurgy Mater. 29, 59–69. doi:10.1007/s12613-020-2125-x
Cismasiu, C. M. (2010). The acidophilic chemolithotrophic bacteria involved in the desulphurization process of lignite and pit coal from Halanga, Mintia and Petrila mines. Romanian Biotechnol. Lett. 15, 5602–5610.
Denisov, G. V., Kovrov, B. G., Trubachev, I. N., Gribovskaia, I. V., and Stepen, A. A. (1980). Composition of a nutrient medium for the continuous cultivation of Thiobacillus ferrooxidans. Mikrobiologiia 49, 473–478.
Dong, B., Jia, Y., Tan, Q., Sun, H., and Ruan, R. (2020). Contributions of microbial “contact leaching” to pyrite oxidation under different controlled redox potentials. Minerals 10, 856. doi:10.3390/min10100856
Dopson, M., and Okibe, N. (2022). “Biomining microorganisms: diversity and modus operandi,” in Biomining technologies: extracting and recovering metals from ores and wastes (Cham: Springer), 89–110.
Elizondo-Álvarez, M. A., Uribe-Salas, A., and Bello-Teodoro, S. (2021). Chemical stability of xanthates, dithiophosphinates and hydroxamic acids in aqueous solutions and their environmental implications. Ecotoxicol. Environ. Saf. 207, 111509. doi:10.1016/j.ecoenv.2020.111509
Estrada-De los Santos, F., Rivera-Santillán, R. E., Talavera-Ortega, M., and Bautista, F. (2016). Catalytic and galvanic effects of pyrite on ferric leaching of sphalerite. Hydrometallurgy 163, 167–175. doi:10.1016/j.hydromet.2016.04.003
Fernández-González, D., Ruiz-Bustinza, I., Mochón, J., González-Gasca, C., and Verdeja, L. F. (2017). Iron ore sintering: raw materials and granulation. Mineral Process. Extr. Metallurgy Rev. 38, 36–46. doi:10.1080/08827508.2016.1244059
Ghosh, A., Kumari, S., and Pandey, B. D. (2015). Microbial biodesulphurisation of coal. Microbiology for minerals, metals, materials and the environment. Florida, United States: CRC Press.
Huang, M.-Q., Zhang, M., Zhan, S.-L., Chen, L., and Xue, Z.-L. (2022). Saturated dissolved oxygen concentration in in situ fragmentation bioleaching of copper sulfide ores. Front. Microbiol. 13, 821635. doi:10.3389/fmicb.2022.821635
Idoine, N., Raycraft, E., Price, F., Hobbs, S., Deady, E., Everett, P., et al. (2023). World mineral production 2017-21. Nottingham, United Kingdom: British Geological Survey.
Jones, D. S., Albrecht, H. L., Dawson, K. S., Schaperdoth, I., Freeman, K. H., Pi, Y., et al. (2012). Community genomic analysis of an extremely acidophilic sulfur-oxidizing biofilm. ISME J. 6, 158–170. doi:10.1038/ismej.2011.75
Kolthoff, J. M., and Sandell, E. B. (1963). Textbook of quantitative inorganic chemistry. New York, NY: Macmillan.
Lambert, G., Bergman, A., Zhang, Q., Bortz, D., and Austin, R. (2014). Physics of biofilms: the initial stages of biofilm formation and dynamics. New J. Phys. 16, 045005. doi:10.1088/1367-2630/16/4/045005
LECO Corp (2019). Carbon and sulfur determination in low carbon ferroalloys. Available at: https://knowledge.leco.com/app-notes/application-note-carbon-sulfur-in-low-carbon-ferroalloys-using-the-cs844-588.
Lizama, H. M. (2001). Copper bioleaching behaviour in an aerated heap. Int. J. Mineral Process. 62, 257–269. doi:10.1016/S0301-7516(00)00057-0
Ma, Y., Yang, Y., Gao, X., Fan, R., and Chen, M. (2021). The galvanic effect of pyrite enhanced (bio) leaching of enargite (Cu3AsS4). Hydrometallurgy 202, 105613. doi:10.1016/j.hydromet.2021.105613
Melaugh, G., Hutchison, J., Kragh, K. N., Irie, Y., Roberts, A., Bjarnsholt, T., et al. (2016). Shaping the growth behaviour of biofilms initiated from bacterial aggregates. PloS one 11, e0149683. doi:10.1371/journal.pone.0149683
Mishra, S., Panda, S., Pradhan, N., Biswal, S. K., and Satapathy, D. (2020). Acidophilic biodesulphurization of calcined pet coke and coal samples in iron and iron-free leaching media. Energy & Environ. 0958305X20935678 32, 424–442. doi:10.1177/0958305x20935678
Morin, D. H. R., and d’Hugues, P. (2007). “Bioleaching of a cobalt-containing pyrite in stirred reactors: a case study from laboratory scale to industrial application,” in Biomining (Cham: Springer), 35–55.
Nakhaei, F., Irannajad, M., Mohammadnejad, S., and Hajizadeh Omran, A. (2019). “Sulfur content reduction of iron concentrate by reverse flotation,” in Energy sources, Part A: recovery, utilization, and environmental effects 1–17 (Oxfordshire United Kingdom: Taylor & Francis).
Norris, P. R., Clark, D. A., Owen, J. P., and Waterhouse, S. (1996). Characteristics of Sulfobacillus acidophilus sp. nov. and other moderately thermophilic mineral-sulphide-oxidizing bacteria. Microbiology 142, 775–783. doi:10.1099/00221287-142-4-775
Ocheri, C., and Mbah, A. C. (2016). Reduction of sulphur content of AGBAJA iron ore using sulphuric acid (H2SO4). J. Mater. Sci. Eng. 6, 22–2169.
Okabe, S., Odagiri, M., Ito, T., and Satoh, H. (2007). Succession of sulfur-oxidizing bacteria in the microbial community on corroding concrete in sewer systems. Appl. Environ. Microbiol. 73, 971–980. doi:10.1128/aem.02054-06
Parro, V., and Moreno-Paz, M. (2003). Gene function analysis in environmental isolates: the nif regulon of the strict iron oxidizing bacterium Leptospirillum ferrooxidans. Proc. Natl. Acad. Sci. U. S. A. 100, 7883–7888. doi:10.1073/pnas.1230487100
Pradhan, N., Nathsarma, K. C., Srinivasa Rao, K., Sukla, L. B., and Mishra, B. K. (2008). Heap bioleaching of chalcopyrite: a review. Miner. Eng. 21, 355–365. doi:10.1016/j.mineng.2007.10.018
Rezvanipour, H., Mostafavi, A., Ahmadi, A., Karimimobarakabadi, M., and Khezri, M. (2018). Desulfurization of iron ores: processes and challenges. steel Res. Int. 89, 1700568. doi:10.1002/srin.201700568
Rezvani Pour, H., Mostafavi, A., Shams Pur, T., Ebadi Pour, G., and Haji Zadeh Omran, A. (2016). Removal of sulfur and phosphorous from iron ore concentrate by leaching. Physicochem. Problems Mineral Process. 52.
Schrama, F. N. H., Beunder, E. M., Van den Berg, B., Yang, Y., and Boom, R. (2017). Sulphur removal in ironmaking and oxygen steelmaking. Ironmak. Steelmak. 44, 333–343. doi:10.1080/03019233.2017.1303914
Shang, H., Wen, J. K., Wu, B., and Mo, X. L. (2015). “Study on bioleaching of sulfur in iron ore by mixed culture,” in Advanced materials research (Switzerland: Trans Tech Publ), 371–374.
Sulbaran-Bracho, Y., Orellana-Saez, M., Castro-Severyn, J., Galbán-Malagón, C., Castro-Nallar, E., and Poblete-Castro, I. (2023). Continuous bioreactors enable high-level bioremediation of diesel-contaminated seawater at low and mesophilic temperatures using Antarctic bacterial consortia: pollutant analysis and microbial community composition. Environ. Pollut. 321, 121139. doi:10.1016/j.envpol.2023.121139
Tat’yana, I. B., Tsaplina, I. A., Kondrat’eva, T. F., Duda, V. I., Suzina, N. E., Melamud, V. S., et al. (2006). Sulfobacillus thermotolerans sp. nov., a thermotolerant, chemolithotrophic bacterium. Int. J. Syst. Evol. Microbiol. 56, 1039–1042. doi:10.1099/ijs.0.64106-0
Tupikina, O. V., Minnaar, S. H., Rautenbach, G. F., Dew, D. W., and Harrison, S. T. L. (2014). Effect of inoculum size on the rates of whole ore colonisation of mesophilic, moderate thermophilic and thermophilic acidophiles. Hydrometallurgy 149, 244–251. doi:10.1016/j.hydromet.2013.10.010
Vera, M., Pagliai, F., Guiliani, N., and Jerez, C. A. (2008). The chemolithoautotroph Acidithiobacillus ferrooxidans can survive under phosphate-limiting conditions by expressing a C-P lyase operon that allows it to grow on phosphonates. Appl. Environ. Microbiol. 74, 1829–1835. LP. doi:10.1128/AEM.02101-07
Xu, G., Guo, Q., Kaneko, T., and Kato, K. (2000). A new semi-dry desulfurization process using a powder-particle spouted bed. Adv. Environ. Res. 4, 9–18. doi:10.1016/s1093-0191(00)00003-4
Yavari, M., Ebrahimi, S., Aghazadeh, V., and Ghashghaee, M. (2019). Kinetics of different bioreactor systems with Acidithiobacillus ferrooxidans for ferrous iron oxidation. React. Kinet. Mech. Catal. 128, 611–627. doi:10.1007/s11144-019-01660-3
Keywords: complex iron ores, pyrrhotite, Acidithiobacillus thiooxidans, stirred tank bioreactor, leaching columns
Citation: Bobadilla-Fazzini RA and Poblete-Castro I (2023) Establishing a green biodesulfurization process for iron ore concentrates in stirred tank and leaching column bioreactors using Acidithiobacillus thiooxidans. Front. Bioeng. Biotechnol. 11:1324417. doi: 10.3389/fbioe.2023.1324417
Received: 19 October 2023; Accepted: 30 November 2023;
Published: 13 December 2023.
Edited by:
Denys Kristalia Villa Gomez, The University of Queensland, AustraliaReviewed by:
Song Yang, Taiyuan University of Technology, ChinaCopyright © 2023 Bobadilla-Fazzini and Poblete-Castro. This is an open-access article distributed under the terms of the Creative Commons Attribution License (CC BY). The use, distribution or reproduction in other forums is permitted, provided the original author(s) and the copyright owner(s) are credited and that the original publication in this journal is cited, in accordance with accepted academic practice. No use, distribution or reproduction is permitted which does not comply with these terms.
*Correspondence: Ignacio Poblete-Castro, aWduYWNpby5wb2JsZXRlLmNAdXNhY2guY2w=
Disclaimer: All claims expressed in this article are solely those of the authors and do not necessarily represent those of their affiliated organizations, or those of the publisher, the editors and the reviewers. Any product that may be evaluated in this article or claim that may be made by its manufacturer is not guaranteed or endorsed by the publisher.
Research integrity at Frontiers
Learn more about the work of our research integrity team to safeguard the quality of each article we publish.