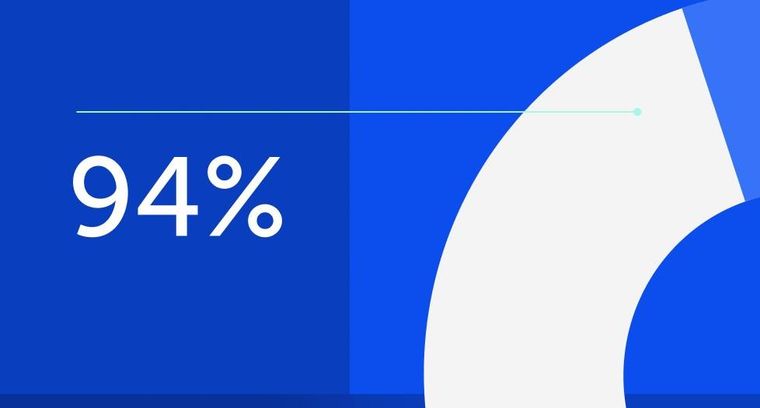
94% of researchers rate our articles as excellent or good
Learn more about the work of our research integrity team to safeguard the quality of each article we publish.
Find out more
REVIEW article
Front. Bioeng. Biotechnol., 26 September 2023
Sec. Biosensors and Biomolecular Electronics
Volume 11 - 2023 | https://doi.org/10.3389/fbioe.2023.1264563
This article is part of the Research TopicIntelligent Neural Interface for Healthcare and RehabilitationView all 7 articles
Flexible tactile sensors have the advantages of large deformation detection, high fault tolerance, and excellent conformability, which enable conformal integration onto the complex surface of human skin for long-term bio-signal monitoring. The breakthrough of flexible tactile sensors rather than conventional tactile sensors greatly expanded application scenarios. Flexible tactile sensors are applied in fields including not only intelligent wearable devices for gaming but also electronic skins, disease diagnosis devices, health monitoring devices, intelligent neck pillows, and intelligent massage devices in the medical field; intelligent bracelets and metaverse gloves in the consumer field; as well as even brain–computer interfaces. Therefore, it is necessary to provide an overview of the current technological level and future development of flexible tactile sensors to ease and expedite their deployment and to make the critical transition from the laboratory to the market. This paper discusses the materials and preparation technologies of flexible tactile sensors, summarizing various applications in human signal monitoring, robotic tactile sensing, and human–machine interaction. Finally, the current challenges on flexible tactile sensors are also briefly discussed, providing some prospects for future directions.
Flexible tactile sensors have attracted significant attention recently owing to their comfortable interface and long-term continuous signal acquisition capabilities (Guo et al., 2017; Li G. et al., 2020; Bae et al., 2022; Chen et al., 2023). Flexible tactile sensors can be integrated onto complex surfaces such as human skin or soft robots due to their low modulus, stretchability, and light weight (Pang et al., 2020; Ainsworth et al., 2022; Liu et al., 2023). Therefore, materials and fabrication techniques for flexible tactile sensors have received significant attention from researchers. Material innovation is the key to achieving flexibility and stretchability of tactile sensors (Jang et al., 2016). Currently, the materials used for flexible tactile sensors mainly include metal, conductive polymer, and composite materials (Castellanos-Ramos et al., 2010; Yoshimura et al., 2016; Kim et al., 2021; Mondal et al., 2022; Mohan et al., 2023). Moreover, traditional fabrication methods cannot meet the needs of complex structure manufacturing and highly personalized monitoring of humans (Ainsworth et al., 2022). A novel advanced manufacturing technology has been developed for flexible tactile sensors, mainly including 3D printing, screen printing, direct ink writing, inkjet printing, pattern transferring processes, spray/spin coating, drop casting, and vacuum filtration processes (Wen et al., 2003; Ishihara et al., 2006; Castellanos-Ramos et al., 2011; Sato et al., 2019; Zhang et al., 2021; Chen et al., 2022; Lee et al., 2022). With advances in materials, processes, and sensing technologies, various flexible tactile sensors have been developed for great potential applications (Amjadi et al., 2016). This paper discusses the materials and preparation technologies of flexible tactile sensors, summarizing various applications in human signal monitoring, robotic tactile sensing, and human–machine interaction. Finally, the current challenges on flexible tactile sensors are also briefly discussed, providing some prospects for future directions.
The development of flexible tactile sensors largely relies on advancements in material science (Cai and Wang, 2015). The materials for flexible tactile sensors are mainly classified as metal materials, polymer materials, and composite materials. Table 1 shows the properties of different materials.
Metals have widespread applications among sensing materials. Patterned structures and interconnect techniques for metal are reliable with the capability of obtaining high-resolution structures. Tactile sensors that are prepared on flexible substrates with metals could significantly shift human perceptions of electronics, providing potential applications in human signal monitoring, robotic tactile sensing, and human–machine interaction (Forrest, 2004).
Traditional metals for flexible tactile sensors include gold (Au), silver (Ag), copper (Cu), magnesium (Mg), zinc (Zn), aluminum (Al), chromium (Cr), and titanium (Ti). The outer shell electrons of metals can move freely within the metal, which enables excellent electrical properties. The conductivity of metals can be adjusted by the length and diameter of the metal strain-sensitive grating. John A. Rogers et al. reported a flexible tactile sensor system based on Cr/Au that achieved ultra-thin thicknesses, compatible elastic modulus, and bending stiffness, matched to human skin (Figure 1A) (Won et al., 2019). The flexible tactile sensor on the skin achieves a conformal attachment and adequate adhesion, according to van der Waals interactions alone. It has a variable shape, which enables the mechanically guided geometric transformation of a two-dimensional planar precursor to generate a 3D structure capable of decoupling complex stress/strain. Complex stimulus responses such as pressure, shear, tension, and bending, which are difficult to achieve with traditional rigid sensors, are essential for soft robotics, human signal monitoring, and human interactions with the physical environment.
FIGURE 1. Materials for flexible tactile sensors. (A) Traditional metal, (B) liquid metal, (C) carbon black-based active materials, (D) CNT-based active materials, (E) graphene-based active materials, (F) nanowire-/nanoparticle-based one-dimensional nanostructured materials, (G) polyurethane/polypyrrole, (H) PEDOT: PSS, and (I) hydrogels (Ladd et al., 2013; Hou et al., 2014; Jung et al., 2014; Li et al., 2014; Lee et al., 2016; Choi et al., 2017; Won et al., 2019; Fu et al., 2020; Liu et al., 2020).
The development of liquid metals enriched the system of sensing materials. Liquid metals (Figure 1B), which are in the fluid phase at normal atmospheric temperature, have been widely used as conductors for flexible devices due to their outstanding stretchability and self-healing ability (Park et al., 2021). Gallium and mercury are typical liquid metals with low melting points. Gallium-based alloys have low volatility and negligible toxicity and hence are actively studied for application in flexible tactile sensors (Park et al., 2021). Gallium and gallium-based alloys exhibit remarkable electrical conductivity with excellent deformability, which provides the possibility of conformal attachment with human skin (Kim et al., 2019). Moreover, some alkali metals, such as rubidium, cesium, and francium, also exist in a fluid state at or near normal atmospheric temperature. The conductivity of liquid metals can be adjusted by the shape of the liquid metal. Inkyu Park et al. introduced a liquid metal-based flexible pressure sensor with a microbump for human signal monitoring. The liquid metal microchannel and rigid microbump arrays are fabricated using the one-step direct process. The sensitivity of the flexible pressure sensor is approximately 0.158 kPa−1, with a repeatable pressure response and ignorable hysteresis under fatigue stimulus (Kim et al., 2019). In recent years, various flexible tactile sensor-based liquid metals have been developed for long-term monitoring of human signals in disease diagnosis (Liu L. et al., 2022).
In recent years, micro-/nanomaterial-based composite materials have attracted considerable research interest in flexible electronics by reasons of excellent carrier mobility, flexibility, and low cost, holding great promise for high-performance flexible tactile sensors. Micro/nano conductive materials mainly include graphene, graphene oxide (GO), carbon nanotubes (CNTs), carbon black (CB), and nanowires/nanoparticles (NW/NPs), which are commonly mixed with polymers to produce conductive composites.
CB (Figure 1C) is a type of paracrystalline carbon comprising spherical particles with significant carbon layer ordering, with the size ranging from tens to a few hundred nanometers. There are honeycomb-like micropores inside carbon black. Electrons can move in micropores, forming conductive pathways. The conductivity of carbon black-based active materials is significantly enhanced after the addition of carbon black to the matrix (Fu et al., 2020). The combination of low-cost production and high electrical conductivity allows CB to be considered an essential component of conductive networks. Wu et al. designed a multi-functional pressure sensor based on a carbon black sponge with a micro-crack design, which can meet the requirements of ultra-small and large-scale motion monitoring through layer-by-layer assembly (Wu et al., 2016). However, most of the dangling bonds at the edges of the carbon layer are bonded to hydrogen bonds. The conjugated structure of the carbon layer is disrupted, resulting in a decrease in conductivity, causing higher electric potential for flexible tactile sensors to operate.
CNT (Figure 1D) is a one-dimensional carbon nanomaterial with excellent strength, superior conductivity, good optical transparency, and outstanding thermal stability. It can be synthesized through various methods, such as chemical vapor deposition, laser ablation, and arc discharge. A single nanotube shows superior conductivity, with the current levels of up to 25 μA per tube (Wang et al., 2013). A nanofiber/nanotube aerogel tactile sensor was developed by cellulose nanofibers with excellent mechanical properties, which are functionalized by small walled carbon nanotubes. Carbon nanotubes form conductive networks inside the nanofiber/nanotube aerogel. They exhibit an elastic mechanical behavior, which combines with a reversible electrical response under compression to achieve responsive conductivity and pressure sensing. A pressure change of 0.1 bar causes a relative change of 10% in resistance. The electrical properties of CNTs play an important role in the performance of CNT-based active materials, which depend on the type, size, and orientation of CNTs in the polymer matrix.
The superior electron mobility, excellent strength, and low resistance of graphene are attributed to the two-dimensional structure of carbon atoms with a honeycomb lattice. The laminated configuration enables adjacent overlapping graphene layers (Figure 1E) to shift the overlapping region by reversible sliding (Liu et al., 2016). It can be selected as building blocks, which are then assembled into graphene-based active materials. Liu et al. reported a high-performance strain sensor with a fish-scale graphene sensing layer, which is manufactured by stretching/releasing a composite film of reduced graphene oxide and elastic bands. It can be used to detect stretching and bending deformation with a wide sensing range, high sensitivity, and ultra-low detection limit (Liu et al., 2016). The laminated configuration enables adjacent overlapping graphene layers (Figure 1E) to shift the overlapping region by reversible sliding (Liu et al., 2016). In addition, graphene oxide (GO) is electrically insulated. It can have the functions of electric conductivity after being reduced by employing a chemical method or thermal method.
One-dimensional nanostructured materials (such as nanowires) are provided with outstanding electrical conductivity and excellent flexibility and hence are expected to be competitive materials in the flexible tactile sensor (Akter and Kim, 2012; Wei et al., 2016). The good optical transparency of nanowires even achieves a breakthrough in the transparency of flexible tactile sensors. Apart from nanowires, nanoparticles have also been considered for the construction of conductive networks via a variety of methods (screen-printing or inkjet printing) because of their low cost, eco-friendly nature, and scalability. In addition, nanowire-/nanoparticle-based one-dimensional nanostructured materials (Figure 1F) can integrate the advantages and disadvantages of each material by combining two or more different materials, indicating significant latent capacity in the construction of conductive networks for flexible tactile sensors. Shu Gong et al. developed a high-sensitivity tactile sensor by sandwiching ultra-thin gold nanowire-impregnated paper between two thin polydimethylsiloxane sheets, which can be easily integrated and patterned in a large area to draw a spatial pressure distribution map (Gong et al., 2014). It is provided with great expectation owing to not only excellent mechanical and electrical performances, great stability, and remarkable human compatibility but also the ease of process by uncomplicated and cost-effective approaches.
Polypyrrole (Figure 1G) is a promising conductive polymer that has attracted widespread attention on account of its ease of production, good conductivity, biocompatibility, and great adhesion to a variety of materials. The good conductivity of polypyrrole is credited to an electron transfer along the conjugated π-molecular orbital skeleton and the movement of charge carriers (Li et al., 2014). In addition, PEDOT-based materials are another competitive material for flexible tactile sensors because of their outstanding thermal stability, great transparency, and adjustable conductivity (10−4–10 (Guo et al., 2017) S*cm−1). Commercially available conductive polymers (CPs) of poly (3,4-ethylenedioxythiophene)/poly (styrenesulfonate) (PEDOT:PSS) (Figure 1H) are applied to various well-known flexible tactile sensors. It is easily handled by traditional common methods owing to its solubility in water, forming uniform slurries with a flexible matrix. Furthermore, hydrogels (Figure 1I) exhibit excellent properties in terms of electricity, mechanics, optics, and swelling/expansion features (Lin et al., 2020; Xia et al., 2021). Hydrogels have a three-dimensional network of polymers and abundant water. They possess a high degree of flexibility due to the abundant water content (Cui et al., 2018) and recently attracted significant attention owing to their potential application prospects as an impeccable material for flexible tactile sensors (Wirthl et al., 2017; Wallin et al., 2018). Guo et al. developed a tactile sensor based on the poly (amidoxime)/polyethyleneimine hydrogel by a hydrogen bonding interaction, which has broad application prospects in wearable sensing devices (Guo X. et al., 2023).
In recent years, as traditional fabrication techniques cannot agree with the personalized needs of people, various advanced manufacturing technologies have been used to manufacture physical objects, resulting in extreme and complex structures. Current methods to pattern flexible tactile sensors include photolithography, transfer printing, 3D printing, screen-printing, direct writing, inkjet printing, pattern transferring processes, spray/spin coating, drop casting and vacuum filtration processes, and solution deposition methods. In this section, the pros and cons of fabrication methods used for flexible tactile sensors are discussed. Table 2 shows the advantages and disadvantages of different preparation methods.
Photolithography (Figure 2A) is the most common process for making patterns and topographical molds. Significant well-developed manufacturing and processing methods with high consistency and excellent precision make it a distinguished candidate for flexible tactile sensors as well. However, it has a high preparative cost.
FIGURE 2. Processing/fabrication methods: (A) photolithography, (B) transfer printing, (C) 3D printing, (D) screen printing, (E) inkjet printing, (F) spray/spin coating, (G) pattern transferring, (H) vacuum filtration processes, and (I) drop casting (Mack et al., 2006; Song et al., 2009; Khan et al., 2015; Carey et al., 2017; Boutry et al., 2018; Liu et al., 2018; Abbasi et al., 2020; Chen et al., 2021; Guan et al., 2022).
Transfer printing can be performed over large areas of uniform or segmented nanomembranes/ribbons using flexible structure stamps. It is usually used to obtain micro/nanopatterns on flat areas (such as wafers and glasses) and then transfer them onto flexible complex substrates with a flexible stamp. Figure 2B shows the processing programs involved in achieving the micro/nanopatterns by transfer printing. A conformable polydimethylsiloxane (PDMS) stamp is applied to pick up the free-standing microstructure silicon from the top of Si wafers and transfer it rapidly with controlled orientation to a flexible substrate (Mack et al., 2006). The type of adhesive stamping is significantly valuable for complex micro-structure processing.
3D printing (Figure 2C) has been followed with interest, attributed to its simplicity in manufacturing, ability to customize microstructures, diverse types of printable materials, and low cost (Liu et al., 2018). 3D printing typically uses a heating nozzle to melt polymer filaments to fabricate objective models or a syringe nozzle to extrude printable ink with fitted rheological properties to fabricate flexible tactile sensors. A variety of printable materials can be modified with the required rheological performance, offering significant advantages for the manufacturing of flexible tactile sensors. This process provides excellent flexibility in the manufacture of enormously complex 3D flexible tactile sensors, which simulate the tactile perceptions of human skin to translate touch reception information such as tension, pressure, shear, torsion, bend, and vibration into electrical signals and play a significant effect on the application of flexible electronic skin (Frutiger et al., 2015; Yan et al., 2016).
The screen printer (Figure 2D) is provided with a sample structure including a screen, squeegee, press bed, and substrate. The screen printer is more generic than those of other methods due to the advantages of adaptability, affordability, and simplicity. The flexible tactile sensor can be developed quickly with several steps and can be reproduced by repeating the optimum operating procedure of screen printing. It should be pointed out that the printing quality and characteristics are influenced by a variety of factors, such as printing speed, solution viscosity, scraper angle, and geometric shape (Jabbour et al., 2001). Screen printing is inclined to high-viscosity inks. Without appropriate adjustments to ink performance and mesh size, a value of 50–100 µm is a common printing resolution with a thickness of several micrometers. The feasibility of screen printing for flexible tactile sensors is verified by a variety of flexible electronics devices (Chang et al., 2009). A variety of materials can be integrated into the screen-printed paste to enhance the sensing performance, which can be classified into three main classes, inorganic (Au, Ag, graphene, etc.), organic (polyaniline, polypyrrole, etc.), and composite (chitosan–Au nanocomposite, CNT-based composite, etc.). (Ong et al., 2021). Among a series of metals used for printed tactile sensors, Ag-based pastes are the most common material attribute for excellent electrical properties. In addition to silver solutions, carbon- and copper-based inks are often frequently selected in the preparation of flexible tactile sensors.
Inkjet printing (Figure 2E) is a high-speed patterning method for the direct patterning of liquid ink with low viscosities by a micrometer-sized inkjet nozzle. The droplets are sprayed with relevant pulses generated by the actuators, which enable specific patterns to be printed directly on the substrates with no masks. In addition, inkjet printing projects individual ink droplets from the nozzle to the desired position to avoid waste, making it a low-cost preparation procedure. Furthermore, inkjet printing is capable of producing a high-precision pattern, attributed to the small size of the droplets (Lakafosis et al., 2010). Zheng et al. show pictures of different patterned electronic devices fabricated by an inkjet printer on a flexible flat (Zheng et al., 2013). By increasing the electric field with the distance between the flexible substrate and the nozzle, the thickness of electronic devices within the nanometer range can be easily realized. It has been successfully applied to manufacture a series of flexible tactile sensors, in particular. The primary weakness of inkjet printing is that certain types of conductive inks are incompatible, attributed to large particle size and nozzle blockage.
Spray/spin coating (Figure 2F) is a simple and low-cost method to fabricate flexible patterned films, which is one of the most general ways of extensive deposition (Lipomi et al., 2011; Wang et al., 2019). Nevertheless, the manufacturing accuracy is relatively low, attributed to airbrush, which increased preparing costs and reduced reliability. To overcome this difficulty, a spray coating method combining a digital x–y plotter and a heated substrate is created to manufacture a CNT-based pattern film (Wan et al., 2017). However, the CNT-based pattern film deposited by the spray coating needs to be a properly functionalized substrate to achieve excellent adhesion (Fu and Yu, 2014).
In the pattern transfer process (Figure 2G), pattern arrays were pre-formed on the substrate, and then, the functional materials formed the required structural array by means of reverse molding. The pattern transfer process is more cost-effective and time-effective than traditional photolithography in the realization of flexible tactile sensors.
Solution-based micro/nanomaterials can be easily coated onto the substrate and formed into patterns through the methods of drop casting (Figure 2H) and vacuum filtration (Figure 2I) (Jeong et al., 2015; Eslamian and Soltani-Kordshuli, 2018). Drop-casting is simple, low cost, and controllable compared with other coating methods (Huang J. F. et al., 2015; Hong et al., 2017). However, the uniformity of the film prepared by drop casting is quite low, attributed to the coffee-ring effect, accompanied by the limitation of large-scale coverage (Deegan et al., 1997). In order to upgrade the uniformity, Zhao et al. studied the interfacial influence between the substrate surface and the reduced graphene oxide. It is indicated that the catechol unit has an effect on the uniform reduced graphene oxide film on the flexible substrate. Therefore, functional modifications to materials are helpful in manufacturing flexible tactile sensors on flexible substrates using drop casting and vacuum filtration methods (Zhang et al., 2014; Zhao et al., 2014; Hossain et al., 2019).
Flexible tactile sensors have substantial potential applications. Low-strain flexible tactile sensors are able to monitor structure health, stress/strain, etc. Meanwhile, largely stretchable tactile sensors can be integrated with humans, attaching to clothing or directly laminating onto skin, for movement monitoring, ranging from small deformation caused by respiration and pulse to large deformation such as stretching, bending, and twisting of body joints. In addition, flexible tactile sensors might be good for stress monitoring in soft robots (Amjadi et al., 2016). They exhibit different working ranges and sensing performances, which made it possible to adapt our detection methods to different environments (Yao et al., 2015). A large number of application examples have proven the possibility of flexible tactile sensors in human signal monitoring, robotic tactile sensing, and human–computer interaction.
With the increasing attack rate of chronic diseases such as hypertension and diabetes, an increasing number of people begin to follow medical care with interest. It is necessary for long-term monitoring of patients for the treatment of chronic diseases. However, traditional medical equipment is cumbersome, making it unsuitable for long-term monitoring. Flexible tactile sensors can be integrated into the wrist and chest to record blood pressure, pulse, and respiratory rate, which is highly related to human health (Figures 3A–E). For example, cellulose composite-based flexible tactile sensors with excellent sensitivity have shown outstanding performance in pulse recording (Chen S. et al., 2018) and respiratory rate (Chen Y. et al., 2018) detection. It exhibits precise peak changes and good stability under pressure (Huang H. D. et al., 2015; Guo et al., 2022a). In addition, a cost-efficient method has been put forward to manufacture multifunctional three-dimensional carbon nanofiber network-based flexible tactile sensors with excellent stress sensitivity using the electrospinning technique. The stress sensitivity of the carbon nanofiber network-based flexible tactile sensor is 1.41 kPa−1, (Han et al., 2019), which also shows repeatable elasticity, great flexibility, and significant compressibility (>95%). Vocal cord vibration, pulse fluctuations, lung breathing, and limb movements are detected by flexible tactile sensors (Li Z. et al., 2020). Overall, flexible tactile sensors will play a significant role in the human health monitoring field, attributed to the advantages of being light weight, having good elasticity, facilities for put on, and long-term monitoring.
FIGURE 3. Human signal monitoring. (A) User-interactive touching; (B) swallowing; (C) twisting motion of the wrist; (D) vocal cord vibration detection; (E) artery pulse pressure; (F) human motions, including walking and jogging; (G) a flexible tactile sensor composed of parallel assemblies of elastomeric light guides; and (H) multilocation decoupling and multimodal deformation decoupling (Bauer, 2013; Park et al., 2015; Han et al., 2019; Bai et al., 2020; Li Z. et al., 2020; Ning et al., 2020).
Flexible tactile sensors can be integrated into the skin of limbs to collect motion signals, which is conducive to evaluating the state of muscle contraction and relaxation. It can also be installed on the human joints to detect a variety of motion modes in real-time, such as walking, jumping, running, and squatting (Figure 3F). In addition, it is possible to evaluate the posture of athletes and adjust the exercise plan in a timely manner by feedback information to upgrade the training efficiency. A flexible tactile sensor is developed, which is made up of elastic light-guide parallel components (Figure 3G). The flexible tactile sensor can detect the position, size, and mode of mechanical deformation (stretching, bending, or pressing) (Wang et al., 2022; Guo X. H. et al., 2023). The flexible tactile sensor is integrated with a wireless glove, which demonstrates the applications of multi-position decoupling and multi-mode deformation decoupling (Figure 3H).
Tactile perception is necessary for precise operations of objects, which will provide crucial tactile perception for robots. Flexible tactile sensors can enhance the safety of object operation and the accuracy of object detection (Figure 4A). In addition, adaptation is a special characteristic of human skin. Attributed to the complexity of sensing mechanisms, only high-precision or bulky handheld instruments are applied to detect material compliance. Flexible tactile sensors are provided with compliance mapping, which can offer a human-like sensation for the robot system when grasping objects composed of multiple materials with varied compliance. It enables the robot to deal with a variety of sophisticated and complex missions on material classification (Figure 4B), normal force, and tangential force classification (Figure 4C). A novel flexible tactile sensor-based porous polydimethylsiloxane is fabricated with a wide pressure-sensing range by optimizing the porosity of the dielectric layer. A wearable fitness hat is manufactured based on 16 flexible tactile sensor arrays to monitor the pressure on the tester’s head (Figure 4D). The real-time spatial distribution of pressure is provided by the wearable fitness hat, which helps observe and understand the correct fit of the helmet in modern sports. Furthermore, a flexible tactile sensor enabling intelligent perception is prepared, which was integrated into the robotic surface to achieve a variety of complex operations (Figure 4E). It is indicated that the flexible tactile sensor is provided with the capability of classifying a variety of materials with excellent sensitivity (Figure 4F). By combining collected signals with machine learning, it can accurately identify different tasks, which shows a classification accuracy rate of 94%. In addition, a flexible tactile sensor-based electronic hat with multi-responsiveness was invented (Liu et al., 2019). The flexible tactile sensor, by fully mimicking human skin, can detect multiple signals of pressure, surface roughness, and airflow rate similar to those of human skin. Inspired by the structural color regulation capability of chameleons, a flexible tactile sensor is proposed for simultaneous tactile sensing and interactive color changing (Figure 4G). All of those flexible tactile sensors provided substantial information for operating a robot’s arm in a variety of missions, indicating prospective applications in robots with tactile feedback (Figure 4H).
FIGURE 4. Environmental signal monitoring. (A) Responses to various hand motions. (B) A robotic hand with an integrated compliance sensor array touching a strawberry. (C) A flexible tactile sensor mounted on an artificial hand was exposed to shear force with a ping-pong ball. (D) Flexible tactile sensing fit cap demonstration. (E) A group of example signal maps when the robot hand grips seven types of garbage. (F) Softness detection. (G) Interactive color changes with pressure. (H) Fabrication of a sensor network to measure the spatial distribution of an input pressure signal (two lady beetles placed at two locations) (Pang et al., 2012; Boutry et al., 2018; Liang et al., 2019; Sun et al., 2019; Li G. et al., 2020; Beker et al., 2020; Liu et al., 2020; Masihi et al., 2021).
Perception and interaction are the foundation to achieve communication between the virtual and physical worlds of humans and the environment (Figure 5). Conventional hard electronic devices cannot afford conformable attachment with the human skin or soft robots, which constrain information communication and interaction between the virtual and physical space (Ma et al., 2020). Currently, the main goal of researchers is to establish a smart human–machine interface system with flexible tactile sensors, which is used to obtain the physiological signals of humans to control intelligent robots or other objects (Guo et al., 2022b; Guo et al., 2022c). For example, a flexible strain sensor based on cellulose composites is invented to develop intelligent gloves. Physiological signals of bending fingers are obtained by the flexible tactile sensor, which controls intelligent robots with a controller and reduces the deviation with real-time feedback. It is indicated that intelligent gloves can perform surgery or some delicate and dangerous tasks that humans cannot complete (Figure 5A). In addition, flexible tactile sensors are used to mimic the functions of human sensory nerves (Figure 5B). Artificial afferent nerves collect stress signals from clusters of tactile sensors and convert the stress signal into action potentials using ring oscillators. Moreover, a flexible tactile microarray sensor-based graphene aerogel with ultrasensitivity and ultrastability was developed (Figure 5C), which achieved high accuracy (80%) in artificially intelligent touch identification that outperformed that of human fingers (30%). Due to its excellent sensitivity, low manufacturing cost, and flexibility, the intelligent system fabricated with flexible tactile sensors has the advantage of digital recognition over the conventional system (Figure 5D).
FIGURE 5. Human–computer interaction. (A) Tactile response during a grasp and manipulation task. (B) A hybrid reflex arc made of an artificial afferent nerve and a biological efferent nerve. (C) Grabbing of a soft ball, enabling tactile feedback. (D) A robotic finger with a microarray sensor is touching the letter patterns of collected letter images of A to Z through flow (Gerratt et al., 2015; Núñez et al., 2017; Kim et al., 2018; Pang et al., 2020).
The human–machine interface (HMI) provides opportunities for the interaction between humans and machines, contributing a significant effect in remotely operating robots. The traditional HMI based on bulky, rigid, and costly machines mainly concentrates on robot/machine control but lacks sufficient feedback to humans, which significantly constraints business applications in executing complex missions. With increasing demands for intuitive and effective manipulation, closed-loop HMIs with both precise sensing and feedback functions are essential. A tactile feedback intelligent glove with flexible tactile sensors has been proposed for the virtual reality system. In virtual space, electrical signals with different degrees of freedom on human hands are used to detect multi-directional bending and sliding states. Object detection can be realized by it with an accuracy rate of 96% (Figure 6A). In addition, a closed-loop HMI system based on flexible tactile sensors is also developed, which is compatible with the entire body and provides wireless movement capture and tactile feedback through the internet, wireless fidelity, and Bluetooth (Figure 6B). Closed-loop HMI-integrated tactile virtual reality shows tremendous potential in various fields such as entertainment, household healthcare, sports exercise, non-contact biological sample collection, and infectious disease patient care.
FIGURE 6. Human computer interaction. (A) Haptic-feedback smart glove as a creative human‒machine interface for virtual augmented reality applications and (B) electronic skin as wireless human‒machine interfaces for robotic VR (Zhu et al., 2020; Liu Y. M. et al., 2022)
Flexible tactile sensors have made important progress in materials and processing/fabrication methods. The essential features, such as excellent sensitivity, quick response, low cost, and stretchability/flexibility, have been significantly enhanced. Compared to traditional fabrication techniques such as photolithography, new fabrication techniques are provided with more cost-effective methods as they do not need costly masks or facilities. Using the direct deposition method, the time from design to production of flexible tactile sensors is saved, and the waste of materials is minimized. New preparation methods are provided to manufacture flexible tactile sensors with customized geometries to satisfy the dimensional requirements and to upgrade their properties. It is crucial to utilize those technological innovations to address the obstructions to manufacturing flexible tactile sensors. In summary, new preparation methods for the development of flexible/stretchable tactile sensors paved the way for compliant sensing systems that conform to the complex unstructured skin of humans/robots.
Various aspects of people’s lives are put forward to intelligence and intelligent systems. It is indicated that incorporating various flexible tactile sensors into new manufactures will broaden the scope of applications in the future. At present, researchers mainly focus on improving the sensitivity of flexible tactile sensors. However, a variety of factors including the complexity of the environment and compatibility with soft robots are overlooked. High integration, multifunctionality, and extensive flexible tactile sensor coverage will proceed to be one of the most important future challenges in the sight of hardware. In the process of physical interaction with the environment, it is necessary to apply a large number of flexible tactile sensors to obtain complex information on a large area. Furthermore, a tactile signal can be integrated with data from other sensors to upgrade recognition accuracy (Someya et al., 2004; Someya et al., 2005; Takei et al., 2010; Zang et al., 2015). Furthermore, it is necessary to develop computational methods that run near or within sensor networks to reduce redundant data transfer between sensing and processing units to effectively process such a large amount of data and reduce energy dissipation (Zhou et al., 2019). The new intelligent artificial systems may enable tactile sensing and memory functions as well as neuromorphic pre-processing with upgraded processing efficiency and a higher recognition rate in subsequent processing tasks (Zhou and Chai, 2020).
In terms of application, current human health signal monitoring is at the initial level of information recording, which is still a long way from intelligent diagnosis (Qiu et al., 2019; Wang et al., 2022). How to combine tactile signal monitoring with intelligent data processing methods to enable the integration of intelligent monitoring and diagnosis is an important development direction (Guo et al., 2022b; Guo et al., 2022d; Guo X. H. et al., 2023). Moreover, based on the natural advantages of combining with the human body, flexible tactile sensing technology can easily realize stress/strain sensing and feedback on the human skin interface, which greatly promotes the development of virtual reality technology. As a result, the combination of autonomous control algorithms and tactile data processing methods to achieve tactile dexterity is an important development trend (Xia et al., 2022). In addition, if the tactile signal can be directly transmitted to the nerve or even the brain, the human body’s direct perception of the external world would be realized, and the human tactile signal would be extended to biology or external equipment. Therefore, the combination of flexible sensing technology and biotechnology has important development potential in the future.
Y-FL: funding acquisition, writing–original draft, and writing–review and editing. WW: writing–review and editing. X-FC: writing–review and editing.
The author(s) declare financial support was received for the research and authorship of this article. This work was supported by the National Natural Science Foundation of China (Grant No. 12002190), the Fundamental Research Funds for the Central Universities (Grant No. SWU-KQ22029), the Chongqing Natural Science Foundation (Grant No. CSTB2022NSCQ-MSX1635), and the China Postdoctoral Science Foundation (Grant No. 2022M710524).
The authors declare that the research was conducted in the absence of any commercial or financial relationships that could be construed as a potential conflict of interest.
All claims expressed in this article are solely those of the authors and do not necessarily represent those of their affiliated organizations, or those of the publisher, the editors, and the reviewers. Any product that may be evaluated in this article, or claim that may be made by its manufacturer, is not guaranteed or endorsed by the publisher.
Abbasi, R., Mayyas, M., Ghasemian, M. B., Centurion, F., Yang, J., Saborio, M., et al. (2020). Photolithography-enabled direct patterning of liquid metals. J. Mater. Chem. C 8 (23), 7805–7811. doi:10.1039/d0tc01466d
Ainsworth, C., Higuchi, K., Simou, E., Guyot, P., and Greene, N. (2022). Relative differences in brain volume loss with teriflunomide versus other disease-modifying therapies in relapsing multiple sclerosis: A systematic review and network meta-analysis. Mult. Scler. J. 28, 58–59. 1_Suppl.
Akter, T., and Kim, W. S. (2012). Reversibly stretchable transparent conductive coatings of spray-deposited silver nanowires. Acs Appl. Mater. Interfaces 4 (4), 1855–1859. doi:10.1021/am300058j
Amjadi, M., Kyung, K.-U., Park, I., and Sitti, M. (2016). Stretchable, skin-mountable, and wearable strain sensors and their potential applications: A review. Adv. Funct. Mater. 26 (11), 1678–1698. doi:10.1002/adfm.201504755
Bae, K., Kang, Y., Jo, E., Sim, S., Yang, W., and Kim, J. (2022). “Washable, inkjet-printed flexible tactile sensor on fabric with temperature tolerance,” in 2022 Ieee 35th International Conference on Micro Electro Mechanical Systems Conference (Mems), Tokyo, Japan, 9-13 January 2022, 79–82.
Bai, H., Li, S., Barreiros, J., Tu, Y., Pollock, C. R., and Shepherd, R. F. (2020). Stretchable distributed fiber-optic sensors. Science 370, 848–852. doi:10.1126/science.aba5504
Bauer, S. (2013). Flexible electronics: sophisticated skin. Nat. Mater. 12 (10), 871–872. doi:10.1038/nmat3759
Beker, L., Matsuhisa, N., You, I., Ruth, S. R. A., Niu, S., Foudeh, A., et al. (2020). A bioinspired stretchable membrane-based compliance sensor. P Natl. Acad. Sci. U. S. A. 117 (21), 11314–11320. doi:10.1073/pnas.1909532117
Boutry, C. M., Negre, M., Jorda, M., Vardoulis, O., Chortos, A., Khatib, O., et al. (2018). A hierarchically patterned, bioinspired E-skin able to detect the direction of applied pressure for robotics. Sci. Robotics 3, eaau6914. doi:10.1126/scirobotics.aau6914
Cai, L., and Wang, C. (2015). Carbon nanotube flexible and stretchable electronics. Nanoscale Res. Lett. 10 (1), 320. doi:10.1186/s11671-015-1013-1
Carey, T., Cacovich, S., Divitini, G., Ren, J., Mansouri, A., Kim, J. M., et al. (2017). Fully inkjet-printed two-dimensional material field-effect heterojunctions for wearable and textile electronics. Nat. Commun. 8 (1), 1202. doi:10.1038/s41467-017-01210-2
Castellanos-Ramos, J., Navas-Gonzalez, R., Macicior, H., Sikora, T., Ochoteco, E., and Vidal-Verdu, F. (2010). Tactile sensors based on conductive polymers. Microsyst. Technol. 16 (5), 765–776. doi:10.1007/s00542-009-0958-3
Castellanos-Ramos, J., Navas-Gonzalez, R., Ochoteco, E., and Vidal-Verdu, F. (2011). Finite element analysis of tactile sensors made with screen printing technology. Bioelectron. Biomed. Bioinspired Syst. V Nanotechnol. V 8068, 34–43. doi:10.1117/12.890092
Chang, W. Y., Fang, T. H., Lin, H. J., Shen, Y. T., and Lin, Y. C. (2009). A large area flexible array sensors using screen printing technology. J. Disp. Technol. 5 (4-6), 178–183. doi:10.1109/jdt.2008.2004862
Chen, S., Song, Y. J., and Xu, F. (2018a). Flexible and highly sensitive resistive pressure sensor based on carbonized crepe paper with corrugated structure. Acs Appl. Mater. Interfaces 10 (40), 34646–34654. doi:10.1021/acsami.8b13535
Chen, W. H., Xu, Y., Chen, Z. Y., Zeng, P. Y., Dang, R. J., Chen, R., et al. (2022). Bidirectional sim-to-real transfer for GelSight tactile sensors with CycleGAN. Ieee Robotics Automation Lett. 7 (3), 6187–6194. doi:10.1109/lra.2022.3167064
Chen, W. M., Luo, M., Yang, K., Liu, C. Z., Zhang, D. T., and Zhou, X. Y. (2021). MXene loaded onto clean wiper by a dot-matrix drop-casting method as a free-standing electrode for stretchable and flexible supercapacitors. Chem. Eng. J. 423, 130242. doi:10.1016/j.cej.2021.130242
Chen, X. G., Liu, B. C., Wang, Y. J., Cui, H. Y., Dong, J. W., Ma, R. J., et al. (2023). Optimizing stimulus frequency ranges for building a high-rate high frequency SSVEP-BCI. Ieee T Neur Sys Reh 31, 1277–1286. doi:10.1109/tnsre.2023.3243786
Chen, Y., Potschke, P., Pionteck, J., Voit, B., and Qi, H. S. (2018b). Smart cellulose/graphene composites fabricated by in situ chemical reduction of graphene oxide for multiple sensing applications. J. Mater. Chem. A 6 (17), 7777–7785. doi:10.1039/c8ta00618k
Choi, T. Y., Hwang, B. U., Kim, B. Y., Trung, T. Q., Nam, Y. H., Kim, D. N., et al. (2017). Stretchable, transparent, and stretch-unresponsive capacitive touch sensor array with selectively patterned silver nanowires/reduced graphene oxide electrodes. ACS Appl. Mater. Interfaces 9 (21), 18022–18030. doi:10.1021/acsami.6b16716
Cui, K., Sun, T. L., Liang, X., Nakajima, K., Ye, Y. N., Chen, L., et al. (2018). Multiscale energy dissipation mechanism in tough and self-healing hydrogels. Phys. Rev. Lett. 121 (18), 185501. doi:10.1103/physrevlett.121.185501
Deegan, R. D., Bakajin, O., Dupont, T. F., Huber, G., Nagel, S. R., and Witten, T. A. (1997). Capillary flow as the cause of ring stains from dried liquid drops. Nature 389 (6653), 827–829. doi:10.1038/39827
Eslamian, M., and Soltani-Kordshuli, F. (2018). Development of multiple-droplet drop-casting method for the fabrication of coatings and thin solid films. J. Coat. Technol. Res. 15 (2), 271–280. doi:10.1007/s11998-017-9975-9
Forrest, S. R. (2004). The path to ubiquitous and low-cost organic electronic appliances on plastic. Nature 428 (6986), 911–918. doi:10.1038/nature02498
Frutiger, A., Muth, J. T., Vogt, D. M., Menguc, Y., Campo, A., Valentine, A. D., et al. (2015). Capacitive soft strain sensors via multicore-shell fiber printing. Adv. Mater. 27 (15), 2440–2446. doi:10.1002/adma.201500072
Fu, L., and Yu, A. M. (2014). Carbon nanotubes based thin films: fabrication, characterization and applications. Rev. Adv. Mater Sci. 36 (1), 40–61.
Fu, Y.-F., Yi, F.-L., Liu, J.-R., Li, Y.-Q., Wang, Z.-Y., Yang, G., et al. (2020). Super soft but strong E-skin based on carbon fiber/carbon black/silicone composite: truly mimicking tactile sensing and mechanical behavior of human skin. Compos. Sci. Technol. 186, 107910. doi:10.1016/j.compscitech.2019.107910
Gerratt, A. P., Michaud, H. O., and Lacour, S. P. (2015). Elastomeric electronic skin for prosthetic tactile sensation. Adv. Funct. Mater. 25 (15), 2287–2295. doi:10.1002/adfm.201404365
Gong, S., Schwalb, W., Wang, Y., Chen, Y., Tang, Y., Si, J., et al. (2014). A wearable and highly sensitive pressure sensor with ultrathin gold nanowires. Nat. Commun. 5, 3132. doi:10.1038/ncomms4132
Guan, R. Q., Zou, F. X., Li, D., and Yao, Y. F. (2022). A high-thermal-stability, fully spray coated multilayer thin-film graphene/polyamide-imide nanocomposite strain sensor for acquiring high-frequency ultrasonic waves. Compos. Sci. Technol. 227, 109628. doi:10.1016/j.compscitech.2022.109628
Guo, S. Z., Qiu, K. Y., Meng, F. B., Park, S. H., and McAlpine, M. C. (2017). 3D printed stretchable tactile sensors. Adv. Mater. 29 (27), 1701218. doi:10.1002/adma.201701218
Guo, X. H., Hong, W. Q., Hu, B., Zhang, T. X., Jin, C. C., Yao, X. M., et al. (2023b). Human touch sensation-inspired, ultrawide-sensing-range, and high-robustness flexible piezoresistive sensor based on CB/MXene/SR/fiber nanocomposites for wearable electronics. Compos Struct. 321, 117329. doi:10.1016/j.compstruct.2023.117329
Guo, X. H., Hong, W. Q., Liu, L., Wang, D. D., Xiang, L., Mai, Z. H., et al. (2022b). Highly sensitive and wide-RangeFlexible bionic tactile sensors inspired by the Octopus sucker structure. Acs Appl. Nano Mater. 5 (8), 11028–11036. doi:10.1021/acsanm.2c02242
Guo, X. H., Hong, W. Q., Zhao, Y. N., Zhu, T., Li, H. J., Zheng, G. Q., et al. (2022c). Bioinspired sandwich-structured pressure sensors based on graphene oxide/hydroxyl functionalized carbon nanotubes/bovine serum albumin nanocomposites for wearable textile electronics. Compos Part a-Appl S 163, 107240. doi:10.1016/j.compositesa.2022.107240
Guo, X. H., Hong, W. Q., Zhao, Y. N., Zhu, T., Li, H. J., Zheng, G. Q., et al. (2022d). Bioinspired sandwich-structured pressure sensors based on graphene oxide/hydroxyl functionalized carbon nanotubes/bovine serum albumin nanocomposites for wearable textile electronics. Compos Part a-Appl S 163, 107240. doi:10.1016/j.compositesa.2022.107240
Guo, X. H., Zhou, D. Y., Hong, W. Q., Wang, D. D., Liu, T. Q., Wang, D., et al. (2022a). Biologically emulated flexible sensors with high sensitivity and low hysteresis: toward electronic skin to a sense of touch. Small 18 (32), e2203044. doi:10.1002/smll.202203044
Guo, X., Lu, Y. F., Fu, D. C., Yu, C. Y., Yang, X. G., and Zhong, W. B. (2023a). Ultrahigh ionic conductivity and alkaline tolerance of poly(amidoxime)-based hydrogel for high performance piezoresistive sensor. Chem. Eng. J. 452, 139208. doi:10.1016/j.cej.2022.139208
Han, Z., Cheng, Z., Chen, Y., Li, B., Liang, Z., Li, H., et al. (2019). Fabrication of highly pressure-sensitive, hydrophobic, and flexible 3D carbon nanofiber networks by electrospinning for human physiological signal monitoring. Nanoscale 11 (13), 5942–5950. doi:10.1039/c8nr08341j
Hong, S., Lee, J., Do, K., Lee, M., Kim, J. H., Lee, S., et al. (2017). Stretchable electrode based on laterally combed carbon nanotubes for wearable energy harvesting and storage devices. Adv. Funct. Mater. 27 (48), 1704353. doi:10.1002/adfm.201704353
Hossain, M. F., Heo, J. S., Nelson, J., and Kim, I. (2019). Paper-based flexible electrode using chemically-modified graphene and functionalized multiwalled carbon nanotube composites for electrophysiological signal sensing. Information 10 (10), 325–339. doi:10.3390/info10100325
Hou, C., Wang, H., Zhang, Q., Li, Y., and Zhu, M. (2014). Highly conductive, flexible, and compressible all-graphene passive electronic skin for sensing human touch. Adv. Mater 26 (29), 5018–5024. doi:10.1002/adma.201401367
Huang, H. D., Liu, C. Y., Zhang, L. Q., Zhong, G. J., and Li, Z. M. (2015b). Simultaneous reinforcement and toughening of carbon nanotube/cellulose conductive nanocomposite films by interfacial hydrogen bonding. Acs Sustain. Chem. Eng. 3 (2), 317–324. doi:10.1021/sc500681v
Huang, J. F., Chen, H., Niu, W. B., Fam, D. W. H., Palaniappan, A., Larisika, M., et al. (2015a). Highly manufacturable graphene oxide biosensor for sensitive interleukin-6 detection. RSC Adv. 5 (49), 39245–39251. doi:10.1039/c5ra05854f
Ishihara, T., Namiki, A., Ishikawa, M., and Shimojo, M. (2006). Dynamic pen spinning using a high-speed multifingered hand with high-speed tactile sensor. 6th Ieee-Ras Int. Conf. Humanoid Robots 1, 258. doi:10.1109/ICHR.2006.321394
Jabbour, G. E., Radspinner, R., and Peyghambarian, N. (2001). Screen printing for the fabrication of organic light-emitting devices. Ieee J. Sel. Top. Quant. 7 (5), 769–773. doi:10.1109/2944.979337
Jang, H., Park, Y. J., Chen, X., Das, T., Kim, M. S., and Ahn, J. H. (2016). Graphene-based flexible and stretchable electronics. Adv. Mater 28 (22), 4184–4202. doi:10.1002/adma.201504245
Jeong, Y. R., Park, H., Jin, S. W., Hong, S. Y., Lee, S. S., and Ha, J. S. (2015). Highly stretchable and sensitive strain sensors using fragmentized graphene foam. Adv. Funct. Mater. 25 (27), 4228–4236. doi:10.1002/adfm.201501000
Jung, S., Kim, J. H., Kim, J., Choi, S., Lee, J., Park, I., et al. (2014). Reverse-micelle-induced porous pressure-sensitive rubber for wearable human-machine interfaces. Adv. Mater. 26 (28), 4825–4830. doi:10.1002/adma.201401364
Khan, S., Tinku, S., Lorenzelli, L., and Dahiya, R. S. (2015). Flexible tactile sensors using screen-printed P(VDF-TrFE) and MWCNT/PDMS composites. Ieee Sensors J. 15 (6), 3146–3155. doi:10.1109/jsen.2014.2368989
Kim, J., Jung, H., Kim, M., Bae, H., and Lee, Y. (2021). Conductive polymer composites for soft tactile sensors. Macromol. Res. 29 (11), 761–775. doi:10.1007/s13233-021-9092-6
Kim, K., Choi, J., Jeong, Y., Cho, I., Kim, M., Kim, S., et al. (2019). Highly sensitive and wearable liquid metal-based pressure sensor for health monitoring applications: integration of a 3d-printed microbump array with the microchannel. Adv. Healthc. Mater. 8 (22), 1900978. doi:10.1002/adhm.201900978
Kim, Y., Chortos, A., Xu, W., Liu, Y., Oh, J. Y., Son, D., et al. (2018). A bioinspired flexible organic artificial afferent nerve. Science 360, 998–1003. doi:10.1126/science.aao0098
Ladd, C., So, J. H., Muth, J., and Dickey, M. D. (2013). 3D printing of free standing liquid metal microstructures. Adv. Mater. 25 (36), 5081–5085. doi:10.1002/adma.201301400
Lakafosis, V., Rida, A., Vyas, R., Yang, L., Nikolaou, S., and Tentzeris, M. M. (2010). Progress towards the first wireless sensor networks consisting of inkjet-printed, paper-based RFID-enabled sensor tags. Proc. Ieee 98 (9), 1601–1609. doi:10.1109/jproc.2010.2049622
Lee, T., Kang, Y. S., Kim, K., Sim, S., Bae, K., Kwak, Y., et al. (2022). All paper-based, multilayered, inkjet-printed tactile sensor in wide pressure detection range with high sensitivity. Adv. Mater. Technol. 7 (2), 2100428. doi:10.1002/admt.202100428
Lee, Y. Y., Kang, H. Y., Gwon, S. H., Choi, G. M., Lim, S. M., Sun, J. Y., et al. (2016). A strain-insensitive stretchable electronic conductor: PEDOT:PSS/Acrylamide organogels. Adv. Mater. 28 (8), 1636–1643. doi:10.1002/adma.201504606
Li, G., Liu, S., Wang, L., and Zhu, R. (2020a). Skin-Inspired quadruple tactile sensors integrated on a robot hand enable object recognition. Sci. Adv. 5 (49), eabc8134. doi:10.1126/scirobotics.abc8134
Li, M. F. F., Li, H. Y., Zhong, W. B., Zhao, Q. H., and Wang, D. (2014). Stretchable conductive polypyrrole/polyurethane (PPy/PU) strain sensor with netlike microcracks for human breath detection. ACS Appl. Mater. Interfaces 6 (2), 1313–1319. doi:10.1021/am4053305
Li, Z., Zhang, S., Chen, Y., Ling, H., Zhao, L., Luo, G., et al. (2020b). Gelatin methacryloyl-based tactile sensors for medical wearables. Adv. Funct. Mater. 30 (49), 2003601. doi:10.1002/adfm.202003601
Liang, Z. W., Cheng, J. H., Zhao, Q., Zhao, X. W., Han, Z. Y., Chen, Y., et al. (2019). High-performance flexible tactile sensor enabling intelligent haptic perception for a soft prosthetic hand. Adv. Mater. Technol. 4 (8), 1900317. doi:10.1002/admt.201900317
Lin, L. W., Wang, L., Li, B., Luo, J. C., Huang, X. W., Gao, Q., et al. (2020). Dual conductive network enabled superhydrophobic and high performance strain sensors with outstanding electro-thermal performance and extremely high gauge factors. Chem. Eng. J. 385, 123391. doi:10.1016/j.cej.2019.123391
Lipomi, D. J., Vosgueritchian, M., Tee, B. C. K., Hellstrom, S. L., Lee, J. A., Fox, C. H., et al. (2011). Skin-like pressure and strain sensors based on transparent elastic films of carbon nanotubes. Nat. Nanotechnol. 6 (12), 788–792. doi:10.1038/nnano.2011.184
Liu, C. Y., Huang, N. G., Xu, F., Tong, J. D., Chen, Z. W., Gui, X. C., et al. (2018). 3D printing technologies for flexible tactile sensors toward wearable electronics and electronic skin. Polymers-Basel 10 (6), 629. doi:10.3390/polym10060629
Liu, D., Cao, T. A., Wang, Q. S., Zhang, M. Y., Jiang, X. R., and Sun, J. W. (2023). Construction and analysis of functional brain network based on emotional electroencephalogram. Med. Biol. Eng. Comput. 61 (2), 357–385. doi:10.1007/s11517-022-02708-8
Liu, L., Huang, H., Wang, X., He, P., and Yang, J. (2022a). Recent advances in printed liquid metals for wearable healthcare sensors: A review. J. Phys. D Appl. Phys. 55 (28), 283002. doi:10.1088/1361-6463/ac5cab
Liu, Q., Chen, J., Li, Y. R., and Shi, G. Q. (2016). High-performance strain sensors with fish-scale-like graphene-sensing layers for full-range detection of human motions. Acs Nano 10 (8), 7901–7906. doi:10.1021/acsnano.6b03813
Liu, Y.-F., Huang, P., Li, Y.-Q., Liu, Q., Tao, J.-K., Xiong, D.-J., et al. (2019). A biomimetic multifunctional electronic hair sensor. J. Mater. Chem. A 7 (4), 1889–1896. doi:10.1039/c8ta10750e
Liu, Y. F., Liu, Q., Long, J. F., Yi, F. L., Li, Y. Q., Lei, X. H., et al. (2020). Bioinspired color-changeable organogel tactile sensor with excellent Overall performance. ACS Appl. Mater. Interfaces 12 (44), 49866–49875. doi:10.1021/acsami.0c12811
Liu, Y. M., Yiu, C. K., Song, Z., Huang, Y., Yao, K. M., Wong, T., et al. (2022b). Electronic skin as wireless human-machine interfaces for robotic VR. Sci. Adv. 8 (2), eabl6700. doi:10.1126/sciadv.abl6700
Ma, Y., Li, H., Chen, S., Liu, Y., Meng, Y., Cheng, J., et al. (2020). Skin-like electronics for perception and interaction: materials, structural designs, and applications. Adv. Intell. Syst. 3 (4), 2000108. doi:10.1002/aisy.202000108
Mack, S., Meitl, M. A., Baca, A. J., Zhu, Z. T., and Rogers, J. A. (2006). Mechanically flexible thin-film transistors that use ultrathin ribbons of silicon derived from bulk wafers. Appl. Phys. Lett. 88 (21), 213101. doi:10.1063/1.2206688
Masihi, S., Panahi, M., Maddipatla, D., Hanson, A. J., Bose, A. K., Hajian, S., et al. (2021). Highly sensitive porous PDMS-based capacitive pressure sensors fabricated on fabric platform for wearable applications. Acs Sensors 6 (3), 938–949. doi:10.1021/acssensors.0c02122
Mohan, B., Ma, S. X., Kumar, S., Yang, Y., and Ren, P. (2023). Tactile sensors: hydroxyl decorated silver metal-organic frameworks for detecting cr2o72-mno4-humic acid, and fe3+ions. Acs Appl. Mater. Interfaces 15 (13), 17317–17323. doi:10.1021/acsami.2c22871
Mondal, I., Ganesha, M. K., Singh, A. K., and Kulkarni, G. U. (2022). Inkjet printing aided patterning of transparent metal mesh for wearable tactile and proximity sensors. Mater. Lett. 312, 131724–131724.4. doi:10.1016/j.matlet.2022.131724
Ning, C., Dong, K., Cheng, R., Yi, J., Ye, C., Peng, X., et al. (2020). Flexible and stretchable fiber-shaped triboelectric nanogenerators for biomechanical monitoring and human-interactive sensing. Adv. Funct. Mater. 31 (4), 2006679. doi:10.1002/adfm.202006679
Núñez, C. G., Navaraj, W. T., Polat, E. O., and Dahiya, R. (2017). Energy-autonomous, flexible, and transparent tactile skin. Adv. Funct. Mater. 27 (18), 1606287. doi:10.1002/adfm.201606287
Ong, C. S., Ng, Q. H., and Low, S. C. (2021). Critical reviews of electro-reactivity of screen-printed nanocomposite electrode to safeguard the environment from trace metals. Monatsh Chem. 152 (7), 705–723. doi:10.1007/s00706-021-02802-x
Pang, C., Lee, G. Y., Kim, T. I., Kim, S. M., Kim, H. N., Ahn, S. H., et al. (2012). A flexible and highly sensitive strain-gauge sensor using reversible interlocking of nanofibres. Nat. Mater. 11 (9), 795–801. doi:10.1038/nmat3380
Pang, K., Song, X., Xu, Z., Liu, X., Liu, Y., Zhong, L., et al. (2020). Hydroplastic foaming of graphene aerogels and artificially intelligent tactile sensors. Sci. Adv. 6, eabd4045. doi:10.1126/sciadv.abd4045
Park, J., Kim, M., Lee, Y., Lee, H. S., and Ko, H. (2015). Fingertip skin-inspired microstructured ferroelectric skins discriminate static/dynamic pressure and temperature stimuli. Sci. Adv. 1 (9), e1500661. doi:10.1126/sciadv.1500661
Park, Y. G., Lee, G. Y., Jang, J., Yun, S. M., Kim, E., and Park, J. U. (2021). Liquid metal-based soft electronics for wearable healthcare. Adv. Healthc. Mater 10 (17), e2002280. doi:10.1002/adhm.202002280
Qiu, J., Guo, X. H., Chu, R., Wang, S. L., Zeng, W., Qu, L., et al. (2019). Rapid-response, low detection limit, and high-sensitivity capacitive flexible tactile sensor based on three-dimensional porous dielectric layer for wearable electronic skin. ACS Appl. Mater. Interfaces 11 (43), 40716–40725. doi:10.1021/acsami.9b16511
Sato, K., Canete, L., and Takahashi, T. (2019). Development of a spray-coated tactile sensor - prototype and modeling of 2D sensor on cylindrical surface. J. Robot. Mechatron. 31 (6), 882–893. doi:10.20965/jrm.2019.p0882
Someya, T., Kato, Y., Sekitani, T., Iba, S., Noguchi, Y., Murase, Y., et al. (2005). Conformable, flexible, large-area networks of pressure and thermal sensors with organic transistor active matrixes. P Natl. Acad. Sci. U. S. A. 102 (35), 12321–12325. doi:10.1073/pnas.0502392102
Someya, T., Sekitani, T., Iba, S., Kato, Y., Kawaguchi, H., and Sakurai, T. (2004). A large-area, flexible pressure sensor matrix with organic field-effect transistors for artificial skin applications. P Natl. Acad. Sci. U. S. A. 101 (27), 9966–9970. doi:10.1073/pnas.0401918101
Song, X. H., Liu, S., Gan, Z. Y., Lv, Q., Cao, H., and Yan, H. (2009). Controllable fabrication of carbon nanotube-polymer hybrid thin film for strain sensing. Microelectron. Eng. 86 (11), 2330–2333. doi:10.1016/j.mee.2009.04.012
Sun, Q. J., Zhao, X. H., Zhou, Y., Yeung, C. C., Wu, W., Venkatesh, S., et al. (2019). Fingertip-skin-Inspired highly sensitive and multifunctional sensor with hierarchically structured conductive graphite/polydimethylsiloxane foams. Adv. Funct. Mater. 29 (18), 1808829. doi:10.1002/adfm.201808829
Takei, K., Takahashi, T., Ho, J. C., Ko, H., Gillies, A. G., Leu, P. W., et al. (2010). Nanowire active-matrix circuitry for low-voltage macroscale artificial skin. Nat. Mater. 9 (10), 821–826. doi:10.1038/nmat2835
Wallin, T. J., Pikul, J., and Shepherd, R. F. (2018). 3D printing of soft robotic systems. Nat. Rev. Mater 3 (6), 84–100. doi:10.1038/s41578-018-0002-2
Wang, X., Sparkman, J., and Gou, J. H. (2017). Strain sensing of printed carbon nanotube sensors on Polyurethane substrate with spray deposition modeling. Compos Commun. 3, 1–6. doi:10.1016/j.coco.2016.10.003
Wang, C., Xia, K., Wang, H., Liang, X., Yin, Z., and Zhang, Y. (2019). Advanced carbon for flexible and wearable electronics. Adv. Mater 31 (9), e1801072. doi:10.1002/adma.201801072
Wang, M., Anoshkin, I. V., Nasibulin, A. G., Korhonen, J. T., Seitsonen, J., Pere, J., et al. (2013). Modifying native nanocellulose aerogels with carbon nanotubes for mechanoresponsive conductivity and pressure sensing. Adv. Mater. 25 (17), 2428–2432. doi:10.1002/adma.201300256
Wang, Y. F., Ruan, X. Y., Xing, C. W., Zhao, H. Q., Luo, M. M., Chen, Y. X., et al. (2022). Highly sensitive and flexible three-dimensional force tactile sensor based on inverted pyramidal structure. Smart Mater. Struct. 31 (9), 095013. doi:10.1088/1361-665x/ac7dcf
Wei, Y., Chen, S., Yuan, X., Wang, P. P., and Liu, L. (2016). Multiscale wrinkled microstructures for piezoresistive fibers. Adv. Funct. Mater. 26 (28), 5078–5085. doi:10.1002/adfm.201600580
Wen, Z. Y., Wu, Y., Zhang, Z. Y., Xu, S. L., Huang, S. L., and Li, Y. L. (2003). Development of an integrated vacuum microelectronic tactile sensor array. Sens. Actuat a-Phys 103 (3), 301–306. doi:10.1016/s0924-4247(02)00392-8
Wirthl, D., Pichler, R., Drack, M., Kettlguber, G., Moser, R., Gerstmayr, R., et al. (2017). Instant tough bonding of hydrogels for soft machines and electronics. Sci. Adv. 3 (6), e1700053. doi:10.1126/sciadv.1700053
Won, S. M., Wang, H., Kim, B. H., Lee, K., Jang, H., Kwon, K., et al. (2019). Multimodal sensing with a three-dimensional piezoresistive structure. ACS Nano 13 (10), 10972–10979. doi:10.1021/acsnano.9b02030
Wu, X. D., Han, Y. Y., Zhang, X. X., Zhou, Z. H., and Lu, C. H. (2016). Large-area compliant, low-cost, and versatile pressure-sensing platform based on microcrack-designed carbon Black@Polyurethane sponge for human-machine interfacing. Adv. Funct. Mater. 26 (34), 6246–6256. doi:10.1002/adfm.201601995
Xia, Y. Q., Gao, S., Yu, R. H., Zeng, Z. J., He, H., Zhou, X. H., et al. (2021). Near-infrared light induced dynamic structural color change of amorphous photonic hydrogel. Acs Appl. Polym. Mater 3 (2), 757–764. doi:10.1021/acsapm.0c01045
Xia, Z., Deng, Z., Fang, B., Yang, Y., and Sun, F. (2022). A review on sensory perception for dexterous robotic manipulation. Int. J. Adv. Robot. Syst. 19 (2), 172988062210959. doi:10.1177/17298806221095974
Yan, H. L., Chen, Y. Q., Deng, Y. Q., Zhang, L. L., Hong, X., Lau, W. M., et al. (2016). Coaxial printing method for directly writing stretchable cable as strain sensor. Appl. Phys. Lett. 109 (8), 083502. doi:10.1063/1.4961493
Yao, X. L., Yu, W. J., Xu, X., Chen, F., and Fu, Q. (2015). Amphiphilic, ultralight, and multifunctional graphene/nanofibrillated cellulose aerogel achieved by cation-induced gelation and chemical reduction. Nanoscale 7 (9), 3959–3964. doi:10.1039/c4nr07402e
Yoshimura, K., Nakano, K., and Hishikawa, Y. (2016). Flexible tactile sensor materials based on carbon microcoil/silicone-rubber porous composites. Compos. Sci. Technol. 123, 241–249. doi:10.1016/j.compscitech.2015.12.018
Zang, Y. P., Zhang, F. J., Huang, D. Z., Gao, X. K., Di, C. A., and Zhu, D. B. (2015). Flexible suspended gate organic thin-film transistors for ultra-sensitive pressure detection. Nat. Commun. 6, 6269. doi:10.1038/ncomms7269
Zhang, X. C., Hu, H., Tang, D. F., Zhang, C. Q., Fu, J. Z., and Zhao, P. (2021). Magnetic flexible tactile sensor via direct ink writing. Sens. Actuat a-Phys 327, 112753. doi:10.1016/j.sna.2021.112753
Zhang, Y., Magan, J. J., and Blau, W. J. (2014). A general strategy for hybrid thin film fabrication and transfer onto arbitrary substrates. Sci. Rep-Uk 4 (1), 4822. doi:10.1038/srep04822
Zhao, C. L., Xing, L., Xiang, J. H., Cui, L. J., Jiao, J. B., Sai, H. Z., et al. (2014). Formation of uniform reduced graphene oxide films on modified PET substrates using drop-casting method. Particuology 17, 66–73. doi:10.1016/j.partic.2014.02.005
Zheng, Y., He, Z. Z., Gao, Y. X., and Liu, J. (2013). Direct desktop printed-circuits-on-paper flexible electronics. Sci. Rep-Uk 3 (1), 1786. doi:10.1038/srep01786
Zhou, F., and Chai, Y. (2020). Near-sensor and in-sensor computing. Nat. Electron. 3 (11), 664–671. doi:10.1038/s41928-020-00501-9
Zhou, F. C., Zhou, Z., Chen, J. W., Choy, T. H., Wang, J. L., Zhang, N., et al. (2019). Optoelectronic resistive random access memory for neuromorphic vision sensors. Nat. Nanotechnol. 14 (8), 776–782. doi:10.1038/s41565-019-0501-3
Keywords: flexible tactile sensors, stretchable materials, human signal monitoring, robotic, human–computer interaction
Citation: Liu Y-F, Wang W and Chen X-F (2023) Progress and prospects in flexible tactile sensors. Front. Bioeng. Biotechnol. 11:1264563. doi: 10.3389/fbioe.2023.1264563
Received: 21 July 2023; Accepted: 11 September 2023;
Published: 26 September 2023.
Edited by:
Ping Zhou, University of Health and Rehabilitation Sciences, ChinaReviewed by:
Hyo-Ryoung Lim, Pukyong National University, Republic of KoreaCopyright © 2023 Liu, Wang and Chen. This is an open-access article distributed under the terms of the Creative Commons Attribution License (CC BY). The use, distribution or reproduction in other forums is permitted, provided the original author(s) and the copyright owner(s) are credited and that the original publication in this journal is cited, in accordance with accepted academic practice. No use, distribution or reproduction is permitted which does not comply with these terms.
*Correspondence: Ya-Feng Liu, liu20220314@swu.edu.cn
Disclaimer: All claims expressed in this article are solely those of the authors and do not necessarily represent those of their affiliated organizations, or those of the publisher, the editors and the reviewers. Any product that may be evaluated in this article or claim that may be made by its manufacturer is not guaranteed or endorsed by the publisher.
Research integrity at Frontiers
Learn more about the work of our research integrity team to safeguard the quality of each article we publish.